TCS 700-30 Instruction manual

TCS900003, Rev.6
04/26/2016
Check us out at www.TCSmeters.com!
Catalog Title
CatalogSubtitle
Installation, Operation &
Maintenance Manual
700-30/35
Rotary Meter

TCS900003, Rev.6
04/26/2016
Check us out at www.TCSmeters.com!
Page 2
Table of Contents
Warning Symbols
CAUTION
Follow the warning instructions within the
following information to avoid equipment
failure, personal injury or death.
TURN POWER OFF
Before performing any maintenance, be sure to
turn system power off to avoid any potential
electric spark
FLAMMABLE
Flammable liquids and their vapors may cause a
fire or explosion if ignited.
EYE PROTECTION
Pressurized systems may cause hazardous leaks
and spray that may be dangerous for your eyes.
Always wear eye protection around pressurized
systems and its hazardous liquids.
INJURY
Wear gloves for protection from hazardous
liquids that may cause irritation or burns.
READ
Read and understand all related manuals
thoroughly. The Engineering and OIM manuals
will provide the knowledge for all systems,
maintenance and operation procedures. If you
have any questions, please consult the factory.
Safety Warning Symbols 2
Receipt & Inspection
3
Notice 3
Meter Overvie 4
Meter Specifications
5
Meter Types
5
Material of Construction
6
System Recommendations
6
System Recommendations (Continued)
7
System Recommendations (Continued)
8
Above Ground Storage System
9
Mobile Fueling System
10
Start Up Recommendations 11
Start Up Recommendations (Continued) 12
Direction of Flo 12
Meter Calibration
13
Meter Calibration (Continued)
14
Meter Calibration (Continued) 15
Calibration Adjustment 15
Split Compartment Testing 16
Split Compartment Testing (Continued) 17
Split Compartment Testing (Continued) 18
Maintenance 19
Maintenance (Continued) 20
Storage Instructions 20
Dimensions 21
Meter Assembly 22
Meter Assembly (Continued) 23
Air Eliminator Assembly 24
Air Eliminator Assembly (Continued) 25
Strainer / High Volume Strainer Assembly 26
Strainer / High Volume Strainer Assembly (Continued) 27
Hydraulic Preset Valve Assembly
28
Hydraulic Preset Valve Assembly (Continued)
29
Air Check Valve Assembly 30
Torque Specifications
31
Drive Components 32
Disassembly of Meter 33
Disassembly of Meter (Continued) 34
Disassembly of Meter (Continued) 35
Inspection of Parts 36
Reassembly of Meter 37
Reassembly of Meter (Continued) 38
Reassembly of Meter (Continued) 39
Reassembly of Meter (Continued) 40
Disassembly of Strainer 41
Reassembly of Strainer 41
Disassembly of Air Eliminator 42
Reassembly of Air Eliminator 42
Disassembly of Hydraulic Preset Valve 43
Disassembly of Hydraulic Preset Valve (Continued) 44
Reassembly of Hydraulic Preset Valve 44
Seal Replacement for Hydraulic Valve 45
Disassembly of Air Check Valve 46
Reassembly of Air Check Valve 46
Meter Trouble Shooting 47
Air Eliminator Trouble Shooting 48
Hydraulic Preset Valve Trouble Shooting 49
Air Check Valve Trouble Shooting 49
Material Safety Data Sheet 50
MSDS (Continued) 51
MSDS (Continued) 52
MSDS (Continued) 53
Notes 54
Warranty 55

TCS900003, Rev.6
04/26/2016
Check us out at www.TCSmeters.com!
Page 3
Receipt & Inspection
Upon receipt of meter shipment, be sure to inspect the packaging and the flow meter assembly for any damage
before signing the receipt of the shipment. Notify the delivery company about possible damage and refuse
receipt of the shipment.
Meters are individually boxed and are protected with packing material. Each package is identified with the flow
meter assembly part number, description, direction of flow and serial number. Verify the meter model is the
correct model, size, and configuration as ordered. Contact your distributor if there is any discrepancy or
question.
Meter assemblies should be handled with appropriate methods for the awkwardness of size and weight involved.
Appropriate clothing and shoes need to be utilized. Transport the meter package to the installation site with
appropriate transportation methods, careful not to damage the flow meter.
Be careful of any loose or protruding staples from the packaging, as they can be very sharp and may potentially
cause injury.
If foam has been used to protect meter, carefully remove top foam layer before attempting to remove meter
assembly from box. Foam packaging maybe formed around the meter assembly making it difficult to remove.
If meter is bolted to a wood pallet remove bolts while being careful not to let the meter tip over when the
support has been removed. Do not lift the meter assembly by flex hoses, thermowells, wires, pulsers, or put
objects through meter. Removing meter assembly from packaging without regard to these warnings may cause
serious injury.
The wooden pallets and bases meet the ISPM 15; Guidelines for Regulating Wood Pac aging Material in
International Trade through the Timber Products Inspection Company (TP #2134).
Every effort has been made to remove the test fluid before shipment. All TCS flow meters are plugged and
enclosed in a plastic bag. The test fluid Material Safety Data Sheet (MSDS) can be reviewed on page 50.
Appropriate precautions should be taken regarding any personal, environmental and material compatibility with
the end use system.
Notice
Total Control Systems (TCS) shall not be liable for technical or editorial errors in this manual or omissions from
this manual. TCS makes no warranties, express or implied, including the implied warranties of merchantability and
fitness for a particular purpose with respect to this manual and, in no event, shall TCS be liable for special or
consequential damages including, but not limited to, loss of production, loss of profits, etc.
The contents of this publication are presented for informational purposes only, and while every effort has been
made to ensure their accuracy, they are not to be construed as warranties or guarantees, expressed or implied,
regarding the products or services described herein or their use or applicability. We reserve the right to modify or
improve the designs or specifications of such products at any time.
TCS does not assume responsibility for the selection, use or maintenance of any product. Responsibility for proper
selection, use and maintenance of any TCS product remains solely with the purchaser and end-user.
All rights reserved. No part of this work may be reproduced or copied in any form or by any means – graphic,
electronic or mechanical – without first receiving the written permission of Total Control Systems, Fort Wayne,
Indiana USA.

