Stroco 15.00 M Operating instructions

SERVICE INSTRUCTIONS
for fuel-burning heater type
STROCO 15.00 M
Applicable from heater no.
12V: 238
24V: 405
STROCO ApS, Viborgvej 50, Voldby, DK-8450 Hammel, ph. +45 86961066, fax +45 86969647
Technical approval no. SP 555 AD 06
EU directive 42/245:
EU technical approval no. E5 10R-03152
Heating directive E 2001/56:
EU technical approval no. R122 E5 00002
ISO certified
Developed with aid from the Danish Environmental Protection Agency
GB 04/18
This manual is also available at www.stroco.dk


IMPORTANT
PAGE 3
The minimum conditions below must be met in order to
maintain the right to claims under the warranty.
1. Installation must be carried out as described in this manual.
2. Service and maintenance must be performed in a proper
professional manner. Maintenance/service must be
performed within the established schedule.
3. Only original spare parts may be used.
4. The heater may only be used for the type of fuel stated on
the model plate.
5. The heater may only be used with the voltage stated on the
model plate.

The heater must not be used in service stations.
The heater must not be used where there is risk of ignition of
flammable vapours and/or materials. Nor where there is risk
of accumulation of toxic gasses, e.g. in closed spaces.
The heater must not be used if the heater or its exhaust
opening is near flammable materials, e.g. dry grass.
IMPORTANT
PAGE 4

CONTENTS
PAGE 5
PAGE:
Description ………………………………………………………………… 6-7
Schematic diagram of fuel-burning heater ………………………………... 7
Built-in dimensions …………………………………………………………. 8
Installation guide/installation plan ...…………………………………... 9-10
List of connections .………………………………………………………… 11
Electrical connections ....…………………………………………………... 12
Technical specifications ………………………………………………... 13-14
Explanation of terminology ..……………………………………………… 14
Maintenance …………………………………………………………….. 15-16
Description of functionality - operation ..………………………………… 17
Description of functionality ..……………………………………………… 18
Troubleshooting - how? …………………………………………………… 19
Dismounting burner and combustion chamber ..………………………... 20
Process control diagram ....………………………………………………... 21
Alarm functionality ....……………………………………………………... 22
Combustion unit .…………………………………………………………... 23
Voltage control of electrodes .……………………………………………... 24
Photoelectric sensor ...……………………………………………………... 25
Under/overvoltage ..………………………………………………………... 26
Replacing the fan motor …………………………………………………... 27
Checking the fuel pump solenoid valve …………………………………... 28
Operating thermostat sensor .……………………………………………... 29
Assembly drawing - parts list ..………………………………………… 30-31
Electrical diagram ……………………………………………………… 32-33
Installation in boats ..…………………………………………………… 34-36
Warranty conditions .……………………………………………………… 37
Dealers .……………………………………………………………………... 38

DESCRIPTION
PAGE 6
It is important to read and understand this manual before using the STROCO heater to ensure
optimum utility and safety. Please mail the warranty card to STROCO ApS.
The presence of the above-mentioned basic elements, in the right quantities and correct mixtures, is
essential to the heat production of the STROCO heater.
In case of failure or unsatisfactory operation, make sure to check these basic elements first.
The STROCO heater is independent of the operation of the vehicle’s engine, and vice versa. This
means that interruptions in one system do not affect the operation of the other. However, lack of
electrical power or fuel will affect both systems, if both engine and heater are connected to the same
battery and fuel tank.
The fuel-burning heater’s job is to heat the water in the heating system. It does this by burning fuel
at a high temperature in the combustion chamber. This heat is transferred to the water in the boiler
section of the heater, and the water is pumped into the heat exchanger units in a continual process,
where the hot water acts as a transfer agent between heat production (the heater) and heat
exchangers.
The heart of the heater is the combustion section. Fuel is pumped to here and vaporized by a nozzle.
This fuel vapour ignites, establishing a flame (combustion). One of the factors that ensure correct
combustion of the fuel vapour is regulation of air intake. The combustion process and other function-
ality of the heater is controlled by the brain of the system: the electronic control and monitoring unit.
This automatic system ensures that the process follows predetermined routines. If the process should
deviate from these routines, or if the combustion process fails or becomes deficient due to poor
supply of the basic elements - fuel, water, and air - the system shuts down the process. In theory, the
presence of the basic elements alone should ensure the combustion process, but since we require the
process to be highly efficient and reliable, it must run in a controlled manner. This manual will help
you to keep the heater running satisfactorily at all times. What to do if the heater is not working, or
performs inadequately?
The section Alarm Functionality can help you to locate the source of an error and analyse the
symptoms.
The section Error Remedy Instructions in the Description of Functionality explains and illustrates
remedial actions.
Fuel
Water
Electrical power
Air
Heat
+=

