Thermo orion 1818 User manual

IMPORTANT NOTICE:
Model 1818 Oxygen Scavenger Monitor is shipped WITHOUT SOFTWARE AND WILL NOT OPERATE UNTIL SOFTWARE IS
INSTALLED. For use with Hydrazine, use software found in Cat. No. HYDRAK; for use with ELIMIN-OX®, use software found in
Cat. No. ELIMAK.
®ELIMIN-OX is a registered trademark of NALCO Chemical Co.
A Thermo Electron business
Model 1818
Oxygen Scavenger Monitor
INSTRUCTION MANUAL


TABLE OF CONTENTS
I. General Information I. 1
Introduction I. 1
Principles of Operation I. 1
Principles of Calibration I. 2
Sample Requirements I. 3
Description of Model 1818AO Monitor I. 4
II. Instrument Preparation II. 1
Unpacking Instrument II. 1
Mounting, Plumbing and Wiring
of Series 1800 Monitor II. 1
Reagent Diffusion Bottle II. 2
Installation of Iodide Electrode II. 3
Installation of Reference Electrode II. 3
Installation of ATC Probe II. 3
Flow Regulation II. 3
III. Instrument Operation III. 1
Description of Basic Unit Controls III. 1
Start Up/ Normal Instrument Operation III. 2
Initial Instrument Set-Up III. 2
Use of Test Mode III. 2
Error Mode III. 3
Shutdown and Start-Up Procedure III. 4
Flow Off III. 4
IV. Installation and Operation of Modules IV. 1
Signal Conditioner Module IV. 1
Removing Installed Module IV. 1
Replacing Installed Module IV. 1
Setting Module Output IV. 1
Electrical Connections IV. 2
Description of Signal Conditioner IV. 2
Programming Measuring Range IV. 3
Installation of Optional Alarm Module IV. 3
Setting Alarm Output IV. 4
Electrical Connections IV. 4
Description of Alarm Module Controls IV. 5
Alarm During Calibration IV. 5
Alarm After Power Failure IV. 5
Setting Alarms 1 and 2 IV. 5
V. Calibration V. 1
VI. Instrument Maintenance VI. 1
Maintenance Schedule VI. 1
Weekly Maintenance VI. 1
Bi-Weekly Maintenance VI. 1
Monthly Maintenance VI. 2
Bi-Monthly Maintenance VI. 2
Quarterly Air Pump Check VI. 2
Yearly Preventive Maintenance VI. 3
VII. Troubleshooting VII. 1
VIII.Repair and Service VIII. 1
IX. Notice of Compliance IX. 1
X. Warranty X. 1
XI. Ordering Information XI. 1
XII. Mounting Dimensions XII. 1
XIII.Wiring Diagram XIII. 1


I. 3
Two-Point Calibration
This procedure provides maximum calibration
accuracy and requires use of dynamic calibrator,
Cat. No. 15DC15/115 V or 15DC20/220 V. In addition
to calculation of electrode Eoas is done in off-line
calibration procedure, this procedure determines
electrode slope.
To perform a dynamic two-point calibration, the 1818 is
first connected to a reductant-free sample stream. An
appropriate diluted standard is then prepared. A sup-
plied syringe is filled with diluted standard and mount-
ed on the calibrator. The calibrator is then mounted
near the monitor and the syringe tubing connected to
the standard injection port. By adjusting calibrator
pump settings, two different flow rates produce two
known standards diluted into the sample background.
By pressing the appropriate keys on the monitor when
prompted, the monitor’s microprocessor completes the
calibration.
If a mistake is made or problems occur during calibra-
tion, an error light will come on and alert the operator.
By pressing the error key, the operator can access
information on the display to help determine the
problem.
Sample Requirements
Sample Inlet Connection - 1/4” NPTF. If particulate
matter is present in sample, prefiltration is necessary.
Moderate amounts of particulates will be removed by
the 60 micron stainless steel filter located after inlet
valve.
Flow Rate - must be 50 mL/min. minimum at monitor
sample inlet.
Pressure - 8-100 psig. Consult ORION for details on
sample handling if pressure is outside range.
Temperature - Temperature must be between
15-40 °C.
Oxygen Scavenger Level - Levels are read directly
in ppb or ppm.
Sample Alkalinity - Sample alkalinity should not
be more than 5 ppm CaCO3equivalent to ensure
two-month reagent life. If sample alkalinity is above
5 up to 10 ppm maximum as CaCO3, reagent life is
reduced to six weeks.
For higher sample alkalinity, contact the ORION
Technical Service.

