Ultra Max Perfoma Series User manual

For Sales & Service questions please
contact your dealer:
Your local dealer is:
742/762 Control
255 and Performa Series Valves
(263, 268, 268FA)
Operation Manual

2
Rev D
TABLE OF CONTENTS
LOGIX™ SERIES INSTALLER QUICK-START SHEET 3
MANUAL OVERVIEW 8
How To Use This Manual
General Warnings And Safety Information
EQUIPMENT INSTALLATION 9
Valve Features
Location Selection
Water Line Connection
Drain Line Connection
Overflow Line Connection
Regenerant Line Connection
Electrical Connection
Valve Camshaft
SYSTEM DISINFECTION 25
Disinfection Of Water Conditioners
DETERMINING IF YOU HAVE A 742 OR 762 CONTROL 27
GENERAL 700 SERIES INSTRUCTIONS 27
Display Icons 700 Controller
Keypad — Buttons
Regeneration Modes
742/762 Series Initial Power-Up
Initial Start-up Step-By-Step Instructions
PLACING CONDITIONER INTO OPERATION (turning on the water) 37
PROGRAMMING THE 700 FOR 5-CYCLE FILTER APPLICATIONS 40
Manganese Greensand Systems
742/762 SERIES ADVANCED PROGRAMMING 43
742/762 LEVEL II PROFESSIONAL PROGRAMMING 44
PARTS AND ACCESSORIES 47
255 Valve Exploded View
255 Valve Parts List
Performa Exploded View
Performa Parts List
Logix 700 Series Controllers Parts List
TROUBLESHOOTING 53

3
Rev D
QUICK START
LOGIX™ SERIES INSTALLER QUICK-START SHEET
Logix Series Controllers See Determining If You Have a 742 or 762 Control on page 27 to identify
your controller.
742 Controller - Electronic time clock control capable of doing 7-day (day of
week)regeneration, or up to a 99 interval day regeneration. This control will
operate both in a conditioner (softener) or 3-cycle filter mode with the same
controller.
762 Controller - Electronic metered-demand (volumetric) controller which
regenerates based on the water usage of the installation site. A calendar override
is a standard feature on this controller.
The Logix Series will operate on both the 255 and Performa valve body
series.
For 5-cycle filter applications, see page 40 for setting details.
Initial Power-up
Initial Power Up - (CAMSHAFT proceeds to HOME position)
• At initial power-up, the camshaft willneed to rotate to the HOME
(in service) position.
• Camshaft may take 1-2 minutes to return to home position.
• Err 3 will be displayed until the camshaft returns to home.
• If more than 2 minutes elapses, verify that the motor is turning the camshaft.
If it is not turning, see the troubleshooting section.
Time & Day
Regen Time & Day
Salt
SU MO TU WE TH FR SA DAYS
LBS
PM
MIN
KG
x100
x2
P
H
C
Capacity
Hardness
Manual Regeneration
UP Button
SET Button
DOWN Button
LCD Display
Time & Day
Regen Time & Day
Salt
Capacity
Hardness
SU MO TU WE TH FR SA DAYS
NOTE: The Logix controller features a self-test sequence. At first power-
up of thecontrol, you may seea numbersuch as 1.00, 1.02,1.04,or 2.00
displayed. This is an indication that the self-test is not completed. To
complete the test, verify that the turbine cable is connected. Blow into
the turbine port (valve outlet) to spin the turbine. The controller will verify
that the turbine works and the self test will finish. Proceed with the initial
start up procedure.

4
Rev D
QUICK START
Initial Start-up Step-by-step Instructions
Step 1: Select Valve Type
This step may have been performed by yoursystem’s OEM manufacturer.
In this case, proceed to step 2.
• Identify your valve body type by looking at the silver ID sticker on the
back or side of the valve body.
• Select your valve body type using the UP or DOWN buttons.
• Display Valve Body
255 255, 7-cycle conditioner
263 Performa filter 263, 3-cycle filter
268 Performa conditioner 268, 7-cycle conditioner
273 Performa Cv 273, 3-cycle filter
278 Performa Cv 278, 5-cycle conditioner
293 Magnum Cv filter, 3-cycle filter
298 Magnum Cv conditioner, 7-cycle conditioner
Step 2: Program System Size
This step may have been performed by your system’s OEM manufacturer. In this
case, proceed to step 3.
• Input system size - resin volume - in cubicfeet or liters.
• Use UP and DOWN buttons to scroll through resin volume choices.
• Choose the nearest volume to your actual system size.
• To choose a 3-cycle filter operation - press DOWN until an "F" is displayed.
• Press SET to accept the system size you’ve selected.
• If incorrect setting is programmed, see "Resetting the Control"section below.
Step 3: Program Time of Day
• While "12:00" is blinking, set the correct time of day.
• Use theUP and DOWN buttons to scroll to the correct time of day.
• "PM" is indicated, "AM" is not indicated.
• Press SET to accept the correct time of day and advance to the next
parameter.
Step 4: Set Day of Week
• Press SET to make the arrow under SU flash.
• Use the UP and DOWN buttons to advance the arrow untilit is under the
correct day of week.
• Press SET to accept and advance to the next parameter.
Step 5: Set Regen Time
• 2:00 (AM) isthe default time of regeneration. To acceptthis time, press the
DOWN buttonto move to step6.
• To changethe regen time, press SET - causing 2:00 to flash.
• Use the UP and DOWN buttons to advance to the desired regen time.
• Press SET to acceptthe time and advanceto the next parameter.
NOTE: Different 742/762 control hardware is necessary to operate the
150S valve body.
Time & Day
Regen Time & Day
Salt
SU MO TU WE TH FR SA DAYS
Capacity
Hardness
Time & Day
Regen Time & Day
Salt
SU MO TU WE TH FR SA DAYS
Capacity
Hardness
Time & Day
SU MO TU WE TH FR SA DAYS
Capacity
Hardness
Time & Day
Regen Time & Day
Salt
SU MO TU WE TH FR SA DAYS
Capacity
Hardness
Time & Day
Regen Time & Day
Salt
SU MO TU WE TH FR SA DAYS
Capacity
Hardness

