SPX 5280 User manual

Model Nos. 5280 / OEM DPF-A
User Manual
Manual del usuario
Manuel de l’utilisateur
Patent No. 7,384,455

This user manual provides cleaning instructions for after-treatment diesel particulate
filters (DPFs).
•The after-treatment diesel oxidation catalyst and the after-treatment diesel particulate
filter housing must be free of dents.
• Mounting flanges must be free of dents, cracks, or gouges in order to seal correctly
with the gaskets.
• After-treatment diesel particulate filters should be inspected prior to cleaning using
appropriate OE technical procedures.
•
DPF cleaning machines are not designed to clean DPF filters that are plugged as
a result of excessive fluids in the exhaust system, such as coolant, fuel, or oil.
• SPX is not liable for a pre-existing condition in the DPF that would render the
filter unstable, if using the cleaning machine identifies such a condition exists.
Particulate filters that do not pass these criteria should be
replaced and not cleaned.

3
536119 Rev. C August 10, 2009
Safety Precautions ......................................4
Explanation of Safety Signal Words......................4
Initial Setup ............................................5
KeypadFunctions ...................................5
Loading the DPF ........................................7
The Cleaning Cycle ....................................11
Automatic Reverse Cleaning Process ...................12
Maintenance ..........................................13
VacuumFilter .....................................13
Air Filter / Dryer ....................................15
Replace the Coalescing Filter.....................15
ReplacetheDesiccant..........................16
Regenerate the Desiccant . . . . . . . . . . . . . . . . . . . . . . .16
Cartridge Filters ....................................17
Air Tank ..........................................19
HEPA Filter........................................19
Bleeding the Hydraulic System ........................20
Replacement and Optional Parts .........................21
Troubleshooting Guide .................................22
Warranty Statement ............................ back cover
Table of Contents

4
WARNING
Safety Precautions
Ash produced by diesel particulate filters has been declared a hazardous waste in some areas of the
United States. Follow federal, state, and local procedures for the handling and disposal of ash.
To prevent personal injury when using the Diesel Particulate Filter Cleaner :
•Study, understand, and follow all instructions before operating this device. If the operator cannot
read these instructions, operating instructions and safety precautions must be read and discussed
in the operator’s native language.
•Wear eye protection that meets OSHA standards. If there is eye contact with the ash, flush eyes
with cold water for 30 minutes.
•Set up the DPF Cleaner in an area where there is adequate ventilation. Wear a dust mask (rated
N95) to avoid breathing the ash. If dust is seen escaping from the machine during a cleaning
procedure, immediately stop the DPF Cleaner and check all connections.
•Wear nitrile gloves that meet OSHA standards. If there is skin contact with the ash, thoroughly
wash the skin with soap and water.
•
Wear ear protection that meets OSHA standards. The noise made during the burst process is within
the acceptable decibel rating for unprotected ears; however, ear protection is recommended.
•Never attempt to clean a DPF that is too hot to touch.
•A DPF must be securely clamped in place before a cleaning cycle is initiated.
•Unplug the DPF Cleaner before beginning any service work. Incorrect use or connections can
cause electrical shock.
•An extension cord may overheat, resulting in a fire. If you must use an extension cord, use the
shortest possible cord with a minimum size of 14 AWG.
•Use the DPF Cleaner only for the purpose of which it was designed. Use only those adapters
approved by the manufacturer.
Explanation of Safety Signal Words
WARNING: Indicates a potentially hazardous situation which, if not avoided, could result in death
or serious injury.
CAUTION: Indicates a potentially hazardous situation which, if not avoided, may result in minor
or moderate injury.
CAUTION: Used without the safety alert symbol indicates a potentially hazardous situation which, if not
avoided, may result in property damage.

