Teknatool NOVA TL1200 User manual


SAFETY
RULES
PLEASE READAND UNDERSTANDTHESE SAFETY RULES
BEFORE OPERATING THISWOODLATHE.
All machinery, including the woodlathe, has cert'ain hazards involvedwith their operation and use. Using the
'
woodlathe with respect and caution, as withany machinery,will considerably lessenthe risk
of
personal injury.
However, if normalsafety precautions, including those listedhere, are overlooked or ignored, personal injuryto
the operator may'result.
This woodlathe was designed for certain applications only. It
MUST
NOT be modified and/or used for any
applicationotherthanfor which itwas'designed. Ifyouhaveanyquestionsabout itsapplication
DO
NOT
usethe
machine untilyou have written to Teknatool (Latalex Ltd) and we have advised you.
TEKNATOOL INTERNATIONAL
(LATALEX LIMITED)
Manager Technical Services
65
The Concourse
Waitakere City
Auckland
NewZealand
.WARNING: FAILURE
TO
FOLLOW THESE RULES MAY
RESULT IN SERIOUS PERSONAL INJURY
SAFETY 'RULES FOR ALL POWER TOOLS/POWER
~~
MACHINERY-THESEALLAPPLYTOTHIS WOODLATHE:
1.
FOR YOUR OWN SAFETY, READ INSTRUCTION
MANUALBEFOREOPERATlNGTHEMACHINEJTOOL.
Learn
the
machine's application and limitations plus
the specific hazards peculiar to it.
2.
GROUNDALL TOOLS.
If
machine
is
equipped
with
a
three
-
prong plug,
it
should be plugged into a three-
hole electrical receptacle.
If
an 'adaptor
is
used to
accommodate a two
-
prong receptacle, the adaptor
lug
must
be attached to a kno'wn ground. Nsver
remove the third prong.
3.
ALWAYS WEAR EYE PROTECTION AND HEAD
PROTECTION.
Always wear eye protection which
complieswith current
ANSI
STANDARD287.1 (USA).
4.
KEEP GUARDS IN PLACE
and
in
working order.
5.
REMOVE ADJUSTING KEYS AND WRENCHES.
Form habit of checking toseethat keys and adjusting
wrenchesare removed fromtool before
turning
it
'on'.
6.
KEEP WORK AREA CLEAN.
Cluttered areas and
benchesinvite accidents.
Built
up of sawdust
is
also a
7.
DON'T USEIN DANGEROUSENVIRONMENT.
Don't
use
power tools
in
damp or wet locations, or expose
them to rain. Keep work area well lighted.
8.
KEEPCHILDREN ANDVISITORSAWAY.
All
children
and visitors shoclld be kept a safe distance from work
area.
9.
MAKE WORKSHOP CHILDPROOF
-
with
padlocks,
master switches, or
by
removing starter keys.
10.
DON'T FORCETOOL.
Don't force tool or attachment
to do a job for which
it
was not designed.
11.
WEAR PROPERAPPAREL.
No looseclothing,gloves,
neckties, rings, bracelets. or other jewellery to get
caught
in
moving parts. Nonslip footwear
is
recommended. Wear protective hair covering to
contain long hair.
12.
AbWAYS VSE SAFETY GLASSES.
Wear safety
glasses (must comply
with
ANSI
287.1). Everyday
eye
-
glasses only have impact resistant lenses; they
are not safetyglasses. Also use face or dust mask
if
cutting operation
is
dusty.
extended periods of operation. Use muffs rated to
103
dBA
LEQ
(8
hour).
L
fire hazard.
13.
USE EAR PROTECTORS.
Use ear
muffs
for
14.
SECURE WORK.
Use clamps or a
vise
to hold work
when
practical.
It's
safer than using your hand and
frees both hands to operate tool.
15.
DON'T OVERREACH.
Keep proper footing and
balance at all times.
16.
ATTENTION TOWORK:
Concentrateon your work.
If
you become tired or frustrated, leave
it
for awhile and
rest.
17.
MAINTAIN TOOLSIN
TOP
CONDITION.
Keep tools
sharp and clean for best and safest performance.
Follow instructions for lubricating and changing
accessories.
\
18.
DISCONNECT TOOLS
before servicing and when
changing accessories such as blades,
bits,
cutters,
etc.
19.
USE RECOMMENDED ACCESSORIES.
The
use
of
improper accessories may cause hazards.
20.
AVOID ACCIDENTAL STARTING.
Make sure
switch
is
in
'OFF
position before plugging
in
power
cord.
21.
NEVER STANDONTOOL.
Seriousinjurycould occur
if
the tool
is
tipped or
if
the cutting tool
is
accidentally
contacted.
22.
CHECK DAMAGED PARTS.
Before further useofthe
tool,
a guard or other part that
is
damaged should be
carefully checked to
ensure
that it will operate
properly and perform
its
intended function
-
check
for
alignment of moving parts, binding of moving
parts. breakage of parts, mounting, and any other
conditions that may affect
its
operation.
A
guard or
other part that
is
damaged should be properly
repaired or replaced.
23.
DIRECTION
OF
FEED.
Feed work into a blade or
cutter against the direction of rotation of the blade or
cutter only.
24.
NEVER LEAVE MACHINE RLiNNlNG UNATTENDED.
TURN POWER OFF.
Don't leave machine
until
it
comes to a complete stop.
25.
'
DRUGS
,
ALCOHOL
,
MEDICATION
.
DO
not operate
tool while underthe
influence
of drugs,alcohol orany
:-.I;
+X:
medication.
r'-$26.
MAKE SURE
TOOL
IS
DISCONNECTED
FROM
POWER SUPPLY
while
motor
is
being mounted
connected or reconnected.
27.
WARNING:
The
dust
generated by certain woods and
wood products can be injurious to, your health.
Always operate machinery
in
well ventilated areas
and provide
for
proper dust removal. Use wood dust
collection systems whenever possible.
$,
C'
;/?t
k
P

ADDITIONAL SAFETY
RULES
FOR WOODLATHES
VI
#
1.
WARNING: DO NOT operate your lathe until it is
completely assembled and installed according to the
instructions.
2.
IF
YOU ARE NOT thoroughly familiar with the
operation of wood lathes, obtain advice from your
supervisor, instructor or other qualified person.
