Total Control Systems 700-LP Series Instruction manual

CatalogTitle
CatalogSubtitle
700-LP Series Rotary Meter
Liquefied Petroleum Gas (LPG)
Installation, Operation & Maintenance Manual
© Copyright 2009 Total Control Systems
WARNING: This equipment is for service on flammable liquid and gas under pressure and must
be installed, operated, maintained, and serviced only by qualified personnel fully trained in all
safety procedures and applicable federal, state, local, and industry codes. Failure to follow proper
procedures for this class of equipment can result in property damage, serious injury or death from
burns, fire, explosion or other hazards.
Listing No. MH45225

Page 2
Safety Warning Symbols 2
Receipt & Inspection 3
Notice 3
Meter Overview 4
Meter Specifications 4
Material of Construction 4
Procedures for LPG Meters 5
System Recommendations 6
System Recommendations (Continued) 7
Start Up Recommendations 8
Direction of Flow 9
Meter Dimensions 10
Meter Calibration 11
Calibration Adjustment 11
Maintenance 12
Maintenance (Continued) 13
Storage Instructions 13
Meter Assembly (Exploded View) 14
Meter Assembly (Bill of Material) 15
Air Eliminator Assembly 16
Air Eliminator Assembly (Continued) 17
Strainer Assembly 18
Strainer Assembly (Continued) 19
Differential Valve Assembly 20
Differential Valve Assembly (continued) 21
Back Check Valve Assembly 22
Table of Contents
Back Check Valve Assembly (continued) 23
Torque Specifications 24
Torque Specifications (continued) 25
Drive Components 26
Disassembly of Meter 27
Disassembly of Meter (Continued) 28
Disassembly of Meter (Continued) 29
Inspection of Parts 30
Re-Assembly of Meter 31
Re-Assembly of Meter (Continued) 32
Re-Assembly of Meter (Continued) 33
Re-Assembly of Meter (Continued) 34
Assembly of Strainer 35
Assembly of Air Eliminator 36
Assembly of Differential Valve 37
Assembly of In-line Check Valve 38
Meter Trouble Shooting 39
Air Eliminator Trouble Shooting 40
Differential Valve Trouble Shooting 40
MSDS 41
MSDS (Continued) 42
MSDS (Continued) 43
MSDS (Continued) 44
Notes 45
Notes (Continued) 46
Warranty 47
Warning Symbols
CAUTION
Follow the warning instructions within the fol-
lowing information to avoid equipment failure,
personal injury or death.
TURN POWER OFF
Before performing any maintenance, be sure to
turn system power off to avoid any potential
electric spark
FLAMMABLE
Flammable liquids and their vapors may cause a
fire or explosion if ignited.
EYE PROTECTION
Pressurized systems may cause hazardous leaks
and spray that may be dangerous for your eyes.
Always wear eye protection around pressurized
systems and its hazardous liquids.
INJURY
Wear gloves for protection from hazardous liq-
uids that may cause irritation or burns.
READ
Read and understand all related manuals thor-
oughly. The Engineering and OIM manuals will
provide the knowledge for all systems, mainte-
nance and operation procedures. If you have any
questions, please consult the factory.

