Xstream AC7580B User manual

operation manual
Model #
AC7580B
AC7580B3
AC7580S
AC7580S3
AC1080S
AC1080SQ
CAUTION READ THIS MANUAL CAREFULLY before operating or servicing this
air compressor, to familiarize yourself with the proper safety, operation, and standard
operating procedures of this unit. FAILURE TO COMPLY WITH INSTRUCTIONS IN
THIS MANUAL COULD RESULT IN THE VOIDING OF YOUR WARRANTY, AND
PERSONAL INJURY, AND/OR PROPERTY DAMAGE. THE MANUFACTURER
OF THIS AIR COMPRESSOR WILL NOT BE LIABLE FOR ANY DAMAGE
BECAUSE OF FAILURE TO FOLLOW THE INSTRUCTIONS IN THIS MANUAL.
By following the instructions and recommendations in this manual you will ensure a
longer and safer service life of your air compressor.

2
Using the Operator’s manual
The operating manual is an important part of your Compressor and
should be read thoroughly before initial use, and referred to often to make
sure adequate safety and service concerns are being addressed.
Reading the owner’s manual thoroughly will help avoid any personal injury
or damage to your pump. By knowing how best to operate this machine
you will be better positioned to show others who may also operate the
unit.
You can refer back to the manual at any time to help troubleshoot any
specific operating functions, so store it with the machine at all times.
Attention: Read through the complete
manual prior to the initial use of your
Compressor
introduction

3
product identification
Record Identification Numbers
Compressor
If you need to contact an Authorized Dealer or Customer Service line
(1-866-770-1711) for information on servicing, always provide the
product model and identification numbers.
You will need to locate the model and serial number for the pump and
record the information in the places provided below.
Date of Purchase:
Dealer Name:
Dealer Phone:
Product Identification Numbers
Model Number:
Serial Number:

4
table of contents
Introduction
2 Using the Operator’s Manual
Product Identification
3 Record Identification Numbers
Safety
7 Safety Precautions and Warnings
Description
9 Compressor
9 Air/Oil System
9 Air Filter
9 Oil Filter
9 Air/Oil Separator
10 Minimum Pressure Valve
10 Cooling
10 Head Load of Compressor
11 Controls
Installation
11 General
11 Foundation
11 Room
11 Air Intake
Receiving Compressor
12 Receiving and Uncrating your Compressor
Compressor Installation
13 Location
13 Mounting
13 Induction System
14 Cooling Air Discharge
14 Electrical
14 Unpacking and Handling
15 Storage
Guidelines
15 Guidelines
16 Operation

5
table of contents
16 Preparation for Initial Start-Up
17 Noise
17 Piping Fitup
17 Pressure Vessels
18 Electrical
18 Pressure Switch
19 Manual Relief and Shutoff Valves
19 Guards
19 Drives
Pre-Operation
21 Start Up Preparation and Procedures
21 Stopping
21 Emergency Stopping
21 Air Filter
21 Element Inspection and Replacement
22 Oil Filter
22 Oil Filter Replacement
22 Air/Oil Separator
22 Separator Element Replacement
23 Lubricant
23 Lubricant Specifications
23 Oil Analysis
24 Checking Oil Level and Adding
Compressor Oil
24 Changing Compressor Lubricant
25 Oil Return Sight Glass
25 Minimum Pressure Valve
25 To Check the Belts
25 Fan
Compressor Diagram
26 Wiring Diagrams
Troubleshooting
29 Troubleshooting Chart
Compressor Breakdown
31 Breakdown
32 Breakdown List

6
Adustments and Alignments
33 Adjusting Belt Tension
33 Pulley Alignment
Maintenance
34 Stopping for Maintenance or Service
35 Daily
35 Weekly
35 Monthly
35 Every 3 Months
35 Yearly
36 Storage of Compressor
36 Safety Procedures
table of contents

