Status Pro mLine F1 User manual

µLine F1
P
RECISION
–
L
ASER
-
I
NTERFEROMETER
M
ANUAL
http://www.statuspro.com

www.Statuspro.com
Status Pro Maschinenmesstechnik GmbH,
Mausegatt 19, D-44866 Bochum, Germany
: +49(0)23 27/98 81-0,
: +49(0)23 27/98 81-81
:
http://www.statuspro.com
Laser Interferometer µLine F1
User manual
Bochum 2011

C
ONTENTS
www.Statuspro.com
INTRODUCTION .................................................................................................................1-1
S
AFETY CONSIDERATIONS
....................................................................................................1-1
W
ARNINGS
...........................................................................................................................1-2
PRINCIPLES OF OPERATION .........................................................................................2-1
T
HE RULES OF LASER DISPLACEMENT MEASUREMENTS
........................................................2-1
T
HE CONSTRUCTION OF REAL INTERFEROMETERS
.................................................................2-2
T
HE INFLUENCE OF THE OUTSIDE CONDITIONS ON THE MEASUREMENT ACCURACY
..............2-5
T
HE ACCURACY OF LASER INTERFEROMETERS
......................................................................2-6
Errors caused by the environment...................................................................................2-6
A dead path error ............................................................................................................2-7
A cosine error..................................................................................................................2-8
An Abbe error................................................................................................................2-10
A laser stability error ....................................................................................................2-10
Other errors...................................................................................................................2-11
A summary of laser measurement system errors...........................................................2-11
PREPARATIONS .................................................................................................................3-2
S
OFTWARE INSTALLATION
....................................................................................................3-2
T
HE
L
ASER
I
NTERFEROMETER SYSTEM ELEMENTS
...............................................................3-3
P
REPARING THE INTERFEROMETER TO WORK
........................................................................3-6
S
WITCHING THE SYSTEM ON
.................................................................................................3-7
G
ETTING BASIC INFORMATION FROM THE SYSTEM
................................................................3-9
BEAM ALIGNMENT...........................................................................................................4-1
B
EAM ALIGNMENT PROCESS
.................................................................................................4-4
LINEAR MEASUREMENTS ..............................................................................................5-1
M
EASUREMENT SET
..............................................................................................................5-1
L
INEAR DISPLACEMENT MEASUREMENT
...............................................................................5-3

C
ONTENTS
www.Statuspro.com
L
INEAR DISPLACEMENT VELOCITY MEASUREMENT
..............................................................5-4
Velocity graph .................................................................................................................5-4
L
INEAR POSITIONING MEASUREMENT
...................................................................................5-6
R
ECORDING MODE
..............................................................................................................5-14
ANGULAR MEASUREMENTS .........................................................................................6-1
M
EASURING SET FOR ANGULAR MEASUREMENTS
.................................................................6-1
M
EASUREMENT OF ANGLE DEVIATIONS
................................................................................ 6-3
S
TRAIGHTNESS MEASUREMENTS
..........................................................................................6-4
FLATNESS MEASUREMENTS.........................................................................................7-1
P
REPARATIONS
.....................................................................................................................7-1
A
LIGNMENT OF OPTICS FOR THE FLATNESS MEASUREMENTS
................................................ 7-2
Optical path alignment in the axis “1”...........................................................................7-4
Optical path alignment in the axes: “3”, “6”, “8”........................................................7-4
Optical path alignment in the axes: “5” and “7” .......................................................... 7-6
Optical path alignment in the axes: “2” and “4” .......................................................... 7-8
STRAIGHTNESS MEASUREMENTS – 3D...................................................................... 8-1
S
QUARENESS MEASUREMENTS
.............................................................................................8-4
VIBRATION MEASUREMENTS ......................................................................................9-1
M
EASUREMENTS
..................................................................................................................9-3
TECHNICAL DATA ..........................................................................................................10-1
S
YSTEM SPECIFICATIONS
.................................................................................................... 10-1
L
ASER HEAD
.......................................................................................................................10-2
S
YSTEM WORK CONDITIONS
............................................................................................... 10-2
P
OWER SUPPLY
...................................................................................................................10-2
PC
INTERFACE
....................................................................................................................10-2
E
NVIRONMENT COMPENSATION
.........................................................................................10-3