5
Rev D
QUICK START
Step 6: Set Days to Regenerate (742 Time-clock Control Only)
• If using 762 control - proceed to step 6a.
• Set number of days between time-clock regeneration (regen frequency).
• Default time is 3 days.
• Days can be adjusted from 1/2 (.5) to 99 days.
• To change, press SET to make the "3" flash.
• Use the UP and DOWN buttons to change to the number of days desired.
• Press SET to accept the regen frequency, and advance to the next cycle.
To use the 7-day timer option - see full Dealer Installation Manual.
Step 6a: Set Calendar Override (762 Demand Control Only)
• If using 742 control - proceed to step 7.
• Set number of days for calendaroverride on demand control.
• "0" days is the default for calendar override.
• Days can be adjusted from 1/2 (.5) to 99 days.
• To change, press SET to make the "0" flash.
• Use the UP or DOWN buttons to change to the number of days desired.
• Press SET to accept the regen frequency, and advance to the next cycle.
Step 7: Set Salt Amount (Regenerant Amount)
• Default setting is "9 pounds per ft3(110 g/L)".
• Use UP or DOWN to select regenerant amount.
• Press SET to accept the setting and advance to next parameter.
See page 34 for more complete information on regenerant settings for different
system sizes, capacities and expected efficiencies.
Step 8: Estimated Capacity
• System capacity isdisplayed intotalkilograins or kilograms of hardness
removed before a regeneration is necessary.
• Value is derived from the system’s resin volume input, andsalt amount input.
• The capacity displayed isa suggested value - as recommended byresin
manufacturers.
• Capacity is only displayed for information purposes on 742 control -it does
not (and cannot) need to be changed.
• To changecapacity on 762 control, press SET to make the defaultcapacity
flash. Use the UP and DOWN buttons to increment to the desired capacity.
• Press SET to acceptthe setting and advance to the next parameter.
If using 742 control, programming is complete. The control will return you to the normal operation mode.
Time & Day
Regen Time & Day
Salt
SU MO TU WE TH FR SA DAYS
Capacity
Hardness
Time & Day
Regen Time & Day
Salt
SU MO TU WE TH FR SA DAYS
Capacity
Hardness
Time & Day
Regen Time & Day
Backwash Time
SU MO TU WE TH FR SA DAYS
Capacity
Hardness
KG
Time & Day
Regen Time & Day
Salt
SU MO TU WE TH FR SA DAYS
Capacity
Hardness

6
Rev D
QUICK START
Step 9: Enter Hardness (762 Demand Control Only)
• Enter inlet water hardness at installation site.
• Default hardness setting is 25 grains(25 ppm for metric)
• To changehardness, press SET to make the setting flash.Use the UPand
DOWN buttons to scroll to the correct hardness.
• Press SET to accept the entered hardness value.
• The control will return you to the normal operation mode.
Initial system programming is now complete. The control will return to normal
operation mode, if a button is not pushed for 30 seconds.
For system start-up procedure, including: purging the mineral tank, refilling the regenerant tank, and drawing
regenerant, see Initial Startup Step-By-Step Instructions on page 32.
Manual Regeneration Procedures
To Initiate a Manual Regeneration:
• Press REGEN once for delayed regeneration.
System will regenerate at next set regen time (2:00 AM).
A flashing regen (recycle) symbol will be displayed.
• Press and hold REGEN for5 seconds to initiate immediate manual
regeneration. A solid regen symbol will be displayed.
• After immediate regeneration has begun, press REGEN again to initiate a
second manual regeneration. An X2 symbol will be displayed, indicating a
second regeneration will follow the first regeneration.
During a Regeneration:
• A "C#" is displayed to show current cycle.
• Totalregen time remaining is displayed on screen.
• Press and hold SET to show current cycle time remaining.
To Advance Regeneration Cycles:
• Press and hold SET - showing current cycle time.
• Simultaneouslypress SET and UPto advance one cycle.
An hourglasswilldisplay while cam isadvancing.
When cam reaches next cycle, "C2" will be displayed.
• Repeat SET and UP to advance through each cycle.
• Press and hold SET and UP buttons for 5 seconds to cancel regen.
Hourglass will begin flashing, indicating regen is cancelled.
Camshaft will advance to home - may take 1-2minutes.
Regeneration Cycles:
•C1-Backwash
• C2 - Regenerant Draw/Slow Rinse (not used in filter mode)
• C3 - Slow Rinse (not used in filter mode)
• C4 - System Pause (to repressurize tank)
• C5 - Fast rinse cycle 1
• C6 - Backwash cycle 2 (not used in filter mode)
• C7 - Fast Rinse cycle 2 (not used in filter mode)
• C8 -Regenerant refill (not usedin filter mode)
Time & Day
Regen Time & Day
Salt
SU MO TU WE TH FR SA DAYS
C
Capacity
Hardness
MIN
x2
Cycle Indicator
Regen Symbol
Second Manual Regen Symbol

