Stober EZ Series User manual

Operating manual
EZ/EZHD/EZHP synchronous servo motors, EZS/EZM synchronous servo motors for screw
drive
105/2019
WE KEEP THINGS MOVING
ID 443032_en.01
en
www.stober.com
These operating instructions contain information about the
transport, installation and commissioning of STOBER EZ,
EZHD, EZHP synchronous servo motors and EZS, EZM syn-
chronous servo motors for screw drive.
For further details, see the catalog with the ID 442437.
In the event of any unclear points, we recommend that you
contact STÖBER with the model designation and serial num-
ber, or have the installation and maintenance work carried out
by a STÖBER service partner.
1 Operation in accordance with its in-
tended use
Synchronous servo motors must be used exclusively for op-
erating machines and systems together with servo inverters.
Stay within the limits defined by the technical data.
Do not use synchronous servo motors in potentially explosive
atmospheres.
For reasons of operational safety, motors may only be used
for the single application for which they were projected.
Any overload on the drives is considered unintended use.
The information and instructions in these operating instruc-
tions must be precisely followed to ensure that claims submit-
ted under the warranty will be honored. If modifications are
made to motors, warranty claims will be rendered void.
Comply with the safety instructions in these operating instruc-
tions and in all supplementary documents for the synchro-
nous servo motor and other components such as gear units
and servo inverters.
2 Technical data
The technical data for synchronous servo motors, geared mo-
tors and servo inverters that are used is indicated on the rel-
evant nameplates.
Acceleration / shock load in operation:
The following value for the shock load indicates the value up
to which the motor can be operated without loss of functional-
ity: 50 m/s² (5 g), 6 ms (maximum value as per DIN EN 60068-
2-27).
Brace the motor connection cable close to the motor so that
vibrations of the cable are not transferred to the motor.
When connecting the motors to drive units such as gear units
or pumps, take into consideration the permissible shock loads
and tilting torques of the units.
Designs: IMB5, IMV1, IMV3
(DIN EN 60034-7)
Protection class: EZ, EZHD: IP56
EZHP: IP56 / IP66 (option)
EZS, EZM: IP40
(DIN EN 60529)
Protection class: I
Thermal class: 155 (F) (DIN EN 60034 / VDE 0530)
155 °C, heating ΔT = 100 K
Surrounding
temperature:
-15 °C to +40 °C (with water cooling +5
°C to +40 °C)
Installation altitude: up to 1000 meters above sea level
Cooling: For IC 410 convection cooling;
or optional IC 416 convection cooling
with forced ventilation (DIN EN 60034-
6), see 2.4.1;
or optionally for water cooling in the A-
side motor flange, see 2.4.2
Surface: Black matte as per RAL 9005
Please note! Repainting will change
the thermal properties and therefore
the performance limits of synchronous
servo motors.
Vibration intensity: as per DIN EN 60034-14 degree N
(half wedge balancing for shafts with
key).
Winding: Three-phase, single-tooth design
Connection
method:
see motor connection diagrams
Information
If brakes are installed, the holding torques may
be reduced by the shock load!

Operating manual
EZ/EZHD/EZHP synchronous servo motors, EZS/EZM synchronous servo motors for screw
drive
2
ID 443032_en.01
WE KEEP THINGS MOVING
05/2019
en
www.stober.com
2.1 Temperature sensor
STOBER synchronous servo motors are equipped with a
PTC thermistor to realize thermal winding protection as stan-
dard. The Pt1000 temperature sensor can be chosen as an
option. The Pt1000 replaces the previously available KTY 84-
130 that is only available for a limited time. The type of in-
stalled temperature sensor is stated on the nameplate of the
motor. Make note of the additional information specified in the
STOBER catalog and in the commissioning instructions for
the drive controller.
CAUTION!
Motor damage, fire risk!
If the winding temperature of the motor is not adequately
monitored, motor damage and fires may result. Claims under
the warranty are then void.
Always connect the installed temperature sensor to an
appropriate triggering unit so that the motor is switched
off if the maximum permitted winding temperature is ex-
ceeded.
You must take precautions to ensure that no hazard could oc-
cur after the thermal winding protection has responded and
the motor has then cooled off by unintentional automatic
switching on of the motor again!
2.1.1 PTC thermistor
The PTC thermistor is designed as a triplet. All three phases
of the motor winding are therefore monitored.
