Versalift VST-8000-I User manual

Operator’s Manual
Time Manufacturing Co. 7601 Imperial Drive P.O. Box 20368 Waco, Texas 76702 Phone: 254-399-2100 Fax: 254-751-0775
Aerial Device
ATTENTION:
THIS MANUAL CONTAINS CONFIDENTIAL INFORMATION
AND IS THE SOLE PROPERTY OF TIME MANUFACTURING CO.
CONTENTS ARE NOT TO BE DISCLOSED, COPIED, OR REPRODUCED
IN ANY MANNER WITHOUT THE EXPRESSED, WRITTEN PERMISSION
OF TIME MANUFACTURING CO.
DO NOT ATTEMPT TO OPERATE THIS VERSALIFT UNTIL
YOU HAVE READ AND UNDERSTOOD ALL INFORMATION IN BOTH
OPERATOR’S AND SERVICE MANUALS, PROVIDED WITH EACH
VERSALIFT.
MANUAL PART NUMBER
39026-03
SERIAL NUMBER
VST-8000/8500/9000/9500-I
Time Manufacturing Co. reserves the right to improve the design or change specifications at any time without notice.
02/17
PLEASE NOTE THE ANSI A92.2 STANDARD AND THE MANUAL OF RESPONSIBILITIES CONTAINS
RECENTLY UPDATED INFORMATION. DEALERS, OWNERS, USERS, OPERATORS, LESSORS AND LESSEES MUST
ADHERE TO THESE UPDATED STANDARDS.


MANUFACTURING COMPANY
OWNER’S WARRANTY
The Versalift Aerial Platform Lift is engineered and designed to perform as stated on
published specifications. Only quality material and workmanship are used in the
manufacture of this product. With proper installation, regular maintenance, and periodic
repair service, the equipment will provide excellent service.
Those parts of the Versalift that are manufactured by Time Manufacturing Company
are warranted for one full year from date of purchase. Structural components will carry
a lifetime warranty for defects in material and workmanship which existed at the time of
initial delivery, wear components are not covered by this statement. This warranty is
issued only to the original purchaser and promises that Time Manufacturing Company
manufactured products are free from defects in material and factory workmanship
when properly installed, serviced, and operated under normal conditions, according to
the manufacturer’s instructions.
Manufacturer’s obligation under this warranty is limited to correcting without charge at
its factory any part or parts thereof which shall be returned to its factory or one of its
Authorized Service Stations, transportation charges prepaid, within one year after being
put into service by the original user, and which upon examination shall disclose to the
Manufacturer’s satisfaction to have been originally defective. Correction of such defects
by repair to, or supplying of replacements for defective parts, shall constitute fulfillment
of all obligations to original user.
This warranty shall not apply to any of the Manufacturer’s products which must be
replaced because of normal wear, which have been subject to misuses, negligence or
accident, or which shall have been repaired or altered outside of the Manufacturer’s
factory (unless authorized by the Manufacturer in writing), products which have not
been maintained and operated in accordance with Time Manufacturing Company’s
operators, maintenance manuals and bulletins, products which are repaired without
using original Time Manufacturing Company parts. This limited warranty does not
cover transportation fees and/or consumables used for the repair. Products or parts
manufactured by others are covered only by such warranties as are extended to TIME
MANUFACTURING CO. by its suppliers.
Manufacturer shall not be liable for loss, damage, or expense directly or indirectly from
the use of its product or from any cause.
The above warranty supersedes and is in lieu of all other warranties, expressed or
implied, and of all other liabilities or obligations on part of Manufacturer. No person,
agent, or dealer is authorized to give any warranties on behalf of the Manufacturer or to
assume for the Manufacturer any other liability in connection with any of its products
unless made in writing and signed by an officer of the Manufacturer.


i39026-03 02/17VERSALIFT VST-8000/8500/9000/9500-I
TABLE OF CONTENTS
TABLE OF CONTENTS
Introduction Section 1
Manual Structure ........................................................................................................................ 1-1
Additional Manual Features ........................................................................................................ 1-1
Nomenclature ............................................................................................................................. 1-2
Responsibilities / Safety Section 2
Responsibilities of Dealers, Owners, Users, Operators, Lessors, and Lessees ........................ 2-1
Decals ......................................................................................................................................... 2-2
Think Safety ................................................................................................................................ 2-6
What is Insulated and What is not Insulated .............................................................................. 2-9
Additional Safety Considerations .............................................................................................. 2-10
Specifi cations Section 3
General Specifi cations ................................................................................................................ 3-1
Option Specifi cations .................................................................................................................. 3-2
Dimensional Specifi cations ......................................................................................................... 3-5
Vehicle Specifi cations ............................................................................................................... 3-17
Operation Section 4
Positioning the Versalift for Operation ....................................................................................... 4-1
Aerial Lift Operations .................................................................................................................. 4-2
Cab Control Operation ............................................................................................................... 4-4
Ground Control Operation ......................................................................................................... 4-4
Lower Control Operation ........................................................................................................... 4-6
Upper Control Operation ............................................................................................................ 4-6
Storing the Aerial Lift ................................................................................................................. 4-8
Lifting Eye ................................................................................................................................... 4-9
Manual Jib Operation ............................................................................................................... 4-10
Hydraulic Jib Operation ............................................................................................................ 4-12
Jib Capacity Determination ....................................................................................................... 4-12
Emergency Operation Section 5
Daily Visual Inspection Section 6


