UEi DIGI COOL User manual

Digi-Cool Industries Ltd.
Digital Refrigeration System Analyzer
Distributed By:
AK900
User manual
To take full advantage of your analyzer, please read this manual
and store in a safe place for future reference.
v1.04

2
Table of Contents
Table of Contents................................................................................. 2!
Package Contents................................................................................. 3!
Features and Use.................................................................................. 4!
General ............................................................................................ 4!
Proper Use....................................................................................... 6!
External Features............................................................................. 7!
Display ............................................................................................ 8!
Keys .............................................................................................. 13!
Using the Pressure Gauges............................................................ 16!
Using Pressure Recall Modes ....................................................... 16!
Using Temperature Modes............................................................ 16!
Specifications..................................................................................... 19!
Care & Maintenance .......................................................................... 20!
General Care ................................................................................. 20!
Replacing Batteries ....................................................................... 20!
Cleaning ........................................................................................ 21!
Maintenance .................................................................................. 21!
Calibration..................................................................................... 22!
Troubleshooting ................................................................................. 23!
End-of-Life Disposal ......................................................................... 26!
Warranty ............................................................................................ 27!
Limitation of Liability........................................................................ 29!
Service and Support ........................................................................... 31!
Refrigerant Expansion................................................................... 31!
Contact Information ...................................................................... 31!
Return for Service.............................................................................. 32!
Product Regulatory Information ........................................................ 36!

3
Package Contents
1 Digi-Cool AK900 Digital Refrigeration System Analyzer Unit
1 9V battery (installed)
1 Dual Temperature Sensor
1 Extended Hanging Hook
1 Two valve ball valve manifold
1 User Manual
1 Product Registration Card

4
Features and Use
General
The unit performs the following tasks:
•Sense and display pressures present in the manifold
•Calculate and display dew / bubble points corresponding to the
sensed pressures, for the selected refrigerant
•Sense and display temperature of probe tip
•Calculate and display system superheat or subcooling, based on
sensed pressure and temperature, for the selected refrigerant
•Displays maximum and minimum pressures observed since
threshold reset
The unit has two 1/8" pressure ports, acting as two gauges: blue for
low side, red for high side. All settings are controlled through the
keypad and affect both sides of the display.
Some features of the unit include:
•Working pressure ranges:
Low side: 0-200psia (1350 kPa, 13.5 bar)
High side: 0-550psia (3000 kPa, 37.9 bar)
•Sensing resolution (precision):
Low side: 0.25psi or 0.4"Hg (2kPa, 0.02 bar)
High side: 1psi (7 kPa, 0.07bar)

5
•Includes profiles for 45 common refrigerants
•"Dynamic Offset" bar graph display
•Pipe-mounted temperature probe for automatic superheat and
subcooling readings
•MAX and MIN pressure monitoring for control set-up
•Zero key automatically calibrates to local atmospheric conditions
•Large, easy to read LCD display
•Adjustable LCD display contrast
•Selectable reading update rates of 1 and 5 seconds, or hold current
reading
•Upgradeable to handle additional refrigerants
•Automatic shutdown after 15 minutes of inactivity
•Low battery indicator
•Tough, weather resistant case for indoor / outdoor field use
Features of the unit are patented in the US (#5,311,745) and Canada
(#2,107,134) by Digi-Cool Industries Ltd.
This unit is intended for use in an industrial or commercial
environment. Use in a residential environment may cause
interference with radio and television reception.

6
Proper Use
This product is intended for use by trained service personnel only, for
use with vapor compression refrigeration, air conditioning and heat
pump systems. Servicing of refrigeration systems require special
training to ensure the safety of the service person, building occupants,
local and global environment.
Ensure your service manifold is properly rated for the operational
pressures of the analyzer, at up to 550psia (3000 kPa, 37.9 bars).
To prevent damage, never exceed the proof pressure of the analyzer:
Low side: 600psia (4100 kPa, 41 bars)
High side: 1500psia (10300 kPa, 103 bars)
For safe operation, ensure that the refrigeration system under test has
working overpressure relief equipment installed, and that they are
rated to trigger below the burst pressures of the analyzer:
Low side: 2000psia (13500 kPa, 135 bars)
High side: 5000psia (34500 kPa, 345 bars)
Refer to the instruction manual for your service manifold on its use.

