Tuthill M-D Pneumatics PD PLUS 64/67 Series Operating instructions

Models
INSTALLATION
OPERATION
MAINTENANCE
REPAIR
MANUAL
4006 5507 5514
4009 5509 5516
4012 5511 5518
5520
Rotary Positive Displacement Blower
Series 17/46 - Lip-Labyrinth (Air Service)
Series 57/81 - Single Envelope Gastight
Series 64/67 - Double Envelope Gastight
(obsolete 16/47 series also included in this manual)
M-D Pneumatics™
4840 West Kearney Street, P. O. Box 2877
Springfield, Missouri USA 65801-2877
Tel 417 865-8715 800 825-6937 Fax 417 865-2950
http://vacuum.tuthill.com
2006 1011 ORIGINAL LANGUAGE - ENGLISH
I
N
T
E
R
N
A
T
I
O
N
A
L
Q
U
A
L
I
T
Y
S
T
A
N
D
A
R
D
R
E
G
I
S
T
E
R
E
D
VACUUM & BLOWER SYSTEMS
TUTHILL CORPORATION

2
TABLE OF CONTENTS
SECTION PAGE
1. INTRODUCTION 3
1.1 APPLICABLE DOCUMENTATION 3
1.2 SCOPE OF MANUAL 3
2. CONVENTIONS AND DATA PLATE 3
2.1 GRAPHIC CONVENTIONS IN THIS MANUAL 3
2.2 DATA PLATE 4
3. LIFTING 5
4. DESCRIPTION 5
4.1 FLOW BY DIRECTION 6
4.2 SPECIFICATIONS 7
5. INSTALLATION 8
5.1 GENERAL 8
5.1.1 LOCATION 10
5.1.2 BLOWER AIR INTAKE 10
5.1.3 SOFT FOOT 11
5.2 SAFETY 11
5.3 LUBRICATION 12
5.3.1 FILLING PROCEDURE 13
5.3.2 FREQUENTLY ASKED QUESTIONS REGARDING LUBRICATION 13
5.3.3 HAZARDS ASSOCIATED WITH BREAKDOWN OR IGNITION OF LUBRICATION 14
5.4 PIPING CONNECTIONS 14
5.4.1 BLOCKAGE OR RESTRICTION 14
5.5 COOLING COILS (OPTIONAL) 15
5.6 COOLING WATER CONNECTIONS AND SPECIFICATIONS — COOLING COILS (OPTIONAL) 15
5.7 MOTOR DRIVES 16
5.7.1 DIRECT COUPLED 16
5.7.2 V-BELTS 16
5.7.3 SETTING V-BELT TENSION 17
5.7.4 V-BELT TROUBLESHOOTING 18
5.8 SPECIAL INSTRUCTIONS FOR BLOWERS WITH EXTERNAL LUBRICATION SYSTEMS 18
5.9 MOTOR AND ELECTRICAL CONNECTIONS 19
6. OPERATION 20
6.1 GENERAL 20
6.2 START-UP CHECKLIST 21
6.3 OPERATING 21
6.4 STOPPING 22
6.5 METHANE GAS APPLICATIONS 22
6.6 WATER INJECTED BLOWERS 22
6.6.1 OPERATION 23
6.6.2 SHUTDOWN 23
6.7 RECOMMENDED SHUTDOWN PROCEDURE TO MINIMIZE RISK OF FREEZING OR CORROSION 23
7. MAINTENANCE 24
7.1 GENERAL 24
7.2 REGULAR MAINTENANCE 25
7.3 SPARE PARTS 25
7.4 FACTORY SERVICE & REPAIR 26
7.5 LONG TERM STORAGE 26
8. MODEL 4000 AND 5500 DISASSEMBLY AND REASSEMBLY 27
8.1 DISASSEMBLY OF BLOWER 27
8.2 ASSEMBLY OF BLOWER 28
9. TROUBLESHOOTING 33
10. ASSEMBLY CLEARANCES 34
11. TORQUE CHART 34
12. RECOMMENDED LUBRICANTS 35
13. SPECIAL TOOL DRAWINGS 36
14. PARTS LISTS AND ASSEMBLY DRAWINGS 37
15. DECLARATION OF INCORPORATION 61
16. WARRANTY — BLOWER PRODUCTS 62
17. OPERATING DATA FORM / PRODUCT REGISTRATION 63

3
1. INTRODUCTION
CONGRATULATIONS on your purchase of a new PD PLUS™Rotary Positive Displacement Blower from
Tuthill Vacuum & Blower Systems. Please examine the blower for shipping damage, and if any damage
is found, report it immediately to the carrier. If the blower is to be installed at a later date make sure it is
stored in a clean, dry location and rotated regularly. Make sure covers are kept on all openings. If blower is
stored outdoors be sure to protect it from weather and corrosion.
PD PLUS blowers are built to exacting standards and if properly installed and maintained will provide
many years of reliable service. We urge you to take time to read and follow every step of these instructions
when installing and maintaining your blower. We have tried to make these instructions as straightforward
as possible. We realize getting any new piece of equipment up and running in as little time as possible is
imperative to production.
NOTE
Record the blower model and serial numbers of your machine in the
OPERATING DATA form on the inside back cover of this manual. You will
save time and expense by including this reference identification on any
replacement part orders, or if you require service or application assistance.
1.1 APPLICABLE DOCUMENTATION
The applicable documents associated with this manual are:
• 2006/42/CE – Machinery Directive
• EN 1012-1:1996 - Compressors and vacuum pumps - Safety Requirements - Part 1: Compressors
1.2 SCOPE OF MANUAL
The scope of this manual and the Declaration of Incorproation includes the bare shaft rotary positive
displacement blower.
2. CONVENTIONS AND DATA PLATE
2.1 GRAPHIC CONVENTIONS IN THIS MANUAL
This manual is the result of a risk assessment according to the applicable documents referenced in section
1.1. The following are hazard levels are referenced within this manual:
DANGER
Indicates an immediate hazardous situation which, if not avoided, will result
in death or serious injury.
WARNING
Indicates that a physical injury or damage to health or property, if not
avoided, could occur.
CAUTION
Indicates that a potential hazard may occur which, if not avoided, could
result in minor or moderate injury.

4
NOTE
Indicates a statement of information which, if not avoided, could cause
damage to the product.
CAUTION
Read manual before operation or bodily harm may result. Attention should
be given to the safety related sections of this manual.
2.2 DATA PLATE
WARNING WARNING CAUTION CAUTION
htt
p
://www.tuthill.com
Hearing protection
re
q
uired.
Do not touch hot
surfaces.
AS
Ueht
n
i
e
d
aM7396
-
5
2
8
)
008
(
READ INSTRUCTION MANUAL BEFORE OPERATION OR BODILY HARM MAY RESULT
Keep body & clothing away
from machine openings.
Do not operate without
g
uards in
p
lace.
R
EBMUN
LA
I
RE
S
RE
B
MUN
LE
DO
M
Tuthill Vacuum & Blower Systems
4840 West Kearney Street
Springfield, Missouri USA 65803
YEARMAWP
MAX RPM
General Operation and Symbols on Data Plate - The following information is contained on the data plate:
WARNING
Keep body & clothing away from machine.
During operation, keep body and clothing away from inlet and outlet of the
blower.
WARNING
Do not operate without guards in place.
CAUTION
Hearing protection is required while the blower is in operation. Noise levels
may reach as high as 81 dBA.
CAUTION
Do not touch hot surfaces.
The upper limit of the blower operation is 400° F (205° C). Do not touch
the blower while it is in operation and assure blower is cool when not in
operation.

