SVS-Vistek CoaxPress EoSens Creation 1.1CXP2 User manual

EoSens® Creation 1.1CXP2
User Guide

Contents
1Before you start 5
1.1 About this manual 5
1.1.1 Tips, remarks, and notes 5
1.1.2 Registered trademarks 5
1.1.3 Conformity and use 5
1.1.4 Supplements 6
1.2 Warranty and non-warranty clause 7
1.3 Support 7
2Introduction 8
2.1 Intended use 8
2.2 Scope of delivery 8
2.3 Optional accessories 8
2.4 System requirements 9
3The camera 10
3.1 Camera description 10
3.2 Operating temperature 11
3.3 Additional cooling 11
3.4 Interfaces of the camera 12
3.5 Status LED 13
4First steps 14
4.1 Connecting a frame grabber 14
4.2 Connecting an external power supply or I/O signals 15
4.3 Connecting camera and image processing system 17
4.4 The power-up profile 17
4.5 Cleaning sensor and lens 18
4.6 Updating the camera firmware 18
5Technical data 20
5.1 Camera specifications 20
5.2 Sensor specifications 21
5.3 Resolution and frame rates 21
2

Figures
Fig.: 3-1: Interfaces of the camera EoSens® Creation 1.1CXP2 12
Fig.: 4-1: Connecting input and output signals with the internal circuit 16
Fig.: 4-2: IO signals 16
Fig.: 4-3: Connecting the camera and image processing system 17
Fig.: 5-1: Rear view (fanless) 22
Fig.: 5-2: Side view (fanless) with C-mount adapter 22
Fig.: 5-3: Side view (fanless) with F-mount adapter 23
Fig.: 5-4: Side view (fanless) with G-mount adapter 23
Fig.: 5-5: Rear view (with fan) 24
Fig.: 5-6: Side view (with fan) with C-mount adapter 24
Fig.: 5-7: Side view (with fan) with F-mount adapter 25
Fig.: 5-8: Side view (with fan) with G-mount adapter 25
Fig.: 5-9: Spectral response - monochrome 26
Fig.: 5-10: Spectral response - color 26
4

1 Before you start
1.1 About this manual
This manual contains helpful information to install and operate the described cam-
era. It has been produced with care. Nevertheless, information might be erroneous or
incomplete. Mikrotron GmbH cannot be held responsible for any problems resulting
from incomplete or erroneous information.
In case you detect errors or need further information, please inform us via mail:
Call +49- 89-7263-4200
We highly recommend to read this manual carefully.
NOTICE This manual is subject to change without notice.
It is intended for staff with technical qualifications who have been specially trained
and have the appropriate knowledge in the field of automation technology, electrical
and optical devices.
INFO Keep this manual for future use.
1.1.1 Tips, remarks, and notes
This manual contains tips and notes that help to avoid data loss or camera damage.
They are emphasized as follows:
INFO Provides information that may help to improve camera handling or avoid data loss.
NOTICE Provides information to avoid damage to the system.
1.1.2 Registered trademarks
In this manual the following registered trademarks may be used:
lMotionBLITZ®
lImageBLITZ®
lEoSens®
lGenICam®
lMicrosoft® and Windows®
lIntel®
Throughout the manual, these trademarks are not specifically marked as registered
trademarks. This in no way implies that these trademarks can be used in another con-
text without the trademark sign.
1.1.3 Conformity and use
This equipment has been tested and found to comply with the limits for a Class A
digital device, pursuant to Part 15 of the FCC Rules. These requirements are
designed to provide reasonable protection against harmful interference when the
equipment is operated in a commercial environment.
1 Before you start 5

This equipment generates, uses, and can radiate radio frequency energy and, if not
installed and used in accordance with the instructions given in this guide, may cause
harmful interference to radio communications. Operation of this equipment in a res-
idential area is likely to cause harmful interference in which case the user will have to
correct the interference at its own expense.
NOTICE You are herewith cautioned that any changes or modifications not expressly
approved in this description could void your authority to operate this equipment.
制造说明:
此设备的生产与测试依照FCC条例第15条条例,符合A类电子设备标准。产品提
供在商用使用环境中的合理保护,以防止使用过程中可能涉及到的损害。
此设备会产生、使用并可发射出无线电波,如果未按照本手册中所述安装和使
用,可能会对无线通信设备产生干扰。如本设备在居民区操作出现干扰等情
况,用户需要自费处理。
备注:请注意,如未按照此使用说明操作而自行更改设备,那么您将无权使用
本设备。
規制適合宣言とご使用について(米国FCC)
この機器は、FCC規則 のパート15に定められたクラスAデジタル装置に関する規制
要件に基づいて所定の試験が実施され、その適合が認証されています。これらの
規制要件は、商業環 境 において機 器 を使 用 する際、有害な干渉に対する妥当
な保 護 を提 供 するために設けられています。この機器は、無線周波数エネルギー
を生成かつ利用するとともに、放射することもあります。このリファレンスガイドの指
示に従って設置および使 用 が行われない場合は、無線通信に有害な干渉を引き
起こす恐れがあります。この機器を住宅地で利 用 すると有害な干渉を起こすこと
もあり、その場 合 、使用者は自己負担において適切な対 策 を講 じる必要がありま
す。
注意事項:このリファレンスガイドに明示的に承認していない変更や修正を行った
場合には、本製品を使用する権利が無効となることがあります。
1.1.4 Supplements
For customers in Canada
This apparatus complies with the Class A limits for radio noise emissions set out in
Radio Interference Regulations.
Pour les utilisateurs au Canada
Cet appareil est conforme aux normes Classe A pour bruits radioélectriques, spé-
cifiées dans le Règlement sur le brouillage radioélectrique.
1 Before you start 6

