UTC Fire and Security DET-TRONICS 95-8533 User manual

Instructions 95-8533
Eagle Quantum Premier®
Fire and Gas Detection/Releasing System
7.1 9/09 95-8533

Section 1 - Safety
ALERT MESSAGES ..............................................................1-1
Section 2 - Introduction
SYSTEM DESCRIPTION...................................................... 2-1
Communications Loop .................................................. 2-1
LON Communication Heartbeat .................................... 2-2
Theory of Operation ...................................................... 2-2
Controller Logs.............................................................. 2-4
Controller User Logic .................................................... 2-4
Communication Network Fault Operation ..................... 2-4
Multiple Wiring Faults .................................................... 2-5
MAJOR COMPONENT DESCRIPTIONS............................. 2-5
System Controller.......................................................... 2-5
Local Operating Network (LON).................................... 2-6
Network Extenders ................................................ 2-6
EQ21xxPS Series Power Supplies and EQ2100PSM
Power Supply Monitor............................................ 2-7
EQ211xPS, EQ213xPS and EQ217xPS Power Supplies....2-7
EQ2220GFM Ground Fault Monitor ...................................... 2-7
Field Devices................................................................. 2-7
Flame Detectors .................................................... 2-7
EQ3730EDIO Enhanced Discrete I/O Module....... 2-8
EQ3700 8 Channel DCIO Module ......................... 2-8
EQ3720 8 Channel Relay Module ......................... 2-9
EQ3710AIM Analog Input Module ......................... 2-9
EQ3740IPM Intelligent Protection Module ........... 2-10
EQ25xxARM Agent Release Module................... 2-10
EQ25xxSAM Signal Audible Module.....................2-11
EQ22xxIDC Series Initiating Device Circuit......... 2-12
EQ22xxDCU / EQ22xxDCUEX Digital
Communication Units ................................... 2-12
PIRECL PointWatch Eclipse................................ 2-12
OPECL Open Path Eclipse.................................. 2-12
Section 3 - Installation
SAFETY SYSTEM DESIGN REQUIREMENTS.................... 3-1
Identifying the Area of Protection .................................. 3-1
Identifying Wiring, Network (LON), and System Power
Requirements ........................................................ 3-1
General Wiring Requirements................................ 3-1
Power Wiring.......................................................... 3-1
Determining Power Requirements ......................... 3-3
EQ211xPS, EQ213xPS and EQ217xPS Power
Supplies ......................................................... 3-5
Backup Battery ...................................................... 3-5
Battery Charger ..................................................... 3-5
EQP2120PS(–B) Power Supplies.......................... 3-5
Determining Power Requirements ......................... 3-6
Shield Grounding................................................... 3-7
Junction Box Grounding ........................................ 3-7
Response Time vs. System Size............................ 3-7
Moisture Damage Protection ................................. 3-7
Electrostatic Discharge.......................................... 3-7
GROUND FAULT MONITOR (GFM) INSTALLATION ........... 3-7
Mounting................................................................ 3-7
Wiring .................................................................... 3-7
NETWORK AND NETWORK EXTENDER INSTALLATION ......3-8
Mounting................................................................ 3-8
Wiring .................................................................... 3-8
INITIATING DEVICE CIRCUIT (IDC) INSTALLATION ........ 3-10
EQ22xxIDC Series Initiating Device Circuit .......................3-10
Mounting.............................................................. 3-10
Wiring .................................................................. 3-10
EQ22xxIDCGF Series Initiating Device Circuit Ground
Fault......................................................................3-11
Mounting...............................................................3-11
Wiring ...................................................................3-11
EQ22xxIDCSC Series Initiating Device Circuit Short
Circuit .................................................................. 3-12
Mounting.............................................................. 3-12
Wiring .................................................................. 3-12
Table of Contents

EQ300X CONTROLLER INSTALLATION........................... 3-13
Enclosure Requirements............................................. 3-13
Mounting ..................................................................... 3-13
Serial Interface Board ................................................. 3-13
Wiring.......................................................................... 3-14
Power Wiring........................................................ 3-14
Electrical Connections......................................... 3-14
Controller to Controller Communication ...................... 3-18
Conguration............................................................... 3-21
Software Dened Addresses ............................... 3-21
EQ300X REDUNDANT CONTROLLER INSTALLATION ... 3-21
Enclosure Requirements............................................. 3-21
Mounting ..................................................................... 3-21
Wiring.......................................................................... 3-21
LON Wiring.................................................................. 3-21
High Speed Serial Link (HSSL)................................... 3-21
Conguration............................................................... 3-22
S3 Conguration.................................................. 3-22
Controller Addresses ........................................... 3-22
Modbus................................................................ 3-22
ControlNet ........................................................... 3-22
EQ21XXPS SERIES POWER SUPPLY AND
POWER SUPPLY MONITOR INSTALLATION .................... 3-22
Mounting ..................................................................... 3-22
Wiring.......................................................................... 3-22
Startup ........................................................................ 3-24
Measuring Battery Voltage and Charging Current....... 3-24
EQP2120PS(–B) POWER SUPPLY AND
REDUNDANCY MODULE INSTALLATION ........................ 3-25
Mounting ..................................................................... 3-25
Wiring.......................................................................... 3-25
Startup ........................................................................ 3-26
EDIO MODULE INSTALLATION......................................... 3-27
Conguration............................................................... 3-31
8 CHANNEL DCIO INSTALLATION.................................... 3-32
Mounting ..................................................................... 3-32
Wiring.......................................................................... 3-32
Conguration............................................................... 3-36
8 CHANNEL RELAY MODULE INSTALLATION................. 3-36
Mounting ..................................................................... 3-36
Wiring.......................................................................... 3-36
Conguration............................................................... 3-37
ANALOG INPUT MODULE INSTALLATION....................... 3-38
Mounting ..................................................................... 3-38
Wiring.......................................................................... 3-38
Conguration............................................................... 3-39
INTELLIGENT PROTECTION MODULE INSTALLATION ....3-40
Wiring .............................................................................3-40
Conguration ..................................................................3-43
GAS DETECTOR LOCATION AND INSTALLATION .................. 3-44
Environments and Substances that Affect Gas Detector
Performance ........................................................ 3-44
EQ22xxDCU Digital Communication Unit used with
Det-Tronics H2S/O2 Sensors or other Two-Wire
4-20 mA Devices ................................................. 3-45
Assembly and Wiring Procedure.......................... 3-45
Sensor Separation for DCU with H2S and O2
Sensors........................................................ 3-46
EQ22xxDCU Digital Communication Unit used with
PointWatch/DuctWatch ........................................ 3-47
Assembly and Wiring Procedure.......................... 3-47
Sensor Separation for DCU with PointWatch ...... 3-47
EQ22xxDCUEX Digital Communication Unit (used with
Det-Tronics Combustible Gas Sensors)............... 3-48
Mounting.............................................................. 3-48
Wiring .................................................................. 3-48
Sensor Separation with DCUEX.......................... 3-49
EQ25xxARM Series Agent Release Module............... 3-51
Mounting.............................................................. 3-51
Wiring .................................................................. 3-51
Supervised Output for Deluge and Pre-action..... 3-53
Jumpers............................................................... 3-53
Address Setting ................................................... 3-53
EQ25xxSAM Series Signal Audible Module ............... 3-53
Mounting.............................................................. 3-53
Wiring .................................................................. 3-53
Jumpers............................................................... 3-54
Address Setting ................................................... 3-54
SYSTEM CONFIGURATION .............................................. 3-55
Setting Device Network addresses ............................. 3-55
Overview of Network Addresses.......................... 3-55
Setting Field Device Addresses ........................... 3-55
TYPICAL APPLICATIONS .................................................. 3-55
Table of Contents – Continued

