Trelawny TPG650 Troubleshooting guide

OPERATION & MAINTENANCE
TPG650
PLANETARY FLOOR GRINDER

OPERATION
Foreword
Thank you for your purchase of the
TRELAWNY TPG650 Floor Grinder.
This manual contains the necessary
maintenance information for you to
ensure proper operation and care for
this machine.
It is essential for you to read
t h r o u g h t h e s e m a n u a l s
thoroughly.
In the unlikely event that you
experience problems with your
TPG650, please do not hesitate to
contact your local Trelawny dealer or
ag ent . W e al ways welc om e
feedback and comments from our
valued customers.
General Information
Before operating, perform ing
maintenance or repairing the
TPG650 FLOOR GRINDER this
manua l m ust be re ad and
understood by the operator, if in any
doubt, ask your supervisor before
using this equipment.
Local safety regulations must be
followed at all times. Failure to follow
these instructions could result in
damage to the TPG650 and/or
personal injury.
Trelawny SPT Limited disclaims all
responsibility for damage to persons
or objects arising as a consequence
of incorrect handling of the machine,
failure to inspect the machine for
damage or other faults that may
influence the operation prior to
starting work, or failure to follow the
safety regulations listed or applicable
to the job site.
This machine is primarily designed
for the grinding and polishing
concrete, marble and terrazzo
surfaces.
It can be used both indoors and out.
This machine must not be used in a
fixture.
Safety
WEAR SAFETY BOOTS, FACE
M A S K , S H A T T E R P R O O F
GLASSES, HELMET, GLOVES and
any other personal protective
equipment required for the working
conditions. Avoid loose clothing; this
may become trapped in moving
TO AVOID NUISANCE DUST,
connect an industrial vacuum
cleaner (minimum 3000 watts or
equivalent) to the 50mm (2”) vacuum
port situated at the rear of the
machine.
BE VERY CAREFUL WITH HOT
COMPONENTS.
The diamond tools and tool heads
can become very hot in use. Always
use gloves when changing or
replacing the grinding segments.
DO NOT OPERATE ELECTRIC
VERSIONS IN WET CONDITIONS.
CAUTION THIS MACHINE IS
HEAVY. It weighs (260kg/573lbs).
Do not lift this machine manually,
use a hoist or crane with the grinder
securely fastened to a pallet.
Risk of Hand-arm
Vibration injury
These tools may cause Hand-arm
Vibration Syndrome injury if their use
is not adequately managed.
Although the vibration from this
machine is low, we advise you to
carry out a risk assessment and to
implement measures such as;
limiting exposure time [i.e. actual
operation time, not total time at
work].
Use job rotation and ensure machine
tools are used correctly, ensuring the
machines are maintained according
to our recommendations, and ensure
that the operators wear personal
p r o t ec t i v e e q u i pm e n t [ P P E ]
particularly gloves and clothing to
keep them warm and dry.
Employers should consider setting
up a progr amme of healt h
su r ve i l lan c e t o es ta b lis h a
benchmark for each operator and to
detect early symptoms of vibration
injury.
We are not aware of any PPE that
provides protection against vibration
injury by attenuating vibration
emissions.
See ‘Specifications’ section for
vibration emission data.
Further advice is available from our
Technical Department.
We strongly advise you to visit the
Health & Safety Executive website
http://www.hse.gov.uk/vibration
This site provides excellent advice
and information on HAV and
currently, includes a Hand-arm
Vibration Exposure Calculator that is
easy to use to work out the daily
vibration exposure for each of your
operators.
Media Types &
Application Guide
Grinding Segments
All the diamond range can be used
wet or dry.
(Resin bound polishing discs)
PD400, PD800, PD1500 and
PD3000.
Universal polishing discs, can be
used wet or dry.
(See page 6 for more information)

