Tornatech GPX Manual

1
INSTALLATION AND MAINTENANCE MANUAL FOR
ELECTRIC FIRE PUMP CONTROLLERS
WITH TRANSFER SWITCH
MODEL GPX + GPU

2
GPXGPUV2-Manual-EN v2.2.0.0
Table of Contents
1. Introduction
2. Installation
3. Main Features
4. Home
5. Alarms
6. Configuration
7. History
8. Service
9. Download Manuals
10. Language
11. Technical Documents

3
Table of Contents
Introduction......................................................................................................................................................................5
Types of Electric Fire Pump Controllers ....................................................................................................................5
Types of Automatic Transfer Switch..........................................................................................................................6
Methods of Starting/Stopping.....................................................................................................................................6
Transfer switch operation Sequence .........................................................................................................................7
Manual Operation of the Transfer Switch ..................................................................................................................8
Installation.......................................................................................................................................................................9
FCC Regulations and Radio Standards Specification (RSS) Rules..........................................................................9
Location......................................................................................................................................................................9
Mounting ..................................................................................................................................................................10
Storage.....................................................................................................................................................................10
Wiring and Connections...........................................................................................................................................10
Water Connections...................................................................................................................................................10
Electrical Wiring .......................................................................................................................................................10
Electrical Connections..............................................................................................................................................10
Energy Consumption................................................................................................................................................10
Sizing........................................................................................................................................................................10
Incoming Power Connections ..................................................................................................................................11
Motor Connections...................................................................................................................................................11
Terminal Strip Descriptions......................................................................................................................................12
Terminal Strip Descriptions......................................................................................................................................13
Quick Start-Up Guide...............................................................................................................................................14
Main Features ...............................................................................................................................................................21
The ViZiTouch..........................................................................................................................................................21
Alarm Bell.................................................................................................................................................................21
First Setup................................................................................................................................................................21
ViZiTouch: Manual Rebooting Method.....................................................................................................................22
Pressure Transducer Test........................................................................................................................................22
Home.............................................................................................................................................................................23
Home (Menu) ...........................................................................................................................................................23
Screen Saver ...........................................................................................................................................................25
Alarms...........................................................................................................................................................................26
Alarms (Menu)..........................................................................................................................................................26
Configuration.................................................................................................................................................................29
Config (Menu) ..........................................................................................................................................................29
NumPad Page..........................................................................................................................................................30
Date and Time Page................................................................................................................................................30
User Login Page / KeyPad Page .............................................................................................................................31
Advanced Configuration Page .................................................................................................................................32
Control Timers..........................................................................................................................................................32

4
Alarms......................................................................................................................................................................33
Transfer Switch parameters and timers...................................................................................................................34
Sensor Selection......................................................................................................................................................35
Outputs.....................................................................................................................................................................38
Update Program Page .............................................................................................................................................39
Factory Settings .......................................................................................................................................................40
Interlock Lockout......................................................................................................................................................40
Inputs........................................................................................................................................................................41
I/O Card Info.............................................................................................................................................................41
Network....................................................................................................................................................................42
Reboot ViZiTouch ....................................................................................................................................................42
History...........................................................................................................................................................................43
History (Menu)..........................................................................................................................................................43
Events Page.............................................................................................................................................................44
Pressure Curves ......................................................................................................................................................44
Power Curves...........................................................................................................................................................45
Saved Logs ..............................................................................................................................................................46
Pump Curves ...........................................................................................................................................................47
Statistic.....................................................................................................................................................................48
All Time Statistics.....................................................................................................................................................48
First Service Statistics..............................................................................................................................................49
Last Service Statistics..............................................................................................................................................50
Download .................................................................................................................................................................50
Service ..........................................................................................................................................................................51
Service .....................................................................................................................................................................51
Download Manuals........................................................................................................................................................52
Language ......................................................................................................................................................................52
Technical Documents....................................................................................................................................................52

