Technibel CMHGV 2101 User manual

1
July 2006 10 11 369 - GB - 05
INSTALLATION INSTRUCTIONS
AIR COOLED WATER CHILLER
WITH BUILT-IN HYDRAULIC MODULE
AIR / WATER
R 407 C refrigerant
CMHGV 2101 / 2140

2
SUMMARY
1 - Generalities ................................................................................... 2
2 - Dimensions.................................................................................... 3
3 - Installation ..................................................................................... 3
4 - Connections................................................................................... 4
5 - Option and accessories................................................................. 5
6 - Starting .......................................................................................... 7
7 - Operation of "ECH" electronic control ........................................... 8
8 - Proportional condensation pressure control operation................ 14
9 - Maintenance ................................................................................ 14
10 - Pressure curves........................................................................... 17
MARKING
This product marked conforms to the essential requirements of the Directives:
- Low voltage no. 73/23 EEC, modified 93/68 EEC.
- Electromagnetic Compatibility no. 89/336 EEC, modified 92/31 and 93/68 EEC.
- Pressure Equipment Directive No. 97/23/CE.
APPLIANCES FILLED WITH R 407 C
R 407 C
• Fluid R 407 C, as opposed to R22, is not a pure fluid but a blend
composed of:
- 23% R 32 + 25% R 125 + 52% R 134 A.
• The compressors approved for operation with this fluid are filled
beforehand with polyalcohol oil.
Contrary to mineral oil, it is very hygroscopic: it absorbs the
humidity of the ambient air very quickly. This can modify its
lubricant properties and lead in time to the destruction of the
compressor.
MAINTENANCE INSTRUCTIONS
1- Never add oil to the appliance; the compressor is filled with
polyalcohol oil, a special oil which cannot tolerate the presence
of other oils.
2- The instruments used for:
- filling,
- pressure measurements,
- emptying under vacuum,
- recovering the fluid,
must be compatible and only used for the R 407 C fluid.
3- Theweight ofthe refrigerantcontainedinthe storage bottle must
be checked constantly. Do not use it from the moment the
remaining weight is less than 10% of the total weight.
4- In the case of a new charge:
- do not use the charging cylinder,
- use a balance and a dip pipe type R 407 C cylinder,
- chargetheweightofR407Casperthevalueindicatedonthe
unit’s identification plate,
- IMPORTANT: see instruction 3 above.
5- The charge must be undertaken in liquid phase.
6- In case of leakage, do not complete the charge: recover the
remaining refrigerant for recycling and perform a total charge.
Recovery, recycling or the destruction of the fluid must be done
in compliance with the laws in force in the country concerned.
7- If the refrigerant circuit is opened, you must:
- avoid the entry of air into the circuit as much as possible,
- replace the filter drier,
- perform the "vacuum operation" at a minimum level of 0.3
mbar (static).
1 - GENERALITIES
• Theequipment must beinstalled, started-up andmaintainedby authorisedandqualified personnel, inaccordance with local
rules and professional standards.
• The recommendations and instructions presented in the manual and on labels must be followed.
1.1 - GENERAL SUPPLY CONDITIONS
• The units must be securely anchored to the truck’s trailer during transport.
• Generally speaking, the material is transported at the consignee’s risk.
• Intheeventof damagesduringtransport,theconsigneemustnotifythecarrierbyregistered letterwithinthreedays following
delivery.
1.2 - VOLTAGE
• Before carrying out any operation, check that the voltage indicated on the unit corresponds to the mains voltage.
• Before servicing the unit, ensure that the electrical power supply has been shut off and warning signs installed.
1.3 - TECHNICAL AND PHYSICAL CHARACTERISTICS
• See technical data.

3
2,200
2,000
2,000
896
460
232
742
B
A
x
G
DD
2 - DIMENSIONS
4 Ø 37 mm holes for
sling attachment
Dimensions (in mm) are given
for standard units without
options.
General tolerance ±10 mm.
Condenser air discharge
Condenser air suction
AWater inlet connection
BWater outlet connection
DPressure gauge (accessory)
Power supply
GCentre of gravity
3 - INSTALLATION
Clearances to be respected
1000
300
300
800
3000
• Prior to all servicing or other actions on the equipment, installation,
commissioning,operation,ormaintenance,thepersonnelinchargeofthese
operations shall become familiar with the instructions and
recommendations provided in the installation manual of the unit as well as
the elements of the project's technical file.
• The personnel responsible for receiving the unit must conduct a visual
inspection in order to identify all damage to which the unit may have been
subjected during transport: refrigerating circuit, electrical cabinet, cassis
and cabinet.
• The unit must not be installed near the following:
- sources of heat,
- combustible materials,
- return/air intake of an adjacent building.
• The unit must be installed, started, maintained and repaired by qualified
servicing personnel in compliance with the requirements of all directives,
laws and regulations and in accordance with standard trade practices.
• Duringinstallation,troubleshootingandmaintenanceoperations,theuseof
pipes as a step: under the stress, the pipe may rupture and the refrigerant
may cause serious burns.
• The unit is delivered on a wooden pallet and shrink-wrapped.
• A lift truck may be used to remove the unit from its pallet.
• Handle the unit with care.
• Crane installation: once the plastic film has been removed, the machine may be lifted by placing the hoisting hooks into the
four Ø 37 holes.
• Spacers or protective pads should be placed between the slings and body to avoid damage.
• The unit's centre of gravity and weight are indicated on the space requirement diagrams and in the table of the technical
documentation.