Image Part Number Tool Description
365.5495L
PCD Removal Diamond Anti Clock Wise
For removal of coatings, adhesives & toppings
365.5495R
PCD Removal Diamond Clock Wise
For removal of coatings, adhesives & toppings
365.5500
16 Grit Single (Quick Release) Soft Bond
For very course grinding and thin coating removal
365.5500/2
16 Grit Double (Quick Release) Soft Bond
For very course grinding and thin coating removal
365.5501
30 Grit Single (Quick Release) Soft Bond
For Hard Concrete
365.5502 30 Grit Single (Quick Release) Medium Bond
For Medium Hardness concrete
365.5503 30 Grit Single (Quick Release) Hard Bond
For Soft Concrete or for very rough concrete
365.5501/2 30 Grit Double (Quick Release) Soft Bond
For Hard Concrete
365.5502/2 30 Grit Double (Quick Release) Medium Bond
For Medium Hardness concrete
365.5503/2 30 Grit Double (Quick Release) Hard Bond
For Soft Concrete or for very rough concrete
365.5504/2 70 Grit Double (Quick Release) Medium Bond
For Light Grinding and Scratch Removal
365.5506/2 120 Grit Double (Quick Release) Medium Bond
For Light Grinding and Scratch Removal
365.5725 3 Segment Quick Release Diamond Plate
(Set of 3)
For use with only the TPG 650/540 Machine
Media Types - Metal Bond Tools

Media Types - Resin Bond Tools
Image Part Number Tool Description
365.5605
50 Grit Hybrid
365.5610
100 Grit Hybrid
365.5620
200 Grit Hybrid
365.5602A
200 Grit Resin Bond
365.5604A
400 Grit Resin Bond
365.5608A
800 Grit Resin Bond
365.5618A
1500 Grit Resin Bond
365.5635A
3000 Grit Resin Bond
350.5666 Polishing Adapter Plate
Used to attach the “Polishing Tools” to the quick release plate
365.5745 3 Segment Polishing Plate
(Set of 3)
Used to attach “Polishing Tools”
For use only on the TPG650/540

Maintenance
Machine Start Procedure:
Check on the Speed Controller that
it is on it‟s lowest speed setting.
Press the White „START‟ Button
Adjust the speed as required.
The machine may oscillate slightly
during use, which is normal.
Move the machine slowly backwards
and forwards and overlap each strip
by 10cm (4”), complete a small area
noting the performance.
Press the Black „STOP‟ Button to
stop the machine and inspect the
finish produced.
If required change the bond of the
diamond tools or speed of rotation,
recheck performance and surface
finish.
: EMERGENCY SHUTDOWN :
Press the “Red Emergency Stop
Button”
Pre-Start Check
ALL VERSIONS
Check all bolts and screws for
tightness. Ensure that all fittings are
secure.
The TPG650 is supplied with a
specially commissioned frequency
inverter, starter switch and electric
motor.
Each unit is fully tested and the
overload relays have been calibrated
a n d s e t a c c o r d i n g t o t h e
manufactures specifications.
In the event of malfunction on a new
machine, the owner should first
check that the power supply on site
is suitable and adequate.
All cables must be fully uncoiled and
never left wrapped around cable
reels or tied in loops.
415v Motor
Take particular care when using
415v Machines, ensure that the
electrical supply is earthed and that
breakers and fuses are correct for
the loading.
The 415v motor requires a minimum
of a 16amp, 380v power supply.
Always use the shortest possible
length of extension cable. To avoid
voltage drop the cable must have a
minimum core wire size of 2.5mm2
cross-section area.
Maximum length of cable 30 meters.
Starting
Check over the whole area to be
worked.
It is important to check the area to
ensure that there are no obstacles or
protrusions that will damage the
machine or the tools.
This is a “flat” surface grinder.
If the surface is very bumpy or
uneven, consider using the Trelawny
Floor Planer to level the floor first,
before starting to use the TPG650.
Ensure that the machine is started
on a level surface.
Machine Operation
Connect a suitable commercial
vacuum which has been designed
for the collection of concrete dust
and possibly toxic paint particles,
Trelawny can supply special HEPA
filtered vacuums suitable for these
applications.
For wet grinding, fill the reservoir
with approximately 40 litres of water.
When filling, ensure that no water
splashes onto any electrical
components.
On the frame below the tank, there is
a valve to regulate the flow of water.
Control Box
The White „START‟ button operates
a soft start circuit and is the only way
to start the machine.
Use the Black „STOP‟ button or the
Red Emergency „Stop‟ Button to stop
the machine.
When changing the direction of
rotation, be sure to let the machine
completely stop before changing
direction.
Be careful with
HOT COMPONENTS.
The discs and diamond segments are
hot during and for some time after
operation.
Do not touch them until they have
cooled down.
Important:
If using the PCD tools ensure that
the direction of rotation is set to
FORWARD - “FWD”.
These tools should only be used in
the forward rotation direction.
Use the speed regulator to adjust the
grinding head speed.
Rotary direction switch,
“FWD” - Forward.
“OFF”.
“REV” - Reverse.

