V&T RS-P-4D2500 User manual

RS-P Solar Water Pump Controller
User Manual

RS−P Solar Water Pump Controller User Manual
Safety Precautions
Safety Precautions
Description of safety marks:
Danger: The misuse may cause fire, severe injury, even death.
Note: The misuse may cause medium or minor injury and equipment damage.
Use
DangerDanger
This series of controller is used to control the variable speed operation of three-phase
motor and cannot be used for single-phase motor or other applications. Otherwise,
controller failure or fire may happen.
This series of controller cannot be simply used in the applications directly related to the
human safety, such as the medical equipment.
This series of controller is produced under strict quality management system. If the
controller failure may cause severe accident or loss, safety measures, such as
redundancy or bypass, shall be taken.
Goods Arrival Inspection
NoteNote
If the controller is found damaged or have missing parts, the controller cannot be
installed. Otherwise, accident may be caused.
Installation
NoteNote
When handling and installing the controller, please hold the controller bottom. Do not
hold the enclosure only. Otherwise, your feet may be injured and the controller may be
damaged because of dropping.
The controller shall be mounted on the fire retardant surface, such as metal, and kept far
away from the inflammables and heat source.
Keep the drilling scraps from falling into the controller during the installation; otherwise,
controller failure may be caused.
When the controller is installed inside the cabinet, the electricity control cabinet shall be
equipped with fan and ventilation port. And ducts for heat dissipation shall be
constructed in the cabinet.

RS−P Solar Water Pump Controller User Manual
Safety Precautions
Wiring
DangerDanger
The wiring must be conducted by qualified electricians. Otherwise, electric shock may
happen or controller damage.
Before wiring, confirm that the power supply is disconnected. Otherwise, electric shock
may happen or fire.
The PE terminal must be reliably grounded , otherwise, the controller enclosure may
become live.
Please do not touch the main circuit terminals. The wires of the main circuit terminals
must not contact the controller enclosure. Otherwise, electric shock may happen.
The connecting terminals for the braking resistor are ⊕2/B1 and B2. Please do not
connect terminals other than these two. Otherwise, fire may be caused.
The leakage current of the controller system is more than 3.5mA, and the specific value
of the leakage current is determined by the operation application conditions. The
controller and the motor must be grounded to ensure the safety.
Wiring
NoteNote
The three-phase power supply cannot connect to output terminals U/T1, V/T2 and W/T3,
otherwise, the controller will be damaged.
It is forbidden to connect the controller output terminals to the capacitor or LC/RC noise
filter with phase lead, otherwise, the internal components of the controller may be
damaged.
Please confirm that the power supply phases, rated voltage are consistent with
those indicated by the nameplate, otherwise, the controller may be damaged.
Do not perform dielectric strength test on the controller, otherwise, the controller may be
damaged.
The wires of the main circuit terminals and the wires of the control circuit terminals shall be
laid separately or in a square-crossing mode, otherwise, the control signal may be
interfered.
The wires of the main circuit terminals shall adopt lugs with insulating sleeves.
The sectional area of controller input and output cables should be selected according to
the controller power.
When the cables between the controller and the motor are longer than 100m, it is
suggested to use output reactor to avoid the controller failure caused by the over current
of the distribution capacitor.
The controller equipped with a DC reactor must be connected with a DC reactor between
the terminals of +1 and +2, otherwise the controller will not display after power on.

RS−P Solar Water Pump Controller User Manual
Safety Precautions
Operation
DangerDanger
Power supply can only be connected after the wiring is completed and the cover is
installed. It is forbidden to remove the cover in live condition; otherwise, electric shock
may happen.
When auto failure reset function or restart function is enabled, isolation measures shall be
taken for the mechanical equipment, otherwise, personal injury may be caused.
When the controller is powered on, its terminals are still live even when it is in stop state.
Do not touch the controller terminals; otherwise electric shock may happen.
The failure and alarm signal can only be reset after the running command has been cut
off. Otherwise, personal injury may be caused.
NoteNote
Do not start or shut down the controller by switching on or off the power supply, otherwise,
the controller may be damaged.
Before operation, please confirm if the motor and equipment are in the normal use range,
otherwise, the equipment may be damaged.
The heat sink and the braking resistor have high temperature. Please do not touch such
device; otherwise, you may be burnt.
When the controller is used by crane or lifting equipment, mechanical contracting brake
shall also be equipped.
Please do not change the controller parameter randomly. Most of the factory settings of
the controller can meet the operating requirement, and the user only needs to set some
necessary parameters. Any random change of the parameter may cause the damage of
the mechanical equipment.
In the applications with power frequency and variable frequency switching, the two
contactors for controlling the industrial frequency and variable frequency switching shall
be interlocked.
Maintenance, Inspection
DangerDanger
In the power-on state, please do not touch the controller terminals; otherwise, electric
shock may happen.
If cover is to be removed, the power supply must be disconnected first.
Wait for at least 10 minutes after power off or confirm that the CHARGE LED is off before
maintenance and inspection to prevent the human injury caused by the residual voltage of
the electrolytic capacitor in main circuit.
The components shall be maintained, inspected or replaced by qualified electricians.

RS−P Solar Water Pump Controller User Manual
Safety Precautions
NoteNote
The circuit boards have large scale CMOS IC. Please do not touch the board to avoid the
circuit board damage caused by ESD.
Others
DangerDanger
It is forbidden to modify the controller unauthorizedly; otherwise, human injury may be
caused.

