Wilo SiFire User manual

Wilo-SiFire EN
Pioneering for You
4 188 030-Ed.01 / 2013-11-Wilo
de Einbau- und Betriebsanleitung
en Installation and operating instructions
fr Notice de montage et de mise en service
nl Inbouw- en bedieningsvoorschriften

Fig. 1:
Fig. 2a:
A
2"
2"
E
B
C
D

Fig. 2b:
Fig. 3:
21 25 26 13
11
12
19 15
22
27 20 24
23
2
1
14
4
16
7
5
6
10
18
179
9
10
8
3

Fig. 4:
Fig. 5:

Fig. 6a:
3,5 DD
4 D
>2/3 C
min
max 1,8 m/s
Fig. 6b:
min
3,5 D
D
4 D
max 2 m >2/3 C
max 1,8 m/s

Fig. 7:
Fig. 8:
max. 3,2 m
min
A
B
C
D
2
456
3871

Fig. 9a:
Fig. 9b:
A
B
C
D
>800
>800
>800

Fig. 1a:
Fig. 9a: (variant)
Fig. 9b: (variant)
A
B
C
D
>800
>800
>800

Fig. 10:
Fig. 11:
1
2
1
2
1


English
26 WILO SE 10/2013
Captions
Fig.1Transport (example)
Fig.2a Installation diagram
A From water mains
B Tank 500 L
COverflow
DDrain
E Standard scope of delivery
Fig.2b Installation diagram
1Jockeypump
2 Non-return valve
3Testdischarge
4 Pressure switch
5 Pressure gauge
6 Diaphragm pressure vessel
Fig.3The booster
1Gatevalve
2 Connection for local sprinkler
3 Double pressure switch circuit main pump
4 Non return valve
5 Flexible vibration-damping sleeves for diesel
pump
6 Connection for recirculation circuit with dia-
phragm
7Divergentconeondischarge side main pump
8 Pump/motor coupling with spacer
9 Main pump electric/diesel motor
10 Coupling guard
11 Main pump control panel
12 Jockey pump control panel
13 Discharge manifold
14 Connection for setting of flow meter option
15 Fuel tank (for diesel pump)
16 Connection for priming circuit of main pump
17 Main pump
18 Jockey pump
19 Tank for fuel leakages
20 Fuel tank vent valve
21 Fuel level gauge
22 Drain for cleaning of deposit in fuel tank
23 Drain for cleaning of deposit in tank for fuel
leakage
24 Fuel filler cap
25 Connection for motor return pipe
26 Connection for fuel supply to the motor
27 Level gauge for fuel
Fig.4Anchoring to the floor
Fig.5Pump test drainage
Fig.6a Unit with positive head
Fig.6b
C = Tank capacity
Fig.7Unit with suction lift
A From water mains
B Tank 500 L
COverflow
DDrain
Fig.8Fuel tank
1 Fuel level indicator
2 Filling cap
3 Fitting for return pipe from motor
4 Drain for removing deposits in tank
5 On/Off valve for fuel to motor
6 Fitting for fuel supply to motor
7 Tank vent valve (should vent outside room)
8 Electricfloatconnectedtomotor pump control
panel
Fig.9a Exhaust air for combustion and cooling diesel
engine
Fig.9b
A Muffler
B Exhaust thermal protection
C Condensation drain
D Expansion joint
Fig.3The booster

English
Installation and operating instructions Wilo-SiFire System 27
Fig.9a Variant;
Exhaust air for combustion and cooling diesel
engine
Fig.9b
A Muffler
B Exhaust thermal protection
C Condensation drain
D Expansion joint
Fig.10 Automatic test of running
Fig.11a Solenoid valve

