TufFlight Tuf-Yak User manual

Page 1
The Toughest R/C Planes Ever!
5376 Amalfi Drive, Clay, NY 13041 www.tufflight.com
Items Included in kit:
Foam:
CNC sliced EPP “block”
CNC sliced fuselage core pieces
Wood:
(3) 1/32" x 2-1/4" x 24" ply
(12) 1/16” x 3” x 24” balsa sheet
(4) 5/16” sq x 24” balsa sticks
(2) 1/2”x 18” balsa tri stock
(3) 1/4” x 5/8” x 18” balsa
(1) 5/8” x 3/4” x 18” balsa
(1) 5/16” x 3” x 8-7/8” balsa
(1) 1/4” 5/8” x 4” bass
(2) 1/32” x 6” x 8” ply
(2) 5/16” x 6” dowels
(1) 5/16” x 2-1/2” dowel
(1) 1/2” x 5/8” x 22” pine
Plastic:
(4) G10 joiner pieces
(4) 1/16” clear plastic control horns
(1) 3/16”" x 4" x 7" white engine plate
(1) 1/16” x 2-1/4” x 15” spacer
(2) 2.5 degree wedges
Hardware:
(8) 10-24 x 1.5" nylon bolts
(8) 10-24 nuts
(8) 6-32 x 3/8” nylon bolts
(2) 1/4” washers
(1) 1/4-20 x 2” nylon bolt
(4) 6-32 nuts
(2) 6-32 x 1-1/4" bolts
(1) 1/4-20 nut
(4) #64 rubber band
(1) roll hinge tape - Frost King # T94
(15) Robart Hinge points
(1) 7” x 1/16” tail skid wire
(1) 21” pre-drilled carbon tube elevator axle
Rev 1.3
Hello, and thanks for buying the Tuf Yak! Our version
of the popular profile Yak 55SP represents a quantum
leap in flying excellence PLUS unprecedented Durabil-
ity for intermediate to advanced 3D pilots.
Wingspan: 46"
Length: 48"
Weight: 4.5 - 4.75 lbs
Engine: .40 - .53 two stroke,
.63-.82 four stroke
Radio: 4 channels
Servos: 5
WingArea: 670 sq in
Tuf-Yak
Caution: The Tuf Yak is not intended as an R/C trainer airplane. This plane is a very agile aerobatic performer
that is capable of quick rolls, hovering flight and many tricks appealing to the “3D” flyer.
The CG location is 3/4” behind the spar.
While you may be tempted to fly close to yourself, please practice in a safe manner.
Always obey safety rules and exercise good judgement when learning new maneuvers.
Please read and understand the instructions before starting to build. We recommend joining the AMA and follow-
ing the AMA safety code. Call 1 (800) I- FLY-AMA for more details.
We assume no responsibility for how you use your plane. That said, let's get started!
Graph Tech profile landing gear
This Instruction Manual
Full Size Plans

Page 2
Items needed to complete:
Equipment:
.46-.53 two stroke engine
or .63-.82 four stroke
radio receiver
(2) 18” servo extension wires
Switch/charge jack or 6” extension wire
battery: 600 mAH
5 servos,
2 aileron, 1 rudder, 1 elevator,
1 metal geared throttle servo if possible
Parts:
2 or 3 rolls Ultracote covering
fuel tubing
poly fill (available at
fabric stores) for radio RX packing
8 oz fuel tank
1/2” latex foam rubber for tank isolation
(4) clevises
(4) 12” 2-56 single threaded end push rods
(2) 5”push rods shafts
(2) 3” diameter wheels
(4) 1-1/4” bolts (for engine mount)
(4) nylon insert lock-nuts
spinner nut
props : 11x4 for a 40 size 2 stroke
14x4, 13x5 or 13x6 for a 4 stroke
Adhesives:
Elmers “Nano” polyurethane glue (formerly
called “Ultimate”
-or- Gorilla Glue (amber color)
Loc Tite “Sumo” polyurethane glue
-or- clear Gorilla glue
3M-77 Spray adhesive
Goop brand adhesive
(household, plumber's, auto,
marine varieties all OK)
epoxy
medium and thin CA
foam safe CA
CA accelerator (also called “kicker”)
masking tape
Helpful Tools:
40 grit sandpaper on block
(available at auto finishing stores and Sears)
hobby knife / utility knife
square
X-acto knife with # 26 blade
(2.25 inches long, great for cutting
servo pockets from foam)
Phillips head screwdriver
straight screwdriver
long nose pliers
hemostats
drill with:
5/16" bit
3/16” bit
5/32” bit
1/8" bit
1/16” bit
#48 bit (for push rod servo arm holes)
#49 bit (for push rod throttle arm holes)
Dremel Tool w/ drum sander
hacksaw, razor saw, coping saw or band saw
covering iron
soldering iron
felt tip pen
pencil
ruler/straight edge
scissors
toothpicks
pins
carpenter’s level
flat building table, at least 6 ft long
“spray safe” area for applying 3M spray glue
(ie. outside, or a large box indoors)
mineral spirits for spray glue cleanup
(also great for cleaning fuel/oil residue!)
acetone
Useful:
2" wide roll thin clear packing tape for field repairs
big spray can of WD-40 for field cleaning
crashed engines
toothbrush and other small stiff brush for field
cleaning crashed engine
cotton swabs for field cleaning engine carb
plentiful supply of props (11 x 4 for 40 size 2 stroke,
14x4 for 4 stroke)
plentiful supply of 10-24 nylon bolts/nuts