I
NTRODUCTION
1-1
www.lasertex.eu
1
I
NTRODUCTION
Laser measurement system µLine F1 is a two frequency laser
interferometer intended to be used mainly in machine geometry measurements.
Its small size and low weight simplify transportation and make the instrument
especially useful for service applications. Software version for Windows
9x/NT/2k/XP and automation of many measurement processes make the
interferometer easy to use. Software, compliant with ISO/DIS 230 and PN–93
M55580, enable making rapports and diagrams. It is possible to choose
statistical results processing according to norms: ISO 230-2 (European),
VDI/DGQ 3441 (German), NMTBA (USA), BSI BS 4656 Part 16 (British) and
PN-93 M55580 (Polish).
Very good technical parameters of the interferometer allow using it also in
scientific laboratories, for precision positioning, for scaling optical and magnetic
liners, etc.
Safety considerations
The Laser Interferometer µLine F1 is a Safety Class I product designed
and tested in accordance with international safety standards. It is also a Class II

I
NTRODUCTION
1-2
www.lasertex.eu
Laser product conforming to international laser safety regulations. The
instrument and the manual should be inspected and reviewed for safety
markings and instructions before operation.
Warnings
Although the laser measurement system µLine F1 was design to be used
in harsh environment, the following conditions must be met:
•The laser head must not be put near strong magnetic fields.
•The head should not be unscrewed from its base and if it is, it may
not be put on a heat sink (e.g. thick metal plate).
•The head must not be thrown or dropped.
•Keep the optical components clean and avoid scratching them.
•When the optics is dusted, clean it with pure alcohol.
•Do not use the system beyond its work conditions.

P
RINCIPLES OF OPERATION
2-1
www.Statuspro.com
2
P
RINCIPLES OF OPERATION
The rules of laser displacement measurements
Displacement measurements with the use of a laser interferometer allow
obtaining the accuracy of a displacement measurements of 0.4 ppm in air and
0.02 ppm in vacuum. The interferometer was first built by A.A. Michelson in
1881. The simplified schematic of the interferometer is shown on fig. 2.1.
Coherent light beam falls on a semi-transparent mirror. This mirror splits
the light into two beams. The first goes to the reference arm and reflects from
the reflector Z
1
; the second goes to the measurement arm and reflects form the
reflector Z
2
. The reflected beams meet again on the detector. Because these
beams come from the same, coherent, source, they will interfere. When the
moving reflector is being displaced, the frequency of the reflected beam in the
measurement arm changes. The detector counts the frequency difference
between reflected beams - f
D
(see fig. 2.1). The measured value of the
displacement is calculated according to
2
2
*
λ
λ
∗== NfL
D
(1)
Where: N – number of pulses,
λ - light wavelength.

P
RINCIPLES OF OPERATION
2-2
www.Statuspro.com
FIG.2.1.
THE MICHELSON INTERFEROMETER.
The construction of real interferometers
The main disadvantage of Michelson interferometer results from the fact
that the detector cannot determine, whether f
D
is negative or positive thus, from
the measurements the displacement of the moving reflector without the sign is
obtained. Currently there are widely used two methods that allow getting also
the direction of the movement. Depending on the number of light frequencies
(wavelengths) used in the interferometer, the first is called homodyne (one
frequency) and the second heterodyne (two frequencies) method.
In the homodyne method, shown on figure 2.2, as a coherent source of
light a linearly polarized laser is used. If it is two-mode laser (i.e. it generates
two wavelengths) than one mode must be cut off with the use of a properly set
polarizer. The polarising splitter splits the light beam from the laser into two
Detector
Z
Coherent
light
source
Reference
reflector
Moving
reflector
m
f
D
f
1
f
1
f
1
f
1
x f
D
Z
1
Z
2
f
1
- frequency resulting from
the Doppler effect
f
D
v
c
2f
1
f
D
=

