Tektronix 7D15 User manual

Ibktronix^
COMMITTED TO EXCELLENCE
PLEASE CHECK FOR CHANGE INFORMATION
AT THE REAR OF THIS MANUAL.
7D15
UNIVERSAL
COUNTER/TIMER
INSTRUCTION MANUAL
Tektronix, Inc.
P.O. Box 500
Beaverton, Oregon 97077 Serial Number
070-1433-00
Product Group 42 First Printing SEP 1974
Revised APR 1985

Copyright ®1974 Tektronix, Inc. All rights reserved.
Contents of this publication may not be reproduced in any
form without the written permission of Tektronix, Inc.
Products of Tektronix, Inc. and Its subsidiaries are covered
by U.S. and foreign patents and/or pending patents.
TEKTRONIX, TEK, SCOPE-MOBILE, and are
registered trademarks of Tektronix, Inc. TELEQUIPMENT
is aregistered trademark of Tektronix U.K. Limited.
Printed in U.S.A. Specification and price change privileges
are reserved.
INSTRUMENT SERIAL NUMBERS
Each instrument has aserial number on apartel insert, tag,
or stamped on the chassis. The first number or letter
designates the country of manufacture. The last five digits
of the serial number are assigned sequentially and are
unique to each instrument. Those manufactured in the
United States have six unique digits. The country of
manufacture is identified as follows:
BOOOOOO
100000
200000
300000
700000
Tektronix, Inc., Beaverton, Oregon, USA
Tektronix Guernsey, Ltd., Channel Islands
Tektronix United Kingdom, Ltd., London
Sony/Tektronix, Japan
Tektronix Holland, NV, Heerenveen,
The Netherlands

7D15
TABLE OF CONTENTS
Page
Section 1SPECIFICATION Section 3CIRCUIT DESCRIPTION (Cont’d)
Introduction 1-1 Readout Theory
Electrical Characteristics 1-1 General
Environmental Characteristics 1-7 CH 1Column and Row Data
Physical Characteristics 1-7 CH 2Column and Row Date
Section 2OPERATING INSTRUCTIONS
Installation 2-1
Overflow
-5 VSupply
Front Panel Controls and Connectors .2-2 Section 4MAINTENANCE
Modes of Operation 2-7 Introduction
Operation and Checkout 2-10 Preventive Maintenance
WARNING
THE FOLLOWING SERVICING INSTRUCTIONS
ARE FOR USE BY QUALIFIED PERSONNEL ONLY.
TO AVOID PERSONAL INJURY, DO NOT PERFORM
ANY SERVICING OTHER THAN THAT CONTAINED
IN OPERATING INSTRUCTIONS UNLESS YOU ARE
QUALIFIED TO DO SO.
Section 3CIRCUIT DESCRIPTION
Introduction 3-1
Block Diagram Description 3-1
General 3-1
Input 3-1
Clock 3-1
Troubleshooting
Corrective Maintenance
Component Replacement .. .
.
Recalibration After Repair ....
Repackaging for Shipment ..
Section 5CALIBRATION
Recalibration Interval
Test Equipment Required
Calibration Procedure
Index to Calibration Procedure
Section 6INSTRUMENT OPTIONS
Section 7ELECTRICAL PARTS LIST
Abbreviations and Symbols
Page
3-10
3-10
3-10
3-12
3-13
3-14
4-1
4-1
4-1
4-3
4-4
4-4
4-4
5-1
5-1
5-4
5-
5
6
-
1
Gate 3-2
Counters and Readout 3-7
Reset 3-7
Trigger Input Amplifiers 3-8
Time Base 3-8
Arm Inputs 3-9
Reset Circuitry 3-9
Section 8DIAGRAMS AND CIRCUIT BOARD
ILLUSTRATIONS
Symbols and Reference Designators
Section 9MECHANICAL PARTS LIST
CHANGE INFORMATION
REV NOV 1981

