Thermionics SEB User manual

Rev. C, February 2011
Instruction Manual
SEB Electron Beam Control System
Thermionics Laboratory, Inc.
P.O. Box 3711 Hayward, CA. 94545 Sales: (510) 538-3304 Fax: (510) 538-2889
Website: http://www.thermionics.com E-mail: sales@thermionics.com

2
WARRANTY STATEMENT
Thermionics warrants each item it manufactures to be free from defects in workmanship and material for a
period of one year from date of shipment. HM2e-Gun evaporation sources are warranted for a period of five years from
date of shipment. Minor deviations which do not affect the performance of the equipment shall not be deemed to
constitute defects of workmanship or materials, or failure to comply with the specifications.
Not withstanding the foregoing, Thermionics shall have no warranty responsibility for expendable items such as
vacuum tubes, diodes, transistors, batteries, lamps, mechanical pump shaft seals and oil, diffusion pump oil, gaskets, or
filaments. In addition, all vacuum gauge sensing devices such as thermocouple tubes, Pirani tubes, ionization gauge
tubes, etc. are warranted against defects in manufacture in normal use, as determined be sellers inspection, for a period of
ninety(90) days from date of shipment, provided the defective gauge tube is returned to the seller’s plant for inspection.
Equipment made or modified to Purchaser’s specifications on special orders shall carry the above warranties
with respect to material and workmanship, but shall be specifically excluded from any other warranties, express or
implied, including those related to performance specifications, and any special components manufactured by others shall
carry only the original manufacturer’s warranties.
This warranty does not extend to Thermionics products which have been subject to misuse, neglect, accident, or
improper application, nor shall it extend to units which have been substantially altered outside the Seller’s plant except by
a Thermionic’s service engineer.
This warranty is expressly in lieu of all other obligations or liabilities on the part of Thermionics unless such
additional warranty is either agreed to in writing, appears in a separate warranty statement provided to the customer, or
appears in a warranty statement accompanying the product shipped to the customer. Under no circumstance will
Thermionics be liable for consequential or resulting loss or damage, whether of or due to causes covered by Thermionics’
warranty. Thermionics neither assumes nor authorizes any other person to make any other representation or warranty on
its behalf, or assume for it any liability in connect with the sale of its products.
WARRANTY REPAIR
Notice of any claim that a product is in any way defective shall be given to Thermionics immediately upon
discovery. Before any items are returned for repair and/or adjustment, approval of Thermionics must be obtained by the
customer. Written authorization for the return and instructions as to how these times should be shipped will be provided.
If any Thermionics products must be returned to the factory, they must be sent prepaid via the means of transportation
indicated as being acceptable in the written authorization. Thermionics reserves the right to reject any warranty claim on
any product that has been shipped by a non-acceptable means of transportation.
When Thermionics products are returned for examination and inspection, it is important that they be properly
packed for shipment. Use the original packing material or equivalent. The sender and the shipping agency must assume
the responsibility for damage resulting from improper packing or handling. And for loss of transit.
When products are returned, it is very important that the customer provide Thermionics with the data on the
operating conditions and any other pertinent information which will enable us to determine the cause of failure. In all
cases, Thermionics has sole responsibility for determining the cause of failure, and sole discretion in determining the
nature and extent of adjustment, if any, to which a customer may be entitled.
If it is found that our product has been returned without cause and is still serviceable, the customer will be
notified and the product be returned. All shipping costs on products returned for warranty repair shall be the customer’s
responsibility. Thermionic’s sole liability hereunder shall be the correction and/or replacement of defective materials and
workmanship.
Thermionics Laboratory, Inc.
P.O. Box 3711
Hayward, CA. 94545
(510) 538-3304

3
DANGER - HIGH VOLTAGE!!!
HIGH VOLTAGE IS PRESENT WITHIN THIS EQUIPMENT. CARE SHOULD BE EXERCISED AT
ALL TIMES WHEN OPERATING OR TROUBLESHOOTING.
HUMAN CONTACT WITH THE VOLTAGES INSIDE THIS UNIT CAN BE FATAL.
Be certain to turn off the input power before opening the doors or panels. Short all
capacitors with a grounding hook. Avoid testing live circuits.
If, in the process of troubleshooting, it becomes necessary to energize portions of the
circuitry, extreme caution should be observed. All test meter connections should be made
with power off. The test leads should be in good repair and have sufficient insulation for at
least twice that to be measured. The test meter should not be touched after the power is
turned on. Do not work in cramped spaces or cluttered areas. Troubleshooting of this
nature should be carried out only by experienced personnel using standard approved safety
procedures.
DANGER - HIGH VOLTAGE!!!
HIGH VOLTAGE IS PRESENT WITHIN THIS EQUIPMENT. CARE SHOULD BE EXERCISED AT
ALL TIMES WHEN OPERATING OR TROUBLESHOOTING.