Life support applications
The products described in this manual are not designed for use in life support appli-
ances or devices and systems where malfunction of these products can reasonably be
expected to result in personal injury.
NOTICE Mikrotron customers using or selling these products for use in such applications do
so at their own risk and agree to fully indemnify Mikrotron for any damages res-
ulting from such improper use or sale.
1.2 Warranty and non-warranty clause
Warranty is described in §8 of our General Terms and Conditions which can be
downloaded on the Mikrotron web page (www.mikrotron.de/en/terms.html).
In addition, take the following non-warranty clauses into account.
NOTICE The camera does not contain serviceable parts. Do not open the body of the cam-
era. If the camera has been opened, the warranty will be void.
NOTICE The camera has to be used with a supply voltage according to the camera’s spe-
cification. Connecting a lower or higher supply voltage, AC voltage, reversal polar-
ity or using wrong pins of the power connector may damage the camera. Doing so
will void warranty.
Our warranty does not protect against accidental damage, loss, or acts of nature.
INFO Mikrotron cannot be held responsible for the loss of data. We recommend a backup
plan.
1.3 Support
1. In case of support or a warranty claim, make a note of the camera type and its
serial number (S/N). You find all necessary information on the identification
plate of the camera.
2. Contact us in one of the following ways:
oContact us via email: [email protected]. Our support team will guide
you through the process.
oOr visit our support website
www.mikrotron.de/en/services/support.html
and fill out the form. You will receive an automatic reply from our ticket sys-
tem.
1 Before you start 7

2 Introduction
2.1 Intended use
The camera EoSens® Creation 1.1CXP2 belongs to the product class of so-called
high-speed machine vision (MV) cameras that are integrated into test or meas-
urement systems.
High-speed MV cameras are designed to capture images with high frame rate for
various purposes in an industrial or scientific environment to deliver image data for
further analysis. The images are transmitted to a frame grabber on a connected com-
puter where they can be evaluated with the help of a software.
Other uses
Any other use is regarded as unintended use and leads to the loss of guarantee and
liabilities. Contact the manufacturer for other uses.
These products are designed for industrial applications only. The cameras are not
designed for life support systems where malfunction of the products might result in
any risk of personal harm or injury.
2.2 Scope of delivery
The following components are part of delivery. Before installing the camera, check if
the delivery is complete:
lCamera as ordered
lF-mount or C-mount lens adapter - as ordered
lUSB storage device with
oGenICam XML file
oProduct documentation
NOTICE Check if the delivery is complete before installing the camera.
INFO The firmware can be updated remotely via a special updating software. For firmware
2.3 Optional accessories
Lenses
Only lenses for industrial purpose are suitable. To find lenses or other accessories,
visit www.mikrotron.de/en.
Cables
For connecting the camera, the following cable must be used.
lCable CXP 12GHz µBNC RG59 (1x) - 5m
2 Introduction 8

We recommend the following cable:
lKKRDRG59UBNCUBNC05/12GX1 (12GHz µBNC RG59) - 5m
Power supply
If you do not use power over CXP, you need an external power supply unit, e.g.:
lNTCAM132X (12 V/2.5A) with 12 pin Hirose connector (HR10A-10P-12S(73)
and 5m cable
lNTCAM132XIO (12 V/2.5 A) with 12 pin Hirose connector (HR10A-10P-12S
(73) and 5 m cable plus additional strobe out line
2.4 System requirements
The PC or image processing system that is connected with the camera must be
equipped with:
lAn image processing system, e.g.: PC and operating system according to the
requirements of the frame grabber
lA fully installed frame grabber with device driver and software
lCoaXPress cable with µBNC connector
lOptional external power supply (NTCAM132X/NTCAM132XIO)
NOTICE To make use of the full performance, all cables, connectors and the frame grabber
must be CoaXPress V2.0 compliant.
INFO If a CXP V1.1 frame grabber is used, only speeds up to CXP-6 (6.25 Gb/s) can be
achieved.
2 Introduction 9

3 The camera
3.1 Camera description
All cameras of the EoSens CXP family are CoaXPress compliant. The high-speed
CMOS cameras come with a 1.1Megapixel sensor of 1280 x 864 (H x V). They are
widely configurable and scalable to fit your needs and are available in monochrome
and color (Bayer filter).
The CoaXPress high speed interface technology allows transfer rates of up to 12.5
Gb/s per channel. The camera supports CoaXPress Link Speeds from 3.125 Gb/s to
12.5 Gb/s at 1, 2, or 4 channels.
In addition the camera offers a very high frame rate of over 3660fps at full res-
olution. By defining a Region of Interest (ROI) the frame rate can be increased to sev-
eral thousand frames per second. An important feature of CXP cameras is the high
photo sensitivity for low-light conditions.
The camera electronic is enclosed in a compact and solid full metal housing robust
enough to comply with the requirements in heavy industrial surroundings. Shielded
coaxial cables as recommended by the CoaXPress standard will support this.
CXP cameras can be equipped with standard C-mount or F-mount lenses made for
industrial purpose.
The color and monochrome cameras are supplied with the following features:
lAnalog/digital gain
lBlack level adjustment
lFPN correction
lImage information field
lLookup table (LUT)
lTest images
lUser profiles
Bayer filter
The sensor of the EoSens color cameras is supplied with a Bayer color filter. In order
to get the color information, the imaging software has to decode the information of
each pixel into red, green, and blue (RGB) by using the values of its neighboring
pixels. Each red, green and blue filter element covers exactly one pixel on the sensor.
A matrix of 2x2 filter elements builds a filter element matrix. A Bayer pattern image
therefore must have an even number of pixels and an even number of lines. The
ordering of the RGB pixels for each sensor is provided in the section on technical
data.
UV/IR cut filter
In addition, color cameras are equipped with an UV/IR cut filter. Light with
wavelengths between 370nm and 670nm will be transmitted. As CMOS sensors are
susceptible to UV and IR rays outside the visible spectrum, UV/IR filter avoid blurred
images and therefore improve color images.
3 The camera 10