PAGE 7
Precautionary measures are always better than repairs, and there are a number of Maintenance
Procedures that should be undertaken regularly to ensure the continued working order of the heater.
Please consult the maintenance section. Section 1 in the manual deals with the installation of the
heater, i.e. the actual fitting. The other sections deal with servicing and maintenance exclusively.
Schematic diagram of fuel-burning heater
1: Supply, diesel fuel, 2: Return, diesel fuel, 3: Filter, 4: Exhaust, 5: Engine, 6:Heating system,
7:Control panel

BUILT-IN DIMENSIONS
PAGE 8
All measurements +/- 2 mm.

PAGE 9
INSTALLATION GUIDE/INSTALLATION PLAN
In general: Installation must be performed in accordance with the ECE 2001/56 standard
These instructions apply to STROCO fuel-burning heater, type 15.00 M.
Material and design of fuel hoses/pipes: TA max. -40°C/+120°C.
In case of replacement of hoses, use ONLY hoses from STROCO ApS, or hoses approved by
STROCO ApS. The heater’s warranty will be void if any other hoses are used. Leaky hoses and
joints lead to increased risk of fire.
Non-insulated exhaust pipes/hoses must have at least 7.5 cm to flammable material.
Fuel hoses placed on the outside of the vehicle must be screened to prevent any damage. Electric
cables may not be placed next to fuel hoses.
The fuel-burning heater should be mounted where it is protected from water and spatter from the
vehicle’s wheels, and from impact or other damaging effects. It is very important to clean the sur-
rounding area thoroughly when servicing the unit, and to check all electrical connections and
plugs, greasing with acid-free grease. The area should be kept free of damp. Covers, casings etc.,
must not be removed.
The heater must be positioned in an way that does not impede maintenance work on the heater and
the vehicle’s other components. If necessary, the heater must be placed in a separate box.
Installation must be performed in such a way that heat impact from the vehicle’s engine and ex-
haust system does not damage the heater. Conversely, the vehicle’s components must be protected
against damage from the heater’s exhaust.
Electrical installations for the heater must comply with SEN 3607111 ”Electric installations for
motor vehicles” or similar.
The water system which the heater will be connected to must be fitted with a pressure control valve
for safety.
The heater should be installed in as low a position as possible relative to the vehicle’s cooling/
heating system.
If the heater is installed inside a casing, this must have an air intake opening of at least 75 cm².
(The air intake must not be blocked off). The casing must be made from a non-flammable material.
Intake air for the heater must not come from rooms where there are people. The placement of the
intake must be such that exhaust gas from the vehicle does not mix with the intake air.
The air intake must be placed and designed to avoid clogging by snow or dirt. The air intake must
be placed to keep the airflow around the vehicle from interfering with the pressure in the system.
Place the orifice of the exhaust pipe so that the combustion is not materially affevted by airflows
around the vehicle to prevent heating damage on adjacent vehicle components, and to prevent igni-
tion of grass, etc.
The exhaust pipe must be designed to work with local exhaust ventilation, although not directly
connected, as this can affect combustion.

