Balcrank PGM-40 Instruction Manual

Thoroughly read and understand this manual before
installing, operating or servicing this equipment.
OPERATION, INSTALLATION,
MAINTENANCE AND REPAIR GUIDE
SERVICE BULLETIN SB3022
Rev. H 11/09
PGM-40 MECHANICAL
CONTROL HANDLE
Model #3330-037
3330-038
3330-039
3330-040
3330-041
3330-042
3330-060
3330-061
®

2
GENERAL SAFETY REQUIREMENTS
NOTE: THOROUGHLY READ AND
UNDERSTAND THIS MANUAL BEFORE
INSTALLING, OPERATING, OR
SERVICING THIS EQUIPMENT.
• Please retain this instruction manual for
future reference.
• Your safety is important to us. Please read,
and follow all safety instructions listed
below.
• Some of these instructions alert you to the
potential for personal injury. “Warnings”
listed throughout this manual advise of
potential practices or procedures which may
cause damage to your equipment.
• This control handle is not designed for in-line
installation. Do not install with a shut-off
valve on the outlet side of the meter. Such
an installation could result in damage to the
meter housing.
• Ensure all operators have access to
adequate instructions about safe operating
and maintenance procedures.
• Do not exceed the maximum working
pressure of 1,500 psi.
• Do not strike the oil control gun if it fails
to operate. Refer to the “trouble shooting
guide” or return unit to your nearest Balcrank
authorized service center.
• Never allow any part of the human body
to come in contact with the control handle
outlet.
• Never point the outlet nozzle at yourself
or anyone else.
• Never exceed the pressure rating of any
component installed in the System.
• Before each use check all hoses for signs of
wear, leaks or loose ttings. Tighten all uid
connections regularly and replace weak or
damaged hoses. Your personal safety and
well-being are at stake.
• Before attempting any repairs or
maintenance of this product disconnect the
air supply on the pump, and release the
line pressure by pressing the lever on your
control handle.
WARNING
!
DANGER: Not for use with
fluids that have a flash point
below 100°F (38°C). Examples:
gasoline, alcohol. Sparking could
result in an explosion which could result in
death.
IMPORTANT
!
Read these safety warnings and
instructions in this manual completely,
before installation and start-up of the
control handle. It is the responsibility of the purchaser
to retain this manual for reference. Failure to comply
with the recommendations stated in this manual will
damage the control handle and void factory warranty.
Before doing any maintenance on
the control handle, be certain all
pressure is completely vented from
the pump, suction, discharge, piping, and all other
openings and connections. Be certain the air supply is
locked out or made non-operational, so that it cannot
be started while work is being done on the control
handle. Be certain that approved eye protection
and protective clothing are worn at all times in the
vicinity of the control handle. Failure to follow these
recommendations may result in serious injury or
death.
WARNING
!
Airborne particles and loud
noise hazards.
Wear ear and eye protection.
WARNING
!
Manual tip cannot be used on
PGM-40 control handle. An auto
tip or semi-auto tip must be used.
Use of manual tip can result in overpressurization,
which can cause control handle to crack.
WARNING
!

3
Threaded Plug
831335 Kit
(not included in
3330-037, 3330-040,
3330-071, 3330-075) 831336
O-Ring
(Included with
models prior to
5/03)
OPER ATION
Use Teon®tape (or suitable thread sealant)
when connecting the control handle to the hose
connection.
Press the lever on the control handle and uid
will start owing. The meter will now record
oil use.
The top accumulative register will record the
total volume of uid passed through the meter.
The bottom register is a reset batch total, which
can be reset by pressing the reset button
GENERAL DESCRIPTION
This manual assists you in operating and maintaining
your new PGM-40 Mechanical Control Handle. The
information contained will help you ensure many
years of dependable performance and trouble free
operation.
Please take a few moments to read through this
manual before installing and operating your new
control handle. If you experience problems please
contact your local Balcrank® distributor or Balcrank
authorized service center.
OUTLET ExTENSION
The outlet extension can be fitted either inline
(forward) or on the outlet port “pistol style” located
under the meter.
Note: The threaded plug removed from the outlet
port on the underside of the meter, is used to seal
the outlet port not in use.