4
• Before installation, verify the following points:
- the unit must be installed outside in an appropriate location and in compliance with environmental requirements (sound
level, integration, etc...),
- the unit’s installation location must be perfectly level and strong enough to support the weight of the unit and must have
adequate inundation protection,
- sufficient space around the unit should be provided in order to facilitate servicing and maintenance operations (see
drawing page 3),
- air suction to the coil and fan discharge must not be obstructed,
- install the unit above the region’s average snowfall level,
- vibrations and noise must not be transmitted to adjacent buildings,
- install the machine on anti-vibration pads and fit hoses on piping elements, as required,
- if necessary, consult an acoustics specialist concerning the unit’s optimum location.
• AVOID:
- excessive exposure to sea-air or corrosive gases,
- the proximity of the extractor fan,
- projections of mud (next to a roadway or path, for example),
- areas where there is strong wind blowing against the unit's air exhaust.
• Protection index of the unit: - IP 44 : for the electrical equipment,
(IPXXB : for the mechanical hazards).
4 - CONNECTIONS
4.1 - HYDRAULIC CONNECTION
• Connect the water pipes to the corresponding connections: male 2" 1/2 (66 x 76).
• Connect the hydraulic filter (supplied with the unit) onto the water intake. Also provide 2 isolation valves for intake cleaning
purposes.
• The pipes must be at a sufficient distance from the removable panels to enable servicing operations to be performed.
• Make the connection with flexible hoses preferably.
•The diameter of the pipes must be calculated according to the installation (take care with high head losses).
4.2 - ELECTRICAL CONNECTION
4.2.1 - GENERALITIES
• In all cases, refer to the wiring diagrams supplied with the unit or supplied upon request.
• The acceptable voltage variation is: ±10% during operation.
• The electrical connection conduits must be fixed.
• Short circuit current: 10 kA as per IEC 947-2.
• Class 1 unit.
• Use the holes fitted with grommets for passing cables into the unit.
• To pass the cables inside the electric box, use stuffing box (not supplied) to be assembled on the plate at the back of the
electric box.
• The electrical installation must comply with the standards and regulations applicable where the unit is being installed (in
particular NFC 15-100 ≈CEI 364).
• The unit is designed to be connected to a mains supply with a TT, IT or TN.S neutral point connection (as per
NF C 15-100).
• Electrical diagram 10 05 814.
4.2.2 - MAINS SUPPLY
• Thepowersupplymust bethree-phase400V/50Hz, connectedtothepowersupplyswitchintheunit’selectricalbox(see
electrical diagrams).
Place cable glands (not supplied) for the passage in the bottom of the box.
• CAUTION:
Before starting the unit, ensure that the phase rotation order is correct. The phase-sequence controller restricts
the unit from operating if the 3 supply phases are not in order or if a phase is absent.
• The power supply must come from an isolation and electric protection device (not supplied) in accordance with existing
regulations.
• The sizing of the power supply cables is to be ensured by the installer in accordance with the installation conditions and
as per current standards.
Cable sizes, indicated below, are given for information purposes.
They are calculated in accordance with NFC 15-100 ( ≈CEI 364) with the following hypotheses:
- Maximum current, see table below.
- Multi-pole copper cable with PR insulation.
- Installation in non-ventilated cable duct (installation method No. 41). No other power cable.
- Ambient temperature 40°C.

5
• The complete electrical specifications are given in the table of the technical documentation.
4.2.3 - CONTROL BY EXTERNAL CONTACT
• Theunitcanbecontrolledremotelybyconnectingagood-quality,
potential-free external contact (not supplied) for the remove
ON/OFF signal (contact closed = operation authorized, contact
open = OFF).
• The ON/OFF signal is connected to terminals 17 and 18 of the
terminal strip located in the electrical box (remove the existing
jumper - see diagram).
• The wiring of this contact must not be routed near power cables
in order to avoid electromagnetic disturbances.
• Use shielded cable with twisted pair (shielding grounded on
generator side).
• Max. connection cable length: 100 m.
• Minimum wire size: 0.5 mm2.
4.2.4 - REMOTE CONTROL
• See § 5.
4.2.5 - MISCELLANEOUS
• Alarm transfer:
Potential-free contact (2A resistive - 250 VAC maximum) available on terminals 25 and 26 of the terminal strip in the
electrical box.
- Contact open = Alarm or power supply loss.
Note: this contact's direction of actuation may be changed through parameterisation. See § 7.
• The lengths indicated below correspond to a voltage drop less than 5% in the cable.
CMHGV
Starting current A
Max. total current A
Power supply cable section mm2
Max. connection length m
2101
220
113
50
200
2124
240
135
50
200
2140
290
143
50
200
17
CMHGV
18
ON/OFF
(❋)
(❋) Jumper to be removed
5 - OPTION AND ACCESSORIES
5.1 - OPTION (FACTORY INSTALLATION)
5.1.2 - BACKUP PUMP OPTION
• Code 70601105.
•
The switchover of the electrical supply onto the 2
nd
pump is performed manually by a switch box placed near the
pumps
.
Procedure: This operation is to be performed by qualified personnel.
- Stop the generator and the pump (time delay).
- Close the valve of the pump to be shut down.
- Open the valve of the pump to be started.
- Select the pump to be started with the switch located in the box.
- Restart the generator.
- Check that the pump is operating.
5.2 - ACCESSORIES
5.2.1 - ANTI-VIBRATION KIT
• The kit includes:
-1 set of 6 anti-vibration plates, thickness 25 mm code 70600036,
5.2.2 - HP AND LP PRESSURE GAUGES
• Code 70970007.
• The accessory includes 1 set of 2 pressure gauges (HP and LP). Two per apparatus must be controlled.
- Remove the caps on the riser of the front panel.
- Install the pressure gauges.
- Connect the capillary tubes to the pressure taps.

6
CONN A CONN B
_S+
24 (S)
25 (+)
26 (-)
5.2.3 - REMOTE CONTROL
• Code 70250057.
• The functions and display are exactly the same as those on controller.
• The only difference concerns the buttons and which are
separated by the “ON/OFF” and “Mode” buttons.
•The controller is designed to be installed inside sheltered rooms.
• Connection:
- ontheelectroniccontrolboard locatedintheelectricbox (inparallel
with the box's display unit connection),
- use twisted pair shielded cable with a cross section of at least
0.5 mm2(shielding of the ground on unit side),
max. length: 100 meters.
CAUTION:
Do not route this cable near power cables.
The operation must take performed with the unit's power supply
off and locked out.
5.2.4 - RS 485 COMMUNICATION INTERFACE (MODBUS
protocol)
• Code 70250056.
• Secure the communication interface on the DIN rail next to the
electronic board located in the electric box.
• Connect the ribbon cable (supplied) between the interface and the
electronic control board located in the electric box.
• Connect the interface's 230 VAC power supply to terminals 1 and 2 on
the terminal strip using the Blue and Black wires supplied, as shown
opposite.
5.2.5 - 800 W ANTI-FREEZE RESISTANCE
• Code 70200010.
• Power supply and control of this resistance shall be separate from all
other installation circuits. It must be installed by qualified service
personnel who are familiar with this type of equipment and in
compliance with local regulations and recognized trade practices.
• Before all operations on the unit, make sure that the power supply
is disconnected and locked out.
• The 230 VAC electrical power supply must be fitted with a separate overcurrent protection and disconnect switch in
compliance with the rules and regulations in force.
• The power supply wiring must be secured. Use the cable gland located on the resistance cover.
- Note 1: The resistance is equipped with an adjustable limiting thermostat set at approximately 7°C.
- Note 2: Power to the resistance must be turned on only when the circuit is full of water.
- Note 3: Make sure that wiring is securely
clamped in the terminal block and the ground
connection is correctly attached.
Electronic control board
Remote control (rear
view)
D
GND
DTR
TX
RX
+5V
987654
RS 485
230 Vac
1
2
321
BUS ADAPTER
Blue
Black
Ribbon cable
Electronic control board
800W
230V
2 1
PE
Thermostat
2
1
3
M5
M4
Cover
Thermostat
-35°C / +35°C
preset at 7°CPhase Neutral
Ground

