Tuthill PD Plus User manual

M-D Pneumatics™
Rotary Positive Displacement Blower
PD Plus
Models
7010 7021
7013 7026
7017
Horizontal Air Flow
Vertical Air Flow
Horizontal Flow, Single Envelope Gastight
Vertical Flow, Single Envelope Gastight
Horizontal Flow, Double Envelope Gastight
Vertical Flow, Double Envelope Gastight
OPERATOR’S MANUAL
Manual 2007 Rev B p/n 2007
Tuthill Vacuum & Blower Systems tuthillvacuumblower.com 800.825.6937
WARNING: Do Not Operate Before Reading Manual
Operator’s Manual: Tuthill PD Plus Rotary Positive Displacement Blower
Copyright © 2018 Tuthill Vacuum & Blower Systems
All rights reserved. Product information and specications subject to change.

Disclaimer Statement:
All information, illustrations and specications in this manual are based on the latest information available at
the time of publishing. The illustrations used in this manual are intended as representative reference views
only. Products are under a continuous improvement policy. Thus, information, illustrations and/or specications
to explain and/or exemplify a product, service or maintenance improvement may be changed at any time
without notice.
Rights Reserved Statement:
No part of this publication may be reproduced or used in any form by any means – graphic, electronic or
mechanical, including photocopying, recording, taping or information storage and retrieval systems – without
the written permission of Tuthill Vacuum & Blower Systems.
Copyright © 2018 Tuthill Vacuum & Blower Systems
All rights reserved. Product information and specications subject to change.

Manual 2007 Rev B p/n 2007 i
Table of Contents
Introduction .................................................................................. 1
Applicable Documentation ................................................................... 1
Scope of Manual................................................................................... 1
Conventions and Data Plate ....................................................... 2
Graphic Conventions in this Manual ..................................................... 2
Data Plate.............................................................................................. 3
Lifting ............................................................................................ 5
Description ................................................................................... 6
Flow by Direction................................................................................... 7
Specifications........................................................................................ 8
Installation .................................................................................. 10
General ............................................................................................... 10
Location.................................................................................... 12
Foundation................................................................................ 12
Blower Air Intake ...................................................................... 12
Soft Foot ................................................................................... 13
Safety .................................................................................................. 13
Lubrication .......................................................................................... 14
Filling Procedure ...................................................................... 15
Frequently Asked Questions Regarding Lubrication ............... 17

Manual 2007 Rev B p/n 2007
ii
Table of Contents
Hazards Associated With Breakdown or Ignition of
Lubrication ............................................................................... 17
Lubrication (Splash) ................................................................. 17
Lubrication (Integral Pressure)................................................. 18
Oil Filter on Integral Lube Blowers........................................... 18
Integral Lube Oil Pressure Adjustment .................................... 18
Piping Connections............................................................................. 18
Hazards Associated With Hazardous Process Fluids.............. 19
Blockage or Restriction ............................................................ 19
Cooling Coils (Optional)...................................................................... 19
Cooling Water Connections and Specifications —
Cooling Coils (Optional)...................................................................... 20
Motor Drives ........................................................................................ 20
Direct Coupled ......................................................................... 20
V-Belts ...................................................................................... 20
Setting V-Belt Tension............................................................... 21
Motor and Electrical Connections ............................................ 22
Operation .................................................................................... 23
General ............................................................................................... 23
Start-Up Checklist............................................................................... 24
Operating ............................................................................................ 25
Stopping.............................................................................................. 25
Methane Gas Applications.................................................................. 25
Water-Injected Blowers ....................................................................... 26
Operation ................................................................................. 26
Shutdown ................................................................................. 26
Recommended Shutdown Procedure to Minimize Risk of
Freezing or Corrosion ......................................................................... 27

Manual 2007 Rev B p/n 2007 iii
Table of Contents
Maintenance ............................................................................... 28
General ............................................................................................... 28
Regular Maintenance.......................................................................... 28
Spare Parts ......................................................................................... 29
Factory Service and Repair ................................................................ 29
Long-Term Storage ............................................................................. 30
Disassembly and Reassembly.................................................. 31
Disassembly of Blower ....................................................................... 31
Assembly of 7000 Blower ................................................................... 33
Preparation of End Plates for Assembly .................................. 33
Mechanical Seal Blowers ......................................................... 33
Gear End Assembly ................................................................. 33
Adjusting Rotor Interlobe Clearance........................................ 35
Drive Shaft Seal Assembly ....................................................... 36
Troubleshooting......................................................................... 37
Assembly Clearances................................................................ 39
Torque Chart............................................................................... 40
Recommended Lubricants........................................................ 41
Recommended Lubricants for Rotary Blowers and Vacuum
Boosters.............................................................................................. 41
Special Tool Drawings............................................................... 43
Parts Lists ........................................................................................... 45
Assembly Drawings ............................................................................ 54
Declaration of Incorporation..................................................... 61
Warranty – Blower Products ..................................................... 62
Operating Data Form / Product Registration........................... 63

