Stober AX 5000 User manual

Axis switch POSISwitch® AX 5000
Operating manual Commissioning
Connecting
Mounting
V 5.6-E or later
04/2012 en

ID 441689.032
Operating manual Axis switch POSISwitch® AX 5000
WE KEEP THINGS MOVING
Table of contents
Table of contents
1 Introduction . . . . . . . . . . . . . . . . . . . . . . . . . . . . . 4
1.1 Purpose of the manual . . . . . . . . . . . . . . . . . . . . . . . . . . . . . . 4
1.2 Other manuals . . . . . . . . . . . . . . . . . . . . . . . . . . . . . . . . . . . . 4
1.3 Further support . . . . . . . . . . . . . . . . . . . . . . . . . . . . . . . . . . . . 4
2 Notes on Safety. . . . . . . . . . . . . . . . . . . . . . . . . . 5
2.1 Component part of the product . . . . . . . . . . . . . . . . . . . . . . . . 5
2.2 Operation in accordance with its intended use . . . . . . . . . . . . 5
2.3 Qualified personnel . . . . . . . . . . . . . . . . . . . . . . . . . . . . . . . . . 5
2.4 Transportation and storage . . . . . . . . . . . . . . . . . . . . . . . . . . . 6
2.5 Installation and connection . . . . . . . . . . . . . . . . . . . . . . . . . . . 6
2.6 Disposal . . . . . . . . . . . . . . . . . . . . . . . . . . . . . . . . . . . . . . . . . 6
2.7 Presentation of notes on safety. . . . . . . . . . . . . . . . . . . . . . . . 7
3 Technical data . . . . . . . . . . . . . . . . . . . . . . . . . . . 8
3.1 Electrical Data . . . . . . . . . . . . . . . . . . . . . . . . . . . . . . . . . . . . . 8
3.2 Mechanical Data . . . . . . . . . . . . . . . . . . . . . . . . . . . . . . . . . . . 9
4 Mechanical Installation. . . . . . . . . . . . . . . . . . . . 10
4.1 Installation Location . . . . . . . . . . . . . . . . . . . . . . . . . . . . . . . . 10
4.2 Mounting . . . . . . . . . . . . . . . . . . . . . . . . . . . . . . . . . . . . . . . . . 11
5 Electrical installation . . . . . . . . . . . . . . . . . . . . . 12
5.1 EMC Connection. . . . . . . . . . . . . . . . . . . . . . . . . . . . . . . . . . . 12
5.2 Connecting . . . . . . . . . . . . . . . . . . . . . . . . . . . . . . . . . . . . . . . 12
5.2.1 POSISwitch® AX 5000 to MDS 5000/SDS 5000 . . . 12
5.2.2 POSISwitch® AX 5000 to Encoder . . . . . . . . . . . . . 12
5.2.3 Temperature Sensors and Braking Contacts . . . . . . 13
5.2.4 Power and Relays / Contactors . . . . . . . . . . . . . . . . 13
5.2.5 Motors . . . . . . . . . . . . . . . . . . . . . . . . . . . . . . . . . . . 13

Table of contents
ID 441689.03 3
Operating manual Axis switch POSISwitch® AX 5000
WE KEEP THINGS MOVING
6 Terminal Overview . . . . . . . . . . . . . . . . . . . . . . . 14
6.1 Overview of the Terminals. . . . . . . . . . . . . . . . . . . . . . . . . . . . 14
6.2 Terminal Allocation . . . . . . . . . . . . . . . . . . . . . . . . . . . . . . . . . 15
7 Configuration . . . . . . . . . . . . . . . . . . . . . . . . . . . 18
8 Principal Circuit Diagrams . . . . . . . . . . . . . . . . . 21
9 Accessories . . . . . . . . . . . . . . . . . . . . . . . . . . . . 24

Introduction
ID 441689.034
Operating manual Axis switch POSISwitch® AX 5000
1
WE KEEP THINGS MOVING
1Introduction
1.1 Purpose of the manual
These operating instructions describe the use of the axis switch POSISwitch® AX 5000.
1.2 Other manuals
The documentation of the MDS 5000 includes the following manuals:
The documentation of the SDS 5000 includes the following manuals:
1.3 Further support
If you have questions about the technology which have not been answered in this document, please contact:
• Telephone: +49 (0) 7231 582-1187
• E-Mail: applications@stoeber.de
If you have questions about the documentation or training programs, please contact:
• E-Mail: electronics@stoeber.de
Manual Contents ID Latest versiona)
Commissioning Instructions Reinstallation, replacement, function test 442297 V 5.6-E
Projecting manual Installation and connection 442273 V 5.6-E
Operating manual Set up the inverter 442285 V 5.6-E
a) At the time of publication. You can find all versions at www.stoeber.de > Products > Doc Center.
Manual Contents ID Latest versiona)
Commissioning Instructions Reinstallation, replacement, function test 442301 V 5.6-E
Projecting manual Installation and connection 442277 V 5.6-E
Operating manual Set up the inverter 442289 V 5.6-E
a) At the time of publication. You can find all versions at www.stoeber.de > Products > Doc Center.

