Toray TMR090 Series User manual

GIRE-097-2-2
Submerged Membrane Module
for MBR
TORAY “MEMBRAY”
"TMR090 Series"
Instruction Manual
Toray Industries, Inc.
Water Treatment Division
1-1, Nihonbashi-muromachi 2-chome, Chuo-ku, Tokyo 103-8666 Japan
Tel: +81-3-3245-4542
Fax: +81-3-3245-4913
URL: http://www.toraywater.com
Published: April 2013

GIRE-097-2-2
Content
I. INTRODUCTION ................................................................................................................................ 1
1. Features of MBR ................................................................................................................... 1
2. Outline of “TMR090 Series”................................................................................................... 2
II. FOR SAFE OPERATION OF “TMR090 Series”............................................................................ 6
1. Unpacking and Installation.................................................................................................... 6
2. Operation and Maintenance.................................................................................................. 7
3. Chemical Cleaning of Element .............................................................................................. 8
III. SPECIFICATIONS AND PERFORMANCE OF “TMR090 Series”............................................ 10
1. Specifications of Element.................................................................................................... 10
2. Specifications of Polyurethane Permeate Tube.................................................................. 10
3. Specifications and Performance of "TMR090 Series" Module............................................ 11
IV. MEMBRANE FILTRATION PROCESS DESIGN FOR “TMR090 SERIES”............................ 13
1. Standard Filtration Pattern .................................................................................................. 13
2. Flow Diagram of Membrane Filtration Process................................................................... 14
3. Layout of “TMR090 Series” Modules in Membrane Submerged Tank ............................... 19
4. Piping................................................................................................................................... 22
V. INSTALLATION OF “TMR090 SERIES”....................................................................................... 26
1. Preparatory Procedure ........................................................................................................ 26
2. Unloading/lifting Products.................................................................................................... 26
3. Checking Products .............................................................................................................. 27
4. Storage Products................................................................................................................. 27
5. Installation Products ............................................................................................................ 28
VI. START OF OPERATION ................................................................................................................ 30
1. Clean Water Operation........................................................................................................ 30
2. Seeding Sludge Injection..................................................................................................... 31
3. Actual Filtration Operation................................................................................................... 31
VII. OPERATION CONTROL .............................................................................................................. 33
1. Standard Operating Conditions........................................................................................... 33
2. Operating Parameters ......................................................................................................... 35
3. Basic Control Philosophy .................................................................................................... 36
4. Daily Inspection ................................................................................................................... 37
VIII. MAINTENANCE OF “TMR090 SERIES” ...................................................................................... 40
1. Maintenance Items and Maintenance Frequency............................................................... 40
2. Air Diffuser Cleaning............................................................................................................ 41
3. Chemical Cleaning of Element ............................................................................................ 42
4. Chemical Agents Used for Chemical Cleaning................................................................... 42
5. Handling of Chemical Agents.............................................................................................. 43

GIRE-097-2-2
6. Chemical Cleaning Procedure............................................................................................. 46
7. Lifting Procedure ................................................................................................................. 50
8. Replacement of Element Fixing Gaskets ............................................................................ 51
9. Element Replacement ......................................................................................................... 52
10. Air Diffuser Replacement................................................................................................. 54
11. Storage Products after Use ............................................................................................. 56
12. Disposing Procedure ....................................................................................................... 57
IX. REPLACEMENT PARTS LIST....................................................................................................... 58
X. TROUBLESHOOTING .................................................................................................................... 59
XI. APPENDIX ........................................................................................................................................ 60
Symbols used in this manual
This symbol is used to indicate an imminent hazardous situation
which, if not avoided, will result in serious injury or death.
This symbol is used to indicate a potentially hazardous situation
which, if not avoided, can result in serious injury or death.
This symbol is used to indicate a potentially hazardous situation
which, if not avoided, may result in injury or property damage.
DANGER
!
WARNING
!
CAUTION
!

GIRE-097-2-2
1
I. INTRODUCTION
“MEMBRAY” is a submerged membrane module suitable for the membrane bioreactor
system (MBR) that has been developed in Toray Industries, Inc based on the years of
experience of polymer science and the membrane technologies.
"TMR090 Series" is a lineup of "MEMBRAY", which is more compact compared to the other
"TMR140 Series", thus, suitable for the application where only a limited space is available,
such as for containerized package plants, domestic wastewater treatment, reclamation in
buildings or on marine boats application.
"TMR090 Series" is equipped with fine-bubble air diffusers, which significantly reduces the
daily cleaning operation of air diffusers and increases the oxygen dissolution efficiency.
This manual describes the specifications of "TMR090 Series", necessary peripheral
equipments and the safe and proper handling method of the module during installation,
operation and maintenance works.
Designer and operators should thoroughly read this manual to ensure stable operation.
1. Features of MBR
The process flow of the conventional activated sludge system (CAS) and MBR are shown in
Fig.I-1 and Fig.I-2, respectively.
MBR provides the following advantages:
(1) Small Footprint
Unlike CAS, MBR separates sludge within aeration tank using membranes, thus eliminate
Sedimentation Tank
Waste
water
Aeration Tank
Discharge
Waste
water
Discharge or Reuse
Reuse
RO
membrane
Submerged Membrane
Module
Membrane
Submerged
Tank
Fig. I-1 CAS Flow
Fig. I-2 MBR Flow