I. 4
Description of Model 1818AO
NOTE: Numbers in the description
refer to Figure 3.
Sample Inlet Valve (1) - Accepts the sample stream
via 1/4 inch NPTF connector. The customer must
supply the sample with a pressure between 8 and
100 psig, and a sample flow rate to the analyzer of
50 mL/min. minimum.
Bypass Filter Assembly (2) - 60 micron stainless
steel filter traps particulate matter in sample stream.
Pressure Regulator (3) - Adjusts flow on incoming
sample stream.
Flow Valve (4) - Used to turn off flow to flow cell.
Flow Meter (5) - Measures sample flow rate.
40 mL/min. nominal flow is required through the
analyzer.
Flow Restrictor Tubing (6) - Maintains steady
sample flow rate in conjunction with pressure regulator.
Pressurized Electrolyte Reservoir (7) - Provides a
constant flow of electrolyte solution through reference
electrode for maximum stability.
Reference Electrode (8) - Provides a constant refer-
ence potential and completes the measurement circuit.
Must be placed in right hand side of flow cell.
Iodide Electrode (9) - Senses iodide ions in sample
stream and produces an electrical potential dependent
on sample oxygen scavenger. Must be placed in left
hand side of flow cell.
ATC Probe (10) - Measures sample temperature
and inputs data to microprocessor for automatic
temperature compensation (ATC).
Reagent Mixing Loop (11) - Mixes iodine reagent with
oxygen scavenger in sample to form iodide, measured
by iodide-sensing electrode.
Flow Cell (12) - Contains reference electrode,
sensing electrode, ATC probe and sample measure-
ment reservoir.
Thumbscrew (13) - Supports the reagent diffusion
bottle.
Fluid Connector Block (14) - Connects reagent diffu-
sion bottle to sample stream and flow cell assembly.
Reagent Diffusion Bottle (15) - Acidifies and adds
iodine to the sample by means of passive diffusion.
LED Display (16) - Provides digital readouts of
concentration, temperature, millivolts and error codes.
Keypad (17) - Consists of five mode keys, four prompt
indicator lights, two scroll keys and one key for enter-
ing data. Mode and error indicators are also incorpo-
rated on keypad.
On/Off Switch (18) - Controls all power to the
electronics.
Drain (19) - Atmospheric drain prevents back pressure
on reference electrode.
Standard Injection Port (20) - Allows connection of
dynamic calibrator tubing to fluid connector block
during two-point calibration.
Bypass Valve (21) - Used to throttle flow in bypass
system.
Check Valve (22) - Prevents backflow of electrolyte
from pressurized reservoir.
Air Pump (23) - Provides air to pressurize the
electrolyte reservoir.
Bottle Clamp Band (24) - Holds reagent diffusion
bottle securely in place.

I. 5
Figure 3
Major Monitor Components
6
16
17
18
22
8
11
10
13
20
19
1
24
15
21
2
14
3
4
12
23
9
5
7
Pure Water™Monitors
1800 Series
Release latches
to access

I. 6

II. 1
II. INSTRUMENT PREPARATION
Figure 4
Unpacking Monitor
Unpacking Instrument
Refer to Figure 4.
Report any obvious damage of shipping container to
carrier and hold for inspection. The carrier (not Orion)
is responsible for any damage incurred during ship-
ment.
1. Open outer box. Remove foam corner support
pieces.
2. Open inner box and remove cardboard retaining
shell. Remove accessory boxes and instruction
manual.
3. Unbolt the monitor from mounting board.
Save all hardware for use during installation.
4. Carefully place the monitor at a convenient
location. Do not pull or lift instrument by its fluidic
components.
Mounting, Plumbing And Wiring of
Series 1800 Monitor
1. Select a site for instrument that allows it to be
permanently bolted in an upright position with ample
height for atmospheric drain operation and ready
access to both electronic controls and flow cell.
The analyzer site must permit connection to sample
line, a drain, an AC power supply, and any connec-
tions for output devices.
2. Prepare mounting holes. Carefully lift the Series
1800 Monitor and bolt into place. Do not lift instru-
ment by pulling on any fluidic components.
Be sure to use the four shoulder washers that
are provided, they will resist future corrosion.
3. Connect a waste line to a drain of sufficient
capacity.
4. Connect sample line to the 1/4-inch tube connector.
It is recommended that a shutoff valve be installed
at the sampling point.
5. Remove decorative panel inside the cabinet by
unscrewing the four Phillips screws. Then remove
protective plug and feed AC power line through
hole. See Figure 5.
6. See APPENDIX for wiring diagram. Disconnect:
jumper wire from TB2 terminal 7 and connect to:
TB2 terminal 6for 100 V AC
5for 115 V AC
4for 220 V AC
3for 240 V AC
Warning: Failure to connect jumping wire to
the proper tab will permanently damage the
monitor.
7. Connect:
COMMON to TB2 terminal 1 (most left)
LINE to TB2 terminal 2
GROUND to ground stud adjacent to terminal 1
using captive type terminal at the end of ground
wire.
Warning: Failure to connect chassis to a
suitable ground may result in hazardous
conditions. Failure to use captive type
terminal could result in potential shock
hazard and may jeopardize CSA approval.

