Stober C0 User manual

C0 – C9 gear units, geared motors
Operating manual
en-US
07/2023
ID 443365_en.00

Table of contents
2
07/2023 | ID 443365_en.00
Table of contents
1 User information....................................................................................................................................................... 4
1.1 Storage and transfer................................................................................................................................................ 4
1.2 Original language..................................................................................................................................................... 4
1.3 Formatting conventions .......................................................................................................................................... 4
1.4 Terms....................................................................................................................................................................... 5
1.5 Supporting documents ............................................................................................................................................ 5
1.6 Limitation of liability................................................................................................................................................ 5
1.7 Product names and brands...................................................................................................................................... 5
1.8 Copyright notice ...................................................................................................................................................... 5
2 General safety instructions........................................................................................................................................ 6
2.1 Intended use............................................................................................................................................................ 6
2.2 Requirements for personnel.................................................................................................................................... 6
2.3 Prevention of personal injury .................................................................................................................................. 6
2.3.1 Mechanical hazards ................................................................................................................................ 6
2.3.2 Thermal hazards ..................................................................................................................................... 7
2.4 Prevention of property damage .............................................................................................................................. 7
3 Product description................................................................................................................................................... 8
3.1 Basic structure......................................................................................................................................................... 8
3.2 Type designation ..................................................................................................................................................... 9
3.3 Nameplate ............................................................................................................................................................. 10
3.4 Mounting positions ............................................................................................................................................... 10
3.5 Direction of rotation.............................................................................................................................................. 11
3.6 Ambient conditions ............................................................................................................................................... 12
3.7 Other product features.......................................................................................................................................... 12
3.8 Additional documentation..................................................................................................................................... 13
4 Transport and storage ..............................................................................................................................................14
4.1 Transport ............................................................................................................................................................... 14
4.2 Storage .................................................................................................................................................................. 14
4.2.1 Long-term storage ................................................................................................................................ 15
5 Installation...............................................................................................................................................................16
5.1 Cleaning agent and solvent ................................................................................................................................... 16
5.2 Mounting the motor on a gear unit....................................................................................................................... 16
5.2.1 Permitted tilting torques at the gear unit input ................................................................................... 17
5.2.2 Tolerances for the add-on motor ......................................................................................................... 17
5.2.3 Mounting the motor on a gear unit with ME adapter.......................................................................... 18

Table of contents
07/2023 | ID 443365_en.00
3
5.2.4 Mounting the motor on a gear unit with MQ/MR adapter with curved tooth coupling...................... 21
5.2.5 Mounting the motor on a gear unit with MQ/MR adapter with plug-in coupling ............................... 23
5.2.6 Mounting the motor on a gear unit with MB adapter.......................................................................... 25
5.3 Mounting drive elements on a solid shaft............................................................................................................. 25
5.4 Mounting the gear unit on the machine ............................................................................................................... 26
6 Tightening torques ...................................................................................................................................................29
7 Commissioning.........................................................................................................................................................30
7.1 Before commissioning ........................................................................................................................................... 30
7.2 During commissioning ........................................................................................................................................... 30
8 Servicing ..................................................................................................................................................................31
8.1 Cleaning................................................................................................................................................................. 31
8.2 Inspection .............................................................................................................................................................. 31
8.2.1 Changing the oil .................................................................................................................................... 31
8.3 Remedying faults................................................................................................................................................... 34
8.3.1 Troubleshooting faults.......................................................................................................................... 35
8.4 Servicing ................................................................................................................................................................ 35
8.5 Service ................................................................................................................................................................... 35
9 Removal and disposal...............................................................................................................................................37
9.1 Removal................................................................................................................................................................. 37
9.2 Disposal ................................................................................................................................................................. 37

1 | User information
4
07/2023 | ID 443365_en.00
1 User information
This documentation is a part of the product. It applies to products in the standard design according to the corresponding
STOBER catalog.
1.1 Storage and transfer
As this documentation contains important information for handling the product safely and efficiently, it must be stored in
the immediate vicinity of the product until product disposal and be accessible to qualified personnel at all times.
Also pass on this documentation if the product is transferred or sold to a third party.
1.2 Original language
The original language of this documentation is German; all other language versions are derived from the original language.
1.3 Formatting conventions
Orientation guides in the form of signal words are used to emphasize specific information so that you are able identify it in
this documentation quickly.
Safety notes indicate special risks when handling the product and are accompanied by relevant signal words that express
the extent of the risk. In addition, warning notes for possible property damage and useful information are also indicated by
signal words.
WARNING!
Warning
This word with a warning triangle means there may be a considerable risk of fatal injury
▪ if the stated precautionary measures are not taken.
CAUTION!
Caution
This word with a warning triangle indicates that minor personal injury may occur
▪ if the stated precautionary measures are not taken.
ATTENTION!
Attention
This indicates that damage to property may occur
▪ if the stated precautionary measures are not taken.
Information
Information indicates important information about the product or serves to emphasize a section in the documentation that
deserves special attention from the reader.

