Tritech SeaKing User manual

SeaKing & SeaPrince Imaging Sonars
0374-SOM-00001, Issue: 08 1 © Tritech International Ltd.
SeaKing & SeaPrince
Imaging Sonars
Product Manual
0374-SOM-00001, Issue: 08

SeaKing & SeaPrince Imaging Sonars
0374-SOM-00001, Issue: 08 2 © Tritech International Ltd.
© Tritech International Ltd
The copyright in this document is the property of Tritech International Ltd. The document is supplied by Tritech International Ltd on
the understanding that it may not be copied, used, or disclosed to others except as authorised in writing by Tritech International Ltd.
Tritech International Ltd reserves the right to change, modify and update designs and specifications as part of their ongoing
product development programme.
All product names are trademarks of their respective companies.

SeaKing & SeaPrince Imaging Sonars
0374-SOM-00001, Issue: 08 3 © Tritech International Ltd.
Table of Contents
Warning Symbols ........................................................................................................ 4
1. Introduction ............................................................................................................. 5
2. Getting Started ....................................................................................................... 6
3. Installation .............................................................................................................. 9
3.1. General Overview ........................................................................................ 9
3.2. Seanet Pro Software .................................................................................... 9
3.3. Installing the Sonar Head ........................................................................... 10
3.3.1. SeaKing Communication Configuration ............................................. 10
3.3.2. Subsea Sensor Electrical Installation ................................................ 11
3.3.3. Ground Fault Monitoring Equipment .................................................. 11
3.4. Waterblock Pin-out Diagram ....................................................................... 12
4. Setup .................................................................................................................... 13
4.1. Identifying the Model .................................................................................. 13
4.2. Changing Configuration for Serial or ARCNET ............................................. 14
4.3. Changing Configuration for Ethernet ............................................................ 15
5. Operation .............................................................................................................. 17
5.1. Basic Principles .......................................................................................... 17
5.2. Operating the SeaKing & SeaPrince in Seanet Pro ....................................... 18
5.2.1. Main Screen .................................................................................... 18
5.2.2. Sonar Settings ................................................................................. 19
5.2.3. Main Menu ...................................................................................... 20
5.2.4. Measurement Tool ........................................................................... 24
5.2.5. Dynamic Range and Sonar Rx Indicator ........................................... 25
5.2.6. Application Tools ............................................................................. 26
6. Maintenance ......................................................................................................... 32
6.1. After using the sonar .................................................................................. 32
6.2. If storing the sonar for extended periods ...................................................... 32
6.3. SeaKing regular maintenance ..................................................................... 32
6.3.1. Disassembly of the SeaKing unit ...................................................... 33
6.3.2. Reassembly of the SeaKing unit ....................................................... 35
6.4. Super SeaPrince regular maintenance ......................................................... 36
6.4.1. Disassembly of the Super SeaPrince unit .......................................... 37
6.4.2. Reassembly of the Super SeaPrince unit .......................................... 38
7. Troubleshooting .................................................................................................... 39
A. Help & Support ..................................................................................................... 40
B. Specification ......................................................................................................... 41
B.1. SeaKing ..................................................................................................... 41
B.1.1. SeaKing Dimensions ....................................................................... 41
B.1.2. SeaKing Physical Properties ............................................................ 42
B.1.3. SeaKing Acoustic Properties ............................................................ 42
B.1.4. SeaKing Display Characteristics ....................................................... 42
B.1.5. SeaKing Electrical and Communication ............................................ 42
B.2. SeaPrince .................................................................................................. 43
B.2.1. SeaPrince Dimensions .................................................................... 43
B.2.2. SeaPrince Physical Properties ......................................................... 43
B.2.3. SeaPrince Acoustic Properties ......................................................... 44
B.2.4. SeaPrince Display Characteristics .................................................... 44
B.2.5. SeaPrince Electrical and Communication .......................................... 44
C. ARCNET Termination ........................................................................................... 45
D. CHIRP Signal Processing ..................................................................................... 46
E. SeaKing Sonar & Profiler Connector Options ......................................................... 48
F. Super SeaPrince External Reset ........................................................................... 49
G. V6 COM PCB Reset ............................................................................................ 51
Glossary ................................................................................................................... 53

SeaKing & SeaPrince Imaging Sonars
0374-SOM-00001, Issue: 08 4 © Tritech International Ltd.
Warning Symbols
Throughout this manual the following symbols may be used where applicable to denote any
particular hazards or areas which should be given special attention:
Note
This symbol highlights anything which would be of particular interest to the reader
or provides extra information outside of the current topic.
Important
When this is shown there is potential to cause harm to the device due to
static discharge. The components should not be handled without appropriate
protection to prevent such a discharge occurring.
Caution
This highlights areas where extra care is needed to ensure that certain delicate
components are not damaged.
Warning
DANGER OF INJURY TO SELF OR OTHERS
Where this symbol is present there is a serious risk of injury or loss of life. Care
should be taken to follow the instructions correctly and also conduct a separate
Risk Assessment prior to commencing work.

