Wavelength Electronics LDTC0520 User manual

ORDERING INFORMATION
PART NO DESCRIPTION
LDTC0520 500 mA LD / ±2.2 ATEC Controller
LDTC1020 1.0 A LD / ±2.2 A TEC Controller
PROVEN RELIABILITY
SAVES YOU TIME AND MONEY
The LDTC Laser Diode and Temperature Controller
combines the proprietary FL500 and ultra-stable WTC3243
in one compact and easy-to-use module.All the controls and
indicators are onboard for simple plug-and-play operation.
APPLICATIONS
LDTC modules are in use around the world providing
trouble-free reliability in range finders, telecom laser
modules, military-aerospace research and development,
airborne metrology, academic research, laser diode LIV
testers, and more.
POWER YOUR APPLICATION WITH
THE RIGHT FEATURES
The popular FL500 is known for trouble-free operation.
The current limit circuit cleanly clamps laser diode current
without ringing or overshoot, and recovers without inducing
a phase shift in a modulated laser signal.
The WTC3243 ultra-stable temperature control module is
known for precision and reliability. Independent cooling-
and heating-current limits allow the LDTC to be used with
thermoelectric coolers or resistive heaters, and either
negative or positive temperature coefficient sensors.
FEATURES AND BENEFITS
• Small package size
• Single supply operation possible
• LD current range 500 mA or 1 A
• Compatible with TypeAand B lasers
• Slow start laser diode protection
• Constant Current or Constant Power modes
• Adjustable laser diode current limit
• Brownout protection
• Drive up to ±2.2 A of TEC current
• Internal or External setpoint control
• Failsafe setpoint default
• Ultra-stable PI control loop
• Separate Heat & Cool current limits
CONTENTS
QUICK CONNECT GUIDE 2
PIN DESCRIPTIONS 5
ELECTRICAL SPECIFICATIONS 7
SAFETY & THERMAL DESIGN CONSIDERATIONS 9
OPERATING INSTRUCTIONS -- TEMP CONTROLLER 10
OPERATING INSTRUCTIONS -- LASER DRIVER 15
ADDITIONAL TECHNICAL INFORMATION 17
TROUBLESHOOTING -- TEMP CONTROLLER 22
TROUBLESHOOTING -- LASER DRIVER 23
MECHANICAL SPECIFICATIONS 25
CERTIFICATION AND WARRANTY 26
e
Pb
RoHS
Compliant
PAGE
Applies to Product Revisions A – C
© April 2015
406-587-4910
www.teamWavelength.com
LDTC0520/LDTC1020
Laser Diode & Temperature Controllers
DATASHEET AND OPERATING GUIDE

© 2015 www.teamWavelength.com 2
LDTC0520 / LDTC1020 LASER DIODE AND TEMPERATURE CONTROLLER
J1
J2
J3
Status LEDs
Laser Current Enable
Laser Current Setpoint
Laser Current Limit
Temperature Current Limit B
Temperature Setpoint
Temperature Current Limit A
DIP Switches *
DIP Switch Functions
LDREF = Internal vs. External Laser Diode Setpoint
CC | CP = Constant Current vs. Constant Power Control Mode
TREF = Internal vs. External Temperature Setpoint
* DO NOT CHANGE SWITCH POSITIONS WHILE THE OUTPUT
IS ENABLED; DOING SO MAY DAMAGE THE LOAD.
!
Figure 1. LDTCxx20 Top View
QUICK CONNECT GUIDE
LDTCxx20 Top View page 2
LDTCxx20 Wiring Diagram page 2
Laser Driver Test Load page 3
Thermoelectric Test Load page 4
!
ITIS IMPERATIVE THAT YOU VERIFY THE UNIT WILL OPERATE
WITHIN THE INTERNAL HEAT DISSIPATION SAFE OPERATING
AREA (SOA).
OPERATING THE CONTROLLER OUTSIDE THE SOA MAY
DAMAGE OR DESTROY THE LDTC AND/OR LOADS.
VisittheWavelengthElectronicswebsiteforthemostaccurate,
up-to-date, and easy to use SOA calculator:
Laser Diode Drivers:
http://www.teamwavelength.com/support/calculator/soa/soald.php
http://www.teamwavelength.com/support/calculator/soa/soald.php
Temperature Controllers:
Temperature Controllers:
http://www.teamwavelength.com/support/calculator/soa/soatc.php
http://www.teamwavelength.com/support/calculator/soa/soatc.php
The model number is stamped on the top cover of the
module. If the top cover is missing, the model number can be
identified by the number of FL500 chips on the circuit board:
the LDTC0520 has a single FL500 on the top; the LDTC1020
has two FL500 chips─one on each side of the circuit board.
Figure 1 is the top view of the LDTC, illustrating the onboard
switches and trimpots.
Figure 2 is the Quick Connect diagram for the LDTCxx20
Controllers with a laser diode, separate power supplies, and
a thermoelectric cooler. This is the most common application
for the LDTCxx20 Controllers.
VDD_FL
VDD_WTC
VS
GND
SP1
SP2
LD SHD (Enable LD current)
COM
EXT LD SETpoint
COM
LD P Monitor
LD I Monitor
ACT T Monitor
SET T Monitor
EXT T SETpoint
COM
LDC
PDA
Spare
LDA
COM
TEC+
TEC-
SEN+
SEN-
COM
J1
J2
J3
VDD_WTC
VDD_FL
VS
- +
See Note
Thermistor
DVM
OPEN or 3 to 5 V = DISABLE
GND = LD ENABLE
1
1
4
12
1
10
Optional Laser Current
External Setpoint (0 to 2 V)
Optional
Temp Control
Ext. Setpoint
11
2
3
1
1. VDD_WTC, VDD_FL, and VScan be tied together if common voltage provides sufficient compliance for laser diode and
thermoelectric loads. Separate VSif higher compliance is required for the temperature controller load.
2. If using the LD SHD input, set the onboard Enable/Disable switch to Enable.
3. Refer to Electrical Specifications for input voltage range.
3
!THE LDTC DOES NOT SUPPORT LASER DIODE
PACKAGES THAT INCORPORATE A BUILT-IN
TEMPERATURE SENSOR THAT IS CONNECTED
TO THE LASER CASE GROUND.
Figure 2. LDTCxx20 Quick Connect Wiring Diagram

© 2015 www.teamWavelength.com 3
LDTC0520 / LDTC1020 LASER DIODE AND TEMPERATURE CONTROLLER
The LDTCxx20 is compatible with Type A and Type B lasers,
but will not drive Type C lasers; see Figure 3.
Type A Laser Diode Type B Laser Diode Type C Laser Diode
Common
Cathode
Laser Diode Anode &
Photodiode Cathode Common Isolated Photodiode
Short the
Laser Diode Anode
to Photodiode Cathode
Common
Anode
Laser Diode Cathode &
Photodiode Anode Common
Figure 3. Laser Type Diagrams
For initial setup and configuration, we recommend using
a simulated load while configuring the laser diode driver,
until familiar with the controller operation. To pre-test or
troubleshoot the temperature controller, please use the
following recommended test loads.
RECOMMENDED LASER DRIVER TEST LOAD
For the laser diode driver, recommended simulated laser
loads are shown in Figure 4 and Figure 5. In Constant
Current Mode, the setpoint correlates to the laser diode
current flow and is measured by monitoring the current at IMON.
When setting ILIM, turn the ILIM trimpot fully counterclockwise
(12 turns CCW). Then turn the setpoint trimpot fully clockwise
(12 turns CW). While monitoring the IMON voltage, turn the
ILIM trimpot CW until the desired voltage relative to current is
reached. Then turn the setpoint trimpot CCW until the IMON
voltage is affected and stop. The limit is now set and the
current can be adjusted within the limit range.
1N4001
1N4001
LDC
(Pin J3-1)
LDA
(Pin J3-4)
ȍ:
Constant Current Mode
Figure 4. Constant Current Mode
In Constant Power Mode, the setpoint correlates to the
photodiode feedback current, which represents a fraction
of the light power emitted by the laser diode. Photodiode
current is measured by monitoring PMON.
ȍ
1N4001
1N4001
2N3906
0.33 μF
PDA
(Pin J3-2)
LDA
(Pin J3-4)
LDC
(Pin J3-1)
Constant Power Mode
7KHȍUHVLVWRUW\SLFDOO\
SURGXFHVDSSUR[LPDWHO\P$
ODVHUGULYHUFXUUHQW9DU\WKH
UHVLVWRUYDOXHWRFKDQJHWKH
RXWSXWFXUUHQW
ȍ:
Figure 5. Constant Power Mode
NOTE: To determine the actual drive current, measure
the voltage drop across the 1 Ωresistor. Do not insert an
ammeter in series with the output circuit; doing so may
cause instability in the control loop. To stay within the
Safe Operating Area, VSmust not exceed 5 V.