English
28 WILO SE 10/2013
1 General information ............................................................................................................................29
2 Safety ....................................................................................................................................................29
2.1 Danger symbols used in this operating instruction .........................................................................................29
2.2 Personnel qualifications ......................................................................................................................................29
2.3 Danger in the event of non-observance of the safety instructions ..............................................................30
2.4 Safety consciousness on the job ........................................................................................................................30
2.5 Safety instructions for the operator .................................................................................................................30
2.6 Safety instructions for installation and maintenance work ...........................................................................30
2.7 Unauthorised modification and manufacture of spare parts ..........................................................................30
2.8 Improper use ........................................................................................................................................................30
3 Transport and storage before use .....................................................................................................30
3.1 Residual risk during transport and storage .......................................................................................................31
4 Intended use .........................................................................................................................................31
5 Product data .........................................................................................................................................31
5.1 Type key .............................................................................................................................................................31
5.2 Technical data ......................................................................................................................................................31
5.3 Scope of delivery .................................................................................................................................................32
5.4 Accessories ...........................................................................................................................................................32
6 Description and function ....................................................................................................................32
6.1 General description .............................................................................................................................................32
6.2 Description of the product .................................................................................................................................33
6.2.1 The booster ...........................................................................................................................................................33
6.2.2 Control box ...........................................................................................................................................................33
6.3 Function of the product ......................................................................................................................................33
7 Installation and electrical connection ...............................................................................................34
7.1 Installation ............................................................................................................................................................34
7.2 Safety recommendations ....................................................................................................................................34
7.3 Control and environment ....................................................................................................................................35
7.4 Electrical connection ...........................................................................................................................................35
7.4.1 General ..................................................................................................................................................................35
7.4.2 Hydraulic connection ...........................................................................................................................................36
7.4.3 Protection of the system ....................................................................................................................................36
7.4.4 Unit with positive head .......................................................................................................................................36
7.4.5 Unit with suction lift ...........................................................................................................................................36
7.4.6 Exhaust air for combustion and cooling diesel engine.................................................................................... 37
8 Commissioning .....................................................................................................................................37
8.1 General preparations and check ........................................................................................................................37
8.2 Group under the charge of water ......................................................................................................................38
8.3 Group over the charge of water (Suction) ........................................................................................................38
8.4 Control operating ................................................................................................................................................38
8.4.1 Commissioning of the main electric pump .......................................................................................................38
8.4.2 Commissioning of the main diesel pump .........................................................................................................38
8.4.3 Commissioning jockey pump ..............................................................................................................................39
8.4.4 Filling of installation ............................................................................................................................................39
8.4.5 Automatic test of running ..................................................................................................................................40
9 Maintenance .........................................................................................................................................41
9.1 General position from maintenance ..................................................................................................................42
9.2 Test of automatic start of pump ........................................................................................................................42
9.3 Test of automatic start of diesel pump .............................................................................................................42
9.4 Periodic tests ........................................................................................................................................................42
9.5 Residual risks during facility management .......................................................................................................43
10 Faults, causes and remedies ...............................................................................................................44
11 Decommissioning and removal ..........................................................................................................47
12 Spare parts ...........................................................................................................................................47

English
Installation and operating instructions Wilo-SiFire System 29
Installation and operating instructions
1 General information
About this document
The language of the original operating instruc-
tions is English. All other languages of these
instructions are translations of the original oper-
ating instructions.
These installation and operating instructions are
an integral part of the product. They must be kept
readily available at the place where the product is
installed. Strict adherence to these instructions is
a precondition for the proper use and correct
operation of the product.
These installation and operating instructions cor-
respond to the relevant version of the product and
the underlying safety standards valid at the time
of going to print.
EC-Declaration of conformity:
A copy of the EC-Declaration of conformity is a
component of these operating instructions.
If a technical modification is made on the designs
named there without our agreement or the decla-
rations made in the installation and operating
instructions on product/personnel safety are not
observed, this declaration loses its validity.
2Safety
These operating instructions contain basic infor-
mation which must be adhered to during installa-
tion, operation and maintenance. For this reason,
these operating instructions must, without fail, be
read by the service technician and the responsible
specialist/operator before installation and com-
missioning.
It is not only the general safety instructions listed
under the main point “safety” that must be
adhered to but also the special safety instructions
with danger symbols included under the following
main points.
2.1 Danger symbols used in this operating
instruction
Symbols:
General danger symbol
Danger due to electrical voltage
Danger due to suspended loads
Danger due to inflammable materials
Risk of electrification
Risk of poisoning
Danger due to hot surfaces
Danger due to hot products
Risk of cuts
Risk of Fall
Risk of irritation
Risk of pollution
Risk of explosion
General ban symbol
No access for unauthorised persons!
Do not touch live parts!
Smoking and
open fire prohibited!
NOTE: ...
Signals:
DANGER!
Acutely dangerous situation.
Non-observance results in death or the most
serious of injuries.
WARNING!
The user can suffer (serious) injuries. “WARN-
ING” implies that (serious) injury to persons is
probable if this information is disregarded.
CAUTION!
There is a risk of damaging the product/unit.
“CAUTION” implies that damage to the product
is likely if this information is disregarded
NOTE:
Useful information on handling the product. It
draws attention to possible problems.
Information that appears directly on the product,
such as
• Direction of rotation arrow,
• Identifiers for connections,
• Name plate,
• Warning sticker
must be strictly complied with and kept in legible
condition.
2.2 Personnel qualifications
The installation, operating, and maintenance per-
sonnel must have the appropriate qualifications
for this work. Area of responsibility, terms of ref-
erence and monitoring of the personnel are to be
ensured by the operator. Ifthe personnel are not in
possession of the necessary knowledge, they are
to be trained and instructed. This can be accom-
plished if necessary by the manufacturer of the
product at the request of the operator.