1 | User information
07/2023 | ID 443365_en.00
5
Embedded warning information
Embedded warning information is integrated directly into the instruction manual and is structured as follows:
SIGNAL WORD! Type of hazard, its cause and possible consequences of disregarding it! Measures for avoiding the hazard.
Signal words in embedded warning information have the same meaning as in the normal warning information described
previously.
1.4 Terms
This documentation describes both STOBER gear units and gear components of STOBER geared motors. For reasons of
clarity, the collective term drives is used for these.
1.5 Supporting documents
Separate documents apply to the drive components which can be attached to STOBER gear units, depending on the design.
These documents can be found by entering the serial number of the drive at https://id.stober.com or by scanning the QR
code on the nameplate of the drive.
Alternatively, you can find supporting documents at http://www.stoeber.de/en/downloads/. Enter the ID of the
documentation in the Search... field:
Drive components Operating manual ID
LM Lean motor 443048_en
EZ synchronous servo motor 443032_en
MB motor adapter with brake 443287_en
Asynchronous motors 442577_en
1.6 Limitation of liability
This documentation was created taking into account the applicable standards and regulations as well as the current state of
technology.
No warranty or liability claims for damage shall result from failure to comply with the documentation or from use that
deviates from the intended use of the product. This is especially true for damage caused by individual technical
modifications to the product or the project configuration and operation of the product by unqualified personnel.
1.7 Product names and brands
Product names that are registered as brands are not specifically identified in this documentation. Existing property rights
(patents, trademarks, protection of utility models) are to be observed.
1.8 Copyright notice
Copyright © STOBER. All rights reserved.

2 | General safety instructions
6
07/2023 | ID 443365_en.00
2 General safety instructions
There are risks associated with the product described in this documentation that can be prevented by complying with the
described warning and safety instructions as well as the included technical rules and regulations.
2.1 Intended use
The drives described in this documentation are intended for installation in industrial machines or systems.
The following are considered non-intended use:
§Any overloading of the drives
§Operation in ambient conditions that deviate from those described in the corresponding technical documentation
§Modifying or refitting the drives
§Using the drives for an application other than that defined during project configuration
Commissioning the machine in which the drives are installed is prohibited until it has been determined that the machine
corresponds to regional laws and guidelines. In particular, the (Machinery) Directive 2006/42/EC is to be observed in the
respective scope.
Operation of the drives in potentially explosive atmospheres is prohibited, unless they are expressly designed for this.
2.2 Requirements for personnel
All mechanical tasks that arise during the assembly, commissioning, maintenance and removal of the product may be
performed only by specialized personnel who hold a corresponding qualification in the field of metal technology.
All electrical tasks that arise during the assembly, commissioning, maintenance and removal of the product may be
performed only by electrically skilled persons who hold a corresponding qualification in the field of electrical engineering.
Tasks that arise during transport, storage and disposal may be performed by personnel who have been instructed in the
suitable method for doing so.
Furthermore, personnel who handle the product must carefully read, understand and observe the valid regulations, legal
requirements and applicable basic rules as well as this documentation and the safety instructions it contains.
2.3 Prevention of personal injury
2.3.1 Mechanical hazards
WARNING!
Dangerous movements of machine parts!
Moving machine parts can cause serious injuries or even death!
üBefore starting the motor or drive:
▪ Install all protective devices necessary for operation.
▪ Make sure that no one is standing in the danger area or able to enter it unchecked.
▪ Leave the danger area.

2 | General safety instructions
07/2023 | ID 443365_en.00
7
WARNING!
Sinking or falling of gravity-loaded axes or vertical axes after switching off the motor due to gravity!
Falling gravity-loaded axes or vertical axes can cause serious injuries or even death!
▪ Be aware that the holding brake of the motor does not offer sufficient safety for persons that are in the hazard area
of gravity-loaded axes or vertical axes.
▪ Move gravity-loaded axes or vertical axes to their lowest position and lock or brace them mechanically before
allowing people to enter the danger area.
WARNING!
Unsecured feather keys or drive elements can be thrown due to the rotation of the input shaft!
Flying metal parts can cause serious injuries!
▪ Mount the provided drive elements properly or remove them before a test run.
2.3.2 Thermal hazards
CAUTION!
The surface of the drive can reach temperatures over 65°C during operation!
Touching the hot surface of the drive can cause severe skin burns!
▪ Do not touch the drive during operation or immediately afterward.
▪ Allow the drive to cool sufficiently before carrying out work on the drive.
▪ Wear protective gloves when working on the drive.
2.4 Prevention of property damage
ATTENTION!Damage to bearings and shafts due to improper assembly! Never use force when installing machine elements
with fittings, e.g. hitting power transmission elements, shafts or the motor or gear housing with a hammer, but rather
install them in accordance with the following instructions.
ATTENTION!Shaft seal rings can be damaged by solvents! Prevent shaft seal rings from coming into contact with solvents
when cleaning and degreasing unpainted surfaces.

