WEIHONG VT320E User manual

PrefacePreface
First of all, thank you for choosing the VT320E follow-up controller developed by Weihong!
This manual introduces the use of VT320E servo controller in detail, including functional characteristic, installation instruction,
operation method, etc.
Before installing and using this product, please read this manual carefully, which will help you quickly become familiar with the
product and use it better.
In order to continue to provide more professional products, we will continue to upgrade product functions. The information
provided is subject to change without prior notice. If you have any questions about product use or have any suggestions about
our products and services, please feel free to contact us.
Contact Us:
Company Name: Shanghai Weihong Electronic Technology Co., Ltd.
Headquarters address: No. 1590, Huhang Highway, Fengxian District, Shanghai
Post code: 201401
Tel: 400-882-9188
Fax: 021-33587519
E-mail: weihong@weihong.com.cn
Official website: http://www.weihong.com.cn
Modify Record:
V ER S I O N D AT E D ES C R IP TI O N
R1 2023.09.27 VT320E 1st version established.

Safety InstructionSafety Instruction
Before using this control system, please read this manual carefully before performing related operations.
Read this manual and user safety instructions carefully, and take necessary safety precautions. If users have other needs, please
contact our company.
Working Environment Requirement
Please store and use this product under the following environmental conditions.
I TE M R EQ U I R E
Environment temperature (during use) 0℃~50℃
Environment temperature (during storage) -40℃~70℃
Environment humidity 0%~90% (no condensation)
Vibration resistant <0.35mm (9 Hz~150 Hz); <0.15mm (2 Hz~9 Hz)
Usage environment No corrosive gas, dust, oil mist
Max heating power <10W
Precautions
If such information is not followed, personal injury, machine damage, or other property damage could result.
Transportation and Storage Related Matters:
Please do not drag or carry the products via cables or devices connected to them.
Pay attention to moisture-proof during storage and transportation.
Installation Related Matters:
The cable interface of the follow-up controller should be sealed.
The product must be installed firmly and without vibration.
During installing, do not cast or knock the product, and do not have any impact or load on the product.
Wiring Related Matters:
The follow-up controller must be reliably grounded, and the grounding resistance should be less than 2Ω.
Please do not use DC 0V or neutral wire instead of ground wire, otherwise it may not work normally.
The wiring must be correct and firm, otherwise malfunctions may occur.
The voltage value and positive/negative (+/-) polarity on any wiring connector must comply with the specifications in the
Interface Description chapter, otherwise faults such as short circuit or permanent damage to the device may occur.
Before plugging or unplugging the connector or toggling the switch, keep your fingers dry to prevent electric shock or
damage to the follow-up controller.
Please do not plug or unplug the connector or disassemble the follow-up controller with power on.
Precautions for Running and Debugging:
Before running, check whether the parameter settings are correct, and wrong settings will cause unexpected movements of
the machine.

The modification of parameters must be within the allowable range of the system (including mechanical and servo drive).
Exceeding the allowable range may cause system instability or damage the machine.
Precautions for Use:
Before power on, make sure the switch is in the off position to avoid unexpected start up.
In order to avoid or reduce the effect of electromagnetic interference to follow-up controller. When making electrical
arrangements, please ensure electromagnetic compatibility. Connecting low-pass filter can avoid or reduce electromagnetic
interference generated by other electronic equipment.
Please do not power on and off frequently. After power failure or blackout, it needs to be powered on again after an interval
of 10s.
Safety Warning and Note Sign
Some contents that need attention when using this product are explained in the following format.
WARNING
This sign is used to warn of potential danger situations. If not avoided, personal injury may result.
CAUTION
The sign is used to provide device or environment safety warning information. If not avoided, device damage, data loss, reduced device
performance, or other unpredictable results may result.
NOTE
This sign is used for content that requires special attention except for safety issues, and provides some supplementary instructions and notes.

