Synectic Electronics SY021 User manual

SY021
Portable Load Meter
User Instructions
Relates to firmware version 5. 2s
revised February 2019

Wheatstone bridge
transducer
Introduction
The SY021 is a portable load meter, which can indicate the load present on any attached cell. A
dual channel version is available which indicates the load on 2 load cell inputs simultaneously.
Calibration details of up to 50 load cells can be stored for each available input. RS232, USB,
Bluetooth printer and data logging options are also available.
Programmable gain amplifiers on the front end allow the instrument to be configured for a wide
range of transducers, see section 8.
Connections
Load cell
Load cells are connected using locking DIN connectors, 4 pin for input 1, 5 for input 2. The pin
connections are:
Pin Signal
1 Excitation positive
2 Signal positive
3 Signal negative
4 Excitation negative
5 Not used (input 2 only)
Depending on your requirements, load cells can be fitted
with the DIN plugs, or you may find it useful to wire a plug
to a 4 way terminal block for general-purpose use.
Other connector types can be requested at time of
ordering.
Connections for Wheatstone bridge type transducers, such
as most load cells and some pressure sensors are
illustrated on the right.
USB
A standard USB type B socket is fitted. When the appropriate driver has been installed which
generally happens automatically when you connect to a PC the connection appears to the PC as a
standard RS232 port. If it does not load automatically. You can download the SY021 software and
drivers from;
http://www.synectic.co.uk/data-acquisition-signal-converters/sy021-dc-dual-channel-load-
meter.html
1.0 Operation
When the instrument is switched on the opening screen will show:
' Synectic '
' SY021 (c) 2012 '
After about 2 seconds the screen will then show:
'Chan1 = xx Mode'
'Chan2 = yy Mode'

CAL used to enter
Calibration mode and
to move on to next step
{
Tare and
Peak hold
Reset for
Input 1
{
Tare and
Peak hold
Reset for
Input 2
Dual function key
Numeric 0 and
STOP
Data Logger
Dual function key
Numeric 7 and
START Data
Logger
ENT used to enter
Measuring mode and
to view/edit settings in
Calibration mode
Dual function keys
2,4, ,8 for numeric
entry and Up/Down
Right/Left keys
Where xx and yy are the last used channel numbers and mode is the current operating mode
(Continuous or Peak hold) of each channel.
If the second channel option is not fitted, the second line will indicate ‘Single channel’
To display the load on each available input, press ENT on the keypad.
If a communications port is fitted and use of Batch Reference has been selected, see 3.75, the
screen will first show:
'ENT when correct'
' atch A C12345'
This allows the current batch reference, ABC12345 in this example, to be changed. This is done
using the sideways arrows (4& ) to select the character and the up/down arrows (2&8) to change
each character. If the up or down arrow keys are held in the display will automatically cycle through
the available characters. Press ENT when correct.
The screen will indicate the weight on each input using the calibration data and units set for each
channel.
In continuous measurement mode Tare buttons marked T1 and T2 can be used to tare either input.
This tare value is not stored; therefore if the unit is switched off and on it will revert to the stored
tare value. The stored tare value can be saved with calibration data using the manual calibration
mode (See 3. 4)
In peak hold mode, Reset buttons R1 and R2 will reset either input, ready to find the next peak.
If the USB option is fitted and use of Batch Reference has been set, pressing 5 will send current
measurement details to the USB port. Eg
Acme Trading Co
atch Ref A C12345
Peak1 = 50.25kg
Peak2 = 25.12kg
Pressing any other key will return the display to indicate the selected channels.
Overview of keypad functions

.0 Changing channels and operating modes
Press 1 to change input 1 or 2 to change input 2.
Pressing 1 will change the display to show:
'Configure input1'
'Setup(00-49) xx'
Where xx is the currently selected setup channel. The unit can store details of up to 50 setup
channels for input 1. The channels are numbered 00 to 49.
To change the setup channel number press ENT and then the setup number. If you enter the
wrong number press ENT again and repeat the process until the required setup channel number is
shown. Pressing CAL will then show the currently selected mode (Continuous or Peak Hold)
Press ENT to switch between the modes.
When correct press CAL.
The option of changing the filter setting is then presented. The initial value will be as set during
calibration, (see 3.1) but it can be changed here without affecting any of the other calibration
settings. When correct press CAL to return to the channel display screen.
The same operation can be carried out for input 2, if fitted, by pressing 2. The only difference is
that the filter option is not given. Input 2 uses the same filter setting as input 1. The available setup
numbers for input 2 are 50 to 99.
3.0 Calibration
To calibrate an input press CAL. The display will show:
Calibration Mode
Enter PIN ----
A pin number should now be entered to access the calibration options. The factory default is 1234.
Once the PIN has been correctly entered, the 2nd line will show:
Calibrate Cell
If a channel needs calibrating to match a cell press ENT and go to step 3.1, otherwise press CAL
and you will move on to the next step (3.7).
3.1 Input selection
If 2 sensor inputs are fitted, the screen will show:
Calibration Mode
Which Input? -
Press 1 or 2 to calibrate the required sensor input.
3.11 Setup Channel selection.
Each sensor input can store up to 50 different setups, these are numbered 0-49 for sensor input 1
and 50-99 for input 2. Enter the required number (0-49 or 50-99).