5
MODEL NUMBER: This identifies the specific model of the blower.
SERIAL NUMBER: Each blower has a unique serial number. This number is to be used with any
service issues and with any contact with the manufacturer.
YEAR: This states the year that the blower was manufactured.
MAWP: This states the maximum allowable working pressure (MAWP) of the blower casing.
This is NOT the allowable maximum pressure differential. When determining the
pressure differential, the inlet pressure shall be taken into account to assure that the
MAWP is not exceeded.
The standard MAWP is per Table 2. The MAWP shall not be exceeded unless
specific factory testing of the pressure containing components of the blower has
been performed.
Contact the factory for testing and documentation if this pressure is to be exceeded.
3. LIFTING
WARNING
The blower must be handled using an appropriate device such as a fork
truck or appropriate lifting device. See Table 1 for approximate weights.
Care should be taken to assure blower does not over-turn during handling
and installation.
4. DESCRIPTION
NOTE
Refer to specific data sheets for flow capacities and vacuum capacities.
NOTE
Refer to diagrams in this manual for proper rotation and orientation in inlet
and discharge.
TuthillVacuum&BlowerSystemsmodel4000and5500Seriesrotarylobeblowersarepositivedisplacement
type units, whose pumping capacity is determined by size, operating speed, and differential pressure
conditions. Blowers employ rotors rotating in opposite directions within a housing closed at the ends by
end plates.
Effective sealing of the inlet to the discharge is accomplished through the use of very small operating
clearances. The resulting absence of moving contact eliminates the need for any internal lubrication.
Clearances between the rotors during rotation are maintained by a pair of accurately machined helical
timing gears, mounted on the two shafts extended outside the air chamber. The intermeshing rotary lobes
are designed to rotate and trap air or gas between each rotor and the housing. As the rotor lobes rotate
past the edge of the suction port, the trapped air or gas is essentially at suction pressure and temperature.
Since the blower is a constant volume device, the trapped air remains at suction pressure until the leading
rotor lobe opens into the discharge port. The close clearances between the rotors inhibit back slippage of
the trapped volume from between the rotors and the trapped volume is forced into the discharge piping.
Compression occurs not internal to the blower, but by the amount of restriction, either downstream of the
blower discharge port, or upstream of the blower inlet port.

6
Figure 1 illustrates that the air
moves not between the rotors but
between the rotors and the side
of the housing. Also, the machine
is bi-directional, meaning that the
direction of rotation of the blower
can make either side the inlet or
discharge. See also the Flow
Direction by Rotation section
below.
No attempt should ever be made
to control capacity by means of
a throttle valve in the intake or
discharge piping. This will increase the power load on the drive system, increase operating temperatures,
and can overload and/or seriously damage the blower. Likewise, if a possibility exists that flow to the blower
inlet may be cut off during normal operation of a process, then an adequate vacuum relief valve must be
installed near the blower. A pressure type relief valve in the discharge line near the blower is also strongly
recommended for protection against cutoff or blocking in this line. Check valves should also be used on
every blower when more than one blower is connected to a discharge line. This is for both safety and
operating conditions.
When a belt drive is employed, blower speed, if necessary, can usually be adjusted to obtain desired
capacity by changing the diameter of one or both sheaves, or by using a vari-speed motor pulley. In a
direct coupled arrangement, a variable speed motor or transmission is required, or excess air or gas may
be blown off through a manually controlled unloading valve and silencer. Gas units can use bypasses, but
some applications may require additional cooling. If there is a large volume of high pressure air or gas
downstream of the blower, a check valve in the piping downstream of the blower will protect the blower from
overspeeding in a backward direction upon shutdown.
Consult your Tuthill Vacuum & Blower Systems sales professional if questions arise.
4.1 FLOW BY DIRECTION
WARNING
Refer to diagrams in this manual for proper rotation and orientation in inlet
and discharge.
Figure 2 - Flow Direction by Rotation
INTAKE INTAKE
DISCHARGE INTAKE
DISCHARGE
HORIZONTAL FLOWVERTICAL FLOW
DISCHARGE
INTAKE DISCHARGE
INTAKE
DISCHARGE
RIGHT DRIVE
CW ROTATION
LEFT DRIVE
CW ROTATION
LEFT DRIVE
CCW ROTATION
RIGHT DRIVE
CCW ROTATION
TOP DRIVE
CW ROTATION
TOP DRIVE
CCW ROTATION
BOTTOM DRIVE
CW ROTATION
BOTTOM DRIVE
CCW ROTATION
DISCHARGEINTAKE INTAKE
INTAKEDISCHARGE DISCHARGE
Figure 1 - Illustration of general operation principle
INLET INLET INLET
DISCHARGE DISCHARGE DISCHARGE

7
4.2 SPECIFICATIONS
TABLE 1 — SPECIFICATIONS
MODEL
APPROXIMATE OIL CAPACITY
FLUID OUNCES / LITERS APPROXIMATE WEIGHT
LBS. / KG
VERTICAL FLOW 46/81/67 HORIZONTAL FLOW 17/57/64 17/46 57/81 64/67GEAR (DRIVE) END BACK END GEAR (DRIVE) END BACK END
4006
24 / 0.70 24 / .070 14 / 0.42 14 / 0.42
170 / 77 180 / 82 185 / 84
4009 200 / 91 210 / 96 215 / 84
4012 225 / 182 235 / 107 240 / 109
5507
57 / 1.7 57 / 1.7 32 / 0.95 32 / 0.95
400 / 182 415 / 189 420 / 191
5509 420 / 191 435 / 197 440 / 220
5511 460 / 209 475 / 216 480 / 218
5514 500 / 227 515 / 234 520 / 236
5516 540 / 245 555 / 252 560 / 255
5518 580 / 264 595 / 270 600 / 273
5520 610 / 277 625 / 284 630 / 286
TABLE 2 — MAXIMUM OPERATING LIMITS
MODEL MAXIMUM RPM
MAXIMUM PRESSURE
DIFFERENTIAL
psi / mbar MAXIMUM VACUUM
in. Hg / mbar
MAXIMUM
TEMPERATURE RISE
°F / °C MAWP
psi / bar
4006
3600
15 / 1035 15 / 508 300 / 167
100 / 6.9
4009 18 / 1241* 17 / 575 360 / 200*
4012 15 / 1035 15 / 508 300 / 167*
5507
3600
18 / 1241* 17 / 575 360 / 200*
5509 18 / 1241* 17 / 575 360 / 200*
5511 17 / 1172 17 / 575 360 / 200*
5514 13 / 896 15 / 508 300 / 167
5516 12 / 827 15 / 508 260 / 144
5518 10 / 690 15 / 508 200 / 111
5520 8 / 551 12 / 406 180 / 100
* High pressure option
WARNING
The maximum pressure differential is based on the difference between the
inlet pressure and the outlet pressure. The maximum pressure differential
shall not be exceeded. Exceeding the maximum pressure differential will
cause serious damage to the equipment and could cause bodily injury.
WARNING
The maximum allowable working pressure (MAWP) is based on the
absolutepressureofthe blower housingandisNOTthemaximumallowable
pressure differential. Exceeding the MAWP will cause serious damage to
the equipment and could cause bodily injury.
To permit continued satisfactory performance, a blower must be operated within certain approved limiting
conditions. The manufacturer’s warranty is, of course, also contingent on such operation. Maximum limits
for pressure, temperature and speed are specified here for various blower sizes when operated under the
standard atmospheric conditions. Do not exceed any one of these limits.

