Wilo Vardo WEEDLESS-VM.F User manual

Pioneering for You
·
Wilo-Vardo WEEDLESS-VM.F
6094313 • Ed.01/2023-08
en Installation and operating instructions

Vardo WEEDLESS-VM
https.//qr.wilo.com/932
Vardo WEEDLESS-VM (60 Hz)
https.//qr.wilo.com/3932

en
Installation and operating instructions • Wilo-Vardo WEEDLESS-VM.F • Ed.01/2023-08 3
Table of contents
1 General information...................................................................4
1.1 About these instructions ..................................................... 4
1.2 Copyright ............................................................................... 4
1.3 Subject to change................................................................. 4
1.4 Exclusion from warranty and liability.................................4
2 Safety...........................................................................................4
2.1 Identification of safety instructions................................... 4
2.2 Personnel qualifications....................................................... 6
2.3 Personal protective equipment........................................... 6
2.4 Electrical work .......................................................................7
2.5 Monitoring devices ............................................................... 7
2.6 Drive unit: Gear motor in mixer version ............................. 8
2.7 Fluids hazardous to health................................................... 8
2.8 Transport................................................................................ 8
2.9 Use of lifting equipment......................................................8
2.10 Installing/dismantling........................................................... 9
2.11 During operation ................................................................... 9
2.12 Maintenance tasks..............................................................10
2.13 Operating fluid ....................................................................10
2.14 Operator responsibilities....................................................10
3 Application/use.........................................................................10
3.1 Intended use........................................................................11
3.2 Improper use........................................................................11
4 Product description..................................................................11
4.1 Design...................................................................................11
4.2 Operation in an explosive atmosphere ............................12
4.3 Type key...............................................................................12
4.4 Rating plate..........................................................................13
4.5 Scope of delivery.................................................................13
5 Transportation and storage.....................................................13
5.1 Delivery.................................................................................13
5.2 Transport..............................................................................13
5.3 Storage .................................................................................15
6 Installation and electrical connection....................................15
6.1 Personnel qualifications.....................................................15
6.2 Operator responsibilities....................................................15
6.3 Installation ...........................................................................16
6.4 Electrical connection..........................................................20
6.5 Recommended monitoring devices..................................21
7 Commissioning .........................................................................21
7.1 Personnel qualifications.....................................................21
7.2 Operator responsibilities....................................................21
7.3 Direction of rotation...........................................................21
7.4 Before activating.................................................................22
7.5 Switch on and off................................................................22
7.6 During operation .................................................................22
8 Shut-down/dismantling...........................................................23
8.1 Personnel qualifications.....................................................23
8.2 Operator responsibilities....................................................23
8.3 Decommissioning................................................................23
8.4 Dismantling..........................................................................24
8.5 Clean and disinfect ..............................................................25
9 Maintenance and repair............................................................26
9.1 Personnel qualifications......................................................26
9.2 Operator responsibilities.....................................................26
9.3 Operating fluid......................................................................26
9.4 Maintenance intervals .........................................................26
9.5 Maintenance measures .......................................................27
9.6 Repairs ...................................................................................29
10 Faults, causes and remedies ....................................................33
11 Spare parts.................................................................................34
12 Disposal......................................................................................34
12.1 Oils and lubricants................................................................34
12.2 Protective clothing ..............................................................34
12.3 Information on the collection of used electrical and elec-
tronic products .....................................................................34
13 Appendix....................................................................................34
13.1 Shrink disc tightening torques...........................................35

en
4 Installation and operating instructions • Wilo-Vardo WEEDLESS-VM.F • Ed.01/2023-08
1 General information
1.1 About these instructions These instructions form part of the product. Compliance with the instructions is essential
for correct handling and use:
•Read the instructions carefully before all activities.
•Keep the instructions in an accessible place at all times.
•Observe all product specifications.
•Observe the markings on the product.
The language of the original operating instructions is German. All other languages of these
instructions are translations of the original operating instructions.
1.2 Copyright WILO SE © 2023
The reproduction, distribution and utilisation of this document in addition to communica-
tion of its contents to others without express authorisation is prohibited. Offenders will be
held liable for payment of damages. All rights reserved.
1.3 Subject to change Wilo shall reserve the right to change the listed data without notice and shall not be liable
for technical inaccuracies and/or omissions. The illustrations used may differ from the ori-
ginal and are intended as an exemplary representation of the product.
1.4 Exclusion from warranty and liabil-
ity
Wilo shall specifically not assume any warranty or liability in the following cases:
•Inadequate configuration due to inadequate or incorrect instructions by the operator or
the client
•Non-compliance with these instructions
•Improper use
•Incorrect storage or transport
•Incorrect installation or dismantling
•Insufficient maintenance
•Unauthorised repairs
•Inadequate construction site
•Chemical, electrical or electrochemical influences
•Wear
2 Safety This section contains basic information about the individual
stages in the life cycle of the pump. Failure to observe this in-
formation leads to:
•Danger to persons
•Danger to the environment
•Property damage
•Loss of claims for damages
2.1 Identification of safety
instructions
These installation and operating instructions set out safety in-
structions for preventing personal injury and damage to property.
These safety instructions are shown differently:
•Safety instructions relating to personal injury start with a signal
word, are preceded by a corresponding symbol and are shaded
in grey.
DANGER
Type and source of the danger!
Consequences of the danger and instructions for avoidance.
•Safety instructions relating to property damage start with a
signal word and are displayed without a symbol.

en
Installation and operating instructions • Wilo-Vardo WEEDLESS-VM.F • Ed.01/2023-08 5
CAUTION
Type and source of the danger!
Consequences or information.
Signal words
•DANGER!
Failure to observe the safety instructions will result in serious
injuries or death!
•WARNING!
Failure to follow the instructions can lead to (serious) injuries!
•CAUTION!
Failure to follow the instructions can lead to property damage
and a possible total loss.
•NOTICE!
Useful information on handling the product
Markups
✓Prerequisite
1. Work step/list
⇒Notice/instructions
▶Result
Identifying cross references
The name of the section or table is in inverted commas [“ ”]. The
page number follows in square brackets [].
Symbols
These instructions use the following symbols:
Danger caused by electric voltage
Danger – risk of bacterial infection
Danger – explosive atmosphere
General danger symbol
Danger of hand injuries
Danger due to hot surfaces
Danger due to suspended load
Personal protective equipment: wear a safety helmet