3. Filter setting
The display will then show the currently set filter value (0-3) of the selected channel. The filter
value determines the number of readings, which are averaged for each sample as follows:
0 = 1 reading (fastest response)
1 = 2 readings
2 = 4 readings
3 = 1 readings (heaviest damping)
Each reading takes approximately 10 mSec. (Standard, but see section 8 to change).
When correct press CAL.
3.3 Selecting Units
The display will indicate the current units for the selected channel. 4 units are available, kg, t, lb
and a 4th user programmable unit. Press ENT until the required units are displayed.
3.4 Decimal places
The display will then show the selected number of decimal places (0-3), this can be changed by
pressing the required number. When correct press CAL.
3.5 The calibration method (automatic or manual) will now be shown.
Two options are available in automatic mode, one by adding a known weight, the other by entering
mV/V figures. The mV/V method is available for PGA gains of 128 or 4, see section 8.
Manual mode allows for fine adjustment of an input, which has already been calibrated. Press ENT
to select the required mode, then CAL.
3.51 Automatic mode
The display will first show ‘ Use known load ‘. If this is the required method, press CAL and go
to 3.52. If ENT is pressed, and input gain is 4 or 128, the display will show ‘ Use mV/V value‘.
If this is the required method, press CAL and go to 3.53. Pressing ENT will toggle between the two.
3.5 Using known load
The instrument will request the value of a known test weight to be entered.
When entered the 1st line of the display will show:
No Load then ENT
Without the test load present, the ENT key should be pressed. The display will then change to:
Add Load then ENT
At this point add the specified test load and press ENT. The channel will now be calibrated.
3.53 Using mV/V value
The instrument will request the value of the full-scale range to be entered using the previously
specified decimal places and units. E.g. if 2dp & kg had been selected, the display will show ‘FS
Range---.--kg’. Enter the value as a 5-digit value, including leading zeroes if appropriate.
The display will then show ‘Value -.----mV/V’ Enter the value from the load cell calibration
certificate.
The instrument then offers the opportunity to tare the input. With the load cell attached and no load
present, or with the signal wires shorted, press the appropriate tare button. If tare is not required,
e.g. if the mV/V value for a previously calibrated load cell is being adjusted, press any other key.
The display will move on to 3.7.

3.54 Manual mode
The instrument will indicate the current weight. This can be zeroed by pressing the tare button, T1
or T2. Pressing CAL introduces a 100k shunt resistor to simulate an applied load. Repeating CAL
will remove the shunt. Pressing the up and down arrow keys will produce a fine adjustment of the
displayed weight. When correctly adjusted, press CAL
3.6 Communications USB
A standard USB type B socket is fitted. When the appropriate driver has been installed which
generally happens automatically when you connect to a PC the connection appears to the PC as a
standard RS232 port. If it does not load automatically. You can download the SY021 software and
drivers from;
http://www.synectic.co.uk/data-acquisition-signal-converters/sy021-dc-dual-channel-load-
meter.html
If this option is not fitted move on to 3.8
3.61 Internal clock date setting
The display will now show:
' Internal Clock '
' DATE dd/mm/yy '
To change the date type in a new digit value in the form ddmmyy or press CAL to move on.
3.6 Internal clock time setting
The display will now show:
' Internal Clock '
' TIME hh:mm:ss '
To change the time type in a new digit value in the form hhmmss or press CAL to move on.
3.63 RS 3 setting
If the USB option has been fitted the display will show
‘CONFIGURE RS232’
‘aud Rate -9600‘
The data format is fixed as 8 data bits, 1 stop bit, no parity. Four baud rates are available, 2400,
9 00, 38K4 & 115k2. Pressing the up arrow (2) or the down arrow (8) will cycle between the
values. When correct press CAL
3.64 Inter Character Gap
This feature is included to accommodate printers and some old computers which only have a small
buffer and may not be able to keep up with a full speed stream of data. It allows a gap between
each transmitted character to be added. The length of the gap is programmable up to 255msec.
The display will show:
‘CONFIGURE RS232’
‘Char Gap xxxmsec‘
xxx is the gap in msec. To change it press ENT and enter a new 3 digit value in the range 0-255.
(Factory default 0msec). If you are experiencing difficulty getting the PC software to work with the
SY021 it may be because the inter character gap is set to high. When correct press CAL.

3.65 Batch Reference
If the RS232 option has been fitted, it is possible to print test results together with an 8 character
batch reference. The display will show
‘CONFIGURE RS232’ ‘CONFIGURE RS232’
‘Use atch Ref Y‘ OR ‘ Use atch Ref N‘
Press ENT to select the required option.
If the bluetooth option is not fitted go to 3.8
3.7 Bluetooth configuration.
If the bluetooth printer option is fitted, the printout details mentioned earlier will be sent to a suitable
bluetooth enabled printer. The printer should support PCL and be set to 9 00 baud with a
password of 1234. The RS232 settings of 3. 3 and 3. 4 will apply to the USB interface. As with the
RS232 option, connecting the USB interface will divert communications from the bluetooth printer
to the USB virtual serial port.
The display will show:
‘luetooth status’
‘ ENT to check ‘
To check and/or reconfigure the the settings press ENT, or press CAL and go to 3.8
3.71 Bluetooth paired device details
The display will show the address of the Bluetooth printer that the SY021 will attempt to pair with.
eg:
‘ 0123-45-6789A ’
‘ENT-New CAL-Exit‘
In this example 0123-45- 789AB is the address of the printer. If pairing with a different printer is
required then make sure the printer is in the vicinity and turned on before pressing ENT, otherwise
press CAL and go to 3.8.