Page 3
Glues Needed:
You will need these glues to assemble your plane. Please do not substitute!
CA(cyanoacrylate) - medium and thin viscosities. Also accelerator spray. Me-
dium CA is used to bond EPP to balsa. Thin CA is used for balsa to balsa
joints-- especially in framing up the tail pieces and joining balsa sheeting.
Odorless (foam safe) thin is best for inner fuselage pieces.
“Gorilla Glue” or Elmers “Nano” Polyurethane Glue - high strength, light weight amber color,
expands while curing to penetrate and fill voids. Until recently the Elmers brand was sold as
“Ultimate Glue” or “Pro-Bond”. It expands more and cures faster when exposed to small
amount of water. Misting parts with a water spray bottle is recommended when spreading glue
onto parts to be bonded. This glue takes about 4 hours to cure at 70 degrees F.
Loc Tite “Sumo Glue” polyurethane Glue : Similar to amber colored polyurethanes
above, but goes on clear, then expands and cures white. DOES NOT SAND
easily. Tougher than amber polyurethane glue and cures much faster-- expansion fin-
ished in 20 minutes and ready to handle in 2 hours. Best choice for gluing clear
plastic control horns and other clear plastic parts in this kit.
Goop : Similar to silicone adhesive/sealant but MUCH stronger. The
only acceptable alternatives are Pacer Zap-a-Dap-a-Goo, PFM
or “Shoe Goo”. Goop is fuel proof and flexible. . Other
TufFlight kits rely heavily on this glue for many critical high strength
joints. Goop is relatively heavy, so use sparingly. May substi-
tute Goop for Sumo glue when gluing clear plastic parts if Sumo glue not available.
3M77 : There is no acceptable substitute. Used in covering adhesion to the EPP foam. The
wing gets much of its strength from the “skin” of the Ultracote Covering (use only Ultracote
as all other brands give inferior strength and adhesion to EPP)..
Do all spraying in a “spray safe” area, as overspray may be hazardous to your health, and will make
an annoying mess if carelessly applied. We find a large box placed on the floor makes a good "overspray
booth" as the spray settles rapidly, but it should be contained. Many modelers have never used this glue
in their hobby practices, but we find it
perfectly suited for foam wing con-
struction, and many other modeling
tasks.
* 3M77 Spray glue may be applied generously, as it
is lightweight.
* 3M77 overspray may be cleaned with odorless min-
eral spirits.
*We consider a "generous" or "heavy" coat to
be "bubbly" and cold to the touch after applied. A
good heavy coat takes about 20 seconds of spray
time to apply to an area roughly 2 feet by 3 feet.

Page 4
Step 5: Carefully pry and push out the foam
center pieces from the wing parts as shown.
Step 4: Carefully separate the wing pieces
from the foam block as shown
Step 3: Save the 5/16” sheet and discard
the thin top foam sheet.
Step 2: Locate the 5/16” sheet foam and
carefully peel it from the block.
Step 1: Gather parts and tools. Step 6: You may discard the shucks and
notched pieces as shown.
Step 7: Peel away the “spider webs” and
chunks left from the foam.
Step 8: Break one of the front foam cavity
pieces as shown to make a “sanding block”
Step 10: Gently sand the aileron pieces to
true the leading edges to make them straight.
Step 9: Use the EPP sanding block to help
clean the foam of spider webs.
Prepare Foam Parts
You’ll need : Pre Sliced foam block
40 grit sandpaper on a block
straight edge at least 24” long
medium viscosity CA (not foam safe)
CA Accelerator
Careful not
to round the
“point” of
the leading
edge!
Don’t discard
any other
pieces! They
will be used
later