Contents
Foreword .................................................................................................................................. 1
Chapter 1 System configuration .......................................................................................... 1
1.1 system components ........................................................................................................ 1
1.2 water pump selection ...................................................................................................... 1
1.3 solar panels selection ..................................................................................................... 2
1.3.1 3PH AC 220v load ................................................................................................ 3
1.3.2 3PH AC 380v load ................................................................................................ 4
1.4 solar water pump controller selection .............................................................................. 5
2.1 Product Model Description .............................................................................................. 7
2.2 Product Nameplate Description ...................................................................................... 7
2.3 Environment for Product Installation ............................................................................... 8
2.3.1 Environment ......................................................................................................... 8
2.3.2 Mounting Direction and Space ................................................................................ 8
2.4 Product Outline、Mounting Dimension and Peripheral Devices ..................................... 9
2.4.1 Product Outline, Mounting Dimension, and Weight ................................................. 9
2.4.2 Wire connection .................................................................................................. 10
2.5 Operation Panel Outline ................................................................................................ 12
2.6 Terminal functions ......................................................................................................... 15
2.7 Installation process ....................................................................................................... 17
Chapter 3 Wells water towers working mode ................................................................... 20
Chapter 4 Routine Repair and Maintenance ..................................................................... 22
4.1 Routine Maintenance .................................................................................................... 22
4.2 Periodic Maintenance ............................................................................................... 23
4.3 Component Replacement ............................................................................................. 23
Appendix I. Fault and Fault Information List .................................................................... 24
Appendix Ⅱ :FAQ ................................................................................................................. 29
After-sales Service Regulation ........................................................................................ 31
RS-P Solar Water Pump ControllerQuality Feedback ......................................................... 35
Company Introduction ........................................................................................................ 3 6

RS−P Solar Water Pump Controller User Manual
Chapter 1 System configuration 1
Foreword
RS-P solar water pump controller is electric power product ,which is installed strictly
according to <User Manual> and safety precaution by technician . If not , the customer
should bear all results .
Chapter 1 System configuration
1.1 system components
The system mainly has 3 parts: power supply, controller and load. The power supply is PV
(Photovoltaic) array, generator or grid. The controller is mainly the RS−P Solar Water Pump Controller. The
load is 3-phase asynchronous motor or pump. The system does not need battery for storing energy, which
not only cuts the cost, but also protects the environment. RS−P PV Pump Controller can directly drive
various kinds of 3-phase asynchronous motor, with high power integration and less components, which
improves the system reliability.
RS- P Solar Water Pump Controller
Power
PV Pump
Motor
1.2 water pump selection
Water pump select based on how many water need per day, and the actual water height .Pump head should
be greater than the actual water height. Also can select water pump by the solar panels total power.
Solar panels total power is double size of water pump power is need .In the area solar power is powerful, this
scaling relation can be reduce.
Please note solar water pump controller only drive Three Phases AC pumps.
The pumps Operating Voltage can be 3 phase AC 220V or 3 phase AC 380V,and 50Hz ,2850RPM.

RS−P Solar Water Pump Controller User Manual
2 Chapter 1 System configuration
1.3 solar panels selection
Solar Array
Circuit breaker
Full water induction
Water shortage induction
WELL+/x5
-/com
-/com
TANK+/x4
+
-
M

RS−P Solar Water Pump Controller User Manual
Chapter 1 System configuration 3
1.3.1 3PH AC 220v load
The Solar Array Power is as much 1.5-2 times as pump current power ,and the Maximum Power
Voltage (Vpm) is above DC310V.
For example:
Water pump used:
Hz kW V A RPM
50 0.37 220 1.85 2850
Single solar panel:
Maximum Power (Pm) 130W
Open Circuit Voltage (Voc) 155.0V
Short Circuit Current (Isc) 1.28A
Maximum Power Voltage (Vpm) 120.8V
Maximum Power Current (Ipm) 1.08A
Maximum System Voltage 1000V
Solar panel total power: 0.37*2*1000=740W (Remark:The power ratio can be1.5 in the place
with strong sunshine.)
The number of panel: 740/130=5.69≈6
The number of tandem repeat: 310/120=2.58≈3
The number of parallel: 6/3=2
As follow the picture (1) :
Picture (1)
Solar Array:
Maximum Power (Pm) 780W
Open Circuit Voltage (Voc) 465V
Short Circuit Current (Isc) 2.56A
Maximum Power Voltage(Vpm) 362.4V
Maximum Power Current (Ipm) 2.16A
Maximum System Voltage −−−−
130W
Vpm=120V
+ -
130W
Vpm=120V
+ -
130W
Vpm=120V
+ -
130W
Vpm=120V
+ -
130W
Vpm=120V
+ -
130W
Vpm=120V
+ -
+ -

RS−P Solar Water Pump Controller User Manual
4 Chapter 1 System configuration
1.3.2 3PH AC 380v load
The Solar Array Power is as much 1.5-2 times as pump current power ,and the Maximum Power Voltage
(Vpm) is from 540V to 650v.
For example:
Water pump used:
Hz kW V A RPM
50 0.55 380 1.65 2780
Single solar panel:
Maximum Power (Pm) 130W
Open Circuit Voltage (Voc) 155.0V
Short Circuit Current (Isc) 1.28A
Maximum Power Voltage (Vpm) 120.8V
Maximum Power Current (Ipm) 1.08A
Maximum System Voltage 1000V
Solar panel total power: 0.55*2*1000=1100W.(Remark:The power ratio can be1.5 in the place
with strong sunshine.)
Solar panel total power: 1100/130≈9
The number of tandem repeat: 540/120=4.5≈5
The number of parallel: 9/5=1.8≈2
As follow the picture( 2) :
Picture (2)
130W
120V
+ -
130W
120V
+ -
130W
120V
+ -
130W
120V
+ -
130W
120V
+ -
130W
120V
+ -
130W
120V
+ -
130W
120V
+ -
130W
120V
+ -
130W
120V
+ -
+ -