3.7 Configuring a different printer.
The display will show:
‘Turn Printer OFF’
‘ Then Press ENT ‘
Follow the instruction and after a while the display will change to
‘Turn Printer ON ’
‘ Then Press ENT ‘
Again, follow the instruction and the display will change to
‘ ’
‘Finding devices ‘
After a delay of a few minutes while bluetooth devices are searched for the display will change to
either,
‘No devices found’ OR ‘ n devices found’
‘ENT-New CAL-Exit‘ ‘ENT-New CAL-Exit‘
If no devices are found, make sure your printer is turned on and try again by pressing ENT. Where
devices are found, n indicates the number, up to 8.
Pressing any number from 1 to n will show the address details and description of that device.
If the address of the printer is known it is simply a matter of checking each number until the match
is found, then press ENT to store that as the paired device.

If the printer address isn't known, the description will usually allow identification.
If not sure about any of the devices found, press CAL to exit.
If ENT has been pressed the display will change to
‘ 0123-45-6789A ’
‘ Storing device ‘
After a while the display will change to
‘Turn Printer OFF’
‘ Then Press ENT ‘
Follow the instructions and finally the display will return to
‘ n devices found’
‘ENT-New CAL-Exit‘
If you are happy that the correct device has been stored, pressed CAL to exit. Otherwise, an
alternative device can be stored by pressing the relevant number then ENT.
3.8 Data logger.
If the data logger is fitted the display will show
‘ Logger status ‘
‘ ENT to check ‘
The logger has the capacity to store 7999 sets of readings for each channel. To check the logger
status press ENT. As an example, the display will then show
‘ 191/7999 used ‘
‘Press 0 to clear’
In this case indicating that 191 of the logger memory locations are used. Pressing 0 will clear the
memory, any other key will move on.
3.81 Data logger mode
The instrument will first present the option of Continuous or Single shot modes
The display will show:
‘DATA LOGGER MODE’ ‘DATA LOGGER MODE’
‘ Continuous ‘ OR ‘ Single shot ‘
In both cases, the logger is activated during the measurement display, by pressing the green start
button (key 7). Continuous logging is stopped by pressing the red stop button (key 0).
The data is stored in comma separated variable spreadsheet format.
Fields are Test,Day,Hour,Min,Sec,Chan1,Chan2.
Note
Single shot readings store data in every field. Continuous readings leave the Day field empty but
record the Seconds field with a resolution of 0.01sec.
During continuous logger mode data will continue to be added to spreadsheet unless logging is
stopped or the logger is full.
Data is added to the spreadsheet until the logger is full. If this happens the display will show
‘ Logger Full ‘
‘ Press any key ‘
Pressing any key will turn off the logger and return to displaying the measurements.
Press ENT to select the required mode and CAL to move on.

3.8 Trigger Interval
If continuous mode the interval between saved readings depends on the filter setting:
Filter Sample interval Maximum logging time
0 10 msec 1 min 20 sec
1 20 msec 2 min 40 sec
2 40 msec 5 min 20 sec
3 160 msec 21 min 20 sec
NOTE: If a longer sampling interval is required, change the A/D
update rate, see section 8. The following tables indicate intervals in
different ADC rates.
62 Readings per second
Filter Sample interval Maximum logging time
0 20 msec 2 min 40 sec
1 40 msec 5 min 20 sec
2 80 msec 10 min 40 sec
3 320 msec 42 min 00 sec
33 Readings per second
Filter Sample interval Maximum logging time
0 30 msec 4 min 00 sec
1 60 msec 8 min 00 sec
2 130 msec 17 min 20 sec
3 500 msec 1 hour 6 min 40 sec
16 Readings per second
Filter Sample interval Maximum logging time
0 60 msec 8 min 00 sec
1 130 msec 17 min 20 sec
2 250 msec 33 min 20 sec
3 1000 msec 2 hour 13 min 20 sec
8 Readings per second
Filter Sample interval Maximum logging time
0 130 msec 17 min 20 sec
1 250 msec 33 min 20 sec
2 500 msec 1 hour 6 min 40 sec
3 2000 msec 4 hour 26 min 40 sec
4 Readings per second
Filter Sample interval Maximum logging time
0 250 msec 33 min 20 sec
1 500 msec 1 hour 6 min 40 sec
2 1000 msec 2 hour 13 min 20 sec
3 4000 msec 8 hour 53 min 20 sec

3.9 Custom units
The display will show ‘ Custom units ??’ Where ?? Can be any pair of characters. To change
the first character, press ENT. Use the up arrow (2) or down arrow (8) to scroll the available
symbols. If either of the keys is held in the symbols will continuously scroll.
When the first character is correct, press the right arrow ( ) and repeat the process for the second
character.
Press ENT when finished.
4.0 Changing the PIN number
The 2nd line of the display will then show:
New PIN?
To change the PIN press ENT and enter the new value. Otherwise press CAL to return to the
channel display screen.
5.0 Accessing data
The data can be downloaded via USB port. PC Software is supplied with the instrument to access
data, or any simple terminal software, such as Hyperlink, can be used. Set the filename to have the
extension .csv to indicate to the spreadsheet that the data is in comma separated variable format.