Page 3
Receipt & Inspection
Upon receipt of your meter, be sure to inspect the packaging and the flow meter assembly for any damage
before signing the receipt for the shipment. If damage is evident or suspected, notify the delivery company and
refuse receipt of the shipment.
Meters are individually boxed and are protected with packing material. Each package
is identified with the flow meter assembly part number, description, direction of flow
and serial number. Verify that the meter Identification Plate reflects the same model,
size, and configuration as ordered. Contact your distributor if there is any discrepancy.
Meter assemblies should be handled with methods appropriate for the shape, size and
weight involved. Appropriate clothing and shoes should be worn. Transport the meter
package to the installation site with appropriate transportation methods, being careful
not to damage the flow meter.
Be careful of any loose or protruding staples from the packaging, as they can be very
sharp and may potentially cause injury.
If foam has been used to protect the meter, carefully remove top foam layer before attempting to remove the
meter assembly from the box. Foam packaging may be formed around the meter assembly making it difficult to
remove. If meter is bolted to a wood pallet, remove bolts while being careful not to let the meter tip over when
the support has been removed. Do not lift the meter assembly by flex hoses, thermowells, wires, or pulsers.
Also, do not lift the meter by putting objects into or through the meter. Removal of the meter assembly from
its packaging without adhering to these warnings may cause serious injury or damage to the meter.
The wooden pallets and bases meet the ISPM 15 Guidelines for Regulating Wood Packaging Material in
International Trade through the Timber Products Inspection Company (TP #2134).
Every effort has been made to remove the calibration fluid before shipment. All TCS flow meters are plugged
and enclosed in a plastic bag. Appropriate precautions should be taken regarding any personal, environmental
and material compatibility with the end use system.
Notice
Total Control Systems (TCS) shall not be liable for technical or editorial errors in this manual or omissions from
this manual. TCS makes no warranties, express or implied, including the implied warranties of merchantability
and fitness for a particular purpose with respect to this manual and, in no event, shall TCS be liable for special or
consequential damages including, but not limited to, loss of production, loss of profits, etc.
The contents of this publication are presented for informational purposes only, and while every effort has been
made to ensure their accuracy, they are not to be construed as warranties or guarantees, expressed or implied,
regarding the products or services described herein or their use or applicability. We reserve the right to modify or
improve the designs or specifications of such products at any time.
TCS does not assume responsibility for the selection, use or maintenance of any product. Responsibility for
proper selection, use and maintenance of any TCS product remains solely with the purchaser and end-user.
All rights reserved. No part of this work may be reproduced or copied in any form or by any means –graphic,
electronic or mechanical –without first receiving the written permission of Total Control Systems, Fort
Wayne, Indiana USA.
Flow Meter Identification Plate

Page 4
Meter Overview
The TCS Model 700-LP series flow meter reflects a simple and efficient
design for application on liquefied petroleum gas (LPG). The meter consists
of a single fluid chamber that contains a single blocking rotor and two
displacement rotors whose rotation is synchronized with mating gears. As the
fluid enters the fluid chamber, the blocking rotor is forced to rotate. The
displacement rotors, also rotating in conjunction with the blocking rotor help
direct the fluid flow through the chamber and to the outlet. The linear flow of
the fluid is thus translated into rotary motion in the meter. The output of the
meter is picked up from the rotation of the blocking rotor and transmitted to a
register or pulse transmitter.
The rotors in the meter are designed to operate at close tolerances to one another and the wall of the fluid chamber.
There are slight clearances between the rotors and the chamber wall. Because of this, it is important that the meter
be properly applied for the flow rate and operating pressure of the system.
Because the fluid flowing through the meter is redirected only slightly from its natural flow, there is very little
pressure drop across the meter, unlike other meters that use multiple measuring chambers.
The meter design uses high performance materials for the rotor bearings and journals. Since there is no contact be-
tween the rotors and the fluid chamber wall, these critical components have a long life expectancy.
Calibration of the meter involves adjusting the rotation of the output shaft relative to the rotation of the internal ro-
tors of the meter. This is accomplished by changing the settings on an adjuster device. Calibration of the meter is
discussed in detail in the section Meter Calibration.
FLOW ILLUSTRATION
Flange Connection: 2‖ NPT Flanges, Standard; 1-1/2‖ NPT Flanges, Optional. BSPT or Slip Weld
flanges available upon request.
Flow Rate: 100 GPM (380 LPM), max flow
Maximum Pressure: 350 PSI (24 BAR)
Working Temperature: -40 F to 160 F (-40 C to 70 C)
Materials of Construction: Housing & Rotors: Anodized Aluminum; Bearing Plates: Ni-Resist II; Bearings:
Antimony carbon graphite; Gears: Stainless Steel; Seals: UL recognized Buna-N
Meter Specifications & Materials of Construction