English
30 WILO SE 10/2013
2.3 Danger in the event of non-observance of the
safety instructions
Non-observance of the safety instructions can
result in risk of injury to persons and damage to
the environment and the product/unit. Non-
observance of the safety instructions results in
the loss of any claims to damages.
In detail, non-observance can, for example, result
in the following risks:
• Danger to persons from electrical, mechanical and
bacteriological influences,
• Damage to the environment due to leakage of
hazardous materials.
• Property damage
• Failure of important product/unit functions
• Failure of required maintenance and repair proce-
dures
2.4 Safety consciousness on the job
The safety instructions included in these installa-
tion and operating instructions, the existing
national regulations for accident prevention
together with any internal working, operating and
safety regulations of the operator are to be com-
plied with.
2.5 Safety instructions for the operator
This appliance is not intended for use by persons
(includingchildren)with reduced physical,sensory
or mental capabilities, or lack of experience and
knowledge, unless they have been given supervi-
sion or instruction concerning use of the appliance
by a person responsible for their safety. Children
should be supervised to ensure that they do not
play with the appliance.
• If hot or cold components on the product/the unit
lead to hazards, local measures must be taken to
guard them against touching.
• Guards protecting against touching moving com-
ponents (such as the coupling) must not be
removed whilst the product is in operation.
• Leakages (e.g. from the shaft seals) of hazardous
fluids (which are explosive, toxic or hot) must be
led away so that no danger to persons or to the
environment arises. National statutory provisions
are to be complied with.
• Highly flammable materials are always to be kept
at a safe distance from the product.
• Danger from electrical current must be eliminated.
Local directives or general directives [e.g. IEC, VDE
etc.] and local power supply companies must be
adhered to.
2.6 Safety instructions for installation and
maintenance work
The operator must ensure that all installation and
maintenance work is carried out by authorised and
qualified personnel, who are sufficiently informed
from their own detailed study of the operating
instructions.
Work on the product/unit must only be carried out
when at a standstill. It is mandatory that the pro-
cedure described in the installation and operating
instructions for shutting down the product/unit
be complied with.
Immediately on conclusion of the work, all safety
and protective devices must be put back in posi-
tion and/or recommissioned.
2.7 Unauthorised modification and manufacture of
spare parts
Unauthorised modification and manufacture of
spare parts will impair the safety of the product/
personnel and will make void the manufacturer's
declarations regarding safety.
Modifications to the product are only permissible
after consultation with the manufacturer. Original
spare parts and accessories authorised by the
manufacturer ensure safety. The use of other
parts will absolve us of liability for consequential
events.
2.8 Improper use
The operating safety of the supplied product is
only guaranteed for conventional use in accord-
ance with Section 4 of the operating instructions.
The limit values must on no account fall under or
exceed those specified in the catalogue/data
sheet.
3Transportandstorage before use
The system fire extinguishing booster is supplied
on a pallet. It is protected from moisture and dust
by a plastic bag.
The equipment must be transported by means of
authorised load devices. (See example on fig. 1)
WARNING! Risk of personal injury!
The static stability of the unit must be taken into
account. Handling of the material must be car-
ried out by qualified personnel, using only suita-
ble and authorised equipment.
Lifting straps must be fastened to the ring bolts
placed on the base frame.
The manifolds do not fit with the handling of the
system and should not be used to fix loads in
transit.
CAUTION! Risk of product damages!
Handling by using discharge manifold can cause
leakages!
When the product is delivered, check it for any
damage in transit. In case of damage, take any
necessary measures from the delivery company
(forwarding agent).
CAUTION! Risk of product damages!
If the product shall be installed later on, store it
in a dry place. Protect it from impacts and any
outside influences (moisture, frost, etc. …). Han-
dle the product with care.