3.2 Operating temperature
If the camera is mounted on mechanical parts, the heat generated during operation
will be dissipated by the optionally attached fan, the cooling fins at the rear of the
camera, and the mechanical parts.
NOTICE The camera body temperature must not exceed the values specified in the technical
data (see "Technical data" on page20).
In case of overheating, the camera will automatically be switched off and the com-
munication between camera and PC will be interrupted.
INFO Durability of the camera will be reduced when being operated in an environment
that is constantly exceeding the maximum permissible operating temperature. In this
case, take additional cooling measures as described below.
NOTICE The camera is not intended for use on an isolated mounting plate or in a closed
housing because the temperature of the camera will rise continuously.
3.3 Additional cooling
INFO If the camera is e.g. mounted on a sturdy aluminum structure, not only cooling is
ensured but also a stable optical path. In addition, vibrations will be minimized
within the entire system.
If the ambient temperature is constantly exceeding 40°C, additional cooling is recom-
mended. This can be achieved by
lAir- or water-cooling system
lAir-conditioned housings
3 The camera 11

3.4 Interfaces of the camera
1
2
3
Fig.: 3-1: Interfaces of the camera EoSens® Creation 1.1CXP2
1Status LED
to verify the operating status of the camera
2Four CoaXPress µBNC connectors
to connect the camera with a CoaXPress compliant frame grabber. The ∆-
marked line can supply the camera with power via power over coax (PoC).
312 pin Hirose power connector
used when an external power supply (12 … 24 V) has to be connected, an
external trigger is connected and / or an output signal is used.
3 The camera 12

3.5 Status LED
The multi-color status LED indicates camera and connection states.
LED State Indication
OFF No power
Solid orange System is booting
Slow pulse red Powered, but nothing connected
(not applicable if PoC is used)
Fast flash alternate
green/orange
Connection detection in progress, PoC active
Fast flash orange Connection detection in progress, PoC not in use
Slow flash alternate
red/green
Device incompatible, PoC active
Slow flash alternate
red/orange
Device incompatible, PoC not in use
Solid green Device connected but no data being transferred
Slow pulse orange Device connected, waiting for event (e.g. trigger)
Fast flash green Device connected, data being transferred
Slow flash alternate
green/orange
Connection test packets being sent
Red - 500 ms pulse Error during data transfer
Slow flash alternate
red/green/orange
Compliance test mode enabled
Fast flash red System error
3 The camera 13

4 First steps
4.1 Connecting a frame grabber
The transmission speed of the camera can either be set to 3.125, 6.25, or 12.5
Gb/s. The possible cable length depends on the cable type used, its quality, and the
selected transmission speed. The following table provides examples. These values will
only be reached if the signal quality meets the requirements of the CXP2.0 spe-
cification.
INFO The maximal cable length depends also on the quality of the cables. We recom-
mend CXP cables from Mikrotron.
CXP-Type Transmission speed [Gb/s] Max. cable length RG59 style [m]
CXP-3 3.125 up to 100
CXP-6 6.25 up to 40
CXP-12 12.5 up to 30
NOTICE All lines have to be of the same length.
µBNC connector
Mikrotron offers cables with the following connectors:
lµBNC çèµBNC (cable KKRDxxx)
NOTICE Carefully connect and release the socket with the connector. Connect them pre-
cisely to avoid deformation of the connectors or other damages!
If connecting individual cables, keep the order on camera side starting at from ∆-
marked link one to channel one on the frame grabber.
INFO Pin 1 always has to be connected.
The master connector (1) is marked by a triangle. Connect it with channel one of the
frame grabber (refer to the frame grabber documentation).
1
2
3
4
4 First steps 14

The possible connector combinations are shown in the table below.
No. of con-
nections Connector combination
11
21+2 (link)
41+2+3+4 (link)
INFO All connections are hot-pluggable.
4.2 Connecting an external power supply or I/O signals
If you prefer an external 12 - 24V DC power supply (min. 18 W), connect it with the
12-pin connector at the rear of the camera.
NOTICE The power connector of the camera has to be connected with a DC power supply
providing 12 to 24 V DC. Connecting a lower or higher supply voltage, an AC
voltage, reversal polarity or using wrong pins of the power connector may damage
the camera and will void warranty!
Mikrotron offers the power supply unit NTCAM132xx with cables of 5 or 10 meters.
INFO If you assemble your own cable, pay attention to the pinning described below.
12-pin connector and I/O signals
1. Connect the external power supply with the 12-pin connector of the camera.
NOTICE The DC power supply must deliver 12-24V DC (18.4 W). It must be equipped with
a HR-10A-10P-12S plug.
The 12-pin connector provides two inputs for an external trigger and two output sig-
nals. The output signal can be controlled.
Pin Signal Pin Signal
1
2
3
4
5
6
7
8
9
10
11 12
1 + 12 GND 6 IN0
2 + 11 VCC
(12 - 24 V)
7 IOGND
3 IOGND 8 OUT1
4 OUT0 9 IOGND
5 IOGND 10 IN1
4 First steps 15

connected with pin 3 + 5
pin 4
pin 6
Internally connected with:
pin 10
pin 8
Fig.: 4-1: Connecting input and output signals with the internal circuit
All inputs accept 3.3V LVTTL signals. They are also 5 V TTL compatible.
All inputs can also accept signals with 12V and 24V.
NOTICE An open (not connected) input will be interpreted as high level from the camera. For
low level an input voltage of 0 - 0.3V must be connected.
Fig.: 4-2: IO signals
If the available external signal cannot deliver a low level voltage <0.3V or the input
signal is >24V, the following transistor circuit can be used. A suitable transistor is for
example BC547, or 2N2222.
NOTICE This circuit will invert the signal. (A high level at the input will be seen as low level at
the camera.)
Examples for R1
Input voltage Resistor
3.3V 2.7 kOhm
5 V 4.7 kOhm
12V 12 kOhm
24V 22 kOhm
4 First steps 16