Type *D to download the data. The logger memory can then be cleared by typing *C. After about
10sec the unit will respond with Y.
6.0 Power supply
The unit is powered by 4 AA batteries. Since the input voltage range in this version is now 3 -7V
DC, 1.5 volt alkaline
or 1.2V rechargeable types are suitable. If rechargeable batteries are used they should be charged
using a suitable external charger.
If fitted with DC 2.1mm socket an external 5V dc supply can be used. It should be fitted with a
2.1mm DC plug with negative to the outer. Rating should be 200mA higher.
Plugging the DC power supply in disconnects the battery supply it does not charge in
circuit.
7.0 RS 3 or USB Interface commands.
When the USB interface is fitted the following commands are available. All start with and the
letters can be upper or lower case.

Command Description Response
@ Read Unit ID Model number, Firmware version and serial number.
Eg. SY021,V5. 0i, 1234cr
C Clear Log If Logger is fitted; ‘Y’ if successful, ‘N’ if unread data
if no logger fitted; ‘?’
D Dump logger If logger fitted; Transfer logger data in CSV spreadsheet
format. If no logger fitted ‘?’
M Logger memory Reports size of data logger memory
eg. 0 4 indicates 4k logger
000 indicates no logger
H Define Header Allows a header of up to 50 characters to be programmed.
After *H type the heading, ending with cr. Batch tickets
and data downloads will contain the header at the top.
S Serial number Reports the instrument serial number, eg. 1234cr
TC Calibrate clock The built in clock can be speeded up or slowed down to
improve accuracy. The range of values is +/- 31. Each
positive step increases the clock speed by 4.0 8ppm,
each negative step reduces it by 2.034ppm. TCF will put
the clock into frequency test mode and report the current
calibration value. To enter a new value sendTC+nn or
TC-nn where nn is a 2 digit number in the range +/-31
TR Read time Reports the current time & date in the form:
YY MM DD hh:mm:ss(cr)
TS Set time Set the clock to a new time and date. Enter in the form:
TSYYMMDDhhmmss
8.0 Instrument calibration and configuration
NOTE: Any changes made in this section only take effect after turning off then back on.
For automatic calibration using mV/V and full scale values, the instrument uses a set of calibration
values stored in its non-volatile memory. There are 2 values, 1 for each input. Each value is a 3
digit number which is nominally 500 and which can be adjusted up or down, each step equating to
a 0.01% change. To access these values press CAL but then instead of entering the PIN, press
CAL, 2, ENT, 1.
The display will then show
'Calibration Mode'
'Ch1 Trim Val ---'
Pressing ENT will display the current value. Pressing ENT again will allow a new value to be
entered or pressing CAL will move on the next value.
Example.

A calibrated loadcell is available with an output of 2.012mV/V at 100kg.
The loadcell is connected to channel 1 of the SY021 and automatic calibration mode is selected.
The given values of 2.012mV/V and 100kg are entered and 2 decimal places are selected. When
tested the displayed weight is found to be 0.03% high. The current value of Ch1 Trim Val is found
to be 512, press ENT and change this to 515. Then re-enter the calibration figures of 2.012mV/V,
100kg. The weight should now be correct.
8.1 Input gain setting
The instrument is shipped as standard with each input configured with a gain of 128, allowing
bridge type transducers with outputs of up to +/-7.5mV/V. The display will show:
' Use ^ v to edit'
'Ch1 PGA Gain 128'
Pressing the up arrow (button 2) or down arrow (button 8) will cycle between 8 different gains from 1 to
128. Input ranges for each gain are:
Gain Input mV/V Voltage Input Notes
128 +/- 7.5 +/- 37.5mV Most load cells
64 +/- 15 +/- 75mV Higher o/p bridge tra ducers
32 +/- 30 +/- 150mV
16 +/- 60 +/- 300mV (All voltage ra ges are
8 +/- 120 +/- 600mV differe tial to withi 0.2V
4 +/- 240 +/- 1.2V of Ex+ a d Ex-)
2 +/- 480 +/- 2.4V
1 +/- 1000 +/- 5V Pote tiometer tra sducers
(Ra ge exte ds to Ex+ & Ex- for gai of 1)
Example
The instrument is required to monitor force against distance traveled. This can be achieved by
connecting a load cell to monitor the force to input 1, with the gain at the default 128. A
potentiometric linear displacement transducer could be connected to input 2, with the gain changed
to 1. The user units could be set to mm and used for the displacement.
8. A/D converter update rate setting.
The factory default setting is 125 readings per second (rps). Like the gain setting this can be cycled
between 8 different rates from 4 rps to 470 rps. Sometimes it may be required to slow the A/D
converter down to increase the time interval between logged readings.
Note that, due to speed limitations of the data logger memory, the maximum logging rate is 100Hz,
10msec per sample, so increasing the A/D rate to 250 or 470 rps would not provide any benefit.
9.0 Instrument Details
To check the serial number and firmware version of the instrument, hold in the CAL button as
power is switched on.
Power requirements.

The instrument is powered by 4xAA batteries. With logger & USB options fitted, typical current
consumption when connected to a 350 ohm load cell is 48mA, giving an operating life with alkaline
cells of approximately 50 hours. With no load cell connected the consumption drops to 35mA.
When the instrument is switched off, consumption is zero.
