Solahart REC290TP2 User manual

Solahart PV Systems must be installed and serviced by a suitably qualified person.
Installation Instructions
Single-Phase PV Systems

PATENTS
This PV System may be protected by one or more patents or registered designs in the name of
Solahart Industries Pty Ltd.
TRADE MARKS
™ Trademark of Solahart Industries Pty Ltd.
Note: Every care has been taken to ensure accuracy in preparation of this publication.
No liability can be accepted for any consequences, which may arise as a result of its application.
Warning: For continued safety of this PV System, it must be installed, operated and maintained in
accordance with these instructions and the installation guide supplied with the PV inverter.
Caution: Only qualified and accredited personnel should perform work on PV systems, such as design,
installation, commissioning, maintenance and repairs. Be sure to follow the safety instructions for all system
components. It is also important to observe relevant local codes and regulations for health and safety and
accident prevention.
Only Solahart parts and Solahart approved parts may be used. No substitute parts may be used without
prior approval from Solahart Industries Pty Ltd. Only parts supplied by Solahart Industries Pty Ltd are
covered by the Solahart warranty.
The warranty can become void if safety devices are tampered with or if the installation is not in
accordance with these instructions.

3
CONTENTS
Contents....................................................................................................................................... 3
Overview....................................................................................................................................... 4
Wiring Diagrams.......................................................................................................................... 6
Earthing Arrangements –All Systems.................................................................................... 10
Installation Procedure............................................................................................................... 11
Planning ..................................................................................................................................... 12
Racking....................................................................................................................................... 17
Rooftop Isolator......................................................................................................................... 24
Wiring ......................................................................................................................................... 25
Power Optimizers (SolarEdge only) ........................................................................................ 27
PV Modules ................................................................................................................................ 30
Inverter ....................................................................................................................................... 35
Meter (SolarEdge Only)............................................................................................................. 39
Labelling..................................................................................................................................... 42
Commissioning.......................................................................................................................... 44
Engineering Certification.......................................................................................................... 51
Solahart PV System Warranty - Australia Only...................................................................... 53

4
OVERVIEW
The following installation instructions detail installation procedures for photovoltaic modules, power optimizers,
inverter, module racking systems and balance of system (BOS) components.
Prior to the installation of any grid connected PV system, a Site Visit shall be performed in accordance with
the Clean Energy Council’s “Grid-Connected Solar PV Systems - Design Guidelines for Accredited Installers”.
SAFETY REQUIREMENTS
The voltages and currents produced by a single module or modules connected in series (voltages added
together) or in parallel (currents added together) can be dangerous.
Although module DC plug connectors are insulated to provide touch safe protection, the following points must
be observed when handling modules in order to avoid the risk of sparking, fire hazard, burn risk, and lethal
electric shocks:
Exercise extreme caution when wiring modules and look out for damaged or split cable ends.
Do not perform wiring work in rainy or damp conditions.
Never insert metallic or otherwise conductive objects into plugs or sockets.
Ensure that all electrical connections are completely dry and free from contaminants before they are
assembled.
Ensure that connections are tight and correctly made.
Keep all materials, tools and work areas clean and dry.
Always use appropriate safety equipment such as insulated tools and wear personal protective equipment
such as insulated gloves.
Solar modules produce current when exposed to sunlight. It is recommended that the system is shielded
with an opaque cover during installation, maintenance or repair work.
INSTALLER RESPONSIBILITIES
The installer is solely responsible for:
Observing and conforming to all relevant Australian Standards, all relevant Clean Energy Council
Accreditation guidelines and all applicable laws, ordinances, regulations, codes of practice and local or
national building codes, including any that may have superseded these Installation Instructions.
Ensuring that the installation complies with AS/NZS 3000, AS/NZS 5033, AS/NZS 1170.2,
AS/NZS 1562.1, AS 4777.1, AS/NZS 1768, AS/NZS 3008, AS 2050 and any relevant electrical service
and installation rules for the state or territory where the system is installed.
Ensuring that the PV System and associated components are appropriate for the particular installation
and the installation environment.
Ensuring that the roof, roof rafters, battens, purlins, connections, and other structural support members
can support the total assembly under building live load conditions. The roof on which the PV system is to
be installed must have the capacity to resist the combined Design Dead Load and Live Load at each
mounting point.
Ensuring only parts supplied by Solahart Industries and installer supplied parts as specified by Solahart
Industries are utilised (substitution of parts may void the warranty and invalidate certification).
Ensuring that lag screws have adequate pull-out strength and shear capacities to suit the installation.
Maintaining the waterproof integrity of the roof, including selection of appropriate flashing.
Ensuring safe installation of all electrical aspects of the PV system.

OVERVIEW
5
DISCLAIMER OF LIABILITY AND WARRANTY
Solahart assumes no responsibility for loss, damage or expense resulting from improper installation, handling
or misuse of PV modules. Refer to “Solahart PV System Warranty - Australia Only” on page 53 for full warranty
terms and conditions.
IEC 61730 INFORMATION
Modules supplied by Solahart are designed to fulfil the criteria of application Class A requirements according
to IEC 61730. Modules are qualified for application Class A: Hazardous voltage (Higher than 50 V DC) and
hazardous power (higher than 240 W) applications where general contact access is anticipated. For the
purposes of AS/NZS 3000, modules are classified as Class I equipment.
FIRE GUIDELINES
Utilise the following fire safety guidelines when installing modules supplied by Solahart:
Modules supplied by Solahart have a Class C Fire Rating.
Check with local authorities for guidelines and requirements concerning fire safety for any building or
structure on to which the modules will be installed.
The system design should ensure that fire fighting personnel can access the system in the event of a
building fire. Check with local authorities for any applicable regulations concerning setbacks or other
placement restrictions that may apply for roof-mounted PV arrays.
Any electrical equipment can pose a fire risk. Modules must therefore be mounted over a fire retardant
roof covering rated for the application and a distance of 60mm between the module and the mounting
surface must be respected to allow free circulation of air beneath the module.
ENVIRONMENTAL FACTORS
Solahart’s limited warranty is based upon modules being installed in accordance with the following conditions:
Modules are not suitable for installation in potentially hazardous locations.
Modules should not be installed in locations:
near sources of flammable gases, vapours or open flames.
in direct contact with salt water/spray. Avoid installing in areas subject to high salt mist content.
which experience extreme hail and/or snow.
where they may be exposed to sulphur e.g. near sulphur springs or volcanoes
where they may be exposed to harmful chemicals.
WARNINGS
Warning: This document provides sufficient information for system installation heights up to 10 m. If the
installation site is more than 10 m in height contact Solahart Industries for further advice.
Warning: This system has not been certified for, and should not be installed in, wind region D.
Warning: During installation and when working on the roof, be sure to observe the appropriate OH&S safety
regulations and relevant regulations of your local region.
Warning: Ensure electrical connection/ disconnection is performed only when the relevant circuit is isolated.
Do not connect / disconnect wiring under load conditions.
Warning: Do not expose the PV modules to artificially concentrated light.
Warning: Do not drill holes in the modules as this will void product warranty.