4.3 Connecting camera and image processing system
NOTICE To make use of the full performance, all cables, connectors and the frame grabber
must be CoaXPress V2.0 compliant.
INFO If a CXP V1.1 frame grabber is used, only speeds up to CXP-6 (6.25 Gb/s) can be
achieved.
1
2
3
4
5
6
7
Fig.: 4-3: Connecting the camera and image processing system
1. Install the frame grabber software on the image processing system (see doc-
umentation of frame grabber board).
2. Switch off the image processing system (1).
3. Unscrew the dust protection cover of the camera (5).
4. Mount the lens (6).
5. Connect the µBNC cables (3) with the camera connectors (4).
6. Connect the other end of the cable with the frame grabber board (2).
7. If required, connect the power supply NTCAM132x via the 12-pin connector
with the camera (5).
INFO If connecting an external trigger, take the pinning into account.
8. If an external power supply (7) is used, connect the power supply with the main
supply.
9. Switch on the image processing system (1).
10. Check the status LED of the camera to verify that the camera is ready for use.
4.4 The power-up profile
If the camera is powered-up, the power-up profile permanently stored in the non-
volatile memory of the camera will be loaded. This profile consists of a number of
camera settings such as sensor resolution and frame rate. It is used to set the camera
into a defined operation mode.
4 First steps 17

INFO The camera has NOT to be configured by the host to start operation. The power-up
profile will deliver all necessary values.
Serial number and firmware version are provided in the non-volatile memory of the
camera. Use the GenICam feature “DeviceSerialNumber” to read the serial number
and the firmware revision.
INFO Read the chapter on Bootstrap Registers in the Reference Guide for more inform-
ation. For the serial number, see the identification plate at the side of the camera.
4.5 Cleaning sensor and lens
Unplug the camera before you clean any parts!
Never open the housing when cleaning the window of the sensor. If the camera has
been opened, the warranty will be void.
1. If there are coarse particles on the lens or the window of the sensor, use a
vacuum cleaner to remove them before cleaning to prevent scratches.
2. Clean the window of the sensor and the lens with a dry and soft lens-cleaning tis-
sue.
NOTICE Do not use tools that may harm the sensor or lens.
4.6 Updating the camera firmware
This section describes how to carry out a firmware update for a camera from
MikrotronGmbH using the software “CXPUpdater”.
Prerequisites
INFO The updater software requires the Microsoft Redistributables for Visual Studio 2015-
2019 (vcredist_x64.exe) that can be downloaded from Microsoft for free.
Procedure
The updater process requires frame grabber specific components. The program
assumes that there is a "Data" folder containing the following files:
lFlashData.ibf
lfpga_app_firmware.ibf
4 First steps 18

1. Open the tool “CXP Updater.exe” in the folder “Firmware”.
2. Select the CTI file that corresponds to the frame grabber board. If unsure, con-
sult the Device Manager.
3. To add a CTI file that is not in the list, select Add another CTIfile and navigate to
the file.
4. Select the board for updating.
5. Start the update process. The progress bar displays the current update status.
NOTICE Do not switch off the camera during the update process.
6. When the update is finished, restart the camera.
4 First steps 19