4
CONTENTS
SECTION 1 SPECIFICATIONS
1.1 INTRODUCTION Pg. 5
1.2 GENERAL DESCRIPTION/SPECIFICATIONS Pg. 5
SECTION 2 INSTALLATION
2.1 ELECTRICAL REQUIREMENTS Pg. 6
2.2 SYSTEM GROUND Pg. 7
2.3 SOURCE CONTROLLERS Pg. 8
2.4 FILAMENT TRANSFORMER ENCLOSURES Pg. 9
2.4 MAIN POWER CONNECTIONS Pg. 10
SECTION 3 THEORY OF OPERATION
3.1 INTERLOCKS Pg. 11
3.2 CLOSED LOOP FEEDBACK SYSTEM Pg. 12
3.3 FILAMENT CHECK Pg. 13
SECTION 4 START UP / SHUT DOWN
4.1 INTRODUCTION Pg. 14
4.2 “MANUAL” Pg. 15
4.3 “AUTO” Pg. 16
4.4 FIRST TIME EVAPORATION Pg. 17
SECTION 5 MAINTENANCE
5.1 CALIBRATION Pg. 19
5.2 TROUBLESHOOTING Pg. 20
5.3 SCHEMATICS /DATA SHEETS Pg. 21

5
SECTION 1
1.1 INTRODUCTION
The Thermionics Laboratory, Inc. Source 1 Controller provides the interlock system and
emission regulation for the models SEB-06 and SEB-15 switching high voltage power
supplies. Everything required for the control and monitoring of one electron beam gun is
provided. If multiple gun operation is desired, additional source controllers can be added up
to a total of 3 each per power supply.
1.2 DESCRIPTION/SPECIFICATIONS
One 19” rack mountable high voltage power supply provides the accelerating high voltage
for up to 3 electron beam guns. See High Voltage power supply manual for specifications.
One half rack mountable Source 1 control chassis: 9.5”W x 21.0” D x 5.25”H.
Input: 85 - 264 VAC 50/60 Hz. 2 Amperes.
Output: 24 VDC to safety/process interlock strings.
0 – 10 VDC control signal to the SCR inside the filament transformer
enclosure
One filament transformer enclosure: 11.0”W x 18.0”D x 11.0”H.
Input: 208 – 240 VAC 50/60 Hz. Single Phase. 5 Amperes
Output: 10 KV Negative (Maximum SEB Output).
10 VAC, 70 Amps (Maximum filament power).
All connecting cables.

6
SECTION 2
INSTALLATION
2.1 ELECTRICAL REQUIREMENTS
Refer to diagram 3-2 on page 22 for an example of the electrical connections for a single e-Gun system.
NOTE: Care MUST be taken when routing all cables. For example, high voltage, AC input, ground and sweep
control cables should not be bundled together but take separate routes to their destinations. Ground cables
should be straight runs not coiled and be as short as possible. Avoid running high voltage cables near
sensitive instruments such as vacuum gauges and microprocessor controlled devices.
Three input power circuits are required for operation. See section 1.2 and the high voltage power supply
manual for detailed information.
Each power circuit has overload protection. The HV Interlock/Source 1 Controller has a fuse within the AC line
cord receptacle located on the rear panel. The high voltage power supply has a 3 pole circuit breaker located
on the front panel and the Gun #1 filament transformer has a 2 pole 15 A circuit breaker located at the input
end of the enclosure.
2.2 SYSTEM GROUND
The ground system is a VERY important aspect of electron beam equipment installation. The vacuum
chamber, high voltage power supply and filament transformer must be connected to a GOOD earth ground.
Under normal conditions, a good earth ground will consist of two ¾ inch diameter copper clad rods 8 feet long
(min) driven through the floor and into the earth 6 feet apart as close as possible to the vacuum chamber
location. These rods should be connected to the vacuum chamber by 2” wide 0.05” thick copper strap. The
strap should be silver soldered to the ground rods after ensuring there is 3 ohm (max) resistance between
them. Braided cable is not recommended and care should be taken to ensure connections are tight and to
clean bare metal surfaces rather than coated or painted ones.
Keep in mind this is a high frequency as well as a DC ground. RF generation during evaporation varies with a
number of parameters including vacuum level, chamber shape and material, evaporant material and high
voltage level. As impedance is the important factor, measuring DC resistance from point to point on the
system or between the system and earth ground will not represent actual RF ground capability. For this reason
Thermionics recommends the physical ground specifications in figure 1 on page 6.

7
If the equipment is installed on upper floors, the system ground may be accomplished by connecting to
the steel structure of the building. This should be done only after insuring the steel structure itself has a
good earth ground. Do not depend on water pipes for the system ground connection. Because of the many
joints and sealing compounds used in water pipe installation, no assumption should be made as to the
impedance of the pipe to earth ground.