8
NOTE
Specially ordered blowers with nonstandard construction, or with rotor end
clearances greater than shown within the Assembly Clearances table, will
not have the operating limits specified here. Contact your Tuthill Vacuum &
Blower Systems sales representative for specific information.
NOTE
Special attention must be paid when a blower has a higher than standard
ambient suction temperature. Special recommendations for operating
parameters and/or additional cooling may be recommended. Consult the
factory or local representative for appropriate information.
5. INSTALLATION
5.1 GENERAL
DANGER
Thebloweris not intendedtobeused withexplosiveproductsor inexplosive
environments.
DANGER
It is the responsibility of the installer to assure that proper guarding is in
place and compliant with all applicable regulatory requirements.
WARNING
The bare shaft blower can generate excessive noise. Methods to reduce
the noise levels by installing inlet and outlet silencers will be required. Even
with inlet and outlet silencers, hearing protection will be required.
WARNING
Customers are warned to provide adequate protection, warning and safety
equipmentnecessaryto protectpersonnelagainst hazardsintheinstallation
and operation of this equipment in the system or facility.
WARNING
The standard MAWP is per Table 2. The MAWP shall not be exceeded
unless specific factory testing of the pressure containing components of the
blower has been performed.
WARNING
Table 2 states the maximum operating speed in RPM (rotations per minute)
and maximum temperature. Do not exceed these limits. The installation of
the blower shall take these critical operating parameters into account and
adequate control features implemented.
WARNING
Upon completion of the installation, and before applying power, rotate the
drive shaft by hand. It must move freely. If it does not, look for uneven
mounting, piping strain, excessive belt tension or coupling misalignment or
any other cause of binding. If blower is removed and still does not move
freely, check inside the blower housing for foreign material.

9
NOTE
Remove the protective covers from the shaft and inspect for damage.
Carefully check to ensure that no transit damage has been sustained. If damage has occurred from
shipment a claim must be filed with the carrier immediately; preserve the shipping container for inspection
by the carrier.
NOTE
In the event that your unit sustains damage while being shipped to your
facility, do not return it to the factory without first obtaining shipping
instructions from us.
Protective covers and plugs should not be removed until the connection is being made. Mount the blower
on a flat, level surface. We recommend a baseplate that is a rigid, solidly supported, and structurally
sound. Shim under the legs where necessary so that each leg of the blower supports an equal share of the
blower weight. This is necessary to prevent eventual twisting of the blower. Make sure feet rest evenly on
the mounting surface before fastening down. Twisting or cramping the blower in mounting will cause rotor
contact and binding during operation, resulting in a condition called “soft foot”. (See the Soft Foot section
of this manual for further details and preventative measures.)
A unit that is factory mounted on a base, should not require the above adjustments. However, since
the assembly can become twisted in shipping or installation, checking for soft foot should be done after
installation of the base. Shims may be needed for alignment. Loosen the foot hold-down screws to check
foot contact with the mounting surface. The base should be mounted on a solid foundation or heavy flooring,
using shims as necessary at bolting points to prevent warping the assembly. (Also refer to the Foundation
section.)
Transmission of small operating vibrations to a support structure may be objectionable in some cases. Use
of vibration isolators or vibration absorbing materials can be effective in overcoming this problem. To avoid
casing distortion, the treatment used should be applied under the common motor/blower base or mounting
plate, rather than directly under the feet alone.
Piping should be accurately squared with the blower and supported independently. Stress imparted from
incorrectly aligned piping or mounting will create problems with bearing and seal life, possibly leading
to premature internal contact. The blower should sit stress free and evenly on its supporting surface.
Care should be taken to evenly tighten the
mounting bolts to not impart undue stress
into the blower. Stress can be checked in a
free state with feeler stock or verified on a
previously installed blower with the aid of a
dial indicator. Less than .002” (.05 mm) spring
or gap should be found.
Use only clean new pipe and make certain it
is free of scale, cuttings, weld beads, dirt, or
any other foreign material. To guard against
damage to the blower, insure that an inlet
filter is used. Make provisions to clean the
filter of collected debris after a few hours of
operation and periodically thereafter. (See
the Piping Connections section for additional
details.)
Figure 3 shows a typical complete installation
of blower and accessories. Note the absence Figure 3 - Typical Blower Installation
AIR FILTER
PRESSURE
RELIEF VALVE
CHECK VALVE
FLEX CONN.
PRESSURE GAUGE DISCHARGE
SILENCER
INTAKE SILENCER
FLOW
FLOW

10
of throttle or shut-off valves in either discharge or intake piping. If it is possible for air flow to be cut off in
either of these lines, make provisions to add a pressure and/or vacuum relief valve. In some installations,
it may be desirable to use only an inlet silencer-cleaner supported directly from the blower connection.
Weight of accessories and piping must be kept to a minimum to prevent blower casing distortion. Weights in
excess of 10% of blower weight should be supported independently of blower and connected with a flexible
hose or connectors. (The approximate weight of your unit is included within the Specifications table.)
A blower may be driven by direct-coupling to the driver or by V-belt drive, to obtain other speeds within
approved range. (See the Motor Drives section for more information.)
Blowers from Tuthill Vacuum & Blower Systems are internally and externally treated after factory assembly
and testing to protect against rusting in normal atmospheric conditions prior to installation. The maximum
period of internal protection is considered to be up to 6 months under average conditions, provided closing
plugs and seals are not removed. Protection against chemical or salt water atmosphere is not provided.
Avoidopeningtheblower until ready tobegininstallation,asprotectionwillbequicklylostduetoevaporation.
(For recommended preparations for long term storage (longer than 6 months), please see the Long Term
Storage section in this manual.)
5.1.1 LOCATION
Install your blower in a room or outdoor area that supplies adequate space and lighting for routine
maintenance. Indoor installation areas should be well ventilated and kept as cool as possible, because
operating the unit at elevated temperatures can result in nuisance overload or temperature shutdowns. An
unprotected outdoor installation is only satisfactory when correct lubrication for expected temperatures is
provided, as per the Recommended Lubricants section in this manual.
5.1.2 BLOWER AIR INTAKE
To minimize maintenance, supply your blower with the cleanest air possible. It is important that the air does
not contain any flammable or toxic gases, as the blower will concentrate these gases. This could result in
damage to the unit and surrounding property, lead to personal injury or death. Do not block or restrict the
opening or the blower and/or motor may overheat and fail.
Do not use blowers on explosive or hazardous gases. Each size blower has limits on pressure differential,
running speed, and discharge temperature. These limits must not be exceeded. Consult Table 2 for details
pertaining to the allowable performance criteria.
If it is necessary to take air from a remote source, such as in a vacuum application, the piping should be
at least the same diameter of the blower inlet. For distances greater than 20 feet (6 m) the pipe diameter
should be enlarged to reduce inlet restriction. Excessive restriction will reduce the efficiency of the blower
and elevate its discharge temperature. The piping used should also be corrosion resistant, and free of
scale and dirt. The inlet should be covered to keep out precipitation, insects, and small animals. Vacuum
kits are available.