GIRE-097-2-2
2
the space for preparing sedimentation tank. Also with membrane, MBR can hold higher
concentration of activated sludge in the aeration tank, so its volume can be reduced. As a
result, MBR provides smaller footprint compared to CAS.
(2) High quality of treated water
MBR removes suspended solid (SS) from the sludge liquid with membrane much more
certainly than conventional sedimentation process. MBR also rejects microorganisms such
as Escherichia coli and Cryptosporidium efficiently.
2. Outline of “TMR090 Series”
“TMR090 Series” is the membrane module composed of the element block and the aeration
block. The element block contains a number of membrane elements set at equal clearance,
each of which has flat sheet membranes fixed on both sides of ABS panel. Each element is
connected via polyurethane tube to the permeated water manifold. The aeration block
consists of fine-bubble air diffusers to supply scouring air (see Fig.I-3). This module is used
submerged in sludge liquid. The following shows the features of “TMR090 Series”.
Aeration Block
Element Block
Permeated Water Manifold
Tube
Fine-bubble
A
ir Diffuser
Element
Element Fixing
Bracket
Fig. I-3 Appearance of "TMR090-050S"

GIRE-097-2-2
3
(1) Shape of Element
The membrane element is a flat sheet type as shown in Fig.I-4. At the normal filtration
operation, the sludge accumulated on the membrane surface is cleaned up effectively with
upward water stream generated with the scouring air supplied from the air diffusers installed
at the bottom side (Fig.I-5). This mechanism ensures stable filtration, since the membrane
does not easily admit of sludge adherence to its surface.In addition, shorter element (1059
mm) compared to "TMR140 Series" allows the use in the space with height limitation.
Fig. I-4 Structure of Element
Fig. I-5 Filtration Principle of Activated Sludge
Supporting panel
Permeated Water
Nozzle
Membrane
1059 mm
515 mm
Air Diffuser
Element
Supporting
panel
Membrane
Permeated
Water
Membrane
Air
Sludge
flock

GIRE-097-2-2
4
3.0 micron
3.0 micron
(2) Membrane Structure
The flat sheet membrane consists of PVDF (Polyvinylidene Fluoride) functional layer and the
base layer of PET (polyester) non-woven fabric. This structure gives the membrane superior
physical strength and high chemical resistance.
(3) Membrane Pore Size
Numerous small-size pores are distributed evenly over the membrane surface with a sharp
pore-size distribution. This structure gives outstanding high treated water quality and
excellent water permeability, making the membrane highly resistant to clogging (see Fig.I-6
and Fig.I-7) compared to other membranes. The average pore size is 0.08 micron meter.
Fig. I-6 Membrane Surface (photo)
Fig. I-7 Pore Size Distribution
Other
Membrane
Toray PVDF
Membrane
Pore Size (micron)
東レ
BF014
クボタ
0
0.5
1.0
1.5
0.2
0.4
0.6
0.8
PVDF
東レ
BF014
クボタ
0
Number of pore (10
12
/m
2
)
Toray PVDF Membrane
Other Membrane

GIRE-097-2-2
5
(4) Element replacement
Each element can be taken out from the modules separately for the inspection or the
replacement. In the case of the membrane damage, the filtration operation can be recovered
in a short time by replacing relevant elements one by one with spare ones.
(5) Fine-bubble Air Diffusers
"TMR090 Series" is equipped with fine-bubble air diffusers, which significantly reduces the
daily cleaning operation of air diffusers and additionally increase the oxygen dissolution
efficiency to 1.3-2.0 times as high as the coarse-bubble diffusers.

GIRE-097-2-2
6
II. FOR SAFE OPERATION OF “TMR090 Series”
Before using “TMR090 Series”, please thoroughly read this Instruction Manual and follow the
instructions described in this manual, especially the safety precautions shown below. The
details of each precaution are described in the relevant chapter.
1. Unpacking and Installation
When lifting “TMR090 Series” or its part, please attach chains or
slings to it and raise it straight upward calmly to prevent it from
shaking. Please never allow any person under lifted article.
Please use chains or slings compatible with lifting weight when
lifting "TMR090 Series" or its part.
When installing “TMR090 Series” module, please set up a foothold
in advance. Please never climb the module. Please use protective
equipment to ensure the safety of workers.
At transportation, storage and installation, please take appropriate
measures to protect "TMR090 Series" or its part from damage.
Please don't put any heavy objects on the module. Please take
care to protect the module from collision with other objects.
Please do not leave "TMR090 Series" for hours in the place where
the temperature is higher than 40 °C or in the place exposed to
direct sunlight.
Please take adequate measures to protect “TMR090 Series” from
sparks caused by welding, fusion cutting or grinding throughout the
entire process from installation work to operation startup.
Please protect “TMR090 Series” from freezing at any time.
Please don't pressurize the permeate side of "TMR090 Series".
Please install the screen with openings of 3.0 mm or under before
the membrane submerged tank. It is recommended to use the
mesh type screen. Overflow or waste carryover must be avoided at
any time.
DANGER
!
DANGER
!
DANGER
!
CAUTION
!
CAUTION
!
CAUTION
!
CAUTION
!
CAUTION
!
CAUTION
!