Maintenance
Carefully tilt the machine backwards
to rest on its handle bar.
Place a heavy object (10kg sand
bag, etc.) across the upper part of
the handle bar or rope down for
additional security.
Remove any build up of material
from around the grinding disc, the
holding pins, springs and nuts.
Using a Soft Headed Mallet apply
force to the outside edge of the
Quick Release tools hitting the tools
inwards. When hitting the tool be
careful not to hit the diamond or the
metal bonding. Repeat for rest of
tools on the Machine.
To replace simply slide the Quick
Release tools into the Taper Slot.
Apply force with use of a soft
headed mallet striking the tools
outwards. Repeat for remaining
tools.
Remove the weight from the handle
bar and/or remove the security rope.
Carefully return the machine to its
upright position and move the handle
bar to is normal working position and
secure with the two pins.
Plate Removal:
Push down on one of the holding
pins nuts by hand and rotate the pin
90deg, repeat with the two pins.
Remove the disc.
Note that the centres of the discs are
different depending on the direction
the discs rotate:-
(Flower Part No 365.5835F)
(Triangle Part No 365.5835T)
Refit the Tool Plates, these can only
be fitted onto the correct hub.
Push down on one of the holding
pins nuts by hand and rotate the pin
90deg, repeat with the two pins.
Ensure that the pin has located into
its recess, and that the disc is
secure.
Repeat with the other plates.
Re-adjust the dust cover rubber ring.
Shut Down
Simply Press the Black „STOP‟
Button.
After the machine has completely
cooled, clean off any concrete dust
from external components and
remove any heavy build up of
concrete dust from inside the front
dust skirt.
Take care when using hoses or
pressure washers and clean within
the dust skirt area only.
Do not hose down any of the
external surfaces.
Do not to allow water to be directed
at or splashed onto the electric
motor or any of the electrical
components.
Once clean and dry, cover the
machine to protect it and store the
grinder in a dry place.
Grinding Tool
Replacement
Switch off the machine and allow the
grinding head tools to cool
completely, disconnect machine
from its power supply.
IMPORTANT
Do not use a mix of old and new
grinding tools, this will cause rapid
wear of the new tools and could
cause the machine to become
uncontr ollable, un stable an d
dangerous in use.
Drain all water from the tank.
Place the machine on a flat and level
surface.
Remove the additional weight from
the machine if fitted.
Remove the retaining pin from the
handle bar height adjustment pin
and raise the handle bar to a near
upright position (vertical).
Replace the adjustment pin and
secure with the retaining pin.
Old Screw Fit System:
After removing the plate from the
machine (Using the steps provided
previously).
Remove the three star screws
retaining each of the tools to the
disc.
(Torx or TX male (size 30 bit))
Replacement is the reverse of
stripping, the diamond tools are
handed and cannot be fitted the
wrong way round.
Tighten the tool screws initially by
hand, finally tighten using a wrench,
do not over tighten.
Belt:
A belt replacement guide can be
f o u n d o n l i n e a t h t t p : / /
trelawnyspt.com/ or can be sent by
request
Machine Storage
Long period storage:
over 3months
Allow the machine to cool
completely.
Clean outside of machine.
Remove any build up of material
from inside of grinding disc area.
Inspect the grinding tools for wear;
replace any worn parts as required.
Ensure that the machine is
completely dry.
Cover the machine to protect it.
Store the machine in a dry place.

Exploded View - Gear Box
.

