ViscoTec preeflow eco-DUO450 Manual

OPERATION &
MAINTENANCE MANUAL
eco-DUO450

TABLE OF CONTENTS
2 / 36 INST-002738 / Aeco-DUO450
1 Introduction ...................................................................................................... 4
1.1 Delivery package ..................................................................................... 4
1.2 Incoming inspection ................................................................................. 5
2 Safety ................................................................................................................ 6
2.1 Explanation of symbols used ................................................................... 6
2.2 Intended use ............................................................................................ 7
2.3 Personnel................................................................................................. 8
2.3.1 Operators..................................................................................... 8
2.3.2 Maintenance staff ........................................................................ 8
2.4 Informal safety precautions...................................................................... 8
2.5 Preventing damage to equipment............................................................ 9
2.6 Organisational safety measures .............................................................. 9
2.7 Residual risks......................................................................................... 10
2.8 Transport and storage............................................................................ 11
3 Product description ....................................................................................... 12
4 Operation ........................................................................................................ 13
4.1 Initial commissioning.............................................................................. 13
4.1.1 Dismantling the dispenser ......................................................... 13
4.1.2 Installing the stator..................................................................... 15
4.1.3 Reassembling the dispenser ..................................................... 16
4.1.4 Connecting the dosing unit to the drive unit............................... 17
4.1.5 Mounting sensors for monitoring dosing pressure..................... 18
4.1.6 Feeding material and bleeding the dispenser for the first time .. 19
4.1.7 Calibration.................................................................................. 20
4.2 Switching on, starting dosing process.................................................... 20
4.3 Recommendations for problem-free operation ...................................... 21
4.4 Switching off, ending dosing process..................................................... 22
4.5 Decommissioning................................................................................... 23
4.6 Re-commissioning ................................................................................. 23

TABLE OF CONTENTS
3 / 36INST-002738 / A eco-DUO450
5 Maintenance ................................................................................................... 24
5.1 Maintenance intervals............................................................................ 24
5.2 Troubleshooting ..................................................................................... 25
5.3 Stator change......................................................................................... 26
5.4 Dismantling before cleaning................................................................... 27
6 Cleaning .......................................................................................................... 28
7 Spare parts ..................................................................................................... 29
7.1 Item list of the spare parts...................................................................... 29
7.2 Overview drawing of the spare parts ..................................................... 31
8 Technical specifications................................................................................ 32
8.1 Installation declaration ........................................................................... 32
8.2 Technical data........................................................................................ 33
8.3 Materials used........................................................................................ 34
8.4 Dimensions ............................................................................................ 34
9 Disposal .......................................................................................................... 35
10 Accessories .................................................................................................... 35

4 / 36 INST-002738 / Aeco-DUO450
1Introduction
Dear customer,
We are delighted that you have decided to purchase a ViscoTec product. We have no doubt
that this product will meet all your requirements. We wish you trouble-free and successful
operation.
The dosing system consists of the eco-DUO450 dispenser and the eco-
CONTROL EC200 DUO dosing control unit or the plug´n´mix dosing control unit.
The eco-DUO450 dispenser is described in this operation manual. A separate operation and
maintenance manual is enclosed with the dosing control unit.
1.1 Delivery package
The scope of supply includes:
• 1 dosing unit (A)
• 2 stators (B)
• 2 eco-PEN450 drive units (C) with
connection cable (1.5 m)
• 1 assembly aid (D)
• 2 screwdriver (E)
• 2 allen wrench (F)
• 1 calibration adapter (G)
• 1 fastening set (2 rear plates) (H)
• 1 mixer set (3 static mixers) (I)
• 1 Operation & maintenance manual
Fig. 1
eco-PEN330
eco-PEN330
B
A
D
G
I E
F
H
C
INTRODUCTION

5 / 36INST-002738 / A eco-DUO450
1.2 Incoming inspection
Damage in transit can lead to malfunctions, and consequently to personal injury and damage
to property. Damaged components must not be put into operation.
Check the delivery immediately on receipt for damage in transit and damage to the
packaging. Check that the delivery is complete according to the enclosed delivery note.
Make sure you have not left any part of the delivery in the packaging.
Compensation for damage during transport may be claimed only if the carrier is notified
immediately.
INTRODUCTION

