Trio MC302X Product manual

Motion Coordinator Technical Reference Manual
Introduction 1-1
CHAPTER
CHAPTER 0INTRODUCTION

1-2 Introduction
Trio Motion Technology

Motion Coordinator Technical Reference Manual
Introduction 1-3
Trio Motion Technology’s range of Motion Coordinator products are designed to
enable the control of industrial machines with a minimum of external compo-
nents. The products may be combined to build a control system capable of driving
a multi-axis machine and its auxiliary equipment. The Motion Coordinator system
described in this manual allows you to control up to 24 servo or stepper motors,
Digital I/O and additional equipment such as keypads and displays from a single
master. Up to fifteen masters can be networked together using the Trio fibre optic
network allowing up to 360 axes of control. The controller is programmed using
the Trio BASIC programming language. This may be used to build stand-alone pro-
grams or commands can be sent from an external computer.
Typical System Configuration
The
Motion
Coordinator system is modular, allowing the user to tailor the controller
to their specific needs, but also allowing the flexibility to incorporate new modules if
needs should change.
ENCODER V+ V- R 0v
8
9
10
11
12
13
14
15
0
OK
AB
STA
1
2
3
4
5
6
7
SERIAL
BAT
5 4 3 2 1
9 8 7 6
MOTION
TECHNOLOGY
IO8
IO9
IO10
IO11
IO12
IO13
IO14
IO15
I 0
I 1
I 2
I 3
I 4
I 5
I 6
I 7
24v
0v
A1
A0
A-
B
0
1
2
3
4
5
6
7
8
9
10
11
12
13
14
15
1
2
4
8
16
32
OFF
MS NS
PR
DR
10 11 12 13 14 15 24v Ov98
7654 321 00v 24v
NODE
ADDRESS
CAN16 -I/O
0
1
2
3
4
5
6
7
8
9
10
11
12
13
14
15
1
2
4
8
16
32
OFF
MS NS
PR
DR
10 11 12 13 14 15 24v Ov98
7654 321 00v 24v
NODE
ADDRESS
CAN16 -I/O
7
4
1
-
8
5
2
0
9
6
3
.
Y
N
CLR
PC for Programming
Operator Interface
Motion Coordinator
CAN I/O
Servo Drive
Servo Drive
Motor
Motor
MOTION
TECHNOLOGY
MOTION
TECHNOLOGY
MOTION
TECHNOLOGY

1-4 Introduction
Setup and Programming
Trio Motion Technology
Setup and Programming
To program the
Motion
Coordinator a PC is connected via an RS-232, USB serial or
Ethernet link. The dedicated
Motion
Perfect program is normally used to provide a
wide range of programming facilities, on a PC running Microsoft Windows 2000, XP or
Vista 32bit versions.
Motion Perfect 2
Once connected to the
Motion
Coordinator, the user has direct access to
Trio
BASIC,
which provides an easy, rapid way to develop control programs. All the standard
program constructs are provided; variables, loops, input/output, maths and condi-
tions. Extensions to this basic instruction set exist to permit a wide variety of motion
control facilities, such as single axis moves, synchronized multi axis moves and
unsynchronised multi axis moves as well as the control of the digital I/O.
The
Motion
Coordinator range described in this manual currently consists of the
MC302X, MC206X, Euro 205x, Euro209 and MC224. The MC464 is not covered here, but
will be described separately. These controllers feature multi-tasking BASIC. Multiple
Trio
BASIC programs can be constructed and run simultaneously to make program-
ming complex applications much easier.