5 Technical data
5.1 Camera specifications
Frame rate (8 bit) max. 3674 fps
Pixel depth 8 /10 bit
Shutter speed 2 µs – 1 s
Shutter time (steps) 1 µs
Max. Jitter via CXP Trigger ±4 ns
Max. Trigger frequency 300 kHz
Quantum efficiency >45% @ 550 nm
Interfaces lCoaXPress 1.x @ 3.125 Gb/s
lCoaXPress 1.x @ 6.25 Gb/s
lCoaXPress 2.x @ 12.5 Gb/s
lCoaXPress lanes switchable to 1, 2, or 4
Frame rates of 12.5 Gb/s can only be reached when the camera is connected to a system that
supports CXP2. Otherwise, frame rates of up to 6.25 Gb/s are possible.
Adapter C- / F-mount
Dimensions
(W x H x L)
80 x 80 x 57.1 mm (without lens adapter)/
80 x 80 x 67.1 mm (with fan, without lens adapter)
80 x 80 x 84.6 mm (C-mount)/
80 x 80 x 94.6 mm (with fan, C-mount)
80 x 80 x 84.6 mm (F-mount)/
80 x 80 x 94.6 mm (with fan, F-mount)
Weight 0.45 kg
Cooling lFanless
lOptional fan at the back of the housing
Noise of optional fan max. 23 dB(A)
Power supply 12 - 24 V DC @ 11 W (Power adapter supplied)
Operating temperature
(camera body)
+5 °C ... +50 °C
Shock resistance 70 g
Vibration resistance 7 grms
Compliance GenICam
CoaXPress 2.0
5 Technical data 20
Table of contents
Other SVS-Vistek Machine Vision System manuals
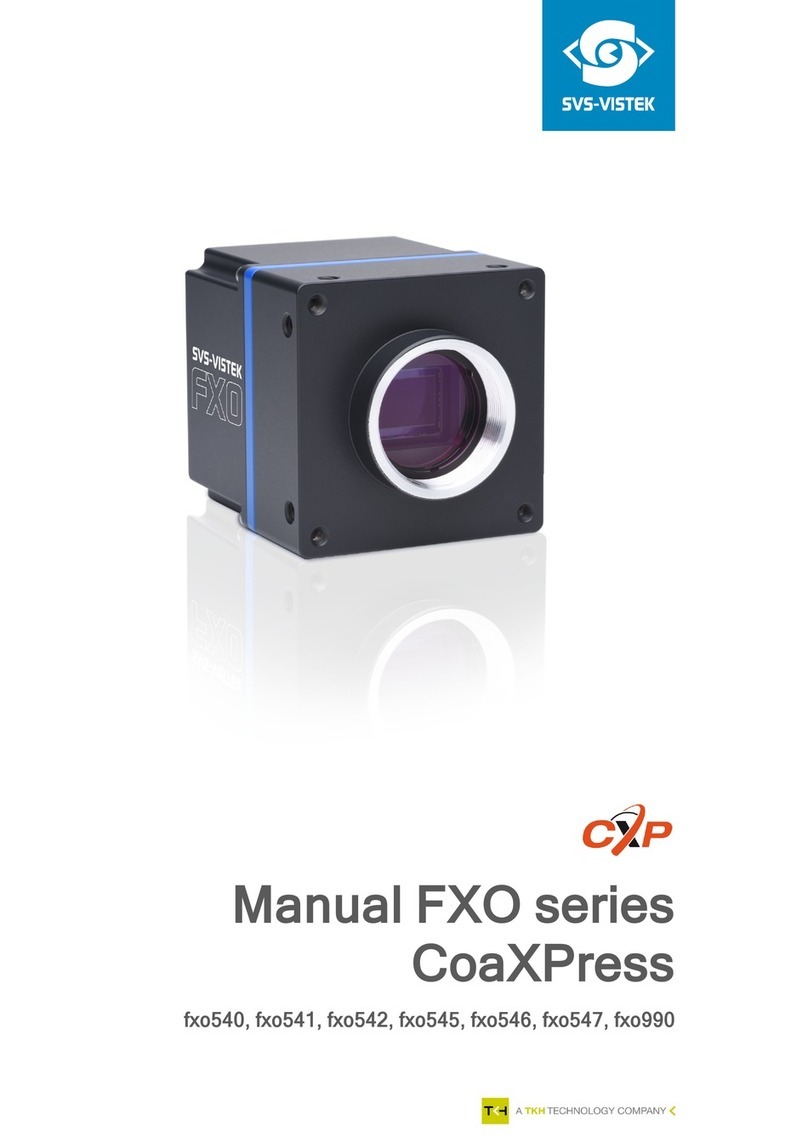
SVS-Vistek
SVS-Vistek CoaXPress fxo540 User manual
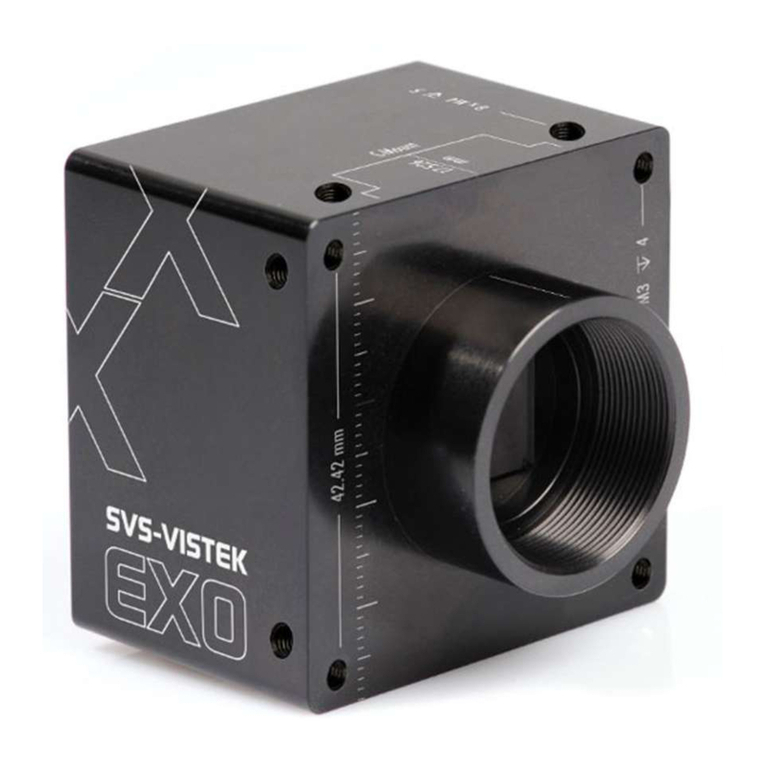
SVS-Vistek
SVS-Vistek EXO Series User manual