Product IntroductionProduct Introduction
VT320E is a slave controller that supports EtherCAT communication and is used as a slave station in the EtherCAT bus
communication system.
VT320E uses a reliable closed-loop control method and greatly improves the sampling rate, so it has good dynamic response
performance and ultra-high positioning accuracy.
Product Appearance and Dimension
VT320E appearance figure:

1. EtherCAT slave interface 2.Indicator light 3.Power interface 4.Input/output interface 5.Servo drive interface 6.Precapacitor
amplifier interface 7.miniUSB
The name and function of the interface are as follows. For details, please see Interface Description.
NAM E FU N CTIO N
EtherCAT slave interface Used for EtherCAT communication, transmission rate 100Mbps.
Indicator light
Used to indicate controller status.
PWR is the power indicator light, and SYS is the system indicator light.
Flashing frequency 0.33Hz means that EtherCAT is in non-OP state;
Flashing frequency 2Hz means EtherCAT is in OP state and can communicate;
Flashing frequency 10Hz means DNA verification failure;
Flashing frequency of 1Hz and 3Hz alternately means that the xml file read failed.
IN and OUT are EtherCAT indicators. Steady light means connected, flashing means there is data
communication.
Power interface For connecting to 24VDC power supply.
Input/output interface Used to connect the input and output of PLC/CNC (including brake port).
Servo drive interface Used to connect analog servo drive.
Precapacitor amplifier
interface For connecting pre-capacitor amplifier SE001.
miniUSB Used to connect and debug the host computer.
Technical Features
The technical features of VT320E are as follows.
I TE M D ES C R IP TI O N
Power input 24VDC±10%, 0.5A (output port closed), with anti-reverse connection protection.
Indicator light 1×Power supply, 1×SYS, 2×EtherCAT.
EtherCAT interface 2×RJ45, 100Mbps
miniUSB Debug serial port
Precapacitor amplifier interface
Analog output ±10V (16bits)
Digital input port
Channel number: 5
Signal type: low level effective
Maximum switching frequency: 1kHz
Threshold voltage: high level 20~24V/low level 0~4V
Minimum drive current: 2mA

Digital output port
Channel number: 4
Maximum switching frequency: 1kHz
Support maximum sink current input:100mA
Maximum leakage current:100μA
Brake port Output voltage: 24VDC@1A(max)
I TE M D ES C R IP TI O N
Working Environment Requirement
Please store and use this product under the following environmental conditions.
I TE M R EQ U I R EM ENT
Working temperature 0℃~55℃
Working humidity 10%~95% (no condensation water)
Storage temperature -40℃~70℃
Storage humidity ≤95% (no condensation water)
Air pressure range 92-106kPa
Protection level IP30
Vibration resistant <0.35mm (9 Hz~150 Hz)
<0.15mm (2 Hz~9 Hz)
Usage environment No corrosive gas, dust, oil mist
Maximum heating power <10W

System Connection and Interface DescriptionSystem Connection and Interface Description
VT320E external device is as follows.
Precapacitor Amplifier Interface
The sensor M16 interface is as follows.
See the following table for the pin number definition of the sensor M16 interface:
PI N NO. D EFI NI T ION
1 +5 V: power supply
2 GND: power ground
3 SIG: capacitive signal
4 PE: shield layer

Servo Drive Interface
The following is a three-row DB15 servo drive interface.
For the pin number definition of the three-row DB15 servo drive interface, please refer to the following table:
PI N NO. D EFI NI T ION PI N NO. D EFI NI T ION
1 A + (encoder A-phase positive) 9 SON (servo enable signal)
2 A - (encoder A-phase negative) 10 RstALM (alarm clear signal)
3 B + (encoder B-phase positive) 11 AGND (analog reference ground)
4 B - (encoder B-phase negative) 12 DA (-10-10 V analog quantity)
5 Z + (encoder Z-phase positive) 13 OS (zero speed clamp signal)
6 VCC_24V (24 V output) 14 NC (not used)
7 Z - (encoder Z-phase negative) 15 COM (digital signal reference ground)
8 ALM (servo alarm signal) PE Shield layer
Among them:
VCC_24V, COM: Provide 24 V DC power supply for the servo drive.
DA, AGND: Output analog signals to provide speed signals for the drive.
OS: Output zero speed clamp, used to suppress the zero drift of the servo.
SON: Output servo drive enable signal.
ALM: Receive the alarm signal of the servo drive.
RstALM: Alarm clear signal of output servo drive.
A+, A-, B+, B-, Z+, Z-: Encoder three-phase input signal.
Input/Output Interface
The input/output interface is as follows.