II. 2
240V
220V
110V
100V
ground
options
AC power
common
line
jumper
Figure 5
Electrical Wiring of 1800 Series Monitors
Figure 6
Reagent Diffusion Bottle Assembly
8. All electrical wire feeding through the chassis must
pass through appropriate electrical fittings in order
to maintain the design integrity of the splash-proof
electronic chassis. Since different types of fittings
are required at various installations, this feed through
is to be supplied by the user.
Warning: A grounded metal conduit is
required for FCC compliance.
9. Replace decorative panel if no further wiring is
required.
Warning: Failure to replace decorative panel
could result in potential shock hazard.
Reagent Diffusion Bottle
Numbers refer to Figure 3, unless otherwise noted.
NOTE: This procedure requires use of ORION
Reagent (Cat. No. 181811).
CAUTION: Care must be taken to avoid con-
tact of skin or clothes with this reagent which
contains concentrated acetic acid and iodine.
Avoid breathing vapor. Wear rubber gloves
and goggles when performing this procedure.
In case of skin contact, flush skin immediately
with water to prevent burns.
1. Support the bottom of the reagent bottle, 15, release
holding clamp, 24, with one hand. Turn thumbscrew,
13, counterclockwise to release diffusion bottle.
Unscrew white bottle cap and gray tubing connector
assembly. (Keep bottle supplied with instrument
as a spare.)
2. Take a new bottle of 181811 reagent to a well-
ventilated area such as a laboratory fume hood.
Unscrew and remove white cap.
3. Connect diffusion tubing (use Cat. No. 181860
ONLY) to tubing connector assembly to conform to
Figure 6. Place the tubing assembly and cap into
the bottle.
4. Replace gray cap and screw white cap on tightly.
5. Insert the four nipples on the top of the reagent
diffusion bottle into the fluid connector block, 14,
as shown in Figure 6.
6. Support the bottom of the reagent bottle with one
hand and tighten the thumbscrew clockwise.
7. Reclamp bottle to panel to secure.
white cap
nipples with
small O-rings
gray cap with
large O-ring
tubing should be connected
to right-hand barbed fittings
only(as seen from the front)
tubing
barbed fittings
reagent
diffusion
bottle
fluid connector
block

II. 3
Installation of Iodide Electrode
1. Unpack iodide electrode (Cat. No. 100022) and
carefully remove protective cap.
2. Polish electrode according to instruction card with
strips (Cat. No. 948201).
3. Insert iodide electrode into sensing hole on left in
flow cell.
4. Connect electrode to cable marked “Sens. Elect”.
Installation of Reference Electrode
1. Unpack reference electrode, 8, (Cat. No. 100056)
and tubing from shipping box. Remove protective
caps from bottom and sidearm of electrode. Save
caps for future storage of electrode. Inspect internal
of electrode (item 7 in Figure 7). Verify it is at least
half filled with the internal fill solution. If not, replace
the electrode.
2. Shake out as much filling solution as possible
through sidearm, 30, into sink or drain.
3. While passing 1/8-inch tubing, 31, into electrode
through sidearm, slide 1/4-inch tubing, 32, over
sidearm. The outside tubing should extend
3/8-1/2-inch over sidearm.
4. Remove cap and fluid seal from electrolyte fill
solution bottle, 33. Hold bottle in upright position.
Check that rubber gasket, 34, is properly aligned,
then connect cap end of tubing assembly to bottle.
The 1/8-inch tubing should extend to the bottom of
the bottle.
5. Dry off ceramic frit on base of electrode with tissue
paper. Squeeze bottle for a few seconds. A small
amount of filling solution should bead up on frit sur-
face, indicating good electrolyte flow. If no moisture
is visible, electrode is clogged and should be
replaced.
6. Invert electrolyte bottle and snap into clip, 35.
Locate discharge tube of air pump on fluidic panel.
End of tubing has hollow push pin for pressurizing
reference reservoir. Puncture base of bottle with pin
and push pin down until its PVC base abuts bottle.
Mark and date level of fill solution in reservoir. Then
electrolyte solution will begin to flow into electrode.
7. Connect electrode to electronic chassis by “keeper
cable” labeled Ref. Elect. Insert electrode into
reference hole on right in flow cell. See Figure 3.
35
33
34
31
32
30
7
Figure 7
Reference Electrode Assembly
Installation Of ATC Probe
The automatic temperature compensation (ATC) probe
is already connected to the electronics housing. Insert
into hole of 3/8-inch tee fitting draining flowcell, located
behind electrodes.
Flow Regulation
When the Model 1818AO Monitor is first commis-
sioned, it is advisable to flush out fluidics system at
least one hour prior to initial calibration and use. The
electronics need not be turned on at this time. Refer to
Figure 3.
1. Open sample inlet valve, 1.
2. Pull out red locking ring of pressure regulator, 3,
then adjust black knob so that ball of flow meter
reads 40ml/min.. Push in red locking ring to secure
the setting.
3. Open bypass valve, 21. Check for appropriate
sample flow. Readjust pressure regulator if required.
4. Wait at least one hour before calibrating analyzer.

II. 4

III. 1
III. INSTRUMENT OPERATION
test sample
°C ppm
mV ppb
slope error
•
E
o
electrode stable
•
a
c
d
b
enter/
done
sample test program
cal.
error
fill/
flow
off
drain/
flow
on
add
std. 1 add
std. 2
amplifier ORION 2A01
Figure 8
Front Panel Keypad
Description of Basic Unit Controls
On/Off Switch - Controls powers to all electronics and
air pump. It is located on electronic chassis bottom
and includes an integral circuit breaker.
LCD Display - Displays four-and-one-half digit plus
polarity sign used to read concentration, slope, Eo,
millivolts, temperature, error messages, and diagnostic
information.
Mode Indicating LED - (Located to left of LCD
display.) Indicates range (ppb or ppm), error codes,
and electrode stable in sample mode. Displays tem-
perature (°C), millivolts, electrode slope, and Eoon
LCD in test mode.
Prompt Indicating LED - Prompts the user during cal-
ibration. Four LED’s located in keypad region are used.
These are: add STD 1, add STD 2, begin calibration,
two-point calibration complete.
/\
and
\/
Keys - increases or decreases displayed val-
ues that can be operator-changed such as alarm level,
analog output range, and off-line calibration values.
Enter/done Key - Enters value displayed on LCD into
“permanent” memory for later use. Key also indicates
to microcomputer that a required calibration step has
been completed.
Sample Key - Puts Series 1800 Monitor into sample
mode and (re)activates any optional modules. This is
also its default mode, e.g., instrument automatically
enters sample mode when first turned on and after
calibration.
Cal Key - Starts Series 1800 Monitor into calibrate
mode. Operator is then prompted through the steps
necessary for calibration.
Test Key - Places Series 1800 Monitor into test mode
where LCD displays temperature, millivolts, Eo and
slope. Each successive push of key, steps instrument
through this sequence, and an LED on the left of
display indicates value displayed.
Error - If error LED is lit (soft error), then pressing key
causes LCD to display an error code. Note, in the
case of “hard error,” the LCD would cease to display
normal output but would display error code only. Refer
to Error Code Table.
Program Key - Used to program expected calibration
concentration increments. Also used in conjunction
with Cal key for off-line calibration.
a, b, c, and d Keys - For future expansion.
enter/
done
cal.
error
two pt.
cal.
complete
begin
cal.
add
std. 2
add
std. 1