8
2.3 SOURCE CONTROLLERS
The Source 1 Controller is provided with the purchase of an SEB High Voltage power supply. If more
than one e-Gun (up to a total of 3) operation is desired, optional Source 2 and Source 3 Controllers
can be provided.
The Source 1 Controller is the master controller for both single and multiple e-Gun operation. Primary
AC input power (115VAC 2A domestic U.S. or 220VAC 1A International) is connected to the fused
input located on the rear panel. All high voltage interlocks originate and end at the Source 1 Controller.
Main power on/off and emission control crossover from “Manual” (potentiometer) to “Auto” (optional
deposition rate controller) is done with the key switch. The output of the rate controller connects to a
BNC connector located on the rear panel of each source controller. The selected key switch mode
applies to all source controllers connected in the system.
A 6 foot cable is provided for connecting the Source 1 Controller interlock string to the SEB HV power
supply. This cable is connected to the rear panel of the Source 1 Controller connector labeled “ HV
Pwr Supply I/O” and to the SEB HV power supply rear panel connectors labeled J4 and J5.
A black 14 pin circular connector serves as a jumper for terminating the connection to additional source
controllers if only one e-Gun is in operation. This jumper is to be located at the Source 1 Controller rear
panel connector labeled “To: Gun 2 Control” and must be removed to connect a Source 2 Controller. A 3
ft. cable is connected between here and the Source 2 Controller rear panel connector labeled “To: Gun 2
Control”. The jumper is then moved to the Source 2 controller rear panel connector labeled “To: Gun 3
Control”. The same connection procedure is used for connecting a Source 3 Controller. As these
controllers are connected in series, the last controller must have the jumper installed.
Hand Held Remote Control is available. These (optional) remote control boxes allow emission and beam
sweep control at the vacuum chamber location. There is also an emergency high voltage off mushroom
switch on each HHRC. Where these remote controls are not used, a 25 pin jumper plug must be installed
on each source controller rear panel connector labeled “Remote”.

9
2.4 FILAMENT TRANSFORMER ENCLOSURES
One filament transformer is provided with each source controller. This filament transformer is mounted
inside an enclosure that must be located near the vacuum tank. Ten foot filament cables terminated
with high voltage connector(s) are designed to plug onto Thermionics high voltage feedthroughs. The
dual high voltage connector has an interlock switch positioned such that the connector must be plugged
all the way onto the feedthrough to satisfy the interlock circuitry.
There are three high voltage output connectors on the rear panel of each SEB HV power supply for
connecting up to three filament transformer high voltage coaxial cables.
Primary AC power (208 – 240 VAC) is connected to the gun 1 enclosure connector labeled “Input”. If a
second e-gun is to be operated a 3 ft. cable is connected to the gun 1 enclosure connector labeled
“Output” and to the gun 2 enclosure labeled “Input”. An additional 3 ft. cable is provided for operating a
third e-gun.
Each filament transformer enclosure is connected to the associated source controller via a control cable.
This control cable also serves to complete the DC current feedback loop. Each filament transformer has a
16 pin connector labeled To: Source 1, 2 or 3 Controller and each source controller has a 14 pin
connector labeled To: Fil. Transformer 1, 2 or 3 for connection of these cables.
The High Voltage interlock string is connected from the Source 1 Controller rear panel TB901 pins 5,6 to
the Gun 1 Filament Transformer Enclosure with the cable provided. A black 4 pin circular connector
serves as a jumper for completing the interlock string. If a Gun 2 Filament Transformer is used the jumper
is removed and a 3 ft. cable is provided to connect the interlock string between the Gun 1 transformer and
the Gun 2 transformer. The jumper is then moved to the Gun 2 transformer.
The same connection procedure is used for connecting a Gun 3 transformer. As these transformer
enclosure interlocks are connected in series, the last enclosure must have the jumper installed for the
interlock circuitry to be satisfied. The last transformer jumper can also be broken for the purpose of
connecting an external safety interlock such as a switch connected to a door or access panel. If the
interlock circuitry is not connected properly or each dual high voltage connector is not plugged all the
way onto the chamber high voltage feedthrough, the Source 1 Controller LED labeled External will not
light and the SEB HV power supply will not turn on.

10
2.5 MAIN POWER CONNECTIONS
After installing all connecting cables, grounds and high voltage feedthrough connectors, the
sources of main power can be connected to the system.
The SEB high voltage power supply is provided with a 12 foot 4 conductor cable for connecting
main three phase power to the unit. One end, stripped and tinned, is connected to the screw
terminals in on the rear panel. The other end is for connection to a user provided service
disconnect.
The Source controllers are provided with computer grade power cord for connecting 115 or 220
VAC to the rear of the Source 1 controller. This cable provides power for all additional source
controllers connected in the system.
The Gun 1 filament transformer enclosure is provided with a 12 foot 3 conductor cable for
connection to 208 – 240 VAC single phase power. One end is connected to the Gun 1 filament
transformer connector labeled input. This cable provides power for all additional filament
transformers in the system.
Where a second filament transformer is used, a three foot three conductor cable is connected
between the Gun 1 filament transformer connector labeled output and the Gun 2 filament
transformer connector labeled input.
The same connection procedure is used for connecting primary power to a Gun 3 filament
transformer.

