Total Control Systems 700-20 Installation and operation manual

Toll: +1 (800) 348-4753
Tele: +1 (260) 484-0382
Fax: +1 (260) 484-9230
www.tcsmeters.com
© Total Control Systems 2007
Fort Wayne, Indiana U. S. A.
ENGINEERING MANUAL
700 SERIES ROTARY FLOW METER

- 1 -
TABLE OF CONTENTS
Page No.
Table of Contents
1
Quote and Purchase Specifications
2
Rotary Design
3
Meter Type Classification
4
Meter Selection Factors
Metrology
5
Accuracy
6
Material Compatibility
6
Flow Rate
6
Pressure
6
Temperature
7
Lubricity
7
Suspension and Suspended Solids
7
Foreign Materials
8
PH
8
Viscosity
8
Pressure Loss
9
Bearing Load
10
System Design
Plumbing Figuration
10
Slow Flooding of System
11
Protection From Debris
11
Calibration
11
Drum Filling System
12
Mobile Fueling System
13
Hydraulic Shock
14
Thermal Expansion
14
Thermal Shock
14
Products that Dry/Congeal/Crystallize
14
LPG
14
Meter Calibration
16 - 18
Product Depletion (Split Compartment)
18 - 20
Calibration Procedure
21
Direction of Flow
22
700 Series Materials of Construction
23
Chemical Compatibility
23 - 35
Metric Conversion Guide
36
Registration Specifications
Gear Plate Information
37
Pulse Output
38
Approximate Weights
39
Glossary
40 - 42
Material Safety Data Sheet (MSDS) for Calibration Fluid
43 - 46

- 2 -
QUOTE & PURCHASE SPECIFICATIONS
When issuing quote and purchase specifications and to assure you of receiving a Total Control
Systems meter with all of the many performance, installation, operating, and maintenance
advantages available only with a TCS meter. We suggest that 700 series meter-engineering
specifications include the following statements in addition to a TCS model number and
description.
“Meter shall be of a flow meter with a positive displacement design having rotary motion
without axial thrust or flow disruption. No eccentric, sliding, reciprocating or oscillating parts to
induce excess liquid shear or liquid compressibility within meter element. Meter shall have three
rotors that rotate in unison within the measuring chamber. Rotary parts to be horizontally
supported on both sides by solid support bearings and rotor journals of materials compatible with
product to be metered. Meter shall have stainless steel timing gears with no ball bearings, springs,
or cams. Rotary drive and meter adjustment output to all mechanical readout shall be capable of
infinite meter accuracy adjustment of 0.02% or better. Meter calibration adjustment device must
be externally accessible not requiring removal of any readout equipment for calibration or
replacement. Meter shall immediately respond to product low flow movement.”
NOTICE
Total Control Systems (TCS) shall not be liable for technical or editorial errors in this manual or
omissions from this manual. TCS makes no warranties, express or implied, including the
implied warranties of merchantability and fitness for a particular purpose with respect to this
manual and, in no event, shall TCS be liable for special or consequential damages including, but
not limited to, loss of production, loss of profits, etc.
The contents of this publication are presented for informational purposes only, and while every
effort has been made to ensure their accuracy, they are not to be construed as warranties or
guarantees, expressed or implied, regarding the products or services described herein or their use
or applicability. We reserve the right to modify or improve the designs or specifications of such
products at any time.
TCS does not assume responsibility for the selection, use or maintenance of any product.
Responsibility for proper selection, use and maintenance of any TCS product remains solely with
the purchaser and end-user.
All rights reserved. No part of this work may be reproduced or copied in any form or by any
means –graphic, electronic or mechanical –without first receiving the written permission of
Total Control Systems, Fort Wayne, Indiana USA.

- 3 -
DESIGN
The TCS Model 700 series flow meter is a simple
and efficient design. The meter consists of a single
fluid chamber that contains a single blocking rotor
and two displacement rotors whose rotation is
synchronized with mating gears. As the fluid
enters the fluid chamber, the blocking rotor is
forced to rotate. The displacement rotors, also
rotating in conjunction with the blocking rotor help
direct the fluid flow through the chamber and to the
outlet. The linear flow of the fluid is thus
translated into rotary motion in the meter. The
output of the meter is picked up from the rotation
of the blocking rotor and transmitted to a register or
pulse transmitter.
The rotors in the meter are designed to operate at close tolerances to one another and the wall of
the fluid chamber. There are slight gaps between the rotors and the chamber wall. Because of
this, it is important that the meter be properly applied for the flow rate and operating pressure of
the system.
Because the fluid flowing through the meter is redirected only slightly from its natural flow,
there is very little pressure drop across the meter, unlike other meters that use multiple measuring
chambers.
The meter design uses high quality long life materials for the rotor bearings and journals. Since
there is no contact between the rotors and the fluid chamber wall, these critical components have
a long life expectancy.
Calibration of the meter involves adjusting the rotation of the output shaft relative to the rotation
of the internal rotors of the meter. This is accomplished by changing the settings on an adjuster
device. Calibration of the meter is discussed in detail in the section Meter Calibration.
700 METER FLOW ILLUSTRATION