English
Installation and operating instructions Wilo-SiFire System 31
3.1 Residual risk during transport and storage
WARNING! Risk of Cut!
Sharp edges or any not protectedthreadedparts
entail the risk of getting cut.
Take necessary cautions to avoid injuries and
use protective equipment (wear specific
gloves).
WARNING! Risk of personal injury!
Do not stand or put members under the sus-
pended parts during handling and installation.
Use clothing dedicated to protection against
accidents (wear helmet and safety shoes).
WARNING! Risk of impact!
Be careful of prominent parts and parts at head
level. Use clothing dedicated to protection
against accidents.
DANGER! Risk of fall!
Prohibit access to wells or tanks, where pumps
are installed. Wells must have closing cover.
WARNING! Risk of irritation!
During handling, avoid spillage of battery acid
solution which could cause irritations or mate-
rial damages. Use special protections to avoid
contact.
CAUTION! Risk of environmental pollution!
Avoid dumping of oil from the engine or diesel
fuel from the tank. During handling, keep them
flat. Use suitable protection and implement the
necessary measures to prevent pollution of soil,
water, etc.
4 Intended use
The fire extinguishing boosters are designed for a
professional use. They are used when an increase
or a maintaining under pressure of the fire net-
work is necessary.
The system must be installed in a special room
which is protected from frost and rain, fireproof
and ventilated enough, with necessary spaces
around pumps for movements and regular main-
tenance .The roommust be in accordance with the
EN 12845 standards. Airflow for ventilation and
for cooling of engines, more specifically diesel
engine -if present- has to be sufficient.
5 Product data
5.1 Type key
Example SiFire EN 40-200180 7,5/10.5/0.55 EDJ
SiFire Name of the Fire Extinguishing System
EN In accordance with EN 12845 standards
40/200 Type of main pump
180 Impeller diameter of main pump
7,5/10.5/
0.55
Nominal power of the pump motors [kW]
(electrical motor/diesel engine/jockey motor)
EDJ Configuration:
E : 1 electric pump
D : 1 diesel pump
EJ : 1 electric pump + 1 jockey pump
EEJ : 2 electric pumps + 1 jockey pump
EDJ : 1 electric pump + 1 diesel pump + 1 jockey
pump
DJ : 1 diesel pump + 1 jockey pump
5.2 Technical data
Maximum operating pressure: 10 bar/16 bar according to the pump
Maximum ambient temperature: +4 to +40 °C (10 to 40°C if diesel pump is installed)
Maximum water temperature: +4 to +40 °C
Supply voltage: 3~400 V ± 10 %
(1~230 V ± 10 %, for diesel pump control panel)
Frequency: 50 Hz
Maximum relative humidity: 50 % with Tmax.: 40 °C (*)
Protection class of Control box: IP54
Protection class of pump: IP54
Motor IE2 insulation class: F
Maximum altitude for installation: 1000 m above sea level (*)
Minimum atmospheric pressure: 760 mmHg (*)
Nominal current: refer to the rating plate
(*) Seen the specific graphs and tables in the catalogues and maintenance manuals for the details of class variations for electric machines and diesel engines with
regard to different temperatures, altitudes, atmospheric pressure, fuel temperature and viscosity compared to standard test conditions.

English
32 WILO SE 10/2013
5.3 Scope of delivery
• Fire Extinguishing Booster
• Operating instructions for fire extinguishing sys-
tem.
• Operating instructions for pumps (1 manual per
kind of pump)
• Operating instructions for panels (1 manual per
kind of panel)
• Operating instructions and maintenance of diesel
motor if present.
5.4 Accessories
• Priming tank(s) complete with electrical float.
• Electric contacts limit for the check valve of the
pumps.
• Flexible vibration-damping sleeves.
• Eccentric suction cone kit with vacuum gauge for
suction side of the pumps.
• Butterfly valves.
• Silencer for diesel engine.
• Water/water heat exchanger for diesel engine
cooling.
•Flowmeter.
• Diesel engine spare parts kit.
• Remote alarm panel.
The installer is responsible for the assembly of the
equipment supplied and for completion of the
system in compliance with the requirements of EN
12845 standards, as well as for integration of our
supply with all other necessary components (cir-
culation piping, flow rate metering circuits with
meter, priming tank, etc).
See the specific instructions provided in the rele-
vant instruction manuals and/or the indications
provided on the items themselves for details of
how to assemble, set and adjust the accessories
listed above or other particular accessories
requested at the order stage and supplied with the
standard pumping unit.
The installer is responsible for issuing the final
certification “installation built-in compliance with
EN 12845 standard”, as required by the relevant
standards, and for issuing the end user with all the
documents required by the applicable standard.
6 Description and function
6.1 General description
The fire extinguishing units in the SiFire series are
built in several variants and models, as indicated in
our catalogues, or in versions modified in order to
satisfy particular customer requirements (trans-
port/handling difficulties, particular perform-
ances, etc), using the main components described
below:
• main normalised “back pull out” pumps, coupled
to an electrical motor or diesel engine by a spacer
allowing the dismantling of the pump and/or
motor without having to work on the other. It also
allows the extraction of the rotating part of the
pump for maintenance without having to remove
the motor and/or the end suction pump housing.
• vertical multistage jockey pump for correcting
small losses and for keeping the system pressure
constant.
• electrical control panels for the main and jockey
pumps (one per pump).
• piping and discharge manifolds in steel.
• valves on the pump discharge that can be locked
in the open position.
• non-return valves on the pump discharge.
• butterfly valves, manometers, pressure switches.
•Connectionforflowmeter to control the perform-
ance of the pumps.
• double pressure switch circuit for start-up of the
main pumps and control of the working order of
each individual pressure switch.
• pressure switch for automatic start-up of the
jockey pump.
• support frame(s) for control panels and manifolds.
• independent fuel tank for the diesel engine, com-
pleted with accessories.
• Two batteries for the start-up of the diesel engine
(if present).
The system is assembled on a base frame in
accordance with the EN 12845 standard, within
the limit of delivery, indicated on installation dia-
gram from fig. 2a-2b.
Each pump is installed on a steel base frame. Die-
sel pumps are connected to hydraulic elements
with intermediary vibration damping joints to
avoid the transmission of vibrations from diesel
motors but also the possible piping or mechanical
structure breaks.
For connection to the public water distribution,
rules and existing standards must be respected,
and possibly completed with rules of water distri-
bution companies. Besides, local particularities
have to be taken into account, for example a too
high or too variable suction pressure which
requests the assembly of a pressure reducing
valve.