6
WIRING DIAGRAMS
SINGLE INPUT INVERTER SYSTEMS
For DC Isolator Wiring refer to “DC Isolator Wiring”on page 26.
REC280TP Modules
Inverter
Min No
of
Modules
Max No of
Modules
per String
Max
No of
Strings
Max No
of
Modules
per
Inverter
Max
System
Power
Rating
(W) *
Isc (A)*
per
String
Voc (V)*
UNO-DM-2.0-TL-PLUS-B
3
8
1
8
2240
9.4
Check
Voltage
Tables on
page 9
SB1.5-1VL-40
3
7
1
7
1960
9.4
SB2.5-1VL-40
3
11
1
11
3080
9.4
REC290TP2 Modules
Inverter
Min No
of
Modules
Max No of
Modules
per String
Max
No of
Strings
Max No
of
Modules
per
Inverter
Max
System
Power
Rating
(W) *
Isc (A)*
per
String
Voc (V)*
UNO-DM-2.0-TL-PLUS-B
3
8
1
8
2320
9.58
Check
Voltage
Tables on
page 9
SB1.5-1VL-40
3
6
1
6
1740
9.58
SB2.5-1VL-40
3
11
1
11
3190
9.58
* Values measured at standard test conditions (STC) defined as: irradiance of 1000 W/m2,Spectrum AM 1.5
and cell temperature 25ºC. Variations from STC values will affect actual Isc and Voc and should be allowed for.
Note: -10oC used to calculate maximum V. If minimum temperatures are expected to be lower than -10oC,
maximum number of modules must be re-evaluated.
For earthing arrangement and wiring diagram refer to “Earthing Arrangements –All Systems” on page 10.

WIRING DIAGRAMS
7
MULTIPLE INPUT INVERTER SYSTEMS
For DC Isolator Wiring refer to “DC Isolator Wiring”on page 26.
REC280TP Modules
Inverter
Min No
of
Modules
Max No of
Modules
per String
Max
No of
Strings
Max No of
Modules
per
Inverter
Max
System
Power
Rating
(W) *
Isc (A)*
per
String
Voc (V)*
SB3.0-1AV-40
5
13
2
14
3920
9.4
Check
Voltage
Tables on
page 9
SB4.0-1AV-40
5
13
2
19
5320
9.4
SB5.0-1AV-40
5
13
2
23
6440
9.4
PVI-3.0-TL-OUTD
4
13
2
14
3920
9.4
PVI-4.2-TL-OUTD
4
13
2
20
5600
9.4
PVI-5000-TL-OUTD
4
13
2
21
5880
9.4
UNO-DM-3.3-TL-PLUS-B
4
13
2
15
4200
9.4
UNO-DM-4.0-TL-PLUS-B
4
13
2
19
5320
9.4
UNO-DM-5.0-TL-PLUS-B
4
13
2
23
6440
9.4
REC290TP2 Modules
Inverter
Min No
of
Modules
Max No of
Modules
per String
Max
No of
Strings
Max No of
Modules
per
Inverter
Max
System
Power
Rating
(W) *
Isc (A)*
per
String
Voc (V)*
SB3.0-1AV-40
5
13
2
13
3770
9.58
Check
Voltage
Tables on
page 9
SB4.0-1AV-40
5
14
2
18
5220
9.58
SB5.0-1AV-40
5
14
2
22
6380
9.58
PVI-3.0-TL-OUTD
4
13
2
13
3770
9.58
PVI-4.2-TL-OUTD
4
14
2
19
5510
9.58
PVI-5000-TL-OUTD
4
14
2
21
6090
9.58
UNO-DM-3.3-TL-PLUS-B
4
14
2
15
4350
9.58
UNO-DM-4.0-TL-PLUS-B
4
14
2
18
5220
9.58
UNO-DM-5.0-TL-PLUS-B
4
14
2
22
6380
9.58

WIRING DIAGRAMS
8
* Values measured at standard test conditions (STC) defined as: irradiance of 1000 W/m2,Spectrum AM 1.5
and cell temperature 25ºC. Variations from STC values will affect actual Isc and Voc and should be allowed for.
Note: -10oC used to calculate maximum V. If minimum temperatures are expected to be lower than -10oC,
maximum number of modules must be re-evaluated.
For earthing arrangement and wiring diagram refer to “Earthing Arrangements –All Systems”on page 10.
SE5000 INVERTER SYSTEMS
For DC Isolator Wiring refer to “DC Isolator Wiring”on page 26.
REC280TP Modules
Inverter
Min No
of
Modules
Max No of
Modules
per String
Max
No of
Strings
Max No of
Modules
per
Inverter
Max System
Power Rating
(W) *
Max
Inverter
Current
(A)*
Max
Inverter
Voltage
(V)*
SE5000
SE5000-xxxxxxx **
8
18
2
23
6440
19.5
500
SE5000H
8
20
2
23
6440
13.5
480
REC290TP2 Modules
Inverter
Min No
of
Modules
Max No of
Modules
per String
Max
No of
Strings
Max No of
Modules
per
Inverter
Max System
Power Rating
(W) *
Max
Inverter
Current
(A)*
Max
Inverter
Voltage
(V)*
SE5000
SE5000-xxxxxxx **
8
18
2
22
6380
19.5
500
SE5000H
8
19
2
22
6380
13.5
480