III. 2
Start Up/Normal Instrument Operation
1. Install the Model 1818AO Monitor according to
instructions in INSTRUMENT PREPARATION.
Power supply should be wired for proper voltage
and instrument suitably grounded.
2. Turn on flow at sample inlet and flush for at least
one hour.
3. Power up Model 1818AO by toggle switch on bot-
tom of electronics case. See Figure 3.
4. LCD will display following information sequence:
a.+ 1.8.8.8.8;
b.1818 while LEDs sequentially light;
NOTE: Mode indicating LEDs and test LED
on modules are not tested during start-up
sequence.
c.Revision number of software program (e.g., -2.3-).
5. After completion of steps 1-4, the Monitor is now in
normal operational mode “sample.”
Initial Instrument Set-Up
Before first sample measurements on Model 1818AO
can be performed, calibration concentration incre-
ments must be programmed into memory.
Program Key Table is found on inside instrument door
and following. Refer to the appropriate APPENDIX for
the particular oxygen scavenger being measured to
find correct P2 and P3 default values.
Table 1
Program Key Table
Code Meaning
P0 Off-line calibration value
P1 (Not used on Model 1818)
P2 Concentration increase for STD 1 addition
P3 Concentration increase for STD 2 addition
1. Press program key three times until the LCD
displays P2. Then the current value for the first
concentration increment will be displayed.
2. Change value, if desired, by using keys marked
/\
and
\/
. Press enter/done key to store appropriate
value in memory. Note P2 cannot exceed the P3
value.
3. Press program key until the LCD displays P3 for
two seconds. Then the current value for the second
concentration increment will be displayed.
4. Change value, if desired, by using
/\
and
\/
. Press
enter/done key to store appropriate value in memo-
ry and unit will automatically return to sample mode.
5. Battery backup of memory will maintain pro-
grammed variables for at least one month if battery
is fully charged.
Use of Test Mode
When test key is pressed, the LCD displays tempera-
ture, millivolts, slope and Eo. Every time the test key is
pressed, the monitor steps through this sequence. An
LED to the left of display indicates value displayed.
If test mode is entered from sample mode, then sam-
ple and test LED are lit. If test mode is entered from
calibration mode, then calibrate and test LED are lit.
Note that while LCD displays test information, the
instrument still continues normal sampling or calibra-
tion sequence. Therefore, when sample and test
modes are pressed, signal conditioning and optional
alarm modules are active. When calibrate and test
modes are pressed, calibration prompt LEDs will light
as usual.
To exit test mode, press sample or calibrate key as
desired. LCD will now display instantaneous computed
concentration.
If sample key is pressed while in the calibration mode,
the current calibration will abort with no data saved.

III. 3
Error Mode
The Model 1818AO Monitor diagnoses two types of
errors which are termed “hard” and “soft.” In the event
of hard error, the analyzer cannot compute any mean-
ingful concentration values, error LED will be lit and
LCD will display an error code. The signal conditioner
module will indicate zero scale and alarms will be
deactivated. Hard error must be corrected prior to
resumption of normal operation (E40 and E50) by per-
forming a complete calibration.
If error LED is active but instrument continues to dis-
play concentration, this is termed “soft” error. Soft
error can affect accuracy and/or precision of displayed
concentration but not interfere with instrument’s ability
to compute sample concentration. To determine cause
of soft error, press error key and LCD will display error
code.
Table 2
Error Codes
Error
Code Meaning
E00 No errors
E01 Default values are used. The monitor has not
been calibrated since start-up or the reset
button was pushed.
E02 Sample is outside the temperature range of
15 - 40 °C
E03 Combination of E01 and E02
E04 Faulty ATC probe, or related circuitry
E05 Combination of E01 and E04
E10 After calibration, the new slope is outside the
expected range.
E20 Calibration due. Last calibration performed
30 days ago. A reminder to perform another
calibration.
E30 Calibration due and slope error. This indicates
that the last calibration performed was at least
30 days ago and the electrode slope was out
of specification at that time.
E40 Calibration overdue. It has been at least 6
weeks since the last calibration. The instrument
beyond this point could be out of specification.
This is a hard error. The only way to exit this
error is to perform a complete two-point or
off-line calibration.
E50 Calibration overdue and slope error. This
indicates that it has been at least 6 weeks since
the last calibration and the electrode slope was
out of specification at that time. The instrument
beyond this point could be out of specification.
This is a hard error. The only way to exit this
error is to perform a complete two-point
calibration (or off-line calibration depending
on reductant used.)
The most common error codes are combinations
of the above codes, but other errors may be displayed:
E12 E10 and E02
E14 E10 and E04
E21 E20 and E01
E22 E20 and E02