English
Installation and operating instructions Wilo-SiFire System 33
6.2 Description of the product
6.2.1 The booster - See fig. 3 – Position:
1Gatevalve
2 Connection for local sprinkler
3 Double pressure switch circuit main pump
4Non-returnvalve
5 Flexible vibration-damping sleeves for diesel
pump
6 Connection for recirculation circuit with dia-
phragm
7 Divergent cone on discharge side main pump
8 Pump/motor coupling with spacer
9 Main pump electric/diesel motor
10 Coupling guard
11 Main pump control panel
12 Jockey pump control panel
13 Discharge manifold
14 Connection for setting of flow meter option
15 Fuel tank (for diesel pump)
16 Connection for priming circuit of main pump
17 Main pump
18 Jockey pump
19 Tank for fuel leakages
20 Fuel tank vent valve
21 Fuel level gauge
22 Drain for cleaning of deposit in fuel tank
23 Drain for cleaning of deposit in tank for fuel
leakage
24 Fuel filler cap
25 Connection for motor return pipe
26 Connection for fuel supply to the motor
27 Level gauge for fuel
6.2.2 Control box
• Ensure complete automatic operations of each
pump and associated functions
• Waterproof, protection class IP 54.
6.3 Function of the product
The operational logic for the fire extinguishing
unit is based on the cascade calibration of the
pressure switches for pump starting. The jockey
pump of pressure boosting is the first to start and
maintains the system full of water and under pres-
sure. It starts when the pressure drops in the sys-
tem. Start and stop control is set up via the
suitably calibrated pressure switch.
When a larger quantity of water is requested, due
to the opening of one or more circuits or due to a
broken sprinkler, pressure decreases in the sys-
tem. This drives the main pump to start.
For systems with more than one pump, if the main
electric pump does not start, due to electricity
problems for example, the drop in pressure will
activate the standby pump pressure switch which
starts the diesel engine. In some cases, two or
more electric pumps could be used.
Once the sprinkler circuit or the gate valve that
supply the sprinkler system is closed, the system
reaches the maintaining pressure of the installa-
tion; it will be necessary to press the –Stop– but-
tons on panels to stop the main pump and standby
pump. The jockey pump is automatically stopped.
discharge of main pump Accessories Manifolds
DN32 DN50 DN65
DN40 DN65 DN65
DN50 DN65 DN80
DN65 DN80 DN100
DN80 DN100 DN125
DN100 DN125 DN150
DN125 DN150 DN200

