Vogel & Plötscher RCAD User manual



© 2016 by Vogel & Plötscher GmbH & Co. KG | RCAD | Version 2.0 | 25.01.2015
User Manual
RCAD

Page: 2 / 28
© 2016 by Vogel & Plötscher GmbH & Co. KG | RCAD | Version 2.0 | 25.01.2015
Table of Contents
Table of Contents ......................................................................................................................... 2
1. Introduction ............................................................................................................................ 4
1.1 Intended use ..................................................................................................................... 4
1.2 Standard supply package .................................................................................................... 4
2. Functional components ............................................................................................................ 5
3. Start-up .................................................................................................................................. 7
3.1 Safety instructions .............................................................................................................. 7
3.2 Preparations ...................................................................................................................... 7
3.2.1 Initial start .................................................................................................................. 7
3.2.2 Illumination ................................................................................................................. 7
3.3 Checking measurement sensors .......................................................................................... 8
3.3.1 Track gauge sensor (minimum gauge check) ................................................................. 8
3.3.2 Initialization of gauge sensor ........................................................................................ 9
3.3.3 Inclination sensor (roll-over test) .................................................................................. 9
3.3.4 Initialization of inclination sensor ................................................................................ 10
4. Measurement practice ............................................................................................................ 11
4.1 Application on the track .................................................................................................... 11
4.1.1 Wide measuring support ............................................................................................ 11
4.1.2 Narrow measuring support ......................................................................................... 12
4.2 Parameters ...................................................................................................................... 13
4.2.1 Track gauge measurement ......................................................................................... 13
4.2.2 Flangeway clearance measurement ............................................................................. 13
4.2.3 Check rail gauge measurement ................................................................................... 13
4.2.4 Measuring of check rail gauge with broad measurement base (optional) ........................ 14
4.2.5 Back-to-back distance measurement ........................................................................... 15
4.2.6 Cant measurement .................................................................................................... 15
5. Maintenance instructions ........................................................................................................ 16
5.1 Care ................................................................................................................................ 16
5.2 Storage and transportation ............................................................................................... 16
5.3 Battery replacement ......................................................................................................... 17
6. Technical data ....................................................................................................................... 18
6.1 RCAD – 1435 mm ............................................................................................................. 18
6.2 RCAD – 1000 mm ............................................................................................................. 19
6.3 RCAD – 1067 mm ............................................................................................................. 20
6.4 RCAD – 1524 mm ............................................................................................................. 21

Page: 3 / 28
© 2016 by Vogel & Plötscher GmbH & Co. KG | RCAD | Version 2.0 | 25.01.2015
6.5 RCAD – 1668 mm ............................................................................................................. 22
7. EC Declaration of Conformity .................................................................................................. 23
8. Miscellany ............................................................................................................................. 24
9. Add-ons and options .............................................................................................................. 25
9.1 Data storage and Bluetooth (= option -BT) ........................................................................ 25
9.2 Data storage on SD card (= option -SD) ............................................................................ 25
9.3 Switch tongue control adapter (option -P) ......................................................................... 26
9.4 Cogwheel operation (option -ZB) ...................................................................................... 26
9.5 Frog tip inclination (option -H) ......................................................................................... 27
9.6 Check rail height measuring device (option -RH) ................................................................ 27
9.7 Interchangeable probes (option -W) .................................................................................. 28
9.8 Transport case ................................................................................................................. 28
Notes
The company and brand names used in this document are generally protected by trademark or patent
law.
All technical data provided in this manual was acquired, collated and verified with the greatest care
and diligence. Since the possibility of error cannot be entirely ruled out, however, we hereby advise
that we provide no guarantee as to the accuracy of the technical data, nor will we accept any legal
responsibility or liability of any kind for the consequences of any incorrect data or information given.
Vogel & Plötscher GmbH & Co. KG reserves the right to make changes to the product, the software
and this manual. Any such changes are made for the sole purposes of ongoing technical development.