- 4 -
METER TYPES
SP STANDARD PETROLEUM
For metering refined petroleum products such as Leaded and Unleaded Gasoline, Fuel Oils,
Diesel, Bio-Diesel, Kerosene, Vegetable Oils, Motor Oils, Ethylene Glycol (Antifreeze), etc.
SPA STANDARD PETROLEUM (AVIATION)
For metering refined petroleum products such as Aviation Gasoline, Jet Fuels, Gasoline, Fuel
Oils, Diesel, Bio-Diesel, Kerosene, Motor Oils, etc.
SPD STANDARD PETROLEUM (DUCTILE IRON)
For metering alternative fuels such as Natural Gasoline, Ethanol, Methanol, Bio-Diesel, Aviation
Gasoline, Fuel Oils, Diesel, Motor Oils, etc.
LP LIQUEFIED PETROLEUM
For metering Liquefied Petroleum Gas (LPG).
IP INDUSTRIAL PRODUCTS
For metering Food Products, Industrial Products, General Solvents and many other liquids; such
as Liquid Sugars, Corn Syrup, Soy Bean Oil, Shortenings, Latex Products, Adhesives, etc.
IC INDUSTRIAL PRODUCTS WITH CARBON BEARINGS
For metering Industrial Chemicals, General Solvents, Water and other Non-lubricating Liquids,
such as Alcohol, Acetones, Ethanol, Naphtha, Xylene, MEK, Toluene, Deionized Water,
Demineralized Water, Potable Water, etc.
AF ALL FERROUS
For metering Pesticides, Nitrogen Solutions, Fertilizer, Chlorinated Solvents, Paints, Inks,
Alcohols, Adhesives, Motor Oils, Molasses, Corn Syrup, Liquid Sugars, etc.
SS STAINLESS STEEL
For metering the same liquids as the SP, SPA, SPD, IP, IC and AF flow meters, but includes
food processing and special handling fluids such as Nitric, Phosphorus and Glacial Acetic Acids,
Anti-Icing Fluids, Vinegar, Fruit Juices, etc.

- 5 -
METER OPERATING SPECIFICATIONS
Meter
Type
Available
Flange
Connection*
Maximum
Capacity
Working
Pressure
Working
Temperature**
700-15
SP, SPA,
IP & IC
1½”NPT Flange;
2” optional
60 GPM
(227 LPM)
150 PSI
(10.5 BAR)
-40°F to 160°F
(-40°C to 71°C)
700-20
SP, SPA,
SPD, IP, IC,
AF & SS
2” NPT Flange;
1½”optional
100 GPM
(380 LPM)
150 PSI
(10.5 BAR)
-40°F to 160°F
(-40°C to 71°C)
700-20
LP
2” NPT Flange;
1½”optional
100 GPM
(380 LPM)
350 PSI
(24.1 BAR)
-30°F to 140°F
(-30°C to 60°C)
700-25
SPA, SPD
2” NPT Flange
150 GPM
(567 LPM)
150 PSI
(10.5 BAR)
-40°F to 160°F
(-40°C to 71°C)
700-30
SP, SPA,
SPD, IP, IC
& AF
3” NPT Flange
2”optional
200 GPM
(760 LPM)
150 PSI
(10.5 BAR)
-40°F to 160°F
(-40°C to 71°C)
700-35
SPA, SPD
3” NPT Flange
300 GPM
(1135 LPM)
150 PSI
(10.5 BAR)
-40°F to 160°F
(-40°C to 71°C)
700-40
SP, SPA,
SPD, IP, IC
& AF
4” NPT Flange;
3” optional
500 GPM
(1893 LPM)
150 PSI
(10.5 BAR)
-40°F to 160°F
(-40°C to 71°C)
700-45
SPA, SPD
4” NPT Flange
600 GPM
(2271 LPM)
150 PSI
(10.5 BAR)
-40°F to 160°F
(-40°C to 71°C)
* Flanged NPT is Standard; BSPT, Slip Weld, ANSI and others are available upon request.
** Higher working temperatures can be achieved at reduced pressures (consult factory for more information)
METER SELECTION FACTORS
WEIGHTS&MEASURES
Before any meter can be specified, knowledge of each application is required. If the liquid is to
be sold through a metered delivery, domestic or international certification from a governing body
may be required. Total Control Systems strictly adheres to all domestic and international
metrology conformance regulations for the custody transfer of fluids. For questions regarding
weights and measures approvals or other issues, please consult factory.

-6 -
TYPICAL ACCURACY CURVE
-0.4
-0.2
0
0.2
0.4
010 20 30 40 50 60 70 80 90 100
PERCENT OF FLOW RATE
% DEVIATION
Gasoline
Fuel Oil
The 700-meter’s accuracy (percent of error over or under the zero – error level) remains within
design parameters (+/- 0.15%) over its minimum rated flow range to its maximum rated flow
range for custody transfer meter requirements. This percentage meets or exceeds the Wholesale
and Vehicle accuracy requirements for accurate custody transfer of product, as specified in the
National Institute of Standards and Technology (NIST) Handbook 44.
PRODUCT CHARACTERISTICS
A) Material Compatibility
The product intended to be measured must review Total Control Systems CHEMICAL
COMPATIBILITY on page 23 to 35 to find the suitable materials and meter type. Materials
incompatible with product will potentially reduce accuracy, operation life, contaminate liquid
and may be harmful to others.
B). Flow Rate
The minimum and maximum system rate of flow must be determined for the selection of
flow meter. The flow rate of the system is dependent upon the product viscosity; the desired
meter configuration, the systems pump capabilities, and the plumbing configuration.
C) Pressure
The maximum working pressure allowed should be reviewed under flow meter type and
pressure rating. All meters meet the European Pressure Equipment Directive (PED) No.
97/23/EC. Failure to adhere to the maximum allowable pressure may potentially cause a seal
leak or casting rupture.