Motion Coordinator Technical Reference Manual
Introduction 1-5
Products
Products
The range of Trio
Motion
Coordinator products covered by this manual:
Motion Coordinator Master Controllers
Product
Code Name Description
P192 MC302X Compact, low cost DIN-rail mounting module features 1 1/2
servo or 2 stepper axes. 4 Opto-isolated Inputs and 4 Opto-
isolated I/O channels are built in user serial support RS232/
RS485. Multi-tasking Trio BASIC. I/O CANbus expansion.
P136 MC206X Low cost, high performance DIN-rail mounting controller for 1-8
axes with additional daughter board. 8 Opto-isolated Inputs
and 8 Opto-isolated Input/Output channels,1 Opto-isolated
analogue input, USB and memory stick socket are built in.
Multi-tasking Trio BASIC. I/O CANbus expansion.
P151 Euro
205x For OEM applications, Trio offer a 3U Eurocard format controller
featuring 4 onboard axes plus the option for a further axis via a
standard Trio daughter board. 16 Opto-isolated Inputs and 8
Opto-isolated Output channels are built in. Multi-tasking Trio
BASIC. I/O CANbus expansion.
P159 Euro 209 For OEM applications, Trio offer a 3U Eurocard format controller
featuring 8 onboard axes plus the option for a further axis via a
standard Trio daughter board. 16 Opto-isolated Inputs and 8
Opto-isolated Output channels are built in. Multi-tasking Trio
BASIC. I/O CANbus expansion. Motion Perfect programming via
Ethernet ports.
P170 MC224 Flexible high performance master controller for 1-24 axes. 8
Opto-isolated Inputs and 8 Opto-isolated Input/Output
channels, 2 Opto-isolated analogue inputs, USB and memory
stick socket are built in. Multi-tasking Trio BASIC. I/O CANbus
expansion.

1-6 Introduction
Products
Trio Motion Technology
Daughter Boards
The Daughter Board concept is a
one of the key features which
give the
Motion
Coordinator
system enormous flexibility in its
configuration.
The Daughter Boards provide the
interface to many types of Servo
or Stepper Axes, plus a number
of advanced communications
options as well.
There are 19 types of daughter boards currently available:
Product
Code: Name Description
P200 /
P201 Servo Encoder +/- 10v Output, Differential Encoder Input
plus Hardware Registration Input
The Servo Encoder daughter board provides the inter-
face to a DC or Brushless servo motor fitted with an
encoder or encoder emulation.
P210 Servo Resolver +/- 10v Output, Resolver Input
plus Hardware Registration Input
The Servo Resolver daughter board provides the inter-
face to a DC or Brushless servo motor fitted with a
resolver. The resolver port provides absolute position
feedback within one motor turn.
P220 Reference
Encoder Differential Encoder Input
plus Hardware Registration Input
The Encoder daughter board provides an encoder input
without any servo feedback facility for measurement,
registration and synchronization functions on convey-
ors, drums, flying shears, etc.
P225 Analog Inputs 8 x 0 to 10 Volt Analogue Inputs
The Analog Inputs daughter board has 8 x 16 bit inputs
for use as general analog input channels or as feedback
for up to 8 axes. When used for feedback, the A to D is
synchronised to the SERVO_PERIOD.

Motion Coordinator Technical Reference Manual
Introduction 1-7
Products
P230 Stepper Open-collector Step, Direction, Boost and Enable out-
puts
The Stepper daughter board generates pulses to drive
an external stepper motor amplifier. Single step, half
step and micro-stepping drives can be used with the
board.
P240 Stepper
Encoder Open-collector Step, Direction, Boost and Enable out-
puts plus Differential Encoder Input.
The Stepper Encoder daughter board with position veri-
fication has all the features of the simpler stepper
daughter board. Position verification is added to a
stepper axis by providing encoder feedback to check
the position of the motor.
P242 Hardware
Pswitch Differential Encoder Input
plus Hardware Position Switch Outputs
The Hardware PSWITCH daughter board allows 4 open-
collector outputs to be switched ON and OFF at pro-
grammed positions. This function is similar to the
PWITCH command which is implemented in the system
software and allows outputs to be switched ON and OFF
over defined position sectors. The Hardware PSWITCH
daughter board performs the position comparison in
electronic hardware on the daughter board. This allows
the pulses generated to be very accurately timed.
P260 Analogue Out-
put +/- 10v Output with direct DAC control
The Analogue Output daughter board provides a 12 bit
+/-10v voltage output for driving inverters and other
devices. The board is a simplified servo daughter board
and the connections are similar.
P270 SSI Absolute
Servo +/- 10v Output, Differential Encoder Input
plus Hardware Registration Input
The SSI daughter board provides the interface to a DC
or Brushless servo motor fitted axis with an absolute
encoder using the Synchronous Serial Interface (SSI).
Product
Code: Name Description