SeaKing & SeaPrince Imaging Sonars
0374-SOM-00001, Issue: 08 5 © Tritech International Ltd.
1. Introduction
The SeaKing and SeaPrince sonar "system" would consist of the sonar head, the Tritech
International Ltd Seanet Pro control and display software and either a Surface Control Unit
(SCU) or SeaHub. This manual deals with the sonar head and any specific aspects of Seanet
Pro that are necessary to get a system working. For more details of Seanet Pro please refer to
the Seanet Pro Software Manual and further details of the SeaHub or SCU can also be found
in their respective manuals (all current manuals are available on www.moog.com/tritech).
The Seanet Pro software is Windows based and provides control of the complete range of
sonars that Tritech International Ltd produce. It is also possible to display multiple devices
within Seanet Pro and as such two or more sonars can be networked together and displayed
on one computer.
The SeaKing and SeaPrince sonar head is typically configured to communicate with the SCU
or SeaHub using the ARCNET LAN telemetry protocol. This is the standard protocol that is
used in all SeaKing devices and provides a high bandwidth at a default communications rate
of 156kbit·s-1. It is also possible to reconfigure sensors to communicate at a lower baud rate
or using serial protocols (such as RS232).
The DST SeaKing DFS & Super SeaPrince sonar heads have the following features:
Scan rate The heads can achieve a very fast scan rate which gives
faster target acquisition, and helps in obstacle avoidance.
Dual Frequency Operation
(SeaKing only)
The SeaKing DFS can use up to two operating
frequencies - one giving long range target acquisition
characteristics and the other giving shorter range, higher
definition, imaging capability. It is effectively two sonar
heads in a single housing.
Protected transducer The SeaKing has a semi-rigid rubber boot and the
SeaPrince units have a rigid plastic boot, both are oil filled
and offer protection of the transducer head. The unit has
no rotating seals to be damaged or wear.
Electrical Connection The SeaKing and SeaPrince heads use a Tritech
International Ltd 6 pin underwater connector but can be
fitted with an alternative connector on request.

SeaKing & SeaPrince Imaging Sonars
0374-SOM-00001, Issue: 08 6 © Tritech International Ltd.
2. Getting Started
This section will detail the basic steps required in order to connect up your Tritech Sonar for
the first time to your surface controller (typically a Tritech SCU, PC or Laptop).
A standard Sonar system will comprise of the following elements:
• The Sonar unit - Super SeaKing or Super SeaPrince in this instance
• The Build Record Sheet - This contains detailed information on the configuration and pin
outs specific to this unit
• Accessory kit - this will contain extra o-rings and screws. Depending on the Sonar unit it
may also contain additional items
• Software and Manual CD - This holds a copy of all commercially released Tritech software
as well as electronic copies of manuals for Tritech International Ltd products
• Cable whip - this is an optional item, but is usually supplied for units fitted with a standard
Tritech International Ltd connector
Ensure that the surface controller has Seanet Pro installed onto it, using the supplied CD if
necessary. The CD will contain a version of Seanet Pro that would have been appropriate
at the time of the manufacture of the Sonar unit, but for the latest version it is recommended
that the Tritech website be checked: www.moog.com/tritech
Before attempting to connect up the Sonar with a test cable, check the communications
setting of the Sonar either by referring to the label on the unit - or by checking the Build
Record Sheet.
Once the setup of the Sonar is confirmed, use the cable whip (if supplied) to create a test
cable. Depending on the setup of the Sonar, differing cable wiring may be required:
ARCNET

Getting Started SeaKing & SeaPrince Imaging Sonars
0374-SOM-00001, Issue: 08 7 © Tritech International Ltd.
RS232 or RS485
Note: The wiring detailed above is for the SCU, SeaHub or MicronNav Hub. If using a third
party RS485 adapter please check the pin outs required as the RS485 A and RS485 B
pins may be configured differently.
Using the test cable, connect the Sonar unit to your surface controller. Your surface controller
can be a SCU, SeaHub, MicronNav Hub or a PC with a RS232 or RS485 port.
Run Seanet Pro and, if working over a serial interface, configure the serial ports using the
Utilities->Com Setup drop down menu option.
For the COM Port being used, ensure that an AIF device has been enabled.
Select the Applications->Setup drop down menu option.

Getting Started SeaKing & SeaPrince Imaging Sonars
0374-SOM-00001, Issue: 08 8 © Tritech International Ltd.
The Node table should display the Node of the connected Sonar (normally Node 2, but the
label on the unit should state what it has been set to) There may also be additional nodes,
depending on how the system is all connected. A SCU or SeaHub will appear as Node 252,
whereas a MicronNav Hub will appear as Node 90.
The Status of the Sonar Node should be OK.
If the Status is UNKNOWN check the following: For RS232 wiring Pin 5 is properly connected
For all wiring The main comms pins (1 and 2 on the waterblock) are wired correctly and have
not been crossed
With the Status showing as OK, select the Applications->Single Sonar option
The data screen will report a centering message, as part of the Sonar boot up, then will start
to scan.
It is recommended that the Super SeaKing Sonar is only run in air for short periods (1 hour
maximum) as the unit will become hot to the touch without a body of water to help dissipate
the heat.