3 | Product description
8
07/2023 | ID 443365_en.00
3 Product description
In this chapter, you will find product details that are relevant for assembly, commissioning and servicing. Detailed technical
data on your drive can be found in the order confirmation. You will find more product information and dimensional
drawings in the corresponding catalog (Additional documentation [}13]). The respective separate technical
documentation applies to attached motors.
3.1 Basic structure
5
2a
4
3
1
5
4
3
2b
1
Tab. 1: Basic structure of a C613N gear unit (left) and C613F gear unit (right)
1 Solid shaft with feather key 2a Foot mount
2b Round flange 3 Nameplate
4 Gear housing 5 MR motor adapter
5
4
2c
3
1
Tab. 2: Basic structure of a C613G gear unit
1 Solid shaft with feather key 2c Pitch circle diameter
3 Nameplate 4 Gear housing
5 MR motor adapter

3 | Product description
07/2023 | ID 443365_en.00
9
3.2 Type designation
In this chapter, you will find an explanation of the type designation with the associated options.
Example code
C 2 0 2 N 0280 ME20
Explanation
Code Designation Design
CType Helical gear unit
2Size 2 (example)
0
1
Generation Generation 0
Generation 1
2
3
Stages Two-stage
Three-stage
G
F
Q
N
Housing Pitch circle diameter
Round flange
Square flange
Foot
0280 Transmission ratio (i x 10 rounded) i = 28.24 (example)
ME20
MQ
MR
MB
Motor adapter ME20 motor adapter (example)
with EasyAdapt coupling
Square motor adapter
with curved tooth or plug-in coupling
Round motor adapter
with curved tooth or plug-in coupling
ServoStop motor adapter with brake
EZ
LM
IE3D
Motor EZ synchronous servo motor
LM Lean motor
IE3D asynchronous motor

3 | Product description
10
07/2023 | ID 443365_en.00
3.3 Nameplate
An example gear unit nameplate is explained in the figure below.
1
2
3
4
5
6
7
8
9
10
Code Designation
1 Name of manufacturer
2 Type designation
3 Gear ratio of the gear unit
4 Lubricant specification
5 Serial number of the gear unit
6 QR code (link to product information)
7 Dimensions of the motor adapter (pilot/bolt circle/motor shaft diameter)
8 Date of manufacture (year/calendar week)
9 Lubricant fill volume
10 Customer-specific data
3.4 Mounting positions
The following table shows the standard mounting positions.
The numbers identify the gear unit sides. The mounting position is defined by the gear side facing downwards.
EL1
IMB3, IMB5, IMB14, IMB34, IMB35
EL2
IMB8
EL3
IMB7

3 | Product description
07/2023 | ID 443365_en.00
11
EL4
IMB6
EL5
IMV1, IMV5, IMV18
EL6
IMV3, IMV6, IMV19
An adhesive label is applied to the gear unit that explains the designated mounting position. The arrow on the adhesive
label indicates the side with which the gear unit must be mounted facing down.
Fig.1: Adhesive label for the mounting position
3.5 Direction of rotation
C002 − C912 C103 − C913
The input and output rotate in the same direction. The input and output rotate in opposite directions.
The pictures show mounting position EL1.

3 | Product description
12
07/2023 | ID 443365_en.00
3.6 Ambient conditions
Standard ambient conditions for transport, storage and operation of the gear unit are described in this chapter. Deviating
ambient conditions for special designs are specified in the order confirmation. Ambient conditions for motors attached to a
gear unit can be found in the technical documentation of the motor.
Feature Description
Transport/storage surrounding temperature −10 °C to +50 °C
Surrounding operating temperature 0 °C to +40 °C
Installation altitude ≤ 1000 m above sea level
Notes
In order to prevent corrosion damage and damage to the shaft seal rings, protect the drive from the following influences:
§Environments with harmful oils, acids, gases, vapors, dust or radiation
§Extreme temperature fluctuations with high humidity
§Condensation or icing
§Strong UV radiation (e.g. direct sunlight)
§Presence of salt spray
§Sparks
In potentially explosive atmospheres, only gear units in an explosion-proof design in accordance with (ATEX) Directive
2014/34/EU may be used. Separate documentation applies to the explosion-proof design.
3.7 Other product features
Other features of gear units in the standard design can be found in the following table.
Feature Description
Maximum permitted gear unit temperature (on the surface
of the gear unit)
≤ 80 °C
Paint Black RAL 9005
Lubricant Synthetic; for specification and quantity, see nameplate
Ventilation C0 – C5: No ventilation
C6 – C9: Air release valves installed according to the
mounting position
Weight See order documents
Protection class: 1IP65
1 Observe the protection class of all the components.