5
536119 Rev. C August 10, 2009
1. There are brakes on the two wheels located on the end of the Diesel Particulate Filter (DPF)
Cleaner. Lock the brakes by stepping on the ON side of the paddle. This helps steady the cleaner
during the cleaning process. See Figure 1.
Figure 1
2. Plug the power cord from the DPF Cleaner
into a 110V, 15 AMP outlet. If an extension
cord is necessary, use the shortest possible
cord with a minimum size of 14 AWG.
3. Connect shop air (120 psi minimum) to the
filter / dryer air fitting located on the end of
the machine. Note: An air line pressure of
120–150 psi is recommended to provide an
optimum tank fill rate.
4. Pull out the ON / OFF button on the control
panel. The display briefly shows the version
of software in the unit.
5. The unit then verifies an air supply has been
connected, and the display message asks
the user to verify the air filter / dryer does
not need maintenance. Note: If the service
indicator on the coalescing filter is red, or if
the color indicator beads in the desiccant are
pink, refer to the Maintenance section of this
manual for replacement instructions.
Initial Setup
Arrow Keys:
Scroll through
menu items.
Digital Display:
Visual interface
between operator
and machine.
Go/Yes Button:
Begin or resume
a function, or
answer a query.
Stop/No
Button:
Terminate
or pause a
function, or
answer a
query.
Number Keys:
Make selections
or enter data.
Keypad Functions
Green LED:
Unit is
functioning
normally.
Red LED:
Process needs
attention.
Control Panel
Diesel Particulate Filter
Cleaning System
OEM-DPF
Brakes
Filter / Dryer
Air Fitting
On / Off Button
Circuit
Breakers

6
Main Menu Choice No. 1: Vacuum
The operator may use the vacuum in an auxiliary mode for cleaning purposes. Use this menu choice to
turn the vacuum ON / OFF.
Main Menu Choice No. 2: Setup
The Setup Menu is displayed on three screens. Press the DOWN arrow to move between the screens.
Press a number key to make a selection.
Printer: Set up a serial printer (Samsung SRP-270A or SRP-270AG) to print out test results each time
a cleaning cycle is completed.
Note:
•Configure the printer DIP switches as follows: Switch 1—all OFF; Switch 2—1 & 8 ON.
•Use a serial extension cable having DB-25 connections (external-to-external).
Set Language: Select a language for the display prompts.
Set Units: Choose to have test results displayed in English or Metric units of measure.
Set Date / Time: If YES was selected for the Setup Menu option “Printer”, use this option to enter
today’s date and time into the unit’s software. The current date and time will appear on a printout each
time a cleaning cycle is completed. Note: The software does not automatically adjust for Daylight
Saving Time (DST).
Edit System Text: If YES was selected for the Setup Menu option “Printer”, use the Printer Header
option to enter text that will appear on a printout each time a cleaning cycle is completed (8 lines max.;
20 characters per line). Note: In order to save the text that has been entered, “Save Entry?” must be
answered with YES before moving to the next line.
Set Contrast: Press the UP or DOWN arrow to adjust the brightness of the text against the background
of the display screen.
Main Menu: Return to the Main Menu.
Beeper: Press the RIGHT or LEFT arrow to turn the display screen beeper ON / Off.
6. The Main Menu is displayed on two screens. Press the DOWN arrow to move between the screens.
Press a number key to make a selection.
Main Menu MORE ↓
1. Vacuum
2. Setup
3. Clean
Main Menu MORE ↓
4. Version
Initial Setup

7
536119 Rev. C August 10, 2009
I. Remove the diesel particulate filter (DPF) from the vehicle according to the appropriate OE technical
manual or bulletin regarding DPFs.
CAUTION: To prevent equipment damage, inspect the DPF to verify it is not plugged with coolant,
oil, fuel, or any other substance which might obstruct the cleaning process.
Loading the DPF
Figure 2
Lower Adapter
DPF
Cleaner
Table
2. Refer to Application Chart No. 554506
and determine the appropriate cone and
adapters for the application.
CAUTION: Some DPF designs contain
open ports. To prevent personal injury from
ash escaping during the burst cycle, use
plastic or steel plugs to close all open ports
on the DPF.
3. Verify the DPF Cleaner table is clean. Place
the lower adapter on the table with the
piloting edge of the adapter in the hole in the
table. The adapter flange should rest on the
o-ring in the table. See Figure 2.
4. Attach the adapter cone to the quick connect
coupler, positioning the cone so the pressure
port is facing the pressure transducer hose.
Connect the pressure transducer hose to the
pressure port on the cone. See Figure 3.
Figure 3
Pressure
Transducer
Hose
Upper Adapter
Quick
Disconnect
Coupler