© 2015 www.teamWavelength.com 4
LDTC0520 / LDTC1020 LASER DIODE AND TEMPERATURE CONTROLLER
RECOMMENDED THERMOELECTRIC TEST LOAD
For the temperature controller, recommended simulated
thermoelectric and thermistor circuits are shown in Figure 6
andFigure7.Configuringthetemperaturecontrollerusingtest
loads is recommended for setting the thermoelectric controller
limits or to check the temperature controller operation.
R
LOAD
TEC+
(Pin J3-6)
TEC-
(Pin J3-7)
R
LOAD
ȍ5DWHG!:
7KHUPDO7HVW/RDG
I
METER
Figure 6. Simulated Thermoelectric Test Load
R1
5 Nȍó:UHVLVWRU
SEN-
3LQ-
SEN+
3LQ-
6LPXODWHG7KHUPLVWRU
Figure 7. Simulated Thermistor
This circuit simulates a 10 kΩthermistor operating at 25°C.
Use the 100 μA bias current setting to create a 1 V sensor
signal. Other resistor values can be used depending on the
sensor voltage you wish to simulate. To drive cooling current,
set SET T to 1.35 V and to drive heating current, set SET T
to 0.85 V.
NOTE: To stay within the Safe Operating Area, VSmust not
exceed 5 V.

© 2015 www.teamWavelength.com 5
LDTC0520 / LDTC1020 LASER DIODE AND TEMPERATURE CONTROLLER
PIN DESCRIPTIONS
Table 1. Pin Descriptions and Wire Colors
PIN NAME CABLE
COLOR PIN DESCRIPTION
Connector J1, Cable WCB303 (included with LDTC0520 and LDTC1020)
1V
DD_FL Green Laser driver and laser diode power supply input; 3 to 12 VDC. Current rated to at least
1.1-times the laser diode forward current plus the driver quiescent current. Low-noise
switching power supply recommended. Reference the Safe Operating Area calculator.
2V
DD_WTC Red Temperature controller power supply input; 5 to 12 VDC. Current rated to at least 100 mA.
Low-noise switching power supply recommended.
3V
SWhite Power supply input for driving the TEC or resistive heater; 5 to 30 VDC. Current rated
to at least 1.1-times the TEC maximum drive current. Low-noise switching power supply
recommended. Reference the Safe Operating Area calculator.
4 GND Black Power supply ground. This is the only ground connection designed as a high current
power supply return.
Connector J2, Cable WCB302 (included with LDTC0520 and LDTC1020)
1 SP1 — No connection
2 SP2 — No connection
3 LD SHD Red Laserdiode shutdown/interlockinput.TheonboardEnableswitch mustbe settoENABLE
when this external enable function is used. TTL-compatible.
Enable = Ground; Disable = OPEN or 3 to 5 V.
4 COM Green/Blk Low current return for monitors, inputs, and status pins.
Do not use for high current return.
5 EXT LD SET White
External laser diode setpoint input, optional. Range 0 to 2 V. Input impedance 5 kΩ.
Transfer function shown in Table 2. Set the LDREF switch to EXT (up) to reference the
EXT LD SET input signal. The EXT LD SET voltage does not sum with the onboard
trimpot setting.
6 COM Green Low current return for monitors, inputs, and status pins.
Do not use for high current return.
7 LD P M Orange/Blk Photodiode current monitor output. The signal on this pin is proportional to the photodiode
current. Voltage range 0 to 2 V. Transfer function shown in Table 2.
8 LD I M Blue Laser current monitor output. The signal on this pin is proportional to the actual laser
output current. Transfer function shown in Table 2.
9 ACT T M Red/Blk Actual temperature sensor voltage monitor output. Output voltage equals the voltage drop
across the temperature sensor. Voltage range 0 V to VDD_WTC.
10 SET T M White/Blk Temperature setpoint voltage monitor output. Output voltage equals the temperature
sensor setpoint voltage set by the onboard trimpot or the EXT T SET input.
11 EXT T SET Orange
External temperature setpoint input, optional. Range 0.3 to (VDD_WTD - 2). Input
impedance > 1 MΩ. Transfer function shown in Table 2. The EXTTEMP SET voltage does
not sum with the onboard trimpot setting. Set the TREF switch to EXT (up) to reference
the EXT T SET input signal. If the signal falls below 0.3 V the setpoint will default to 1 V.
To reset the default safety circuit, the EXT T SET voltage must be > 0.4 V.
12 COM Black Low current return for monitors, inputs, and status pins.
Do not use for high current return.
Continued ...

© 2015 www.teamWavelength.com 6
LDTC0520 / LDTC1020 LASER DIODE AND TEMPERATURE CONTROLLER
PIN DESCRIPTIONS (CONTINUED)
PIN NAME CABLE
COLOR PIN DESCRIPTION
Connector J3, Cable WCB301 (included with LDTC0520 and LDTC1020)
1 LDC Black Laser diode cathode connection
2 PDA White Photodiode anode connection
3 PDC Blue Photodiode cathode connection
4 LDA Red Laser diode anode connection
5 COM Green Low current return for monitors, inputs, and status pins.
Do not use for high current return.
6 TEC+ Red/Blk Positive side of TEC. This pin supplies the current to the TEC (when using NTC
sensors). Refer to the operating instructions for proper connections to a TEC or
Resistive Heater based on the type of sensor being used.
7 TEC– Orange Negative side of TEC. This pin sinks the current from the TEC (when using
NTC sensors).
8 SEN+ White/Blk Positive side of temperature sensor. Bias current is driven from SEN+ to SEN–.
9 SEN– Orange/Blk Ground connection for the temperature sensor. Refer to the Specifications table for input
voltage range. Do not use for high current return.
10 COM Green/Blk Low current return for monitors, inputs, and status pins.
Do not use for high current return.
Table 2. Control and Monitor Transfer Functions
FUNCTION LDTC0520 LDTC1020 DESCRIPTION
EXT LD SET, CC
Mode 250 mA / V 500 mA / V External setpoint input to control the laser drive current in Constant
Current mode.
EXT LD SET, CP Mode 1 mA / V External setpoint input to control the photodiode current in Constant
Power mode.
LD P MON 500 μA / V The power monitor transfer function can be modified by changing a
resistor on the circuit board. Contact the factory for details.
LD I MON 250 mA / V 500 mA / V The laser current monitor indicates the current driven to the laser.
ILIM (Internal Test Point) 250 mA / V 500 mA / V Refer to page 20 for location of the ILIM test point on the circuit board.
ACT T M 1 V / V The ACT T M voltage matches the voltage drop across the temperature
sensor.
SET T M 1 V / V The SET T M voltage matches the setpoint voltage set by the onboard
trimpot or the EXT T SET input (pin J2-11).
EXT T SET 1 V / V The external temperature setpoint input.
Table 3. Wiring Diagram Reference and LIM Trimpot Functions
SENSOR TYPE LOAD
TYPE VDD_WTC AND VS
TIED FIGURE, PAGE LIM A TRIMPOT LIM B TRIMPOT
NTC
(Thermistor)
TEC Either Figure 11 on page 13 Cooling Current Limit Heating Current Limit
Heater* Yes Figure 17 on page 17 Set to OFF (fully CCW) Heating Current Limit
No Figure 18 on page 17
PTC
(RTD, LM335, etc)
TEC Either Figure 19 on page 18 Heating Current Limit Cooling Current Limit
Heater* Yes Figure 20 on page 18 Heating Current Limit Set to OFF (fully CCW)
No Figure 21 on page 18
* Setting the LIM A and LIM B trimpots requires a special procedure when using a resistive heater.