11
5.1.3 SOFT FOOT
Soft foot is a condition in which one of the blower feet does not sit
flat on the base. Usually, this is due to irregularities in the surface
to which the blower is mounted. When you tighten the bolt on the
foot, the blower will distort slightly, but enough to cause problems
with bearing and seal life, and premature internal contact between
the rotors and the housing.
1. Place blower on base.
2. Check each foot for gaps between foot and base (soft foot),
shim as necessary to fill gap within .002” (.05 mm) Below are
shown the two most common types of soft foot conditions. If
either type is present, and measures more than .003” (.076
mm), the blower may fail prematurely.
3. Tighten all bolts.
4. Mount a dial indicator on base contacting one foot at 12
o’clock position.
5. Loosen bolt on that foot. Observe indicator travel and add
shims as needed to reduce “spring” to less than .002” (.05
mm). Repeat steps 4 and 5 on remaining feet.
5.2 SAFETY
TuthillVacuum&Blower Systemsrecommendstheuse ofreliefvalvesto protectagainstexcessive pressure
or vacuum conditions. These valves should be tested at initial start-up to be sure they are properly adjusted
to relieve at or below the maximum pressure differential rating of the blower.
DANGER
It is the responsibility of the installer to assure that proper guarding is in
place and compliant with all applicable regulatory requirements.
DANGER
Internal and external rotating parts of the blower and driving equipment can
produce serious physical injuries. The blower should never be run with the
inlet or discharge piping removed. If it becomes necessary to inspect the
rotating parts of the blower or to change V-belts, be absolutely sure that all
power to the motor controls has been shut off, the motor controls are locked
out, and properly tagged before proceeding.
DANGER
Assure that properly sized vacuum breaks/relief valves are used on the inlet
side of the blower. Also assure that properly sized pressure relief valves
are used on the outlet of the blower. The sizing shall be such to assure that
the proper flow can be achieved without exceeding the rated vacuum and
pressure ratings.
DANGER
Blower housing and associated piping or accessories may become hot
enough to cause major skin burns on contact.
Figure 4 - Illustrations of Soft Foot
ANGULAR
SOFT FOOT
PARALLEL
SOFT FOOT

12
WARNING
Use lock out/tag out procedures to disable the electrical energy source
before any service or work is done on the blower.
WARNING
Avoid extended exposure in close proximity to machinery with high intensity
noise levels. Wear adequate ear protection.
NOTE
Use proper care and good procedures in handling, lifting, installing,
operating, and maintaining the equipment.
5.3 LUBRICATION
Every blower from Tuthill Vacuum & Blower Systems is factory tested, oil drained and shipped dry to its
installation point. Both independent oil reservoirs must be filled to the proper level before operation. Oil
reservoirs are under vacuum.
Shaft bearings at the gear end of the blower are splash lubricated by one or both gears dipping into an oil
reservoir formed in the gear end plate and cover. Shaft bearings at the drive end of the blower are lubricated
by a slinger assembly dipping into an oil reservoir. Before starting the blower, fill oil sumps as shown below
within the Filling Procedure section.
Add oil to the blower in the quantity shown within the Specifications Table. The oil level must be maintained
within the notched area of the sight glass. See Figure 5. Lower drive units have “bull’s eye” type oil level
gauges. Maintain oil levels at the center of the glass.
WARNING
Never attempt to change or add lubrication while the blower is running.
Failure to heed this warning could result in damage to the equipment or
personal injury. Oil must be checked when the blower is NOT running.
WARNING
Properly dispose of the spent lubricants. Refer to the manufacturer of the
lubricant and any regulations to assure proper and safe disposal.
WARNING
Do not start the blower until you are sure oil has been put in the gear
housing and rear cover. Operation of the blower without proper lubrication
will cause the blower to fail and void the warranty.
NOTE
Assure oil is compatible with copper/yellow metals (if equipped with cooling
coils).
NOTE
Refer to Table 1 for oil capacities.

13
5.3.1 FILLING PROCEDURE
See Figure 5. Recommended lubricants are shown on page 35.
1. Remove fill plugs or breathers from both gear end and drive end plates.
2. SLOWLYpour oil through fill until oil appears in the oil sight glass. Bring oil level to center of sight glass.
3. Verify oil level is at proper level in BOTH gear end and drive end sight glasses.
4. Replace fill plugs or breathers that were removed in step 1.
HORIZONTAL FLOW VERTICAL FLOW
END END
SIDE SIDE
MAGNETIC
DRAIN PLUG
(1) EA
END PLATE
MAGNETIC
DRAIN PLUG
(1) EA
END PLATE
OIL LEVEL
GAUGE
(1) EA
END COVER
OIL LEVEL
GAUGE
(1) EA
END PLATE
BREATHER
& OIL FILL
(1) EA
END PLATE
BREATHER
& OIL FILL
(1) EA
END PLATE
Figure 5 - Oil Fill, Drain Connections and Oil Level Gauges
5.3.2 FREQUENTLY ASKED QUESTIONS REGARDING LUBRICATION
What is the functional detriment if the “wrong oil” is used?
The lubricant is selected based on bearing and gear speed, and operating temperature. Too light
of a lubricant increases wear by not separating the sliding surfaces and it will not remove the heat
adequately. If the lubricant is too thick, the drag in the bearings is increased causing them to run hotter.
Since it is thicker, it will not flow as readily into the gears and it will reduce the available backlash.
Lubricants at our conditions are incompressible.
What is the functional detriment if the oil is not serviced?
If the lubricant is not serviced at the proper interval the shearing action in the bearing and the gears will
begin to take their toll and the lubricant will thicken, making matters worse. The unit will run hotter and
the wear on running surfaces will increase. Generally, the lubricant will appear dirtier, this is actually
material rubbed off the unit’s components. The discoloration comes from overheating the additive
package. An indicator of the breakdown of a lubricant is the increase in the TAN (Total Acid Number),
and a change in the base viscosity of ten percent.
Several things are happening as the lubricant goes through the unit. First, it is absorbing frictional
energy in the form of heat. This heat has to be dissipated through either surface contact with cooler
materials, or in a rest volume of lubricant. While reducing the friction, the lubricant is also going through
a shearing process and the molecular structure is broken down.
The result is that the lubricant will begin to thicken because of the shorter molecular chains and the drop
out of additive packages. The thickened lubricant will cause more drag, increasing the friction and heat,
and further degrading the lubricant.
Operation of the blower (environment, run time, speed, and pressure) has a direct effect on duty cycles.
Our published cycles are based on worst-case conditions.

14
5.3.3 HAZARDS ASSOCIATED WITH BREAKDOWN OR IGNITION OF LUBRICATION
DANGER
There is a risk associated with the lubrication media breaking down and
resulting in a hazardous fluid or vapor. There may also be a hazard
associated with the ignition of the lubrication media. Refer to the lubrication
manufacture’s applicable instruction for safety precautions.
5.4 PIPING CONNECTIONS
WARNING
Pipe loading on the blower should be negligible as pipe loading can cause
distortion of the blower. Use proper supports and pipe hangers to assure
that there is no loading.
NOTE
Remove the protective covers from the inlet and outlet ports and inspect for
dirt and foreign material.
Inlet and outlet connections on all blowers are large enough to handle maximum volume with minimum
friction loss. Maintain same diameter piping. Silencers must not be supported by the blower. Stress loads
and bending moments must be avoided.
Be certain all piping is clean internally before connecting to the blower. We recommend placing a 16-mesh
wire screen backed with hardware cloth at or near the inlet connections for the first 50 hours of use until the
system is clean. Make provisions to clean the screen after a few hours of operation and completely discard
it once the system is clean, as it will eventually deteriorate and small pieces going into the blower can cause
serious damage. A horizontal or vertical air flow piping configuration is easily achieved by rearranging the
mounting feet position.
HAZARDS ASSOCIATED WITH HAZARDOUS PROCESS FLUIDS
DANGER
It shall be the responsibility of the installer to ensure that piping is adequate,
sealing between pipe joints is adequate for the process fluids and proper
process and pressure protection devices are in place. It is also the
responsibility of the installer to assure that process gasses are not vented
in a manner that would be hazardous.
Refer to the manufacturer of the process media to assure that proper safety
precautions are in place.
5.4.1 BLOCKAGE OR RESTRICTION
WARNING
Damage to the blower could occur if there is blockage in the inlet or outlet
ports or piping. Care should be taken when installing the blower to assure
that there are no foreign objects or restrictions in the ports or piping.