7D15
OPERATORS SAFETY SUMMARY
The general safety information in this part of thesummary
is for both operating and servicing personnel. Specific
warnings and cautions will be found throughout the
manual where they apply, but may not appear in this
summary.
Terms In This Manual
CAUTION statements identify conditions or practices that
could result in damage to the equipment or other property.
WARNING statements identify conditions or practices
that could result in personal injury or loss of life.
Terms As Marked on Equipment
CAUTION indicates a personal injury hazard not im-
mediately accessible as one reads the marking, or a
hazard to property including the equipment itself.
DANGER indicates apersonal injury hazard immediately
accessible as one reads the marking.
Symbols In This Manual
AThis symbol indicates where applicable
cautionary or other information is to be
found.
Grounding the Product
This product is grounded through the grounding conduc-
tor of the power cord. To avoid electrical shock, plug the
power cord into aproperly wired receptacle before
connecting to the product input or output terminals. A
protective ground connection by way of the grounding
conductor in the power cord is essential for safe opera-
tion.
Danger Arising From Loss of Ground
Upon loss of the protective-ground connection, all
accessible conductive parts (including knobs and con-
trols that may appear to be insulating) can render an
electric shock.
Use the Proper Power Cord
Use only the power cord and connector specified for your
product.
Use only apower cord that is in good condition.
For detailed information on power cords and connectors,
see maintenance section.
Refer cord and connector changes to qualified service
personnel.
Symbols As Marked on Equipment
DANGER —High voltage.
%
Protective ground (earth) terminal.
ATTENTION —refer to manual.
Power Source
This product is intended to operate from apower source
that will not apply more than 250 volts rms between the
supply conductors or between either supply conductor
and ground. Aprotective ground connection by way of the
grounding conductor in the power cord is essential for
safe operation.
Use the Proper Fuse
To avoid fire hazard, use only the fuse of correct type,
voltage rating and current rating as specified in the parts
list for your product.
Refer fuse replacement to qualified service personnel.
Do Not Operate in Explosive Atmospheres
To avoid explosion, do not operate this product in an
explosive atmosphere unless it has been specifically
certified for such operation.
Do Not Remove Covers or Panels
To avoid personal injury, do not remove the product
covers or panels. Do not operate the product without the
covers and panels properly installed.
i
II REV BJAN 1981

7D15
SERVICE SAFETY SUMMARY
FOR QUALIFIED SERVICE PERSONNEL ONLY
Refer also to the preceding Operators Safety Summary.
Do Not Service Alone
Do not perform internal service or adjustment of this
product unless another person capable of rendering first
aid and resuscitation is present.
Use Care When Servicing With Power On
Dangerous voltages exist at several points in this product.
To avoid personal injury, do not touch exposed connec-
tions and components while power is on.
Disconnect power before removing protective panels,
soldering, or replacing components.
Power Source
This product is intended to operate from apower source
that will not apply more than 250 volts rms between the
supply conductors or between either supply conductor
and ground. Aprotective ground connection by way of the
grounding conductor in the power cord is essential for
safe operation.
@JAN 1981 m


Section 1—7D15
SPECIFICATIONS
Introduction
The 7D15 is adigital counter plug-in designed for use with all readout-equipped 7000-Series Oscilloscope mainframes.
It will function in any plug-in compartment; however, in the vertical compartment, aselectable display is internally con-
nected to the oscilloscope. When used in the horizontal compartment, mainframe triggers are available to the 7D15.
The 7D15 has eight modes of operation: Frequency—DC to 225 MHz direct. Frequency Ratio—0to 10® :1, Period-
10 ns to 10® s. Period Averaging— 10 ps resolution, TIM— 10 ns to 10® s, TIM Averaging— 1ns accuracy. Totalize— 1to 10®
events. Manual Stop Watch—to 10® s.
The electrical specifications listed in the Performance Requirement column are valid over the stated environmental range
for instruments calibrated at an ambient temperature of -»-20°C to +30‘*C and after afive minute warmup unless otherwise
noted. The information listed in the Supplemental Information column indicates typical instrument operation and is not to
be construed as a requirement for proper instrument operation.
TABLE 1-1
ELECTRICAL CHARACTERISTICS
Characteristics
MEASUREMENT MODES
Frequency Mode
Range DC to 225 megahertz
Performance Requirement
Resolution 0.1 hertz minimum
‘Accuracy
Period Mode
Range
Efreq (hertz) =±TB XF-,n ±1/T
Efreq (%) =100% r± TB *
10 nanoseconds to 10^ seconds with averaging times of XI to X1000 in decade
steps.
Resolution
*Accuracy
Time Interval Mode
Range
Resolution
10 picoseconds maximum.
Eper (sec) =±TB XPj^ ±1X10-® ±K± Pck
M
Eper (%) =100% T„,±1X10-»lKlPck
PinXM
6nanoseconds to 10® seconds with averaging times of XI to XI 000.
0.1 nanosecond usable.
'Accuracy (nominal) Eji (sec) =TB XPj„ ±(Pck/VM) ±10“® ±K
(Pck/VM) ±10-9 ±K
Eji (%) =100% ±TB ±—
Iin
The complete expression for Time Interval averaging depends on signal to noise
ratio and statistical distribution factors.
'Refer to Figs. 1-2 through 1-7 et the reer of this section for edditionel eccurecy informetion.
REV. A, APR. 1976 1-1