P
RINCIPLES OF OPERATION
2-3
www.Statuspro.com
beams polarized vertically (90
o
) and horizontally (0
o
). The former is directed to
the measurement arm and the latter to the reference one. The frequency of the
beam in the measurement arm changes with the movement of the moving
reflector. The polarization of the reflected beams is changed to circular with the
use of a λ/4 waveplate. After 0° and 45° polarizers, two signals shifted in phase
are obtained. The phase shift is +90
o
when the measurement arm moves to and -
90
o
when it moves from the laser.
FIG.2.2.
THE BLOCK DIAGRAM OF AN INTERFEROMETER WORKING
ACCORDING TO THE HOMODYNE METHOD
In the heterodyne method, shown on figure 2.3, two laser frequencies are
used. Therefore a two-frequency laser is needed, e.g. a Zeeman laser. A two-
Polarizer 0
Pulse counter
Reference
reflector
Polarizing
splitter
Photodetectors
Polarizer 45
λ/4
Moving
reflector
f
2
f
1
m
f
D
m
f
D
f
1
f
1
f
1
f
1
f
1
f
1
f
2
f
1
Two perpendicular
linear polarizations
- frequency resulting from
the Doppler effect
f
D
x f
D
v
c
2f
1
f
D
=
sin cos
vertical polarization
horizontal polarization
polarization +45
polarization -45
o
o
oo
Two-mode
laser

P
RINCIPLES OF OPERATION
2-4
www.Statuspro.com
mode laser is not suitable for the heterodyne method interferometer, because the
difference between f
1
and
f
2
is usually too high for an electronic counter. The
output beam of a Zeeman laser consists of two circularly polarized beams, one
polarized leftward and the second rightward. A λ/4 waveplate changes circular
polarization to linear. The main difference between two described methods is
that in the heterodyne one the beam frequency in reference arm differs from the
beam frequency in the measuring arm. A detection path is also different –
subtracting differential frequencies of reference and measuring arms does the
measurement.
FIG.2.3.
THE BLOCK DIAGRAM OF AN INTERFEROMETER, WORKING
ACCORDING TO THE HETERODYNE METHOD
Zeeman laser
Reference
reflector
Polarizing
splitter
Photodetectors
λ/4
Moving
reflector
f
1
m
f
D
f
1
f
1
f
1
f
1
f
2
Two circular
polarizations
Two perpendicular
linear polarizations
- frequency resulting from
the Doppler effect
f
D
x f
D
c
f
2
f
2
f
2
f
2
m
f
D
f
2
f
1
Counter Counter
Substractor
Polarizers
f
1
-f
2
- ( )
f
2
f
1
m
f
D
Nonpolarizing
splitter
Reference path Measurement
path
v
2f
1
f
D
=
vertical polarization
horizontal polarization

P
RINCIPLES OF OPERATION
2-5
www.Statuspro.com
The heterodyne method gives correct results only when f
D
does not
exceed the difference between the laser frequencies, i.e.: f
2
– f
1
. In reality, that
difference, resulting from the Zeeman effect, is about 1MHz. This limits the
maximum available velocity of measuring arm, in one direction, to 0.3 m/s. The
next disadvantage of the heterodyne method is, that two frequencies must be
used for measurements, while in the homodyne method the second may be used
for measuring e.g. a second axis.
The influence of the outside conditions on the measurement
accuracy
According to equation (1) an interferometer’s unit of measure in length
measurement is laser’s wavelength. From definition
f
v
=
λ
(2)
a wavelength depends on laser’s frequency fand the speed of light vin the
measuring path. If the measurement is done in vacuum, than ν = c = 3*10
8
m/s.
The speed of light in a medium other than vacuum (e.g. air, water) is lower and
is described as
n
c
v
=
(3)
Where: n – a refraction coefficient.
Normally the refraction coefficient n is a complex variable or even a
tensor, but for less accurate calculations it is simplified to a constant. The air
coefficient depends mostly on the pressure P, temperature T and humidity H.