Instrument identification
The serial number and firmware version can be found by holding in the CAL button as the
instrument is turned on. The serial number and firmware version will be displayed. If you have any
technical queries it will be useful to have this information available. Pressing any key will set the
unit for normal operation.
Specifications
Parameter Min Typ Max
Supply voltage (DC) 3 (4xAA) 7
Input sensitivity (mV/V) 10.5 7.5
Excitation voltage (V dc) 4.95 5 5.05
Conversion Rate per second 14 470
Peak Hold (msec) 110 1 0
Full scale accuracy 0.01%
Current consumption(mA) 35; no transducer connected 48 55
Inputs 1 2
Calibration Known weight, mV/V value, or fine nudging. 50 set-ups can be stored for
each input.
Display 2 x 1 Character LCD
Temperature drift (ppm/C) 50
Shunt calibration 100kΩ internal resistor
Communication options USB, Bluetooth
Operating temp.(C) -20 80
Storage temperature (C) - 5 150
Case ABS black IP 5 case W=101. mm, L=190.5mm, H=35mm
Connections 4&5 pin binder 80 connectors as standard. Others available
Notes
1 Input sensitivity and conversion rate can now be configured by the user, see section 8.
Peak input capture values
RPS Readings/sec Minimum pulse width capture
470 3msec
250 10msec
125 12msec
62 22msec
33 42msec
16 85msec
8 200msec
4 400msec

A1.0 Connecting alternative transducers
By using the configuration options described in section 8, the SY021 can be used with other
transducers.
eg 1 – A potentiometric linear displacement transducer.
A linear displacement transducer can be simply connected
to one of the SY021 inputs by connecting as shown. A 5V
excitation supply, suitable for most of such transducers is
provided by the SY021. The output is connected to Signal +
and signal – is linked to Excitation -. The gain for the input is
set to 1, see section 8. At this gain the full input range is
useable by the SY021. Suitable units, such as mm, can be
defined as the user units for this input, see 3.9
eg – A wire 4- 0mA transducer
This can be achieved with the addition of 3 low
cost components. The 1 ohm shunt resistor
converts the 4-20mA to 4-20mV. An input gain of
128 with +/-35mV range would be suitable. As an