INSTALLATION GUIDE/INSTALLATION PLAN
PAGE 10
The vehicle must have safety measures to ensure that no exhaust ends up in rooms where there are
people.
The exhaust pipe should be max. 4000 mm in length and should be 65 mm in diameter.
If the heater is mounted in driver, passenger or storage room, this part of the fuel line must be
made from solid-drawn pipe steel. Connection to the fuel supply of the vehicle must be established
outside these rooms.
If the heater is mounted in driver or passenger rooms, the air inlet must be led to fresh air.
The exhaust pipe should be made from a material that resists heat and corrosion
(AISI 304 SS 2333 alloy steel resistant to max. 800°C with at least 0.75 mm wall thickness).
Connections to the exhaust system must be tight and secured with brackets.
If the heater is installed in a cargo area, the exhaust must be made from an unbroken steel pipe.
After installation, the model plate must be accessible and readable.
THE EXHAUST MUST BE ROUTED OUTSIDE OF THE VEHICLE IN HOSE OR PIPE.
There should be adequate room at the combustion end of the heater to remove the combustion unit
and combustion pipe. Minimum distances are shown in the illustration. We recommend mounting the
heater unit on vibration dampers. In this case, the heater connections should be made with flexible
hoses.

LIST OF CONNECTIONS
PAGE 11
Water/fuel connection
Pos 1: Exit for supply water:
3/4” thread
Pos 2: Inlet for fuel supply (to the fuel pump of the heater from the fuel tank):
Connection of fuel hose with 1/4 x 1/4 mm nipple.
Pos 3: Exit for return fuel (to fuel tank):
Fuel hose with 1/4 x 1/4 nipple.
Pos 4: Electric connecteion, 8- and 2-pin connectors.
Pos 5: Inlet for return water:
3/4” thread.
Pos 6: Exhaust:
External dimensions Ø65 mm.

ELECTRICAL CONNECTIONS
PAGE 12
The heater is available in two versions that can be used only for either 24V DC or 12V DC. The
external connections are gathered in 8-pin connectors A and B. The internal connectors of the heater
appears on a separate diagram, see page 32. Connect connectors as follows:
Connector A: Connected to the circulation pump.
Pin B1: Connected to the diagnostic lamp. The other end of the diagnostic lamp is connected
to + (positive) contact. The diagnostic lamp must be a LED.
Pin B2: Connect to - for a low temperature.
Pin B3: Connect through a 10A (at 24V) and 8A (at 12V) fuse to + (positive).
Pin B5: Connect to the room fan relay.
Pin B7: Connect to the main switch or timer. Connect the other end of the switch through an
8A fuse to + (positive).
Pin B8: Connect to frame (negative).
NOTE: The Heater can be set to adjust the temperature within two ranges (see
page 8-9: high/low temperature). Select the low range by connecting wire B2 to frame
point M. Select the NORMAL range by NOT connecting B2.

TECHNICAL SPECIFICATIONS
PAGE 13
Technical data:
STROCO Fuel-burning
heater type 15.00 M: Fuel-burning heater unit with integrated automatic controls and alarm
functions.
Dimensions L x W x H: 409 x 178 x 307 mm
Weight: 17.5 kg
Connections: The fuel-burning heater is connected to the electrical installation, fuel
tank and water/heating system of the vehicle.
Supply voltage: 24 or 12V DC
Fuel: Diesel EN 590
Fuel consumption: approx. 1.25 kg/h
Fuel filter: Filter area: 1937 cm2
Filter degree: 0.02 mm
Connection: 1/4”RG
Heating effect: Output approx. 13 kW
Power consumption: approx. 5A at 24V DC (incl. circulation pump)
9A at 12V DC (incl. circulation pump)
Combustion data: CO2: approx. 10%, Soot figure: 0-1 Bacharach
Circulation pump: approx. 22.5 l/min.
Fuel pump: Operating pressure: 8 bar (kg/cm2)
Nozzle: 1.46 kg/h (0.40 Usgal/h 80°S)
Photo unit: Type LDR
Over boiling protection: Type Therm-o-disce
Breaking temperature 110°C
Control thermostat: NTC 10 K sensor. Boiler temperature:
High: making/breaking approx. 73/80°C
Low: making/breaking approx. 55/60°C
Cab ventilation: Start approx. 50°C/Stop approx. 45°C.
MAX. AMBIENT
TEMPERATURE: 80°C
IMPORTANT! THE HEATER SYSTEM MUST BE FILLED WITH AN ANTI-CORROSIVE
ADDITIVE (E.G. 40-60% ANTI-FREEZE) (SEE ENGINE SPECIFICATIONS).