7
6 - STARTING
6.1 - CHECK:
• That all hydraulic connections are properly tightened and that the hydraulic system functions correctly:
- purge the circuits,
- position of valves,
- hydraulic pressure.
• That there are no leaks.
• That the machine is stable.
• That the power cables are well fixed to their connection terminals (loose terminals can cause heat build-up on the terminal
board).
• That the electric cables are well insulated from any sections of sheet metal or metal parts which could damage them.
• That electrical wiring is a safe distance from refrigeration lines.
• That probe, control and power cables are properly separated.
• That the machine is earthed.
• That there are neither tools nor other foreign objects in the unit.
• IMPORTANT: If antifreeze is added (monopropylene glycol), a minium rate of 15% to 20% is needed to avoid any
risk of corrosion.
6.2 - STARTING-UP THE UNIT
• Power up the unit.
• Start the unit. The water circulating pump must function. See details in § 7.5.
6.3 - CHECKS TO BE MADE
• Checkthat therotation directionof thefan(s) andthe pumpiscorrect.
If not, reverse 2 phases on the electrical power supply.
• HP and LP pressure and amperages are in accordance with the
commissioning sheet.
• Check water flow.
• Check control system operation.
• Water circuit pressure.
NOTE: The equipment's buffer tank is equipped with a safety
pressure switch which prohibits the water circulating
pump from operating and thus the unit in case of insufficient pressure (cut-out 0.6 bar, interlocking
1.4 bar).
•Purge the hydraulic system, with special attention given to the circulating pump.
IMPORTANT:
• The unit's electronic control features a frost protection device that automatically starts the water circulating pump
depending on the outside temperature (threshold: 0°C), even if the unit is turned off.
• When the unit is turned on, It is thus important to make sure that the hydraulic circuit is ready to operate (purge, water
pressure, position of valves).
• The following must be undertaken in the event the unit is taken out of service or if there is a high risk of freezing:
- either drain the installation,
- or add glycol to the hydraulic circuit.
Draining

8
• See wiring diagrams supplied with the machine.
7.1 - DELIVERY STATE
• The control unit is supplied fitted in the
machine and factory pre-set.
• Alltheconnectionsaremadeexceptthose
concerning the available signals or the
options.
7.2 - PRINCIPLE
• The microprocessor controls the
operation of the machine and of the
associated alarms.
It continuously compares the water
temperature measured by the probe (Ai1)
and the setpoint temperature value
entered via the keyboard.
Each operating request generated by the
control system is signalled by indicator lights (6) or (8) - see below.
Each light flashes if a safety delay is in progress. The light shines steady when the corresponding circuit is in operation.
• The control probe is located on the water inlet in the factory.
7.3 - PRESENTATION
7.3.1 - DISPLAY KEYBOARD
(1) Key for:
- local On / Off control,
- access to parameters (in combination with button (2)),
- alarm clearance,
- hour counter reset.
(2) Key for:
- access to parameters (in combination with button (1)).
(3) LED display.
(4) Cooling mode indicator.
(5) Heating mode indicator (not used).
(6) Compressor on indicator, circuit A.
(7) Anti-freeze on indicator (not used).
(8) Compressor on indicator, circuit B.
(9) Decimal point: if illuminated when the operating time is displayed, the value must be multiplied by 100.
7.3.2 - CTN TYPE TEMPERATURE PROBE
• 10 kΩat 25°C
7 - OPERATION OF "ECH" ELECTRONIC CONTROL
ECH 420 SRD
MICROPROCESSOR
CARD
Temperature
probe Ai2
(water outlet for
anti-freeze
protection)
Temperature
probe Ai1
(water inlet for
control) DIGITAL INPUTS
ACTUATORS
12 VAC
SUPPLY
TRANSFORMER
Outside
temperature
probe Ai4
Temperature (°C)
-20
-10
0
10
20
25
30
40
50
60
70
Ohmic value (Ohm)
67,740
42,450
27,280
17,960
12,090
10,000
8,313
5,820
4,161
3,021
2,229
6 4 2
7
83 9 1
5
DISPLAY
KEYBOARD

9
7.3.3 - INPUT / OUTPUT BOARD
Water inlet probe - Ai1
Water outlet probe - Ai2
(not used) - Ai13
Outside temperature sensor - Ai4
GND
GND
(not used) - AN1
12V
AN2 - (not used)
GND
GND
ID11 - Thermic, ventilation, circuit B
Ai6 - (not used)
Ai5 - (not used)
S
12345678910
+-
CONN A
1
9
8
16
CONN B
1
9
8
16
12V
12C
TC1
LP pressure switch, circuit A - ID5
HP pressure switch, circuit A - ID4
Water output - ID3
(not used) Heating / Cooling - ID2
On / Off - ID1
ID6 - Thermic, compressor, circuit A
ID7 - Thermic, ventilation, circuitA
ID8 - HP pressure switch, circuit B
ID9 - LP pressure switch, circuit B
ID10 - Thermic, compressor, circuit B
TC2
12C
Keyboard / display unit
terminal strip
Extension board connector
(not used)
TTL series port:
for connection:
- communication interface,
- parameterisation key.
Compressor, circuit A
Compressor, circuit B
Ventilation, circuit A
Ventilation, circuit B
Pump
Common
Alarm
Alarm
Common, inputs
Triac control
output (not used)
Common, inputs
12 VAC
power supply
Triac control
output (not used)
Digital outputs
Alarm report digital output
7.4 - OPERATING MODE COOLING
• Staged triggering of cooling circuits depending on the
difference in relation to the water setpoint temperature.
• Note: An automatic refrigerating circuit switchover
system allows their operating time to be shared.
7.5 - STARTING
• Initial condition:
- Machine hydraulically and electrically connected ready to operate.
- If connected, the remote On/Off contact is open (Off ).
•Turn the installation on:
- The display unit is off (except for the "decimal" point which remains illuminated); this
meansthat the controlleris off. Turnit off bypressing andholdingthe "ON/OFF" button
for 2 seconds.
- The cooling indicator light (4)illuminates and the display unit then indicates the
message "E00" which identifies shutdown by the remote On/Off contact (if used).
• To start the unit:
- Close the remote On/Off contact. The water inlet temperature is displayed. The circulating pump starts.
- Theoperatinglightsofthecompressors(6)and(8)illuminateifrequired(seediagram,paragraph7.4). Ifthelightflashes,
it means that the compressor is starting required but that a safety delay is in progress. This light stays on when the
compressor has started.
0
C03
C05
C03
1
1st circuit
Water temperature
Difference between
stages
Cooling setpoint
Hystereris Hystereris
2nd circuit
2 seconds