Specifications—7D15
TABLE 1-1 (cont)
Characteristics Performance Requirement
Frequency Ratio
CH B/EXT clock
Range 10-’ to 10-*
Totalize, CH B:
Range 0to 10® counts
(Manual ON—OFF control or electrical control from CH A,)
Manual Stop Watch
Range 0to 10® seconds
NOTE
Formulas given where TB (dec %) is the time base accuracy; is the period or time interval of the unknown
signal (whichever is applicable); Mis the number of averages taken; is the measurement dock period; Tis the
gate time; is the frequency of the unknown signal; is equal to the peak noise amplitude at the input to
the counter gate circuit; dv/dt is the signal slope at the input to the gate; Kis equal to
Characteristics Performance Requirements Supplemental Information
INPUT SIGNALS CH A&B
Frequency Range (CH Bonly)
DC Coupled
AC Coupled
DC to 225 megahertz
5hertz to 225 megahertz
Sensitivity
CH A&Binputs
TRIG SOURCE
100 millivolts peak-to-peak
1
Vertical deflection of:
0.5 divisions to 50 MHz
1.0 divisions to 225 MHz
or to the vertical system bandwidth,
whichever is less.
Input Resistance and
Capacitance
Approximately 1megohm, 22 picofarads
Minimum Pulse Width 5nanoseconds
Minimum gate “OFF" time
Between Samples During
TIM Averaging Operation
10 nanoseconds
Maximum Input Voltage 200 volts DC linearly derated to 20 volts
at 200 megahertz
Emax =20 +180 (1 -Fjp(MHz)/200
1-2 REV CXJT 1982

Specifications—7D1
5
TABLE 1-1 (cont)
Characteristics Performance Requirements Supplemental Information
Minimum Signal Period in
"PER" Mode 10 nanoseconds
Minimum CH AInput Pulse
Width in "FREQ B-CH A
Gate" Mode
10 nanoseconds
Triggering
Preset Position Automatically triggers at 0volts
Level Control
Range: (CH Aand CH B) .1 V, ±5(X) millivolts; 1V,±5 volts; 10 V,
±50 volts
Range: TRIG SOURCE Approximately ±2.5 divisions
Arming Inputs
Input Rand CApproximately 10 kiiohm, 20 picofarads
Lead Time for Pulse to
become effective
5nanoseconds
Lead Time to Negate
effect of "ARM" 5nanoseconds
Minimum rise and fall rate dv/dt >10 Volts per microsecond
Sensitivity AARM Alogical "1" occurs with either no signal
applied or with +0.5 volt or greater. A
logical "0" occurs with less than +0.2 volt
@1sink <0.2 milliampere
BARM 1
Logic "1" <0.2 volt or no signal applied
Logic "0" >+0.5 volt
Maximum Operating Voltage +10 volts to —5 volts
Maximum Input Voltage ±15 volts
External Clock In
input Requirements Internal switch selectable
Minimum Amplitude 0.8 volt peak-to-peak sine wave or pulse
with 30% to 70% duty cycle
Coupling AC
@1-3

Specifications—7D1
5
TABLE 1-1 (cont)
Characteristics Performance Requirements Supplemental Information
Maximum Input Voltage ±50 volts DC, 20 volts peak-to-peak
Frequency Range 1megahertz ±5%; Phase Lock Opera-
tional. 10 nanosecorKis, 100 nanoseconds
clock available.
20 hertz to 5megahertz; Phase Lock
Nonoperational.
RESET—Front Panel Reset initializes the instrument. All
counters are affected, including averagir^g
circuits.
Input Rand CApproximately 10 kilohms, 30 picofarads
Input Requirements
Amplitude Logic "1 "+2volts or greater
Logic "0" +0.5 volt or less
Pulse Width >500 nanoseconds
Maximum Operating
Input Voltage
+10 volts to —10 volts
Rise and Falltime 100 nanoseconds or less
Maximum Input Voltage ±15 volts
Reset (located on Rear
Interface B13) Negative-going transition TTL compatible
pulse
Rise and Falltime <100 nanoseconds
Width >500 nanoseconds
Hold Signal (located on
Rear Interface B22) TTL compatible, negative-logic signal
Rise and Falltime <200 nanoseconds
Propagation Delay for
Signal to become
effective or ineffective
<100 nanoseconds
I
@
1-4

Specifications—7D15
TABLE 1-1 (cont)
Characteristics Performance Requirements Supplemental Information
INTERNAL TIME BASE
Crystal Oscillator
Frequency 5megahertz
Accuracy
0°C to +50° CWithin 0.5 part per million
Long Term Drift 1part or less in 10^ per month
OUTPUT SIGNALS
Monitor Signals
Clock Out Logic "1" =+0.5 volt ±10% into 50 ohms
Logic "0" <0volt into 50 ohms. TTL
compatible without 50 ohm load (1.6
milliamper current capacity)
Zout ohms
Aand BTrigger Level
Externally Programable
with ±5 volt Signal
maximum and in the
Preset Position
Zout 1kilohm
Vq,j^ =±0.5 volt into 1megohm
(lOX scaling)
Analog Display (Internally
Connected)
Position
Front panel switch selects either "True
Gate" signal, "Pseudo Gate", or "Channel
"B" out
Controlled by front panel screwdriver
control
The Pseudo Gate signal is ahigh-speed
representation of the 7D15 gate signal
Amplitude 1.0 division. Can be set from 0.2 to 1div
±20%. Changed by resistor alteration
Rise and Falltime Less than 2nanoseconds
Propagation delay: Input
BNC's to plug-in interface
True Gate; 20 nanoseconds
Pseudo Gate; 18 nanoseconds
CH B: 16 nanoseconds

