STARKE ARVID MB-06 Operating instructions

Starke Arvid AB
Lyckåsvägen 3 Tel: +46 522 - 22 000 Fax: +46 522 - 22 344
SE-459 30 Ljungskile www.starkearvid.se [email protected]
1
USER AND MAINTENANCE MANUAL
LIFTING FORK
This user and maintenance manual was drafted according to the Standard ISO 12100-2:2009.
It complies with the Machinery Directive 2006/42/EC.
It complies with requirements in Standard EN 13155:2009 type C.
Reference standards:
EN ISO 12100-1 Machinery safety –Fundamental concepts, main design concepts - Part 1: basic terminology, methodology
EN 10204:2005 Metal products –Type of control documents –Also applicable to non-metal products
ISO 8686-1 Cranes - Design principles for loads and load combinations - General
•ISO International standard
•EN European standard
•CEN European standardisation committee
•ISO International standardisation organisation
In compliance with common CEN/CENELEC regulations, the national standardisation bodies of the following countries must comply
with the European standards:
Austria, Belgium, Bulgaria, Croatia, Cyprus, Czech Republic, Denmark, Estonia, Finland, France, Germany, Greece, Hungary,
Iceland, Ireland, Italy, Latvia, Lithuania, Luxembourg, Malta, Netherlands, Norway, Poland, Portugal, Romania, Slovakia, Slovenia,
Spain, Sweden, Switzerland and the United Kingdom.

Starke Arvid AB
Lyckåsvägen 3 Tel: +46 522 - 22 000 Fax: +46 522 - 22 344
SE-459 30 Ljungskile www.starkearvid.se [email protected]
2
Lifting fork to move loads to heights
Introduction
In compliance with accident prevention standards, the company has drafted this instructions booklet to inform users on
the most correct use of lifting forks.
We therefore recommend that before using the equipment, you read and comply with all the instructions.
For further load situations not covered in this booklet, comply with common accident prevention standards.
1. USE AND CONSERVATION OF USER AND MAINTENANCE MANUAL
•The user and maintenance manual is for those responsible for installation and maintenance and all user operators
during functioning of the equipment, especially the parts relevant to safety in the workplace.
•The information contained in the manual is used to indicate the correct use of the equipment, according to the design
and manufacturing purposes planned.
•Information is also provided on movement, installation, maintenance and servicing, all in compliance with the
limitations set by the manufacturer in the manual.
•The user and maintenance manual is an integral part of the equipment and should be conserved until its disposal.
The manual should be conserved in a protected place, near the equipment, and easily available for consultation.
•If the manual is damaged or lost, the user must request a copy from the manufacturer.
•The manufacturer reserves the right to make changes to the equipment and the manuals, without updating previous
editions.
•The user can request information and updates which, when issued, becomes an integral part of the user manual.
•In case of terminating the equipment, it must be terminated with this manual, as specified in the Directive 2006/42/EC.
1.1. Cases where manufacturer declines responsibility
The manufacturer declines all responsibility due to:
•Incorrect use of equipment or its use by staff untrained for professional use;
•Use non-compliant with specific standard;
•Incorrect installation;
•Serious lack of planned maintenance and servicing;
•Changes, intervention or handling of any type performed by unauthorised staff.
The manufacturing company declines all responsibility when the lifting forks are not used in complete compliance with
safety standards.
INDEX
1. USE AND CONSERVATION OF USER AND
MAINTENANCE MANUAL
1.1.Cases where manufacturer declines responsibility
5. INSTRUCTIONS
5.1.For staff
5.2.For transport and warehousing
5.3. For use
2. DESCRIPTION OF FORK
2.1. Technical features
2.2. Dimensions
6. MAINTENANCE
6.1.Ordinary maintenance
6.2.Replacing spring
6.3.Replacement of the restraint
6.4.Conservation
3. USE CONDITIONS
7. USE LIMITATIONS
4. GENERAL SAFETY SPECIFICATIONS
8. GUARANTEE

Starke Arvid AB
Lyckåsvägen 3 Tel: +46 522 - 22 000 Fax: +46 522 - 22 344
SE-459 30 Ljungskile www.starkearvid.se [email protected]
3
2. DESCRIPTION OF FORK
Lifting fork: equipment composed of two or more fixed arms on a support with an upper arm, essentially to lift loads on
pallets and similar.(point 3.8 EN 13155:2009)
They are used to move any type of pallet and are suitable to lift unit loads (load on pallet wrapped in plastic) to heights
and fastened to the fork using a hold device (for example a chain, belt or bar).
