SRP BRL40 Series Manual

Series BRL40 Page 1 LT234 August 2019
Installation, Operation and Service Instructions
INFRARED BROODER
SERIES
BRL40
WARNING
FOR YOUR SAFETY
Improper installation, adjustment, alteration, service
or maintenance can cause property damage, injury or
death. Read the installation, operating and
maintenance instructions thoroughly before installing
or servicing this equipment.
Do not store or use gasoline or other flammable vapors
and liquids in the vicinity of this or any other appliance.
If you smell gas:
1. Open windows
2. Don’t touch electrical switches
3. Extinguish any open flame
4. Immediately call your gas supplier
OWNER
INSTALLER
Retain this Manual & ensure available for service.
Improper installation, adjustment, alteration, service
or maintenance can cause injury, death or property
damage.
Read the installation, operation and service
instructions thoroughly before installing or servicing
this equipment
Provide Manual to Owner upon completion of
installation!
Read and thoroughly understand these Instructions
before attempting any installation
Canada: 563 Barton Street, Stoney Creek, Ontario L8E 5S1
USA: 315 N Madison Street, Fortville, IN 46040
www.superiorradiant.com

Series BRL40 Page 2 LT234 August 2019
WARNING: FIRE OR EXPLOSION HAZARD
Maintain clearance to combustible constructions as further specified in this manual. Failure to do so
could result in a serious fire hazard. Heaters should not be located in hazardous atmospheres
containing flammable vapors or combustible dusts. Signs should be provided in storage areas
specifying maximum safe stacking height.
CAUTION: FIRE OR EXPLOSION HAZARD
This heater is equipped with an automatic ignition device. Do not attempt to light the burner by hand.
Failure to comply could result in a serious fire and personal injury hazard.
CAUTION: MECHANICAL HAZARD
Do not use high pressure (above 1/2 psi) to test the gas supply system with the burners connected.
Failure to do so could result in damage to the burner and its control components requiring replacement.
CAUTION: SERVICE LIFE RISK
Do not install equipment in atmospheres containing halogenated hydrocarbons or other corrosive
chemicals. Failure to do so may lead to premature equipment failure and invalidation of the warranty.
WARNING –California Proposition 65
This appliance, its related accessories and by-product of operation, contain chemicals known to the
State of California to cause cancer and birth defects or other reproductive harm.
For more information go to www.P65Warnings.ca.gov.

Series BRL40 Page 3 LT234 August 2019
CONTENTS
CONTENTS ............................................................................................................................................................................. 3
INTRODUCTION...................................................................................................................................................................... 4
INSTALLATION CODES ...................................................................................................................................................................... 4
GENERAL SPECIFICATIONS ..................................................................................................................................................... 5
INPUT .......................................................................................................................................................................................... 5
GAS SUPPLY .................................................................................................................................................................................. 5
ELECTRIC SUPPLY............................................................................................................................................................................ 5
VENTILATION ................................................................................................................................................................................. 5
SHIPPING CONFIGURATION ............................................................................................................................................................... 5
HIGH ALTITUDE RATINGS ................................................................................................................................................................. 5
DIMENSIONAL CHARTS .......................................................................................................................................................... 5
BROODER PARTS.................................................................................................................................................................... 6
GENERAL ASSEMBLY ....................................................................................................................................................................... 7
PACKAGE CONTENTS.............................................................................................................................................................. 8
CLEARANCE TO COMBUSTIBLES ............................................................................................................................................. 9
ASSEMBLY............................................................................................................................................................................ 10
INSTALLATION...................................................................................................................................................................... 14
VENTING & COMBUSTION AIR ............................................................................................................................................. 15
GENERAL REQUIREMENTS .............................................................................................................................................................. 15
GAS PIPING .......................................................................................................................................................................... 16
ELECTRICAL CONNECTIONS .................................................................................................................................................. 18
WIRING DIAGRAM ........................................................................................................................................................................ 18
LIGHTING AND SHUTDOWN INSTRUCTIONS......................................................................................................................... 20
STARTING SEQUENCE OF OPERATION ................................................................................................................................................ 20
FUEL CONVERSION KIT ......................................................................................................................................................... 21
MAINTENANCE .................................................................................................................................................................... 23
TROUBLESHOOTING ............................................................................................................................................................. 24
REPLACEMENT PARTS .......................................................................................................................................................... 25
WARRANTY .......................................................................................................................................................................... 26

