VFTech GNOM SUPER User manual

Underwater remotely
operated vehicle for inspections
GNOM SUPER
Operator manual
VFTECH, spol. s r.o.
Vapenicka 24, 971 01 Prievidza, Slovakia
Tel/Fax +421 46 54264 56
https://: WWW.ROV-1.EU
2020 v7

V07/2020
2
TABLE OF CONTENTS
Warning!!!
Voltage on cable 180VDC!
Do not touch the cable in water during operation!
In case of any damage on the cable shield, it must be repaired or changed!
ttention! C power maximum 240V!
1. Description 3
1.1 Purpose 3
1.2 Design 4
1.3 Technical specifications 6
2. User’s anual for operation with GNOM 7
3. Keys and Buttons at the control panel 12
4. Screen odes 17
5. Installation of additional equip ent 18
6. Calibration 19
7. Maintenance operation 20
8. Safety require ents 22
9. Warranty state ent 23
10. Exa ples of odule linking 24
11. Appendix 27

V07/2020
3
1. DESCRIPTION
1.1 PURPOSE
LIST OF ABBREVIATIONS:
Underwater odule
Surface control odule
Protective polypropylene fra e
Hand reel
Coaxial cable
Joystick
Digital video recorder
Co puter
Monitor
Waterproof case
Grabber
Underwater spear gun with laser
Sector sonar
USBL positioning syste
Remotely operated underwater vehicle GNOM is intended for inspection of underwater wrecks
and other objects by video camera.
The device uses modern computer and telecommunication technologies, that make it easy to
handle, compact, light, and inexpensive.
These solutions allowed us to use thin (only 6 mm diameter) and flexible communication cable
for the transmission of data, power and video signals to/from the vehicle. The special Kevlar threads
help to improve the tensile strength of the cable, and to keep the highest degree of stabilization,
very important for inspections. The vehicle has a good maneuverability and can easily turn on the
spot.
High-effective electric motors with magnetic couplings and hi-tech electronics provide high speed of
the GNOM with low power consumption.
One of the most important features of this device is a possibility to operate from PC and via
LAN/Internet.
The GNOM is an underwater helicopter with the video camera,, that moves in any direction
according to the operator instructions.
For updated info, please visit our website www.vftech.sk

1.2 DESIGN
ROV GNOM Super basic complete set
– ROV GNOM Super
– Protective
polypropylene frame
– Hand reel with tether
– Surface
control/power
– L D monitor 15“
– 2x waterproof cases
- Joystick
ROV GNOM Super full complete set + options
– ROV GNOM Super,
– Joystick, –
LCD monitor 15",
sonar, -
USBL positioning system
Main features
•High Resolution
color
•6
thrusters, adjustable speed
•
Slow/fast mode, tilt
•LED lights
•Fle ible thin cable
•Depth gauge,
autodepth mode
•
Heading (compass), autoheading
•
Videote t overlays with graphics
•On screen menu
•
Easy game joystick control
•
Digital data channel
•PC interface, LAN
/Internet web video/control (option
•
All packed in 2 cases, hand carried
V07/2020
1. DESCRIPTION
ROV GNOM Super basic complete set
polypropylene frame
control/power
supply unit with joystick
ROV GNOM Super full complete set + options
– Control box integrated in waterproof case,
–
LCD monitor 15",
– Grabber, - Underwater
speargun with laser,
USBL positioning system
color
video
camera with tilt servo and digital zoom
thrusters, adjustable speed
Slow/fast mode, tilt
mode
autodepth mode
Heading (compass), autoheading
Videote t overlays with graphics
Easy game joystick control
Digital data channel
/Internet web video/control (option
al)
All packed in 2 cases, hand carried
4
–
Hand reel with slip ring,
speargun with laser,
- Sector
camera with tilt servo and digital zoom