8
Loading the DPF
Figure 4
CORRECT
DPF correctly positioned on lower adapter.
INCORRECT
Gap between DPF & lower adapter.
DPF is tipped
FLOW
5.
Place the DPF on the lower adapter with the arrow on the side of the DPF pointing UP (indicating the
direction of the exhaust flow). The DPF must be flat on the lower adapter with no visible gaps between
the DPF and the adapter. See Figure 4.
6. If an upper adapter is necessary for your
application, place the upper adapter on the
DPF with the rubber seal facing the DPF.
See Figure 5. The upper adapter must be flat
on the DPF with no visible gaps between the
adapter and the DPF.
Figure 5

9
536119 Rev. C August 10, 2009
Loading the DPF
CAUTION: Always ground the DPF canister to prevent static electricity that could cause
personal injury or damage to the unit’s microprocessor.
Figure 6
Ground wire clamped to
edge of canister.
Ground wire clamped to
magnet on canister.
Magnet
7. Attach the magnet (provided) to the side of the DPF. Clamp the alligator clip of the DPF cleaner’s
ground wire to the magnet. Note: If the DPF canister has a protruding edge that can securely hold
the alligator clip, or if the DPF is not magnetic, it is permissible to ground the unit by clamping the
alligator clip to a protruding edge instead. See Figure 6.
8. Close and latch the doors to the pressure
chamber. The DPF Cleaner will not operate
until the doors are secure. See Figure 7.
Diesel Particulate Filter
Cleaning System
OEM-DPF
Figure 7
Secure the doors to the
pressure chamber.

10
9. Verify the cartridge filter covers are securely
clamped. The handles point DOWN when
the covers are correctly closed and locked
into place. See Figure 8.
Figure 8
Handles in
locked position.
Loading the DPF

11
536119 Rev. C August 10, 2009
1. Once a DPF has been loaded into the DPF Cleaner according to the instructions in the Loading the
DPF section of this manual, select CLEAN from the Main Menu.
2. Default cleaning parameters by manufacturer are displayed on multiple screens. Use the DOWN
arrow to move between the screens. Note: Parameters may include burst cycle time, burst pressure,
clamp force, and number of cycles.
The Cleaning Cycle
3. Once a cleaning protocol has been chosen, follow the prompts on the display screen.
4. The vacuum cleaner will run for five seconds to check the condition of the vacuum filter. If the
display message indicates the vacuum filter needs to be replaced, refer to the section of this manual
titled Maintenance – Vacuum Filter.
CAUTION: To prevent personal injury, wear a dust mask (rated N95) to avoid
breathing the ash. If dust is seen escaping from the machine during a cleaning
procedure, immediately stop the DPF Cleaner and check all connections.
Press the STOP / NO button at any time to
halt the cleaning process.
Figure 9
Test clean:
Increase Clamp Force
Air Tank XX of XX
Clamp XXXX of XXXX
5. The display asks the user to adjust the
clamp force on the DPF. Operate the hand
pump to raise the table and DPF to the
cone. See Figure 9. Watch the display,
and stop pumping when the clamp force
value is equal to, or greater than, the
clamp force parameter. The cone must fit
uniformly on top of the upper adapter.
Note: If the hand pump is over-pressurized,
a fault occurs. The red LED illuminates
and the display reads REDUCE CLAMP
FORCE. Release pressure by slowly
turning the control knob on the pump.
6.
The unit builds pressure in the air tank and
sounds out four “beeps” to alert the user
that there will be a low pressure burst of air
to verify the DPF is capable of withstanding
the cleaning process.
7. The unit then builds pressure in the
air tank to equal the burst pressure
parameter. (This may be watched on the
display.) The unit sounds four “beeps” and
completes another burst of air – this time
at full burst pressure.
8. The cycle repeats according to the
specified number of cycles parameter.
Main Menu MORE ↓
1. Vacuum
2. Setup
3. Clean
Follow on-screen instructions. Select OEM parameters.
∆ ∆