Notes on Safety
Operating manual Axis switch POSISwitch® AX 5000
5ID 441689.03
WE KEEP THINGS MOVING
2
2 Notes on Safety
The devices may cause risks. For these reasons, comply with the following:
• The safety notes listed in the following sections and points
• The technical rules and regulations.
In addition, always read the appropriate documentation. STÖBER ANTRIEBSTECHNIK GmbH + Co. KG
accepts no liability for damages caused by non-adherence to the instructions or applicable regulations.
Subject to technical changes to improve the devices without prior notice. This documentation is purely a
product description. It does not represent promised properties in the sense of warranty law.
2.1 Component part of the product
The technical documentation is a component part of a product.
• Since the technical documentation contains important information, always keep it handy in the vicinity of
the device until the machine is disposed of.
• If the product is sold, disposed of, or rented out, always include the technical documentation with the
product.
2.2 Operation in accordance with its intended use
The axis switcher POSISwitch Ax 5000 may only be used for the sequential switching of up to four servo
motors at a POSIDRIVE® MDS 5000 or POSIDYN® SDS 5000.
Any other use is not permitted.
2.3 Qualified personnel
Since the devices may harbor residual risks, all configuration, transportation, installation and commissioning
tasks including operation and disposal may only be performed by trained personnel who are aware of the
possible risks.
Personnel must have the qualifications required for the job. The following table lists examples of occupational
qualifications for the jobs:
Activity Possible occupational qualifications
Transportation and storage Worker skilled in storage logistics or comparable
training
Configuration - Graduate engineer (electro-technology or
electrical power technology)
- Technician (m/f) (electro-technology)
Installation and connection Electronics technician (m/f)

Notes on Safety
ID 441689.036
Operating manual Axis switch POSISwitch® AX 5000
2
WE KEEP THINGS MOVING
Tab. 2-1: examples of occupational qualifications
In addition, the valid regulations, the legal requirements, the reference books, this technical documentation
and, in particular, the safety information contained therein must be carefully
•read
• understood and
• complied with
2.4 Transportation and storage
Immediately upon receipt, examine the delivery for any transportation damages. Immediately inform the
transportation company of any damages. If damages are found, do not commission the product. If the device
is not to be installed immediately, store it in a dry, dust-free room. Please see the documentation for how to
commission an inverter after it has been in storage for a year or longer.
2.5 Installation and connection
Installation and connection work are only permitted after the device has been isolated from the power!
2.6 Disposal
Please comply with the latest national and regional regulations! Dispose of the individual parts separately
depending on their nature and currently valid regulations such as, for example:
• Electronic scrap (PCBs)
• Plastic
• Sheet metal
• Copper
•Aluminum
Commissioning
(of a standard application)
- Technician (m/f) (electro-technology)
- Master electro technician (m/f)
Programming Graduate engineer (electro-technology or
electrical power technology)
Operation - Technician (m/f) (electro-technology)
- Master electro technician (m/f)
Disposal Electronics technician (m/f)
Activity Possible occupational qualifications

Notes on Safety
Operating manual Axis switch POSISwitch® AX 5000
7ID 441689.03
WE KEEP THINGS MOVING
2
2.7 Presentation of notes on safety
NOTICE
Notice
means that property damage may occur
Xif the stated precautionary measures are not taken.
CAUTION!
Caution
with warning triangle means that minor injury may occur
Xif the stated precautionary measures are not taken.
WARNING!
Warning
means that there may be a serious danger of death
Xif the stated precautionary measures are not taken.
DANGER!
Danger
means that serious danger of death exists
Xif the stated precautionary measures are not taken.
Information
indicates important information about the product or a highlighted
portion of the documentation which requires special attention.