1-1 39026-03 02/17VERSALIFT VST-8000/8500/9000/9500-I
INTRODUCTION
DANGER: READ AND UNDERSTAND
THIS MANUAL BEFORE ATTEMPTING TO
OPERATE THIS AERIAL DEVICE.
The manual identifies all the controls and their
locations and describes how the controls function.
Routine preventive maintenance is very important in
maintaining reliable aerial lift service. A preventive
maintenance schedule is provided and must be
understood and followed by all operators.
DANGER: THIS IS NOT MAINTENANCE
FREE EQUIPMENT.
NOTICE: THIS MANUAL IS A PERMANENT
PART OF THE VERSALIFT AERIAL DEVICEAND
MUST REMAIN WITH THE UNIT ALWAYS.
Time Manufacturing Company reserves the right
to improve the design or specifi cations at any time
without any obligation to incorporate new features
into products previously sold.
MANUAL STRUCTURE
This manual is divided into six, numbered chapters.
The fi rst number in the page number at the bottom
of each page identifi es the chapter number. Chapter
tabs, with titles printed on them, allow easy location
of the desired subject.
ADDITIONAL MANUAL FEATURES
Danger, caution, and warning notes are indented,
bold faced, and separated from the regular text
to emphasize their importance and the need for
attention.
English measurements are followed by equivalent
metric measurements in parenthesis.
Non-critical units of measure are usually rounded-off
to the nearest whole unit.
Notes referring the reader to related information
in the manual indicate the chapter or a section of a
chapter, not to a single page. The reader may need
to scan a few pages to fi nd the needed information.
The Versalift aerial device has been designed and
engineered to conveniently place personnel at work
stations above the ground. This aerial device, as
manufactured, meets or exceeds all applicable ANSI
A92.2. Full controls at the platform and complete
freedom of boom movements make the Versalift a
truly fl exible and functional work platform.
NOTE: As the aerial device users, you must read,
understand, and follow the instructions in this
manual and other manuals supplied with this
aerial lift unit.
This manual is furnished to provide practical and
essential information for effi cient operation of the
Versalift aerial device. Proper operation of this aerial
lift is the responsibility of the operator and requires a
thorough understanding of its capabilities. Personnel
responsible for the operation of the aerial lift must be
familiar with and understand this manual.
In addition to, dealers, owners, operators, renters,
lessors and lessees are required to comply with the
requirements of the applicable section or sections
found in ANSI A92.2.
NOTE: For additional safety information
and required responsibilities, refer to the
accompanying EMI Safety Manual and Manual
of Responsibilities.
Detailed information for the maintenance inspection
and service of the Versalift aerial device can be
found in the accompanying Service Manual. Should
further installation information be required, contact
your local Versalift dealer or Time Manufacturing
Company.
DANGER: THIS EQUIPMENT SHOULD
BE OPERATED AND SERVICED ONLY BY
COMPETENT PERSONNEL FAMILIAR WITH
GOODSAFETYPRACTICES. THISINSTRUCTION
IS WRITTEN FOR SUCH PERSONNEL AND
IS NOT INTENDED AS A SUBSTITUTE FOR
ADEQUATE TRAINING AND EXPERIENCE
IN SAFE PROCEDURES FOR THIS TYPE OF
EQUIPMENT.
INTRODUCTION
THIS MANUAL CONTAINS CONFIDENTIAL
INFORMATION AND IS SOLE PROPERTY OF
TIME MANUFACTURING, AND IS NOT TO BE
DISCLOSED, COPIED, OR REPRODUCED
WITHOUT EXPRESSED PERMISSION OF
TIME MANUFACTURING.