12
The Cleaning Cycle
Automatic Reverse Cleaning Process
After a number of DPFs have been cleaned, the back pressure in the ash collection tank will increase to
a level that triggers an automatic reverse cleaning process for the internal cartridge filters. This consists
of small air bursts passing backward through the cartridge filters to remove ash from the filter media
and prolong cartridge life.
The display message spells out REVERSE CLEANING while this process takes place.
After the reverse cleaning is complete, the normal DPF cleaning process resumes.
Note: The first time the reverse cleaning process occurs, it is a signal for the user to purchase
replacement cartridge filters. At some point, the reverse cleaning process will no longer be successful,
and the cartridge filters will need to be replaced.
When this occurs, the display message will be INTERNAL FILTERS BAD. At this point, disconnect the
power cord and air line, and replace the cartridge filters as outlined in the section of this manual titled
Maintenance – Cartridge Filters.

13
536119 Rev. C August 10, 2009
Maintenance—Vacuum Filter
Replace the Vacuum Filter
1. Shut off the machine, and remove the power
cord from the outlet.
2. Open the door to the vacuum cleaner
chamber located on the front of the DPF
Cleaner. See Figure 10.
3. Grasp the handle on the vacuum filter pail
and lift the vacuum out of the cabinet. See
Figure 11.
Note: It is possible to extend the life of a
vacuum filter by tapping the bottom of the
pail on the floor—this settles the contents of
the filter and restores suction for a short time.
4.
Disconnect the vacuum cleaner’s power cord
and vacuum hose.
5. Open the three rubber latches holding the
vacuum motor to the filter canister, and lift
the motor off the canister.
Figure 10
Door
Diesel Particulate Filter
Cleaning System
OEM-DPF
Power Cord Vacuum
Hose
Latch
Figure 11

14
6.
Open the latch on the connecting band and
remove it from the old filter. See Figure 12.
Maintenance—Vacuum Filter
7. When you purchased the new vacuum filter,
it was shipped with a filter cover. Remove the
cover from the box and, using a soft hammer,
tap the cover onto the old filter canister. See
Figure 13.
8. Assemble the connecting band to the new
filter canister.
Connecting
Band
Figure 12
Figure 13
Cover
9. Assemble the motor, vacuum hose, and power cord to the new filter. It may be necessary to adjust
the connecting band to reconnect the rubber keepers.
10.
Place the vacuum back into the cabinet, with the vacuum hose connection positioned toward the
front of the unit. Close the door.
11.
Dispose of the sealed filter canister according to local, state, and federal regulations.

15
536119 Rev. C August 10, 2009
Maintain the Air Filter / Dryer
Replace the Coalescing Filter
The coalescing filter removes oil from the
compressed air, preventing the oil from coating
the desiccant and hampering its ability to dry
the air.
The service indicator on the coalescing filter
turns red when the filter element needs to be
replaced. Filter elements cannot be cleaned;
they must be replaced.
1. Shut OFF air flow to the air filter / dryer, and
depressurize the cleaner.
2. Shut off the machine, and remove the power
cord from the outlet.
3. Remove the bowl / guard assembly from the
coalescing filter housing by pushing the bowl
toward the housing body, rotating the bowl
CCW (counterclockwise), and then pulling
the bowl downward. See Figure 14.
4. Use a clean cloth to clean the bowl. Inspect
the bowl for damage, and replace it if
necessary.
5. Grasp the bottom of the used filter element,
and turn it counterclockwise to remove it.
6. Install the new filter element, being careful to
seat the o-ring in the groove. CAUTION: To
prevent damage to the new filter element,
grasp it by the end opposite the threads.
Do not touch the foam cover.
7. Reinstall the bowl on the housing by pushing
it into the housing and turning the bowl to
catch the locking tabs under the retainers.
Maintenance—Air Filter / Dryer
Coalescing
Filter Desiccant
Filter
Service
Indicator
CAUTION: To prevent personal injury
and equipment damage,
•Depressurize the air filter / dryer unit
before removing a filter bowl.
•Do not use the coalescing filter without
the bowl guard installed.
•Confirm each filter bowl is securely
fastened to its housing before turning ON
the air flow to the air filter / dryer.
Figure 14