English
34 WILO SE 10/2013
7 Installation and electrical connection
DANGER! Risk of electric shock!
Personnel dedicated to the connection of elec-
trical equipment and motors must be skilled for
such work. They shall make the connection
according to the wiring diagrams supplied, in
accordance with regulations and laws in force. In
addition, they must ensure that they have shut-
down power before performing any operation
which provides the possible contact with the
electrical parts . Check earth continuity.
7.1 Installation
Install the booster in an easily accessible room,
ventilated and protected from rain and frost.
To make sure that the booster can pass through
the room door.
For maintenance works, a sufficient place must be
provided. The unit must be easily accessible.
Installation place has to be horizontal and flat. It
must be robust enough to support the system
weight.
The room must be exclusively dedicated to fire
equipment, directly accessible from the outside,
and having a fire resistance of at least 60 minutes
(see standards).
The room must be, in order of preference:
• separate from the protected building (isolated)
• closed to the protected building
• Inside the protected building.
NOTE:
For rooms with closed walls or inside the building,
it is preferable to have a fire resistance superior to
120 minutes. The temperature inside the room
must not be less than 10 °C (4 °C in the presence
of electric pumps) or more than 25 °C (40 °C in the
presence of electric pumps).
The room shall be equipped with openings to the
outside to ensure adequate ventilation for cooling
engines (electric and diesel) and for diesel engine
combustion.
The room also shall be equipped with a sprinkler-
type protection (EN 12845).
Sprinkler protection can be directly supplied by
the discharge manifold of the booster, as required
by the EN 12845 standard.
Access to the room must be guaranteed and easy
for people, even if the installation of fire is on,
without light, if there is snow or rain, and in any
case that can affect access negatively. Access to
the room must be sufficiently reported and admit-
ted only to authorised, specialised and properly
trained personnel.
Avoid access to the system for unauthorised
persons!
The booster is a fire equipment using AUTO-
MATIC START and MANUAL STOP ONLY. For this
reason, there must have a clearly visible sign in
the system room warning that this logic opera-
tion makes the possibility of an unexpected auto
start.
The pump unit is NOT equipped with emergency