1-8 Introduction
Products
Trio Motion Technology
P280 Differential
Stepper Differential Line Driver outputs for Step, Direction,
Boost and Enable, plus Hardware Registration Input
The Differential Stepper daughter board is a stepper
daughter board with the output signals provided as dif-
ferential 5 volt signals on a 15 way 'D' connector. The
daughter board does not feature an encoder port for
position verification, but does have a registration input
to allow for capture of the number of step pulses when
a registration signals arrives.
P290 /
P293 CAN Digital Link to CANBus drives
The CAN daughter board provides synchronous control
of up to four axes using the CanOpen protocol. Alterna-
tively, it can be set up as a DeviceNet slave node, or
may use the can directly from Trio Basic.
P291 SERCOS Digital Link to SERCOS drives
The SERCOS daughter board provids digital control to
appropriate servo drives via a Fibre Optic loop. Up to 8
axes can be connected to each P291, which allows the
MC224 to control up to 24 axes.
P292 SLM Digital Link to SLM drives
The SLM daughter board is aimed at providing digital
control channels for servo drives utilising the SLM proto-
col.
P295 USB Interface Universal Serial bus interface for high-speed PC
communications
The USB daughter board provides a high speed interface
between the Euro205x and Euro 209 and a host PC fitted
with a USB port. Support for this high speed interface is
included in Trio's MotionPerfect 2 application and soft-
ware libraries allow developers to support the interface
within their own programs.
Product
Code: Name Description

Motion Coordinator Technical Reference Manual
Introduction 1-9
Products
Custom Daughter Boards
Trio can produce custom daughter boards for specific customer applications where
required.
P296 Ethernet 10 base-T Ethernet interface for TCP/IP networks
The Ethernet daughter board provides a very high speed
interface between the Motion Coordinator and a host
PC fitted with an Ethernet port. Support for Ethernet is
included in Trio's MotionPerfect 2 application and soft-
ware libraries allow developers to support the interface
within their own programs. In addition to this, support
for Modbus TCP is included on the board..
P297 Profibus Profibus Fieldbus Interface
With the Profibus Daughter Board and appropriate soft-
ware on the Motion Coordinator, it is possible to con-
nect to external devices using the Profibus protocol.
P298 Ethernet IP Ethernet IP interface
Adds 1 channel of Ethernet IP server for connection to
PLC’s and other devices supporting Ethernet Common
Industries Protocol (CIP).
Product
Code: Name Description

1-10 Introduction
Products
Trio Motion Technology
I/O Expansion options
MC224 and the P301 Axis Expander
Prod.
Code Name Description
P316 CAN 16 IO DIN Rail mounted 24v I/O expander module pro-
vides 16 opto-isolated channels each of which may
be used as an Input or an Output.
P325 CAN Analog Inputs DIN Rail mounted +/- 10v Analog Input module pro-
vides 8 opto-isolated channels.
P301 Axis Expander Expansion module provides housing for up to 4
additional axis daughter boards. Up to 3 connect to
the MC224 and MC224.
P316 - CAN-16 I/O P325 - CAN-8 Analog Inputs

Motion Coordinator Technical Reference Manual
Introduction 1-11
Products
Operator Interfaces
Name Name Description
P502 Mini-Membrane
Keypad Compact operator keypad/display
P503 Membrane Keypad High performance general purpose operator key-
pad/display