Technical data
ID 441689.038
Operating manual Axis switch POSISwitch® AX 5000
3
WE KEEP THINGS MOVING
3 Technical data
3.1 Electrical Data
Product key
General data
ID no. 49578
Voltage 24 V +20 % / -15 % (protected against
polarity reversal)
IE
without encoder and contactor <100 mA
with encoder, without contactor < 1 A
Ambient temperature 0 - 45°C
Encoder system EnDat®
EnDat® Port
Input level TIA/EIA 422
Connection, encoder input Sub D 15-pole (STÖBER contact allocation)
Connection, encoder output SUB D 15-pole (STÖBER contact allocation
- see 9 Accessories)
Output level TIA/EIA 422
EnDat® version EnDat® 2.1, EnDat® 2.2
Max. clock pulse frequency 2 MHz
Umschaltzeit < 200 μs
Galvanic isolation EnDat® input to
EnDat® input
No
Galvanic isolationEnDat® input to
24 V supply
500 V
Max. cable length between
POSISwitch® and inverter
80 ma)
a) Only valid in connection with STÖBER cables.
Max. cable length between
POSISwitch® and encoder
20 ma)
Voltage for encoder 5.25 V
Imax for encoder 200 mA
POSISwitch AX 5000
®
Designation 5 generation
th

Technical data
Operating manual Axis switch POSISwitch® AX 5000
9ID 441689.03
WE KEEP THINGS MOVING
3
3.2 Mechanical Data
Specifications in mm.
Power protection
Number of protective connections 4
Max. output current 200 mA
Output voltage min. 22 V at 200 mA
Connection Screw-type terminal (max. 1.5 mm2)
Galvanic isolation to EnDat® Yes
35 Ø 6
10159
179
45
70
6

Mechanical Installation
ID 441689.0310
Operating manual Axis switch POSISwitch® AX 5000
4
WE KEEP THINGS MOVING
4 Mechanical Installation
This chapter gives you complete information on the subject of mechanical installation. Only specialized
personnel qualified for this task may instal, commission and control the device.
4.1 Installation Location
• Operate only in closed switching cabinet.
• Avoid installation above heat-generating devices.
• Ensure sufficient air circulation in the switching cabinet. (The installation site of POSISwitch® AX 5000
may not hinder the air circulation of the inverter).
• The installation site must be free of dust, corrosive fumes and all liquids (in accordance with soil degree
2 as per EN 50178).
• Avoid humidity.
• Avoid condensation (e.g., due to anti-condensation heaters.
• To satisfy EMC requirements, use mounting plates with conductive surfaces (e.g., unpainted).

Mechanical Installation
Operating manual Axis switch POSISwitch® AX 5000
11ID 441689.03
WE KEEP THINGS MOVING
4
4.2 Mounting
approx.
15-20 mm
I
n
v
e
r
t
e
r
I
n
v
e
r
t
e
r
POSISwitch connection cable
Length: 500 mm (Id. no. 45405)
®
Length: 2500 mm (Id. no. 45386)
~
~
~
~
~
~
~
~
Encoder 1...4
E
n
c
o
d
e
r
1
.
.
.
4
159 mm
Drilling jig
Possible arrangement
ESC
I/O
ESC
I/O
max.
8
0
m
1
1
Valid only in connection
with STÖBER cables

Electrical installation
ID 441689.0312
Operating manual Axis switch POSISwitch® AX 5000
5
WE KEEP THINGS MOVING
5 Electrical installation
This chapter gives you complete information on the subject of electrical installation. Only specialized
personnel qualified for this task may install, commission and control the device.
5.1 EMC Connection
• Mount device on conductive surface (unpainted).
• Install motor cable and encoder cable separately from each other.
• Use only shielded cables for motor and encoder lines (corresponding cabels can be ordered from
STÖBER ANTRIEBSTECHNIK).
• Apply shield of the motor cable on both sides.
• The circuit breakers may not interrupt the shield lines.
• Use output derating for motor lines > 50 m.
• When an additional transmission plug connector is installed in the motor cable, the shield may not be
interrupted and the plug connection may not be opened when the motor is electrified.
• When the braking line is installed in the motor cable, the braking line must be shielded separately.
5.2 Connecting
5.2.1 POSISwitch® AX 5000 to MDS 5000/SDS 5000
POSISwitch® AX 5000 is controlled by POSIDRIVE® MDS 5000 or by POSIDYN® SDS 5000. A connection
via socket X4 on the inverter to plug X500 on the AX 5000 enables the switching of the axes. Completely
prefabricated cables are available in the lengths 500 mm (ID no. 45405) and 2500 mm (ID no. 45386). Cf.
chap. 9 Accessories). POSISwitch® AX 5000 is usually installed in the immediate vicinity of the inverter (see
chap. 3.1 Electrical Data and chap. 3.2 Mechanical Data). However, if this is not possible or desirable, a cable
of up to 80 m1in length can be used.
5.2.2 POSISwitch® AX 5000 to Encoder
The encoders of the individual servo motors are connected to POSISwitch® AX 5000 with the STÖBER
encoder cable. The encoder of the first motor is connected with the socket Enc. 1.The encoder of the second
motor is connected with the socket Enc. 2 and so on.
The length of the encoder cable may not exceed 20 m2.
Information
This chapter gives you general information on EMC-suitable
installation. These are only recommendations. Depending on the
application, the ambient conditions and the legal requirements,
measures in addition to the following recommendations may be
necessary.
1 Only valid in connection with STÖBER cables.