Instruction from
a
professional woodturning
instructor is strongly recommended.
3. MAKE SURE wiring codes and recommended
electrical connections are followed and that the
machine is properly grounded.
4.
NEVERturntheIathe'ON'beforeclearing the latheof
all objects (tools, scraps of wood, etc).
5.
ALWAYS stand to one side of revolving wood where
possible.
EXAMINE set
-
up carefully before turning on the
.,.,power.
7. MAKESURE tool rest height is adjusted properly.
8.
MAKE SURE tool rest is adjusted as close to the
9. ROTATE workpiece by hand to check clearance
10. NEVERadjustthetool restwhileworkpieceisturning.
11. REMOVE the tool rest before sanding or polishing.
12. WHEN TURNING between centres MAKESURE the
tailstock centre is snug against the workpiece and
locked. Thetailstock centreshould belubricated
if
it
is not a revolving/live/ball bearing centre. Suitable
lubricants are beeswax or parafin wax.
13. NEVER drive workpiece into drive centre when drive
centreis
in
headstock. Setdrivecentreintoworkpiece
with a soft mallet prior to installing it into the
headstock.
14.
NEVERattempt
to
drivecentre pieces intowood using
he tailstock quill action. Impaction of centre into
--wood must bedonewith a malletpriorto installation
*
between centres
in
the lathe. Secure work between
centreswith lightpressure from tailstock quill action.
See operation section.
15.
NEVER loosen tailstock spindle or tailstock while
workpiece is turning.
16. WHEN faceplate turning, MAKE SURE workpiece is
Securely fastened to the faceplate and that
appropriatesizefaceplateisusedto properlysupport
workpiece.
workpiece as possible.
before engaging power.
17. WHEN faceplate turning, MAKE SURE the screw
fasteners do not interferewith the turning tool at the
finished dimension of the workpiece.
18. ROUGH CUT workpiece as close as possible to
finished shape beforeinstalling
on
faceplate.
19. TIGHTEN all clamp handles beforeoperating.
20. EXAMINE workpiece for flaws and test glue joints
before placing workpiece in lathe.
21. NEVER use spindle turning chisels for faceplate/
headstock only mounted work. Using them for
faceplate
turning
could result
in
spindle chisel
grabbing the workpiece pulling the chisel from your
control and being flung
in
any direction.
22. WHEN roughing off,
DO
NOT jam tool (chisel) into
workpiece or take too biga cut.
23.
USElowest speed when starting a new workpiece.
24. ALWAYS operate the lathe at the recommended
speeds. Consult owner's manual for suggested
speeds.
25. MAKE all adjustments with the power
'OFF'.GRanqe
26. DISCONNECTlathefrompowersourcewhen making
27. DISCONNECTlathefrompowgrsourceandclean the
28. MAKESUREthe work area is cleanedbeforeleaving
29. SHOULD any partof your lathe bemissing. damaged
or fail
in
any way, or any electrical component fail to
perform properly, shut off switch and remove plug
from the power supply outlet. Replace missing,
,
damaged or failed parts before resuming operation.
i
-.when4athe+-
--
repairs.
machine before leaving it.
I\
the machine.
30. CAUTI0N:To reducetheriskofinjury,ALWAYSwear
safety glasses and face and head protection when
operatingwoodlathe.
31.
ADDlTlONALINFORMATIONregardingthesafeand
properoperation ofthis product is available from the
National Safety Council,
444
N. Michigan Avenue,
Chicago, IL60611
in
theAccident Prevention Manual
of Industrial Operations and also
in
the Safety Data
Sheets providedby the NSC. Please also refer to the
American National Standards Institute ANSI 01.1
Safety RequirementsforWoodworking Machinesand
the
U.S.
Department of Labour OSHA 1910.213
Regulations.

90
-
9412
-
004
TL1200 WOODLATHE
Page 3
Thank you forbuying one of the latestmachines in ourrange
-
the Nova TL1200woodlathe. The TL1200is avery versatilelathe
designed to provide the beginner, ormore experiencedturner
with amoderatelypriced unit capable of many differentturning
applications.
Thismachine is designedto accommodate largerinboardwork than
ourprevious TLl000. The TL1200 has an inboard capacityof
400mm (16in). Whenthe headstockispositioned at 90deg. to the
bed the capacity is increased to 600mm (24in)for largerbowl
turning (withan outriggersystem).
The followingpaged willprovideyou with basic setup
instructionsto enable you to begin turning. If you have any
queries about the setup
or
operation please don't hesitate to
contact the manufacturers.
At
Teknatoolwe value contactwith our customerswho areusing
our products.
If
you have any suggestionsor comments about our
productswe would greatly appreciate hearing from you.
WARNING
!!
SOURCE UNTIL THE LATHE
IS
COMPLETELY ASSEMBLED AND
....
YOU HAVE READ AND UNDERSTOOD INSTRUCTIONS IN THIS OWNERS
MANUAL.
FOR
YOUR
OWN
SAPETY,DO
N'OTCONNECT
THE
LATHE
TO
A
POWER
SPECIAL WARNING:
USNCANADA CUSTOMERS PLEASE NOTE SPEEDS
ARE
RATED
4'
20%
HIGHER RPM. See speedratings on page
6.
STANDARD EQUIPMENT
2 MT Spur(DrivingCenter),2MT Live RevolvingCentre (Tailstock),
300mm (12in) Toolrest, Polyvee Drive Belt, MotorPulley,
Adjustment wrenchesand locks.

TL1200 Preliminary Manual
Page 4
'*.
90
-
9404
-
003
*'
ASSERIBLY
Sr
SET
UP
INSTRUCTIONS
FORTL1200
WOODLATHE
.'
.
The photograph above is of the Motor Mount assembly. It consists
of
a. Motor Mount Plate
with
circlip attached to
the
shaft
b.
Heavy Duty Washer: to retairi the shaft. (B)
c. Left Hand Retaining Bolt.
(B)
-
-
d.
Adjusting Lever, threaded to screw into boss of Retaining Bolt.(B)
e. Circlip
on
Motor Mount Shaft. (B)
f.
Fastenings and Washers to
fix
motor
to
Motor Mount Plate.