15
5.5 COOLING COILS (OPTIONAL)
CAUTION
If the blower is to be located outdoors or in a building where the temperature
surrounding the blower or the water supply and return piping can fall below
35°F (2°C), then care must be taken to ensure that the water (or other
cooling liquid) does not freeze and cause damage. Cooling coils must be
drained of liquid during downtime unless a recirculating unit using a glycol
mixture has been installed.
NOTE
Water cooled endplates are discontinued. Consult factory for connection
details.
NOTE
Units are never shipped from the manufacturer with liquid in the end plates
or cooling coils.
Blowers supplied with cooling coils are identified by the letter located in the tenth position of the complete
blower model number.
Blowers supplied with coiling coils can also be identified by the hose that connects the top of the gear (drive)
end cover to the bottom of the free (non-drive) end cover. See Figures 5 and 6 for details. Tuthill Vacuum
& Blower Systems recommends water cooling for blowers in applications where the blower operates with
discharge temperatures of 250° F (120° C) for periods of 4 hours or greater per day. The use of water
cooling reduces oil temperature and improves oil viscosity for better lubrication. Generally, a water flow or
0.5-1.0 GPM (1.9-3.8 L/min) is sufficient to maintain oil temperatures of 150° F (65° C) or below. Do not
allow water pressure to exceed 75 PSIG (510 kPa g).
5.6 COOLING WATER CONNECTIONS AND SPECIFICATIONS — COOLING COILS
(OPTIONAL)
Figure 6 - Water Cooling Connections
46/81 SERIES 64 SERIES 67 SERIES
END END END
SIDE SIDE SIDE
1/8 NPT
WATER
INLET
1/8 NPT
WATER
OUTLET
BREATHER
& OIL FILL
(1) EA
END COVER
1/4 NPT
WATER INLET 1/4 NPT
WATER INLET
1/8 NPT
WATER
OUTLET
OIL FILL
PLUG
(1) EA
END PLATE
1/8 NPT
WATER
OUTLET
WARNING
The cooling water pressure shall not exceed 75 psig (5.17 bar g)

16
Proper gap between coupling halves must be established according to coupling manufacturers instructions
with the motor armature. This will minimize the change for end thrust on the blower shaft.All direct coupled
base mounted units must be re-aligned and greased after field installation.
5.7 MOTOR DRIVES
Two drive connections commonly used are direct drive and V-belt drive.
5.7.1 DIRECT COUPLED
When installing the motor directly to the blower, align shafts to coupling in accordance with the coupling
manufacturer’s instructions. Blowers shipped with motor directly coupled and mounted on a common base
have been aligned prior to shipment and normally no further alignment is necessary. However, alignment
should be checked and adjustments made if necessary prior to starting the unit.
Coupling halves must correctly fit the blower and drive shafts so that only light tapping is required to install
each half. The two shafts must be accurately aligned, A direct coupled blower and motor must be aligned
with the two shafts not having more than .005” (13 mm) T.I.R. (Total Indicator Reading). Face must be
aligned within .002”(.05 mm) .
Proper gap between coupling halves must be established according to coupling manufacturers instructions
with the motor armature. This will minimize the change for end thrust on the blower shaft.All direct coupled
base mounted units must be re-aligned and greased after field installation.
5.7.2 V-BELTS
If the motor and blower are V-belt connected, the sheaves on both motor and blower shafts, should be as
close to the shaft bearings as possible. Blower Sheave is not more than 1/4” (6.5 mm) from the blower
drive end cover. The drive sheave is as close to the driver bearing as possible. Care should be taken when
installing sheaves on the blower and motor shafts. The face of the should be accurately in line to minimize
belt wear.
Adjust the belt tension to the to the manufactures specifications using a belt tension tester. New belts should
be checked for proper tension after 24 hours of run time. When manufacturer data is not available industry
guidelines are 1/64 inch deflection for each inch of span at 8 to 10 pounds of force in the center of the belt.
Insufficient tensioning is often indicated by slipping (squealing) at start up. Belt dressing should not be
used on V-belts. Sheaves and V-belts should
remain free of oil and grease. Tension should be
removed from belts if the drive is to be inactive
for an extended period of time. For more specific
information consult the drive manufacturer. In a
v-belt drive, the blower sheave must fit its shaft
accurately, run true, and be mounted as close
to the bearing housing as possible to minimize
bearing loads.
Atight or driving fit will force the drive shaft out of
its normal position and cause internal damage. A
loose fit will result in shaft damage or breaking.
The motor sheave must also fit correctly and be
properly aligned with the blower sheave.
Adjust motor position on its sliding base so
that belt tension is in accordance with drive
manufacturer’s instructions. Avoid excessive
belt tension at all times. Recheck tension after
the first ten hours of operation and periodically
thereafter to avoid slippage and loss of blower
speed.
Too Tight
Slight Bow Too Loose
20/64” = 5/16” (8 mm)
20”
(50.8 cm)
8-10 lbs.
(3.6-4.5 kg)
Figure 7 - General appearance of a V-Belt drive
Figure 8 - Setting of proper tension for a V-Belt drive

17
Check blower after installation and before applying power by rotating the drive shaft by hand. If it does not
rotate freely, look for uneven mounting, piping strain, excessive belt tension, or coupling misalignment.
Check blower at this time to insure oil was added to the reservoirs.
5.7.3 SETTING V-BELT TENSION
Proper belt tension is essential to long blower life. The following diagrams and procedures are provided to
aid in field adjusting V-belts (when blower is so equipped) for maximum performance.A visual inspection of
the V-belt drive should yield the appearance shown in Figure 7.
Factors outside the control of the belt tensioning system used on an individual blower package assembly
may contribute to decreased belt life, such as environmental factors, and quality of the belts installed. This
can cause wear of the belts beyond the ability of the tensioning system to compensate.
As such, it is recommended to check belt tension monthly and make any manual adjustments found
necessary.
1. Turn off and lock out power.
2. Remove the fasteners from the belt guard (if equipped)
3. Remove the belt guard.
4. Check and adjust the belt tension as necessary. It should be 1/64” deflection per inch of span (0.157
mm) deflection per centimeter of span) between sheaves, with 8-10 lbs. (3.6-4.5 kg) force applied at
center point of the top section of belt.
5. Install the belt guard, making sure that all drive components are free of contact with the guard.
6. Install belt guard fasteners removed in step 2.
7. Unlock the power and start your blower.
8. Resume normal operation.