NOTICE
Damage to the PTC thermistor due to high connection
voltage.
Make sure that the maximum connection voltage of the
PTC thermistor is below 7.5 V DC.
2.1.2 Temperature sensor Pt1000
Optionally the temperature-dependent resistor Pt1000 can be
installed as a temperature sensor in one phase of the motor
winding. The resistance of the Pt1000 is proportional to the
temperature of the motor winding.
Make sure that the Pt1000 temperature sensor only protects
the motor to a limited degree before overload. For this reason,
parameterize the I2t monitoring of the drive controller to
"WARNING".
NOTICE
Falsification of the measured value due to self-heating of
the temperature sensor for a sensor current > 4 mA.
Ensure a constant sensor current of 2 mA.
2.1.3 Temperature sensor KTY
Optionally the temperature-dependent resistor KTY 84-130
can be installed as a temperature sensor in one phase of the
motor winding. The resistance of the KTY is proportional to
the temperature of the motor winding.
Make sure that the KTY temperature sensor only protects the
motor to a limited degree before overload. For this reason, pa-
rameterize the I2t monitoring of the drive controller to
"WARNING".
Ensure a constant sensor current of 2 mA.
NOTICE
Damage to the temperature sensor!
Prevent sensor currents > 4mA that can cause unaccept-
ably high self-heating of the temperature sensor as well
as damage to its insulation and at the motor winding.
Pay attention to the polarity of the connections that are
described in the supplied connection plan when connect-
ing the temperature sensor KTY.
Do touch your fingers on the connector contacts of the
motor because the temperature sensor can get damaged
due to electrostatic discharge.
2.2 Encoder systems
Synchronous servo motors have an encoder system integrat-
ed into the motor for motor commutation and recording of po-
sition. Two-pole resolvers are possible as well as absolute
encoders in various versions.
Note the relevant motor connection diagram and the details
on the motor nameplate. The encoder systems have been set
to the respective servo inverters in the factory.
WARNING!
Changes to the factory settings of encoder systems may
result in uncontrolled startup or vibrating movements of
the motor shaft.
Therefore the factory settings must not be changed.
CAUTION!
ESD/EGB safety information
This product contains components that can be damaged or
destroyed by electrostatic discharges.
Always avoid directly touching the pin contacts with your
fingers!

Operating manual
EZ/EZHD/EZHP synchronous servo motors, EZS/EZM synchronous servo motors for screw
drive
305/2019
WE KEEP THINGS MOVING
ID 443032_en.01
en
www.stober.com
2.3 Holding brake (optional)
A brake with permanent magnet excitation can be installed to
serve as a holding brake.
Power supply: 24 VDC ± 5 % smoothed.
The air gap of the brakes cannot be readjusted.
CAUTION!
An incorrect connection can cause the brake and motor
to be destroyed.
Please note when connecting the brake the associated
motor connection plan.
2.3.1 Brakes on gravity-loaded vertical axes
WARNING!
Unintentional lowering or falling of unsecured gravity-
loaded vertical axes can lead to serious personal injuries
or even death!
The holding brake of the motor does not provide ade-
quate safety for person in the hazardous area around
gravity-loaded vertical axes. Therefore the machine man-
ufacturer must take additional measures to minimize
risks (for example by providing a mechanical substruc-
ture for maintenance work).
Check brake functionality for gravity-loaded vertical axes by
performing a cyclic brake test. To do this load the brake with
1.3 times the load torque. Make certain while doing this that
the suspended load of the vertical axis is already exerting
torque on the motor when it is at a standstill. Take this into
consideration when supplying power to the motor.
2.3.2 Testing holding brake
After making the connection check functionality and measure
the holding torque of the holding brake.
Please note, that the brake types are not defined as working
brakes. Therefore braking from full speed during emergency
stops (power failure or dangerous situations) and braking
while setup mode is active are only permitted within the de-
fined limits. For further details refer to catalog SMS-EZ.
To ensure that the brakes receive the full braking torque, they
are ground according to a special grinding cycles after final
assembly of the motors. If a brake is not required to exert any
friction over an extended period of time, the friction factor may
change as a result. This can occur due to accumulations of
flash rust or vapors resulting from the high motor tempera-
ture. Slight material distortion may also occur as a result of
major fluctuations in temperature. All of these factors affect
the braking torque.