(C)
Other
Parts:
8
s
eed Motor Pulley with
5/8"
bore
(C)
i.
4mm Allen Wrench to adjust
8mm
grubscrew (A)
7
j. 2MT Live Centre
(C)
.
k. 2MT Spur Centre
(C)
1.
Polyvee Drive Belt (Type
508
56)
(C)
(A)=
Part
of
Motor Mount Fastening
Kit
(in
accessory box)
(B)=
Part of Motor h4ount .Arm
&
Lock Arm
Kit
(C)=
Included
in
accessory box.
All
these part
are
either
with
the motor mount plate placed between lathe beds
or
in
the accessory box.
t
by
8:
Mfx
Smm
grubscrew to secure motor pulley to shaft
(A)

.TL1200Preliminary Manual
Page 10
MOTOR REQUIREMENTS
''
90
-
9412
-
004
New Zealand/Australia
A
singlephase, or split phase, continuous
duty,
50
Hertz electric
motor with a is recommended. A totallly enclosed fan cooled type
it provides extra dust protection for
the
motor.
Canada/USA
A
singlephase, ca acitator startor split phase, continuous duty, 60 Hertz electric
motor with a spee
B
of 1710 A totallly enclosed fan cooled type
(TEFC) is also recommende dust protection for the motor.
REMEMBER THAT
THE
AT 1710 RPM. THIS IS APPROX.
20%
FASTER THAN THE STANDARD 1425 RPM FOR
NEW
ZEALAND/AUSTRALIA
MOTORS. THIS MEANS THAT THE SPEED RANGE
IS
RATED
APPROX. 20%FASTER ALSO
-
SEE SPEED RANGE
P7.
POWER:
A
motor with a power ratin of
not
less
than 560
KW
(3/4
HP)
should
be
used.
A
___,
motor with less power will not be
suf
B
lcient for
the
larger diameter work that the
TL1200 is capable of. A 750
KW
(1
HP)
motor is also a good option, providing good
power with reasonable cost. Larger, heavy motor
o
tions are not recommended.
A
motor with a foot mounting frame size of B56
(N
E
,AUSTRALIA,UK)
or
NEMA 56
(USA,CANADA) is required
so
it
will
line
up
with
the
motor mount slots.
ROTATION
OF
MOTOR:
Motor
needs to rotate under power in
an
ANTI
-
CLOCKWISE direction (looking at
motor
from shaft side)
to
ensure lathe
spindle turns in an anti
-
clockwise direction
(lookingface on to lathe spindle).
To chan
e
to correct rotation: Refer Motor instructions or have wiring changed
by
qualifie
f
electrician.
MOUNTING PULLEY
ON
MOTOR SHAFT
First check
the
motor shaft size carefully. There is only 2
-
3 thousands of an inch
between imperial and metric sizes
-
BUT the difference is enough to make the pulley
either too tight to mount or loose when mounted. Standard shait sizes for motors:
1.
Diameter 5/8" 0.625
"
2. Diameter 16mm
0.6299
"
3. Diameter 3/4" 0.750
"
4. Diameter 19mm
0.748
"
An
eight step motor ulley is included with your accessor
-
kit.
It has a standard
5/8"
bore
as this
is
t
e motor shaft size most commonl available. If your motor has
.
a different shaft diameter then the
5/8"
pulley will nee
d
to be reamed/bored to the
correct size. This could be clone by a local engineering company.
v
E
FITTING PROCEDURE:
1.
Check for any burrs or dents
in
shaft with raised ridges. File these off
if
necessary.
2.
Fit key wa . Check that the key size
on
the
motor shaft will
fit
pulley.
The key shou
r
d
be a neat fit. Check keyway is free
of
burrs
and dents that will
5
Push
on
by hand until the pulley
just
clears the boss
on
motor. If necessary
GENTLY
tap
on
with
block of wood. Spin to check ulley is clear of boss.
4.
Use
tile
8mm rubscrew in place
using
the 4mm
A
P
en Wrench (both provided).
DO
NOT
USE
8NDUEFORCE.
revent the key seating.

w
TL1200 Preliminary Manual
Page
7
SPEED
ADJUSTMENT
90
-
9412
-
004
Please refer to photo
3,
page
5.
The TL1200 woodlathe has an 8 speed range:
NEW
ZEALAND/AUSTRALIA:
178,
300,
570,
850, 1200, 1800,2400,
3000
FOR MOTOR RATED AT 1425RPM.
CANADA/USA:
214,
360,
684,
1020, 1440, 2160, 2880,
3600
FOR MOTOR RATED
AT
1710 RPM.
Speeds can be changed by moving the belt to the required position on the 8 step
pulleys.
CHANGING
SPEEDS
x.__
The Motor Mount/Speed change lever is located to the
right
and at the back of
the
headstock. The assembly of this unit is described on page
6
of
this manual.
Please refer to photo
3,
page
5.
The motor is locked in position and the belt tensioned when the handle
is
pb'lled
towards the operator.
1. Push handle away from headstock to release tension.
2. Open front cover,
3.
Support motor weight with your left hand while positioning belt to required pulley
step
wlth
your right hand.
For
s
eed chanue onto largest step of headstock pulley (i.e. lowest speed):
Feed
YJ
elt rounzheadstock pulley
by
rotating spindle.
..,
4.
Remove left hand to allow the belt to take the weight of motor.
P
5.
Re
-
tighten motor mount plate by pulling handle towards the.headstock.
6.
Close front cover.
.i'

"_
'
TL1200
Preliminary
Manual
90
-
9404
-
003
Page
5
2
3
IVhen
the
motor
is
swung
up
to
change belts
the motor pulley should be slightly clear
of
the
headstock
pulley

-1200
Preliminary Manual
Page
8
HEADSTOCK SWIVEL OPERATION
For
turning bowls laroer than the inboard capacity of 400mm(16in)
the
headstock can
be rotated throught 98deg.
1.
Unscrew the headstock retaining
nut
(located between the bed rails under
the
headstock) sufficiently to rotate
the
securing plate parallel to the gap between the
bed rails.
2.
Make sure the bed rails under headstock are absolutely clean with no woodchips
or
even wood dust to
foul
the reseating
of
the headstock.
90
-
94
12
-
004
3.