10
2 seconds
• To stop the unit:
- Open the remote Off (stop) contact.
- The indicator lights of compressors (6) and (8) go off and the message "E00" is displayed.
- The water circulating pump stops after 1 minute.
Note: the unit can be shut off locally by pressing and holding the "ON/OFF" button for 2
seconds. Locally-controlled shut-off has priority over the remote control command. The
display unit is off at this time (except for the "decimal" point which remains illuminated).
7.6 - PARAMETERS - DISPLAYING AND ADJUSTING
7.6.1 - GENERALITIES
• Parameter access is structured within a multi-level menu, see the diagram below. Simultaneously pressing the
"ON/OFF" (1) and "Mode" (2) buttons for a brief moment (less than 2 seconds) gives access to the next level.
Simultaneously pressing for a long moment (longer than 2 seconds) turns you to the previous level.
• Button (1) or button (2) is used to scroll through the entries ("Label") within the same level or to increase or decrease a
parameter value.
7.6.2 - PARAMETERS ACCES DIAGRAM
(*) Accessible to qualified personnel only after entering the password (PSS).
Note 1: Indicator lamps (6) and (8) flash when levels 1 and above are accessed.
Note 2: The normal display (level 0) returns automatically after 5 minutes if no buttons are pressed.
Level 0
Normal display Level 1 Level 2 Level 3 Level 4
Temperature S1
Alarm active Set value SET Cooling setpoint
Coo Setpoint value
Temperature
probes TP Probe code t01…t04 Temperature value
Alarms Err Alarm code E00...
Digital inputs Id (*) Input code 01… input status
Parameters PAr (*) Config. para. CnF Parameters codes
H01… Parameter value
Compressor
parameter CP Parameters codes
C01… Parameter value
Fan parameter FAn Parameters codes
F01… Parameter value
Alarm parameter
ALL Parameters codes
A01… Parameter value
Pump para. PUP Parameters codes
P01… Parameter value
Frost. para. Fro
Password PSS
Hour counters OHr Counter value
Counter value
Pump counter OHP Counter value
Compressor counter
circuit A OH1
Compressor counter
circuit B OH3
Not used
Password value
t < 2 sec. --> Upper level t > 2 sec. --> Return to the previous
level

11
7.6.3 - SET POINT ADJUSTMENT
• Simultaneously press buttons (1) and (2) for at least 2 seconds, "SET" is displayed.
• Press the 2 buttons again, "Coo" is displayed.
• Simultaneouslypress the2 buttonsagain for2seconds. Thesetpoint valueappears. Ifneeded,modifythevalue withthe
buttons.
• Press the 2 buttons simultaneously to validate the setpoint.
• Return to the normal display by simultaneously pressing the 2 buttons for more than 2 seconds.
Reminder: control on the installation return temperature.
Note:
All units are factory configured and parameterized for optimum operation in the terminal unit application.
7.6.4 - DISPLAY OF TEMPERATURES, ALARMS, AND HOUR COUNTERS
Accessible directly via the menu, see diagram 7.6.2.
• Temperatures "TP":
Displays the values indicated by each temperature probe.
• Alarms "Err":
Displays the list of all current alarms (scroll through the alarm messages with buttons (1) and/or (2)).
• Hour counters "OHr":
Displays the operating time of the compressors on circuit A("OH1"), and the compressors on circuit B("OH3") and the
circulating pump ("OHP"). The counter can be reset by a long press (> 2 seconds) on button (1) when the counter value
is displayed.
7.6.5 - ACCESS TO THE TECHNICAL PARAMETERS "PAr"
For qualified personnel after entering the password "PSS". Any incorrect adjustment may lead to serious
malfunctions.
• Go to the "PSS" section in the menu. Briefly and simultaneously press buttons (1) and (2). The "---" message appears.
Display the password ("199") using buttons (1) and (2) and validate it by simultaneously pressing buttons (1) and (2). It
is now possible to enter the parameters section "PAr".
CAUTION:
After modifying one or more technical parameters, the controller must be turned off then back on again to reset
it with its new parameters.
7.7 - ALARMS
• When an alarm occurs:
- the alarm report is activated,
- the corresponding code flashes on the display unit. See table,
- the unit stops if necessary (see table below).
• Remedy the fault.
IMPORTANT NOTE:
All work must be carried out by qualified, experienced personnel.
•CAUTION: the alarms:- HP,
- LP (low pressure),
- Anti-freeze,
- Water flow rate,
normally with automatic reset, have an event counter that shifts the alarm to manual reset if the alarm occurs several times
during the last hour.
• The alarms are reset by briefly pressing the "ON/OFF" button (1).
• When the alarm is cleared:
- the alarm report is de-activated,
- the display reverts to normal (not flashing),
- the machine can re-start (if it was stopped).
•Note: Alarms are active in off mode.
•Special features of the alarm report:
- Potential-free contact (2A resistive - 250 VAC) available on the terminal strip of the electric box.
Contact open in case of alarm or loss of power supply.
- This report's operating logic can be changed by changing parameter H45 from 1to 0.
- The alarm report can be activated in case of shutdown by remote contact by changing parameter H72 from 1to 0.
Factory setting
(terminal units)
Coo Cooling set point 12°C 12 to 25°C
ParametersCode Adjustment range