16
Maintenance—Air Filter / Dryer
Maintain the Air Filter / Dryer contd.
Air dryers are designed to remove water vapor
from a compressed air system.
Replace the Desiccant
The desiccant, visible through the clear
desiccant filter bowl, contains color indicator
beads that change from blue (dry) to pink (wet).
The pink color indicates the desiccant must be
regenerated or replaced.
1. Shut OFF the air flow to the air filter / dryer,
and depressurize the system.
2. Shut off the machine, and remove the power
cord from the outlet.
3. Remove the bowl from the dryer housing by
depressing the locking tab and rotating the
locking ring counterclockwise until the bowl
can be pulled downward. See Figure 15.
4. Discard the used desiccant.
5. Pour new desiccant into the bowl, filling to
within 1/2 inch of the top of the bowl. Do not
allow desiccant to enter the center tube.
6. Reinstall the bowl on the housing, and
secure it in place.
Regenerate the Desiccant
Used (pink) desiccant may be recycled for
longer use by baking it in an oven until the blue
color returns.
1. Preheat an oven to 350° F (176° C).
2. Pour the used, pink desiccant into a flat pan.
3. Bake the pan of desiccant in the oven
for approximately three hours or until the
desiccant color has changed from pink back
to blue.
4. Remove the desiccant from the oven, and
allow it to cool down to ambient temperature.
5. Pour the desiccant back into the bowl,
shaking and tapping on the bowl to settle the
desiccant. Do not allow desiccant to enter
the center tube.
6. Reinstall the bowl on the housing and secure
it in place.
CAUTION: To prevent personal injury
and equipment damage,
•Depressurize the air filter / dryer unit
before removing a filter bowl.
•Do not use the desiccant filter without the
bowl guard installed.
•Confirm each filter bowl is securely
fastened to its housing before turning ON
the air flow to the air filter / dryer.
Figure 15
Locking
Tab
Coalescing
Filter
Desiccant
Filter
Color Indicator
Decal

17
536119 Rev. C August 10, 2009
Maintenance—Cartridge Filters
During operation of the DPF Cleaner, the contaminated airstream is drawn into an ash collector, where
its velocity is reduced by inlet baffle plates to provide even air distribution across the entire surface
area of cartridge filters. This design enhances filtration efficiency by establishing a uniform dust cake
on the filters. The airstream is then directed around the cartridge filters and down toward the bottom of
the collector, where the heavier particles accumulate.
The contaminated air then passes through the cartridge filters. The filter media strips most of the ash
from the airstream, and the air then passes into the clean air plenum and through a HEPA filter before
being discharged from the unit. When back pressure in the ash collector tank exceeds a preset value,
and the reverse cleaning process is no longer effective, a display message will prompt the user to
change the cartridge filters.
Replace the Cartridge Filters
This procedure describes how to replace the
cartridge filters using the Bag-out Kit included
when a new filter is purchased.
1. Shut off the machine, and remove the power
cord from the outlet.
2. Unlock and remove the cover to the upper
cartridge filter.
3. Use the cinch strap provided in the Bag-Out
Kit to securely attach a bag to the collar of
the cartridge chamber. See Figure 16.
4. Pull the used filter out of the dust collector
and into the bag. See Figure 17.
Figure 17
Figure 16

18
Maintenance—Cartridge Filters
Figure 19
Replace the Cartridge Filters contd.
5. Twist the top of the bag and secure it with
the cable tie provided. See Figure 18.
6. Release the cinch strap from the collar.
7. Repeat Steps 1–5 for the lower cartridge
filter. Note: For easier access when attaching
the cinch strap to the lower cartridge filter,
fasten the strap at the side of the filter.
Figure 18
8. Power ON the DPF Cleaner, and select VACUUM from the Main Menu. Use the vacuum hose and
attachments to remove ash from the cartridge door area and from inside the chamber. See Figure 19.
9. Install the new filters in the dust collector with the gasket end inserted first.
10.
Install the filter covers and lock them in place.
11.
Dispose of the used filters according to local, state, and federal laws regarding hazardous waste.