Lift motor/headstock unit clear of bed rails,
turn through
90
deg. and reseat on the bed
kaving suificient room
on
the left of the
or Outrigger unit.
4.
Rotate headstock securing plate to again
cross both beds at 90 deg.
Check underneath to see that the securing
gee illustration right.
5.
Do
nut
up finger tight.
6.
Try
to move headstock back and
forth
to make sure it
is
seated properly.
7.
Tighten
nut
up one quarter turn with spanner.
--,leadstock to position the toolslide/rest
late
is
squareacross the beds.
Securing plate must be square to beds
CPNDLE
NDEX
The TL1200 is equipped with a
24
division spindle index.
The index unit is located above the spindle housin .
Sight hole for the index numbers is located to
the
eft of the spindle index.
To engaoe spindle index simply twist wheel until the larger central index pin drops
into
the
Role positions in headstock pulley.
To disengagepull wheel forward and twist to one side.
Make sure the guide pin drops into the indentation provided.
This will prevent index pin accidently re
-
engaging while spindle
is
turning under
power.
If
you have difficulty reading the number through the sight hole with larger diameter
work mounted, use
a
small hand mirror.
d
P
i
I
Oivisions
Required:
Index
Positfans
(siaht
hole)
~
2
0.12
3
08
6
0:6:!2,15
6
0.4.8.12,16,21
d
8
0,3.6.9,12,15,18,21
12
24
0.2.4,6,8,10,12,15,16,18,20,22
Ever.{
Position

TL1200
Preliminary Manual
90
-
9404
-
003
Page
9
CONNECTING TL1200 WOODLATHE TO POWER SOURCE
If
the motor is not provided with a lead and male plug, this must be wired in by a
registered electrician.
NEW
ZEALAND/AUSTRALIA/CANADAPUSA
The TL1200 woodlathe is supplied
to
all markets without a motor, switch or wiring.
The motor, switch and wiring leads are supplied as kits separately
from
suppliers
in
Canada and the
USA.
Canada: The motor with switch mounted
on
it can be supplied.
In New ZealandAustralia motors
can
be supplied with switches.
Please enquire with
your
stockist.
PLEASE FOLLOW MOTOR/SWITCH MANUFACTURERS
SAFETY
AND
INSTALLATION INSTRUCTIONS
GROUNDING INSTRUCTIONS
1,
WARNING: THEMOTOR, SWITCH
&
WIRING MUST BE GROUNDED
WHILE
IN
USE TO PROTECT
THE
OPERATOR FROM ELECTRIC SHOCK
If
there is a malfunction or breakdown, grounding in the electical circuit provides a
path
of
least resistance for electric current to reduce the risk
of
electric shock.
Check that
the
leads and wiring used
with
the motor and switch wirin have a
grounding conductor and have a grounding
lug.
The plug must be p ugwed into a
matching outlet that is properly installed an grounded in accordance wit6 all local
codes and ordinances.
Have a certified electrician check the electrical circuit and plugs
if
the grounding
instructions are not completely understood
or
if
in
doubt
as
to whether the machine
or
motor/switch is properly grounded.
Improper connection
of
the equipment grounding conductor can resilt
in
the risk of
an
electric shock. The conductor
with
insulation with an outer surface that is green,
with or without yellow stripes is the equipment roundinu conductor.
If
repair
or
replacement
of
the electrlc cord
is
neccesary,%O NOT connect the equipment grounding
conductor
to
a live terminal.
B
H
DO
NOT
MODIFY
THE
PLUG PROVIDED
WITH
MOTOR
&
SWITCH
-
IF
IT
WILLNOT
FIT
THE
OUTLET HAVE
THE
PROPER OUTLET
'INSTALLED
BY
A QUALIFIED ELECTRICIAN.
USMCANADA

TL1200
Preliminary Manual
‘(*
90
-
94
12
-
004
Page
6
MOTOR MOUNT PLATE
Please also refer to pages
2
&
3.
The first stage of assembly is to
fix
the motor mount plate to the lathe.
Stage
1
1.
Remove Red back cover by unscrewing
the
6
M5xlOmm
screws.
2.
Slide shaft
of
the motor mount plate into bored hole at the back of headstock
casting (see hot0
1,
page
5).
3.
Push
the
K
otor Mount Shaft home until the circlip (see photo page
2,
part
e.)
butts
up
against
the
rim
of the bored hole in Headstcock.
4.
Screw the Left Hand Retaining Bolt (photo page
2
art
c.
)
through the Heavy Duty
Washer (photo page
4,
part b.) into the end
of
the shg. Remember that the bolt has
a left hand thread.
5.
Screw the bolt as tight as possible by hand.
6.
The Adjusting Lever (Photopage
4,
part d.) can now be screwed into the boss of
belt tension when changing speeds.
‘-~-
the Left Hand Retaining Bolt. This now becomes
the
lever you use to apply/release
MAKE
SURE
THE
MOTOR
HAS
A
FOOT MOUNTING
AND
A
FRAME
SIZE
B56: NZ,
AUSTRALIA,
UK.
NEMA
56:
USA/CANADA
Stage
2
7.
Mount motor pulley
on
motor shaft and
fix
in place by means of the 8mm grubscrew
I
provided.,Use 4mm wrench provided to tighten.
Stage
3
8.
Loosely bolt motor
to
plate using the
M8x25
bolts, M8 nuts and M8 washers
Yl.
Use a straight edge butted against one of the headstock pulley steps and move
the
motor to line
up
the corresponding motor pulley position
by
line of slght.
12.
Check that the motor pulley is square to
the
line
of
the headstock pulley and a
final check that it is ositioned correctly with the matching steps
of
the headstock
pulley. These shoul
2
be matching in a ste ped osition with the face of the pulley
.
Check
thwhen you
swing
the motor up, the
motor
pu ey
is
;lightly
clear,
of
the
headstock pulley.
rovided.
L
steps slimhtly behind that
of
the motor pufey. feephoto
2,
Rage
5
13.
Now tighten the motor firmly to plate.
14. Replace Red back cover.
CHECK THAT THE MOTOR
IS
PROPERLY POSITIONED
SO
PULLEY DOES NOT FOUL
COVER

*r
TL1200
Preliminary Manual ~
9-
90
-qsot-
-
uD
re
Page 11
VENCH/STAND REQUIREMENTS
A
sturdy and rigid bench/stand ortant
so
that the TL1500 can give optimum
performance. It needs to be ade braced for the stresses of larger turning
work.