III. 4
Shutdown And Start-Up Procedure
The following steps should be taken if a loss of sample
flow is expected for more than two days. These proce-
dures will prevent possible build-up of acidic reagent
vapors in the monitor.
NOTE: At cycling power plants or on units
where sample flow to the monitor is frequent-
ly interrupted, the installation of a backup
sample is recommended. Connect a suitable
high purity water source (such as condensate
storage tank) into the sample line just
upstream of the monitor’s sample inlet. By
putting shutoff valves in both sample and
backup lines at this point, backup or actual
sample flow can be quickly valved in or out
as required. In this way, continuous flow to
the monitor can be supplied and the need for
the following startup/shutdown, equilibration
and recalibration procedures is eliminated.
(Note, however, that for sample flow loss of
only a few hours, monitor recalibration
should not be required.)
Shutdown
1. Shut off sample flow prior to the monitor inlet.
2. Turn power OFF.
WARNING: Wear rubber gloves and safety
goggles to avoid possible injury from reagent
residuals in the system.
3. Loosen clamp securing reagent bottle to fluidics
panel. Support bottom of bottle with one hand, and
turn thumbscrew on top of fluid connector block to
release reagent bottle. Store in a well-ventilated
area such as a laboratory fume hood. If bottle is to
be stored more than two days, remove top cap and
tubing assembly and store in a large beaker of tap
water. Otherwise, tubing will become brittle and may
break when analyzer is restarted.
4. Carefully pull iodide and reference electrodes out of
the top of the electrode holder and let them hang by
their connectors. Locate protective end cap from ref-
erence electrode kit and place on base of reference
electrode. This will prevent reference electrode from
drying out.
Start-Up
1. If reagent bottle has been stored longer than two
days without removal of tubing, tubing must be
replaced. If acid reagent is more than four to six
weeks old depending on sample alkalinity, or age is
unknown, it should be replaced. Use a fume hood,
rubber gloves and goggles for these procedures.
Unscrew bottle cap and carefully lift out gray cap
with tubing connected. Remove old diffusion tubing
from nipples. Replace with new tubing, replace
reagent if required, and reinstall bottle on analyzer.
2. Polish iodide electrode per Monthly Maintenance
instructions. Looking at monitor, reinstall carefully in
the left section of the electrode holder.
3. Restore sample flow to analyzer. If necessary,
adjust pressure and flow rate through analyzer to
normal ranges.
4. Remove protective end cap from reference elec-
trode. Looking at the monitor, reinstall electrode in
the right section of the electrode holder, being care-
ful not to disconnect reservoir tubing from electrode
sidearm.
5. When meter reading stabilizes (about one hour),
recalibrate according to instructions in appropriate
oxygen scavenger APPENDIX.
Flow Off
If the analyzer is expected not to have flow for time
periods of less than twenty-four (24) hours, leave the
instrument on and neglect its output.
If the time is expected to be greater than twenty-four
hours, follow Shutdown procedures.

IV. 1
IV. INSTALLATION AND OPERATION OF MODULES
Signal Conditioner Module (Cat. No. 180001)
The Model 1818AO Monitor is shipped with signal
conditioner module (Cat. No. 180001) factory installed.
Read section Setting Module Output and if you
need to change the factory settings, see Removing
Installed Module.
When factory settings are correct for your instrument,
then proceed to section Electrical Connections -
Signal Conditioner Module.
Removing Installed Module
1. Ensure power to the Series 1800 Monitor is turned
off at power source.
2. Unscrew module keypad from the black brackets
using the two screws on the keypad.
3. Make certain the plungers are pulled back so that
the grommets are in a closed position.
4. Slide out module far enough to access DIP
switches.
Replacing Installed Module
1. Ensure power to the Series 1800 Monitor is turned
off at power source.
2. Open door of electronic assembly. Use No. 2
Phillips screwdriver to remove four screws on deco-
rative panel.
3. Remove module keypad from shipping box.
4. Unscrew module keypad from the black brackets
using the two screws on the keypad.
5. Make certain the plungers are pulled back so that
the grommets are in a closed position.
1234
Figure 9
Dip Switches on Signal Conditioner Board
Setting Module Output
The signal conditioner has two voltage outputs
(0-5 or 0-10 volts) and two current outputs (4-20 or
0-20 mA isolated). Switches are preset by manufactur-
er at 0-5 volts and 4-20 mA but can be reset by DIP
switch (see Figure 9) on signal conditioner printed
circuit board. When required, alter preset output values
before sliding the module into the monitor as follows
(also refer to Table 3).
1. Current output, factory set at 4-20 mA. 0-20 mA is
obtained when switching S1-2 into “OFF” position
and S1-3 into “ON” position.
2. Voltage output, factory set at 0-5V DC. 0-10V DC is
obtained when switching S1-1 into “ON” position.
3. Slide PC Board onto instrument guide rails. Rear of
PC Board should touch backplane and plug should
fit securely into its socket. Check that module brack-
et is against both rails.
4. Push plungers in.
5. Make certain flex cable is attached to keypad and to
PC Board. If not, carefully slide header into socket.
Table 3
Signal Conditioner Output Modes
S1-1 S1-2 S1-3 S1-4
0-5 V OFF X X X
0-10 V ON X X X
4-20 mA X ON OFF X
0-20 mA X OFF ON X
X = No effect