Series BRL40 Page 4 LT234 August 2019
INTRODUCTION
Superior Radiant Products is a company in the infrared heating industry founded on the principles of product quality
and customer commitment.
Quality commitments are evidenced by superior design, a regard for design detail and an upgrade of materials
wherever justifiable.
Customer commitment is apparent through our ready responses to market demands and a never ending training
and service support program for and through our distributor network.
The series BRL is an infrared brooder for agricultural installations.
IMPORTANT
The manufacturer’s instructions, the layout drawing, national and local codes and ordinances, and all applicable
standards which apply to gas piping and electrical wiring comprise the basic information needed to complete the
installation. These criteria must be thoroughly understood before proceeding.
Only personnel who have been trained and understand all applicable codes should undertake the installation.
Manufacturer representatives are Factory Certified in the service and application of this equipment and can be
called on for helpful suggestions about installation.
Installation Codes
Installations must comply with local building codes, or in their absence, the latest edition of the national regulations
and procedures as listed below.
This heater complies with IAS U.S. No. 8-94 (Draft No. 2) and CAN-1-2-20-M85.
General Installation and Gas Codes
Heaters must be installed only for use with the type of gas appearing on the rating plate, and the installation must
conform to the National Fuel Gas Code, ANSI Z223.1/NFPA 54 in the US and CSA B149.1 Installation Code in
Canada.
Not for use in residential dwellings, refer to Rating plate.
Gas Supply Lines
Gas supply pipe sizing must be in accordance with the National Fuel Gas Code, ANSI Z223.1/NFPA 54 in the US
and CSA B149.1 Installation Code in Canada.
A 1/8" NPT plugged tap must be installed in the gas line connection immediately upstream of the burner farthest
from the gas supply meter to allow checking of system gas pressure.
Electrical
All heaters must be electrically grounded in accordance with the National Electric Code, ANSI/NFPA 70 in the US,
and the Canadian Electric Code, CSA C22.1 in Canada, and must comply with all local requirements.

Series BRL40 Page 5 LT234 August 2019
GENERAL SPECIFICATIONS
Input
40,000 BTU/hr
Gas Supply
Inlet Pressure
Natural Gas:
Minimum
Maximum
5.0”W.C.
14.0”W.C.
Propane Gas:
Minimum
Maximum
11.0” W.C.
14.0”W.C.
Manifold Pressure
Natural Gas:
4” W.C.
Propane Gas:
10”W.C.
Inlet Connection
Natural Gas or Propane: 3/8” female NPT
Electric Supply
24 VAC, 60 HZ, 0.8 Amp
Ventilation
For indoor installation only and unvented. Minimum ventilation required is 160 CFM per brooder.
Shipping configuration
This heater ships from the factory for use with LP gas. To convert from propane to natural gas, refer to
Gas Conversion Instructions within this manual.
High Altitude Ratings
40,000 BTU/hr. For Canada 0-4500 feet above sea level. In the U.S. 0-2000 feet above sea level, anything
over 2000 feet is derated by 4% per thousand feet above sea level as per National Fuel Gas Code.
DIMENSIONAL CHARTS
Figure 1: Overall Dimensional Information

Series BRL40 Page 6 LT234 August 2019
BROODER PARTS
Get to know your heater parts (list referencing Figure 2).
Figure 2: General Overview

Series BRL40 Page 7 LT234 August 2019
General Assembly
Refer to Figure 2 for component identification.
No.
Qty
PN
Description
No.
Qty
PN
Description
1
5
CH118
Screw S/S #8-32x3/8” Pan Phillips
15
1
BS014
Brooder Main Hanging Bracket
2
1
CH095
Washer, Flat 3/16 x 3/4”
16
1
BE008
Control Box Assembly
3
1
BS001
Dust Pan
17
1
BS012
Control Box Mounting Bracket
4
1
BG005
Brass Adapter
18
1
BS011
Heat Shield
5
1
UG029
Orifice #49 LPG
19
1
BS010
Manifold Mounting Bracket
6
1
BG010
Brooder Burner
20
1
BG003
WR Gas Valve 25M18-716
7
1
BS006
Brooder Cone Assembly
21
1
BE004
Ignition Cable 35”
8
7
CH190
Keps Nut #10-24
22
2
BG006
Brass Tube Fitting, 3/8 NPT to 3/8
Pressure Fitting Female
9
3
CH051
Hex Head Bolt S/S 1/4”-20
23
1
BG007
Gas Tube, 3/8 S/S
10
3
BS009
Cone Hanging Bracket
24
1
BS005
Electrode Bracket
11
1
BS013
Reflector
25
1
BE003
Electrode PSE-GF26
12
8
CH143
Washer, 1/4” flat S/S
26
3
BS004
Spacer Screw #10-24
13
8
CH260
Keps Nut S/S 1/4”-20
27
1
BS003
Burner Top Plate
14
1
CH261
304 S/S Eyebolt 1/4”-20 x 1”
NO.
QTY
PN
DESCRIPTION
1
1
BE006
Controls Enclosure
2
1
BE002
Ignition module
3
3
Weld Bolt #10-24 x 1", S/S
4
2
CH130
Screw, 8-32 x 3/4" Pan Phillips
5
1
Lid
6
4
Lid Screw
7
1
CH262
Liquid Tight Fitting PG11
8
1
BE007
ON/OFF switch
9
1
BE009
Terminal Block
10
1
BS016
Module Mounting Plate
11
1
CH190
Keps Nut #10-24
*12
2
CE280
WAGO 3 Conductor Lever Nut
*Not shown in diagram; only used in conjunction with gas valve 25M18-716B1
Figure 3: Control Box (BE008) Components