11
SECTION 3 THERORY OF OPERATION
3.1 INTERLOCKS
The first LED indicator in the interlock string is labeled “KEY”. It is provided to give an
indication that the control power is on or off. When the key is switched into either the “Manual”
or “Auto” mode, two DC power supplies are turned on inside the Source 1 Controller. 24 VDC
supplies power to the interlock circuits. +/- 15 VDC supplies power to the closed loop current
feedback systems.
The second LED indicator is labeled “VACUUM”. It is energized by providing a closure to
terminals 1 and 2 of TB901, located on the rear panel of the Source 1 Controller. This is a point
for connecting the relay output of vacuum gauge controller for the purpose of ensuring there is
sufficient vacuum in the chamber before High Voltage can be turned on.
The third LED indicator is labeled “WATER”. It is energized by providing a closure to terminals
3 and 4 of TB901, located on the rear panel of the Source 1 Controller. This is a point for
connecting the relay output of a water flow switch for the purpose of ensuring there is sufficient
cooling water to the e-Gun in the chamber before High Voltage can be turned on.
The forth LED indicator is labeled “EXTERNAL”. It is energized by providing a closure to
terminals 5 and 6 of TB901, located on the rear panel of the Source 1 Controller. This is a
point for connecting the filament transformer interlocks for the purpose of ensuring that all
High Voltage Connectors are installed properly before high voltage can be turned on.
The fifth LED indicator is labeled “REMOTE”. It is energized when all emergency mushroom
switches on the Hand Held Remote Control boxes are in the up position. Where the HHRC boxes
are not used, jumper plugs must be installed on the rear panels of the source controllers at the 25
pin connectors labeled “REMOTE”.
When all of the interlock conditions are satisfied, a green LED indicator labeled “READY” will
light. This will also enable the OFF pushbutton on the front panel of the SEB High Voltage power
supply. The system is now ready for operation.
Additional Source Controllers connected in the system have operational interlocks for protection
of the source as well.
The first LED indicator is labeled “VACUUM”. It is energized by providing a closure to terminals
1 and 2 of TB1001, located on the rear panels of the Source 2 and 3 Controllers. This is a point for
connecting the relay output of vacuum gauge controller for the purpose of ensuring there is
sufficient vacuum in the chamber before High Voltage can be turned on.
The second LED indicator is labeled “WATER”. It is energized by providing a closure to
terminals 3 and 4 of TB1001, located on the rear panels of the Source 2 and 3 Controllers. This is
a point for connecting the relay output of a water flow switch for the purpose of ensuring there is

12
sufficient cooling water to the e-Gun in the chamber before High Voltage can be turned on.
When all of the interlock conditions are satisfied, a green LED indicator labeled “READY” will
light. This will also enable the OFF pushbutton on the front panels of the additional Source
Controllers. These controllers are now ready for operation.
3.2 CLOSED LOOP FEEDBACK SYSTEM
The emission current of the electron beam gun is determined by the power applied to the filament
and this current must be tightly controlled to keep the emission current constant. A closed loop
feedback system is used to drive an SCR located in the Filament Transformer enclosure. This
SCR controls the primary (208-240VAC) input to a filament transformer.
A transducer whose output is proportional to the e-Gun emission current generates the feedback
signal. This device also drives the current meter on the front panel of the associated source
controller. The feedback signal is compared to a DC signal developed by the Emission
potentiometer (in “Manual” mode) or the input signal from an optional deposition rate controller
(in the “Auto” mode). The resultant error signal is applied to the SCR controlling the input to the
filament transformer. An increase of the error signal results in increased filament current to the e-
Gun.
During an arc or over current situation as is common in e-Gun operation, the filament current is
reduced to the level set by the Bias potentiometer located on the rear panel of the Source
controllers. When the arc is extinguished, emission current regulation resumes.

13
Figure 2
Simplified diagram of the closed loop feedback system.
3.3 FILAMENT CHECK
The Filament Check circuit is provided to allow the user to check the operation and or the
condition of the e-gun filament without high voltage. A momentary rocker switch and indicator
LED are located on the Source controller front panels for this purpose.
When the Filament Check switch is depressed with the key in the “Manual” or “Auto” mode, the
“Filament Check LED” and the “Emission On” pushbutton will illuminate indicating the filament
circuits are in operation. As Filament Check is a test of the e-Gun filament only, the high voltage
if on will turn off. An upscale reading of 0.250 to 0.500 Amps by the emission meter indicates
current is passing through the e-gun filament. It is a good idea to hold the Filament Check switch
down for a few seconds to ensure the filament can maintain a steady flow of current. When the
Filament Check switch is released, the meter and filament circuits will return to their “Ready”
states.
If there is no upscale reading indicated by the emission meter or the reading cannot be
maintained while holding the switch depressed, it may be necessary to replace the e-gun
filament.

14
SECTION 4
START UP / SHUT DOWN
4.1 INTRODUCTION
As Hand Held Remote Control options are available with the SEB series systems, “Manual”
mode will refer to filament operation control by either the front panel of a Source Controller or a
HHRC connected to a Source Controller. The “Auto” mode refers to filament operation control
by means of an external signal. Thermionics Laboratory , Inc. Source Controllers are designed to
accept the zero to negative 10 Volt DC output of many commercially available Deposition Rate
Controllers.
4.2 MANUAL MODE
Insert key into the switch on the Source 1 Controller and rotate counterclockwise to the “Manual”
position. Observe the interlock LED’s. If all interlock conditions are satisfied, the green “Ready”
indicator will be on. The green lamp on the emission off pushbutton will also be on. Turn on the
circuit breaker on the filament transformer enclosure
NOTE: The SEB series high voltage power supplies are configured for manual operation See
the SEB instruction manual for additional information about remote operation.
Turn on the circuit breaker on the SEB High Voltage power supply front panel. The yellow
“Mains” and green “Interlock” LEDs should be on and the “HV Off” pushbutton should be
illuminated indicating all safety, process interlocks are satisfied and the high voltage is ready to be
turned on. Press the “HV On” pushbutton. The “HV Off” lamp should go out and the “HV On”
indicator should stay lit.
Rotate the “Output Adjust” potentiometer clockwise observing the “HV Output” meter until the
desired high voltage level is obtained. The Source Controllers are interlocked such that emission
cannot begin until the high voltage is set above 3.8 Kilovolts. Thermionics e-Guns will run from
4KV to 10KV. See the e-Gun instruction manual for appropriate high voltage operating level.
From this point either Source Controller front panel or Hand Held Remote Control will be used to
control emission. Press the “Emission On” pushbutton. The red indicator should remain
illuminated. Rotate the “Emission Adjust” potentiometer clockwise observing the “Emission”
meter until the desired level of emission current is obtained.
When deposition is complete, rotate “Emission Adjust” potentiometer fully counterclockwise and
press the “Emission Off” pushbutton.
Rotate “Output Adjust” potentiometer on the SEB power supply fully counterclockwise
and press the “HV Off” pushbutton.
Return the key on the Source 1 Controller to the “Safe” position. Allow several minutes for the
SEB High Voltage power supply to cool and turn off the main circuit breaker.