Electrical installation
Operating manual Axis switch POSISwitch® AX 5000
13ID 441689.03
WE KEEP THINGS MOVING
5
5.2.3 Temperature Sensors and Braking Contacts
Activation of a halting brake and the evaluation of the temperature sensors on the motors is handled with
braking module for 24 V brake (BRM 5000 for MDS 5000, BRS 5000 for SDS 5000). The brakes or
temperature sensors (positor lines) allocated to the motors are activated and deactivated via auxiliary
contacts of the applicable power relays/contactors. Chap. 8 contains examples of correct wiring.
5.2.4 Power and Relays / Contactors
POSISwitch® AX 5000 is powered with 24 V via the screw-type terminal strip X501 (terminals X501.24V and
X501.0V). Power consumption is a maximum of 1 A. The power relays/contactors are controlled via the AX
5000 on terminals X501.K1 to X501.K4. The contactors are powered via terminals X501.K+ and X501.K-.
Chapter 8 contains examples of correct wiring.
5.2.5 Motors
The motors are activated and deactivated via power relays / contactors. POSISwitch® AX 5000 controls and
checks the power relays/contactors. Chapter 8 contains examples of correct wiring.
Please adhere to the EMC recommendations.
2 Only valid in connection with STÖBER cables.
Information
Use to switch the motor temperature sensor relay contacts for low
currents/voltages (gold contacts).

Terminal Overview
ID 441689.0314
Operating manual Axis switch POSISwitch® AX 5000
6
WE KEEP THINGS MOVING
6 Terminal Overview
This section explains the position, designation and allocation of the terminals.
6.1 Overview of the Terminals
1 X500 Connection for the POSIDRIVE® MDS 5000 or POSIDYN® SDS
5000
2Enc.1
3Enc.2
4Enc.3
5Enc.4
6LED
7 X501 Power and relays
Enc. 1 to Enc. 4: Connection for encoder 1 to encoder 4
1
2
3
4
6
5
7

Terminal Overview
Operating manual Axis switch POSISwitch® AX 5000
15ID 441689.03
WE KEEP THINGS MOVING
6
6.2 Terminal Allocation
This section presents and describes all interfaces.
Terminal description X500 – Connection for MDS 5000 or SDS 5000
Please note that pin 4 is jumpered internally with pin 12.
POSISwitch® cable
Pin Designation Function
plug
1 NC Not connected
2 GND Reference for power supply
3 NC Not connected
4 VCC Power supply 5 VDC
5 DATA Differential input DATA
6 NC Not connected
7 ERROR Differential output ERROR
8 CLK Differential input CLOCK
9 NC Not connected
10 NC Not connected
11 NC Not connected
12 Sense Sense connection
13 /DATA Inverted, diff. input DATA
14 /ERROR Inverted, diff. output ERROR
15 /CLK Inverted, diff. input CLOCK
15
9
8
1
1
9
15
14
13
12
10
11
9
15
14
13
12
10
11
2
3
6
4
7
5
8
1
2
3
6
4
7
5
8
POSISwitch
X500
®

Terminal Overview
ID 441689.0316
Operating manual Axis switch POSISwitch® AX 5000
6
WE KEEP THINGS MOVING
Terminal description X501 – voltage supply and relays
LED
Pin Designation Function Data
+24 VDC Voltage supply —
0 V Reference for 24 V —
PE Protective conductor —
K+ Power for the relays + Potential for powering power
relays/contactors
Umin = 5 V
Umax = 30 V
K- Reference potential for Pin 4 —
K1 OUT Relay output for 1st axis
Imax (24 V) = 0.2 A,
Internal safety circuit with free-
wheeling diode for relay coil.
K2 OUT Relay output for 2nd axis
K3 OUT Relay output for 3rd axis
K4 OUT Relay output for 4th axis
Designation Meaning
ON When the LED is on, the axis switch is supplied with
voltage.
1 When the LED is on, axis 1 is selected.a)
a) When the LED is on, communication is taking place with the encoder of the axis. The
relay output (X501.K1 OUT to X501.K4 OUT) becomes active when the axis is activated
by axis management (device control).
2 When the LED is on, axis 2 is selected.a)
3 When the LED is on, axis 3 is selected.a)
4 When the LED is on, axis 4 is selected.a)