If the brake does not exhibit the required braking torque, it
must be reground.
To do this, drive the motor as well at max. 20 rpm. Release
and close the brake once per second so that the motor is re-
quired to work against the closed brake for about 0.7 sec-
onds. After about 20 cycles perform the process in the
reverse direction of rotation. In some circumstances you may
need to perform this process several times until the nominal
holding torque of the brake has been reestablished. If the
braking torque has not been reestablished after the grinding
process is repeated four times, other factors may also be re-
sponsible (for example reaching the wear limit). Options for
automatically integrating a grinding routine, if available, are
described in the documentation for the relevant servo inverter
2.4 Motor cooling
The heat produced while a motor is in operation must be dis-
sipated into the surrounding air as efficiently as possible. Re-
duced heat dissipation is frequently the reason why
temperature monitoring devices respond.
Accumulations of dirt also reduce the performance of the mo-
tor.
Therefore remove dirt that has settled on the surface of the
motor regularly.
2.4.1 Forced-air cooling (optional)
Forced ventilation is optional and can also be retrofitted due
to the modular layout. This makes it possible to optimize
drives subsequently. Technical data can be found in the
nameplate of the motor and in the relevant STOBER catalog.
CAUTION!
Overheating of the motor!
Reduced cooling, for example due to accumulation of dirt or
fan failure, will cause the motor to overheat, thereby resulting
in damage and/or destruction of the winding.
Therefore check the functionality of the external fan
during commissioning and at regular intervals thereafter.
2.4.2 Water cooling (optional)
NOTICE
Material damage!
To prevent damage to the synchronous servo motor or your
machine, please observe the following:
Comply with the coolant specifications described in this
chapter.
The nominal data for synchronous servo motors with wa-
ter cooling refers to water as a coolant. If another coolant
is used, you will have to determine the nominal data
again.
Coolant with fresh water from the public supply grid with
coolants, lubricants or cutting agents from the machining
process is not permitted.
If the temperature of the coolant is lower than the sur-
rounding temperature, interrupt the supply of coolant
when the motor is stopped for extended times to prevent
condensation water from forming.
Information
The brake must only be tested at a motor speed
of max. 20 rpm!

Operating manual
EZ/EZHD/EZHP synchronous servo motors, EZS/EZM synchronous servo motors for screw
drive
4
ID 443032_en.01
WE KEEP THINGS MOVING
05/2019
en
www.stober.com
Cooling circuit specification
2.5 Warning labels on the motor
Warning labels are attached to the motor. Over time, these
warning labels can become dirty or illegible for other reasons.
Keep the warning labels in good, legible condition. Replace
damaged warning labels.
3 Safety information
Also follow the instructions in the operating manuals as well
as applicable national, local and system-specific require-
ments.
WARNING!
- Danger of electrical shock if unpainted parts conducting
voltage are touched.
- Moving and rotating parts can cause injuries
- Touching the gear unit and motor housing may cause
burns (surface temperatures of over 100°C are possible)
The machine manufacturer must provide suitable protec-
tive measures. The connector or terminal box cover of
the motor must remain closed during operation. All work
on the drive must only be performed when no current is
present.
WARNING!
Incorrect operation, improper use, insufficient maintenance or
unauthorized removal of required covers can result in severe
injuries or material damage!
3.1 Personnel requirements
All work on the electrical equipment of the drive units must be
performed by qualified electricians. Installation, maintenance
and repairs of mechanical parts must be performed by fitters,
industrial mechanics or persons with comparable qualifica-
tions.
3.2 In the event of disruptions
Changes compared to normal operation indicate that the
function of the drive has been impaired. This includes:
• Higher power consumption, temperatures or vibrations
• Unusual noises or odors
• Leaks on the gear unit
• Monitoring devices responding
In this case, stop the drive as quickly as possible and contact
STOBER Service.
3.3 Safety during installation and mainte-
nance
NOTICE
Damage to the motor.
Prevent undue force on the motor such as impact, shock,
pressure or high acceleration.
WARNING!
Risk of injury due to moving parts.
The machine manufacturer must provide suitable protec-
tive measures for personnel who must work in the travel
range of a motor within a system or machine, especially
under raised loads.