TECHNICAL SPECIFICATIONS
PAGE 14
Pre-ventilation period: At first start approx. 60 sec.
At restart approx. 10 sec.
Post-ventilation period: approx. 120 sec.
Under voltage: At 24V system:
Connection or disconnection approx. 20.5/22 VDC
At 12V system:
Connection or disconnection approx. 10.5/11.5 VDC
Over voltage: At 24V system:
Connection or disconnection approx. 30/29.5 VDC
At 12V system:
Connection or disconnection approx. 15/14.5 VDC
Safety time: Max. 15 sec.
Contact load: Max. 10 Amp (cabin fan pin B5)
Electrical connection: 15 pin AMP connector (A in electrical diagram)
Explanation of terminology
Low temperature boiler supply water
At low supply water temperatures, the control thermostat cuts out at approx. 60°C and cuts in at
approx. 55°C. This is referred to as the low range in this text.
Please note: Connect cable B2 if the low temperature range is desired.
High temperature boiler supply water
At high supply water temperatures, the control thermostat cuts out at approx. 80°C and cuts in at
approx. 73°C. This is referred to as the high range in this text. This is the temperature range most
commonly used.
Please note: Do not connect cable B2 if the high temperature range is desired.
Overheating protection (max. temperature)
Excessive heating of the boiler water is prevented by means of a circuit breaker in the overtempe-
rature thermostat, which is activated at approx. 110°C. If the circuit is tripped, disconnecting the
electrical system, it must be reactivated manually by pressing the black button on the thermostat.
The system does not restart automatically, even if the water has cooled down again.
Safety period in case of flame failure
If no flame is established, the safety relay switches on the ignition to attempt a restart. If there is still
no flame within the relay’s safety period of 15 seconds, the relay cuts out and the systems starts to
post-ventilate. If the safety relay cuts out, the error lamp comes on.
Pre-ventilation
The heater starts up with a pre-ventilation period of 60 seconds. This period is reduced to 10 seconds
once the heater is in regular operation where start and stop is controlled by the thermostat.