Series BRL40 Page 8 LT234 August 2019
PACKAGE CONTENTS
The radiant brooder is sold in packages of six or one, depending on the customer’s quantity order. Verify that you
have received all heater components included with the unit. The unit is packaged as sub-assemblies in kits, listed
below. To purchase replacement parts, refer to page 23.
BS013 - Reflector
BK006 Emitter Cone Assembly
BS001 - Dust Pan
BK001- Hanger Kit
BK002 - Heat Shield Kit
BG010 - Burner
BE008 - Control Box Kit
BK004 - Electrode Assembly Kit
BK003 - Manifold Assembly
BK014 - Natural Gas Conversion Kit
Figure 4

Series BRL40 Page 9 LT234 August 2019
CLEARANCE TO COMBUSTIBLES
Minimum clearances to combustible materials shall be measured from outer surface of the reflector.
In addition to this it is very important to observe the minimum clearance to combustibles at all times to
avoid any possibility of property damage or personal injury.
Combustible materials are considered to be wood, compressed paper, plant fibres, plastics, Plexiglas or other
materials capable of being ignited and burned. Such materials shall be considered combustible even though flame-
proofed, fire-retardant treated or plastered.
The stated clearance to combustibles represents a surface temperature of 90°F (50°C) above room temperature.
Building materials with low heat tolerance (i.e. plastics, vinyl siding, canvas, tri-ply, etc.) may be subject to
degradation at lower temperatures.
It is the installer’s responsibility to ensure that adjacent materials are protected from deterioration.
A
B
C
64’’ (1625mm)
36’’ (915mm)
15’’ (380mm)
Table1: Minimum clearance to combustible materials
Figure 5: Clearance to Combustible

Series BRL40 Page 10 LT234 August 2019
ASSEMBLY
1. Before assembling, check that all components are included in the package.
2. Fasten the burner assembly to the cone assembly using three (3) #10-24 hex locknuts, and attach the
igniter bracket to the burner assembly using a #10-24 hex locknut, as shown in Fig. 6.
Figure 6
3. Fasten the short end of the hanging bracket (with eyebolt) to the centre hole of the reflector, using a ¼”-20
S/S bolt and appropriate washer and locknut. Align the other end of the hanging bracket with the alignment
holes on the reflector. Attach the cone assembly to the reflector, aligning the igniter bracket with the
alignment holes, using ¼”-20 hex nuts and ¼ flat washers.
Figure 7

Series BRL40 Page 11 LT234 August 2019
4. Attach the heat shield and control box mounting bracket to the reflector at the alignment holes, using two
(2) ¼-20 S/S bolts, nuts and washers.
5. Attach the gas manifold assembly by securing the T-clamp over the tube, covering up to the gas fitting.
Insert the orifice block into the bottom of the burner and use the swivel clamp to hold it in place.
Figure 8
6. Attach the igniter to its bracket with two (2) #8-32 Phillips pan head screws.
Figure 9
7. Attach the dust pan to the orifice block with a #8-32 pan head screw and flat washer.

Series BRL40 Page 12 LT234 August 2019
Figure 10
8. Mount the control box onto the bracket, securing it with two (2) #10-24 locknuts.
Figure 11
9. Attach the wiring as shown in the wiring diagram (see ELECTRICAL CONNECTIONS section below), Plug
the ignition cable into the igniter, then secure the boot over the igniter. After attaching the ignition cable to
the igniter, secure the cable to the gas tube with zip ties.

