Vishay P3 User manual

March 2004 130-000109
Model P3
Strain Indicator
And Recorder
Instruction Manual
Vishay Micro-Measurements
P.O. Box 27777 Raleigh, NC 27611 USA
Telephone: (919) 365-3800
Facsimile: (919) 365-3945
www.vishaymg.com

© Copyright 2003-2004 Vishay Micro-Measurements Inc. Printed in USA
All Rights Reserved
TABLE OF CONTENTS
TABLE OF CONTENTS..........................................................I
1DESCRIPTION................................................................ 2
1.1 GENERAL ................................................................. 2
1.2 FUNCTIONAL FEATURES ..................................... 3
2SPECIFICATIONS.......................................................... 4
2.1 INPUT CONNECTIONS .................................................. 4
2.2 BRIDGE CONFIGURATIONS .......................................... 4
2.3 DISPLAY...................................................................... 4
2.4 DATA CONVERSION..................................................... 4
2.5 MEASUREMENT RANGE/RESOLUTION ......................... 5
2.6 MEASUREMENT ACCURACY ........................................ 5
2.7 GAGE FACTOR CONTROL ............................................ 5
2.8 BALANCE CONTROL .................................................... 5
2.9 BRIDGE EXCITATION ................................................... 5
2.10 COMMUNICATION INTERFACE ..................................... 5
2.11 DATA STORAGE .......................................................... 5
2.12 SHUNT CALIBRATION .................................................. 5
2.13 ANALOG OUTPUT........................................................ 6
2.14 POWER ........................................................................ 6
2.15 OPERATIONAL ENVIRONMENT .................................... 6
2.16 CASE ........................................................................... 6
2.17 SIZE &WEIGHT........................................................... 7
3FRONT PANEL............................................................... 8
3.1 USB INTERFACE ......................................................... 8
3.2 MEMORY CARD SLOT ................................................. 9
3.3 INPUT CONNECTORS.................................................... 9
3.4 LCD DISPLAY ........................................................... 10
3.5 KEYPAD .................................................................... 10

II
3.6 POWER CONNECTOR ................................................. 10
3.7 ANALOG OUTPUT CONNECTOR ................................. 10
4OPERATION ................................................................. 11
4.1 GETTING STARTED .................................................... 11
4.2 POWER UP................................................................. 11
4.3 INPUT CONNECTIONS ................................................ 12
4.3.1 Quarter Bridge Connections............................. 12
4.3.2 Half Bridge Connections.................................. 13
4.3.3 Full Bridges and Transducers........................... 13
4.4 OPERATIONAL MODES .............................................. 14
4.4.1 Run Mode Operation........................................ 14
4.4.2 Command Mode Operation.............................. 18
4.5 MENU COMMANDS.................................................... 18
4.5.1 Main Menu....................................................... 18
4.5.2 Select Channels Menu...................................... 19
4.5.3 Bridge Type Menu ........................................... 20
4.5.4 Gage Factor/Scaling Menu............................... 23
4.5.5 Recording Menu............................................... 27
4.5.6 Balance Mode Menu ........................................ 28
4.5.7 Shunt Calibration Menu ................................... 30
4.5.8 Options Menu................................................... 31
4.5.9 Display Options Menu ..................................... 32
4.5.10 Output Options Menu....................................... 33
4.5.11 Save Setup Option............................................ 34
4.5.12 Clock Options .................................................. 34
4.5.13 Advanced Options Menu ................................. 35
4.5.14 Calibrate System .............................................. 35
4.5.15 Erase MMC ...................................................... 39
4.5.16 Poisson’s Ratio................................................. 40
4.5.17 Factory Defaults............................................... 40
4.5.18 Version ............................................................. 40
5BATTERY REPLACEMENT ...................................... 41

III
6SOFTWARE OPERATION.......................................... 42
6.1 OVERVIEW ................................................................ 42
6.2 34
12
SELECT CHANNELS........................................... 44
6.3 BRIDGE TYPE ................................................... 45
6.4 KGAGE FACTOR/SCALING ................................... 46
6.5 POWER............................................................. 47
6.6 MENU MENU .............................................................. 48
6.7 RECORD............................................................ 49
6.8 BALANCE .......................................................... 52
6.9 CALIBRATE ....................................................... 54
6.10 BACKLIGHT ...................................................... 55
6.11 LOADING/SAVING SETUP INFORMATION ................... 56
6.12 TRANSFERRING DATA ............................................... 57
6.13 UPGRADING FIRMWARE ............................................ 59