3.4 Safe function and EMC of the drive
system
The drive controller, cable and motor must be matched to
each other. Each product has specific electrical properties in
and of itself that may affect other products. Unsuitable match-
es can therefore result in impermissibly high voltage peaks on
the motor or drive controller, which could destroy the motor
and cause malfunctions in the system. Legal requirements for
EMC (electromagnetic compatibility) must also be observed.
STÖBER offers a product line of matching cables to ensure
this with suitable shielding technology and cable layout for the
power connection and the various encoder systems.
Using other connection cables and drive controllers may re-
sult in voiding of any claims made under the warranty.
Feature Description
Coolant Water
Temperature at
inlet
+5 °C to +40 °C (max. 5 K below the
surrounding temperature)
Cooling circuit Closed, with recooling unit
Cleanliness Clear, with no suspended matter or dirt
(use particle filter ≤ 100 μm if necessary)
pH value 6.5 – 7.5
Hardness 1.43 – 2.5 mmol/l
Salinity NaCl < 100 ppm, demineralized
Anticorrosive Maximum percentage 25 %,
neutral relative to AlCuMgPb F38, GG-
220HB
Operating
pressure
≤ 3.5 bar (provide a pressure relief valve in
the supply line)
Flow rate EZ4 – EZ5: 6 l/min ( 4.5 l/min)
EZ7 – EZ8: 7.5 l/min ( 5.0 l/min)
Warning of high electrical voltage. Do not
connect or disconnect the plug connectors
until after the motor is de-energized. Only
perform work on the motor when the motor
shaft is at a standstill.
The surface of the motor can reach high
temperatures during operation. Do not touch
the motor during operation or immediately
afterward.

Operating manual
EZ/EZHD/EZHP synchronous servo motors, EZS/EZM synchronous servo motors for screw
drive
505/2019
WE KEEP THINGS MOVING
ID 443032_en.01
en
www.stober.com
3.5 Synchronous servo motors EZHD,
EZHP
NOTICE
The hollow shaft of the motors moves in relation to the
supply elements passing though during operation.
The supply elements must be protected so they do not
scrape against the hollow shaft.
CAUTION!
The hollow shaft can heat up to 100°C in operation.
Observe the temperature for the supply elements that
pass through.
3.6 Servo spindle motors EZS/EZM
WARNING!
Risk of injury due to moving parts!
Check the following before commissioning:
Are the spindle shaft and the motor properly installed in
the machine?
Are no persons at risk by the axial movement of the spin-
dle shaft or slide?
Can no one touch the spindle shaft by coming in physical
contact with it?
WARNING!
Crushing due to contact with the spindle shaft!
Turning the spindle shaft manually with your hand can lead to
crushing injuries.
Never turn the spindle shaft manually.
NOTICE
Destruction of the spindle system!
Removing the spindle shaft from the spindle nut will cause the
system to be destroyed and will void the warranty.
Never remove the spindle shaft from the spindle nut!
CAUTION!
When EZM synchronous servo motors for screw drives
are in operation the spindle shaft moves axially in refer-
ence to the motor.
Fix the spindle shaft in place and install it in the machine.
Screw the motor together with the machine or moving
slide.
Make certain there are no objects in the axial movement
range of the slide or spindle shaft.
4 Transportation and storage
4.1 Transportation
Use the ring screws in the motor housing for vertical transport
of the motors. Sling the motors without ring screw with a suit-
able support cable directly on the gear unit housing. Note that
ring screw are only intended for vertical transport of the mo-
tors without additional attachments. In addition sling the mo-
tor attachments and make sure that there is no diagonal pull.
If the ring screws are removed after assembly, permanently
seal the threaded holes according to the protection class of
the motor.
When transporting the motors make certain not to damage
the shafts and bearings with impacts.
The motors must not be exposed to acceleration levels or
working times of more than 300 m/s² (30 g) as an individual
shock load during transport as per EN 60 068-2-27. The val-
ues for operation apply to long-term shock loads.
Motors with forced-cooling fan
For a motor with a forced-cooling fan, make sure that the mo-
tor is not supported on the cover of the forced-cooling fan or
connected to it.
Motors with water cooling
If you will be storing or transporting the system in which a syn-
chronous servo motor with water cooling is installed below +3
°C, drain the water completely out of the cooling circuit in ad-
vance.