en
6 Installation and operating instructions • Wilo-Vardo WEEDLESS-VM.F • Ed.01/2023-08
Personal protective equipment: wear safety footwear
Personal protective equipment: Wear protective
gloves
Personal protective equipment: wear safety harness
Personal protective equipment: wear face mask
Personal protective equipment: wear safety glasses
General warning signs. Observe the notices!
Useful information
2.2 Personnel qualifications •Personnel have been instructed on locally applicable regula-
tions governing accident prevention.
•Personnel have read and understood the installation and oper-
ating instructions.
•Electrical work: qualified electrician
Person with appropriate technical training, knowledge and ex-
perience who can identify and prevent electrical hazards.
•Installation/dismantling work: trained sewage technology pro-
fessional
Fixation and pipework in wet well and dry well installation, lift-
ing equipment, basic knowledge of wastewater facilities
•Maintenance work: trained sewage technology professional
Application/disposal of operating fluids used, basic engineering
knowledge (installation/dismantling)
•Lifting work: trained specialist for the operation of lifting
devices
Lifting equipment, lifting gear, attachment points
Children and persons with limited abilities
•Persons under the age of 16: Use of this product is prohibited.
•Persons under the age of 18: Supervise them during use of the
product (supervisor)!
•Persons with limited physical, sensory or mental capacities: Use
of this product is prohibited!
2.3 Personal protective
equipment
The protective equipment specified is the minimum requirement.
Observe the requirements of the work regulations.

en
Installation and operating instructions • Wilo-Vardo WEEDLESS-VM.F • Ed.01/2023-08 7
Protective equipment: Transport, installation, removal and
maintenance
•Safety shoes: Protection class S1 (uvex 1 sport S1)
•Protective gloves (EN388): 4X42C (uvex C500 wet)
•Safety helmet (EN397): Conforms to standards, protection
against lateral deformation (uvex pheos)
(If lifting equipment is used)
Protective equipment: Cleaning work
•Protective gloves (ENISO374-1): 4X42C + Type A (uvex pro-
tector chemical NK2725B)
•Safety goggles (EN166): (uvex skyguard NT)
–Labelling frame: W 166 34 F CE
–Labelling disc: 0-0.0* W1 FKN CE
* Protection level according to EN170 not relevant for this
work.
•Breathing protection mask (EN149): Half mask 3M series 6000
with filter 6055 A2
Article recommendations
The branded products in the parentheses constitute non-binding
suggestions. Similar products from other brands can also be used.
Adherence to the standards mentioned is required.
WILO SE does not assume any liability for the adherence of the
aforementioned products to the corresponding standards.
2.4 Electrical work •Electrical work must be carried out by a qualified electrician.
•Disconnect device from the mains and secure it against being
switched on again without authorisation.
•Observe applicable local regulations when connecting to the
mains power supply.
•Comply with the requirements of the local energy supply com-
pany.
•Train personnel on how to make electrical connections.
•Train personnel on the options for switching off the device.
•Follow the motor’s instructions to connect electricity.
•Earth the device.
2.5 Monitoring devices The following monitoring devices must be provided by the cus-
tomer:
Circuit breaker and motor protection switch
•Install circuit breaker and motor protection switch in accord-
ance with the motor manufacturer’s instructions.
•Instable mains supply systems: if necessary, install further pro-
tective devices on-site (e.g. overvoltage, undervoltage or phase
failure relays, etc.).
•Observe local regulations.

en
8 Installation and operating instructions • Wilo-Vardo WEEDLESS-VM.F • Ed.01/2023-08
Residual-current device (RCD)
•Install a residual-current device (RCD) in accordance with the
regulations of the local energy supply company.
•If people can come into contact with the device and conductive
fluids, install a residual-current device (RCD).
2.6 Drive unit: Gear motor in
mixer version
The drive unit is the mixer version of a gear motor. For all inform-
ation, consult the manufacturer’s instructions. Retain these in-
structions and store them with the product.
2.7 Fluids hazardous to
health
Hazardous germs form in sewage or in stagnant water. There is a
danger of bacterial infections!
•Wear protective equipment!
•Clean and disinfect the product thoroughly after removal!
•Inform all persons about the pumped fluid and the danger it
poses!
2.8 Transport •Locally applicable laws and regulations on work safety and ac-
cident prevention must be complied with.
•Demarcate and cordon off the working area.
•Keep unauthorised persons away from the working area.
•Remove loose components from the product.
•Always attach the lifting gear to the attachment points.
•Ensure that the lifting gear is securely attached.
•Observe packaging instructions:
–Impact-resistant
–Water-resistant
–Ensure that the product is properly fixed in place.
–Use transport securing mechanisms.
–Protect it against dust, oil and moisture.
2.9 Use of lifting equipment If lifting equipment (lifting device, crane, chain hoist…) is used,
observe the following points:
•Wear a safety helmet according to EN397!
•Comply with local regulations on the use of lifting equipment.
•The technically correct use of the lifting equipment is the oper-
ator’s responsibility!
•Lifting gear
–Use legally specified and approved lifting gear.
–Select lifting gear based on the attachment point.
–Attach lifting gear to the attachment point according to local
regulations.
•Lifting equipment
–Check it functions properly before use!
–Sufficient bearing capacity.

en
Installation and operating instructions • Wilo-Vardo WEEDLESS-VM.F • Ed.01/2023-08 9
–Ensure stability during use.
•Lifting operation
–Do not jam the product when lifting and lowering it.
–Do not exceed the max. permissible bearing capacity!
–If necessary (e.g. blocked view), assign a second person to
coordinate.
–No one should stand under suspended loads!
–Do not move loads over workplaces where persons are
present!
2.10 Installing/dismantling •Wear a safety harness.
•Locally applicable laws and regulations on work safety and ac-
cident prevention must be complied with.
•Demarcate and cordon off the working area.
•Keep working area free from ice.
•Remove objects lying around from the work area.
•Keep unauthorised persons away from the working area.
•If the weather conditions mean it is no longer possible to work
safely, stop work.
•Work must always be carried out by two persons.
•When working at a height of more than 1m (3ft) above the
ground, use scaffolding with a safety harness.
•Ensure enclosed spaces have sufficient ventilation.
•Toxic or asphyxiating gases may build up in enclosed spaces or
buildings. Observe protective measures in accordance with
work regulations, e.g. carry a gas detector with you.
•If there is a risk of explosion, do not carry out welding work or
work with electrical devices.
•Disconnect device from the mains and secure it against being
switched on again without authorisation.
•All rotating parts must stop.
•Disinfect product.
2.11 During operation •Demarcate and cordon off the working area.
•No persons are allowed in the working area during operation.
•Depending on the process, the product is activated and deac-
tivated using separate controls. The product may automatically
be activated following power cuts.
•If the motor emerges, the motor housing can heat up to above
40°C (104°F).
•Superior must be informed immediately of any faults or irregu-
larities.
•The product must be switched off immediately if faults occur.
•Propeller must not crash into fixtures or walls. Observe defined
clearances in accordance with consulting documents.