- 1 -
Model P3 Strain Indicator and Recorder

- 2 -
1 DESCRIPTION
1.1 GENERAL
The Model P3 Strain Indicator and Recorder is a portable, bat-
tery powered precision instrument for use with resistive strain
gages and strain-gage-based transducers.
The Model P3 accepts full- half- and quarter-bridge inputs; all
required bridge completion components for 120-, 350-, and
1000-ohm bridges are supplied. The Model P3 utilizes tool-free
input connections, and is dust and moisture-resistant.
Operation of the Model P3 is straightforward and intuitive, us-
ing menu-driven commands, and can be controlled by either the
front panel keypad or remotely via a USB connection.
The Model P3 utilizes modern digital signal processing tech-
nology to provide excellent noise rejection and stability. Pro-
prietary scaling and linearization algorithms provide unsur-
passed measurement accuracy for strain gage bridge measure-
ments.
Data may be stored on industry-standard multimedia (MMC)
cards or streamed to a PC using the on board USB interface.

- 3 -
1.2 FUNCTIONAL FEATURES
The Model P3 Strain Indicator and Recorder incorpo-
rates the following features:
•Four input channels.
•Direct-reading, backlit LCD display.
•Data storage using the multimedia card.
•Hardware and software support for quarter-, half-
and full-bridge circuits.
•Built-in precision bridge completion for 120-, 350-
and 1000-ohm half and quarter bridges.
•Automatic and manual zero-balance and calibration.
•Intuitive, menu-driven operations.
•Full control of all functions via USB Interface.
•Selectable analog output.
•Portable, lightweight and rugged design.
•Battery, USB, or line-voltage power.
•Intuitive, user-friendly software.

- 4 -
2 SPECIFICATIONS
Note: Performance may be degraded at high levels of repetitive electrostatic
discharge; however, no damage to the unit will occur.
2.1 Input Connections
Type: Tool-free eccentric lever release
Quantity: Four
Wire size: 16 to 28 AWG [1.29 to 0.31mm Φ]
2.2 Bridge Configurations
Types: Quarter-, half-, and full bridges
Bridge Impedance: 60 to 2000 Ω
Internal Bridge Completion:
Quarter bridge: 120Ω, 350Ωand 1000Ω±0.01%
Half bridge: 1000Ω±0.01%
2.3 Display
Type: 128 x 64 pixel FSTN positive, gray transflective
LCD with backlight
Update rate: 2 updates/second typ.
2.4 Data Conversion
A/D Converter: Delta-sigma with integral chopper-
stabilized programmable gain instrumentation amplifier
Resolution: 24 bits. Noise-free resolution: 18 bits typ.
Output rate:
Normal mode: 50 or 60 samples/sec.
Analog output mode: 480 samples/sec.
Filter: Integrated linear phase FIR Sinc5filter followed
by a Sinc3filter with a programmable decimation rate.
Software selectable output rate provides >120 dB rejec-
tion of 50 or 60Hz and higher level harmonics.

- 5 -
2.5 Measurement Range/Resolution
Strain Range: ±31,000 µεat GF = 2.000. (±15.5 mV/V)
Resolution: ±1 µεat GF = 2.000 (±0.0005 mV/V)
2.6 Measurement Accuracy
±0.1% of reading ±3 counts. (Analog output disabled,
instrument Gage Factor = 2.000)
2.7 Gage Factor Control
Range: 0.500 to 9.900
2.8 Balance Control
Type: Software
Control: Manual or automatic
2.9 Bridge Excitation
Value: 1.5 VDC nominal
Control: Software enable/disable
Measurements are fully ratiometric, and not degraded by
variations in excitation voltage
2.10 Communication Interface
Universal serial bus (USB). Cable included
2.11 Data Storage
Type: Removable Multimedia Card (16M supplied).
Recording rate: Software-selectable from 1 reading per
second to 1 reading per hour
2.12 Shunt Calibration
Location: Across bridge completion resistors