Section 4 - Operation
SYSTEM CONTROLLER...................................................... 4-1
Pushbuttons .................................................................. 4-1
Controller Status Indicators........................................... 4-2
Text Display................................................................... 4-2
Controller Menu Options ............................................... 4-2
Controller Audible Alarm................................................ 4-6
ControlNet Status Indicators (Optional)......................... 4-7
Sequence of Events During a Conguration Data
Download............................................................... 4-7
Controller Redundancy ................................................. 4-9
ENHANCED DISCRETE I/O MODULE ...............................4-11
Power-Up Sequence ....................................................4-11
8 CHANNEL DCIO MODULE ............................................. 4-12
Power-Up Sequence ................................................... 4-12
8 CHANNEL RELAY MODULE........................................... 4-13
Power-Up Sequence ................................................... 4-13
ANALOG INPUT MODULE ................................................ 4-14
Power-Up Sequence ................................................... 4-14
INTELLIGENT PROTECTION MODULE............................ 4-15
Power-Up Sequence ................................................... 4-15
Embedded Logic - Purpose ........................................ 4-15
Embedded Logic - Control Transfer Sequence Description. . 4-15
Embedded Logic - S3 Congurable Options............... 4-16
Embedded Logic - Operation ...................................... 4-17
EQ21XXPSM POWER SUPPLY MONITOR....................... 4-18
EQ2220GFM GROUND FAULT MONITOR ........................ 4-18
EQ22XXIDC SERIES INITIATING DEVICE CIRCUIT........ 4-19
EQ22XXDCU AND EQ22XXDCUEX DIGITAL
COMMUNICATION UNITS ................................................. 4-19
EQ25xxARM AGENT RELEASE MODULE........................ 4-20
EQ25xxSAM SIGNAL AUDIBLE MODULE ........................ 4-20
EQ24xxNE NETWORK EXTENDER.................................. 4-20
SYSTEM STARTUP ............................................................ 4-21
Pre-Operation Checks................................................. 4-21
General Start-up Procedures ...................................... 4-22
Startup Procedure for Controller.................................. 4-23
Startup Procedure for EDIO Module ........................... 4-23
Startup Procedure for DCIO Module ........................... 4-24
Table of Contents – Continued

Section 5 - Maintenance
ROUTINE MAINTENANCE .................................................. 5-1
Batteries ........................................................................ 5-1
Manual Check of Output Devices.................................. 5-1
O-Ring Maintenance ..................................................... 5-1
GAS SENSOR MAINTENANCE........................................... 5-1
CALIBRATION AND ADJUSTMENTS .................................. 5-2
Calibration Algorithm A For Manual Calibration of Universal
DCU....................................................................... 5-2
Normal Calibration................................................. 5-2
Sensor Replacement ............................................. 5-3
Calibration Algorithm C For Combustible Gas DCUs and
Automatic Calibration of Universal DCUs .............. 5-3
Routine Calibration ................................................ 5-3
Initial Installation and Sensor Replacement —
Combustible Gas............................................ 5-4
Sensor Replacement — Toxic Gas........................ 5-4
Calibration Algorithm D For Universal DCUs with O2
Sensor ................................................................... 5-5
Normal Calibration................................................. 5-5
Sensor Replacement ............................................. 5-5
Calibration Algorithm G For DCUs with PointWatch or
DuctWatch ............................................................. 5-6
Routine Calibration ................................................ 5-6
Sensor Replacement ............................................. 5-6
DEVICE CALIBRATION LOGS AND RECORDS ................. 5-6
TROUBLESHOOTING.......................................................... 5-6
REPLACEMENT PARTS ...................................................... 5-8
DEVICE REPAIR AND RETURN.......................................... 5-8
ORDERING INFORMATION ................................................ 5-8
Section 6 - Specications
EQ300X Controller ............................................................... 6-1
LON Termination Module ...................................................... 6-2
EQ3730EDIO Enhanced Discrete I/O Module ..................... 6-3
EQ3700 DCIO Module.......................................................... 6-5
EQ3720 Relay Module.......................................................... 6-6
EQ3710AIM Analog Input Module ........................................ 6-7
HART Interface Module ........................................................ 6-7
EQ3740IPM Intelligent Protection Module ............................ 6-8
EQ21xxPS Power Supplies .................................................. 6-9
EQP2120PS(–B) Power Supplies....................................... 6-10
Redundancy Module Quint-Diode/40 ................................. 6-10
EQ21xxPSM Power Supply Monitor ................................... 6-10
EQ22xxIDC Series Initiating Device Circuit.........................6-11
EQ2220GFM Ground Fault Monitor.................................... 6-12
EQ22xxDCU Series Digital Communication Unit ............... 6-12
EQ25xxARM Agent Release Module.................................. 6-13
EQ25xxSAM Signal Audible Module................................... 6-13
EQ24xxNE Network Extender ............................................ 6-14
Combustible Gas Sensor.................................................... 6-15
Electrochemical Sensors .................................................... 6-15
EQ21xxPS Power Supply ................................................... 6-15
APPENDIX A — FM APPROVAL DESCRIPTION ................ A-1
APPENDIX B — CSA CERTIFICATION DESCRIPTION......B-1
APPENDIX C — CE MARK..................................................C-1
APPENDIX D — EQP MARINE, USCG APPROVAL............D-1
APPENDIX E — ROCKER SWITCH TABLE ........................E-1
Table of Contents – Continued

Section 1
Safety
ALERT MESSAGES
The following Alert Messages, DANGER, WARNING,
CAUTION, and IMPORTANT are used throughout this
manual and on the system to alert the reader and
operator to dangerous conditions and/or important
operational or maintenance information.
DANGER!
Identies immediate hazards that WILL result in
severe personal injury or death.
WARNING!
Identies hazards or unsafe practices that COULD
result in severe personal injury or death.
CAUTION!
Identies hazards or unsafe practices that COULD
result in minor personal injury or damage to
equipment or property.
IMPORTANT!
A brief statement of fact, experience or importance
that is given as an aid or explanation.
WARNING!
The hazardous area must be de-classied prior
to removing a junction box cover or opening a
detector assembly with power applied.
CAUTION!
1.
Be sure to read and understand the entire instruction
manual before installing or operating the Eagle
Quantum Premier® system. Only qualied personnel
should install,maintain or operate the system.
2. The wiring procedures in this manual are intended
to ensure proper functioning of the devices under
normal conditions. However, because of the many
variations in wiring codes and regulations, total
compliance with these ordinances cannot be
guaranteed. Be certain that all wiring and
equipment installation meets or exceeds the latest
revisions of the appropriate NFPA Standards,
National Electrical Code (NEC), and all local
ordinances. If in doubt, consult the Authority
Having Jurisdiction (AHJ) before wiring the system.
All wiring shall be installed in accordance with the
manufacturer’s recommendations.
3. Some Eagle Quantum Premier devices contain
semiconductor devices that are susceptible to
damage by electrostatic discharge. An
electrostatic charge can build up on the skin and
discharge when an object is touched. Always
observe the normal precautions for handling
electrostatic sensitive devices, i.e. use of a wrist
strap (if available) and proper grounding.
4. To prevent unwanted actuation, alarms and
extinguishing devices must be secured prior to
performing system tests.
INSTRUCTIONS
Eagle Quantum Premier®
Fire and Gas Detection/
Releasing System
7.1 ©Detector Electronics Corporation 2009 9/09 95-8533
*oiis Detector Electronics' Trademark for its patented Optical
Integrity Systems, U.S. Patent 3,952,196, United Kingdom Patent
1,534,969, Canada Patent 1,059,598.

7.1 95-85332-1
Section 2
Introduction
SYSTEM DESCRIPTION
The Eagle Quantum Premier (EQP) system combines
"fire detection and extinguishing agent release" and
"hazardous gas monitoring" in one complete package.
The system is intended for use in hazardous locations
and is designed to meet the requirements of approval
agencies from around the world.
The system consists of a Controller and a number of
addressable microprocessor based field devices.
The Controller coordinates system device
configuration, monitoring, annunciation, and control,
while the field devices communicate their status and
alarm conditions to the Controller.
The EQP controller can be arranged in a redundant
configuration, thereby increasing the availability of the
system. The controllers work in “Master” and “Hot
Standby” mode.
Various combinations of field devices can be
configured as part of the system. The actual selection
depends on the requirements of the application and
the regulations that cover the type of protection
required. See Figure 2-1 for a block diagram of the
Eagle Quantum Premier system.
All field devices are tied into a communication loop
that starts and ends at the Controller. Each device
connected to the communication loop is assigned a
unique identity by setting its address switches. All
other device operation parameters are configured
through Det-Tronics “Safety System Software”. These
selections define the type of device and how it is to
operate. This system configuration data is then
downloaded into the Controller.
A programmed Controller is configured to
automatically download the configuration data into the
individual devices when they first communicate with
the Controller.
In addition to Det-Tronics advanced flame and gas
detectors, Eagle Quantum Premier offers the
capability of incorporating third party fire and gas
protection equipment into the system. These can be
either input or output devices. Typical input devices
include manual fire alarm "call boxes", heat detectors,
and analog combustible or toxic gas measurement
instruments. Typical output equipment includes
solenoids, strobes, and horns. All equipment is
monitored for wiring fault conditions.
For complete system integration, the Controller has
the capability to communicate with other systems
such as PLCs and DCSs. Different communication
protocols are supported, allowing the Controller to
communicate with other systems either directly or
through communication gateways.
NOTE
Existing Eagle Quantum eld devices such as
EQ22xxUV, EQ22xxUVIR and EQ22xxUVHT are
supported by the Eagle Quantum Premier system
(not FM Approved).
NOTE
For specic information relating to the SIL 2 rated
EQP system, refer to manual number 95-8599.
COMMUNICATIONS LOOP
Eagle Quantum Premier utilizes a Det-Tronics
Signaling Line Circuit (SLC), a version of Echelon’s
Local Operation Network (LON) customized
specifically for Eagle Quantum Premier. This network
provides several key advantages:
• ANSI/NFPA Class A, Style 7 performance of SLC
• Peer-to-peer communications
• Short message formats
• Expandability
The Controller utilizes several mechanisms to
continuously check the LON loop for fault conditions,
thereby providing the highest level of reliable
communication.
Every device on the LON loop has the ability to
communicate with the Controller at any time. This is
typically referred to as distributed peer-to-peer
communications. This design allows for immediate
alarm messages to be sent from the field devices to
the Controller.
All messages are kept short in order to maximize
network performance. This minimizes network
bottlenecks.
The Eagle Quantum Premier system is easily modified
to accommodate design changes or plant expansions.
This can involve adding LON sections, repositioning
LON sections, or removing LON sections from the loop.
There are LON communication implementation details
that affect and limit how the LON loop is changed.
Only devices that have been approved for use with
Eagle Quantum Premier can be connected up to the
LON. All approved devices have been tested and
certified to operate properly on the LON.