18
5.7.4 V-BELT TROUBLESHOOTING
PROBLEM POSSIBLE CAUSES SOLUTION
Belts slip (sidewalls glazed) Not enough tension Replace belts; apply proper tension
Drive squeals Shock load Apply proper tension
Not enough arc of contact Increase center distance
Heavy starting load Increase belt tension
Belt(s) turned over
Broken cord caused by prying on sheave Replace set of belts and install correctly
Overloaded drive Redesign drive
Impulse loads Apply proper tension
Misalignment of sheave and shaft Realign drive
Worn sheave grooves Replace sheaves
Excessive belt vibration Check drive design
Check equipment for solid mounting
Consider use of banded belts
Mismatched belts New belts installed with old belts Replace belts in matched sets only
Breakage of belt(s)
Shock loads Apply proper tension; recheck drive
Heavy starting loads Apply proper tension; recheck drive
Use compensator starting
Belt pried over sheaves Replace set of belts correctly
Foreign objects in drives Provide drive guard
Rapid belt wear
Sheave grooves worn Replace sheaves
Sheave diameter too small Redesign drive
Mismatched belts Replace with matched belts
Drive overloaded Redesign drive
Belt slips Increase tension
Sheaves misaligned Align sheaves
Oil or heat condition Eliminate oil. Ventilate drive.
5.8 SPECIAL INSTRUCTIONS FOR BLOWERS WITH EXTERNAL LUBRICATION SYSTEMS
Blowers furnished with external lube
systems are designated with a special
series number after the model number;
for example, 4009-84. On older units,
it will appear before the model number.
There are four variations manufactured:
• 85 - Lip Seal/Vertical Flow (46)*
• 84 - Mechanical Seal
Single Envelope Gastight /
Vertical Flow (81)*
• 18 - Lip Seal/Horizontal Flow (17)*
• 54 - Mechanical Seal
Single Envelope Gastight /
Horizontal Flow (57)*
* Use this corresponding number when following the repair procedure. The blowers are the same except for
the end plates which have different drillings for lubrication purposes.
CAUTION
Field conversions cannot be made on 46 and 81 series without replacing
end plates. Consult factory before making any conversions.
END SIDE
EXTERNAL LUBE
PRESSURE EQUALIZATION CONN
COMPRESSION FITTING FOR 3/8"
O.D. TUBING (1) EA END COVER
LUBE OIL RETURN
COMPRESSION FITTING
FOR 3/4" O.D. TUBING
(1) EA END PLATE
MAGNETIC DRAIN
PLUG (1) EA
END PLATE
LUBE OIL INLET CONN
COMPRESSION FITTING
FOR 1/4 O.D. TUBING
OIL FILL
PLUG (1) EA
END COVER
Figure 9 - External Lube Oil Connections

19
1. The external lube tank is equipped with an oil filter which has a replaceable element. The part number
for the element is 91999-1.
2. Each tank has an oil pressure relief valve which is set at the factory at 12 - 15 PSIG (80 - 100 kPa g)
and normally requires no adjustment. If an adjustment becomes necessary, remove the cap and adjust
the screw. Clockwise will increase pressure, and counterclockwise will reduce pressure.
3. Oiltank shouldbeon alevel surface withreturn connectionsof tank belowthe blowerreturnconnections
at approximately 2 inches drop per foot (16.5 cm drop per meter). Each end of blower shall have
separate return hose lines (3/4” [19 mm] I.D. minimum) not over six feet from farthest blower.
4. The oil supply hose and connections must be kept free of dirt and foreign material during installation to
prevent clogging of blower oil supply restrictors (.055” [1.40 mm] diameter).
5. Make sure motor pump wiring connection is for correct rotation as indicated by arrow on motor.
6. Tanks equipped with heat exchangers should have water flow direction counter to oil flow. Required
water flow rate is approximately 0.25 - 1.0 GPM (0.95 - 3.8 L/min) depending upon blower operating
condition (oil sump temperature should not exceed 250° F [120° C] maximum).
CAUTION
Fill both ends of blower with oil to proper level, then operate oil supply
system, and be sure oil is returning from both blower return hoses prior to
starting blower.
5.9 MOTOR AND ELECTRICAL CONNECTIONS
WARNING
The motor and connections shall be protected to assure that product and
environmental condensation does not come in contact with the electrical
connections.
NOTE
Itistheresponsibility of theinstallertoassure that themotorisin compliance
with the latest edition of IEC 60204-1 and all electrical connections
performed per IEC 60204-1, this includes over current protection.
Wire the motor and other electrical devices such as solenoid valves and temperature switch to the proper
voltage and amperage as indicated on the nameplate of each component being wired. Turn the blower by
hand after wiring is completed to determine that there are no obstructions and if the blower turns freely;
then momentarily start the blower to check the direction of rotation. Figure 2 shows direction of air flow in
relation to rotor rotation. The air flow direction can be reversed by reversing the appropriate motor leads.