1-2 39026-03 02/17VERSALIFT VST-8000/8500/9000/9500-I
INTRODUCTION
Figure 1.1 Model VST-8000/8500/9000/9500-I Nomenclature

2-1 39026-03 02/17VERSALIFT VST-8000/8500/9000/9500-I
RESPONSIBILITIES / SAFETY
DANGER:FAILURE TOCOMPLY WITH
YOUR REQUIRED RESPONSIBILITIES IN THE
USE AND OPERATION OF THE AERIAL DEVICE
COULDRESULTINDEATHORSERIOUSINJURY.
IMPORTANT
You are required by ANSI/SIA A92.2 to read and
understand YOUR RESPONSIBILITIES before
you use or operate the Aerial Device. It is your
responsibility and your employer’s responsibility to
identify and comply with applicable codes, standards,
and regulations.
The operation of any aerial device is subject to
certain HAZARDS that can be protected against
only by the exercise of INTELLIGENCE, CARE
AND COMMON SENSE. It is essential to have
COMPETENT, CAREFUL PERSONNEL, TRAINED
in the INTENDED USE, SAFE OPERATION,
MAINTENANCE AND SERVICE of this type of
equipment.
The USER and OPERATOR MUST MAKE
DECISIONS on the maintenance, use and operation
of the Aerial Device with due consideration for the fact
that the SAFETY OF THE OPERATOR AND OTHER
PERSONNEL is dependent on those decisions.
FAILURE TO COMPLY with your REQUIRED
RESPONSIBILITIES in the use and operation of the
Aerial Device could result in DEATH OR SERIOUS
INJURY.
DANGER: READ AND UNDERSTAND
THIS MANUAL BEFORE ATTEMPTING TO
OPERATE THIS AERIAL DEVICE.
RESPONSIBILITIES
(for Dealers, Owners, Users, Operator, Lessors and Lessees)

2-2 39026-03 02/17VERSALIFT VST-8000/8500/9000/9500-I
RESPONSIBILITIES / SAFETY
Only properly trained operators are qualifi ed to
operate the Versalift aerial lift. Operator training
shall include complete instruction and understanding
of the manufacturer’s manuals, employer’s work
rules, and all related governmental regulations. Prior
to operation from the platform the machine must be
operating properly, must have been installed properly,
inspected, and maintained in accordance with the
manufacturer’s instructions. All safety signs, guards,
and covers must be in place and in proper condition.
DANGER: ANUNTRAINEDORCARELESS
OPERATOR SUBJECTS HIM/HERSELF AND
OTHERS TO DEATH OR SERIOUS INJURY.
Throughout this manual there are danger, warning,
and caution notes that emphasize the possible
hazards when operating the Versalift. It is the
responsibility of the operator to become familiar with
the contents of this manual.
Two of the main risks associated with operating an
aerial lift:
(1) Electrocution caused by operating too close
to power lines.
(2) Injuries caused by falling as a result of
equipment failure or the operator performing
an unsafe or unstable maneuver.
No manual can address every conceivable operating
hazard. Therefore, the prevention of accidents
is greatly dependent upon good judgement and
common sense of the operator.
It is the responsibility of the operator to use the
Versalift only when it has been installed and
maintained in accordance with the manufacturer’s
manuals. The preventive maintenance program
outlined in this manual and the Service manual must
be followed.
It is extremely important for the operator to be
thoroughly familiar with the Versalift aerial device.
Study the information in this manual and the Versalift
controls until both are completely mastered. Then go
to a large, open area to practice using the aerial lift.
Decals are installed at numerous locations on the
aerial lift to warn personnel of the potential hazards
during the use and operation of the aerial lift. It is
important that the operator and ground personnel
read and understand the information on the decals. If
any decals are defaced, illegible or lost, they must be
replaced. Refer to the “Decal Placement” illustration
in this manual for a complete listing and the locations
of the decals. For your convenience these decals are
pictured on the following pages as a quick reference
for reviewing safety concerns and for providing part
numbers when ordering replacements.
DECALS
All the warning and instruction decals, and their
respective part numbers, on the Versalift aerial
device are included below and on the following pages.
The decals are not shown at actual size.
SAFETY

2-3 39026-03 02/17VERSALIFT VST-8000/8500/9000/9500-I
RESPONSIBILITIES / SAFETY

2-4 39026-03 02/17VERSALIFT VST-8000/8500/9000/9500-I
RESPONSIBILITIES / SAFETY

2-5 39026-03 02/17VERSALIFT VST-8000/8500/9000/9500-I
RESPONSIBILITIES / SAFETY

2-6 39026-03 02/17VERSALIFT VST-8000/8500/9000/9500-I
RESPONSIBILITIES / SAFETY
A safe attitude is very important to you, the operator.
Practice anticipating accidents and operating haz-
ards. Then determine a corrective course of action
to respond to the situa tion. This habit will sharpen
your safety awareness, quicken your reaction time,
and prevent many accidents.
THINK SAFETY
The following sketches illustrate some of the unsafe
situations that might occur during the use or operation
of the Versalift. Some of these safety problems are
very basic and as a result are often taken for granted.
Always engage the outriggers, and maintain the
correct tire pressure to increase vehicle stability.
Always wear a personnel restraint system attached
to the lanyard anchor.
Don’t park the truck on a hill unless absolutely
necessary. When the truck is parked on a slope,
take the special precautions defi ned in Chapter 4,
“Operation”.
Remember to set the parking brake and chock the
truck’s wheels.
Watch the booms to make sure they clear the truck
and other obstructions.