19
536119 Rev. C August 10, 2009
Maintenance—Air Tank, HEPA Filter
Drain the Air Tank
Once per month, drain the air tank on the DPF
Cleaner of water that may have accumulated in
the tank.
1. Depressurize the DPF Cleaner and unplug it
from its power source.
2. Place a shop towel or shallow pan under the
air tank’s drain plug. See Figure 20.
3. Use an open-end wrench to remove the drain
plug, and let the water drain out.
4. Install and tighten the drain plug into the air
tank pipe fitting, and dispose of the water.
Air Tank
Figure 20
Replace the HEPA Filter
1. Remove the nut from each corner of the HEPA
filter. See Figure 21.
2. Lift the two z-shaped brackets off the HEPA filter.
3. Replace the existing filter with a new HEPA filter.
4. Install the z-shaped brackets and nuts.
Figure 21
Z-shaped Brackets
and Nuts
Drain Plug

20
Maintenance—Hydraulic Assembly
Bleeding the Hydraulic System
Air can accumulate in the hydraulic
system, causing the table lift cylinders to
respond slowly or in an unstable manner.
To remove the air:
1. Shut off the machine, and remove the
power cord from the outlet.
2. Open the hand pump release valve
to completely lower the DPF Cleaner
table.
3. Close the pump release valve.
4. Remove the bleed plug from one table
lift cylinder. See Figure 22.
5. Slowly actuate the hand pump handle
until oil starts to flow out the cylinder
bleed hole.
6.
Install the bleed plug again with the
o-ring positioned as shown in
Figure 23. CAUTION: If the o-ring is
not correctly installed on the bleed
plug, the o-ring could be cut, causing
the cylinder to leak.
7. Repeat Steps 3–6 with the second
table lift cylinder.
8. With the cylinders fully retracted, check
the oil level in the pump reservoir by
removing the fill cap located on the
end cap of the pump. The oil should be
within 2–4 inches from the bottom of
the fill hole. See Figure 24. Add high-
grade hydraulic oil, if needed.
OEM-DPF
Bleed Plug
Table Lift
Cylinder
Figure 22
Correct
Incorrect
Figure 23
OEM-DPF
Figure 24
2" to 4"
Oil level should be
2–4 inches from
bottom of fill hole.
CAUTION: If
the o-ring is
not correctly
installed on the
bleed plug, the
o-ring could be
cut, causing the
cylinder to leak.
Table of contents
Other SPX Water Filtration System manuals
Popular Water Filtration System manuals by other brands
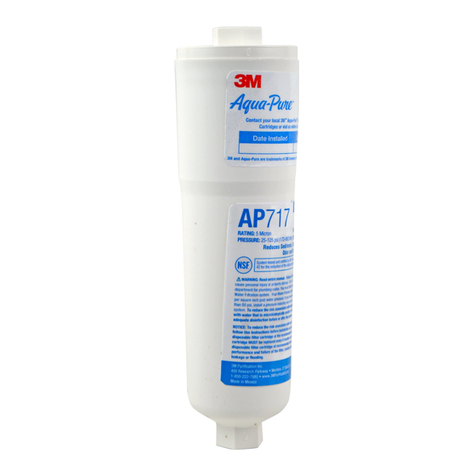
3M
3M Aqua-Pure AP717 Installation and operating instructions
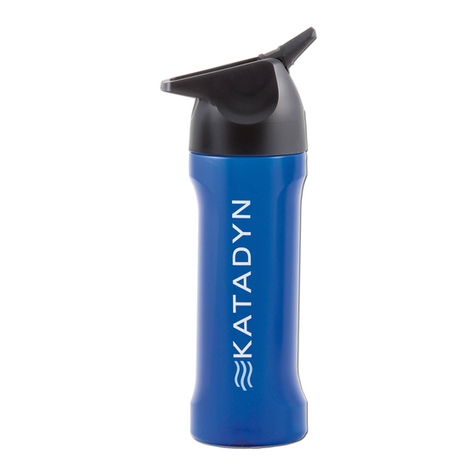
Katadyn
Katadyn MyBottle manual
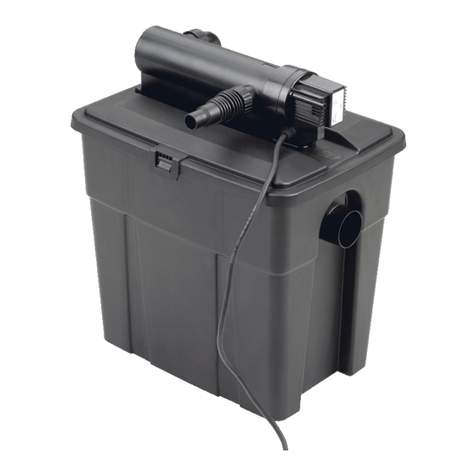
Pontec
Pontec MultiClear 5000 operating instructions