en
10 Installation and operating instructions • Wilo-Vardo WEEDLESS-VM.F • Ed.01/2023-08
•Observe required water immersion. If water level varies signific-
antly, use level monitoring.
•Sound-pressure level depends on several factors (installation,
duty point, etc.). Measure the current noise level under operat-
ing conditions. Wear hearing protection at noise levels of
85dB(A) and over. Demarcate the working area!
2.12 Maintenance tasks •Disconnect device from the mains and secure it against being
switched on again without authorisation.
•Only carry out maintenance tasks described in these installation
and operating instructions.
•Only original parts of the manufacturer may be used. The use of
any non-original parts releases the manufacturer from any liab-
ility.
•Collect any leakage of fluid and operating fluid immediately and
dispose of it according to the locally applicable guidelines.
Changing gear oil in the drive unit
The oil change procedure uses compressed air. Observe the fol-
lowing points:
•Allow the gear to cool down before opening the gear oil cham-
ber.
•Only insert compressed air in the gear’s fill hole.
•To avoid inhaling oil mist, limit the compressed air to 0.8bar
(11.5psi).
2.13 Operating fluid The drive unit’s gear is filled with gear oil at the factory. Consult
the manufacturer’s instructions for information on change inter-
vals and disposal of operating fluid.
The interior of the hub is covered with water-resistant grease.
Dispose of operating fluid in accordance with local guidelines.
2.14 Operator responsibilities •Provide installation and operating instructions in a language
which the personnel can understand.
•Make sure that the personnel have received the required train-
ing for the specified work.
•Provide protective equipment. Ensure that the protective
equipment is worn by personnel.
•Ensure that safety and information signs mounted on the
device are always legible.
•Train the personnel on how the system operates.
•Fit dangerous components within the system with an on-site
guard.
•Demarcate and cordon off the working area.
•Measure the noise level. At noise levels of 85dB(A) and over,
wear hearing protection. Demarcate the working area!

en
Installation and operating instructions • Wilo-Vardo WEEDLESS-VM.F • Ed.01/2023-08 11
3 Application/use
3.1 Intended use For suspension and homogenisation in commercial areas of:
•Process sewage
•Sewage containing faeces
•Wastewater (with small amounts of sand and gravel)
•Sludge
Intended use also includes compliance with this manual. Any other use is regarded as non-
compliant with the intended use.
3.2 Improper use
The mixers must not be used in:
•Drinking water
•Non-Newtonian fluids
•Severely contaminated fluids containing hard components such as stone, wood, metals,
etc.
•Highly flammable and explosive fluids in pure form
4 Product description
4.1 Design Low-speed vertical mixer with gear motor for stationary installation.
1
2
3
4
5
Fig.1: Overview
1 Drive unit
2 Motor plate
3 Mixer shaft
4 Hub
5 Propeller blade
4.1.1 Drive unit
1
6
3
2
4
5
Fig.2: Drive unit components
1 Motor
2 Oil drain line
3 Motor plate
4 Bearing lantern
5 Output shaft
6 Gear
Gear motor
IE3/IE4 gear motor for continuous operation with mixer lantern and additional bearing. The
available rated power of the motor is between 0.5kW and 7.5kW.
Mains frequency Efficiency class IE3 Efficiency class IE4
50Hz • •
60Hz • −

en
12 Installation and operating instructions • Wilo-Vardo WEEDLESS-VM.F • Ed.01/2023-08
Motor plate
The motor plate connects the drive unit to the structure. For this purpose, the motor plate is
available in three versions. If required, the motor plate can be designed according to the sys-
tem-specific requirements.
4.1.2 Hydraulics
1
2
35
4
Fig.3: Hydraulics components
1 Shrink disc
2 Mixer shaft
3 Propeller blade
4 Cover cap
5 Hub
Mixer shaft
Mixer shaft made of thick-walled hollow steel. The mixer shaft is connected to the gear mo-
tor by a shrink disc. The hub is mounted on the other end of the mixer shaft via two clamping
sets.
Propeller
2-blade or 3-blade propeller made of solid material. The nominal diameter of the propeller is
1500, 2000 or 2500mm. Each propeller blade is attached to the hub. The setting angle of the
propeller blade is determined in the process. The direction of thrust can be directed towards
the water surface of basin floor. A cover cap is fitted to the hub to protect the hub and pro-
peller fixture from dirt and corrosion.
4.1.3 Materials Drive unit
•Motor housing: EN-AC
•Gear housing: EN-GJL-200 (ASTMA48 Class30)
•Output shaft: Steel (C45)
•Motor plate: Stainless steel A4 (AISI316L/316Ti)
Hydraulics
•Mixer shaft: Stainless steel A4 (AISI 316L/316Ti)
•Rotary shaft seals: FKM
•Hub: PUR/A4 (AISI316L/316Ti)
•Propeller blades: PUR
•Cover cap: PUR
4.2 Operation in an explosive atmo-
sphere Vardo WEEDLESS-VM
IECEx certification −
ATEX approval −
FM approval o
Key: − = not possible, o = optional
For use in explosive atmospheres, the drive unit be marked as follows on the rating plate:
•“Ex” symbol of the corresponding approval
•Ex classification
•Certification number (depending on the approval)
If required by the approval, the certification number is printed on the rating plate.
Consult the explosion protection chapter in the appendix of these installation and oper-
ating instructions for corresponding requirements!
FM approval
The mixers are suitable for operation in potentially explosive atmospheres:
•Protection class: Explosionproof
•Category: Class I, Division 1
Notice: If the cabling is carried out according to Division 1, installation in Class I, Division
2 is also permitted.
4.3 Type key Example: Wilo-Vardo WEEDLESS-VM.F7-1/325.39-400Ex
Vardo Mixer, vertical with standard motor
WEEDLESS Series with gear motor

en
Installation and operating instructions • Wilo-Vardo WEEDLESS-VM.F • Ed.01/2023-08 13
VM.F Version: securely attached
7Size
1Model
3Number of propeller blades
25 x100 = nominal propeller diameter
39 Propeller speed
400 /100 = rated power in kW
Ex Ex-rated
4.4 Rating plate The following section provides an overview of the abbreviations and associated data on the
rating plate:
Vertical mixer
WEEDLESS-F...Typ
S/N xxxxxxxxx JJJJWww
MFY
P20,37 kW n29 1/min
MSØ60 mm MSL2000 mm
PBn 2 PBa 40°
DoT DoR
M 90.00 kg PUØ2500 mm
WILO SE
Wilopark 1
44263 Dortmund Germany
Made in Germany
Fig.4: Rating plate
Type Product name
S/N Serial number
MFY Date of manufacture (according to ISO8601)
- JJJJ = year
- ww = calendar week
P2Required rated power of the mixer
n2Propeller speed
MSØDiameter of mixer shaft
MSLLength of mixer shaft
PBn Number of propeller blades
PBa Setting angle of propeller blades
DoT Direction of thrust
DoR Direction of rotation
MMass of the mixer without drive unit
CAUTION!For the total mass, the mass of the drive unit must also be added.
See rating plate!
PUØNominal diameter of the propeller
NOTICE!For technical data on the drive unit, consult the rating plate!
4.5 Scope of delivery •Vertical mixer with motor plate, mixer shaft and hub
•Propeller blades packed individually, installation on-site
•Operating and maintenance manual
5 Transportation and storage
5.1 Delivery •After receiving the shipment, check it immediately for defects (damage, completeness).
•Defects must be noted on the freight documentation.
•Defects must be notified to the transport company or the manufacturer on the day of
receipt of shipment.
•Subsequently notified defects can no longer be asserted.
5.2 Transport
WARNING
Suspended loads!
Danger of (serious) injuries caused by falling parts.
• Standing under suspended loads is prohibited!
• Do not move loads over workplaces where persons are present!