SPECIFICATIONS
Accuracy..................+- 1% (of Reading)
Flow Range ......................0.26-8 gpm
Max Operating Pressure ..............1,500psi
Weight .............................2.55 lbs
Outlet:..................3/8”NPT (prior to 5/03
. . . . . . . . . . . . . . . . . . . . . . . . . 3/8”NPS (after 5/03)
SwivelInlet ........................ 1/2”NPT
Operating Temperature . . . . . . . . . . . . . .230-1220F
Wetted parts . . . . . . . . . . .Aluminum, Acetal, Steel,
. . . . . . . . . . . . . . . . . . . . . . . . . . . . . . . Nitril Rubber
Fluid Compatibility ............Engine Oil, Diesel
. . . . . . . . . . . . . . . . . . Oil, ATF, Antifreeze, Gear Oil
Dimensions . . . . . . . . . . . . 10” L x 3.7” W x 4.33” H
Before maintenance or repair, shut
off the compressed air line, bleed
the pressure, and disconnect the
air line from the pump. The discharge line may be
pressurized and must be bled of its pressure.
WARNING
!
MAINTENANCE
Inspect your control handle daily for any signs
of damage. Replace any damaged parts or
components as required.
HANDLE DISASSEMBLY
Use a clean work area to carry out maintenance.
A) Remove the uid hose from the control handle
inlet swivel (46).
B) Unscrew and remove swivel (46), washer (44),
and o-ring (45) from the control handle inlet.
Clean or replace the strainer and o-ring.
CAUTION: The swivel is under spring tension.
C) Slide off the handle sleeve (43).
D) Remove valve spring (42), seal/valve body
assembly (40, 41) and plunger (39).
LEVER AND VALVE REMOVAL
A) Using a 2.5mm allen wrench, remove the two
handle screws (38).
B) Remove lever (34).
C) Remove the washer (32) and o-ring (31), then
push the valve cam (30) from the handle body
(4), and remove o-ring (33).

4
HANDLE REASSEMBLY
A) Clean and inspect all parts. Replace any suspect,
worn, or damaged components.
NOTE: Lightly lubricate the valve cam (30) before
assembly.
B) Place o-ring (31) onto valve cam (30).
NOTE: The cutout section in the middle of the valve
cam (30) must face the inlet swivel (46).
C) Replace the valve cam (30) into the body (4).
Note the orientation shown on the assembly
drawing. Fit the second o-ring (33) and washer
(32).
D) Slide lever assembly (34) into position and
replace the two allen screws (38). Use Loctite
or similar sealant.
E) Replace plunger (39).
NOTE: The end hole in the plunger must face
the meter.
F) Assemble the seal/valve body (40, 41) and spring
(42) and replace into the handle body.
NOTE: Install the spring, small end rst.
G) Replace handle sleeve (43).
H) Replace washer (44), o-ring (45), and swivel
assembly (46) and screw rmly into place. Use
Loctite or similar sealant.
METER DISASSEMBLY
A) Unscrew the swivel assembly (46) two complete
turns to allow easy disassembly and reassembly
of the meter and remove boot (28).
B) Unscrew the 4 philips head screws (21), from
the underside of the handle body (4).
C) Using 4mm allen wrench remove 4 screws (29)
from the underside of the handle body (4).
D) Remove register housing (23) assembly.
NOTE: Take care when removing register housing
as the outlet shaft (16) and seal assembly are also
removed.
E) Remove gearbox housing (10) assembly.
GEAR AND O-RING REPLACEMENT
A) Pull bevel gear off the shaft (24) from inside
register housing (23).
B) Remove gear (17), E-clip (18), washer (19),
o-ring (20), and shaft (16) from the underside
of register housing.
NOTE: Use all new parts when reassembling the
gear and shaft assembly.
C) Assembly is a reversal of disassembly.
MODULE REPLACEMENT
Note: Refer to Meter Disassembly Parts A and B.
A) Remove module assembly (25) and remove the
register bracket clip (27).
B) Remove facia (26).
C) Assembly is a reversal of disassembly.
METER REASSEMBLY
A) Clean and inspect all parts. Replace any suspect,
worn, or damaged components.
B) Replace rotors (8,9).
NOTE: Ensure the rotor with the magnets is
assembled with the magnets facing up and positioned
on the correct side of the meter. Both rotors must
also be positioned at 90 degrees to each other.
C) Replace the handle body o-ring (5).