3 | Product description
07/2023 | ID 443365_en.00
13
3.8 Additional documentation
You will find more information about the product at http://www.stoeber.de/en/downloads/. Enter the ID of the
documentation in the Search... field.
Product combination Catalog title ID
Gear unit + ME/MEL/MF/MFL motor adapter Servo gear units 443054_en
Gear unit + MB motor adapter with brake ServoStop servo gear units with brake 443234_en
Gear unit + MQ/MR motor adapter Power transmission gear units 441834
Gear unit + EZ synchronous servo motor EZ synchronous servo geared motors 442437_en
Gear unit + LM Lean motor Lean motors 443016_en
Gear unit + IE3D asynchronous motor Asynchronous geared motors 443136_en
Gear unit Lubricant filling quantities for gear units 441871
If you have questions about your drive that are not answered by this documentation, please contact STOBER Service
(Service [}35]).

4 | Transport and storage
14
07/2023 | ID 443365_en.00
4 Transport and storage
STOBER products are packaged carefully and delivered ready for installation. The type of packaging depends on the product
size and the transport method.
Observe the following information during transport and storage:
§Inspect the delivery for any transport damage immediately upon receiving it and report any transport damage
immediately. Do not put damaged products into operation.
§Check your delivery for completeness using the delivery note and report any missing parts to the supplier.
§Transport and store the product in the original packaging in order to protect it from damage. Remove the original
packaging and transport safety devices shortly before assembly.
Ambient conditions
The ambient conditions for transport and storage can be found in the chapter Ambient conditions [}12].
4.1 Transport
WARNING!
Suspended loads!
Loads that become loose and fall during the lifting process can cause serious injuries or even death!
▪ Observe the following instructions.
▪ Cordon off the danger zone and ensure that no one stands under the suspended loads.
▪ Wear safety shoes.
Lifting and transporting the drive may require lifting gear (e.g. a crane), depending on the weight. The weight of your drive
is specified in the accompanying delivery documents.
Lift and transport the drive as follows:
§Use lifting gear with a sufficient lifting capacity for the weight of the drive.
§Run hoist slings directly around the drive housing and secure the hoist slings from slipping.
In order to prevent the drive from falling or getting damaged during transport, observe the following:
§Do not lift or fasten the drive on the output shaft or attached parts.
§Fasten the motor installed on the gear unit as well and make sure that there is no diagonal pull.
4.2 Storage
Store the drive in a dry, dust-free environment in the original packaging at a storage temperature between −10°C and
+50°C.

4 | Transport and storage
07/2023 | ID 443365_en.00
15
4.2.1 Long-term storage
If you would like to store the drive for longer than 6 months, take the following steps to prevent corrosion damage:
1. Apply a suitable corrosion protection agent to unpainted surfaces, such as shaft ends or flange contact surfaces.
2. Completely fill the gear unit with lubricant. The lubricant specification can be found by entering the serial number of
the gear unit at https://id.stober.com or by scanning the QR code on the nameplate of the gear unit.
Before commissioning the gear unit, reduce the lubricant fill volume to the fill volume that is specified on the nameplate of
the gear unit.

5 | Installation
16
07/2023 | ID 443365_en.00
5 Installation
This chapter contains information on how to correctly mount standard STOBER drive designs and avoid injury to persons or
damage to property. Differing information for customer-specific designs is included in the order documents.
Observe the technical documentation of the motor for the assembly and electrical connection of the motor.
Inspect the drive for transport or storage damage. If the drive is damaged, do not install it and contact the STOBER Service
department.
The following tools and equipment are required for mounting the drive:
§If necessary due to the overall weight, lifting gear with appropriate fastening elements and sufficient lifting capacity
§Open-end wrench set
§Socket wrench set
§Long hexagon insert set
§Torque wrench
§Grease
§Cleaning agent or solvent
Information about the specific tools or equipment can be found in the respective chapter.
5.1 Cleaning agent and solvent
Upon delivery, unpainted surfaces of the drive are protected by a corrosion protection agent. The corrosion protection
agent must be removed from contact surfaces such as shaft ends and flange contact surfaces before assembly. STOBER
recommends removing the corrosion protection with a suitable cold cleaner (e.g. Carlofon Autocleaner) which, in contrast
to volatile solvents, is almost odorless and does not weaken the sealing lips of the shaft seal rings. Otherwise, you can use
commercially available solvents.
Be aware that all surfaces that come into contact with each other in a clamp connection must be degreased with a cold
cleaner or solvent for error-free torque transmission. Additional information can be found in the following chapters.
ATTENTION!Shaft seal rings can be damaged by solvents! Prevent shaft seal rings from coming into contact with solvents
when cleaning and degreasing unpainted surfaces.
5.2 Mounting the motor on a gear unit
This chapter contains information on how to mount a motor on a STOBER gear unit with a motor adapter. The motor
adapter type of your gear unit can be found on the nameplate of the gear unit. STOBER recommends using a motor with a
shaft without a feather key, since the keyway negatively affects smooth operation.
If you have a STOBER geared motor, you can skip this chapter.
ATTENTION!Damage to encoders, bearings and shafts due to improper assembly! Never use force when mounting drive
elements with fittings, e.g. hitting drive elements, shafts or the motor or gear housing with a hammer, and instead install
them in accordance with the instructions in the documentation.
Information
To make mounting the motor easier, stick to the following principal assembly order when possible:
▪ First mount the motor on the gear unit, then the geared motor on the machine
▪ Mount the motor on the gear unit with the motor shaft pointing down vertically in order to prevent unfavorable
shifting and tilting of the motor shaft.