5
Electric fire pump controllers are designed to start an electric motor driven fire pump. It can either start the fire
pump manually through the local start pushbutton or automatically through the sensing of a pressure drop in the
sprinkler system. The fire pump controller is supplied with a pressure transducer. The fire pump can be stopped
manually with the local stop pushbutton or automatically after the expiration of a field programmable timer. In both
cases, stopping is only allowed if all starting causes have disappeared.
Types of Electric Fire Pump Controllers
FIRE PUMP CATALOG NUMBER
MODEL No. EXAMPLE: GPA - 208 / 50 / 3 / 60
Model Prefix: GPA
Voltage: 208 V
HP Rating: 50 HP
Phase: 3
Frequency: 60 Hz
ACROSS-THE-LINE STARTER
MODEL GPA:
This model is intended to be used where the local utility or the capacity of the power source permits across-
the-line starting.
Full voltage is applied to the motor as soon as the controller receives a start command.
REDUCED VOLTAGE STARTERS
These models are intended to be used where the local utility or the capacity of the power source does not permit full
voltage starting.
In all the reduced voltage models, the manual “EMERGENCY RUN” device will initiate across-the-line starting.
MODEL GPP: PART WINDING STARTER
This model requires the use of a motor with two separate windings and 6 power conductors between the
controller and the motor.
Upon a start command, the first winding is connected to the line immediately. The second winding is
connected to the line after a very short time delay.
MODEL GPR: AUTOTRANSFORMER STARTER
This model does not require a multi-connection motor. It only requires 3 conductors between the controller
and the motor.
Upon a start command, an autotransformer is utilized to supply reduced voltage to the motor. After a time
delay, the autotransformer is shunted out and the motor is connected to full voltage by a closed transition
switching sequence.
MODEL GPS: SOLID STATE STARTER
This model does not require a multi-connection motor. It only requires 3 conductors between the controller
and the motor.
Upon a start command, a solid-state starter is utilized to supply a step less ramp-up voltage to the motor
until the motor reaches its full speed. At that time, a fully horsepower rated by-pass contactor is energized
connecting the motor directly to full voltage and eliminating all heat loss within the solid-state starter.
This controller also features a soft motor stopping mode and a hard stop mode. For a hard stop, hold the
stop pushbutton until the motor stop.
Introduction

6
MODEL GPV: ACCELERATION RESISTOR STARTER
This model does not require a multi-connection motor. It only requires 3 conductors between the controller
and the motor.
Upon a start command, a set of acceleration resistors in each phase is utilized to supply a reduced voltage
to the motor. After a time delay, the resistors are shunted out and the motor is connected to full voltage by a
closed transition switching sequence.
MODEL GPW: WYE-DELTA CLOSED TRANSITION STARTER
This model requires a multi-connection motor and 6 conductors between the controller and the motor.
Upon a start command, the motor is connected to the line in the wye connection. After a time delay, the
motor is reconnected to the line in the Delta configuration applying full voltage to the motor windings by a
closed transition switching sequence.
The power source does not « see » any open circuit during the transition from wye to delta. During the
transition from Wye to Delta, a resistor bank is connected in the starting circuit and allows to keep the motor
coils energized. An 80 second delay is then triggered and prevent the motor from stoping. This delay allows
the resistors to cool down and will only be triggered if the transition occur. An emergency stop can still be
perform by pulling the disconnecting mean handle.
MODEL GPY: WYE-DELTA OPEN TRANSITION STARTER
This type of starter requires a multi-connection motor and 6 conductors between the controller and the
motor.
Upon a start command, the motor is connected to the line in the Wye connection. After a time delay, the
motor is reconnected to the line in the Delta configuration applying full voltage to the motor windings. This
controller is of the open transition type. The motor is disconnected from the line during the transition from
start (wye) to run (delta) mode.
Types of Automatic Transfer Switch
TRANSFER SWITCH CATALOG NUMBER
MODEL No. EXAMPLE: GPA+GPU - 480 / 20 / 3 / 60
Model Prefix GPA+GPU
Voltage 480 V
HP Rating 20 HP
Phase 3
Frequency 60 Hz
Methods of Starting/Stopping
The controllers are available as combination automatic / non-automatic with provision for manual or automatic
shutdown (an automatic shutdown is only possible after an automatic start).
METHODS OF STARTING
AUTOMATIC START
The controller will start automatically on low pressure detection by the pressure sensor when the pressure drops
below the cut-in threshold.
MANUAL START
The motor can be started by pressing the START push button, regardless of the system pressure.
REMOTE MANUAL START
The motor can be started from a remote location by momentarily closing a contact of a manual push button.
REMOTE AUTOMATIC START, DELUGE VALVE START
The motor can be started from a remote location by momentarily opening a contact connected to an automatic
device.