15
4.3 AUTO MODE
Insert key into the switch on the Source 1 Controller and rotate counterclockwise to the “Auto”
position. Observe the interlock LED’s. If all interlock conditions are satisfied, the green “Ready”
indicator will be on. The green lamp on the emission off pushbutton will also be on. Turn on the
circuit breaker on the filament transformer enclosure.
NOTE: The SEB series high voltage power supplies are configured for manual operation See
the SEB instruction manual for additional information about remote operation.
Turn on the circuit breaker on the SEB High Voltage power supply front panel. The yellow
“Mains” and green “Interlock” Leds should be on and the “HV Off” pushbutton should be
illuminated indicating all safety interlocks are satisfied and the high voltage is ready to be turned
on. Press the “HV On” pushbutton. The “HV Off” lamp should go out and the “HV On” indicator
should stay lit.
Rotate “Output Adjust” potentiometer clockwise observing the “HV Output” meter until the
desired high voltage level is obtained. The Source Controllers are interlocked such that emission
will not begin until the high voltage is set above 3.8 Kilovolts. Thermionics e-Guns will run from
4KV to 10KV. See the e-Gun instruction manual for appropriate high voltage level.
From this point only a closure at the source 1 rear panel I/O connector pins 5 and 6 will turn on
the emission contactor. The red indicator should remain illuminated. Start the program on the
Deposition Rate Controller. After the desired rate has been obtained, press the “Emission Off”
pushbutton.
Rotate “Output Adjust” potentiometer on the SEB power supply fully
counterclockwise and press the “HV Off” pushbutton. Return the key on the Source
1 Controller to the “Safe” position. Allow several minutes for the SEB High Voltage
power supply to cool and turn off the main circuit breaker.
4.4 FIRST TIME EVAPORATION
Before initial operation of an electron beam source is attempted several items should be
checked first.
Cooling water should be supplied to the electron beam source as recommended in the
evaporation source manual.
Crucible loaded to approximately 80 % with evaporant material.

16
Electrical connections can be checked with an ohm meter at the high voltage feedthroughs.
Check between the two conductors for continuity less than 1 ohm. Check between each
conductor and the chamber wall (ground) for an open circuit.
Verify the power supply and vacuum chamber are properly grounded in accordance with
section 2.2 of this manual. Connect the high voltage connector(s) to the feedthrough
conductors. Ensure the connections are tight.
If an optional XY axis beam sweep controller is used, verify the current at both axis’ is at zero.
Once becoming familiar with the power supply control features, the system is ready to be
operated.
A vacuum of 5 x 10 –5 torr (mm of Hg ) or better is recommended. At higher pressures interaction with
residual gasses can result in causing defects and impurities in the deposited film. Increased arcing and a more
diffused beam concentration result as well as the formation of glow discharge regions at higher pressures.
The high voltage is then turned on and after a stable voltage is present, the filament power can be
applied (emission current). This current should be brought up slowly until a slight bluish glow is
observed. The emission meter will be at a small value at this point (under 50 mA). If an emission
current in excess of 50 mA is measured and no visible indication of the beam is observed the
system will need to be shut off and opened for investigation of the problem. Improper magnetic
field orientation or strength and/or incorrect acceleration voltage can cause the beam to be emitted
in such a fashion as not to reach the evaporant material. If the electron beam is run at high power
under such a condition, damage to the area of the beam impact will result.
Once the beam has been located use the optional X-Y axis sweep coil system to position the beam
on the center of the evaporant material. If the material is capable of melting bring up the power
until the material begins to melt. If the material is in a pellet or chunk form, sweeping of the
beam can be used to speed up the melting process. Some materials transfer heat readily to
adjacent material resulting in a constant flow of material back into the melt, however some
materials do not act as well in this respect and require sweeping to maintain a constant molten
pool of material. Tunneling of the beam into the material should be avoided. The beam sweep
should be used in all situations where a constant flat vapor emitting surface area can not otherwise
be maintained.
It is always best to increase the power slowly as this will result in a more stable increase in
temperature. Most materials require a period of outgassing of impurities. During this period a
shutter system is normally utilized to prevent the deposit of these impurities onto the substrate.
After the material has been melted and degassed, the power can again be increased gradually to
the desired point of evaporation. The evaporant material should be allowed a brief period to
achieve thermal equilibrium and then the shutter can be opened and the desired film can be
deposited. After the film has been deposited, the shutter can again be closed and the electron
beam source turned off.
Adequate time should be provided after shutting off the source to allow the filament cool down
before releasing the system to atmosphere. If the air is introduced too soon the filament will be
destroyed. After a few minutes the system can be released to air (the use of dry nitrogen will

17
result in improved filament life).
SECTION 5 MAINTENANCE
DANGER - HIGH VOLTAGE!!!
HIGH VOLTAGE IS PRESENT WITHIN THIS EQUIPMENT. CARE SHOULD BE EXERCISED AT
ALL TIMES WHEN OPERATING OR TROUBLESHOOTING.
HUMAN CONTACT WITH THE VOLTAGES INSIDE THIS UNIT CAN BE FATAL.