stop. The main pumps can only be manually
stopped (see corresponding manual of control
box).
For this reason, before an intervention on group
of pumps, make sure you switch off power sup-
ply and avoid any start of pumps.
If possible, pumps must be installed under the
charge of water. They are considered as such if
at least two thirds of the actual capacity of the
suction tank is above the level of the axis of the
pump and the minimum useful level of the water
in the tank is not more than two meters below
the axis of the pump.
If the conditions mentioned above are not
respected, the booster is considered on suction
conditions, which are accepted after installation
of special devices, explicitly described by the
standard (priming tanks, separated pipes suc-
tion, etc).
7.2 Safety recommendations
WARNING! Risk of Cut!
Do not remove the protection on any rotating
parts, belts, hot surfaces etc. Never leave tools
or disassembled parts of the booster on it or
around it.
DANGER! Risk of fatal injury!
Do not remove the protection of live parts. Pre-
vent each possibility for operate any element
that isolates the installation or subassemblies
on which to work.
Take all precautions to avoid a risk of electrocu-
tion. Control earth connection, presence and
continuity, and if a device for protection against
indirect contact is installed (differential switch).
If necessary, make operation on the unit by
using required equipment (insulating gloves,
isolating base plate).
Never leave the electrical panel or the terminal
box of electrical motor powers opened. Check if
there is no possibility of contact with live parts.
Check if electrical connections and auxiliary
power are correctly connected. Check the label
data of electrical panels, in particular tension
and availability of an adapted power supply.
WARNING! Risk of fire or flash fire!
The charging diesel pump batteriesmayproduce
potentially explosive gas; avoid flames and
sparkles.
Never leave flammable liquids or rags dipped in
acid around the booster or electrical equip-
ments.
Table of contents
Other Wilo Other manuals
Popular Other manuals by other brands
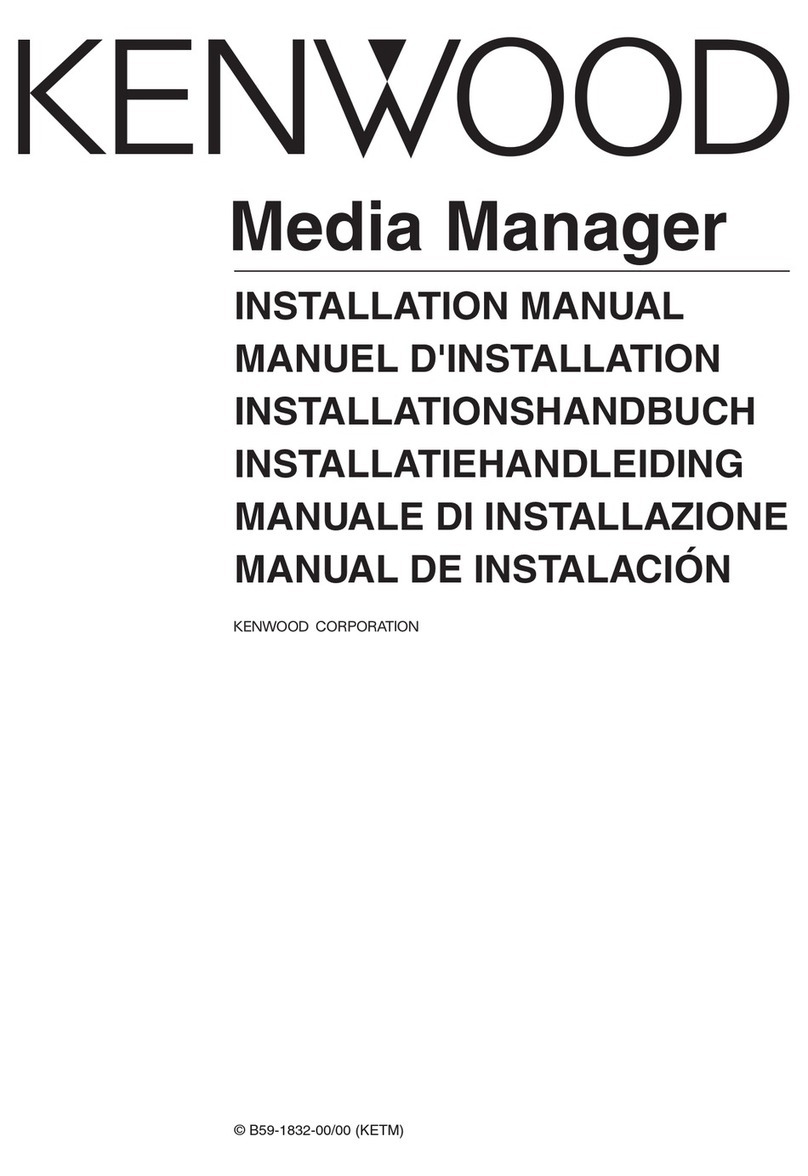
Kenwood
Kenwood Media Manager installation manual
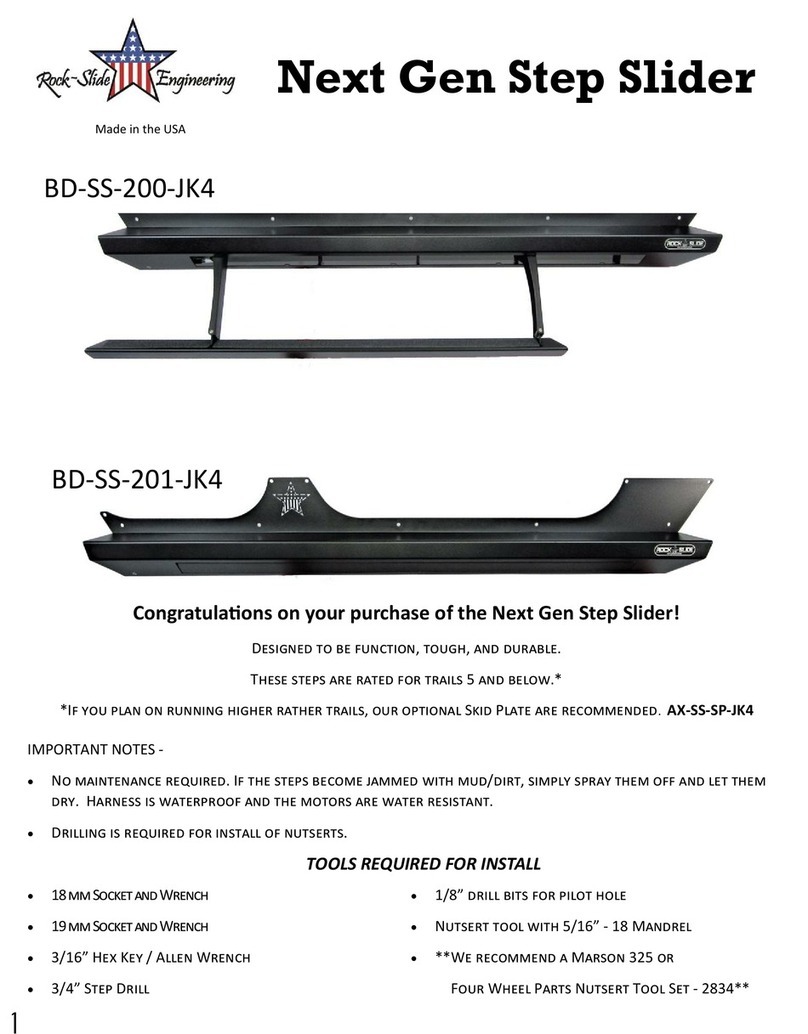
Rock-Slide Engineering
Rock-Slide Engineering BD-SS-200-JK4 Installation instructions manual
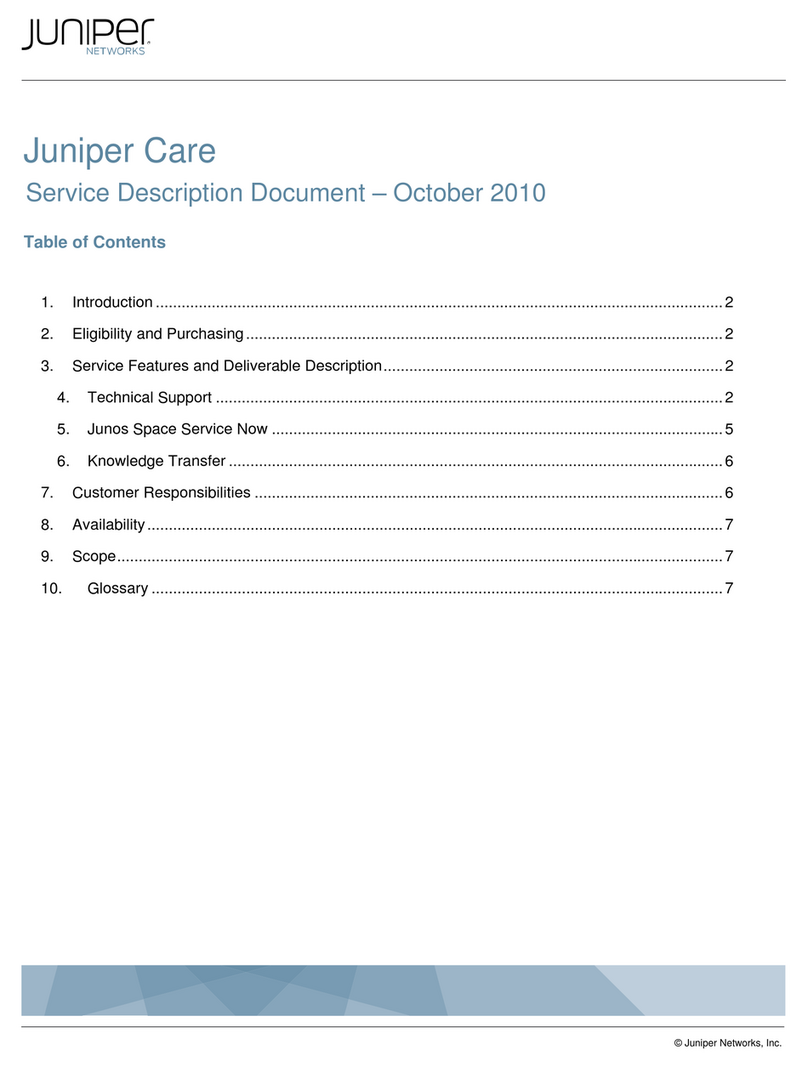
Juniper
Juniper IMPLEMENTATION SUPPORT - SERVICE DESCRIPTION DOCUMENT... manual