A
very common fault woodlathe installations is that inadequate
attention is given to bench/stand requirements which can result in poor lathe
performance.
STAND DESIGN:
Plans for a stand design for
the
TL1200
&
TL1500 that can be easily
constructed from wood are included at the back of this manual.
LOCATION
IN
WORKSHOP
F*
Your space re uirements are depent
on
the
sort
of turning you want to do. If
you
wish to do out
8
oard turning or dee hole drilling, for example, space must be left
around
the
lathe to give you room
F
or these operations.
Other points to consider:
-
locatxon in relation to windows, lights and power source.
-
handy stora e of chisels and other lathe tools.
-
location of
i:
athe
so
that it does not restrict the use of other machines in the
workshop.
LATHEHEIGHT
FROM
FLOOR
The height of the lathe from floor is determined by the hei
ht
of turners that use
the lathe. Ideally the lathe should be positioned such that
t
a
e centre line through
the lathe spindle to centre of tailstock spindle, is at the same height as the
turner's forearm bent
so
that it is at a relaxed position arallel to the floor.
If there are several ersons which may be using the lat e, it might be better to
position it at a goo average height.
Alternatively make the stand for the tallest turner and use duckboards for others to
stand on, to adjust their height.
SECURING LATHE
TO
BENCHBTAND
...
a
K
1.
Make sure that the surface to bolt lathe to is level and flat.
L'
*
If surface
is
not level and flat this could result
in
twisting of
P
the lathe bed which
will
affect lathe centering.
Use
a
bubble level to check bench.
2.
4
x
M12
bolts, nuts of suitable length for your benchlstand top plus washers.
These fastenin
s
are not provided.
3.
Check benc
B
I
surface is clean
so
no rubbish
will
get trapped under lathe before
boltin down.
4.
Tig
a
ten down the 2 headstock bolts
-
tightening down positions in a diagonal
sequence. Then tighten down 2 bolts on lathe foot.
c
i
,..
..
...
.
.
,
..
.
.
.
.
,
.
-
.
-
..
-
-
-
I

,
%'
(
Step
4.
-
Glueand screw the end panels into place flush wiih
the
top
of
the legs as
'
shown
in
Diagram D.
Dl
aoTroM
RAILS
10Ox501nm
:
Step
5.
-
Measure and cut the bottom panel
to
width. Glue and screw into position.
"
Step
6.
-
At
this stage your bench could be painted
if
desired.
..
Step
7.
-
Load
up
theinteriorwith bagsof sand, bricksorrocks. (Firstposition
it
inthe
j
workshop).
Step8.
-
Boltyour lathe
to
thebenchtop. Makesureyour bowlblankwillclearthe
top
:
rails and legs when it is swivelled through
90"
for
larger turnings.
j
Step9.
-
Bolt the bench top
to
the top rails.
:
There aremanyvariations andalterations that could be rnade:but
so
longas the basic
~ sheet bracingeffect is retained, a strong, rigidbenchshould result.
;
Finally the area
of
the side panel between the legs could make a convenient place to
.
rack chisels, faceplates
or
other accessories.
~
>
9
1
-
93
12-008
STAND
PLANS
FOR
NOVA
TL1500
and
NOVA
TL1200
WOODLATHES
SIMPLE
'DIY'
CONSTRUCTION, LOW COST MATERIALS, ROBUST DESIGN.
LATALEX LIMITED
Aucklaod,
New
Zealantl
.
65
The Concourse, Henderson

LATHE STAND
.$
(
Designed
by
Trevor
Cole
-
01993
TEKNA
I
ciOL
Vibration in a woodlathe
is
the woodturner's worst enemy and a good stand can go a
longway towards eliminating this.
Any lathe deserves the best stand you can afford or build and the NOVA
TL1500/TL1200 woodlathes are
no
exception.
A
lathestandshouldbestrong, rigid,thecorrect heightandfastenedtothefloor.
If
you
donotwish tqfastenyourlathestandtothefloorthenconsiderincreasingtheweight by
loading
it
with bags of sand, bricks, rocksoranyweighty materialyou haveavailable.
Strengthisachieved by usingsuitable sizes of materials. Rigidityis achieved by sound
construction methods.The height
is
different
for
each individual.
A
spindle height
approximately50mrnabovetheelbow easesthelower back byallowingamore upright
stance during turning.
This simple design for a lathe stand is very strong. Rigidity is achieved by the use
of
panels as sheet braces and it has provision for the maker to increase its weight by
loadingthe boxed interior.
Constructionissimple, usingonlyonewoodworking joint andhelping
to
keepcoststo
a minimum.
Use
of recycled materials could further reduce the cost.
MATERIALS LIST
-
1
Sheet of2.4mx1.2mx18mm medium density fibreboard
(MDF
orCustomwood).This
is for the side panels and the base of the box.
4
Piecesof1.6mx100mmx50mmRadiatapineorsimilar.Thesemakethetopandbottom
rails.
4
Pieces ofmk100rnmRadiata pineorsimilar. These makethe legs
-
the lengthwill
vary dependlag onwhat height you makeyourstandbutyouwill needapproximately
750mm for each leg.
1
Pleceof 1.636mx500mmx50mm of any suitable solid material
to
make the top.
Hardware
-
Glue and screws
to
fasten panels.
Havingassembled allyourmaterials, constructioncanbestartedbyfollowingthesteps
as set out.
Bolts, length
to
suit for bolting lathe to top and bolting top
to
top rails.
Step
1.
-
Mark and cut
your sheet
of
SIOE
PANEL
M.D.F.
to
the
I
6111.U
45,ll
sizes shown in
Diagram
A.
IlOlTOM
I'ANEL
1.6181
~111111
ID
wahu
OYUI.II
0
511,
DIAGRAM
WASTE
/'
Step 2.
-
1
,in
the top rails to the legs
we need
to
,.,ark and cut the angle halving
joint as shown
in
diagram B.
DIAGRAM
B
10Ox50mm
i;J
lOOxlOOmm
Step
3.