Page: 4 / 28
© 2016 by Vogel & Plötscher GmbH & Co. KG | RCAD | Version 2.0 | 25.01.2015
1. Introduction
1.1 Intended use
RCAD is an electronic track and switch measurement device for checking vignole and
grooved rails on railways. In general the following parameters can be measured:
§ Track gauge
§ Check rail gauge
§ Flangeway clearance
§ Back-to-back distance
§ Cant
Depending on the technical design and configuration options, RCAD can be used to measure
and record a range of different measurement variables. Data is acquired within the specified
measuring ranges and tolerances (à chapter 6).
Users must be properly trained and qualified to use the measurement device. Consequently,
users are advised to undergo a practical induction course by V&P or someone authorised by
V&P to supplement the information provided in this user manual.
1.2 Standard supply package
1 x Digital measuring device RCAD
2 x Rechargeable batteries type AA
1 x User manual
If RCAD is not used in accordance with this requirement, safe operation of the
measurement system cannot be guaranteed. Users themselves, not V&P, are re-
sponsible for any resultant injury or damage to property.

Page: 5 / 28
© 2016 by Vogel & Plötscher GmbH & Co. KG | RCAD | Version 2.0 | 25.01.2015
2. Functional components
The measurement device comprises the following functional components:
Fig. 1:
#
Designation
1
Narrow support (moveable)
2
Adjusting knob (incl. clutch-mechanism)
3
Display with keypad
4
Handle
5
Base frame
6
Wide support
7
Battery box

Page: 6 / 28
© 2016 by Vogel & Plötscher GmbH & Co. KG | RCAD | Version 2.0 | 25.01.2015
Fig. 2:
Key
Mode
Function
Device ON | OFF
Illumination ON | OFF
Press button for ~ 1 second to switch device on. (*)
For switching off press and hold button.
Cant
Press button to read the current cant value.
Press and hold button for 5 seconds to start the cant initialization.
Flangeway clearance
Press button for starting measurement of the flangeway clearance.
(default initial value is 20 mm = diameter of the probe).
Check-rail gauge
Press button to read the current check-rail gauge value.
Back-to-back distance
Press button to read the current back-to-back distance.
Track gauge
Press button to read the current track gauge value.
(*)
Background illumination will be enabled (disabled) if ON/OFF button is pressed again while device is already
switched on.
Activated background illumination of the display will stress the batteries
and shorten operation time.

Page: 7 / 28
© 2016 by Vogel & Plötscher GmbH & Co. KG | RCAD | Version 2.0 | 25.01.2015
3. Start-up
3.1 Safety instructions
RCAD is a state-of-the-art system, assuring a high degree of reliability.
However, that reliability can only be attained in practice if all the necessary measures are
taken. It falls within the duty of care of the company operating the measuring device to en-
sure that those measures are taken, and to monitor their implementation.
The operating company must in particular ensure that…
1. The measuring device is used only in accordance with its intended purpose.
2. The measuring device is only operated in perfect working condition.
3. The measuring device is only operated by adequately qualified and authorised personnel.
4. This user manual is available at the place of use, and is readable and complete.
3.2 Preparations
To ensure correct and proper operation of the measuring device, observe the following
points:
§ All device components are in correct and proper condition and undamaged.
§ The batteries are fully charged and/or charged replacement batteries available.
3.2.1 Initial start
Press and hold the ON/OFF-button for about 1 second. The display will show the message
“ON” and afterwards the current track gauge value.
3.2.2 Illumination
After the device has been switched on, press ON/OFF-button again for enabling (or disa-
bling) the background illumination of the display.
The measuring device must be checked for visible damage prior to every
measurement. It must be ensured that the measuring device is operated
only when in proper working order.

Page: 8 / 28
© 2016 by Vogel & Plötscher GmbH & Co. KG | RCAD | Version 2.0 | 25.01.2015
3.3 Checking measurement sensors
3.3.1 Track gauge sensor (minimum gauge check)
A reference value for the minimum gauge is imprinted on the underside of the measuring
device. This reference value must be compared against the displayed actual track gauge
value in measuring mode. The narrow support must be at the innermost position when doing
so. The actual value should be in the range of ± 0.5 mm relative to the reference value.
In the event of variation > 1 mm, you are advised to initialize the gauge sensor (à Section
3.3.2).
#
Procedure
Details
1
Read off reference value from underside of measuring device
à Fig. 3a
2
Start-up measuring device
à section 3.2.1
3
Press button 5 on the keypad
à Fig. 2
4
Move narrow support all the way in
à Fig. 3b
5
Read off displayed actual value and compare against reference value
Fig. 3a Fig. 3b
Check the proper functioning and accuracy of the track gauge and
inclination sensors before every working shift.