D) Fit gears (13,14,15) into gear box (10).
NOTE: Gears are marked in order of assembly
1, 2, and 3.
E) Replace o-ring (11) on gearbox housing (10)
and position gearbox assembly on top of handle
body (4).
F) Replace register-housing assembly (23) on top
of gearbox housing assembly (10).
NOTE: The gear shaft (16) on the register housing
assembly (23), must be located through gear 2
(14) inside the gearbox and tted into the location
hole in the gearbox housing (10).
G) Replace 4 allen head screws (29) and screw the
meter assembly together.
H) Fit bevel gear (24) inside the register housing
(23).
I) Fit Module assembly (25) into register housing
(23) and replace 4 Phillips head screws (21).
J) Firmly tighten the swivel assembly (46).
K) Replace the boot (28).
L) Test the control handle for correct operation.

5
ITEM PART NO. QTY. IN KIT DESCRIPTION
1 - 1 - Compression Fitting
2 - 1 - Olive
3 - 1 - Adapter
4 - 1 - Control Handle Body
5 - 1 - O-Ring
6 - 2 - Roto Shafts
7 - 1 - 3/8” Plug
8 - 1 - Oval Gear
9 - 1 - Oval Gear and Piston
10 - 1 - Gearbox Housing
11 - 1 - O-Ring
12 - 1 - Middle Shaft
13 - 1 - Q1 Quart Gear
14 - 1 - Q2 Quart Gear
15 - 1 - Q3 Quart Gear
16 - 1 - Outlet Shaft
17 - 1 - Q4 Quart Gear
18 - 1 - E-Clip
19 - 1 - Washer
20 - 1 - O-Ring
21 - 4 - Hi-Lo Screws
22 - 1 - Brass Boss
23 - 1 - Register Housing
24 - 1 - Bevel Gear (Quart)
25 830724 1 - Module, PGM
26 - 1 - Facia (Quart)
27 - 1 - Register Bracket Clip
28 830725 1 - Boot, PGM
29 - 4 - Screws
30 - 1 - Valve Cam
31 - 1 O-Ring
32 1 Washer**
33 - 1 O-Ring
34 - 1 - Lever, Non Latching
35 - 1 - Button Spring
36 - 1 - Lever Plug
37 - 1 - Push Button
38 - 2 Countersink Screws
39 - 1 - Plunger
40 - 1 Seal
41 - 1 - Valve Body
42 - 1 Valve Spring
43 - 1 - Handle Sleeve
44 - 1 Washer
45 - 1 O-Ring
46 830728 1 - Swivel, Control Handle
47 - 1 Strainer
48 - 1 O-Ring
49 - 1 - Adapter (Pistol Style)
831336 1 - O-Ring*
PGM-40 Mechanical Control Handle
Parts List
* To be used with exible hose outlet
when used as pistol style.(see page 2)
(for control handles prior to 5/03 only)
Control Valve Service Kit
(Order 900013) ** Prior to 7/03 (stamped on handle 0283)
use metal washer.
After 7/03 (stamped on handle 0293)
use plastic washer.

6
Parts Diagram
PGM-40 Mechanical Control Handle
Manual tip cannot be used on
PGM-40 control handle. An auto
tip or semi-auto tip must be used.
Use of manual tip can result in overpressurization,
which can cause control handle to crack.
WARNING
!

7
Revision Log:
Rev. E - Added o-ring and 831335 kit
Rev. F - Changed from 3/8” NPT to 3/8” NPS on outlet port.
Rev. G - Note about washer (item 32).
Rev. H - Removed semi-automatic tip models and changed part number for automatic tip to 3332-086.
TROUBLE CAUSE REMEDY
No uid passing through the A. Blocked strainer A. Clean or replace strainer (47)
meter B. Dirt particles jamming the rotors B. Dismantle meter assembly and clean
C. Damaged plunger seal C. Replace damaged plunger seal (40)
The meter is not registering Damaged Mechanical Module Replace Module (item 25)
uid output
Constant oil leak from the tip Damaged plunger seal Replace plunger seal (check for damage)
Intermittent drip from the tip Dirt in the tip Remove the tip and blow out any dirt particles,
replace if necessary
Tip not closed (semi-auto tip) Tip must be manually closed
Oil leak from the lever Damaged o-rings Replace damaged o-rings (item 33 & 31)
assembly area
Low ow rate Blocked strainer Replace strainer (item 47)
Oil leaking from the swivel inlet Damaged o-ring or swivel Replace o-ring (item 48) or swivel (item 46)
* 806895 (-112) o-ring included with extension.