GIRE-097-2-2
7
2. Operation and Maintenance
Don't use the treated water for drinking.
Before discharging the treated water to the environment or reusing
it, make sure to analyze its quality and confirm that the water
quality meets the intended purpose.
Don't burn the membranes without appropriate facilities since
harmful Hydrogen fluoride (HF) gas is generated at burning.
When dispose membranes, please apply a service of a qualified
waste disposing company.
When the clean water operation, charging clean water to the
membrane submerged basin with the air discharge valve open to
release air from the elements. After charging water, close the air
discharge valve.
Don’t use the ground water, which contains considerable amount
of iron, manganese, calcium or silica, for the clean water operation
as it may cause the clogging of the membrane.
Don't continue the clean water operation unnecessarily. A
long-time filtration of clean water tends to cause the clogging.
Once the membrane gets wet, keep it wet. If the wet membrane is
dried up again, the permeability of the membrane might be
decreased seriously.
When feeding the seeding sludge, be sure to remove foreign
substances from it with the screen with openings of 5mm or under.
Don't do the filtration operation without supplying the scouring air in
a right way, or the membrane will be clogged severely.
Don't put in the activated sludge liquid chemicals, toxic agents, oils
or other substances that may adversely affect activated sludge.
WARNING
!
WARNING
!
WARNING
!
CAUTION
!
CAUTION
!
CAUTION
!
CAUTION
!
CAUTION
!
CAUTION
!
CAUTION
!

GIRE-097-2-2
8
Please avoid abrupt changes of operating conditions, especially
pH, temperature and the suction pressure of the membrane even
within the range of the standard operating conditions (Table VII-1).
Please replace the renewal parts periodically or when the
deterioration is detected at the inspection.
Prevent “TMR090 Series” from freezing at any time.
Please take care not to dry the membranes when taking "TMR090
Series" out of the liquid for the inspection or the maintenance. If
the wet membrane is dried up again, the permeability of the
membrane might be decreased seriously.
Please stop the scouring air when the filtration operation stops
except for the following conditions:
1) In case of applying intermittent filtration, do not stop the
scouring air for each relaxation period.
2) In case that the plant operation stops for a while, aeration is
applicable for mixing or aeration demand, however, the flow
rate should be controlled minimal.
Please don’t re-use the old permeate tubes once disconnected
from the nozzles since the connection tightness of the tubes are
reduced.
3. Chemical Cleaning of Element
The chemical agents used for the chemical cleaning are harmful to
the health. When handling chemical
s, please read their material
safety data sheet (MSDS) in advance and make sure to wear
necessary protectors such as protective goggles and protective
gloves.
If the chemical agents stick to your skin or clothes, immediately
wash it away with enough amount of running water.
If the chemical agents enter your eyes, immediately wash it away
with enough amount of running water and see the doctor.
WARNING
!
WARNING
!
CAUTIO
N
!
CAUTION
!
CAUTION
!
CAUTION
!
CAUTION
!
WARNING
!
CAUTION
!

GIRE-097-2-2
9
If any abnormality is found in the equipment during chemical
cleaning, immediately stop operation and check it.
If chemical is injected forcibly directly with the chemical feed pump
or by any other means, the internal pressure of the elements will
increase and the elements will get damaged. Be sure to inject
chemical with the pressure of lower than 10 kPa (100 mbar).
When injecting the chemical agents at the chemical cleaning,
please confirm beforehand that
the modules are completely
submerged in the liquid and the liquid level of the membrane
submerged tank is higher by more than 300 mm than the top of the
module.
Please store the chemical agents in a dark cold place free from
direct sunlight.
Please use the appropriate tank or the container, for storing the
chemical agent, made of the material having enough corrosion
resistance to each chemical agent.
Don't mix sodium hypochlorite with acids, including oxalic acid or
citric acid; otherwise toxic chlorine gas is generated.
Don't mix sodium hypochlorite with heavy metals.
Please stop the scouring air during the chemical cleaning, or the
membrane elements might be damaged.
WARNING
!
WARNING
!
WARNING
!
WARNING
!
CAUTION
!
WARNING
!
WARNING
!
CAUTION
!

GIRE-097-2-2
10
III. SPECIFICATIONS AND PERFORMANCE OF “TMR090 Series”
1. Specifications of Element
TableIII-1 and Fig.III-1 shows the specifications and the appearance of the element for
TMR090 Series, respectively.
Table III-1 Specifications of Element (TSP-50100)
Model name
TSP-50100
Membrane configuration Flat sheet
Application Filtration of activated sludge
Filtration method
Suction filtration
Nominal pore size (
µ
m)
0.08
Effective membrane area (m2)
0.9
Dimensions (mm)
Total width
515
Total height
1059
Thickness
13.5
Weight (kg)
Dry
3.0
Wet (Reference)
5.0
Main material
Membrane
PVDF and PET non-woven fabric
Supporting panel
ABS resin
Permeated water nozzle
Fig.III-1 Appearance of Element (unit: mm)
2. Specifications of Polyurethane Permeate Tube
Table III-2 shows the specifications of polyurethane permeate tube.
Table III-2 Specifications of Polyurethane Permeate Tube
Material
Thermoplastic polyether-polyurethane
TPU-ARET*
1
Inside diameter / outside diameter / total length (mm)
8/11/380
*Allowable temperature limit: 60 degree C
*1 The material name due to the ISO-18064.
105
9
51
5
9
0