5 | Installation
07/2023 | ID 443365_en.00
17
5.2.1 Permitted tilting torques at the gear unit input
If you mount a STOBER gear unit on the machine in a horizontal mounting position, check that the permitted tilting torque
is not exceeded on the gear unit input before mounting the corresponding motor. Information on the permitted tilting
torque can be found in the corresponding catalog (Additional documentation [}13]).
5.2.2 Tolerances for the add-on motor
This chapter describes tolerances for motors that are required for assembly on a STOBER gear unit with motor adapter.
Dimensional drawings of the motor adapter can be found in the corresponding catalog (Additional documentation [}13]).
Tolerances for shafts in accordance with DIN 748-1
Diameter [mm] Tolerance
≤ 50 ISO k6
> 50 ISO m6
Tolerances for centering diameter on the motor flange in accordance with EN 50347
Centering diameter [mm] Flange size [mm] Tolerance
≤ 230 65 – 300 ISO j6
> 230 350 – 500 ISO h6
Tolerances for radial runout, axial runout and concentricity in accordance with IEC 60072-1 (normal class)
Symbol Unit Explanation
kx µm Concentricity of the flange centering in relation to the shaft
pl µm Axial runout of the flange mounting surface in relation to the shaft
r µm Radial runout of the shaft end

5 | Installation
18
07/2023 | ID 443365_en.00
∅d [mm] r [µm]
d ≤ 10 30
10 < d ≤ 18 35
18 < d ≤ 30 40
30 < d ≤ 50 50
50 < d ≤ 80 60
Centering diameter [mm] Flange size kx [µm] pl [µm]
50 – 95 65 – 115 80 80
110 – 130 130 – 165 100 100
250 – 450 300 – 500 125 125
5.2.3 Mounting the motor on a gear unit with ME adapter
This chapter describes the assembly of a motor on a STOBER gear unit with an ME motor adapter.
Prerequisites
§Dimensional tolerances of the motor correspond to the requirements in the chapter Tolerances for the add-on motor
[}17]
§The permitted tilting torque on the gear unit input is not exceeded (see Permitted tilting torques at the gear unit input
[}17])
§Four screws of strength class 8.8 are available for mounting the motor on a gear unit. The minimum screw depth for
these screws is 1.6x the nominal diameter of the screw
§The necessary tools and aids are available (see Installation [}16])
§The information in the chapter Cleaning agent and solvent [}16] is observed
Procedure
In order to prevent unfavorable shifting or tilting of the motor shaft, STOBER recommends mounting the motor on the gear
unit with the motor shaft pointing down vertically.
1. Position the gear unit (5), if necessary with the aid of lifting gear, so that the motor can be mounted in a vertical
position.
2. Remove the transport cover of the motor adapter.
3. If a feather key is installed on the motor shaft, remove it.
4. Remove all corrosion protection from the motor shaft and contact surfaces of the motor and motor adapter.
5. Carefully remove any lubricant from the inner hole of the clamping hub (15) and, if available, the inner and outer
surface of the adapter bushing (6) for the motor shaft.
6. Unscrew the screw plug (13).
7. Turn the clamping hub so that the locking screw (11) can be turned over the bore for the screw plug (13), guide the
hexagon insert (3) through the bore and insert it into the hexagon socket of the locking screw.
8. If an adapter bushing (6) is necessary, insert the adapter bushing into the inner hole of the clamping hub (15) as far as
it will go and turn the adapter bushing so that the slot of the adapter bushing coincides with the slot of the clamping
hub (10).