alternative, a 10 ohm shunt resistor could be
used, giving 40 – 200mV. A gain of 1 would
then be best. The diode can be almost any type.
It's needed because, with gains higher than 1,
the input range is within 200mV of the supply.
If the 5V excitation from the SY021 is enough for the transducer, the 4.7V zener diode isn't
required, but if a higher, external supply is needed it protects the SY021 input for over voltage
damage. In this case the transducer supply + should connect to the external supply + rather than
the SY021 Ex+. The negative of the higher supply should be linked to Ex-, along with
the 2 diodes.
eg 3 – A 3 wire 4- 0mA transducer
This is achieved in a very similar way to the
2 wire transducer. Again, if the transducer
requires a supply of higher than 5V, an
external supply should be connected between
the transducer supply + and supply -, with no
connection to EX+ on the SY021.
Applications
This manual suits for next models
1
Table of contents
Other Synectic Electronics Measuring Instrument manuals
Popular Measuring Instrument manuals by other brands
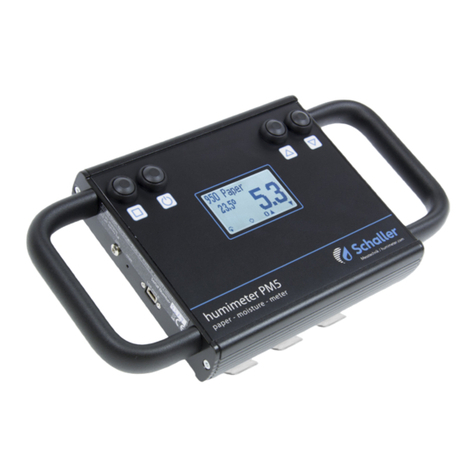