Specifications—7D15
TABLE 1-1 (cont)
Characteristics Performance Requirements Supplemental Information
Displayed gate width to
"effective" gate width Matches to within 1nanosecond; depends
on correct calibration of horizontal time
base used
In "Freq" or "events":
operation, lead time required
of gate display over CH B
display to guarantee
proper accumulation or
non-accumulation of count.
>1nanosecond
External Display Located on front partel, same as "analog
display" except position and amplitude
controls have no effect
Amplitude Logic "1" =-^0.5 volt ±10% into 50
ohms.
Logic "0" <0volt Into 50 ohm TTL
compatible without 50 ohm load (1.6
milliamper current capability)
Rise and Falltime >1.5 nanoseconds with 50 ohm load
Propagation delay from
input BNC's to display
1
True Gate: ^21 nanoseconds
Pseudo Gate: *»19 nanoseconds
CH B^17 nanoseconds
"True Gate" &"Pseudo
Gate" output pulse width
to "Effective Gate"
Matches to within 1nanosecond
Busy Signal (located on
Rear Interface A22) Nominally TTL compatibility, positive
logic
Rise and Falltime 100 nanoseconds maximum
Delay After Reset Command 150 nanoseconds maximum
DISPLAYS
Gate Indicator ALED lamp indicates internal gate
condition
Display Mode Switch Front panel switch allows selection
of readout "follow or store"
Display Time Control Continuously variable from 0.1 second or
less to approximately 5seconds. With
control in maximum clockwise position,
the display is held indefinitely

Specifications—7D 15
TABLE M<cont)
Characteristics Performance Requirements Supplemental Information
Readout 8digits of display, the four most signifi-
cant digits have zero suppression.
Overflow by ">" arrow. Legend located
on Channel 2of readout system
•
Resolution, Minimum
Frequency 0.1 hertz
Per, TIM 10 nanoseconds
Multi-per 10 picoseconds
Multi-TIM 100 picoseconds (limited)
TABLE 1-2
ENVIRONMENTAL CHARACTERISTICS
Refer to the specification for the associated oscilloscope.
TABLE 1-3
PHYSICAL CHARACTERISTICS
Size Fits all 7000-Series plug-in compartments.
Weight 3.1 Pounds (1.4 kilograms)
@1-7

10%
Specifications—7D 1
5
N
X
o
N
I
s
8
N
I
S
o
N
X
S
>-
o
z
LU
D
a
LU
OC
LL
h-
D
Q.
z
N
X
8
N
X
o
ae ae a? a«
°8
WORST CASE MEASUREMENT ERROR
N
X
o
o
o
1432-2
1-8 REV. A, APR. 1975
Fig.
1-2.
7D15
Frequency
mode
accuracy
stated
in
percent.

Fig.
1-3.
7D15
Frequency
mode
accuracy
stated
in
hertz.

10%
Specifications—7D 15
6
(/)
E
o
o
Q
O
oc
UJ
lA Q-
v>
a.
o
o
(
(
WORST CASE MEASUREMENT ERROR 1432-4
1-10 REV. A. APR. 1975

CLOCK
=
1ms
AVERG
=
X1
Specifications—7D 15
WORST CASE MEASUREMENT ERROR 1432-5
REV. A, APR. 1975 1-11
Fig.
1-5.
7D15
Period
mode
accuracy
stated
in
time.

10
%
Specifications—7D 15
(/)
E
o
o
t/t
E
o
(A
E
in
a.
o
o
in
a.
o
I/I
c
o
<
>
oc
m
h-
Z
IXI
5
I-
t—
D
a.
Z
WORST CASE MEASUREMENT ERROR 1432-8
1-12 REV. A, APR. 1975
Fig.
1-6.
7D15
Time
Interval
mode
accuracy
stated
in
present.

Specifications—7D 15
WORST CASE MEASUREMENT ERROR 1432-7
REV. A, APR. 1975 1-13
Fig.
1-7.
7D15
Time
Interval
mode
accuracy
stated
in
time.