SeaKing & SeaPrince Imaging Sonars
0374-SOM-00001, Issue: 08 9 © Tritech International Ltd.
3. Installation
3.1. General Overview
The SeaKing and SeaPrince heads are supplied with a waterblock fitted to the device and as
standard a proprietary connector usually referred to as the "Tritech 6-Way Connector". Other
connectors are available (see Appendix E, SeaKing Sonar & Profiler Connector Options) and
various lengths of test cable can be supplied with the connector. For more details contact
Tritech International Ltd.
The waterblock is fastened to the body tube of the head, and provides a 4000m rated
pressure bulkhead. This will protect the electronics from water ingress in case the connector
is damaged or not fitted correctly. The connector may be disconnected from the heads by
unscrewing the four securing screws.
Note
It is not necessary to remove the water block when removing the connector
or taking the head apart. Whilst the connector is removed from the head, the
blanking plugs supplied should be fitted to prevent the ingress of dirt or moisture.
3.2. Seanet Pro Software
Warning
SeaPrince Sonars with serial numbers 318289 and above incorporate the Mod
B improvements and updated firmware. If being used with Seanet Pro version
V2.24 dated prior to Feb 2020 do not “Update” the firmware as this will install a
previous version and may render the unit inoperable.
It is recommend that the Seanet Pro software be updated to V2.24 dated
03/02/2020 available from the Tritech website and contained on Rev 3 of the
Software and Manuals USB (0084-SOF-00002).
Should the previous version of firmware be loaded onto the SeaPrince Sonar
connection of the unit to an installation of Seanet Pro V2.24 (03/02/2020) will
allow the firmware to be updated to the correct revision.
The Seanet Pro Windows software will be provided either on an Installation CD-ROM (for
SeaHub interface to user computer) or pre-installed on the Seanet SCU.
For the CD-ROM Installation, if Setup does not auto-run on disc insertion, run the
SETUP.EXE file from the disc to start the installation.
Note
A DST SeaKing or SeaPrince sonar head will not work with the SONV3
application or run on a SCUv3

Installation SeaKing & SeaPrince Imaging Sonars
0374-SOM-00001, Issue: 08 10 © Tritech International Ltd.
3.3. Installing the Sonar Head
Caution
Although the sonar heads are rugged, they should be handled with care,
particularly the connector and transducer.
The heads should be secured by clamping on the cylindrical body section such that the
transducer is unimpeded and not shielded. A guard can be fitted over the head to protect
from impact damage but this must not overlap the transducer area or it may have an effect
on the sonar image.
Caution
It is important that no clamping force is applied to the boot.
The clamp should be applied centrally to the aluminium body tube and should not be over-
tightened. Any metallic clamps should be electrically insulated from the sonar body by means
of rubber or plastic strips or mount brackets of at least 3mm thickness and extending at
least 3mm beyond the clamp boundary to reduce any galvanic corrosion effect. Non-metallic
clamps are preferable: if metallic clamps are used they should be painted or lacquered with
at least two or three coatings.
Caution
Avoid any metal alloys containing copper such as brass or bronze.
Care should be taken to mount sonar heads to ensure that they are mounted as close to
the true vertical as possible in relation to the trim position of the vehicle. The front filling plug
and red LED should be aligned with the natural direction of travel of the vehicle. Errors in the
head alignment can give rise to unreliable results.
3.3.1. SeaKing Communication Configuration
Caution
The power should be turned off before making a connection between the sonar
head and surface controller (SCU or SeaHub).
The Sonar head may form part of an ARCNET multi-drop, network of sensors that are
normally interfaced to the Surface Unit through the internal AIF interface PCB (installed in
the SCU) or external SeaHub serial interface module.
Normal communications with the Sonar head is via a customised version of the ARCNET
network system and requires a good quality balanced twisted pair cable. It is possible to
interface the ARCNET to wide band multiplexer systems - contact Tritech International Ltd
for details.
Note
For an ARCNET connection termination resistors need to be fitted at each end
of the umbilical. Refer to Appendix C, ARCNET Termination
The Seanet SCU and SeaKing heads cannot be used with RS232 or RS485 AIF Cards
as used in earlier WINSON based SCU-3 systems. They must be used with SeaKing AIF

Installation SeaKing & SeaPrince Imaging Sonars
0374-SOM-00001, Issue: 08 11 © Tritech International Ltd.
ARCNET cards (AIFV3/V4). Conversely, Series 2 Sonar, Profiler and other heads cannot be
directly used with SeaKing and Seanet systems. Note that the SCUv5 units do not have a
dedicated AIF ARCNET card but instead process the ARCNET data through the SCU main
board. In terms of software and hardware interface though this is exactly the same as uing
an AIF card as in the older SCUv4 units.
An optional RS232 interface can be provided to allow telemetry connection through a fibre
optic system capable of 115kbps transmission. The RS232 interface is available in the
guise of an RS232 to ARCNET converter PCB that is installed in a dry pod on the vehicle.
Alternatively, an intelligent 4000m pressure rated Junction Box will provide the RS232
interface to the network of SeaKing ARCNET devices.
Note
SeaKing units with a V6 COM PCB are capable of using a single-head RS232
or RS485 interface. Older units with a COMv5 PCB, or older, will only be able
to communicate via RS232.
Super SeaPrince units are capable of communicating on all three protocol
options as standard
Refer to the Seanet Pro and Seanet SCU manuals for more information on serial RS232/
RS485 configuration and baud setup.
3.3.2. Subsea Sensor Electrical Installation
If using a rectified transformer PSU, the output of the PSU must have a filter capacitor of not
less than 470μF, for each head being powered. If an unregulated PSU is used, then make
sure that the voltage value measured at the head is in the range 20-36v DC, in power on/off
and running conditions. If powering the head(s) down a long lead or umbilical, the maximum
recommended loop resistance of the power line must not exceed 10Ω for one head, 5Ω for
two heads, and 3Ω for three heads. If the supplied voltage is less than 20V DC (or 12V for
Super SeaPrince DST) the sonar head may not operate correctly.
Caution
Never try to make SeaKing or SeaPrince sonar work down a long cable by
increasing the PSU output voltage above 36V DC (or 56V DC for the high voltage
Super SeaPrince).
3.3.3. Ground Fault Monitoring Equipment
The power supply within SeaKing subsea devices includes an electrically isolated DC-DC
converter front-end, There is a small capacitive connection to the sonar chassis which should
not noticeably affect any impressed current ground fault indicator (GFI) equipment.