The underwater vehicle
consists of
and the back cylinder
. The vertical thrusters
there is a glass dome
for
the
camera.
The composite video
signal from
to the LCD monitor input or another video device.
4 horizontal thrusters
with
clusters of
cylinder. Plastic float
installed
The 6-thruster ROV version has
the
in vertical direction for 45-60
o
. At
In front of every
horizontal thruster
the control panel.
All the electrical parts (the
power supply
camera are installed in the
main aluminium hull.
the vehicle. The connector for
the communication tether
V07/2020
1. DESCRIPTION
consists of
three aluminium cylinders – the front cylinder
. The vertical thrusters
(
and
)
are located between
the
main camera. At the back, there is an
another glass dome
signal from
the high resolution cameras (720 TV lines,
sensitivity 0,1 lux
to the LCD monitor input or another video device.
The active camera
is switched using the controller.
clusters of
LED lights at the front
are
attached to
installed
at the top of the protective frame provides
the
tilt function, that
allows to increase the field of vision
the back of the thursters, there are axes with
screw propellers
horizontal thruster
, there is a cluster of 14 LED lights.
Brightness
power supply
converter, central processing unit,
electronic compass)
main aluminium hull.
The depth
sensor is installed
on the left side at the back of
the communication tether
is at the bottom of the vehicle
5
, the main cylinder
are located between
the cylinders. At the front,
another glass dome
for the back
sensitivity 0,1 lux
) is transmitted
is switched using the controller.
attached to
the sides of the main
the buoyancy.
allows to increase the field of vision
by tilting the vehicle
screw propellers
.
of the lights is adjusted from
electronic compass)
and the
on the left side at the back of
is at the bottom of the vehicle
.

V07/2020
6
1. DESCRIPTION
Two DC motors inserted in the aluminium hulls serve as the thrusters . The rotation is transmitted to the
screw propeller using magnetic coupling disks. One disk is fastened to the motor shaft inside the body, and
the other one to the screw propeller shaft inside the cone-shaped head . The cone-shaped head is filled
up with water and may be removed by operator for cleaning (see manual).
The vehicle is connected with the surface unit via thin cable transmitting power voltage, operating instructions,
data, and video signal from and to the vehicle.
The cable with diameter 6mm is stregthened by the Kevlar threads (breaking effort is 90kg) and the additional
polyehylene shield. The maximum cable length is up to 250m. To counterbalance the weight of the vehicle
and give it neutral buoyancy, the foam polystyrene float is installed to the top of the vehicle. Similar floats can
be put on the cable to change the neutral buoyancy to a little positive. The maximal operating depth of the
vehicle is 200m.
Using the control pads and the joystick, the operator can move GNOM forward-backward, turn to the right –
left, up – down; adjust the thruster speed and the brightness of the lights. All the data are displayed on the
monitor in "TV-text" mode. By pressing one of the buttons on the joystick, the operator can enter the menu to
tune up some of the functions – calibrate the depth sensor and the compass, as well as some other functions.
The "Sony PS" controller is connected to the control and power module installed in a waterproof case,
with built-in 15" monitor. The power supply operates from 100 to 230 VAC or 12 VDC.
1.3 TECHNICAL SPECIFICATION
Speed:
horizontal motion, up to 1,5 m/s
vertical motion, up to 0.5 m/s
(above numbers depend on a length of pooling cable)
Max operating depth 150 m
Power voltage 100-230VAC or 12 VDC
Operating temperature range -5…+45°C
Operating environment humidity, up to 100%
Weight of the vehicle 6 kg
Full weight of the system 25 kg
Dimensions of the vehicle 330x180x160mm
Cable:
diameter 6 mm
length up to 250m
Options:
•Rear camera with LEDs (color or b/w with IR lights)
•Additional lights
•Laser pointers
•Grabber
•Slip ring cable reel
•LCD 8-15" built in case
•Sector sonar Micron, Tritech