Page 5
Step 15: Gather parts and tools
Step 14: Now glue the rear split similar to
the front as shown.
Step 13: Place a straight edge on the wing
and press down while spraying CA “kicker”
Step 12: Place and open the wing as shown
to apply medium viscosity CA to the split.
Step 11: Open the “hinge” as shown and
sand/clean these surfaces too as shown.
Step 16: Mark two of the spar pieces 2”
from one end of each piece
Step 17: Cut off the ends at the 2” marks as
shown (see next step)
Step 18: You should now have spar parts as
shown above
Step 20: Draw lines to the center at the
edge to make “points” tapered to 3” marks
Step 19: Now take these two spar pieces
and mark one end 3” as shown.
Make and Assemble Spar pieces
You’ll need : (3) 1/32” plywood spar pieces
ruler, pencil, hobby knife
fine line felt tip marker
small drafting square
1/16 plastic spacer material
Place on a
table edge to
allow the
wing to fold
open as
shown
Make cuts
perpendicular
to edge as
shown
It helps to skip
ahead to see what
you’re working
toward during
these steps
Repeat for
other wing
half when
both front
and rear
splits have
been glued

Page 6
Step 25: You should now have the pieces as
shown
Step 24: Cut away wood as shown and
SAVE THE SCRAP PIECES
Step 23: Draw lines to create 6” tapered
points similar to previous step.
Step 22: Mark the unused spar piece 6”
from each end as shown
Step 21: Cut on the lines to make the 3” points
as shown (do one end only on both pieces)
Step 26: Mark the center line on the 6”
double tapered spar piece as shown
Step 27:Apply medium viscosity CAto half
of the tapered piece to the tip as shown
Step 28:Apply one of the spar pieces even
with the center mark as shown and press down
Step 30: apply medium viscosity CAin the
area between the lines as shown
Step 29: Mark the assembly 1” from the
center mark as shown
leave the assembly
in this orientation
for the next step--
but be careful not
to glue to table!
you should be
drawing this line
on the piece you
just glued on top in
the last step

Page 7
Step 35: Locate the white plastic piece to
the 6” tapered spar end and trace as shown
Step 34: Mark the unglued spar piece 3/8”
from the untapered edge as shown.
Step 33: Draw marks 3/8” from the center
on both sides of the center line.
Step 32: Mark the center line again on the
2” piece applied on top in the last step.
Step 31:Apply the 2” piece as shown Step 36: Cut the white plastic to match the
wood spar’s 6” tapered point
Step 37: Test fit the unglued spar into the
“pocket” made in the previous steps
Step 38: The unglued spar fits into the
pocket from the right in the above picture
Step 40: Mark the plastic piece where you
see the line 3/8” to the right of center as shown
Step 39: Apply the plastic piece exactly to
the 6” tapered spar end as shown
Note, half of this 2”
piece should
“overhang” and
not be glued to
anything at this
point
Make sure spar fits
snugly to the
opposite piece as
shown with no
gaps.
Fix any interference
The plastic is semi-
transparent.
Use a felt tip
marker
Don’t move the
plastic piece for the
next step!
(Note, your
white plastic
piece will
probably be
longer than the
one shown.)

Page 8
Step 46:Arrange spar and plastic spacer
with lines even with foam edge as shown.
Step 44: Spread the glue as shown taking
care not to get glue under the plastic piece
Step 43:Apply glue to the exposed foam but
NOT underneath the plastic!
Step 42: Insert the plastic spacer piece so the
line is even with the foam edge as shown.
Step 41: Gather supplies
Step 45: Spray the unglued spar piece with
water and blot away excess moisture.
Step 47: Wrap masking tape around wing to
clamp it shut as shown.
Glue wing parts together
You’ll need : Assembled spar pieces
1/16” plastic spacers
Gorilla Glue
water spray bottle
masking tape
popsicle stick
Bottom of wing is up
with Leading Edge of
wing facing down
Wood piece faces
“forward” (nearest LE)
Insure both lines even
with foam edge
Start with the
left wing.
flip open the
“hinge” as shown
The plastic piece
protrudes out of
the edge during
all these steps
a popsicle
stick makes a
good glue
spreading
tool
spray both
sides
Step 50: Set the left wing half aside for the
glue to cure.
Step 49: Wrap tape around whole wing (top
and bottom surface)
Step 48: Continue to wrap tape around
foam as shown
The tape sticks
best when you
stick it to itself
in big loops
around the wing
take care to keep
the spar and plastic
spacer pressed fully
down in the crack
as you tape the
wing tightly closed