Page: 9 / 28
© 2016 by Vogel & Plötscher GmbH & Co. KG | RCAD | Version 2.0 | 25.01.2015
3.3.2 Initialization of gauge sensor
Procedure
Ensure that the device is switched off. The measurement probes have to be adjusted into a
distance of 1435 mm. This is best done by use of a suitable template or calibration jig. Oth-
erwise use a ruler and set markings determining a distance of 1435 mm use. Then adjust the
measurement probes according to the markings.
Press and hold button 5 on the keypad while switching on the device. Finally release button
5 as soon as the display indicates the value of 1435,0 mm.
Now perform the minimum gauge check (à Section 3.3.1) again if the situation has been
improved.
In case the initialization procedure fails to deliver any improvement, the measuring device
must be checked and recalibrated at the factory.
3.3.3 Inclination sensor (roll-over test)
#
Procedure
Details
1
Start-up measuring device
à Abschnitt 3.2.1
2
Press button 1 on the keypad
à Fig. 2
3
Place measuring device correctly on track and wait about 5-10 seconds
4
Read off and record cant value #1
5
Rotate measuring device by 180°, place it at same track position and wait about
5-10 seconds
6
Read off cant value #2
7
Finally compare cant value #1 with cant value #2
The two recorded cant values are compared. The values should not differ by more than 1,0
mm, with an inverted preceding sign.
In the event of a variation > 2 mm, the inclination sensor has to be initialized (à Section
3.3.4).

Page: 10 / 28
© 2016 by Vogel & Plötscher GmbH & Co. KG | RCAD | Version 2.0 | 25.01.2015
3.3.4 Initialization of inclination sensor
Procedure
Put the device on the track and switch on the device. Press and hold button 1 until the dis-
play will show a rotating square (à Fig. 4a).
Wait about 10 seconds then press button 1 again and wait for the rotating square is chang-
ing its running direction (à Fig. 4b). Now lift up the device, turn it by 180° and place it on
same track position again. Wait for about 10 seconds before pressing button 1 again. The
new sensor setting will be saved while the current cant value is shown in the display.
Now perform the roll-over test (à Section 3.3.3) again to check if the situation has been
improved.
In case the initialization procedure fails to deliver any improvement, the measuring device
must be checked and recalibrated at the factory.
Fig. 4a
Fig. 4b

Page: 11 / 28
© 2016 by Vogel & Plötscher GmbH & Co. KG | RCAD | Version 2.0 | 25.01.2015
4. Measurement practice
4.1 Application on the track
4.1.1 Wide measuring support
During measurement, the two outer measuring probes (B) of the wide measuring support
must be contacting on the rail head in order to avoid measurement inaccuracy due to angle
errors. (à Fig. 5a | 5b).
Fig. 5a: Fig. 5b:
Legend
#
Designation
A
Wide measuring support
B
Outer measuring probes
C
Centre measuring probe (for measurements at check rail)
C
B
A
B

Page: 12 / 28
© 2016 by Vogel & Plötscher GmbH & Co. KG | RCAD | Version 2.0 | 25.01.2015
4.1.2 Narrow measuring support
Turn the adjusting knob (A) to move the measuring probe (C) of the narrow support (B) to
the rail (à Fig. 6). The final measuring position has been reached as soon as the clutch-
mechanism of the turning knob contacts the stop (= loose rotation).
Fig. 6:
Legend
#
Designation
A
Adjusting knob (incl. clutch-mechanism)
B
Narrow measuring support
C
Measuring probe
C
B
A

Page: 13 / 28
© 2016 by Vogel & Plötscher GmbH & Co. KG | RCAD | Version 2.0 | 25.01.2015
4.2 Parameters
4.2.1 Track gauge measurement
The measuring device must be correctly inserted into the track at the measuring point. Press button 5
on the keypad. With the adjusting knob, turn the measuring probe of the narrow support towards the
rail head as far as it will go (Fig. 7). The measurement value can now be read.
Fig. 7:
4.2.2 Flangeway clearance measurement
The measuring device must be correctly inserted into the track at the measuring point. Press button 2
on the keypad. With the adjusting knob, turn the measuring probe of the narrow support towards the
track construction (e.g. check rail or wing rail) until the measuring probe is contacting (à Fig. 8). The
measurement value can now be read.
Fig. 8:
4.2.3 Check rail gauge measurement
The measuring device must be correctly inserted into the track at the measuring point. Press button 3
from the keypad. Position the measuring device so that the centre measuring probe of the broad sup-
port makes contact on the inside (that is, on the check rail) (à Fig. 9). With the adjusting knob, turn
the measuring probe of the narrow support towards the crossing as far as it will go. The measurement
value can now be read.