Item Part No Description Item Part No Description
1 365.2250K Central Axis Bearing Support - Bottom 02A 365.2250J Axis Bearing Support - Top
3 365.2248D Axis Seal Support 02B 365.2250A Axis Bearing Support - Bottom
4 365.2255D Axis Cover B01 365.2250B Axis Bearing - Top
5 365.2248G Central Axis Cover B02 365.2250L Centeral Axis Bearing Bottom
6 365.2255F Central Axis Seal Support B03 365.2250Q Central Axis Bearing Top
7\8 365.2250P Central Pulley G03 365.2248E Gasket Ø110 x Ø 52
9 365.2250R Central Axis Bearing Support - Top G04 365.2255C Gasket Ø110
10 365.2250O Central Axis G05 365.2248H Gasket Ø120
11 365.2250D Axis G06 365.2255E Gasket Ø200 x Ø 116
18 365.2248F Box Bottom Plate S01 853.0816 CS Head Screw M8 x 16
19 365.2255B Box Top Plate S02 853.0830 CS Head Screw M8 x 30
20 365.2255A Box Cylinder S03 852.0616 Button head Screw M6 x 16
38 365.2250N Central Axis Pulley S04 853.1025 CS Head Screw M10 x 25
39 365.2250C Axis Pulley
40 365.2250G Tension Block Top Plate
41 365.2250H Tension Block Spacer
42 365.2250I Tension Block Bottom Plate
43 365.2250F Tension Roller
44 365.2250E Tension Roller axis-1
45 365.2248A Tension Block Cover
47 365.2250M Tension Roller Axis-2
61 365.9137 Main Belt
62 365.9138 Top Belt
63 365.2248B Oil Seal Ø 52 x Ø 25 x 8
64 365.2248C Oil Seal Ø 62 x Ø 45 x 9
Exploded View - Gear Box

Exploded View - Plate Holder

Parts List - Plate Holder
ITEM No Part No Description
32 365.2260H Driving Disk Ring
33 365.2260I Driving Disk - Coupling
51 365.2260G Driving Disk- Stud Ring
52 365.2260K Driving Disk Base
54 365.2260L Disk Holding Pin
64 365.2248C Oil Seal Ø 62 x Ø 45 x 9
31A 365.2260A Axis Coupling
31B 365.2260B Frictional Disk
31C 365.2260C Drive Coupling
31D 365.2260D Compress ring (2 piece set)
31E 365.2260E Torque Cover
53A 365.2260M Driving Disk - Central Block 1
53B
365.2260N
Driving Disk - Central Block 2
AV1 365.9146A Anti-Vibration Element 1
AV2
365.9146B
Anti-Vibration Element 2
AV3 365.9146C Anti-Vibration Element 3
AV4
365.9146D
Anti-Vibration Element 4
K01 365.2260F Keyway
L01 365.2260J Compress Spring for disk holding pin
S01 853.0816 CS Head Screw M8 x 16
S09
831.1030
Hexagon H.T. Bolt M10 x 30
S10 853.0616 CS Head Screw M6 x 16
S11 824.0600 Anti-Vibration Nut M6
S12 824.0800 Anti-Vibration Nut M8

Exploded View - Machine Assembly
T01
T02
T03
T05

Parts List - Machine Assembly
ITEM No Part No Description
13- 15 365.2230A Motor Support
16 365.2230B Holding Block
17 365.2230C Dust Cover Support
21 365.2225 Dust Cover
36 365.2242 Oil Seal Ø120 x Ø150 x 12
37 365.2243 Oil Seal Ø130 x Ø160 x 12
12A 365.2241A Motor Coupling part on Motor Shaft
12B 365.2241B Flex Element
12C 365.2241C Motor Coupling part on Central Axis
Motor 365.9575 Motor
S05 852.0812 Button Head Screw M8 x 12
S06 806.0650 Socket Cap Screw M6 x 50
S07
853.0825
CS Head Screw M8 x 25
S08 831.1230 Hexagon H.T bolt M12 x 30
T01
365.2235
Handle
T02 365.2220 Water Container
T03
365.2200
Frame
T04 365.2219 Wheel

Electrical Control Box - Parts
Part Part No Description
M22-A
365.9570A
Fixing Adaptor
M22-K01
365.9570B
Contact Block
M22-K10
365.9570C
Contact Block
M22-LED-W
365.9570D
LED Element
M22-PV
365.9570E
Emergency Stop Button
M22-XZK-GB99
365.9570F
E-stop label 33x50mm
M22-WRK3
365.9570G
3 Position 60° Rotary
Switch
M22-R4K7
365.9570H
Rotary Potentiometer
M22-DDL-WS-X1/X0
365.9570I
Start/Stop Button
M22-T-DD
365.9570J
Transparent diaphragm