They are composed of the following models:
Mod. version MB, MBA
Mod. version MBCR, MBACR
Mod. version MBR, MBR-A
Mod. version MBR-M, MBRA-E
Mod. version MBL-A, MBL-R
Mod. version ITA, ITA-4D, MBR-4D
Examples of lifting fork
2.1. Technical features
The auto-balancing lifting forks mod. MB and MBA, are essentially composed of two mobile points. On request, you can
have a central point, which is non-influential on the capacity and is fixed to a mobile sleeve with a through screw. The
sleeve moves vertically upwards and downwards and controls opening and closing of the side points using a specific
device which guarantees its perfect alignment in any opening position.
The auto-balancing lifting forks mod. MBRA-E, ITA and ITA-4D are composed of two or four points (mod.ITA-4D) that
are adjustable by sliding on a tube (mod. MBRA-E) and on a plate (mod. ITA and ITA-4D). Mod. MBRA-E is also height
adjustable at regular intervals.
Lifting forks mod. MBCR and MBACR (not auto-balancing) have the same system to regulate opening of the points on
models MB and MBA. Fork balance is obtained by positioning the link on the correct “unload-load” position.
Lifting forks mod. MBR, MBR-M, MBR-4D (not auto-balancing) are composed of two or four side points (mod. MBR-4D)
that are adjustable by sliding on a tubular crosspiece on the base. These models are also height adjustable at regular
intervals, not mod.MBR-4D.
Lifting forks mod. MBL-A and MBL-R are composed of two, fixed side points. They have different balancing, automatic
in mod. MBL-A and manual in mod. MBL-R.
Other models are built based on specific requests and can be auto-balanced or not and with regulation of the points by
sliding on tubes or plates.
2.2. Dimensions

Starke Arvid AB
Lyckåsvägen 3 Tel: +46 522 - 22 000 Fax: +46 522 - 22 344
SE-459 30 Ljungskile www.starkearvid.se [email protected]
4
MOD. MB
COD. ART
PORTATA
kg
A
B
C*
DIMENSIONI mm
D** E F
G
L
M
PESO
Kg
MB-06
600
1400
340
1100
1000
2140
1080
1000
25
80
85
MB-10
1000
1400
340
1100
1000
2140
1080
1000
25
90
110
MB-15
1500
1400
340
1100
1000
2140
1080
1000
30
90
120
MB-20
2000
1400
340
1100
1000
2140
1080
1000
35
100
136
MOD. MBA
COD. ART
PORTATA
Kg
A
B
C*
DIMENSIONI mm
D** E F
G
L
M
PESO
kg
MBA-06
600
1600
340
1300
1000
2360
1080
1000
25
80
95
MBA-10
1000
1600
340
1300
1000
2360
1080
1000
25
90
120
MBA-15
1500
1600
340
1300
1000
2360
1080
1000
30
90
130
MBA-20
2000
1600
340
1300
1000
2360
1080
1000
35
100
150
MBA-25
2500
1600
380
1300
1000
2360
1080
1000
35
120
170
MBA-30
3000
1600
380
1300
1000
2360
1080
1000
35
120
175
MOD. MBCR
COD. ART
PORTATA
DIMENSIONI mm
PESO
kg
A
B
C*
D** E F
G
L
M
kg
MBCR-10
1000
1400
340
1100
1000
1600
1080
1000
25
90
110
MBCR-15
1500
1400
340
1100
1000
1600
1080
1000
30
90
120
MBCR-20
2000
1400
340
1100
1000
1600
1080
1000
35
100
136
MOD. MBACR
COD. ART
PORTATA
DIMENSIONI mm
PESO
kg
A
B
C*
D** E F
G
L
M
kg
MBACR-10
1000
1600
340
1300
1100
1800
1080
1000
25
90
120
MBACR-15
1500
1600
340
1300
1100
1800
1080
1000
30
90
130
MBACR-20
2000
1600
340
1300
1100
1800
1080
1000
35
100
146
* altezza utile di carico in apertura ottimale delle punte ** altezza utile di carico alla massima apertura delle punte
MOD. MBR
COD. ART
PORTATA
kg
A
B
C
DIMENSIONI mm
D E F
G
L
M
PESO
kg
MBR-10
1000
1000
1250
300
1000
1450
450
1000
25
90
104
MBR-15
1500
1000
1250
300
1000
1600
450
1000
30
90
140
MBR-20
2000
1000
1250
300
1200
1800
450
1000
35
100
152
MBR-25
2500
1000
1400