7
Rev D
QUICK START
Resetting The Control
To reset the control:
1. Press and hold SET and DOWN simultaneously for 5 seconds.
2. H0 and thesystem’s set resin volume (or "F" mode) will be displayed.
3. If a history value other than "H0" is displayed, use the up arrow to scroll
through the settings until "H0" is displayed.
4. To reset the control, press and hold SET for 5 seconds.
5. The control willbe reset to an unprogrammed state.
6. Go to "Initial Set-up" section of this sheet to reprogram control.
Further programming or set-up instructions can be found in this manual.
Unprogrammed control after reset
Resetting the Logix Controller
Time & Day
Regen Time & Day
Salt
SU MO TU WE TH FR SA DAYS
H
Capacity
Hardness
Time & Day
Regen Time & Day
Salt
SU MO TU WE TH FR SA DAYS
Capacity
Hardness
WARNING: Resetting the control will delete all information stored in its
memory. This willrequireyoutoreprogramthecontrolcompletelyfrom
the initial power up mode.

8 How To Use This Manual
Rev D
MANUAL OVERVIEW
How To Use This Manual
This installation manualis designed to guide the installer through the
process of installing and starting conditioners featuring the 700 Logix
series controllers.
This manualis a reference and will not include every system installation
situation. The person installing this equipment should have:
• Training in the 700 Logix series controllers and water conditioner
installation
• Knowledge of water conditioning and how to determine proper
control settings
• Basic plumbing skills
• The directional instructions "left"and “right" aredetermined by looking
at the front of the unit.
Icons That Appear In This Manual
Left Side Right Side
WARNING: Failure to follow this instruction can result in personalinjury
or damage to the equipment.
NOTE: This will make the process easier if followed.

General Warnings And Safety Information 9
Rev D
EQUIPMENT INSTALLATION
General Warnings And Safety Information
The 268 water conditioner’s control valve conforms to NSF/ANSI44 and
61formaterialsandstructuralintegrityonly.Genericsystemsweretested
and certified by WQA as verified by the performance data sheet.
Electrical
There are no user-serviceable parts in the AC adapter, motor, or controller.
In the event of a failure, these should be replaced.
• All electrical connections must be completed according to local codes.
• Use only the power ACadapter that is supplied.
• The power outlet must be grounded.
• To disconnect power, unplug the AC adapter from its power source.
Mechanical • Do not use petroleum based lubricants such as vaseline, oils,or
hydrocarbon based lubricants.Use only100% silicone lubricants.
• All plastic connections should be hand tightened. Teflon tape may be
used on connections that do not use an O-ring seal. Do not use pliers
or pipe wrenches.
• All plumbing must be completed according to local codes.
• Soldering near the drain line should be done before connectingthe
drainline to the valve. Excessiveheatwillcause interior damageto the
valve.
• Observe drain line requirements.
• Do not use lead-based solder for sweat solder connections.
• The drain line mustbe a minimum of 1/2-inchdiameter. Use
3/4-inch pipe if the backwash flow rate is greater than 7 GPM
(26.5 Lpm) or the pipe length is greater than 20 feet (6 m).
• Do not support the weight of the system on the control valve fittings,
plumbing, or the bypass.
• It is not recommended to use sealants on the threads. Use Teflon*
tape on the threads of the 1-inch NPT elbow, the drain line
connections, and other NPT threads.
*Teflon is a trademark of E.I. duPont de Nemours.