SVS-Vistek
SVS-Vistek GIGA VISION ECO 4I/O User manual
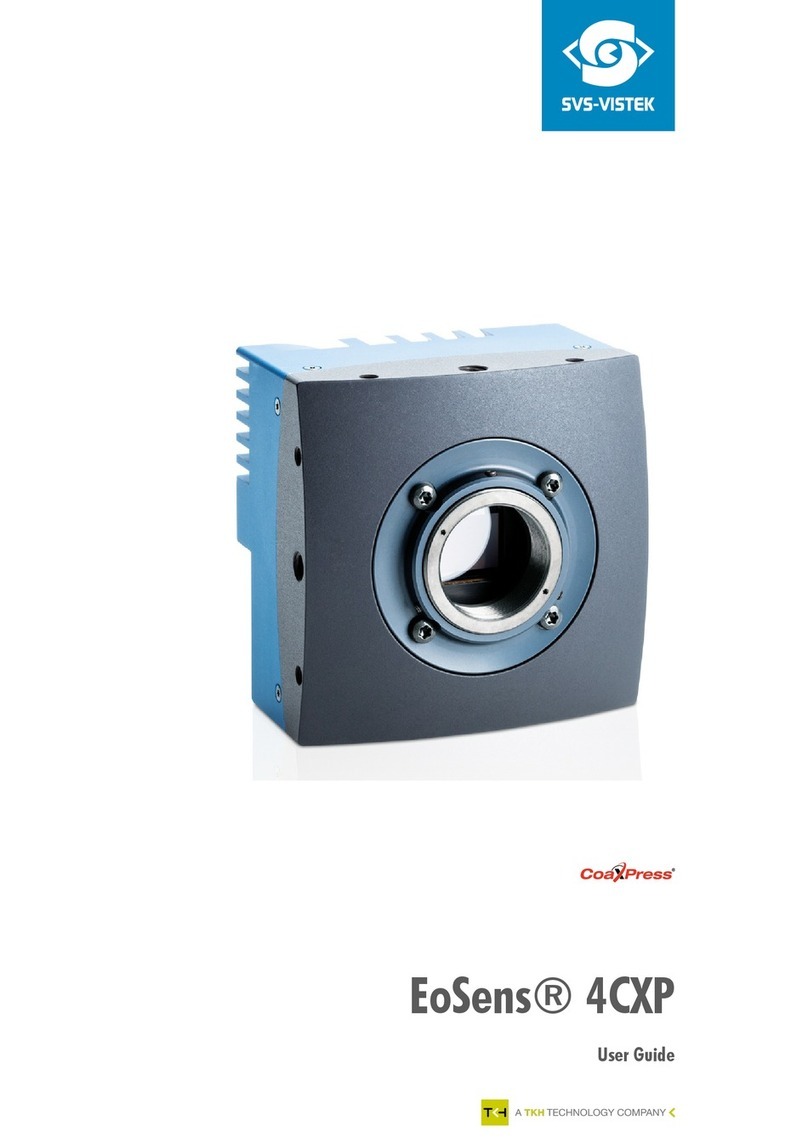
SVS-Vistek
SVS-Vistek CoaXPress EoSens 4CXP User manual
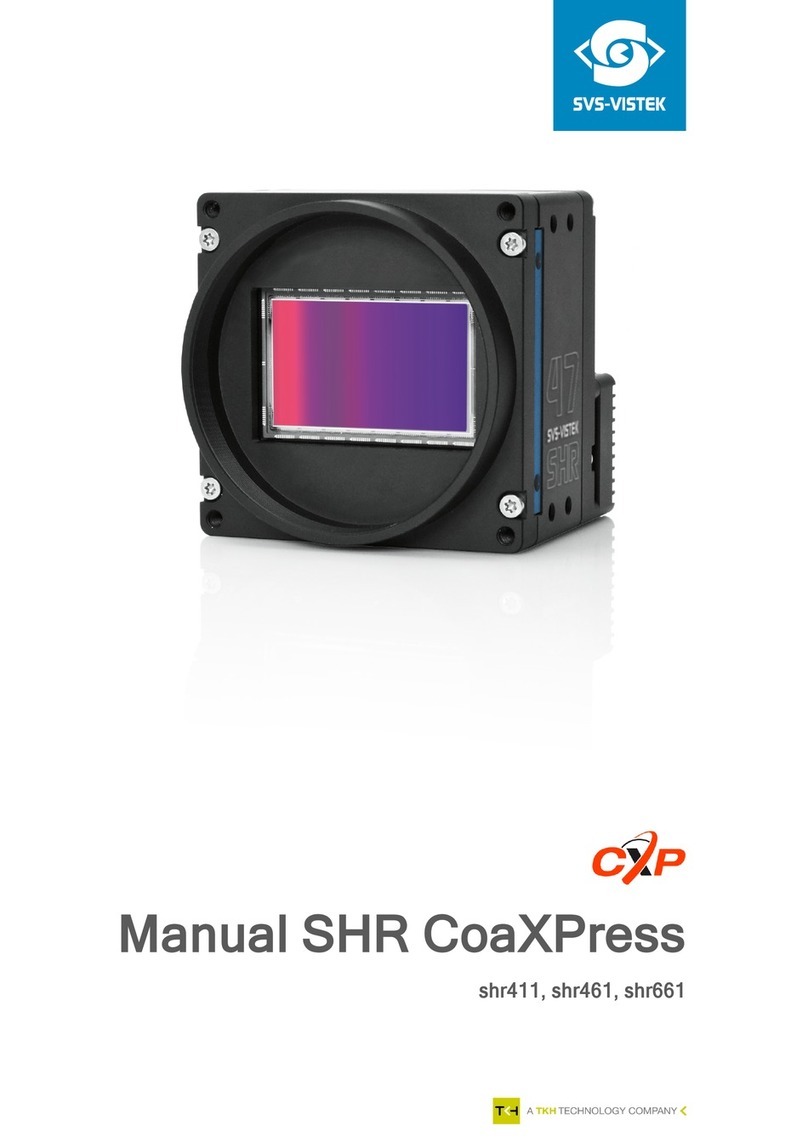
SVS-Vistek
SVS-Vistek shr 411 User manual