Page 9
Step 52: Spread glue with a popsicle stick
or similar tool
Step 51: Open the right wing and apply
Gorilla glue to the entire opening as shown
Step 53: Spray water on the remaining spar
piece and blot away excess moisture
Step 54: Insert spar with the “pocket” facing
forward aligned to the foam edge as shown
Step 55: Tape the right wing like the left half
and set it aside for the glue to cure.
Step 60: Cut out the foam parts with a
hobby knife that has a new SHARP blade.
Step 59:Apply the template to the foam
sheet
spray both
sides of the
longer end
up to the
marks near
the center
The 3rd mark
should be
even with the
foam
Step 56: Gather parts and tools.
Step 57: Cut the full size foam template
sheet as shown
Step 58: Lightly spray the backside of the
template with 3M77
Make foam tail feathers
You’ll need : 5/16” foam sheet, medium CA, kicker
ruler, pencil, hobby knife, 3M77
balsa tri stock, carbon elevator tube
Robart hinges, template sheet
hand drill 1/16”, 1/8” and 5/32” bits
Keep the
parts group
together -- it
fits the foam
exactly in the
next steps

Page 10
Step 65: Kick the joint with CA accelerator.
Step 64: Carefully center the balsa tri stock
and glue to the foam as shown.
Step 63:Apply medium viscosity CAtothe
rudder hinge line area as shown.
Step 62: Cut the balsa triangle stock to the
length as shown for the rudder hinge line.
Step 61: Here are the foam parts cut out. Step 66: Sand the balsa triangle corners off
so the balsa is even with the foam surface.
Step 67: Here is the rudder sanded flat.
Step 68: Using the full size plans, mark the
hinge locations on the balsa as shown.
Step 70: Enlarge the holes with a 1/8” drill
Step 69: Drill hinge locations with a 1/16”
drill / pin vise as shown.
Be sure to
drill the
holes
straight
(sight in both
directions)

Page 11
Step 75: The hinge will fit as shown. Repeat
for all holes on one side of the carbon tube.
Step 74: With a 5/32” drill, enlarge ONE
side wall only!
Step 73: Fit a hinge into the carbon tube and
notice it will not slide down all the way.
Step 72: Test fit the hinge and cut the balsa
as necessary for a good fit as shown.
Step 71: Use a hobby knife to carve out the
balsa so a hinge will fit inside.
Step 76: Use a hinge in the tube to see which
side will be glued to the foam elevators
Step 79: Rotate and align the tube so a test
hinge points to the foam in the next step
Step 77: Place the tube in the foam eleva-
tors on the plans as shown
Step 80: Glue the tube to the foam with
medium CA.
Step 78: Insure the foam is lined up so it leaves
a small gap to the horiz stab on the plans.
Repeat
process for
all rudder
hinge holes
Only elevator plans
shown for clarity
“horiz stab” is short
for “horizontal
stab”
Trim the foam so the
tube has a snug fit
Center the tube within
the foam thickness
(do one half at a time
with a hinge in the
other half as above for
alignment)

Page 12
Step 85: Measure and mark the balsa sticks
over the plan.
Step 84: Cover the plans with plastic wrap
Step 83: Gather parts and tools
Step 82: Glue other half to match the first
half (lay on table to help alignment)
Step 81: Kick the CAtaking care to keep
the tube centered and aligned to the foam.
Step 86: Cut the sticks to the correct length.
Step 87: Lay the sticks over the plan in the
correct position and pin to hold them down
Step 88: Glue sticks together with CA
Repeat process for entire stab.
Step 90: Glue the center block as shown.
Step 89: Using the full size template, make
the center stab block (see below)
Make balsa tail stabilizers
You’ll need : 5/16” sq balsa sticks, 5/16” sheet
thin/ medium CA, kicker, pins
ruler, pencil, hobby knife, razor saw
balsa tri stock, plastic wrap
hand drill 1/16”, 1/8” and 5/32” bits
sanding block, full size plans / template
elevator assembly
Only
horizontal
stab shown
for clarity
Cut the
longest
pieces first
then work
your way to
the next
shorter ones.
It’s often
wiser to cut a
little long,
and slowly
sand to the
correct
length and
angle