6 / 36 INST-002738 / Aeco-DUO450
2Safety
2.1 Explanation of symbols used
The following symbols are used in this manual:
The following notices indicate safety instructions and must be followed:
This manual is structured so that text and the related figure are on the same page as far as
possible. In this way the information can be understood quickly. If reference is made to a
component in a figure, the part has a key number.
Work step
• List
Fig. 1 Legend number, reference to a figure
* Reference to a comment
COMMAND Designations of buttons/switches, menu items and input dialogs
DANGER
indicates a hazardous situation which, if not avoided, will result in death or serious injury.
WARNING
indicates a hazardous situation which, if not avoided, may result in death or serious injury.
CAUTION
indicates a hazardous situation which, if not avoided, may result in minor injury.
NOTE
indicates a technical tip to avoid damage to property or equipment.
SAFETY

7 / 36INST-002738 / A eco-DUO450
2.2 Intended use
The eco-DUO450 dispenser is used to feed and precisely dose viscous materials.
The dispenser is controlled using the eco-CONTROL EC200 DUO dosing control unit or the
plug´n´mix dosing control unit.
Check the chemical resistance of the materials that are in contact with the material before
commissioning. Information on the materials can be found in the order confirmation or in
Section 8.3 “Materials used” (page 34).
No liability can be accepted for damage caused by failure to observe this operation manual
or due to a lack of maintenance or checks.
Misuse
Any use other than the stipulated intended use shall be considered as misuse.
This includes
• use outside the permissible operating limits
• use in explosive environments
• use underground
• use outdoors
Misuse also includes the following actions carried out without the explicit written approval of
the manufacturer:
• Conversions and/or extensions
• Use of non-original spare parts (e.g. rotor)
• Repairs carried out by unauthorised companies or persons
• Use of non-approved materials
Misuse is not permissible, and will result in voiding of guarantee, warranty and liability claims.
SAFETY

8 / 36 INST-002738 / Aeco-DUO450
2.3 Personnel
The operating organisation shall ensure that only appropriately qualified and authorised
personnel work on this machine. It is responsible for ensuring that operators and
maintenance staff possess the necessary qualifications. Personnel must be at least 15 years
old.
All personnel working with or on the machine must have read and understood this
operation manual.
The operating company shall document the operators' and maintenance staff's
acknowledgement of this manual, and shall ensure their compliance with it by means of
regular training.
2.3.1 Operators
Before starting work, the personnel assigned as operators must be adequately instructed
regarding the nature and scope of their duties and the potential risks. Training shall be
conducted on a regular basis (at least once a year). Training shall be conducted after any
technical modifications.
2.3.2 Maintenance staff
The maintenance and repair staff must be authorised and
• adequately trained for the relevant activities
• familiar with and comply with the applicable technical rules and safety regulations
Competent personnel are persons who, by virtue of their training, experience and knowledge
of the relevant requirements, standards and safety regulations, can carry out the necessary
activities while recognising and avoiding potential hazards.
2.4 Informal safety precautions
The following documents must be read, understood and followed. They must always be
available at the machine's operating location, and must be kept in legible condition:
• The operation manual for this product
• Generally applicable and local accident prevention and environmental protection
regulations
• Safety data sheets for the conveyed materials, as well as for any cleaning products or
lubricants being used
SAFETY

9 / 36INST-002738 / A eco-DUO450
2.5 Preventing damage to equipment
In order to prevent damage to equipment and to ensure precision dosing, note that
• the dispenser must never be operated without material (the stator will be destroyed)
• the material inlet (feed) and the material outlet must never be closed during operation
• the material outlet (e.g. dosing needle or mixer) must not be damaged or blocked
• the dispenser is operated with a positive feed (inlet pressure)
• there is adequate inlet pressure when conveying highly viscous material
• when pumping without a positive feed (inlet pressure), no dry running or cavitation of the
dispenser occurs
• the direction of rotation of the drive is always the same as the direction of flow of the
dispenser
• the specifications in the product data sheet for the material are observed and adhered to
2.6 Organisational safety measures
The necessary personal protective equipment must be provided by the operating
organisation. Personal protective equipment must be worn when carrying out all work and
procedures.
To ensure the provision of suitable personal protective equipment, the safety data sheet for
the conveyed material must be observed. Specifications for e.g. cleaning products and
lubricants must also be checked and observed.
All personal protective equipment must be checked to ensure it is working properly before
starting work.
Eye protection Hand protection Body protection Foot protection
SAFETY