TCS900003, Rev.6
04/26/2016
Check us out at www.TCSmeters.com!
Page 4
Meter Overview
The TCS Model 700 series flow meter is a simple and
efficient design. The meter consists of a single fluid
chamber that contains a single blocking rotor and two
displacement rotors whose rotation is synchronized
with mating gears. As the fluid enters the fluid
chamber, the blocking rotor is forced to rotate. The
displacement rotors, also rotating in conjunction with
the blocking rotor help direct the fluid flow through
the chamber and to the outlet. The linear flow of the
fluid is thus translated into rotary motion in the meter.
The output of the meter is picked up from the rotation
of the blocking rotor and transmitted to a register or
pulse transmitter.
The rotors in the meter are designed to operate at close tolerances to one another and the
wall of the fluid chamber. There are slight clearances between the rotors and the chamber
wall. Because of this, it is important that the meter be properly applied for the flow rate
and operating pressure of the system.
Because the fluid flowing through the meter is redirected only slightly from its natural
flow, there is very little pressure drop across the meter, unlike other meters that use
multiple measuring chambers.
The meter design uses high performance materials for the rotor bearings and journals.
Since there is no contact between the rotors and the fluid chamber wall, these critical
components have a long life expectancy.
Calibration of the meter involves adjusting the rotation of the output shaft relative to the
rotation of the internal rotors of the meter. This is accomplished by changing the settings
on an adjuster device. Calibration of the meter is discussed in detail in the section Meter
Calibration.
FLOW ILLUSTRATION

TCS900003, Rev.6
04/26/2016
Check us out at www.TCSmeters.com!
Page 5
Meter Specifications
Flange Connection: 3” NPT Flange Connection, 2” NPT Flange. Optional BSPT,
Slip Weld or ANSI flanges available upon request.
Flow Rate: 700-30 up to 200 GPM (760 LPM)
700-35 up to 300 GPM (1135 LPM); only for fluids under 225
SSU
Maximum Pressure: 150 PSI (10.5 BAR)
Working Temperature: -20 F to 160 F (-28.9 C to 71 C)
-40 F to 160 F (-40 C to 71 C) with low temperature seal kit
Meter Types
SP - Standard Petroleum
For metering refined petroleum products such as Gasoline, Fuel Oils, Diesel, Bio-Diesel, Kerosene,
Vegetable Oils, Motor Oils, Naptha, Ethylene Glycol (Antifreeze), etc.
SPA - Standard Petroleum (Aviation)
For metering refined petroleum products such as Aviation Gasoline, Jet Fuels, Ethanol, Gasoline, Fuel
Oils, Diesel, Bio-Diesel, Kerosene, Vegetable Oils, Motor Oils, Naptha, Ethylene Glycol, etc.
SPD - Standard Petroleum (Ductile Iron)
For metering refined petroleum products such as Ethanol, Methanol, Gasoline, Fuel Oils, Diesel,
Bio-Diesel, Kerosene, Aviation Gasoline, Vegetable Oils, Motor Oils, Naptha, Ethylene Glycol, etc.
AF - All-Ferrous
For metering Pesticides, Fertilizers, Food Processing Liquids, Industrial Chemicals, Solvents, Paints,
Inks, Alcohols and many other liquids such as Liquid Sugars, Liquid Feeds, MEK, Ethanol, Corn Syrup,
Soy Bean Oil, Shortenings, Latex Products, Adhesives, Naptha, etc.
IP - Industrial Products
For Food Processing, Chemicals, General Solvents and many other liquids such as Corn Syrup, Soy Bean
Oil, Liquid Sugars, Shortenings, Latex Products, Adhesives, etc.
IC - Industrial Products (Carbon Bearings)
For metering Alcohols, Chemicals, Solvents, Water and many other non-lubricating liquids, such as
Acetones, Ethanol, Naptha, Xylene, MEK, Toluene, Resins, etc.