MAINTENANCE
PAGE 15
To ensure reliable operation of the fuel-burning heater, perform the following maintenance
inspections at least once per year, at the end of the heating season, or well ahead of the start of
the season.
General servicing:
Replacement of the fuel filter.
Replacement of the nozzle.
Inspection of motor carbon brushes.
Inspection of pipes and hoses for any leaks. It is particularly important that the heater’s fuel suc-
tion hose has absolutely no leaks. All fuel hoses should be replaced every 2 years. Use only hoses
sourced from STROCO, or hoses approved by STROCO. The heater’s warranty will be void if it is
fitted with hoses not approved by STROCO, or if there is no documentation of replacement of fuel
hoses with 2 year intervals.
Inspection of the boiler and combustion pipe. Removal of any soot or incrustation from the boiler.
Replacement of the combustion pipe if damaged.
Inspection of the combustion unit.
Electrodes, nozzle, and turbolator should be clean and undamaged.
Replacement of the nozzle and subsequent check that the nozzle is centred in the turbolator.
Checking of electrode setting as per page 24.
Improper combustion can lead to boiler or combustion pipe being blackened by soot.
The nozzle service life is limited. Do not attempt to clean or repair the nozzle, but replace it with a
new one.
Inspection of the photoelectric sensor for cracks; cleaning if necessary.
Inspection of the coupling between fan motor and fuel pump; replacement of the coupling if the
contact surfaces are worn.
When the combustion unit is fitted back on the boiler, adjust the fuel pressure to the correct value
and then adjust the air setting to comply with relevant combustion data.
Inspection of all cables and electrical connections for possible damage or corrosion.
Outside the heating season, run the heater for at least 15 min. per week.
IMPORTANT!
When using biofuel, the fuel pump must be replaced every 2 years.
Fuel hoses must be replaced every 2 years regardless of fuel type. Fuel hoses must be replaced with
original STROCO fuel hoses, or approved hoses that meet the same minimum specifications.
It is important that hoses, seals etc. be inspected for leaks continually. Leaky fuel lines present a
serious safety hazard. The warranty on the STROCO fuel-burning heater will be void in case of
deficient or improper servicing.

PAGE 16
Inspection of pump suction
Is there fuel in the tank?
Check vacuum, max. -0.4 bar, connect to port ”V” and check with vacuum gauge
STROCO part no. 13.909.
Are the fuel filter, intake line, or any taps clogged or closed?
Is the fuel very cold and viscous?
Inspection of pump pressure
Check fuel pressure; connect gauge to port ”P”.
Adjust the pressure at port ”P1”; check with pressure gauge STROCO part no. 13.902.
Unsteady gauge readings are a sign of air in the intake line.
For fuel pressure, please consult the technical specifications.
Fuel filter
The filter is located on the fuel intake line between the fuel pump and the fuel tank.
Install the filter so that the arrows correspond to the flow direction.
On replacement, inspect the filter and joints for any leaks.
Circulation pump
The circulation pump transports water in the heating system.
The pump is running continuously while the main switch/start clock is connected and the oil burner
system is running.
The pump is connected to connector A.
Pressure regulation
Intake line G 1/4
Return line G 1/4
Nozzel attachment left G 1/8 (alternatively right)
Pressure gaugeattachment front G 1/8 (alternatively
left)
Vacuum gauge attachment G 1/8
Cartridge filter

DESCRIPTION OF FUNCTIONALITY - OPERATION
PAGE 17
The heater can be started using the main switch on the dashboard. Alternatively, a stating clock can
function as main switch.
The start-up process connects control current from the installation (12V or 24V battery).
The main power supply is connected directly to the heater’s control system, which controls the power
supply to the heater.
The pump relay is activated immediately on start-up to start the circulation pump. The pump runs
constantly when the main switch is activated.
The control thermostat sends a signal to start up the combustion unit when the boiler temperature
drops below the set value.
During the pre-ventilation period, the ignition electrodes (sparks) receive current, the fan motor runs,
and the nozzle pre-heater is engaged.
The fuel pump solenoid valve is switched on approx. 60 seconds after system start-up to release fuel
to be vaporised in the nozzle. The safety timer is engaged at the same time.
Once the flame is established, the nozzle pre-heater and ignition are disengaged. The starting
sequence is now complete, and the combustion unit remains operational until the control thermostat
cuts it off and the ventilation period begins.
When the control thermostat completes the circuit again, the starting sequence repeats with a
pre-ventilation period of 10 seconds.
The control system’s monitoring is focused primarily on the combustion process.
If the fuel does not ignite on start-up, the safety relay remains active. After approx. 10 seconds, the
safety relay disconnects, and post-ventilation begins.
If the flame goes out during operation, the safety relay switches on the ignition to attempt a restart. If
the fuel does not ignite, the safety relay disconnects, the fuel supply stops, and the alarm is activated.
If the fuel does ignite successfully, the combustion process continues until the control thermostat cuts
it off.
The electronic circuit is controlled automatically, so fuel supply stops in case of component failure in
photoelectric or engine circuits. In case of abnormal operating conditions, such as flame failure
during operation or false light during pre-ventilation, the automatic safety system stops the heater
and activates Alarm functions. It is therefore important to install the LED lamp that displays this
alarm from the system within the driver’s field of vision so that potential errors can be detected
quickly.
The control system has an integrated motor voltage regulator, which maintains a constant approx.
21V/11.8V on the fan motor.
The heater’s pre- and post-ventilation and low voltage logic is also controlled by the automatic system.