V07/2020
7
2. USER’S MANUAL FOR OPERATION
2.1 Deployment
1. Before use, check all parts of the vehicle, especially the propellers, the cable, and the dome. Clean it, if
necessary. Check propeller rotation by finger.
2. Plug the 3-pin plug of the connector to the reel, power and video cables to the monitor.
If you use the built-in monitor, it’s necessary to weaken a clamp before connecting!
Also the AC power cable (if you work from 100-230VAC).
Do not rotate thrusters on air!
Do not switch lights on a full power on air!
Be very careful with cable, do not:
- stand on it
- press it
- twist it.
Voltage on the cable is 180VDC! In case of any damage, you must repair or
change the cable.
2.1.1 NOTE
You cannot connect the GNOM and other devices (accessories) to the mains with the
following problems:
• incorrect wire connections of L and N conductors in the appropriate slot
• without protective earthing conductor
Note. Before use, the operator must always check the correct wiring connections (phase
conductor - L) e.g. by phase tester.

V07/2020
8
2. USER’S MANUAL FOR OPERATION
2.1.2 Checking the RCD
Checking the RCBO (residual circuit breaker with overcurrent protection) must be performed
before any underwater operation at the new location.
• If the requirements of paragraph 2.1.1 are met, connect only the surface module to the
power supply.
• Switch the mains voltage button on the control panel on.
• After 5 seconds, press the "TEST" button on the RCBO. It would immediately lead to a
safe shutdown of the module.
• Switch the mains voltage button on the control panel off. Switch the RCBO on.
• Switch the power supply button on the control panel on again. The RCBO must remain
switched on.
Switch the main 230V switch ON (UP position).
After the power is ON, the message WELCOME appears. GNOM is ready for operation.
If you use GNOM in a sea, you need to add additional weight. Open the plastic pipes underneath the GNOM
and insert metal weights (the best is lead).

2.
USER’S MANUAL FOR OPERATION
3. Operation
Do not rotate the
thrusters on air!
Do not switch the
lights on a full power on air!
Put the vehicle into the water. To start
following buttons
on a joystick
All control functions are
described
#To move the vehicle
Forward/Back
#Slow mode (SLOW). Press
gradually
(25%, 50%, 75%, 100%).
You can adjust the
speed gradually (128 grades)
The direction and speed are
shown
#To move the vehicle
Up/Down
#To tilt
the vehicle, use the
#Jump mode - A
llows to push the vehicle slightly for a distance 30
then stop.
Press
②
to enter
the Jump mode
arrows (
Left/Right, Up/Down
ANALOG
MODE
right joystick
left joystick
left joystick
Click + UP/DOWN
V07/2020
USER’S MANUAL FOR OPERATION
thrusters on air!
lights on a full power on air!
Put the vehicle into the water. To start
the operation, press one of the
on a joystick
:
described
on the drawing below.
Forward/Back
and turn Right/Left, use the
the and adjust the power
(25%, 50%, 75%, 100%).
speed gradually (128 grades)
by
pressing the joystick.
shown
on the monitor.
Up/Down
use the
the vehicle, use the
- press and hold Up/Down
llows to push the vehicle slightly for a distance 30
–
50 cm,
the Jump mode
. To choose the jump direction, press
the
Left/Right, Up/Down
). To adjust the jump power, use the
HOME
right
joystick
left joystick
left joystick
9
USER’S MANUAL FOR OPERATION
50 cm,
the