Page 5
Procedures for LPG Meters
Procedure for Relieving Pressure in LPG Meters
NOTE: All procedures to de-pressurize and purge an LPG tank system must be performed out-of-doors in an
open environment free from any ignition sources such as sparks, flames, or heat sources.
1. Close the belly valve of the supply tank.
2. Close the valve on the vapor return line.
3. Close the manual valve in the supply line on the inlet side of the meter. If no manual valve exists on the
inlet side, consult the system manufacturer for procedures to depressurize the system.
4. Slowly open the valve/nozzle at the end of the supply line
5. After product is bled off, close the valve/nozzle at the end of the supply line.
6. Slowly crack the fitting on top of the differential valve to relieve the product pressure in the system. Product
will drain from the meter system.
7. As product is bleeding from the differential valve, slowly reopen and close the valve/nozzle on the dis-
charge line. Repeat this step until the product stops draining from the differential valve and discharge line
valve/nozzle.
8. Leave the discharge line valve/nozzle open while working on the system.
This manual provides warnings intended to inform the owner/operator of the hazards present with this type of
equipment. Knowledge of these warnings and avoidance of potential hazards is the sole responsibility of the
owner/operator of the equipment. Neglect of that responsibility is not within the control of the manufacturer of
this equipment, and the manufacturer bears no responsibility for damages, injuries or deaths resulting from
improper or inappropriate use or servicing of the equipment.
WARNING
All internal pressures must be relieved (to zero psi) before inspection, disassembly,
or servicing of any part of this meter or metering system. Property damage and
serious injury or death from fire or explosion could result from improper use of
this equipment, or from maintenance of an improperly depressurized and
evacuated meter and metering system. Always follow all federal, state, and local
laws, ordinances, and industry codes when installing, operating, or servicing this
equipment.

Page 6
Meter Selection
The flow meter must be carefully chosen from the Meter Selection factors in the Engineering Manual. The meter
must be selected based on the operating system and product characteristics. System variables include flow rate,
temperature and pressure. The product characteristics include the material compatibility, lubricity, viscosity,
suspensions, pH, and whether the product can congeal, crystallize or leave a dry film. Failure to select the correct
flow meter may result in system failure or serious injury.
Air or Vapor Elimination
In any system where the tank may be completely drained or multiple products manifold into one metering system,
the possibility of air or vapor being present increases. The solution is an air or vapor eliminator located before the
flow meter to vent the air or vapor from the system before it can be measured. Air or vapor elimination is required
for all weights and measures regulatory approvals in custody transfer applications.
System Recommendations
Control Valves
Safety and isolation valves should be used throughout the metering system. In any pumping system where there is
one (1) pump and multiple flow meters, a digital or hydro-mechanical Rate-of-Flow control valve must be used at
each flow meter to prevent over speeding of the flow meters.
Best Plumbing Configuration
1) Flow meter must have secure mounting to a riser or foundation
2) The inlet and outlet piping must be securely supported, in a manner to not allow pipe stress on flow meter.
3) System should be designed to keep the flow meter full of liquid at all times.
4) System piping should have full 2‖ pipe diameter throughout the metering system to allow for minimal
pressure loss.
5) The pipe should be laid out as straight as possible to reduce pressure loss from flow restrictions.
6) The meter and piping must be installed in such as way as to avoid accidental draining of the meter. Meter inlet
and outlet should be lower than the associated system plumbing (sump position).
7) It is not necessary for the vapor eliminator to be installed directly to the meter. It can be installed upstream
from the meter. For effective operation of the vapor eliminator, it should be mounted between the meter and any
valves, tees or any other potential places where air or vapor may enter the system.
8) The metering system should include a means for calibration.
Protection From Debris
On new installations, care must be taken to protect the meter from damage during start-up. It is recommended to
put a strainer before the meter. Damage may result from the passage through the meter of dirt, sand, welding slag
or spatter, thread cuttings, rust, etc. The insertion of a spool (a flanged length of pipe equal in length to the meter
and accessories attached to the meter) in place of the meter until the system is flushed, temporarily bypassing the
plumbing around the meter, will also protect the meter from debris. Once the system has run ―clean‖ for a period of
time the meter may be reinstalled or protective devices removed.
Thermal Expansion
Most liquids will expand and contract with temperature. This is particularly true for LPG. In any system where
there is a chance for liquid to be captured between closed valves without relief, thermal expansion will likely occur
and create dangerously high pressures within the system. Care should be taken in designing the system in which
thermal shock may occur by implementing Pressure Relief Valves or Thermal Expansion Joints in the system
design.