7
External Features
1 Display
Extended temperature LCD display, protected with clear resilient
window to prevent damage.
2 Keypad
Tactile response keypad is easy to operate, even with gloved hands.
3 Transducer Ports
1/8" NPT ports connect to the gauge ports of the manifold using
supplied straight swivel fittings.
4 Temperature Probe Plug
Connect the temperature probe to this port. When not in use, cover
the plug with the sealing cap to maintain water resistance.

8
5 Vent
Allows for atmospheric and internal pressure adjustment without
moisture entry. Do not cover this port.
6 Temperature Probe
The temperature probe can be secured onto piping from 3/8” to 3” in
outer diameter (1 to 7.5cm) with the attached hook-n-loop strap. The
connectors are water resistant when mated or when covered by their
protective caps. For accurate measurements, use a piece of pipe
insulation over the sensor and pipe to insulate them against the
ambient air.
To install the connector, align the key on the plug with the slot on the
connector. Push connector while
wiggling to mate together, and then
tighten the thread on the black collar
to lock connector into place. When
not in use, apply the attached cover to
the connector to keep moisture and
dirt out. The probe comes with a 10’
(3m) long cord.
Display
The display of the unit is very user friendly. For users familiar with
traditional manifold gauges, the readouts should be self-explanatory.
The quantity of information offered to the user is more than any other
gauge traditionally available. A full understanding of these features
allow for rapid system analysis, for easier and more accurate trouble-
shooting.

9
1 Low and High Side
In general, displays on the left side of the screen are associated with
the low-pressure side of the refrigeration system, represented by the
blue labeling. The right side of the display reflects the high-pressure
side, represented by the red labeling.
The low or high side display will flash when one of the following
abnormal pressure conditions occur on each side of the service
manifold:
•The pressure detected has exceeded the working pressure range of
the gauge, or
•The pressure detected far exceeds the proper operating range for
the selected refrigerant, resulting in out-of-range temperature
readings.
This may be caused by improper use of the ZERO key, or if the
working pressure range has been exceeded. Try depressurizing the
manifold and press ZERO to recalibrate to a proper atmospheric
reference. Also ensure the proper refrigerant is selected.
Bear in mind that readings are subject to device accuracy limitations.
For example, a perfect vacuum of 29.9"Hg may be displayed as
29.8"Hg or cause the device to blink due to an excessive vacuum

10
reading. Given the wide operating range of the analyzer, extremely
accurate vacuum readings are intrinsically difficult to achieve.
When no pressure unit is indicated, the amounts shown are in bars.
2 Dynamic Offset Bar Graph
Each bar graph represents changes to each pressure reading since the
digits were updated. The graphs are updated four times every second.
They allow the user to monitor pressure dynamics in the system
closely.
Each segment in the low side bar graph represents ¼psi (2 kPa, 0.02
bars) of change in the low side reading. On the high side, each
segment represents 1psi (8 kPa, 0.08 bars) of change in the high side
reading. The hash marks above the bar graph show these units for
quick reference. Segments on the left of the center mark mean
decreased pressure, while segments on the right indicate increased
pressure.
3 Pressure
The "numeric pressure" display is below the bar graph. The low side
pressure is shown in 0.1 PSI (1 kPa, 0.01 bar); the high side is shown
in PSI (kPa, 0.1 bar).
When operating in imperial gauge mode, vacuum readings below
atmosphere are shown in "Hg below atmosphere.
4 Temperature
This field displays the saturation temperatures of the selected
refrigerant at the indicated pressure. The left side reading is the vapor
saturation (dew) point for the low side pressure, while the right side
reading is the liquid saturation (bubble) point for the high side
pressure reading.