RS−P Solar Water Pump Controller User Manual
Chapter 1 System configuration 5
the whole solar panels :
Maximum Power (Pm) 1300W 130W*10
Open Circuit Voltage (Voc) 775V 155.0V*5
Short Circuit Current (Isc) 2.56A 1.28A*2
Maximum Power Voltage (Vpm) 604V 120.8V*5
Maximum Power Current (Ipm) 2.16A 1.08A*2
Maximum System Voltage ---- 1000V
1.4 solar water pump controller selection
There are too types of solar water pump controllers. One is 2D,the other is 4D.
RS-P-2D□□□ Single-phase AC power & PV DC power
Power (W) 600 800 1200 1700 2500
MotorPower (kW) 0.55 0.75 1.1 1.5 2.2
Outpu
Voltage (V) Three−phase AC 220V (adjustable area 0 ~ Rated Input AC voltage)
Rated current (A) 2.9 4.5 6.0 7.5 10
Overload 150%: 1 minute, 180%: 10 seconds, 200%: 0.5 second, interval: 10 minutes (inverse time
lag feature)
Input
Rated Single or Three−phase 200~240V 50Hz/60Hz ; PV Area VocDC410V±30V
Allowable AC 180V to 260V, Voltage imbalance: ≤3%, allowable frequency fluctuation: ±5% ; MPPT
Area DC300~360V
Rated
current
(A
)
AC1/3PH 5.5 / 3.5 9.2 / 5.4 11.4 / 7.2 14.5 / 9 23 / 12
DC 3.5 5.4 7.2 9 12
Protection class IP20
Cooling mode Natural−cooling Forced air convection cooling

RS−P Solar Water Pump Controller User Manual
6 Chapter 1 System configuration
RS-P-4D□□□ Three-phase AC power & PV DC
* Above RS−P−4D17K are customized products.
The model of RS-P solar water pump controller should be elected according to requirement and take
account of pump’s rated voltage 、rated current、rated power、rated frequency and AC power and etc.The
AC out voltage should be consistent with rated voltage of pump.
Power (W) 600 800 1200 1700 2500 3600 5000 6600 7700 11K 12K 17K 21K 23K 33K
Motor
power (kW) 0.55 0.75 1.1 1.5 2.2 3.0 4.0 5.5 7.5 9.2 11.0 15.0 18.5 22.0 30.0
Output
Voltage (V) Three−phase AC 380V (adjustable area 0 ~ Rated Input AC voltage)
Rated current
(A) 1.7 2.5 3.5 3.8 5.5 8.5 9.0 13.0 17.0 22.0 24.0 30.0 39.0 45.0 60.0
Overload 150%: 1 minute, 180%:10 second, 200%: 0.5 second, interval: 10 minutes (inverse time lag feature)
Input
Rated
Voltage/Freq
uency
Three−phase 380V/ 480V 50Hz/60Hz ;
PV Area Voc DC700V±50V Maximum DC800V
Allowable Three−phase 323V to 528V, Voltage imbalance: ≤3%, allowable frequency fluctuation: ±5% MPPT
Area DC520~650V,
Rated
Current
(A)
AC 1.9 2.8 3.9 4.2 6.1 9.4 9.9 14.3 18.7 24.2 26.4 33 42.9 49.5 66
DC 2.1 3.0 4.2 4.6 6.6 10.2 10.8 15.6 20.4 26.4 28.8 36 46.8 54 72
Protection class IP20
Cooling mode Natural−cooling Forced air convection cooling
Power (W) 40K 47K 66K 77K 100K 120K 140K 170K 210K 230K 270K 280K 330K 400K 450K
Motor
power (kW) 37.0 45 55 75 90 110 132 160 200 220 250 280 315 355 400
Output
Voltage (V) Three−phase AC 380V (adjustable area 0 ~ Rated Input AC voltage)
Rated current
(A) 75 91 112 150 176 210 253 304 380 426 470 520 600 650 690
Overload 150%: 1 minute, 180%:10 seconds, 200%: 0.5 second, interval: 10 minutes (inverse time lag feature)
Input
Rated
Voltage/Freq
uency
Three−phase 380V/ 480V 50Hz/60Hz ;
PV Area Voc DC700V±50V Maximum DC800V
Allowable Three−phase 323V to 528V, Voltage imbalance: ≤3%, allowable frequency fluctuation: ±5% ; MPPT Area
DC520~650V,
Rated
current
(A)
AC 82.5 99 123.2 165 193.6 231 278.3 334.4 418 468.6 517 572 660 715 759
DC 90 108 134.4 180 211.2 252 303.6 364.8 456 511.2 564 624 720 780 828
Protection class IP20
Cooling mode Natural−cooling Forced air convection cooling

RS−P Solar Water Pump Controller User Manual
Chapter 2 Use and installation of PS-P Solar water pump controller 7
Chapter 2 Use and installation of PS-P Solar water pump controller
2.1 Product Model Description
The digits and letters in the product model field on the nameplate indicate such information as the
product series, power supply class, power class and software/hardware versions.
2.2 Product Nameplate Description

RS−P Solar Water Pump Controller User Manual
8 Chapter 2 Use and installation of PS-P Solar water pump controller
2.3 Environment for Product Installation
2.3.1 Environment
Do not install the controller in the sites with oil mist, metal powder and dust.
Do not install the controller in the sites with hazardous gas and liquid, and corrosive, combustible and
explosive gas.
Do not install the controllers in salty sites.
Do not install the controller in the sites with direct sunlight.
Do not mount the controller on the combustible materials, such as wood.
Keep the drilling scraps from falling into the controller during the installation.
Mount the controller vertically in the electric control cabinet, mount the cooling fan or air conditioner to
prevent the ambient temperature from rising to above 45 ºC.
For the sites with adverse environment, it is recommended to mount the controller heat sink outside the
cabinet.
2.3.2 Mounting Direction and Space
Note: For the non-standard unit such as control box, the clearance between the ventilation ports and
surrounding building shall be less than 300mm.
Please install vertically as shown in Figure 2−1 and Figure 2−2 so as to keep some clearance.
Picture ( 3 ) Installation direction and space of RS−P−4D600 to 4D5000