P
RINCIPLES OF OPERATION
2-6
www.Statuspro.com
The dependence n
T,P,H
,for the air was empirically determined by Edien and is
described as
n
T
TP
Pn
HPT
∆+
+
−+
=−
−
−
*003661,01
)*00997,0613,0(**101
*10*8775,21
6
7
,,
(4)
T
eHn
*057627,09
**10*033,3
−
−=∆
(5)
From the above equations one may obtain the refraction coefficient
dependences on T, P and H in usual conditions (T=293K, P=1000hPa, H=50%):
−=
∂
∂−
KT
n1
10*93,0 6
+=
∂
∂−
hPaP
n1
10*27,0 6
−=
∂
∂−
%
1
10*96,0 8
H
n
It is worth to notice that the most critical parameter is the temperature,
because its change influences the coefficient n more than changes in the pressure
and much more than changes in the humidity.
The accuracy of laser interferometers
Errors caused by the environment
The most impotent source of errors in machine geometry measurements is
the temperature (or more exactly, the change of the temperature) of the
measured machine. For example, if the machine’s base is made of steel, than the
base’s length increases 11.7µm when its temperature changes 1K. It shows how
important it is for very precise measurements to measure the temperature of the
controlled part of the machine and to use it in readout corrections. This is not a

P
RINCIPLES OF OPERATION
2-7
www.Statuspro.com
simple task for a few reasons, but the most important one is that, than when the
machine operates, there are temperature gradients on it. That means that more
than one temperature sensor is needed and that the more sensors are used the
better accuracy can be achieved. Moreover the shape of the measured part of
the machine may “absorb” a part of the expansion of the material or the part
may be built of materials of different expandability.
As was mentioned in the previous chapter, the temperature influences the
accuracy also as it changes the refraction coefficient of the medium the
measurements are made in (usually it is air, but may be e.g. water). An Edien
equation was presented, showing how the refraction coefficient of the air
changes with the change of the air temperature, pressure and humidity. The
errors caused by the change of the wavelength are less important than the
mentioned above, but they cannot be abandoned. Roughly, a 1ppm error (i.e.
1µm/m) is caused by: the air temperature change of o 1K, the air pressure
change of 4hPa and the air humidity change of 30%.
A dead path error
A dead path error is an error associated with the change in environmental
parameters during a measurement. This error occurs when some part of the light
path (a dead path) is not included in the temperature (both air and base),
pressure and humidity compensation.
The dead path of the light path is a distance between the optical
interferometer and the base (or the null point) of the measuring position (L
1
on
figure 2.4). Let the position of the interferometer and the retro-reflector do not
change. When there is a change in the air temperature, pressure or humidity,
than the wavelength changes on the whole path length (L
1
+ L
2
). The path length
changes also when the temperature of the base changes. But the correction
system will use the correct wavelength only on the length L2 and will correct

P
RINCIPLES OF OPERATION
2-8
www.Statuspro.com
only this length. The correction will not be made on a dead path L
1
. In this way,
the laser system will “move” the base point.
A dead path error is the more severe the greater is the distance between
the interferometer and the base point. This error is especially important in laser
interferometers where the interferometer is build-up in a common casing with a
laser head, because it is than very difficult to reduce a dead path.
FIG.2.4.
AN ILLUSTRATION OF A DEAD PATH ERROR
A cosine error
If the laser beam is not parallel to a measured axis of a machine (i.e. the
optical path is not properly adjusted) than a difference between the real distance
and the measured distance occurs. This error of un-alignment is known as a
Laser head
Interferometer
Reflector
L
1
L
2
Base point
(Null point)
Laser head
Interferometer
Reflector
L
1
L
2
Base point
(Null point)
The correct deployment of the optical
components for reducing a dead path error

P
RINCIPLES OF OPERATION
2-9
www.Statuspro.com
cosine error, because its magnitude depends on the angle between the laser beam
and the axis of the machine (fig. 2.5).
If, as a reflector a flat mirror is used, than the beam must be perpendicular
to it. If the machine changes its position form point A to point B, than the beam
stays perpendicular to the mirror, but moves on its surface. The distance
measured by the laser interferometer L
LMS
, will be smaller, than the real distance
L
M
, according to
L
LMS
= L
M
* cosΘ (6)
The above equation is valid also when as a reflector a corn cube is used.
FIG.2.5.
THE BEAM UNALIGNMENT AS A CAUSE OF A COSINE ERROR
The only method of eliminating the cosine error is a proper laser beam
alignment done before a measurement.
Laserhead
L
LMS
L
M
Θ
Reflectors
Laser beam
Machine's movement
axis