WIRING DIAGRAMS
9
* Values measured at standard test conditions (STC) defined as: irradiance of 1000 W/m2,Spectrum AM 1.5
and cell temperature 25ºC. Variations from STC values will affect actual Isc and Voc and should be allowed for.
** This model may have suffixes indicating different options and functionality.
Note: -10oC used to calculate maximum V. If minimum temperatures are expected to be lower than -10oC,
maximum number of modules must be re-evaluated.
For earthing arrangement and wiring diagram refer to “Earthing Arrangements –All Systems”on page 10.
VOLTAGE TABLES FOR SMA AND ABB SYSTEMS
Voc of REC280TP = 39.2V
REC280TP
No of Modules per String
Voc of the String
No of Modules per String
Voc of the String
3
117.6
9
352.8
4
156.8
10
392
5
196
11
431.2
6
235.2
12
470.4
7
274.4
13
509.6
8
313.6
Voc of REC290TP2 = 38.8V
REC290TP2
No of Modules
per String
Voc of the
String
No of Modules per
String
Voc of the
String
3
116.4
9
349.2
4
155.2
10
388
5
194
11
426.8
6
232.8
12
465.6
7
271.6
13
504.4
8
310.4
14
543.2
VOLTAGE TABLES FOR SOLAREDGE SYSTEMS
Note: SolarEdge Inverters operate on a fixed string voltage. The Voc of the string is fixed to the nominal DC
voltage of the inverter regardless of the panel Voc.
Voc of REC280TP = 39.2V
Voc of REC290TP2 = 38.8V
Inverter Model
Nominal DC Voltage
Voc of string
SE5000
350 Vdc
350 Vdc
SE5000-xxxxxxxxx *
400 Vdc
400 Vdc
SE5000H
380 Vdc
380 Vdc
* This model may have suffixes indicating different options and functionality.

10
EARTHING ARRANGEMENTS –ALL SYSTEMS
Earthing connections must be made so the removal of one component (e.g. a module) does not interrupt the
earthing to other parts of a system (e.g. other modules). Daisy chaining is not permitted. The PV system earth
connection must be directly connected to the switchboard earth link, not via the inverter earth connection. If
the earth cable could be exposed to direct sunlight, it must have a physical barrier to protect the earth cable
from this exposure.
Earth wires must be sized in accordance with requirements set out in Earthing and bonding arrangements of
AS/NZS 5033.
Solahart approved earthing plates may be used to earth modules via the racking, instead of wiring directly to
the module frames. Refer to “Earthing” on page 31 for more information.
Warning: Do not drill holes in the modules as this will void product warranty.
The racking may be earthed by means of a rooftop isolator bracket. Refer to “Rooftop Isolator” on page 24 for
details.
Where it is necessary to make an earthing connection to a rail that does not have a rooftop isolator bracket
fitted, a rail splice piece will provide a suitable surface for connection. In this case, the splice should be attached
to the end of the rail using both fixing bolts, and then the earth lug connected to the splice as shown in the
figures below:
1. Slide rail splice onto end of rail, ensuring an overhang of approximately 50 mm.
2. Secure rail splice by tightening both Allen head bolts to 15 Nm.
3. Drill a hole in the centre of the rail splice, attach the earth cable using the earthing set supplied, and tighten
to 5 Nm.
Rail splice attached to rail with both Allen head bolts
Earth cable connected to splice

11
INSTALLATION PROCEDURE
1. Planning –Design the system and layout. Refer to “Planning” on page 12.
2. Determine the spacing of the Rail Supports using the “Maximum Rail Support Spacing Tables” on page
18 and considering the following factors (refer to “Planning” on page 12):
a. Wind Region
b. Terrain Category
c. Roof Type
d. Roof Area
e. Building Height
f. Array Orientation
3. Install the Racking (Rail and Rail Supports). Refer to “Racking” on page 17.
4. Install the remainder of the roof top components as follows:
a. Rooftop Isolator. Refer to “Rooftop Isolator” on page 24.
b. Rooftop Wiring. Refer to “Wiring”on page 25.
c. Power Optimizers. Refer to “Power Optimizers (SolarEdge only)” on page 27.
d. PV modules. Refer to “PV Modules” on page 30.
5. Install the inverter. Refer to “Inverter” on page 35.
6. Install the energy meter (optional component). Refer to “Meter (SolarEdge Only)” on page 39.
7. Install the system labels. Refer to “Labelling” on page 42.
8. Commission the PV system. Refer to “Commissioning” on page 44.

12
PLANNING
INSTALLATION TOOLS
4,5 & 6 mm Allen keys or 4,5 & 6 mm Allen Key fittings to suit torque adjustable drill (for racking
components and inverter)
Torx T20 screwdriver (ABB inverter systems only)
Cordless torque adjustable drill
Angle grinder with stone disk (for tile cutting if required)
Electricians hand tools (screwdrivers, pliers etc.)
String line
Timber to shim tile roof interfaces (if required)
STRUCTURAL ASSESSMENT
The installer is responsible for ensuring that the building and building structures are capable of withstanding
the additional loads and forces generated as a result of installing the PV system. For domestic dwellings, it is
recommended that a structural engineering assessment is completed. For all other installations, a structural
assessment is required to be completed by a qualified structural engineer.
COMMUNICATIONS DEVICES
Complete installation of inverter communications devices requires the installer to register the communication
device and inverter on the inverter manufacturer’s web portal. Hence, to complete the communications
equipment installation, the installer must have access to the PV system owner’s internet connection. An
example of items that should be organised prior to onsite installation are:
Confirmation that an internet accessible network port is available
Length of networking cable required from inverter to networking port
Wi-Fi access including SSID and password
PV system owner’s network administrator permission and assistance to adjust firewall, network
address translation (NAT) and port forwarding settings.
PV MODULE ORIENTATION AND INCLINATION
To maximize system output, install modules at optimum orientation and inclination (tilt) angles. The specifics
of this will depend on the installation location and must be calculated by a qualified system designer. The ideal
angle for mounting a module should result in the sun’s rays falling perpendicular (i.e. at a 90° angle) to the
module surface.
Note: All modules in each series string must have the same orientation and inclination to ensure that modules
do not underperform due to a mismatching of each module’s output.
Modules should be installed in a shade free position. Even minor or partial
shading of the modules/array will reduce array/system output. A module is
considered shade free when it is both:
Free from shade or shadows all year round.
Exposed to several hours of direct sunlight, even during the
shortest days of the year.
Note: The following information is provided as a guide only:
Modules should be installed facing toward true north. Where this
orientation is not practical, a system facing up to 45° (NW or NE)
from true north is satisfactory however losses of up to
approximately 6% will occur. A module facing due east or due
west will experience a loss in performance of approximately 18%.
Inclination of modules should be approximately equal to the local latitude angle. The latitude of some
Australian cities is shown in the “Latitude of Some Australian Cities”on page 13. Modules may be