300
1200
1800
450
1000
35
120
175
MBR-30
MBR-4D
3000
2000
1000
1000
1400
1800
300
1300
1200
1800
1800
30
450
90
1000
35
120
185
214
MOD. MBRA
COD. ART
PORTATA
kg
A
B
C
DIMENSIONI mm
D E F
G
L
M
PESO
kg
MBRA-10
1000
1000
1250
300
1000
1450
700
1000
25
90
131
MBRA-15
1500
1000
1250
300
1000
1600
700
1000
30
90
140
MBRA-20
2000
1000
1250
300
1200
1800
700
1000
35
100
174
MBRA-25
2500
1000
1400
300
1200
1800
700
1000
35
120
241
MBRA-30
3000
1000
1400
300
1200
1800
700
1000
35
120
250
MOD. MBR-M
COD. ART
PORTATA
kg
A
B
C
DIMENSIONI mm
D E F
G
L
M
PESO
kg
MBR-15M
1500
950
1000
400
1100
1640
1000
30
90
155
MBR-20M
2000
950
1000
400
1100
1640
1000
35
100
170
MBR-25M
2500
1000
1400
400
1100
1640
1000
35
120
175
MBR-30M
3000
1000
1400
400
1100
1640
1000
35
120
185
MOD. MBRA-E
COD. ART
PORTATA
kg
A
B
C
DIMENSIONI mm
D E F
G
L
M
PESO
kg
MBRA-15E
1500
950
1000
400
1100
1640
1000
30
90
140
MBRA-20E
2000
950
1000
400
1100
1640
1000
35
100
155
MOD. ITA
COD. ART
PORTATA
kg
A
B
C
DIMENSIONI mm
D E F
G
L
M
PESO
kg
ITA-10
1000
1000
850
1270
2250
25
90
135
ITA-15
1500
1000
1200
1270
2250
30
90
165
ITA-20
ITA-4D
2000
2000
1000
1000
1200
1800
1270
1300
2250
2250
35
30
100
90
180
230
MOD. MBL
COD. ART
PORTATA
kg
A
B
C
DIMENSIONI mm
D x (MBL-A) D x (MBL-R)
E
F
M
PESO
kg
MBL-10
1000
1000
600
1100
1900
1600
25
90
75
MBL-15
1500
1000
700
1750
2550
2350
30
90
120
MBL-20
2000
1000
735
1750
2550
2350
35
100
138
MBL-25
2500
1000
755
1750
2550
2350
35
120
172

Starke Arvid AB
Lyckåsvägen 3 Tel: +46 522 - 22 000 Fax: +46 522 - 22 344
SE-459 30 Ljungskile www.starkearvid.se [email protected]
5
3. USE CONDITIONS
It is necessary to conduct a visual control and general daily control before starting any type of work.
Do not use the fork before having clearly understood the indications in this manual.
Check the material to move meets the following requirements:
•Variable dimensions within the field of opening and length of the points.
•The weight of the goods must fall within the capacity indicated on the plate applied to the fork.
•The maximum height must fall within the measurements indicated in the tables above.
•The depth of the pallet or similar must not exceed 100 cm (unless forks are designed and manufactured on requested
specifications).
•The maximum length of the pallet or similar must not exceed 20% of the external opening of the two points. Example
of fork regulated to 100 cm external point, maximum width allowed for pack 120 cm.
•The material placed on the pallet or similar must guarantee even distribution of the load above the fork points.
•when using a fork lift in a worksite, make sure the protection net is in position.
Operating method:
Unit loads
The lifting forks were designed and manufactured to move and lift any unit material placed on a pallet or similar to
heights, according to the requirements indicated in points 3.8 and 5.2.5 EN 13155:2009;
The pallets used to move materials to heights (re-usable customised wooden pallets) must meet the requirements
indicated in the definitions of Standard EN ISO 445:2009;
The re-usable customised wooden pallets must be marked;
The loads on the pallets to be moved to a height must be identified as a unit load (point 5.2.5.5 EN 13155:2009);
The unit load on the pallet must be wrapped in plastic (thermo-retractable film) and supported with crossed supports.
The support materials must meet UNI reference standards. The load must be certified by the manufacturer.