RS−P Solar Water Pump Controller User Manual
Chapter 2 Use and installation of PS-P Solar water pump controller 9
Picture ( 4 )Installation direction and space of RS−P−4D3600 to 4D17k
2.4 Product Outline、Mounting Dimension and Peripheral Devices
2.4.1 Product Outline, Mounting Dimension, and Weight
Picture ( 5 )RS−P−4D5000 and below power class

RS−P Solar Water Pump Controller User Manual
10 Chapter 2 Use and installation of PS-P Solar water pump controller
Picture ( 6 )RS−P−4D3600 to RS−P−4D17k
Product outline, mounting dimension, and weight
Controller model
Outline and mounting dimension (mm) Approximate
weight
(kg)
W H D W1 H1 T1 Installatio
n holes d
RS−P−4D600 to 4D2500
236 350 160 220 270 4 8.5 6
RS−P−2D600 to 2D800
RS−P−4D3600 /4D5000
236 350 160 220 270 15.5 8.5 8
RS−P−2D1200/2D1700
RS−P−4D6600
260 410 186 244 326 30 8.5 10
RS−P−4D7700
RS−P−4D12k
300 491 216 284 405 60 9 15
RS−P−4D17k
RS−P−4D21k to 4D450k Customized according to user requirements
2.4.2 Wire connection
1. Parts of installation specification:
The specification is fixed with screws GB9074.13-88-M8x25 Cross recessed hexagon bolt, spring
washer and plain washer assemblies, a total of four sets of assembly

RS−P Solar Water Pump Controller User Manual
Chapter 2 Use and installation of PS-P Solar water pump controller 11
2. Connection of the controller and Peripheral Devices:
The customer can select devices with “* ” according to the site condition
Power supply
Input AC reactor
DC reactor
controller
Grounding
Output noise filte
Output AC reactor
Motor
Grounding
Picture ( 7)
Circuit breaker or
RCCB*RCCB
Contactor
Input noise filter
Solar supply
Pv distribution box
Contactor
DC reactor

RS−P Solar Water Pump Controller User Manual
12 Chapter 2 Use and installation of PS-P Solar water pump controller
Description of Peripheral Devices for Main Circuit
* PV distribution box PV distribution box can reduce connectiong ware between PV array and controler , improve
reliability and maintance .
Circuit breaker
The circuit breaker capacity shall be 1.5 ~ 2 times of the controller rated current.
The time features of the circuit breaker shall fully consider the time features of the controller
overload protection.
* RCCB
Because the controller output is the high-frequency pulse, there will be high-frequency leakage
current. Special RCCB shall be used when installing RCCB at the controller input side.
It is suggested that B type RCCB be used, and the leakage current value shall be set to 300mA.
* Contactor
Frequent contactor tripping will cause controller failure, so the highest frequency for contactor
tripping shall not exceed 10 times/min.
When a braking resistor is used, to avoid the overtemperature damage of the braking resistor, a
thermal protection relay with braking resistor overtemperature detection shall be installed to
disconnect the contactor at the contact control power side of the thermal protection relay.
* Input AC reactor
or DC reactor
The controller power supply capacity is more than 600kVA or 10 times of the controller capacity.
If there is switch type reactive-load compensation capacitor or load with silicon control at the same
power node, there will be high peak current flowing into input power circuit, which damages the
rectifier components.
When the voltage imbalance of the three-phase power supply of the controller exceeds 3%, the
rectifier component will be damaged.
It is required that the input power factor of the controller shall be higher than 90%.
When the above situations occur, install the AC reactor at the controller input side or DC reactor to
the DC reactor terminal.
* Input noise filter The noise input from the power end to the controller and output from the controller to the power
end can be reduced.
* Thermal
protection relay
Although the controller has motor overload protection function, when one controller drives two or
more motors or multi-pole motors, to prevent the motor over temperature failure, a thermal
protection relay shall be installed between the controller and each motor, and the motor overload
protection parameter P9.16 shall be set to “2” (motor protection disabled).
* Output noise filter When the output of the controller is connected with noise filter, the conduction and radiation
interference can be reduced.
* Output AC reactor
When the cable connecting the controller and the motor is longer than 100m, it is suggested to
install AC output reactor to suppress the high-frequency oscillation to avoid damaging motor
insulation, large leakage current and frequent controller protective action.
2.5 Operation Panel Outline
Picture (8 ) Standard 3-button operation panel picture (9) Operation panel
(RS−P−4D7700 and below power class) ( RS−P−4D21K and above power class)

RS−P Solar Water Pump Controller User Manual
Chapter 2 Use and installation of PS-P Solar water pump controller 13
For the end users the product provide standard three key panels, this panel is a function limited version
of Control panel. It can set controller run or stop, can reset controller from FAULT, can monitor running
frequency, current, voltage, power, and total energy.
Control panel is more complex, and for the technician to use. Can modify parameter of the solar water
pump controller.
To use Control panel need take off controller’s front cover, and put the Control panel ware in the JACK on
the control board. For the safety, power offs the controller before the operation. And don’t touch any other
things.
LED Indicator on control panel:
Indicator name meaning color
Unit
indicator
light
Standard three key panel
Hz Frequency indicator Bright: display running frequency.
Flash: display preset frequency. green
A Current Indicator Bright: display current. green
V Voltage Indicator Bright: display voltage. green
W Power Indicator Bright: display power. red
kWh Energy Indicator Bright: display energy generated by the solar panel. red
Control panel
Hz+A Rotation rate Indicator Bright: display rotation rate.
Flash: display preset rotation rate. green
Hz+V Percent Indicator Bright: parameter is in percentage terms. green
Hz+A+V Time Indicator Bright: parameter is time. green
No unit Indicator Dark: parameter is no unit value. -
State
Indicator
light
Standard three key panel
FAULT Fault Indicator bright:in fault state
Dark: normal operation red
AUTO Running mode Indicator Bright: automatic running mode.
Dark: manual operation mode. green
RUN Running state Indicator
Bright: is Running.
Dark: has Stopped.
Flash: is stopping running.
red
Control panel
MULTI Multifunction key Indicator red
MON Running command
Source Indicator
Bright: given by control panel.
Dark: given by terminal input.
Flash: given by computer.
red
FWD Forward Indicator
Bright: in stop condition, controller has forward rotate
command.
In running condition, controller is in foreword rotate
direction.
Flash: is turning from forward rotate to reverse rotate.
red
REV Reverse
Indicator
Bright: in stop condition, controller has reverse rotate
command.
In running condition, controller is in reverse rotate
direction.
Flash: is turning from reverse rotate to foreword rotate.
red