GIRE-097-2-2
11
3. Specifications and Performance of "TMR090 Series" Module
Table III-3 shows the specifications of "TMR090 Series" modules.
EPDM is equipped as standard membrane material for the diffuser. EPDM has been used in
a lot of application for sewage treatment and industrial wastewater treatment and wears well.
However, EPDM is weak to oil and solvent. For wastewater containing high concentration of
oil and solvent, polyurethane is the preferable choice. We have the line-up of polyurethane
membrane diffuser-equipped TMR090 as an option. Please contact us if you have any
difficulties in choosing the type of diffuser.
Table III-3 Specifications of "TMR090 Series" Modules
Model name TMR090-050S TMR090-100S
Number of membrane elements
50
100
Element block structure 1 deck 1 row 1 deck 1 row
Dimensions
*1
Width (mm)
730
730
Length (mm)
990
1720
Height (mm) 1470 1470
Weight(kg
)
Module (dry)
(Aeration block + Element
block)
265 460
Module (wet)
(Maximum weight in case of
sludge clogging)
*2
475 885
Material
Permeate water manifold
304 stainless steel
(316LSS as option)
Housing
304SS/ABS resin
(316LSS as option)
Diffuser
EPDM rubber/PVC/304SS
(316LSS as option)
Element fixing gaskets
EPDM rubber
Operating
Range
Temperature (degree C)
not higher than 40
pH*4 of liquid
5-10
MLSS (mg/L)
not higher than 18,000
Trans-membrane pressure
(kPa )
not higher than 20 (200 mbar)
Cleaning chemicals feed
pressure (kPa )
not higher than 10 (100 mbar)
Scouring Air Flow rate
(NL/min/Module)
*6
500-650 1,000-1,300
Connection
s
Manifolds: Flanges*3
ANSI 1 1/2 inch
ANSI 2 inch
Air diffusers : Screws
NTP 1 1/2 (one side)
NTP 1 1/2 (both sides)
*1 The total dimensions excluding the connection tube
*2 The weight assumed in the case of sludge clogging between elements.
*3 The flange dimensions are described in the drawings attached to this manual. UNI (ISO) flange is also
available as option.

GIRE-097-2-2
12
*4 Except when the chemical cleaning with the designated chemical agents.
*5 The connecting socket has an internal thread. The use of tapered screw is recommended for screw
connections.
*6 “NL” means air volume as being 0 degree C and 101.325 kPa (1 atm).
Table III-4 and III-5 show the performance of "TMR090 Series" modules.
Table III-4 Permeate water quality
Model name TMR090-050S TMR090-100S
Permeate
water
quality
*1
TSS (mg/L) *2 Not higher than 3.0
Turbidity (NTU) *3
Not higher than 1.0
*1 This value is a guarantee value of Toray that can be attained when the modules are installed and
operated appropriate under the standard conditions as specified in this Instruction Manual and
Operation and Maintenance Guideline during a period specified separately by Toray.
*2 Measuring method of TSS is complied with Standard Method of Examination of Water and Wastewater
20th Edition (1998), Section 2540D, Total Suspended Solids Dried at 103-105 degree C or ISO 11923.
*3 Measuring method of NTU is complied with Standard Method of Examination of Water and Wastewater
20th Edition (1998), Section 2130, Turbidity or ISO 7027.
Table III-5 Flow capacity (Reference value)
Model name TMR090-050S TMR090-100S
Continuous
Filtration Flow
(m
3
/d)
Sewage 5 - 35 10 - 70
Industrial wastewater
5 - 23
10 - 46
*4 This value is just a reference value and is not a guarantee value of Toray. Sustainable operating
filtration flow capacity varies among the plant depending on the type of wastewater, total process
design and operating condition. In case of industrial wastewater application, it is strongly recommended
to conduct a pilot test before membrane tank designing.

GIRE-097-2-2
13
IV. MEMBRANE FILTRATION PROCESS DESIGN FOR “TMR090 SERIES”
The standard filtration pattern time chart, the schematic flow diagram of the membrane
filtration, the layout of “TMR090 Series” modules in the membrane submerged tank, and the
piping procedures are described in this section. These would help you design the membrane
filtration process with “TMR090 Series”.
1. Standard Filtration Pattern
Two kinds of the filtration patterns are available with "TMR090 Series". Usually intermittent
filtration (filtration with relaxation) is adopted and details are shown below, whereas
sometimes simple continuous filtration can also be applied. In both cases aeration shall be
done continuously while filtrating.
In the case of the intermittent filtration, the filtration is suspended (“relaxed”) for a short
period at certain intervals while the scouring air continues, as shown in Fig. IV-1. While the
filtration is suspended, the membrane surface is cleaned up more effectively with the
scouring air due to the absence of suction. Although the automatic system control for
periodical start and stop of the filtration is required, the intermittent filtration is recommended
for stable and efficient membrane filtration. The recommended time cycle for the intermittent
filtration is 9-minute filtration and 1-minute relaxation.
Please stop the scouring air when the filtration operation stops except for the following
conditions:
1) Each relaxation period in case of applying intermittent filtration.
2) In case that the plant operation stops for a while, aeration is applicable for mixing or
aeration demand, however, the flow rate should be controlled minimal.
Fig.IV-1 Recommended Time Cycle for Intermittent Filtration
Filtration
Air diffusion
Continuous
Filtration: 9 min.
Relaxation: 1 min.
Cycle of 10 minutes
F1: Average flow rate for treatment capacity
and membrane area calculation
F2: Filtration flow rate for suction pump
capacity calculation
F1
F2