Before forking the load, the operator verifies the unit load is not damaged;
Having forked the load secure it with the lifting fork, using the hold device (band or chain), to avoid it sliding during the
lifting phase.
Proceed to lifting. The authorised employees must conduct the various movements according to the information and
training received, and/or in relation to their experience matured over their working lives.
Non-unit loads
The lifting forks were designed and manufactured to move and lift any unit material placed on a pallet or similar to
heights, according to the requirements indicated in points 3.8 and 5.2.5 EN 13155:2009;
A non-unit load is loose material placed on a pallet or material on a pallet without plastic wrapping and/or crossed
supports or plastic or deteriorated supports. A non-unit load is also material wrapped in plastic and supported, placed
on a disposable pallet (Standard EN ISO 445:2009);
To lift non-unit loads, systems must be exclusively used that prevent all and/or part of the load falling. In this case the
lifting fork, compliant with Standard EN 13155:2009, should be used combined with the secondary positive hold device
or rather a metal bin manufactured by us or the load protective net provided by us.
Proceed to lifting. The authorised employees must conduct the various movements according to the information and
training received, and/or in relation to their experience matured over their working lives.
To use secondary positive hold devices, consult the relevant user and maintenance manuals.
It is strictly forbidden to use the lifting fork to lift loose materials to heights or using methods other than those
indicated.

Starke Arvid AB
Lyckåsvägen 3 Tel: +46 522 - 22 000 Fax: +46 522 - 22 344
SE-459 30 Ljungskile www.starkearvid.se [email protected]
6
4. GENERAL SAFETY SPECIFICATIONS
➢Operators must use IPDs (Individual Protection Devices) made available to them and in compliance with the
information and training they have received.
➢Individual contracting companies will proceed to inform, train and qualifytheir employees (crane operators and those
loading and unloading) on the correct actions to take when lifting and moving loads to heights. It being understood
that employees such as crane operators must be trained.
➢It is necessary to choose equipment compatible with own machinery. The total mass of the suspended load should
fall within the nominal capacity of the lifting equipment during normal use conditions.
➢The combination of the lifting equipment with the load hold moving equipment must only be activated by staff trained
for this use and under safe conditions.
➢Lifting and support must occur under controlled conditions and under the management of a specifically designated
person.
➢The operations involved in using the lifting equipment with the load hold moving equipment should be suspended in
the event of winds exceeding the maximum speed planned (which would no longer enable the complete control of
the machine) and storms, ice, snow, fog or other adverse weather conditions which could compromise staff safety.
➢Where multiple machines are used simultaneously in the same location, communication among crane operators
must occur via transceivers, with the crane operator always having one in his hand and the operator on the ground
responsible for the harnesses having the other.
➢Measures must be taken to ensure employees do not stay under the suspended loads.
➢It is not permitted to pass loads over unprotected workplaces, usually occupied by employees.
➢It is strictly forbidden to use the equipment before having blocked access to
the work area for people and/or animals. For this reason, it is necessary to
fence off the area and implement all measures considered appropriate to make
the work safer.
➢Signs must be clearly visible that indicate forbidden access to the work area to
unauthorised employees and the danger of suspended loads.
➢Transit is strictly forbidden in the working radius of the equipment.
➢Danger of falling materials.
➢Danger of crushing.
➢Danger of knocks.
➢Transit is strictly forbidden with the load outside the enabled work area.
➢The load hold moving equipment (lifting forks and gravity activated pliers) are suitable for lifting and movement of
unit loads placed on pallets or similar (see point 5.2.5 and point 5.2.7 EN 13155:2009).
➢Any intervention on the equipment should take place on the ground and in a stable position.
➢Safety of the equipment is linked to the efficiency of the safety systems on the machine on which they are assembled.
➢The machine must have an acoustic alarm device to warn people the machine and equipment are operating.
5. INSTRUCTIONS
5.1 For staff
•Lifting operations to move loads to heights must be performed by staff specialising in and trained for this
activity. Never allow use by production staff or temporary staff in general.
•It is forbidden to abandon the workplace with load hold moving equipment operating.
5.2. For transport and warehousing
•Adequate means must be used for lifting and transport based on weight and dimensions. To lift, connect
to the ring placed over the fork using the crane hook or chain firmly connected to it. Warehousing of the
fork must be carefully conducted, ensuring its stability.