Installation SeaKing & SeaPrince Imaging Sonars
0374-SOM-00001, Issue: 08 12 © Tritech International Ltd.
3.4. Waterblock Pin-out Diagram
1
4
6
2
35
Figure 3.1. Tritech
Waterblock
Pin MAIN port AUX port Cable colour
1 RS232 TX
ARCNET A
RS485 A
RS232 RX
ARCNET A
RS485 A
Yellow
2 RS232 Rx
ARCNET B
RS485 B
RS232 TX
ARCNET B
RS485 B
Blue
3 +DC Power Red
4 -DC Power Black
5 RS232 Ground Green
6 Earth/cable shield cable screen

SeaKing & SeaPrince Imaging Sonars
0374-SOM-00001, Issue: 08 13 © Tritech International Ltd.
4. Setup
The SeaKing and SeaPrince sonar heads, when newly purchased, will be setup as requested.
However, should the setup of the units need to be changed the following instructions can be
used to reconfigure the units are desired.
4.1. Identifying the Model
Before proceeding with any reconfiguration, it is vital to know what model of SeaKing Sonar
you are operating with.
SeaKing V5 or older
SeaKing Sonars that are V5 or older models need to be opened in order to change their
configuration. Additionally these Sonars may, or may not have a V6 COMS PCB installed
and so will use physical jumpers to set up the communications options. Please see 0374-
SOM-00003 for jumper configurations as well as V6 COMS PCB DIP switch settings for these
units.
SeaKing V6
A V6 SeaKing Sonar will typically have the part number S06332A, printed on the main product
label. It should also have the V6 Comms box checked on the label.
SeaKing V7
A V7 SeaKing Sonar has a different style of product label from that of the V6.

Setup SeaKing & SeaPrince Imaging Sonars
0374-SOM-00001, Issue: 08 14 © Tritech International Ltd.
4.2. Changing Configuration for Serial or ARCNET
Note
These instructions are intended for units that support software selectable
communications. If you are unsure if your Sonar supports this function, please
check Section 4.1, “Identifying the Model” or contact Tritech International Ltd for
assistance.
To change the configuration of the SeaKing or SeaPrince Sonar, the following steps should
be undertaken:
1. Place the Sonar on a short test cable and connect to your controlling computer (either
directly or via SeaHub / MicronNav Hub / SCU)
2. Using the Applications - Setup ensure that you can see the Node of the Sonar - typically
Node 2
3. In the Action column, click on the down arrow and select Setup
4. Click Ok on the pop up warning and the Sonar Setup page should now appear
5. Select the desired communication options from the MAIN and AUX drop down lists
6. If required, click on the Baud Rates button to open and change the baud rates used by
the ARCNET and serial outputs of the Sonar
7. Once all changes have been made, click Ok to apply the changes
8. The Sonar will now be reprogrammed and will disappear from the Node Table
9. Wait for the Green LED on the Sonar to start flashing, then power it down and disconnect
the test cable
10. Re attach the Sonar to the computer using a new test cable suitable for the new
communications method
11. Power the Sonar back on and, after a brief delay, the Sonar Node number should
reappear

Setup SeaKing & SeaPrince Imaging Sonars
0374-SOM-00001, Issue: 08 15 © Tritech International Ltd.
For Sonars using Ethernet communications, changing the IP Address of the Sonar will not
require a change in test cable - but it will need the computer and Sonar to be on the same
domain in order to establish communications.
4.3. Changing Configuration for Ethernet
Note
Currently only the SeaKing V7 supports Ethernet communications, with the label
showing this option instead of ARCNET.
To change the setup of an Ethernet enabled sonar the following steps should be undertaken:
1. Place the unit on a short test lead directly into the Ethernet port of the controlling computer
2. Change the IP address of the controlling computer to the same domain as the Sonar -
typically in the 192.168.2.xxx range
3. Using the Applications - Setup ensure that you can see the Node of the Sonar - typically
Node 2
4. In the Action column, click on the down arrow and select Setup
5. Click Ok on the pop up warning and the Sonar Setup page should now appear
6. In the Sonar Setup page, click on the COMV7 tab to show the IP settings of the Sonar
7. Enter the new IP Address for the Sonar as required
8. Once all changes have been made, click Ok to apply the changes
9. The Sonar will now be reprogrammed and will disappear from the Node Table
10. If you have changed one of the first three numbers in the IP address, the controlling
computer will need to change its IP domain to match once again
11. If the last number of the IP Address has been updated, the Sonar should be detected
after a short delay

Setup SeaKing & SeaPrince Imaging Sonars
0374-SOM-00001, Issue: 08 16 © Tritech International Ltd.
Note
The SeaKing Sonar uses a set Subnet Mask of 255.255.255.0.