11
5 Selected Refrigerant
The currently selected refrigerant is shown here. The characteristics
of the selected refrigerant are reflected in the temperature readings
discussed above.
ASHRAE
Trade # shown
Trade #
R12
12
12
R1234yf
R22
22
22
R-123
123
R-124
124
R134A
134A
134A
R236ea
R-236ea
R236fa
R-236fa
R245ca
R-245ca
R245fa
R-245fa
R290
290
R-290 (Propane)
R401A
39
MP39
R401B
66
MP66
R402A
80
HP80
R402B
81
HP81
R404A
62
HP62 FX-70
R406A
406A
406A / GHG12
R407A
407A
407A
R407C
9000
Suva 9000
R408A
10
FX-10
R409A
56
FX-56
R410A
20
AZ-20
R413A
49
R414B
414B
HotShot
R416A
416A
FRIGC® FR-12
R417A
59
ISCEON® 59
R420A
420A
420A
R421A
421A
Choice R421A
R421B
421B
Choice R421B
R422A
79
ISCEON® 79
R422B
22b
ICOR XAC1
R422C
422
ICOR XLT1
R422D
29
ISCEON MO29
R424A
44
RS-44
R426A
24

12
R427A
R-427A
R428A
52
R434A
45
RS-45
R437A
49
R438A
99
R500
500
500
R502
502
502
R507
50
AZ-50
R508B
95
Suva 95
R600A
600A
600A (Isobutane)
If the "R" prefix is visible, the ASHRAE reference number is being
shown. If "R" prefix is not visible, the number shown is the numeric
portion of the refrigerant's trade name, as shown below. The user
may change the set of names displayed by holding "R-!" during
power up.
The unit has been designed for use with modern HCFC and HFC
refrigerants, some of which operate at substantial pressures. The
resolution may be somewhat coarse for work with low-pressure
refrigerants such as R-11 or R-123. Therefore, these refrigerants are
not included with the unit. Contact the manufacturer if you wish to
upgrade your unit to handle these or other refrigerants.
6 Hold Time
These indicators show how often the digital readings are being
updated. The 1SEC indicator shows that it is updated once every
second. The 5SEC indicator means the digits are updated once every
5 seconds. The HOLD indicator means the digits are not being
updated but the bargraph remains dynamic.
7 Low Battery
The indicator will be visible when the battery should be replaced.
Continuing to use the unit when batteries are low will lead to less
accurate measurements.
8 SubCool Temperature
This character of the display is for the subcooling reading, in either °F
or °C. If temperature reading higher than the high-side bubble point
for the selected refrigerant, the SC is negative.

13
9 SuperHeat
This character set of the display is the superheat reading, in either °F
or °C. If temperature reading lower than the low-side dew point for
the selected refrigerant, SH is negative.
10 SuperHeat Temperature (lowside sensor)
The is the actual temperature being measured by the Superheat sensor
on the line it is mounted on.
11 SubCool Temperature (highside sensor)
This is the actual temperature of the highside sensor on the line it is
mounted on.
12 Delta T
This is the differential temperature of the highside sensor temperature
minus the lowside sensor temperature should you want to take a ‘delta
T’ differential reading.
When the MODE key is toggled the dt will then disappear and either
the HI or LO will appear to:
•HI Maximum pressure recall mode: pressure fields display
highest pressures sensed since threshold reset, and their
associated saturation temperatures. In this mode, the
15-min automatic shutdown is disabled.
•LO Minimum pressure recall mode: pressure fields display
lowest pressures sensed since threshold reset, and their
associated saturation temperatures. In this mode, the
15-min automatic shutdown is disabled.
Keys
PWR
This key turns unit on for a period of 15 minutes. If it is pressed
again while the unit is on, the unit will turn off.
•To disable automatic shutdown, hold UNIT while pressing PWR
to turn the unit on. "Pr" will be shown on the screen. Press PWR
to continue.
•Automatic shutdown is disabled when in HI or LO modes.