1-12 Introduction
System Building
Trio Motion Technology
System Building
The modules and boards may be mixed within the system rules:
1) Every system must start with one Motion Coordinator master unit as this contains
the processor and logic power supply for the system.
2) The MC224 master unit can house up to 4 daughter boards. The Euro 205x, Euro
209 and MC206X will accept a single daughter board. These can be of any type.
3) The MC224 can have up to 3 axis expander modules added to house up to 16
daughter boards. 4 being housed in the Master and 4 in each of the axis expand-
ers.
4) Up to 16 CAN-16 I/O and 4 CAN Analog Input modules can be connected to any
Motion Coordinator.
Typical System Configuration
ENCODER V+ V- R 0v
8
9
10
11
12
13
14
15
0
OK
AB
STA
1
2
3
4
5
6
7
SERIAL
BAT
5 4 3 2 1
9 8 7 6
MOTION
TECHNOLOGY
IO8
IO9
IO10
IO11
IO12
IO13
IO14
IO15
I 0
I 1
I 2
I 3
I 4
I 5
I 6
I 7
24v
0v
A1
A0
A-
B
0
1
2
3
4
5
6
7
8
9
10
11
12
13
14
15
1
2
4
8
16
32
OFF
MS NS
PR
DR
10 11 12 13 14 15 24v Ov98
7654 321 00v 24v
NODE
ADDRESS
CAN16 -I/O
0
1
2
3
4
5
6
7
8
9
10
11
12
13
14
15
1
2
4
8
16
32
OFF
MS NS
PR
DR
10 11 12 13 14 15 24v Ov98
7654 321 00v 24v
NODE
ADDRESS
CAN16 -I/O
7
4
1
-
8
5
2
0
9
6
3
.
Y
N
CLR
PC for Programming
Operator Interface
Motion Coordinator
CAN I/O
Servo Drive
Servo Drive
Motor
Motor
MOTION
TECHNOLOGY
MOTION
TECHNOLOGY
MOTION
TECHNOLOGY

Motion Coordinator Technical Reference Manual
Introduction 1-13
System Building
System Examples
Example 1
Simplest Possible System - Single MC302X
• 1½ Axis Servo (Servo + reference encoder)
or 2 Axis Stepper
• 8 Channels of 24v I/O on board
- 4 Inputs
- 4 I/O
Example 2
Euro205x, 5 Axis Rack mounted System
The Euro 205x controller provides a
compact rack-mounted controller ideal
for volume OEM applications.
The four internal axes are configured
as stepper axes and connected via the
backplane to third party stepper
drives.
An optional P200 Servo Daughter Board
provides a fifth axis connected to a
servo drive.
•5servoaxes
• 40 Channels of 24v I/O
- 16 in + 8 out on Euro205x, plus
- 16 I/O on CAN-16 I/O expander
P192
012389101124v0vV+V-
AXIS 0
AXIS 1
SERIAL A
SERIAL B
MC302X
OK STATUS
P315
7654321 0
24v
0v
CAN16-I/O
MS
EURO205
CAN-16 I/O