Manual 2007 Rev B p/n 2007
iv
Table of Contents

Manual 2007 Rev B p/n 2007 1
CONGRATULATIONS on the purchase of a new
PD PLUS®Rotary Positive Displacement Blower
from Tuthill Vacuum & Blower Systems. Please
examine the blower for shipping damage, and if
any damage is found, report it immediately to the
carrier. If the blower is to be installed at a later
date, make sure it is stored in a clean, dry location
and rotated regularly. Make sure covers are kept
on all openings. If blower is stored outdoors, be
sure to protect it from weather and corrosion.
PD PLUS blowers are built to exacting standards
and, if properly installed and maintained, will
provide many years of reliable service. Read
and follow every step of these instructions when
installing and maintaining your blower.
OTE:NRecord the blower model and serial
numbers of the machine in the
OPERATING DATA form on the inside
back cover of this manual. Use this
identifi cation on any replacement part
orders, or if service or application
assistance is required.
APPLICABLE DOCUMENTATION
The applicable documents associated with this
manual are:
• 2006/42/CE – Machinery Directive
• EN 1012-1:1996 - Compressors and vacuum
pumps - Safety Requirements - Part 1:
Compressors
SCOPE OF MANUAL
The scope of this manual and the Declaration of
Incorporation includes the bare shaft rotary positive
displacement blower.
INTRODUCTION
01

Manual 2007 Rev B p/n 2007
2
GRAPHIC CONVENTIONS IN THIS
MANUAL
This manual is the result of a risk assessment
according to the applicable documents referenced
in “Applicable Documentation” on page 1.
The following hazard levels are referenced within
this manual:
DANGER
!
Indicates a hazardous situation that, if not
avoided, will result in death or serious injury.
WARNING
!
Indicates a hazardous situation that, if not
avoided, could result in death or serious
injury.
CAUTION
!
Indicates a hazardous situation that, if not
avoided, could result in minor or moderate
injury.
Indicates a situation that can cause damage
to the engine, personal property, and/or
the environment or cause the equipment to
operate improperly.
OTE:N Indicates a procedure, practice, or
condition that should be followed in
order for the equipment to function in the
manner intended.
CAUTION
!
Read manual before operation
or bodily harm may result.
Attention should be given to the
safety related sections of this
manual.
CONVENTIONS AND DATA PLATE
02

Manual 2007 Rev B p/n 2007 3
02
Conventions and Data Plate
DATA PLATE
WARNING WARNING CAUTION CAUTION
http://www.tuthill.com
Hearing protection
re
q
uired.
Do not touch hot
surfaces.
AS
Ueht
n
i
e
d
aM7396
-
5
2
8
)
008
(
READ INSTRUCTION MANUAL BEFORE OPERATION OR BODILY HARM MAY RESULT
Keep body & clothing away
from machine openings.
Do not operate without
g
uards in
p
lace.
REBMUNLAIRESREBMUNLEDOM
Tuthill Vacuum & Blower Systems
4840 West Kearney Street
Springfield, Missouri USA 65803
YEARMAWP
MAX RPM
Figure 1-1 – General Operation and Symbols on Data Plate
The following information is contained on the data
plate:
WARNING
!
Keep body and clothing away
from machine.
During operation, keep body
and clothing away from inlet
and outlet of the blower.
WARNING
!
Do not operate without guards
in place.
CAUTION
!
Hearing protection is required
while the blower is in operation.
Noise levels may exceed 81 dBA.
CAUTION
!
Do not touch hot surfaces.
The upper limit of the blower
operation is 400°F (205°C). Do
not touch the blower while it is
in operation and assure blower
is cool when not in operation.

Manual 2007 Rev B p/n 2007
4
02
Conventions and Data Plate
MODEL NUMBER: The specific model of the blower
SERIAL NUMBER: Unique to each blower
YEAR: Year of manufacture
MAWP: Maximum Allowable Working Pressure
The standard MAWP is per Table 4-3 – Maximum Operating Limits on page
9. The MAWP shall not be exceeded.

Manual 2007 Rev B p/n 2007 5
WARNING
!
The blower must be handled using an
appropriate device such as a fork truck or
appropriate lifting device. See Table 4-1
and Table 4-2 on page 8 for approximate
weights. Care should be taken to assure
blower does not over-turn during handling
and installation.
LIFTING
03