-
Fastenthetoprailsandlegs.Glueandscrewthesidepanel
to
thelegsandtop
rail. Finallyfasten the bottomrail
to
thelegs
and
hardupagainst the bottomof the side
panel. Your assembly shouldlook like Diagram
C.
Repeat the same procedure which
gives you the two sides of the bench.
DIAGRAM
C
Table of contents
Other Teknatool Lathe manuals
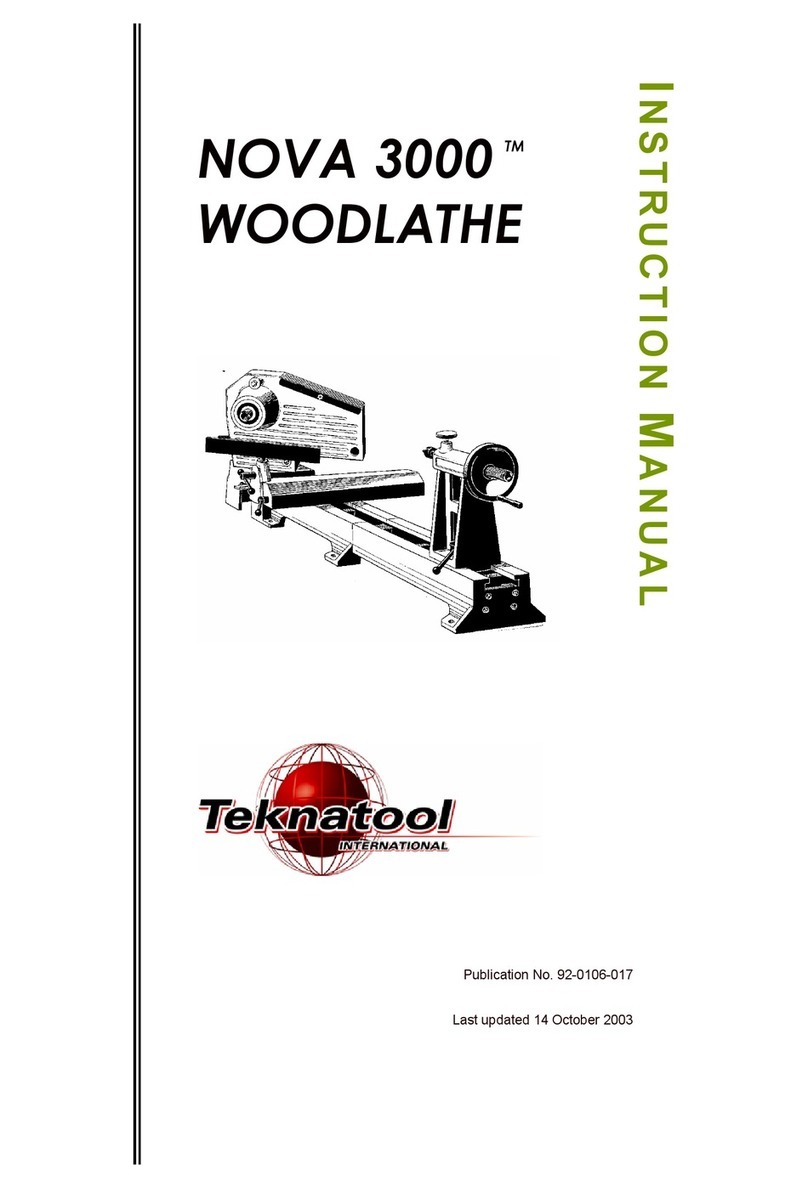