The pin number definition of the input/output interface is shown in the following table:
PI N NO. D EFI NI T ION PI N NO. D EFI NI T ION
Y0 Output 0 reserved X0 Input 0 upper limit
Y1 Output 1 reserved X1 Input 1 emergency stop
Y2 Output 2 reserved X2 Input 2 lower limit
Y3 Output 3 reserved X3 Input 3 reserved
GND 24V power ground X4 Input 4 reserved
+24V 24V power output BK+ Brake output positive, active output 24V
GND 24V power ground BK- Brake output negative pole, active output 24V reference ground
EtherCAT Slave Station Interface
The EtherCAT slave station interface is as follows.
For the definition of the EtherCAT slave station interface, see the following table:
NA ME D ES CR I PT I O N
IN Connect to the OUT of the EtherCAT master station or upper level slave station

OUT Connect the IN of the next level EtherCAT slave station
NA ME D ES CR I PT I O N
Power Interface
The power terminal is a three-core terminal, which are +24V, 0V, and PE from left to right.
NA ME D ES C R IP TI O N
+24V Connect to 24 V or positive terminal of DC power supply
0V Connect to 0V/COM or negative terminal of DC power supply
PE Connect the ground wire of the machine tool
Note: Please do not connect the PE terminal to the neutral wire of the power supply line.
mimiUSB Interface
The miniUSB interface is debugging interface, connected to the host computer.

Installation PrecautionsInstallation Precautions
The metal structural parts of the machine tool and the shell of SE001 are the negative pole of the capacitor under test. In order to
ensure the stable operation of the SE001 measurement circuit, the ground pin of the power interface of VT320E must be reliably
connected to the metal structural parts of the machine tool (that is, it is well connected with the machine tool). The shell of SE001
must also be well connected with the metal structural parts of the machine tool.
When the follow-up controller is connected to related peripheral devices, the requirements for the connection cable
are as follows:
Digital signal transmission lines need to use twisted pairs.
Analog signal transmission lines require shielded twisted pairs.
The power supply cable can use unshielded three-core wire, and the PE wire needs to be connected to the ground cable of
the machine tool control cabinet.
It is recommended to use a minimum φ0.25mm specification for the IO signal line.
It is recommended to use a minimum φ0.5mm specification for the power supply line.
It is recommended to use a minimum size of φ1.5mm specification for the ground cable.
In order to ensure the stability of the follow-up and comply with the EMS and EMI characteristics specified by CE
standards, the following basic rules must be followed:
Ensure that there is a good electrical connection between the follow-up controller shell and the machine tool control cabinet
(DC resistance is less than 10Ω).
Ensure a low impedance connection between the follow-up controller and the precapacitor amplifier shell (DC resistance
less than 10Ω).
Ensure that the machine tool control cabinet is star grounded.
For safety reasons, add an additional ground cable between the PE terminal of the follow-up controller power supply and
the star ground point of the machine tool control cabinet.
Analog signal line, digital signal line, and power line should be routed separately to avoid interference and abnormal
operation of the controller.
2
2
2

Install Follow-up ControllerInstall Follow-up Controller
The package of the follow-up controller includes: the follow-up controller host, terminal blocks, and guide rail buckles (already
installed on the host).
The follow-up controller is installed in a guide rail type (DIN 35*7.5mm). To facilitate wiring, please leave 100mm space at the top,
bottom, left and right, and keep it ventilated.
The front view and side view of VT320E are as follows (unit: mm):
The VT320E installation rails are as follows:

SE001 front view and rear view (dimension drawing) are as follows (unit: mm):

OverviewOverview
After the VT320E follow-up control system is correctly wired, debugging work is required before using the system.
The basic debugging process includes:
1. According to the drive used, set the corresponding servo parameters. For details, please see Description of Select Different
Drives.
2. Power on and wait for initialization to complete and enter the main page.
3. Set mechanical parameter. For details, please see Set Mechanical Parameter.
4. Test whether each input and output port is valid and whether the mechanical parameter are set correctly. For details, please
see Detection Device.
5. Return to the machine origin and calibrate the follow-up coordinate system. For details, please see Return to Machine
Origin.
6. Servo calibration. For details, please see Execute Servo Calibration.
7. Capacitance calibration. For details, please see Execute Capacitance Calibration.
8. Verify the switch following action and the following function is normal. For details, please see Detect Follow and Lift.
9. After completing the above settings and function verification, you can set other parameters as needed. For details, please
see Parameter Description.