- 6 -
Control: Software
Values:
P- to D120: 11.9KΩ±0.1% (5000µεat GF = 2.00)
P- to D350: 34.8KΩ±0.1% (5000µεat GF = 2.00)
P- to D1000: 99.5KΩ±0.1% (5000µεat GF = 2.00)
Remote calibration: Switch contacts at input terminal
block
2.13 Analog Output
Value: 0 to 2.5V max
Ranges: ±320 µε, ±3200 µε, ±32000 µε
Update rate: 480 samples/sec
Output Load: 2000Ω
Connector: BNC
2.14 Power
Battery: Two Alkaline "D" cells
Battery life: 400 hours typ.
AC Adapter: 6-15VDC 100mA
USB: 5V 100mA
2.15 Operational Environment
Temperature: 0° to +50°C
Humidity: Up to 90% RH. Non-condensing
2.16 Case
Material: Aluminum
Accessories: Two rubber grommets installed in the lid
allow leadwires to enter the case with the lid closed for
increased resistance to water splash

- 7 -
2.17 Size & Weight
Size: 9 x 6 x 6 in (228 x 152 x 152 mm)
Weight: 4.4 lb (2.0 kg), including batteries

- 8 -
3 FRONT PANEL
3.1 USB Interface
The USB interface is the communication channel between the
P3 and a host PC. All front panel controls (except the system
calibration option) are accessible via the USB interface.
USB
Interface
Memory
Card Slot
Input
Terminals
Keypad Power
Connector
Analog
Output
Connector
LCD
Display

- 9 -
When connected, the PC (running Windows 98, 2000, or XP)
will identify the Model P3 as a standard USB Human Interface
Device, therefore, no special device drivers are required to
communicate with the device.
The Model P3 is supplied with user-friendly Windows-based
application software which provides complete control of the
Model P3.
In addition, an ActiveX control is supplied to simplify the de-
velopment of user-defined applications.
The Model P3 can also operate as a stand-alone system, without
being connected to the USB interface. In the stand alone con-
figuration, all functions are controlled by the keypad.
3.2 Memory Card Slot
The memory card slot accommodates industry-standard multi-
media (MMC) cards. Data can be recorded to the MMC by se-
lecting the appropriate recording options. The multimedia card
supports FAT16 or FAT12-formatted cards, such as the one
supplied with the unit.
Recorded can be either uploaded to a PC using the on-board
USB interface and the supplied software, or by using an indus-
try standard Multimedia Card (MMC) reader.
3.3 Input Connectors
The input connectors connect the strain gage or transducer to
the Model P3. To attach a wire to the input connector, simply
lift the eccentric lever, insert the wire into the terminal opening,
and lower the eccentric lever.

- 10 -
3.4 LCD Display
The LCD display provides the visual interface to control, setup,
and monitor the P3.
3.5 Keypad
The keypad is a membrane-switch type. Functionality of the
keys is described in the Operation section.
3.6 Power Connector
The power jack accepts a 6 to 15V DC source (0.1A max).
3.7 Analog Output Connector
The analog output jack provides a 0-2.5 volt output signal that
corresponds to the displayed value. The output range is user-
selectable.

- 11 -
4 OPERATION
4.1 Getting Started
The Model P3 is designed for ease of use. This section de-
scribes the operation of the Model P3 Strain Indicator and Re-
corder.
4.2 Power Up
The Model P3 is ready to use as received. The unit is shipped
with two D cells pre-installed.
The Model P3 has three sources of power: Battery, USB or AC
adapter. If more than one power supply is present, the power
source is determined in the following order: (1) USB, (2) AC
Adaptor, and (3) battery. If the Model P3 is using USB or the
AC adaptor, the system will always remain on as long as power
is supplied. If the Model P3 is using the USB or AC adapter as
the power source, an "x" is displayed on the lower right corner
of the LCD display, indicating the unit is running on external
power. If the system is running on battery power, the ‘x’ is re-
placed by a battery strength indicator.
If no external supply is detected, the system must be turned on
by pressing the Power key, .
When the unit is powered up, the firmware is loaded into the
DSP. During this time an audible beep will be heard, indicating
the unit is booting. After approximately two seconds, the beep
tone will cease, unit will display the opening screen.