PLANNING
13
installed at the roof angle for simplicity of installation and appearance, however, if inclination varies by
±15º or more from the correct inclination, performance losses of 4% or more will occur.
Modules should be inclined at an angle of at least 10° to support the self-cleaning function of the
glass.
Losses for incorrect orientation and incorrect inclination will be compounded.
If the roof angle is flat, adjustable or fixed tilt legs should be considered to optimise inclination
depending upon area.
For an installation at right angles to (across) a tile roof pitch, landscape tile roof hooks are required.
Each module and its fittings including racking weighs approximately 25 kg.
LATITUDE OF SOME AUSTRALIAN CITIES
Adelaide
35°S
Cairns
17°S
Hobart
42°S
Port Hedland
20°S
Alice Springs
24°S
Canberra
35°S
Mildura
34°S
Rockhampton
24°S
Brisbane
27°S
Darwin
12°S
Melbourne
38°S
Sydney
34°S
Broken Hill
31°S
Geraldton
28°S
Perth
32°S
Townsville
19°S
WIND REGION
Use the wind region diagram shown below to determine the wind region of the installation site.
Wind region notes:
Wind regions are predefined for all of Australia by Australian Standard AS/NZS 1170.2. The Wind
Region has nothing to do with surrounding topography or buildings.
Most of Australia is designated Region A which indicates a Regional Ultimate Basic Wind Velocity of
45 m/s.
Some areas are designated Region B (57 m/s). Local authorities will advise if this applies in your
area.
Region C areas (66 m/s) are generally referred to as Cyclonic and are generally limited to northern
coastal areas. Most Region C zones end 100 km inland.
Region D (80 m/s) Australia's worst Cyclonic Region between Carnarvon and Pardoo in WA.

PLANNING
14
TERRAIN CATEGORY
The terrain over which the approaching wind flows towards a structure must be assessed on the basis of the
following category descriptions:
Terrain Category 2: Open terrain, including grassland, with well-scattered obstructions having heights
generally from 1.5 m to 5 m, with no more than two obstructions per hectare, e.g. farmland and cleared
subdivisions with isolated trees and uncut grass.
Terrain Category 3: Terrain with numerous closely spaced obstructions having heights generally from 3 m to
10 m. The minimum density of obstructions shall be at least the equivalent of 10 house-size obstructions per
hectare, e.g. suburban housing or light industrial estates.
ROOF TYPE
Determine the roof type of the building where the PV modules are to be installed and select the appropriate
rail support.
Rail support systems are available as follows:
Roof Type
Roof Pitch
Rail Support Category
Rail Support Name (Options)
Standard tile
10 - 30º
Tile roof interface
Tile interface (Portrait)
Tile interface (Landscape)
Low profile tile
Flat tile interface
Slate
Slate interface
Metal
10 - 30º
Metal roof interface
Metal roof interface
Metal
Corrugated
< 10 º
or
< Latitude minus 15º
Tilt leg interface
10 - 15° adjustable tilt legs
15 - 30° adjustable tilt legs
30° fixed tilt legs
30 - 60° adjustable tilt legs
ROOF AREA
Determine the installation area on the roof (roof position area). The diagrams below show roof position areas
designated as “Edge Zone”areas and “Centre Zone”areas according to interface type.
Edge zone areas are subject to higher wind loadings and therefore will require closer rail support spacing.
Warning: If any part of the system array is located in one of the edge zones, the entire array must use the
support spacing specified for the edge zones.

PLANNING
15
Use the following diagram, tables and worked example to determine the minimum required roof area for
the array when designing and installing with REC280TP modules.
REC280TP spacing and dimensions
Worked Example:
Number of rows: 2
Number of modules per row: 10
Total number of modules = 20
Calculating H:
H=Nrows×(1,665+20)-20
H=2×1,685-20
H=3,350 mm
Calculating W:
W=
Nmodules/row×(991+18)+(2×25)-18
W=10×1,009+50-18
W=10,122 mm
Calculating AreaRoof in mm2:
AreaRoof=H×W
AreaRoof=3,350×10,122
AreaRoof=33,908,700 mm2
Converting AreaRoof in mm2to m2:
AreaRoof=33,908,700
1,000,000 =33.91 m2
Calculating AreaRoof in m2:
AreaRoof=H
1,000 ×W
1,000
AreaRoof=3,350
1,000 ×10,122
1,000
AreaRoof=3.35×10.122
AreaRoof=33.91 m2
Notes:
Modules installed in portrait as per diagram
For tilt leg systems, row spacing must prevent shading of one row by another and needs to be calculated on
an individual site basis, taking into account orientation, roof pitch and module inclination
All dimensions are in mm, unless otherwise stated.
Number of modules per row –REC280TP
1
2
3
4
5
6
7
8
9
10
…
Number of rows
H
1665
1665
1665
1665
1665
1665
1665
1665
1665
1665
1
X
X
X
X
X
X
X
X
X
X
X
W
1041
2050
3059
4068
5077
6086
7095
8104
9113
10122
H
3350
3350
3350
3350
3350
3350
3350
3350
3350
3350
2
X
X
X
X
X
X
X
X
X
X
X
W
1041
2050
3059
4068
5077
6086
7095
8104
9113
10122
…
Number of modules per row –REC280TP
1
2
3
4
5
6
7
8
9
10
…
Number of rows
Roof
1
Area
1.73
3.41
5.09
6.77
8.45
10.13
11.81
13.49
15.17
16.85
(m2)
Roof
2
Area
3.49
6.87
10.25
13.63
17.01
20.39
23.77
27.15
30.53
33.91
(m2)
…