Series BRL40 Page 13 LT234 August 2019
For gas valve BG003
For gas valve BG003 (alternate wiring)
10. The blue wires coming from the control box
connect to the gas valve, follow the diagram below
for proper connections. V1 from the module
connects to 1 and 3 on the valve, and V2 connects
to 2 and 4.
10. The gas valve has two (2) blue leads and two (2) red
leads. Feed the leads through the liquid tight cable gland.
Inside the box are two (2) WAGO lever nuts, one (1)
connected to a blue wire and one (1) connected to a red
wire. Connect the valve leads to the lever nuts of the
appropriate color by inserting the wire into the fitting then
closing the lever to secure the wire. The blue wires should
connect to GV1 and the red wires should connect to GV2.
See ELECTRICAL CONNECTIONS section below.
Figure 12a –Gas valve wiring
Figure 12b&c –Connect valve leads to WAGO lever
nut with matching color wire
11. The 24VAC and neutral wires connect to the terminal block. See the wiring diagram for proper routing.
12. Close the lid on the control box and tighten the screws with a Phillips or flathead screwdriver.
13. Check the assembly to make sure there are no loose parts before proceeding with the installation.
BLUE
BLUE
RED
RED
V2
V1
4
3
2
1

Series BRL40 Page 14 LT234 August 2019
INSTALLATION
WARNING
NEVER USE THE GAS HOSE AS A SAFETY CHAIN
1. Hang the brooder at the appropriate height above the floor (litter) level, approximately 65”-75” (1650mm-
1900mm). When using a winch, use a cable or chain suitable for the weight of each brooder. DO NOT USE
ROPE.
2. Connect a safety chain from every brooder to a rigid structure.
3. Connect the gas line and electrical supply to each brooder.
4. Position the brooder so that the control side is approximately 1/2” (13mm) lower from the other side to
prevent damaging.
Figure 13: Hanging Diagram
Safety chain connected to
rigid ceiling structure
(allow 6” of slack)
This side (with control box
and manifold) should be
1/2” (13mm) lower than the
opposing side
Move the eyebolt along the
hanging bracket to level
the heater
Chain or cable attached
to winch system
capable of supporting
weight of system

Series BRL40 Page 15 LT234 August 2019
VENTING & COMBUSTION AIR
General Requirements
ATTENTION
VENTILATION REQUIREMENTS
BE SURE THE AIR INLET GRILLS, LOUVERS AND DAMPERS ARE INSPECTED REGULARLY AND
THAT THEY ARE CLEAR AND FREE OF DUST, DIRT, SNOW, ICE, FROST AND OTHER FOREIGN
MATERIAL SO THAT AIR MAY FREELY ENTER INTO THE BUILDING TO PROVIDE ADEQUATE
COMBUSTION AND VENTILATING AIR.
FOR PROPER AND SAFE OPERATION OF THE BROODER INSTALLATION, THERE SHALL BE
PROVIDED A COMBINED INFILTRATION AND NATURAL AND MECHANICAL VENTILATION RATE OF
NOT LESS THAN ¼ S.C.F.M. (standard cubic foot per minute) PER BIRD.
Refer to the National Fuel Gas Code, ANSI Z223.1 (NFPA 54) in the US and CSA B149.1 Installation Code
in Canada, as well as all local requirements for general venting guidance.
The Nation Fuel Gas Code requires a minimum of 4 CFM per 1000 Btu/hr of brooder input for ventilation.
This requirement means that a total of 160 CFM is required per brooder.
FOR YOUR SAFETY
Exhaust fans must be operating on an appropriate cycle when heating the building to avoid high
concentration of carbon monoxide and water vapor.
WARNING
Carbon Monoxide is an odorless and poisonous gas. Extended exposure to carbon monoxide may lead to
death. Early signs of carbon monoxide poisoning resemble the flu, including headaches, dizziness and/or
nausea. If you experience these signs, GET FRESH AIR IMMEDIATELY. Have the brooders serviced as
soon as possible and check the ventilation in the house.