7.1 95-85332-2
LON COMMUNICATION HEARTBEAT
The Controller continuously broadcasts a heartbeat
signal over the LON loop. This heartbeat is used for
verifying the integrity of the LON loop and for keeping
the field devices from going into a fault isolation
mode. Once every second, the heartbeat contains the
current time and date, which are used by the field
devices to log status events and calibrations.
The Controller continuously tests LON continuity by
sending out a heartbeat on one LON port and then
listening for it on the other LON port. The Controller
also broadcasts the heartbeat signal in the opposite
direction around the loop. This ensures that all field
devices, the LON Network Extenders (NE), and
communication wiring are correctly passing the digital
information around the loop.
The field devices use the heartbeat as a mechanism
to ensure that there is a communication path back to
the Controller. If the field device does not receive a
heartbeat for a period of time, the device will go into a
LON fault isolation. In this situation, the device opens
one side of the LON and listens for a heartbeat on the
other side. If the device doesn’t receive a heartbeat, it
listens on the other side of the LON and opens the
opposite LON connection.
THEORY OF OPERATION
During normal operation, the Controller continuously
checks the system for fault conditions and executes
user defined programmed logic that coordinates the
control of the field devices. At the same time, the field
devices are continuously monitoring for device based
fault and alarm conditions.
When a fault condition occurs, the Controller displays
the fault condition on the Vacuum Fluorescent Text
Display, activates the appropriate fault LED(s),
activates the Trouble signal using the Controller’s
internal enunciator, and de-energizes the Controller’s
Trouble relay.
CONFIGURATION
PC
MODBUS
INTERFACE
NETWORK
EXTENDER
DIGITAL
COMMUNICATION
UNITS
PIRECL
GAS
DETECTOR
OPECL
GAS
DETECTOR
SIGNAL
AUDIBLE
MODULES
HORNS
&
BEACONS
GAS DETECTION
COMBUSTIBLE, TOXIC,
POINTWATCH OR
OTHER 4-20 MA INPUT
RS-232
RS-232
RS-232
RS-485
RS-485
8 DRY CONTACT INPUTS 8 RELAY
OUTPUT POINTS
UNSUPERVISED INPUTS AND OUTPUTS
8 CHANNEL DCIO MODULE
DRY CONTACT INPUTS CONFIGURABLE
OUTPUT POINTS
CONFIGURABLE INPUTS AND OUTPUTS
FIRE DETECTION
UV
DETECTOR
UVHT/C7050
DETECTOR
X3301
DETECTOR
X3302
DETECTOR
UV/IR
DETECTOR
IR
DETECTOR
INITIATING
DEVICE
CIRCUIT
CONTACT
CLOSURE
DEVICES
SIGNALING LINE CIRCUIT (SLC)
HARDWIRED I/O
SERIAL INTERFACE
EQP CONTROLLER
CONTROLNET
(OPTIONAL
INTERFACE)
ONBOARD
SERIAL
INTERFACE
OPTIONAL
SERIAL
INTERFACE
G2114
+ – + –
AGENT
RELEASE
MODULES
FIRE
SUPPRESSION
(SOL)
RELAY
MODULE
POWER
SUPPLY
MONITOR
BATTERY
CHARGER
AC
POWER
INPUT
SYSTEM
POWER
NOTE: CHANNELS CAN BE CONFIGURED
AS EITHER INPUTS OR OUTPUTS.
FAULT RELAY
(NC CONTACT)
8 UNSUPERVISED
RELAY OUTPUT POINTS
INTELLIGENT
PROTECTION
MODULE
ANALOG
INPUT
MODULE
8 4-20 MA INPUTS
PRECONFIGURED INPUTS
PRECONFIGURED OUTPUTS
2 SMOKE DETECTOR LOOPS
HSSL
CHANNELS CAN BE CONFIGURED AS INPUTS,
OUTPUTS, SMOKE/HEAT DETECTORS,
CLASS A INPUTS, OR CLASS A OUTPUTS.
8 CHANNEL EDIO MODULE
Figure 2-1—Block Diagram of Eagle Quantum Premier System

7.1 95-85332-3
Controller based fault conditions include the Controller
status and LON communications such as the
heartbeat being sent around the loop and the field
device loss of communications. Controller based fault
conditions are listed in Table 2-1.
Field device based fault conditions are transmitted to
the Controller, where they are then annunciated. Refer
to Table 2-2 for a listing of field device faults. Each
field device transmits its status to the Controller
on a regular basis.
When an alarm condition occurs, the Controller
displays the alarm condition on the text display,
activates the appropriate Alarm LED(s), and activates
the alarm signal using the Controller’s internal
annunciator.
Each field device must communicate alarm and fault
conditions to the Controller. The timing for transmitting
alarms and faults to the Controller is displayed in
Table 2-3.
Controller Faults Trouble LON Fault Trouble
Shown on Text Display LED LED Relay
Controller Fault X X
Device Offline X X
Extra LON Device X X
Invalid Cong X X
Lon Fault X X X
LON Ground Fault X X
Power Fail 1 X X
Power Fail 2 X X
RTC Fault X X
Redundancy Fault* X X
Field Device Faults Trouble Trouble
Shown on Text Display LED Relay
290 Volt Fault X X
AC Failed X X
Battery Fault X X
Beam Block X X
Calibration Fault X X
Channel Open X X
Channel Short X X
Dirty Optics X X
Ground Fault Negative X X
Ground Fault Positive X X
IR Auto Oi Fault X X
IR Fault X X
IR Manual Oi Fault X X
Low Aux Power Fault X X
Missing IR Sensor Fault X X
Missing UV Sensor Fault X X
Power Supply Fault X X
Sensor Fault X X
Supply Voltage Fault X X
Tx Lamp Fault X X
UV Auto Oi Fault X X
UV Fault X X
UV Manual Oi Fault X X
Table 2-1—Controller Based Faults Table 2-2—Field Device Based Faults
Table 2-3—Eagle Quantum Premier Status Update Rates
Number of Devices Output Devices Old Input Devices Newer Input Devices
ARM IDC DCU*
SAM UV Detector DCIO*
UVIR Detector X3301*
X3302*
PIRECL*
OPECL*
X5200*
X2200*
X9800*
AIM*
IPM*
PSM
1 to 100 1 Second 1 Second 1 Second
101 to 200 2 Seconds 2 Seconds 2 Seconds
201 to 246 5 Seconds 2 Seconds 3 Seconds
*Alarms are transmitted immediately. For Eclipse, the Status Update Rate is 1 second for all network sizes.
*Only for controller pair congured for redundancy.