TCS900003, Rev.6
04/26/2016
Check us out at www.TCSmeters.com!
Simriz®is a registered trademark of Freudenberg-NOK.
Page 6
Material of Construction
Description SP SPA SPD IP IC AF
Housing
Hardcoat
Anodized
Aluminum
Hardcoat
Anodized
Aluminum
Ductile Iron
Hardcoat
Anodized
Aluminum
Hardcoat
Anodized
Aluminum
Ductile Iron
Rotors
Hardcoat
Anodized
Aluminum
Hardcoat
Anodized
Aluminum
Ni-Resist
Hardcoat
Anodized
Aluminum
Hardcoat
Anodized
Aluminum
Ni-Resist
Rotor
Journals Plated SS Plated SS Plated SS Plated SS Plated SS Plated SS
Bearing Plates Ni-Resist Ni-Resist Ni-Resist Ni-Resist Ni-Resist Ni-Resist
Bearing
Sleeves Ni-Resist Carbon
Graphite
Carbon
Graphite Ni-Resist Carbon
Graphite
Carbon
Graphite
Timing Gears Stainless
Steel
Stainless
Steel
Stainless
Steel
Stainless
Steel
Stainless
Steel
Stainless
Steel
Packing Seal FKM FKM Simriz® Simriz® Simriz® Simriz®
Body
O-rings FKM FKM FKM PTFE PTFE PTFE
Meter Selection
The flow meter must be carefully chosen from the Meter Selection factors in the Engineering Manual.
The meter must be selected based on the operating system and product characteristics. System variables
include flow rate, temperature and pressure. Product characteristics include the material compatibility,
lubricity, viscosity, presence of suspensions, pH, and whether the product can congeal, crystallize or leave
a dry film. Failure to select the correct flow meter may result in system failure or serious injury.
Air Elimination
In any system where the supply tank may be completely drained or multiple products manifold into one
metering system, the possibility of air being introduced into the fluid piping increases. The solution is to
utilize an air or vapor eliminator in the system, located upstream of the flow meter. The purpose of this
device is to vent the air or vapor from the system before it can be measured by the meter. Air or vapor
elimination is required for all weights and measures regulatory approvals in custody transfer applications.
System Recommendations

TCS900003, Rev.6
04/26/2016
Check us out at www.TCSmeters.com!
Page 7
System Recommendations Continued)
Control Valves
Safety and isolation valves should be used throughout the metering system. In any pumping system where
there is one (1) pump and multiple flow meters, a digital or hydro-mechanical Rate-of-Flow control valve
must be used at each flow meter to prevent over-speeding of the flow meters.
Best Plumbing Configuration
1) The flow meter must be securely mounted to a riser or foundation.
2) The inlet and outlet piping must be securely supported, in such a manner so as to avoid pipe stress on
the flow meter.
3) The system should be designed to keep the flow meter full of liquid at all times.
4) System piping should have full 3” pipe diameter throughout the metering system to allow for minimal
pressure loss.
5) The pipe should be laid out as straight as possible to reduce pressure loss from flow restriction.
6) The meter and piping must be installed in such a way so as to avoid accidental draining of the meter.
The inlet and outlet of the meter should be lower than the associated system plumbing. This is known
as the sump position.
7) It is not necessary for the air eliminator to be installed directly adjacent to the meter. It can be
installed upstream from the meter. For effective operation of the air eliminator, it should be mounted
between the meter and any valves, tees or any other potential places where air may enter the system.
8) The metering system should include a means for calibration.
Protection From Debris
On new installations, care must be taken to protect the meter from damage during start-up. It is
recommended that a strainer be installed in the system upstream from the meter. The meter could be
subject to damage from the passage through of dirt, sand, welding slag or spatter, thread cuttings, rust, etc.
A spool can be fabricated and installed in place of the meter until the system is flushed. A spool is a
flanged length of pipe equal in length to the meter and any accessories attached to the meter such as an air
eliminator or control valve. Another method is to temporarily bypass the plumbing containing the meter
until the system is flushed. This will also protect the meter from debris. Once the system has run “clean”
for a period of time the meter may be reinstalled or protective means removed.
Thermal Expansion
Most liquids will expand and contract with temperature. In any system where there is a chance for liquid
to be captured between closed valves without relief, thermal expansion will likely occur. This can create
dangerously high pressures within the system. When product is trapped within the system, the pressure
will increase as temperature increases.
Care should be taken in designing the system in which thermal expansion may occur by implementing
Pressure Relief Valves or Thermal Expansion Joints in the system design.

TCS900003, Rev.6
04/26/2016
Check us out at www.TCSmeters.com!
Page 8
Thermal Shock
The metal parts within the flow meter will expand or contract with variations in the system operating temperature.
For any systems where sudden or immediate temperature increases of 68 F (20 C) degrees or more are
possible, the meter will require clearance rotors. The extra clearance will be necessary to eliminate the
effects of immediate expansion of the rotors vs. the meter body, caused by thermal shock.
Hydraulic Shock (Water Hammer)
Hydraulic shock is a rise in pressure, which happens when an operating system undergoes an immediate
change in flow direction. This is most often the result of a rapid valve closure while the system is
operating at a high flow rate. Hydraulic shock can damage any system component. Particularly
susceptible are internal components of the meter, valves, and pump. System design and improper
operating procedures will contribute to the seriousness of this problem. In order to eliminate hydraulic
shock, the valve closure rate must be slowed. The use of 2-stage preset control valves or surge
suppressing bladders or risers will help reduce or eliminate this problem.
Products that Dry/Congeal/Crystallize
There are many liquids that crystallize, harden and/or solidify on contact with air or with an increase in
temperature. A proper system design and a good understanding of the product being measured will help
to avoid the possibility of air entering into the system and the product and effective operation of the meter
being affected.
Calibration
The meter shall be tested and calibrated with the product it is intended to measure when installed. Total
Control Systems shall not be responsible for loss of product or any damages resulting from the end user’s
failure to test this meter to insure proper calibration. Every 700 series meter is tested at the factory to
prove that the meter can be calibrated in your system. It is the owner’s responsibility to report this device
to the local Weights and Measures officials for their inspection before the meter is put to use.
System Recommendations Continued)