12
SUMMARY TABLE OF ALARMS
A= Auto
M= Manual
7.8 - SPECIAL OPERATING FEATURES
•Water circulating pump control:
- the pump is actuated when the unit operating,
- thepumpisstoppedwhentheunitisstopped.Theshut-downofthepumpisdelayed1minuteafterthecompressorstops,
- the unit's electronic control features a frost protection device that automatically starts the water circulating pump
depending on the outside temperature (threshold: 0°C), even if the unit is turned off.
In the event of a faulty outside temperature sensor, circulating pump operation is forced, for safety reasons.
The"Water output" alarm(E41)stopsthecirculatingpumpwhenthisalarmshiftstomanual reset.Inthe eventofa fault,
the alarm report is actuated.
Alarm Code Inhibition delay Reset Remarks
ABAB
Water inlet
temperature
probe fault, Ai1 E40 XXXX A
Water inlet
temperature
probe fault, Ai2 E06 XXXX A
Outside
temperature
sensor fault, Ai4 E42 XXXX A
Force water pump
operation
H.P. circuit A E01 X X A/M
H.P. circuit B E21 X X A/M
L.P. circuit A E02 120'' at start-up X X A/M
L.P. circuit B E22 120'' at start-up X X A/M
Thermic,
compressor,
circuit A E03 X X M
Thermic,
compressor,
circuit B E23 X X M
Thermic, fan,
circuit A E04 X X M
Thermic, fan,
circuit B E24 X X M
From probe Ai2
A/M (water outlet)
Threshold = 6°C
Configuration
error E45 XXXX X Consult the After-Sales
Service Department
A
Shutdown by
remote contact E00 XXXX X A
No alarm report with
H72 = 1
Threshold = 35 °C
Water inlet
temperature too
high E46 2 '
XA/M
30'' at start-up
If manual reset
XX
Water flow rate E41 10'' in operation
E05 X X
Compressor
stop Fan stop Water
pump
shutdown
See also reset of the
corresponding circuit
breaker
Anti-freeze
(water heat
exchanger)

13
•Pre-ventilation:
- incaseofanoperatingrequestandinordertopreparetheairexchanger,thefansareactuatedapproximately20seconds
before the first compressor starts up.
•Anti short-cycle time delays:
- the control of each cooling circuit features a time delay system in order to respect:
• a maximum number of starts per hour (12),
• a minimum stop time (150 seconds).
•Starting the compressors:
- in order to reduce start-up currents:
• the triggering of the 2nd cooling circuit is time delayed (10 seconds),
• the triggering of the 2nd compressor of a cooling circuit is delayed (time delay unit on the compressor switch set at
approximately 5 seconds).
•Control hysteresis:
- see the operating diagrams in § 7.4,
- thehysteresis ofeach stagein coolingmode isfactorysetat1.5 k.Modification ispossible. Todo this,change parameter
C03 (cooling hysteresis) in the compressor section "CP",
- the difference between the 2 stages is factory set at 1.5 k. Modification is possible. To do this, modify parameter C05 in
the compressor section "CP".
•"Dynamic" set point:
- bychanging H50 from0 to1, anautomatic setpoint compensationsystem is activatedbased ontheoutside temperature,
- the following parameters allow the compensation slopes to be set:
•Principle:
•Example: Factory setting in cooling mode
•Adjustment of the value measured by the temperature probes ("Offset"):
allows the difference between the value displayed and the verified value to be compensated.
< 0 > 0
Set point offset
H51 > 0
Outside temperature
H55 H55
H53
Set point
Outside temperature
H55
H51
Parameter Designation Factory setting
H51 = Set point "offset" in cooling mode 5 k
H53 = Outside temperature setting ("foot of slope") in cooling mode 25°C
H55 = Proportional strip in cooling mode + 10 k
Parameter Probe offset Units Factory setting
H57 Probe Ai1 offset Degree 0
H58 Probe Ai2 offset Degree 0
H60 Probe Ai4 offset Degree 0

14
9 - MAINTENANCE
IMPORTANT :
Before carrying out any work on the machine, make sure that it is switched off and that access to it is prevented.
Any work must be carried out by personnel qualified and authorised to work on this type of machine.
9.2 - REFRIGERANT CIRCUIT RECOMMENDATIONS
• A new filter dryer must be installed after all servicing operations performed on the refrigerant circuit.
9.2.1 - MAINTENANCE
• Prior to all servicing or other actions on the equipment, installation, commissioning, operation, or maintenance, the
personnelinchargeofthese operationsshallbecomefamiliarwith theinstructions andrecommendationsprovided inthe
installation manual of the unit as well as the elements of the project's technical file.
• The unit must be installed, started, maintained and repaired by qualified servicing personnel in compliance with the
requirements of all directives, laws and regulations and in accordance with standard trade practices.
• During installation, troubleshooting and maintenance operations, the use of pipes as a step: under the stress, the pipe
may rupture and the refrigerant may cause serious burns.
• During unit maintenance operations, the composition and the condition of the coolant will be checked, as well as the
absence of all trace of refrigerant.
• During the unit's annual seal test, in accordance with the law, check that the high and low-pressure pressure controllers
are correctly connected on the refrigerating circuit and that they disconnect the electrical circuit in case of tripping.
• During maintenance operations, make sure that there is no trace of corrosion or oil stains around the refrigerating
components.
• Priortoallmaintenanceandservicing ontherefrigeratingcircuit,onemustfirstshutdowntheunitthenwaitafewminutes
before installing temperature or pressure sensors. Certain equipment, such as the compressor and piping, may reach
temperatures above 100°C and high pressures may lead to serious burns.
9.1 - PERIODIC CHECKS
• Carryoutthefollowingoperationsatleastonceayear(thefrequencydependsontheinstallationandoperatingconditions):
- Cleaning the air exchanger.
- Checking the wear parts.
- Checking the operating set points and temperatures.
- Check the refrigerant circuit in accordance with the
regulations in force.
- Checking the safety devices.
- De-dusting the electrical equipment cabinet.
- Checking that the electrical connections are secure.
- Checking the earth connection.
- Check for leaks.
- Check the operation and parameters as per the start-up
data sheet.
- Check the hydraulic circuit in accordance with standard
trade practices (output, pressure, purge the circuit and
particularlythepump–seeparagraph6.3,filtercleaning).
- Check that the safety valve operates correctly.
GENERAL MAINTENANCE:
All equipment must be properly maintained in order to provide optimum performance over time. Faulty maintenance can result in
thecancellation oftheproduct guaranty.Depending ontheproducts, maintenanceoperations consistinthe cleaningof filters (air,
water), internal and external exchangers, casings, and the cleaning and protection of condensate tanks. Treating odours and the
disinfection of room surfaces and volumes also contributes to the cleanliness of the air breathed by users.
TECHNIBELproposesawiderangeofperfectlyadaptedprofessionalcleaning,maintenanceandrepairproductsforcompleteand
efficient maintenance. For an optimum result, TECHNIBEL air-conditioners must be maintained with TECHNIBEL maintenance
products.
8 - PROPORTIONAL CONDENSATION PRESSURE CONTROL OPERATION
U
P
• The unit is equipped with a separate condensation
pressure control device.
• 1 voltage selector per refrigeration circuit for the power
supply of the electric fans.
• Based on the information gathered by the specific
pressure sensors, the control varies the supply voltage of
theelectric fansin accordancewith thediagram opposite.
• Factory-set for optimal operation. For all other settings,
consult us.
• The variable regulators are mounted inside the electric
box.
Max. voltage
Min. voltage
Condensation pressure (Bar)