10 General Warnings And Safety Information
Rev D
General
• Observe allwarnings thatappear in this manual.
• Keep the media tank in the upright position. Do not turn on side,
upside down, or drop.Turning the tank upside down will cause media
to enter the valve.
• Operating ambient temperature is between 34°F (1°C) and 120°F
(49°C).
• Operating water temperature is between 34°F (1°F) and 100°F (38°C).
• Working water pressure range is 20 to 120 psi (1.38 to 8.27 bar). In
Canada the acceptable working water pressure range is 20 to 100 psi
(1.38 to 6.89 bar).
• Use only regenerantsalts designed for water softening. Do not use ice
melting, block, or rock salts.
• Follow state and local codes for water testing.Do not use waterthat is
micro biologically unsafe or of unknown quality.
• When filling mediatank, do not open water valve completely. Fill tank
slowly to prevent media from exiting the tank.
• When installing the water connection (bypass or manifold) connect to
the plumbing system first. Allow heated parts to cool and cemented
parts to set before installing any plastic parts. Do not get primer or
solvent on O-rings, nuts, or the valve.
System Regeneration Cycles (7-Cycle Operation)
1. Service (Downflow) — Cycle C0:
Untreated water is directed down through the resin bed and up
through the riser tube. The hardness ions attach themselves to the
resin and are removed from the water. The water is conditioned as it
passes through the resin bed.
2. Backwash (Upflow) — Cycles C1, C6:
The flow of water is reversed by the control valve and directed down
the riser tube and up through the resin bed. During the backwash
cycle,the bed is expanded and debris is flushed to the drain.
3. Brine/Slow Rinse (Downflow) — Cycles C2, C3:
The control directs water through the brine injector and brine is drawn
from the regeneranttank. The brine is then directed down through the
resin bed and upthrough the risertube to the drain. The hardness ions
are displaced by sodium ions and are sentto the drain. The resin is
regenerated during the brine cycle. Brinedraw is completed when the
air check closes.
4. Repressurize Cycle (Hard Water Bypass Flapper Open) — Cycle C4:
This cycle allows the air and water to hydraulically balancein the
valve before continuing the regeneration.

General Warnings And Safety Information 11
Rev D
5. Fast Rinse (Downflow) — Cycles C5, C7:
The control directs water down through the resin bed and up through
the riser tube to the drain. Any remainingbrine residualis rinsed from
the resin bed.
6. Brine Refill — Cycle C8:
Brine refill occurs during a portion of the fast rinse cycle. Water is
directed to the regeneranttankat a controlled rate, to create brine for
the next regeneration.
Figure 1
SERVICE BACKWASH BRINE/SLOW RINSE
FAST RINSE
From Regenerant
Tank
To Regenerant
Tank
BRINE REFILL
REPRESSURIZE
C0 C1 and C6 C2 and C3
C4 C5 and C7 C8

12 Valve Features
Rev D
Valve Features
Figure 2
255 Valve Identification
Check Ball AirCheck
Regenerant Tank
Refill Controller
Injector and Cap
Outlet
Inlet
Drain
Backwash
Locking Bar
Injector
Valve Discs
Camshaft
Drain Control
Screen Filter
Manifold
Motor
Optical Sensor
Control Module
Mount
One Piece Valve
Tube Connection
Connection
Disc Spring
Right Side
Left Side

Valve Features 13
Rev D
Figure 3
Performa Valve Identification
Refill Controller
Regenerant Tube Connection
Injector and cap
Valve Discs
Outlet
Drain
Inlet Backwash
Injector Screen
Camshaft
Drain Control
Filter
Control Module
Mount
One Piece Valve
Disc Spring
Motor
Optical Sensor
Right Side
Left Side

14 Location Selection
Rev D
Figure 4
700 Series Controller Identification
Location Selection
Location of a water treatment system is important.The following
conditions are required:
• Level platform or floor
• Room to access equipment for maintenance and adding regenerant
(salt) to tank.
• Ambient temperatures over 34°F (1°C) and below 120°F (49°C).
• Water pressure below 120 psi (8.27 bar) andabove 20 psi
(1.4 bar).
• In Canada the water pressure must be below 100 psi (6.89 bar).
• Constant electrical supply tooperate the controller.
• Total minimum pipe run to water heater of ten feet (three meters) to
prevent backup of hot water into system.
• Local drain for discharge as close as possible.
• Water line connections with shutoff or bypass valves.
• Must meet anylocal and state codes for site of installation.
• Valve is designed for minor plumbing misalignments. Do not support
weight of system on the plumbing.
• Be sure all soldered pipes are fully cooled before attaching plastic
valve to the plumbing.
Time & Day
Regen Time & Day
Salt
SU MO TU WE TH FR SA DAYS
LBS
PM
MIN
KG
x100
x2
P
H
C
Capacity
Hardness
LCD Display
Manual Regen Button
Down Button Set Button Up Button
742/762 Turbine Inputor Dry Contact SignalInput
Main Motor &
Optical Sensor
Connection
AC Adapter
(low voltage)
Input
No Salt Detector
Connection
Front
Back