TCS900003, Rev.6
04/26/2016
Check us out at www.TCSmeters.com!
Page 9

TCS900003, Rev.6
04/26/2016
Check us out at www.TCSmeters.com!
Page 10

TCS900003, Rev.6
04/26/2016
Check us out at www.TCSmeters.com!
Page 11
Start up Recommendations
Start-up instruction for new installations or after maintenance and repairs:
1) Only properly trained personal should design, install, or operate metering system.
2) Remove plastic threaded plugs placed in meter for shipping protection. They are not to be used in
meter system because of the PVC plugs low rated pressure, compatibility, and sealing issues.
3) Place the meter in an area with ample workspace, secure from vibration, and pipe line stress. Mount
and bolt down on to a fixed stand or platform. This prevents meter stress, which will cause leakage
and metal fatigue.
4) Apply thread sealing compound and gasket materials that are compatible with product.
5) Do not weld to meter or meter accessories such as valves and air eliminators. This will weaken
housings, cause O-ring and casting leaks and potentially distort the critical tolerances within the flow
meter.
6) Always wear personal safety protection equipment such as goggles, steel toed shoes, gloves and full
body clothing.
7) Be sure to install a pressure relief valve or expansion joint in the system to protect against thermal
expansion.
8) Make sure all system components are properly secured and tightened.
9) All meter assembly bolts and connections are tight.
10) The air eliminator vapor release must be properly vented to atmospheric pressure and piped into a
reservoir container or back to the supply tank.
11) Electrical connections are properly installed and start/stop switches are off and locked-out.
12) Ensure that there is flooded suction to the Pump and that fluid is available to system to prevent the
starving or cavitation of the pump.
13) Flood the system slowly. Start the system with all shut off valves in the closed position. When a
pump is turned on and a valve opened in a new, dry system, tremendous liquid and air pressure can
build up in the piping and be forced through the meter. The high pressure and volume of air causes
the meter to rotate more rapidly than normal. When the fluid product reaches the meter, there is an
abrupt slowing of the meter rotor. This can cause damage to the register, rotor shafts, packing gear
and/or blade, timing gears and other components.
The recommended method of starting any system is to flood the piping gradually. This allows
product to slowly force the air from the entire system.
¡WARNING!
Test equipment should be grounded to prevent a possible spark. Test area should have no ignition source. Operators should
wear personal protection and prevent any product exposure and environmental issues.

TCS900003, Rev.6
04/26/2016
Check us out at www.TCSmeters.com!
Page 12
Start-Up Recommendations CONTINUED)
Direction of Flow
The meter is set up at the factory for left to right flow. To change the meter for right to left flow, begin
by removing the screws (#9 on the Meter Assembly Breakdown) and the adjuster cover plate (#7) on the
front of the meter. Remove the screws (#1), the drive shaft retainer (#10), the drive shaft (#3), the e-ring
(#4) and the face gear (#5). Reinstall the gear on the shaft with the gear teeth facing up. Snap the e-ring
back into place to hold the gear in place. Reinstall the shaft, mating the face gear with the drive gear of
the packing capsule assembly. Reinstall the screw and cover plate. The meter will now be set up for
right to left flow. See Page 22 for a parts breakdown of entire meter assembly.
14) When operating the meter with accessories, valves should be opened slowly to avoid a pressure
surge that can damage the meter or air eliminator. System pressures should be maintained below
70 PSI (4.9 BAR).
15) Custody transfer metering systems must be calibrated by a regulatory agency before product can
be sold off the meter. Contact your local authorities for proper calibration.
16) Strainers should be cleaned frequently as part of a regular maintenance schedule. Doing so
will ensure a clean system and long service life.

TCS900003, Rev.6
04/26/2016
Check us out at www.TCSmeters.com!
Page 13
Meter Calibration
The method of proving should be selected, and necessary provisions made, during the design stage of the
installation. Of the most commonly used systems, portable provers have the advantage of more closely reproducing
the conditions under which the product is normally delivered.
Use an Accurate Prover
Scientifically designed provers are commercially available for proving meters, and no other kind should be used.
Scientifically designed test measures have proper drainage means built into them, a calibration gauge glass neck
and protection against deformation (which would cause volume changes).
Scientifically designed provers are not merely truck compartments or drums. A “homemade” prover, whether a
drum or a tank is not likely to be satisfactory, and may cause expensive errors due to inaccurate meter calibration.
Even scientifically designed provers should be checked periodically for accuracy. Weights and Measures officials
have been very cooperative in giving assistance to checking privately owned volumetric provers.
Recommended size of test measure
The prover capacity should be equal to at least one minute’s flow through the meter at its maximum rate.
Setting the Prover
The prover should be set level, using the levels provided on the prover, or separate leveling means. This insures
consistent results when moving the prover from meter to meter and provides the basis for accurate readings on the
prover scale.
Where to Test a Meter
The best place to test a meter is in its normal operating position, instead of a test stand. In this way, the correctness
of the installation and of the operating conditions of the system will be verified by the test. Always test a meter with
the same liquid it is to measure. Even slight differences in viscosity, temperature or system plumbing can have a
significant effect on meter accuracy.
Discharge Line from Meter
Where a portable prover is used, the liquid is generally discharged into the prover in the same manner as a normal
delivery would be made (with a hose reel and nozzle, for example). Where a special delivery test connection is
used, the discharge line must be arranged to drain to the same point on each test. The meter flow rate and start and
stop must be controlled at the end of the discharge line.
Wetting the Prover
Reset the meter register to zero, and fill the prover to the zero line or 100% marking of the scale. Disregard this
meter reading. Drain the prover and reset the register. The reason for disregarding the first meter reading is that
the prover must be wetted. The calibrated capacity of the prover has been determined by its manufacturer based its
wet measure capacity. Once wetted, the prover will be wet for all the subsequent tests to be run.
Allow the prover to drain for a set amount of time before closing the dump valve. 30 seconds is a commonly used
time interval. However, you must ensure that the prover is completely empty prior to closing the dump valve. This
time interval must be the same for each test to ensure uniform results. If a considerable length of time is to elapse
between tests (lunch break or phone call), the wetting operation can be eliminated by allowing the prover to remain
full until the next test is to be run.