Page 7
System Recommendations (Continued)
Thermal Shock
The system operating temperature will expand or contract the metals within the flow meter. Systems that have
sudden or immediate temperature increases of 68 F (20 C) degrees or more, will require clearance rotors.
Clearance rotors will be necessary to eliminate the effect of immediate expansion of the rotors vs. meter body,
caused by thermal shock.
Hydraulic Shock (Water Hammer)
Hydraulic shock is a rise in pressure, which happens when an operating system has immediate change in direction
of flow such as a fast valve closure at a high operating flow rate. Hydraulic shock can damage any item in the way
of the product flow such as internal parts of the meter, valves, and pump. System design and improper operating
procedures will amplify this problem. The use of 2-stage preset control valves or surge suppressing bladders or
risers will help reduce or eliminate this problem.
To compute the shock pressure when a valve is closed quickly (recommended to be less than 6 PSI):
Shock Pressure (PSI) = 63 x Velocity (FPS)
In order to eliminate hydraulic shock, you need to slow down the valve closure rate. The time required to close the
valve so that the line pressure will not exceed the normal pressure at no flow is:
Time (seconds) = 0.027 x L x V
N –F
V = Velocity in Feet/Seconds
L = Length of pipe before the valve in feet
N = Line pressure at no flow
F = Line pressure at full flow
Calibration
The meter shall be tested and calibrated with the product it is intended to measure when installed. Total Control
Systems shall not be responsible for loss of product or any damages resulting from the end user‘s failure to test this
meter to insure proper calibration. Every 700 Series meter is tested and calibrated at the factory to prove it is
calibratable in your system. It is the owner‘s responsibility to report this device to the local Weights and Measures
officials for their inspection before the meter is put to use.

Page 8
Start up Recommendations
Start-up instruction for new installations or after maintenance and repairs:
1) Only properly trained personal should design, install, or operate metering system.
2) Remove plastic threaded plugs placed in meter for shipping protection. They are not to be used in meter system
because of the PVC plugs low rated pressure, compatibility, and sealing issues.
3) Place the meter in an area with ample workspace, secure from vibration, and pipe line stress. Mount and bolt
down on to a fixed stand or platform. This prevents meter stress, which will cause leakage and metal fatigue.
4) Apply thread sealing compound and gasket materials that are compatible with product.
5) Do not weld to meter or accessories. This will weaken housings and cause o-ring and casting leaks and
potentially distort the critical tolerances within the flow meter.
6) Always wear safety protection equipment such as goggles, steel toed shoes, gloves and full body clothing.
7) Be sure to install a pressure relief valve or expansion joint in the system to protect against thermal
expansion.
8) Make sure all system components and meter assembly bolts are properly secured and tightened.
9) Make sure the vapor eliminator vapor release is properly vented and piped back to the supply tank.
10) Make sure electrical connections are properly installed and start/stop switches are off and locked-out.
11) Ensure a flooded suction to the pump so that the system will not starve or cavitate the pump.
12) Ensure slow flooding of system. Start up system with all shut off valves in the closed position. When a pump
is turned on and a valve opened in a new, dry system, tremendous liquid and air pressure can be built up in the
piping and forced through the meter. The high pressure and volume of air causes the meter to operate more
quickly than normal. When product reaches the meter, there is an abrupt slowing of the meter rotors, which
could cause damage to the register, rotor shafts, packing gear and/or blade, timing gears and other
components. The recommended method of starting any system is to flood the piping gradually. This allows
product to slowly force the air or vapor from the entire system.
WARNING
Test equipment should be grounded to prevent a possible spark. Test area should have no ignition source. Operators should
wear personal protection and prevent any product exposure and environmental issues.
13) When operating the meter with accessories, valves should be opened slowly to avoid a pressure surge that can
damage the meter or air eliminator. System pressures should be maintained below 350 PSI (24 BAR).
14) Custody transfer metering systems must be calibrated by a regulatory agency before product can be sold off
the meter. Contact your local authorities for proper calibration.
15) Strainers should be cleaned frequently or have a maintenance schedule. This will ensure a clean system and
long service life.

Page 9
Direction of Flow
The meter is set up at the factory for left to right flow. To change the meter to right to left flow, begin
by removing the screws (#9 on the Meter Assembly Breakdown) and the adjuster cover plate (#7) on the
front of the meter. Remove both the screws (#1), the drive shaft retainer (#10), the drive shaft (#3), the e
-ring (#4) and the face gear (#5). Reinstall the gear on the shaft with the gear teeth facing up. Snap the
e-ring back into place to hold the gear in place. Reinstall the shaft, mating the face gear with the drive
gear of the packing capsule assembly. Reinstall the screw and cover plate. The meter will now be set
up for right to left flow. See Page 14 for a parts breakdown of entire meter assembly.