PLANNING
16
Use the following diagram, tables and worked example to determine the minimum required roof area for
the array when designing and installing with REC290TP2 modules.
REC290TP2 spacing and dimensions
Worked Example:
Number of rows: 2
Number of modules per row: 10
Total number of modules = 20
Calculating H:
H=Nrows×(1,675+20)-20
H=2×1,695-20
H=3,370 mm
Calculating W:
W=
Nmodules/row×(997+18)+(2×25)-18
W=10×1,015+50-18
W=10,182 mm
Calculating AreaRoof in mm2:
AreaRoof=H×W
AreaRoof=3,370×10,182
AreaRoof=34,313,340 mm2
Converting AreaRoof in mm2to m2:
AreaRoof=34,313,340
1,000,000 =34.31 m2
Calculating AreaRoof in m2:
AreaRoof=H
1,000 ×W
1,000
AreaRoof=3,370
1,000 ×10,182
1,000
AreaRoof=3.37×10.182
AreaRoof=34.31 m2
Notes:
Modules installed in portrait as per diagram
For tilt leg systems, row spacing must prevent shading of one row by another and needs to be calculated on
an individual site basis, taking into account orientation, roof pitch and module inclination
All dimensions are in mm, unless otherwise stated.
Number of modules per row –REC290TP2
1
2
3
4
5
6
7
8
9
10
…
Number of rows
H
1675
1675
1675
1675
1675
1675
1675
1675
1675
1675
1
X
X
X
X
X
X
X
X
X
X
X
W
1047
2062
3077
4092
5107
6122
7137
8152
9167
10182
H
3370
3370
3370
3350
3370
3370
3370
3370
3370
3370
2
X
X
X
X
X
X
X
X
X
X
X
W
1047
2062
3077
4092
5107
6122
7137
8152
9167
10182
…
Number of modules per row –REC290TP2
1
2
3
4
5
6
7
8
9
10
…
Number of rows
Roof
1
Area
1.75
3.415
5.15
6.85
8.55
10.25
11.95
13.65
15.35
17.05
(m2)
Roof
2
Area
3.53
6.95
10.37
13.79
17.21
20.63
24.05
27.47
30.89
34.31
(m2)
…

17
RACKING
OVERVIEW OF RACKING COMPONENTS
Overview of components for tile roof
Rail
(a)
Rail splices
(c)
Tile roof
Interfaces (b)
Z-modules with
Allen head bolt
Wood screws M6
x 80
Overview of components for metal roof
Rail
(a)
Rail splices
(c)
Metal roof
interfaces (b)
Z-modules with
Allen head bolt
Wood screws M6
x 90 *
Overview of components for adjustable tilt legs
Rail
(a)
Rail splices
(c)
Z-modules with
Allen head bolt
Front rail &
leg foot (d)
Adjustable
tilt leg (e)
Wood Screws
M6x90 *
Overview of components for 30º fixed tilt legs
Rail
(a)
Rail splice
(c)
Z-modules with
Allen head bolts
Front rail &
leg foot (d)
Fixed
tilt leg (e)
Wood Screws
M6x90 *
* Note: Screws must be fit for purpose e.g. screws used in metal purlins must be suitable for metal structures
and have a TPI (threads per inch) of 14.
Tile & Metal Roof Diagram (Tile Roof shown)
Tilt Leg Diagram (Adjustable Tilt Leg shown)
Rail Support Spacing
Rail Support Spacing
Rail
Spacing
Rail
Spacing
Rail Overhang

RACKING
18
RAIL SUPPORT SPACING
Use the following tables to determine the rail support spacing for the relevant roof type based on the previously
determined wind region, terrain category, roof position area (Edge Zone or Centre Zone) and maximum height
of the installation.
MAXIMUM RAIL SUPPORT SPACING TABLES
Wind Region A
Terrain Category
2
3
Roof Area
Edge Zone
Centre Zone
Edge Zone
Centre Zone
Roof Height (m)
5
10
5
10
5
10
5
10
Tile Roof (Timber Rafters only)
1200
950
1575
1275
1475
1800
Metal Roof with Timber Battens
1505
1247
1700
1600
1675
1800
Metal Roof with Steel Battens
1075
890
1523
1261
1432
1800
Tilt Legs –PV Module Angle 15°
1325
1025
1500
1254
1400
1575
Tilt Legs –PV Module Angle 30°
1089
902
1400
1350
1325
1500
Wind Region B
Terrain Category
2
3
Roof Area
Edge Zone
Centre Zone
Edge Zone
Centre Zone
Roof Height (m)
5
10
5
10
5
10
5
10
Tile Roof (Timber Rafters only)
825
675
1100
875
1025
1350
Metal Roof with Timber Battens
938
777
1329
1101
1250
1759
Metal Roof with Steel Battens
670
555
949
786
893
1265
Tilt Legs –PV Module Angle 15°
927
768
944
782
1235
1257
Tilt Legs –PV Module Angle 30°
679
562
1078
892
904
1435
Wind Region C
Terrain Category
2
3
Roof Area
Edge Zone
Centre Zone
Edge Zone
Centre Zone
Roof Height (m)
5
10
5
10
5
10
5
10
Tile Roof (Timber Rafters only)
525
450
700
575
650
850
Metal Roof with Timber Battens
582
526
825
745
910
735
1289
1042
Metal Roof with Steel Battens
416
375
589
532
650
525
921
744
Tilt Legs –PV Module Angle 15°
576
520
586
529
850
727
915
740
Tilt Legs –PV Module Angle 30°
421
380
669
604
658
532
1045
845
Roof interfaces must be fixed to rafters or purlins under the roof cladding. Screw minimum embedment into
timber rafters is 50 mm and 35 mm for timber battens.
Steel purlins must meet the following minimum requirements:
Roof interface
Minimum steel purlin specification
Metal roof interface
0.55 mm BMT 550 Grade or 0.75 mm BMT 450 Grade
Tilt leg interface
1.0 mm BMT 500 Grade
Note: Screws supplied with the roof interfaces are wood screws suitable for timber only. Screws used in metal
purlins must be suitable for metal structures and have a TPI (threads per inch) of 14.