en
14 Installation and operating instructions • Wilo-Vardo WEEDLESS-VM.F • Ed.01/2023-08
NOTICE
Only use properly functioning hoisting and lifting gear!
Only use properly functioning hoisting gear to lift and lower the mixer.
Screw the lifting eyes needed for attachment to the motor plate. Ensure
that the mixer is not damaged during lifting and lowering. Do not exceed
the maximum permissible bearing capacity of the lifting equipment.
Check that lifting equipment is functioning properly before use!
CAUTION
Material damage due to incorrect transport.
The hub and propeller blades can be damaged when the mixer is lifted.
• When lifting the mixer, place foam padding (min. 20mm/1in thick)
beneath the hub.
•Never set the mixer down on the hub during transport.
•Wear protective equipment! Observe the work regulations.
–Safety shoes: Protection class S1 (uvex 1 sport S1)
–Wear safety helmet (EN397 Conforms to standards, protection against lateral de-
formation (uvex pheos))! Observe the factory regulations!
•Only remove the outer packaging at the site of use to ensure that the mixer is not dam-
aged during transport.
•Only transport the mixer horizontally when on a pallet and using a forklift truck!
•Only transport the mixer vertically using hoisting gear and lifting slings!
•Use tear-proof plastic sacks of sufficient size to package used mixers for transport in a
leak-proof manner.
•Package the drive unit in a water-resistant manner. Moisture ingress will lead to total
failure! For further information, consult the manufacturer’s instructions.
Attachment points
Fig.5: Motor plate attachment points
•Comply with applicable national safety regulations.
•Use lifting eyes permitted for angular loading up to 90° (e.g. “Theipa Point TP”)
–Up to 3kW: M12 lifting eye
–4kW and over: M16 lifting eye
–Consult type key for motor power!
•Always screw two lifting eyes into the motor plate for horizontal transport.
•Use legally specified and approved lifting gear.
•Select the lifting gear based on the prevailing conditions (weather, attachment point,
load, etc.).
•Only attach the lifting gear to the attachment point. Fix in place with a shackle.
•Do not stretch lifting gear over the drive unit. If necessary, use a load bar!
•Use lifting equipment with sufficient bearing capacity.
•The stability of the hoisting gear must be ensured during use.
•When using hoisting gear, ensure a second person is present to coordinate the procedure
if required (e.g. if the operator’s field of vision is blocked).

en
Installation and operating instructions • Wilo-Vardo WEEDLESS-VM.F • Ed.01/2023-08 15
5.3 Storage
DANGER
Danger due to fluids which are hazardous to health!
Danger of bacterial infection!
• Disinfect the mixer after removal.
• Observe the specifications of the work regulations.
CAUTION
Total damage due to moisture ingress
The ingress of moisture into the drive unit will result in total damage! En-
sure the drive unit is sealed watertight during storage. Prevent condens-
ation from forming! The storage location must be overflow-proof. Ob-
serve information in the manufacturer’s instructions!
CAUTION
Material damage to the drive unit
If the product is stored in environments with high humidity (e.g.maritime
or tropical environments), severe rusting can damage the gear. In such
environmental conditions, simply moving the propeller on a regular basis
is no longer sufficient. In such cases, add an oil-soluble concentrate with
anti-rust additives (concentration approx. 2%) to the gear oil. For fur-
ther information, consult the manufacturer’s instructions!
Newly supplied mixers can be stored for 2years. Consult customer service before storing
the mixer for more than 2years.
The following must be observed as regards storage:
•Place the mixer on a solid surface and secure it against slipping and falling over!
•The max. storage temperature is -15°C to +60°C (5°F to 140°F) at a max. relative hu-
midity of 90%, non-condensing. Frost-proof storage at a temperature of 5°C to 25°C
(41°F to 77°F) with relative humidity of 40% to 50% is recommended.
•Do not store the mixer in rooms in which welding work is carried out. The resulting gases
or radiation can corrode the elastomer parts and coatings.
•Protect the mixer from direct sunlight and heat. Extreme heat can cause damage to the
propeller and the coating!
•For information on storing the drive unit, consult and observe the manufacturer’s in-
structions!
After storage, remove any dust and oil from the mixer and check the coatings for damage.
Repair damaged coatings before further use.
6 Installation and electrical con-
nection
6.1 Personnel qualifications •Electrical work: qualified electrician
Person with appropriate technical training, knowledge and experience who can identify
and prevent electrical hazards.
•Installation/dismantling work: trained sewage technology professional
Fixation and pipework in wet well and dry well installation, lifting equipment, basic
knowledge of wastewater facilities
6.2 Operator responsibilities •Observe locally applicable accident prevention and safety regulations.
•Observe all regulations for working with heavy loads and under suspended loads.
•Provide protective equipment. Ensure that the protective equipment is worn by person-
nel.
•Demarcate the working area.
•Keep unauthorised persons away from the working area.
•If the weather conditions (e.g. ice formation, strong wind) mean it is no longer possible
to work safely, stop work.