- 12 -
4.3 Input Connections
Strain gages and strain gage-based transducers are connected to
the P3 through the input terminals. The P3 can accommodate up
to four input channels, labeled 1 through 4. To connect the
leadwire to the input terminal, lift the black arm of the desired
terminal, insert the leadwire all the way into the terminal, and
carefully lower the arm to clamp the wire to the terminal. Con-
nections can be made whether the unit is on or off.
4.3.1 Quarter Bridge Connections
The following configuration illustrates the connections for mak-
ing a three-wire quarter bridge connection:
Select the dummy terminal (D120, D350, or D1K) to correspond
with the nominal resistance of the strain gage.
350
D
P+ DS- 120 DP-
1K S+
T

- 13 -
4.3.2 Half Bridge Connections
The following figure illustrates the connections for making a
three-wire half-bridge connection.
4.3.3 Full Bridges and Transducers
The following figure illustrates the connections for making a
full-bridge connection:
P+ S+D
350
S- D
120 P-D
1K
TC
1K
D
120
DP+ S- 350
D P- S+
EXTERNAL CAL CIRCUIT
TC
CT

- 14 -
In addition to bridge wiring, a switch closure is provided for an
external shunt calibration resistor. This feature will normally be
used to implement shunt calibration of the transducer according
to the transducer manufacturer’s recommendation.
The transducer manufacturer will generally specify exactly how
a specific value of shunt calibration resistor is to be connected.
In some cases, the manufacturer may also supply leadwires, in-
tegral to the transducer assembly, which are used for this pur-
pose. In any case, the transducer manufacturer’s recommenda-
tions should be followed.
4.4 Operational Modes
The Model P3 has two operational modes: the run mode and the
command mode.
4.4.1 Run Mode Operation
In the run mode, the display is divided into four quadrants (one
for each channel), along with a status line on the bottom of the
display.
Ch1 µεCh2 µε
+01000 +00216
Ch3 µεCh4 µε
+00524 +00914
REC OFF CAL OFF

- 15 -
4.4.1.1 Display Pause
While in the run mode, the display can be paused (for example,
to make a handwritten record of the current data). To pause the
display, press the key.
Ch1 µεCh2 µε
+01000 +00216
Paused ->Resume
Ch3 µεCh4 µε
+00524 +00914
REC OFF CAL OFF
Note: While in the pause mode, recording to the MMC is also
suspended. To resume to normal operation, press the key.
4.4.1.2 Peak Read
In addition, the Model P3 can be used as a peak hold indicator.
The peak hold function is accessed by using the and arrow
keys.
Pressing the key will update the display if a value larger than
the currently displayed value is measured.
Ch1 µεCh2 µε
+01000 +00216
Max Peak ↑=Reset
Ch3 µεCh4 µε
+00524 +00914
REC OFF CAL OFF