SeaKing & SeaPrince Imaging Sonars
0374-SOM-00001, Issue: 08 17 © Tritech International Ltd.
5. Operation
5.1. Basic Principles
On completion of installation of the sonar on a vehicle, it can be tested in air by powering
up the system and observing that the red LED illuminates as the head scans through the
ahead direction.
As with any active sonar, the SeaKing and SeaPrince sonar heads only show echoes of
objects that reflect sound back to the sonar transducer, such that hard shiny surfaces are
sometimes only seen when they are at right angles to the sonar beam. Rough seabed
textures can blot out smaller targets completely. The plan view also does not show how high
an object is, unless a shadow is cast, in which case the length of the shadow is related to the
height of the object, its range, and the height of the sonar head.
The SeaKing DFS Sonar is normally supplied with two operating frequencies, typically
325kHz and 675kHz. SeaPrince DST heads only have a single operating frequency, typically
675kHz. DST heads use chirped frequencies centred close to these values. The lower 325
kHz frequency is capable of detecting large targets at ranges in excess of 200 metres. The
higher frequency has a narrow horizontal beam and wider vertical beam, for higher detail of
closer targets. Switching between the two operating frequencies is performed by using RAT
button F5 (or the RAT mimic in Seanet Pro). The current operating frequency is indicated in
the F5 panel above the sonar display. If operating on range scales greater than 100 metres,
use the lower frequency for maximum range performance.
Interpretation of sonar data develops with experience. Sonar reflections of isolated small
objects give no indication of shape or attitude. Man-made structures, such as platforms or
rock walls tend to have regular patterns that are easier to identify. Using sonar is rather like
looking at a world made of shiny black plastic, in the dark, with only a narrow torch beam for
illumination. Remember that when close to large objects, or in a depression in the seabed,
that the viewing range may be severely limited. Very strong reflectors may give multiple
echoes along a bearing line, and are identified by being equally spaced in range. If they
persist, reduce the gain.
When searching for objects, hold the vehicle heading as steady as possible to stop the image
blurring. Sit on the seabed if necessary.
Depending on water depth and vehicle depth, there may be ring like echoes. These can be
caused by surface or seabed direct reflections and may be difficult to avoid.
Experience with the sonar will enable the operator to be able to quickly and effectively set the
"Gain" and "Threshold" controls to give as even a background as possible, without swamping
the display, and maximise the performance capabilities of the head. The threshold control is
used to mask out any unwanted clutter caused by the weaker returns.
There are 4 range resolutions available, selected from the Main Menu. As you increase
the resolution from Low to Medium to High to Ultimate, the sonar display will show better
resolution, but at a lower scan speed. Use of a lower resolution will give faster scan speed,
but with coarser detail. When searching for smaller targets close by, select a higher resolution
mode at the higher frequency. When searching for large targets at long range use a lower
resolution on a lower frequency

Operation SeaKing & SeaPrince Imaging Sonars
0374-SOM-00001, Issue: 08 18 © Tritech International Ltd.
5.2. Operating the SeaKing & SeaPrince in Seanet Pro
Note
These instructions detail the use of the Seaking and the Seaprince imaging
sonars with the Seanet Pro software.
Please refer to the relevant software and quick start guides for the use of the
sonars with the Genesis software suite.
5.2.1. Main Screen
The Seanet Pro application can be run from the Programs group in the Windows Start
menu or from the desktop by double clicking on the shortcut icon.
The Seanet Pro screen display shown below is a Gemini, SeaKing & Bathymetric application,
although the view will vary depending on the applications chosen, each application will have
a similar layout.
Figure 5.1.
The main areas of the display are:
1. Display Header This part of the screen is used for system/software identification.
2. Menu Bar This is where system set-up functions can be accessed. Printing, Application
selection, Colour Scheme setup and Logging are some of the features that can be
accessed in this screen area.
3. Settings Bar This is where the Sensor can be controlled and configured. The Settings
bar is on top of every display window for each device that is connected to the system. It
includes a Tools Setup button, Led indicator (Pause/Go) and RAT dials and buttons
4. Status Bar This part of the screen is used to display system status information, typically
the AIF card interface status, Logging status/progress and Job specific information.
5. Sensor Display Area This part of the screen is where the main Sensor data
is displayed. Other pertinent data such as Range Scale, Cursor and status messages

Operation SeaKing & SeaPrince Imaging Sonars
0374-SOM-00001, Issue: 08 19 © Tritech International Ltd.
pertaining to the Sensor may also be displayed within this area - Refer to the manual
section provided with each Sensor for further details of its display area.
6. Sidebar This is where Serial input data and user text can be displayed. This bar can
be placed on the Left or Right hand side with RHS the default setting. The operator can
choose to have this bar visible or not and it can also be folded away.
5.2.2. Sonar Settings
These controls are displayed on the Sonar Settings bar. When the RAT is used or screen
cursor is moved over the Sonar Settings bar, a pop-up control panel will appear which will
display the remaining controls. These mimic the positions of the rotary controls (C1 to C5)
and function buttons (F1 to F7) on the RAT. Adjustments may be made using the RAT or the
on screen controls using the pointer device.
Figure 5.2.
Note
F1, F2 are not applicable in single window applications, F7 is not used.
Sonar Gain (C1) This sets the sonar receive gain as required – typically
this is around 50% but is varied according to water and
target conditions and user preference.
Contrast (C2) This sets the display contrast between hard and soft
targets. Usually set to user preference, it can help
find small features in generally featureless situation or
exclude clutter from a heavily featured seabed.
Range (C3) This sets the maximum range the sonar will scan. Long
ranges are scanned more slowly than short ranges due
to the limit imposed by the velocity of sound in water.
Sector Scan Direction (C4) This is used to set the centre of the scanned sector
particularly useful when using a narrow sector width to
concentrate on a particular feature. A well positioned,
narrow sector will allow faster scan updates than a wide
sector.
Sector Scan Width (C5) This sets the width of the scanned sector. Typically
this will be adjusted according to the required seabed
coverage.
Display Sensitivity (C6) This sets the display sensitivity threshold. A low setting
will effectively remove very low level returns from being
displayed which may include (soft) seabed backscatter
whereas a higher setting will start to remove higher
amplitude echoes which may include objects of interest.

