WEG CFW500 Series User guide

Safety Functions Module
Módulo de Funciones de Seguridad
Módulo de Funções de Segurança
CFW500-SFY2
Safety Manual
Manual de Seguridad
Manual de Segurança
Motors | Automation | Energy | Transmission & Distribution | Coatings

Safety Manual
Series: CFW500
Language: English
Document: 10006503387 / 01
Date: 10/2019

2 | CFW500
English
Summary of Revisions
The table below describes all revisions made to this manual.
Version Manual
Revision
Product
Revision Description
-R00 AFirst edition
-R01 AGeneral revision and inclusion of TÜV certificate for safety
functions

CFW500 | 3
English
Contents
1 SAFETY .................................................................................................5
1.1 GENERAL INFORMATION ..........................................................................5
1.2 IMPLEMENTED SAFETY FUNCTIONS ......................................................6
1.2.1 Safe Torque Off (STO) .......................................................................7
1.2.2 Safe Stop 1 Time Controlled (SS1-t) ................................................7
1.3 SAFETY DATA .............................................................................................8
1.4 DECLARATION AND CERTIFICATION ......................................................9
2 INSTALLATION ...................................................................................11
2.1 SAFETY FUNCTIONS MODULE INSTALLATION ....................................11
2.2 SAFETY FUNCTIONS MODULE CONNECTIONS ...................................12
2.3 TYPES OF INSTALLATION .......................................................................13
2.4 SAFETY FUNCTIONS MODULE CONFIGURATION................................15
2.4.1 DIP Switches S1...............................................................................15
2.4.2 DIP Switches S2...............................................................................16
3 COMMISSIONING...............................................................................17
3.1 PARAMETERS RELATED TO THE SAFETY FUNCTIONS MODULE .....17
3.1.1 Parameters.......................................................................................17
3.2 START-UP..................................................................................................19
3.3 CONFIGURING THE SAFETY FUNCTION ..............................................20
4 MAINTENANCE AND TROUBLESHOOTING ....................................23
4.1 MAINTENANCE .........................................................................................23
4.2 ALARMS AND FAULTS RELATED TO THE SAFETY FUNCTIONS
MODULE ..........................................................................................................24
5 DECOMMISSIONING..........................................................................26

4 | CFW500
English
Contents

CFW500 | 5
English
Safety
1 SAFETY
1.1 GENERAL INFORMATION
NOTE!
These are the original instructions.
This safety manual provides the information necessary to install, configure and operate the
CFW500 frequency inverters equipped with the CFW500-SFY2 safety functions module and
must be used together with the other manuals of the CFW500. Please refer to the user’s
manual and the programming manual of the CFW500 for further details on installation, start-up,
technical features, troubleshooting and programming. All manuals are available for download
on website: www.weg.net.
NOTE!
Use the CFW500-SFY2 safety functions module only on WEG frequency
inverters from the CFW500 series.
DANGER!
Only duly qualified personnel, familiar with Functional Safety, with the
CFW500 frequency inverter, as well as any related equipment must plan
or perform the installation, commissioning, operation and maintenance of
this equipment.
Personnel must follow the safety instructions described in this manual and/
or defined by local standards.
Noncompliance with the safety instructions may result in death risk and/
or equipment damage.
NOTE!
For the purposes of this manual, qualified personnel are those trained in order
to be able to:
1. Install, ground, power up and operate the SCA06 in accordance with this
manual and the safety legal procedures in force.
2. Use the protective equipment according to the relevant standards.
3. Give first aid.
DANGER!
Always disconnect the general power supply before touching any electrical
component associated with the frequency inverter.
Many components may remain charged with high voltages and/or moving
(fans), even after the power supply input is disconnected or turned off.
Wait for at least ten minutes so as to guarantee the full discharge of the
capacitors.
Always connect the equipment to the protective earth (PE) at the appropriate
point.

6 | CFW500
English
Safety
ATTENTION!
The electronic boards have components sensitive to electrostatic discharges.
Do not touch directly the components or connectors.
If necessary, use proper grounding strap.
1.2 IMPLEMENTED SAFETY FUNCTIONS
When equipped with the CFW500-SFY2 safety functions module, the CFW500 frequency
inverter is able to perform two standardized safety stopping functions:
1. Safe torque off (STO) according to IEC/EN 61800-5-2 or Stop category 0 according to
IEC/EN 60204-1.
2. Safe stop 1 time controlled (SS1-t) according to IEC/EN 61800-5-2 or Stop category 1 according
to IEC/EN 60204-1.
ATTENTION!
Even when the safety stop function is active, dangerous voltage levels may
be present in the motor. Thus, before any intervention on electrical parts, the
system must be completely de-energized.
ATTENTION!
In applications where external influences are relevant (e.g. fall of suspended
loads), additional measures (e.g. use of mechanical brakes) may be necessary
to prevent any hazard. The risk analysis must be performed by the end user
in order to identify and cover all possible hazards and risks in the application.
NOTE!
The safety stop functions should not be used as a control for starting and/or
stopping the motor.
NOTE!
The safety stop functions take priority over all other functions of the frequency
inverter.
NOTE!
The safety of the entire system depends on the final certification of the
equipment where the frequency inverter is applied. WEG is not liable for
damages and/or losses during the use or application of the frequency inverter.
For these reasons, WEG cannot be held accountable for applications based
on the figures and examples described in this manual, which are presented
for illustrative purposes only.