IV. 2
Electrical Connections
1. If module keypad is still attached, then unscrew
module keypad from black brackets using the two
screws on the keypad.
2. Feed wire through hole in chassis bottom labeled
option. See Figure 6.
3. Run wire along wire trough to signal conditioner.
4. Connect wires to voltage (0-5 V or 0-10 V) or cur-
rent (0-20 mA or 4-20 mA) output. See Figure 10.
5. Double check the flex cable connections.
6. Screw the keypad on the black metal brackets.
7. Double check the flex cable connections.
8. Measure to ensure appropriate number of panels
has been removed.
9. Align decorative panel against four stand-offs and
reattach with Phillips screws. Decorative panel
should not cover any module.
Warning: For safety reasons, the Series 1800
Monitor should not be operated without the
decorative panel in place. Failure to replace
the panel could expose the user to dangerous
voltages.
Table 4
Outputs Of Signal Conditioner Terminals
Output Terminals
Voltage ( + ) 1
( – ) 2
Current ( – ) 7
( + ) 8
Description Of Signal Conditioner
Set Zero - Sets lower level concentration output. In
this mode LED above set zero is active. To set output
to either linear or logarithmic, hold key down to toggle
between these two output forms.
Set Full Scale - Sets upper level concentration output.
In this mode LED above set full scale is active.
Test - Generates zero or full scale output to set up an
external recording device. Test key deactivates signal
conditioner module and either set zero or full scale
LED will be active. After pressing test key, there will be
an output delay of up to three seconds. Press sample
key to reactive module.
Mode Indicating LED - (located on left of module
keypad). Indicates linear of logarithmic signal output.
When set zero key is held, the mode toggles between
these output forms.
Figure 10
Wiring Diagram of Signal Conditioner Module
log output
linear output test set
zero set full
scale
signal output ORION 2B01
Figure 11
Signal Conditioner Keypad
12345678
0 to 5V DC or
0 to 10v DC
Output
1K ΩLoad Min.
NC NC NC NC
+– –+
0 mA to 20 mA or
4 mA to 20 mA Current Output
1K Ω Load Min.

IV. 3
Programming Measuring Range
1. Press set zero key. LED above set zero will acti-
vate and LCD will display current programmed
value. Present default value is 1 ppb for log range
and 1 ppb for linear range.
2. Alter value by using
/\
and
\/
keys. Lowest possible
value is 1 ppb.
3. Press enter/done key when the correct value is
displayed.
4. Set upper range by pressing set full scale then
follow above procedure. Preset default value is
100 ppb. Note that it is not possible to set zero
value higher than full scale, and a range of at least
two decades should be used.
5. To send 0% and 100% of full scale signal to an
external recording device, press test key on signal
conditioner module. The first time causes 0% signal
to be sent, the second time causes full scale signal.
Remember, there may be up to a three second
delay when test key is pressed.
6. To alternate from log to linear mode:
Press set zero key. The output mode will toggle
between log and linear, indicated by the LED. The
log and linear zero and full scale are independent
and should be set separately. Press enter/done
when in desired mode.
Table 5
Default Values - Model 1818
P0 Off-line CAL Value 000
P1 Not Used 000
P2 STD 1 *
P3 STD 2 *
Set Zero (log) 1 ppb
Set Zero (linear) 1 ppb
Set Full Scale (log) 100 ppb
Set Full Scale (linear) 100 ppb
Set Alarm 1 100 ppb
Set Alarm 2 1.00 ppm
Slope *
Eo*
* See appropriate oxygen scavenger APPENDIX for
correct default values for P2, P3, Slope, and Eo.
Installation Optional Alarm Module
(Cat. No. 180011)
The optional module is mounted in the instrument in
the following manner:
1. Ensure power to the Model 1818 Monitor is turned
off at power source.
2. Open door of electronic assembly. Use No. 2
Phillips screwdriver to remove four screws on
decorative panel.
3. Remove optional module keypad assembly from
shipping box.
4. Unscrew module keypad from the black brackets
using the two screws on the keypad.
5. Make certain the plungers on the black metal frame
are pulled back so that the grommets are in a
closed position.