Operation SeaKing & SeaPrince Imaging Sonars
0374-SOM-00001, Issue: 08 20 © Tritech International Ltd.
It is normal to keep this at a low setting of no more than
5dB to remove low level ‘noise’.
CYC (F1) - Cycle Window This can be used when one of the display windows is
maximised using the Expand (F2) button and will cycle
between the Sonar display windows. Also use the F1
button to switch focus between the display windows. The
optional RAT controller will switch its control to the display
that has the focus. Note: clicking on a display with the
mouse pointer will also switch focus to that display.
EXP (F2) - Expand Window This will maximise the current display window that is in
focus. Either click on a display window to switch focus
to it before expanding, or press the Cycle (F1) button to
switch focus to a display window.
ZOOM (F3) This will toggle the Acoustic Zoom window on/off. This
draws a zoom box on the display positioned by the
cursor. This control is also toggled via Application Tools -
Acoustic Zoom. The Zoom window size and magnification
can then be adjusted in ‘Zoom Setup’ in the Application
Tools.
RES (F4) – Sonar Resolution Resolution toggles through preset step sizes for the
sonar scanning. Available step sizes is dependant on the
sonar being used. Smaller angles give a higher resolution
picture but slower scan speeds. Usually a Lo or Med
resolution is used for tracking moving targets and Hi or
Ult for detailed examination of static targets.
FREQ (F5) - Sonar Frequency This toggles between the channels available on the
sonar. For a single frequency sonar unit this control will be
inactive and will lock to indicate the operating frequency
of the sonar.
REV (F6) - Reverse Scan
Direction
This allows the operator to instantly reverse the scan
direction without waiting to reach the end of the scanned
sector.
Sector Quick Select This group of 5 buttons in the bottom right of the control
allows the user to make a quick selection of a full 360°
scan or 180° forward, back, left or right. The display view
is changed automatically and the appropriate sector width
and direction set.
5.2.3. Main Menu
Figure 5.3.
1. Print Output screenshot to printer.
This manual suits for next models
1
Table of contents
Other Tritech Sonar manuals
Popular Sonar manuals by other brands
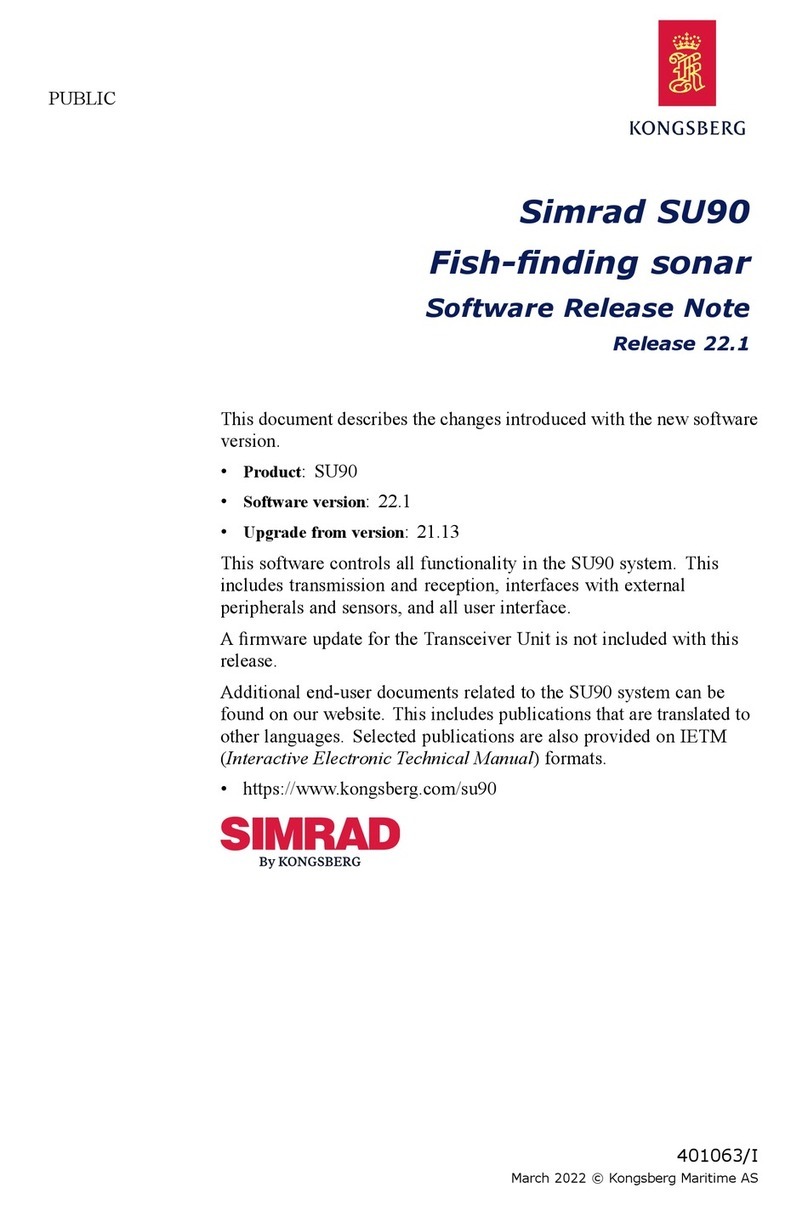
Kongsberg
Kongsberg Simrad SU90 Series manual
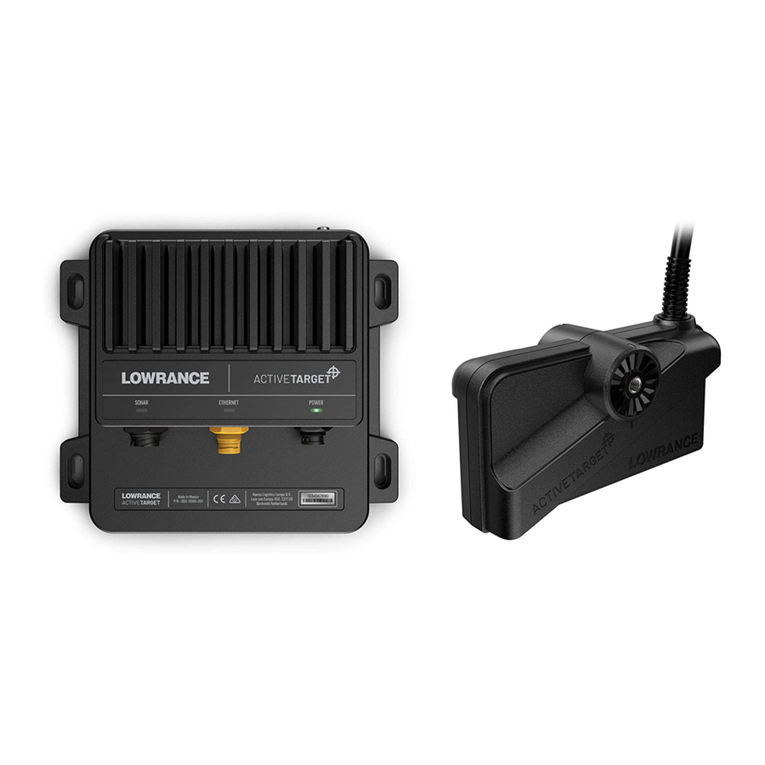
Lowrance
Lowrance ActiveTarget installation manual