TCS900003, Rev.6
04/26/2016
Check us out at www.TCSmeters.com!
Page 14
Meter Calibration Continued)
Making the Tests
Reset the register to zero, and run the required test quantity through the meter. Do not exceed the maximum
recommended rate of flow for the meter. Maximum and minimum recommended rates of flow for each 700 series
flow meter is marked on the meter identification plate and also in the maintenance manual.
Determining Test Results
Run the meter close to the mark on the indicator corresponding to the full prover capacity. Read the over or under
delivery in cubic inches, gallons or percent on the calibrated plate on the neck of the prover. If the plate is
calibrated in cubic inches, the percentage error can readily be computed on the following basis:
One gallon is equal to 231 cu.in.
Example: A 100-gallon prover holds 23,100 cu.in. Therefore, 23.1 cu.in. represents 0.1% error.
Meter Tolerance
In the United States, the National Institute of Standards and Technology, in NIST Handbook 44 specifies plus or
minus tolerances according to the following:
In Europe, the plus or minus meter tolerances are specified by OIML R117-1. In Canada, the plus or minus toler-
ances are specified by the National Measurement Act.
Acceptance tolerances apply to new meters and repaired meters after reconditioning. Maintenance tolerances apply
to meters already in service. Special tolerances apply to meters in the United States only, for special instances as
determined by weights and measures officials.
Changing Meter Calibration
Refer to meter literature for method of changing meter calibration. Any change in the meter calibration adjustment
will change the delivery in the same amount for all rates of flow. That is, the calibration curve retains its shape, but
is moved up or down. Therefore, if a meter tests satisfactorily at full flow, but drops off too much at low flow,
changing the calibration will not remedy this condition; it will bring the low flow test to 100%, but it will also bring
the full flow above 100% by the same amount that the low flow was raised. A condition of this kind is caused either
by the metering system, need for meter cleaning or repairs, or because of an attempt to retain accuracy below the
minimum recommended rate of flow for the meter.
Repeatability
Consider the percentage error readings from each test run made at the same flow rate and draft size (calibration
run). The difference between the reading with the highest value and that with the lowest value must be less than a
value which is 40% of the applicable maintenance tolerance. For example, a meter in the USA, this would be
0.12% (0.30% x 0.4 = 0.12%). The percentage error of all test runs at each flow rate must still be within the
applicable tolerance.
Tolerance
Acceptance Test Maintenance Test Special Test Repeatability
USA-Wholesale +/- 0.20% +/- 0.30% +/- 0.50% 0.12%
USA-Vehicle +/- 0.15% +/- 0.30% +/- 0.45% 0.12%
Indication of Device
Tolerance
Acceptance Test Maintenance Test Special Test Repeatability
Europe +/- 0.30% +/- 0.50% N/A 0.20%
Canada +/- 0.1875% +/- 0.375% N/A 0.15%
Indication of Device

TCS900003, Rev.6
04/26/2016
Check us out at www.TCSmeters.com!
Meter Calibration Continued)
One complete turn of the adjuster barrel is equal to 1 gallon in 100 gallons or 1% of delivered volume. The
adjuster body will show divisions of 1%, while the adjuster barrel has divisions of 0.02%. For volumes other
than 100 gallons, the following formula may be used to calculate the Adjuster percent to increase or decrease
prover volume.
Volume on Prover minus Volume on Meter Counter
Volume on Meter Counter
Page 15
Calibration Adjustment
Temperature Correction
If the testing conditions are such that the temperature of the liquid differs by more than a few degrees between the
meter and the prover, it is advisable to apply temperature correction to the prover readings. Thermowells must be
installed into the system and temperature readings must be taken during test runs at the meter and in the prover.
Corrections are made by the use of API Volume Correction Factor Tables.