GIRE-097-2-2
14
Membrane Module
FIC
FI
L
H
L:CLOSE
H:OPEN
L:OPEN
H:CLOSE
Permeate water outlet
Manifold
Lower
Limit alarm
Air Outlet
Feed
Chemical
Air Diffuser
Membrane
Submerged
Tank
PIA
PIA
“U-shape”
2. Flow Diagram of Membrane Filtration Process
Two schematic flow diagrams of the membrane filtration process are shown below. One is for
the gravity filtration with water head difference and the other is with suction pump. Major
necessary peripheral devices for membrane filtration process are described in the latter part
of this section.
In any cases, the fine screen with openings of 3.0 mm or under should be installed before the
membrane submerged tank, or the modulesmight be polluted and clogged severely with
trashes brought with the raw water.
It is also recommended to prepare enough capacity of the buffer tank (flow equalization tank)
prior to the MBR process to equalize BOD load and filtration flow capacity so as to enable
stable operation of the biological treatment and membrane filtration process.
(1) Gravity filtration configuration
The filtration can be performed with using a natural water head differential pressure
generated from a vertical distance between the liquid level of the membrane submerged
tank and the level of the permeate water outlet (see Fig. IV-2).
Fig. IV-2 Schematic Flow Diagram for Gravity Filtration
LS
Wastewater
Fine Screen
FIC: Flow
Rate Indicator/Controller
L
S : Level Switch
PIA: Pressure
Indicator/Alarm
FI : Flow Meter

GIRE-097-2-2
15
In order to obtain enough suction pressure for the filtration considering the friction loss of
pipe and valves, the permeate water outlet should be located sufficiently below the liquid
level of the membrane submerged tank (normally 3 m below water level or lower).
It is recommended that the piping from the permeate water manifold to the permeate water
outlet should directly penetrate the tank wall, as shown in Fig.IV-2. Also if the permeate
water outlet is located in the open air, it is also recommended to make the pipe just before
the permeate water outlet U-shape to seal the piping with water.
The permeate water flow is controlled with the automatic control valve (the permeate control
valve). When the liquid level of the membrane submerged tank gets to the lower limit, this
control valve fully closes the permeate water line to stop the filtration. When the liquid level
gets to the higher limit, the automatic shutter valve on the raw water feed line closes its line
to stop raw water coming.
In this gravity filtration, the air accumulated in the permeate water line should be discharged once
a day at least; otherwise the effective water head is reduced seriously. The air purge nozzle
should be installed at the highest position of the permeate water line and the automatic shutter
valve (the air purge valve) is recommended to be installed on the line just before the nozzle. (As
shown in Fig.IV-2) Stopping the filtration (fully closing the permeate control valve) and opening
the air purge valve for a few minutes, the air is easily purged.

GIRE-097-2-2
16
Membrane Module
Air diffuser
FIC
Permeate water
Manifold
PIA
Lower
limit alarm
Air outlet
Feed
chemical
FI
L
H
L:OPEN
H:CLOSE
L:CLOSE
H:OPEN
VFD or auto valve
PIA
(2) Pump suction configuration
Figure Fig. IV-3 illustrates the general configuration for pump suction filtration.
Fig.IV-3 Schematic Flow Diagram for Pump Suction Operation
The permeate water flow is controlled by a flow meter and a suction pump with an automatic
control valve or by a flow meter and a suction pump with VFD control. In case water level in
the membrane submerged basin gets to the lower limit, filtration has to be stopped. If the
water level reaches the upper limit, the level controller will stop raw water inflow.
In some cases with this pump suction configuration, an equipment may be needed to
discharge the air accumulated in the permeate water line. A range of methods can be applied
for this air removal such as vacuum pump, ejector or manual water injection. Please contact
TORAY or refer to the engineering manual for the details.
(3) Necessary devices for membrane filtration process
Major necessary peripheral devices to operate membrane filtration process are explained
below. Some other devices than mentioned below might be required case by case.
Raw water
Fine screen
FIC : Flow rate indicator/
Controller
LS : Level Switch
PIA : Pressure indicator/
Alarm
FI : Flow indicator
LS