2-7 39026-03 02/17VERSALIFT VST-8000/8500/9000/9500-I
RESPONSIBILITIES / SAFETY
Stow the booms securely before moving the truck.
Whenever tools or equipment are included with the
operator in the platform the combined weight must
not exceed the rated load capacity.
Avoid dropping tools. Use a hand line to raise or
lower tools to/from the platform.
Maintain safe clearances from electrical power lines
and apparatus. The aerial lift does not provide
protection from contact or proximity to an electrically
charged conductors and another conductor.
Never allow anyone on the ground to touch the
unit when the lift is being used to work on or near
electrical lines.
Never use the VERSALIFT as a crane

2-8 39026-03 02/17VERSALIFT VST-8000/8500/9000/9500-I
RESPONSIBILITIES / SAFETY
Stand only on the platform fl oor.
Don’t climb out of a raised platform onto poles, etc.
Keep the fi berglass booms clean and dry. Foreign
substances on the booms conduct electricity.

2-9 39026-03 02/17VERSALIFT VST-8000/8500/9000/9500-I
RESPONSIBILITIES / SAFETY
Area 1, Boom Tip Area – The boom tip area does
not provide insulation. This area includes everything
past the insulated section decal* on the upper boom.
This includes the upper end of the boom, platform
support, platform(s), controls, and the jib/winch/rope
(when so equipped).
All components at the boom tip area must be
considered to be conductive and electrically
connected, even with an insulated liner in place.
Any contact with a ground and a phase or between
two phase conductors will create a hazard of serious
personal injury or death. Contact between an
energized conductor and any part of the boom tip
will energize the entire boom tip.
When working near an energized conductor, ground
conductor, or other grounded objects, the operator
must use the proper safety equipment (such as
rubber gloves, covers, hot sticks, etc.), maintain
safe approach distances, and follow company work
practices.
Area 2, Upper Boom Insulation Section – This
section provides insulation** between the boom
tip area and earth ground when clean and properly
maintained. On some confi gurations, it is necessary
to extend the boom until the insulated section decal
is visible.
Area 3, Intermediate Structure – This section
does not provide insulation. This area includes
the lower steel portion of the upper boom, knuckle,
and the steel upper portion of the lower boom and
compensation link (when applicable).
Area 4, Lower Boom Insulating Section – (When
so equipped) This section provides insulation**
between the intermediate structure (Area 3) and the
vehicle when clean and properly maintained.
Area 5, Lower Structure – This area does not
provide insulation. This area includes the steel lower
portion of the lower boom and compensation link
(when applicable), turret, lower controls, pedestal,
and the vehicle.
* On VST and T-Series models not supplied with an
upper insulated section decal, the insulated section
begins 11 inches below the center of the platform
pivot.
** Insulation properties are defi ned by ANSI A92.2
WHAT IS INSULATED AND WHAT IS NOT INSULATED
ARTICULATED/TELESCOPIC AND ARTICULATED MODELS