© 2015 www.teamWavelength.com 7
LDTC0520 / LDTC1020 LASER DIODE AND TEMPERATURE CONTROLLER
ELECTRICAL SPECIFICATIONS
ABSOLUTE MAXIMUM RATINGS SYMBOL LDTC0520 LDTC1020 UNIT NOTE
LD Supply Voltage VDD_FL 3 to 12 VDC
TC Electronics Supply Voltage VDD_WTC 4.5 to 12 VDC
TC Load Supply Voltage VS4.5 to 30 VDC
Max LD Output Current ILD 505 1010 mA
Max TC Output Current ITEC ±2.2 A
Laser Driver Internal Power Dissipation1PLD_MAX 24WT
AMBIENT = 25ºC 1
Temp Controller Internal Power Dissipation PTC_MAX 9W
Case Operating Temperature TOPR -40 to 85 ºC
Case Storage Temperature TSTG -55 to 125 ºC
Weight 3.04 3.13 oz 86.2 g (LDTC0520)
88.7 g (LDTC1020)
Size 2.9 x 2.35 x 1.08 inches 73.6 x 59.7 x 27.3 mm
LASER DRIVER
SPECIFICATIONS SYMBOL LDTC0520 LDTC1020 UNIT NOTE
CONSTANT CURRENT CONTROL
Short Term Stability, 1 hour 35 to 40 ppm TAMBIENT = 25ºC
Long Term Stability, 24 hours 50 to 75 ppm TAMBIENT = 25ºC
CONSTANT POWER CONTROL
Short Term Stability, 1 hour 0.019 % TAMBIENT = 25ºC
Long Term Stability, 24 hours 0.011 % TAMBIENT = 25ºC
OUTPUT
Peak Current IMAX 495 to 505 990 to 1010 mA
Compliance Voltage VDD_FL - (0.5 * VEXT LD SET)VI
MAX = 500 mA
Rise Time 300 nsec ILD = 500 mA
Fall Time 300 nsec ILD = 500 mA
Bandwidth, Constant Current 2500 kHz Sinewave input signal
Delayed Start 100 msec
Slow Start Ramp 15 mA / msec
Depth of Modulation 99 % 100 kHz sinewave
POWER SUPPLY
Power Supply Voltage VDD_FL 3 to 12 V
Quiescent Current, VDD_FL 2.2 to 4.6 4.4 to 9.2 mA
EXT LD SET INPUT
Input Impedance 5 kΩ
Input Voltage Range VEXT LD SET 0 to 2 V
Damage Threshold -0.3 > VEXT LD SET > VDD_FL + 0.3 V
NOISE
Noise and Ripple (RMS) 7.5 22 μA RMS ILD =100mA;100kHzbandwidth
Leakage Current 1
0.2
0.3 mA VEXT LD SET = 0 V, Output = ON
VEXT LD SET = 0 V, Output = OFF
VEXT LD SET = 2 V, Output = OFF
1. Derate laser driver internal power dissipation by 34 mW / °C when operating above 25ºC. For the LDTC1020 with
dual FL500 chips, derating should be applied to both chips for a total of 68 mW / °C.
2. Modulation bandwidth in Constant Power mode is dependent on photodiode bandwidth, and is typically lower than the
bandwidth in Constant Current mode because of the frequency response of the photodiode.

© 2015 www.teamWavelength.com 8
LDTC0520 / LDTC1020 LASER DIODE AND TEMPERATURE CONTROLLER
ELECTRICAL SPECIFICATIONS (CONTINUED)
TEMPERATURE CONTROLLER
SPECIFICATIONS MIN TYP MAX UNIT NOTE
OUTPUT CURRENT
Max Output Current ±2.0 ±2.2 A
Compliance Voltage, TEC VS- 0.7 VS- 0.5 V Full Temp Range, ITEC = 100 mA
Compliance Voltage, TEC VS- 1.2 VS- 1.0 V Full Temp Range, ITEC = 1 A
Compliance Voltage, TEC VS- 1.6 VS- 1.4 V Full Temp Range, ITEC = 1.5 A
Compliance Voltage, TEC VS- 1.8 VS- 1.6 V Full Temp Range, ITEC = 2 A
Compliance Voltage, Resistive Heater VS- 1.7 VS- 1.6 V Full Temp Range, ITEC = 2 A
Short Term Stability, 1 hour 10.001 0.002 0.010 ºC OFF ambient, 10 kΩthermistor @ 25ºC
Short Term Stability, 1 hour 10.005 ºC ON ambient, 10 kΩthermistor @ 25ºC
Long Term Stability, 24 hours 10.003 0.008 0.010 ºC OFF ambient, 10 kΩthermistor @ 25ºC
Quiescent Current, VS20 50 100 mA
POWER SUPPLY
Power Supply Voltage, VDD_WTC 4.5 12 VDC
Quiescent Current, VDD_WTC 55 105 mA
Power Supply Voltage, VS4.5 30 VDC
TEMPERATURE SENSORS
Sensor Compatibility Thermistor, RTD, IC Sensors
Sensor Input Voltage Range2 0.25 to (VDD_WTC – 2.0) V
Sensor Input Damage Threshold 3.6 V
Sensor Bias Current Selection Adjustable, 2 μA to 1 mA
EXTERNAL SETPOINT AND MONITORS
EXT T SET Input Impedance 1 MΩ
EXT T SET Input Voltage Range 0 to 3.3 V
EXT T SET Input Damage Threshold 0 to 3.6 V
Setpoint vs. Actual Temperature Accuracy 0.1 2 4 mV TSET = 25ºC, 10 kΩthermistor
FEEDBACK LOOP
P (Proportional Gain) 18 20 22 A / V
I (Integrator Time Constant) 2 3 4.5 sec
1. When using resistive heaters, stability can only be consistently achieved when specified temperatures are 10°C or more
above ambient.
2. The sensor bias source has a compliance up to (VDD_WTC – 2.0 V). In normal operation this limits the sensor voltage range
to (0.25 V to VDD_WTC – 2.0 V). While voltages up to ±0.5 V outside this range on the EXT T SET pin will not damage the unit,
the controller will not provide proper control under these conditions.
NOTE: Operation at VS> 5 V or VDD_FL > 5 V requires evaluation of the SOA curves and current limit settings. Damage to
the LDTC will occur if it is operated outside the Safe Operating Area (SOA). See our online SOA calculator for:
WTC3243 at http://www.teamwavelength.com/support/calculator/soa/soatc.php
FL500 at http://www.teamwavelength.com/support/calculator/soa/soald.php.

© 2015 www.teamWavelength.com 9
LDTC0520 / LDTC1020 LASER DIODE AND TEMPERATURE CONTROLLER
THEORY OF OPERATION
The LDTC Laser Diode Driver and Temperature Controller
combines Wavelength’s proprietary FL500 and highly
stable WTC3243 in one compact module.
The LDTC0520 employs a single FL500 laser diode control
chip; the LDTC1020 parallels two FL500 chips. The current
source continually monitors the actual output current,
compares it to the setpoint, and adjusts the current if there
is a difference between the two signals.
Itmay be usefultorememberthat you do notdirectlysetthe
drive current setpoint; instead, you adjust a voltage signal
that represents the output current. The setpoint voltage is
controlled by the onboard trimpot or by an external input.
As current is driven through the load, there is a voltage
drop across the load because of the impedance. As the
current increases, the voltage drop may increase to the
point that it reaches the Compliance Voltage limit of the
current source. Once that occurs the current source is no
longer able to increase the current driven to the load even
if you increase the setpoint.
The LDTC laser driver includes features that help protect
your laser and make the driver more versatile in a wide
array of applications:
• The current limit is set by an onboard trimpot and
protects the laser from over-current conditions. The
current limit circuit is designed to avoid overshoot,
ringing,orsaturatingthecontrolelements,andrecovers
from limit events without phase shifts or inversions.
• Slow-start delays the current ramp by 100 msec,
and then ramps the current to setpoint at a rate
of 15 mA / msec.
• The photodiode feedback control loop allows for
Constant Power operation whereby the driver adjusts
the laser forward current in order to maintain a constant
photodiode current.
• Brownout protection switches off the laser diode drive
current if VDD_FL drops below 2.7 VDC.
The WTC3243 delivers bidirectional current to a Peltier
Effect thermoelectric cooler, or unidirectional current to a
resistive heater. The controller adjusts the output current
in order to change the temperature of the sensor that is
connected to the thermal load. The goal is to make the
voltage across the sensor match the setpoint voltage,
and then keep them equal in spite of changes to ambient
conditions and variations in thermal load.
SAFETY INFORMATION
& THERMAL DESIGN
CONSIDERATIONS
SAFE OPERATING AREA — DO NOT EXCEED
INTERNAL POWER DISSIPATION LIMITS
Before attempting to operate the LDTC, it is
imperative that you first determine that the laser driver
and temperature controller will operate within the
Safe Operating Area (SOA). Operating the unit outside of
the SOAmay damage the controller or the load, and will void
the warranty.
Go to the Wavelength Electronics website for the most
accurate, up-to-date, and easy to use SOA calculators:
Laser Diode Drivers:
http://www.teamwavelength.com/support/calculator/soa/soald.php
http://www.teamwavelength.com/support/calculator/soa/soald.php
Temperature Controllers:
Temperature Controllers:
http://www.teamwavelength.com/support/calculator/soa/soatc.php
http://www.teamwavelength.com/support/calculator/soa/soatc.php
SOAcharts are included in this datasheet for quick reference
(page 22), but we recommend you use the online tools
instead.
TOENSURE SAFE OPERATION OF THE LDTC CONTROLLER,
IT IS IMPERATIVE THAT YOU DETERMINE IF THE UNIT IS GOING
TO BE OPERATING WITHIN THE INTERNAL HEAT DISSIPATION
SAFE OPERATING AREA (SOA).
For more information on Safe Operating Area, see our
Application Note AN-LDTC01: The Principle of the Safe
Operating Area.
When you assemble and mount the TEC (or heater),
heatsink, and temperature sensor, make sure the physical
connections between the components are solid. We
recommend using thermal paste or thermal washers at the
load/TEC and TEC/heatsink interfaces. The thermistor must
be in firm contact with the load in order to achieve stable and
reliable temperature control.
PREVENT DAMAGE FROM
ELECTROSTATIC DISCHARGE
Before proceeding, it is critical that you take precautions to
prevent electrostatic discharge (ESD) damage to the driver
and your laser. ESD damage can result from improper
handling of sensitive electronics, and is easily preventable
with simple precautions.
Enter the search phrase “ESD Precautions for Handling
Electronics” in an internet search engine to find information
on ESD-safe handling practices.
We recommend that you always observe ESD precautions
when handling the LDTC controller and loads.
!