10 / 36 INST-002738 / Aeco-DUO450
2.7 Residual risks
Thorough training, observance of the operation manual and compliance with safety
regulations are key to permanently accident-free operation.
The following residual risks may occur when operating this machine:
WARNING
Material hazardous to health
The conveyed material may contain constituents which are hazardous to health.
Such constituents may cause serious acute or chronic harm to health if they come into
contact with skin, are inhaled or swallowed.
• Always wear appropriate protective equipment
• Observe the specifications in the safety data sheet for the material
WARNING
Risk of injury from moving components
The machine is driven by an electrical drive unit. These generate very high forces.
Touching the components during operation may result in serious injuries.
• Do not operate the machine unless there is unrestricted visual contact with the moving
component
• There must be no persons or foreign objects in the danger area
WARNING
Pressurised material
Depending on the setting of the machine, the material is conveyed under very high
pressure. If the delivery rate is not adapted to the dosing needle being used,
unwanted spraying of the material might occur. This may result in serious injury.
Defective components can also cause spraying.
• Shut down the machine immediately
• The leak must be repaired by qualified maintenance staff before operation is re-started
SAFETY

11 / 36INST-002738 / A eco-DUO450
2.8 Transport and storage
The following ambient conditions must be observed for transportation and storage:
• Temperature within the range -10 °C to +40 °C (263 K to 313 K)
• Relative air humidity less than 60 % (non-condensing)
• Uniform room climate
• Dry and free of dust
• No exposure to direct sunlight
• No aggressive, corrosive substances (solvents, acids, alkalis, salts, etc.) in
the environment
For storage always remove the stator and store separately (at 15–20 °C).
CAUTION
Splashing material
During initial commissioning and after being refilled, air bubbles in the material could
cause an uncontrollable spraying from the conveying area. This may result in injury.
• Always wear appropriate protective equipment
• Fully bleed the system before start of production
CAUTION
Pointed dosing needle
Depending on its size, the dosing needle can be very thin and pointed.
Carelessness during assembly work can lead to needle stick injuries.
• Carry out assembly work with appropriate care.
SAFETY

12 / 36 INST-002738 / Aeco-DUO450
3Product description
The dispenser has been developed and tested for precision dosing of materials ranging from
low to high viscosity with extremely high repeat accuracy.
preeflow dispensers are positive displacement pumps. The conveying elements comprise a
rotating part, the "rotor", and a stationary part, the "stator". The rotor, which is in the form of
a type of knuckle thread, rotates inside the stator, which has one more thread turn and twice
the pitch length of the rotor. As a result, conveying areas are produced between the stator
and the rotor rotating inside the stator. The rotor also moves radially within the stator.
The conveying spaces move forward continuously due to the movement. The flexible shaft
used to drive the rotor compensates for the eccentric movement of the rotor and is completely
maintenance-free.
The sealing effect of the conveying elements of the dispenser is dependent on the viscosity
and pressure.
Since the direction of flow is reversible, the material can be sucked back to allow a clean
thread break.
The dispenser can be dismantled very quickly.
Together with the eco-CONTROL EC200 DUO dosing control unit, the dispenser forms a
dosing system which is typically installed in a dosing station. The dosing control unit controls
the required parameters (e.g. dosing quantity, dosing speed, etc.).
PRODUCT DESCRIPTION

13 / 36INST-002738 / A eco-DUO450
4Operation
4.1 Initial commissioning
All activities described below may only be carried out by qualified staff.
When delivered, the stator is not installed so as to avoid bearing damage to the elastomer of
the stator.
4.1.1 Dismantling the dispenser
Remove the 2 screws (9).
Remove the locking plate (11) and eccentric ring (10).
Remove the 4 screws (9).
Remove the centring cover (8).
Tip: If the eccentric ring (10) cannot be easily removed (stuck with material), then
• use a screwdriver to lever it up at the recesses (C), or
• evenly screw the screws (9) into the threaded holes (D) to press it off
9
911 10
8
9
9
D
C
Fig. 2
OPERATION