Series BRL40 Page 16 LT234 August 2019
GAS PIPING
The gas meter and service must be sufficiently large to supply gas to the connected building gas load
including the heating equipment and any other gas fired equipment. Additionally, the gas distribution piping
must be designed according to local and national ordinances. Generally (low pressure) systems designed
with a maximum ½" W.C. total pressure drop meet this requirement.
Gas supply pipe sizing must be in accordance with the National Fuel Gas Code, ANSI Z223.1 (NFPA 54) in
the US and CSA B149.1 Installation Code in Canada.
Before connecting brooders to the gas supply system, verify that high pressure testing of the system has
been completed. Failure to do so may expose the brooder components to damaging high pressure, requiring
replacement of key components.
Pipe joint compounds must be resistant to the action of liquefied petroleum (LP) gases
Flexible gas connectors of approved type must be installed as shown in Figure 13, in one plane, and without
sharp bends, kinks or twists. Failure to install the gas connection in the approved manner will result in a
hazardous and potentially deadly situation due to the movement of the heater in the normal course of operation
Figure 14: Flexible Gas Connections
The following components not included, may be ordered separately.
NO.
QTY
PART NUMBER
DESCRIPTION
1
1
CG011
VALVE, MANUAL BALL ½”
2
1
BG002
MALE FTG 45FLARE 3/8TUBEx1/2NPT
3
1
HOSE, 3/8IDx6FT with 3/8”F SWIVEL FITTINGS
4
1
MALE FTG 45FLARE 3/8TUBEx3/8NPT

Series BRL40 Page 17 LT234 August 2019
WARNING
FIRE HAZARD
Tighten flexible gas hose and components
securely.
Flexible gas hoses must be installed without
any twists or kinks in them. DO NOT allow
the hose to touch any part of the brooder
canopy during operation
Failure to do so may result in death, serious
injury or property damage
Install a manual shut-off valve in the gas piping to each brooder. This will allow service of individual brooders
without having to shut down the entire gas supply system.
A sediment trap must be installed in the supply line in the lowest spot prior to connecting to the heater. The trap
length should be at least three (3) inches long. Periodically remove the cap from the trap and drain any
accumulation of dirt and/or water.
Figure 15: Sediment Trap
After all gas connections and adjustments are made, check all gas connections for leaks using a heavy
soapsuds solution.
WARNING
DO NOT USE AN OPEN FLAME OF ANY SORT TO TEST FOR LEAKS!

Series BRL40 Page 18 LT234 August 2019
ELECTRICAL CONNECTIONS
Wiring diagram
All fields wiring to the brooder must be done in accordance with the National Electric Code, ANSI/NFPA 70 in the
USA, and the Canadian Electric Code, CSA C22.1 in Canada, and must comply with all local requirements.
The brooder must be electrically grounded.
Figure 16a –Wiring diagram for gas valve BG003
Figure 16b –Gas valve BG003, which has male quick-disconnect terminals

Series BRL40 Page 19 LT234 August 2019
Figure 17a: Wiring Diagram for gas valve BG003 (alternate wiring)
Figure 17b&c: WAGO lever connectors are used with gas valve BG003, which has its own leads
BLUE
BLUE
RED
RED