TCS900003, Rev.6
04/26/2016
Check us out at www.TCSmeters.com!
Page 16
Split Compartment Test
Purpose: A product depletion test verifies the proper operation of the air elimination system when the
storage tank for the product being measured is pumped dry. This test is necessary for meters that may
drain a tank completely, such as a vehicle tank meter.
Multiple-Compartment Test Procedure:
1) Begin the test from a compartment (ideally the largest compartment) containing an amount of fuel
equal to or less than one-half the nominal capacity of the prover being used. Operate the meter at the
normal full flow rate until the compartment is empty. There are several methods for determining that
the compartment is empty. There may be a significant change in the sound of the pump. There may
be visual evidence that the compartment has run dry. The meter register may stop entirely or may
begin to count erratically (pause, resume running, then pause, then run again.)
2) Continue the test until the meter indication stops entirely for at least 10 seconds. If this occurs,
proceed to Step 3. If the meter indication fails to stop entirely for a period of 10 seconds, continue to
operate the system in this condition for 3 minutes.
3) Close the valve from the empty compartment, and if top filling, close the nozzle or valve at the
end of the delivery hose. Open the valve from another compartment containing the same product.
Carefully open the valve at the end of the delivery hose. Pockets of vapor or air may cause product
to splash out of the prover. The test results may not be valid if product is splashed out of the prover.
Appropriate attire and protection is required, and always use caution.
4) Continue delivering product at the normal full flow rate until the liquid level in the prover reaches the
nominal capacity.
5) Close the delivery nozzle or valve and stop the meter. Allow any entrained air to settle, then read the
prover sight gauge.
6) Compare the meter indication with the actual delivered volume in the prover.
7) Calculate the meter error. Apply the Product Depletion Test Tolerance to determine whether the
meter error is within acceptable limits. Refer to NIST Handbook 44 for further information.
Product Depletion Test Tolerance for Vehicle-Tank Meters:
Marked Maximum Flow Rate Product Depletion Test Tolerance
Less than 100 GPM (380 LPM) 0.5%
100 GPM (380 LPM) or greater 0.6%
The results of the product depletion test may fall outside of the applicable test tolerance as this is a
stand-alone test.
The test draft should be equal to at least the amount delivered by the device in 1 minute at its
maximum discharge rate, and in no case should it be less than 50 gallons.

TCS900003, Rev.6
04/26/2016
Check us out at www.TCSmeters.com!
Page 17
Split Compartment Test Continued)
Single Compartment Test Procedure:
The test of single-compartment tanks is easier to accomplish if there is a quick-connect hose coupling
between the compartment valve and the pump that supplies product to the meter. If the system does not
have quick-connect couplings between the compartment and the meter, an additional source of sufficient
product at the test site is required.
Without a quick-connect coupling:
1) Begin the test from a compartment (ideally the largest compartment) containing an amount of fuel
equal to or less than the nominal capacity of the prover being used. Operate the meter at the
normal full flow rate until the compartment is empty. There are several methods for determining that
the compartment is empty. There may be a significant change in the sound of the pump. There may
be visual evidence that the compartment has run dry. The meter register may stop entirely or may
begin to count erratically (pause, resume running, then pause, then run again.)
2) Continue the test until the meter indication stops entirely for at least 10 seconds. If this occurs,
proceed to Step 3. If the meter indication fails to stop entirely for a period of 10 seconds, continue to
operate the system in this condition for 3 minutes.
3) Close the valve from the empty compartment, and if top filling, close the nozzle or valve at the
end of the delivery hose. Stop the pump and load sufficient product from the alternate source into the
supply compartment that feeds the meter being tested. Allow a brief time for the product to stand in
the compartment to allow entrained vapor or air to escape.
4) Open the compartment valve and restart the pump without resetting the meter to zero. Carefully
open the nozzle of valve at the end of the delivery hose. Pockets of vapor or air may cause product to
splash out of the prover. The test results may not be valid if product is splashed out of the prover.
Appropriate attire and protection is required, and always use caution.
5) Continue delivering product at the normal full flow rate until the liquid level in the prover reaches the
nominal capacity.
6) Close the delivery nozzle or valve and stop the meter. Allow any entrained air to settle, then read the
prover sight gauge.
7) Compare the meter indication with the actual delivered volume in the prover.
8) Calculate the meter error. Apply the Product Depletion Test Tolerance to determine whether the
meter error is within acceptable limits. Refer to NIST Handbook 44 for further information.

TCS900003, Rev.6
04/26/2016
Check us out at www.TCSmeters.com!
Page 18
Split Compartment Test Continued)
With a quick-connect coupling:
1) During a normal full flow test run, close the compartment valve when the prover is approximately
one-half full to its normal capacity. Then slowly and carefully disconnect the quick-connect
coupling, allowing the pump to drain the supply line.
2) Continue the test until the meter indication stops entirely for at least 10 seconds. If the meter fails
to stop entirely for at least 10 seconds, continue to operate the system for 3 minutes.
3) After 10 seconds (or 3 minutes if the meter indication did not stop entirely), close the delivery
nozzle or valve at the end of the delivery hose if top filling.
4) Disconnect and reconnect the quick-connect coupling and open the compartment valve.
5) Carefully open the nozzle or valve at the end of the delivery hose. Pockets of vapor or air may
cause product to splash out of the prover. The test results may not be valid if product is splashed
out of the prover. Appropriate attire and protection is required, and always use caution.
6) Continue the delivery of product at the normal full flow rate until the liquid level in the prover
reaches the prover’s nominal capacity.
7) Close the delivery nozzle or valve. Stop the pump. Allow any entrained air to settle, then read the
prover sight gauge.
8) Compare the meter indication with the actual delivered volume in the prover.
9) Calculate the meter error. Apply the Product Depletion Test Tolerance to determine whether the
meter error is within acceptable limits. Refer to NIST Handbook 44 for further information.
Product Depletion Test Tolerance for Vehicle-Tank Meters:
Marked Maximum Flow Rate Product Depletion Test Tolerance
Less than 100 GPM (380 LPM) 0.5%
100 GPM (380 LPM) or greater 0.6%
The results of the product depletion test may fall outside of the applicable test tolerance as this is a
stand-alone test.
The test draft should be equal to at least the amount delivered by the device in 1 minute at its
maximum discharge rate, and in no case should it be less than 50 gallons.