- 7 -
D) Temperature
The operating temperature has a great effect on the meter seals and its relationship to the
maximum pressure allowed with the flow meter castings. It will be necessary to reduce the
maximum rated working pressure as the operating temperature increases. Any metering
system operating over 160F (71C) will require extra clearance rotors to compensate for
material expansion. Any metering system operating over 180F (82 C) will require at least a
one (1) foot registration extension to protect the registration devices. Increase in temperature
may increase the corrosion rate of some products.
1) O-ring / Packing Seal Temperature Rating
UL Buna -20F to 140F -30C to 60C
UL Viton -104F to 221F -75C to 105C
Viton -31F to 400F -35C to 204C
Simriz -40F to 450F -10C to 230C
Teflon -20F to 500F -30C to 260C
The Acetyl Face Gear and Bushings, in the register support assembly;
maximum temperature is 180F (82C)
2) Pressure rating at elevated temperatures.
Meter Type
SP/SPA/SPD/IP/IC/AF/SS
LP
150F/150PSI
150F/350PSI
200F/100PSI
200F/275PSI
250F/75PSI
250F/250PSI
300F/50PSI
300F/150PSI
E) Lubricity
The lubricity or non-lubricity of the product will determine the bearing sleeve material
suitable for use. Products with no lubrication will require the use of Carbon Graphite or
Ceramic bearing sleeves. Products with lubrication will reduce friction between two metal
surfaces and help dissipate heat.
F) Suspensions & Suspended Solids
Products with a low percentage of soft suspensions or suspended solids will require clearance
rotors and/or Ceramic bearing sleeves to protect the meter from its abrasive effects. High
percentages (5%) of suspensions or suspended solids, or any hard solids, such as sand, are
not recommended for the 700 series meter. Due to the very tight machining tolerances any
solid, larger than the thickness of a piece of paper, has the potential of stopping the flow
through the meter and can cause damage to the meter.

- 8 -
G) Foreign Materials
Products that are to be measured may have foreign materials present. The inlet side of any
positive displacement meter should be equipped with a strainer. Matching the strainer size or
one size larger, with an appropriate size screen will protect the meter and accessories from
damage in the system. A minimum of 40-mesh screen is recommended for petroleum service.
H) pH
The metal resistance to the effects of high or low
PH is difficult to calculate because of the varying
concentrations and corrosiveness of properties.
This is a generalized rating for pH resistance.
pH SCALE
NEUTRAL
0
1
2
3
4
5
6
8
9
10
11
12
13
14
◄——— ACID REACTION ———
——— ALKALINE REACTION ——►
7
I) Viscosity
Viscosity is the property of a fluid that is a measure of its resistance to flow. Among the
earliest to express this quantitatively was Sir Isaac Newton. He reasoned that the viscosity of
a liquid was proportional to its shear stress (or resistance to shear). Liquids that behave in
this manner are referred to as “Newtonian” liquids and are typically by petroleum fluids,
water and similar chemicals.
Other types of fluids are grouped into a general category called “Non-Newtonian” which
includes dilatants, plastic, pseudoplastic and thixotropic. Liquids in this group are
characterized by viscosity that changes with the rate of shear as compared to the Non-
Newtonian fluids where viscosity is basically constant with shear and flow rate. As a
consequence, Newtonian fluids are much easier to predict with regard to their performance
through a flow meter than are the Non-Newtonian liquids.
Many of the more viscous liquids pumped through the 700 series rotary flow meter are
plastic and pseudoplastic and as such are reduced in effective viscosity after being pre-
sheared by the pump. The diagram below shows how viscosity varies as a function of shear
rate on various types of liquids.
1) Thixotropic Liquids (Plastic and Peudoplastic)
Viscosity decreases as shear rate increases. Typical liquids include
Gels, Latex paints, lotions, Shortening, Mayonnaise, Printers Ink, Hand
cleaner and Yeast.
2) Newtonian Liquids –Viscosity remains unchanged with shear.
3) Dilatants Liquids –Viscosity increases as shear rate increases. Most
liquids in this category are unsuitable with PD flow meters; these
include Clay, Slurries and some confectionary bases.
Material pH
Aluminum 5 –8
Ductile Iron 5.5 –11
Ni-Resist 5.5 –14
Stainless Steel 0 –14