DESCRIPTION OF FUNCTIONALITY
PAGE 18
1 Nozzle 18 Operation thermostat
2 Nozzle retainer 19 Exit water 3/4“RG
3 Nozzle retainer plate 20 Outer boiler
4 Photo 21 Inner boiler
5 Igniters 22 Copper pins
6 Flange 23 Burner pipes
7 Air shutter 24 Entry water 3/4“RG
8 Fan Wheel 25 Chimney
9 Fan motor 26 Burner
10 Automatic controls 27 Foot
11 Coupling 28 Foot
12 Fuel pump 29 Oli pipes
13 Fuel hose 30 Gasket
14 Fuel hose 31 End cover
15 Ignition coil 32 Plastic cover ABS
16 Ignition oscillator 33 Spiral
17 Over boiling protection

TROUBLESHOOTING - HOW?
PAGE 19
If you initiate troubleshooting because the heater is not working correctly, be sure to note the state
and condition of the unit before and after the fault, if possible, in order identify the problem prior to
repairs.
Is the main switch or starting clock inactive?
Is the operation/diagnostics lamp on?
Does the operation/diagnostics lamp show an error in case of alarm functions?
Have any irregularities with the heater been observed prior to the fault? Any unusual smells,
sounds, of visible changes?
Is there fuel in the tank?
Is there water in the system?
Is the power supply to the heater okay? 24V plug B pin 3, 4, and 7 (see page 32).
Is the air intake unobstructed?
Are the fuses in the electrical circuit intact?
Has the overtemperature control been tripped?
Has the desired temperature range been selected correctly using cable A13? (see page 32)
Before further troubleshooting, note the automatic control of the heater in various sequences.
Certain functionality, e.g. pre-ventilation and ignition, only runs in limited periods.
If the heater stops automatically due to errors, the post-ventilation will run for approx. 120 seconds,
and the diagnostics lamp will come on (see page 23).
Servicing and repairs may only be performed by qualified personnel. Unauthorised tampering
presents a serious safety hazard. The warranty may be void if repairs are attempted by unauthorised
persons.