TCS900003, Rev.6
04/26/2016
Check us out at www.TCSmeters.com!
Page 19
Maintenance
¡WARNING!
Test equipment should be grounded to prevent a possible spark. Test area should have no ignition source. Operators should
wear personal protection and prevent any product exposure and environmental issues.
1) Keeping accurate maintenance and calibration records can be an excellent tool in determining the
frequency of inspection or maintenance for a system. As the meter wears, the calibration will be
affected and require adjustment. A personality profile can be created for each meter to help guide in
a maintenance schedule.
2) Great care should be utilized in the maintenance of the metering system. Personal safety protection,
environmental hazards, and government regulations need to be the foremost priority. Only fully
trained personnel should be involved in maintenance. Failure to use original TCS replacement parts
will void any Weights and Measures approvals, warranty and risk damage to the meter system.
3) ALWAYS RELIEVE INTERNAL SYSTEM PRESSURE TO ZERO BEFORE DISASSEMBLY
OR INSPECTION.
4) SERIOUS INJURY OR DEATH FROM FIRE OR EXPLOSION COULD RESULT FROM
MAINTENANCE OF AN IMPROPERLY DEPRESSURIZED AND EVACUATED SYSTEM.
5) Total Control Systems flow meters and accessories are often used with petroleum, solvents,
chemicals, and other liquids that may be explosive, extremely flammable, very toxic, oxidizing, and
corrosive. Severe injury or fatalities may arise if appropriate safety precautions are not followed.
6) Before replacing or cleaning filter/strainer screen, the electrical system must be turned off. Product
must be drained from system. Collect all product and return to storage or dispose of properly.
Replace all drain plugs that were removed. Personal safety protection must be warn at this time.
Make sure there is adequate ventilation in the area. The metering system will not completely drain
so extra product must be collected when the strainer cover is removed. Clean the screen once a
week, or more often if there is a lot of sediment in the system. Ensure that there is no ignition
source and that the system is grounded. Replace all plugs that were removed for drainage.
7) The metering system is heavy and awkward so take precaution to handle it properly.
8) Do not use force to disassemble or use a screwdriver to pry open any part of the metering system.
Have the proper tools available before trying to repair the meter system. Use caution when handling
the internal parts as they can be sharp and heavy. Do not drop the housing or rotors as they can
cause injury and can be damaged or destroyed. Use caution when inspecting and aligning the timing
gears and rotors as they can pinch fingers. Turn these slowly to verify smooth operation.
9) When inspecting the spring loaded preset valves do not place anything inside the housing, as the
action of the valve will pinch this object when the valve closes.

TCS900003, Rev.6
04/26/2016
Check us out at www.TCSmeters.com!
Page 20
Maintenance CONTINUED)
10) When removing gaskets or O-rings, carefully check for damage or corrosion. Any cracked, rough,
worn, elongated or swollen O-rings must be replaced. When replacing the O-rings, place grease
along the inside of the O-ring groove or completely around the O-ring to help the O-ring stay in the
O-ring groove during assembly. If an O-ring is pinched or not in the O-ring groove, the meter
system will leak and cause serious problems to the environment and equipment. Collect all replaced
parts and dispose of properly.
11) Do not weld onto any part of the meter system or accessories as this will weaken the part and allow
for leaks.
12) Bolts and screws must be coated with Anti-Seize lubricant. Follow the torque specifications for
each flow meter, air eliminator, strainer or preset valve bolt found on page 31.
13) Recommended levels of maintenance and inspection will depend upon the system variables, such as
the characteristics of the products being measured (viscosity, corrosiveness, suspensions, etc.),
system pressure requirements, government or company regulations, and the age of the metering
system. If hydrostatic testing is required, the system pressure should not exceed 1.5 times the
marked meter pressure. It is not recommended to pneumatically test the meter system at any time.
14) If any component of the meter system is removed from the system, it should be thoroughly flushed
with a compatible liquid. After this is done, immediately refill the meter or accessory with a
compatible liquid to prevent corrosion and water build up.
¡WARNING!
Test equipment should be grounded to prevent a possible spark. Test area should have no ignition source. Operators should
wear personal protection and prevent any product exposure and environmental issues.
Storage Instructions
Short periods of non-use of the meter (a week or less) should present no problem, provided that the meter re-
mains full of product. For long periods of non-use, such as winter storage, the following procedure is recom-
mended.
1). To store the meter when it is left in line, flush the system with clean water until 70-80 gallons of water
have passed through the meter.
2). Pump a 50% anti-freeze / 50% water solution through the entire system (100% RV antifreeze may be used
instead). With the pump running, shut off a valve downstream from the meter, making sure that the
system is full of anti-freeze solution to that point. Then close an upstream valve, such that the meter
remains full of anti-freeze solution.
3). Remove the register from the meter, and lubricate the drive coupling shaft. After lubrication, reassemble
the register onto the meter.
When starting the system after a period of storage, it is recommended that the meter calibration be rechecked.
Other manuals for 700-30
1
This manual suits for next models
1
Table of contents
Other TCS Measuring Instrument manuals
Popular Measuring Instrument manuals by other brands
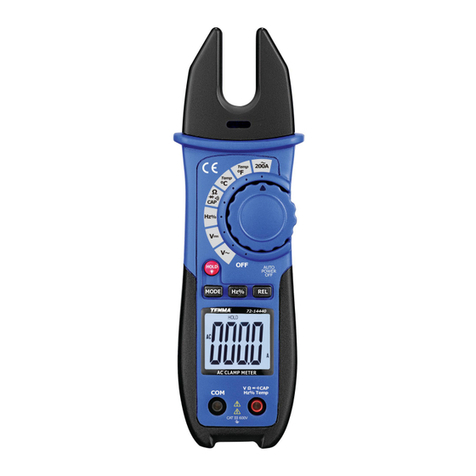
Tenma
Tenma 72-14440 user manual