GIRE-097-2-2
17
PIA
a mm
P1
P2
PIA
b mm
a. Fine screen
The wastewater should be treated by screen with openings of 3.0 mm or under
before flowing into the membrane submerged tank, otherwise the modules are
polluted and clogged with foreign substances seriously. It is recommended to use
the mesh type screen. Overflow or waste carryover must be avoided at any time.
b. Flow control device
A flow rate controller, a flow meter combined with an automatic control valve, or a
flow meter combined with VFD controlled suction pump should be installed on the
permeate water line to control the flow rate of permeate water. In the case of
operating a number of “TMR090 Series” modules simultaneously in one train, it is
advised to install one flow rate controller for one train of the modules.
c. Differential pressure measuring instrument
For trans-membrane pressure (TMP) determination the differential pressure (in the
permeate line and water level) has to be measured and calculated, either by
installing two pressure sensors and calculating the readings in the PLC or by using a
differential pressure device.
In the former case, one pressure gauge should be installed on the permeate water
line and the other one in the membrane submerged tank, to monitor the
trans-membrane pressure. In case of operating a number of “TMR090 Series”
modules simultaneously in one train, it is advised to install one differential pressure
measuring instrument for one train of the modules.
[Example]
Fig.IV-4 Differential Pressure Measurement & Calculation
This manual suits for next models
2
Table of contents
Other Toray Control Unit manuals
Popular Control Unit manuals by other brands
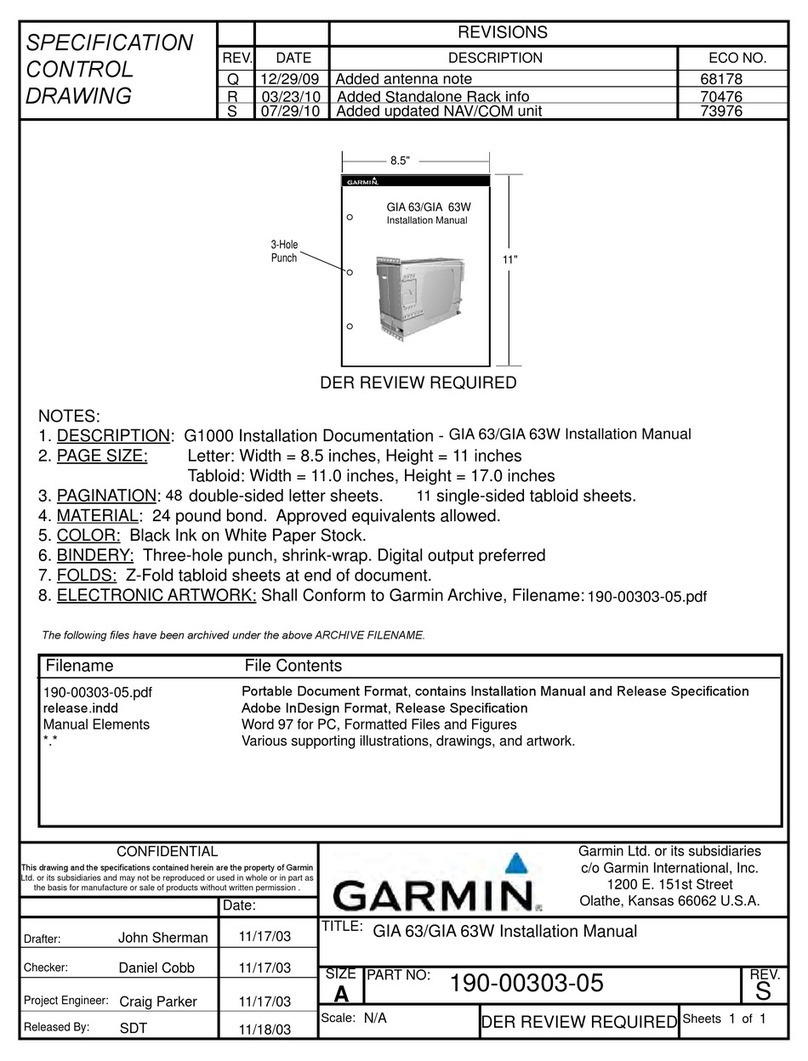
Garmin
Garmin GIA 63W installation manual
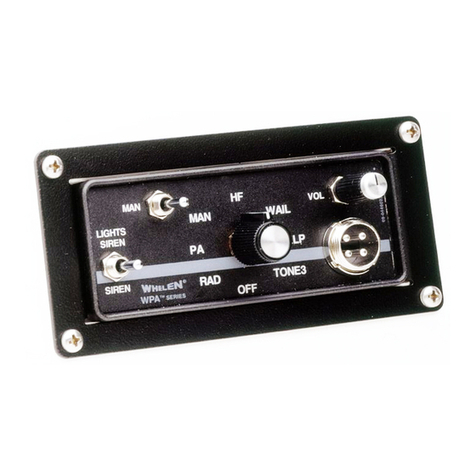
Whelen Engineering Company
Whelen Engineering Company WPA Series installation guide
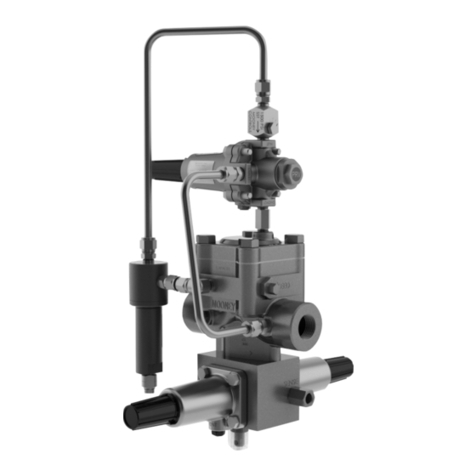
Baker Hughes
Baker Hughes Mooney Flowgrid Slam Shut instruction manual
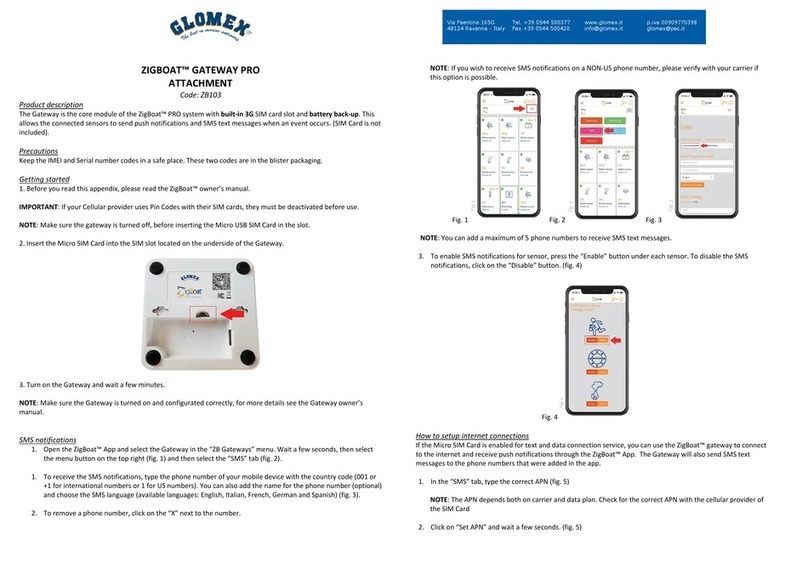
Glomex
Glomex Zigboat Gateway Pro quick start guide