Set Mechanical ParameterSet Mechanical Parameter
Setting the correct mechanical parameters is used to ensure that the machine tool's running direction, speed, etc. are consistent
with the control direction, speed, etc. Avoid damage to the machine tool or unexpected situations caused by inconsistent axis
directions, speeds, etc. as expected when the machine tool is moving.
Operation Step:
1. Set parameters by operating the corresponding SDO. For details, please see Mechanical Parameter Description.
2. After the parameter setting is completed, write save(0x2100_0x01) as 1 to save the parameters.
NOTE
The value of save cannot be actually written as 1. You only need to write 1 once to complete the parameter saving.
You can perform the once parameter saving operation after setting all the parameters.
Mechanical Parameter Description
This section detailed introduces the meaning of mechanical related parameters.
Screw Pitch
Transmission mechanism per travel used. Such the screw rod is the screw pitch (lead). Theoretically, at the same speed, the
larger the lead of the screw used, the faster the axis moves. It is recommended to use a ball screw with a lead of
5mm~10mm.
Speed Upper Limit
The upper limit of the allowable speed of the servo motor is set according to the characteristics of the motor and load, and
generally does not exceed 3000r/min.
Speed Gain
The actual rotational speed corresponding to each volt of voltage. It needs to be consistent with the parameters set in the
drive. Generally, this value is 300~500r/min/V.
Pulse Number per Revolution
The pulse number of servo motor per rotation encoder feedback. It needs to correspond to the Feedback Pulse Number
of Motor per Rotation 1 Turn keep in the drive.
NOTE
Generally, the pulse number per revolution here is 4 times the number of feedback pulses of the drive corresponding to one
revolution of the motor.
The pulse number per revolution and pitch need to satisfy the formula:
Pulse equivalent = pitch*1000/pulse number per revolution , which can be divisible to 1 decimal place to ensure that the speed is
correct.
Example: When the current pitch is 10mm, the pulse number per revolution should be set to 10000, 20000, 50000, 100000 to
ensure normal speed.
Servo Direction
The rotation direction of the servo motor.

Encoder Direction
The direction of encoder pulse feedback.
Brake Release Delay
After the follow-up controller gives the servo enable signal, it delays the time to release the brake.
Servo Type Classification
Different servo, the control logic of zero-speed clamp, the logic of input and output signals and the system control
parameters are different, so the corresponding servo type needs to be set.
Panasonic, Mitsubishi series servo.
Yaskawa, Delta, and Wise series servo.
TECO series servo.
Input Port Software Logic
There are five parameters in total, corresponding to the software logic (NO/NC) of the input ports (X0~X4)
Normally closed (NC): When there is no signal from the hardware, the software determines it to be valid.
Normally open (NO): When the hardware has a signal, the software determines it to be valid.

Detection DeviceDetection Device
After setting the mechanical parameters, you can use the test function to check whether the following functions of the device are
correct:
Servo analog output function
General IO port function
Servo IO port function
Operation Step:
1. Detect general IO port function
You can directly view the input status of the general IO port in the input PDO.
According to the settings of the software port logic in the mechanical parameters, when the input signal is valid, the
corresponding port will become true.
After entering the test mode, set the corresponding output port status open-loop control IO output in the SDO device
test (0x2400).
NOTE
SDO device test (0x2400) only takes effect in test mode
2. Detect servo IO port function
You can check the input status of the servo IO port directly in the input PDO.
When the input signal is valid, the corresponding port will become true.
After entering the test mode, set the corresponding output port status open-loop control IO output in the SDO device
test (0x2400).
NOTE
SDO device test (0x2400) only takes effect in test mode
3. Detect servo analog function
First enter the test mode and perform function testing of the servo analog quantity by setting Test_AVO
(0x2400_0x01)
When Test_AVO(0x2400_0x01) is set to 1, according to the servo direction setting, VT320E will move downward
(positive direction) at a speed of 1/50 of the maximum speed for 1s
When Test_AVO(0x2400_0x01) is set to -1 , according to the servo direction setting, VT320E will move upward
(negative direction) at a speed of 1/50 of the maximum speed for 1s
The normal situation is: the follow-up axis moves downward, and the coordinates of the follow-up axis increase. The
follow-up axis moves upward, and the coordinates of the follow-up axis decrease.
NOTE
SDO device test (0x2400) only takes effect in test mode If the movement direction is inconsistent with the button, please modify
the Servo Direction of the mechanical parameter. If the movement direction is inconsistent with the follow-up axis position
change, please modify the Encoder Direction of the mechanical parameter. If the actual movement distance is inconsistent with
the displayed distance, please modify the mechanical parameter Screw Pitch and Pulse Number per Revolution.