1-14 Introduction
System Building
Trio Motion Technology
Example 3
MC206X - 5½ Axis Servo System
Utilising the four internal axis as servo
axes, an optional servo daughter board
and the reference encoder input to
provide a total of 5 servo axes plus the
reference (master) encoder.
The MC206X has 16 channels of 24v I/O as
standard, this is expanded up to 32
channels with the addition of a CAN-16 I/O
module. 8 Analog Inputs (+/- 10v) are
provided by the CAN Analog Inputs
module.
• 5 servo / stepper axes
• 32 Channels of 24v I/O
- 8 in + 8 I/O on MC206, plus
- 16 I/O on CAN-16 I/O expander
• 8 Analogue Input Channels
Example 4
MC224 - 7 Axis System
The system comprises an MC224 Master
with and additional three axes in the
optional Axis Expander module. The
axes can be any combination of servo
and stepper drives determined by the
daughter boards used.
The MC224 has 16 channels of 24v Digital
I/O as standard, this is expanded up to
32 with the addition of a CAN-16 I/O
module. 8 Analog Inputs (+/- 10v) are
provided by the CAN Analog Inputs
module.
•7axes
- 4 on MC2224 Master, plus
- 3 on Axis Expander
• 32 Channels of 24v I/O
- 8 in + 8 I/O on MC204, plus - 16 I/
O on CAN-16 I/O expander
• 8 Analogue Input Channels
P325
76543210
24v
0v
CAN
ANALOG
INPUTS
MS NS
P315
76543210
24v
0v
CAN 16-I/O
MS
CAN-16 I/O
Axis 0
Axis 1
Axis 2
Axis 3
STATUS
OK
0
1
2
3
4
5
6
7
MC206X
Motion
Coordinator
P136
0v
A
0
1
2345670
v24v 89
10 11 12 13 14 15
E-
A
/A
B
/B
Z
/Z
V-
V0 V1 V2 V3
SERIAL A
SERIAL B
CAN-Analog Inputs
MC206X + Daughter Board
P325
765432
1
0
24v
0v
CAN
ANALOG
INPUTS
MSNS
P315
76543210
24v0v
CAN16-I/O
MS
CAN-16 I/O
Axis Expander
MC224 Motion Coordinator
CAN-Analog Inputs

Motion Coordinator Technical Reference Manual
Introduction 1-15
System Building
Example 5
MC224 - 16 axis system with maximum I/O expansion
The example system illustrated below shows an MC224 controller with the maximum
possible I/O expansion. Applications for a system of this complexity might include
collating or packaging machinery where there are multiple operations performed on a
product and many I/O are used for sensors etc.
•16Axes(Anytype)
• 272 Channels of 24v I/O
- 8 in + 8 I/O on MC224, plus
- 256 I/O (16 * 16) on the 16 CAN-16 I/O modules
• 32 Analogue Input Channels (8 per module)
P325
76543210
24v
0v
CAN
ANALOG
INPUTS
MS NS
P325
765432
1 0
24v
0v
CAN
ANALOG
INPUTS
MS NS
P325
76543210
24v
0v
CAN
ANALOG
INPUTS
MS NS
P325
765432
1 0
24v
0v
CAN
ANALOG
INPUTS
MS NS
P315
7654321 0
24v
0v
CAN 16-I/O
MS
P315
7654321 0
24v
0v
CAN 16-I/O
MS
P315
7654321 0
24v
0v
CAN 16-I/O
MS
P315
76543210
24v
0v
CAN 16-I/O
MS
P315
7654321 0
24v
0v
CAN 16-I/O
MS
P315
7654321 0
24v
0v
CAN 16-I/O
MS
P315
7654321 0
24v0v
CAN 16-I/O
MS
P315
76543210
24v
0v
CAN 16-I/O
MS
P315
76543210
24v
0v
CAN 16-I/O
MS
P315
76543210
24v
0v
CAN 16-I/O
MS
P315
7654321 0
24v
0v
CAN 16-I/O
MS
P315
7654321 0
24v
0v
CAN 16-I/O
MS
P315
7654321 024v
0v
CAN 16-I/O
MS
P315
765432
10
24v0v
CAN 16-I/O
MS
P315
7654321 0
24v0v
CAN 16-I/O
MS
P315
7654321 0
24v
0v
CAN 16-I/O
MS
CAN-16 I/O
Axis Expanders
MC224 Motion Coordinator
CAN-Analog Inputs