Manual 2007 Rev B p/n 2007
6
Refer to specific data sheets for flow capacities
and vacuum capacities.
OTE:NSee Figure 4-2 on page 7 for proper
rotation and orientation in inlet and
discharge.
Tuthill Vacuum & Blower Systems model 7000
rotary lobe blowers are positive displacement type
blowers, whose pumping capacity is determined
by size, operating speed, and differential pressure
conditions. Blowers employ rotors rotating in
opposite directions within a housing closed at the
ends by end plates.
The inlet to the discharge is sealed with operating
clearances that are very small. Internal lubrication
is not needed, as there is no moving contact.
Clearances between the rotors during rotation are
maintained by a pair of accurately machined helical
timing gears, mounted on the two shafts extended
outside the air chamber. The intermeshing rotary
lobes are designed to rotate and trap air or gas
between each rotor and the housing. As the rotor
lobes rotate past the edge of the suction port, the
trapped air or gas is essentially at suction pressure
and temperature. Since the blower is a constant
volume device, the trapped air remains at suction
pressure until the leading rotor lobe opens into the
discharge port. The close clearances between the
rotors inhibit back slippage of the trapped volume
from between the rotors and the trapped volume
is forced into the discharge piping. Compression
occurs not internal to the blower but by the amount
of restriction, either downstream of the blower
discharge port or upstream of the blower inlet port.
Figure 4-1 illustrates the air movement within the
machine. The air moves not between the rotors
but between the rotors and the side of the housing.
Also, the machine is bi-directional, meaning that
the direction of rotation of the blower can make
either side the inlet or discharge. See also Figure
4-2 on page 7.
Never attempt to control capacity by means of a
throttle valve in the intake or discharge piping.
This will increase the power load on the drive
system, will increase operating temperatures,
and can overload and/or seriously damage the
blower. Likewise, if a possibility exists that flow
to the blower inlet may be cut off during normal
operation of a process, install an adequate vacuum
relief valve near the blower. A pressure-type relief
valve in the discharge line near the blower is also
recommended for protection against cutoff or
blocking in this line. Use check valves on each
blower when more than one blower is connected to
a discharge line.
When a belt drive is used, blower speed, it is
possible to adjust blower speed to obtain the
desired capacity by changing the diameter of one or
both sheaves, or by using a variable-speed motor
pulley. In a direct-coupled arrangement, a variable-
speed motor or transmission is required, or excess
air or gas may be blown off through a manually
controlled unloading valve and silencer. Gas units
can use bypasses, but some applications may
require additional cooling. If there is a large volume
of high-pressure air or gas downstream of the
blower, a check valve in the piping downstream of
the blower will protect the blower from overspeeding
in a backward direction upon shutdown.
Consult a Tuthill Vacuum & Blower Systems sales
professional if questions arise.
DESCRIPTION
04

Manual 2007 Rev B p/n 2007 7
04
Description
INLET INLET INLET
DISCHARGE DISCHARGE DISCHARGE
Figure 4-1 – General Operation Principle
FLOW BY DIRECTION
WARNING
!
Refer to diagrams in this manual for
proper rotation and orientation in inlet and
discharge.
INTAKE INTAKE
DISCHARGE INTAKE
DISCHARGE
HORIZONTAL FLOWVERTICAL FLOW
DISCHARGE
INTAKE DISCHARGE
INTAKE
DISCHARGE
RIGHT DRIVE
CW ROTATION
LEFT DRIVE
CW ROTATION
LEFT DRIVE
CCW ROTATION
RIGHT DRIVE
CCW ROTATION
TOP DRIVE
CW ROTATION
TOP DRIVE
CCW ROTATION
BOTTOM DRIVE
CW ROTATION
BOTTOM DRIVE
CCW ROTATION
DISCHARGEINTAKE INTAKE
INTAKEDISCHARGE DISCHARGE
Figure 4-2 – Flow Direction by Rotation

Manual 2007 Rev B p/n 2007
8
04
Description
SPECIFICATIONS
MODEL
APPROXIMATE OIL
CAPACITY PORT SIZE MAXIMUM
RPM
APPROXIMATE WEIGHT
VERTICAL
FLOW
HORIZONTAL
FLOW
VERTICAL
FLOW
HORIZONTAL
FLOW
7010 8.0 qt (7.5 L) 5.0 qt (4.75 L) 6 in. (150 mm) 3,000 – 1,120 lb (510 kg)
7013 8.0 qt (7.5 L) 5.0 qt (4.75 L) 8 in. (200 mm) 3,000 1,255 lb (570 kg) –
7017 8.0 qt (7.5 L) 5.0 qt (4.75 L) 10 in. (250 mm) 3,000 – 1,390 lb (635 kg)
7021 8.0 qt (7.5 L) 5.0 qt (4.75 L) 12 in. (300 mm) 3,000 1,530 lb (695 kg) 1,530 lb (695 kg)
7026 8.0 qt (7.5 L) 5.0 qt (4.75 L) 12 in. (300 mm) 3,000 1,695 lb (770 kg) 1,695 lb (770 kg)
Table 4-1 – Specifications (Sump Oil Lubrication)
MODEL
APPROXIMATE OIL
CAPACITY PORT SIZE MAXIMUM
RPM
APPROXIMATE WEIGHT
VERTICAL
FLOW
HORIZONTAL
FLOW
VERTICAL
FLOW
HORIZONTAL
FLOW
7010 15qt (14.2 L) 12 qt (11.4 L) 6 in. (150 mm) 3,000 – 1,120 lb (510 kg)
7013 15qt (14.2 L) 12 qt (11.4 L) 8 in. (200 mm) 3,000 1,255 lb (570 kg) –
7017 15qt (14.2 L) 12 qt (11.4 L) 10 in. (250 mm) 3,000 – 1,390 lb (635 kg)
7021 15qt (14.2 L) 12 qt (11.4 L) 12 in. (300 mm) 3,000 1,530 lb (695 kg) 1,530 lb (695 kg)
7026 15qt (14.2 L) 12 qt (11.4 L) 12 in. (300 mm) 3,000 1,695 lb (770 kg) 1,695 lb (770 kg)
Table 4-2 – Specifications (Integral Lubrication)