Page: 14 / 28
© 2016 by Vogel & Plötscher GmbH & Co. KG | RCAD | Version 2.0 | 25.01.2015
Fig. 9
4.2.4 Measuring of check rail gauge with broad measurement base (optional)
Mount the broad measuring base on the corresponding fixture on the RCAD and fix it in place by the
screw fitting. Then insert the broad measuring base in the switch on the crossing side. When doing
so, bridge the tip of the crossing and the inside edge of the wing rail in front of the wing rail bend
point (à Fig. 10).
For measurement follow the instructions as explained in section 4.2.3.
Fig. 10:

Page: 15 / 28
© 2016 by Vogel & Plötscher GmbH & Co. KG | RCAD | Version 2.0 | 25.01.2015
4.2.5 Back-to-back distance measurement
The measuring device must be correctly inserted into the track at the measuring point. Press button 4
from on the keypad. Position the measuring device so that the centre measuring probe of the broad
support makes contact on the inside (that is, on the check rail)! With the adjusting knob, turn the
measuring probe of the narrow support towards the wing rail as far as it will go (à Fig. 11). The
measurement value can now be read.
Fig. 11:
4.2.6 Cant measurement
The measuring device must be correctly inserted into the track at the measuring point. Press button 1
on the keypad. With the adjusting knob, turn the measuring probe of the narrow support towards the
rail head as far as it will go (à Fig. 12). Wait a few seconds until the inclination sensor has come to
rest, then you can read off the measurement value.
Fig. 12:

Page: 16 / 28
© 2016 by Vogel & Plötscher GmbH & Co. KG | RCAD | Version 2.0 | 25.01.2015
5. Maintenance instructions
5.1 Care
(1) Any contamination, such as dirt, grinding dust or tar, must be removed from the
measuring device and accessories (e.g. measuring probes) directly when the meas-
urement is finished.
(2) When operating in a damp/humid climate or in rain, be sure to dry the measuring de-
vice off before placing it back in the transport case.
(3) Heavy impacts i.e. caused by pushing, shaking or falling down of the device may badly
influence its proper operation or calibration setting and therefore has to be avoided.
(4) A regular service and calibration duty (i.e. every 12 months) performed by V&P or any
authorized V&P service partner is recommended.
5.2 Storage and transportation
(1) The measuring device is best stored and transported in a suitable case
(à Section 9.8).
(2) When transporting the case on a flat load space, secure it so that it cannot slide.
(3) The measuring device must be dry and clean when being transported and stored in a
case.
(4) Check the measuring device for damage every time after transporting it.
(5) When out of the transport case, the measuring device is carried by the handle mount-
ed in the centre of the unit.

Page: 17 / 28
© 2016 by Vogel & Plötscher GmbH & Co. KG | RCAD | Version 2.0 | 25.01.2015
5.3 Battery replacement
The electronics of RCAD is supplied by two pieces of AA batteries inside. A screen message
in the display (= Low Batt) will indicate to the user, if the batteries are weak and need to be
replaced.
Therefore open the cover of the battery box by using a suitable tool (i.e. screwdriver, coin).
Remove the empty batteries inside and insert new ones.
Note: the batteries must be inserted with the minus pole first à Fig. 13a | 13b).
Finally put on the cover and fix it again.
Fig. 13a
Fig. 13b

Page: 18 / 28
© 2016 by Vogel & Plötscher GmbH & Co. KG | RCAD | Version 2.0 | 25.01.2015
6. Technical data
6.1 RCAD – 1435 mm
Nominal track width
1435 mm
Measurement
parameters
Measuring range
[mm]
Resolution
[mm]
Measurement uncer-
tainty U95 [mm]
Track gauge
1367 – 1475
0.1
± 0.25
Check rail gauge
1347 – 1455
0.1
± 0.25
Back-to-back distance
1327 – 1435
0.1
± 0.25
Flangeway clearance
20 – 128
0.1
± 0.25
Cant
± 200
0.1
± 0.50
Dimensions and weight
RCAD (length x width x height)
~ 1618 x 100 x 156 mm
Weight RCAD
~ 2,5 kg
Transport case (length x width x height)
~ 1750 x 200 x 190 mm
Weight transport case (unloaded)
~ 7.0 kg
Operating conditions
Ambient temperature
-10°C | +45°C
Humidity (non-condensing)
30% to 80% relative humidity
Miscellany
The measuring device is insulated.
The measuring device is DB approved.
Table of contents
Other Vogel & Plötscher Measuring Instrument manuals
Popular Measuring Instrument manuals by other brands