P
RINCIPLES OF OPERATION
2-10
www.Statuspro.com
An Abbe error
An Abbe error occurs when, during measurements, the measured part
does not move perfectly straight and there appear angular movements, which
cause sloping of the retro-reflector. The sloping of the reflector is the greater the
longer is the distance between the axis of the measurement and the axis of
movement. This distance is called An Abbe offset. Only the movements in the
axis of the measurement are important (see fig. 2.6). An Abbe error may be
avoided only when there are no angular movements of the retro-reflector in the
axis of the measurements.
FIG.2.6.
AN ILLUSTRATION OF AN ABBE ERROR
A laser stability error
As was already mentioned, in laser measurements the laser wavelength
instability changes directly the readout from the interferometer, e.g. a relative
instability of the laser in the range of 1ppm (10
-6
), causes an error of 1µm on
every 1m of a measured distance. Therefore the laser instability error is
Reflector
Axis of
measurement
Reflector
axis of
movement
Measured distance
Real distance
Θ
Abbe
offset
Error

P
RINCIPLES OF OPERATION
2-11
www.Statuspro.com
important mainly in measurements in vacuum (where a refraction coefficient is
constant) and when a low stability laser is used (e.g. a semiconductor laser). The
stability of usually used in laser measurement systems, HeNe gas lasers is 0.02
ppm, so the stability error may be neglected.
Other errors
In some conditions, a noticeable error may be caused by the electronic
part of the interferometer. As the electronics is used mainly for counting, the
errors may be associated either with miscounting (some pulses are not counted)
or with miscalculating (the calculations are made with finite precision).
A summary of laser measurement system errors
In order to show which of the errors influence the accuracy of a laser
measurement system the most, an exemplary calculation of errors on a 1m long
steel machine is shown on figures 2.7 and 2.8. Different scales of the charts
should be taken into account.

P
RINCIPLES OF OPERATION
2-12
www.Statuspro.com
FIG.2.7.
A CALCULATION OF ERRORS FOR A LASER MEASUREMENT SYSTEM
WITHOUT THE COMPENSATION
OF THE ENVIRONMENT
FIG.2.8.
A CALCULATION OF ERRORS FOR A LASER MEASUREMENT SYSTEM
WITH THE COMPENSATION
OF THE ENVIRONMENT
0 0,05 0,1 0,15 0,2 0,25 0,3
1
Positioning error [um/m]
Laser Environment Cosine Dead path Electronics Unlinearities Thermal drift
0 1 2 3 4 5 6 7 8 9 10
1
Positioning error [um/m]
Laser Environment Cosine Dead path Electronics Unlinearities Thermal drift

P
REPARATIONS
3-2
www.statuspro.com
3
P
REPARATIONS
To start the measurements using the Laser Interferometer µLine F1,
software "LSP 30 -3D" should be installed on HD of a PC computer. The
hardware requirements are:
-Windows 9x/NT/2k/XP system,
-CR-ROM
-Pentium processor, 600 MHz or better
-SVGA graphic card making possible working with resolution
800x600.
Software installation
To install the LSP program on the PC computer put the CD disc " µLine
F1 " into the CD-ROM. The program will be installed automatically. If the
installation does not start automatically, explore the CD and double click on
setup.exe icon.

P
REPARATIONS
3-3
www.statuspro.com
The Laser Interferometer system elements
The number of elements the system consists depends on desired types of
measurements. To the standard set (for linear measurements) belong:
1. 1 x Laser head – Laser Interferometer
2. 1 x Power supply - Laser Interferometer Power Supply
3. 1 x Tripod stand
4. 1 x Environmental Compensation Unit - (ECU) SM1
5. 1 x Laser head to power supply cable
6. 2 x Magnetic holder UM1
7. 1 x Linear interferometer IL1
8. 1 x Linear retro-reflector RL1
9. 3 x Basis temperature sensor T1, T2, T3
10. 1 x USB cable
11. 1 x Manual Strobe cable
See fig. 3.1b on the next page for pictures of the elements of the standard set and fig.3.1a
present
the suitcase for transportation and storing of the interferometer system.
.
Additional elements for angular measurements are:
1. 1 x Angular interferometer IK1
2. 1 x Angular retro-reflector RK1
3. 2 x Beam directing mirror ZK1
4. 1 x Rotary table SO1
Other manuals for mLine F1
1
Table of contents
Other Status Pro Measuring Instrument manuals
Popular Measuring Instrument manuals by other brands