FAULT CAUSE
Machine does not start. Check that the stop button on the control panel is in the up position.
Check the electricity connections between the machine and the electricity supply is
secure.
Check that the fuse(s) at the mains outlet haven‟t blown.
Check that the circuit breaker switches inside the electric box are in the “on” position.
Check the connections between the frequency controller and the motor.
Machine stops. Check that the circuit breaker switches inside the electric box are in the “on” position.
Check that the cable isn't warm. If so, check wire diameter section is correct.
Check if there is a signal of failure on the screen of the frequency converter (See below).
Grinder is slow or erratic. Check for heavy build up of dirt on the grinding disk.
Check that the segments are not worn down and that they are securely fixed to the disk.
The grinding discs turn, but
the main disc is stationary. The top belt has broken, contact your nearest reseller.
The motor runs but nothing
turns underneath. The main belt has broken, contact your nearest reseller.
If problem has not been cured by any of the above actions, contact your local Trelawny SPT dealership for assistance.
Fault Finding
FREQUENCY CONVERTER
MONITOR ERROR CODES
Do not investigate any electrical problem on this machine unless you are a
qualified electrician, a separate manual is available for this control box.

TECHNICAL SPECIFICATIONS
(k) ** Equals the factor of uncertainty, which allows for variations in measurement and production. Vibration Data figures are tri-axial, which gives the
total vibration emission. Because of various factors, the range of vibration from these tools may vary 1.6m/s2& 5m/s2. The vibration is dependent on
the task, the operators grip and power source etc.
NOTE: The above vibration levels were obtained from tri-axial measurements to comply with the requirements of “The Control of Vibration at Work
Regulations 2005*” and the revisions to the (8662) now EN ISO 28927:2012 and EN ISO 20643:2005 series of standards. These values are at least
1.4 times larger than the values obtained from single axis measurements.
*Based on European Union Council Directive 2002/44/EC (Physical Agents (Vibration) Directive)
This tool has been designed and produced in accordance with the following directives:
2006/42/EC Machinery Directive
2006/95/EC Low Voltage Directive
If your company has any problem with our products or would like to discuss the possibility of an improvement being made to them, then please do not
hesitate to contact us. Your comments are both important and appreciated.
Trelawny SPT Ltd
Trelawny House, 13 Highdown Road, Sydenham Industrial Estate, Leamington Spa, Warwickshire,
CV31 1XT, United Kingdom
Telephone: +44 (0)1926 883781
Fax: +44 (0)1926 450352
Email: sales@trelawny.co.uk
Website: www.trelawnyspt.com
© TSPT UK 2009 Part No: 735.6650 issue 3
SURFACE PREPARATION TECHNOLOGY
All rights reserved. Any unauthorised use or copying of the contents or part thereof is prohibited.
This applies to trademarks, model denominations, part numbers and drawings.
Use only genuine Trelawny spares.
The use of non-Trelawny spare parts invalidates the warranty.
Height (Handle in working position) 83mm(Lower) & 108mm(Higher) 32.5”(Lower) & 42.5”(Higher)
Height (Handle in raised position) 1920 mm 75.6”
Width 700 mm 27.5”
Length 1220 mm 48”
Cutting width 650 mm 25.5 inch
Average depth of cut (dependent on concrete) 1 mm
Disc rpm (Variable) 300 to 1400 rpm
Working distance from wall 40 mm 1.58”
Water tank capacity 40 litres (8.5 galls)
Weight 260kg 573lbs
Electric Motor
Dual voltage 7.5kW 400v 50/60hz
Noise LwA SWL 87.2 dB (A)
Vibration (AEQ) at the Handle Bar a=1.97 m/s2 (K= +40% -0%)
Noise level measured in accordance with EN ISO 15744: 2008
Vibration measured in accordance with EN ISO 28927:2012
EN ISO 20643:2005
Other manuals for TPG650
1
Table of contents
Other Trelawny Floor Machine manuals
Popular Floor Machine manuals by other brands