Lampa
Lampa 38862 manual

Endress+Hauser
Endress+Hauser tmt142 Brief operating instructions
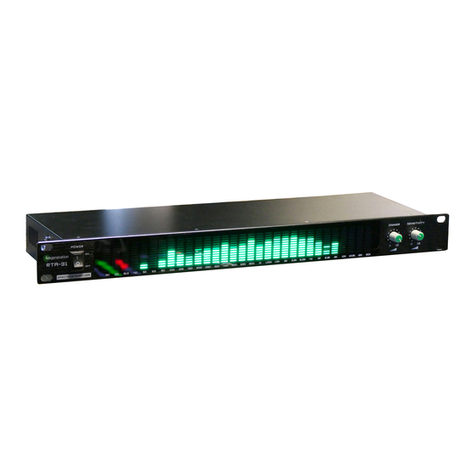
Fun Generation
Fun Generation RTA-31 user manual
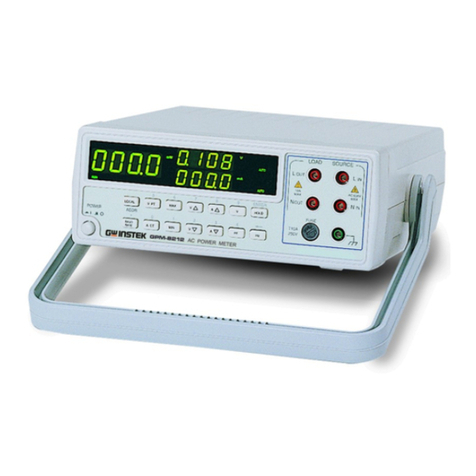
GW Instek
GW Instek 82PM-82120MB user manual

Transforming Technologies
Transforming Technologies Resistance RANGER CM2800 instruction manual
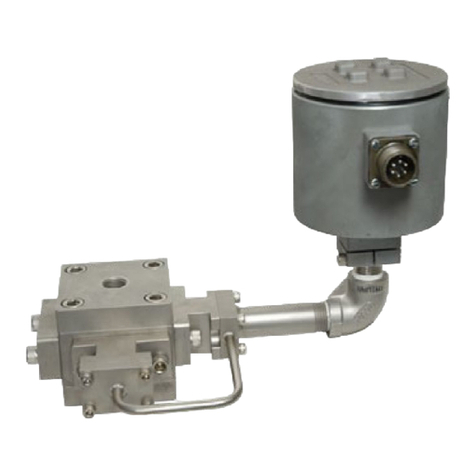
Max Machinery
Max Machinery 234 Series instruction manual
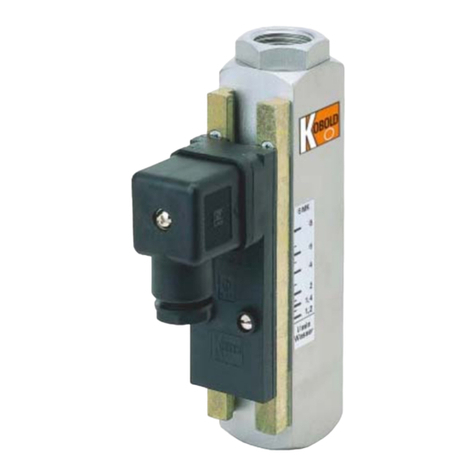
Kobold
Kobold DSS Series Operating instruction
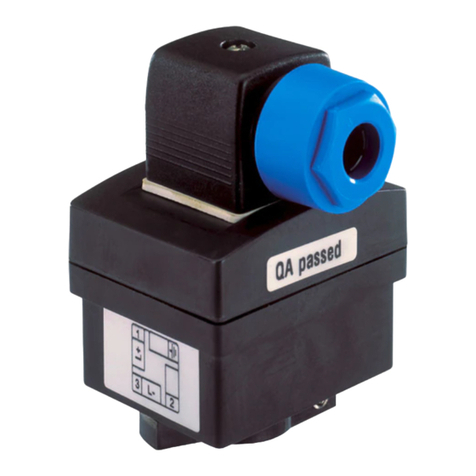
Burkert
Burkert SE30 Ex Namur operating instructions

Hydac
Hydac FMM Operating and maintenance instructions
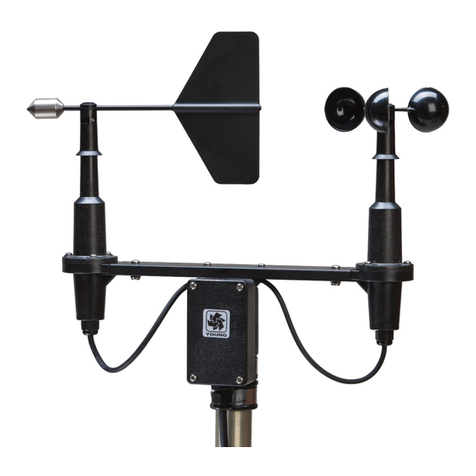
Young
Young Wind Sentry Series instruction manual

Siemens
Siemens SITRANS F MAG 6000 I operating instructions