Manual 2007 Rev B p/n 2007 9
04
Description
MODEL MAXIMUM RPM
MAXIMUM
PRESSURE
DIFFERENTIAL
MAXIMUM VACUUM
MAXIMUM
TEMPERATURE
RISE
MAWP
7010 3,000 18 psi (1,241 mbar) 17 inch-Hg
(575 mbar) 300°F (166°C)
100 psi
(6.9 bar)
7013 3,000 18 psi (1,241 mbar) 17 inch-Hg
(575 mbar) 300°F (166°C)
7017 3,000 15 psi (1,034 mbar) 15 inch-Hg
(507 mbar) 300°F (166°C)
7021 3,000 15 psi (1,034 mbar) 15 inch-Hg
(507 mbar) 280°F (156°C)
7026 3,000 12 psi (827 mbar) 15 inch-Hg
(507 mbar) 220°F (122°C)
Table 4-3 – Maximum Operating Limits
WARNING
!
The maximum pressure differential is based
on the difference between the inlet pressure
and the outlet pressure. The maximum
pressure differential shall not be exceeded.
Exceeding the maximum pressure differential
will cause serious damage to the equipment
and could cause bodily injury.
WARNING
!
The maximum allowable working pressure
(MAWP) is based on the absolute pressure of
the blower housing and is NOT the maximum
allowable pressure differential. Exceeding
the MAWP will cause serious damage to the
equipment and could cause bodily injury.
To permit continued satisfactory performance, a
blower must be operated within certain approved
limiting conditions. The manufacturer’s warranty is,
of course, also contingent on such operation.
Maximum limits for pressure, temperature, and
speed are specified in Table 4-3 on page 9
for various blower sizes when operated under the
standard atmospheric conditions. Do not exceed
any of these limits.
Specially ordered blowers with nonstandard
construction, or with rotor end clearances
greater than shown in Assembly Clearances
on page 39, will not have the operating
limits specified here. Contact your
Tuthill Vacuum & Blower Systems sales
representative for specific information.
Special attention must be paid when a blower
has a higher than standard ambient suction
temperature. Special recommendations
for operating parameters and/or additional
cooling may be recommended. Consult the
factory or local representative for appropriate
information.

Manual 2007 Rev B p/n 2007
10
INSTALLATION
05
GENERAL
DANGER
!
The blower is not intended to be used
with explosive products or in explosive
environments. The blower is not intended
to be used in applications that include
hazardous and toxic gases. Consult the
factory for support.
DANGER
!
It is the responsibility of the installer to
assure that proper guarding is in place and
compliant with all applicable regulatory
requirements.
WARNING
!
The bare shaft blower can
generate excessive noise.
Methods to reduce the noise
levels by installing inlet and
outlet silencers will be required.
Even with inlet and outlet
silencers, hearing protection
will be required.
WARNING
!
Customers are warned to provide adequate
protection, warning and safety equipment
necessary to protect personnel against
hazards in the installation and operation of
this equipment in the system or facility.
WARNING
!
The standard MAWP is per Table 4-3. The
MAWP shall not be exceeded unless specific
factory testing of the pressure containing
components of the blower has been
performed.
WARNING
!
Table 4-3 states the maximum operating
speed in RPM (rotations per minute) and
maximum temperature. Do not exceed these
limits. The installation of the blower shall
take these critical operating parameters
into account and adequate control features
implemented.

Manual 2007 Rev B p/n 2007 11
05
Installation
WARNING
!
Upon completion of the installation, and
before applying power, rotate the drive
shaft by hand. It must move freely. If it
does not, look for uneven mounting, piping
strain, excessive belt tension or coupling
misalignment or any other cause of binding.
If blower is removed and still does not move
freely, check inside the blower housing for
foreign material.
Remove the protective covers from the shaft
and inspect for damage.
Carefully check to ensure that no transit damage
has been sustained. If damage has occurred from
shipment, file a claim with the carrier immediately.
Preserve the shipping container for inspection by
the carrier.
In the event that your unit sustains damage
while being shipped to your facility, do not
return it to the factory without first obtaining
shipping instructions from us.
Do not remove protective covers and plugs until
the connection is being made. Mount the blower on
a flat, level surface. Use a baseplate that is rigid,
solidly supported, and structurally sound. Shim
under the legs where necessary so that each leg of
the blower supports an equal share of the blower
weight. This is necessary to prevent twisting of
the blower. Make sure the feet rest evenly on the
mounting surface before fastening down. Twisting
or cramping the blower during mounting will
cause rotor contact and binding during operation,
resulting in a condition called “soft foot.” See
Soft Foot on page 13 for further details and
preventative measures.
A blower that is factory-mounted on a base should
not require such adjustments. However, since
the assembly can become twisted in shipping or
installation, check for soft foot after installing the
base. Shims may be needed for alignment. Loosen
the foot hold-down screws to check foot contact
with the mounting surface. Mount the base on a
solid foundation or heavy flooring, using shims as
necessary at bolting points to prevent warping the
assembly. See also Foundation on page 12.
Transmission of small operating vibrations to a
support structure may be objectionable in some
cases. Use of vibration isolators or vibration-
absorbing materials can be effective in overcoming
this transmission. To avoid casing distortion, apply
the treatment under the common motor/blower
base or mounting plate rather than directly under
the feet alone.
Make sure piping is accurately squared with the
blower and supported independently. Stress
imparted from incorrectly aligned piping or
mounting will create problems with bearing and
seal life, possibly leading to premature internal
contact. The blower should sit stress-free and
evenly on its supporting surface. Take care
to evenly tighten the mounting bolts to avoid
imparting undue stress into the blower. Stress
can be checked in a free state with feeler stock or
verified on a previously installed blower with the aid
of a dial indicator. Spring or gap should be found
less than 0.002 in. (0.05 mm).
Use only clean, new pipe and make certain it is
free of scale, cuttings, weld beads, dirt, or any
other foreign material. To guard against damage
to the blower, make sure that an inlet filter is used.
Clean the filter of collected debris after 3 hours of
operation and periodically thereafter. See Piping
Connections on page 18 for additional details.
Figure 5-1 shows a typical complete installation
of blower and accessories. Note the absence of
throttle or shut-off valves in both discharge and
intake piping. If it is possible for airflow to be cut off
in either line, add a pressure and/or vacuum relief
valve. In some installations, it may be desirable to
use only an inlet silencer-cleaner supported directly
from the blower connection. Keep the weight of
accessories and piping to a minimum to prevent
blower casing distortion. If the weight exceeds
10% of blower weight, support the components
independently of the blower and connect them with
a flexible hose or connectors. The approximate
weights of the blowers are listed in Table 4-1 and
Table 4-2 on page 8.