7.1 95-85332-4
NOTE
All fault and alarm conditions are latched on the
Controller. To reset the Controller, conditions
indicated on the text display must currently be in
the OFF state. Pushing the reset button then
initiates a Controller reset. Active alarms will
remain through a Controller reset.
CONTROLLER LOGS
The controller has an internal alarm and event log.
The logs can be accessed via the S3software
configuration ports (Configuration Port or Port 3) using
a RS-232 serial cable and a Windows™computer.
The controller can save up to 4,095 alarms and events
in the controller memory.
CONTROLLER USER LOGIC
The Controller continuously executes the user logic
programs that are programmed using S3software.
The user logic programs are set up in the same
fashion as IEC 61131-3 programmable logic
programmed into Programmable Logic Controllers
(PLCs). Block diagram logic gates are tied together
with inputs, outputs, and other logic gates to perform
a specific task. A number of tasks can be tied
together to perform a system function.
Typical programmed functions include flame/gas
voting, timing delays, timing executions, latching
conditions, alarm and trouble notification, suppression
control, condition control, and process shutdown
notification.
The Controller executes program logic by starting with
the first logic page of the first program and then
progressing onto subsequent pages of the same
program. In turn, subsequent programs are then
executed.
Every one hundred milliseconds, the Controller will
start executing the user logic that is programmed into
the Controller. Within this logic execution cycle, the
Controller will execute as many of the logic pages as
possible. If all programmed logic is executed in a
cycle, the Controller will start executing program logic
with the next cycle. Otherwise, subsequence logic
execution cycles are used to finish executing the
remaining logic gates. Only when all the logic gates
have been executed will the Controller start over. The
Controller will start executing the first logic page of
the first program at the beginning of the next logic
cycle.
COMMUNICATION NETWORK FAULT OPERATION
During normal operation, the Controller is continuously
broadcasting a heartbeat around the communication
loop as shown in Figure 2-2. The Controller
broadcasts the heartbeat in both directions. At the
same time, the field devices are transmitting status
information to the Controller over the communication
loop.
Every field device except the network extender has
two LON fault isolation relays. Each relay is tied to a
communication port on the device. When a field
device fails to receive the heartbeat from the
Controller, the device initiates a LON fault isolation
routine. The isolation routine disconnects one of the
communication ports via one of the LON fault isolation
relays. The device listens for a heartbeat on the
communication port that is connected. If a heartbeat
is not found, the routine then disconnects the other
communication port and listens for a heartbeat on the
connected side. The process is repeated until either
a heartbeat is located or a LON fault timeout period of
two hours is reached. The LON fault isolation routine
is disabled and the LON fault isolation relays are
closed when the LON fault timeout period has
elapsed. The LON fault isolation routine will be
enabled when the device again receives a heartbeat.
For a single wiring fault, the field devices with the fault
will isolate the fault by opening LON fault isolation
relays. After the field devices isolate the wiring fault,
communications will be resumed between the
Controller and field devices. Refer to Figure 2-3.
Figure 2-2—Normal Communication over the LON
Figure 2-3—Communication over the LON with a Single Wiring Fault
D1851
NODE 1 NODE 8
NODE 3 NODE 6
NODE 2 NODE 7
NODE 4 NODE 5
EQP
CONTROLLER
EAGLE QUANTUM PREMIER
Safety System Controller
DE T-TRON IC S
D1852
NODE 1 NODE 8
NODE 3 NODE 6
NODE 2 NODE 7
NODE 4 NODE 5
PATH A PATH B
WIRING FAULT
EQP
CONTROLLER
EAGLE QUANTUM PREMIER
Safety System Controller
DE T-TRON IC S

7.1 95-85332-5
MULTIPLE WIRING FAULTS
In the event of multiple wiring faults on the LON, the
devices between the faults will continue to function,
but the faults will prevent them from communicating
with the Controller. See Figure 2-4. In this example,
nodes 1 to 4 communicate using one Controller port
(path A) and nodes 7 and 8 use the other Controller
port (path B). Nodes 5 and 6 are unable to report to
the Controller because they are isolated by the two
wiring faults. If a device is prevented from
communicating with the Controller, the text display on
the Controller will show the message “Device Offline”.
IMPORTANT!
Since it is impossible to predict where a network
fault might occur or exactly what effect it will
have on actual system operation, it is important
to diagnose and repair any fault as soon as
possible after it is detected to ensure continuous,
uninterrupted system operation.
MAJOR COMPONENT DESCRIPTIONS
The system has three (3) main component groups —
the System Controller, LON (Local Operating
Network), and Intelligent Field Devices.
SYSTEM CONTROLLER
The Controller (see Figure 2-5) performs all
communication, command, and control functions for
the system. The Controller supports both “Static” and
“Programmable” logic. Other features include:
• Redundant controller capability
• User pushbutton controls (reset, acknowledge, etc.)
• “Real time” system clock
• Internal alarm sounder
• Vacuum fluorescent text based display that shows
current system status
• 8 programmable unsupervised inputs
• 8 programmable unsupervised relay outputs
• RS-485 Modbus RTU communication interface that
supports coils, discrete inputs, and holding
registers
• Optional ControlNet communication board that
supports redundant communication channels.
• Optional Serial Interface Board (required for
controller redundancy).
Figure 2-5—System Controller
Controller Redundancy
The EQP controllers can be configured as a redundant
pair. See Figure 2-6. The redundancy scheme is a hot
standby system that offers the following primary
features:
• Automatic configuration of the standby controller
• Bumpless transfer
• Forced and automatic switchover
• No downtime on controller replacement
• Automatic synchronization between controllers
• Increased system availability
Figure 2-4—Communication over LON with Multiple Wiring Faults
D1853
NODE 1 NODE 8
NODE 3 NODE 6
NODE 2 NODE 7
NODE 4 NODE 5
PATH A PATH B
WIRING FAULTS
EQP
CONTROLLER
EAGLE QUANTUM PREMIER
Safety System Controller
DE T-TRON IC S
LON
S3
CONFIGURATION
SOFTWARE
ONE PROJECT FILE
LOADED TO
CONTROLLER A
CONTROLLER A
LON ADDRESS 1
CONTROLLER B
LON ADDRESS 2
DCS/PLC/HMI
HIGH SPEED
RS-232
SERIAL LINK
RS-232
SERIAL LINK
MODBUS
RS-485
A2275
Figure 2-6— Block Diagram of EQP System
with Redundant Controllers

7.1 95-85332-6
During normal operation one controller acts as the
“Master” while the other acts as the “Hot Standby”.
Terminology used for redundancy:
Master controller This is the normal mode for
non-redundant and master
controllers. User logic is
executed, outputs are being
controlled and all serial ports
are active.
Standby controller This controller is receiving all
inputs but does not have any
control over the outputs and
user logic is not executed. The
standby controller receives
update information from the
master controller to ensure a
bumpless transfer should a
controller switchover occur.
Primary controller The controller assigned
address 1.
Secondary controller The controller assigned
address 2.
Bumpless transfer During a controller switchover
no change in output will occur
due to the switchover.
Serial Interface Board
An optional serial board is available that supports up
to four additional serial ports. See Table 2-4. For a
redundant controller configuration, the board is
required in both controllers.
Controller-to-Controller Communication (SLC485)
The EQP controllers can be configured to
communicate with up to 12 controllers via RS-485
communication. The controller-to-controller scheme
provides the ability to meet NFPA 72 SLC requirements
with the following primary features:
• Modular trouble and alarm configuration
• Multiple zone application with controller-to-controller
communication
• Multiple media options.
EQP Supervising System (EQPSS)
The Det-Tronics EQP controllers can be supervised
via the EQPSS using PCs and HMI. Each EQPSS PC
can communicate with up to 12 EQP controllers over
an Ethernet. This is a Det-Tronics solution. Please
consult the factory for more information.
EQP Marine Application System
For information regarding EQP Marine Application
Systems, refer to Appendix D.
LOCAL OPERATING NETWORK (LON)
The LON is a fault tolerant, two wire, digital
communication network. The circuit is arranged in a
loop starting and ending at the Controller. The circuit
supports up to 246 intelligent field devices spread
over a distance of up to 10,000 meters (32,500 feet).
NOTE
All LON devices support ANSI/NFPA 72 Class A,
Style 7 communication with the Controller.
Network Extenders
Transmitted signals can travel a maximum distance of
2,000 meters through LON communication wire. At
the end of this distance, a network extender (see
Figure 2-7) must be installed to rebroadcast the
communications into the next wire segment. For
every network extender added, the length of the
communications loop extends up to 2,000 meters.
Due to propagation delays around the loop, the
maximum loop length is limited to 10,000 meters.
NOTES
A n e t w o r k e x te n d e r i s r e q u i r e d f o r
communication loops greater than 60 nodes.
Port Name Comm Function
Serial Port 2 RS485 ModBus (Master/Slave)
Ground Fault Monitored,
Isolated
Serial Port 3 RS232 ModBus (Master/Slave)
S3 Conguration
Serial Port 4 RS232 ModBus (Master/Slave)
HSSL Redundancy RS232 Redundant Controller to
Port Controller Only
Table 2-4—Ports on Optional Serial Interface Board