7
safety
Safety Precautions and Warnings
Listed are some, but not all safety precautions that must be observed
with compressors and compressed air systems. Failure to follow any
of these warnings may result in severe personal injury, death, property
damage and/or compressor damage.
Air from this compressor will cause severe injury or death if used for
breathing or food processing.
Air used for these processes must meet OSHA 29 CFR 1910 or FDA 21
178.3570 regulations.
This compressor is designed for use in the compression of normal
atmospheric air only. No other gases, vapors or fumes should be exposed
to the compressor intake, nor processed through the compressor.
Disconnect all power supplies to the compressor plus any remote
controllers prior to servicing the unit.
Relieve all pressure internal to the compressor prior to servicing.
Do not depend on check valves to hold system pressure.
A properly sized safety valve must be installed in the discharge piping
ahead (upstream) of any shutoff valve (block valve), heat exchanger,
orifice or any potential blockage point. Failure to install a safety relief
valve could result in rupturing or explosion of some compressor or safety
component.
Do not change the pressure setting of the safety relief valve, restrict the
function of the safety relief valve, or replace the safety valve with a plug.
Over pressurization of some system or compressor component can
occur, resulting in severe personal injury, death and property damage.
Never use plastic pipe, rubber hose, or soldered joints in any part of
the compressed air system. Failure to ensure system compatibility with
compressor piping is dangerously unsound.
Never use a flammable or toxic solvent for cleaning the air filter or any
parts.
Do not attempt to service any part while the compressor is operating.
Do not operate the compressor at pressures in excess of its rating.
Do not remove any guards while the compressor is operating.
Observe gauges daily to ensure compressor is operating properly.
Follow all maintenance procedures and check all safety devices on
schedule.
Compressed air is dangerous, do not play with it.
Use the correct lubricant at all times.

8
safety
This Compressed Air Systems industrial rotary screw compressor is an
electric motor driven single stage helical rotary screw compressor. It is
sold as a complete package mounted on a steel base. This unit can come
with options of being tank mounted, Enclosure mounted or Enclosure
tank mounted. The package includes the compressor air end, electric
motor, motor controls, air intake system, cooling system, SMART contact
capacity control system, air/oil separator, and instrumentation. Installation
requires only electric power and a service line.
This air compressor is a rotating piece of equipment and should not be
worked on or serviced while there ispower to the unit. You should always
turn the power off to the compressor unit before performing and kind
of service to the machine. If you have any questions please contact the
factory for clarifications before making any changes to the delivered state
of the compressor.
WARNING
Compressed Air from this machine is not suitable for breathing and will
cause death or server personal injury .
Consult an air filtration specialist for proper treatment for breathing
WARNING
Compressed Air Systems design for the compressors is for indoor installation.
Consult the factory for any other areas of installation.
WARNING
This rotary screw compressor is a constantly running air compressor. It
DOES NOT START AND STOP. The compressor will only turn off for, high
temperature, high pressure, over amperage of electrical systems, timer limit
reached.

9
Descriptions
Compressor
The compressor assembly is a positive displacement, oil flood lubricated,
helical rotary screw type unit employing a single stage of compression.
The components include housing or stator, two rotors or screws,
bearings and bearing supports.
In operation two helical grooved rotors mesh to compress air. Inlet air
entering the compressor becomes trapped between the lobes of the
rotors. As the rotors turn, this trapped volume of air is reduced in volume
or compressed and is pushed to the discharge end of the compressor.
This process delivers smooth flowing air at full pressure to the receiver.
During the compression cycle, oil is injected into the compressor for the
purposes of lubricating, cooling, and sealing. Compressed air laden with
oil leaves the compressor through a discharge port designed to provide
optimum performance within the desired pressure range.
Air/Oil System
The air/oil system is almost completely contained within the compressor
housing. Within or directly attached to the housing are the air filter, oil
filter and the air/oil separator element.
Air Filter
The air filter is a high efficiency ring style located on top of the inlet valve
of the compressor. It will provide nearly constant efficiency of filtration at
all load conditions. The element has a high dirt holding capacity
for a long life. It is specially treated to be insensitive to heat, cold, water,
and oil.
Oil Filter
The oil filter is a 10-micron spin-on style. It is sized to maintain system
cleanliness and to give good service life. The housing is equipped with a
bypass to insure that there is oil flow on startup. The restriction created
at the filter will have a direct effect on the operating temperature of the
compressor. So you must be sure to maintain it.
Air/Oil Separator
This unit utilizes a spin-on air/oil separator to make maintenance much
more convenient than the element in vessel design. This does not
diminish its operating efficiency. In fact the separation of the element from
the pre-separation tank enhances the performance. The purpose of
the separator is to remove aerosols. The vapor pressure of the oil, the
operating temperature of the unit, operating pressure of the unit and the
operating cycle will affect its performance.
description