2-10 39026-03 02/17VERSALIFT VST-8000/8500/9000/9500-I
RESPONSIBILITIES / SAFETY
ADDITIONAL SAFETY CONSIDERATIONS
1. Report any unusual occurrence during the
operation of the aerial lift that may require repair
or adjustment.
2. Keep the work space in the truck bed clean and
neat.
3. Avoid parking on soft surfaces. Soft surfaces
may suddenly collapse, shift, or sink beneath
the truck’s weight.
4. There is no insulating value in the fi berglass
platform without a platform liner.
5. No attempt should be made to clean, oil, or adjust
a machine while the machine is in motion.
6. If an aerial lift has set idle for an extended period
(i.e. overnight) or has been recently serviced,
cycle the aerial-lift through it’s full range of
motion several times. This procedure will force
any trapped air out of the hydraulic system. Do
not operate the lift from the platform until this
process is completed. Air trapped in the hydraulic
oil can cause lift movements to be erratic and
unpredictable.
7. Don’t operate any part of the unit (platform,
booms, outriggers, etc.) outside the work-site
barricades into the traffi c lanes. Set up adequate
cones or barricades to mark the boundaries of
the work-site to alert motorists and pedestrians.
8. Only qualifi ed mechanics are authorized to
service the aerial lift.
9. The polyester winch rope is not an insulator. Dirt,
grease, and moisture (humidity) make the rope
conductive.
10. Make a thorough check of the winch rope for
abrasive wear, pulled strands, cuts, and other
defects daily.
11. Replace the winch rope at the fi rst sign of damage
or deterioration. Use only non-conductive rope
of the size and type specifi ed.
12. Avoid shock loads. A shock load is caused by
jerking a line with a load or a sudden change in
rope tension from a light load to a heavy load.
13. Do not contact energized conductors with the
winch line. Contacting the load line with an
energized conductor could create a complete
path for electricity when the rope is extended to
the ground. This could cause death or serious
injury.
14. Avoid using the winch line to wrap or tie an object
for lifting. The hook attached to the end of the
winch line can damage or cut the rope. A sling
or lifting strap is recommended for this purpose.
15. Do not stand in line with a rope under tension. If
the rope should fail the recoil could cause serious
injury to personnel.
16. Inspect the jib-pole assembly to make sure the
various lock pins are secure.
17. Make sure the winch-rope coils are spooling
evenly to avoid clogging the winch or producing
shock loads when lifting a load.
18. Avoid contacting a spray or mist produced by a
high pressure hydraulic leak. This spray or mist
can puncture or become embedded beneath the
skin or contaminate the eyes. These conditions
requires immediate medical attention.
19. Hydraulic oil is fl ammable. Avoid any contact
between hydraulic oil and sources of high heat
or open fl ames.
20. Bodily contact with hot hydraulic oil can cause
serious burns which require immediate medical
attention.

3-1 39026-03 02/17VERSALIFT VST-8000/8500/9000/9500-I
SPECIFICATIONS
GENERAL SPECIFICATIONS
Note: Specifications on units may vary or change
without prior notifications due to option selections.
This section includes a brief description of each of
the major (standard) components.
PLATFORM - The fi berglass platform is 24 in. x 48
in. x 42 in. (0.61 m x 1.22 m x 1.07 m) deep with an
inside and outside step for easy access.
VST-8000/8500/9000-I - The standard platform
capacity is 800 lbs. (360 kg). With the optional
jib/winch installed, the platform capacity is 700 lbs.
(318 kg). A cushioned platform support is provided.
VST-9500-I - The standard platform capacity is 600
lbs. (272 kg). With the optional jib/winch installed, the
platform capacity is 500 lbs. (227 kg). A cushioned
platform support is provided.
PERSONNEL RESTRAINT SYSTEM - A safety
belt or harness and a lanyard are required and can