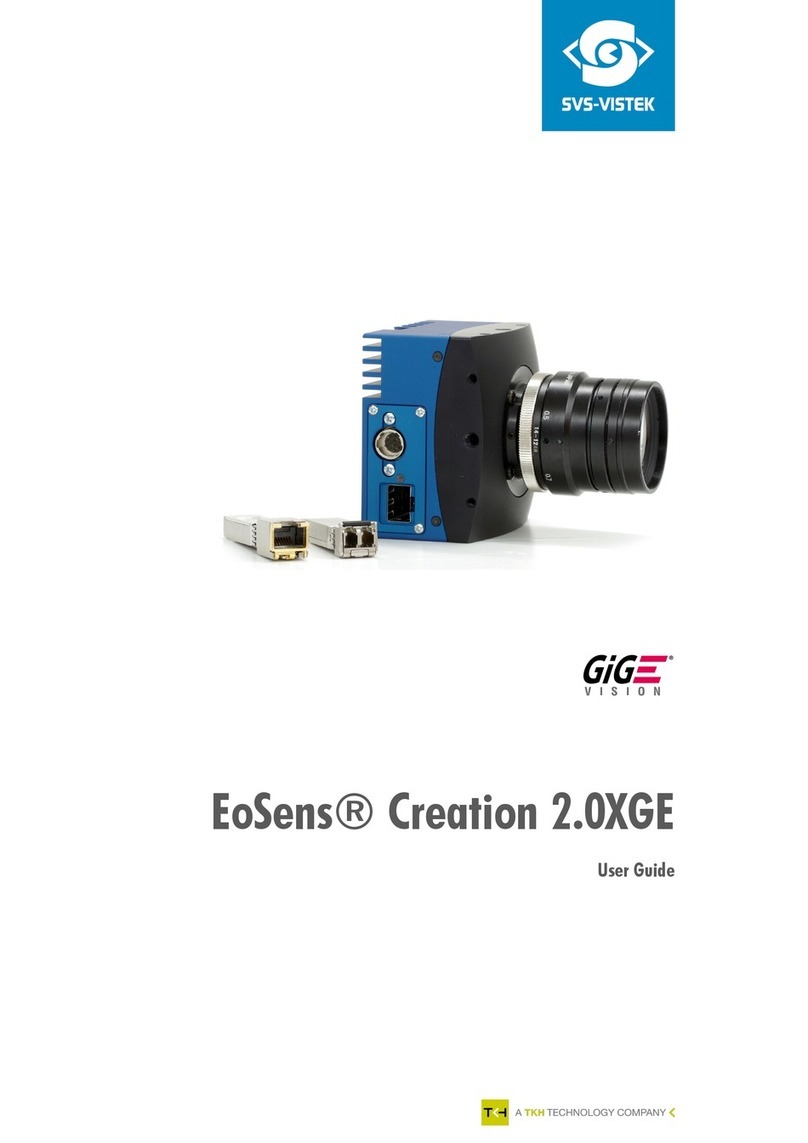
SVS-Vistek
SVS-Vistek EoSens Creation 2.0XGE User manual
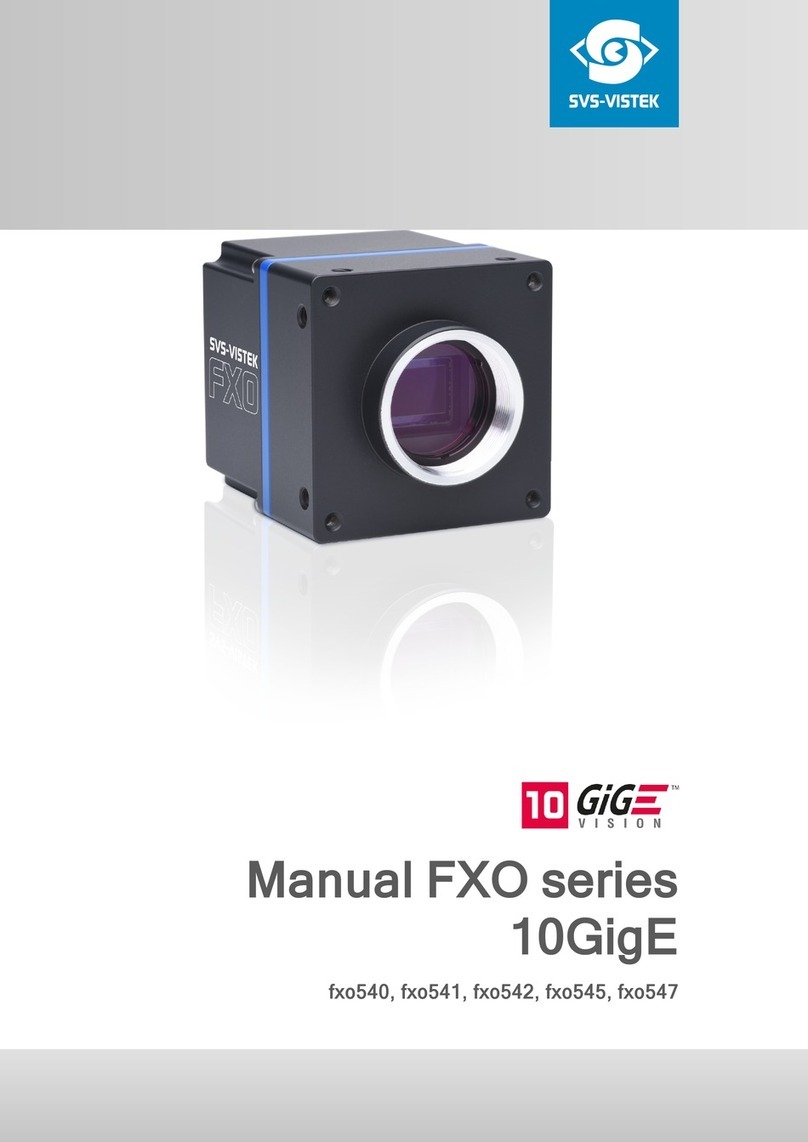
SVS-Vistek
SVS-Vistek 10 GiGE FXO Series User manual
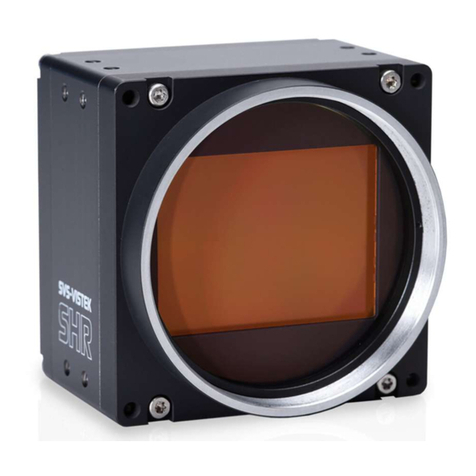