7.1 95-85332-7
Communication wire segment lengths are
dependant upon physical and electrical
characteristics of the cable. Refer to the
installation section for LON cable wire
information.
No more than six network extenders may be
used on the communication loop.
When a network extender is installed in the
communication loop, up to 40 eld devices can
be installed per network segment. The network
segment is the wiring segment between two
network extenders or between a network
extender and a controller.
EQ21xxPS Series Power Supplies and
EQ2100PSM Power Supply Monitor
The Power Supply, Power Supply Monitor, and backup
batteries are used to provide power to the system.
The power supply monitor communicates trouble
conditions to the Controller. Monitored status
conditions include: power supply failure, loss of AC
power, loss of battery power, power ground fault, AC
and DC voltage (hi/low level), and backup battery
current charge levels.
EQ211xPS, EQ213xPS and EQ217xPS Power
Supplies
The Power Supply provides main and backup power
to the EQP System. The device includes many
features such as voltage regulation, high efficiency,
and high power factor.
An equalize switch is located on the front panel of the
charger for manual activation, or a multi-mode
electronic timer can be used for automatic activation.
Steady state output voltage remains within +/– 1/2%
of the setting from no load to full load for AC input
voltages within +/– 10% of the nominal input voltage.
EQ2220GFM Ground Fault Monitor
The EQ2220GFM Ground Fault Monitor (see Figure
2-8) provides ground fault monitoring in a system that
includes a floating 24 Vdc power source. The device
detects ground fault conditions on +/– power and all
secondary I/O circuits. A positive or negative ground
fault condition is indicated immediately by local
LEDs, and by a relay contact after a 10 second time
delay. The ground fault monitor is intended to be
mounted in the same enclosure as the controller.
FIELD DEVICES
Flame Detectors
For flame detector installation, operation,
maintenance, specifications and ordering information,
refer to Table 2-5.
For information regarding USCG Approval of the
X3301 Flame Detector, refer to Appendix D.
Table 2-5—Flame Detector Manuals
Detector Manual Number
X3301 95-8527
X3301A 95-8527 & 95-8534
X3302 95-8576
X5200 95-8546
X2200 95-8549
X9800 95-8554
UVHT 95-8570
Figure 2-8—Ground Fault Monitor
Figure 2-7—Eagle Quantum Premier Network Extender

7.1 95-85332-8
EQ3730EDIO Enhanced Discrete Input/Output Module
The 8 Channel EDIO Module (see Figure 2-9) expands
the Input and Output capability of the Eagle Quantum
Premier System.
The unit is designed to provide continuous and
automated fire/gas protection, while ensuring system
operation through continuous supervision of System
Inputs/Outputs.
The EDIO module provides eight channels of
configurable input or output points that can be
programmed for supervised or unsupervised
operation. Each input point can accept fire detection
devices such as heat, smoke, or unitized flame
detectors. Each output point can be configured for
signaling or releasing output operation. Each channel
on the module is provided with individual indicators
for active and fault conditions.
important
For Class A wiring, two input/output channels are
combined, thereby supporting up to four input/
output circuits.
NOTE
An input must be active for at least 750
milliseconds in order to be recognized.
The EDIO module can be mounted directly to a panel,
or it can be DIN rail mounted. System status can be
determined using the trouble-shooting procedures,
Eagle Quantum Safety System Software (S3) and the
status indicators on the module.
Refer to the Enhanced Discrete Input/Output Module
Specification Data sheet (form number 90-1189) for
additional information.
EQ3700 8 Channel DCIO Module
The 8 Channel Discrete Input/Output (DCIO) Module
(see Figure 2-10) consists of eight individually
configured channels. Each channel is configured as
either an input or output with the appropriate wiring
supervision. Wiring supervision includes none, open
circuits, and "open and short" circuits. In addition to
defining the type of supervision, an input channel is
also configured to generate the appropriate static
logic alarm message to the controller.
NOTE
NFPA 72 requires wire supervision selection for
re detection and notication devices (IDC, NAC,
supervisory and releasing devices).
Heat, smoke, or unitized flame detectors can be wired
into channels defined as inputs. Horns, strobes/
beacons, and solenoids can be wired into channels
defined as outputs.
NOTE
The DCIO outputs only support equipment that
operates on 24 vdc (not to exceed 2 amperes
per channel).
The DCIO has two device status LEDs, as well as two
LEDs for each channel. On the device level, one
green LED indicates power, while the other amber
LED indicates a LON CPU fault. For each channel,
one red LED indicates channel activation and the
other amber LED indicates a fault condition when
wiring supervision is defined for the channel.
Refer to the DCIO Specification Data sheet (form
number 90-1149) for additional information.
Figure 2-10—DCIO Module
Figure 2-9—Enhanced Discrete Input/Output Module

7.1 95-85332-9
EQ3720 8 Channel Relay Module
The 8 Channel Relay Module (see Figure 2-11)
consists of eight individually configured output
channels.
NOTE
The relay module only supports equipment that
operates on 24 vdc (not to exceed 2 amperes) at
each output channel.
The relay module has two LEDs for the device and
two LEDs for each channel. On the device level, one
green LED indicates power, while the other amber
LED indicates a LON CPU fault. For each channel,
one red LED indicates channel activation and the
other amber LED indicates that the module operating
voltage is low or that the module has not been
configured (all eight channel LEDs blink).
Refer to the Relay Module Specification Data sheet
(form number 90-1181) for additional information.
EQ3710AIM Analog Input Module
The 8 Channel Analog Input Module (see Figure 2-12)
provides a means of connecting devices with a
calibrated 4-20 mA output signal to the Eagle
Quantum Premier System.
The Analog Input Module (AIM) provides 8
configurable channels that can be set for either
combustible gas mode or universal mode. The
combustible gas mode provides a number of
automatically programmed settings, and alarm
thresholds that are limited to approval body
requirements. The universal mode is used for generic
devices where control over all configuration
parameters is required. All devices must provided
their own calibration facilities.
For fire detector 4-20 mA inputs, the Analog Input
Module (AIM) is certified for use as an NFPA 72 Class
B, Style B Approved input.
Refer to the Analog Input Module Specification Data
sheet (form number 90-1183) for additional
information.
Figure 2-12—Eight Channel Analog Input Module
Figure 2-11—Eight Channel Relay Module

7.1 95-85332-10
EQ3740IPM Intelligent Protection Module
The IPM
(see Figure 2-13)
is designed to provide
continuous and automated local area fire protection,
while monitoring system operation through continuous
supervision of its Inputs/Outputs and Local Operating
Network/Signalling Line Circuit (LON/SLC) connection to
the EQP controller.
In addition the module contains a unique “embedded
logic program” that if enabled during configuration
allows the IPM to perform local area protection in a
“back-up mode” without controller interaction.
The IPM utilizes eight pre-configured Input/Output (I/O)
channels to perform its monitoring, supervison and
mitigation functions.
On the input side, three supervised channels provide
connections for an Abort station, a Manual Release
station and a Supervisory device. Two additional input
channels (zones) provide connections for “two-wire”
conventional (non-relay based) smoke and heat
detectors.
On the output side, three supervised outputs provide
connections for a notification appliance such as a
bell, horn or lamp and two releasing circuits for a main
and reserve or secondary agent release.
Each channel on the module is provided with
individual indicators for active and fault conditions.
Refer to the Intelligent Protection Module Specification
Data sheet (form number 90-1184) for additional
information.
EQ25xxARM Agent Release Module
The EQ25xxARM Series Agent Release Module (ARM)
(see Figure 2-14) provides agent release or deluge
pre-action capability. The device is controlled by
programmable logic in the Controller. Time delay,
abort and manual release sequences allow the device
output to be programmed for use in unique
applications.
The device is field programmed to operate in one of
the following modes:
Squib– Output is activated for a factory-set
time period to set off the explosive
device.
Timed– Output is activated for a field
selectable duration from 1 to 65,000
seconds.
Continuous– Output latches until reset.
Non-latching– Output follows the input.
The device can monitor and control two output
devices (24 vdc rated) that are programmed and
energized together. The release circuits are
compatible with a variety of solenoid or initiator
(squib) based suppression systems.
The release circuit is supervised for open circuit
conditions. If a trouble condition occurs (open circuit
or solenoid supply voltage less than 19 volts), it will
be indicated at the Controller. Each output is rated at
2 amperes and auxiliary input terminals are provided
for additional 24 vdc output power where needed.
NOTE
For deluge and pre-action applications, the input
voltage to the ARM or DCIO must be 21 VDC
minimum with connection to any solenoid listed
in Table 2-6 or 2-7. Wiring must be in accordance
with the listed maximum wiring lengths.
Refer to the EQ25xxARM Specification Data sheet
(form number 90-1128) for additional information
Figure 2-13—Intelligent Protection Module