- 9 -
J) Pressure Loss
The pressure drop is the difference between of the inlet and outlet pressure of the flow meter
while operating. When measuring a liquid, the pressure drop will increase as the flow rate
increases. When the metering system has accessories such as an air eliminator or valve,
these items will be approximately the same pressure drop through equivalent size meter.
PRESSURE DROP CURVE
32 SSU SOLVENT
0
0.5
1
1.5
2
2.5
3
010 20 30 40 50 60 70 80 90 100
PERCENT OF FLOW RATE
P.S.I.
EXAMPLE:
A 700-20SP flow meter, air eliminator, strainer and preset valve. Operating at 80 GPM on a
2000 SSU lubricating oil.
Flow Meter: 1.5 PSI x 4.0 = 6 PSI Pressure Loss
Air Eliminator/Strainer: 1.5 PSI x 4.0 = 6 PSI Pressure Loss
Preset Valve: 1.5 PSI x 4.0 = 6 PSI Pressure Loss
Total Pressure Loss is 18 PSI
VISCOSITY CONVERSION
(Specific Gravity = 1)
SSU
SSU
SSU
SSU
CPS
Saybolt
CPS
Saybolt
CPS
Saybolt
CPS
Saybolt
Centipoise
Universal
Centipoise
Universal
Centipoise
Universal
Centipoise
Universal
1
31
200
1,000
900
4,300
7,000
32,500
2
34
220
1,100
1,000
4,600
8,000
37,000
4
38
240
1,200
1,200
5,620
8,500
39,500
7
47
260
1,280
1,300
6,100
9,000
41,080
10
60
280
1,380
1,400
6,480
9,500
43,000
15
80
300
1,475
1,500
7,000
10,000
46,500
20
100
320
1,530
1,700
8,000
15,000
69,400
25
130
340
1,630
1,800
8,500
20,000
92,500
30
160
360
1,730
1,900
9,000
30,000
138,500
40
210
380
1,850
2,000
9,400
40,000
185,000
50
260
400
1,950
2,200
10,300
50,000
231,000
60
320
420
2,050
2,400
11,200
60,000
277,500
70
370
440
2,160
2,500
11,600
70,000
323,500
80
430
460
2,270
3,000
14,500
80,000
370,000
90
480
480
2,380
3,500
16,500
90,000
415,500
100
530
500
2,480
4,000
18,500
100,000
462,000
120
580
550
2,660
5,000
23,500
125,000
578,000
140
690
600
2,900
5,500
26,000
150,000
694,000
160
790
700
3,380
6,000
28,000
175,000
810,000
180
900
800
3,880
6,500
30,000
200,000
925,000
Centistokes
=
Centipoise
Centipoise
=
Centistokes x Specific Gravity
Specific Gravity
CONVERSION FACTOR
SSU
Multiplier
30
=
1.0
100
=
1.5
500
=
2.5
1000
=
3.2
2000
=
4.0
3000
=
4.7
4000
=
5.0
5000
=
5.5
7500
=
6.5
10000
=
7.0
25000
=
10.0
50000
=
13.5

- 10 -
K) Bearing Load
The product viscosity will have a direct relationship on the flow rate of the system. The
following chart is a flow meter selection guide based on the relationship of viscosity and
flow rate. The bearing material is illustrated according to maximum bearing load allowable.
In the following flow chart, please choose the system flow rate and the product viscosity.
Then select the proper bearing sleeve material to identify the flow limitations of the flow
meter. If the system flow rate and viscosity do not meet your requirements, choose the next
size of flow meter or reduce the flow rate.
SYSTEM DESIGN
Meter Selection
The flow meter must be carefully chosen from the Meter Selection factors in the Engineering
Manual. The meter must be selected based on the operating system and product characteristics.
System variables include flow rate, temperature and pressure. The product characteristics
include the material compatibility, lubricity, viscosity, suspensions, pH, and whether the product
can congeal, crystallize or leave a dry film. Failure to select the correct flow meter may result in
system failure or serious injury.
Air Elimination
In any system that the tank may be completely drained or multiple products manifold into one
metering system, the possibility of air being present increases. The solution is an air or vapor
eliminator located before the flow meter to vent the air or vapor from the system before it can be
measured. Air or vapor elimination is required for all weights and measures regulatory
approvals in custody transfer applications.

- 11 -
Control Valves
Safety and isolation valves should be used throughout the metering system. In any pumping
system where there is one (1) pump and multiple flow meters, a digital or hydro-mechanical
Rate-of-Flow control valve must be used at each flow meter to prevent over speeding of the flow
meters.
Best Plumbing Configuration
1). Flow meter must have secure mounting to a riser stand or the foundation.
2). The inlet and outlet piping must be securely supported, in a manner of not to allow pipe
stress on flow meter.
3). System should be designed to keep the flow meter full of liquid at all times.
4). System piping should have the same full pipe diameter or larger as the flow meter,
throughout the metering system to allow for minimal pressure loss.
5). The pipe should be laid out as straight as possible to reduce pressure loss from flow
restriction.
6). The meter and piping must be installed in such as way as to avoid accidental draining of the
meter. Meter inlet and outlet should be lower than the associated system plumbing (sump
position).
7). It is not necessary for the air eliminator to be installed bolted directly to the meter. It can be
installed upstream from the meter. For effective operation of the air eliminator, it should be
mounted between the meter and any valves, tees or any other potential places where air may
enter the system.
8). The metering system should include a means for calibration.
Protection From Debris
On new installations, care must be taken to protect the meter from damage during start-up. It is
recommended to put a strainer before the meter. Damage may result from the passage through
the meter of dirt, sand, welding slag or spatter, thread cuttings, rust, etc. The insertion of a spool
(a flanged length of pipe equal in length to the meter and accessories attached to the meter) in
place of the meter until the system is flushed, temporarily bypassing the plumbing around the
meter, will also protect the meter from debris. Once the system has run “clean” for a period of
time the meter may be reinstalled or protective devices removed.
Thermal Expansion
As with most liquids, they will expand and contract with temperature. In any system where there
is a chance for liquid to be captured between closed valves without relief, thermal expansion will
likely occur and create dangerously high pressures within the system. Care should be taken in
designing the system in which thermal shock may occur by implementing Pressure Relief Valves
or Thermal Expansion Joints in the system design.
When product is trapped within the system, the pressure will increase by 126 PSI (8.69 BAR) for
every one (1) temperature degree increase.