Other manuals for 7D15
2
Other Tektronix Timer manuals
Popular Timer manuals by other brands
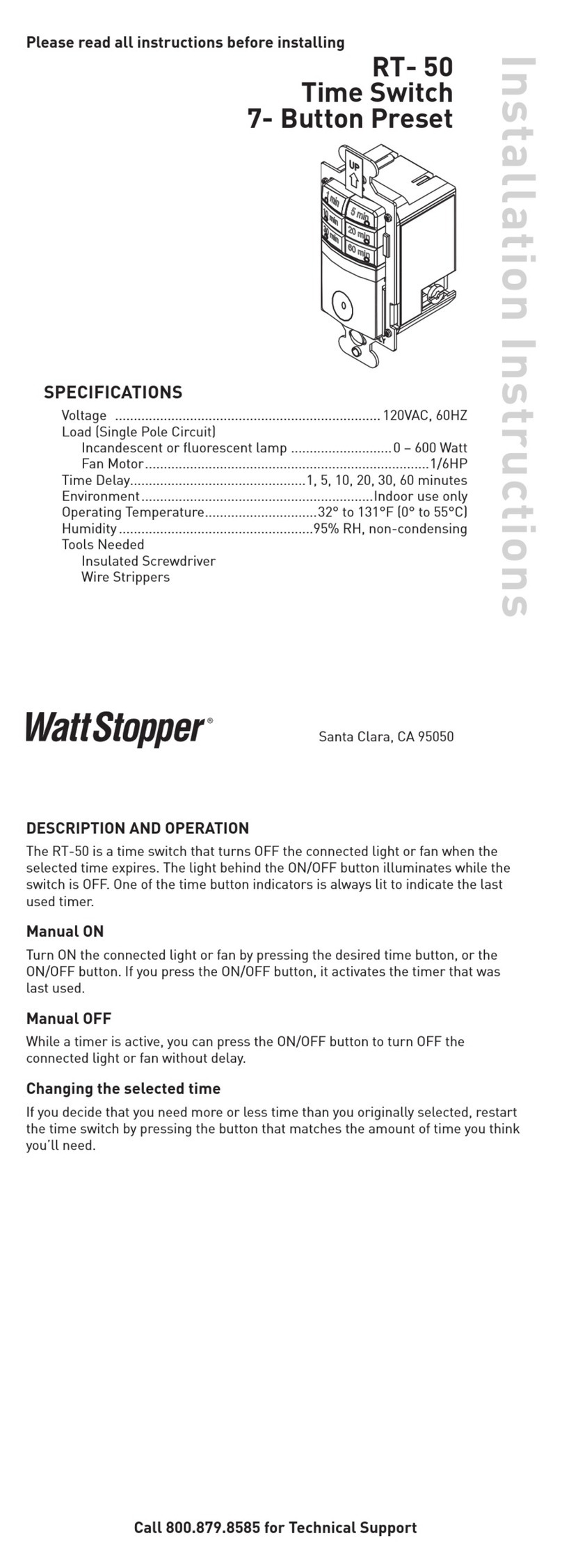
wattstopper
wattstopper RT-50 installation instructions
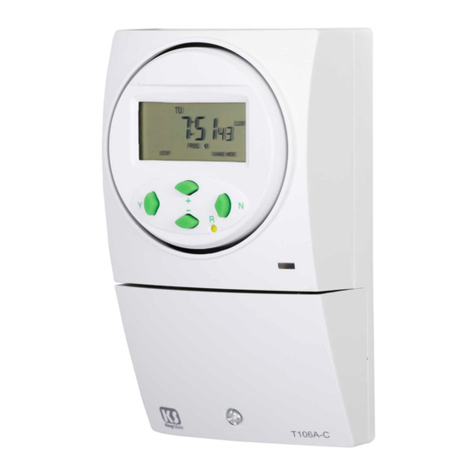
Green Brook
Green Brook KingShield T106A-C Installation & operating instructions