7
EMERGENCY START
The motor can be started manually by using the emergency handle. This handle can be maintained in a closed
position.
Important: to avoid damaging the contactor, it is recommended to start the motor in this manner:
1) Shutdown the main power by using the main disconnect means,
2) Pull the emergency handle and lock it in closed position,
3) Turn the power back on by using the main disconnect means.
SEQUENTIAL START
In case of a multiple pump application, it may be necessary to delay the automatic (pressure drop) starting of each
motor to prevent simultaneous starting of all motors.
FLOW START, HIGH ZONE START
The pump can be started by opening/closing a contact on the FLOW/ZONE START/STOP input.
WEEKLY START
The engine can be started (and stopped) automatically at the preprogrammed time.
TEST START
The motor can be started manually by pressing the run test button.
METHODS OF STOPPING
MANUAL STOP
Manual stop is done by pressing the priority STOP push button. Note that pressing the stop push button will
prevent the motor from restarting as long as the button is pressed, plus a two second delay.
AUTOMATIC STOP
Automatic stop is possible only after an automatic start and this function has been activated. When this function is
enabled, the motor is automatically stopped 10 minutes after the restoration of the pressure (above the cut-out
threshold) given that no other run cause is present.
FLOW STOP, HIGH ZONE STOP
If the controller has been started by the FLOW/ZONE START/STOP input and the signal has returned to normal,
the motor will be stopped given that no other run cause is present.
EMERGENCY STOP
The emergency stop is always possible in any starting condition and is done by using the main disconnecting
means located on the door.
Transfer switch operation Sequence
TRANSFER TO ALTERNATE POWER SOURCE
The Transfer to Alternate Power Source starts automatically when at least one of the following conditions are
present:
- Normal Power voltage falls below 85% of nominal voltage,
- Normal Power Phase Reversal is detected,
- Transfer Switch Test push button is pressed.
When an under voltage condition on any phase of the Normal Power source is detected by the sensor, a 3 second
normal power source outage delay timer starts timing.
If the normal source voltage rises above the sensor dropout setting before the 3 second time delay expires, the
transfer sequence is cancelled.
If the Normal Power source voltage is still below the sensor dropout setting (85%) when the time delay expires, a
relay is deactivated sending a signal to start the generator set. At the same time, a voltage and frequency sensor
begins monitoring the Alternate Power Source. The sensor will accept the alternate power source only when both
voltage and frequency reach a pre-set pickup value. An approximate 15 second time span occurs because the
engine-driven generator cranks, starts and runs up to nominal pickup value.

8
When the Alternate Power Source is within acceptable limits (above 90% of the nominal voltage) for a certain set
time (factory set at 3 seconds), the transfer to alternate power source is initiated.
The transfer switch will remain in the alternate power source position until the normal source is restored.
RETRANSFER TO NORMAL
Important: The transfer switch will stay in alternate position, if the motor is running, for as long as the alternate
power source is within acceptable limits. The retransfer sequence is enabled if the motor is not running.
The Retransfer to the Normal Power source starts when the voltage sensor detects restoration of the Normal Power
Source within acceptable limits. The voltage level must rise above the pre-set pickup value (90%) on all phases
before the sensor will accept the normal source.
When the normal source is accepted by the sensor, the retransfer to normal delay timer starts timing (factory set at
5 minutes). This delay can be by-passed by pressing on the count-down timer displayed on the screen (if a flashing
“X” is displayed).
This delay prevents immediate load retransfer to the normal source. The delay insures that the normal power
source has stabilized before reconnection of the Fire Pump Motor. If the normal source voltage falls below the pre-
set dropout value before the time delay expires, the timing cycle is reset to zero. If the alternate power source fails
during the timing cycle, the load is immediately retransferred to the normal source, if that source is acceptable.
The Automatic Transfer Switch is now feeding the Fire Pump Motor from the Normal Power Source again.
Upon retransfer to the normal source, the 5 minute cooling timer starts counting down, keeping the engine running
during this cool-down period. This delay can be by-passed by pressing on the count-down timer displayed on the
screen (if a flashing “X” is displayed).
After the time delay, the relay is re-activated to shut down the engine-driven generator. All circuits are reset for any
future normal source failure.
Every time the transfer switch needs to change from one power source to the other, a running motor is stopped
during the transfer to prevent instant across the line starting of an already turning motor. If the motor still needs to
run when the transfer sequence has completed (plus a factory set 2 second timer), the motor will be restarted
following its default start-up sequence.
Manual Operation of the Transfer Switch
There is 180° between the Normal position (I) and the Alternate position (II). To operate manualy the Transfer
Switch:
1 - Use the Disconnect Switches to turn OFF the power of both Normal and Alternate sides.
2 - Open the door of the Alternate side.
3 - On the Transfer Switch, put the selector switch in Manual mode.
4 - Take the handle, situated inside the controller door and insert it in the square hole on the Transfer Switch.
5 - Turn the handle clockwise 180° to transfer from Alternate to Normal position.
Turn the handle counterclockwise 180° to transfer from Normal to Alternate position.
6 - Remove the handle and put it back on the support inside the controller door.
7 - On the Transfer Switch, put the selector switch in Automatic mode.
8 - Close the door and using the disconnecting switch handles put back the power on both sides.
BE CAREFUL:
- Do not close the controller door if the handle is still installed in the Transfer Switch.
- Do not operate manualy the Transfer Switch if the Normal side power is still ON.
- Do not forget to replace the Transfer Switch in Automatic mode.