Kärcher
Kärcher KM 75/40 W P manual
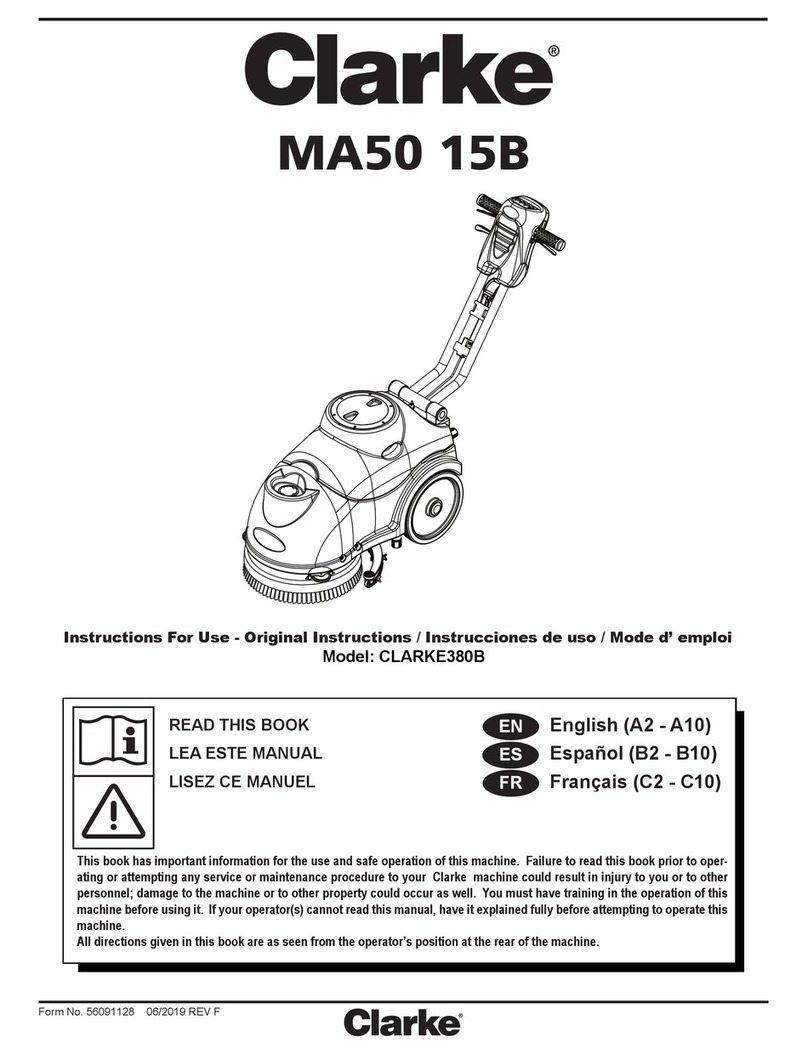
Clarke
Clarke CLARKE380B Instructions for use
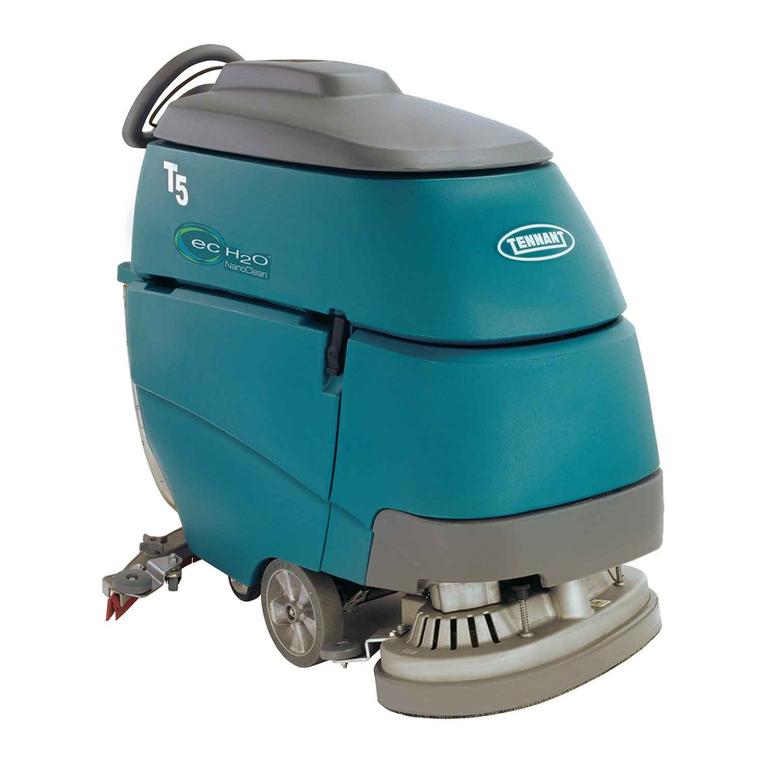
Tennant
Tennant T5 Service information manual
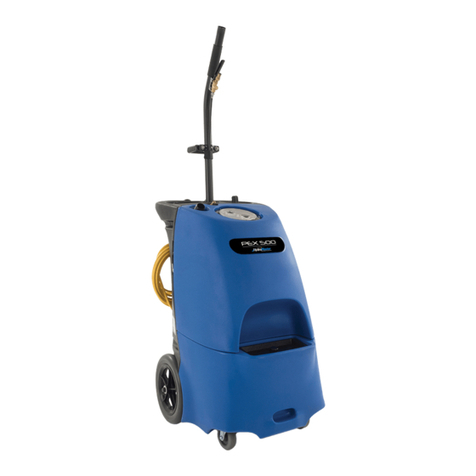
U.S. Products