CFW500 | 7
English
Safety
1.2.1 Safe Torque Off (STO)
The STO safety function acts on the removal of torque from the motor, i.e., no power that can
generate torque is present on the motor after enabling this function. The difference between
STO and other ways to disable the motor is that the former does it with very high levels of
reliability against unexpected motor starts, even under a fault condition - refer to Section 1.3
SAFETY DATA on page 8.
Once activated, the STO safety function removes the power from the frequency inverter’s
output electronic circuit, causing the motor to coast to a stop - see Figure 1.1 on page 7.
Time
Motor speed
STO
Figure 1.1: STO behavior
1.2.2 Safe Stop 1 Time Controlled (SS1-t)
Differently from the STO safety function, which, when active, must promptly ensure that there
is no torque-generating energy at the frequency inverter output, the SS1-t safety function,
when active, will wait a predefined delay time before performing the STO, in order to allow the
frequency inverter to impose a deceleration ramp to the motor before removing the torque-
generating energy. The SS1-t is especially useful in applications where inertial loads need to
be decelerated before torque is removed from the motor.
Figure 1.2 on page 7 illustrates the behavior of the SS1-t safety function, where it is possible
to observe the controlled delay time between the green bars in the figure. The safety functions
module should be configured with a time value equal to or greater than the frequency inverter's
capacity to decelerate the load; otherwise, the torque-off state may be reached before the
complete stop of the load.
P0108
Motor speed
SS1-t STO
Time
Figure 1.2: SS1-t behavior

8 | CFW500
English
Safety
NOTE!
According to IEC/EN 61800-5-2, the deceleration ramp of the SS1-t safety
function may fail undetectably. Therefore, this function must not be used if this
failure could cause a dangerous situation in the final application.
1.3 SAFETY DATA
The safety data for the CFW500 frequency inverter equipped with the CFW500-SFY2 is
presented in Table 1.1 on page 8.
Table 1.1: Safety data
Safety functions
Safe torque off (STO), as per IEC 61800-5-2
Stop category 0, as per IEC 60204-1
Safe stop 1 time controlled (SS1-t), as per IEC 61800-5-2
Stop category 1, as per IEC 60204-1
Safety category SIL 3, as per IEC 61508 / IEC 62061 / IEC 61800-5-2
PL e, category 4, as per EN ISO 13849-1
PFDavg < 2.74 . 10-4
PFH (1/h) < 3.13 . 10-9
MTTFd(y) > 1600 years
DCavg > 93 %
Proof test interval 20 years (*)
Response/reaction time < 100 ms
OSSD test pulses
Pulse duration: < 1 ms
Interval between pulses on the same channel: > 8 ms
Interval between pulses on different channels: > 4 ms
Safety input signals ON: 15 Vdc … < 30 Vdc
OFF: < 2 V
Maximum discrepancy time between
safety input signals 1 s
Safety power supply
+ 24 Vdc ± 15 %,
SELV type according to IEC 60950-1
or PELV type according to IEC 60204-1
(*) This means that the lifetime, or mission time, of the product is limited to 20 years, i.e. the product shall be replaced after
20 years.
NOTE!
The control accessories of the CFW500 frequency inverter provide a + 24 Vdc
power supply (150 mA, PELV type), which can be used to supply the CFW500-SFY2.
NOTE!
General data about the CFW500 frequency inverter can be found in the user’s
manual, available for download on the website: www.weg.net.