9
The GPx electric fire pump controller is cULus listed, FM certified and is intended to be installed in accordance with
the latest edition of the Standard of the National Fire Protection Association for the Installation of Centrifugal Fire
Pumps, NFPA20 2016 (Centrifugal Fire Pumps) and
in the USA, National Electrical Code NFPA 70
in Canada, Canadian Electrical Code, Part 1
others * Local Electrical Codes *
*Only American and Canadian applicable codes have been considered during the design of the controllers and the
selection of components.
Except, in some cases, the controller is also seismic approved and has been tested in accordance with the ICC-ES
AC156, IBC 2015, CBC 2016, OSHPD Special Seismic Certification Preapproval –OSP and ASCE 7-10 Chapter
13 standards. Proper installation, anchoring and mounting is required to validate this compliance report. Refer to
this manual and drawings to determine the seismic mounting requirements and location of the center of gravity (you
may need to contact factory). The equipment manufacturer is not responsible for the specification and performance
of anchorage systems. The structural engineer of record on the project shall be responsible for anchorage details.
The equipment installation contractor shall be responsible for ensuring the requirements specified by the structural
engineer of record are satisfied. If detailed seismic installation calculations are required, please contact the
manufacturer for the performance of this work.
FCC Regulations and Radio Standards Specification (RSS) Rules
To comply with FCC and Industry Canada RF exposure compliance requirements, a separation distance of at least
20 cm must be maintained between the antenna of this device and all nearby persons. This device must not be co-
located or operating in conjunction with any other antenna or transmitter.
This device complies with Industry Canada licence-exempt RSS standard(s). Operation is subject to the following
two conditions: (1) this device may not cause interference, and (2) this device must accept any interference,
including interference that may cause undesired operation of the device.
This device complies with part 15 of the FCC Rules. Operation is subject to the following two conditions: (1) This
device may not cause harmful interference, and (2) this device must accept any interference received, including
interference that may cause undesired operation.
Note: This equipment has been tested and found to comply with the limits for a Class A digital device, pursuant to
part 15 of the FCC Rules. These limits are designed to provide reasonable protection against harmful interference
when the equipment is operated in a commercial environment. This equipment generates, uses, and can radiate
radio frequency energy and, if not installed and used in accordance with the instruction manual, may cause harmful
interference to radio communications. Operation of this equipment in a residential area is likely to cause harmful
interference in which case the user will be required to correct the interference at his own expense.
“Changes or modifications not expressly approved by the party responsible for compliance could void the user's
authority to operate the equipment.”
Location
The controller shall be located as close as practical to the motor it controls and shall be within sight of the motor.
The controller shall be located or protected so that it will not be damaged by water escaping from the pump or pump
connections. Current carrying parts of the controller shall be not less than 12 in. (305 mm) above the floor level.
Working clearances around the controller shall comply with NFPA 70, National Electrical Code, Article 110 or
C22.1, Canadian Electrical Code, Article 26.302 or other local codes.
Installation