7.1 95-85332-11
EQ25xxSAM Signal Audible Module
The EQ25xxSAM Series Signal Audible Module (SAM)
(see Figure 2-15) provides two indicating circuits for
controlling UL Listed 24 vdc polarized audible/visual
indicating appliances.
The device is located on the LON and is controlled by
programmable logic in the Controller.
Each output circuit is independently programmable to
allow notification of separate events. Each output can
be individually activated for any one of the following
pre-defined outputs:
1. Continuous
2. 60 beats per minute
3. 120 beats per minute
4. Temporal pattern.
Device outputs operate in the reverse polarity manner
when activated. Each output is rated at 2 amperes.
Auxiliary power input terminals are provided for
additional 24 vdc signaling power where required.
The output circuits are supervised for open and short
circuit conditions. If a wiring fault occurs, a trouble
condition will be indicated at the Controller.
Refer to the EQ25xxSAM Specification Data sheet
(form number 90-1129) for additional information
Figure 2-15—Signal Audible Module
Table 2-7—Maximum Wiring Length for FM Approved Solenoids for Deluge and Pre-Action Applications
Solenoids Maximum Wire Length in Feet (Meters)
FM Solenoid Group Manufacturer Model 12 AWG 14 AWG 16 AWG 18 AWG
B ASCO T8210A107 183 (56) 115 (35) 72 (22) 46 (14)
D ASCO 8210G207 314 (96) 198 (60) 124 (38) 78 (24)
E Skinner 73218BN4UNLVNOC111C2 331 (101) 208 (63) 131 (40) 82 (25)
F Skinner 73212BN4TNLVNOC322C2 130 (40) 82 (25) 51 (16) 32 (10)
G Skinner 71395SN2ENJ1NOH111C2 331 (101) 208 (63) 131 (40) 82 (25)
H Viking HV-274-0601 180 (55) 110 (34) 70 (21) 45(14)
Table 2-6—Solenoid Compatibility with Agent Release Module
for Deluge and Pre-Action Applications
FM Group Device
B ASCO T8210A107
D ASCO 8210G207
E Skinner 73218BN4UNLVNOC111C2
F Skinner 73212BN4TNLVNOC322C2
G Skinner 71395SN2ENJ1NOH111C2
H Viking HV-274-0601
Figure 2-14—Agent Release Module

7.1 95-85332-12
EQ22xxIDC Series Initiating Device Circuit (IDC)
There are three IDC models available (see Figure 2-16):
The EQ22xxIDC allows discrete inputs from smoke/
heat detectors, manual call stations or other contact
devices.
The IDC accepts two dry contact inputs for use with
devices such as relays, pushbuttons, key switches,
etc. The IDC supports ANSI/NFPA 72 Class B, Style B
supervised input circuits
Each circuit requires its own end of line (EOL) resistor
for monitoring circuit continuity. Nominal resistance of
the resistor is 10 k ohms.
The EQ22xxIDCGF Initiating Device Circuit Ground
Fault Monitor (IDCGF) responds to the presence of a
ground fault within the power circuitry of the system.
It provides an unsupervised dry contact input and
ground fault monitoring circuitry for indicating a power
supply trouble condition. It is intended for use with a
third party power supply.
The EQ22xxIDCSC Initiating Device Circuit Short
Circuit (IDCSC) is similar to the IDC, but supports
ANSI/NFPA 72 Class B Style C supervised input
circuits. (Not FM Approved.)
Refer to the EQ22xxIDC Specification Data sheet
(form number 90-1121) for additional information.
Figure 2-16—Initiating Device Circuit
NOTE
Input types (e.g. fire alarm, trouble, and gas
alarms) are configurable through Det-Tronics
Safety System Software (S3).
EQ22xxDCU and EQ22xxDCUEX
Digital Communication Units
The EQ22xxDCU Digital Communication Unit (DCU) is
an analog signal input device that accepts a 4 to 20
milliampere signal. The device is typically connected
to gas detectors, where the analog signal represents
the gas concentration.
Calibration of the DCU involves a non-intrusive
procedure that can be performed by one person at
the device without declassifying the area.
The device supports two alarm setpoints that are
defined as part of the device’s configuration setup.
When detecting combustible gases, the alarm
setpoints represent low and high gas alarm levels.
When detecting oxygen, the alarms represent the
range for the acceptable oxygen level. If oxygen
drops below the alarm range, a low alarm is
generated by the device.
PointWatch/DuctWatch IR gas detector as well as
electrochemical sensors (hydrogen sulfide, carbon
monoxide, chlorine, sulfur dioxide, and nitrogen
dioxide) are examples of devices that can be
connected to the DCU.
NOTE
A catalytic sensor can be connected to a DCU
through a transmitter, which converts the millivolt
signal to a 4 to 20 milliampere signal.
The EQ22xxDCUEX is a specialized version of the
DCU that contains a transmitter for connection to a
Det-Tronics Model CGS catalytic combustible gas
sensor.
Refer to the EQ22xxDCU Specification Data sheet
(form number 90-1118) for additional information.
PIRECL PointWatch Eclipse
For PIRECL installation, operation, maintenance,
specifications and ordering information, refer to form
number 95-8526.
NOTE
The low alarm range for the EQP PIRECL is
5-40% LFL (the standard PIRECL is 5-60% LFL).
For information regarding USCG Approval of the
PIRECL Detector, refer to Appendix D.
OPECL Open Path Eclipse
For OPECL installation, operation, maintenance,
specifications and ordering information, refer to form
number 95-8556.

3-17.1 95-8533
Section 3
Installation
SAFETY SYSTEM DESIGN
REQUIREMENTS
Many factors need to be considered when
determining proper EQP System design. The following
paragraphs will discuss these factors and other issues
useful in designing, installing and configuring the
Eagle Quantum Premier System.
IDENTIFYING THE AREA OF PROTECTION
In order for the system to provide optimum coverage
and protection, it is critical to properly define the
required “Area of Protection” (total area being
monitored by the system). The area of protection
should include all hazard sources requiring
monitoring, as well as suitable locations for mounting
detection, extinguishing, notification, and manual
devices. In order to accurately define the area of
protection and provide maximum protection, all
potential “Real” and “False” hazard sources must be
identified. The number and location of Real Hazards
determines the extent of the area of protection, and
impacts all subsequent design decisions.
WARNING!
When drilling through surfaces in the process of
mounting equipment, verify that the location is
free of electrical wiring and electrical
components.
IDENTIFYING WIRING, NETWORK (LON), AND
SYSTEM POWER REQUIREMENTS
General Wiring Requirements
WARNING!
DO NOT open any junction box or device
enclosure when power is applied without rst
de-classifying the hazardous area.
CAUTION!
Any deviation from the manufacturer’s
recommended wiring practices can compromise
system operation and effectiveness. ALWAYS
consult the factory if different wire types or
methods are being considered.
NOTE
All eld wiring must be marked per NFPA 70
Article 760.
NOTE
Specific installation requirements may differ
depending on local installation practices and
compliance with third party certications. For
local installation practices, consult the local
authority having jurisdiction. For compliance
with third party certifications, consult the
appropriate appendix in this manual for
additional installation requirements.
Power Wiring
IMPORTANT!
For deluge and pre-action applications, input
voltage to the DCIO or ARM must be 21 vdc
minimum to ensure proper operation of the
connected output device.
IMPORTANT
To ensure proper operation of eld devices, the
voltage input to the device (measured at the
device) must be within the range indicated for
that device in the “Specications” section of this
manual (18 Vdc minimum).