RS−P Solar Water Pump Controller User Manual
14 Chapter 2 Use and installation of PS-P Solar water pump controller
Control panel function keys:
Logo
name function
Key
type
Rotate
type
c
Programmin
g key
PRG
1.into sub menu
2.Conform data store.
3.check parameters by sequence
4.Change running command source assist
With M key.
c
Escape key
ESC
1.When is in second level menu, back to first level menu. When is in first level menu,
back to standby state or running state or fault state.
2.After change the value, abort data store.
3.Keep press for 5 seconds, back to basic menu mode. When can not display all the
function code,use this method to display all the function code.
4.After use >> key switch FALUT display mode to stop/run parameter display mode,
push ESC key can switch back to FALUT display mode.
Turn+
Turn-
Up key
∧
1.When is in first menu, parameter PX.YZ increase at the edit bit.
2.When is in second menu, parameter’s value increase.
3. When is in STOP/RUN state, preset frequency or preset closed loop increase.
Down key
∨
1. When is in first menu, parameter PX.YZ decrease at the edit bit.
2. When is in second menu, parameter’s value decrease.
3. When is in STOP/RUN state, preset frequency or preset closed loop decrease.
Shift key>>
1.When is in first menu, use Shift key>> change PX.YZ edit bit.
2.When is in second menu, use Shift key>> change parameter’s value edit bit.