Page 13
Step 95: Round the leading edges only of
each stab.
Step 94: Sand the edges even and surfaces
flat on both stabs.
Step 93: Glue tri stock to the stab as shown.
Step 92: Cut tri stock to fit the rear of the
horizontal stab and apply centered as shown.
Step 91: Make the vertical stab in similar
fashion.
Step 96: Use the elevator assembly to mark
the horiz stab hinge locations at each hole.
Step 97: Mark hinge hole locations with
small drill or prick punch.
Step 98: Drill 1/8”hole in at all hinge loca-
tions as shown.
Step 100: Enlarge hole with drill to depth as
shown.
Step 99: With a 5/32” drill, use masking
tape as a “depth gauge” to 11/16”
Apply tri stock
ONLY to the horiz
stab for now!
(Vertical stab will
get glued later)
Center the
stab within
the elevator
assembly
(gaps on
sides should
be equal)
This is an alternate
approach to using
a hobby knife as
done when
enlarging rudder
hinge holes. You
can use either
method here.

Page 14
Step 105: When glue has fully cured,
remove masking tape from wing halves.
Step 104: Gather parts and tools
Step 103: Once satisfied, trim foam to be
even with balsa stab as shown.
Step 102: Test fit hinges in stab and elevator
simultaneously. Trim/ adjust as needed.
Step 101: Test fit hinge. Trim with knife as
needed.
Step 106: Using 40 grit sandpaper, sand the
wing bottom spar areas flush with surface
Step 107: Sand the top spar areas also to
clear any glue which squirted out.
Step 108: Carefully trim the root edge areas
to remove any glue bumps with hobby knife.
Step 110: Mark both wing bottoms 7” from
the root edge at the spar as shown.
Step 109: Using the full size plans/template,
trim both wing panel tip edges as shown.
Hinge pivot point
center should be
aligned with tri
stock point, and
free to move up and
down as shown.
a gap of 1/16”
between balsa and
carbon is desired.
Hinge pivots
should all be
centered in this gap
Prepare Foam Wings
You’ll need :
assembled foam wings
40 grit sandpaper on sanding block
full size plans / template
throttle and aileron servos, pliers
gorilla glue, masking tape
Don’t cut into the
wood spars! Just
trim any glue which
is in the corners.
Trim both wing root
edges.
A band saw is best
for this, but you can
use a sharp knife
too with patience.
Sand contour
smooth with 40 grit
paper on a block.
This marks the
inner location of
the aileron servo

Page 15
Step 115: Mark the right wing bottom 1”
from the root edge along the spar as shown
Step 114:Apply gorilla glue to the cavity
and moisture and tape servo in place.
Step 113:A Dremel tool with drum sander
helps remove foam to the correct depth.
Step 112: Use pliers to pull foam to create a
cavity for the servo
Step 111: Trace around and cut the outline
of servo as shown with a sharp knife.
Step 116: trace around the throttle servo
location as shown (metal gears recommended)
Step 117: Mount the throttle servo in the
same fashion as the aileron servos.
Step 118: This is a view looking inside the
right wing root.
Step 120: Insert the foam piece into the wing
tip until it stops and trace the edge as shown
Step 119: Retrieve the front wing cavity
core pieces
Aileron servos will
sit directly in front
of the spar with the
wire pointing to the
root edge as shown
Make recesses for the
servo lugs too.
Test fit servo to check
the fit. The hole depth
is good when the servo
body top is even with
the foam surface.
Be sure this is the
RIGHT WING
BOTTOM!
The Throttle Servo will
sit directly in front of
the spar with the wire
pointing to the root
edge as shown
repeat for left wing
also
Look ahead to see
inside view of servo
wires to compare
with your wing.
Push the foam until
it fits snugly