5 | Installation
07/2023 | ID 443365_en.00
19
9. If necessary, use two suitable attachment points to secure the motor with the lifting gear so that the motor shaft is
pointing down vertically.
10. Turn the motor in an axial position to the gear unit so that the nameplates are on the same side, if possible, and can
also be read after installation in the machine.
11. If the motor shaft has a keyway, position the motor shaft so that the keyway faces the slot of the clamping hub (10).
12. An elastic bellow coupling is installed in the MF/MFL motor adapter that can assume a slightly tilted position, as long
as the clamping hub is not connected with the motor shaft. Correct any existing tilt of the clamping hub before
inserting the motor shaft.
13. Carefully place the motor on the motor adapter (4) and make sure that the motor shaft is inserted (7) in the clamping
hub (15) so that it is centered and not at an angle.
14. If the motor shaft cannot be inserted into the clamping hub, do not use force and instead turn the locking screw (11)
counterclockwise one quarter rotation with the hexagon insert (3) (in this process, the clamping hub widens because
the grooved pin (12) locks against the cylinder head of the locking screw). The size of the hexagon insert can be found
on the adhesive label (14) as well as in the following tables.
15. If necessary, repeat the previous step.
16. The contact surfaces of the motor flange and motor adapter flange must fit together without a gap. If this is not the
case, do not use force and instead check the dimensions of the motor.
17. Mount the motor on the motor adapter with screws (9). Tighten the screws evenly, with increasing torque and
alternating diagonally. The tightening torque can be found in the chapter Tightening torques [}29].
18. Insert the torque wrench (2) in the hexagon insert (3) and tighten the locking screw (11). The corresponding tightening
torque can be found in the following table and on the adhesive label on the motor adapter.
19. If the motor flange does not fully cover the bores or openings of the motor adapter, seal off the openings with a
suitable sealant. This maintains the protection class of the gear unit so that dust and water cannot get into the interior
of the motor adapter.
20. Plug the access hole with the screw plug (13) by screwing it in until it is flush with the surface of the motor adapter.

5 | Installation
20
07/2023 | ID 443365_en.00
5
4
14
13
6
2
7
3
8
9
15
10
11
12
Fig.2: Mounting a motor on a K gear unit with ME motor adapter (example)
2 Torque wrench 3 Hexagon insert
4 Motor adapter 5 Gear unit
6 Adapter bushing (if present) 7 Motor shaft
8 Motor 9 Screw
10 Slot of the clamping hub 11 Locking screw
12 Grooved pin 13 Screw plug
14 Adhesive label 15 Clamping hub
Tightening torques for the locking screw (11)
The tightening torques for the locking screw are in line with the size of the ME adapter on the gear unit input and the
diameter of the motor shaft.
Type d2 KS s MA
[mm] [mm] [Nm]
_ME10 d2≤14 M5 4 5.9
_ME10 14<d2≤19 M6 5 10
_ME20 d2≤19 M6 5 10
_ME20 19<d2≤24 M8 6 25
_ME30 d2≤24 M8 6 25
This manual suits for next models
9
Table of contents
Other Stober Engine manuals
Popular Engine manuals by other brands
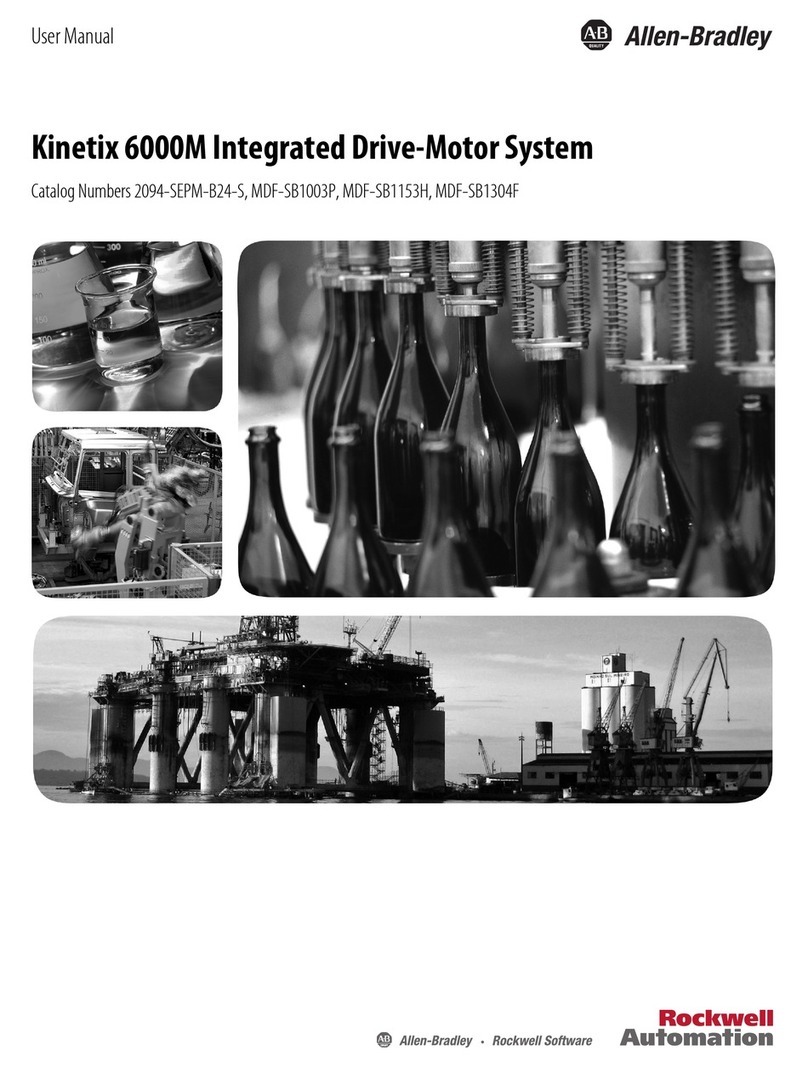
Allen-Bradley
Allen-Bradley Kinetix 6000M user manual