© 2015 www.teamWavelength.com 10
LDTC0520 / LDTC1020 LASER DIODE AND TEMPERATURE CONTROLLER
The controller measures the load temperature by driving a
current through the temperature sensor and measuring the
voltage drop across it. Similarly to the laser driver, you do
not directly adjust the setpoint on the temperature controller;
rather, you adjust a voltage signal that represents the sensor
voltage at the desired temperature setpoint. The controller
continuously compares the setpoint voltage and the actual
sensor voltage. If there is a difference between the two
signals the controller adjusts the output current—thereby
driving the TEC or heater to change temperature—until the
difference is zero.
Once the actual sensor voltage equals the setpoint voltage,
the controller makes minor adjustments to the output current
in order to keep the difference at zero.
The controller includes features that help protect the load
from damage, and also make it more versatile in a wide
array of applications.
• Independent heating and cooling current limits to protect
from thermal runaway situations.
• The temperature setpoint can be adjusted with the
onboard trimpot or by an external voltage signal.
• Controlloop:thecontrolleremploysasmartProportional-
Integrating control loop to adjust the drive current. The
proportional term is user-adjustable, and when properly
configured will quickly settle the load to temperature with
minimal overshoot and ringing.
OPERATING INSTRUCTIONS --
TEMPERATURE CONTROLLER
These instructions are written for the most common
application of the LDTCxx20 Controllers: driving a laser
diode, and controlling a Peltier-type thermoelectric cooler
witha10kΩthermistorsensor.Werecommendyoureadand
completely understand these instructions before proceeding
with wiring the controller. Information for other configurations
is also included in the technical support section on page
17.
Wavelength recommends configuring the temperature
controller before configuring the laser diode driver.
Additionally, we recommend using test loads to simulate
the thermistor, TEC or heater, laser diode, and photodiode.
Schematics for test loads are presented in Figure 6 and
Figure 7 on page 4.
These instructions detail the steps necessary to configure
the current limits for the temperature controller using a test
load. Once that is done, the controller is reconfigured with
the thermal load and sensor for your application. Then the
laser driver is configured with a test load. Finally, the laser
diode is connected and the LDTCxx20 is ready to enter
regular service.
!
MAKE CERTAIN THE OUTPUT LEADS ARE NOT SHORTED. IFTHE
LASER OUTPUT OR TEMPERATURE CONTROLLER OUTPUT
LEADS ARE SHORTED DURING SETUP, CURRENT WILL FLOW
AND THE LDTC MAY BE DAMAGED.
Wavelength recommends that initial wiring and configuration
of the LDTCxx20 is performed with test loads in place of
the TEC and thermistor. Using test loads reduces the risk
of damaging expensive components, and can make the
configuration process simpler.
The configuration sequence is as follows:
• Connect the power supplies and test loads
• Set the current limit
• Replace the test loads with your temperature sensor
and TEC
• Configure for external or local (internal) control
• Adjust the temperature setpoint and monitor the
controller

© 2015 www.teamWavelength.com 11
LDTC0520 / LDTC1020 LASER DIODE AND TEMPERATURE CONTROLLER
NECESSARY EQUIPMENT
The following equipment is the minimum necessary to
configure the LDTC for basic operation.
• LDTC controller
• Power supplies; choose low-noise power supplies for
the best performance and refer to page 11 for details
on each power supply requirement.
• VDD_FL – power supply for the laser driver electronics
and the laser diode
• VDD_WTC – power supply for the temperature controller
electronics
• VS– power supply to drive the TEC
• Digital multimeter, 4-½ digit resolution recommended
• Laser diode
• Thermistor or other temperature sensor
• Peltier-type thermoelectric module, or resistive heater,
heatsink for the temperature-controlled load, mounting
hardware, thermal washers or paste
• Connecting wires
ONBOARD ADJUSTMENTS AND CONTROLS
Figure 8 shows the onboard adjustments and controls that
are accessible with the cover on.
J1
J2
J3
Status LEDs
Laser Current Enable
Laser Current Setpoint
Laser Current Limit
Temperature Current Limit B
Temperature Setpoint
Temperature Current Limit A
DIP Switches *
DIP Switch Functions
LDREF = Internal vs. External Laser Diode Setpoint
CC | CP = Constant Current vs. Constant Power Control Mode
TREF = Internal vs. External Temperature Setpoint
* DO NOT CHANGE SWITCH POSITIONS WHILE THE OUTPUT
IS ENABLED; DOING SO MAY DAMAGE THE LOAD.
!
Figure 8. LDTC Top View
POWER SUPPLY REQUIREMENTS
The power supplies can be configured in a number of
different ways in order to integrate the LDTC more smoothly
into your application. The instructions provided in the
Configuration sections are for separate power supplies.
If the laser anode is connected to the laser diode case,
special precautions must be followed when configuring
the power supply. Refer to page 21 for more detailed
information.
Likewise, if the thermistor or TE module are case-common
with the laser diode, the LD and temperature controller
power supplies may need to be isolated from each other, or
a bipolar supply may be required. Refer to page 21.
• Separate VDD_WTC, VS, and VDD_FL
• VDD_WTC must be rated to at least 100 mA
• VSmust be rated for at least 1.1-times the current of
the temperature controller load
• VDD_FL must be rated for 1.1-times the laser current
plus 10 mA for the laser driver electronics
• Tied VDD_WTC and VS, separate VDD_FL
• The temperature controller power supply must be
rated for at least 1.1-times the maximum TEC or
heater current, plus 100 mA for the TEC control
electronics
• VDD_FL must be rated for 1.1-times the laser current
plus 10 mA for the laser driver electronics
• Refer to page 21 for important information if the
power supply inputs will be tied
• All three power supply inputs tied together and driven
from a single supply.
• The power supply must be rated for at least
1.1-times the maximum TEC or heater current, plus
1.1-times the maximum laser diode current, plus 100
mA for the TEC control electronics, plus 10 mA for
the laser driver electronics
• Refer to page 21 for important information if the
power supply inputs will be tied
Wavelength recommends using the best quality power
supplies available. Noise on the power supply inputs will
affect the overall system noise performance, particularly on
the laser driver.

© 2015 www.teamWavelength.com 12
LDTC0520 / LDTC1020 LASER DIODE AND TEMPERATURE CONTROLLER
WIRE THE TEMPERATURE CONTROLLER
POWER SUPPLIES AND TEST LOADS
Reference Figure 9 and wire the temperature controller
power supplies. Also connect the digital multimeter to the
monitor pins, as shown.
VDD_FL
VDD_WTC
VS
GND
SP1
SP2
LD SHD (Enable LD current)
COM
EXT LD SETpoint
COM
LD P Monitor
LD I Monitor
ACT T Monitor
SET T Monitor
EXT T SETpoint
COM
J1
J2
VDD_WTC
VS
1
1
4
12
DMM
Figure 9. Temperature Controller Power Supply and
Monitor Wiring
Next wire the temperature controller test loads, referencing
Figure 10 for details. With the test loads, to stay within the
Safe Operating Area, VSmust not exceed 5 V.
LDC
PDA
Spare
LDA
COM
TEC+
TEC-
SEN+
SEN-
COM
J3
1
10 Nȍ
RLOAD ȍ!:
IMETER
Figure 10. Temperature Controller Test Load Wiring
!OPERATING THE LDTC WITHOUT ATEMPERATURE
SENSOR WILL DRIVE MAXIMUM CURRENT THROUGH THE
TEC OR HEATER, POTENTIALLY DAMAGING IT.
SET THE TEMPERATURE CONTROLLER
CURRENT LIMITS
These instructions are for a TEC application; if you are
using a resistive heater refer to page 17 for instructions.
Refer to the datasheet for your TEC to determine the
maximum allowable drive current (ILIM). Measure the exact
resistance of the test load (RLOAD), then calculate the VLIM
voltage drop:
Equation 1. VLIM = ILIM * RLOAD
Adjust the simulated thermistor to a total resistance value of
10 kΩOhm to simulate room temperature.
Switch on the VDD_WTC and VSpower supplies; the
WTC POWER ON LED will illuminate green. As soon as
power is applied the temperature controller is active and will
drive current through RLOAD.
!
THE TEMPERATURE CONTROLLER OUTPUT IS ENABLED AS
SOON AS POWER IS SUPPLIED TO V
DD_WTC
AND V
S
. THE
WTC PWR ON LED ILLUMINATES GREEN WHEN POWER
IS ON TO THE TEMPERATURE CONTROLLER.
Next adjust the T SET trimpot fully counter-clockwise to
simulate a “high temperature” setpoint; this will cause the
controller to drive current through RLOAD in the direction that
would cause a TEC to heat. Adjust the LIM B trimpot until
the voltage displayed on the voltmeter matches the VLIM
value calculated above.
Adjust the T SET trimpot fully clockwise to simulate a “low
temperature” setpoint. This will cause the temperature
controller to drive current through RLOAD in the direction that
would cause a TEC to cool.Adjust the LIMAtrimpot until the
voltage matches VLIM.
Finally, adjust the T SET trimpot until the voltage across
RLOAD is zero. This step ensures that when the TEC and
thermistor are connected the temperature setpoint will be
approximately 25ºC, and the controller will not drive high
current through the TEC.
Switch off the power supplies.