Water Line Connection 15
Rev D
Outdoor Locations
When the water conditioning system is installed outdoors, several items
must be considered.
• Moisture — The valve and 700 controllerare rated for NEMA 3
locations. Falling water should not affect performance.
The system is not designed to withstand extreme humidity or water
spray from below. Examples are:constantheavy mist, near corrosive
environment, upwards spray from sprinkler.
• Direct Sunlight — The materials used will fade or discolor over time in
direct sunlight. The integrity of the materials will notdegrade to cause
system failures.
If it is necessary to locate the conditioner in direct sunlight, a
protective outdoor cover (P/N 1267811)over the valve andcontroller is
necessary.
• Temperature — Extreme hot or cold temperaturesmay cause damage
to the valve or controller.
Freezingtemperatureswillfreeze thewaterinthevalve.This willcause
physical damage to the internal parts as well as the plumbing.
High temperatures will affect the controller. The display may become
unreadable but the controller should continue to function.When the
temperature drops down into normal operating limits the display will
return to normal. A protective cover, P/N 1267811, should assist with
high temperature applications.
• Insects— The controller andvalve have been designed to keep allbut
the smallest insects out of the critical areas. Any holes in the top plate
can be covered with a metal foil duct work tape. The top cover should
be installed securely in place.
• Wind — The Logix cover is designed to withstand a 30 mph
(48 Kph) wind when properly installed on the valve.
Water Line Connection
A bypass valve system should be installed on allwater conditioning
systems. Bypass valvesisolate the conditioner from the water system and
allow unconditioned water to be used. Service or routine maintenance
procedures may also require that the system is bypassed. Figures 5, 6,
and 7 show the three common bypass methods.

16 Water Line Connection
Rev D
Figure 5
Series 256 bypass for use with 255 valve body
Figure 6
Series 1265 bypass for use with Performa valve bodies
Figure 7
Typical Globe Valve Bypass System
Normal Operation In Bypass
B
Y
P
A
S
S
B
Y
P
A
S
S
B
Y
P
A
S
S
B
Y
P
A
S
S
In Out In Out
Normal Operation In Bypass
B
Y
P
A
S
S
B
Y
P
A
S
S
B
Y
P
A
S
S
B
Y
P
A
S
S
Water
Conditioner
In Out
Water
Conditioner
In Out
Water Water
Cdii
Normal Operation In Bypass
Water
Conditioner Water
Conditioner

Drain Line Connection 17
Rev D
Drain Line Connection
1. The unit should be above and not more than 20 feet (6.1 m) from the
drain.Use an appropriate adapter fitting to connect 1/2-inch (1.3 cm)
plastic tubing to the drain line connection of the control valve.
2. If the backwash flow rate exceeds 5 gpm (22.7 Lpm) or if the unit is
located 20-40 feet (6.1-12.2 m) from drain, use 3/4-inch (1.9 cm)
tubing.Use appropriate fittings to connect the 3/4-inch tubing to the
3/4-inch NPT drain connection on valve.
3. The drain line may be elevated up to 6 feet (1.8 m) providing the run
does not exceed 15 feet (4.6 m) and water pressure at the conditioner
is not less than 40 psi (2.76 bar). Elevation can increase by 2 feet (61
cm) foreach additional 10 psi(.69 bar) of water pressure at the drain
connector.
4. Where the drainline is elevated but empties into a drain below the
level of the control valve, form a7-inch (18-cm)loop atthe far end of
the line so that the bottom of the loop is level with the drain line
connection. This willprovide an adequate siphon trap.
WARNING: The inlet water must be connected to the inlet port of the
valve. When replacing non-Autotrol valves, the inlet and outlet may be
reversed. It is also possible for the plumbing to be installed in an
opposite order.
Do not solder pipes with lead-based solder.
WARNING: Do not use tools to tighten plastic fittings. Over time,stress
may breakthe connections.Whenthe 1265or 256bypassvalveisused,
only hand tighten the plastic nuts.
WARNING: Do not use petroleum grease on gaskets when connecting
bypass plumbing. Use only 100% silicone grease products when
installing any plastic valve. Non-silicone grease may cause plastic
components to fail over time.
NOTE: Standard commercial practices are expressed here. Local codes
may require changes to the following suggestions. Check with local
authorities before installing a system.

18 Overflow Line Connection
Rev D
Where the drain empties into an overhead sewer line, a sink-type trap
must be used.
Secure the end of the drain line to prevent it from moving.
Figure 8
Drain Line Connection
Overflow Line Connection
(not used with 3-cycle filter system)
In the event of a malfunction, the regenerant TANK OVERFLOW will direct
“overflow” to thedrain instead of spilling on thefloor. Thisfitting should be
on the side of the cabinet or regenerant tank. Most tank manufacturers
include a post for the tank overflow connector.
Toconnect the overflow line, locate hole onside of tank. Insert overflow
fitting into tank and tighten with plastic thumb nut andgasketas shown
(Figure 9). Attach length of 1/2-inch (1.3-cm) I.D. tubing (not supplied) to
fitting and run to drain. Do not elevate overflow line higher than overflow
fitting.
Do not tie into drainline of control unit. Overflow line must be a direct,
separate line from overflow fitting to drain, sewer or tub. Allow an air gap
as per drain line instructions.
Right Way
Air Gap
Drain
NOTE: Waste connections or drain outlet shall be designed and
constructed to provide for connection to the sanitary waste system
through an air-gap of 2 pipe diameters or 1 inch (22 mm) whichever is
larger.
WARNING: Never insert drain line directly into a drain, sewer line, or
trap (Figure 8). Always allow an air gap between the drain line and the
wastewater toprevent the possibility of sewage beingback-siphoned
into the conditioner.