be supplied by Time Manufacturing Company at an
additional cost. Consult applicable work practices
and regulations to choose between a safety belt and
a harness. The anchor for the lanyard is attached
to the platform.
INDIVIDUAL LOWER CONTROLS - Individual
full-pressure controls at the turret actuate all boom
functions. The lower control station is equipped with
a selector valve to override the upper controls and
serve as the emergency stop from lower controls.
SINGLE STICK UPPER CONTROL - The full-
pressure single stick upper control includes a
safety trigger to prevent inadvertent operation.
The lift movements correspond with control handle
movements. An emergency stop and a tool selector
control are located at the upper controls.
HYDRAULIC PLATFORM ROTATOR - A hydraulic
platform rotator, operated by a control lever, rotates
the platform 180° from one side of the outer/inner
boom assembly, across the end-hung position, to the
other side of the outer/inner boom assembly.
HYDRAULIC PLATFORM LEVELING - A master
and slave cylinder arrangement automatically levels
the platform in all boom positions. This system also
provides hydraulic platform tilt to adjust platform level,
tilt the platform for clean out, or to ease the removal of
an injured operator. The platform tilt can be activated
from the upper and lower controls.
OUTER/INNER BOOM ASSEMBLY- The outer/inner
boom assembly includes an outer boom, telescopic
inner boom, extension system, and hose assemblies.
The outer boom consists of a 12 in. x 14 in. (305 mm
x 355 mm) steel section. The inner boom consists
of a 9-1/4 x 11-1/4 in. fi berglass section and a 10 x
12 steel section. The fi berglass section provides a
108 in. insulation gap (52 in insulation gap for VST-
9500-I only). The inner boom can be easily removed
and disassembled for service and inspection. The
extension system consists of a hydraulic cylinder, two
integral holding valves, and a “cat-track” type hose
carrier housed entirely within the boom assembly.
The hoses routed through the outer/inner boom
assembly are non-conductive and fully contained
within the boom assembly. The outer/inner boom
assembly articulates from 25° +/-2° below horizontal
to 75° +/-2° above horizontal. Actuated by a double
acting cylinder, equipped with two integral holding
valves; the outer/inner boom assembly is off set to
one side to provide easy access to the platform. A
boom support cradle and a boom tie down strap
are included.
LOWER BOOM WITH CHASSIS INSULATING
SYSTEM - Each end of a high strength fi berglass
insert (chassis insulating system) is installed over a
rectangular 12 in. x 14-in. (305mm x 355 mm) high
strength steel section. The steel and fi berglass
sections are bonded with pressure injected adhesive
to fi ll any voids. A compensation link with a fi berglass
section maintains the 24-in. (0.61 m) insulation gap
in all the boom positions. The double acting cylinder,
with an integral holding valve, allows the lower boom
to articulate from horizontal to 88° above horizontal.
CYLINDERS - Both the upper and lower cylinders
are a threaded head-cap design. Both cylinders are
equipped with two integral holding valves to prevent
creep down and to lock the booms in position in case
of hose failure.
TURRET - The 5/8 in (16 mm) thick turret wings are
designed for strength and rigidity. The 1-1/2 in (38
mm) thick turret base plate is machined to provide
a fl at surface to support the rotation bearing.
CONTINUOUS ROTATION - Unrestricted rotation
is accomplished by a hydraulically driven worm and
spur gear with a shear-ball rotation bearing. The
critical bolts holding the lift to the rotation bearing
and the rotation bearing to the pedestal are grade 8
hex head capscrews. These critical bolts are torque
seal marked to provide a quick means of detecting
any turning of the bolt upon inspection.
LUBRICATION - Non-lube bearings are used at all
SPECIFICATIONS