14
R- !/ "
These keys select between available refrigerants. When the last
available refrigerant has been reached, the first one is shown again. If
the unit has been upgraded with additional refrigerants, they will be
shown following the original refrigerants. Refrigerants are labeled
according to their ASHRAE designations or trade numbers.
•To change between ASHRAE and trade number display, hold
R-!while pressing PWR when turning the unit on.
ZERO
Depress this once to calibrate the unit. Regardless of what pressures
the low and high side are sampling at the time that this key is pressed,
these pressures will then be considered the “0” or atmospheric
pressure reference reading. For best accuracy, allow unit to reach
ambient temperature before pressing ZERO.
UNIT
This key toggles the pressure and the temperature readings through
the following combinations of pressure units in sequential order:
•kPa / ºC (atmospheric reference)
•BAR/ ºC (atmospheric reference)
•PSIA / ºC
•PSIG / ºC
•PSIA/ ºF
•PSIG/ ºF
Temperature units also apply to superheat and subcooling readings
when active.
NB To toggle the backlight on and off in the display, hold the UNIT
key down for 5 seconds.

15
1SEC / 5SEC / HOLD
This key selects the time between updates of the numeric pressure
reading and corresponding temperature displays.
For example, if the update time selected is 1SEC, the pressure and
temperature displays are updated every second. With 5SEC, the
display is updated every 5 seconds. If the update time selected is
HOLD, the temperature and pressure readout are held at the readings
when HOLD was initiated.
In HI and LO pressure recall modes, only 1SEC setting is available.
Regardless of the update period, the bar graph updates automatically 4
times per second. At the moment that the numeric readout is updated,
the bar graph will clear itself. In this way, the bar graph indicates the
current deviation from the displayed numeric reading.
LCD !/ "
These keys increase and decrease the contrast of the LCD display
respectively.
MIN / MAX CLR
This key clears the memory of the HI and LO pressure recall modes.
Depress this when you wish to begin a session of minimum and
maximum pressure monitoring. Depending on the mode selected,
there may not be any visible effect from this key press.
MODE
This key toggles between the following modes in sequence:
•Normal Mode*
•HI Maximum pressure recall mode
•LO Minimum pressure recall mode
•no temperature display if temperature sensor is not plugged in.

16
Using the Pressure Gauges
Once mounted properly onto a service manifold, the pressure gauges
behave just like traditional needle pressure gauges. Usually, the low
side of the manifold is connected to the low-side service port, and the
high side of the manifold to the high-side service port.
Using Pressure Recall Modes
The pressure recall modes are useful when setting switching
equipment and observing load changes over long periods. In HI
mode, the highest pressure sensed since the MAX / MIN CLR button
was pressed is shown for both low and high pressure sides, along with
the corresponding saturation temperatures. In LO mode, the lowest
pressures are shown.
To begin observing pressure fluctuations, press the MIN/MAX CLR
key. If not in HI or LO mode, the display will not show any changes,
but the threshold memory has been updated to the current pressure
readings.
When in HI or LO modes, the dynamic update bar graphs is inactive.
15-minute automatic shutdown is also disabled to allow continuous
monitoring of pressure. Be sure to turn off the unit manually when
finished.
Using Temperature Modes
The temperature probe is designed for pipes of varying diameters.
Using the hook-and-loop fastener or other types of straps, secure it
firmly onto the pipe, with the concave side firmly on the pipe surface.
For best accuracy on temperature related measurements, insulate the
sensor against ambient air by wrapping the installed sensor and pipe
with a piece of pipe insulation.