- 12 -
Thermal Shock
The system operating temperature will expand or contract the metals within the flow meter. For systems
that have sudden or immediate temperature increases of 68 F (20 C) degrees or more, will require
clearance rotors. Clearance rotors will be necessary to eliminate the effect of immediate
expansion of the rotors vs. meter body, caused by thermal shock.
Hydraulic Shock (Water Hammer)
Hydraulic shock is a rise in pressure, which happens when an operating system has immediate
change in direction of flow such as a fast valve closure at a high operating flow rate. Hydraulic
shock can damage any item in the way of the product flow such as internal parts of the meter,
valves, and pump. System design and improper operating procedures will elevate this problem.
The use of 2-stage preset control valves or surge suppressing bladders or risers will help reduce
or eliminate this problem.
To compute the shock pressure when a valve is closed quickly (recommended to be less than 6
PSI):
Shock Pressure (PSI) = 63 x Velocity (FPS)
In order to eliminate hydraulic shock, you need to slow down the valve closure rate. The time
required to close the valve so that the line pressure will not exceed the normal pressure at no
flow is: Time (seconds) = 0.027 x L x V
N –F
V = Velocity in Feet/Seconds
L = Length of pipe before the valve in feet
N = Line pressure at no flow
F = Line pressure at full flow
Products that Dry/Congeal/Crystallize
There are many liquids that crystallize, harden and/or solidify on contact with air or with an
increase in temperature. A proper system design and a good understanding of the product being
measured will help to avoid the possibility of air entering into the system and the product being
affected.
Calibration
The meter shall be tested and calibrated with the product it is intended to measure when installed.
Total Control Systems shall not be responsible for loss of product or any damages resulting from
the end user’s failure to test this meter to insure proper calibration. Every 700 series meter is
tested and calibrated at the factory to prove it is calibratable in your system. It is the owner’s
responsibility to report this device to the local Weights and Measures officials for their
inspection before the meter is put to use. Refer to the Material Safety Data Sheet of the
calibration fluid used in testing on pages 43 to 46 for more information.

- 13 -

- 14 -

- 15 -
LPG SYSTEM DESIGN
LPG will have a high vapor pressure and tends to vaporize easily. The successful meter
operation will depend on the care exercised to prevent this from happening.
In order to prevent vaporization of LPG, certain elements must be adhered to in the design,
fabricating and operation.
1) The piping from the storage tank to the pump inlet should be at least one pipe size
larger than the pipe size of the pump inlet. Any valves, strainers or other fittings in
the inlet piping system should be similarly sized. During operation the pressure at the
pump inlet must be equal to or greater than the vapor pressure of the product.
2) All shut-off valves should be full-port ball type or similar free-flow type.
3) An external pump bypass (pressure relief) line from the pump outlet to the storage
tank should be provided. This should include a pressure relief valve set to permit
circulation through this line at a pressure that is about 25 PSI lower than the pump
bypass relief valve setting. This is to prevent recirculation within the pump, which
may cause heating and formation of vapor.
4) The piping system from the pump to the meter should be the same pipe size as the
pump outlet. Shut-off valves should be the ball type or an equally free-flow type. A
minimum number of elbows and fittings should be employed.
5) Safety valves or pressure relief valves should be included in the installation so that
any section of the installation that might be isolated when valves are closed will be
protected.
6) There must be provision for determining product temperature as it pass through the
meter. The thermometer used should have no less than one graduation per degree F,
preferably five.
7) Calibration of LPG flow meters should follow National Institute of Standards and
Technology (NIST) Handbook 44 regulations pertaining to LPG.
LPG is flammable when mixed with air and the same safety precautions should be observed that
would be used in handling a liquid such as gasoline. Dangerous concentrations of LPG may not
be readily detected; therefore, adequate ventilation is a primary requirement.
LPG has a lighter coefficient of expansion than other petroleum liquids. A change in liquid
temperature of 1 degree F will result in a change in volume of 0.17%. Due to this characteristic,
it is common to use Automatic Temperature Compensators (ATC) on LPG meters used in the
resale of LPG. The use of an ATC will automatically correct the delivered volume to 60 degrees
F.