Teknatool
Teknatool NOVA 3000 User manual
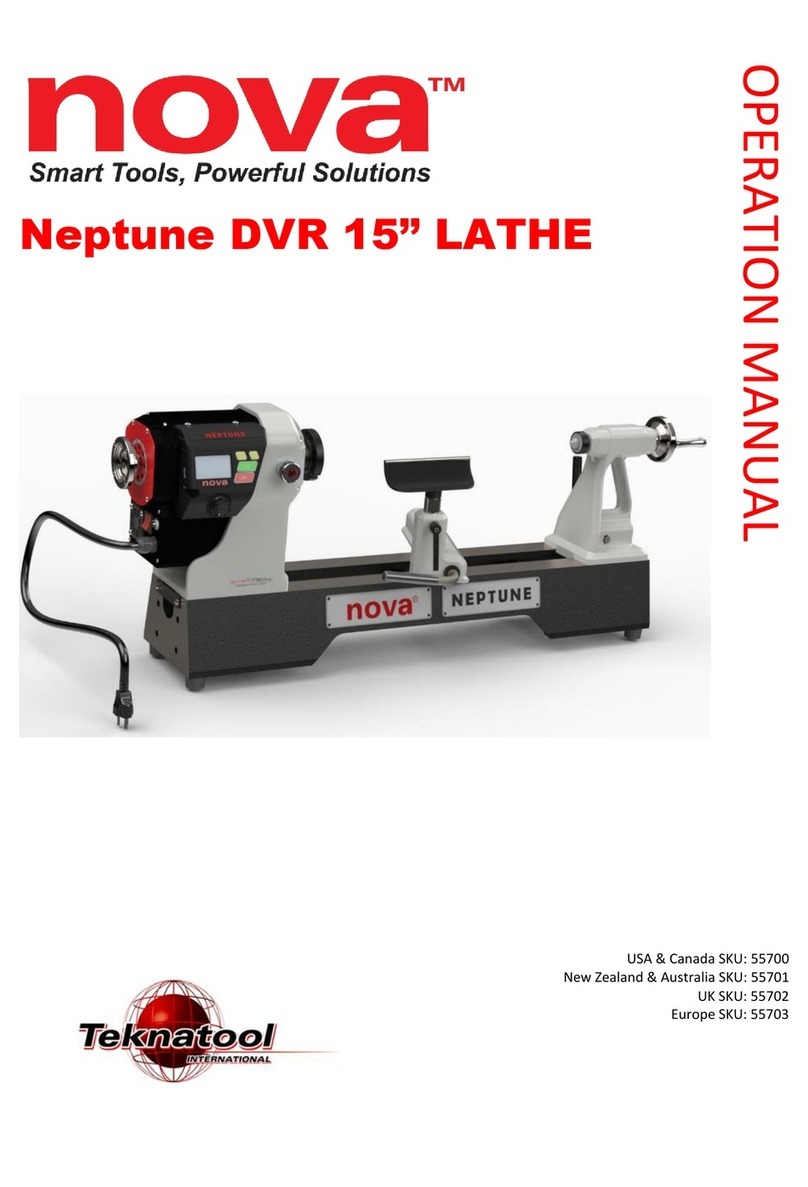
Teknatool
Teknatool nova Neptune DVR User manual
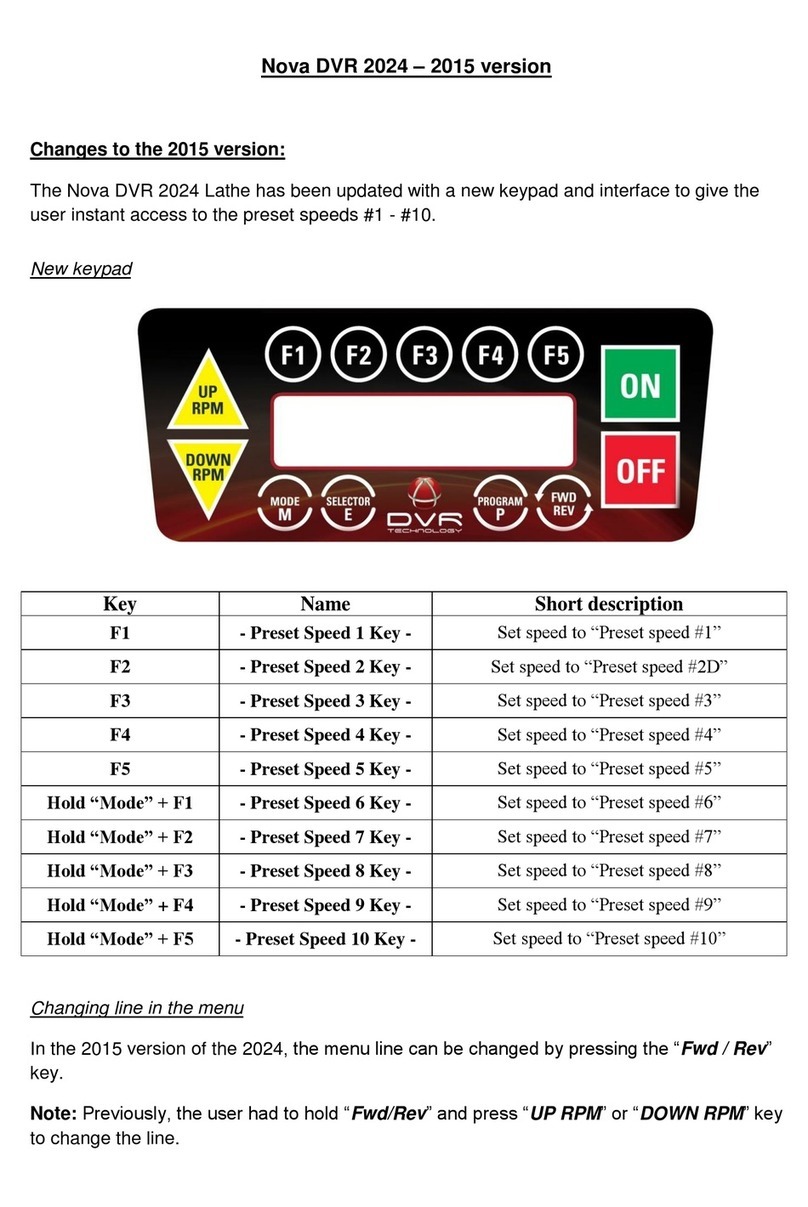
Teknatool
Teknatool Nova DVR 2024 User manual

Teknatool
Teknatool NOVA 1624 II User manual
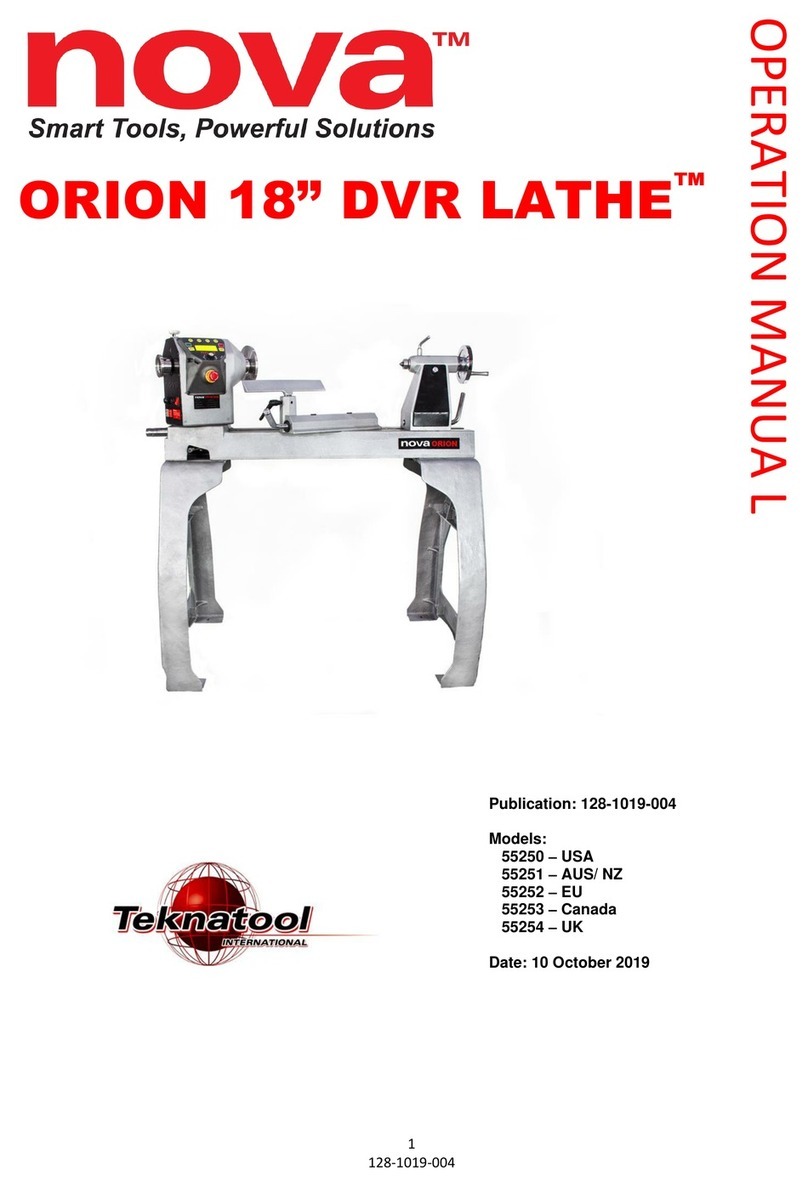
Teknatool
Teknatool nova ORION Series User manual