Manual 2007 Rev B p/n 2007
12
05
Installation
AIR FILTER
PRESSURE
RELIEF VALVE
CHECK VALVE
FLEX CONN.
PRESSURE GAUGE DISCHARGE
SILENCER
INTAKE SILENCER
FLOW
FLOW
Figure 5-1 – Typical Blower Installation
A blower may be driven by direct-coupling to
the driver or by V-belt drive for the purpose of
obtaining other speeds within the approved
range. See Motor Drives on page 20 for more
information.
Blowers from Tuthill Vacuum & Blower Systems
are internally and externally treated after factory
assembly and testing to protect against rusting in
normal atmospheric conditions prior to installation.
The maximum period of internal protection is
considered to be up to 6 months under average
conditions, provided closing plugs and seals are
not removed. Protection against chemical or salt-
water atmosphere is not provided. Avoid opening
the blower until ready to begin installation, as
protection will be quickly lost due to evaporation.
For recommended preparations for long-term
storage (longer than 6 months), see Long-Term
Storage on page 30.
Location
Install the blower in a room or outdoor area that
supplies adequate space and lighting for routine
maintenance. Make sure that indoor installation
areas are well ventilated and kept as cool as
possible, because operating the blower at elevated
temperatures can result in nuisance overload or
temperature shutdowns. An unprotected outdoor
installation is satisfactory only when correct
lubrication for expected temperatures is provided.
See Recommended Lubricants on page 41.
Foundation
The blower does not need a special foundation.
However, it does require a solid, level floor and
adequate frame support. Bolt the blower system to
the floor, and seal any cracks.
Blower Air Intake
To minimize maintenance, supply the blower with
the cleanest air possible. The air must not contain
any flammable or toxic gases, as the blower will
concentrate these gases. This could result in
damage to the blower and surrounding property
and lead to personal injury or death. Do not block
or restrict the opening of the blower and/or motor,
as they could overheat and fail.
Do not use blowers on explosive or hazardous
gases. Do not exceed the limits described in Table
4-3. Each size blower has limits on performance
criteria such as pressure differential, running
speed, and discharge temperature.
If it is necessary to take air from a remote source,
such as in a vacuum application, make sure the
diameter of the piping is at least equal to the
diameter of the blower inlet. For distances greater
than 20 ft (6 m), enlarge the pipe diameter to
reduce inlet restriction. Excessive restriction will
reduce the efficiency of the blower and elevate its
discharge temperature. The piping used should
also be corrosion-resistant and free of scale and
dirt. Keep the inlet covered to keep out foreign
objects and rain. Vacuum kits are available.

Manual 2007 Rev B p/n 2007 13
05
Installation
Soft Foot
Soft foot is a condition in which one of the blower
feet does not sit flat on the base. Soft foot is
usually due to irregularities in the surface to which
the blower is mounted. When the bolt on the
foot gets tightened, a slight distortion occurs that
can affect bearing and seal life as well as cause
premature internal contact between the rotors and
the housing.
ANGULAR
SOFT FOOT
PARALLEL
SOFT FOOT
Figure 5-2 – Illustrations of Soft Foot
1. Place the blower on the base.
2. Check each foot for gaps between the foot and
base (soft foot). Shim as necessary to fill gap
within 0.002 in. (0.05 mm).
Figure 5-2 shows the two most common types
of soft foot conditions. If either type is present
at a measurement of more than 0.003 in.
(0.076 mm), the blower may fail prematurely.
3. Tighten all bolts.
4. Mount a dial indicator on the base contacting
one foot at 12 o’clock position.
5. Loosen the bolt on that foot. Observe indicator
travel and add shims as needed to reduce
“spring” to less than 0.002 in. (0.05 mm).
Repeat steps 4 and 5 on the remaining feet.
SAFETY
Tuthill Vacuum & Blower Systems recommends
the use of relief valves to protect against excessive
pressure or vacuum conditions. Test these valves
at initial start-up to be sure they are properly
adjusted to relieve at or below the maximum
pressure differential rating of the blower.
DANGER
!
It is the responsibility of the
installer to assure that proper
guarding is in place and
compliant with all applicable
regulatory requirements.
DANGER
!
Internal and external rotating
parts of the blower and driving
equipment can produce
serious physical injuries. The
blower should never be run
with the inlet or discharge
piping removed. If it becomes
necessary to inspect the
rotating parts of the blower or
to change V-belts, be absolutely
sure that all power to the motor
controls has been shut off, the
motor controls are locked out,
and properly tagged before
proceeding.