- 16 -
To reset the peak display, press the . To return to the normal
(tracking) mode, press MENU .
Pressing the key will update the display if a value larger than
the currently displayed value is measured.
Ch1 µεCh2 µε
+01000 +00216
Min Peak ↓=Reset
Ch3 µεCh4 µε
+00524 +00914
REC OFF CAL OFF
To reset the peak display, press the key. To return to the
normal (tracking) mode, press MENU .
4.4.1.3 Shunt Calibration
The shunt calibration switch may be toggled while in the run
mode by pressing the cal key. When activated, a precision
shunt resistor is placed between the P- and the appropriate
dummy (Dxxx) resistor, additionally, the Remote Cal switch
closed. The internal shunt calibration resistors simulate an
equivalent strain of 5000 microstrain at a gage factor of 2.000.
The lower right of the screen indicates whether the calibration
switch is active (CAL ON) or inactive (CAL OFF).
Table of contents
Other Vishay Measuring Instrument manuals
Popular Measuring Instrument manuals by other brands
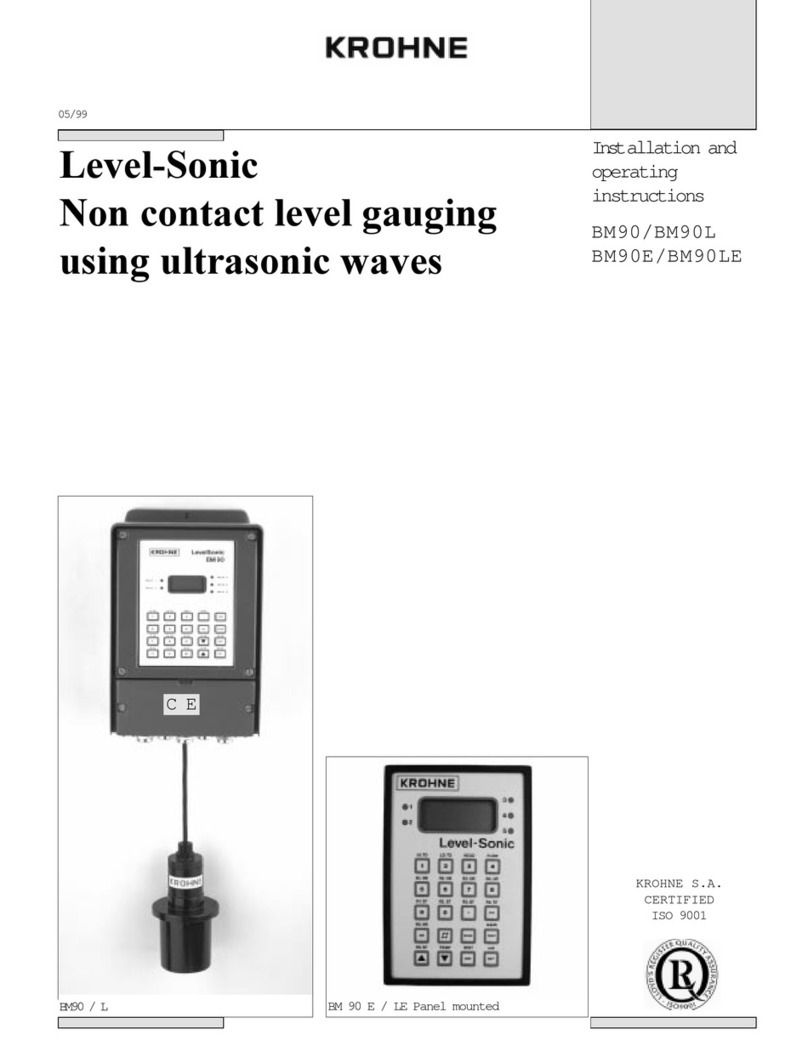
KROHNE
KROHNE LEVEL-SONIC BM90 Series Installation and operating instructions
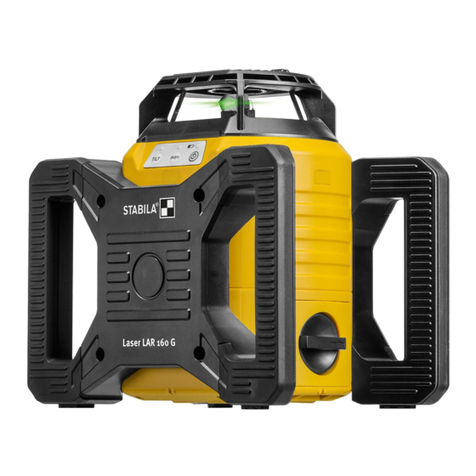
Stabila
Stabila LAR 160 operating instructions
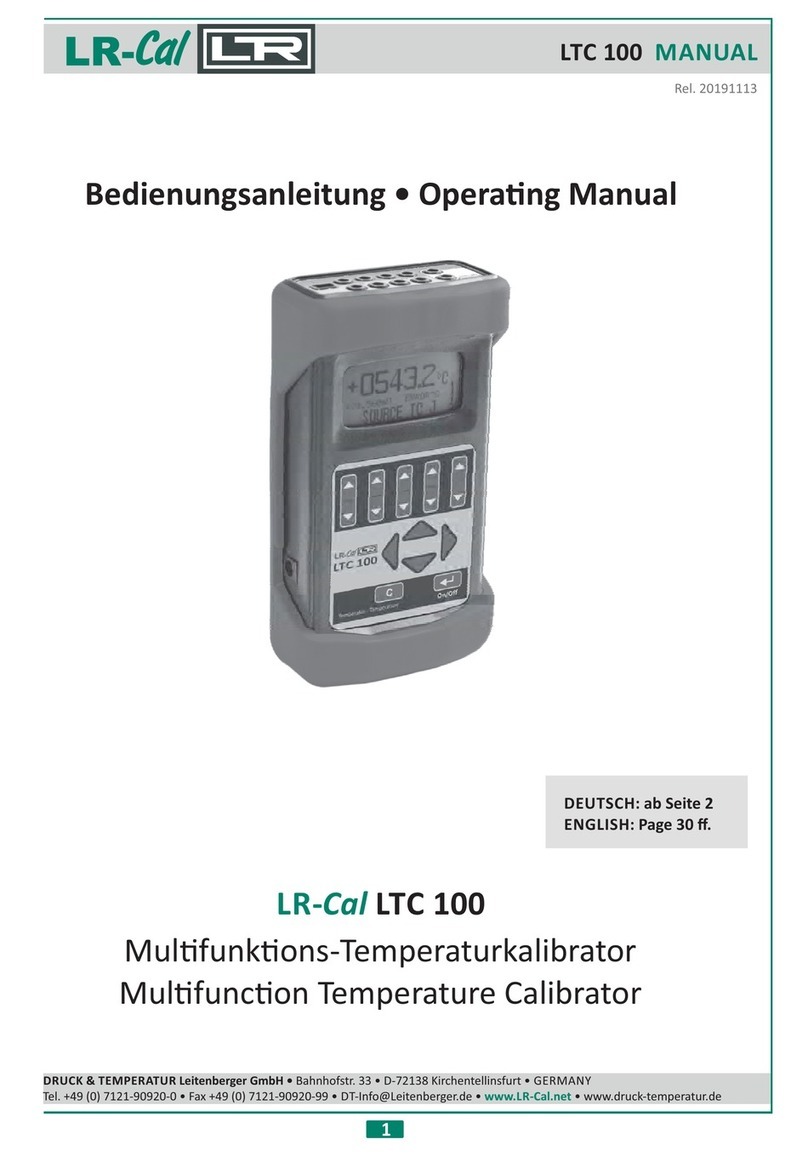
DRUCK & TEMPERATUR Leitenberger
DRUCK & TEMPERATUR Leitenberger LR-Cal LTC 100 manual