20
6. OPERATION
6.1 GENERAL
DANGER
Thebloweris not intendedtobeused withexplosiveproductsor inexplosive
environments.
WARNING
Do not operate without guards in place.
WARNING
Maximum operating speed: Table 2 states the maximum operating speed in
RPM (rotations per minute), the maximum pressure differential, maximum
vacuum and maximum temperature rise. Do not exceed these limits.
Before starting the blower for the first time under power, recheck the installation thoroughly to reduce the
likelihood of troubles. Use the following check list as a guide, but also consider any other special conditions
in your installation.
1. Be certain no bolts, rags, or dirt have been left in blower.
2. Be certain that inlet piping is free of debris. If an open outdoor air intake is used, be sure the opening is
clean and protected by an inlet filter. This also applies to indoor use.
3. If installation is not recent, check blower leveling, drive alignment, belt tension, and tightness of all
mounting bolts.
4. Be certain the proper volume of oil is in the oil reservoir chambers.
5. Be certain the driving motor is properly lubricated, and that it is connected through suitable electrical
overload devices.
6. With electrical power off and locked out to prevent accidental starting, rotate blower shaft several times
by hand to make sure blower is rotating freely. Unevenness or tight spots is an indication of a problem
that should be corrected before progressing.
7. Check motor rotation by momentarily pushing the start button and check flow direction of the blower.
Reverse the motor connections if flow is in the wrong direction.
Initial operation should be carried out under “no load” conditions by opening all valves and venting the