© 2015 www.teamWavelength.com 13
LDTC0520 / LDTC1020 LASER DIODE AND TEMPERATURE CONTROLLER
WIRE THE LDTC FOR YOUR
TEMPERATURE CONTROL APPLICATION
Remove the test loads, and reconfigure the temperature
controller with your temperature sensor and load. Refer
to Table 4 to find the proper wiring diagram for your
configuration.
If the sensor is not a 10 kΩthermistor then you must make
internal modifications to the LDTC; refer to page 18.
Table 4. Wiring Diagram Reference
SENSOR TYPE LOAD
TYPE VDD_WTC AND
VSTIED SEE
FIGURE
NTC
(10 kΩThermistor)
TEC Either Figure 9
Heater* Yes Figure 17
No Figure 18
PTC
(RTD, LM335, etc)
TEC Either Figure 19
Heater* Yes Figure 20
No Figure 21
* Note that setting the LIM A and LIM B trimpots requires a
different procedure when using a resistive heater.
LDC
PDA
Spare
LDA
COM
TEC+
TEC-
SEN+
SEN-
COM
J3
See Note
Thermistor
1
10
-
+
Note: Current flows from TEC+ to TEC-.
Connect the TEC+ lead to pin J3-6 and
the TEC- lead to pin J3-7. Keep the wires
as short as possible to reduce lead voltage
drop at high current.
Figure 11. NTC sensor and TEC Wiring
CONFIGURE ONBOARD OR EXTERNAL
SETPOINT CONTROL
The temperature setpoint can be controlled with an onboard
trimpot, or by external signal input to pin J2-11.
Select the temperature setpoint reference by setting the
TREF switch; refer to Figure 12. To use the onboard trimpot
for temperature setpoint control, set the TREF switch to
INT (down). To reference the EXT T SET input, set the
TREF switch to EXT (up).
J1
J1
J2
J2
J3
J3
Figure 12. Configuration DIP Switches
ADJUST THE TEMPERATURE SETPOINT
If the LDTC is configured for onboard temperature control,
the setpoint is adjusted using the T SET trimpot, accessible
through the hole in the cover. The temperature setpoint
corresponds directly to the desired voltage drop across the
temperature sensor.
If the LDTC is configured for external setpoint control,
connect the signal source to pin J2-11. Example setpoint
circuits are shown on page 20, and the transfer function
for the EXT T SET input is shown in Table 2.
If the external temperature setpoint signal falls below 0.3 V,
the failsafe circuit in the controller will reset the temperature
setpoint to 1 V, corresponding to 25ºC when using a
10 kΩthermistor. To reset the failsafe circuit, the external
setpoint voltage must be set to > 0.4 V. The default safety
temperature can be changed at the factory; contact Sales
for more information.
MONITOR SENSOR VOLTAGE AND SETPOINT
VOLTAGE
Connector J2 includes outputs for monitoring actual
temperature sensor voltage and temperature setpoint
voltage. The specifications for the pins are indicated on
page 5, and the transfer functions listed in Table 2 on
page 6.
CONTROL LOOP TUNING
The PI loop parameters are configured at the factory, and
designed to work for a wide range of loads and applications.
The factory defaults are:
RP= R5 = 24.9 kΩ[PGAIN = 20 A / V]
RI= R6 = 31.6 kΩ[ITIME-CONSTANT = 2.2 seconds]

© 2015 www.teamWavelength.com 14
LDTC0520 / LDTC1020 LASER DIODE AND TEMPERATURE CONTROLLER
Table 5 lists the suggested resistor values for RPversus
sensor type and the ability of the thermal load to change
temperature rapidly.
Table 5. Proportional Gain Resistor RPvs. Sensor Type and
Thermal Load Speed
PROPORTIONAL
GAIN RESISTOR
RP
PROPORTIONAL
GAIN ( A / V)
SENSOR TYPE /
THERMAL LOAD
SPEED
4.99 kΩ5 Thermistor / Fast
24.9 kΩ20 Thermistor / Slow
100 kΩ50 RTD / Fast
Open 100 RTD / Slow
24.9 kΩ20 AD590 or LM335 /
Fast
100 kΩ50 AD590 or LM335 /
Slow
Use Equation 2 to calculate RPfrom PGAIN.
Equation 2. Calculating RPfrom PGAIN
R5 = R
P
=
(
100,000
)
[]
100 - 1
PGAIN
To calculate PGAIN from RPuse Equation 3.
Equation 3. Calculating PGAIN from RP
PGAIN =
(
100
)
[A / V]
100,000 + 1
RP
To locate RIand RP on Rev C only, refer to Figure 13.
Figure 13. RPand RIComponent Locator (Topside of Board)
Product Rev C only
Table 6 lists the suggested resistor values for RIversus
sensor type and the ability of the thermal load to change
temperature rapidly.
Table 6. Integrator Time Constant vs. Sensor Type and
Thermal Load Speed
INTEGRATOR
RESISTOR RI
INTEGRATOR
TIME
CONSTANT
(SECONDS)
SENSOR TYPE /
THERMAL LOAD
SPEED
21.4 kΩ3 Thermistor / Fast
13.3 kΩ4.5 Thermistor / Slow
Open 0.53 RTD / Fast
112 kΩ1 RTD / Slow
112 kΩ1AD590 or LM335 /
Fast
13.3 kΩ4.5 AD590 or LM335 /
Slow
Equation 4 demonstrates how to calculate a value for RI
given a desired integrator time constant. The Integrator
Time Constant, ITC, is measured in seconds.
Equation 4. Calculating RIfrom ITC
R6 = RI=
(
100,000
)
[]
(1.89) ITC - 1
Equation 5 demonstrates how to calculate the ITC, given a
value for RI.
Equation 5. Calculating ITC from RI
I
TC
= (0.53)
(
100,000 + 1
)
[Seconds]
R
I
To locate RIand RPon Rev A & B only, refer to Figure 14.
Figure 14. RPand RIComponent Locator (Topside of Board)
Product Rev A & B only
R
P
R
I

© 2015 www.teamWavelength.com 15
LDTC0520 / LDTC1020 LASER DIODE AND TEMPERATURE CONTROLLER
OPERATING INSTRUCTIONS --
LASER DRIVER
Wavelengthrecommendsthatinitial wiring andconfiguration
of the LDTCxx20 is performed with test loads in place of
the laser. Using test loads reduces the risk of damaging
expensive components, and can make the configuration
process simpler.
The configuration sequence is as follows:
• Connect the power supply and test load
• Set the current drive limit
• Replace the test load with your laser diode
• Adjust the laser drive setpoint
• Configure for external or local (internal) control
• Adjust the current setpoint and monitor the driver
WIRE THE LASER DRIVER POWER SUPPLY
AND TEST LOAD
The current limit is set with the driver in Constant Current
mode and can be set in two ways; the method described
here is done with the cover on the LDTC but requires the
output current be enabled.An alternate method is presented
on page 20.
Leave in place all the components that were connected
during the temperature controller configuration, and now
wire the laser driver power supply per Figure 15.
VDD_FL
VDD_WTC
VS
GND
SP1
SP2
LD SHD (Enable LD current)
COM
EXT LD SETpoint
COM
LD P Monitor
LD I Monitor
ACT T Monitor
SET T Monitor
EXT T SETpoint
COM
J1
J2
VDD_FL
1
1
4
12
DMM
Figure 15. Laser Driver Power Supply and
Monitor Wiring
Next wire the laser driver test load; refer to Figure 16. With
the test loads, to stay within the Safe Operating Area, VS
must not exceed 5 V.
LDC
PDA
Spare
LDA
COM
TEC+
TEC-
SEN+
SEN-
COM
J3
1
10
1N4001
(2x req’d)
ȍ:
Figure 16. Laser Driver Test Load Wiring
SET THE LASER DRIVER CURRENT LIMIT
Refer to the datasheet for your laser diode to determine the
maximum allowable drive current (ILIM). Measure the exact
resistance of the test load (RLOAD), then calculate the VLIM
voltage drop across the test load resistor:
Equation 6. VLIM = ILIM * RLOAD
Set the I SET trimpot to zero by turning fully counter-
clockwise at least 12 turns; set the I LIM trimpot to full-scale
by turning it clockwise at least 12 turns. Set the CC | CP
switch to CC.
Switch on the VDD_FL power supply; the FL POWER LED will
illuminate green. Set the onboard laser output switch to EN
to enable the current; the LD EN LED will illuminate green.
Adjust the I SET trimpot clockwise until the voltage on the
LD I Monitor pins (pin J2-8 to J2-6) matches the VLIM value
calculated above. Now adjust the I LIM trimpot down by
turning counter-clockwise until the voltage on the voltmeter
startstochange. Now the limit is setatthemaximumdesired
operating current.
Measure the voltage on the LD I MON pin; it should
correspond to the desired limit current value. Refer to Table
2 for the LD I MON transfer function for your LDTC model,
andverifythatthedrivecurrentiscorrect usingthisequation:
Equation 7. ILD = VLD MON * Transfer Function
Adjust the I SET trimpot counter-clockwise to zero the
setpoint current. Set the enable switch to DIS to disable
the output current, and switch off the VDD_FL power supply.
Remove the test load.
To practice using the driver in Constant Power mode, refer
to page 3 for the Constant Power test circuit.