10
The controller is suitable for use in locations subject to a moderate degree of moisture, such as a damp basement.
The pump room ambient temperature shall be between 39°F (4°C) and 104°F (40°C).
The standard controller enclosure is rated NEMA 2. It is the installer's responsibility to insure that either the
standard enclosure meets the ambient conditions or that an enclosure with an appropriate rating has been
provided. Controllers must be installed inside a building and they are not designed for outside environment. The
paint color may change if the controller is exposed to ultraviolet rays for a long period of time.
Mounting
The fire pump controller shall be mounted in a substantial manner on a single incombustible supporting structure.
Wall mounted controllers shall be attached to the structure or wall using all four (4) mounting ears provided on the
controller with hardware designed to support the weight of the controller at a height not less than 12 in. (305 mm)
above floor level. Floor mounted controllers shall be attached to the floor using all holes provided on the mounting
feet with hardware designed to support the weight of the controller. The mounting feet provide the necessary 12 in.
(305 mm) clearance for current carrying parts. For seismic applications, the mounting arrangement should be rigid
wall and base only. The structural engineer of record on the project shall be responsible for anchorage details.
Storage
If the controller is not installed and energized immediately, Tornatech recommend following the instructions from the
chapter 3 of the NEMA ICS 15 standard.
Wiring and Connections
Water Connections
The controller must be connected to the pipe system according to the latest edition of NFPA20 and also to a drain
pipe. The water connections are on the left side of the controller. The connection to the system pressure is a Male
½ NPT. If a drain is present, the connection to the drain is a tapered connection for plastic tubing.
Electrical Wiring
The electrical wiring between the power source and the fire pump controller shall meet the latest edition of NFPA
20, NFPA 70 National Electrical Code Article 695 or C22.1 Canadian Electrical Code, Section 32-200 or other local
codes. Electrical wiring shall be typically sized to carry at least 125% of the full load current (FLC or FLA) of the fire
pump motor.
Electrical Connections
A licensed electrician must supervise the electrical connections. The dimension drawings show the area suitable for
incoming power and motor connections. No other location shall be used. Only watertight hub fittings shall be used
when entering the cabinet to preserve the NEMA rating of the cabinet. The installer is responsible for adequate
protection of the fire pump controller components against metallic debris or drilling chips. Failure to do so may
cause injuries to personnel, damage the controller and subsequently void warranty.
Energy Consumption
Standby power: 13W
Sizing
Incoming power terminals on the controller are suitable to accept wire based on that selection with insulation not
less than 60°C. (Refer to terminal diagram for terminal sizes.)
The electrical wiring between the fire pump controller and the pump motor shall be in rigid, intermediate, or liquid
tight flexible metal conduit or Type MI cable and meet the requirements of NFPA 70 National Electrical Code or
C22.1 Canadian Electrical Code or other local codes.
The number of conductors required varies depending on the model of starter:
3-wires plus ground sized at 125% of full load current for models GPA, GPR, GPS and GPV.
6-wires plus ground sized at 125% of 50% of the motor full load current for GPP model.
6-wires plus ground sized at 125% of 58% of the motor full load current for GPY and GPW models.

11
Incoming Power Connections
Incoming normal power is to be connected to terminals located on the disconnecting means IS.
- For 3 phases motor: identified L1-L2 and L3.
- For single phase motor: identified L1 and L3
For the transfer switch, incoming alternate power is to be connected to terminals located on the disconnecting
means AIS (transfer switch side).
- For 3 phases motor: identified AL1-AL2 and AL3.
- For single phase motor: identified AL1 and AL3
Motor Connections
Motor wires shall be connected to terminals identified by:
- T1-T2 and T3 located on main contactor (1M) for models GPA, GPR, GPS and GPV
- T1-T2 and T3 located on contactor (1M) and T7-T8 and T9 located on contactor (2M) for model GPP
- T1-T2 and T3 located on contactor (1M) and T6-T4 and T5 located on contactor (2M) for models GPY and GPW
It is the responsibility of the installer to obtain connection information on the motor and to assure that the motor is
connected as per the motor manufacturer recommendations. Failure to do so may cause injuries to personnel,
damage the motor and/or the controller and subsequently void warranty on both items.