4.2 Storage
The motors may only be stored in enclosed, dry rooms. Stor-
age in open air areas with a roof is only permitted for brief pe-
riods. Protect the motors from all damaging environmental
effects and mechanical damage.
When temporarily storing motors, prevent extreme tempera-
ture fluctuations at high humidity so that no condensation wa-
ter forms.
Long-term storage
If long-term storage is planned, protect motor parts that are
not painted against corrosion. Before placing a motor in oper-
ation again, have the winding checked for its insulation resis-
tance by an electrical specialist.
5 Mounting
NOTICE
The lip seals of the shaft seal rings can be damaged by
the use of solvents.
When removing the corrosion protection, make sure that
the lip seals of the shaft seal rings do not come into con-
tact with solvents.
Completely remove all corrosion protection on the shaft ends
prior to installation.
NOTICE
Damage to the bearing raceway and encoder.
Mount the motor/geared motor correctly without knocking
the shafts or housing.

Operating manual
EZ/EZHD/EZHP synchronous servo motors, EZS/EZM synchronous servo motors for screw
drive
6
ID 443032_en.01
WE KEEP THINGS MOVING
05/2019
en
www.stober.com
5.1 Assembly of the motors/geared mo-
tors EZHD/EZHP
The motors/geared motors can be operated in any installation
position. Mount the motors/geared motors on an even, vibra-
tion-reducing and torsion resistant substructure. Use screws
of strength class 10.9 to fasten.
Fit the motors/geared motors on the pilot.
Make sure that the permitted shear and axial forces are not
exceeded during assembly.
5.2 Assembly of the threaded spindle on
the EZS motor
Tab. 5-1: Assembly information for clamping units
6 Commissioning
Electrical connections provided by the customer must comply
with applicable regulations.
Note:
The electrical connection diagram and safety regulations are
with the delivery documents of the motor. Comply exactly with
the information and safety regulations therein.
WARNING!
If the motor is in operation while plug connectors are
being disconnected, electric arcs can cause severe in-
jury or even death.
Do not connect or disconnect the plug connectors until after
the motor is deenergized.
WARNING!
Risk of injury due to moving parts!
Before switching on the drive, check the following:
Are no persons in danger due to start-up?
Is all protection and safety equipment properly installed,
in test operation too?
Is the drive not blocked?
Are the brakes released?
Is the direction of rotation of the drive correct?
Are components attached to the output such as feather
keys or coupling elements adequately secured against
centrifugal forces?
7 Maintenance
7.1 EZHP synchronous servo geared mo-
tors with hollow shaft
The planetary gear unit of the synchronous servo geared mo-
tor with hollow shaft is provided with life-long lubrication and
does not need maintenance. The specification and filling
quantity of the lubricant is given on the nameplate of the plan-
etary gear unit.
7.2 Servo spindle motors EZS/EZM
Axial angular ball bearings are installed on the A-side in the
EZS and EZM motors that directly absorb the threaded spin-
dle forces. These axial angular ball bearings are greased with
lithium soap grease GA28 at the factory. Under certain appli-
cation conditions, for example after a prolonged downtime or
for high humidity, relubrication may be required. Mineral-
based grease is suitable for relubrication, for example Arca-
nol Multitop.
Protect the threaded spindle against dirt.
8 Troubleshooting
In the event of a malfunction of the drive unit, call the
STÖBER service department at 07231 582-1190 (-1191, -
1224, -1225) in order to locate the nearest STÖBER service
partner for further action.
In urgent cases outside of normal business hours, you
can call the STÖBER 24-hour service hotline at 01805
786323 / 01805 STOEBER
9Spare parts
Include the following when ordering replacement parts:
– item no. of the part according to the replacement parts lis
– model designation according to the rating plate
– serial number according to rating plate
You can reach the STÖBER replacement parts service by
phone: 07231 582-1190 (-1191, -1224, -1225), or fax: 07231
582-1010.
Important notice: The replacement parts lists are not assem-
bly instructions! They are not binding for assembly of the gear
unit. Use only original replacement parts from Stöber. Other-
wise we will provide no guarantee and will assume no liability
for resulting damages!
Mount the threaded spindle on the EZS motor:
1. Degrease the threaded spindle in the area where it
comes into contact with the clamping unit.
2. Insert the threaded spindle through the clamping set in
the hole of the motor shaft.