© 2015 www.teamWavelength.com 16
LDTC0520 / LDTC1020 LASER DIODE AND TEMPERATURE CONTROLLER
WIRE THE LDTC FOR YOUR LASER DRIVER
APPLICATION
If you are comfortable with the operation of the LDTC laser
driver, connect your laser diode per Figure 2 on page 2.
This figure also shows how to connect the optional external
enable switch and external setpoint signal source. Example
setpoint circuits are shown on page 20. The transfer
function for the EXT LD SET input is shown in Table 2.
!
DONOT INSERT OR REMOVE THE LASER DIODE FROM THE
CIRCUIT WHILE POWER IS APPLIED TO THE LDTC. THE
LASER DIODE MAY BE DAMAGED OR DESTROYED.
SET CONSTANT POWER OR CONSTANT
CURRENT CONTROL MODE
Refer to Figure 12, and set the mode switch for Constant
Current or Constant Power mode: the mode switch is the
center DIP switch, labeled “CC | CP”. For Constant Current
mode operation, set the switch to INT (down); for Constant
Power mode, set the switch to EXT (up).
!
DONOT ADJUST THE CC | CP SWITCH WHILE THE OUTPUT
IS ENABLED AND DRIVING ALASER DIODE. THE LASER DIODE
MAY BE DAMAGED OR DESTROYED.
In CC mode, the setpoint voltage correlates directly to the
laser diode current. In CP mode the setpoint correlates to
the photodiode feedback current. See Table 2 on page
6for the transfer functions for CC and CP mode.
SET THE DRIVER FOR ONBOARD OR
EXTERNAL SETPOINT CONTROL
Next, set the reference source for the laser current setpoint.
To use the onboard trimpot to control the laser current
setpoint (Constant Current mode) or the laser power
(Constant Power mode),
1. Set the LDREF DIP switch to INT (down).
2. Ensure that LD SHD (pin J2-3) is tied to ground.
To use an external setpoint signal,
1. Set the LDREF DIP switch to EXT (up).
2. Connect the signal source to EXT LD Setpoint (pin
J2-5).
3. Ensure that the LD SHD (pin J2-3) is tied to ground.
!
DONOT ADJUST THE LDREF SWITCH WHILE THE OUTPUT IS
ENABLED AND DRIVING ALASER DIODE. THE LASER DIODE
MAY BE DAMAGED OR DESTROYED.
The laser output enable can be controlled from the onboard
switch, or by an external signal. If the external switch is
used, the onboard switch must be set to EN (enabled).
Both the external enable signal and the onboard enable
switch must be set to ENABLE for the LDTC to drive current
to the laser.
ADJUST THE LASER OUTPUT SETPOINT
If the LDTC is configured for onboard laser control, the
setpoint is adjusted using the I SET trimpot, accessible
through the hole in the front cover.
If the LDTC is configured for external setpoint control,
connect the signal source to pin J2-5. Example setpoint
circuits are shown on page 20, and the transfer function
for the EXT LD SET input is shown in Table 2.
MONITOR LASER DIODE AND PHOTODIODE
CURRENT
Connector J2 includes monitors for laser forward current
and photodiode current. Pin J2-8 is LD I Mon and pin J2-7
is LD P Mon.
The LD I Mon pin outputs a voltage proportional to the laser
diode forward current according to the transfer functions
listed in Table 2.
Both monitor signals are available at all times, regardless of
whether the driver is operating in CC or CP mode.
The LD P Mon pin outputs a voltage proportional to the
photodiode current; refer to Table 2 for the transfer function.
The standard maximum photodiode current is 2 mA. The
photodiode current range can be changed by replacing
a 1206-sized surface-mount resistor on the circuit board;
contact the factory for assistance.

© 2015 www.teamWavelength.com 17
LDTC0520 / LDTC1020 LASER DIODE AND TEMPERATURE CONTROLLER
ADDITIONAL TECHNICAL
INFORMATION
This section includes useful technical information on these
topics:
• Set the Current Limit When Using Resistive Heaters
• Wire the LDTC Temperature Controller, Alternate
Applications
• Set the Sensor Bias Current Resistor
• Use The LM335
• Use The AD590
• Adjust Sensor Gain
• External Setpoint Circuits
• An Alternate Method for Setting the
Laser Driver Current Limit
• Safely Tie the Power Supply Inputs
• Safe Operating Area Calculation
SET THE CURRENT LIMIT WHEN USING
RESISTIVE HEATERS
The instructions on page 12 do not apply when a
resistive heater is used. Follow the instructions provided
here instead.
First, set up the controller per page 13. Then follow these
steps:
• Calculate the voltage drop across the load resistor at
the limit current: VLIM = ILIM * RLOAD
• Adjust the “thermistor” test load to 10 kΩresistance
• Place the multimeter leads across the test load resistor
• Switch on the power supplies
• Adjust T SET fully counter-clockwise to simulate a high
temperature setpoint
• If you are using an NTC sensor:
• If VDD_WTC and VSare tied, the LIMAtrimpot must be set
to zero (fully counterclockwise at least 12 turns). This
trimpot is irrelevant if VDD_WTC and VSare separated.
• Adjust the LIM B trimpot until the voltage measured
across RLOAD matches VLIM calculated above.
• If you are using a PTC sensor:
• IfVDD_WTC and VSare tied, theLIMBtrimpotmust be set
to zero (fully counterclockwise at least 12 turns). This
trimpot is irrelevant if VDD_WTC and VSare separated.
• Adjust the LIM A trimpot until the voltage measured
across RLOAD matches VLIM calculated above
• Now adjust the T SET trimpot until the voltage across
RLOAD is close to zero. This step helps ensure the
controller will not drive high current once the resistive
heater is attached.
• Switch off the power supplies, disconnect the test loads,
and rewire the LDTC for your application.
WIRE THE LDTC TEMPERATURE CONTROLLER,
ALTERNATE APPLICATIONS
The LDTC can be wired in a number of different
configurations using different temperature sensors and load
transducers. Table 7 identifies which wiring diagram to use
for each case.
If the sensor is not a 10 kΩthermistor then you must make
internal modifications to the LDTC. Refer to page 18 and
page 19 for instructions on changing the internal gain
resistor and sensor bias resistor.
Table 7. Wiring Diagram Reference and LIM Trimpot
Functions
SENSOR TYPE LOAD
TYPE VDD_WTC AND
VSTIED SEE
FIGURE
NTC
(Thermistor)
TEC Either Figure 11
Heater* Yes Figure 13
No Figure 14
PTC
(RTD, LM335, etc)
TEC Either Figure 19
Heater* Yes Figure 20
No Figure 21
* Note that setting the LIM A and LIM B trimpots requires a
different procedure when using a resistive heater.
LDC
PDA
Spare
LDA
COM
TEC+
TEC-
SEN+
SEN-
COM
J3
Thermistor
1
10
V
DD_WTC
and V
S
Tied
Set LIM A trimpot to zero (fully counterclockwise)
Figure 17. Wiring for NTC Sensor and Resistive Heater,
VDD_WTC and VSTied
LDC
PDA
Spare
LDA
COM
TEC+
TEC-
SEN+
SEN-
COM
J3
Thermistor
1
10
VS
Separate V
DD_WTC
and V
S
LIM A trimpot setting is irrelevant
Figure 18. Wiring for NTC Sensor and Resistive Heater,
VDD_WTC and VSSeparate