VOLTCRAFT
VOLTCRAFT ENERGY MONITOR 3000 operating instructions
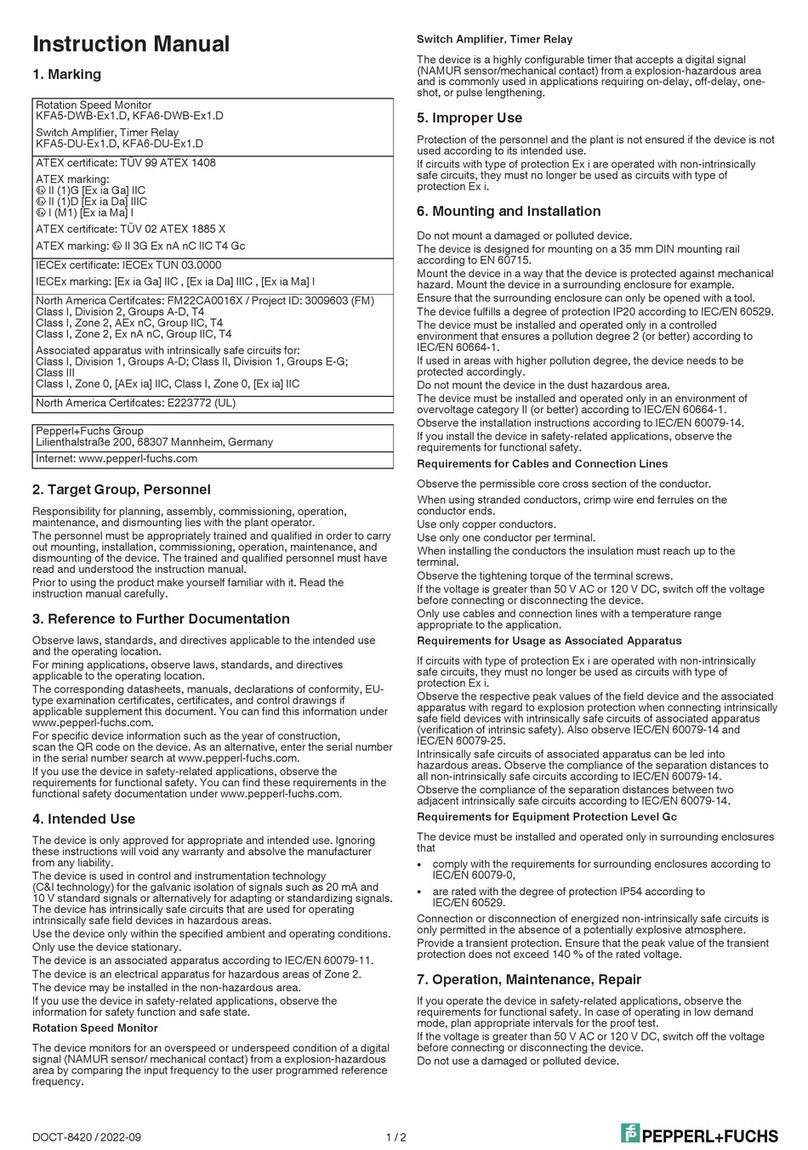
Pepperl+Fuchs
Pepperl+Fuchs KFA5-DWB-Ex1.D instruction manual
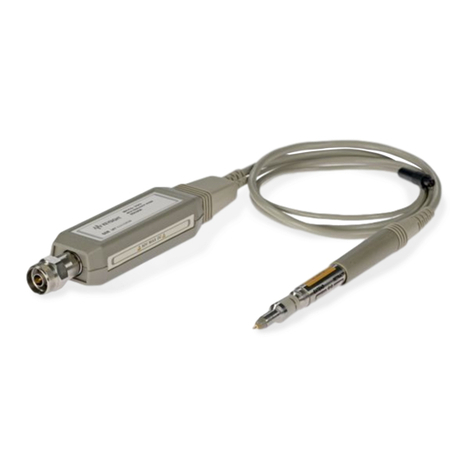
Agilent Technologies