Series BRL40 Page 20 LT234 August 2019
The brooder is designed to operate on an external 24VAC electrical system.
Provide only 24VAC with a Class 2 transformer, field supplied, to the control wires.
The transformer size depends on the number of brooders controlled in the same time.
Transformer Size = No. of Brooders x 20VA
NO. OF BROODERS
MINIMUM TRANSFORMER VA
6
120
12
240
18
360
24
480
LIGHTING AND SHUTDOWN INSTRUCTIONS
Starting sequence of operation
Turn on the gas and electrical supply
Set the thermostat to call for heat.
Ignition should occur immediately
If the burner fails to light, or flame is not detected during the first trial for ignition (a period of approximately 10
seconds) the gas valve is de-energized and the control goes through an inter-purge delay of approximately
15 seconds before another ignition attempt. The control will attempt two additional ignition trials before going
into lockout.
If the heater does not light, shut off the gas completely for 5 minutes before attempting to relight.
If the thermostat is still calling for heat after one hour, the control will automatically reset and attempt to ignite
the burner again.
NOTE: The heater must be grounded. Poor grounding will give nuisance lockouts, particularly during momentary
power interruptions.
To shut down the heater, turn off the gas and electrical supply.
Table of contents
Other SRP Heater manuals
Popular Heater manuals by other brands
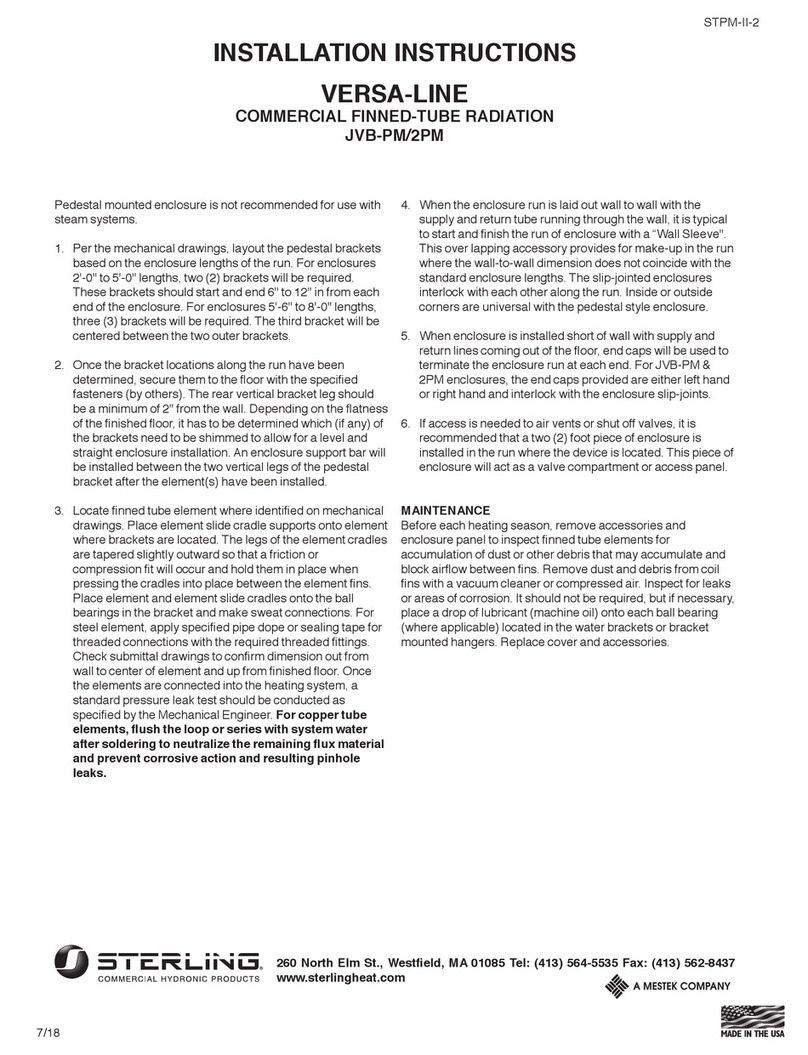
Sterling
Sterling VERSA-LINE installation instructions