17
Once the temperature probe is connected to the analyzer, the system
automatically enters t mode after several seconds. Several operation
modes are then available through the MODE key:
t mode
The temperature of the probe is shown on the lower right, following t.
It is in ºF or ºC, depending on the unit selected. Depending on the
measurement and sensor contact, it takes 30 seconds to 2 minutes for
the sensor to settle to the correct temperature reading.
SH mode
The superheat mode is useful when verifying proper operation, to
safeguard against compressor damage. Secure the temperature probe
on the compressor suction line. Ensure the correct refrigerant is
selected. If the system is operating properly, superheat should be
between 10 to 30°F (5 to 15°C) while the compressor is operating
steady-state. If superheat is negative, the compressor may be drawing
some liquid.
SC mode
The subcooling mode is useful to verify full condensation. Some
systems required subcooling for proper operation; refer to the
equipment specifications. Secure the temperature probe on the
condenser outlet line. Ensure the correct refrigerant is selected. If
subcooling is negative, the refrigerant is not completely condensed,
indicating poor heat rejection.
Backlight
In order to turn on the green backlight you will need to push on and
hold down the units button for 5 seconds. This will then turn on the
backlight for the duration of the 15 minute on cycle.

18
The absolute zero function
This gives the 900 the ability to zero the pressure readouts to absolute
zero and thus read out accurately in high altitude locations. In order
to take advantage of this function you will need to put the 900 into the
oF/psia mode and then with both the low side and high side connected
to a vacuum pump at 100 microns or less (the lower the better); press
the zero key and hold it down for 4 seconds. The unit will then read 0
psia and reference every other pressure to that so that a high elevation
atmospheric may read 3”Hg. with the hoses open to atmosphere. In
order to go back to the factory settings, select oF/psig and again press
and hold down the zero key for 4 seconds.
Dual Temperature Sensors and Delta T
The last feature enhancement is the dual temperature sensor assembly
and the ability to switch not only back and forth between SH and SC
but to read a ‘dt’ or delta temperature as the blue lead (SC) sensor
temperature is subtracted from the red lead (SC) sensor. The blue
sensor is the SH sensor as it is always associated with the low side
and the vast majority of SH settings are taken for the evaporator
superheat. Remember; blue=low side=superheat for evaporator
whereas red=high side=subcooling for the condenser. The
temperature “t” mode is always accessing and referring to the blue
sensor.

19
Specifications
Sensing resolution:
Low side: 0.25psi (2kPa, 0.02bars)
High side: 1psi (7 kPa, 0.07 bars)
Sensing accuracy: 0.6% FS ± 1 least significant digit
Working pressure:
Low side: 0-200psia (1350 kPa, 13.5 bars)
High side: 0-550psia (3000 kPa, 37.9 bars)
Proof pressure: Tolerable pressure without internal damage
Low side: 600psia (4100 kPa, 41 bars)
High side: 1500psia (10300 kPa, 103 bars)
Burst pressure: Tolerable pressure without lost of seal
Low side: 2000psia (13500 kPa, 135 bars)
High side: 5000psia (34500 kPa, 345 bars)
Temperature sensor range: -40 to 250°F (-40 to 125°C)
Temperature accuracy: ±0.9°F (±0.5°C)
between 32 to 158°F (0 to 70°C)
Dimension: 7.3 x 4.9 x 2.6"
(18.5 x 12.5 x 6.5cm)
Weight with batteries: 1.6 lb (~720g)
Battery life: approx. 6 months with normal use
Usage environment: Indoors and outdoors
Dew and splash resistant
Do not immerse in water
Storage and operational temperature:
-4°F to 122°F (-20°C to 50°C)