18
Be certain to turn off the input power before opening the doors or panels. Short all
capacitors with a grounding hook. Avoid testing live circuits.
If, in the process of troubleshooting, it becomes necessary to energize portions of the
circuitry, extreme caution should be observed. All test meter connections should be made
with power off. The test leads should be in good repair and have sufficient insulation for at
least twice that to be measured. The test meter should not be touched after the power is
turned on. Do not work in cramped spaces or cluttered areas. Troubleshooting of this
nature should be carried out only by experienced personnel using standard approved safety
procedures.
DANGER - HIGH VOLTAGE!!!
HIGH VOLTAGE IS PRESENT WITHIN THIS EQUIPMENT. CARE SHOULD BE EXERCISED AT
ALL TIMES WHEN OPERATING OR TROUBLESHOOTING.

19
5.1 CALIBRATION
This section describes the procedure for calibrating the emission current meter. A calibrated
precision power supply capable of displaying current is required for this procedure.
With the circuit breaker on the SEB high voltage power supply in the off position and input power
removed, DISCONNECT THE COAXIAL CABLE FROM THE REAR OF THE POWER
SUPPLY. Disconnect the connector(s) from the vacuum chamber feedthroughs. This leaves only
the input (208 – 240 VAC) cable and the control cable connected to the filament transformer
enclosure.
Connect the coaxial cable from the filament transformer enclosure to the ground terminal on the
precision power supply. The positive output of the supply connects to one of the filament power
leads at the vacuum chamber feedthrough connector(s). Remove the top cover of the source
controller under test. Care should be taken due to the presence of input voltage (115 or 220 VAC)
inside this controller. Observe the location of the calibration potentiometer behind the emission
current meter.
Turn the key switch on the source 1 controller to the “On” position. Allow a minute for the
circuitry to energize and observe the emission current meter. The meter should display a reading
of zero amps. Plus or minus adjustments can be made with a potentiometer located behind the
digital meter.
Set the output of the precision power supply to 0.5 amps. Observe the emission current meter.
If a reading of 500 milli amps is present , no further action is required. Plus or minus
adjustments can be made by turning the calibration potentiometer located behind the emission
current meter inside the source controller.
5.2 TROUBLESHOOTING
One of the most common problems associated with electron beam equipment is the loss of or
absence of emission current. This is in most cases due to problems with the e-Gun filament. At
the end of service lifetime a filament will open breaking the connection to the filament
transformer.
The condition of the filament can be checked in two ways. First use the Fil Chek feature on the
associated source controller. When the Filament Check switch is depressed with the key in the
“Manual” or “Auto” mode, the “Filament Check LED” and the “Emission On” pushbutton will
illuminate indicating the filament circuits are in operation. An upscale reading of 0.250 to 0.500
Amps by the emission meter indicates current is passing through the e-gun filament. It is a good
idea to hold the Filament Check switch down for a few seconds to ensure the filament can
maintain a steady flow of current. When the Filament Check switch is released, the meter and
filament circuits will return to their “Ready” or “Off” states.
If no reading is observed on the meter, the vacuum chamber feedthrough connector(s) should be
removed and the e-Gun filament resistance checked With an ohm meter, check between the two
conductors for continuity less than 1 ohm. Check between each conductor and the chamber wall
(ground) for an open circuit. If an “open” circuit is measured between the two feedthrough