CFW500 | 9
English
Safety
1.4 DECLARATION AND CERTIFICATION

10 | CFW500
English
Safety
EC Type-Examination Certificate
Reg.-No.: 01/205/5723.00/19
Product tested Safety Functions "Safe Torque Off
(STO)" and "Safe Stop 1 time
controlled (SS1-t)" within Frequency
Inverters
Certificate
holder
WEG DRIVES &
CONTROLS -
AUTOMAÇÃO LTDA
AV. Pref. Waldemar
Grubba, 3000
89256-900 Jaraguá do Sul
/ SC
Brazil
Type designation Safety Module CFW500-SFY2 for the CFW5XX inverter series.
Details see current "Revision List"
Codes and standards EN 61800-5-2:2017
EN 61800-5-1:2007 + A1:2017
EN 61800-3:2018
EN ISO 13849-1:2015
EN 62061:2005 + AC:2010 + A1:2013 +
A2:2015
IEC 61508 Parts 1-7:2010
EN 60204-1:2018 (in extracts)
Intended application The safety functions STO and SS1-t comply with the requirements of the relevant
standards (Cat. 4 / PL e acc. to EN ISO 13849-1, SIL 3 / SIL CL 3 acc. to
EN 61800-5-2 / IEC 61508 / EN 62061) and can be used in applications up to
Cat. 4 / PL e acc. to EN ISO 13849-1 and SIL 3 acc. to EN 62061 / IEC 61508.
Specific requirements The instructions of the associated Installation and Operating Manual shall be
considered.
It is confirmed, that the product under test complies with the requirements for machines defined in Annex I of the EC
Directive 2006/42/EC.
Valid until 2024-09-25
The issue of this certificate is based upon an examination, whose results are documented in
Report No. 968/FSP 1886.00/19 dated 2019-09-25.
This certificate is valid only for products which are identical with the product tested.
Notified Body for Machinery, NB 0035
Dipl.-Ing. Eberhard Frejno
Köln, 2019-09-25
10/222 12. 12 E A4 ® TÜV, TUEV and TUV are registered trademarks. Utilisation and application requires prior approval.
TÜV Rheinland Industrie Service GmbH, Am Grauen Stein, 51105 Köln / Germany
www.fs-products.com

CFW500 | 11
English
Installation
2 INSTALLATION
The inverter must be installed according to the instructions of the CFW500 user’s manual.
Table 2.1 on page 11 presents the technical data related to the CFW500-SFY2 safety functions
module.
Table 2.1: CFW500-SFY2 technical data
Dimensions Figure A.3 on page 80 in Appendix A
Mass 56 g
Enclosure IP20
Operating Temperature -10 °C … 40 °C (14 °F ... 104 °F)
Storage Temperature -25 °C … 60 °C (-13 °F ... 140 °F)
Air Relative Humidity 5 % to 95 % non-condensing
Maximum Altitude
Up to 2000 m: nominal conditions
From 2000 m to 4000 m: voltage derating of 1.1 % for each 100 m above
2000 m
Pollution Degree
2 (according to EN 50178 and UL 508C), with non-conductive pollution
Condensation must not originate conduction through the accumulated
residues
ATTENTION!
If pollution degree 2 cannot be guaranteed, IP54 protection class must be used.
2.1 SAFETY FUNCTIONS MODULE INSTALLATION
For the proper installation of the safety functions module, follow the steps below:
Step 1: With the CFW500 de-energized, remove the STO jumper connector locate on top of
the frequency inverter according to Figure A.1 on page 79 (a).
Step 2: Fit and press the CFW500-SFY2 to be installed on top of the frequency inverter according
to Figure A.1 on page 79 (b).
Step 3: Follow the energization and start-up procedure described in the CFW500 user's manual.
Step 4: Check whether parameter P0028 is showing value 1 (P0028 = 1). If this is not the case,
check the connection of the CFW500-SFY2 module on top of the frequency inverter and repeat
the steps above.
NOTE!
Either the STO jumper connector or the CFW500-SFY2 safety functions module
must be installed on top of the frequency inverter. Otherwise, the fault message
"F0086" will be displayed by the frequency inverter during power-on.

12 | CFW500
English
Installation
2.2 SAFETY FUNCTIONS MODULE CONNECTIONS
The safety-related signals must be connected to connector XC7 of the CFW500-SFY2. The
location of this connector, as well as the location of the DIP switches S1 and S2, is indicated
in Figure 2.1 on page 12.
XC7
S2S1
Figure 2.1: Location of connector XC7 and DIP switches S1 and S2
Table 2.2 on page 12 describes the safety signals on connector XC7.
Table 2.2: Safety signals on XC7
Pin Name Description
1 + 24 Vdc Input for + 24 Vdc PELV/SELV
2SP1 Safety signal for STO1 input
3STO1 Safety input 1
4SP2 Safety signal for STO2 input
5STO2 Safety input 2
6GND Reference for + 24 Vdc PELV/SELV power supply
The + 24 Vdc power supply to be used with the CFW500-SFY2 must comply with the low
voltage directive 2006/95/EC, applying the specifications of IEC/EN 61131-2, Programmable
controllers - Part 2: Equipment requirements and tests, and it must comply with one of the
following specifications:
Safety extra-low voltage (SELV), according to IEC/EN 60950-1.
Protected extra-low voltage (PELV), according to IEC/EN 60204-1.
NOTE!
The control accessories of the CFW500 frequency inverter provide a + 24 Vdc power
supply (150 mA, PELV type), which can be used to supply the CFW500-SFY2.