10
Minimum Pressure Valve
As the compressed air leaves the compressor it goes through a minimum
pressure valve. This is set to maintain at least 85 psig (586kPa) in the
sump when the compressor is running. This is to insure that there is
pressure to force the oil out of the sump and through the oil system so
that sufficient oil is injected into the compressor. It is also necessary to
provide good air/oil separation. The valve acts as a check valve to
prevent back flow into the compressor from the plant system.
Cooling
The compressor has an air-cooled and after-cooler as standard. The
following are the heat loads and cooling airflow rates that must be
accommodated.
Head Load of Compressor
The compressor is an oil flooded unit. The oil lubricates, seals, and cools the
internals of the compressor.In cooling it picks up the heat generated by the
compression process and the mechanical friction from the bearings. So the oil
must be cooled to within 60 degrees Fahrenheit of the ambient temperature.
The after-cooler has been designed for a minimum approach of 15 degrees F
MODEL TOTAL HEAT LOAD REQUIRED FLOW
B/MIN CFM
5-7.5HP 805 1767
10HP 1064 2335
15HP 1587 3483
20HP 2104 4619
25HP 2727 5985
30HP 3250 7134
40HP 4256 9341
50HP 5325 11,700
60HP 6390 14,040
75HP 7988 17,550
100HP 10,650 23,400
125HP 13,313 29,250
150HP 15,975 31,100
200HP 21,300 46,800
250HP 26,625 58,500
300HP 31,950 70,200
description

11
Controls
The RS series of units is equipped with a normally closed inlet valve. This
means that when the unit is started, the inlet valve remains closed while
the unit builds up pressure by means of a bypass line. After startup
the inlet valve is controlled by a simple on/off action of a pressure switch
working with a solenoid valve.
For instrumentation the unit has a discharge temperature gauge, air
pressure gauge
Installation
General
The standard RS series was designed for indoor applications. For
outdoor applications consult the factory for modifications. Failure to
obtain factory approval will void the warranty.
Foundation
Your Compressed Air Systems LLC rotary screw compressor does not
require a special foundation. However, it is necessary that the floor be
level and the frame adequately supported. Consult the SPECIFICATIONS
section of this manual for the compressor weight and dimensions. We do
recommend that the compressor be bolted to the floor. We recommend
the compressor be mounted on vibration reduction pads
Room
The room should be of adequate size to provide full access to the
machine for routine maintenance. It should have ventilation to keep the
room as cool as possible. Operating at elevated temperatures will cause
nuisance overload and temperature shutdowns. Room temperature
should not exceed 1100 F.
Air Intake
To achieve the longest filter and lubricant life and the least maintenance
you need to supply the compressor with the cleanest air possible. It must
not contain any flammable or toxic gases. These will be concentrated
by the compressor, and could result in personal injury or death and
property damage.
WARNING
Inlet containing reactive gases will cause the failure of the lubricant and
compressor. Insure an air supply that is well clear of any reactive gas source.
If it is necessary to take air from a remote source, the piping should be
at least the diameter of the air filter inlet. For distance over twenty feet
the diameter needs to be enlarged to reduce the restriction. This pipe
should also be corrosion resistant and free from scale and dirt. The inlet
should also be covered to prevent rain and small animals from entering.
description