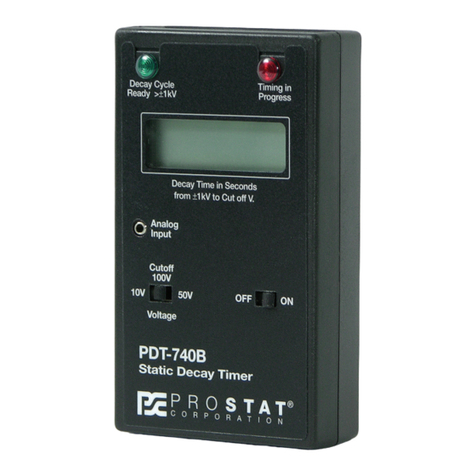
Prostat
Prostat PDT-740B user manual
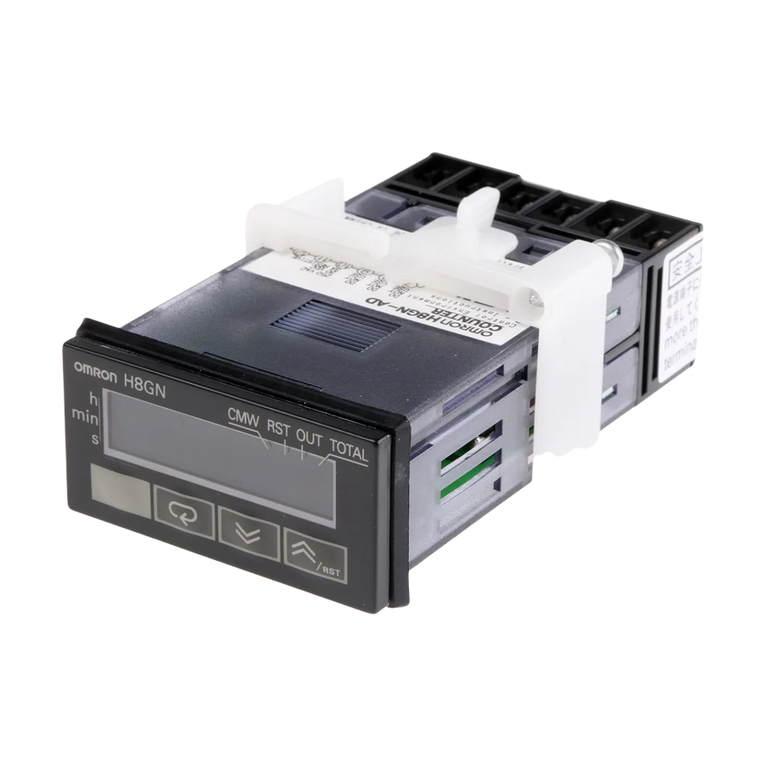
Omron
Omron H8GN owner's manual
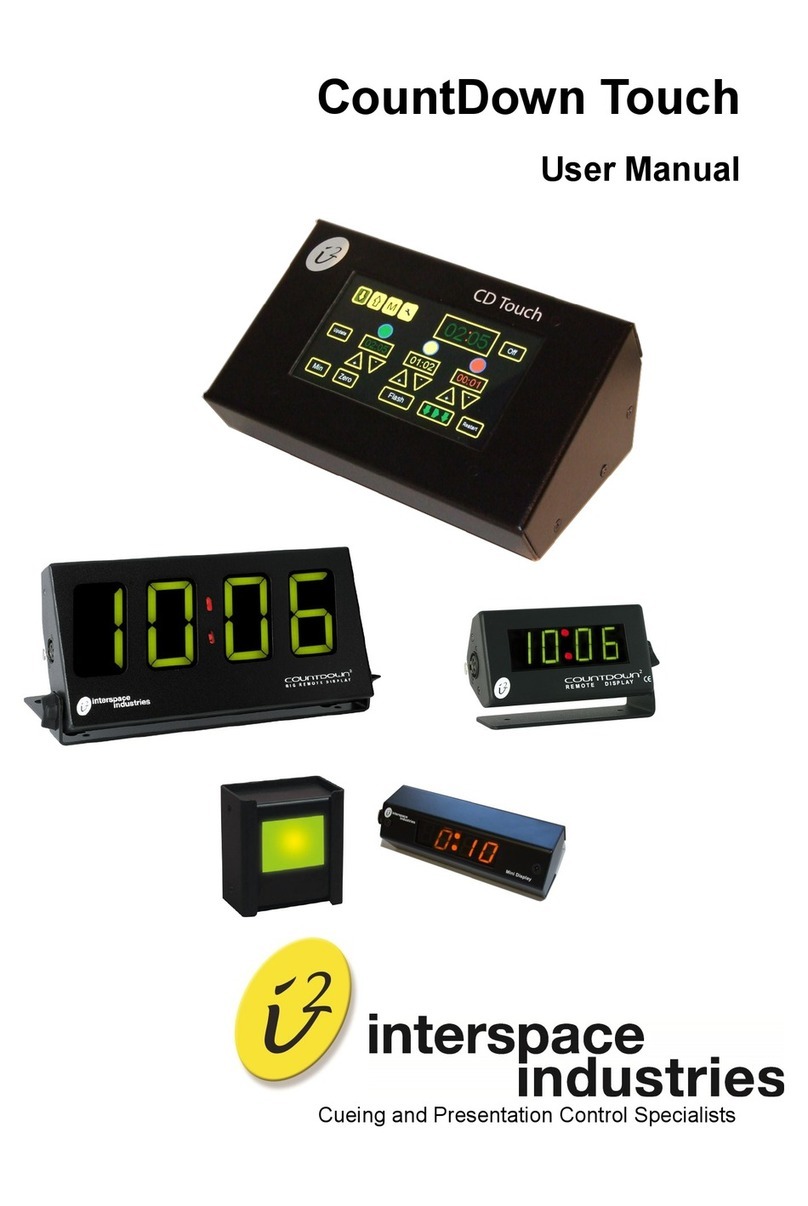
Interspace Industries
Interspace Industries CountDown Touch user manual
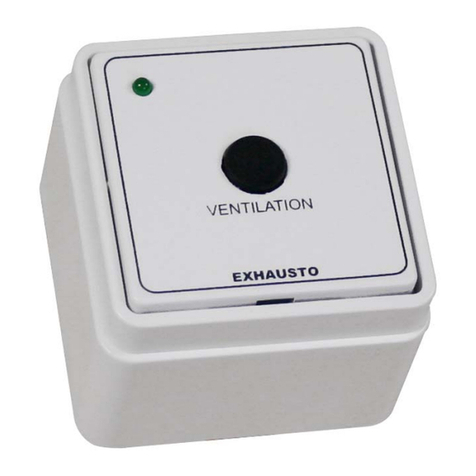