Regenerant Line Connection 19
Rev D
Figure 9
Overflow Line Connection
Regenerant Line Connection
(not used with 3-cycle filter system)
The regenerant line from the tank connects to the valve. Make the
connections and hand tighten. Be sure that the regenerantline is secure
and free from air leaks.Even a smallleakmay cause the regenerantline to
drainout, and the conditionerwill not draw regenerantfrom the tank. This
may also introduce air into the valve causing problems with valve
operation.
Mostinstallations utilize a tank check valve. This is not necessary when
using the 255 valve with the built-in aircheck. Using atank check valve
with the 255 valve with aircheck will resultin premature checking of the
aircheck valve, before the tank is empty.
Figure 10
Air Check for 255 valve
Overflow Fitting
Drain Tubing
Air Gap
Drain
Secure hose in place
Regenerant LineConnection

20 Regenerant Line Connection
Rev D
Figure 11
RegenerantConnectionfor
Performa Valve
An aircheck must be used in the regenerant line when installing a
Performa valve.
NOTE: When installing a 3-cycle filter (253, 263, or 273 valve) use a cap
on the regenerant line connection to prevent water seepage from the
port. See Parts and Accessories section for part number.
Regenerant Line Connection
NOTE: Be sure to use a 3/8 inch NPT
plumbing connection when attaching
regenerant line to the Performa valve.
This manual suits for next models
6
Table of contents
Popular Control Unit manuals by other brands
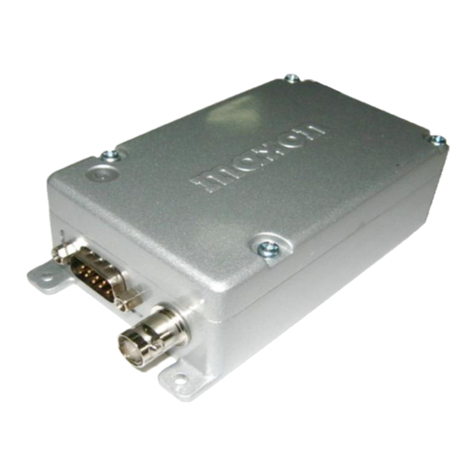
Maxon
Maxon SD-17OEX Series User instruction manual
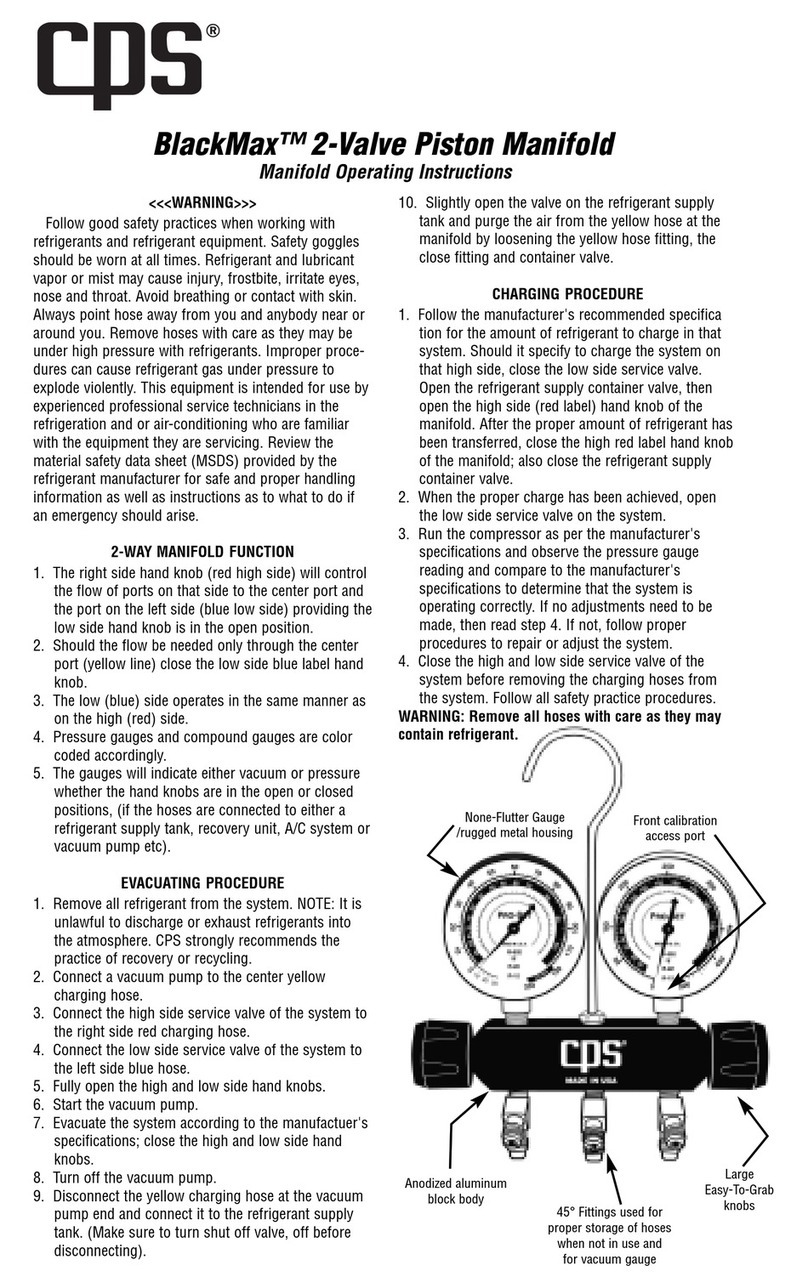
CPS
CPS BlackMax operating instructions