Page 10
Meter Dimensions in Inches (Millimeters)

Page 11
The method of proving should be selected, and necessary provisions made, during the design stage of the
installation. Use only an accurate, specifically and scientifically designed prover. No other kind should be used.
All provers should be checked periodically for accuracy. Weights and Measures officials have been very coopera-
tive in giving assistance in checking provers.
Note: The prover capacity should be equal to at least one minute‘s flow through the meter at its maximum rate.
The prover should be set level, using the levels provided on the prover, or separate ones. This insures consistent
results when moving the prover from meter to meter. A detailed description of LP Gas test procedures may be
found in the NCWM Course 305 ―Liquefied Petroleum Gas Liquid Measuring Devices‖. Specifications and
Accuracy Tolerances are contained in Handbook 44. Tolerances are shown below.
Meter Calibration
Calibration Adjustment
One complete turn of the adjuster barrel is equal to 1 gallon in 100 gallons or 1% of delivered volume. The adjuster
body will show divisions of 1%, while the adjuster barrel has divisions of 0.02%. For volumes other than 100
gallons, the following formula may be used to calculate the Adjuster percent to increase or decrease prover volume.
Volume on Prover minus Volume on Meter Counter
Volume on Meter Counter
Tolerance
Indication of Device Acceptance Test Maintenance Test Special Test
Wholesale or Vehicle 0.6% 1.0% 1.0%

Page 12
Maintenance
WARNING
Test equipment should be grounded to prevent a possible spark. Test area should have no ignition source. Operators should
wear personal protection and prevent any product exposure and environmental issues.
1). Keeping accurate maintenance and calibration records can be an excellent tool in determining the frequency
of inspection or maintenance for a system. As the meter wears, the calibration will be affected and require
adjustment. A personality profile can be created for each meter to help guide in a maintenance schedule.
2). Great care should be utilized in the maintenance of the metering system. Personal safety protection, environ-
mental hazards, and government regulations need to be the foremost priority. Only fully trained personnel
should be involved in maintenance. Failure to use original TCS replacement parts will void any Weights &
Measures approvals and risk damage to the meter system.
3). ALWAYS RELIEVE INTERNAL SYSTEM PRESSURE TO ZERO BEFORE DISASSEMBLY OR
INSPECTION.
4). SERIOUS INJURY OR DEATH FROM FIRE OR EXPLOSION COULD RESULT FROM MAINTE-
NANCE OF AN IMPROPERLY DEPRESSURIZED AND EVACUATED SYSTEM.
5). Total Control Systems flow meters and accessories are often used with LPG, petroleum, solvents, chemicals,
and other liquids that may be explosive, extremely flammable, very toxic, oxidizing, and corrosive. Severe
injury or fatalities may result if appropriate safety precautions are not followed.
6). Before replacing or cleaning filter/strainer screen, the electrical system must be turned off. Product needs to
be drained from system. Collect all product and return to storage or dispose of properly. Replace all drain
plugs that were removed. Personal safety protection must be worn at this time. Make sure there is adequate
ventilation in the area. The metering system will not completely drain so make sure you collect extra product
when you remove the strainer cover. Clean the screen once a week, or more often if there is a lot of sediment
in the system. Make sure there is no ignition source and the system is grounded. Replace all plugs that were
removed for drainage.
7). The metering system is heavy and awkward so take precaution to handle it properly.
8). Do not use force to disassemble or use a screwdriver to pry open any part of the metering system. Have the
proper tools available before trying to repair the meter system. Be careful of the parts as they can be sharp
and heavy. Do not drop housing or rotors as they can cause injury and can destroy the parts. Be careful when
inspec ting and turn i ng the timing gears and r otor s a s t hey can pinch
fingers, turn slowly to verify smooth operation.
9). When inspecting the spring loaded preset valves do not place anything inside the housing, as the action of the
valve will pinch this object when the valve closes.