12
Receiving and uncrating your compressor
Before uncrating the compressor the following steps should be taken.
Immediately upon receipt of the equipment, it should 1. be inspected for
damage that may have occurred during shipment. If any damage is found,
demand an inspection immediately by an inspector from the carrier. Ask
him how to file a claim for damages. (See Appendix “A” for Details).
2. Insure that adequate lifting equipment is available for moving the
machinery.
3. Read the compressor nameplate to be sure the compressor is the
model and size ordered.
4. Read the motor nameplate to be sure the motor is compatible with
your electrical conditions. (Volts-Phase-Hertz).
NOTE
Standard motors are open drip proof with a maximum ambient temperature
rating of 104 degrees F. They are not suitable for salt laden, corrosive, dirty,
wet, or explosive environments.
CAUTION
Improper lifting can result in component or system damage or personal injury.
Follow good shop practices and safety procedures
IMPORTANT: If voltage supplied to the compressor is below 208 volts the
unit need a 200 Volt drive motor. Motors rated at 208-230-460 Volt should not
be used below 208 volts.
receiving compressor

13
Location
Locate the compressor in an indoor area that is clean, dry, well lighted,
and well ventilated, with sufficient space for safe and proper inspection
and maintenance. Ambient temperatures should not exceed 104 degrees.
For fall below 30 degrees unless an electric motor rated for a higher
temperature is used. Inspection and maintenance checks are required
daily, therefore, ample space is required around the compressor.
The compressor must not be installed closer than fifteen inches from a
wall or from another compressor to allow ample circulation or air across
the compressor cylinders and head, and through the coolers if they are
part of the system. Additional safety can be achieved by locating the
pulley guard next to the wall.
Mounting
We recommend the use of rubber pads or isolators between the tank
legs and the floor. If a shim is required to level the unit, place it between
the pad and floor. If you bolt the unit to the floor, use the bolts as
guide pins and do not tighten the bolts. The rubber pads are used to
absorb machine vibration and cannot
work effectively if bolted tightly.
Induction System
Do not locate the compressor where it could ingest or ignite toxic,
explosive or corrosive vapors, ambient air temperatures exceeding 104
degrees F, water or extremely dirty air. Ingestion of any of the above noted
atmospheres by the compressor could jeopardize the performance of the
equipment and all personnel exposed to the total compressed air system.
Depending on the size of the compressor and the size and construction
of the compressor room it may be necessary to locate the air pickup point
outside the room. Destructive pulsations can be induced by reciprocating
compressors that will damage walls and break windows. Pulsation can
be minimized by adding a pulsation dampener on the inlet side of the
compressor.
CAUTION
Under no circumstances should a compressor be placed in an area that may be
exposed to a toxic, volatile or corrosive atmosphere nor should toxic, volatile or
corrosive agents be stored near the compressor.
compressor installation

14
Cooling Air Discharge
The cooling air discharge must be restriction free. Any louvers or
ducting must not exceed a quarter of an inch static head. Above this
a booster fan will be required. Consult a local HVAC contractor for
recommendations prior to installation. Excessive restriction to the cooling
air discharge will cause the unit to operate at elevated temperatures that
could result in high temperature shutdowns. Ducting of cooling air to the
unit is not generally recommended.
Electrical
A qualified electrician in compliance with standards and local codes
should do all electrical wiring. Be sure to investigate the local
requirements before installing the compressor. The power supply should
be adequate and free of parasitic loads that will cause an under voltage
condition during the operation of the compressor, otherwise there will
be nuisance electrical shutdowns. Always connect the compressor to its
power source through a fusible disconnect and insure the unit is
properly grounded.
Unpacking and Handling
Occasionally damage will occur during shipping. Be sure to carefully
inspect the unit before unpacking. After unpacking before you sign the
receiver, if anything damage has occurred, document it with the
trucking firm immediately. Contact your Compressed Air Systems LLC.
representative for assistance.
To move your compressor to its installation site we recommend that you
leave the unit on its shipping skid as long as possible. The forks should
be extended the width of the compressor and padding should be placed
between the compressor and the truck boom.
If it is necessary to lift the compressor with a crane, we recommend the
use of the spreader bar and chains. The spreader bar should be greater
than the width of the compressor and padding is placed on
the edges to prevent chain damage. Consult the installation drawing at
the end of this section for the center of gravity.
compressor installation