Burkert
Burkert 5406 operating instructions
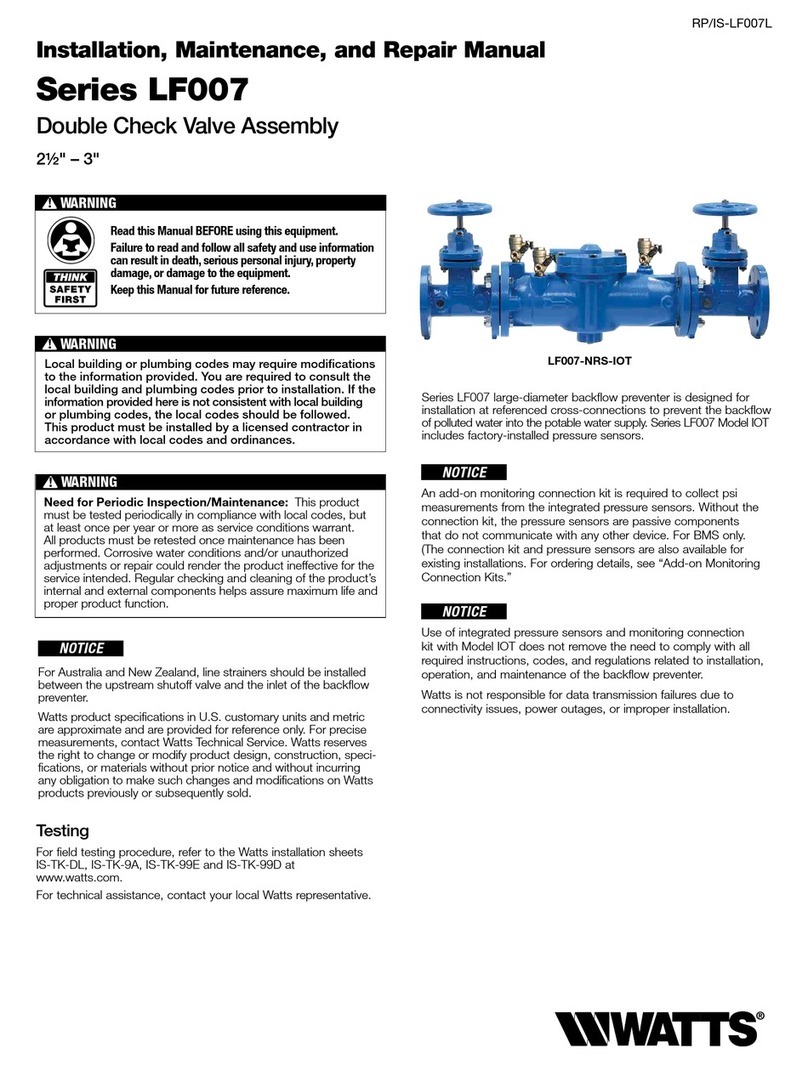
Watts
Watts LF007 Series INSTRUCTION, INSTALLATION, MAINTENANCE AND REPAIR MANUAL