Striem
Striem SI-UPC-1016 Installation, operation and maintenance guide

JBA
JBA 1962S Installation instructions manual
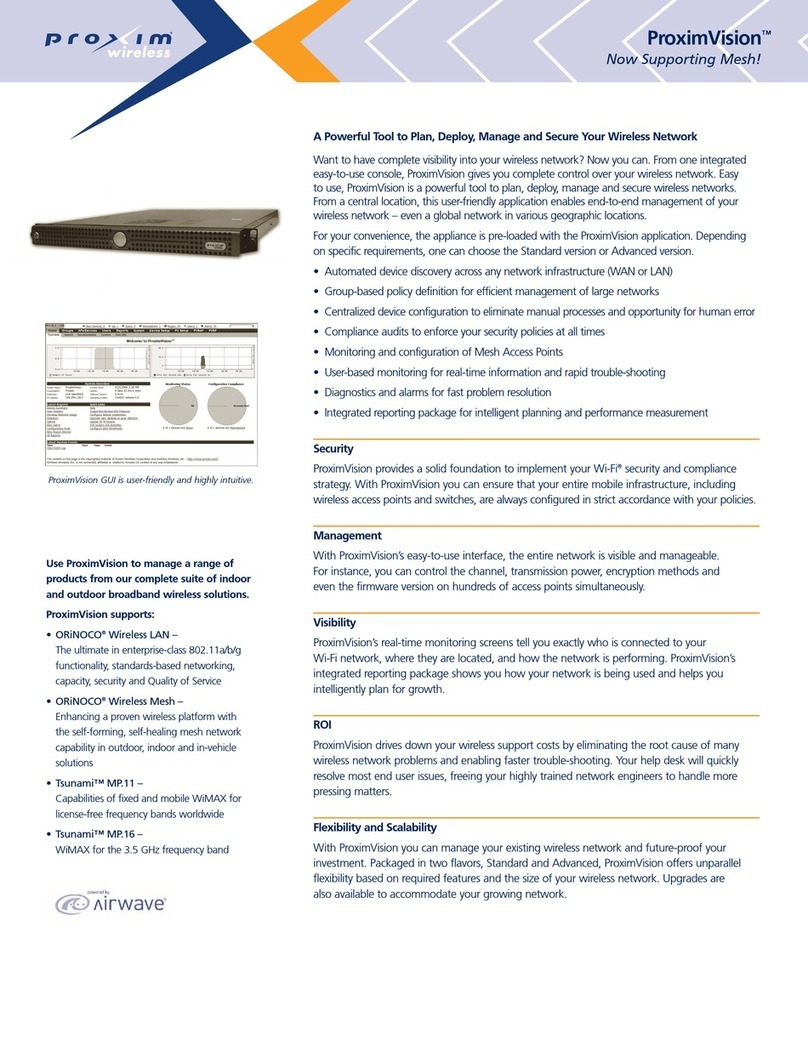
Proxim
Proxim ProximVision Specifications