CFW500 | 13
English
Installation
For XC7 cabling, consider the following:
Wire stripping length: 6.0 mm (0.236 in).
Wire gauge from 0.5 mm² (20 AWG) to 1.5 mm² (16 AWG).
Maximum tightening torque of 0.40 Nm (3.5 lbf.in).
Run the cables separated from the remaining circuits (power, 110 V / 220 V control, etc.).
NOTE!
The other control signals that are not related to safety (digital/analog inputs
and outputs) are connected to one of the control accessories of the frequency
inverter. The cables for these control signals must not exceed 30 m when the
CFW500 frequency inverter is equipped with the CFW500-SFY2.
2.3 TYPES OF INSTALLATION
There are two types of installation, depending on the type of the safety device that requests
the safety function:
Installation with dry contact devices, i.e. devices that have electromechanical output
(conventional relays, for example).
Installation with OSSD (Output Signal Switching Device), i.e. solid state devices that have
outputs containing test pulses (light curtain, for example).
Figure 2.2 on page 13 illustrates the installation with dry contacts, and Table 2.3 on page 14
describes its operation.
+ 24 Vdc
STO1
STO2
GND
1
2
3
4
5
6
Figure 2.2: Installation using dry contacts

14 | CFW500
English
Installation
Table 2.3: Truth table for dry contacts operation
STO1
(contact
between
XC7:2 and
XC7:3)
STO2
(contact
between
XC7:4 and
XC7:5)
Safety Stop
Function Frequency Inverter Behavior
Open Open Enabled
Frequency inverter remains in the safe state. Starting
commands are not accepted in this state. HMI display
indicates alarm A0160
Open Closed
Fault
Frequency inverter trips to fault F0160 if such input
configuration lasts longer than 1 s. To reset this fault, STO1
and STO2 must be in the same logical state and the frequency
inverter must be de-energized and re-energized
Closed Open
Closed Closed Disabled Frequency inverter operates normally, accepting starting
commands
Figure 2.3 on page 14 illustrates the installation with OSSD, and Table 2.4 on page 14
describes its operation.
STO1
STO2
GND
1
2
3
4
5
6
Figure 2.3: Installation using OSSD signals
Table 2.4: Truth table for OSSD signals
STO1
(voltage on
XC7:3)
STO2
(voltage on
XC7:5)
Safety Stop
Function Frequency Inverter Behavior
0 V 0 V Enabled
Frequency inverter remains in the safe state. Starting
commands are not accepted in this state. HMI display indicates
alarm A0160
0 V + 24 V
Fault
Frequency inverter trips to fault F0160 if such input configuration
lasts longer than 1 s. To reset this fault, STO1 and STO2 must
be in the same logical state and the frequency inverter must be
de-energized and re-energized
+ 24 V 0 V
+ 24 V + 24 V Disabled Frequency inverter operates normally, accepting starting
commands

CFW500 | 15
English
Installation
2.4 SAFETY FUNCTIONS MODULE CONFIGURATION
2.4.1 DIP Switches S1
In order to configure the CFW500-SFY2 safety functions module for the appropriate type of
installation, the DIP switches S1 must be set before energization, according to Table 2.5 on
page 15, where "D" stands for "dry contacts" and "O" stands for "OSSD".
NOTE!
Setting the DIP switches S1 to "D" or "O" after energization has no effect on
the equipment.
Table 2.5: DIP switches S1
Configuration Description
D
O
Both DIP switches set to "D" (dry contact)
This configuration must be chosen when the safety signals are
controlled by dry contacts as shown in Figure 2.2 on page 13
D
O
One DIP switch set to "D" (dry contact) and the other set to "O" (OSSD)
This is not a valid combination and results in a fault state (F0160),
displayed on the frequency inverter after the energization. The
frequency inverter will not work
D
O
D
O
Both DIP switches set to "O" (OSSD)
This configuration must be chosen when safety signals are
controlled by an OSSD output, as shown in Figure 2.3 on page 14

16 | CFW500
English
Commissioning
2.4.2 DIP Switches S2
The DIP switches S2 control the access to the programming mode of the CFW500-SFY2, which
enables the selection of which safety function will be used, as well as the definition of the delay time
in case of SS1-t. The programming procedure is described in details in Section 3.3 CONFIGURING
THE SAFETY FUNCTION on page 20.
Table 2.6: DIP switches S2
Configuration Description
OFF
ON
Both DIP switches set to ON
This configuration activates the programming mode of the
CFW500-SFY2, displaying alarm A0162 on HMI. For programming
the safety functions module, proceed according to Section 3.3
CONFIGURING THE SAFETY FUNCTION on page 20
OFF
ON
One DIP switch set to ON and the other to OFF
This is not a valid combination and the programming cannot be
completed
OFF
ON
OFF
ON
Both DIP switches set to OFF
This configuration disables the programming mode of the
CFW500-SFY2
NOTE!
The DIP switches S2 must only be set to the ON position when CFW500-SFY2
is in the safe state, which is indicated by alarm A0160 on HMI. Trying to enter
the programming state from any state other than the safe state will result in the
fault state, which is indicated by fault F0160 on HMI.