Page 13
Maintenance
WARNING
Test equipment should be grounded to prevent a possible spark. Test area should have no ignition source. Operators should
wear personal protection and prevent any product exposure and environmental issues.
10). When removing gaskets or o-rings, carefully check for damage or corrosion. Any cracked, rough, worn, elon-
gated or swollen o-rings need to be replaced. When replacing the o-rings, place grease along the inside of the o
-ring groove or completely around the o-ring to help the o-ring stay in the
o-ring groove during assembly. If o-ring is pinched or not in the o-ring groove, the meter system will leak and
cause serious problems to the environment and equipment. Collect all replaced parts and dispose of properly.
Do not weld any part of the meter system or accessories as this will weaken the part and allow for leaks
11). All bolts and screws need to be coated with anti-seize. Then follow the torque specifications for each flow
meter.
12). Recommended levels of maintenance and inspection will depend upon the system variables, such as the prod-
ucts being measured, their corrosiveness, system pressure requirements, government or company regulations,
and age of metering system. If hydrostatic testing is required, the system pressure should not exceed 1.5 times
the marked meter pressure. It is not recommended to pneumatically test the meter system at anytime.
13). If any component of the meter system is removed from the system, it should be thoroughly flushed with a
compatible liquid. After this is done, immediately refill the meter or accessory with a compatible liquid to
prevent corrosion and water build up.
Storage Instructions
Short periods of non-use of the meter (a week or less) should present no problem, provided that the meter remains
full of product. For long periods of non-use, such as winter storage, the following procedure is recommended.
Before long-term storage, a good practice is calibration of the meter to determine that it is functioning properly.
1). To store the meter when it is left in line, flush the system with clean water until 70-80 gallons of
water have gone through the meter.
2) Pump a 50% anti-freeze / 50% water solution through the entire system (100% RV antifreeze may be used
instead). With the pump running, shut off a valve downstream from the meter, making sure that anti-freeze
solution is present at that point. Then close an upstream valve, such that the meter remains full of anti-freeze
solution.
3) Remove the register from the meter, and lubricate the drive coupling shaft. After lubrication, reassemble the
register onto the meter.
When starting the system after a period of storage, check the meter's calibration as detailed earlier in the service
manual.

Page 14
700-20-LP Meter Assembly

Page 15
700-20-LP Meter Assembly
Item Description Qty 700-20-LP
110-24 x 1/2 Rd Hd Slotted Machine Screw 81-128279
2Adjuster Assembly 1 700100
3Drive Shaft 1700019
4E-Ring 1700016
5Face Gear 24T 1700018
6Drive Bushing 2700020
7Register Support Cover 1700029
8Seal Wire and Seal 11-118849
910-24 Slotted Drilled Machine Screw 2700042D
10 Drive Shaft Retainer 1700022
11 1/4-20 x 3/4 Hex Head Bolt 4700040
12 1/4‖ Split Lockwasher 4700071
13 Register Support 1700200
14 Packing Retaining Plate 1700015
15 Packing Capsule 1700180
16 O-Ring 1700049
17 3/8‖ Plug 2700064
18 Front Cover 1702505
19 5/16-18 x 1 Grade 8 Bolt 20 702027
20 Rear Cover 1702555
21 10-24 x 3/4 Rd Hd Slotted 10 702014
22 Bearing Plate w/ AT Carbon Bearings 2 702225
23 Cover Gasket 2 702028
24 LP Meter Housing Assembly 1 702115
25 Special Spacer 8 702018
26 3/8-16 x 1-1/2 Grade 8 Bolt 8 702026
27 2‖ NPT Steel Flange 2 702613
28 2‖ Flange Quad Ring 2 702025
29 Blk Rotor Gear Sintered 1 702351
30 Rotor Lock Nut 3 702010
31 Disp Rotor Gear Sintered 2 702451
32 Rotor Key 3 702008
33 Disp Rotor Assembly 2 702405
34 Blk Rotor Assembly 1 702305

Page 16
730-20-LP Vapor Eliminator Assembly

Page 17
730-20-LP Vapor Eliminator Assembly
Item Description Qty 730-20-LP
15/16-18 x 1-1/2 Grade 8 Bolt 12 740056
2Ring Washer SM OD 12 740051
3Outlet Cover, LPG 2740115
4Valve Plate, Nitrite 2740206
51/4‖ Hydro Relief Valve 1740110
6LPG Air Eliminator Housing 1740060
78-32 x 1/4 Phillip Pan Head 6740030
8# 8 Split Lockwasher 6740017
9Retaining Clip 2740012
10 Reed Air Eliminator 2740007
11 Float and Stop Assembly 1 740013
12 Diffuser/Shaft Assembly 1 740035
13 3/8-16 x 1-1/4 Grade 8 Bolt 6 700063
14 Special Spacer 6 702018

Page 18
720-20-LP Strainer Assembly

Page 19
720-20-LP Strainer Assembly
Item Description Qty 720-20-LP
13/8-16 x 1-3/4 Grade 8 Bolt 4742026
2Special Spacer 8 702018
33 Port Basket Cover 1742355
4Seal Ring 1742024
5Strainer Basket 100 Mesh 1742025
6Top Seal 1740053
7Aluminum Strainer Housing 1742081
8Flange Quad Ring 1702025
92‖ NPT Steel Flange 1702613
10 3/8-16 x 1-1/2 Grade 8 Bolt 4702026