- 16 -
METER CALIBRATION
The method of proving should be selected, and necessary provisions made, during the design
stage of the installation. Of the most common used systems, portable provers have the advantage
of more closely reproducing the condition under which the product is normally delivered.
Use this information for all flow meters, except on Liquefied Propane Gas (LPG) flow meters.
Use Accurate Prover
Scientifically designed provers are commercially available for proving meters, and no other kind
should be used. Even scientifically designed provers should be checked periodically for accuracy.
Weights and Measures officials have been very cooperative in giving assistance to checking
privately owned volumetric provers.
Recommended size of test measure:
The prover capacity should be equal to at least one minute’s flow through the meter at its
maximum rate.
These provers are not merely truck compartments or drums, but are scientifically designed test
measures, having proper drainage means built into them, a calibration gauge glass neck, and
protection against deformation (which causes volume changes).
A “homemade” prover, whether a drum or a tank is not likely to be satisfactory, and may cause
expensive errors due to inaccurate meter calibration.
Setting a Prover
The prover should be set level, using the levels provided on the prover, or separate ones. This
insures consistent results when moving the prover from meter to meter.
Where to Test a Meter
The best place to test is in its normal operating position, instead of a test stand. In this way, the
correctness of the installation and of the operation conditions will be verified by the test. Always
test a meter with the same liquid it is to measure, because a difference in viscosity, temperature
and system plumbing slightly affects meter accuracy.
Discharge Line from Meter
Where a portable prover is used, the liquid is generally discharged in to the prover in the same
manner, as a normal delivery would be made. Where a special test connection is used, the
discharge line must be arranged to drain to the same point on each test. The meter flow rate and
off/on is controlled at the end of the discharge line.
Wetting the Prover
Reset the meter register to zero, and fill the prover to the zero or 100% marking of the scale.
Disregard the meter reading. Drain the prover, and reset the register. The reason for disregarding
the first meter reading is that the prover must be wetted, as its calibrated capacity is determined
on its wet measure capacity by its manufacturer, and because the prover will be wet for the
subsequent tests to be run.

- 17 -
After the prover has drained, allow a definitive time of a few minutes for drainage from the sides
of the tank. Total drainage time should be the same between all tests to insure inform results. If a
considerable length of time is to elapse between tests, the wetting operation can be eliminated by
allowing the prover to remain full until the next test is to be run.
Making the Tests
The setup is now ready for the accuracy test. Reset the register to zero, and run the required tests
through the meter. Do not exceed the maximum recommended rate of flow for the meter.
Maximum and minimum recommended rates of flow for various sizes and types of 700 series
meters are marked on their identification plates and maintenance manuals.
Determining Test Results
Run the meter to the mark on the dial corresponding to the prover capacity, and read the over or
under delivery in cubic inches or percent on the calibrated plate on the neck of the prover. If the
plate is calibrated in cubic inches, the percentage error can readily be computed on the following
basis:
(a) One gallon equals 231cu.in.
(b) A 100-gallon prover holds 23,100cu.in. Therefore, 23.1cu.in. represents 0.1% error.
The National Institute of Standards and Technology, in its NIST Handbook 44 specifies a
tolerance of plus or minus the following:
METER TOLERANCE
Acceptance tolerances apply to new meters and repaired meters after reconditioning.
Repeatability
When multiple tests are conducted at approximately the same flow rate and draft size, the range
of test results for the flow rate shall not exceed 40% of the absolute value of the
maintenance/normal tolerance and the results of each test shall be within the applicable tolerance.
Changing Meter Calibration
Refer to meter literature for method of changing meter calibration. Any change in the meter
calibration adjustment will change the delivery in the same amount for all rates of flow. That is,
the calibration curve retains its shape, but is moved up or down. Therefore, if a meter tests
satisfactorily at full flow, but drops off too much at low flow, changing the calibration will not
remedy this condition; it will bring the low flow test to 100%, but it will also bring the full flow
above 100% by the same amount that the low flow was raised. A condition of this kind is caused
either by the metering system, need for meter cleaning or repairs, or because of an attempt to
retain accuracy below the minimum recommended rate of flow for the meter.
Tolerance
Indication of Device
Acceptance Test
Maintenance Test
Special Test
Wholesale
0.2%
0.3%
0.5%
Vehicle
0.15%
0.3%
0.45%

- 18 -
Temperature Correction
If the conditions of testing are such that there will be a change of more than a few degrees in the
temperature of the liquids between the time it passes through the meter and the time the prover is
read, it will be advisable to make a temperature correction to the prover readings. To do this, it is
necessary to install thermowells; to take readings of the temperature of the liquids in the meter
and in the prover; and to take the degrees API of the liquid. Corrections can then be easily made
by the use of the National Standard API Tables.
PRODUCT DEPLETION TEST (SPLIT COMPARTMENT)
Purpose: A product depletion test verifies the proper operation of air elimination when the
storage tank for the product being measured is pumped dry. This test is necessary for meters that
may drain a tank completely, such as a vehicle tank meter.
Multiple-Compartment Test Procedure:
1. Begin the test from a compartment (ideally the largest compartment) containing an amount of
fuel equal to or less than one-half the nominal capacity of the prover being used. Operate the
meter at the normal full flow rate until the compartment is empty. There are several methods for
determining that the compartment is empty. There may be a significant change in the sound of
the pump. There may be visual evidence that the compartment has run dry. The meter may stop
entirely or may begin to move in jumps (pause, resume running, then pause, then run again.)
2. Continue the test until the meter indication stops entirely for at least 10 seconds. If the meter
stops for 10 seconds or more, proceed to step 3. If the meter indication fails to stop entirely for a
period of 10 seconds, continue to operate the system for 3 minutes.
3. Close the valve from the empty compartment, and if top filling, then close the nozzle or valve
at the end of the delivery hose. Open the valve from another compartment containing the same
product. Carefully open the valve at the end of the delivery hose. Pockets of vapor or air may
cause product to splash out of the prover. The test results may not be valid if product is splashed
out of prover. Appropriate attire and protection is required, but caution is still necessary.
4. Continue delivering product at the normal full flow rate until the liquid level in the power
reaches the nominal capacity of the prover.
5. Close the delivery nozzle or valve, stop the meter. Allow any foam to settle, then read the
prover sight gauge as quickly as practical.
6. Compare the meter indication with the actual delivered volume in the prover.
7. Calculate the meter error, apply Product Depletion test tolerance, and determine whether or
not the meter error is acceptable.