3.When is in STOP/RUN state, use Shift key>>change display parameters, e.g.
frequency, current, voltage, etc.
4.When is in FALUT state, use Shift key>> change display from FALUT display to
STOP/RUN parameter display.
Run key
RUN
1.When running command source is Control panel, run key Start controller to run.
2.When set auto learning parameters, Run key Start auto learning.
Stop/reset
key
STOP/RST
1. When Running command source is Control panel, Stop/reset key stop controller
running.
2. When only display FALUT message not Stop, Stop/reset key stop controller
running.
3. When FALUT occur and controller stopped, Stop/reset key function as reset key,
reset FALUT message.
Multifunctio
n key
M
Forward/Re
verse key
FWD/REV
When running command source is Control panel, use to control controller’s rotate
direction.
Note:
The ENTER key of shuttle type operation panel is equivalent to PRG Key.
Using PRG key continuously can realize fast browse of all function codes.
Table of contents
Popular Controllers manuals by other brands
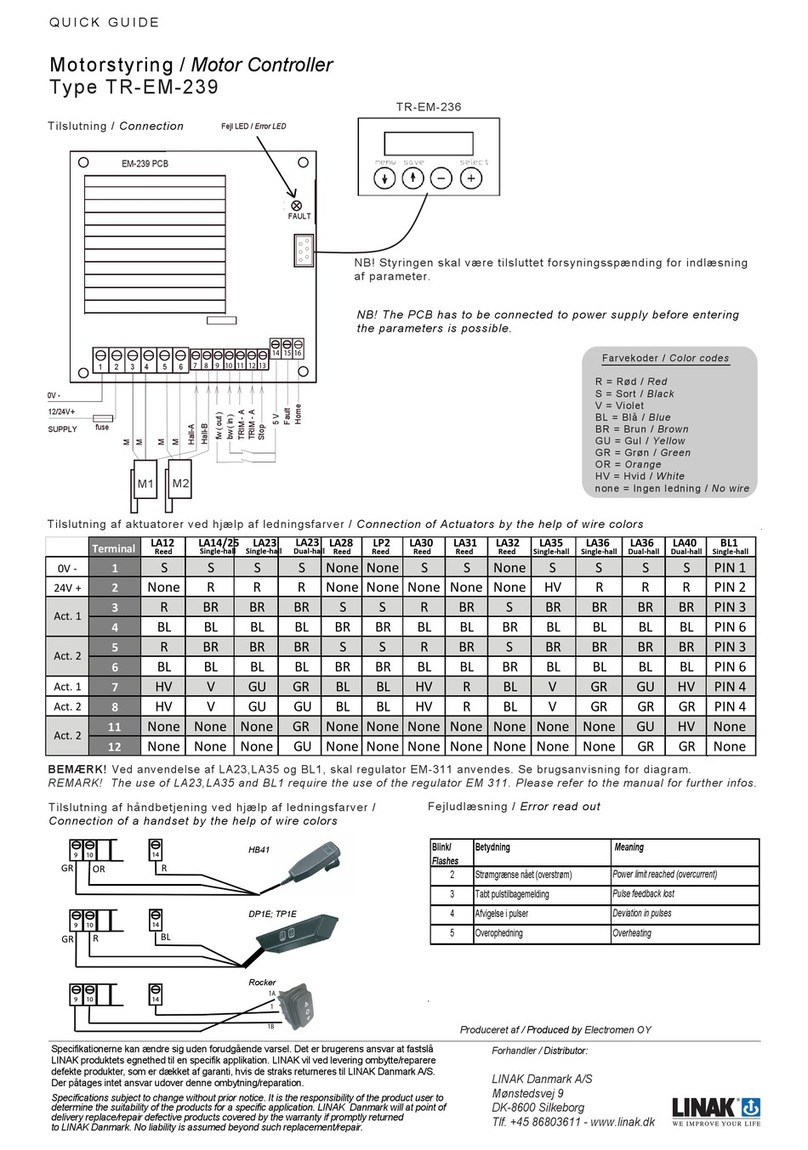
Linak
Linak TR-EM-239 quick guide
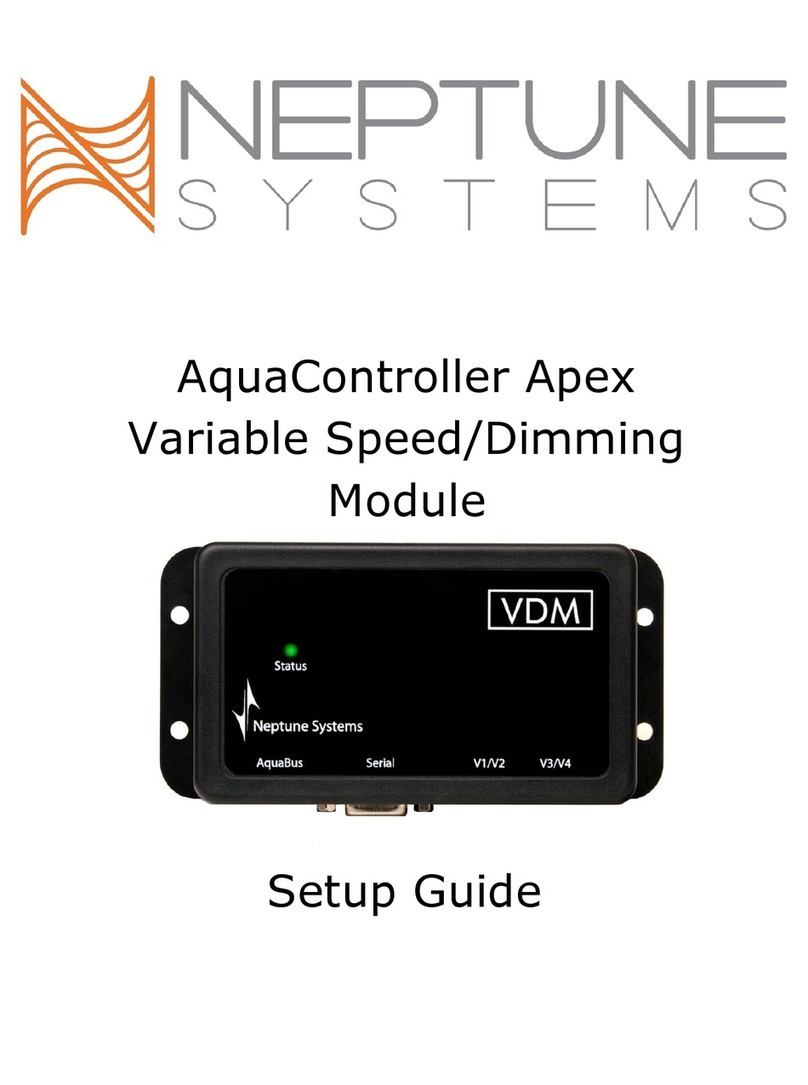
Neptune Systems
Neptune Systems AquaController Apex Setup guide
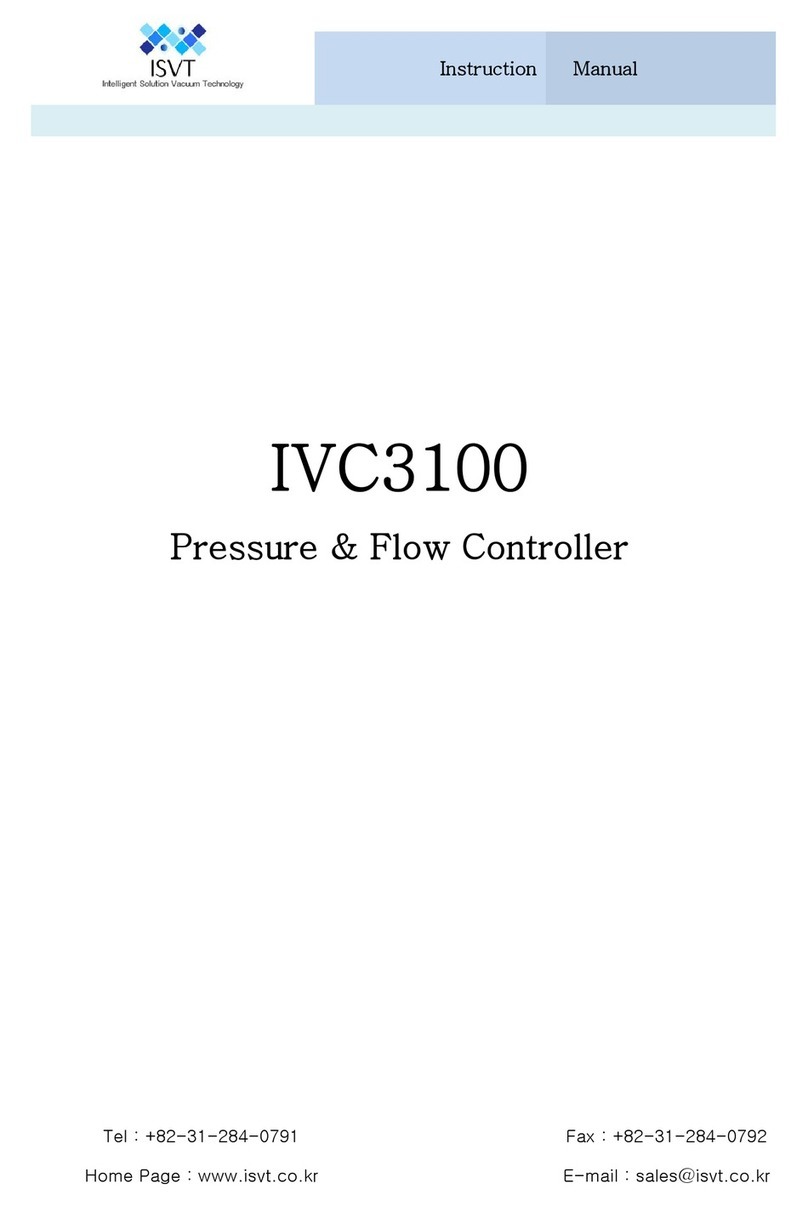
ISVT
ISVT IVC3100 instruction manual
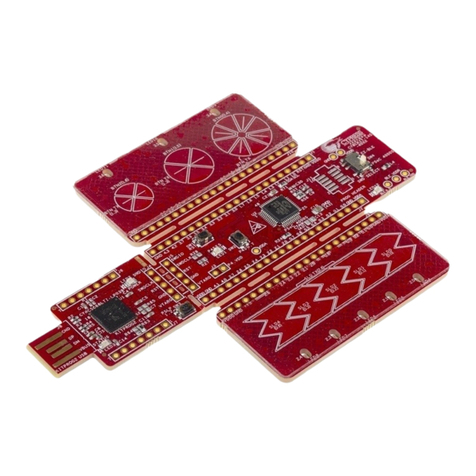
Cypress
Cypress CapSense AN64846 Getting started