Outlet
Extensions
Model
Number Nozzle / Tip
Extensions
Before 5/03
3/8” NPT
After 5/03
3/8” NPS
Rigid 3330-037 Qt.
3330-040 Lt. 3332-086
829648 831471
plus seal-
ing nut
831470
Flex 3330-038 Qt.
3330-041 Lt. 3332-086 829973 831469*
Flex 900 3330-039 Qt.
3330-042 Lt. 3332-086 830276 831429*
Straight 3330-060 Qt.
3330-061 Lt. 3332-086
81334 plus
jam nut
831333
831472
plus seal-
ing nut
831470
9” Flex 3330-053 Lt. 3332-086 830107 831473

Balcrank®Corporation
Weaverville, NC 28787
800-747-5300
800-763-0840 Fax
www.balcrank.com
SERVICE BULLETIN SB3022
Rev. H 11/09
For Warranty Information Visit:
www.balcrank.com
This manual suits for next models
8
Table of contents
Other Balcrank Control System manuals
Popular Control System manuals by other brands
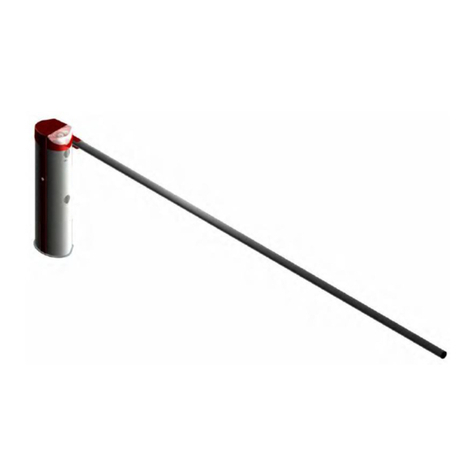
Stagnoli
Stagnoli DAPHNE 4 manual
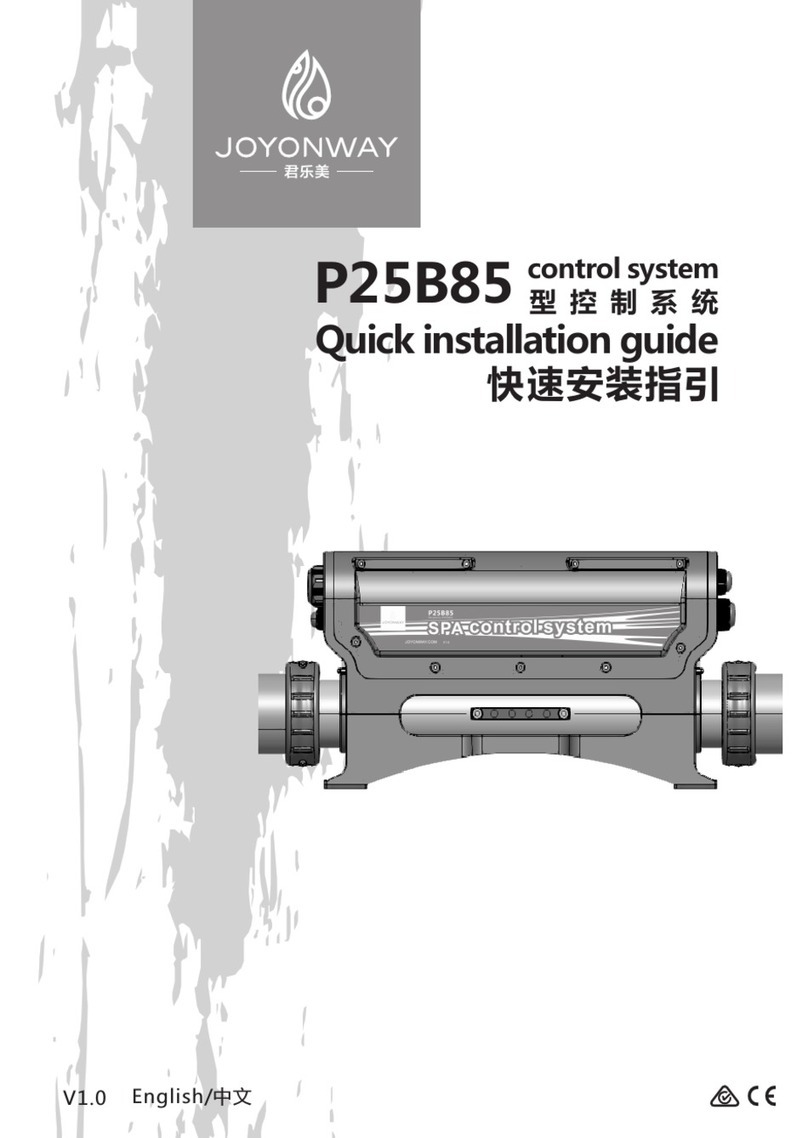
Joyonway
Joyonway P25B85 Quick installation guide
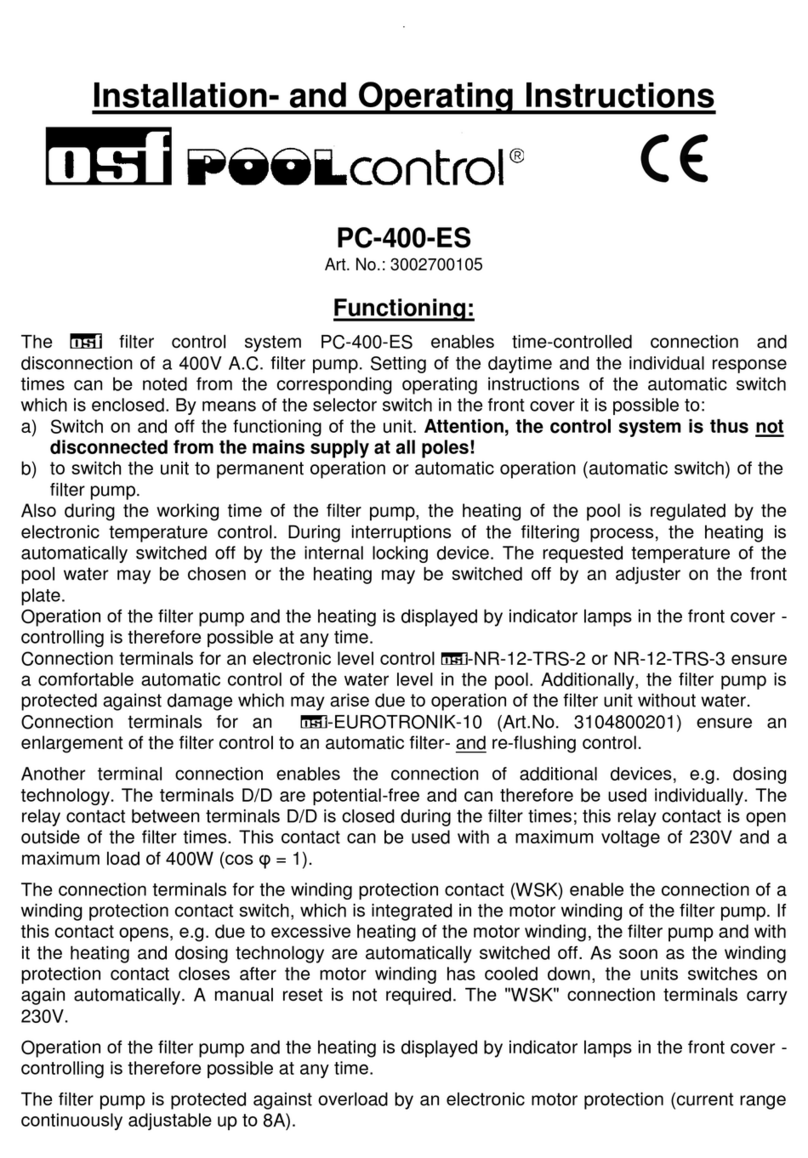
OSF