U.S. Products PEX 500 Information and operating instructions
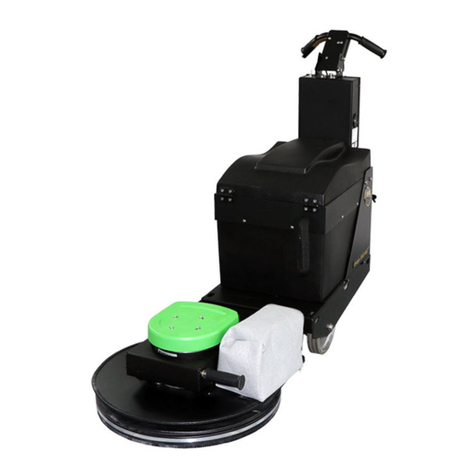
NSS
NSS CHARGER 2022 ABLT Operation manual
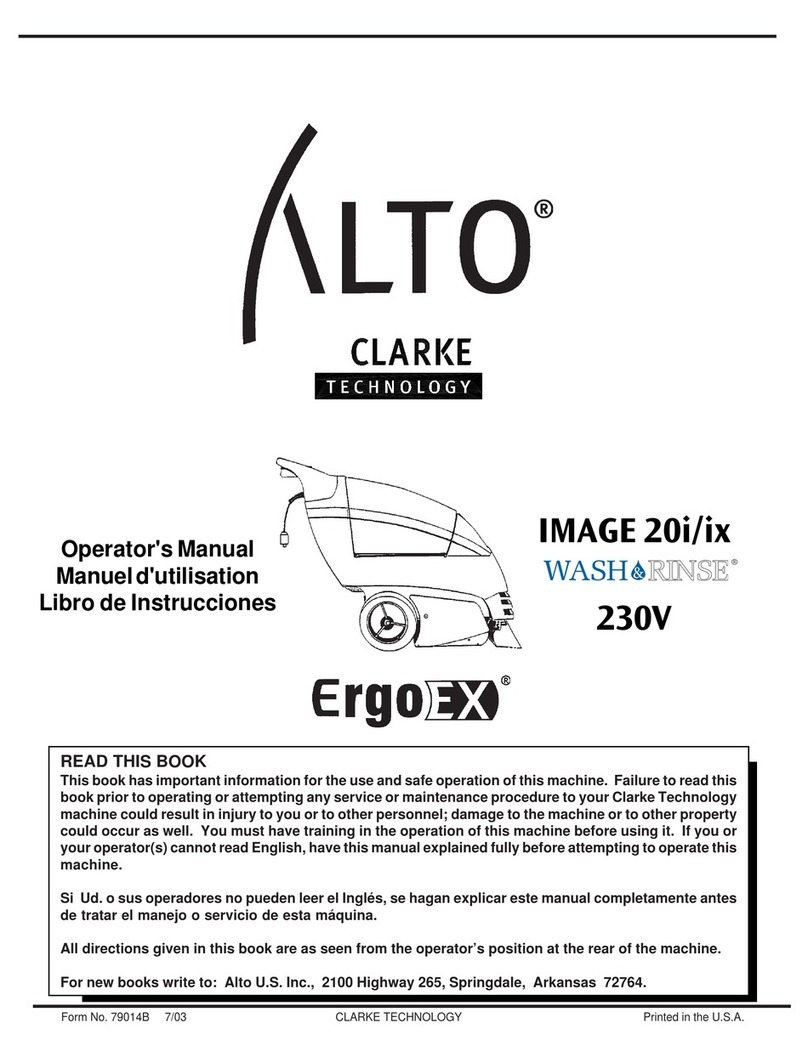
Clarke Technology
Clarke Technology Alto IMAGE 20i ErgoEX Operator's manual