SmartieParts
SmartieParts 9x installation instructions

Mitsubishi Electric
Mitsubishi Electric MELSEC FX Series Programming manual
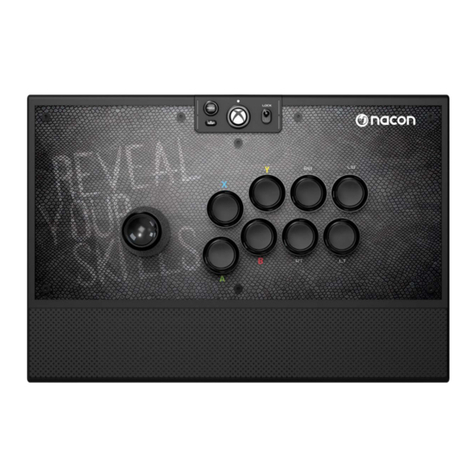
NACO
NACO XBOX DAIJA ARCADE STICK Start guide
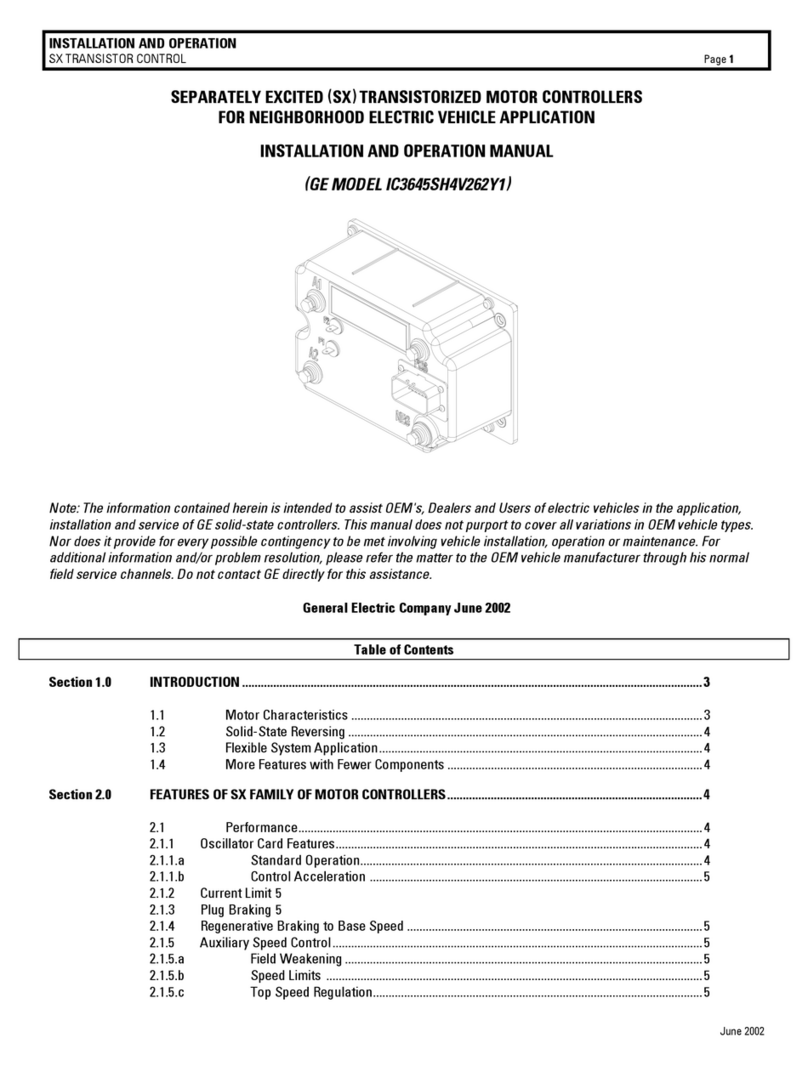
GE
GE H4V262Y1 Installation and operation manual
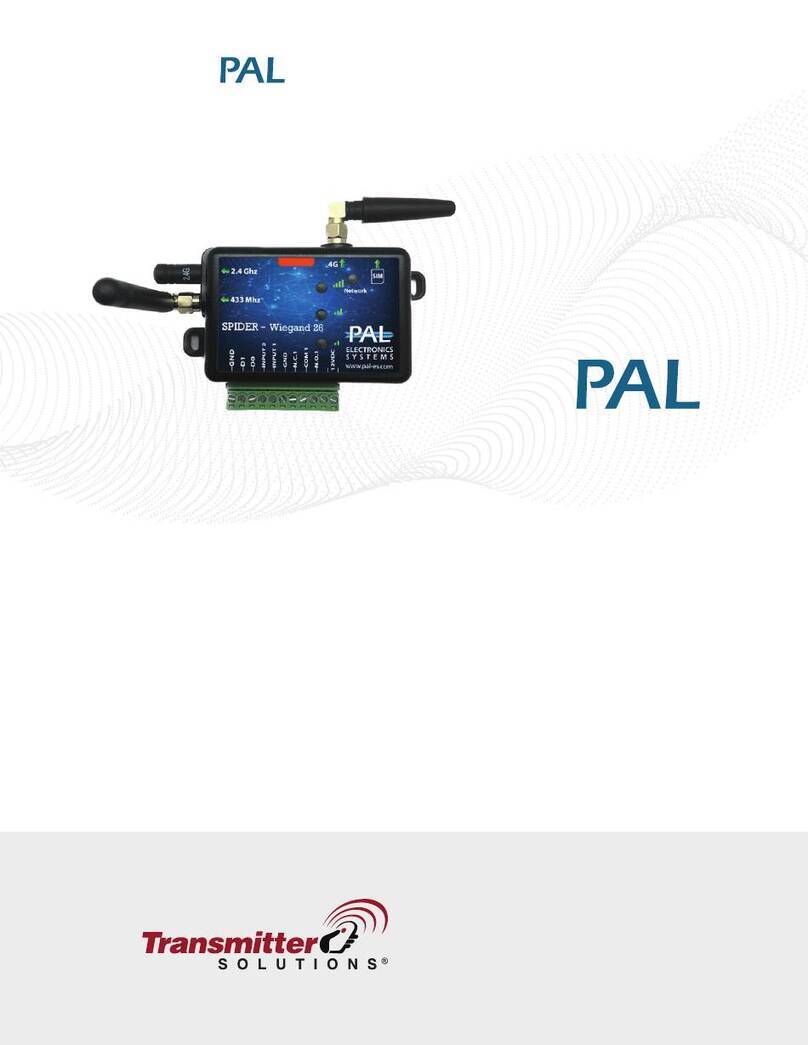