12
Terminal Strip Descriptions
Electric IO Board
Alarm output terminals (DPDT Relay, C:Common,
NC:Normally Closed, NO:Normally Open):
A: Motor Run
B: Power Available (Failsafe relay)
C: Phase Reversal
D: Pump Room Alarm
E: Motor Trouble
F: Factory Reserved
Field input terminal (Dry Contact Only: Voltage Free):
G: Remote Manual Start (NO)
H: Lockout (NO)
I: Remote Automatic Start (NC)
J: Deluge Valve (NC)
K: Factory Reserved 3 (NO)
L: Flow/Zone Start/Stop (NO)
M: Factory Reserved 2 (NO)
N: Factory Reserved 1 (NO)
Factory IO:
O: Analog Input sensor (depending on the options)
P: Analog Input sensor (depending on the options)
Q: PT2 Discharge Pressure sensor (redundant opt. only)
R: PT1 Discharge Pressure sensor
S: Emergency Handle limit switch
T: Communication ports to ViZiTouch and IO cards
U: Alarm Bell
V: Test Solenoid Valve
W: Shunt Trip
X: Factory Reserved
Y: 24VAC input power
Z: Main Coil power relay
AA: Delay Coil power relay
BB: Input Current sensing and Ground Fault detecting
CC: Ground
DD: Input Voltage sensing

13
Terminal Strip Descriptions
Transfer Switch IO Board
Outputs terminals:
A: Transfer Switch in Alternate Position
B: Transfer Switch in Normal Position
C: Alternate Circuit Breaker Status
D: Start/Stop Generator Signal
Factory IO:
E: Alternate position limit switches
F: Normal position limit switches
G: AIS/ACB limit switches
H-I-J: Transfer Switch motor
K: CANBUS: UP to ViZiTouch, DOWN to Exp. IO board
L: ACB shunt trip
M: Factory Reserved
N: 24VAC input from alternate power
O: 24VAC input from normal power
P: Ground
Q: Alternate Voltage sensing Input
R: Normal Voltage sensing Input

14
Quick Start-Up Guide
The rating label is the most important label. It must be read carefully to ensure the compatibility between the
controller and the installation.
Verify that the controller is installed securely on the wall, or optionally on the mounting stand.
Make sure to drill holes for the motor and power connections and run the cables inside the panel, all in accordance
with the specifications in order to minimize interference with other equipment.

15
Verify and/or install the proper water connections for the water input and the drain. They must be securely installed
and tightened. Refer to the silkscreen markings on the plastic cover.

16
Connect the normal input power, the alternate input power and the motor on their respective terminals. Secure with
the appropriate torque as indicated on the torque label and verify all connections.
Secure the doors in the closed position then put the normal power circuit breaker disconnecting means in the ON
position. Wait 10 seconds for the controller to load correctly, then put the alternate power circuit breaker
disconnecting means to the ON position. Verify the readings on the controller main screen.
Once the controller has booted up, the “First Start Up” page appears. The controller will automatically detect and
display the frequency of the power source. It is then possible to manually choose the frequency of the voltage.
Press “User Login” and enter a valid authorization code. Once logged in, press “Power”.

17
This page is used to verify the supply voltage. It displays the voltage that the controller reads between each phases
for the “Line Voltage”, the “Normal Voltage” (N1-N2-N3) and the “Alternate Voltage” (A1-A2-A3).
If one of these voltages is not the same as the controller's Nominal voltage, a red “X” will be displayed beside the
incorrect voltage reading.
If the Alternate power phases are not in the same order as the Normal power phases, a warning signal will display
at the bottom of the screen. To fix this problem, change the power wire connections A-AL1 and B-AL2 on the
Alternate side Isolation switch.
If the voltage reading are accurate (green check marks), go back to the “Controller Start-up” page and press the
“Go to rotation check”.
Press “Motor Rotation”
Press the “Start” button to start the electric motor and validate that the electric motor is rotating in the correct
direction. If it is not rotating in the correct direction adjus the motor connections as per below. Press the “Stop”
button to stop the electric motor.

18
Once the motor rotation has been checked, go back to the controller start-up page and press the “Verify pressure”
button.
WARNING!
On a Wye-Delta closed transition starter, if the transition from Wye to Delta occurs (after 5 to 8 seconds depending
on the motor HP), the manual stop push button will be disabled for 80 seconds. To stop the engine before the end
of the 80 second delay, use the disconnecting mean handle.
Press “Pressure”.
- Verify that the pressure reading on the screen matches with the calibrated pressure gauge installed on the
sensing line.
- Choose the desired units of measurement for pressure reading.
- Adjust, if required, the range of the digital pressure gauge at Max. Pres.
- Insert the Cut-Out and Cut-In pressure values of the fire pump.
- Insert, if so desired, the Cut-Out and Cut-In pressure values of the jockey pump.
Note: The jockey pump Cut-Out and Cut-In values must be set at the jockey pump controller itself. Inserting these
values at the Fire Pump Controller is only for pressure recording data purposes.
To continue to next step, press “ ˂ First Start Up “.