Page 16
Step 125: Tape the tip caps flush with the
edges as shown. Set aside to cure.
Step 124: Glue the foam cap pieces inside
the tip cavities as shown with poly u glue.
Step 123: From a scrap of 5/16” foam, cut
a wedge which fits inside rear tip cavity
Step 122: Using a band saw sharp knife,
slice this section from the foam piece.
Step 121: Pull the foam out 1/2” and trace
the outline again as shown
Step 127: Once glue has cured, temporarily
remove the white plastic spacer piece.
Repeat for both
wing tips
We want to break it
free of the poly-u
glue that may have
expanded into the
groove
Watch your fingers!
Step 126: Sand both foam tips to make the
surfaces flat and even using 40 grit.
Step 128: Mark 3/4” from the root edge of
the left wing panel along the spar as shown
Step 129: Slice between the wood and foam to
the 3/4” mark on both sides of the spar.
Step 130: Insert the right spar where the
plastic spacer was and press halves together
A long thin hobby
knife works best
here
Be careful not to
cut into the wood
spar
The left spar protrusion
should fit into the
spar“pocket”
The spar “pocket”
protrusion should fit
into the slice from the
last step

Page 17
Step 135:Apply a moderate coat of 3M77
to the wing bottom surfaces and let sit
Let the glue rest
until it isn’t “wet”
to the touch-- only
slightly tacky--
about 5 minutes
Step 132: Gather parts and tools
Step 131: Re-insert the white plastic spacer
piece the way it was before.
Step 134:Apply masking tape to exposed
spar areas also
Step 133: Put a small piece of masking tape
over the aileron and throttle servo splines.
Cover wing halves and make / hinge ailerons
You’ll need : wing assemblies, hinges, old credit cards
3M77, covering iron, masking tape
sandpaper, pliers, ruler, toothpick
Ultracote covering, small scissors
prick punch, marker, 1/8” drill
single edge razor blade and/or knife
This tape will
protect against
unwanted 3M77
spray glue in these
areas.
Step 139: Poke the servo spline through the
covering as shown
Step 138: Use a sanding block to locate and
free servo splines (gently sand spline “corners”)
Step 137:Apply a piece of Ultracote to the
wing and gently stretch it to minimize wrinkles
Step 136: Remove masking tape from
servos
Cut covering to have
about 2” extra all
around
Covering will stick to
glued area and when a
covering iron is
applied
Step 140: Step omitted

Page 18
Step 150: Mark outline of aileron as shown
Step 149:Apply template over foam aileron
pieces as shown
Step 148: Copy / cut full size paper tem-
plates for the ailerons
Step 147: Remove white plastic pieces
permanently.
Step 146: Iron all surfaces to minimize
wrinkles.
Set Iron
temperature to
~300 deg F
Step 141: Iron around the servo spline to
minimize wrinkles
Step 142: Once wrinkles are minimized, iron
edges and trim leaving about 1/4” overhang
Step 143: Iron edges only at this point!
Step 145: Apply covering to the top and tip
surfaces and trim neatly
Step 144:Apply masking tape to covering
edges and spray 3M77 to wing top and tip
iron temperature
should be about
250 degrees F
After this step is a
good time to clean
the iron with
mineral spirits and/
or acetone
We need to mask areas
where covering will
overlap to itself (LE,
TE , root and tip edges)
Let the glue sit 5
minutes and remove
tape

Page 19
Step 160: Drill the hinge holes ~1” deep
with a 1/8” drill
Step 159: Poke a hole in all hinge locations
with a prick punch as shown
Step 158: Insure both aileron markings are
symmetrical
Step 157: Mark location of control horn on
aileron bottom as shown
Step 156: Use full size plans to transfer
hinge locations to wing and aileron as shown
Ailerons are held
with fat edges
facing together
here
Step 151: Trim root, tip and trailing edges of
ailerons with sharp hobby knife
Step 152: Use a ruler to trim the trailing
edge as shown
Step 153: Spray one side of aileron with
3M77 and allow to sit 5 minutes
Step 155: Carefully iron both sides taking
care to keep aileron straight
Step 154:Apply Ultracote covering to glued
side and follow the wing covering procedure
be sure to hold
aileron STRAIGHT
during this step
(check leading
edge with another
ruler)
Warning:
Do NOT iron one
side surface until
both sides are
covered.
If aileron curves
during this step,
gently bend to
desired shape while
heating, then
remove iron and let
cool until straight