Transmitter Solutions
Transmitter Solutions PAL SPIDER WIEGAND 26 user manual
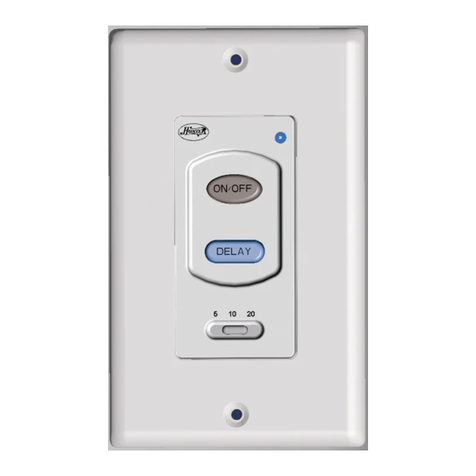
Hunter
Hunter 27178 installation guide
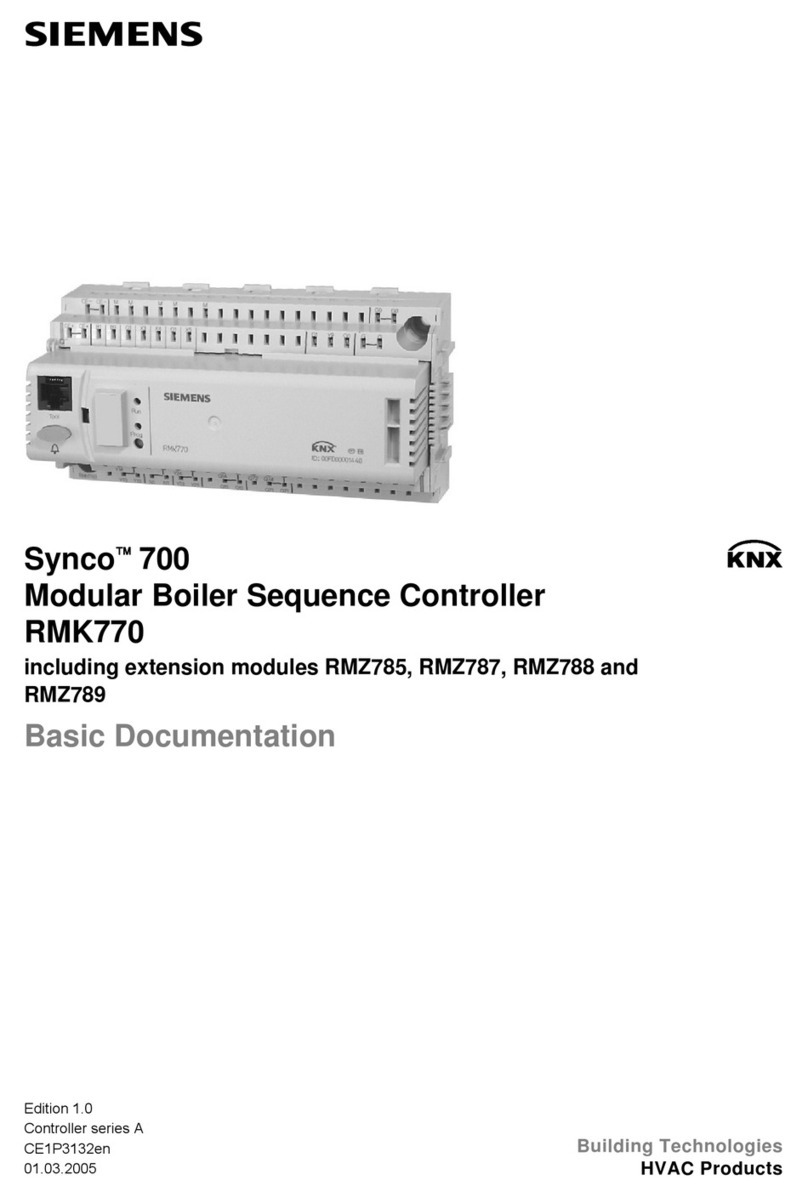
Siemens
Siemens Synco700 RMK770 Documentation handbook

Technische Alternative
Technische Alternative UVR 63H Operation and installation manual