15 / 36INST-002738 / A eco-DUO450
On both dispenser halves perform
Remove screws (6).
Remove the end piece (5).
4.1.2 Installing the stator
On both dispenser halves perform
Plug the star-shaped coupling (22) into the rotor assembly seal housing (1).
Plug the assembly aid (25) into the rotor assembly seal housing (1).
Coat the rotor (26) with material or a suitable lubricant.
Turn the stator (4) in the correct position (see detailed view) on the rotor (26) until the
dowel pin (7) begins to dip into the keyway (3).
Lightly press the stator towards the pump housing (2) and turn the assembly aid (25) in the
direction of the arrow until the stator (4) has been guided into the pump housing (2).
Uncouple the assembly aid (25).
Fig. 4
6
5
Fig. 5
X
Y
4
26 3
22
2
25
1
11
X
Y
7
X
4
OPERATION

16 / 36 INST-002738 / Aeco-DUO450
4.1.3 Reassembling the dispenser
For reassembly, the work steps outlined in Section 4.1.1 (page 13) are carried out in reverse
order.
When doing this, observe the following
Join the end piece (5) and the pump housing (2) in parallel so that the dispensers can be
assembled suitably to each other.
Tighten the screws (6).
NOTE
Carry out the assembly on an even surface.
Do not exceed a tightening torque of 0.35 Nm when mounting the screws.
Fig. 6
5
2
6
OPERATION

17 / 36INST-002738 / A eco-DUO450
4.1.4 Connecting the dosing unit to the drive unit
Screw the set screws (21) into the thread so that they do not protrude into the coupling area.
Danger of damage to the fit.
Attach the star-shaped couplings (22) onto the coupling of the drive units (A).
Set the anti-rotation device (23) in the correct position relative to the dispenser.
Fully assemble the dispenser with the drive units (A).
Lightly screw in the set screws (21) to centre the drive units in the correct position.
Fig. 7
21 22
23
22
21
21
A
23
OPERATION

18 / 36 INST-002738 / Aeco-DUO450
4.1.5 Mounting sensors for monitoring dosing pressure
Remove the seals (14) from the adapters (13) and mount on the sensors (37).
Mount the sensors (37) by hand together with the seals (14) using the installation
wrench provided.
NOTE
The sensor cables must not be twisted during assembly!
The surface of the sensors (37) is extremely sensitive. Do not bring into contact with
sharp objects!
37
37
13
13
14
14
Fig. 8
OPERATION

19 / 36INST-002738 / A eco-DUO450
4.1.6 Feeding material and bleeding the dispenser for the first time
Connect the material supply (feed line, cartridge) to the material inlet (B) of the dispenser.
Bring the eco-DUO450 into a vertical position.
Position the static mixer (24) and lock in place.
On both dispenser halves perform
Tip: Connecting a hose to the mixing pipe can protect the eco-DUO450 from being wetted
with the material.
* When filling for the first time, the blocking medium is first removed from inside the dispenser
(stator).
Pressurise the material.
Connect the drive unit to the power supply
and run it slowly until material escapes
from the static mixer (24) without
bubbles.*
Unscrew the bleed screw (27) and sealing
washer (28) to bleed.
Tighten the bleed screw (27) and the
sealing washer (28) again.
Remove leaking material with a cloth.
NOTE
When cleaning the dispenser, never use the same cloth for both materials,
as the components will react.
B
B
24
28 27
C
Fig. 9
OPERATION