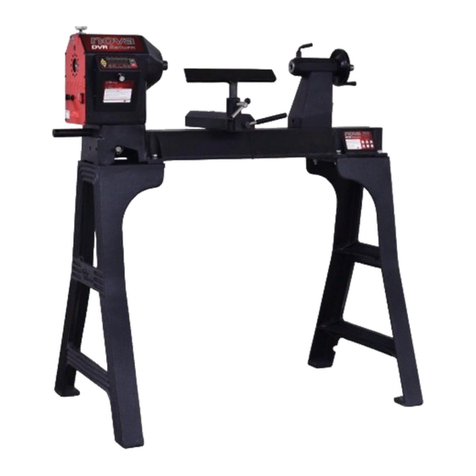
Teknatool
Teknatool NOVA DVR SATURN User manual
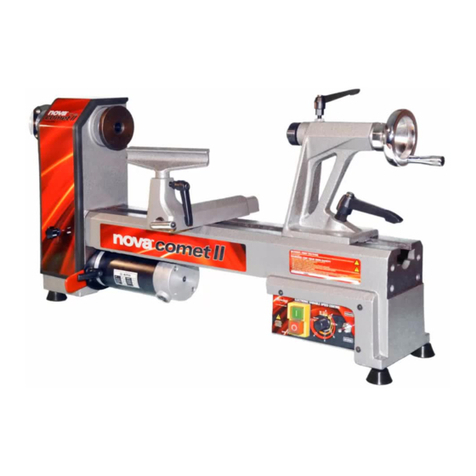
Teknatool
Teknatool NOVA Comet II Technical reference manual
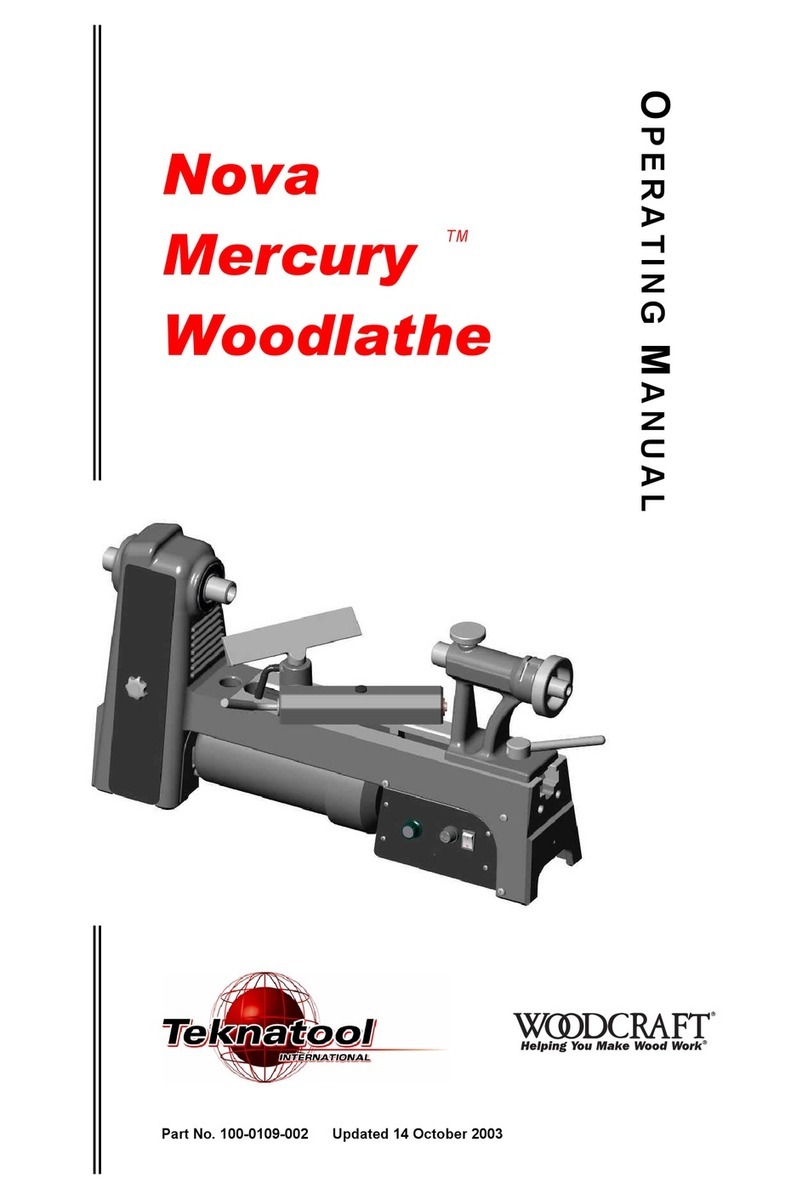
Teknatool
Teknatool Nova Mercury User manual
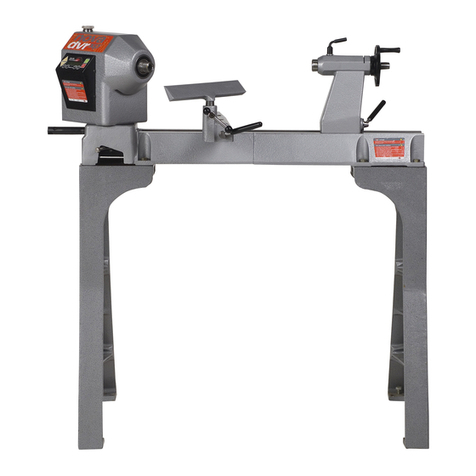
Teknatool
Teknatool NOVA DVR XP User manual