CFW500 | 17
English
Commissioning
3 COMMISSIONING
3.1 PARAMETERS RELATED TO THE SAFETY FUNCTIONS MODULE
The parameters of the CFW500 frequency inverter that are directly related to the safety functions
module are presented below.
Symbols used to describe parameter properties:
ro: read only parameter.
sy: parameter only visible on HMI when the safety functions module is in the programming mode.
3.1.1 Parameters
P0028 - Safety Functions Module
Adjustable
Range:
0 = STO Jumper Connector
1 = CFW500-SFY2
Factory
Setting:
-
Properties: ro
Access Groups
via HMI:
READ
Description:
It identifies the safety functions module connected to the frequency inverter, according to
Table 3.1 na página 17.
Table 3.1: Identification of the safety functions module
Name Description P0028
STO Jumper Connector Frequency inverter without functional safety 0
CFW500-SFY2 Frequency inverter is equipped with a safety functions module
capable of performing STO and SS1-t 1
NOTE!
Either the STO jumper connector or the CFW500-SFY2 must be installed on
top of the frequency inverter. Otherwise, the fault message "F0086" will be
displayed by the frequency inverter during power-on.
P0106 - 3rd Ramp Time
Adjustable
Range:
0.1 to 999.0 s Factory
Setting:
5.0 s
Properties:
Access Groups
via HMI:
Description:
It defines the acceleration time from zero to maximum speed (P0134) or deceleration from
maximum speed (P0134) to zero for the 3rd Ramp.

18 | CFW500
English
Commissioning
NOTE!
The frequency inverter uses the 3rd Ramp to decelerate the motor when the
SS1-t safety function is requested. The frequency inverter uses the 3rd Ramp
to decelerate the motor when the SS1-t safety function is requested. Therefore,
when using SS1-t, only modify this parameter during the configuration of the
CFW500-SFY2.
P0108 - SS1-t Time
Adjustable
Range:
0 to 999 s Factory
Setting:
0 s
Properties: sy
Access Groups
via HMI:
Description:
It defines the delay time of the SS1-t safety function to be programmed in the safety functions
module. If the delay time value is 0 seconds, the safety functions module is programmed with
the STO safety function.
NOTE!
P0108 is only visible on HMI and, therefore, can only be modified when the
safety functions module is in the programming mode.
P0109 - SS1-t Time Confirmation
Adjustable
Range:
0 to 999 s Factory
Setting:
Properties: ro, sy
Access Groups
via HMI:
Description:
During the programming procedure of the safety functions module, it indicates the actual value
of the delay time programmed in the safety module for the user's confirmation.
NOTE!
P0109 is only visible on HMI and, therefore, can only be accessed when the
safety functions module is in the programming mode.