20 / 36 INST-002738 / Aeco-DUO450
4.1.7 Calibration
To obtain a precise dosing result, the dosing quantity must be calibrated. This is performed
using the eco-CONTROL EC200 DUO dosing control unit. The exact procedure can be found
in the dosing control unit manual.
4.2 Switching on, starting dosing process
Daily at the start of the shift / when starting work, perform the activities as described in
Section 5.1 “Maintenance intervals” (page 24).
Start supply of material to the dispenser.
If present, remove cover.
Switch on the dosing control unit.
Dose the individual components (in manual operation) from the mixing head without static
mixer. Use the calibration adapter (35) for this.
Check whether both components escape without bubbles and that the outlet opening are not
blocked or stuck together.
Check the dosing quantity of each of the two components in order to guarantee a consistent
dosing result. If there are deviations, dosing must be calibrated. The exact procedure can be
found in the dosing control unit manual. The result of the check must be recorded together
A calibration adapter (35) is available for calibrating
the dispenser. It is mounted on the outlet openings.
Remove the static mixer.
Unscrew the screws (9) in the locking plate (11).
Mount the calibration adapter (35).
Perform calibration according to the dosing
control unit operation manual.
Dismantle the calibration adapter (35).
Tighten the screws (9) and locking plate (11).
Position the static mixer.
NOTE
The supply of material to the dispenser must be ensured before dosing starts.
Dry running may destroy the stator.
Fig. 10
35
11
99
OPERATION
Table of contents
Popular Measuring Instrument manuals by other brands
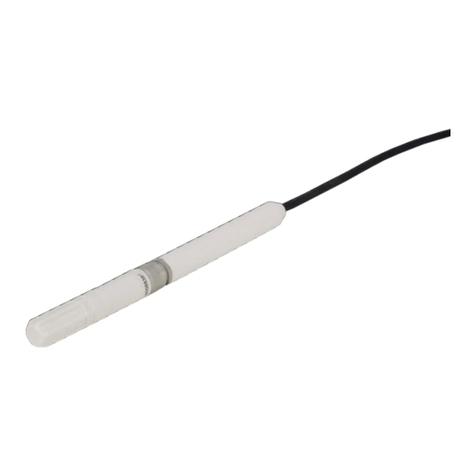
Campbell
Campbell HC2S3 instruction manual
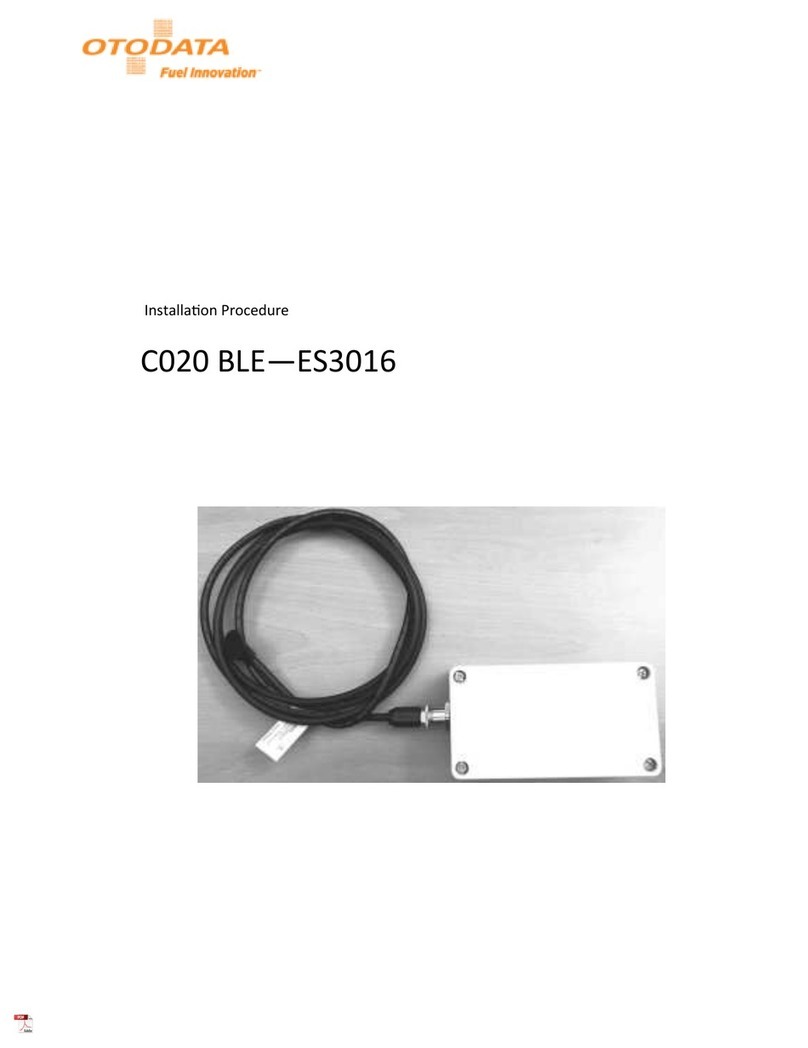
Otodata
Otodata C020 BLE-ES3016 INSTALLATION PROCEDURE