Fluxer Heaters
Fluxer Heaters Flite 3S quick start guide
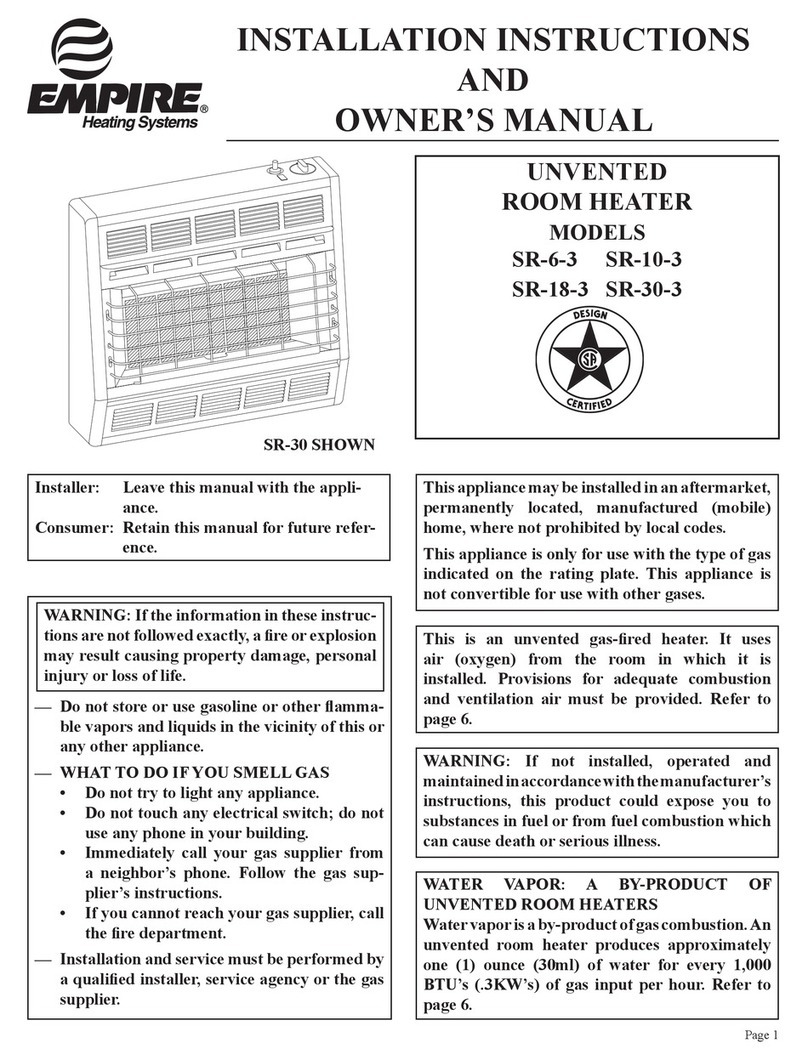
Empire Heating Systems
Empire Heating Systems SR-6-3 Installation instructions and owner's manual
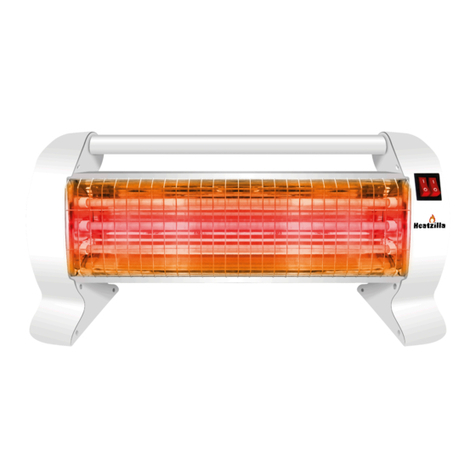
Heatzilla
Heatzilla SY-CLQ10 user manual
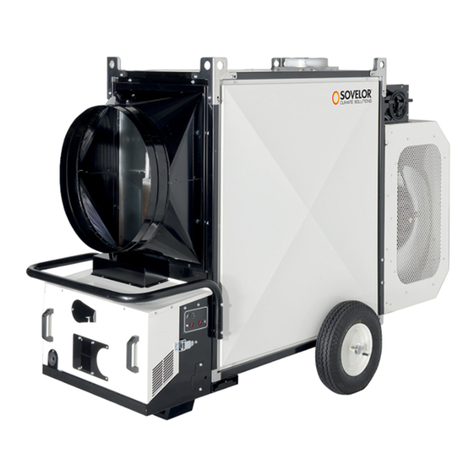
Sovelor
Sovelor TITAN 155 instruction manual
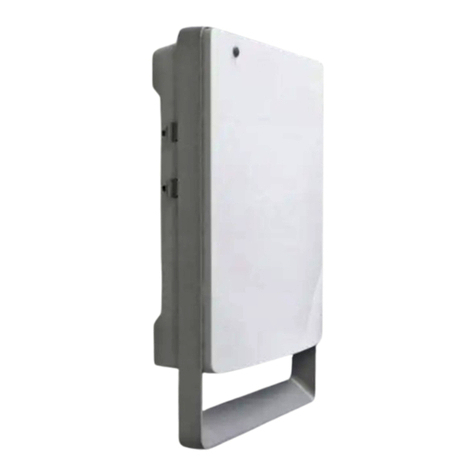
Aurora
Aurora FOLIO instructions
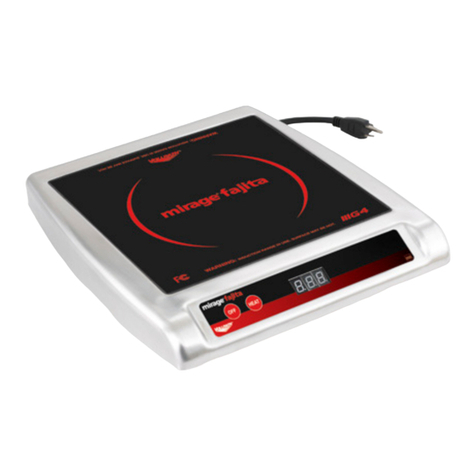
Vollrath
Vollrath mirage fajita 59500F Operator's manual