15
9.2.2 - TROUBLESHOOTING
• Allmaintenanceandservicingoperationsontherefrigeratingcircuitmustbeconductedinaccordancewithstandardtrade
practices and safety rules: recovery of the refrigerant, inert shielded (nitrogen) brazing, etc…
• All brazing operations must be conducted by qualified welders.
• For equipment charged with R 407 C, refer to the specific instructions in the installation manual.
• Thisunitis equipped with pressurized equipment, forexample piping. Use only genuine partslistedin the spare parts list
for replacing defective refrigeration components.
• Pipes may only be replaced by copper tubing in compliance with standard NF EN 12735-1.
• Leak detection, in the case of pressure testing:
- Never use oxygen or dry air, as the risk of fire or explosion is present
- Use dehydrated nitrogen or a nitrogen and refrigerant mix indicated on the manufacturer's plate
- The test pressure, low and high pressure, must not exceed 20 bar and 15 bar in the case where the unit is equipped
with the pressure gauge option.
• For high pressure circuit pipes made with copper tubing having a Ø = or > 1"5/8, the supplier will be requested to submit
a certificate § 2.1 in accordance with standard NF EN 10204, which will be filed in the installation's technical file.
• All part replacement with other than genuine parts, all modifications of the refrigerating circuit, all replacement of
refrigerant by a fluid other than that indicated on the manufacturer's plate, all use of the unit outside the application limits
defined in the documentation, shall result in the cancellation of PED CE marking compliance which shall fall under the
liability of the individual who carried out these modifications.
START-UP DATA SHEET
CMHGV Range
CMHGV 2101 to 2140
Code:
Serial Number:
Started by: Company: Site: Date:
Voltage measured on unit V L1-L2 L2-L3 L3-L1
FANS
Measured amperage circuit A - Fan 1
A/phase
L1 L2 L3
Circuit breaker thermal setting A
Measured amperage circuit A - Fan 2
A/phase
L1 L2 L3
Circuit breaker thermal setting A
Measured amperage circuit B - Fan 1
A/phase
L1 L2 L3
Circuit breaker thermal setting A
Measured amperage circuit B - Fan 2
A/phase
L1 L2 L3
Circuit breaker thermal setting A
COMPRESSORS
Measured amperage circuit A - Comp 1 A/phase
L1 L2 L3
Circuit breaker thermal setting A
Measured amperage circuit A - Comp 2 A/phase
L1 L2 L3
Circuit breaker thermal setting A
Measured amperage circuit B - Comp 1 A/phase
L1 L2 L3
Circuit breaker thermal setting A
Measured amperage circuit B - Comp 2 A/phase
L1 L2 L3
Circuit breaker thermal setting A
HEAD PRESSURE CONTROL
setting
SENSORS (see control sheet)
Water temperature control sensor positioned in: Inlet Outlet
TEMPERATURES (°C) / PRESSURES (bar)
Outside temperature
Water type Pure Glycol water % Glycol
Water inlet, generator
Water outlet, generator
Water circuit pressure
Water flow rate
∆T : Circuit A Circuit B
Suction, compressor
Discharge, compressor
Inlet, thermostatic expansion valve
Outlet, thermostatic expansion valve
Condensing pressure
Evaporating pressure
Superheating = (Compressor suction temperature - Evaporating temperature) = 7 to 8°C
Sub-cooling = (Condensating temperature - Expansion valve inlet temperature) = 3 to 5°C

16
START-UP DATA SHEET
CMHGV ECH PARAMETER SETTINGS
Code: Standard application
Serial Number:
Started by: Company: Site: Date:
Parameter Min. Max. Unit Factory value Setting
G01 - Cooling set point 12 25 °C/°F12
H03 - Max. cooling set point limit 12 99 °C/°F25
H04 - Min. cooling set point limit -40 12 °C/°F12
H45 - Alarm report polarity 0 1 flag 1
H50 - "Dynamic set point" validation 0 1 flag 0
H51 - Cooling "dynamic set point" offset -50 80 °C/°F5
H53 - Cooling "dynamic set point" setting -127 127 °C/°F25
H55 - Cooling "dynamic set point proportional strip -50 80 °C/°F10
H57 - Probe Ai1 offset -12.70 -12.70 °C/°F0
H58 - Probe Ai2 offset -12.70 -12.70 °C/°F0
H60 - Probe Ai4 offset -12.70 -12.70 °C/°F0
H64 - Temperature measurement unit (°C/°F) 0 1 flag 0
H65 - Family series address (for communication) 0 14 num 0
H66 - Device series address (for communication) 0 14 num 1
H72 - Remote alarm report deactivation - to OFF 0 1 flag 1
A01 - LP alarm disabling time 0 255 sec 120
A02 - Number of events/hour, LP alarm 0 255 num 3
A06 - Number of events/hour, water output 0 255 num 2
A11 - Anti-freeze alarm set point -127 127 °C/°F3
A12 - Anti-freeze alarm hysteresis 0 25.50 °C/°F2
A13 - Number of events/hour, anti-freeze alarm 0 255 num 2
A15 - Max. alarm setpoint Water inlet temperature -127 127 °C/°F35
A18 - Number of events/hour, HP alarm 0 255 num 3
C03 - Control hysteresis in cooling mode 0 25.50 °C/°F 1,5
C05 - Difference between stages 0 25.50 flag 1,5
P01 - Water pump configuration (0 = permanent operation) 0 1 num 0