Terminal Overview
Operating manual Axis switch POSISwitch® AX 5000
17ID 441689.03
WE KEEP THINGS MOVING
6
Enc. 1, Enc. 2, Enc.3, Enc. 4 – Connection for encoder 1 - 4
Encoder connection to POSISwitch® AX 5000
Pin Designation Function
socket
1 NC Not connected
2 GND Reference
3 NC Not connected
4 VCC Power supply 5 VDC, jumpered internally with pin 12
5 DATA Differential input DATA
6 NC Not connected
7 NC Not connected
8 CLK Differential output CLOCK
9 NC Not connected
10 NC Not connected
11 NC Not connected
12 Sense Sense connection, jumpered internally with pin 4
13 /DATA Inverted, diff. input DATA
14 NC Not connected
15 /CLK Inverted, diff. output CLOCK
9
15
1
8
Signal Clock+ Sense DATA- DATA+ Clock- UB+ DGND
Enc. 1-4 812 13 515 4 2
Motora)
a) PIN number of 12-pin encoder plug for STÖBER ED/EK motor.
125681210
Cableb)
b) Color when STÖBER encoder cable is used.
yellow pink brown white green red blue
rs rs 2
1
9
15
14
13
12
10
11
2
3
6
4
7
5
8
1
2
3
45
6
7
89
10 12
11
Encoder connection
bracket flange
socket motor
Terminal, enc. 1 to 4
on POSISwitch
®
*
*
*
* Cables twisted in pairs.

Configuration
ID 441689.0318
Operating manual Axis switch POSISwitch® AX 5000
7
WE KEEP THINGS MOVING
7 Configuration
This chapter describes the configuration of POSISwitch® AX 5000. The user decides whether POSISwitch®
will be used in the configuration assistants during the step "inverter selection". An appropriate selection is
offered here (see Fig. 7-1)
Fig. 7-1: POSITool configuration assistants / Umrichterauswahl
For further information on the functionality (e.g., encoder simulation and time behavior), see operating
manuals of the inverter:
• MDS 5000: ID 442285
• SDS 5000: ID 442289
When POSISwitch® AX 5000 configured, the device is adjusted to the application via the following
parameters.

Configuration
Operating manual Axis switch POSISwitch® AX 5000
19ID 441689.03
WE KEEP THINGS MOVING
7
Par. Description Fieldbus-
address
A63
Global,
OFF
r=1, w=1
Axis selector 0 source: There are 2 "axis selector 0/1" signals with which one
of the max. of 4 axes are selected in binary coding. The A63 parameter specifies
where bit 0 for the axis selection is coming from. The possible selections "0:Low"
and "1:High" are the same as fixed values. With A63 = 0:Low, the bit is set
permanently to 0. With A63 =1:High, it is permanently set to 1. With A63= 3:BE1
... 28:BE13-inverted, the axis selection can be made via the selected binary
input. With A63 = 2:Parameter, A180, bit 3 is used as the signal source (global
parameter).
NOTE
• Axis switchover is not possible unless the enable is off and E48 device
control state is not 5:fault.
• With the FDS 5000, the axes can only be used as parameter records for a
motor. The POSISwitch® AX 5000 option cannot be connected.
Value range: 0 ... 0: Low... 28
Fieldbus: 1LSB=1; Type: U8; USS-Addr: 01 0F C0 00 hex
203Fh 0h
A64
Global,
OFF
r=1, w=1
Axis selector 1 source: There are 2 "axis selector 0/1" signals with which one
of the max. of 4 axes are selected in binary coding. The A64 parameter specifies
where bit 0 for the axis selection is coming from. The possible selections "0:Low"
and "1:High" are the same as fixed values. With A64 = 0:Low, the bit is set
permanently to 0. With A64 =1:High, it is permanently set to 1. With A64= 3:BE1
... 28:BE13-inverted, the axis selection can be made via the selected binary
input. With A64 = 2:Parameter, A180, bit 4 is used as the signal source (global
parameter).
NOTE
• Axis switchover is not possible unless the enable is off and E48 device
control state is not 5:fault.
• With the FDS 5000, the axes can only be used as parameter records for a
motor. The POSISwitch® AX 5000 option cannot be connected.
Value range: 0 ... 0: Low ... 28
Fieldbus: 1LSB=1; Type: U8; USS-Addr: 01 10 00 00 hex
2040h 0h
F90
Global
r=2, w=3
Release time axis-switch: Specifies the release time of the contactor used for
the axis switchover. This minimum time is waited before the inverter lets the next
contactor be applied.
Value range in ms:0 ... 20 ... 32767
Fieldbus: 1LSB=1ms; Type: I16; USS-Adr: 06 16 80 00hex
2A5Ah 0h