CFW500 | 19
English
Commissioning
3.2 START-UP
Start-up sequence:
1) Execute the mechanical and electrical installation of the frequency inverter according to the
CFW500 user's manual and the safety manual.
2) Configure the DIP switches S1 according to the type of safety signal (dry contact or OSSD),
and set the DIP switches S2 to OFF.
3) Set the safety inputs to the safe state, i.e. open contacts or apply 0 V on STO1 and STO2.
4) Make sure the motor is not coupled to the machine or, if coupled, it must be able to rotate
in any direction without any risk of human harm or machine damage.
5) Energize the frequency inverter.
6) Load CFW500 factory default parametrization via P0204 and check that parameter P0028
indicates 1 (CFW500-SFY2).
7) Program the frequency inverter according to the application requirements.
8) If the SS1-t safety function is required, follow the steps described in Section 3.3
CONFIGURING THE SAFETY FUNCTION on page 20.
9) Set the safety inputs to the operational state, i.e. close contacts or apply + 24 V on STO1
and STO2 simultaneously.
10) Check if the motor runs and stops by pressing the "I" and "0" keys of the HMI.
11) Run the motor and set the safety inputs to the safe state, i.e. open contacts or apply 0 V
on STO1 and STO2 simultaneously.
12) Check if the motor stops when the safe state is activated, indicating alarm A0160 on the HMI.
13) Set the safety inputs to the operational state, i.e. close contacts or apply + 24 V on STO1
and STO2 simultaneously.
14) Check if the motor runs again using the "I" and "0" keys.
15) Check all other application functionalities in order to ensure the correct behavior and the
overall safety of the system in which CFW500 is installed.
ATTENTION!
The steps above are the minimum necessary to verify the integrity of the
frequency inverter's safety function. In order to verify the overall operation and
safety of the machine or system, other steps may be necessary. The machine
manufacturer is responsible for the final verification and certification of the safety
of the machine or system where the frequency inverter is applied.
ATTENTION!
Whenever the safety function is reconfigured, it is mandatory to carry out an
operation verification test.
Other manuals for CFW500 Series
3
This manual suits for next models
1
Table of contents
Languages:
Other WEG Control Unit manuals
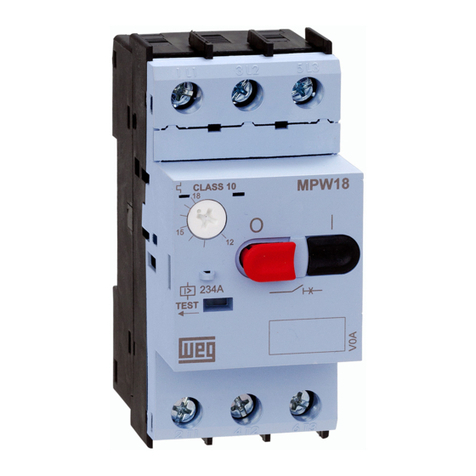
WEG
WEG MPW18 User manual
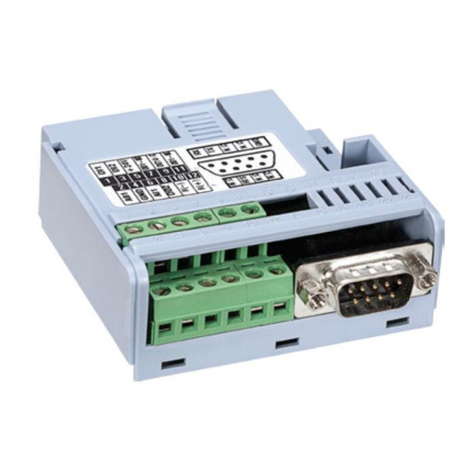
WEG
WEG CFW500-RS232 Quick guide
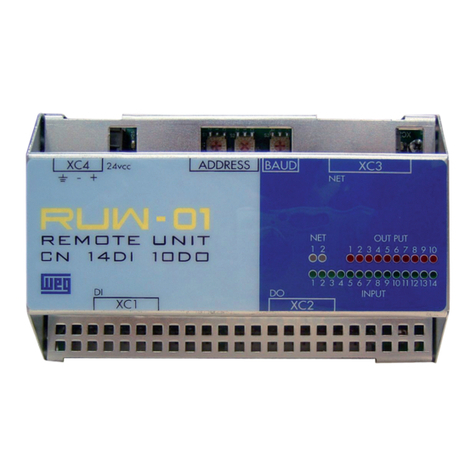
WEG
WEG RUW-01 Quick guide
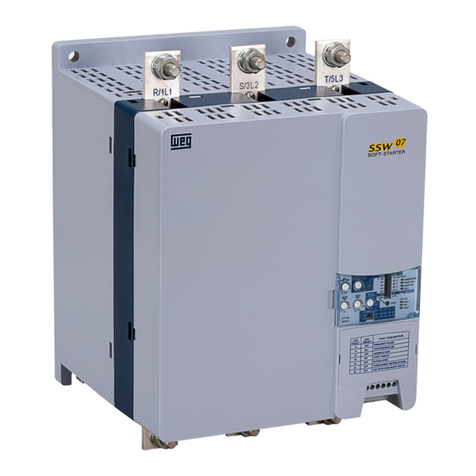
WEG
WEG SSW07 Series User manual
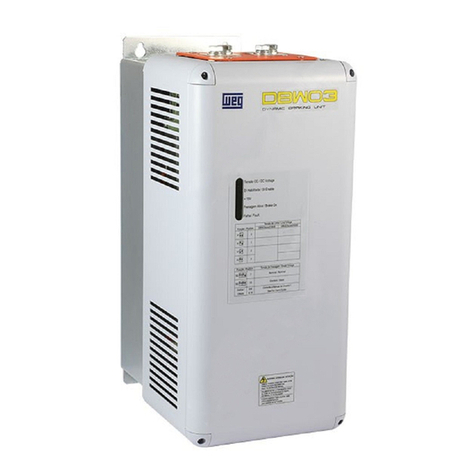
WEG
WEG DBW03 Series User manual
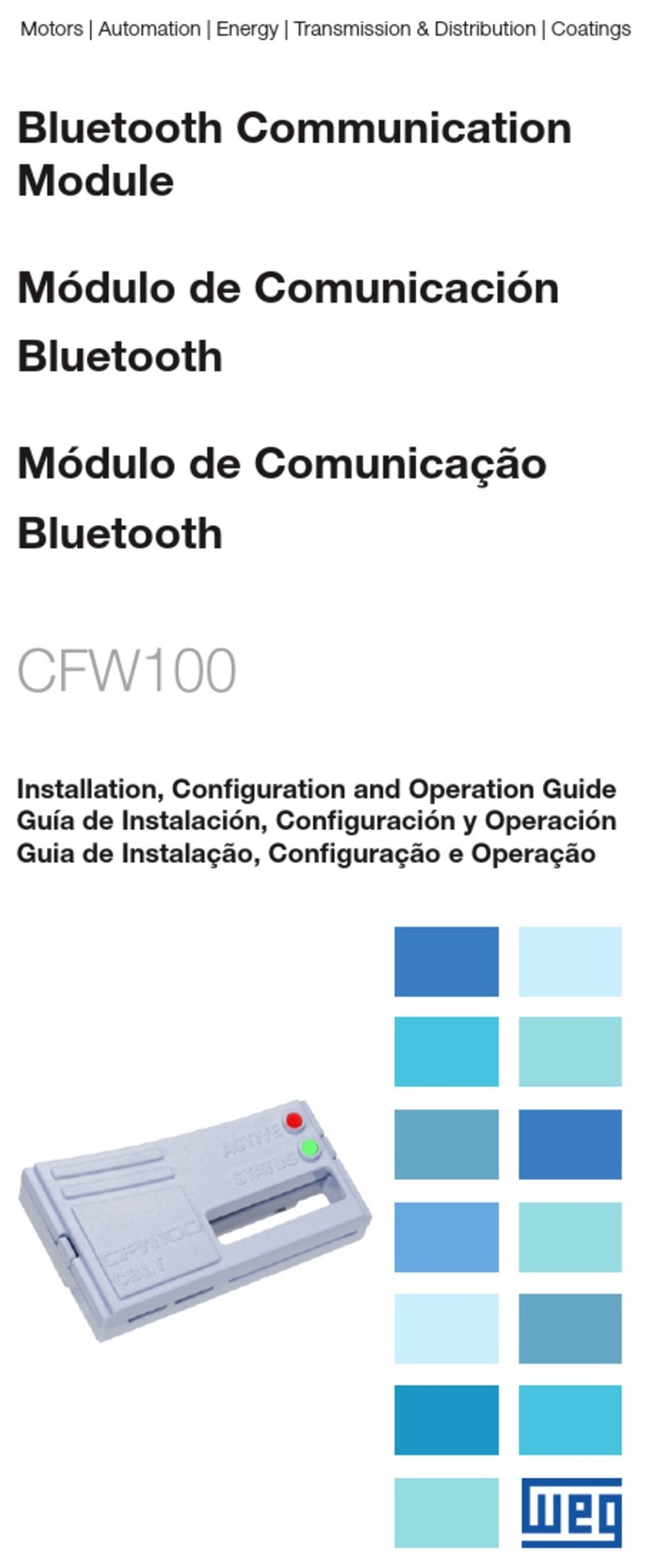
WEG
WEG CFW100 series Quick guide
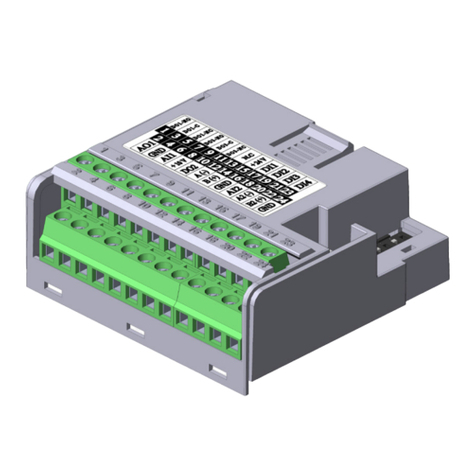
WEG
WEG DeviceNet CFW500 Quick guide
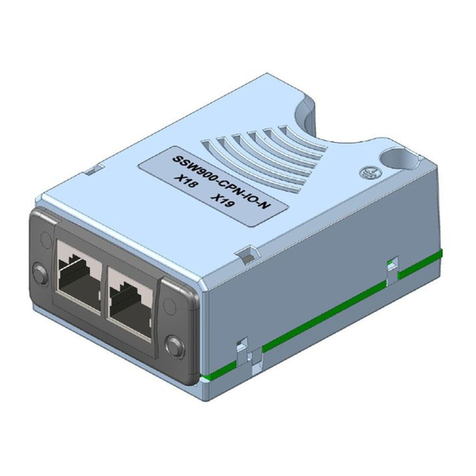
WEG
WEG SSW900-CPN-IO-N Quick guide