Lowrance
Lowrance X-28 Installation and operation instructions
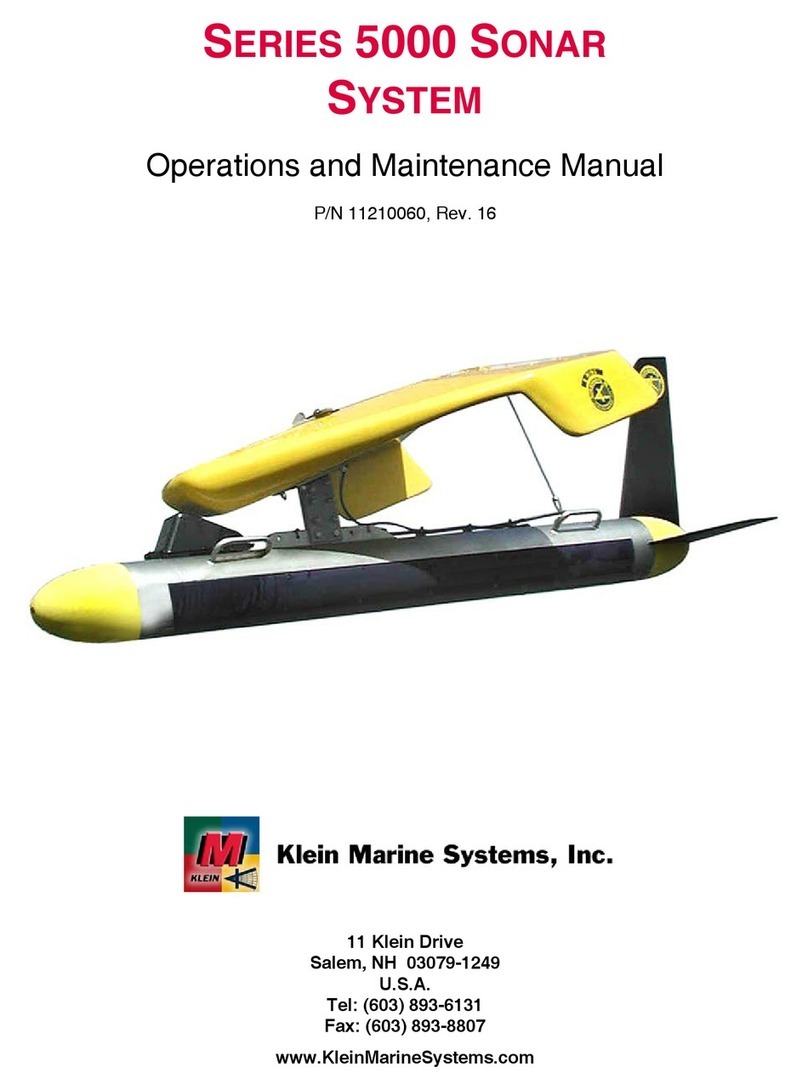
Klein
Klein 5000 SERIES Operation and maintenance manual