20
Care & Maintenance
General Care
Follow these basic precautions to ensure that your analyzer will
perform well for years to come:
•Do not push keys with sharp objects
•Do not expose the unit to extreme heat, or leave in direct sunlight
for extended periods of time.
•Do not leave the unit in contact with water or other fluids for
extended periods of time.
•Do not immerse the unit in liquids.
•Do not pull on the temperature probe cord.
•Avoid rapidly heating or cooling the unit.
•Store in a dry location near room temperature, away from direct
sunlight, in a vibration-free environment.
Replacing Batteries
The unit is designed for use with a 9V alkaline battery. Carefully
follow all instructions and warnings on the battery label and package.
1. Find a dry environment, preferably at room temperature or lower.
This will keep condensation from forming in the unit at a later
time. Air-conditioned rooms are ideal.
2. Remove the rubber boot if installed by stretching it and shifting it
toward the front of the analyzer.
3. Using a dry towel, clean exterior so it is free of dirt and fluids.
4. Using Phillips screwdriver, remove the 5 screws and back cover.
5. Remove old battery by pulling the middle of the contact terminal
with your fingers. Do not pry with metallic objects. Do not pull
on the wire.
6. Each contact on the battery snap mates
against the opposite gender contact on
the battery. DO NOT connect the
battery in reverse.
Table of contents
Other UEi Measuring Instrument manuals
Popular Measuring Instrument manuals by other brands
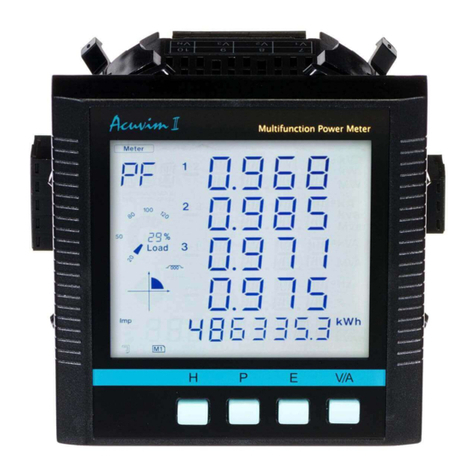
AccuEnergy
AccuEnergy Acuvim II series user manual
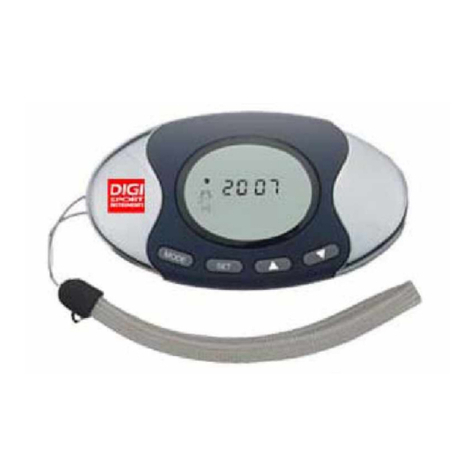
Digi Sport Instruments
Digi Sport Instruments DW-2005 instruction manual
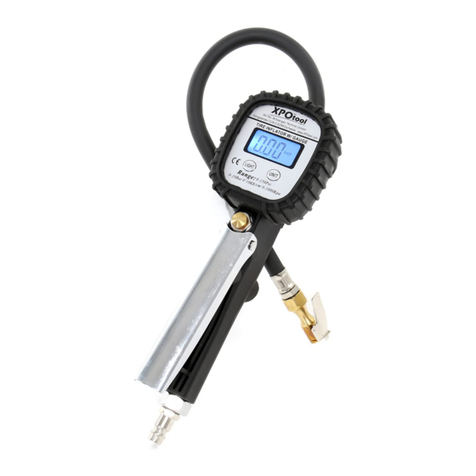
XPOtool
XPOtool 63039 Operation manual

Huato
Huato A200 Operation manual
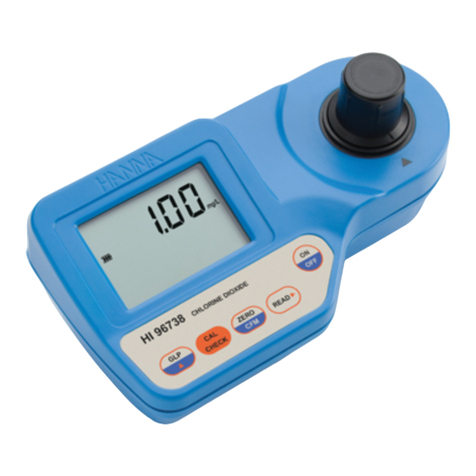
Hanna Instruments
Hanna Instruments HI 96738C instruction manual

Amphenol
Amphenol Protimeter ReachMaster Pro instruction manual