Configuration
ID 441689.0320
Operating manual Axis switch POSISwitch® AX 5000
7
WE KEEP THINGS MOVING
F91
Global
r=2, w=3
Set time axis-switch: Specifies the set time of the contactor used for the axis
switchover. This time is at least waited before the inverter lets the axis be
electrified.
Value range in ms:0 ... 20 ... 32767
Fieldbus: 1LSB=1ms; Type: I16; USS-Adr: 06 16 C0 00hex
2A5Bh 0h
H08
Axis,
OFF
r=2, w=2
POSISwitch® encoder selector: Available as an option, the POSISwitch®
control module permits the connection of several motors to one inverter. In H08
it can be set separately for each of the four (software) axes which connection on
the POSISwitch® (i.e., which motor) is allocated to the particular axis
configuration. This routine permits two or more applications to be run together on
separate (software) axes with a single motor.
NOTE
Following a change in parameter H08, correct evaluation of the electronic
nameplate is not ensured until after a device new start.
0: Enc1;
1: Enc2;
2: Enc3;
3: Enc4;
Fieldbus: 1LSB=1; Type: U8; USS-Adr: 08 02 00 00hex
Only visible when a POSISwitch® was detected on X4.
2E08h 0h
H18
Global,
OFF
read (2)
POSISwitch® port-status: Indicates as a binary word the POSISwitch® ports
to which encoders are connected. This is determined by the inverter during
startup.
Fieldbus: 1LSB=1; Type: U8; USS-Adr: 08 04 80 00hex
Only visible when a POSISwitch® was detected on X4.
2E12h 0h
U12
Global
r=3, w=3
Level motor connection: When the axis switch via POSISwitch® is utilized, the
inverter can test during switching whether the contactor of the motor to be
switched off has actually broken contact (opened). In addition, under certain
circumstances, it can be determined that no motor is connected.
0: inactive;
3: Fault;
Fieldbus: 1LSB=1; Type: U8; USS-Adr: 15 03 00 00hex
480Ch 0h
Par. Description Fieldbus-
address
Table of contents
Popular Switch manuals by other brands