IV. 4
12345678
NC
ALARM 1
Alarm contacts
10A 250VAC max
NO
NC
NO
NC
E6 E8
E7
ALARM 2
Alarm contacts
10A 250VAC max
Disable output contacts
Choose either NC or NO
contacts 10A 250VAC m
NO NO NO
Setting Alarm Output
For both alarms 1 and 2, NO and NC conditions are
available simultaneously. For “alarms disabled” condi-
tion, either NO (factory set) or NC is available. To
change factory setting, perform the following steps:
1. Soldered the appropriate jumper, to change
between the NO and NC mode for an “alarms dis-
abled” remote indication (terminals 7 and 8). See
Figure 12.
2. Place PC Board onto instrument guide rails. Rear of
PC Board should touch backplane and plug should
fit securely into its socket. Check that module brack-
et is against both rails. Press the two plastic
plunger down to lock module in place.
3. Make certain flex cable is attached to keypad and to
PC Board. If not, carefully slide header into socket.
Table 6
Terminals 7 And 8 Alarms Disabled
Mode Jumper
NO E7 to E8 (factory set)
NC E6 to E8
Figure 12
Jumper Connections on Alarm Module PC Board
Electrical Connections
1. Feed wire through hole in chassis bottom labeled
“options” (see Figure 5).
2. Run wire along wire trough to alarm module.
3. Connect wires output as required (see Figure 13).
4. Double check the flex cable connections.