Sony
Sony RYZ-CU164 operating instructions
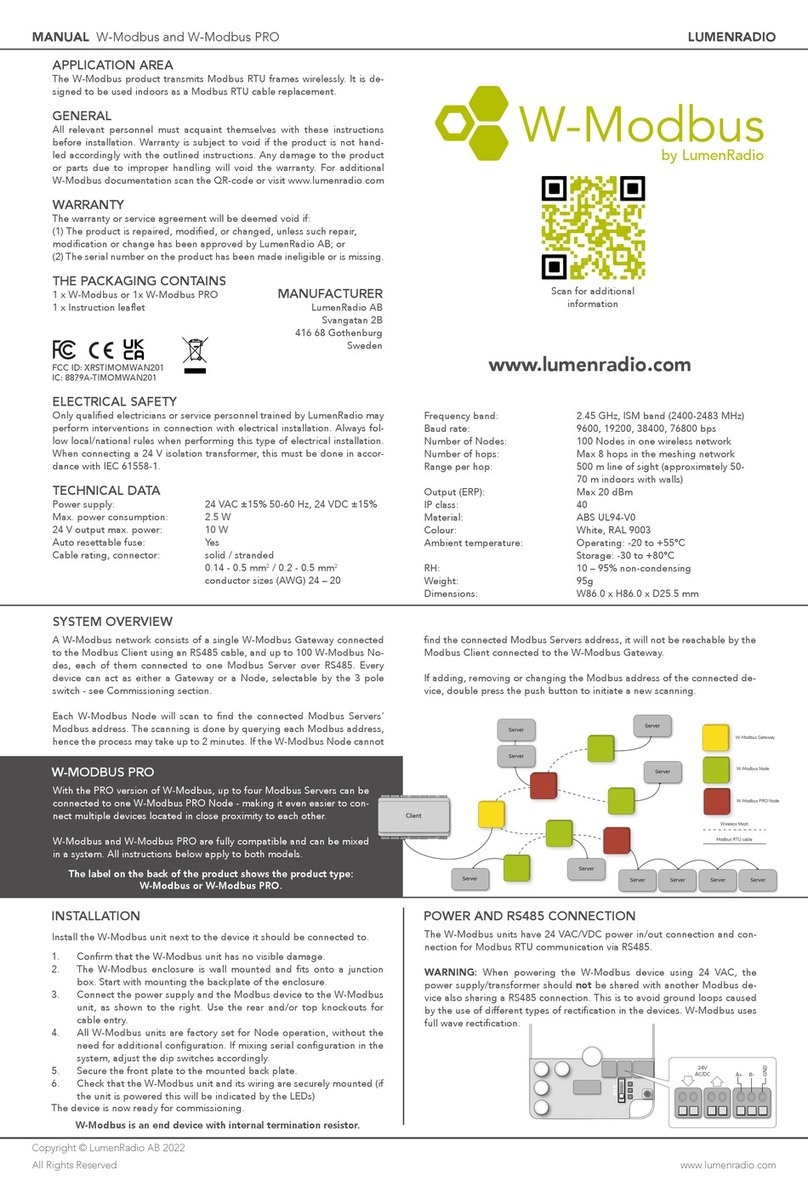
LumenRadio
LumenRadio W-Modbus manual
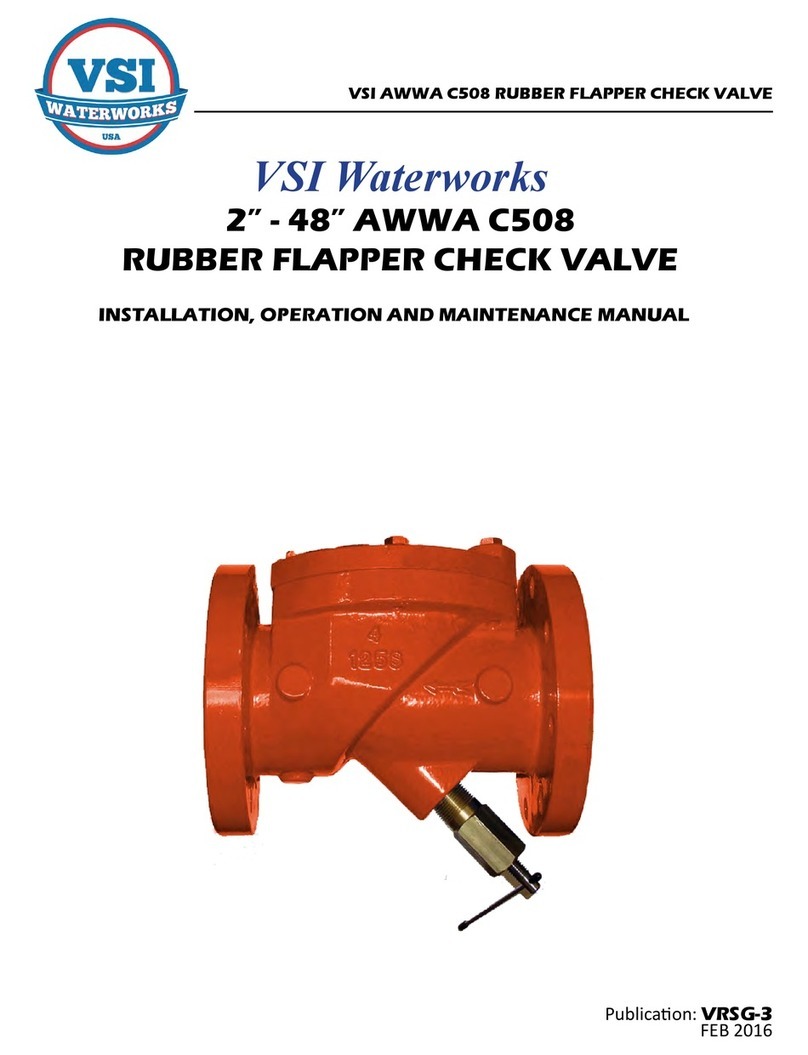
VSI
VSI AWWA C508 Series Installation, operation and maintenance
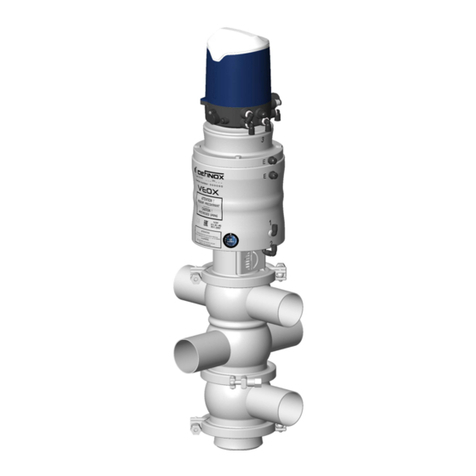
Definox
Definox VEOX SP 3 BODY Maintenance notice
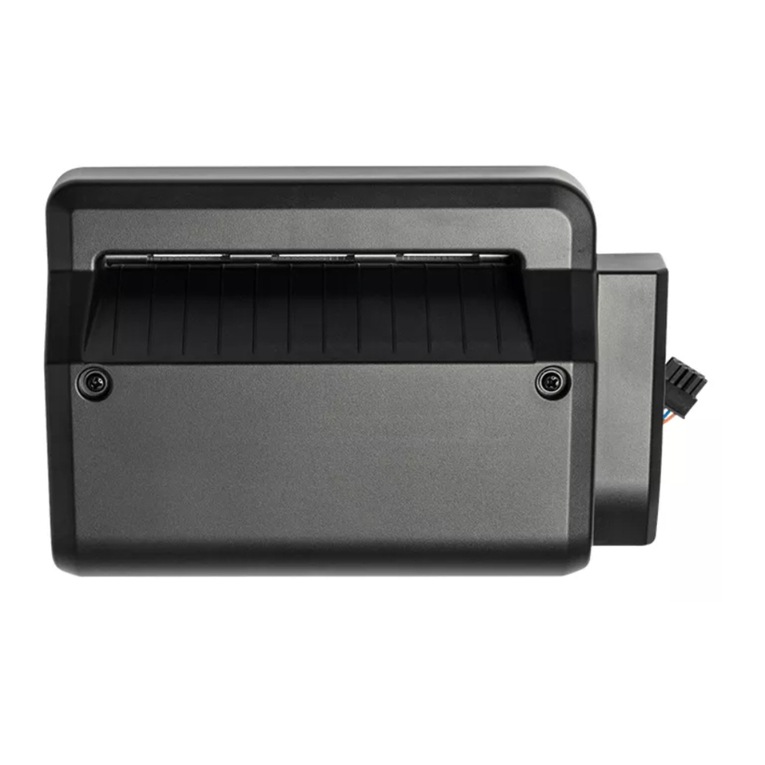
Brother
Brother PA-CU-005 Setup guide