Siemens
Siemens SITRANS F M MAG 8000 quick start
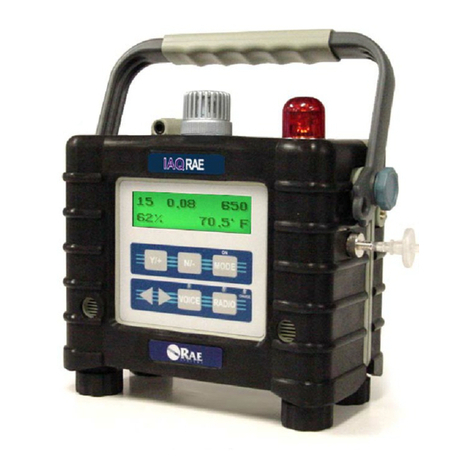
Rae
Rae IAQRAE PGM-5210 Operation & maintenance manual
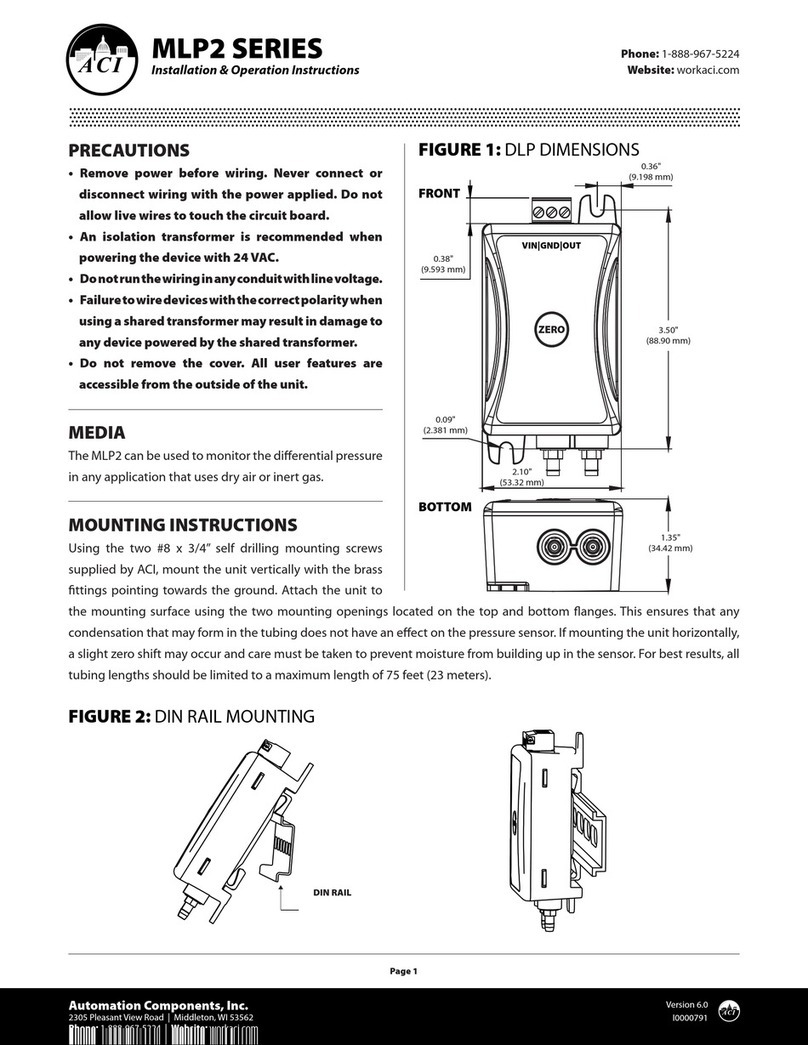
aci
aci Zero Installation & operation instructions
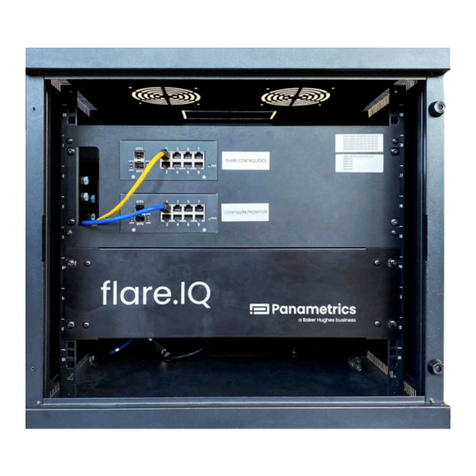