Starke Arvid AB
Lyckåsvägen 3 Tel: +46 522 - 22 000 Fax: +46 522 - 22 344
SE-459 30 Ljungskile www.starkearvid.se [email protected]
7
5.3. For use
•Use equipment exclusively for lifting and moving materials with features as described in point 3.
•Ensure the material to move has a weight that falls within the capacity indicated on the identification plate of the fork
and, obviously, that the material and the equipment fall within the capacity of the crane.
•Important. To correctly use the fork, it is indispensable to place a welded mesh chain between the crane hook and
the fork ring. The chain must have an upper end with a ring and the lower part with an entry closure hook. Ensure
the chain is suitable for the weight of the load supported, with multiple materials forked (Standards EN 814-4).
•During operations using the fork, it must be grasped using your hands only using the specific handles.
To regulate point width, proceed as follows:
Mod. MB, MBA, MBCR, MBACR
-With fork on the ground and without load, laterally push the neck until point slightly lifts, with the weight weighing on
the other point;
-Use your heel to move the point slightly lifted outwards to the desired width;
-To block the points, release the fork and screw the hand wheel situated on the upper part up to contrast;
-To close, gradually unscrew the hand wheel and push the neck to the side. The points will slowly close until the fork
is released.
Mod. MBR MBR-A MBR-M MBRA-E ITA
-With fork without load and lifted, loosen the wing screws placed over the sleeves on the base;
-Regulate the width of the points and block them by screwing the wing screws in.
The MBR, MBR-A, MBR-M and MBRA-E models are also height adjustable; proceed as follows:
-Connect the equipment to the crane as described in point 5.2 and rest it on the ground with no load;
-Remove the through plug. The upper tube is free to slide on the lower one;
-Lift the upper part of the fork with the crane to the desired height, corresponding to the perforations;
-Block the fork by re-inserting the through plug and the safety stop.
Positioning the ring on the different neck points (MBR –MBCR - MBACR):
1) Fork slightly tilted forward to insert and remove pallet points more easily;
2) Balanced fork with full load.
•The external points must be opened as much as possible based on the dimensions of the material moved and in any
case they must always remain inside the pallet cross-pieces.
•To correctly lift materials remember that the centre of gravity of the pack lifted must coincide with that of the lifting
fork.
Non-compliance with this condition can cause:
-The load to tip;
-Overloading of the two teeth or worse, only one of the two.
•The capacity indicated on the marking relates to the load uniformly distributed on both points.
•Avoid moving the load using the end parts of the points.

Starke Arvid AB
Lyckåsvägen 3 Tel: +46 522 - 22 000 Fax: +46 522 - 22 344
SE-459 30 Ljungskile www.starkearvid.se [email protected]
8
•Having forked the load, before starting to lift it, secure it with a chain or belt, suitable for this purpose,
to the specific hooks placed on the side supports of the fork. The ends of the chains or belts must
be equipped with an anti-unhooking device and the length must ensure the right tension during the
transport operational phase.
Safety precautions to conduct with anchoring system using belt
-Before use always visually inspect anchorage.
-Never use if damaged (for example cuts on belt and/or deformations on metal
parts).
-Comply with the tensioning value planned for anchorage.
-Use edge guards on sharp edges.
-Avoid exposure to heat sources over 100°C.
-Do not knot or twist the belt.
•When moving and lifting materials, avoid abrupt acceleration and jolts. Increase speed progressively and use the
buzzer alarm on the crane to signal the start of the movement operations.
•Avoid using the equipment to strap or pull any object, since the equipment was designed to support loads in a vertical
position. This manoeuvre may be dangerous.
•When the work phase is complete, ensure the fork points are free of any types of material.
Non-compliance with the aforementioned instructions may create dangerous situations and/or damage the
equipment, making it unsafe.
6. MAINTENANCE AND REPLACEMENT OF COMPONENTS SUBJECTED TO NORMAL WEAR
•A control must be conducted by previously assigned, trained and qualified staff on the use of the load hold moving
equipment (forks and pliers), it being understood that employees must be trained to work on the crane.
•The control on the information, training and qualifications provided must be backed up by a report on the training
provided, kept by the contractor.
•Any maintenance or service operations must be conducted with the equipment resting on the ground in a stable
position.
We recommend that checks of the efficiency and good maintenance of the materials constituting these accessories are
carried out at least on a quarterly basis.