3-2 39026-03 02/17VERSALIFT VST-8000/8500/9000/9500-I
SPECIFICATIONS
pivot points. Only the rotation bearing and rotation
bearing gear teeth require periodic lubrication.
PEDESTAL - The pedestal is rectangular with a
reinforced mounting plate. The top plate of the
pedestal is 1-1/2 in. (38 mm) thick and machined
fl at to support the rotation bearing.
HYDRAULIC OIL RESERVOIR – A 35 gallon (132 l)
hydraulic oil reservoir is built integral to the pedestal.
The reservoir includes an anti-splash baffl e and sight
gauge for quick hydraulic fl uid level checks, and a
return fi lter pressure gauge.
HYDRAULIC SYSTEM - The open-center hydraulic
system operates at 3000 psi (210 kg/cm2) at 10 gpm
(38 lpm). A 10-micron return-line fi lter, mounted
above the hydraulic oil level and inside the pedestal,
can be easily changed without draining the reservoir.
A fi lter gauge with a color-coded range is used
to monitor the condition of the return line fi lter for
replacement. The 100 mesh (149 micron) suction
strainer in the reservoir can be removed for cleaning.
A gate valve, located below the reservoir, prevents
oil loss when the pump is serviced. A magnetic drain
plug attracts metal particles from the oil.
TWO-SPEED MANUAL THROTTLE CONTROL -
Changes the engine/pump speed to give the operator
a choice between slow and normal boom speeds,
and also at slow speed provides reduced fl ow to
operate hydraulic tools. The manual throttle control
is designed to operate only when the truck engine is
running and the master control is activated. An air
cylinder at the platform or a toggle switch at the turret
can be used to energize the manual throttle control.
PAINT - The complete unit is primed and painted
before assembly. The standard color is white
urethane.
HOSES AND FITTINGS - The hoses routed through
the booms are high pressure and non-conductive with
swaged hose end fi ttings. Nylon sleeves are installed
over hoses at points of movement. Reusable fi ttings
can be installed if a hose is damaged.
ENGINE START/STOP - The start/stop circuit has
been designed so the lift cannot be operated unless
the truck ignition switch is in the “RUN” position and
the master control is activated. This feature makes
it diffi cult for unauthorized individuals to operate the
lift when the truck is locked. An air cylinder at the
upper controls and a toggle switch at the pedestal
energize this system.
HYDRAULIC TOOL CIRCUIT AT THE PLATFORM
- This system is designed for open center hydraulic
tools. The tool circuit provides approximately 6 gpm
at engine idle and 10 gpm with the throttle control
engaged. The tool pressure is 2000 psi (140 Bars).
ELECTRICAL INSULATION SPECIFICATIONS -
The outer/inner boom assembly is tested and certifi ed
for electrical work at 46 kv and below in accordance
with ANSI A92.2 requirements. Aerial devices may
be designed and confi gured for gloving work and
tool methods at 46KV and below. The outer/inner
boom assembly is fully insulated even in a retracted
position. The chassis insulating system (lower boom
insert) is also tested according to ANSI A92.2.
LINE-LIFTING SOCKET - Built as part of the platform
support structure, is a vertical line-lifting socket for
3 in. (76 mm) diameter line-lifting attachments. The
socket is automatically leveled with the platform.
OUTRIGGER/BOOM INTERLOCK SYSTEM - The
outrigger/boom interlock option is a feature designed
to prevent the lift from being operated until the
outriggers contact the ground. The interlock also
prevents the outriggers from being retracted before
the aerial lift is properly stored.
SLOPE INDICATORS – Slope indicators are required
on Versalift units and supplied by Time Manufacturing
Co. Slope indicators shall be installed to indicate
the level of rotation bearing relative to the ground.
MANUALS - Two Operator’s Manuals and two
Service Manuals, one Manual of Responsibilities,
and one EMI Safety Manual are included.
OPTION SPECIFICATIONS
Below is a brief description of some of the available
options for the aerial lift.
4-AXIS CONTROL - The 4-Axis controller option
is a full pressure control located at the platform
which consists of a multi-jointed handle control that
actuates the interlock section and four individual
boom function valves.
TRUGUARD - This advanced upper controls isolation
system provides 4” of electrical isolation from the
entire upper controls, including the control dash
panel. This system also includes a protective shield
which helps prevent environmental and work related
contaminants from making direct contact with the
isolating surfaces.
This manual suits for next models
4
Table of contents
Other Versalift Lifting System manuals
Popular Lifting System manuals by other brands
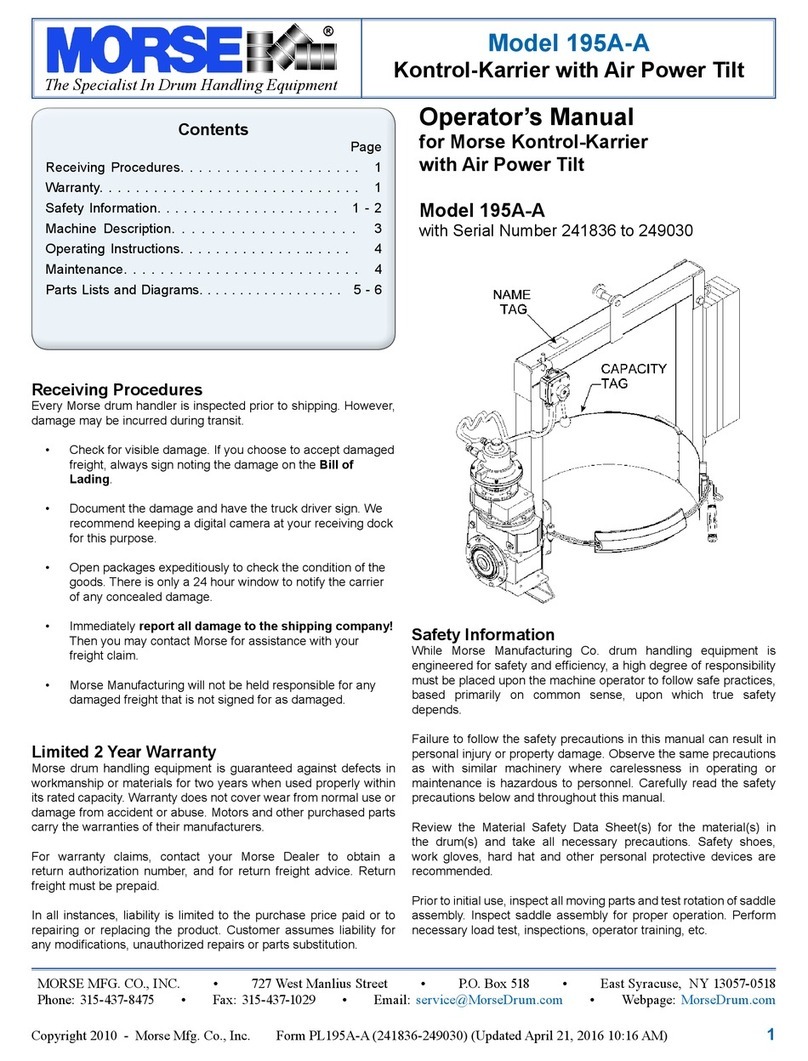
morse
morse 195A-A Operator's manual