1-16 Introduction
System Building
Trio Motion Technology
Features and Typical Applications
Trio
BASIC contains accurate motion control functions for the generation of complex
movements of various types, including:
• Linear interpolation of up to 24 axes
• Circular and helical interpolation
• Variable speed and acceleration profiles
•Electronicgearboxes
• Electronic cam profiles
The operator interface may be achieved by any combination of the following:
• Dedicated host computer (connected via USB, Ethernet or RS-232 serial port)
• Membrane Keypad with Vacuum Fluorescent Display
• Dedicated Operator Panel using the’Modbus’ serial protocol.
• Switches / Thumbwheels
•Statuslamps
The system is able to control a wide range of mechanisms and equipment including:
• Brushless servo motors
•Steppermotors
• Brushed DC servo motors
• Hydraulic servo valves
• Hydraulic proportional valves
• Pneumatic/hydraulic solenoids
•Relays/contactors
Typical applications:
• Cut to length • Coil winding • Automotive welding
• Flying shears • Laser guidance • Spark erosion
• Glue laying • Electronic assembly • Drilling
• Web control • Printing • Milling
• Tension control • Collating
• Pick & Place • Packaging • YOUR application

Motion Coordinator Technical Reference Manual
Introduction 1-17
System Building
The Trio Motion Technology Website
The Trio website contains up to the minute news, information and support for the
Motion
Coordinator product range.
Website Features
•LatestNews
•ProductInformation
• Manuals
• Support Software
• System Software Updates
• Technical Support
• User’s Forum
• Application Examples
• Employment Opportunities
WWW.TRIOMOTION.COM