2. USER’S MANUAL FOR OPERATION
# Simultaneously press
③
+
lights (LOOP : 0% ÷
100%, 100%
simultaneously for
100% brightness
(Simultaneously press
③
+
#Hand mode - control
the GRABBER (if
Press
②
to enter the
Hand mode
( = OPEN / =
CLOSE
#Control the Grabber turn
by the arrows
#To tilt the camera
Up/Down
Press +
simultaneously
# Laser -
switch the laser on/off by pressing
# By the
key switch
# Autodepth mode. Press
①
To change the depth,
use left joystick. Autodepth mode
current depth are shown on
the
#Autoheading
maintains the speed and the direction.
ON/OFF by
the key (version: left joystick to left
OFF ). Select the
forward speed
R 2
L
1
L
2
SELECT
Start
R 1
R 2
V07/2020
2. USER’S MANUAL FOR OPERATION
+
to change the intensity of the front
100%, 100%
÷0% ...). Press
③
+ +
100% brightness
.
+
to adjust the rear lights – if installed)
the GRABBER (if
installed)
Hand mode
.
CLOSE
)
by the arrows
Up/Down
press /
simultaneously
, to return the camera to the initial
position.
switch the laser on/off by pressing
③
+
the active camera (front/back)
①
to fix the vehicle at the depth you need
use left joystick. Autodepth mode
status and the
the
monitor.
maintains the speed and the direction.
Switch
the key (version: left joystick to left
– ON, to right
forward speed
, then switch the autoheading on.
R
1
R
1
R 2
R 2
L
1
L
2
SELECT
10
2. USER’S MANUAL FOR OPERATION
position.

V07/2020
11
2. USER’S MANUAL FOR OPERATION
# Press
④
to select the SCREEN MODE :
Mode1 or Mode2 or Mode3 (see below)
# You can choose the menu language (Russian/English).
5. Finishing the operation
To finish the operation, switch the power OFF, then disconnect the cables and wind them up into
the reel.
Try to avoid nods and twisting of the cable.
After operation, clean the propellers and motor shafts, and wash the vehicle in fresh water.
Sleep mode (Power Saving Mode)
In order to save the power and extend the battery life, the wireless joystick has the power saving
system. The joystick enters the sleep mode (power saving mode) under the following conditions:
A. There is no operation within 30 seconds after the connection between the controller and the
receiver.
B. The pause between individual operations lasts for more than 5
minutes.
To wake from the sleep mode, press one of the following buttons:
ANALOG
HOME
MODE

V07/2020
12
3. KEYS AND BUTTONS AT THE CONTROL PANEL

V07/2020
13
3. KEYS AND BUTTONS AT THE CONTROL PANEL
Alternative without a computer

V07/2020
14
3. KEYS AND BUTTONS AT THE CONTROL PANEL
Alternative with computer

V07/2020
15
3. KEYS AND BUTTONS AT THE CONTROL PANEL
Alternative with external computer

V07/2020
16
3. KEYS AND BUTTONS AT THE CONTROL PANEL
For furt er information about t e controls and function description, see t e
attac ed LYYN manual.

V07/2020
17
4. SCREEN MODES/OVERLAYS

V07/2020
18
5. Installation of additional equipment
-Installing the manipulator
When transporting the system, the manipulator is mounted in transport position. To install the manipulator in
the working position, proceed as follows:
Loosen the two screws on the collar of fastening arm frame (see Appendix).
Move the manipulator (grabber) forward. Set the way that the joint of the manipulator overlaps with the
fastening collar border.
In the working position, the manipulator arm should be visible to camera, when tilted by 30°.
Tighten the screws on the clamp.
joint

V07/2020
19
6. CALIBRATION
To enter this ode, you have be in the start ode ( essage WELCOME on the screen). To calibrate the depth
sensor and co pass, press and hold key
③
for 7-8 sec only while the message WELCOME shows. Message
"Calibration mode" appears. To select the function, use the arrows on the left. To enter the function, use the
key
②
on the right.
-“Set urrent depth as 0”. To alibrate the depth sensor, set 0 when GNOM is on the surface. To finish
the calibration, press
②
to confir the 0 depth. We reco end to set the 0 depth 5 inutes after
turning the power ON.
-“Compass Calibration”. Set by the manufa turer. Only perform, if it works in orre tly.
Calibration pro edure
:
1. Put the GNOM on flat surface away fro etal objects, with front ca era pointing North.
2. Press
②
to start the calibration
3. Slowly turn the GNOM, clockwise, around own axis. Turn at least two ti es.
4. Press
②
) to finish the calibration.
-“Joysti k for left-handler”. Unavailable.
-
“Camera olor adjust”. Unavailable.
-
“Max verti al power”. Set up the axi u power of vertical thrusters in %.
-
“Max horizontal power” Set up the axi u power of horizontal thrusters in %.
-
“Max straight jump power”. Set up the length of the straight ju p
-
“Date/Time Setup”. Set up the date and ti e.
-
“Video systems”. Select PAL or NTSC.
-
“Перейти на Русский”. Select the language (Russian or English).
-
“- Bereg Vx.xxx -” and “- Bort Vx.xxx -” software version.
To exit the calibration enu, set the cursor to Exit and press Enter (right key ②).