19
Go back to the controller start-up page and press the “Other Configuration” button. Enter the time and date. Select
the “Automatic shutdown” and the duration the pump will keep running after the automatic stop if an automatic stop
is desired. Select the frequency at which the periodic test will occur, the day of the week, the hour and the duration
of the test. Also, enter the duration of the Manual Run Test.
From the “Home” page, verify that the displayed values are correct.

20
The “First Start up” is now completed. The controller is fully installed and configured.
Other manuals for GPX
2
This manual suits for next models
1
Table of contents
Other Tornatech Controllers manuals
Popular Controllers manuals by other brands
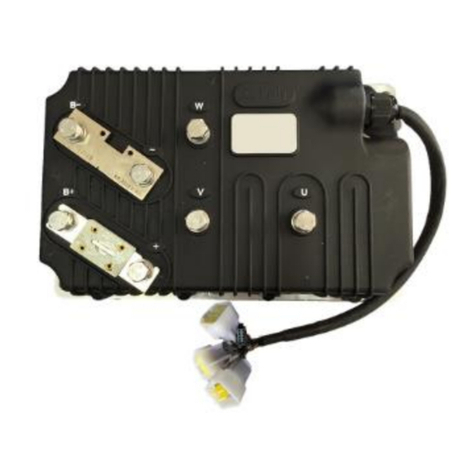
Kelly
Kelly KLS6045H user manual
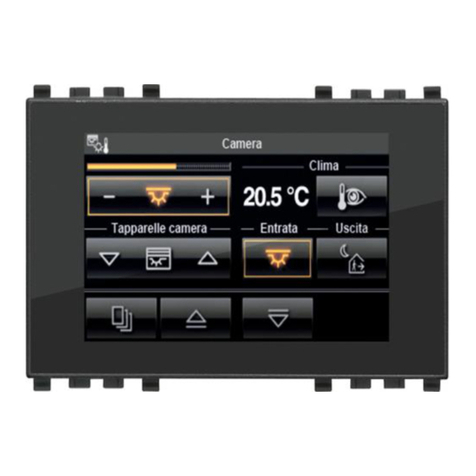
Vimar
Vimar Eikon Evo Well-contact Plus 21849 instructions
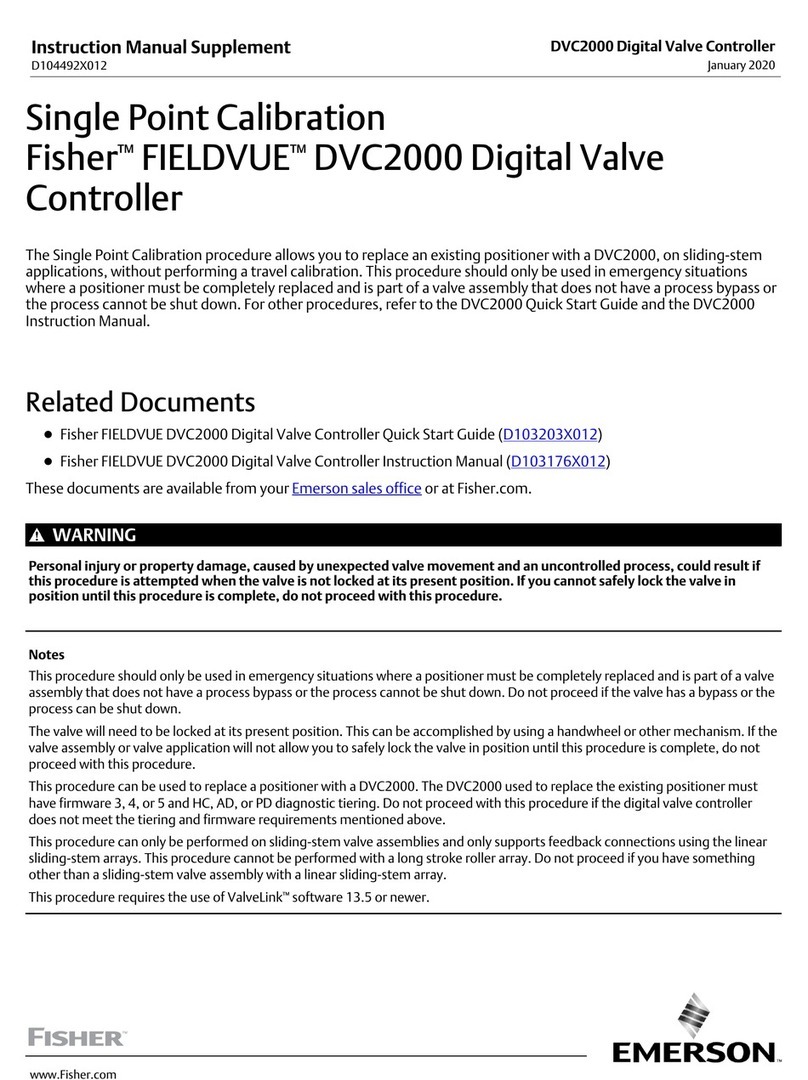
Emerson
Emerson Fisher FIELDVUE DVC2000 Instruction manual supplement
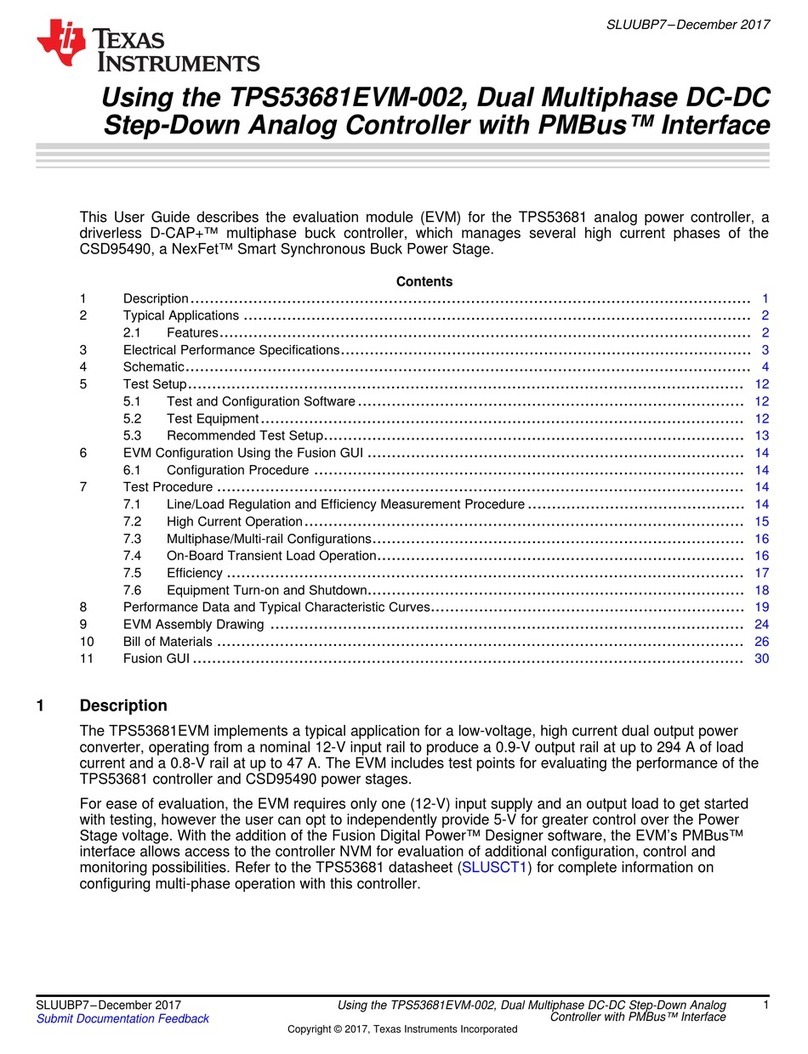
Texas Instruments
Texas Instruments TPS53681EVM-002 manual

Kohler
Kohler 8.5RES Service manual

DEEP SEA ELECTRONICS
DEEP SEA ELECTRONICS DSEM840 Operator's manual