WEG
WEG Anybus Quick guide
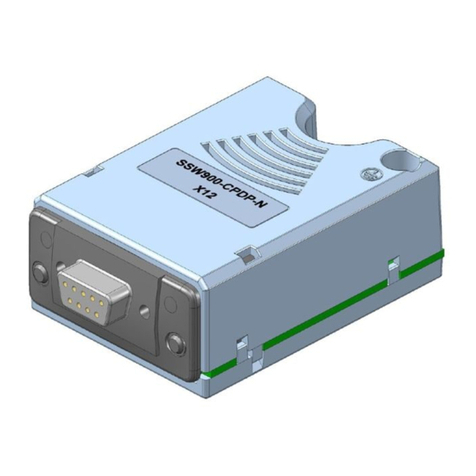
WEG
WEG SSW900-CPDP-N Quick guide
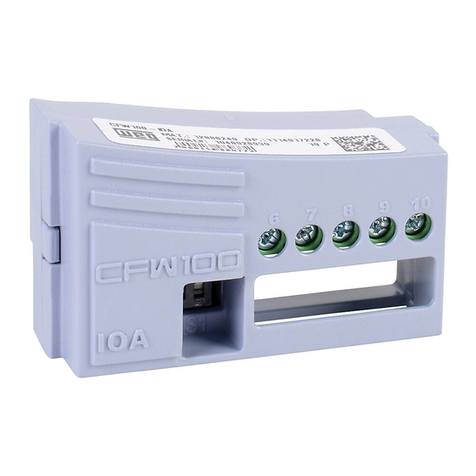
WEG
WEG CFW100-IOA Quick guide