discharge to atmosphere, if possible. Then start motor briefly, listen for unusual noises, and check that the
blower coasts freely to a stop. If no problem appears, repeat this check, and let the motor run a little longer.
If any questions exist, investigate before proceeding further.
Assuming all tests are satisfactory, the blower will now be ready for continuous full load operation. During
the first several days, make periodic checks to determine that all conditions remain acceptable and steady.
These checks may be particularly important if the blower is part of a process system where conditions may
vary.At the first opportunity, stop the blower and clean or remove inlet filter.Also, recheck leveling, coupling
alignment or belt tension, and mountlng bolts for tightness.
This manual suits for next models
12
Table of contents
Other Tuthill Blower manuals
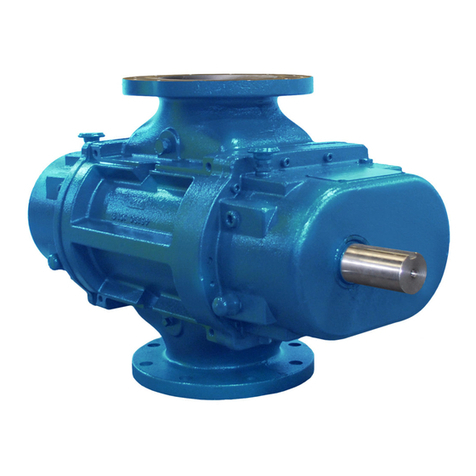
Tuthill
Tuthill Qx Series User manual
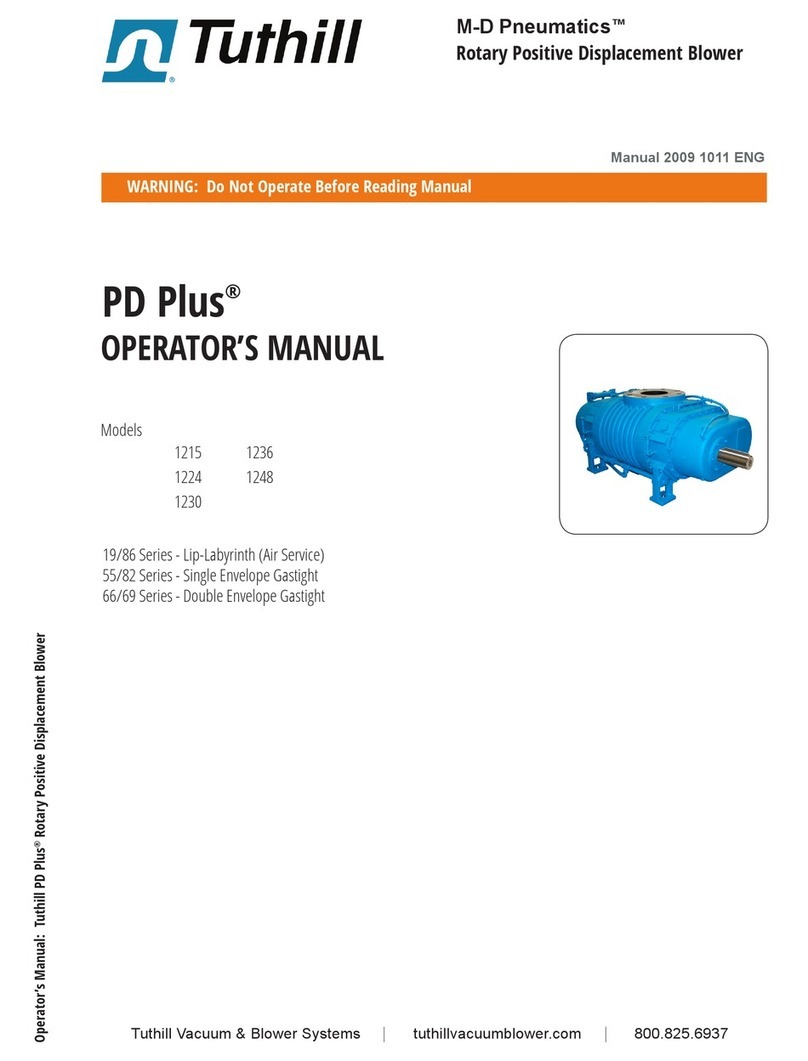
Tuthill
Tuthill PD Plus 1215 User manual
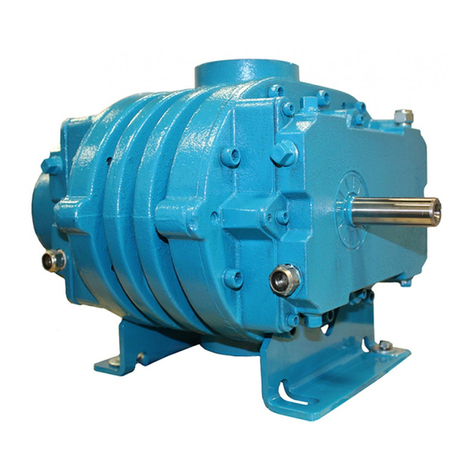
Tuthill
Tuthill 2002 User manual
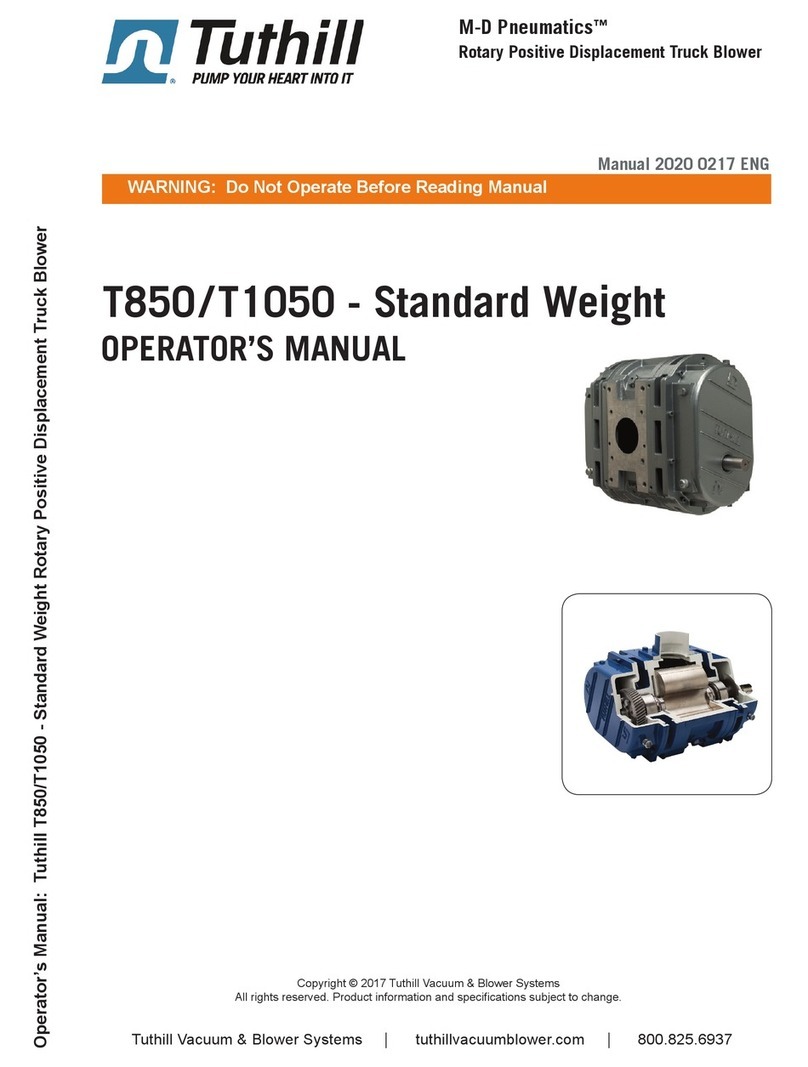
Tuthill
Tuthill T850 User manual
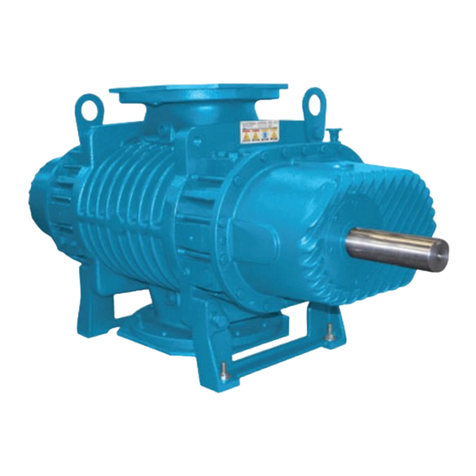
Tuthill
Tuthill PD Plus User manual
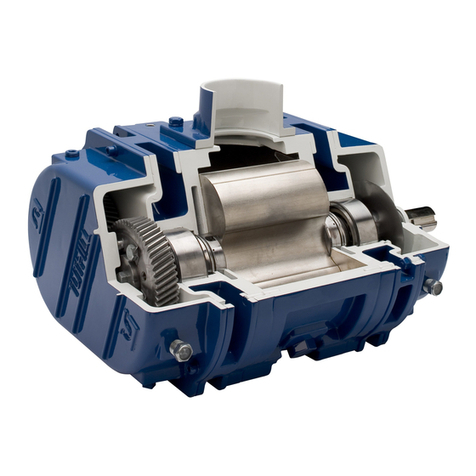
Tuthill
Tuthill TI850 Operating instructions
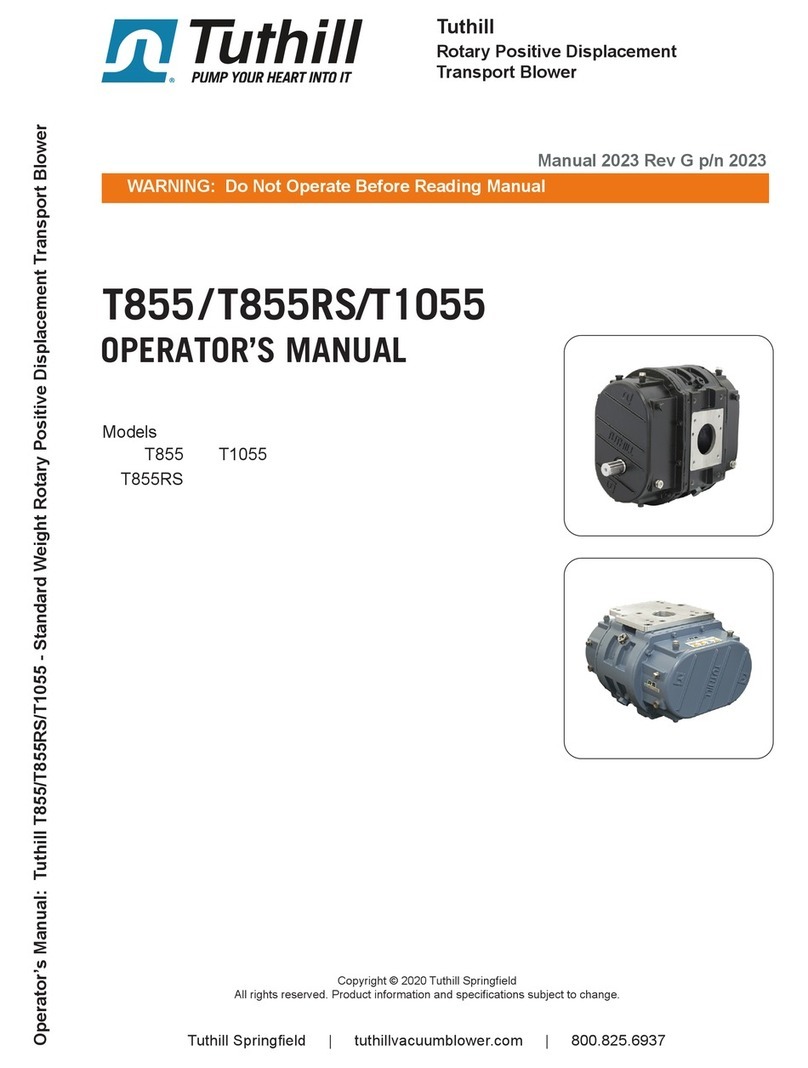
Tuthill
Tuthill T855RS User manual
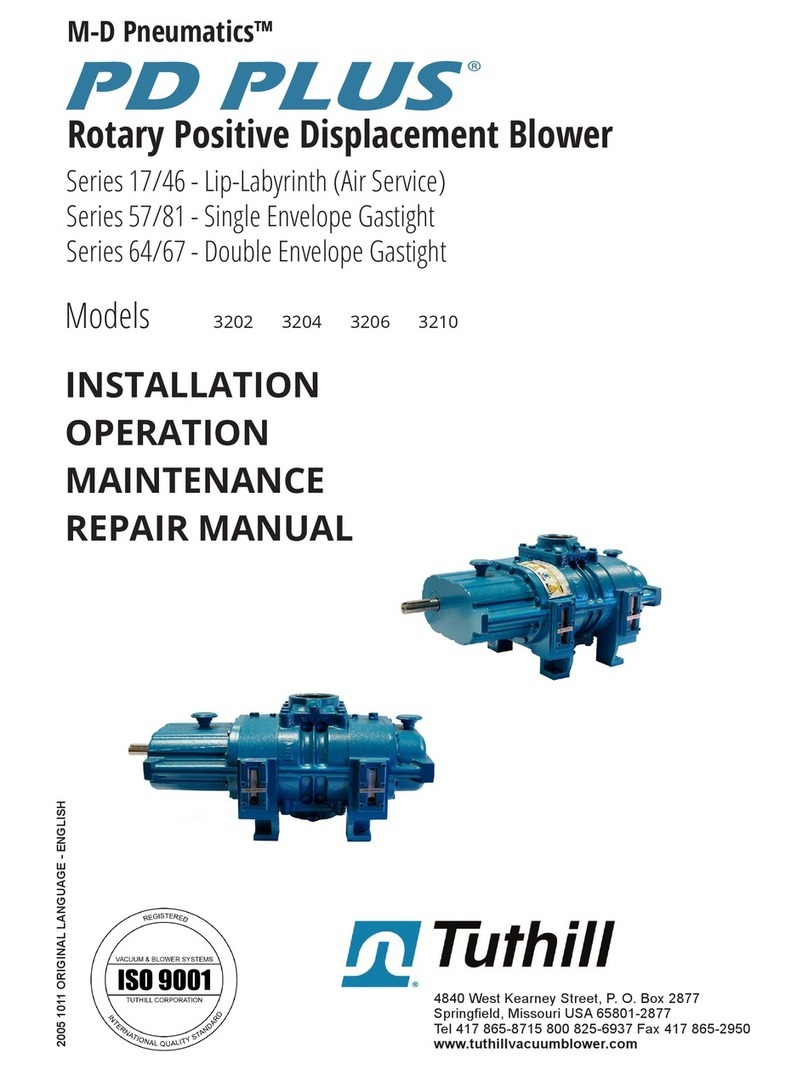
Tuthill
Tuthill M-D Pneumatics PD PLUS 17/46 Series Operating instructions
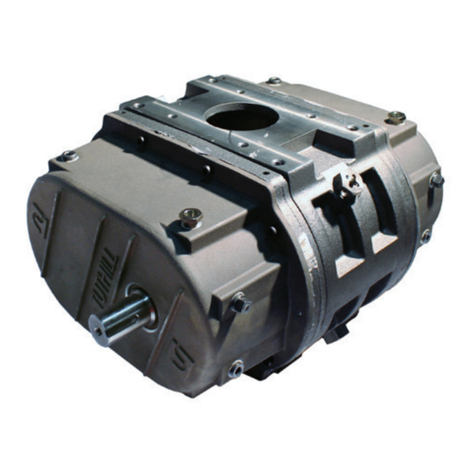
Tuthill
Tuthill T855 User manual

Tuthill
Tuthill M-D Pneumatics Qube 400 User manual