Agilent Technologies 85024A User's and service guide
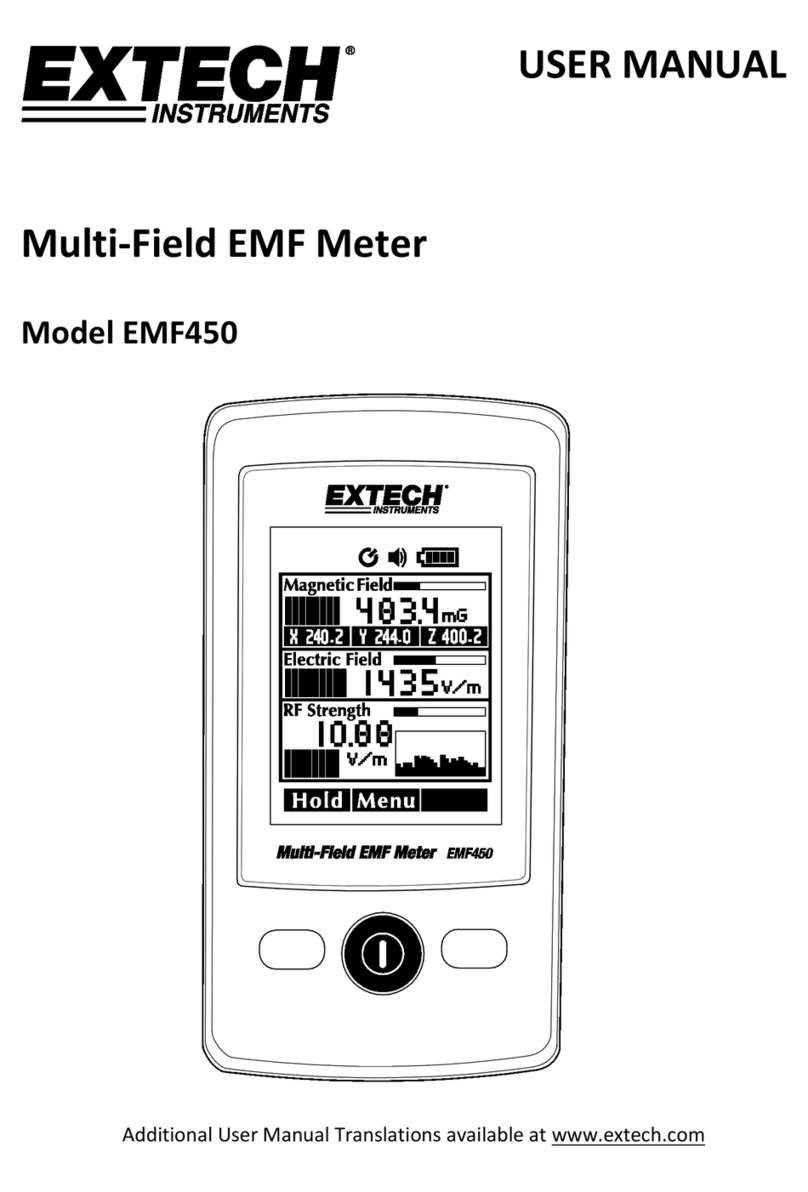
Extech Instruments
Extech Instruments EMF450 user manual
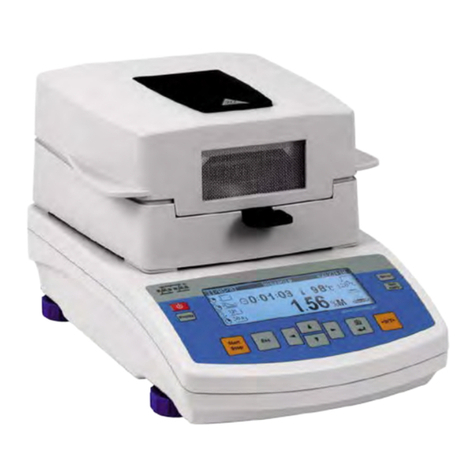
RADWAG
RADWAG MAX 60 user manual

Milwaukee
Milwaukee MW500 user manual