Page 20
Step 169: Gather parts and tools.
Step 168: Insert 2 credit cards to preserve
the gap while the glue dries
Step 167: Tape the aileron to the wing
leaving a 1/16” gap as shown
Step 166: Fit the aileron onto the hinges as
shown taking care to center hinge in gap
Assemble Fuselage pieces
You’ll need : rear fuselage foam core, 5/8” pine,
5/16” balsa sheet, 5/8” balsa sticks
sandpaper, pliers, ruler, scrap 1/32” ply
razor saw, elevator/rudder servos
marker, foam safe CA / kicker, scissors
Step 161: Insert dowel and test fit hinge
near root edge of wing as shown
Step 162: Trim 2 hinges to so they won’t
obstruct dowels and test fit as in previous step.
Step 163:Apply glue to the hinges.
Step 165: Insert the hinges as shown
Step 164:Apply glue inside the holes too
Don’t glue the
dowels in yet!
Work the glue into
the holes with a
toothpick or
similar
Step 170: Insert the 5/8” x 3/4” sticks into the
foam and sand for a good fit as needed.
Table of contents
Other TufFlight Toy manuals
Popular Toy manuals by other brands

Hobbico
Hobbico FLYZONE ME 109 Assembly
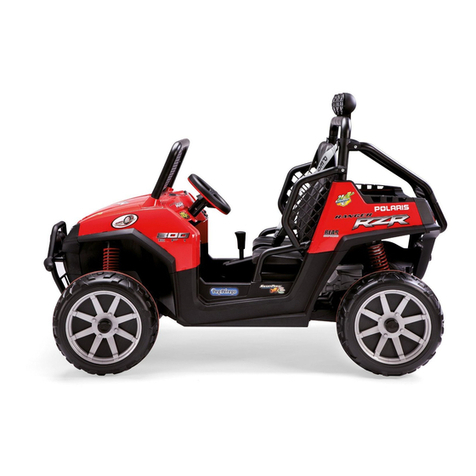
Peg-Perego
Peg-Perego Polaris RANGER RZR IGOD0516 Use and care
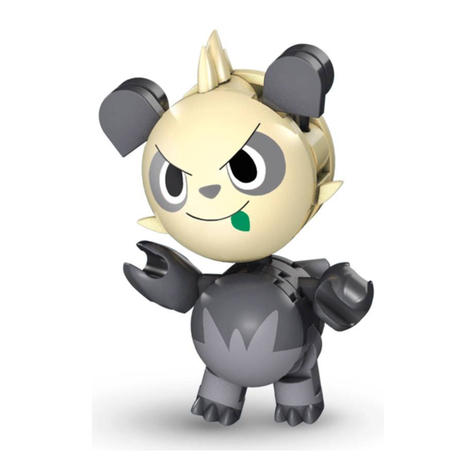
Mega Construx
Mega Construx POKEMON WONDER BUILDERS PANCHAM GFV74 manual
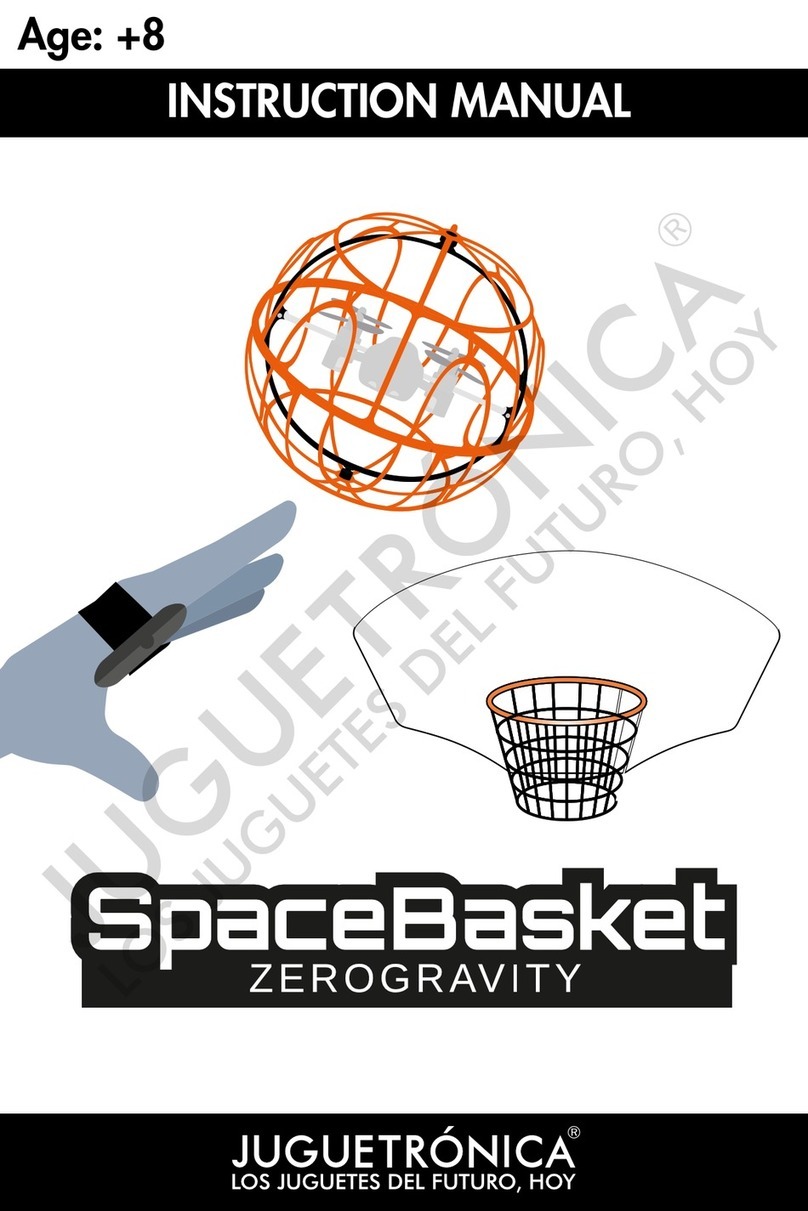
Juguetronica
Juguetronica Space Basket Zero Gravity instruction manual
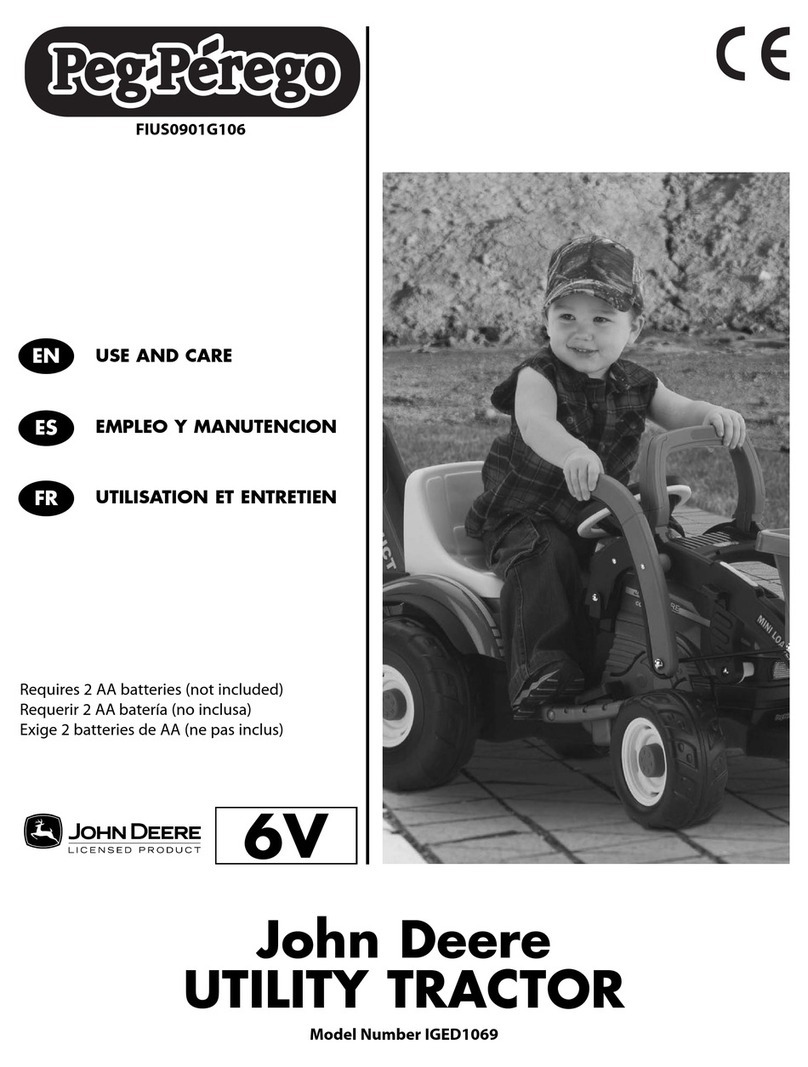
Peg-Perego
Peg-Perego John Deere UTILITY TRACTOR IGED1069 Use and care

Ripmax
Ripmax Hellcat Slim instruction manual