Katadyn
Katadyn MOT-31 manual
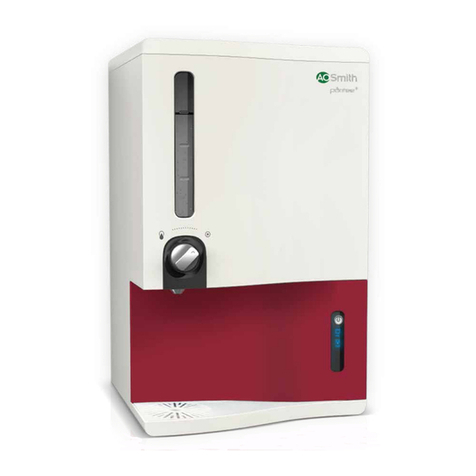
A.O. Smith
A.O. Smith Pure&Sure 329843-000_R0 user guide
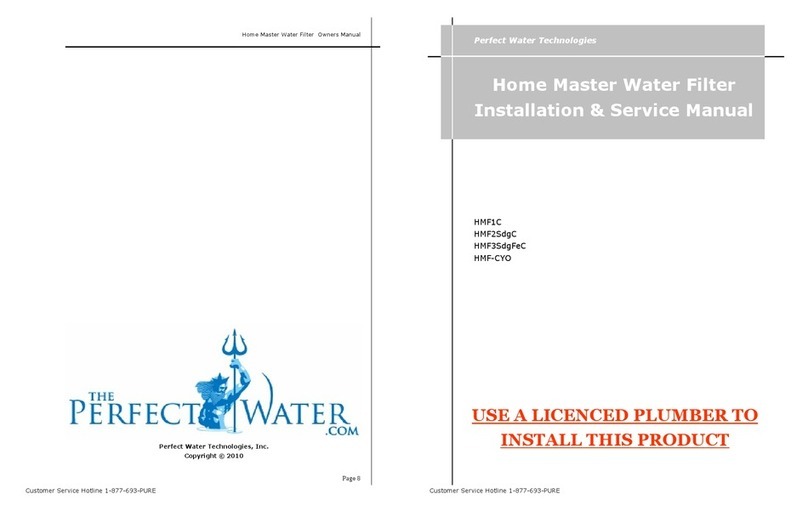
Perfect Water Technologies
Perfect Water Technologies Home Master HMF1C Installation & service manual