7.1 3-2 95-8533
The Eagle Quantum Premier system utilizes a power
supply that provides an isolated 24 vdc battery
backed-up power to the fire protection devices as
described in NFPA 72. More than one power supply
may be used in a system to provide power to different
sets of equipment as part of the system.
The power supply wiring may consist of one or more
daisy-chained wire segments providing power to the
devices. For each of the daisy-chained wire
segments, the installer must calculate the voltage
drops that occur across the devices in order to
determine the gauge of the wire that will be installed.
A power supply wiring diagram should contain
information describing wire distances and current
draws associated with all devices connected to the
wire segment. A typical power supply wiring
recommendation is that the voltage drop from the
power source to the end device should not exceed
ten percent. Using 24 vdc as a reference, the
maximum voltage drop should not exceed 2.4 vdc. A
wire gauge must be selected to ensure that the end
device has at least 21.6 vdc or higher.
In order to calculate the power supply voltage for the
end device, calculate the voltage drops that occur
due to each wire segment between the devices. This
involves determining the total current draw and the
two conductor wire resistance per each wire segment.
Example:
Can 18 AWG wire be used to power three devices
from the 24 vdc power supply? Refer to the figure
below for wiring and device current draw information
along with voltage drop calculations.
Answer: If the Authority Having Jurisdiction (AHJ)
requires a voltage loss of 10% or less, only 16 AWG
wire could be used, since the end device would
require 21.4 vdc. If there is no local requirement, then
18 AWG wire could be used to provide power to the
devices.
Device 1
65 mA
Current Draw
Device 2
65 mA
Current Draw
Device 3
565 mA
Current Draw
24 vdc Power
Supply
18 AWG Single Wire Resistance: R = 0.6385 Ohms per 100 ft
2 Conductor Resistance: CR = 2 • R
Device 1 Voltage = Supply Voltage – (Voltage Drop)
= 24 – (I • CR)
= 24 – (0.695 • 0.6385)
= 23.55 vdc
Device 2 Voltage = Device 1 Voltage – (Voltage Drop)
= 23.55 – (I • CR)
= 23.55 – (0.630 • 1.9155)
= 22.35 vdc
Device 3 Voltage = Device 2 Voltage – (Voltage Drop)
= 22.35 – (I • CR)
= 22.35 – (0.565 • 1.9155)
= 21.27 vdc
50 ft
0.6385 Ohms
150 ft
1.9155 Ohms
150 ft
1.9155 Ohms
Total Current
695 mA
Total Current
630 mA
=
Device 2
+
Device 3
Total Current
565 mA
=
Device 3
Table of contents
Other UTC Fire and Security Controllers manuals
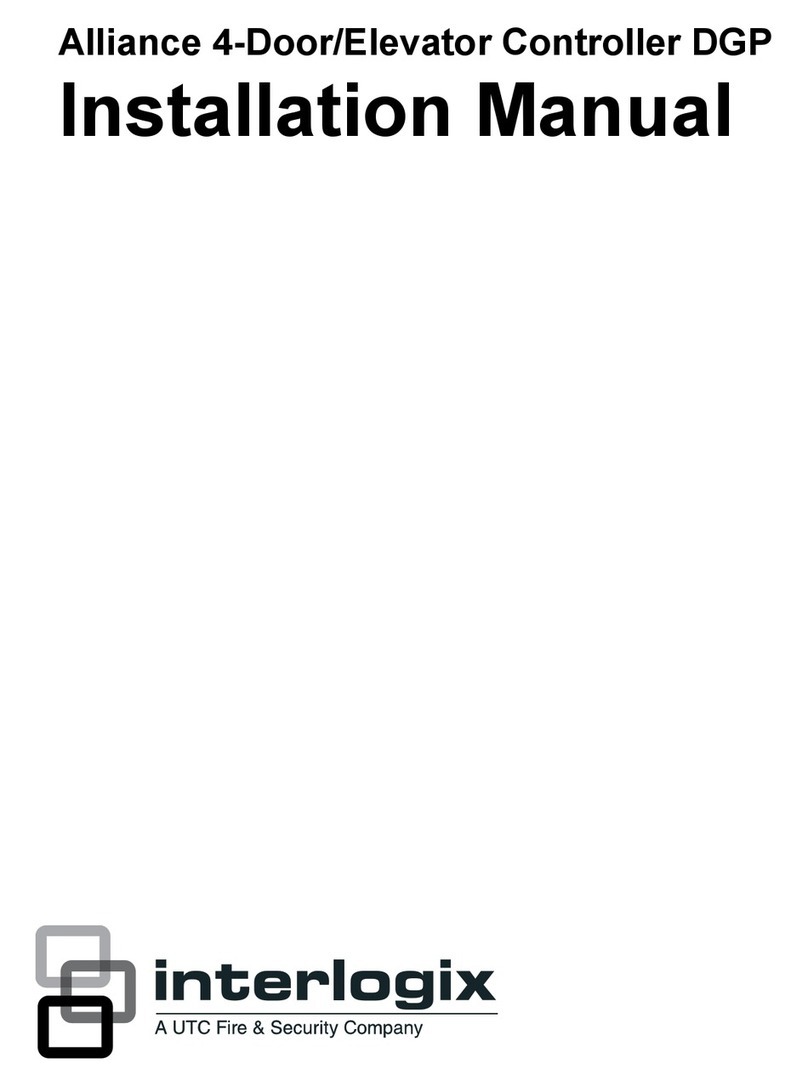
UTC Fire and Security
UTC Fire and Security interlogix AL-1255 User manual
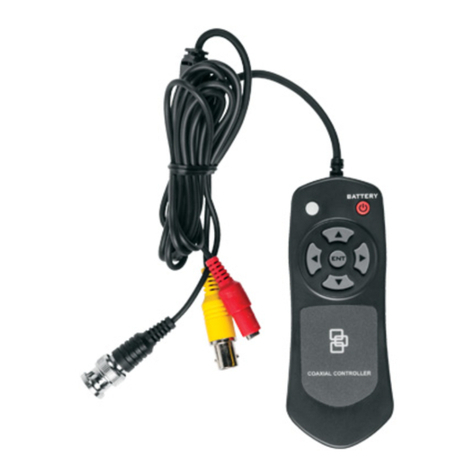
UTC Fire and Security
UTC Fire and Security TruVision TVS-C100 User manual
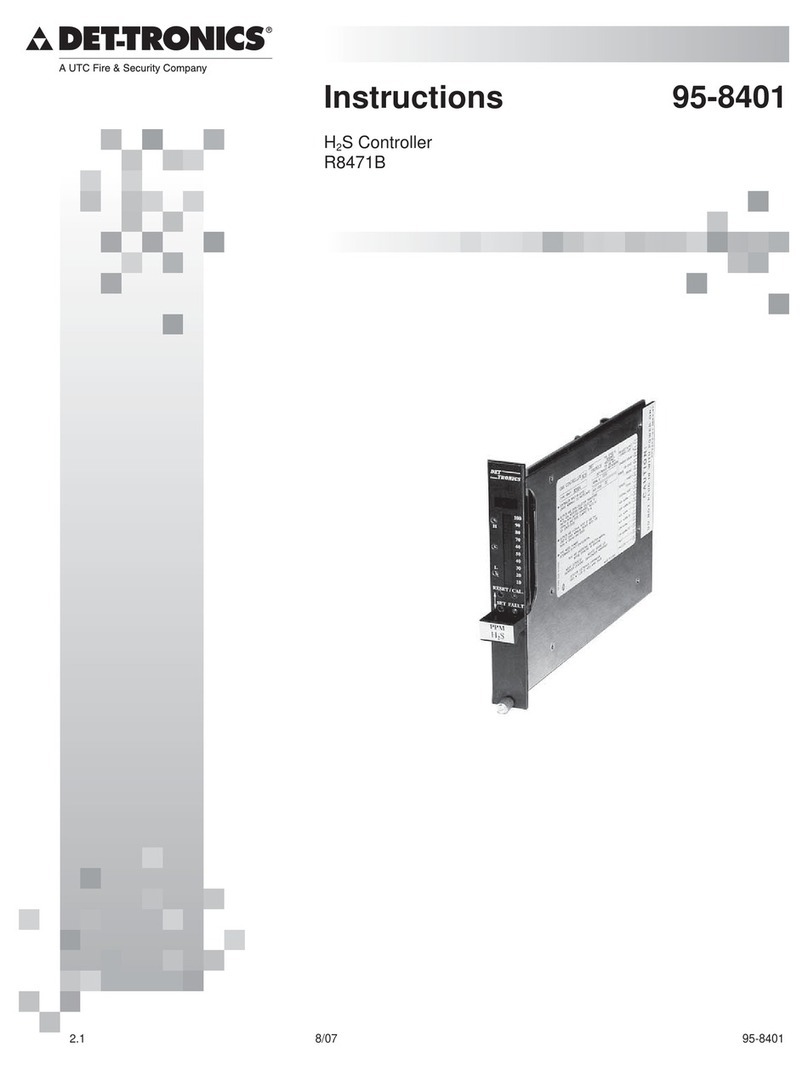
UTC Fire and Security
UTC Fire and Security Det-Tronics R8471B User manual
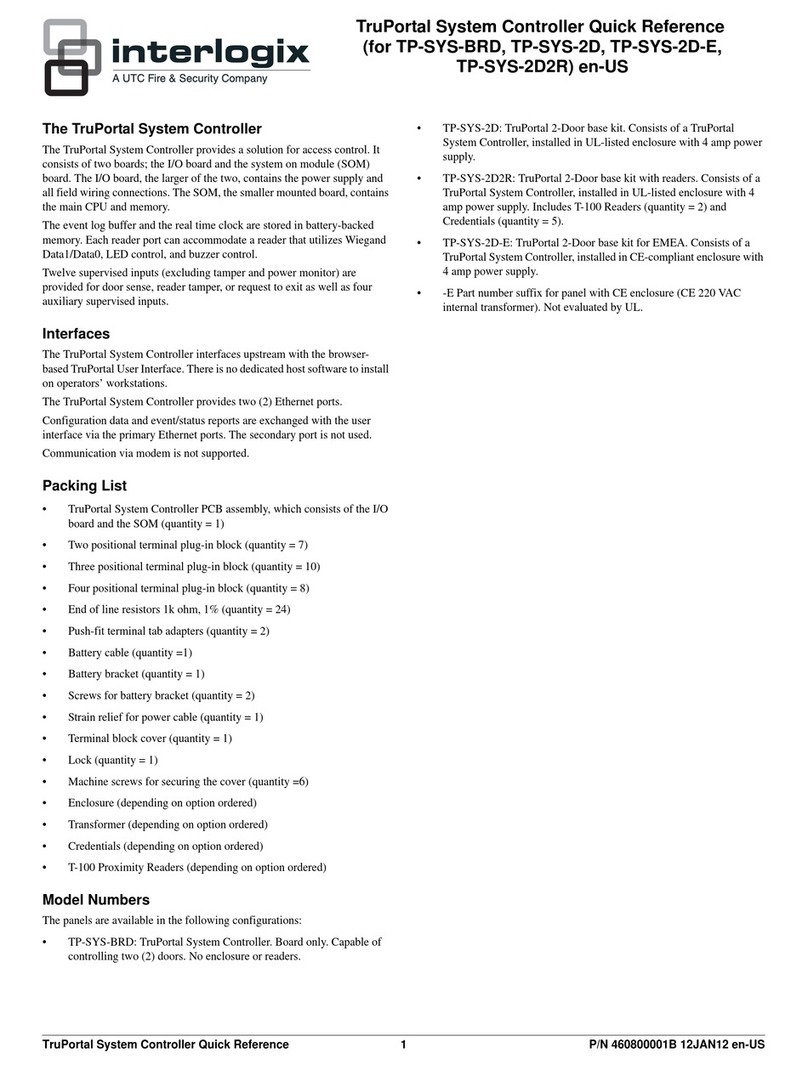
UTC Fire and Security
UTC Fire and Security Interlogix TruPortal TP-SYS-BRD User manual
Popular Controllers manuals by other brands
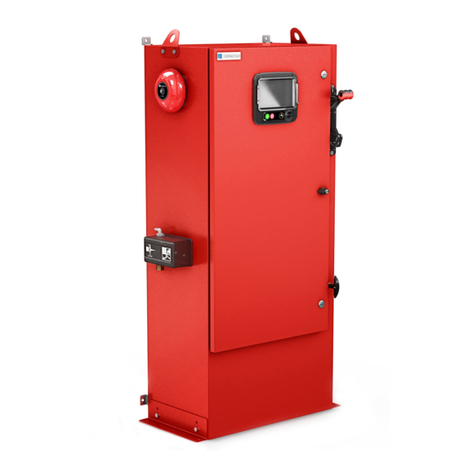
Tornatech
Tornatech GPX Installation and maintenance manual