en
16 Installation and operating instructions • Wilo-Vardo WEEDLESS-VM.F • Ed.01/2023-08
•Observe local sewage technology regulations for the operation of sewage systems.
•Structural components and foundations must be of sufficient stability in order to allow
the device to be fixed in a secure and functional manner. The operator is responsible for
the provision and suitability of the structural component/foundation!
•Check that the available consulting documents (installation plans, installation location,
inflow conditions) are complete and accurate.
6.3 Installation
DANGER
Danger due to fluids hazardous to health during installation!
Danger of bacterial infection!
• Clean and disinfect installation location.
• Wipe up drips immediately.
• Observe the specifications of the factory regulations!
• If contact with fluids that are hazardous to health is possible, wear the
following protective equipment:
– sealed safety glasses
– mouth protection
– safety gloves
DANGER
Risk of fatal injury due to dangerous lone working practices!
Work in chambers and narrow rooms as well as work involving risk of fall-
ing are dangerous work. Such work may not be carried out autonom-
ously!
• Only carry out work with another person!
CAUTION
Material damage due to incorrect fixation
Defective fixation may limit the functionality of the mixer or damage it.
• If the mixer is fixed to a concrete structure, use anchor bolts for fixa-
tion. Follow the manufacturer’s installation instructions! Temperature
specifications and hardening periods must be strictly observed.
• If the mixer is fixed to a steel structure, ensure that the structure is
sufficiently strong. Use fixation materials with sufficient strength!
Use suitable materials to avoid electrochemical corrosion!
• Tighten all screwed connections. Observe torque specifications.
•Wear protective equipment! Observe the work regulations.
–Protective gloves: 4X42C (uvex C500 wet)
–Safety shoes: Protection class S1 (uvex 1 sport S1)
–Wear a safety harness.
–Safety helmet: EN397 Conforms to standards, protection against lateral deformation
(uvex pheos)
(When using lifting equipment)
•Prepare the installation site:
–Clean, free of coarse solids
–Dry
–Frost-free
–Disinfected
•Work must always be carried out by two persons.
•Demarcate the working area.
•Keep unauthorised persons away from the working area.
•From a working height of more than 1m (3ft) above the ground, use scaffolding with a
safety harness.
•Toxic or asphyxiating gases may build up during work:

en
Installation and operating instructions • Wilo-Vardo WEEDLESS-VM.F • Ed.01/2023-08 17
–Observe protective measures in accordance with work regulations (gas measurement,
carry a gas detector with you).
–Ensure adequate ventilation.
–If toxic or asphyxiating gases accumulate, leave the workplace immediately!
•Install lifting equipment: even surface, clean, firm base. Warehouse and installation loca-
tion must be easily accessible.
•Attach chain or wire rope to handle/attachment point with a shackle. Only use lifting
gear that has been technically approved.
•Do not stay within the swivel range of the hoisting gear.
•All connection cables must be laid properly. The connection cables must not pose any
risk (i.e. tripping, damage during operation). Check whether the cable cross-section and
the cable length are sufficient for the selected installation type.
•Observe minimum clearances to walls and any fixtures.
6.3.1 Installing the mixer
CAUTION
Material damage due to excessive bending stresses!
If the mixer shaft is not installed perpendicularly, it may be subjected to
high bending stresses. These bending stresses can damage the mixer
shaft and the gear. To ensure perpendicular installation of the mixer
shaft, install the motor plate precisely using equalisation sheets.
Affix the drive unit, with the mixer shaft and hub mounted, to a suitable support structure.
Once the mixer has been installed, attach the propeller blades.
1
2
3
4
5
Fig.6: Installing the mixer
1 Drive unit
2 Motor plate
3 Mixer shaft
4 Support structure
5 Motor plate fixation
✓Slinging point installed on the motor plate.
✓Work area demarcated and free of any other objects or contaminants.
✓Ensure work is carried out by two persons.
1. Fasten the hoisting gear to the slinging points.
2. Slowly lift the mixer. CAUTION!Material damage! Place a soft surface underneath the
mixer while lifting.
3. Position the mixer over the support structure.
4. Slowly lower the mixer. CAUTION!Material damage! Do not impact the support struc-
ture heavily while lowering!
⇒Make precise positioning adjustments by hand while lowering.
5. Lower the mixer until the motor plate rests completely on the support structure.
⇒Check perpendicular alignment of the mixer shaft. If necessary, adjust the motor
plate with equalisation sheets.
6. Affix the motor plate to the support structure. Tightening torque according to assembly
drawing!
7. Detach hoisting gear.
▶Mixer is installed. Prepare and attach propeller blades.
6.3.2 Attaching the propeller blades

en
18 Installation and operating instructions • Wilo-Vardo WEEDLESS-VM.F • Ed.01/2023-08
6.3.2.1 Adjusting the setting angle
1
2
3
30°
35°
40°
45°
Fig.7: Propeller blade setting angle
1 Hub
2 Mixer shaft
3 Propeller blade
In order to achieve the design-relevant specifications in mixing operation, the blades must
be attached to the hub with the specified angle of attack. For this purpose, one union insert
with an angle of attack of 35/40° is included in the scope of delivery per blade.
The system-specific setting angle is marked on the rating plate.
NOTICE!Other setting angles may only be used following consultation with customer
service.
NOTICE
Different setting angles can cause malfunction
Attach all propeller blades with the same setting angle. Different angles
may lead to malfunctions.
6.3.2.2 Defining the direction of thrust
1 1
A B
2
2
33
Fig.8: Propeller blade direction
A Direction of thrust: upward
B Direction of thrust: downward
1 Mixer shaft
2 Union insert
3 Propeller blade
The mixer can exert thrust either upwards or downwards in the operating space. To do this,
the direction of rotation and propeller blade direction must match. The illustration shows the
blade alignment in relation to the respective thrust direction:
•Clockwise rotation: Upward direction of thrust
•Anti-clockwise rotation: Downward direction of thrust
Observe the following points:
•*The information on direction of rotation exclusively relates to the mixer when viewed
from above!
•The propeller blade direction and direction of rotation must match!
•The system-specific specifications regarding direction of rotation (DoR) and direction of
thrust (DoT) are noted on the rating plate!
NOTICE!For the proper direction of rotation, the motor has to be connected in the clock-
wise or anti-clockwise rotation. The specifications for the electrical connection can be
found in the motor instructions!

en
Installation and operating instructions • Wilo-Vardo WEEDLESS-VM.F • Ed.01/2023-08 19
6.3.2.3 Attaching the propeller blades
2
1
3
4
4
2
3
5
1
6
2 4
7
6
8
9
3
4
Fig.9: Mounting the propeller
1 Flat gasket 6 Threaded pin
2 Hub 7 Washer
3 Union insert 8 Hexagon nut
4 Propeller blade 9 Hexagon counter nut
5 Drilled hole for union insert
✓The drive unit, with pre-assembled mixer shaft and hub, is firmly affixed to the support
structure.
✓Propeller blades and required union inserts are to hand.
✓Setting angle defined.
✓Direction of thrust defined.
✓Torque wrench with width across flats of 55 and 750Nm (553ft·lb) is to hand.
✓Ensure work is carried out by two persons.
1. Insert the union insert sideways into the drilled hole.
NOTICE!Observe the angle specification engraved on the union insert. The angle
specification must be visible when inserted.
NOTICE!Ensure the propeller blade alignment matches the direction of thrust!
2. Place flat gasket on threaded pin.
3. Insert propeller blade with threaded pin into the specified attachment on the hub, and
fix in place. NOTICE!The union insert must engage in the specified notch on the hub.
4. Slide the washer onto the threaded pin.
5. Screw the hexagon nut on the threaded pin until hand-tight.
6. Tighten the hexagon nut with the torque wrench. Tightening torque: 750Nm
(553ft·lb).
7. Screw the hexagon counter nut on the threaded pin until hand-tight.
8. Tighten the hexagon counter nut with the torque wrench. Tightening torque: 750Nm
(553ft·lb).
9. Repeat these work steps for each propeller blade.
10. Check that all propeller blades are firmly fixed in place.
▶Propeller blades are installed. Mount the cover cap.