17
10 - REFRIGERANT PRESSURE CURVES
468101214161820
18
19
21
22
25
20
23
24
26
27
28
25°C
45°C
35°C
468101214161820
4
5
6
7
8
25°C
45°C
35°C
468101214161820
17
21
23
19
25
27
25°C
45°C
35°C
468101214161820
3
4
5
6
7
25°C
45°C
35°C
468101214161820
10
15
20
25
30
25°C
45°C
35°C
15°C
468101214161820
3
4
5
6
7
25°C
45°C
35°C
15°C
HIGH PRESSURE
LOW PRESSURE
High pressure (bar)
Water outlet temperature (°C)
CMHGV
2101
Low pressure (bar)
Water outlet temperature (°C)
High pressure (bar)
Water outlet temperature (°C)
CMHGV
2124
Low pressure (bar)
Water outlet temperature (°C)
High pressure (bar)
Water outlet temperature (°C)
CMHGV
2140
Low pressure (bar)
Water outlet temperature (°C)
Outside temperature (°C) Outside temperature (°C)
Outside temperature (°C)
Outside temperature (°C)
Outside temperature (°C) Outside temperature (°C)

Due to our policy of continuous development, our products are liable to modification without notice.
R.D. 28 Reyrieux BP 131 01601 Trévoux CEDEX France
Tel. 33 4 74 00 92 92 - Fax 33 4 74 00 42 00
R.C.S. Bourg-en-Bresse B 759 200 728
This manual suits for next models
1
Table of contents
Other Technibel Control Unit manuals
Popular Control Unit manuals by other brands
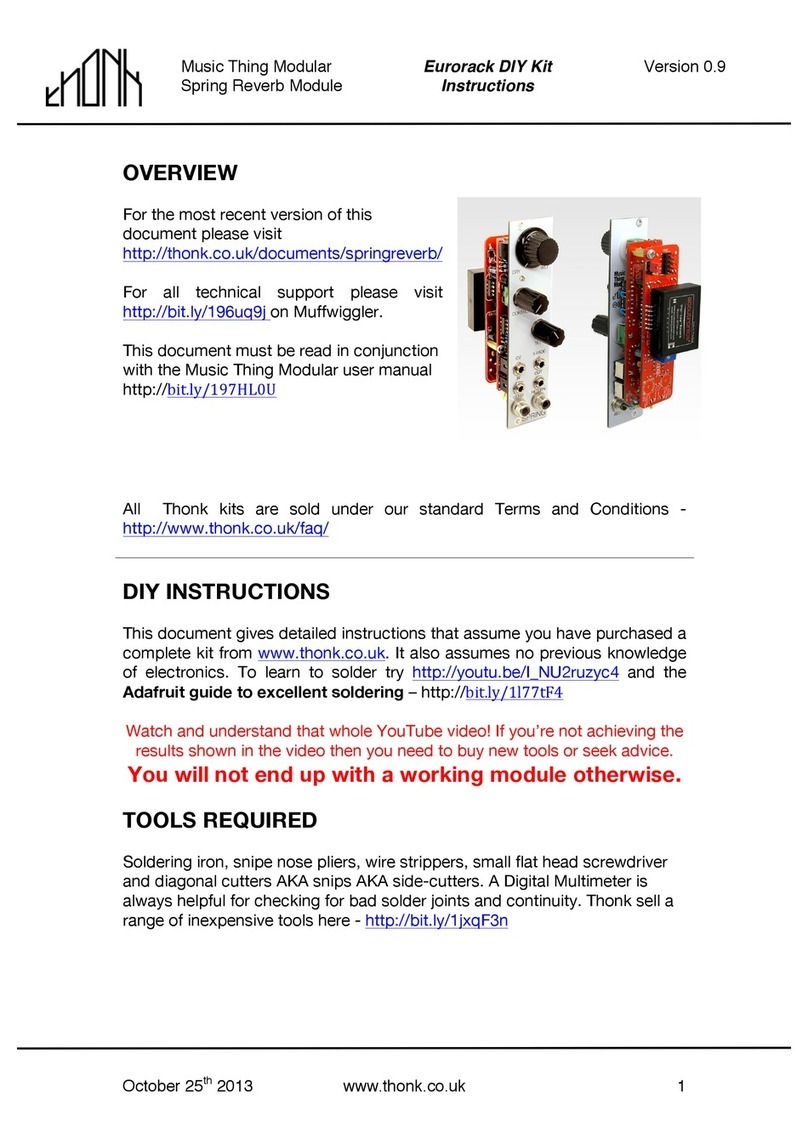
Thonk
Thonk Spring Reverb instructions
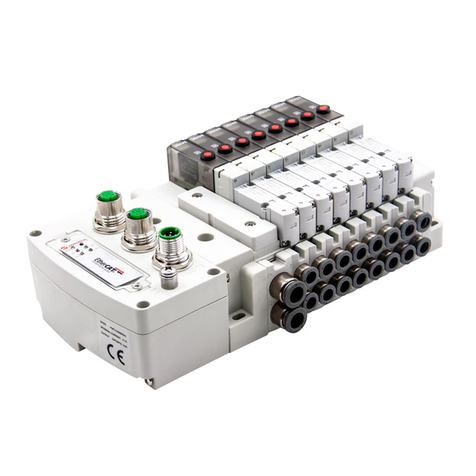
Norgren
Norgren VR10 Installation & Maintenance Instruction
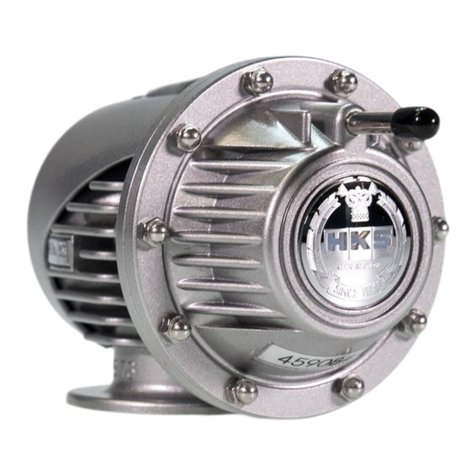
HKS
HKS Super SQV IV 71008-AK001 manual
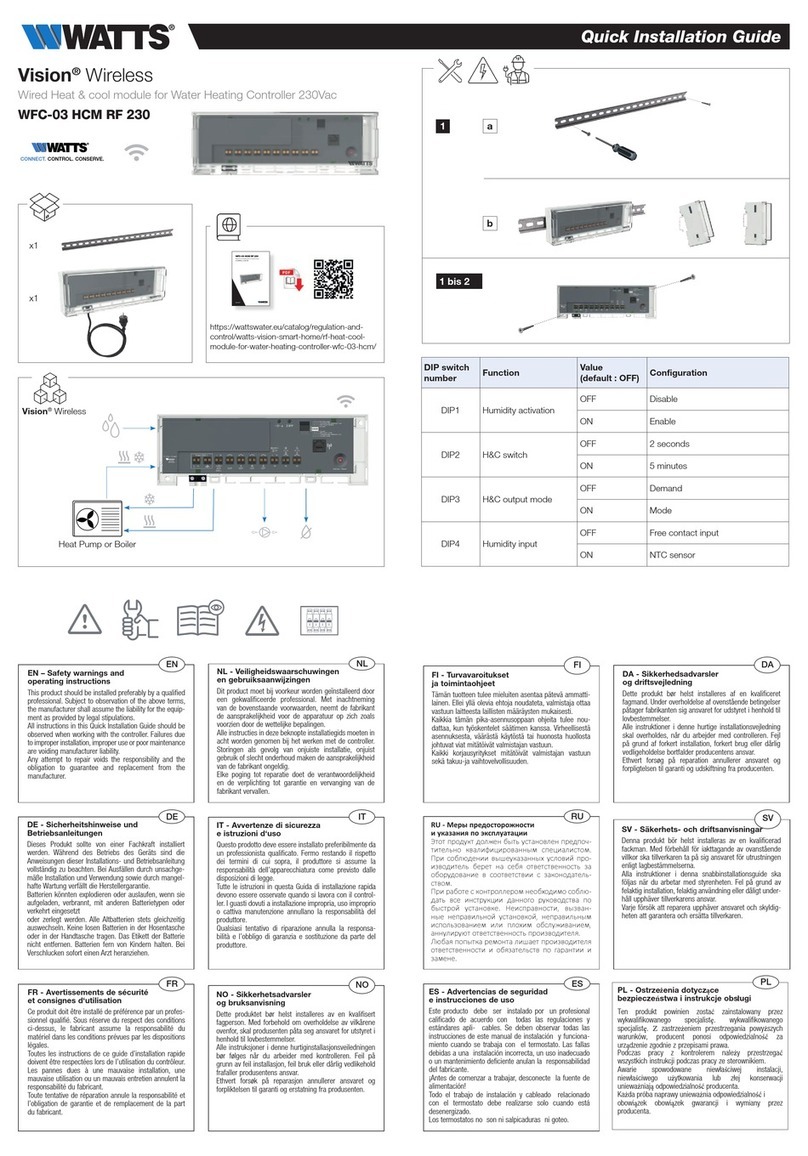
Watts
Watts WFC-03 HCM RF 230 Quick installation guide