Panametrics
Panametrics flare.IQ Generation 2 Operation and maintenance manual
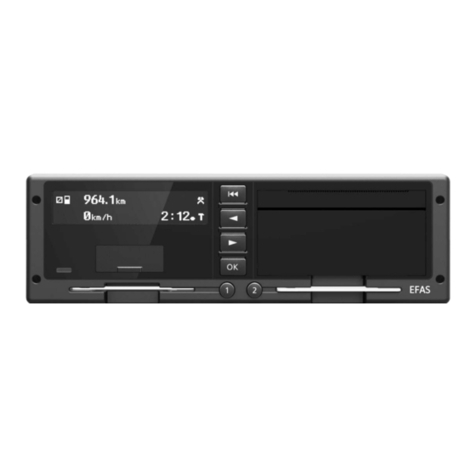
intellic
intellic Bosch EFAS-4.10 Workshop manual
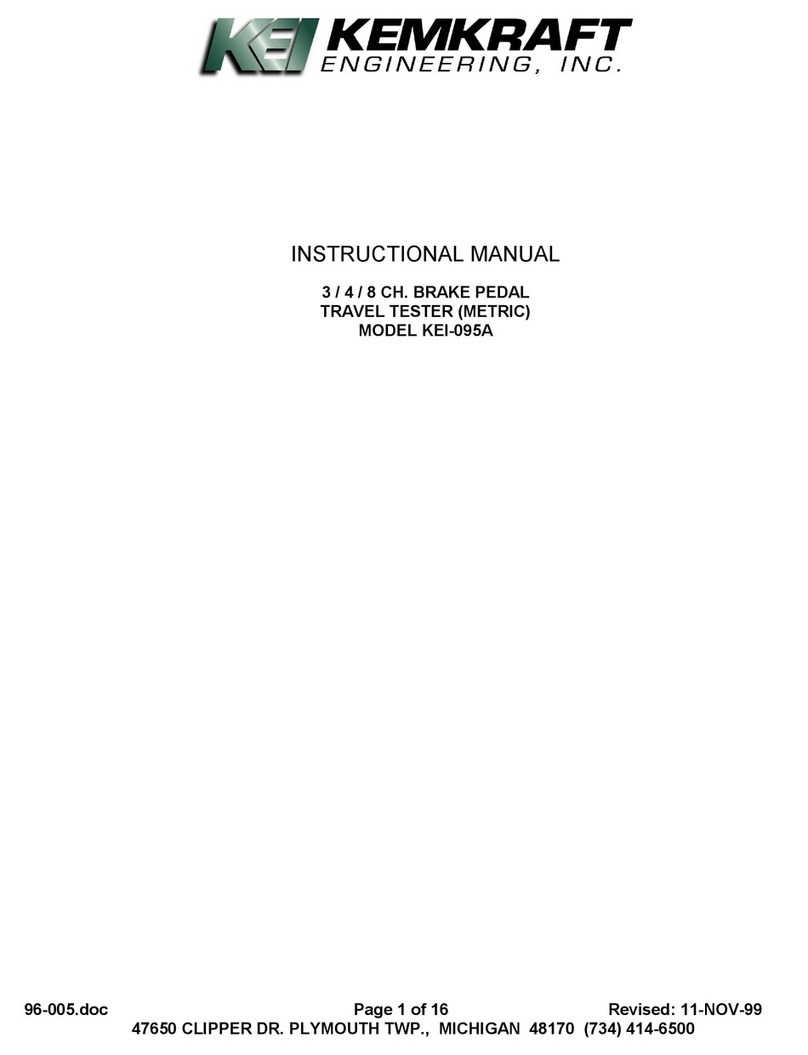
KEMKRAFT
KEMKRAFT KEI-095A Instructional manual