© 2015 www.teamWavelength.com 18
LDTC0520 / LDTC1020 LASER DIODE AND TEMPERATURE CONTROLLER
SENSORS OTHER THAN A 10 KTHERMISTOR
The LDTCxx20 is factory-configured to bias a 10 kΩ
thermistor with 100 μAcurrent, but with simple modifications
other sensors can be used. The instructions for making the
changes are included here, and are recommended for users
with experience soldering surface mounted components.
These modifications can be made at the factory, as well.
SET THE SENSOR BIAS CURRENT RESISTOR
To change the sensor bias current, the 1206-sized surface
mount RBIAS resistor must be replaced. Table 8 indicates
the proper RBIAS and RSvalues, and Figure 22 shows the
location of the RBIAS resistor and RSpins.
The IBIAS current can be adjusted to other values based on
the value of RBIAS, according to the relation:
Equation 8. RBIAS = 2 / IBIAS (Ω)
The 100 Ωsensor gain resistor (RS) may need to be added
to two pins that protrude from the top of the circuit board
(read the Adjust Sensor Gain section below).
Table 8. RBIAS and RSValues for Alternate Temperature
Sensors
SENSOR TYPE RBIAS
VALUE
SENSOR
BIAS
CURRENT
RS
VALUE GAIN
2.25 kΩThermistor 2 kΩ1 mA Open 1
5 kΩThermistor 10 kΩ200 μA Open 1
10 kΩThermistor
Default 20 kΩ100 μA Open 1
20 kΩThermistor 40 kΩ50 μA Open 1
50 kΩThermistor 100 kΩ20 μA Open 1
100 kΩThermistor 200 kΩ10 μA Open 1
500 kΩThermistor 1 MΩ2 μA Open 1
100 ΩPt RTD 2 kΩ1 mA 100 Ω10
1 kΩPt RTD 2 kΩ1 mA Open 1
LM335 2 kΩ1 mA Open 1
AD590 Open – Open 1
LDC
PDA
Spare
LDA
COM
TEC+
TEC-
SEN+
SEN-
COM
J3
See Note
RTD
1
10
-
+
Note: Current flows from TEC- to TEC+. Connect the TEC+ lead to pin J3-7
and the TEC- lead to pin J3-6. Keep the wires as short as possible to reduce
lead voltage drop at high current.
Refer to AD590 and LM335 datasheets for instructions on using those sensors.
Nȍ
AD590
V+
LM335
R1
V+
Figure 19. Wiring for PTC Sensor and TEC
LDC
PDA
Spare
LDA
COM
TEC+
TEC-
SEN+
SEN-
COM
J3
1
10
RTD
VDD_WTC and VSTied
Set LIM B trimpot to zero (fully counterclockwise)
Nȍ
AD590
V+
LM335
R1
V+
Refer to AD590 and LM335 datasheets for instructions on using those sensors.
Figure 20. Wiring for PTC Sensor with Resistive Heater,
VDD_WTC and VSTied
LDC
PDA
Spare
LDA
COM
TEC+
TEC-
SEN+
SEN-
COM
J3
1
10
VS
RTD
Separate VDD_WTC and VS
LIM B trimpot setting is irrelevant
Refer to AD590 and LM335 datasheets for instructions on using those sensors.
Nȍ
AD590
V+
LM335
R1
V+
Figure 21. Wiring for PTC Sensor and Resistive Heater,
VDD_WTC and VSSeparated

© 2015 www.teamWavelength.com 19
LDTC0520 / LDTC1020 LASER DIODE AND TEMPERATURE CONTROLLER
RBias
Sensor Gain Resistor
5V ȍ
Figure 22. Sensor Gain Resistor and Location of RBIAS —
Rev C only
RBias
Sensor Gain Resistor
5V ȍ
Figure 23. Sensor Gain Resistor and Location of RBIAS —
Rev A & B only
ADJUST SENSOR GAIN
If the desired temperature setpoint results in a sensor
voltage below 250 mV, the temperature controller may
not achieve high levels of precision and stability. In such
cases the sensor voltage can be amplified by a factor of 10
by adding a 100 Ωsensor gain resistor (RS) as shown in
Figure 22.
Adding the sensor gain resistor to amplify the sensor
voltage requires amplifying the setpoint voltage, as well. For
example,inasystemusing a 100 ΩRTDbiasedat1mA, the
actual sensor voltage is 110 mV at 25ºC. If the RSresistor
is added, the controller will amplify the voltage internally to
1.10 V. The temperature setpoint value, therefore, will also
have to be 1.10 V.
USE THE LM335
To use an LM335 sensor refer to Table 7 for wiring
instructions specific to your application. Refer to the sensor
datasheet for the external resistor value and temperature
transfer function. Change the RBIAS resistor to 2 kΩ.
USE THE AD590
To use an AD590 sensor refer to Table 7 for wiring
instructions specific to your application. Refer to the sensor
datasheet for supply voltage requirements and temperature
transfer function. Remove RBIAS from the LDTC.
ADJUST THE PHOTODIODE FEEDBACK
CURRENT RANGE
The photodiode feedback resistor (R31) is 1 kΩ±1%, which
sets the maximum photodiode feedback current to 2 mA.
The RPD resistor can be changed in order to adjust the
photodiode feedback range.
To locate R31 on Rev C only, refer to Figure 24.
Figure 24. RPD Component Locator (Bottom of Board) —
Rev C only
To locate R31 on Rev A & B only, refer to Figure 25.
RPD
Figure 25. RPD Component Locator (Bottom of Board) —
Rev A & B only
To change RPD,
1. Remove the four screws from the four supports and lift
off the PCB to access the parts on the bottom side of
the board.
2. Calculate RPD value using Equation 3 -- IPDMAX is in mA
and RPD is in Ω.