V07/2020
20
7. MAINTENANCE OPERATION
To maintain the vehicle, always perform the following steps:
•clean the propellers from algae, sand and mud
•rinse the vehicle in the fresh water after using in the sea
•inspect the cable after the operation - in case of any damage, the cable must be
repaired or changed
•check the magnetic disk coupling regularly
•use the silicone oil spray to lubricate the propeller shafts every time after diving. Oil
must get inside the conical heads of motors. See appendix position 96, 147, 217 of
thruster assembly.
•avoid nods and twists on the cable
Within the certificate of warranty, the bond (joint) maintenance manual is included.
Use it only in case of emergency, if the standard maintenance is insufficient.
Before this service, consult technical problems in our company on email address:
Attention:
In case of non-professional action and damage of any part, the consecutive service in our
company will be charged.
Table of contents
Other VFTech Analytical Instrument manuals
Popular Analytical Instrument manuals by other brands

Bosch
Bosch Professional GIC 12V-4-23 C Original instructions
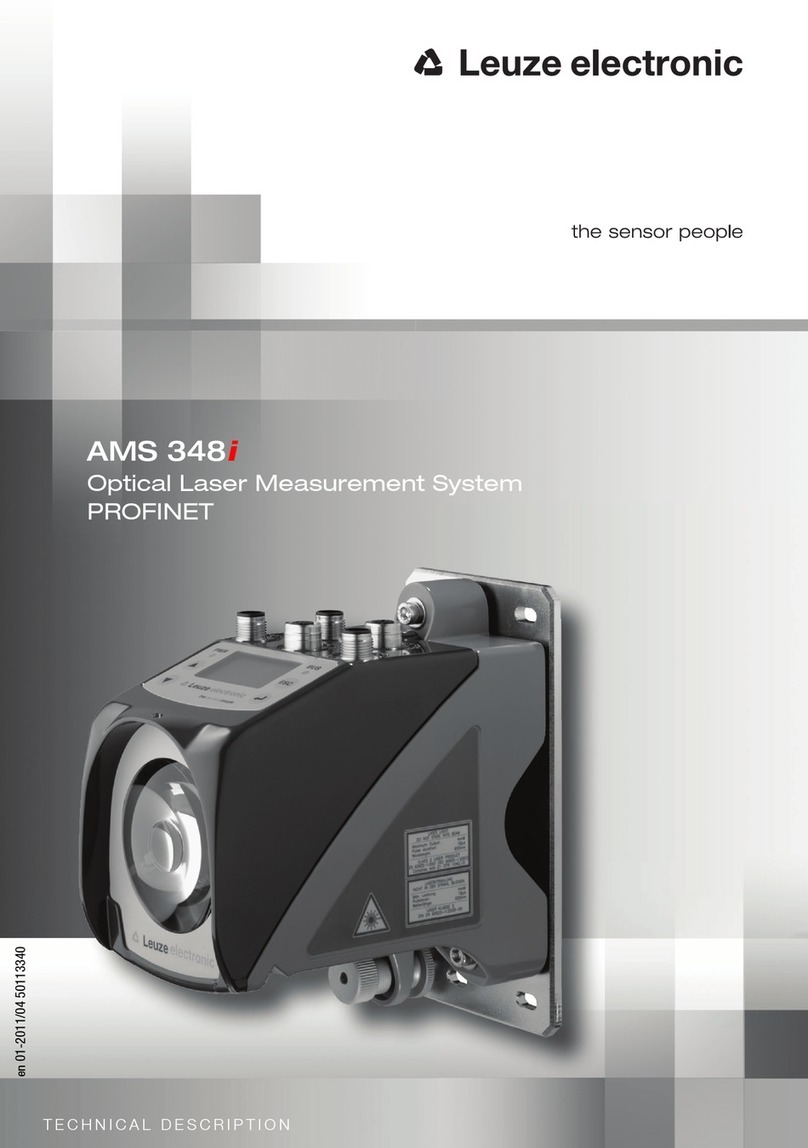
Leuze electronic
Leuze electronic AMS 348i manual