en
20 Installation and operating instructions • Wilo-Vardo WEEDLESS-VM.F • Ed.01/2023-08
6.3.3 Mounting the cover cap
5
4
6
3
12
Fig.10: Installing the cover cap
1 Hub
2 Groove for O-ring
3 Tie rod
4 Installation aid (steel rod, 2pcs, 9x250mm)
5 Cover cap
6 O-ring
✓Propeller blades attached.
✓Installation aid is to hand.
✓Lubricant is to hand.
1. Cover the interior of the hub with water-resistant grease.
2. Lightly coat the O-ring with lubricant.
3. Place the O-ring in the groove.
4. Screw the short threaded side of the tie rod completely into the drilled hole in the mixer
shaft until hand-tight.
5. Screw the cover cap onto the tie rod until hand-tight. CAUTION!If the O-ring is not
completely in the groove, the O-ring will be squeezed and the cover cap will not be
sealed!
6. Insert the installation aid into the holes on the cover cap and screw tight.
7. Remove steel rods and retain for future dismantling.
8. Check that the cover cap is firmly secured.
▶Cover cap is installed. Make the electrical connection.
6.3.4 Environmental conditions after in-
stallation
Flood the basin after installation. Min. immersion in water: 1m (3ft). This protects the
propeller against environmental influences such as direct sunlight or prolonged periods of
frost. If it is not possible to flood the basin, adhere to the storage requirements. See “Stor-
age [”15]”.
CAUTION!Environmental factors such as direct sun exposure or long periods of frost
can damage or destroy the elastomer components and coatings. If necessary, pack the
propeller in order to provide suitable protection.
6.4 Electrical connection
DANGER
Risk of fatal injury due to electrical current!
Improper conduct when carrying out electrical work can lead to death
due to electric shock!
• Electrical work must be carried out by a qualified electrician!
• Observe local regulations!
NOTICE
Observe motor instructions!
For more information, read and comply with the separate motor instruc-
tions.
•The mains connection must match the specifications on the motor’s rating plate.
•The customer must provide the connection cable and lay it in accordance with local reg-
ulations.
•Earth the mixer in accordance with local regulations. The cross-section of the cable
must comply with local regulations.
6.4.1 Connecting the drive unit For information on connecting the drive unit to the mains, consult the manufacturer’s doc-
umentation!
Table of contents
Other Wilo Engine manuals
Popular Engine manuals by other brands

Ruggerini
Ruggerini RY 50 Use & maintenance
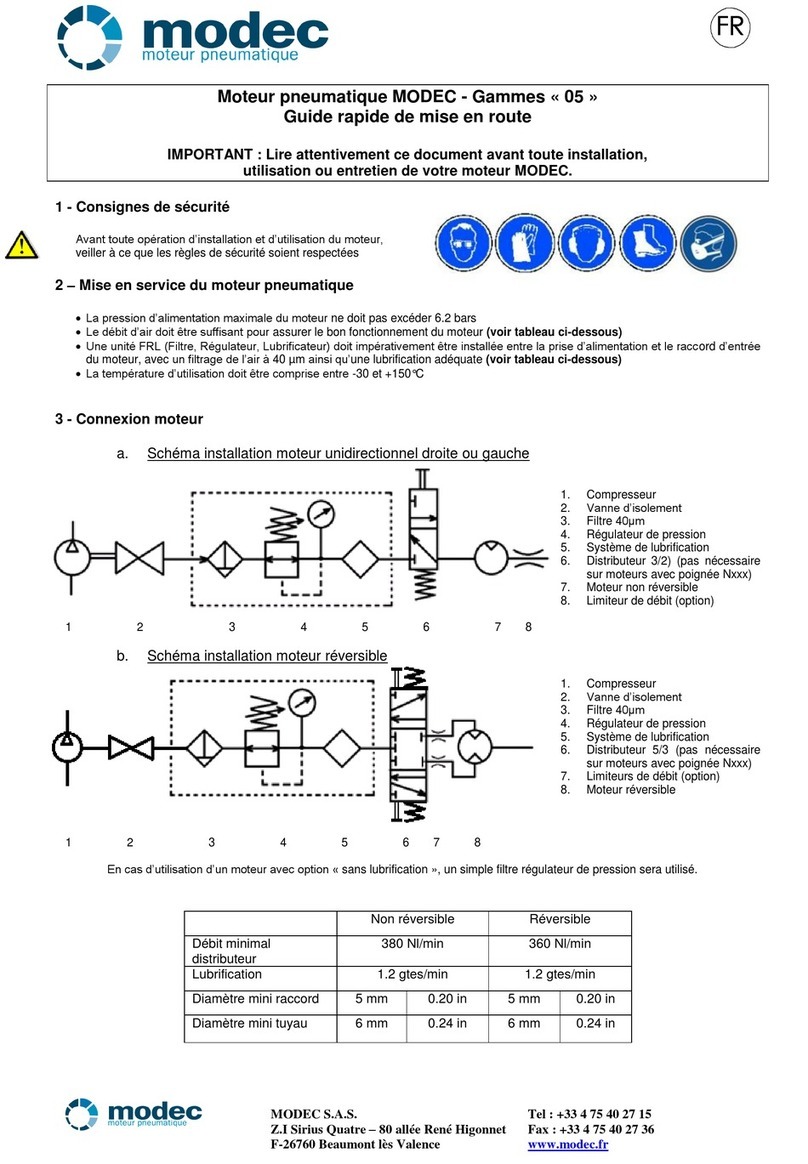
modec
modec 05 Series Quick start instruction manual
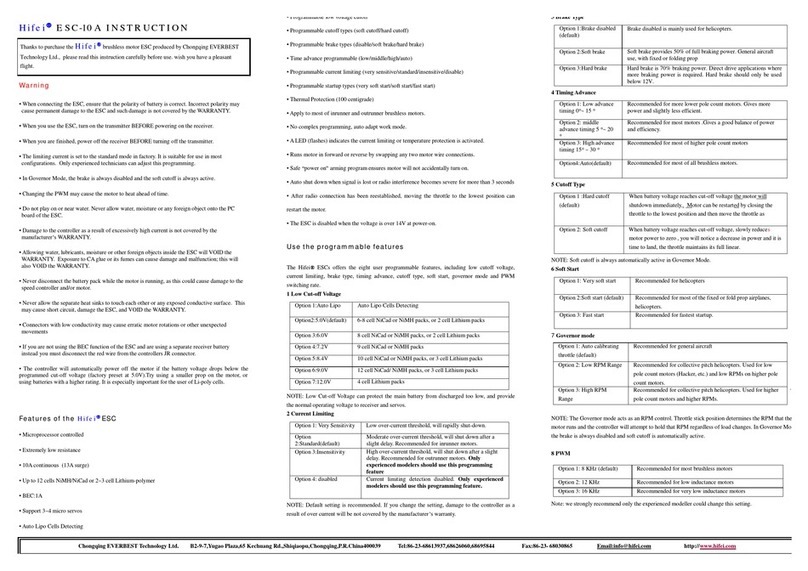
HIFEI Technology
HIFEI Technology ESC-10A Instruction