YS
YS DZ140 Operator's manual
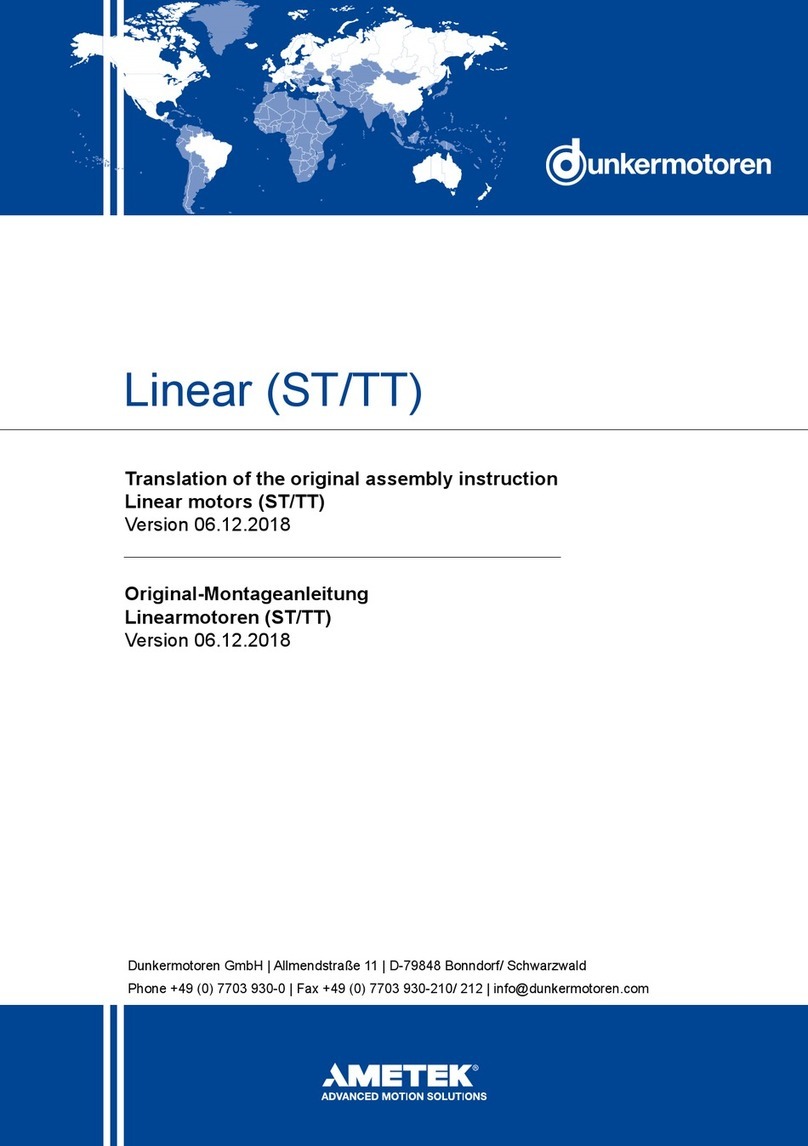
Ametek
Ametek Dunkermotoren Linear Series Translation of the original assembly instruction
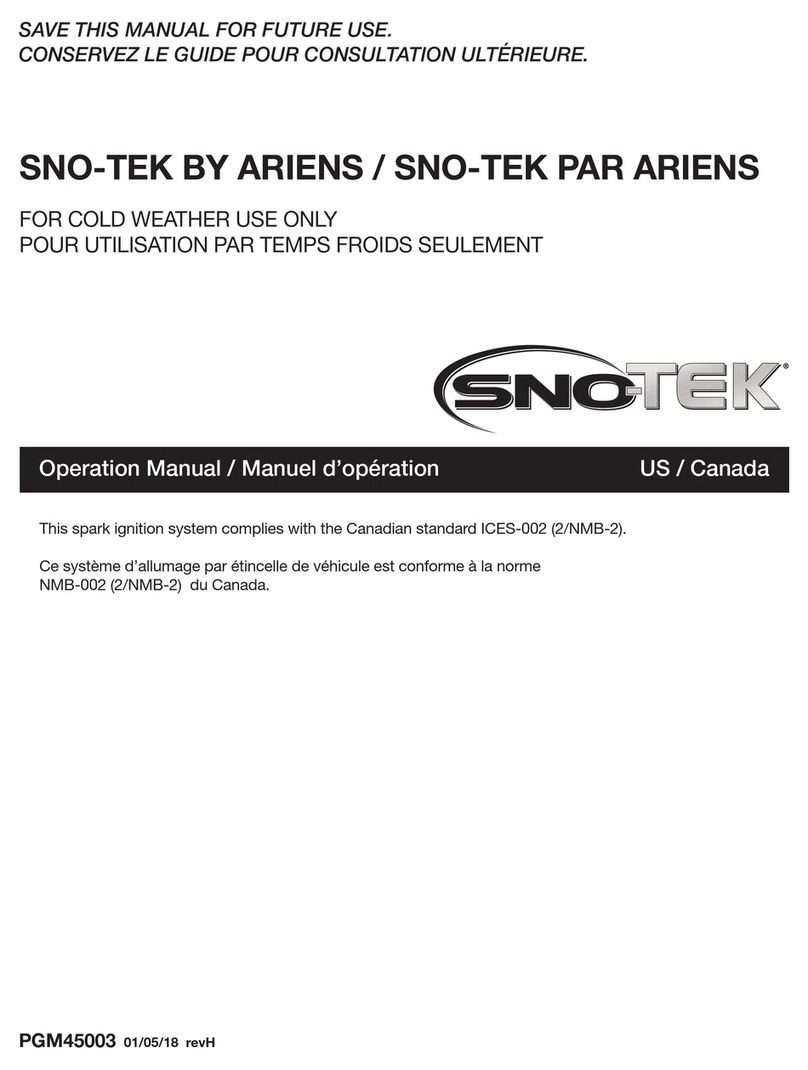