ASL INTERCOM
ASL INTERCOM LP01 Configuration guide
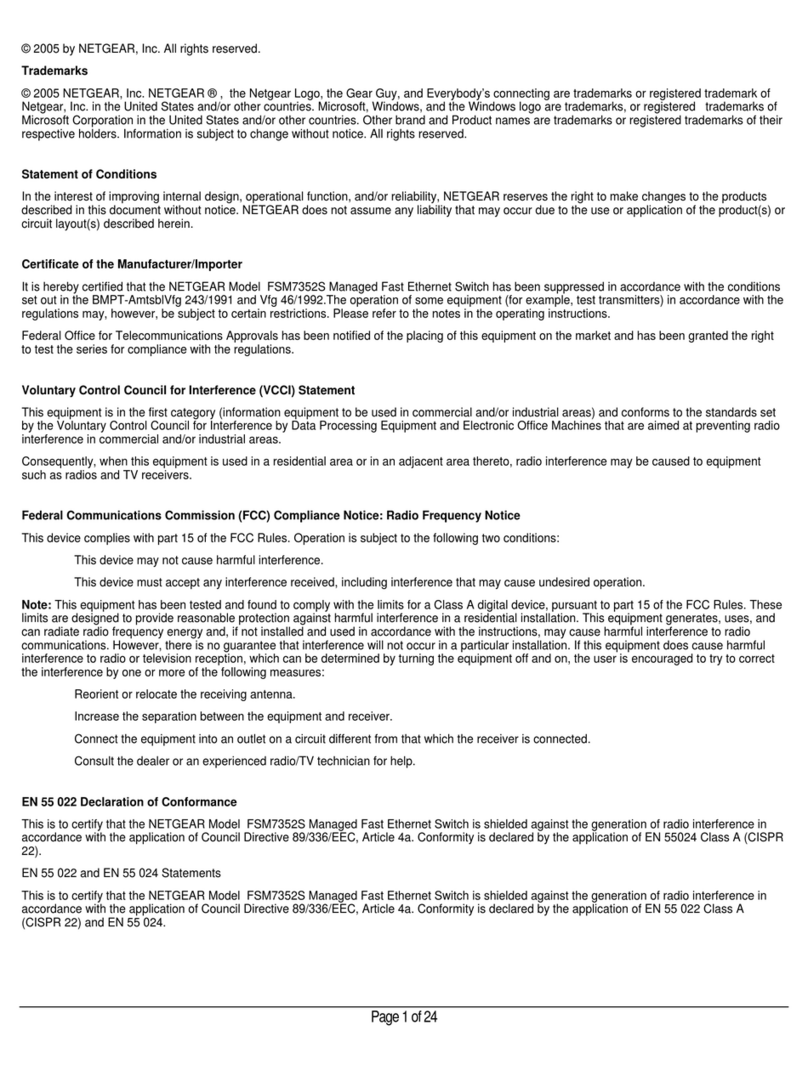
NETGEAR
NETGEAR FSM7352S - ProSafe Switch user manual
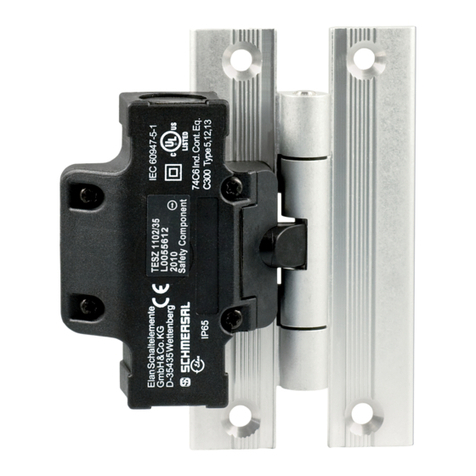
schmersal
schmersal TESZ operating instructions
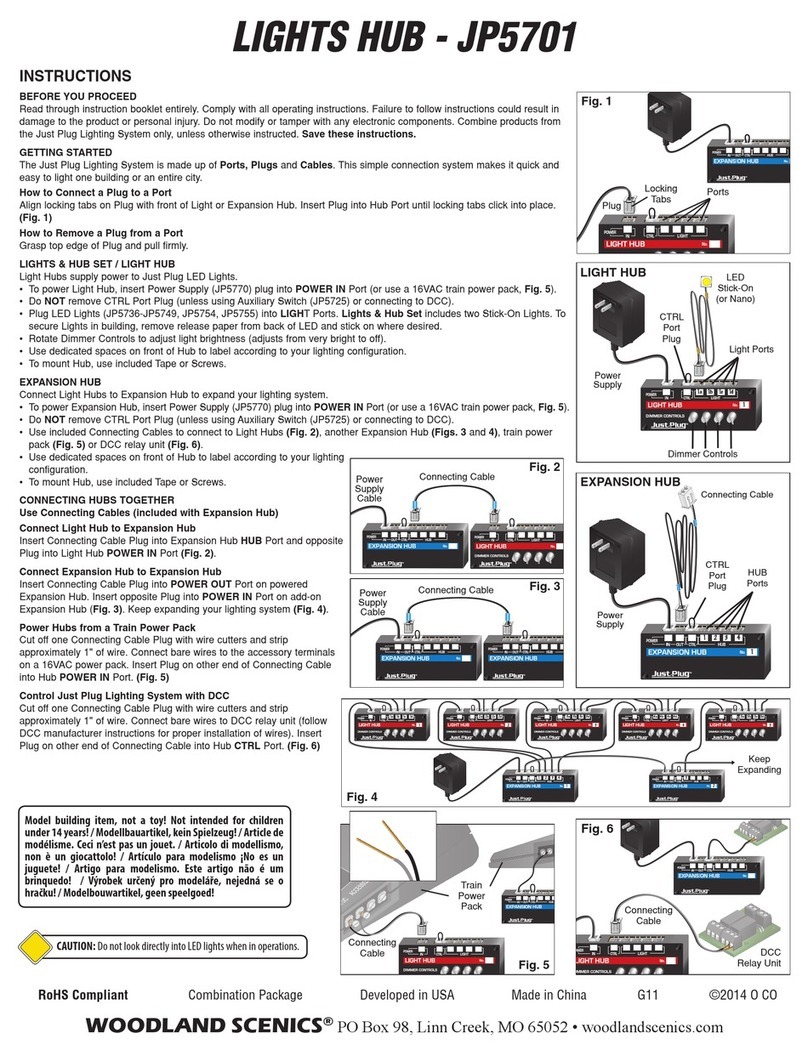