Remember also that on the basis of the above, if reductions greater than 10% are detected in the section of the
constituent elements of the accessories, the accessory must be replaced. This replacement must be carried out also
when, as a result of stress, the material exceeds its elastic capacity with a permanent effect.
6.1. Ordinary maintenance
The fork lift must be compulsorily inspected:
•whenever it is removed from the warehouse and every day before start up in the worksite;
•after a repair;
•during the service life of the equipment.
Control of the equipment is necessary to ensure the efficiency of the equipment and consists of:
•Checking there are no cracks in the welding;
•Checking the range conditions of the pivots and in particular point alignment;
•Checking for breakages and/or deformations on the metal structure;
•Checking the conditions of the screws and correct tightening of the nuts;
•Checking the status of the spring, where present, in particular any cracks that can occur with onerous use;
•Periodically greasing the regulation locking wheel on the models versions MB and MBA and versions MBCR and
MBACR;
•Replacing the worn parts with original replacement parts provided by the manufacturing company.
In the case any anomalies are detected contact the manufacturer for the servicing of the device. Operations
conducted incorrectly make the equipment dangerous. All repair and servicing of the forks must be performed by
qualified personnel at our facilities. The use of aftermarket parts may compromise the safety of the device, as well
as invalidate the CE compliance of the equipment.

Starke Arvid AB
Lyckåsvägen 3 Tel: +46 522 - 22 000 Fax: +46 522 - 22 344
SE-459 30 Ljungskile www.starkearvid.se [email protected]
9
6.2. Replacing the spring (where present)
The lifting fork springs are very stressed parts and are subject to normal wear during use. The springs with defects (for
example cracks) or stress due to heavy loads, also following onerous or careless use, must be replaced.
The spring must be replaced in the following circumstances:
•When cracked.
•When stressed.
•In any case, after 2 years from the purchase date due to natural deterioration of the spring.
The replaced spring must be disposed of as special waste.
6.3 Replacement of the restraint (belt with ratchet)
The restraint (belt or chain), must be replaced in the following cases:
•wear and tear due to normal use of the device;
•damage (cuts on the strap and/or deformation of the metal parts) resulting from improper use and/or as a result of
severe stress even after containment of the load (for having fulfilled its purpose);
•after 2 years from date of purchase in any event, due to natural deterioration of the belt.
The device replaced must be disposed of as special waste
6.4. Conservation
The equipment must rest on the ground in a stable position during storage and in a dry place far from dangerous
substances which could affect the components (for example acid, alkaline solutions and solvents).
7. USE LIMITATIONS
The equipment was designed and dimensioned for use equal to 20,000 lifting cycles. Once this limit is reached it must
be serviced in our workshop and if necessary replaced.
Wear of the lifting fork is subject to various situations (such as conservation and care during use), therefore the lifting
cycles also depend on the aforementioned circumstances.
8. GUARANTEE
The company guarantees its device for a maximum period of 12 months from the delivery date for material and
construction defects.
On receiving the goods, check:
•The data reported on the transport document (addressee, type of goods, number of packages);
•That the goods received are undamaged.
IN CASE OF ANOMALIES, IMMEDIATELY NOTIFY THE CARRIER, WITH WRITTEN RESERVATION ON THE TRANSPORT
DOCUMENT AND ADVISE THE COMPANY WITHIN 8 DAYS OF RECEIPT OF THE GOODS.
If manufacturing defects are found, the purchaser is obliged to communicate such defects within 8 days from the date
of receipt to the company which will undertake to resolve the anomaly as quickly as possible without any additional
costs.
The guarantee excludes parts that were damaged due to carelessness or negligence during use, inadequate
maintenance, improper use or normal wear, defects due to tampering, damage caused due to transport, non-compliance
with the information contained in this manual and any other circumstances which cannot be attributed to manufacturing
defects.
The lifting fork whether repaired under guarantee or not must be accompanied by the photocopy of the invoice and the
user and maintenance manual.