uhlmann & zacher
uhlmann & zacher CX8936 user manual
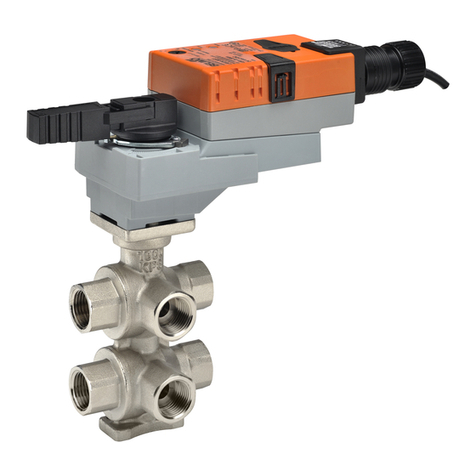
Belimo
Belimo 6-Way ePIV Installation instruction
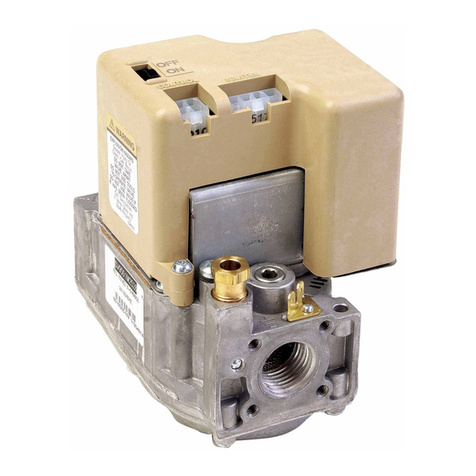
resideo
resideo SmartValve SV9401 installation instructions