1-18 Introduction
System Building
Trio Motion Technology
Other manuals for MC302X
1
This manual suits for next models
4
Table of contents
Other Trio Controllers manuals
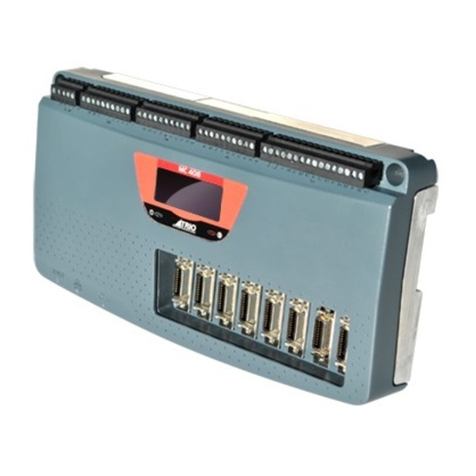
Trio
Trio MC508 P848 User manual
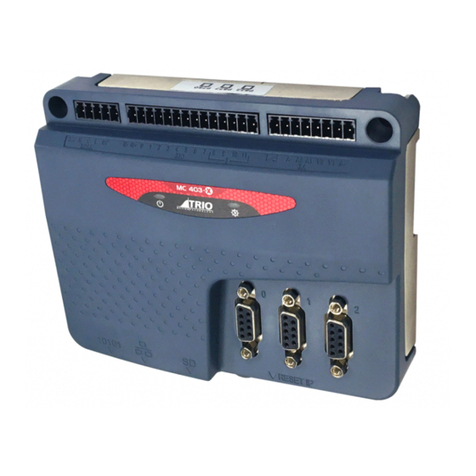
Trio
Trio MC403-X User manual
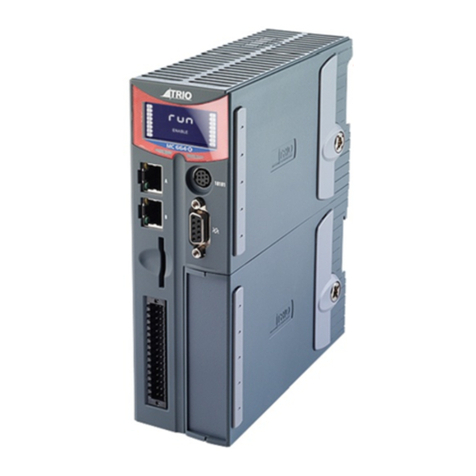
Trio
Trio MC664 User manual
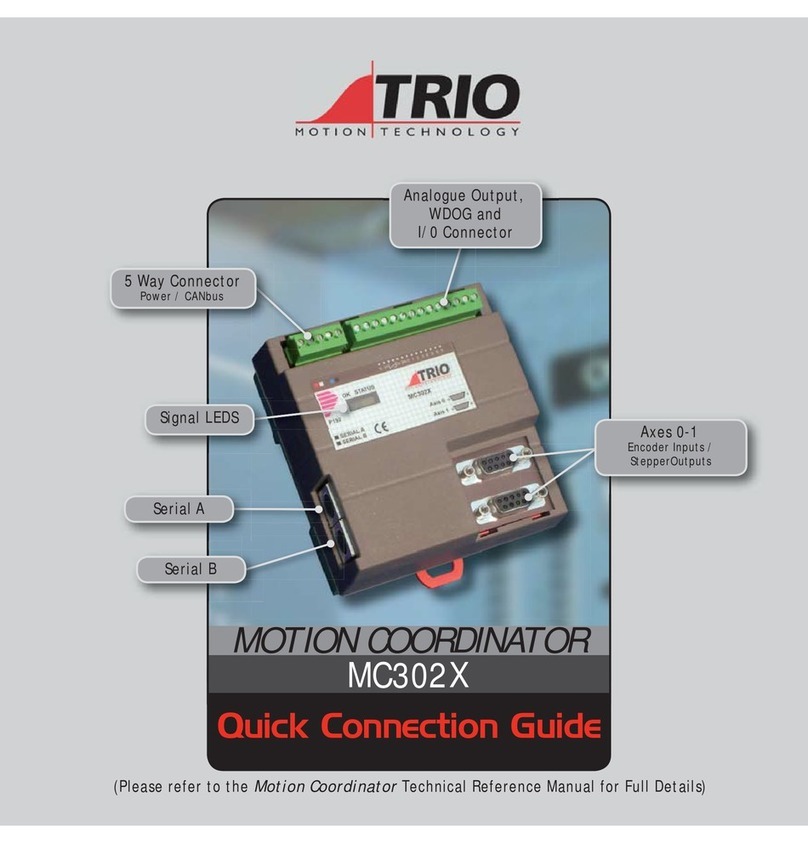
Trio
Trio MC302X Instruction Manual