Starke Arvid AB
Lyckåsvägen 3 Tel: +46 522 - 22 000 Fax: +46 522 - 22 344
SE-459 30 Ljungskile www.starkearvid.se [email protected]
10
MAINTENANCE AND REPAIRS
Note
Date
Operation
Outcome
Signature

Starke Arvid AB
Lyckåsvägen 3 Tel: +46 522 - 22 000 Fax: +46 522 - 22 344
SE-459 30 Ljungskile www.starkearvid.se [email protected]
11
MAINTENANCE AND REPAIRS
Note
Date
Operation
Outcome
Signature

Starke Arvid AB
Lyckåsvägen 3 Tel: +46 522 - 22 000 Fax: +46 522 - 22 344
SE-459 30 Ljungskile www.starkearvid.se [email protected]
12
Manufactured by:
BOSCARO S.r.l. –36020 Campiglia dei Berici (Vicenza –Italy), Via G. Cederle 1
Tel. +39 (0) 444/866520 - Fax +39 (0) 444/866350
e-mail: info@boscaroitalia.it –www.boscaroitalia.it
The images and any documents delivered with this manual are the property of BOSCARO S.R.L. and all rights are reserved.
Any reproductions, even partial, of the text and illustrations are strictly forbidden.
All the documentation is protected pursuant to law. BOSCARO S.R.L. reserves the right to exercise protection rights.
This manual suits for next models
40
Table of contents
Other STARKE ARVID Lifting System manuals
Popular Lifting System manuals by other brands
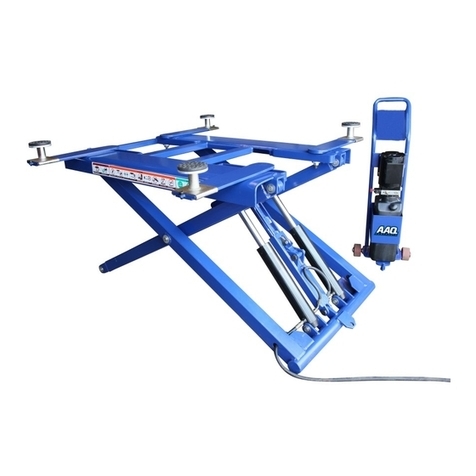
AAQ
AAQ AL-3060 Installation manual & operation instructions

WERTHER INTERNATIONAL
WERTHER INTERNATIONAL 280AZ manual
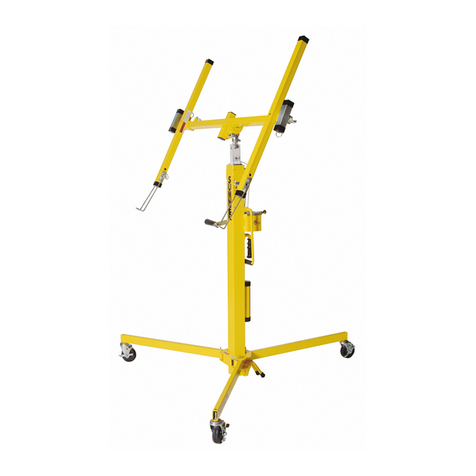
Sumner
Sumner 2311 Series Replacement instructions

Dhollandia
Dhollandia DH-L Series installation manual
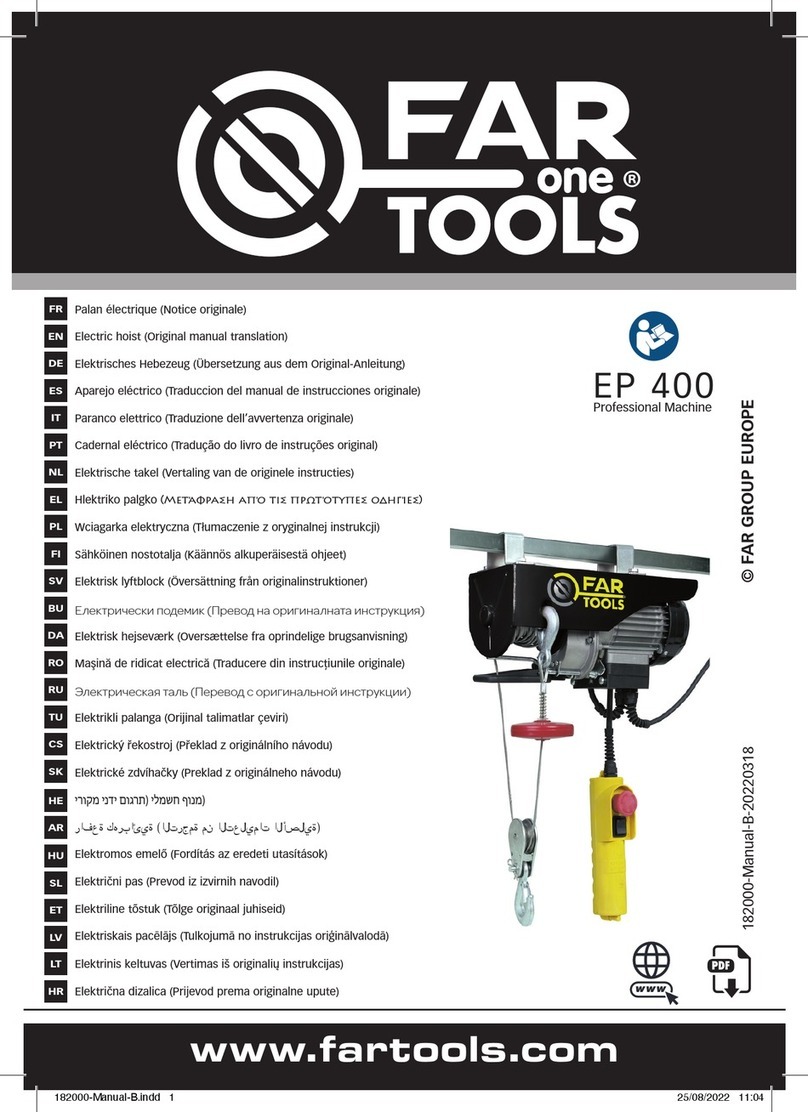
Sigma
Sigma Far Tools One EP 400 Original manual translation
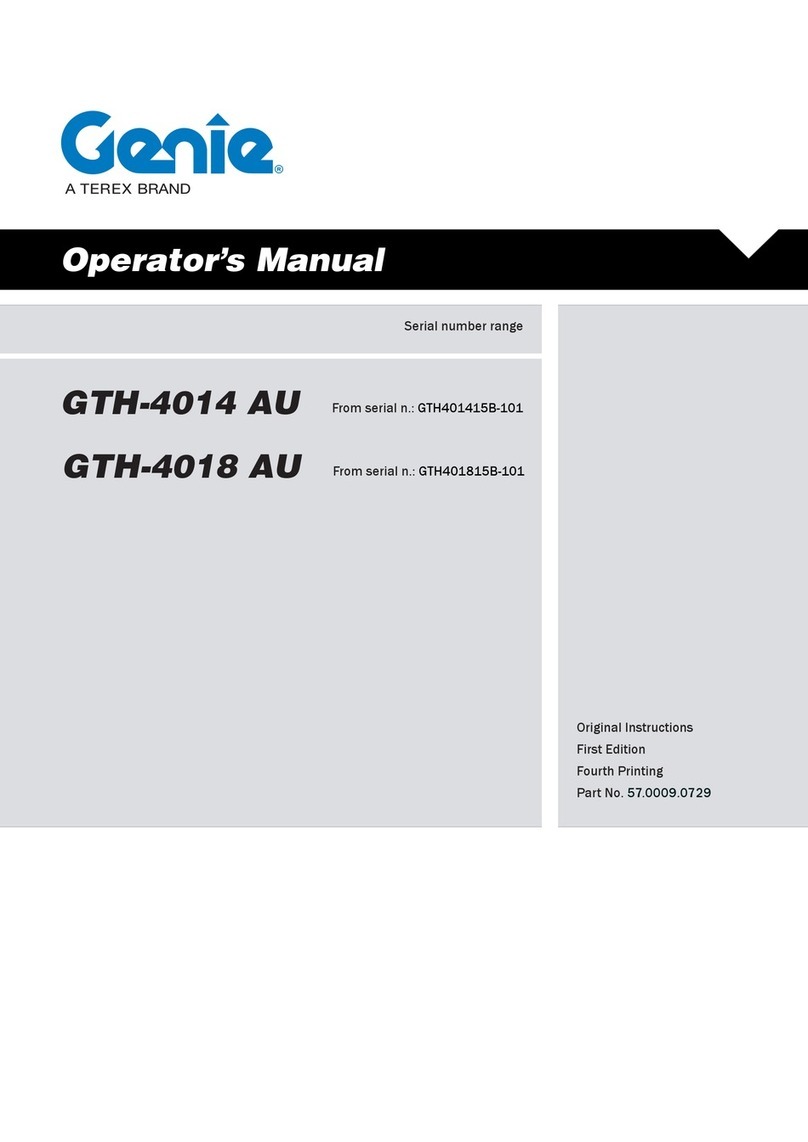
Terex
Terex Genie GTH-4014 AU Operator's manual