DISMOUNTING BURNER AND COMBUSTION CHAMBER
PAGE 20
Access to the burner and combustion chamber is obtained by dismounting the end cover
(pos. 31) at the three 6 mm nuts (pos. 29) and the three 6 mm stay bolts (pos. 32).
Dismount the oil pipe (pos. 48) and the connectors (pos. 38).
Remove the burner (pos. 34), and the combustion chamber (pos. 47) is free.
Table of contents
Other Stroco Heater manuals
Popular Heater manuals by other brands
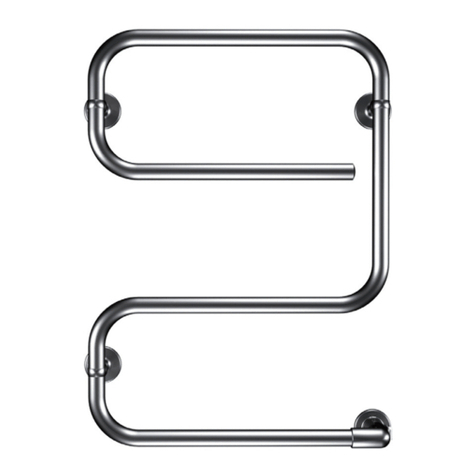
RADSON
RADSON COSMOLEDO E Instruction
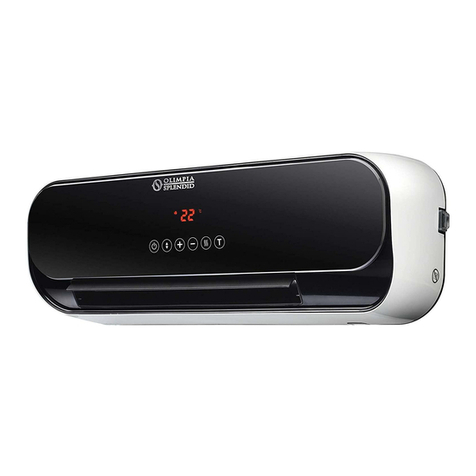
Olimpia splendid
Olimpia splendid CALDO CRYSTAL Instructions for installation, use and maintenance
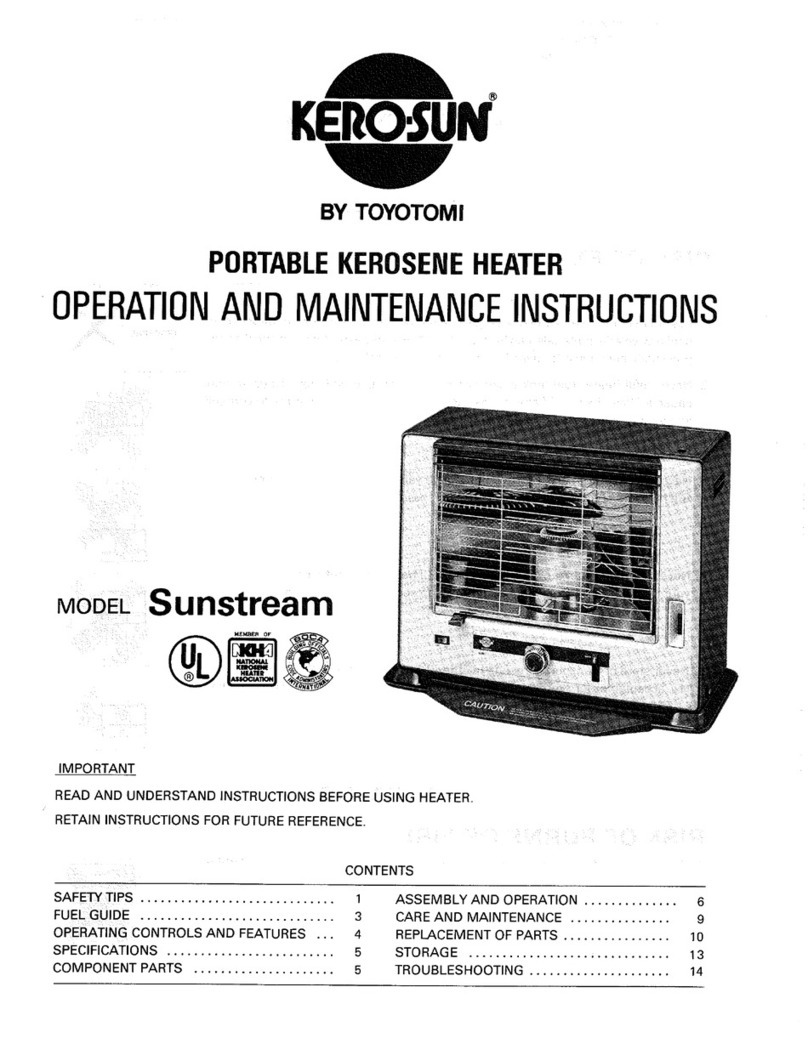
Toyotomi
Toyotomi Sunstream user guide
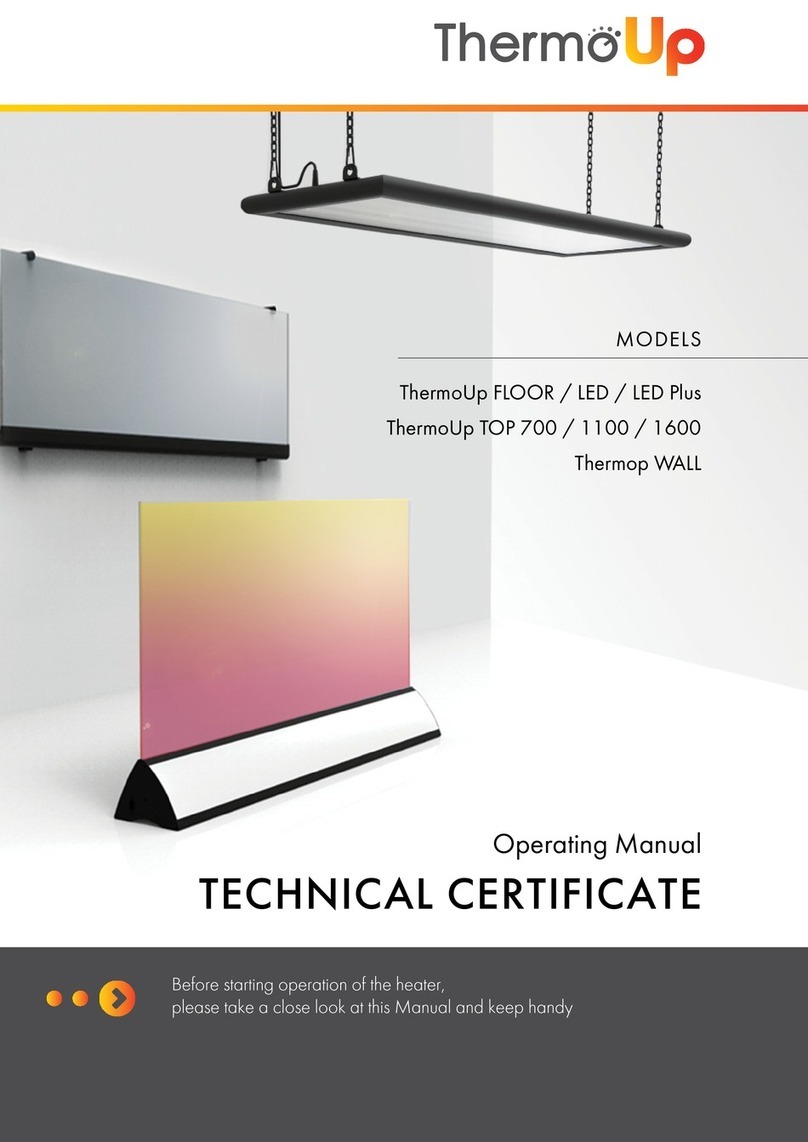
ThermoUp
ThermoUp FLOOR operating manual

TwinStar
TwinStar 7HM1000 Owner's operating manual
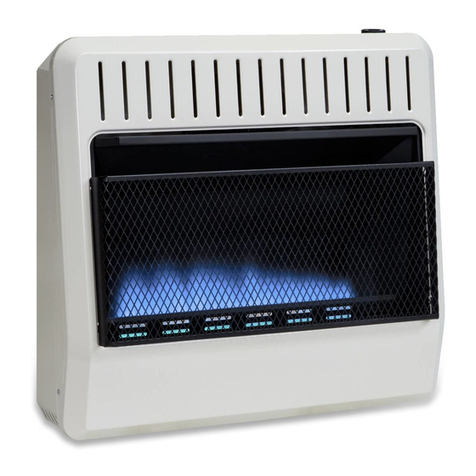
Avenger
Avenger BLUE FLAME FDT1IR BLUE FLAME FDT2IR OWNER'S OPERATION AND INSTALLATION MANUAL