Wohler
Wohler SC 602 Operation manual
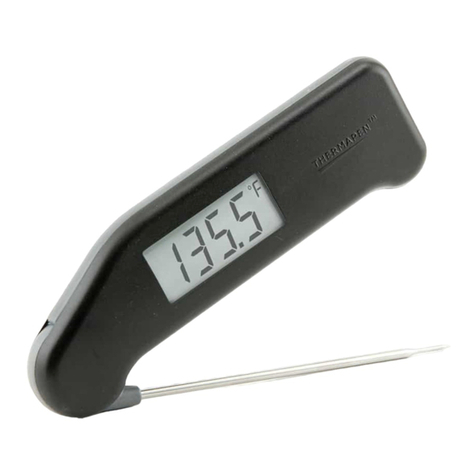
ThermoWorks
ThermoWorks Classic Thermapen operating instructions

Anaheim Scientific
Anaheim Scientific M150 user manual

Hanna Instruments
Hanna Instruments HI 717 quick start guide
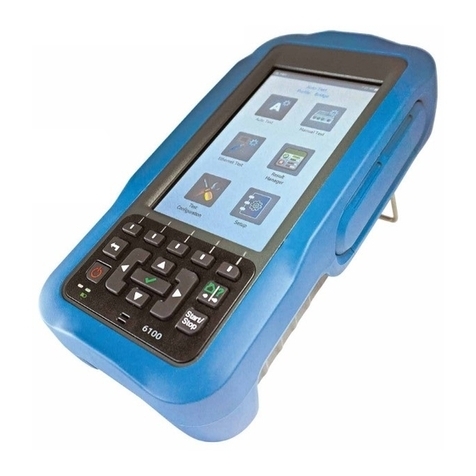
Radiodetection
Radiodetection 6100-Gfast Operation manual
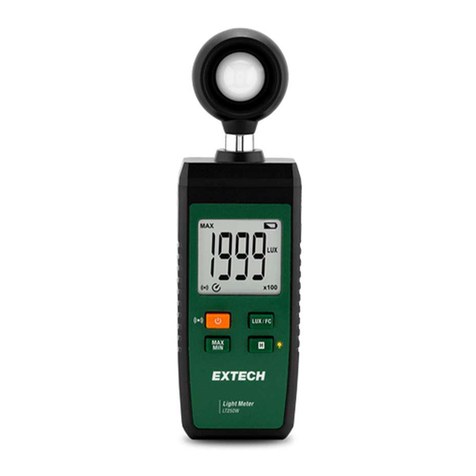
Extech Instruments
Extech Instruments LT250W user manual