Perkins
Perkins 1103D XK Systems operation testing and adjusting
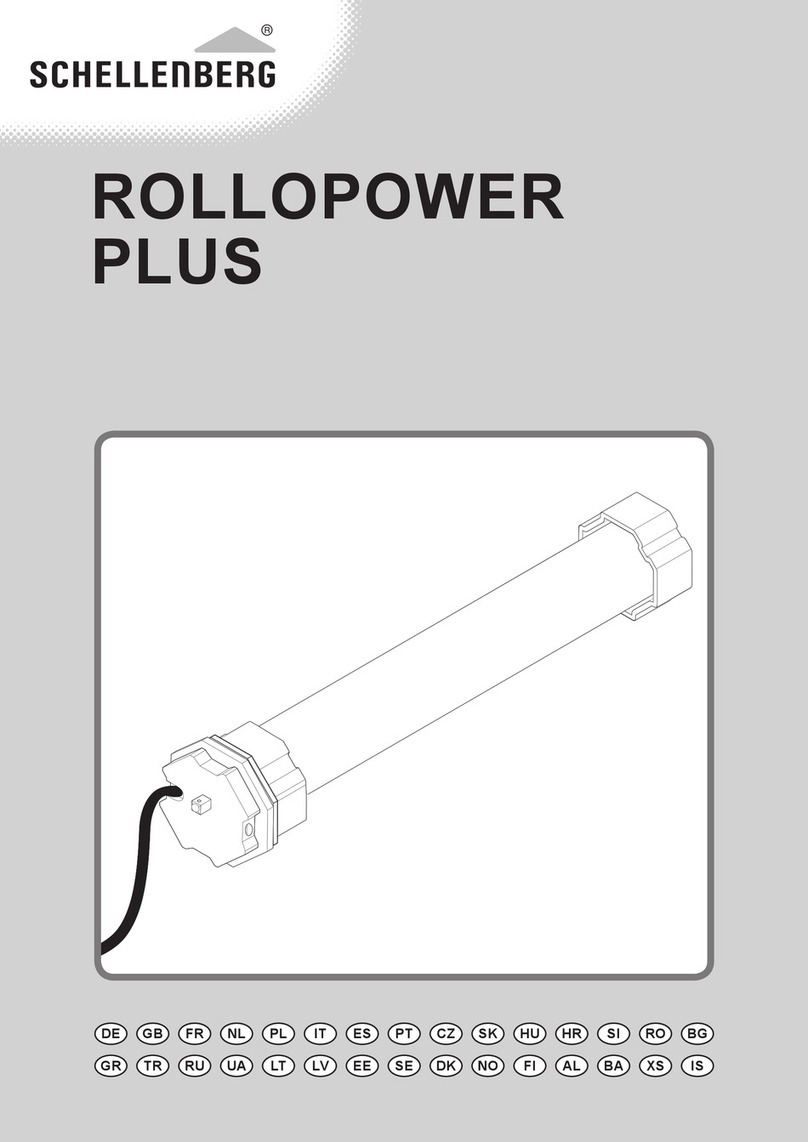
Schellenberg
Schellenberg ROLLOPOWER PLUS Series manual
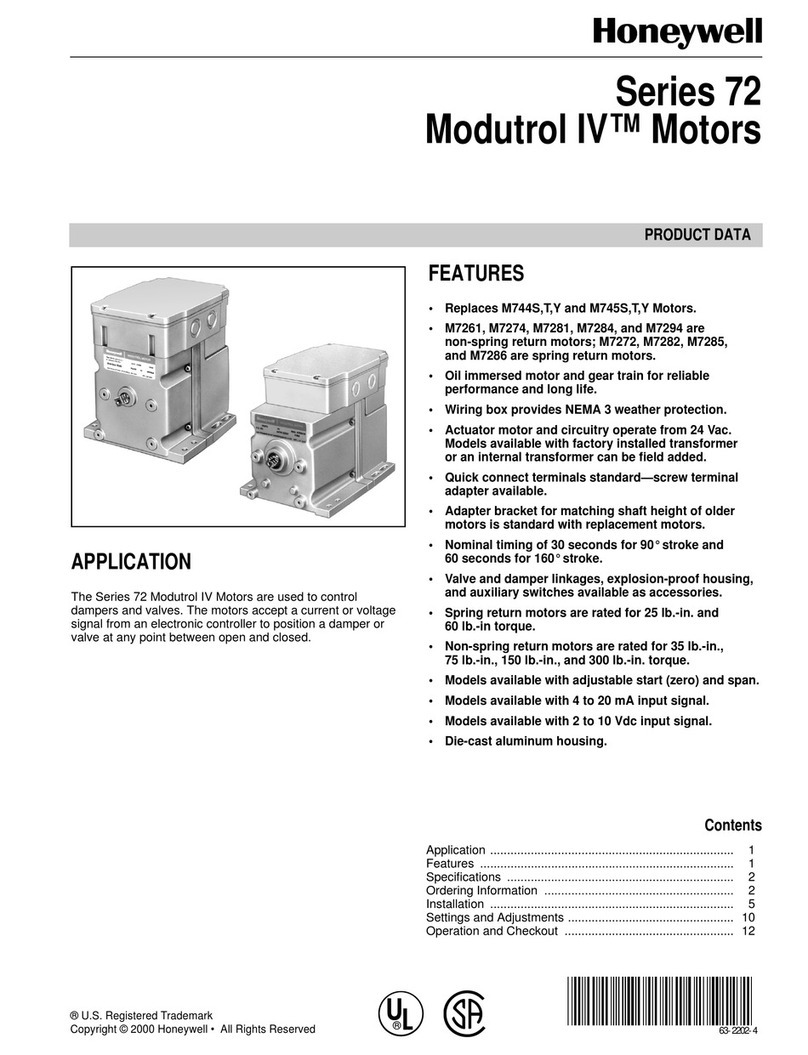
Honeywell
Honeywell Modutrol IV 72 Series Product data
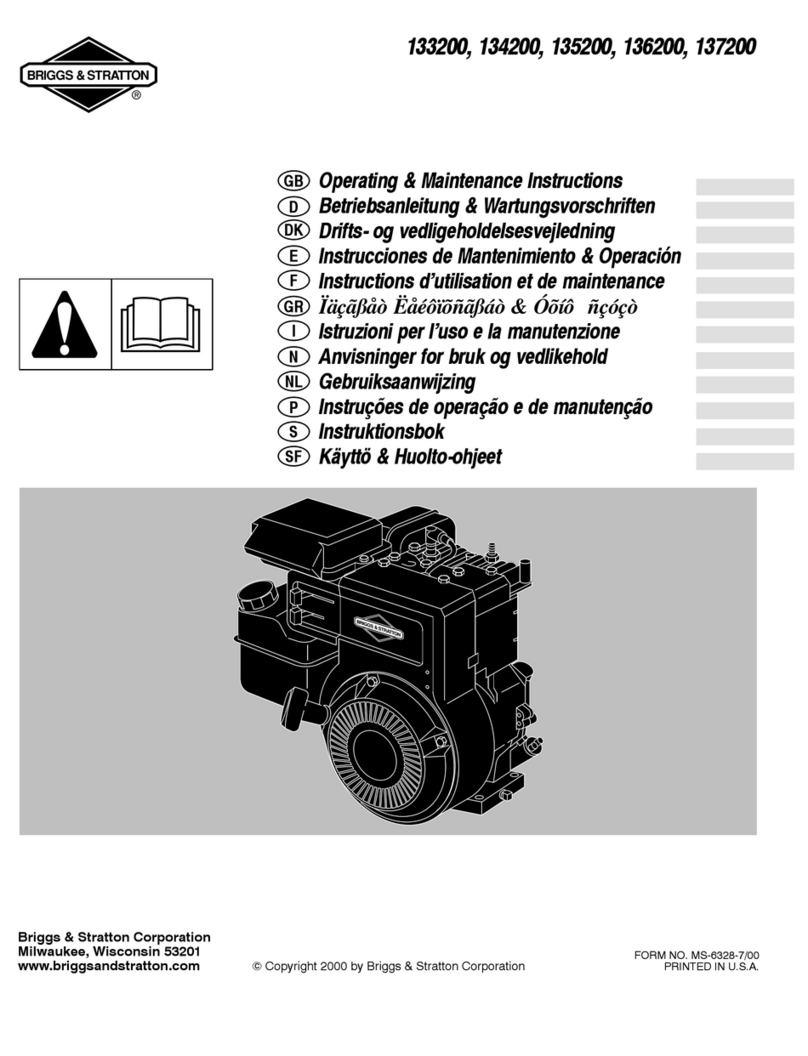
Briggs & Stratton
Briggs & Stratton 133200 Series Operating & maintenance instructions