System Sensor
System Sensor M902M Installation and maintenance instructions
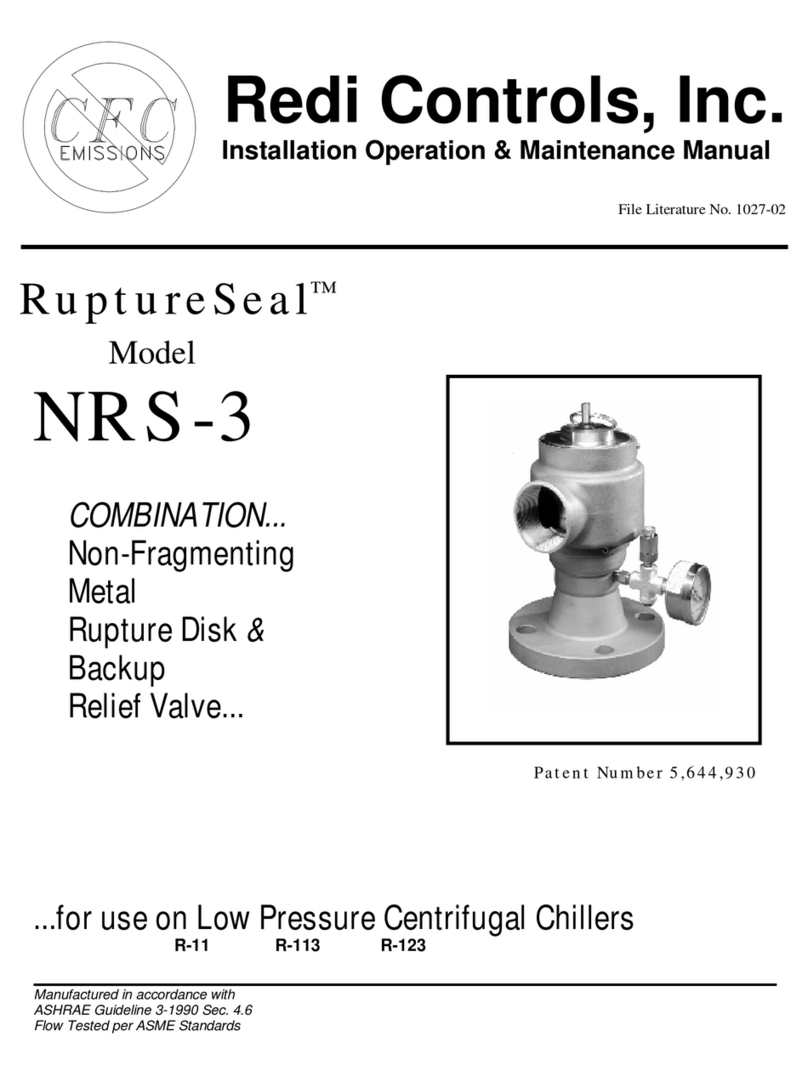
Redi Controls
Redi Controls RuptureSeal NRS-3 Installation, operation & maintenance manual