20
connectors, the system must be vented and opened to inspect and or replace the e-Gun filament.
If no reading is observed on the emission meter when the Filament Check switch is pressed and
the e-Gun filament measures the correct resistances, the filament control circuitry may need to be
checked for proper operation.
Two test power supplies are required for checking the operation of the filament control circuitry.
A precision power supply capable of displaying current as in section 5.1 and a source of greater
than 4 VDC but not more than 10 VDC. A 9 volt battery will work for this test.
Place the source 1 controller key switch in the “Off” mode. Remove the 15 pin connector located
on the rear panel of the source 1 controller labeled “HV PS I/O”. Connect the output of a nine volt
battery (or test power supply) to pins 3(+) and 4(-) at the open rear panel connector. Connect the
leads from a volt meter to both filament cables removed from the vacuum chamber feedthroughs.
Set the volt meter to measure volts AC.
If the chamber is not currently under vacuum and the water is not flowing to the e-Gun, these
two interlocks must be shorted at the rear panel of the source controller under test. Jumper
positions 1, 2 and 3, 4 on the interlock terminal block.
Turn the source 1 controller key switch to the “Manual” mode. Press the filament “On”
pushbutton on the source controller under test and rotate the emission potentiometer clockwise.
Observe the meter voltage increase from zero to approximately 10.5 VAC. Rotate the
potentiometer counterclockwise and observe the voltage decrease to nearly zero.
If there is no increase and or decrease of this AC voltage, this would indicate a problem with
filament control amplifier PCB located inside the associated source controller. Contact
Thermionics for information regarding replacement parts or additional testing procedures.
Table of contents
Popular Control System manuals by other brands
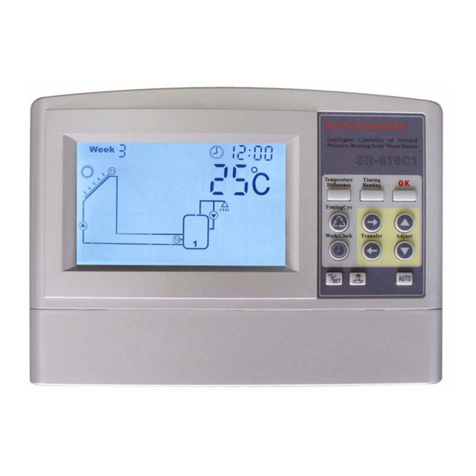
Shuangri Electric
Shuangri Electric SR618C1 Installation and operating manual
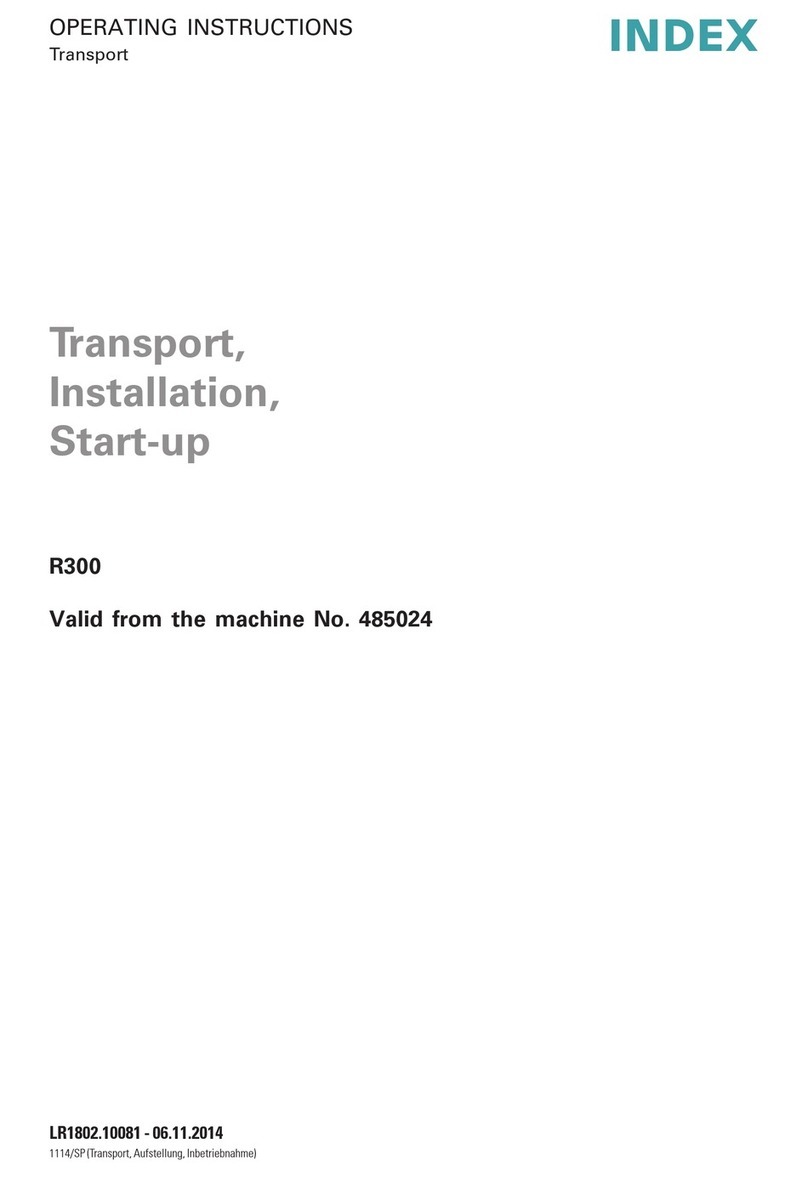
Index
Index R300 operating instructions