Sno-Tek
Sno-Tek 136cc Operation manual
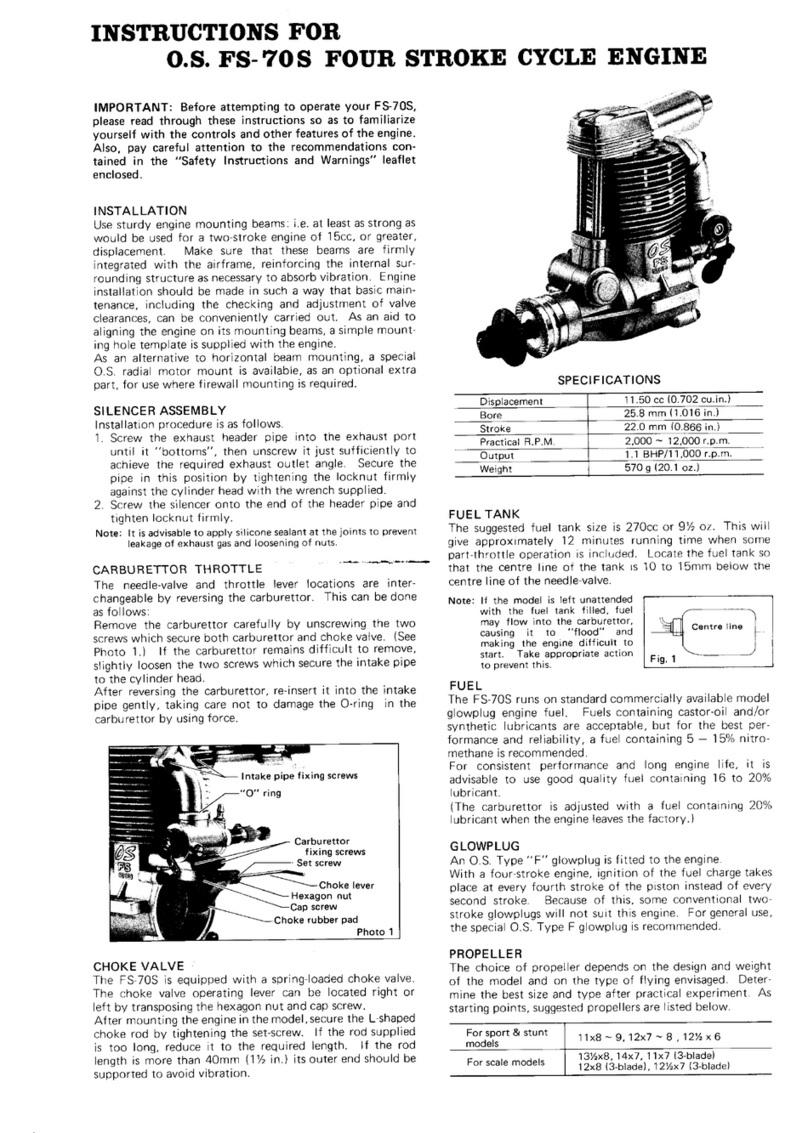
O.S. engine
O.S. engine FS-70S instructions

CHERUBINI
CHERUBINI BLUE TRONIC RX Series instructions