Return to Machine OriginReturn to Machine Origin
The purpose of returning to the machine origin is to calibrate the coordinate axis of the current follow-up axis to ensure stable
operation of the machine tool and accurate coordinates.
The direction of returning to the machine origin defaults to the direction away from the workpiece, and the upper limit switch is
the origin switch.
Prerequisite:
Mechanical parameter have been correctly set. For details, please see Set Mechanical Parameter.
It has been verified and ensured that the movement direction, follow-up axis coordinates, and upper limit switch signals are
correct and valid. For details, please see Detection Device.
CAUTION
In order to prevent possible damage to the machine tool, it is prohibited to return to machine origin without setting the mechanical parameters
or failing the test.
Operation Step
1. Correctly set related parameters
For the description of parameters related to returning to machine origin, please refer to the following table.
PAR AME T ER NAME ME AN
Whether to zero return
when power on
Whether to automatically execute the return to machine origin operation when power on. Please set this
option to Yes after debugging is completed
Return to berth after zero
return After returning to machine origin, whether to move to the set berth position
Zero return speed Movement speed during return to machine origin
Retract distance After touching the upper limit switch, retract the distance and set this position as the machine
coordinate origin
2. Operate Motor Control to execute the action of returning to machine origin.
Note:
Quickly Set the Machine Origin: VT320E can operate SetZero (0x2100_0x04) to quickly set the current position as machine
origin.

Perform Servo CalibrationPerform Servo Calibration
The main function of servo calibration is to detect and compensate the zero drift voltage of the servo motor to ensure that the
follow-up controller can accurately control the movement of the servo motor.
Due to servo calibration, the motor may oscillate back and forth in a small amplitude. Therefore, it is necessary to manually
control the follow-up axis in the middle of the travel to prevent the follow-up axis from exceeding the travel range when
oscillating.
Prerequisite:
Mechanical parameters have been set correctly. For details, please see Set Mechanical Parameter.
The cutting head has been manually moved to the middle of the travel.
Operation Step:
1. Operate Motor Control to perform servo calibration.
2. CurFollowState displays Servo Calibration , which starts servo calibration.
3. After the servo calibration is completed, CurFollowState displays Still .