Schaller
Schaller humimeter PM5 operating manual
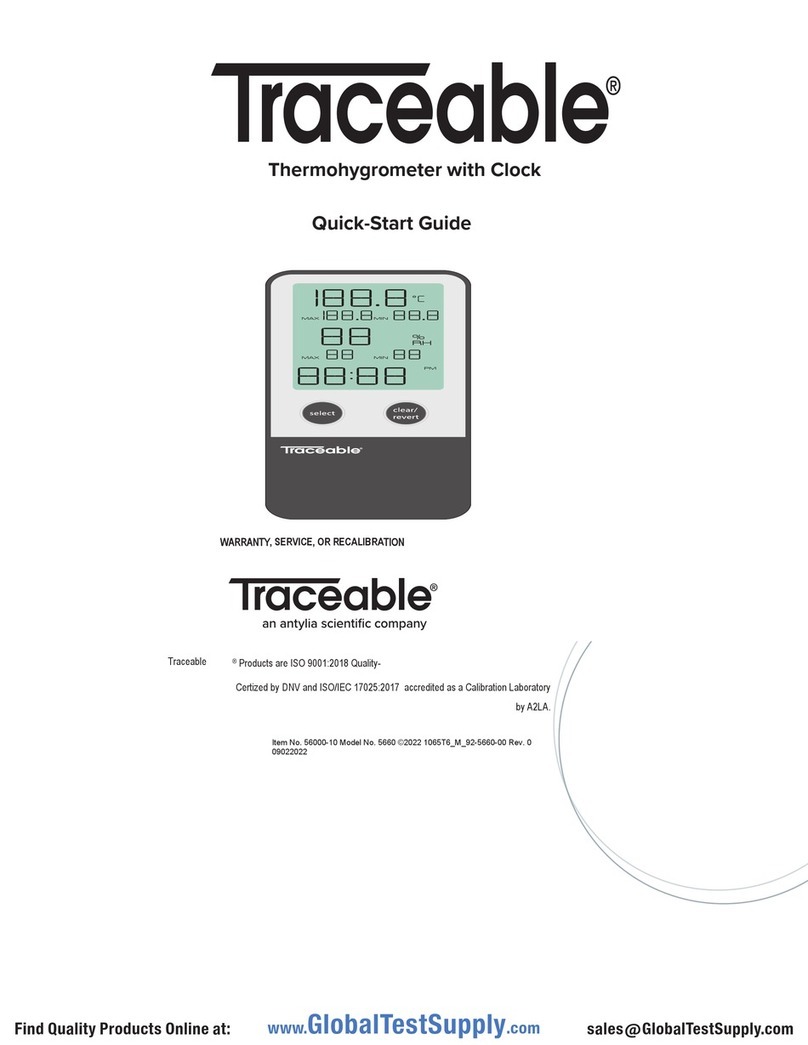
Traceable
Traceable 5660 quick start guide
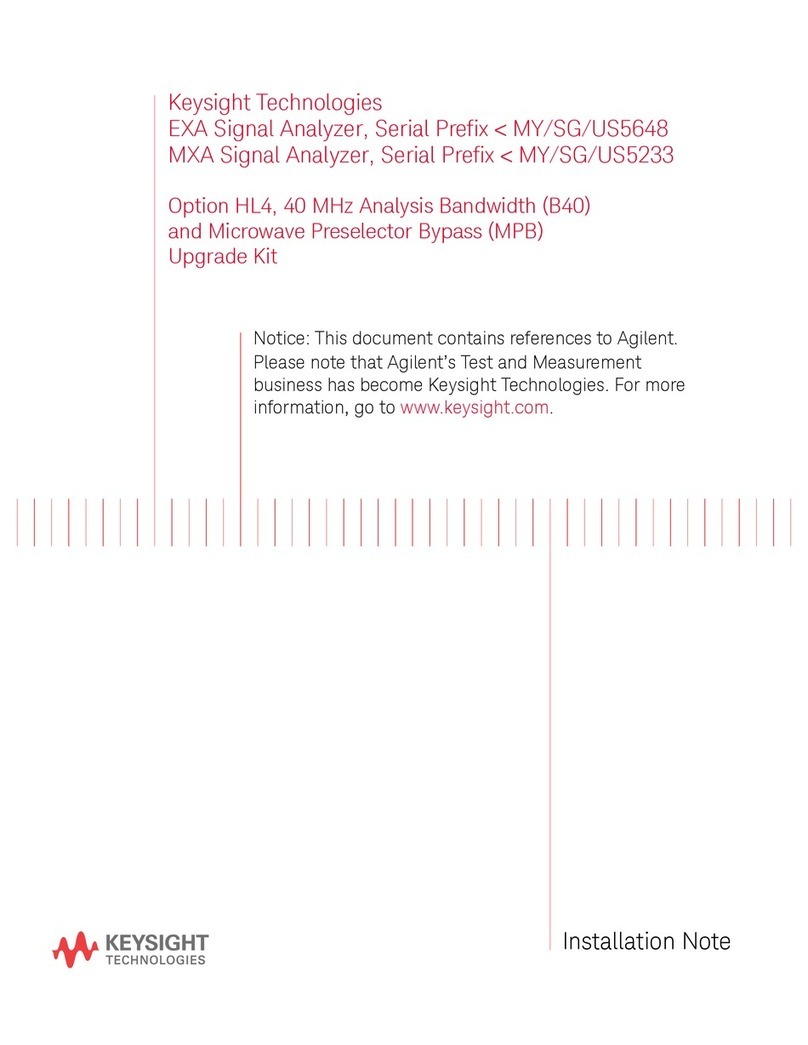
Keysight Technologies
Keysight Technologies N9020A Installation note
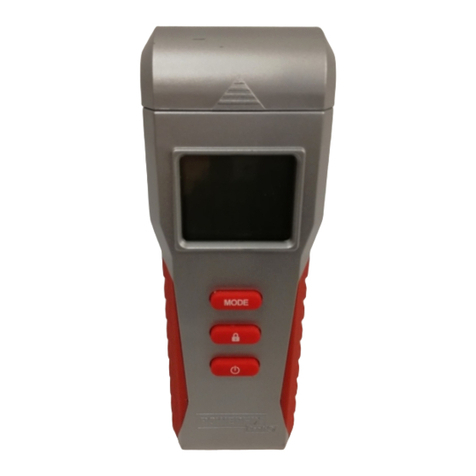
Powerfix Profi
Powerfix Profi 278296 Operation and safety notes
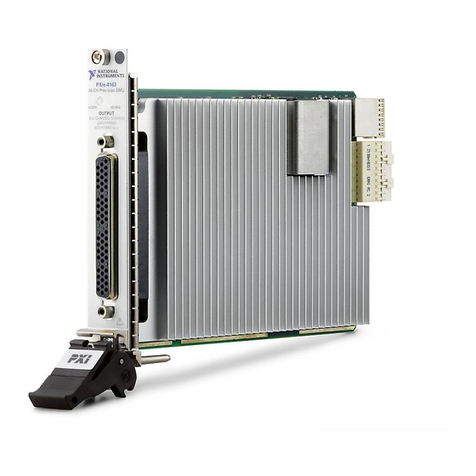
National Instruments
National Instruments PXIe-4163 Getting started guide
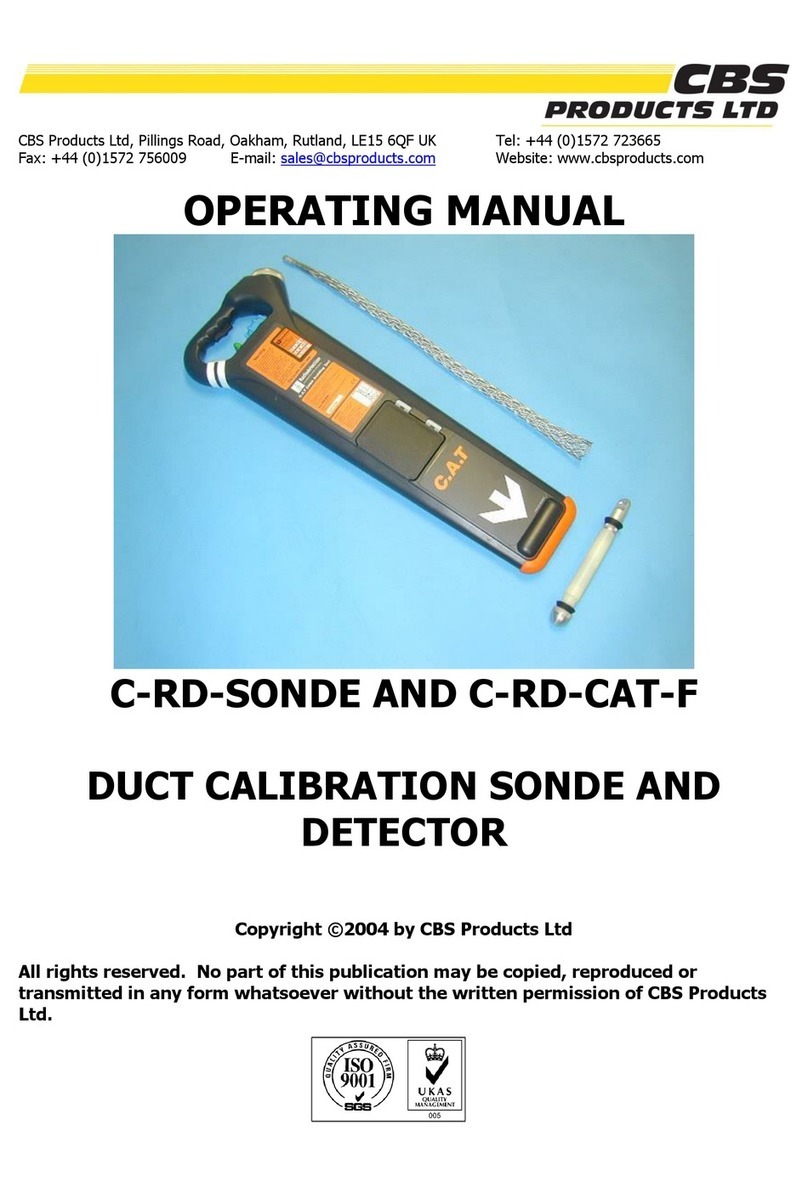
CBS
CBS C-RD-SONDE operating manual
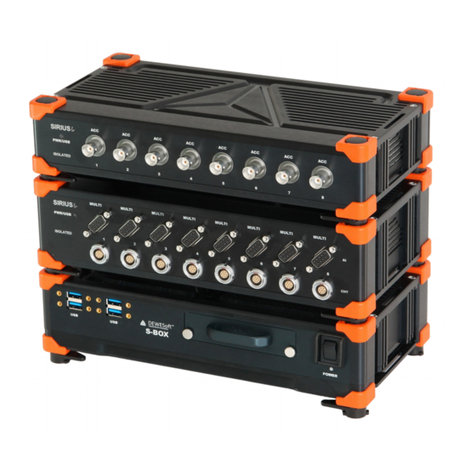
DEWESOFT
DEWESOFT SIRIUS Technical reference manual
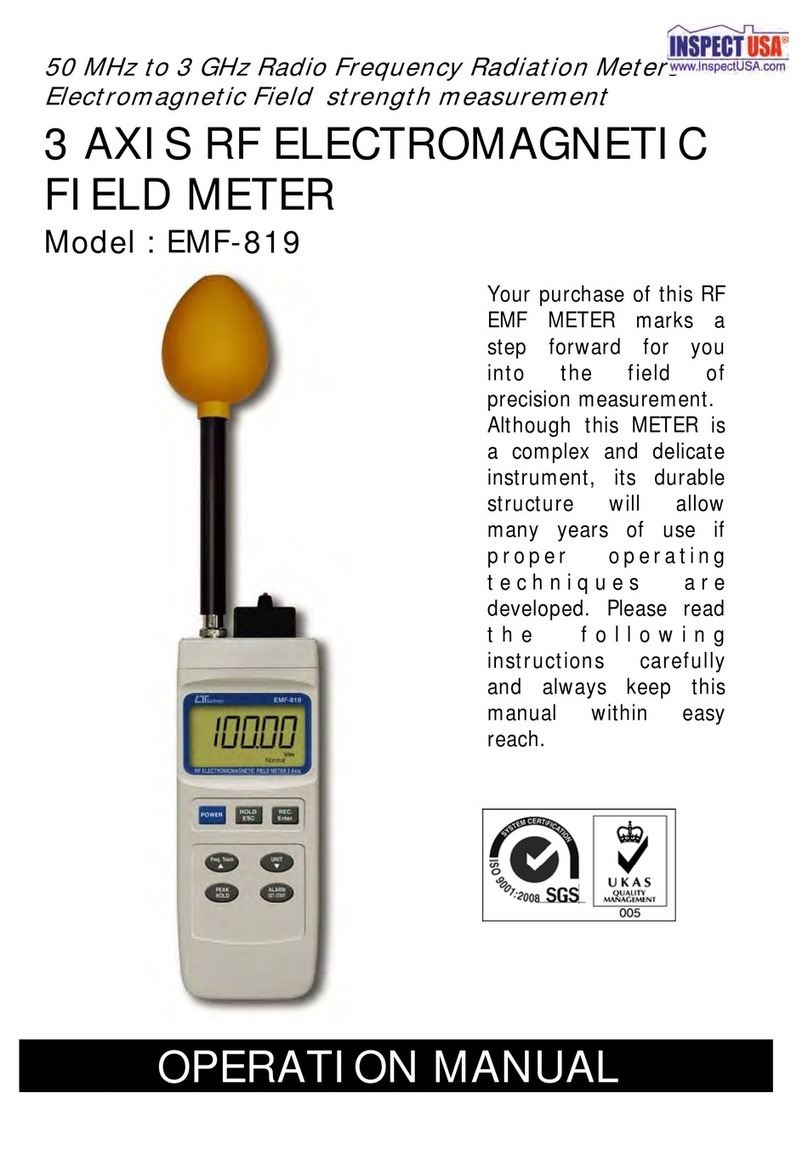
Lutron Electronics
Lutron Electronics EMF-819 Operation manuals
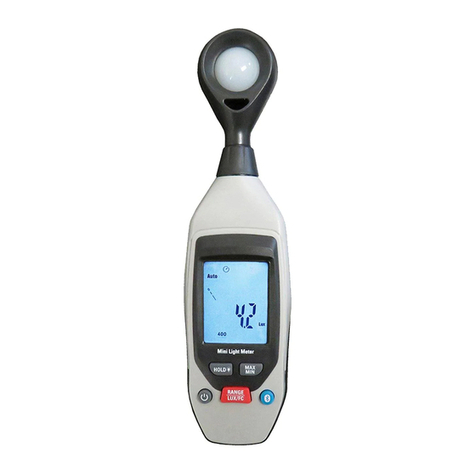
Sper scientific
Sper scientific 850004 instruction manual
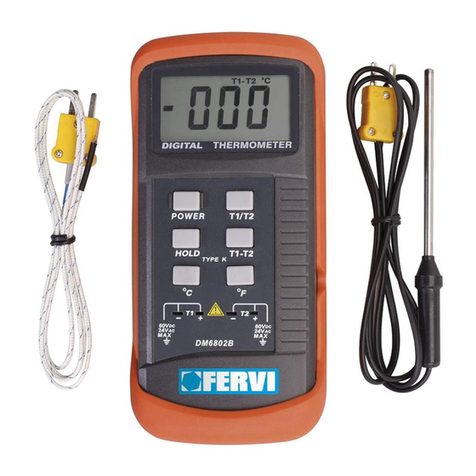
Fervi
Fervi T063 Operation and maintenance manual
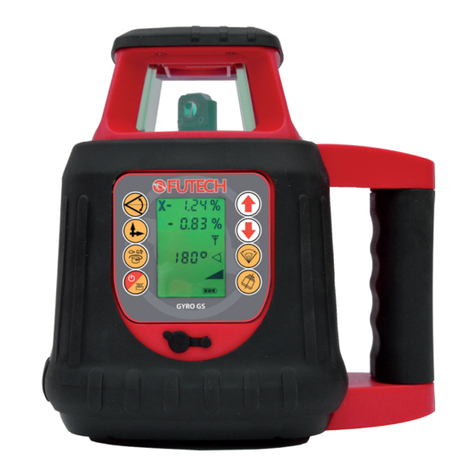
Futech
Futech Gyro GS user manual
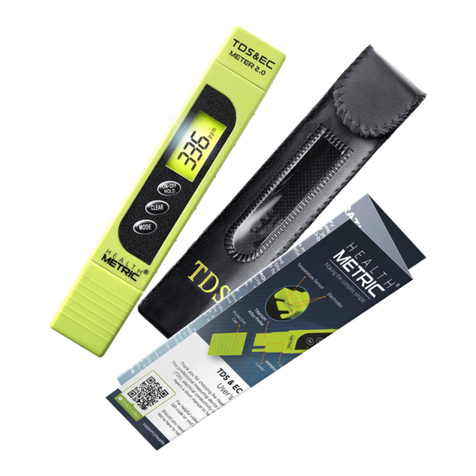
Health Metric
Health Metric TDS & EC METER 2.0 user manual