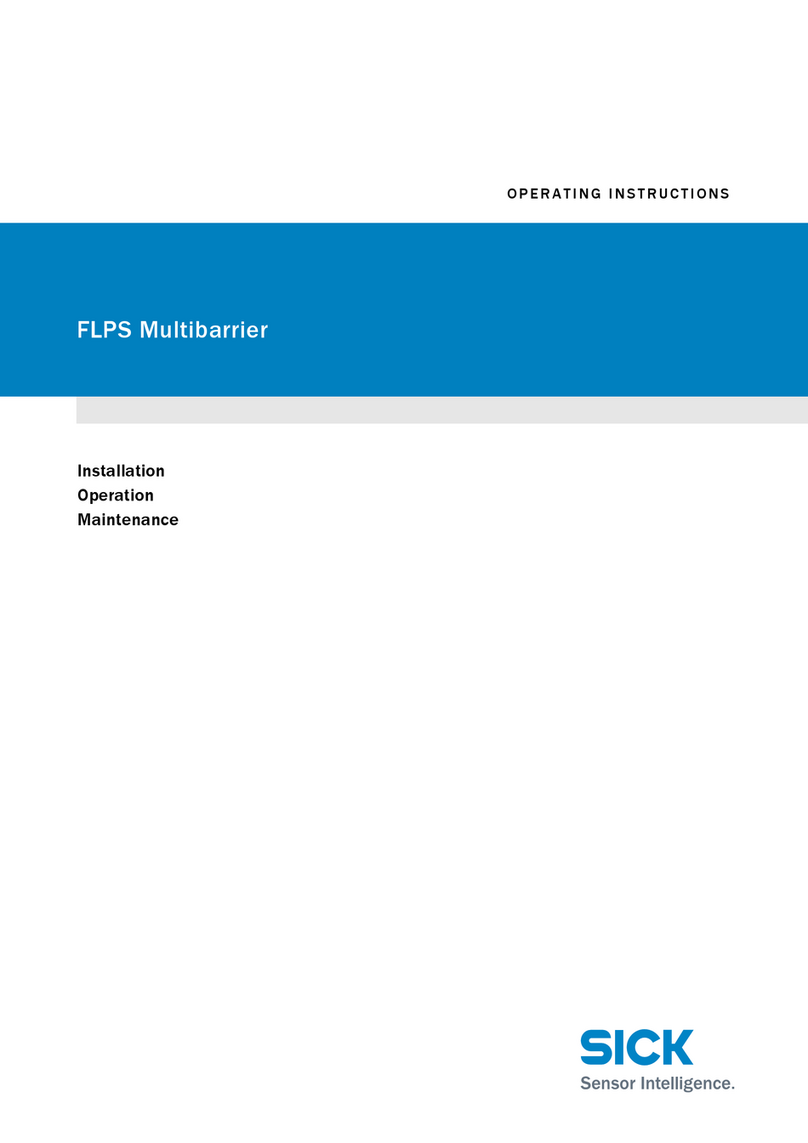
SICK
SICK FLPS Series operating instructions
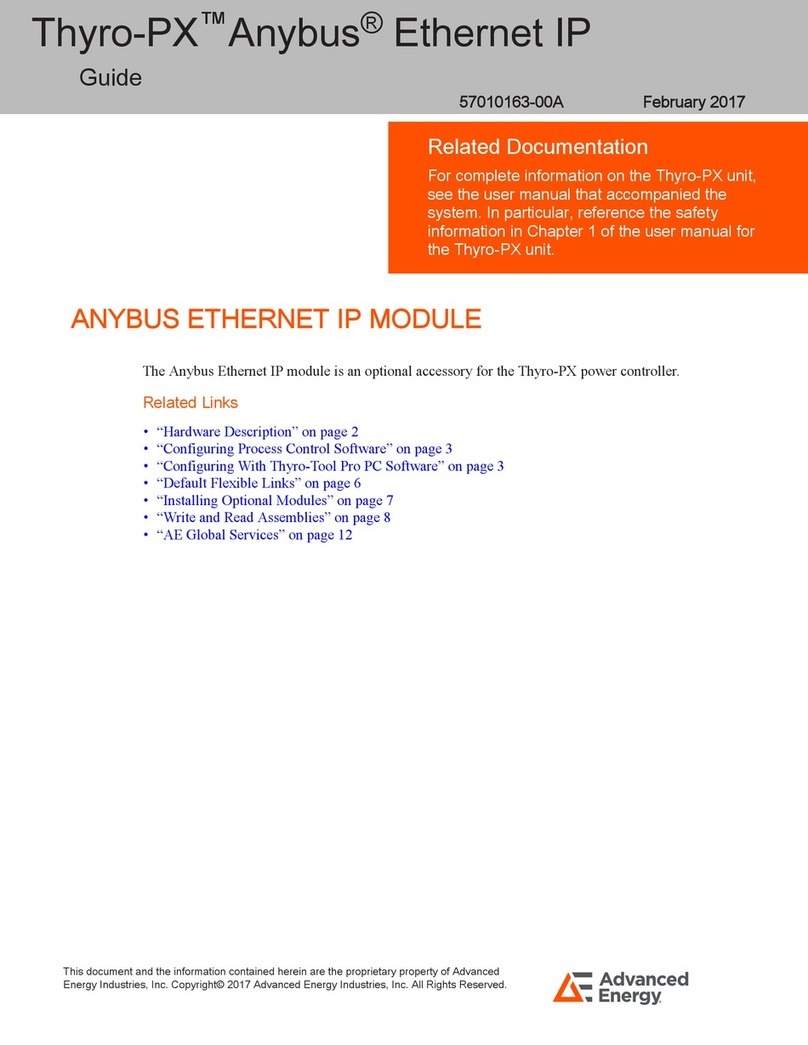
Advanced Energy
Advanced Energy Thyro-PX Anybus Guide