Perform Capacitance CalibrationPerform Capacitance Calibration
The main function of capacitance calibration is to detect and calibrate the distance between the precapacitance amplifier and the
workpiece to ensure that the follow-up controller can accurately control the servo motor to follow.
During capacitance calibration, the cutting head will first approach the workpiece slowly and then slowly lift up. The result of
capacitance calibration will directly affect the following effect.
Prerequisite:
Make sure that there is no debris near the cutting head and the workpiece during the capacitance calibration process, and that the
workpiece does not move or vibrate.
WARNING
To avoid calibration failure or personal injury, please stay away from the cutting head during the calibration process.
Operation Step:
1. Set parameters related to capacitance calibration
For the functions and uses of calibration parameters, please refer to the following table:
PA R AM E T ER
NAME FU NCT ION U S E
Calibration
object The material that follows the object.
Touch part
capacitance
When the cutting head is in contact with the workpiece, the capacitance value collected by the precapacitance
amplifier. And it is judged that when the capacitance value is less than the value, it is the touch part.
Calibration
length The lifting distance during calibration and record the corresponding data. The default is 18mm.
One-key
calibration One-key calibration function switch.
2. Operate Motor Control to perform capacitance calibration:
NOTE
If you operate Motor Control to perform other operations during the capacitance calibration process, the capacitance calibration process
will be interrupted. The normal capacitance calibration process takes about 10 seconds.
3. After the capacitance calibration is completed, the cutting head will be raised to the berth position, and CurFollowState will
display Still .
4. The capacitance calibration results can be viewed in SDO (0x2200).
For parameter descriptions of calibration results, see the following table:
Table of contents
Other WEIHONG Controllers manuals
Popular Controllers manuals by other brands
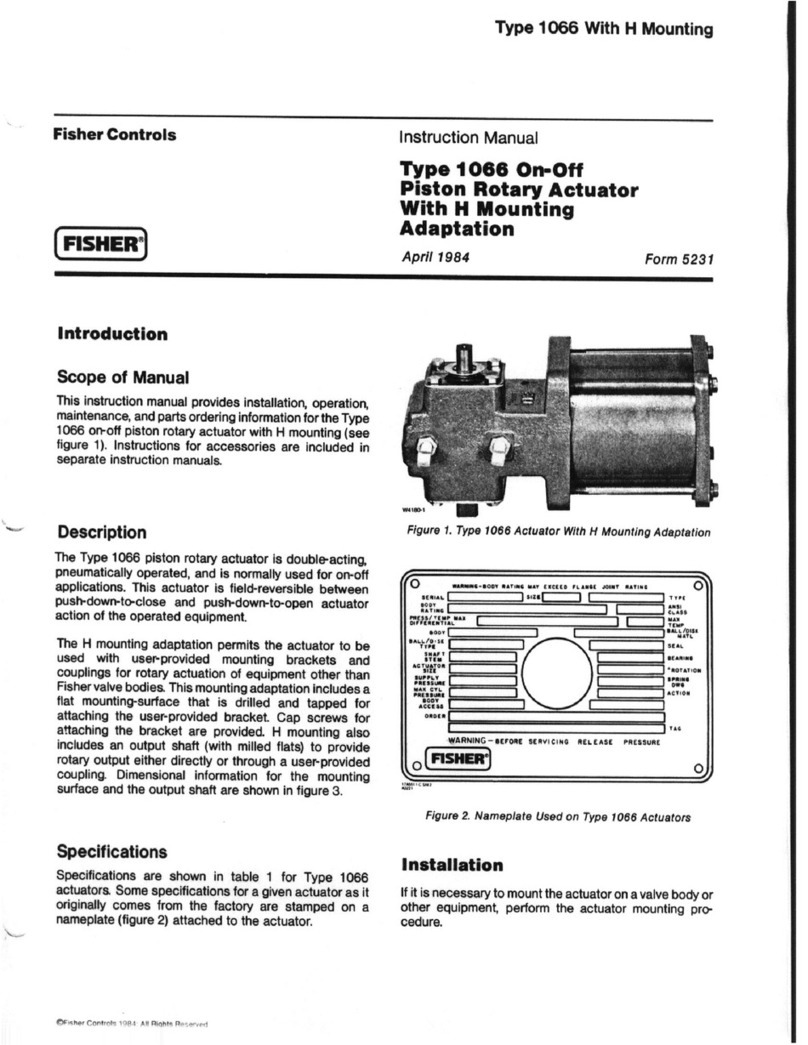
Fisher
Fisher 1066 instruction manual
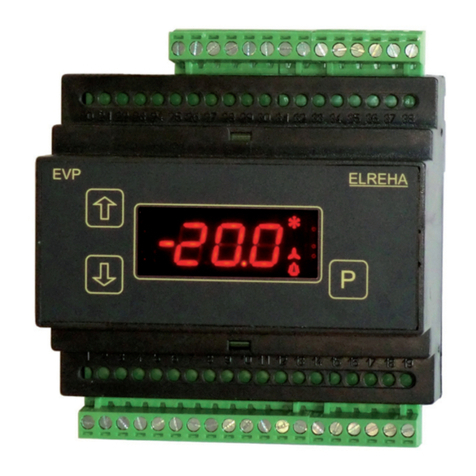
ELREHA
ELREHA EVP 3150-1 Technical manual
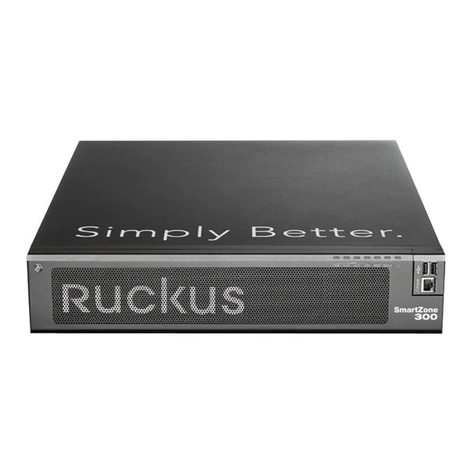
Arris
Arris Ruckus SmartZone 300 Quick setup guide
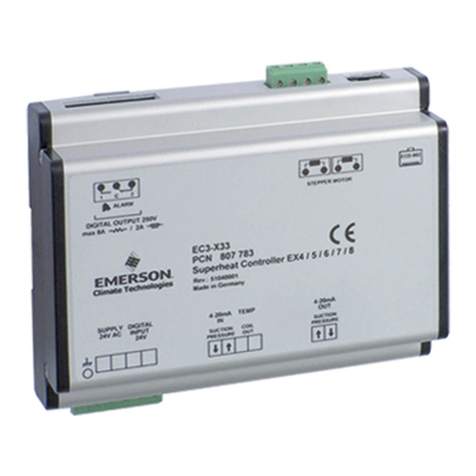
Emerson
Emerson Alco Controls EC3 Series operating instructions
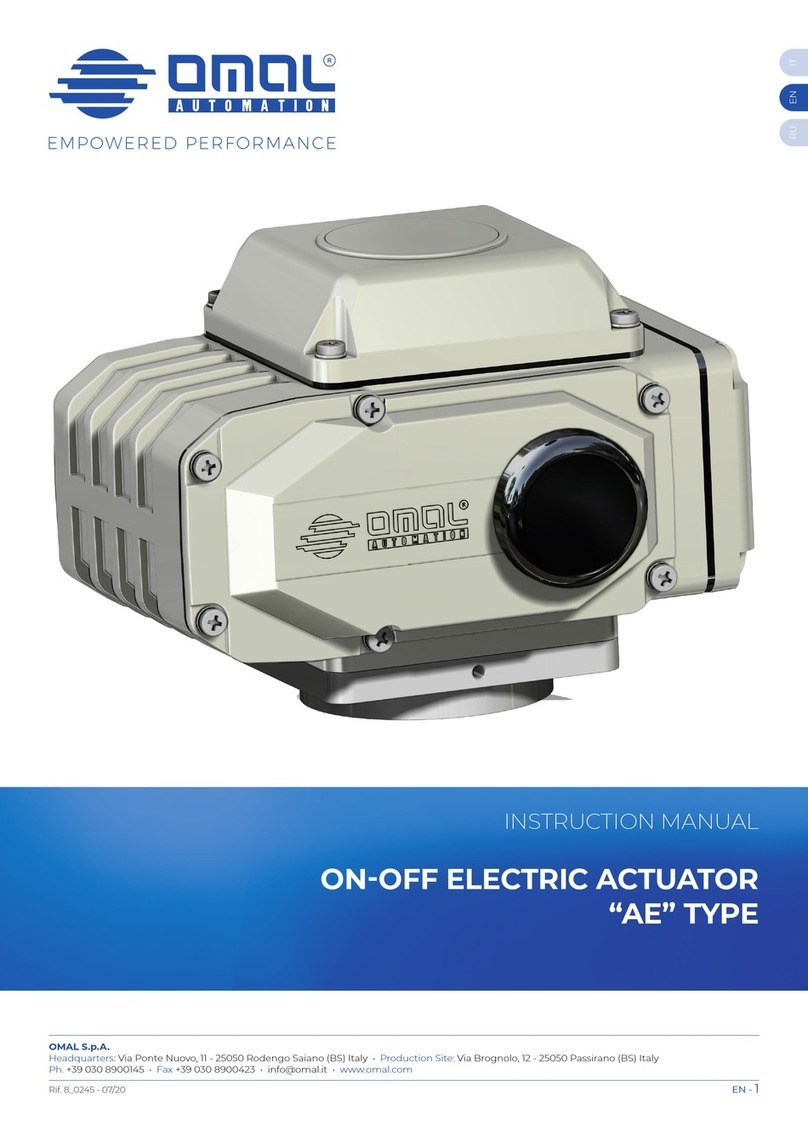
omal automation
omal automation AE 10 instruction manual
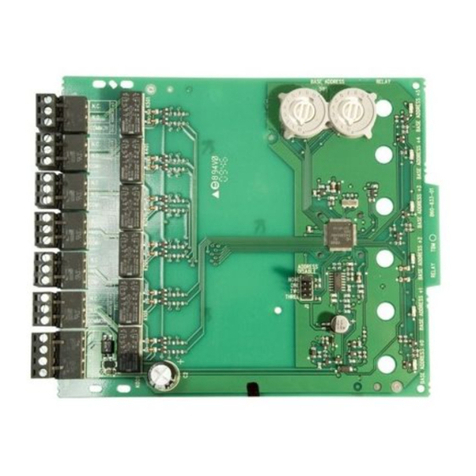
Honeywell
Honeywell NOTIFIER NFXI-RM6 Installation and maintenance instructions