Water quality
Water quality ng5 Installation & service manual

Vetus
Vetus 330VTEB Operation manual and installation instructions
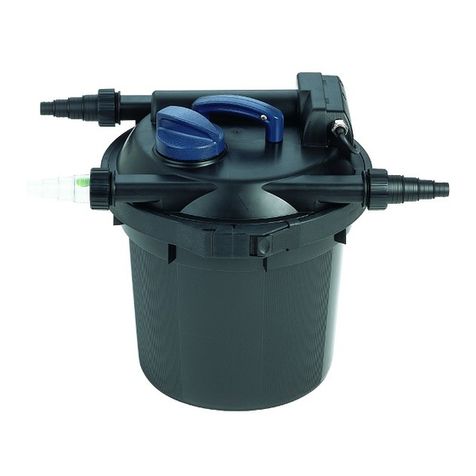
Oase
Oase Filtoclear 3000 Warranty, safety and operating instructions
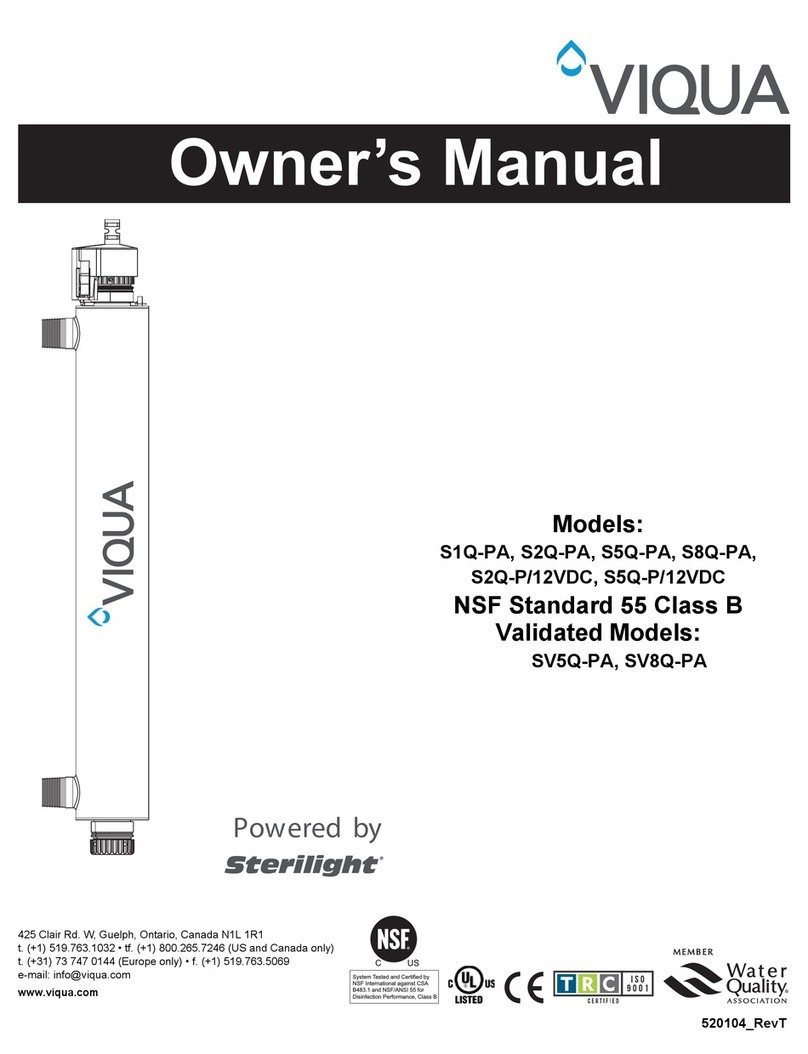
Viqua
Viqua Sterilight S1Q-PA owner's manual
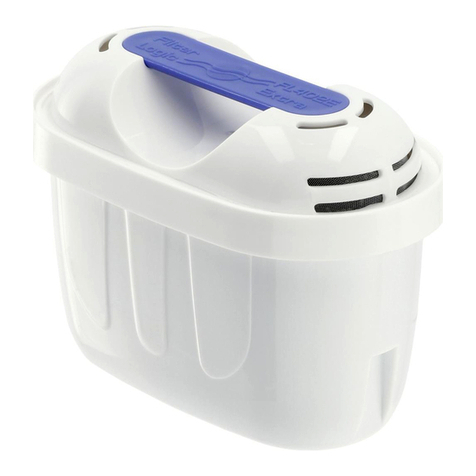
Xavax
Xavax 00111243 operating instructions

Esta
Esta VACUMAT 1000 operating instructions