WOODLAND SCENICS
WOODLAND SCENICS JP5701 instructions
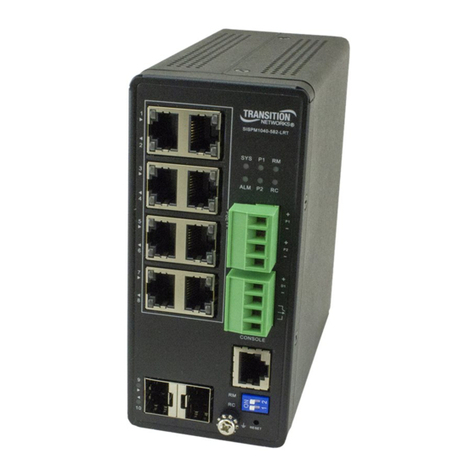
Transition Networks
Transition Networks SISPM1040-582-LRT Cli reference manual
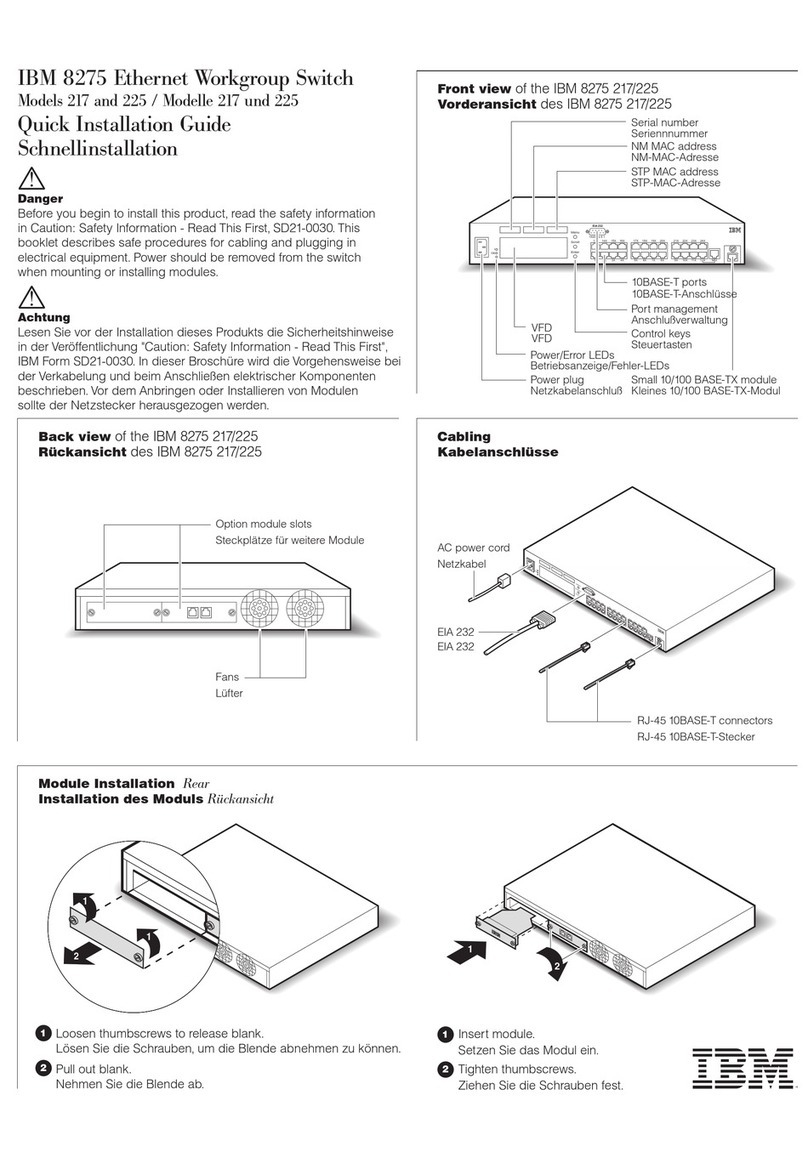
IBM
IBM 8275 217 Quick installation guide