MIR
MIR 500 quick start

Blue Giant
Blue Giant LPJ-44 Operator's manual
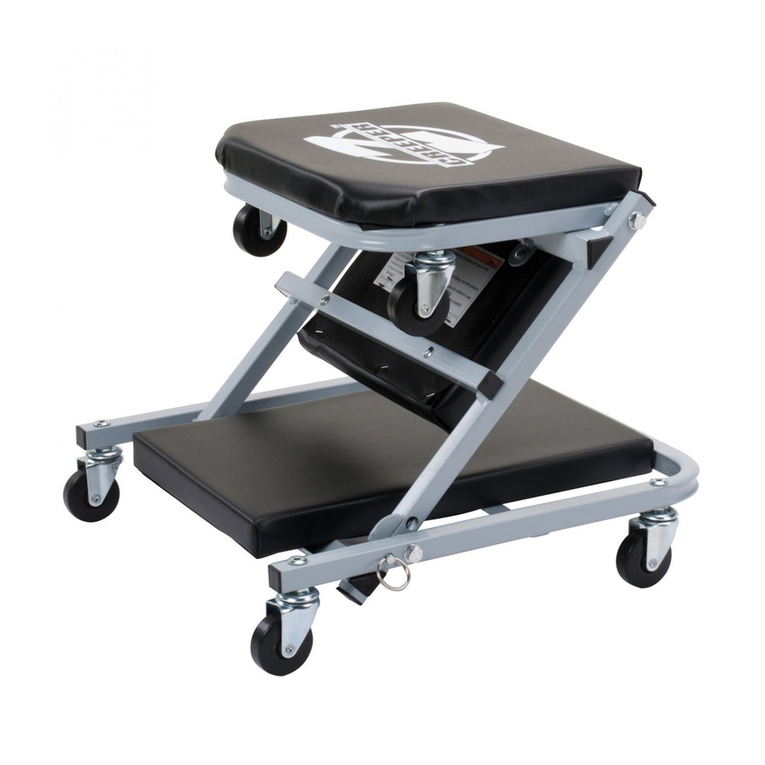
Pro-Lift
Pro-Lift C-2036 Operating instructions & parts manual

Nova Technology International, LLC
Nova Technology International, LLC NAS Series Owner & user manual
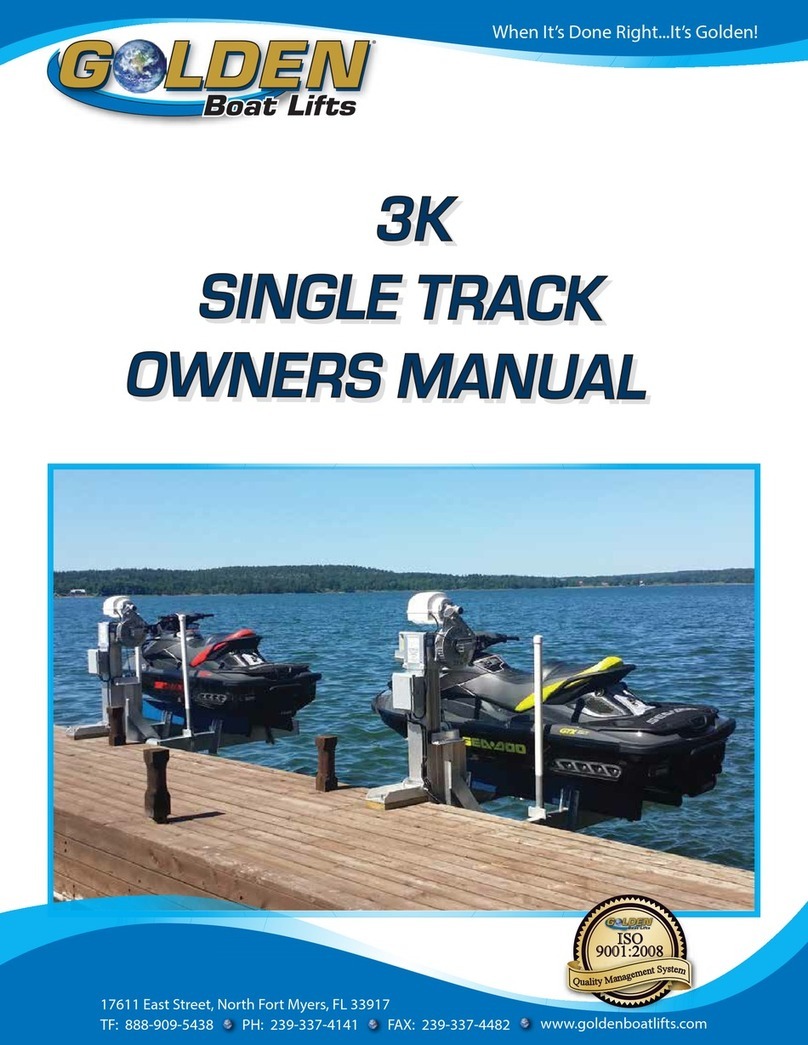
Golden
Golden 3K Single Track owner's manual