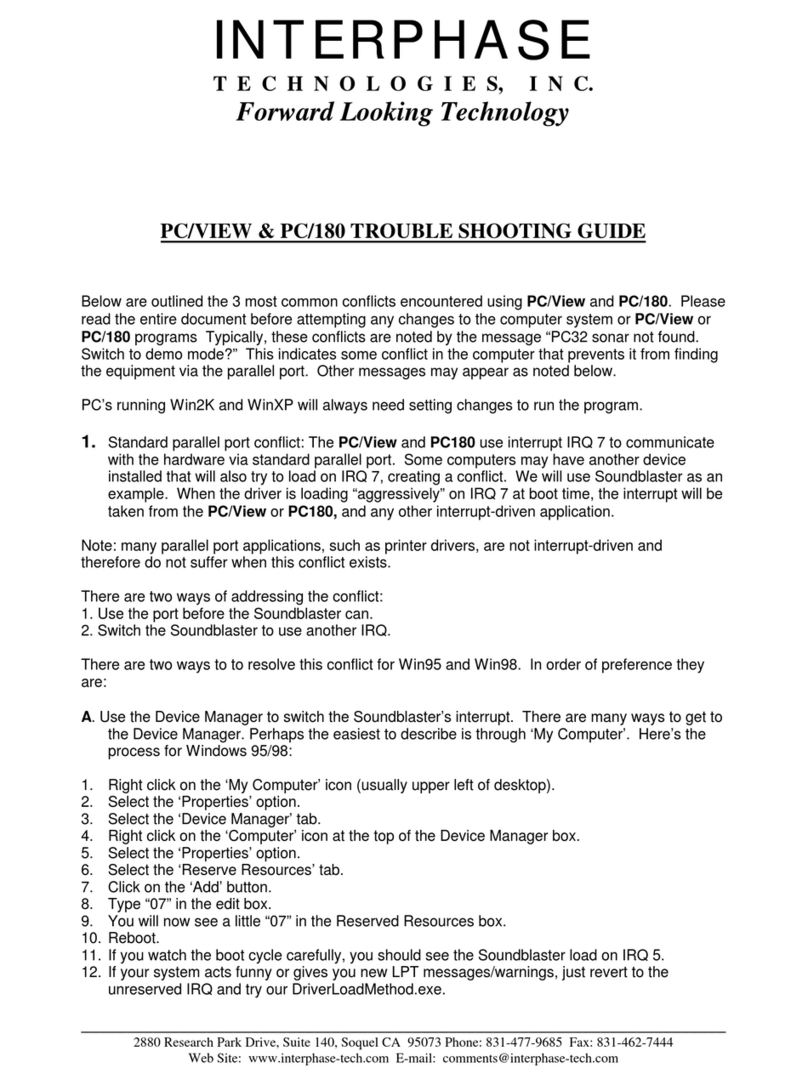
Interphase
Interphase PC/180 troubleshooting guide
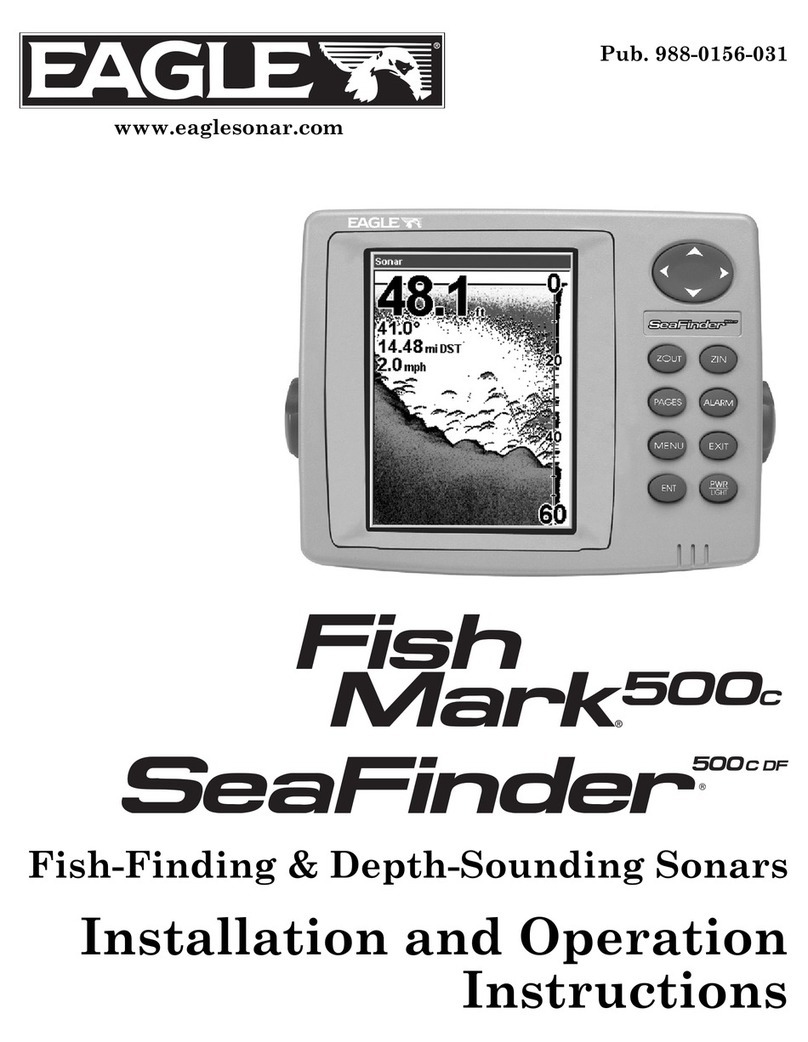
Eagle
Eagle FishMark 500C Installation and operation instructions