SVS-Vistek
SVS-Vistek SHR 10GigE User manual
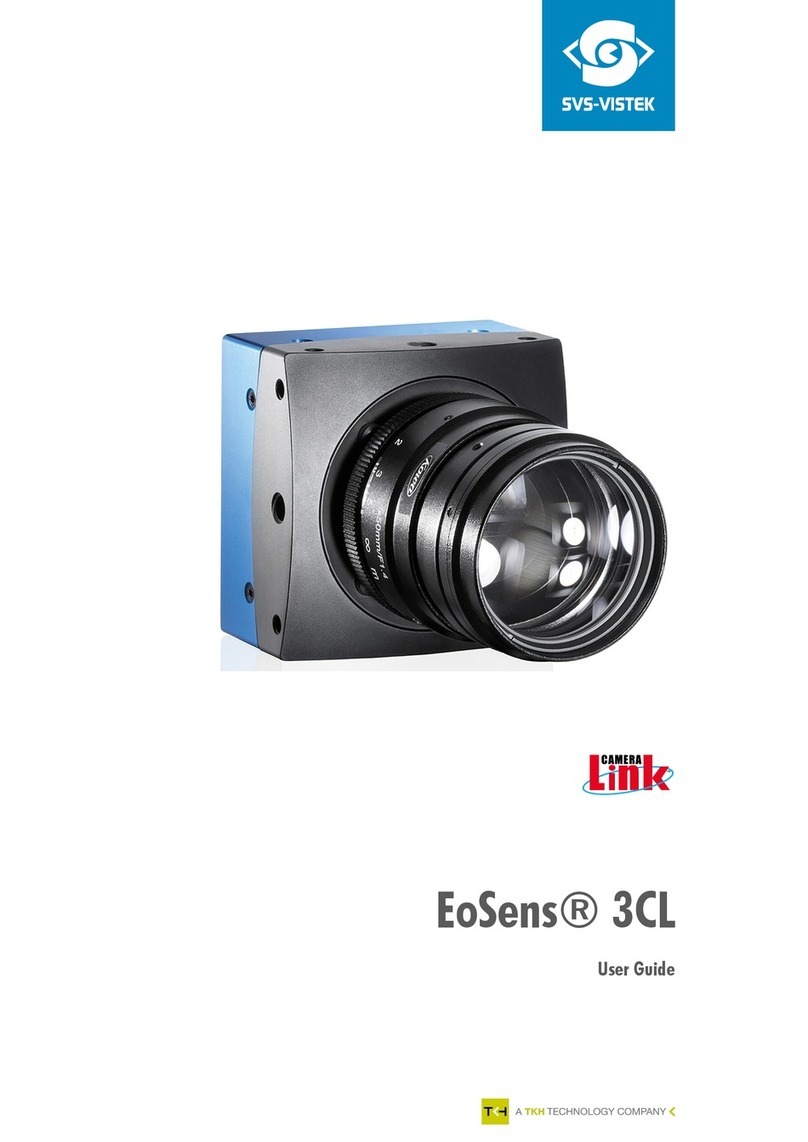
SVS-Vistek
SVS-Vistek CAMERA Link EoSens 3CL User manual
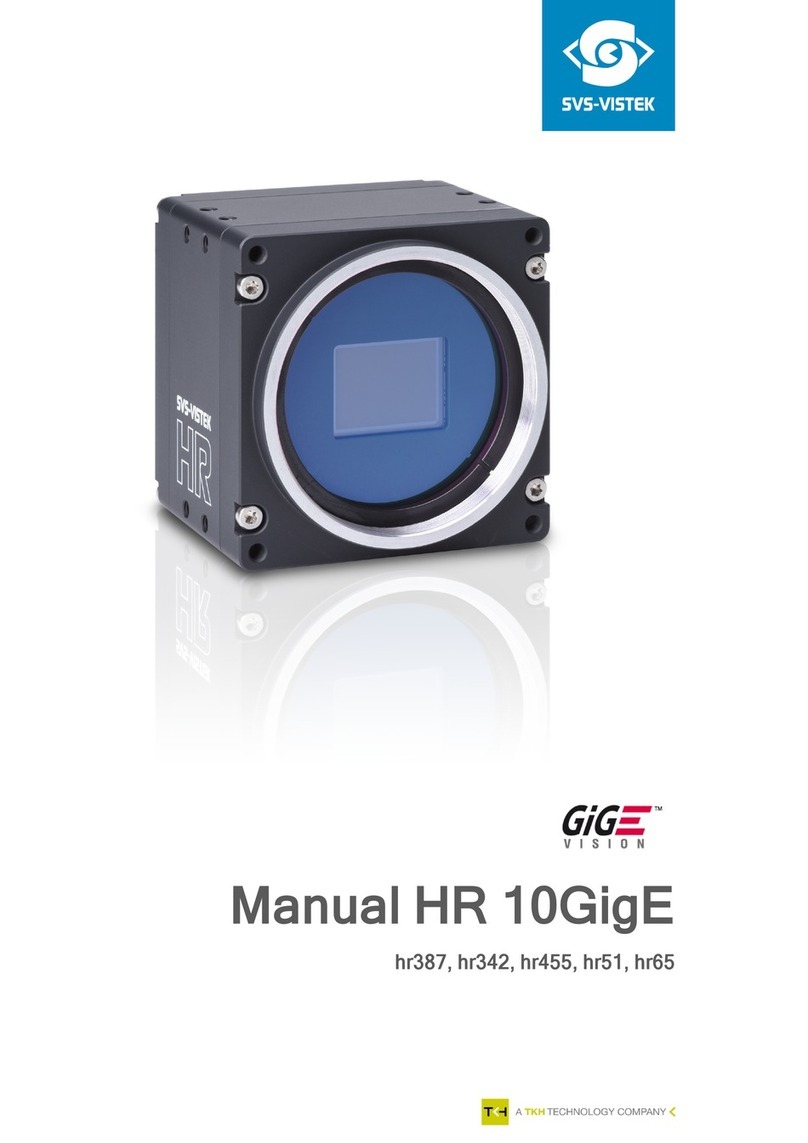
SVS-Vistek
SVS-Vistek hr387 Series User manual