Manual 2007 Rev B p/n 2007
14
05
Installation
DANGER
!
Assure that properly sized vacuum breaks/
relief valves are used on the inlet side of
the blower. Also assure that properly sized
pressure relief valves are used on the outlet
of the blower. The sizing shall be such to
assure that the proper flow can be achieved
without exceeding the rated vacuum and
pressure ratings.
DANGER
!
Blower housing and associated
piping or accessories may
become hot enough to cause
major skin burns on contact.
WARNING
!
Use lock out/tag out procedures
to disable the electrical energy
source before any service or
work is done on the blower.
WARNING
!
Avoid extended exposure in
close proximity to machinery
with high intensity noise levels.
Wear adequate ear protection.
OTE:NUse proper care and good procedures in
handling, lifting, installing, operating, and
maintaining the equipment.
LUBRICATION
Every booster from Tuthill Vacuum & Blower
Systems is factory-tested, oil-drained, and shipped
dry to its installation point. Fill both independent oil
reservoirs to the proper level before operation. Oil
reservoirs are under vacuum.
Shaft bearings at the gear end of the blower are
splash-lubricated by one or both gears dipping into
an oil reservoir formed in the gear end plate and
cover. Shaft bearings at the drive end of the blower
are lubricated by a slinger assembly dipping into
an oil reservoir. Before starting the blower, fill the
oil sumps as described in Filling Procedure on
page 15.
Add oil to the blower in the quantity listed in
Table 4-2 on page 8. Make sure oil level is
maintained within the notched area of the sight
glass. See Figure 5-3 and Figure 5-4. Lower drive
blowers have “bull’s eye” type oil level gauges.
Maintain oil levels at the center of the glass.
WARNING
!
Never attempt to change or add lubrication
while the blower is running. Failure to heed
this warning could result in damage to the
equipment or personal injury. Oil must be
checked when the blower is NOT running.
WARNING
!
Properly dispose of the spent lubricants.
Refer to the manufacturer of the lubricant and
any regulations to assure proper and safe