RACKING
19
RAIL SPACING
Rails should be spaced so that the module is clamped in the correct positions.
In general, the rails may be spaced between 833 mm and 1249 mm apart for REC280TP modules and 843 mm
and 1259 mm apart for REC290TP2 modules.
RAIL OVERHANG
Rail end overhang must be no greater than 50% of rail support spacing. For example; if rail support spacing is
1200 mm, rail end overhang can be up to 600 mm. In this case, two rail support brackets can support a rail up
to 2400 mm in length (1200 mm between brackets and 600 mm of overhang at each end).
Note: Drawings not to scale
Rail Spacing:
REC280TP: 833 –1249 mm
REC290TP2: 843 –1259 mm
Rail Support
Spacing = x
Rail Overhang < x/2

RACKING
20
TILE ROOF INSTALLATION
Note: The tile roof interface is only suitable for installation on timber rafters.
1. Determine and mark the position of the
tile roof interfaces according to your
plans. Remove the roof tiles at marked
positions or, if possible, simply move the
tiles up slightly.
2. Fix the tile roof interfaces to rafters
using two M6 X 80 mm wood screws.
Ensure a 50 mm minimum screw
embedment into the rafters.
3. Warning: Tile roof interfaces must not
press against roof tiles and must be
fixed parallel with rafters. If necessary,
pack underneath tile roof interfaces with
timber.
Incorrect
Correct
4. Warning: Do not use tile roof interfaces
as a climbing support as extreme
loading of this point could cause
damage to the tile below.
5. For thin tiles (such as slate, shingles)
proceed directly to step 6.
For thick tiles (such as grooved tiles), if
necessary, use an angle grinder to
chase a recess (or remove raised
groves) on the tile that covers the tile
roof interface at the point where the
interface protrudes through so that the
tile lies flat.
For thick tiles it may also be necessary
to cut a recess into the tile located below
the tile roof interface.
Now proceed to installation of the rails.
Refer to “Rail Installation”on page 23.
This manual suits for next models
1
Table of contents
Other Solahart Solar Panel manuals
Popular Solar Panel manuals by other brands
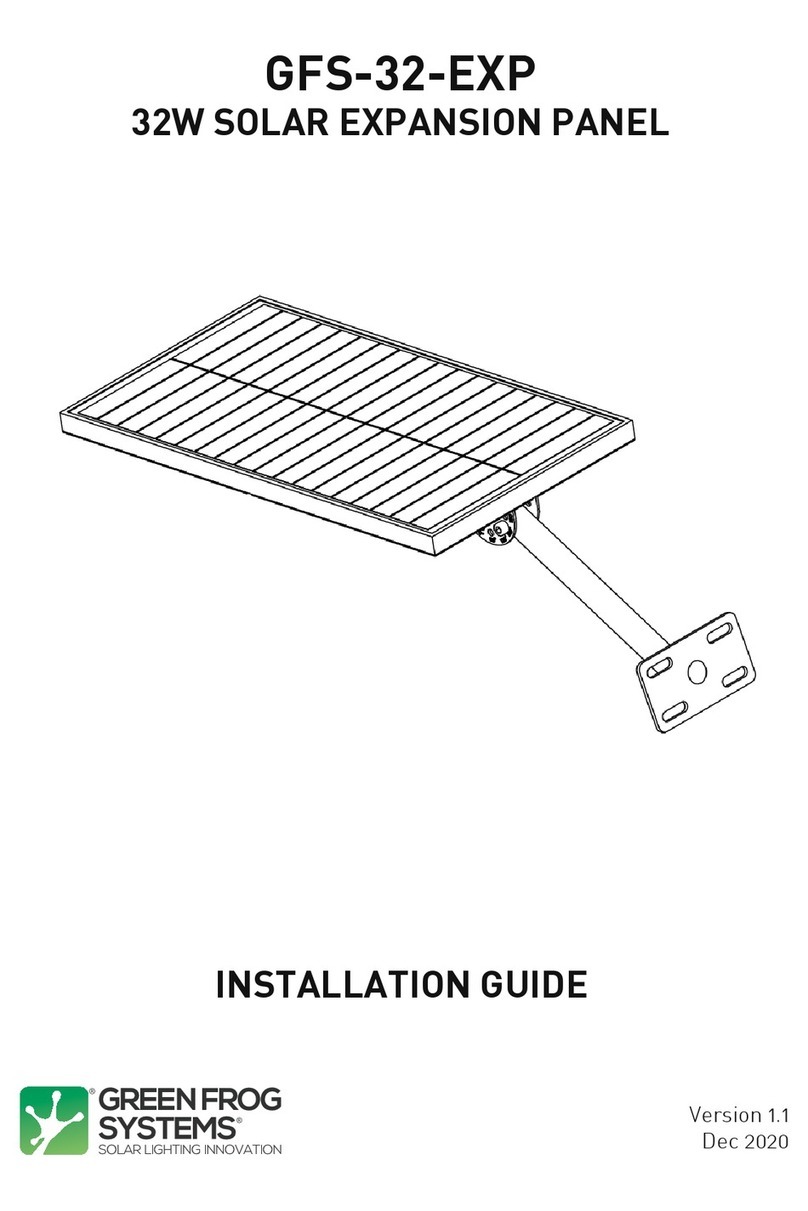
GREEN FROG SYSTEMS
GREEN FROG SYSTEMS GFS-32-EXP installation guide
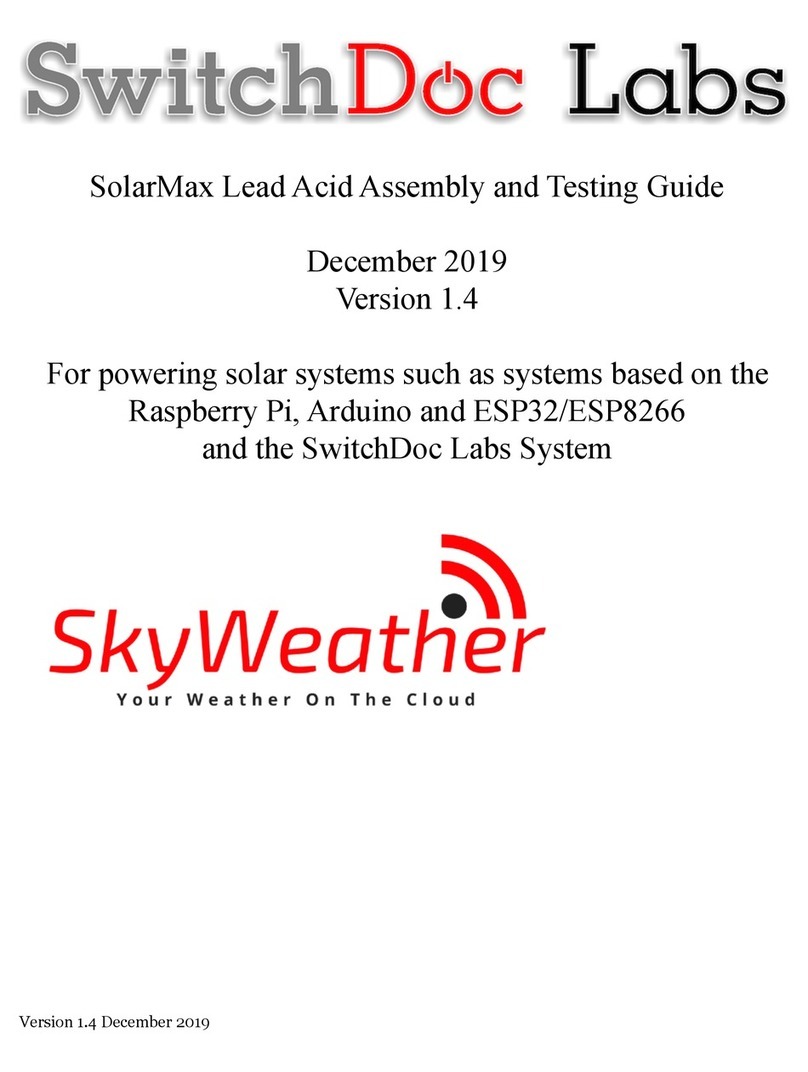
SwitchDoc Labs
SwitchDoc Labs SolarMax Lead Acid ASSEMBLY AND TESTING GUIDE