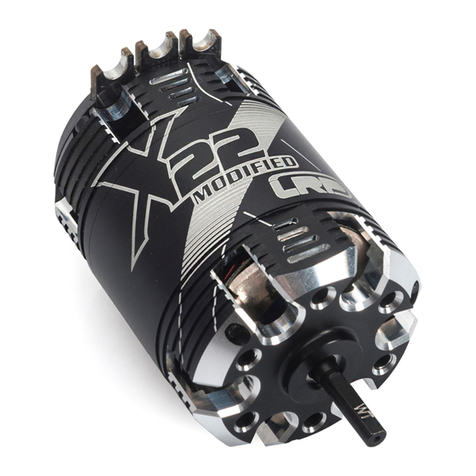
LRP
LRP X22 Modified Series Quick start manual
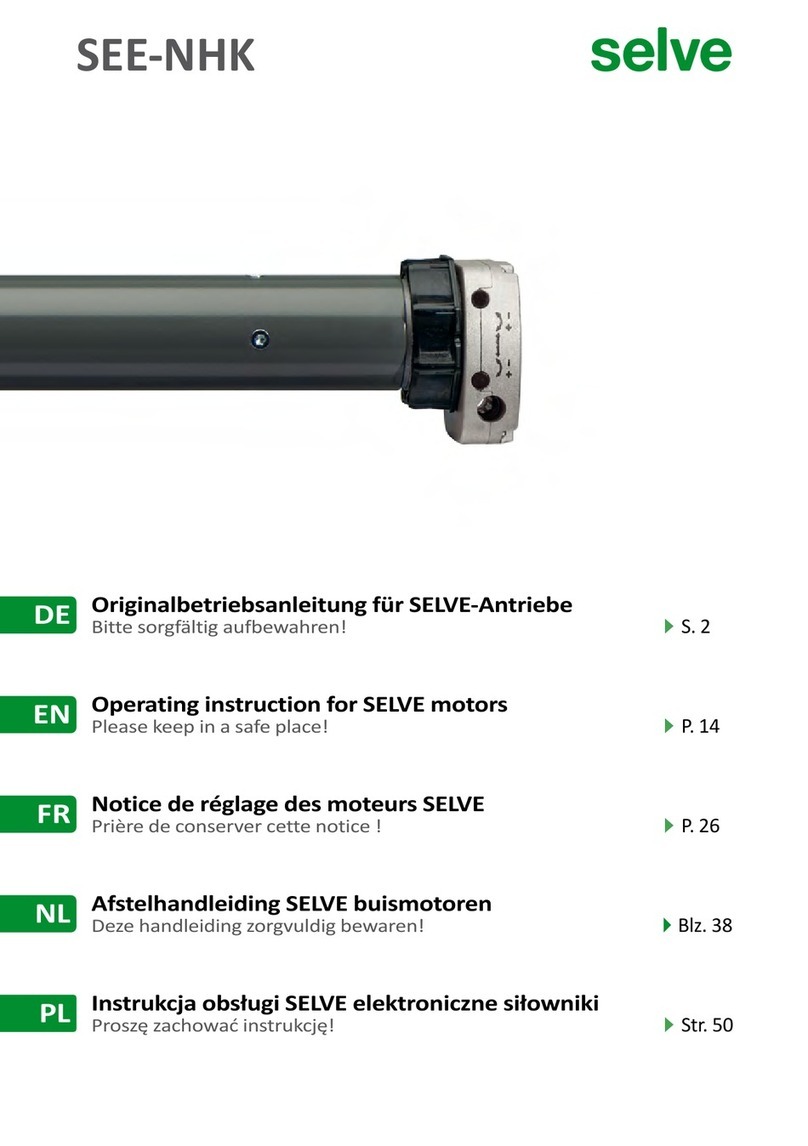
Selve
Selve SEE-NHK Operating instruction

Champ
Champ FX230 owner's manual

Superior
Superior O-360 SERIES Installation & operation manual

Kohler
Kohler K161 operating & maintenance manual