Page 20
757-20-LP Differential Valve Assembly
Table of contents
Other Total Control Systems Measuring Instrument manuals
Popular Measuring Instrument manuals by other brands
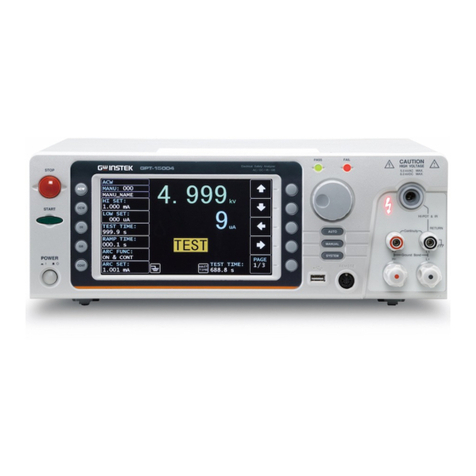
GW Instek
GW Instek GPT-10000 Series user manual
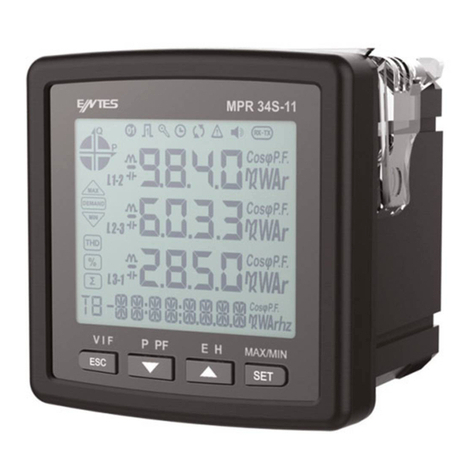
Entes
Entes MPR-3 Series user manual
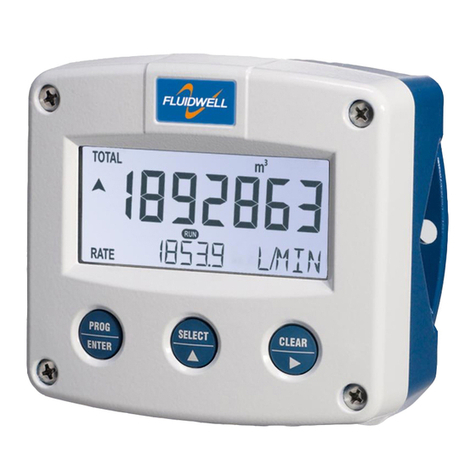