KORADO
KORADO KORALUX LINEAR CLASSIC-E operating instructions
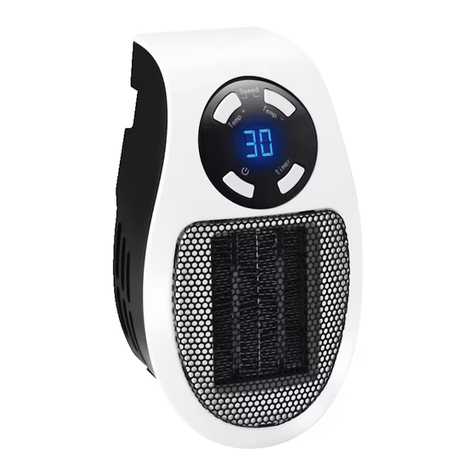
MILL
MILL HT500 Assembly and instruction manual
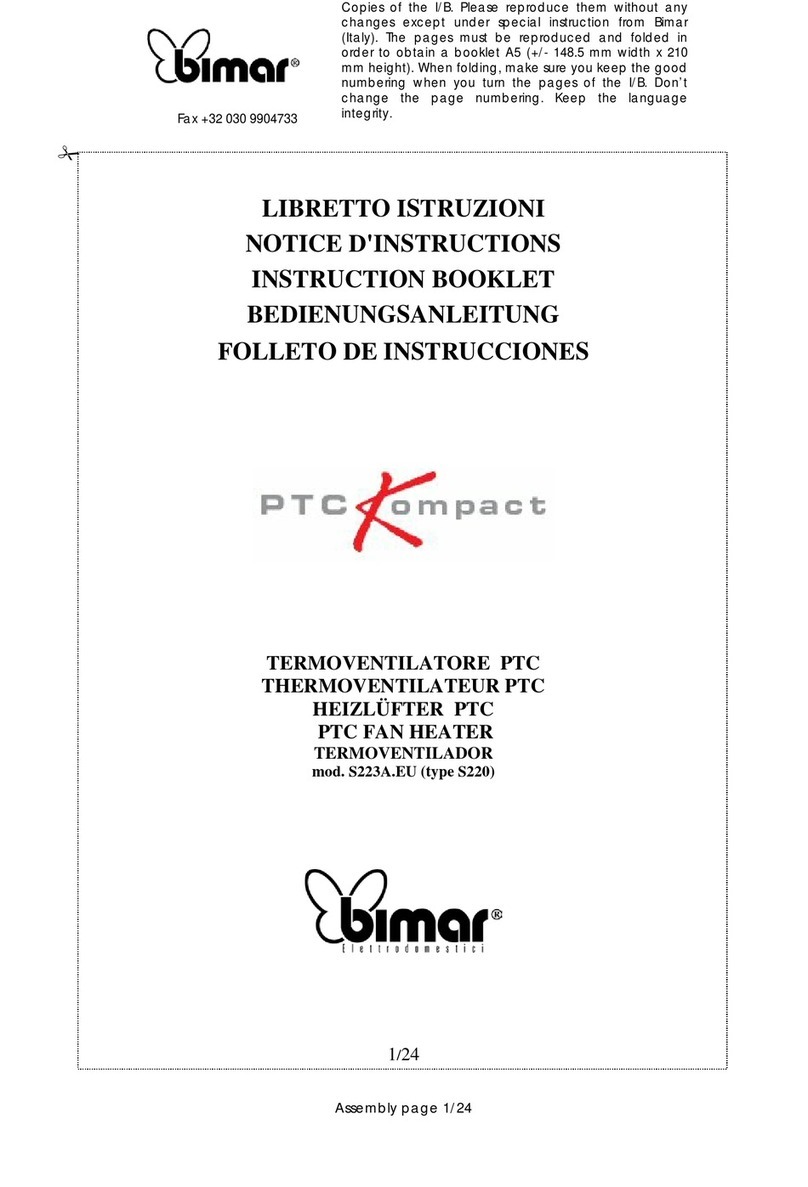
Bimar
Bimar PTC Kompact S223A.EU Instruction booklet

Jaga
Jaga MINI FREESTANDING HYBRID Installation and operation manual
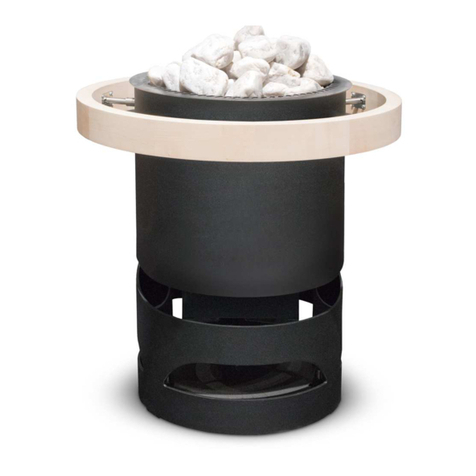
EOS
EOS Zeus S Installation and operating instructions