disposal.
WARNING
!
Do not start the blower until you are sure oil
has been put in the gear housing and rear
cover. Operation of the blower without proper
lubrication will cause the blower to fail and
void the warranty.
This manual suits for next models
5
Table of contents
Other Tuthill Blower manuals
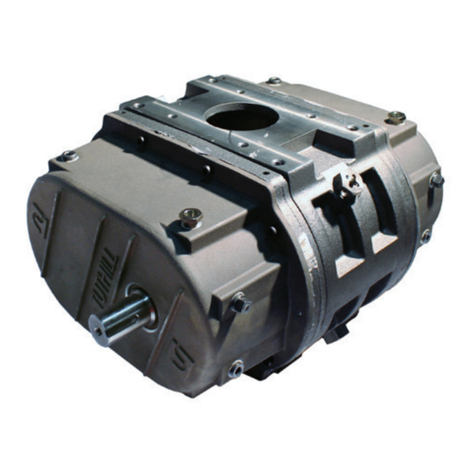
Tuthill
Tuthill T855 User manual
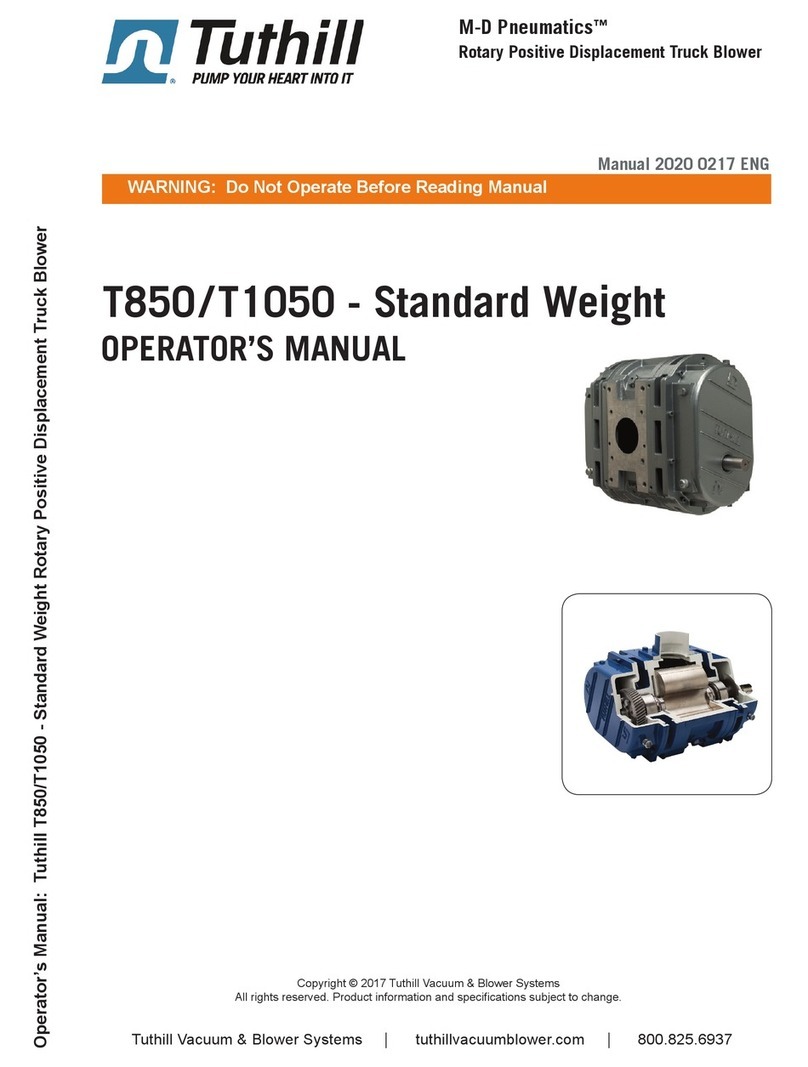
Tuthill
Tuthill T850 User manual
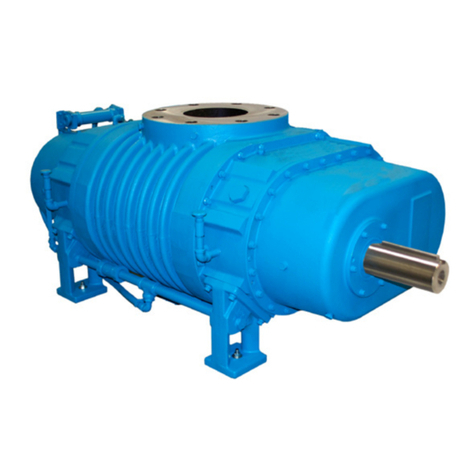
Tuthill
Tuthill PD Plus 1215 User manual
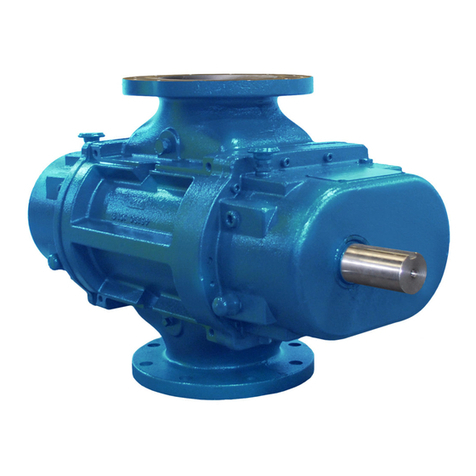
Tuthill
Tuthill Qx Series User manual
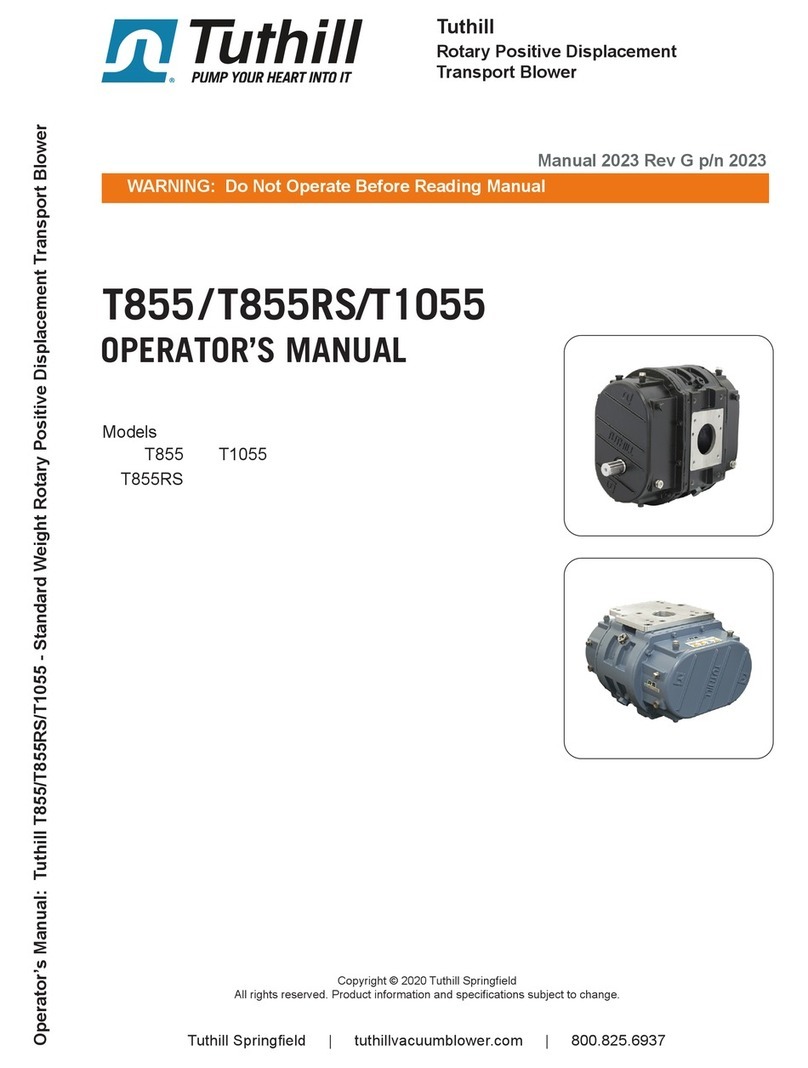
Tuthill
Tuthill T855RS User manual
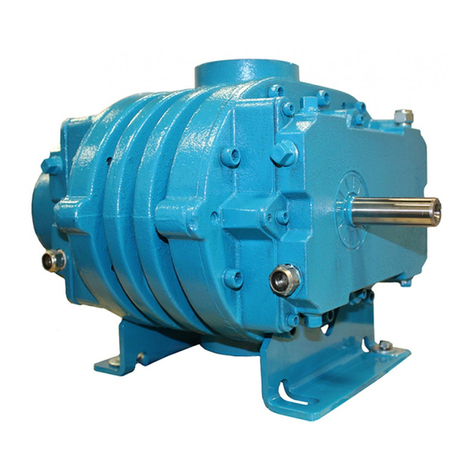
Tuthill
Tuthill 2002 User manual
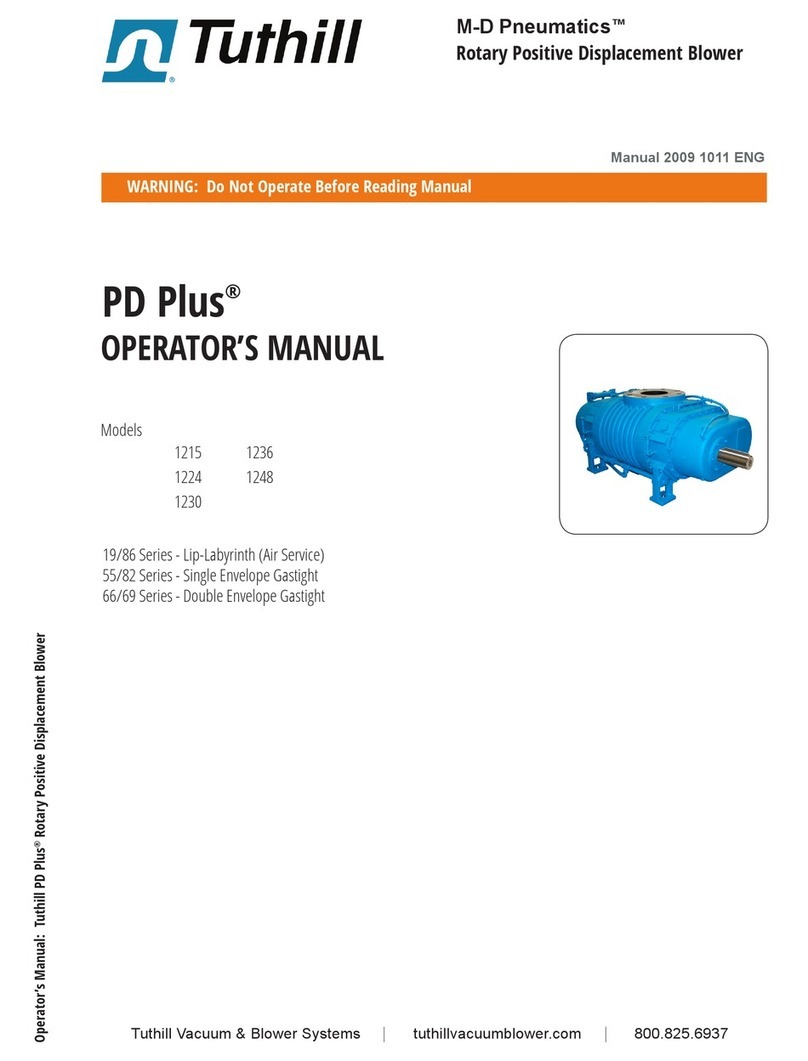
Tuthill
Tuthill PD Plus 1215 User manual
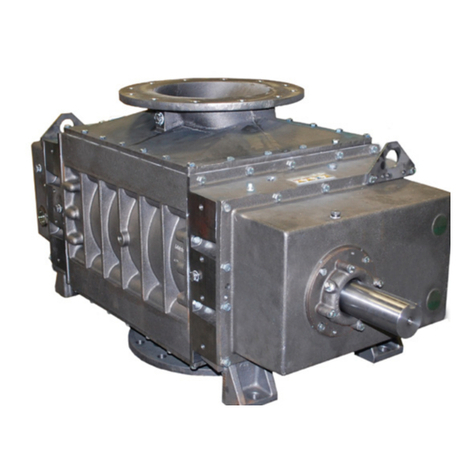
Tuthill
Tuthill PD Plus 9000 Series User manual
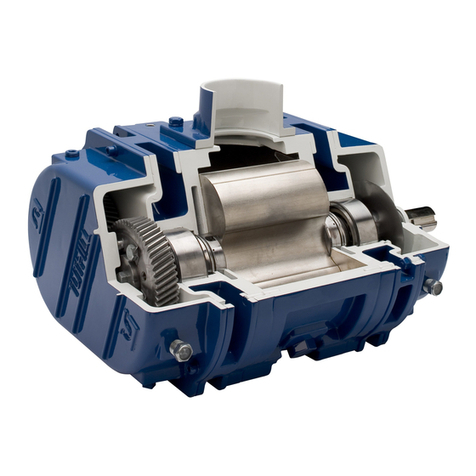
Tuthill
Tuthill TI850 Operating instructions

Tuthill
Tuthill M-D Pneumatics Qube 400 User manual