WEG
WEG CFW500-IOR-B User manual

WEG
WEG CFW500 Series Quick guide

WEG
WEG PBW-1 User manual
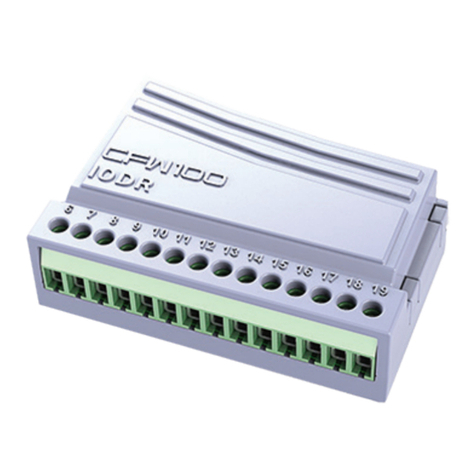
WEG
WEG CFW100-IODR Quick guide
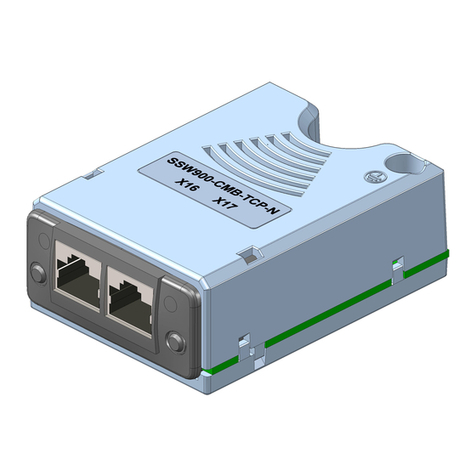
WEG
WEG SSW900-CMB-TCP-N Quick guide
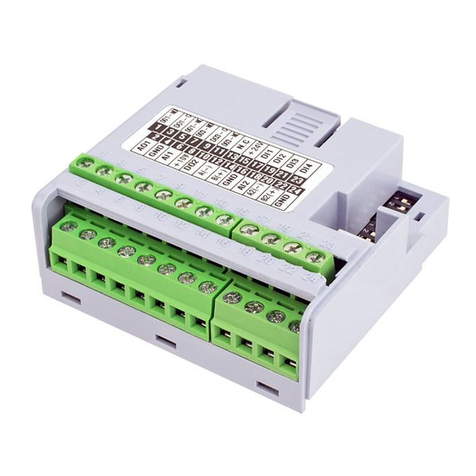
WEG
WEG CFW500 Series Quick guide
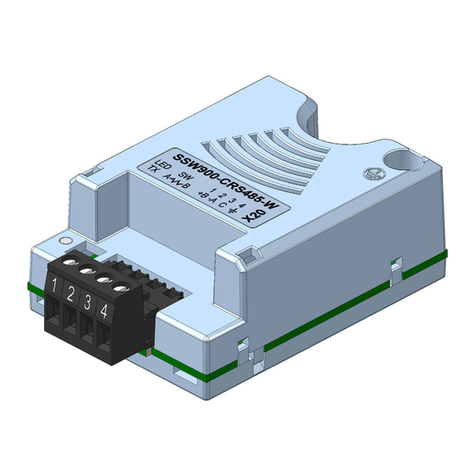
WEG
WEG SSW900-CRS485-W User manual
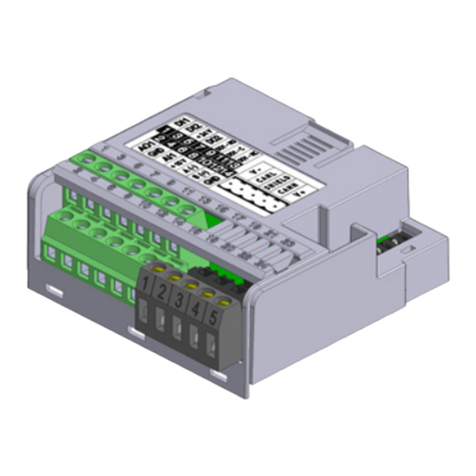
WEG
WEG DeviceNet CFW500 Quick guide

WEG
WEG DeviceNet CFW500 Quick guide