OSF Pool control PC-400-ES Installation and operating instructions
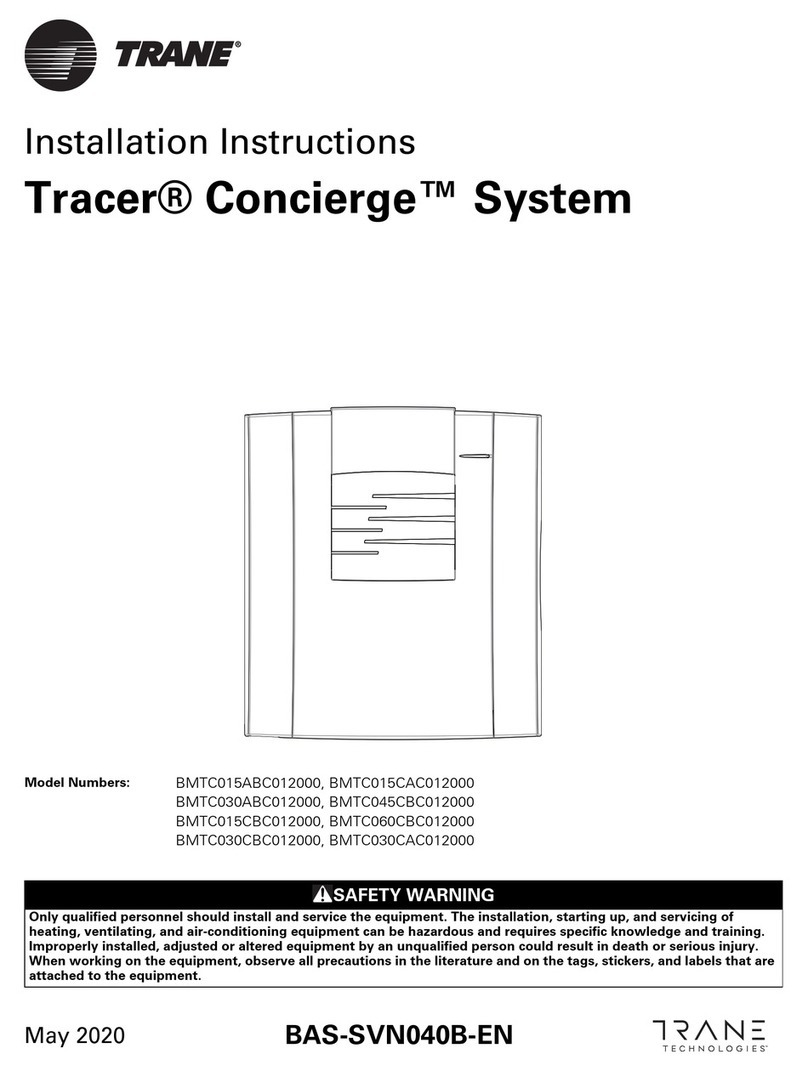
Trane
Trane Tracer Concierge BMTC015ABC012000 installation instructions
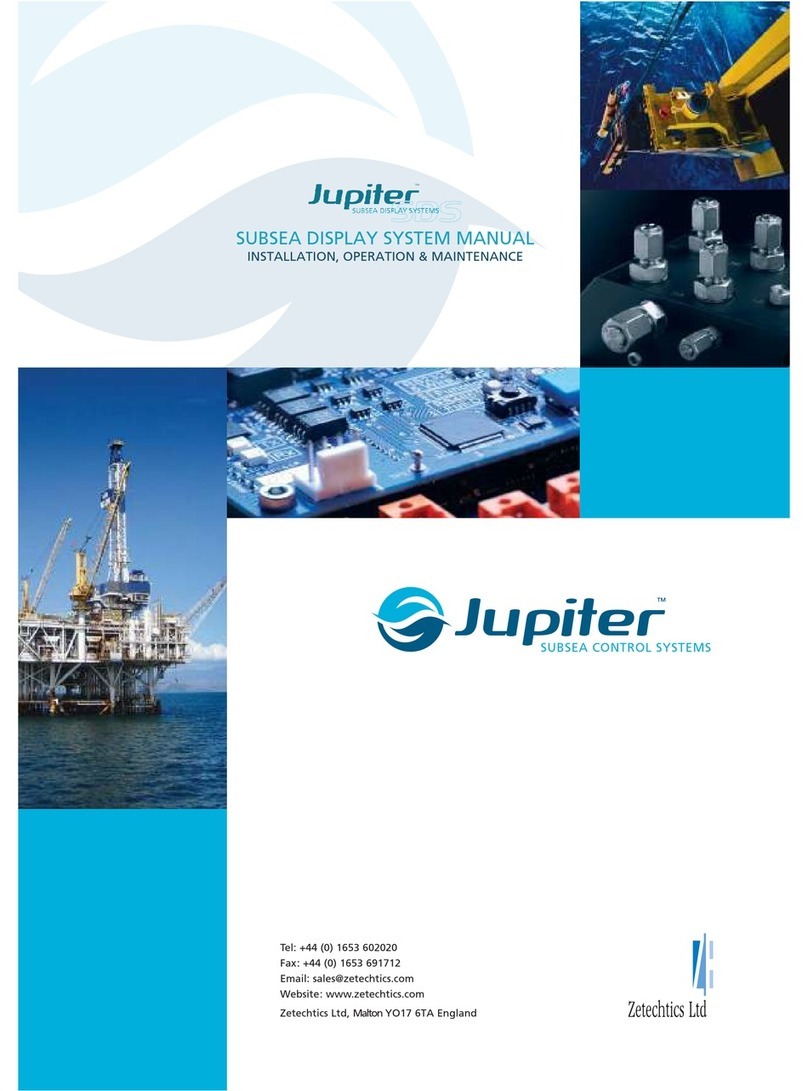
Zetechtics
Zetechtics Jupiter Installation operation & maintenance
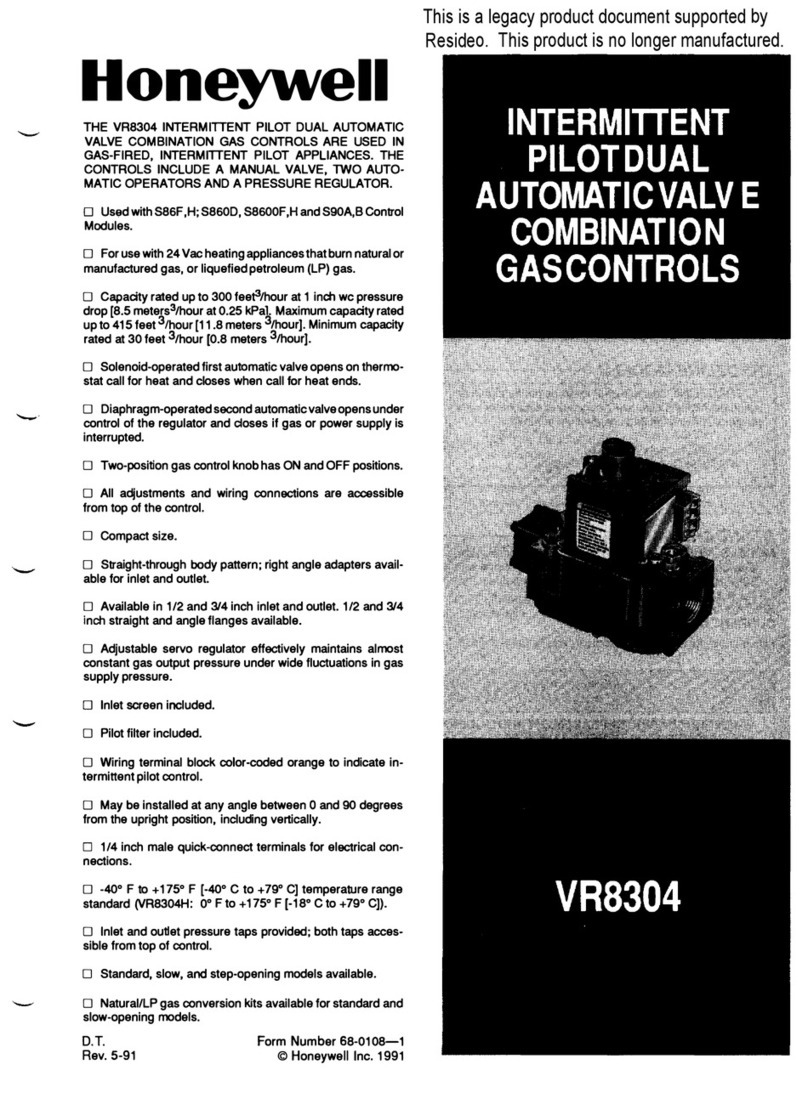
Honeywell
Honeywell VR8304 manual