Exhausto
Exhausto TIMERBUTTON2 Product information
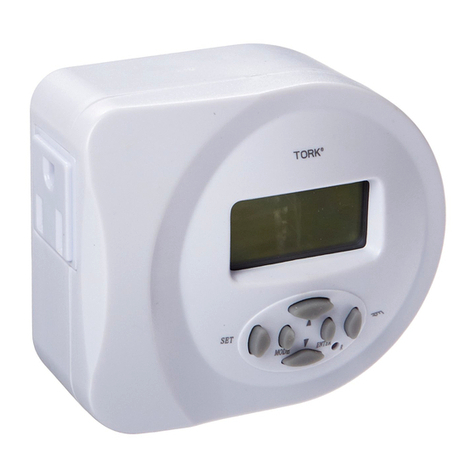
NSi INDUSTRIES
NSi INDUSTRIES TORK 457Z Programming instructions
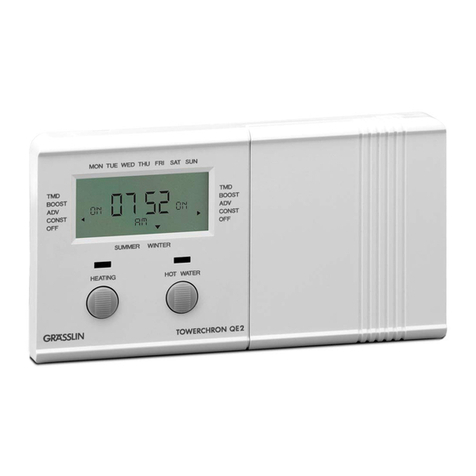
Intermatic
Intermatic GRASSLIN thermio eco QE1 operating manual
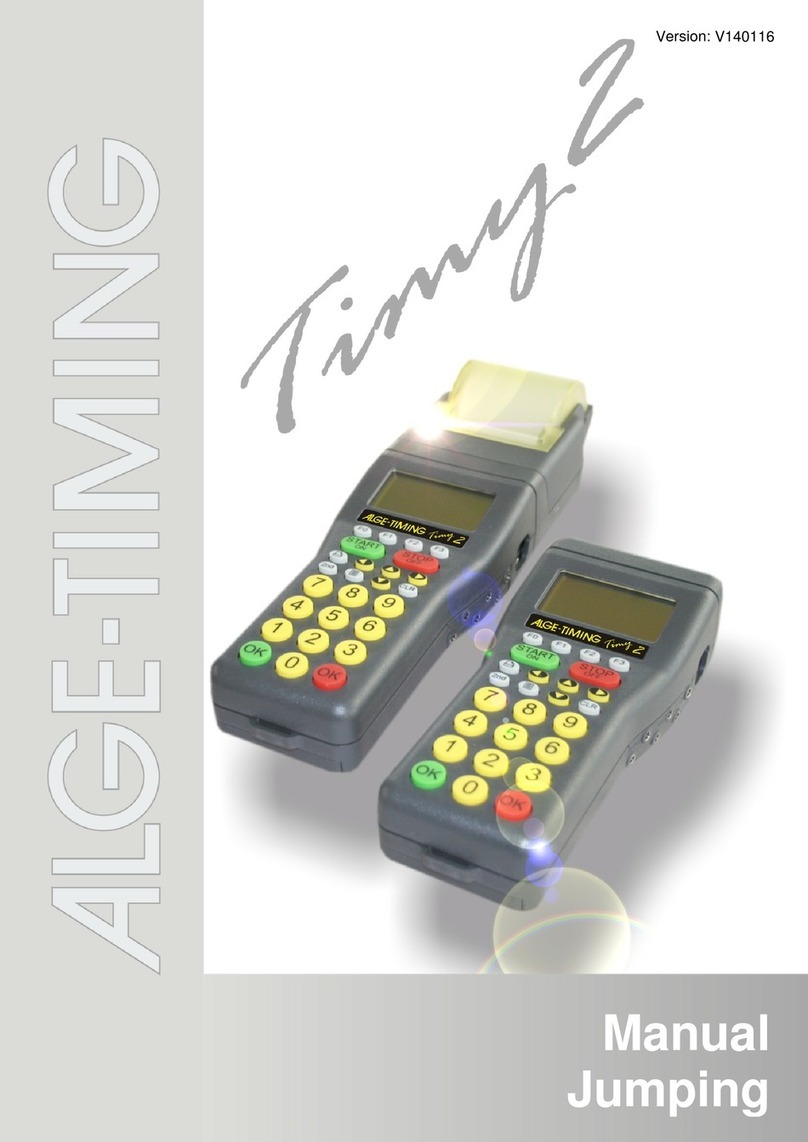
ALGE-Timing