STIEBEL ELTRON
STIEBEL ELTRON SOL 27 PREMIUM S Operation and installation
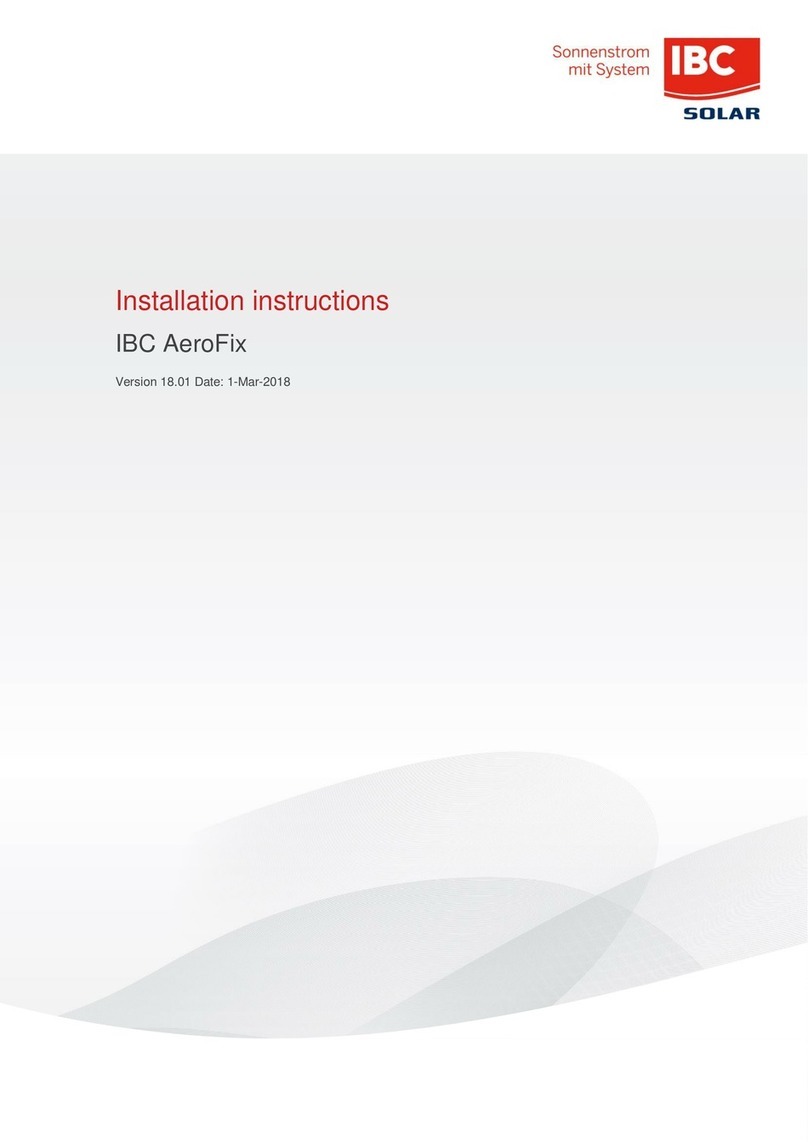
IBC SOLAR
IBC SOLAR AeroFix 15-S installation instructions