© 2015 www.teamWavelength.com 20
LDTC0520 / LDTC1020 LASER DIODE AND TEMPERATURE CONTROLLER
Equation 3. Calculate RPD
I
PDMAX
=
(
2
)
R
PD
3. Change R31 appropriately.
4. Replace thermal compound on the FL500(s) and
reinstall PCB on the supports.
EXTERNAL SETPOINT CIRCUITS
With the TREF and LDREF switches set to EXT (up) the
LDTC will reference the analog inputs for the temperature
and laser current setpoints, respectively.
In both cases, a benchtop voltage source or DAC can be
used to generate the signal, or a simple voltage source
circuit can be built; refer to Figure 26 and Figure 27.
2.1 V Bandgap
Reference
VDD_WTC
EXT T SET
(Pin J2-11)
COM
(Pin J2-12)
R2
R1
R1 = 2.2 kΩ Multiturn Trimpot
R2 = VDD_WTC − 2.1
0.0015
Figure 26. Temperature Controller External Setpoint Circuit
2.1 V Bandgap
Reference
VDD_FL
COM
(Pin J2-4)
EXT LD SET
(Pin J2-5)
R1
R2
R1 = 2.2 kΩ Multiturn Trimpot
R2 = VDD_FL − 2.1
0.002
Figure 27. Laser Driver External Setpoint Circuit
AN ALTERNATE METHOD FOR SETTING THE
LASER DRIVER CURRENT LIMIT
The laser drive current can be set while using the test load,
as recommended on page 15, or it can be set while
monitoring an internal test point. Using this method, it is
not necessary to connect a test load or switch on the driver
output, but the cover must be removed from the LDTC.
Refer to the datasheet for your laser diode to find the
maximum recommended forward current, ILIM. Then
calculate the test point voltage value for the current limit
setting. The transfer function is found in Table 2, and varies
according to the controller model number.
Equation 4. VLD I LIM = ILIM / Transfer Function
RemovethetwoscrewssecuringthecoveroftheLDTCxx20,
lift off the cover, and locate the test point above the I LIM
trimpot; refer to Figure 28 for Rev C only and Figure 29 for
RevA& B only. Connect the positive lead of the DVM to the
test point, and the negative lead to one of the ground pins
on the J2 connector.
Connect the laser driver power supply and switch it on.
ILIM
J2
Figure 28. Current Limit Test Point and Trimpot —
Rev C only
Adjust the I LIM trimpot until the voltage displayed on the
multimeter matches the VLD I LIM value calculated above.
ILIM
J2
Figure 29. Current Limit Test Point and Trimpot —
Rev A & B only
Other manuals for LDTC0520
2
This manual suits for next models
1
Table of contents
Other Wavelength Electronics Control Unit manuals
Popular Control Unit manuals by other brands
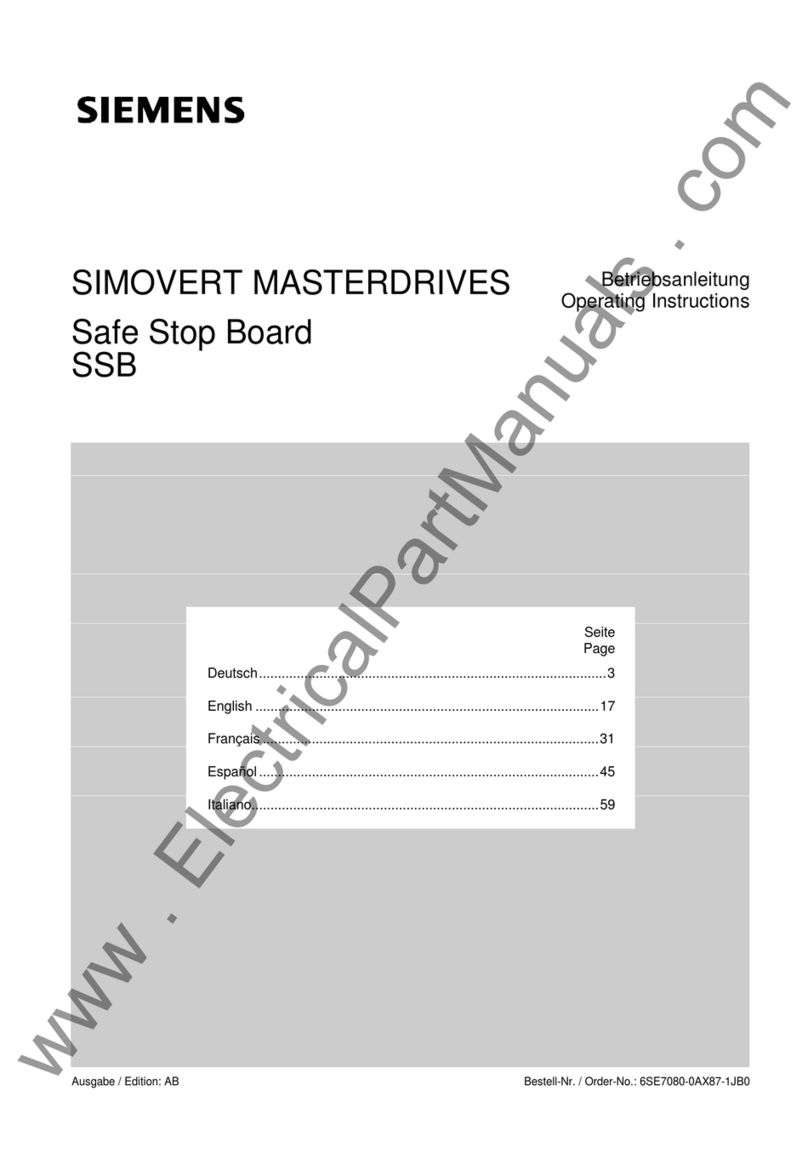
Siemens
Siemens SIMOVERT Masterdrives SSB operating instructions
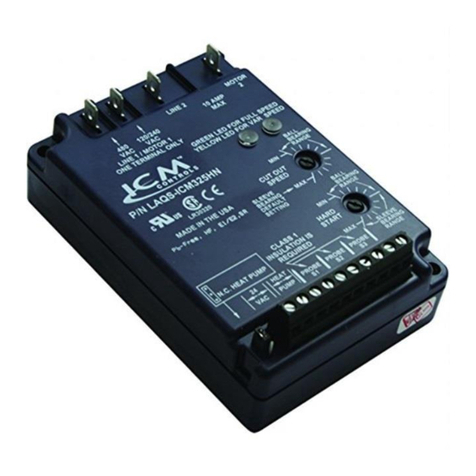
ICM Controls
ICM Controls ICM325HN Installation, operation & application guide
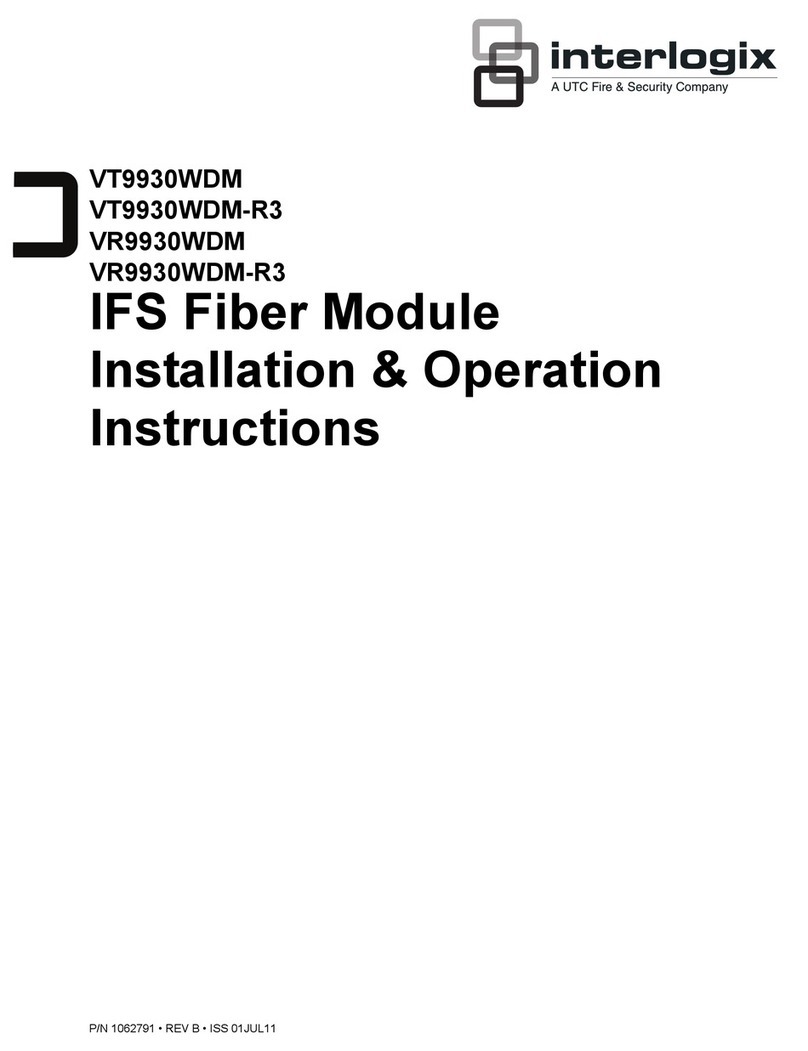
UTC Fire and Security
UTC Fire and Security interlogix VT9930WDM Installation & operation instructions
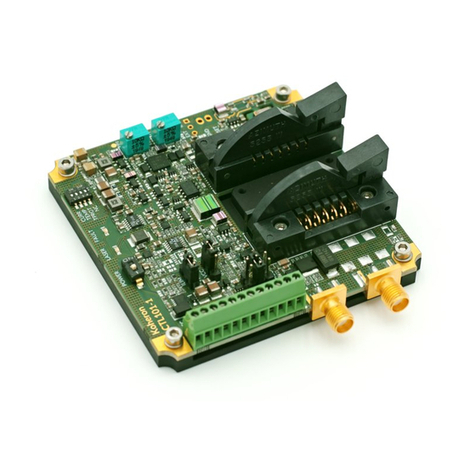
Koheron
Koheron CTL101 Series user guide
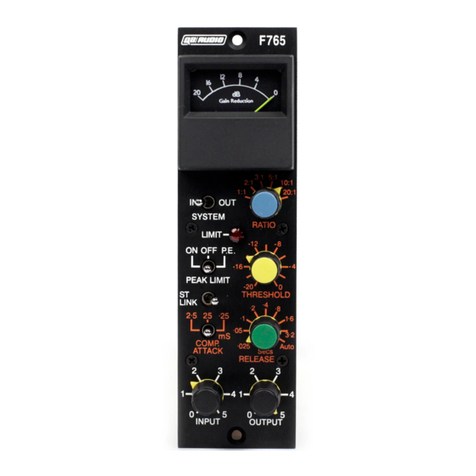
Q2 Audio
Q2 Audio F765 500 Series QUICK STAR
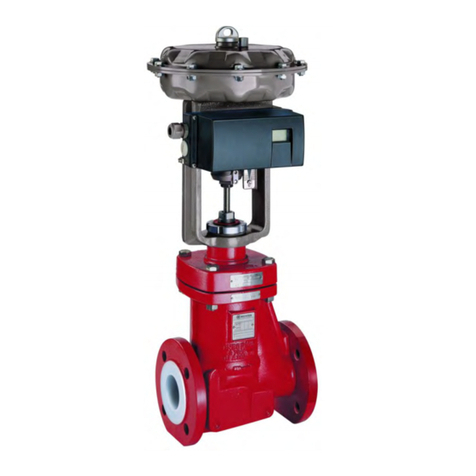
Richter
Richter RSS/F Series Installation and operating manual