AEMC
AEMC 1020 user manual
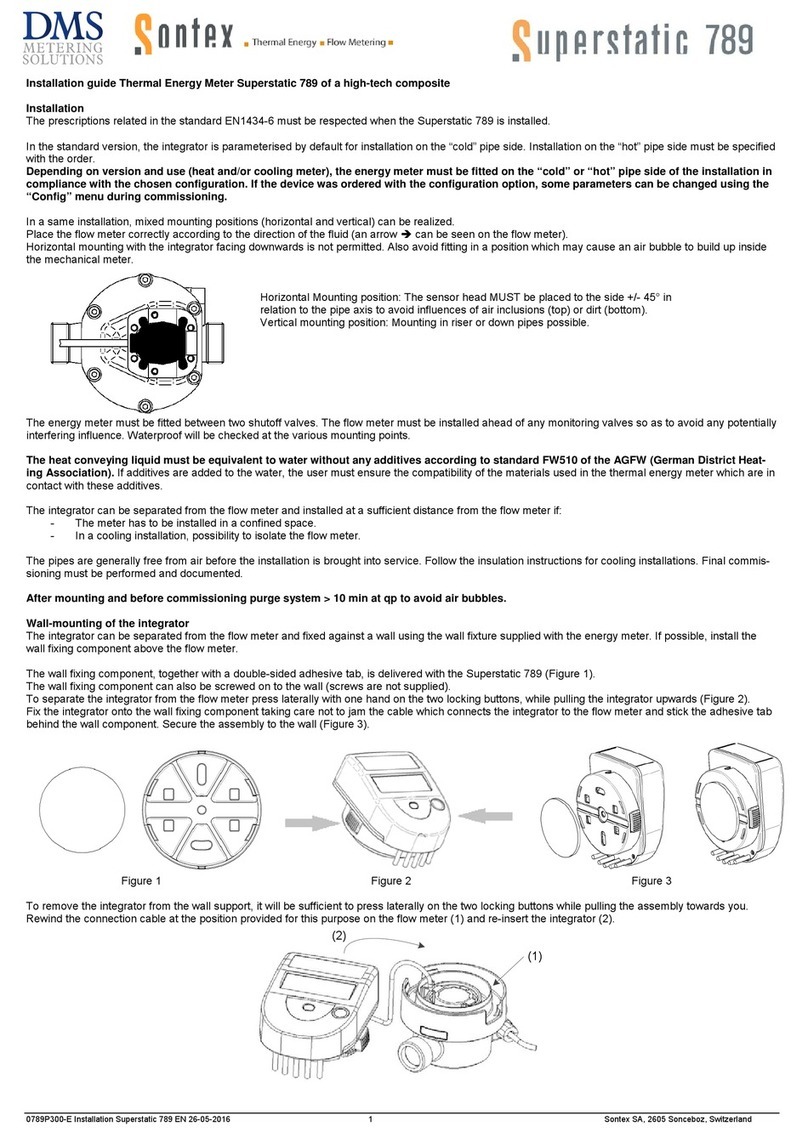
Sontex
Sontex Superstatic 789 installation guide
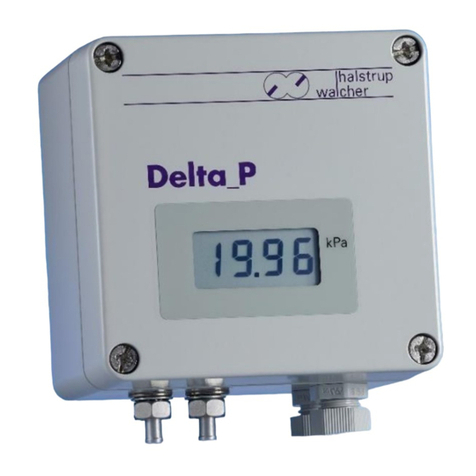
halstrup-walcher
halstrup-walcher PU Original instruction manual