Dewetron
Dewetron TRIONet Technical reference manual

Teledyne
Teledyne 3000ZA operating instructions
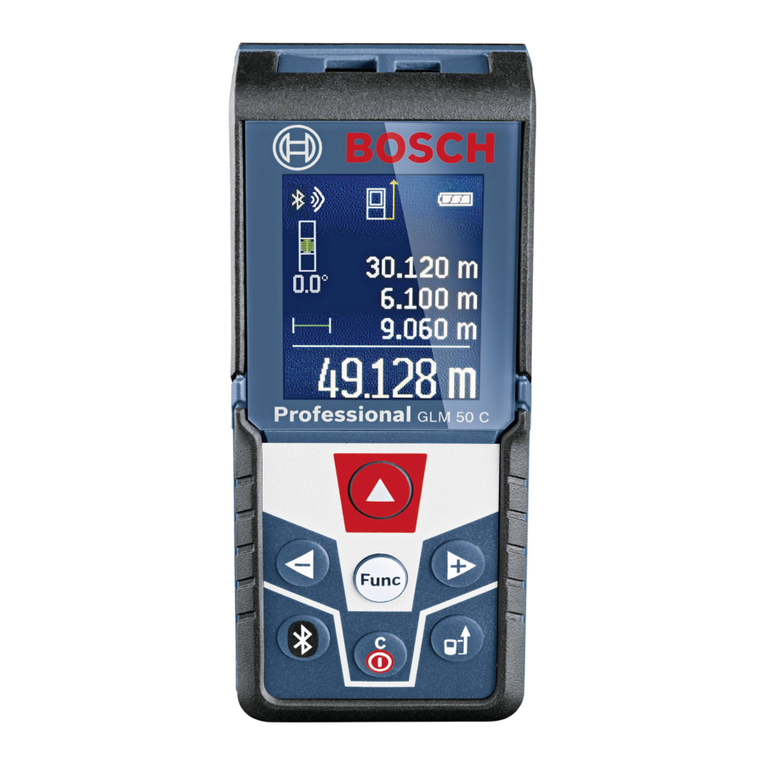
Bosch
Bosch GLM 50 C Professional Original instructions
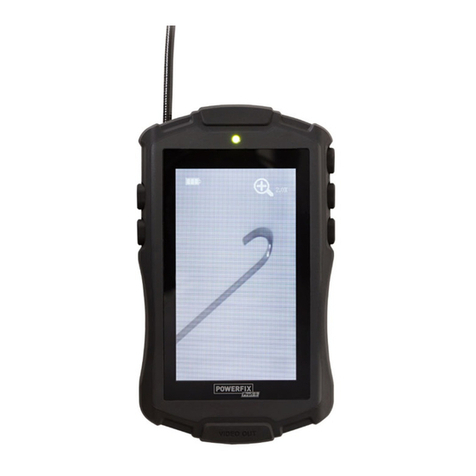
Powerfix Profi
Powerfix Profi PEKK 4.3 A1 Operating instructions and safety instructions