Burkert
Burkert 8025 Series installation manual
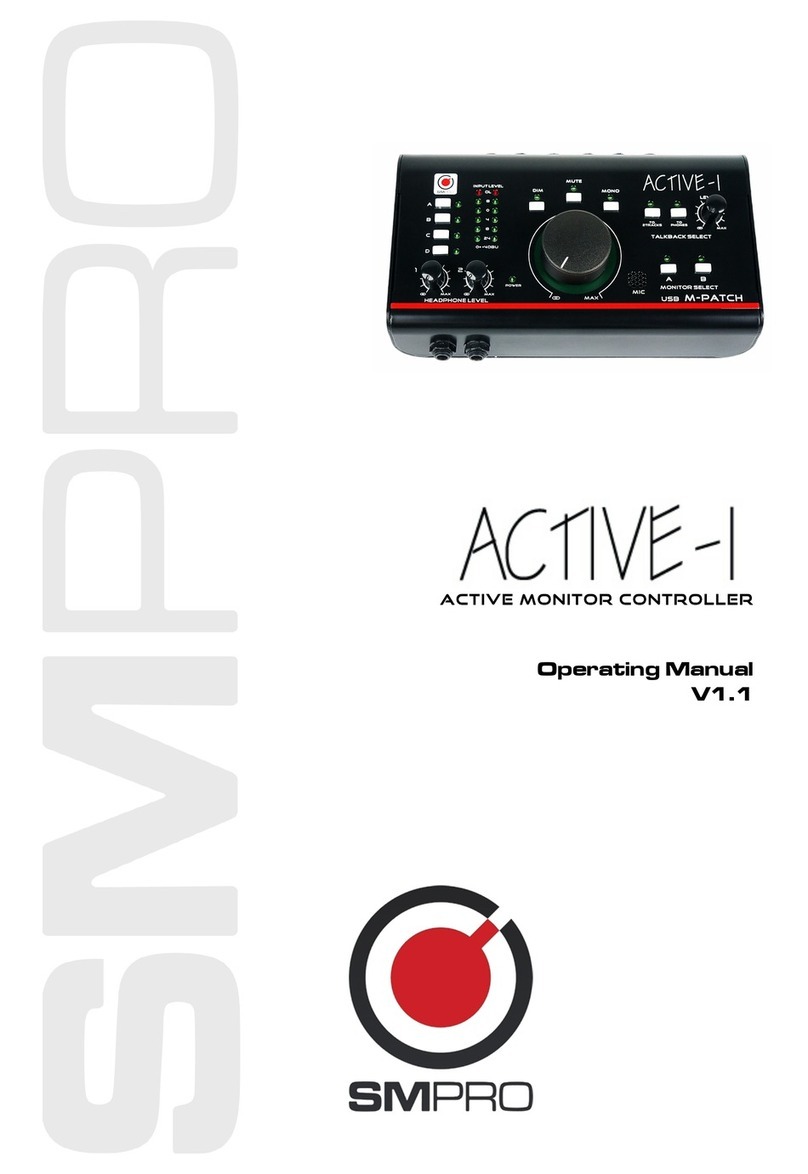
SM Pro
SM Pro Active-1 operating manual
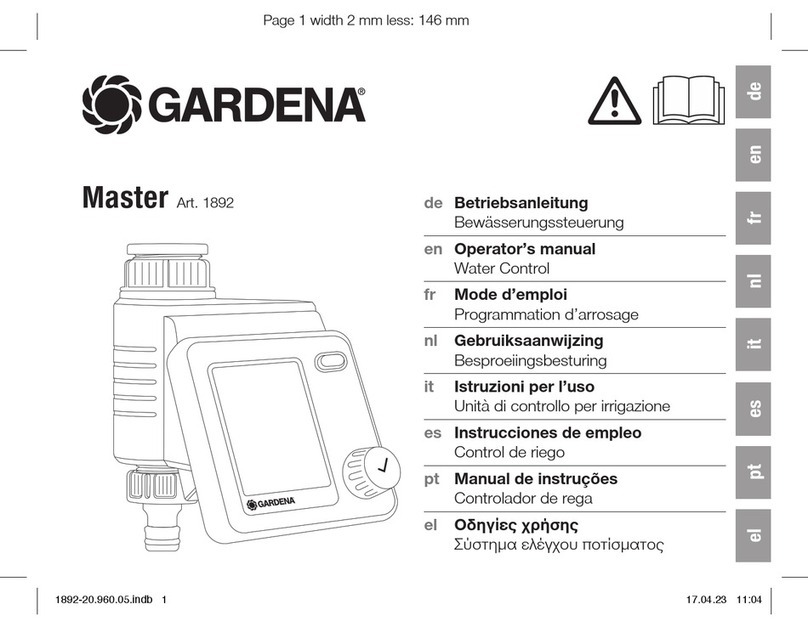
Gardena
Gardena 1892 Operator's manual

DEEP SEA ELECTRONICS
DEEP SEA ELECTRONICS DSEM840 Operator's manual
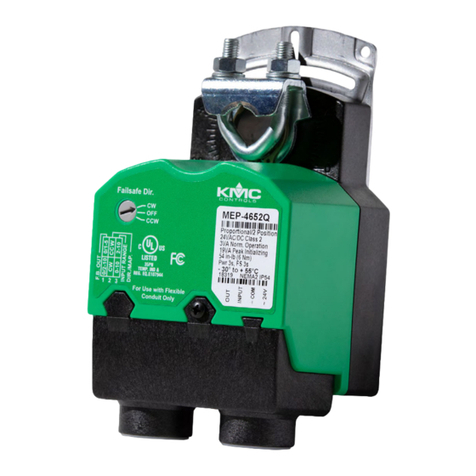
KMC Controls
KMC Controls MEP-46 Q Series quick start guide