5. Screw the keypad on the black metal brackets.
6. Double check the flex cable connections.
7. Measure to ensure appropriate number of panels
have been removed.
8. Align decorative panel against four stand-offs and
reattach with Phillips screws. Decorative panel
should not cover any optional module.
WARNING: For safety reasons, the Series
1800 Monitor should not operate without the
decorative panel in place. Failure to replace
the panel could expose the user to dangerous
voltages.
Table 6
Outputs Of Alarm Module Terminals
Outputs Terminals
Alarm 1 Comm 1
NC 2
NO 3
Alarm 2 Comm 4
NC 5
NO 6
Disable Comm 7
NO/NC 8
Figure 13
Wiring Diagram of Alarm Module
This manual suits for next models
1
Table of contents
Other Thermo orion Measuring Instrument manuals
Popular Measuring Instrument manuals by other brands
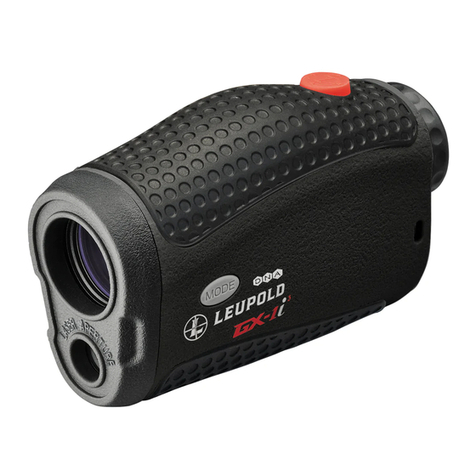
Leupold
Leupold GX-1i3 operating instructions
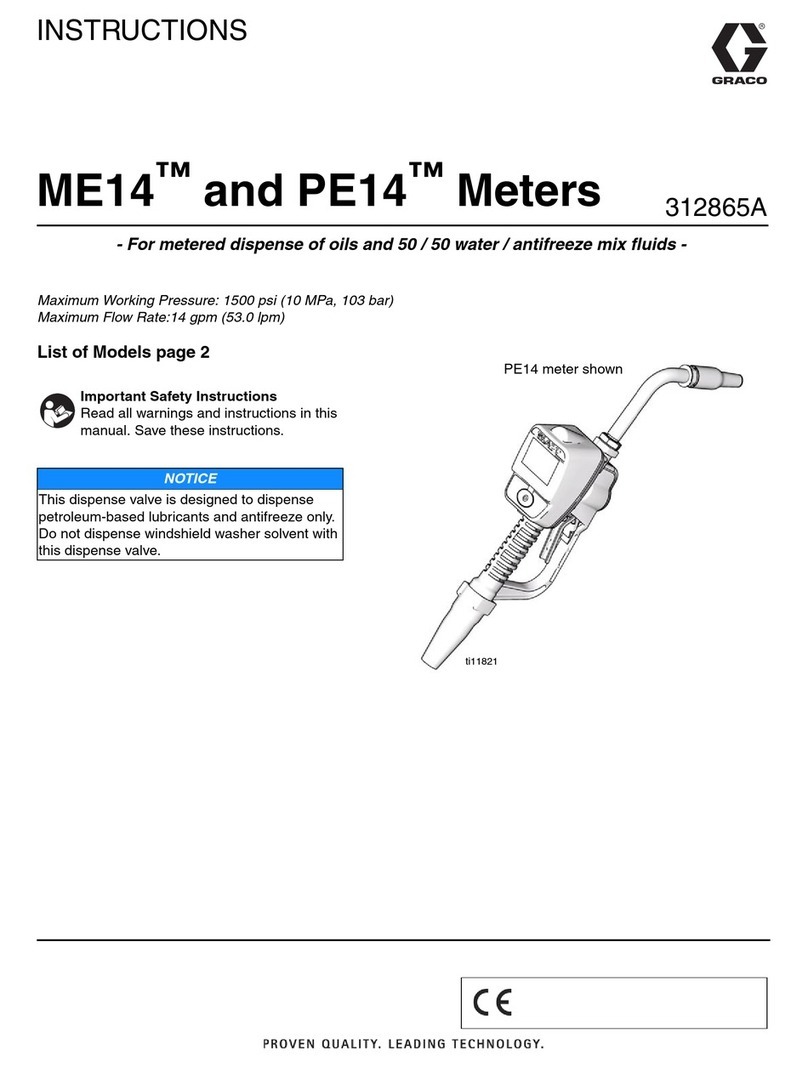
Graco
Graco PE14 instructions
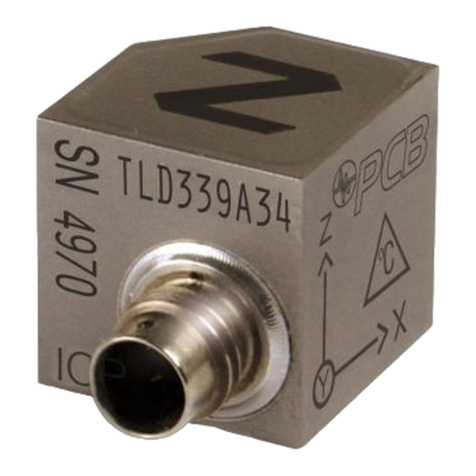
PCB Piezotronics
PCB Piezotronics TLD339A34 Installation and operating manual
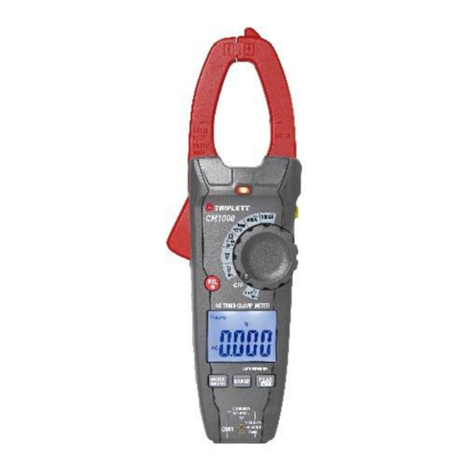
Triplett
Triplett CM1000 user manual
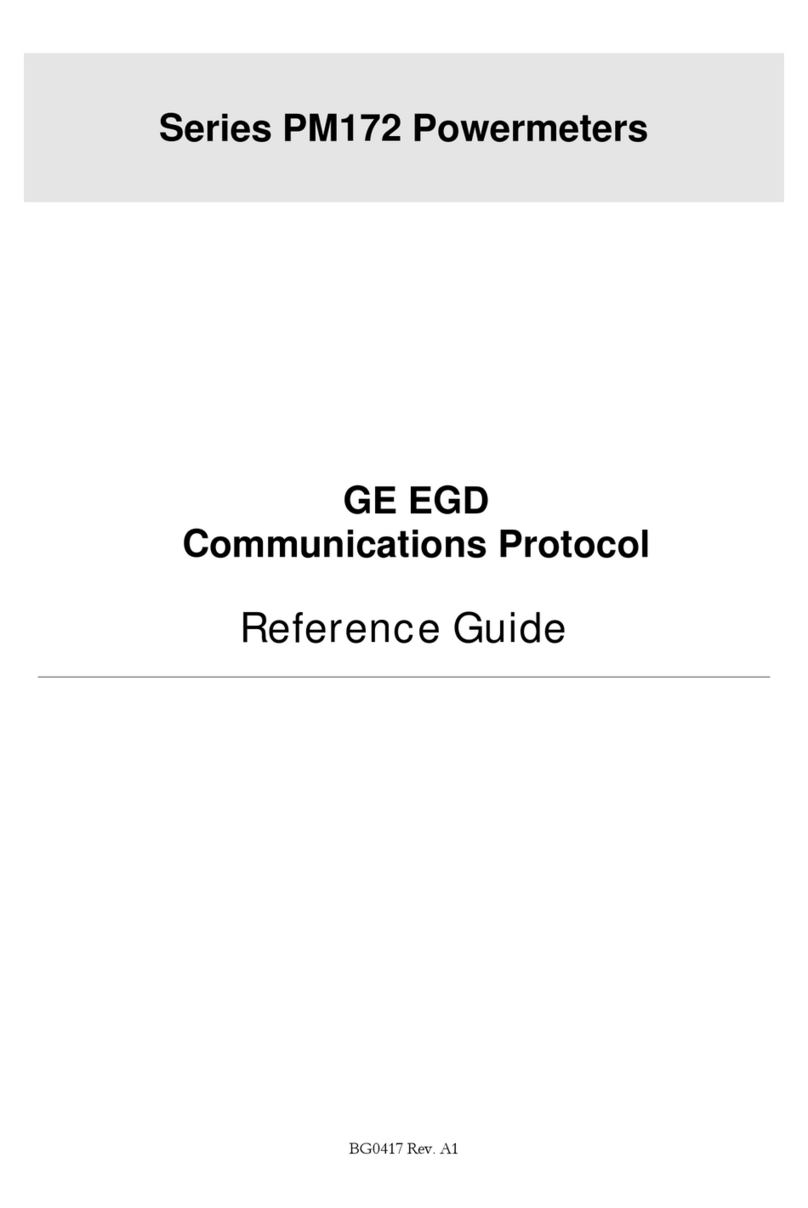
Satec
Satec PM172 Series reference guide
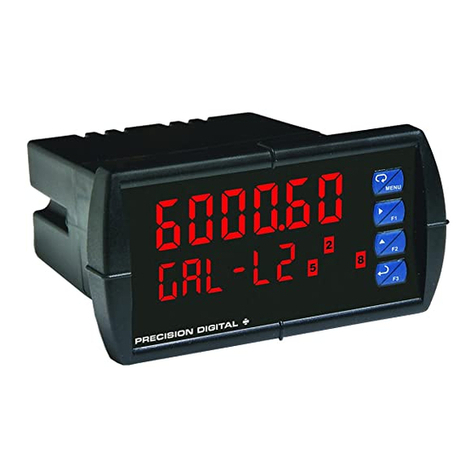
Precision Digital Corporation
Precision Digital Corporation PROVU Series manual