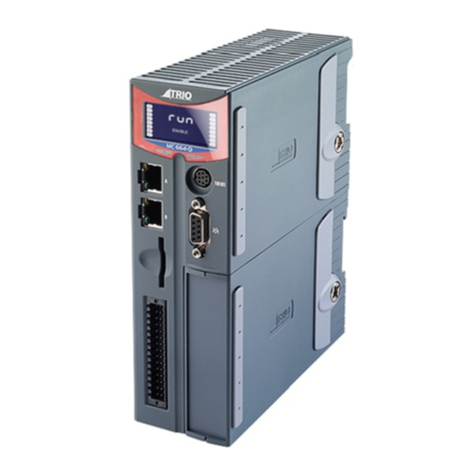
Trio
Trio MC664 Instruction Manual
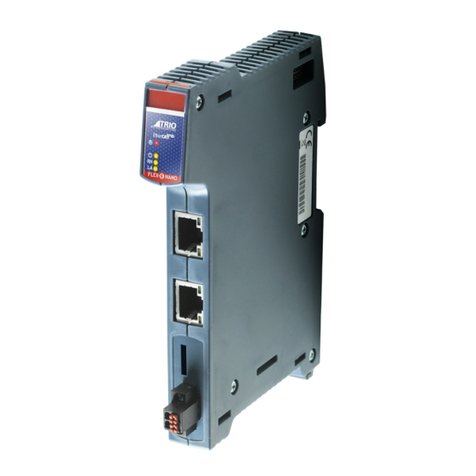
Trio
Trio Flex-6 Nano P601 User manual
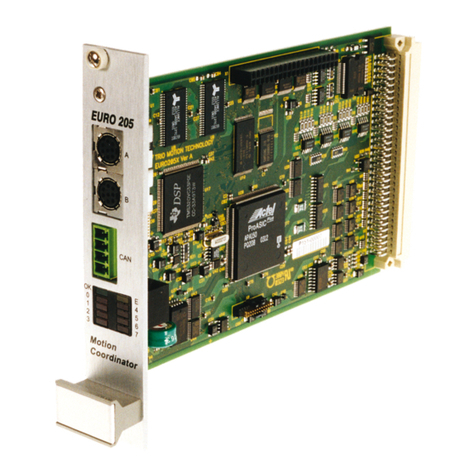
Trio
Trio Motion Coordinator MC216 Product manual
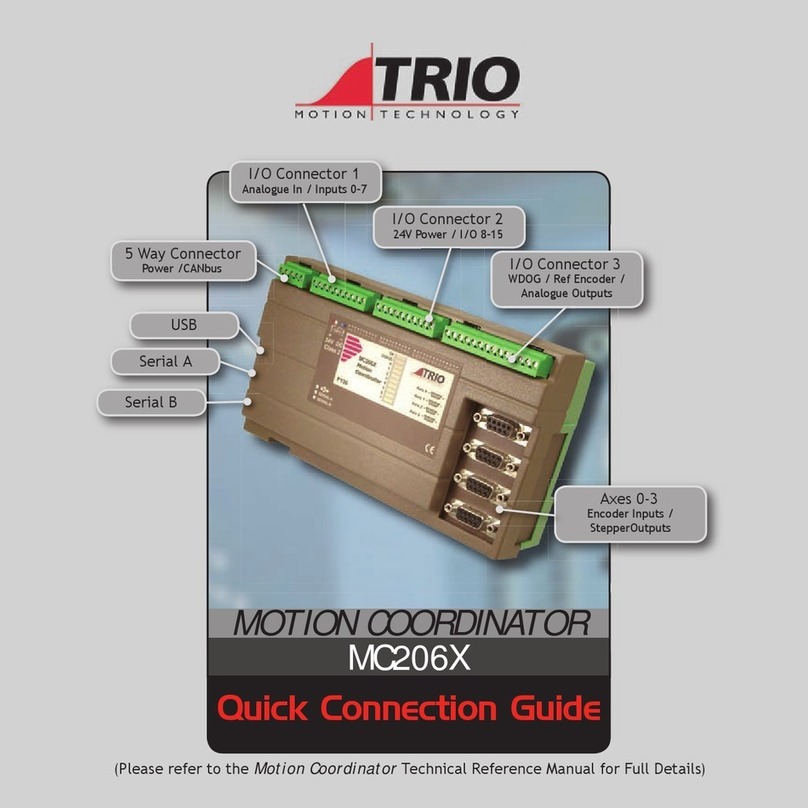
Trio
Trio MC206X Instruction Manual

Trio
Trio MC508 Instruction Manual
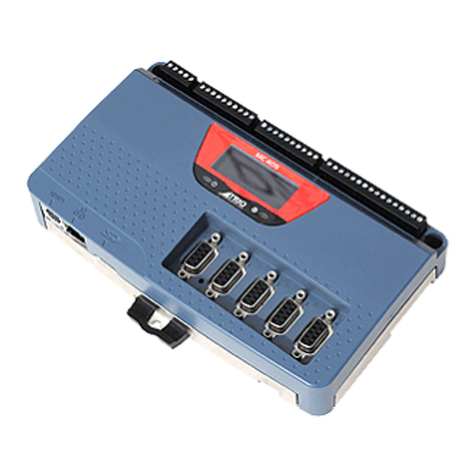
Trio
Trio MC405 Instruction Manual