Fluidwell
Fluidwell F115-P Operation manual
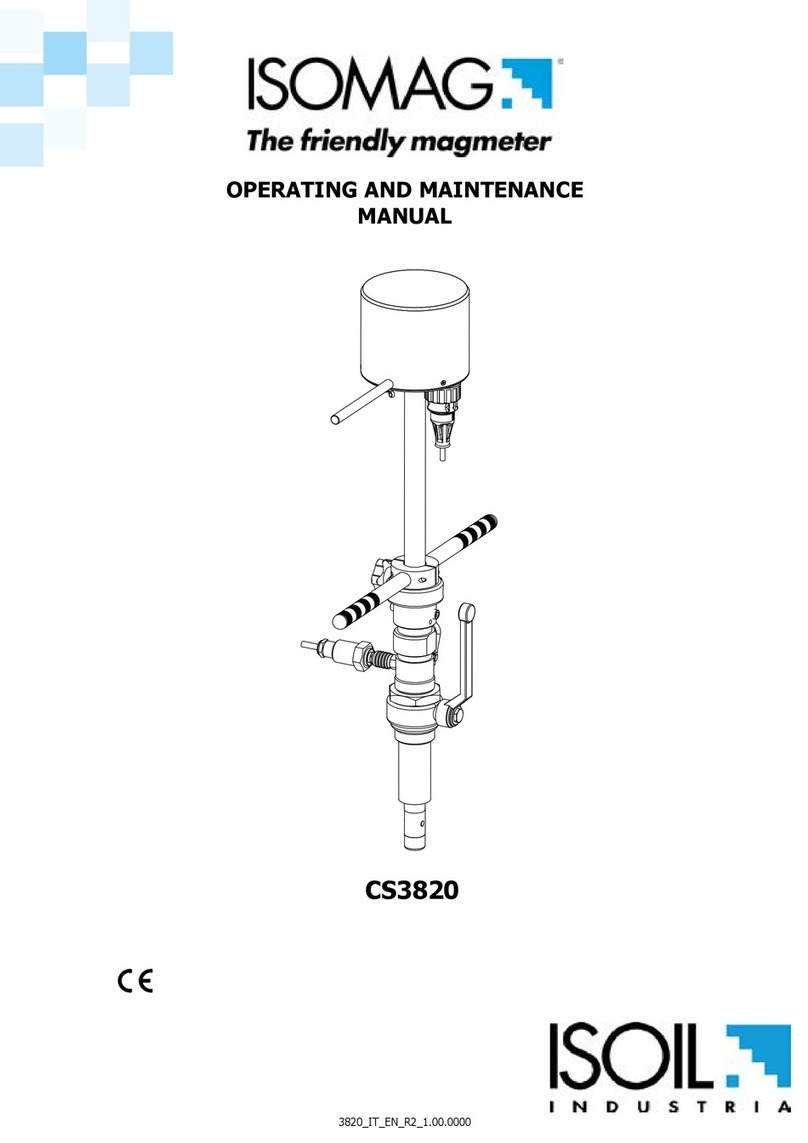
ISOMAG
ISOMAG CS3820 Operating and maintenance manual
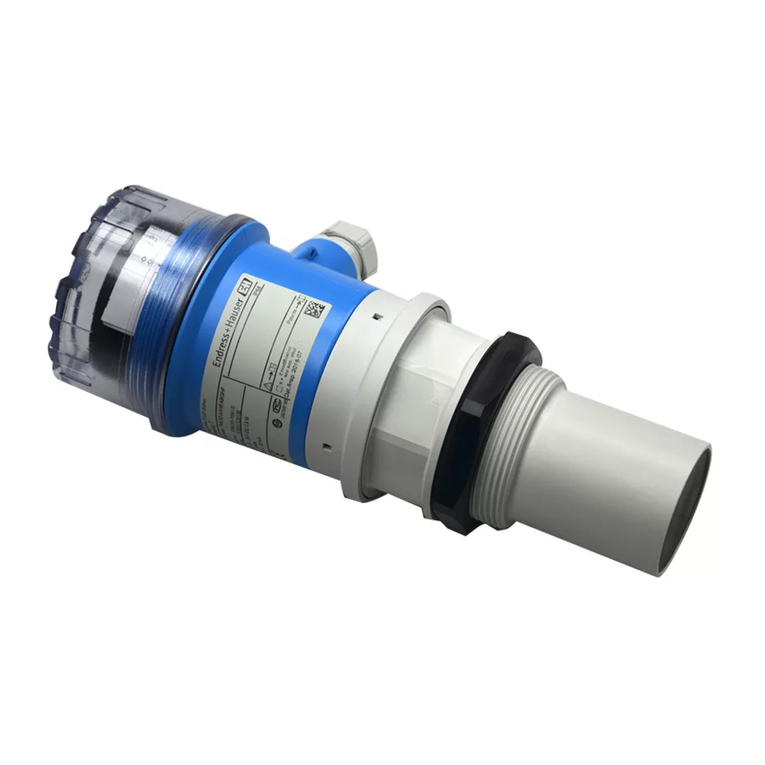
Endress+Hauser
Endress+Hauser Prosonic T FMU30 Brief operating instructions
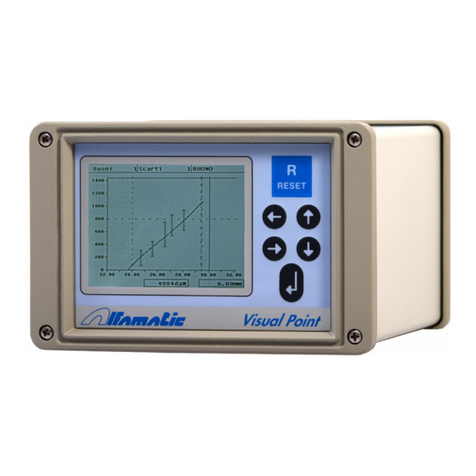
ALFAMATIC
ALFAMATIC Visual Point installation manual