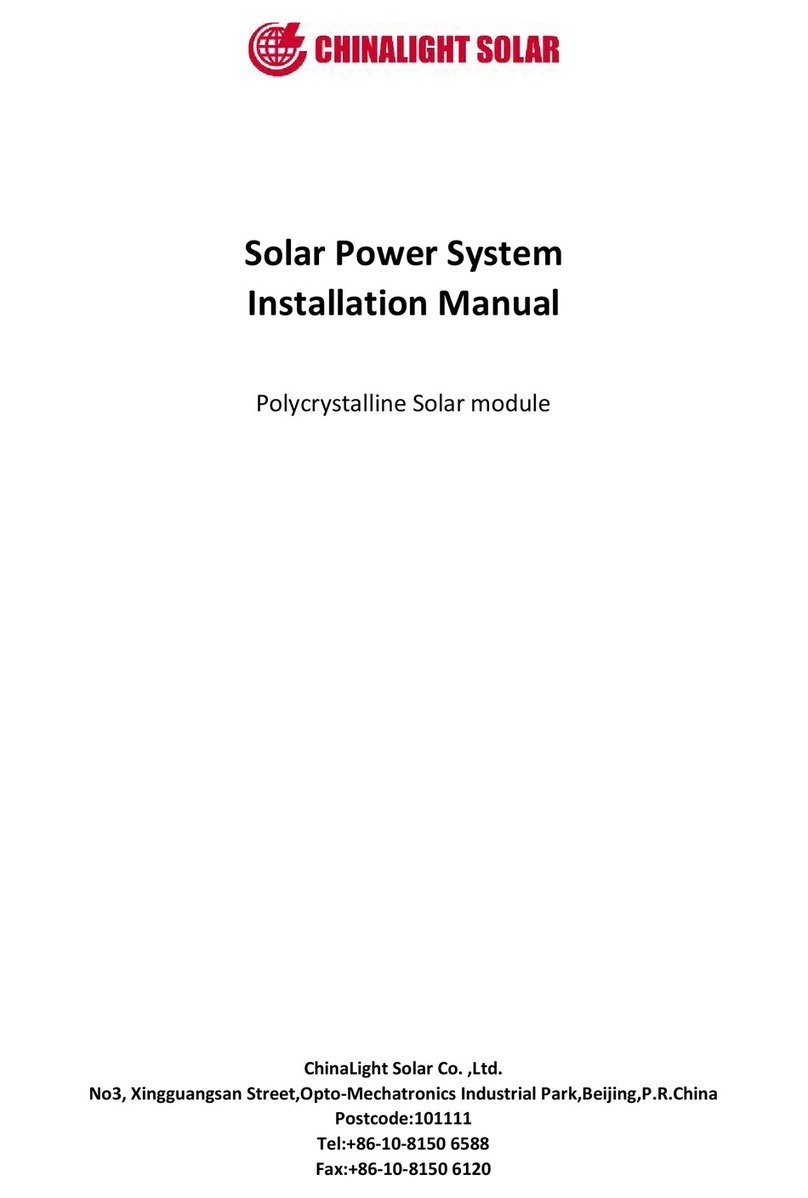
ChinaLight Solar
ChinaLight Solar CLS-230P installation manual
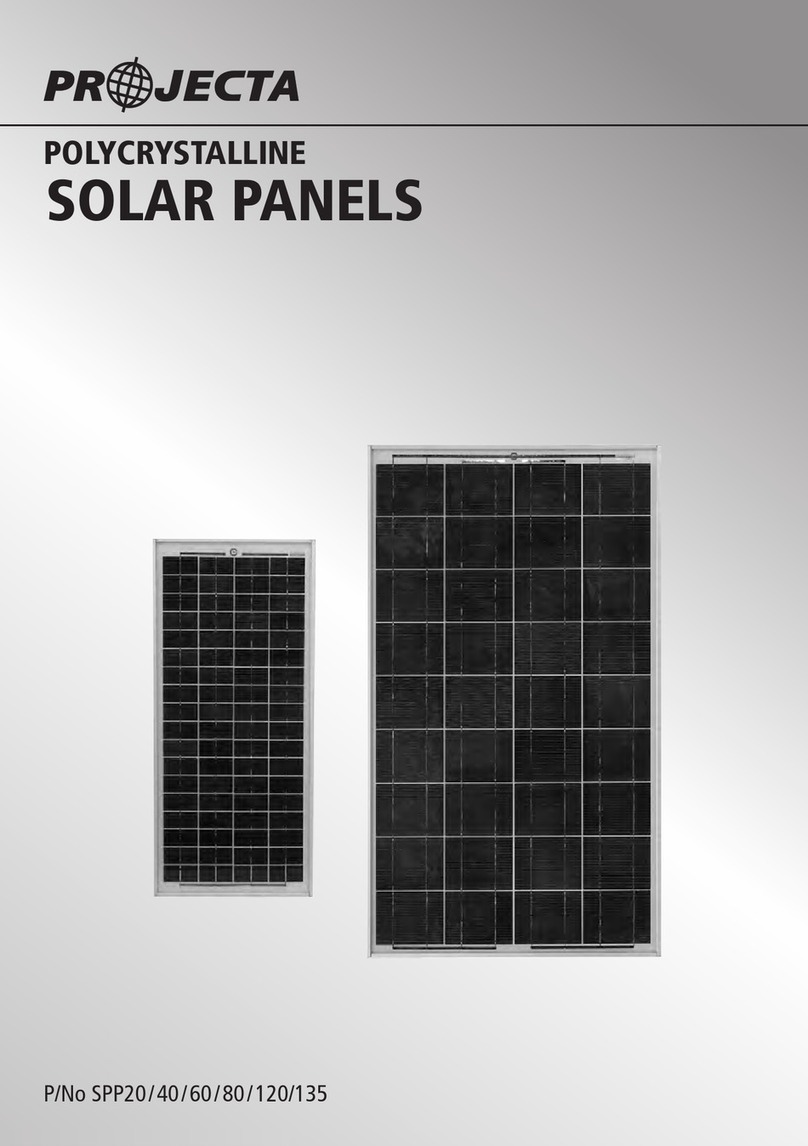
Brown & Watson
Brown & Watson SPP20 user guide