ALGE-Timing TIMY2 manual
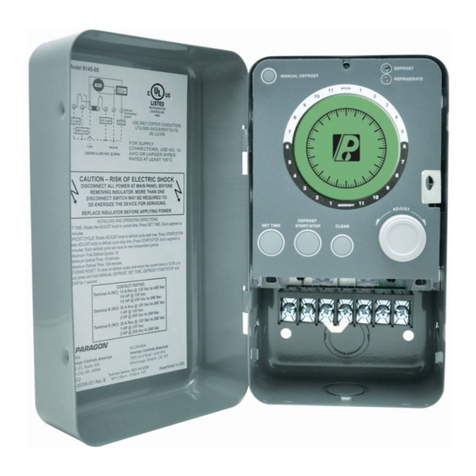
Robertshaw
Robertshaw Paragon 9145 manual
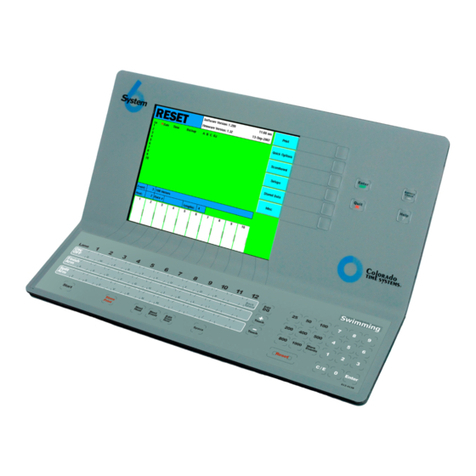
Colorado time systems
Colorado time systems System 6 user guide
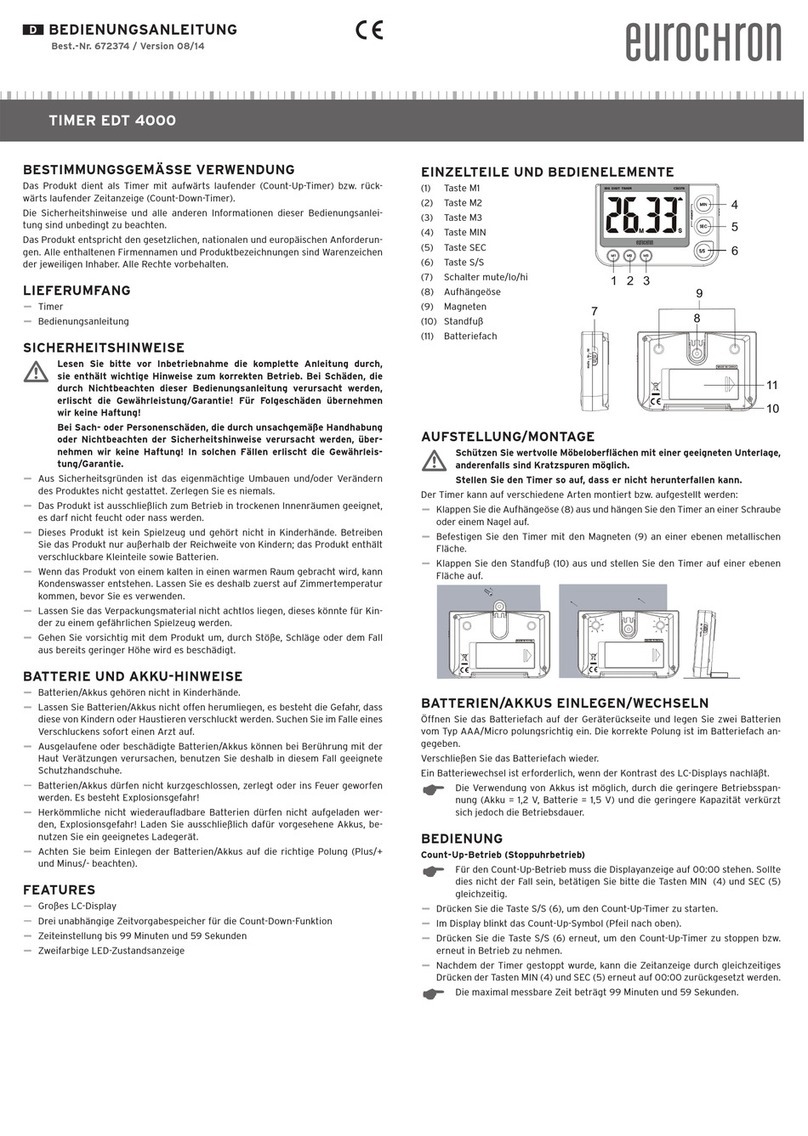
Eurochron
Eurochron EDT 4000 operating instructions