- 19 -
Single Compartment Test Procedure:
The test of single-compartment tanks is easier to accomplish if there is a quick-connect hose
coupling between the compartment valve and the pump that supplies product to the meter. If the
system does not have quick-connect couplings between the compartment and the meter, an
additional source of sufficient product at the test site is required.
Without a quick-connect coupling:
1. Begin the tests with the compartment containing an amount of fuel equal to or less than one-
half the nominal capacity of the prover being used. Operate the meter at the normal full flow rate
until the supply tank is empty. There are several methods for determining that the tank is empty.
There may be significant change in the sound of the pump. Someone may visually watch for the
tank to run dry. The meter may stop entirely or may begin to move in jumps (pause, resume
running, the pause, then run again).
2. Continue the test until the meter indication stop entirely for at east 10 seconds. If the meter
stops for at least 10 seconds, proceed to step 3. If the meter indication fails to stop entirely for at
least 10 seconds, continue to operate the system for 3 minutes.
3. Close the compartment valve and the delivery nozzle or valve if top filling. Stop the pump and
load sufficient product from the alternate source into the supple to compartment for the meter
being tested. Allow the product to stand in the compartment for a brief time to allow entrained
vapor or air to escape.
4. Open the compartment valve and restart the pump without pump resetting the meter to zero.
Carefully open the nozzle of valve at the end of the delivery hose. Pockets of vapor or air may
cause product to splash out of the prover. The test results may not be valid if product is splashed
out of the prover. Appropriate eye protection is required, but caution is still necessary.
5. Continue delivery of product at the normal full flow rate until the liquid level in the prover
reached the nominal capacity of the prover.
6. Close the delivery nozzle or valve, stop the meter, and allow any foam to settle, then read
prover sight gauge.
7. Compare the meter indication with the actual delivered volume in the prover.
8. Calculate the meter error, apply Product Depletion test tolerance, and determine whether or
not the meter error is acceptable.
This manual suits for next models
7
Table of contents
Other Total Control Systems Measuring Instrument manuals
Popular Measuring Instrument manuals by other brands
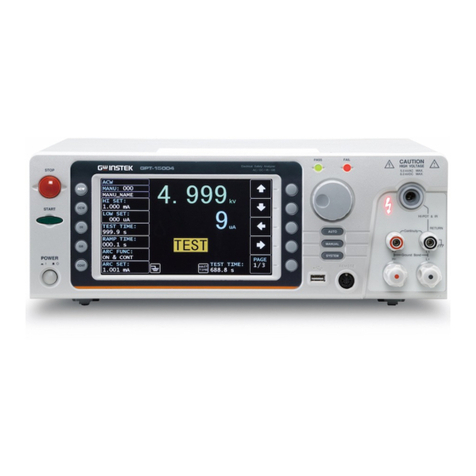
GW Instek
GW Instek GPT-10000 Series user manual
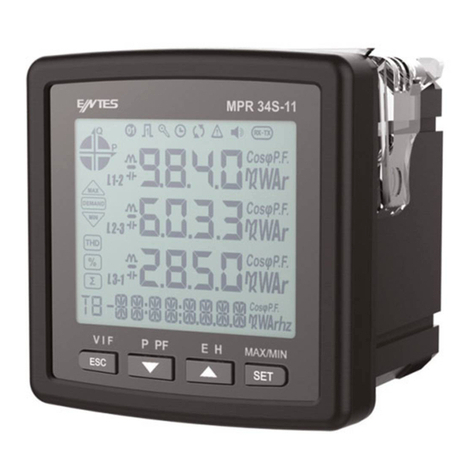
Entes
Entes MPR-3 Series user manual
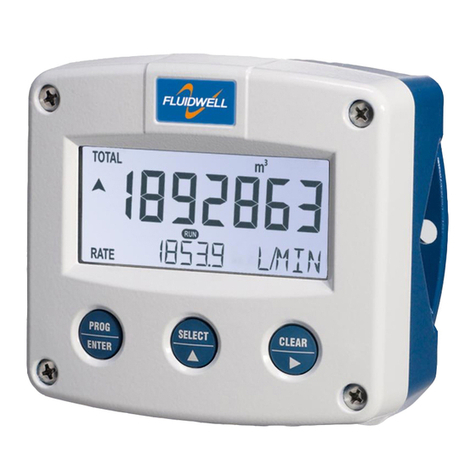
Fluidwell
Fluidwell F115-P Operation manual
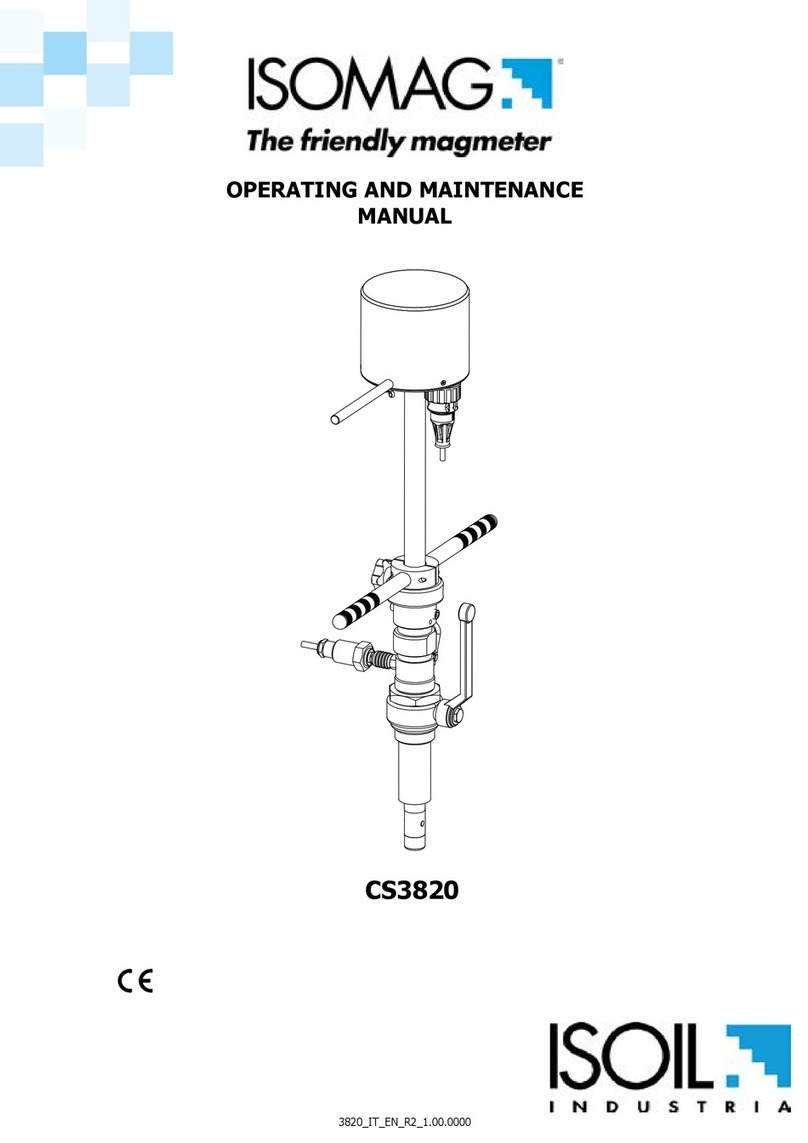
ISOMAG
ISOMAG CS3820 Operating and maintenance manual
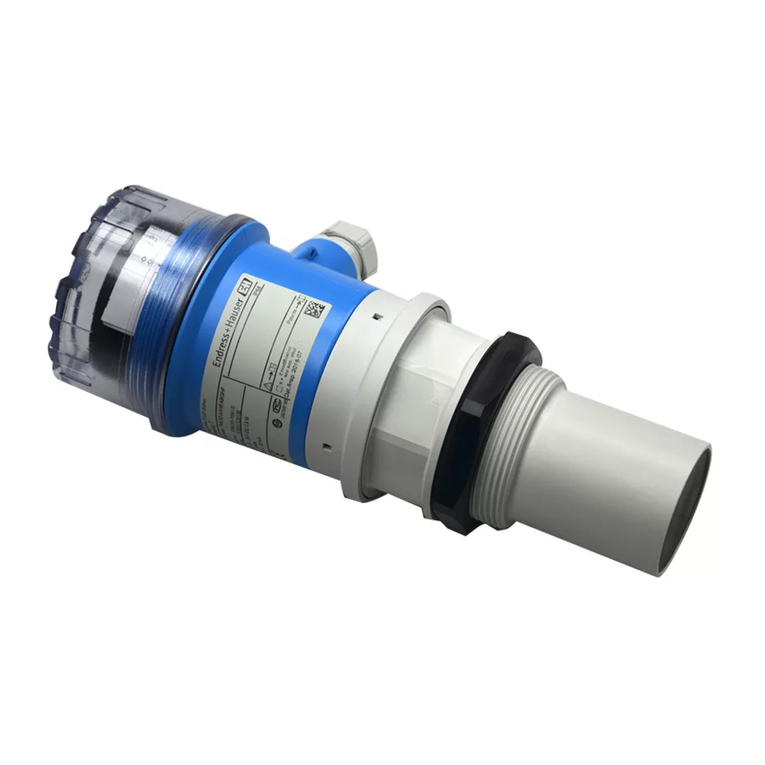
Endress+Hauser
Endress+Hauser Prosonic T FMU30 Brief operating instructions
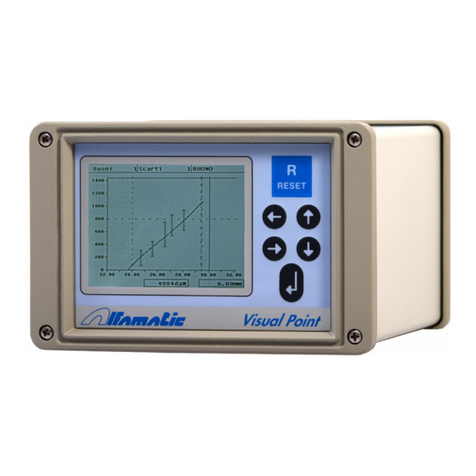
ALFAMATIC
ALFAMATIC Visual Point installation manual