3. The wrench size and the tightening torque that
corresponds to the size of your EZS motor can be found
in the table Tab. 5-1:
4. Tighten the hexagonal screws of the clamping unit
successively in several tightening sequences (approx. 1/
4 revolution per sequence) properly with a torque
wrench until all of them are tightened to the prescribed
tightening torque. Make sure that both spring washers lie
parallel to each other (maximum permitted deviation 0.2
mm).
EZS5 EZS7
Thread M5 M6
Strength class 8.8 10.9
Wrench size [mm] 8 10
Tightening torque [Nm] 5 12

Operating manual
EZ/EZHD/EZHP synchronous servo motors, EZS/EZM synchronous servo motors for screw
drive
705/2019
WE KEEP THINGS MOVING
ID 443032_en.01
en
www.stober.com
10 Disposal
This product contains recyclable materials. Observe local ap-
plicable regulations for disposal.
This manual suits for next models
10
Table of contents
Other Stober Servo Drive manuals
Popular Servo Drive manuals by other brands
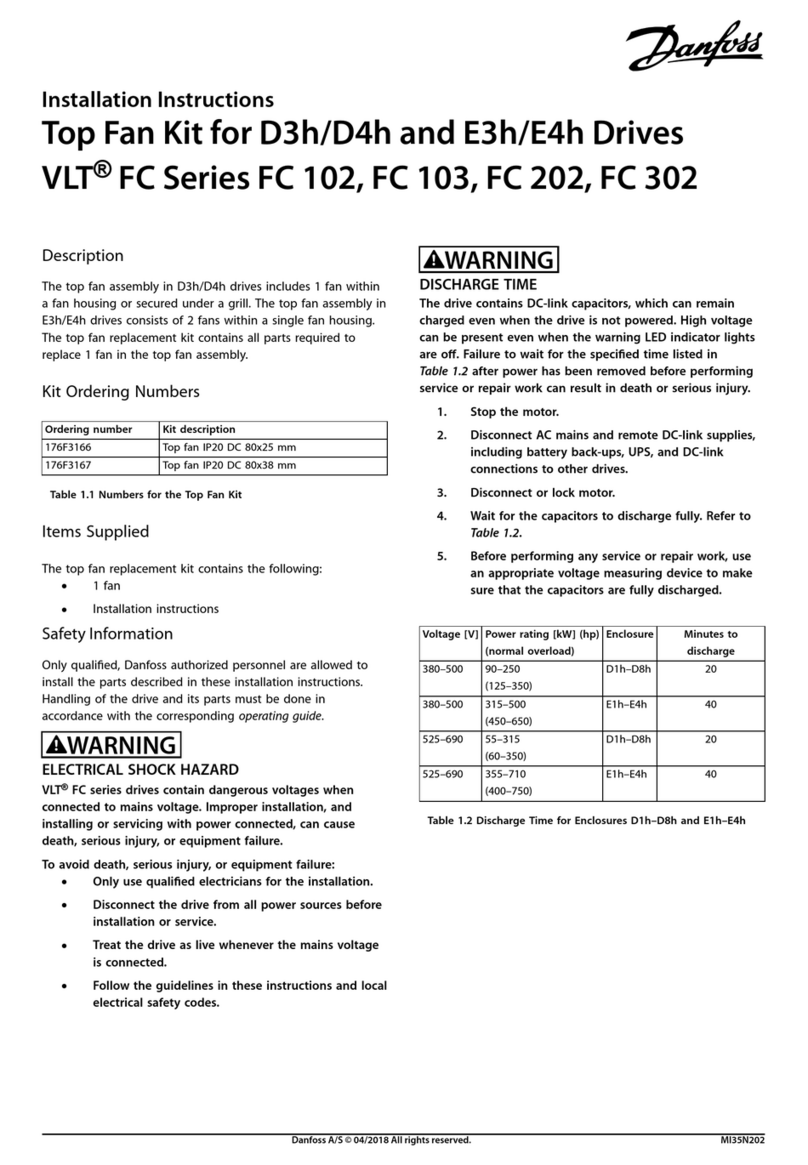
Danfoss
Danfoss 176F3166 installation instructions
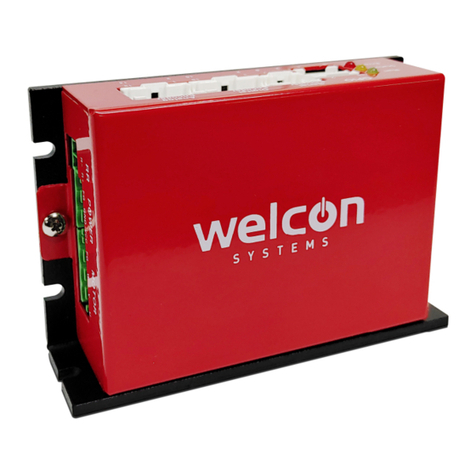
Welcon
Welcon WER-D048-FS00FD Series Hardware manual
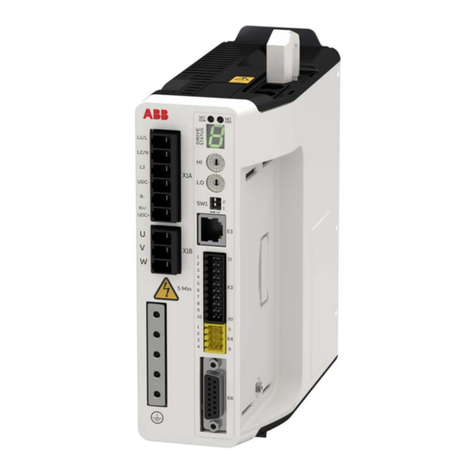
ABB
ABB MicroFlex e190 Quick installation guide

National Instruments
National Instruments NI 9502 Getting started
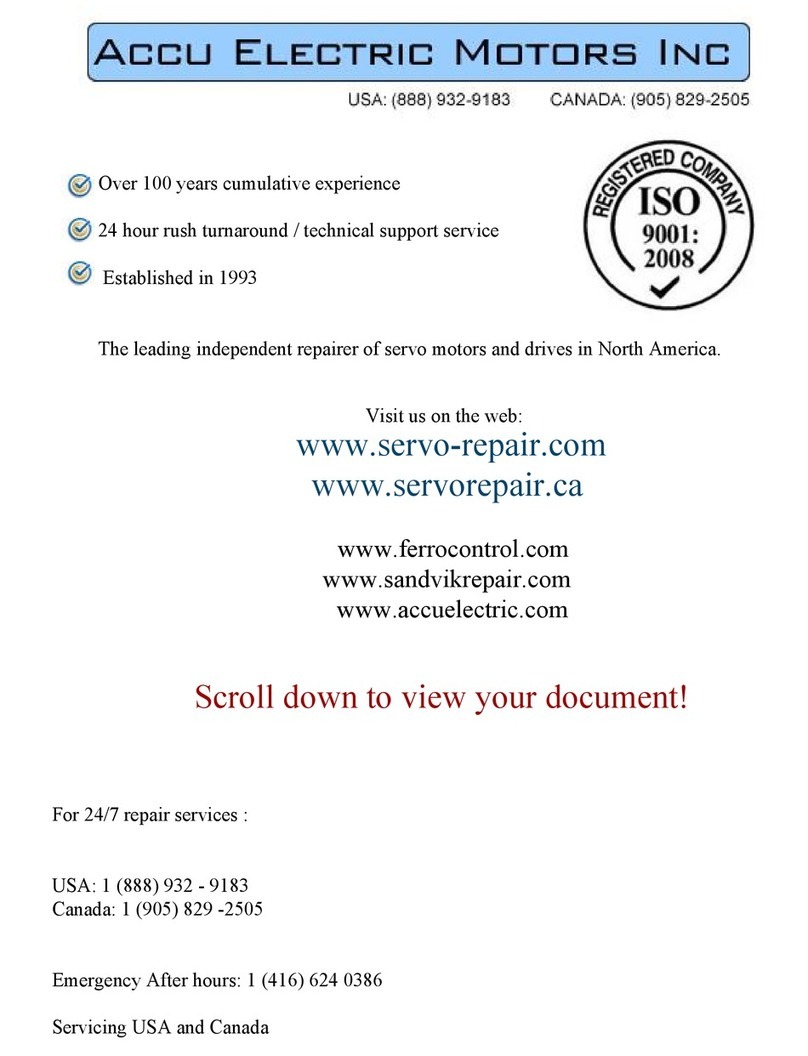
Baldor
Baldor UM Series Installation & operating manual

Astor
Astor Astraada SRV-63 series Operation manual