Eversan
Eversan 9658 instruction manual
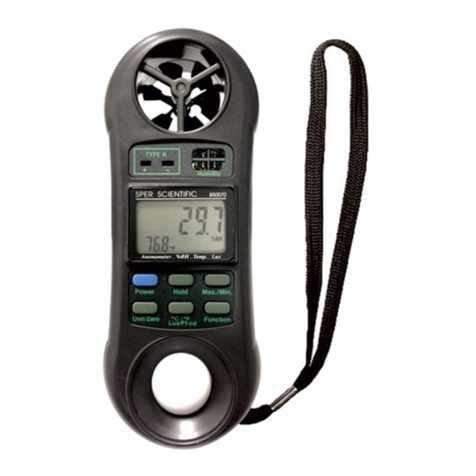
Eastern Energy
Eastern Energy 850070 instruction manual
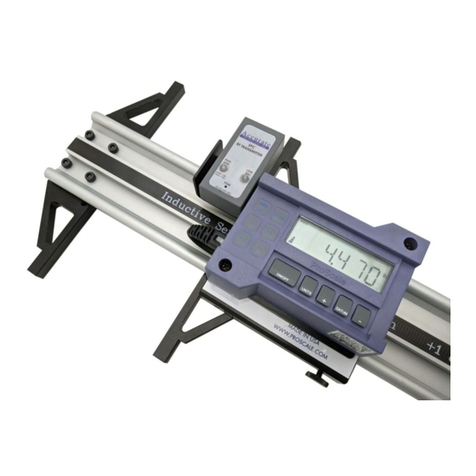
Accurate Technology
Accurate Technology ProPanel-HD General instruction manual
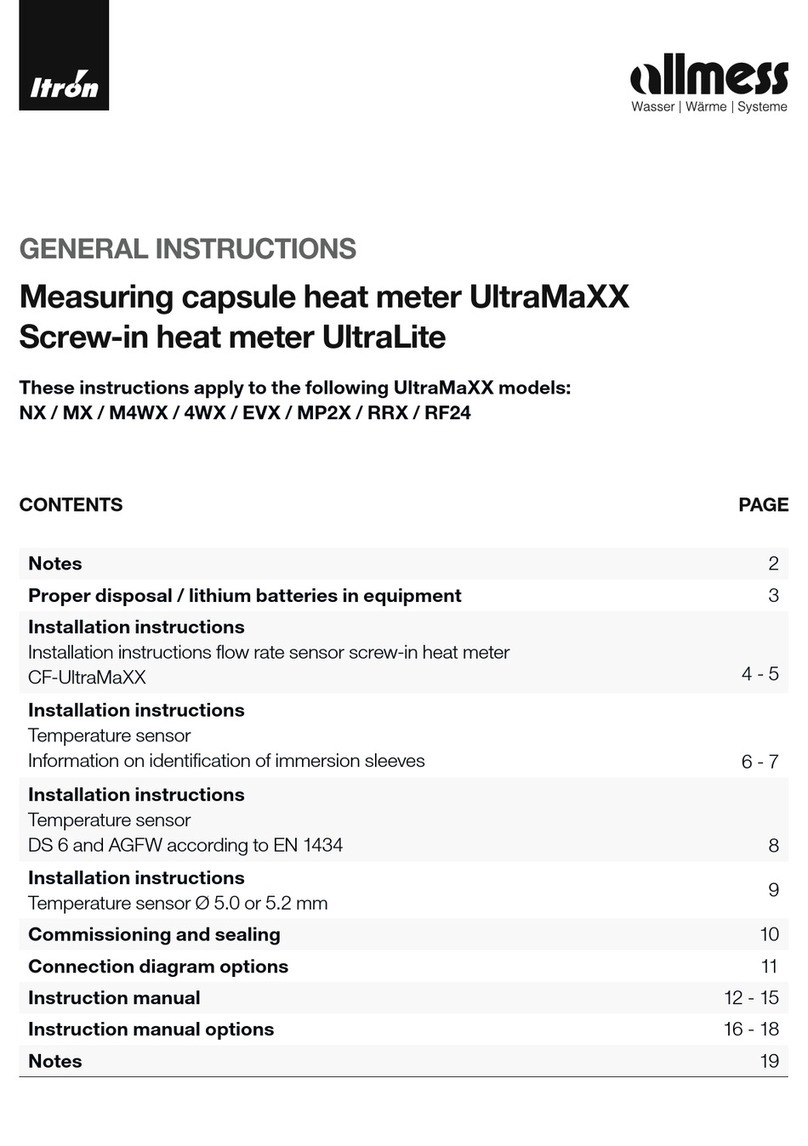
Allmess
Allmess Itron UltraLite General instructions