Roger
Roger MC16-PAC-2-KIT installation manual

Balcrank
Balcrank PGM-40 Operation, installation, maintenance and repair guide
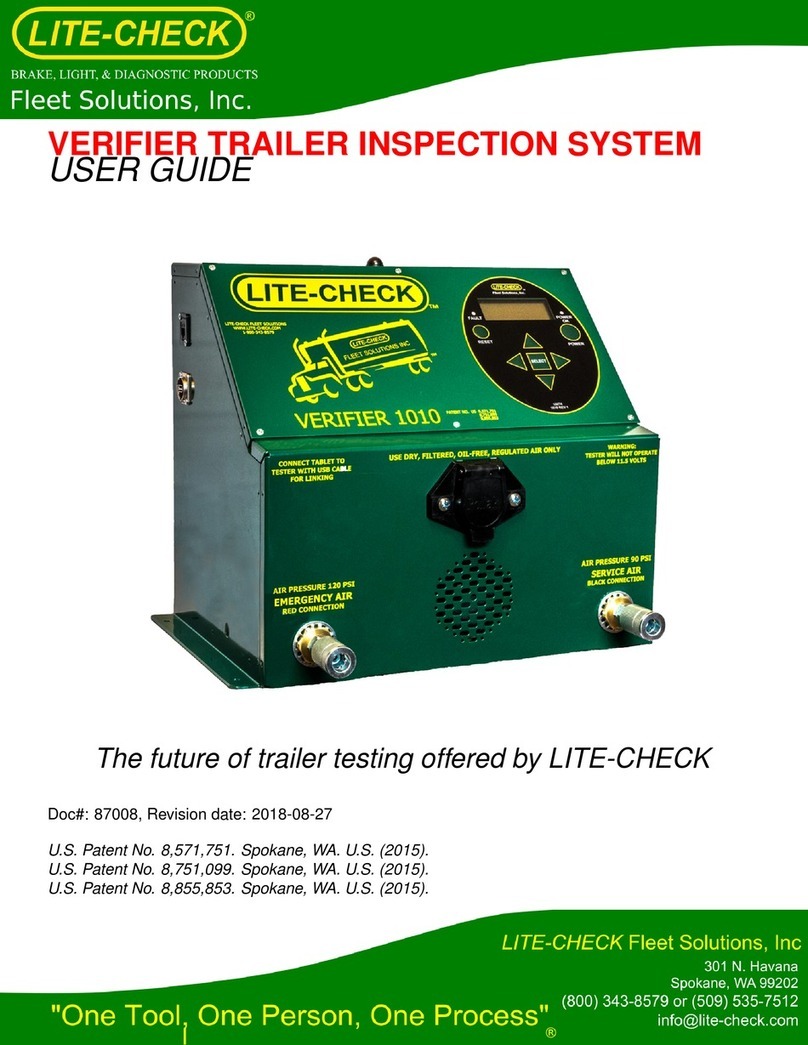
Lite-Check
Lite-Check VERIFIER 1010 user guide
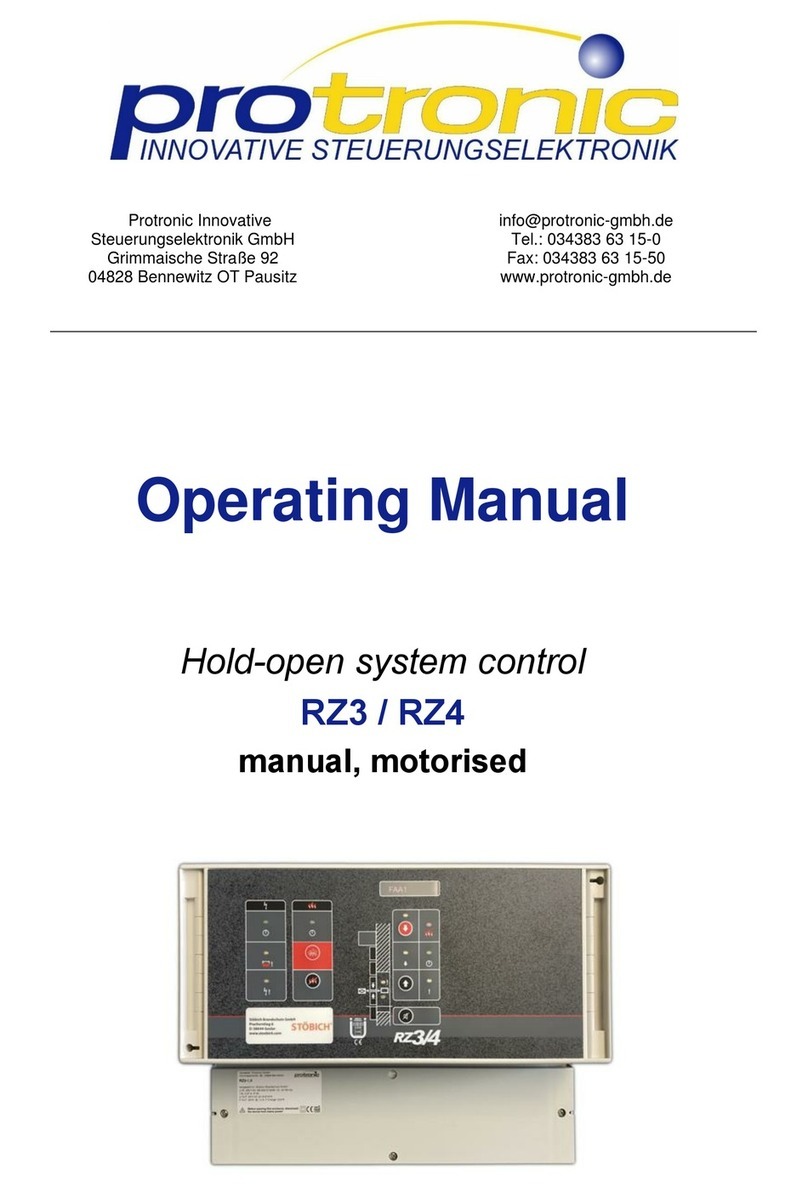
Protronic
Protronic RZ3 operating manual