15
Storage
In some cases it may be necessary to store the compressor for extended
periods of several months before placing the unit in operation. When this
is required do the following:
Cover and seal all machine openings to prevent the
entrance of water and dirt.
Cover all openings in open drip proof motors to prevent
the entrance of rodents.
If the storage conditions are below freezing; drain the after cooler,
traps, water-cooled heat exchanges and attendant piping. We do not
recommend outside storage.
Cover with a waterproof tarpaulin that can easily be removed for in-
storage maintenance.
While in storage, every two or three months, rotate the compressor
and motor by hand to prevent flat spots on the bearings that will lead to
premature failure.
At the end of the storage period, follow the uncrating and start-up
procedures. If the unit has been stored for more than eighteen months,
you should contact Compressed Air Systems before restarting the
compressor.
Guidelines
The air pressure drop between the compressor and the point of use is
not recoverable.
Pipe size should be large enough that the pressure drop does not exceed
10% between the air receiver and the point of use.
Arrange the air distribution piping to avoid the following types of strain:
Strains that are due to dead weight of the pipe itself.
Strains that are due to expansion or contraction of the piping due to
temperature.
Strains due to internal pressure within the pipe.
Design inlet and discharge piping for smooth airflow.
Plan for future emergencies and establish an area of the loop to install a
temporary compressor.
Consider a second receiver at the end of the line or opposite side of the
loop.
installation/guidelines

16
Guidelines
Locate runaways from the main header close to the point of application.
Take air off the top of the header to prevent carryover of condensed
moisture to tools.
Slope piping so that it drains toward a drop leg or moisture trap away
from the compressor.
Operation
Every Compressed Air Systems LLC compressor has been operated
and thoroughly tested at the factory prior to shipment. The test assures
that the compressor will deliver its rated capacity and is in good working
order. However, there is the possibility that damage may occur in
shipping. For this reason, it is recommended that the unit be carefully
inspected for evidence of damage or malfunction before installation
and during the first hours of operation
Preparation for Initial Start-Up
1. Pull the main disconnect switch and ensure that there is no power
to the unit.
2. Review the installation instructions to see that everything is complete.
3. Inspect for visible signs of damage that could have happened during
shipment or installation.
4. Make certain protective coverings required for shipment or painting
are removed from the compressor.
5. Fill the sump to the proper oil level. Do not overfill, if it is, drain to
proper level. Tighten the fill cap securely.
6. Reconnect the main disconnect.
7. Refer to control section and check out panel components.
8. “Jog” the motor (press start and stop in quick succession) and check
for the correct direction of rotation. Reverse LS1 and L2 connections
if incorrect
9. Start the unit and run for several minutes, then shutdown. Check the
oil level and add, if necessary, to compensate for filling the system.
10. Begin normal operation
WARNING
Reverse rotation will cause air end damage. Exchange leads L1 and L2, if
reverse rotation.
guidelines

17
CAUTION
ASME coded pressure vessels must not be modified, welded, repaired,
reworded or subjected to operation conditions outside the nameplate ratings.
Such actions will negate code status, affect insurance status and may cause
severe personal injury, death, and property damage.
Noise
Noise is a potential health hazard that must be considered. There are
local and federal laws specifying maximum acceptable noise levels
that must not be exceeded. Most of the noise from a reciprocating
compressor originates from the air inlet point. Excessive noise can be
greatly reduced by installing an intake noise silencer.
Piping Fitup
Care must be taken to avoid assembling the piping in a strain with
the compressor. It should line up without having to spring or twist into
position. Adequate expansion loops or bends should be installed to
prevent undue stresses at the compressor resulting from the changes
between hot and cold conditions. Pipe support should be mounted
independently of the compressor and anchored as necessary to limit
vibration and prevent expansion strains.
SAFETY VALVES Safety valves are pressure relief valves and should be sized
and purchased with a pressure setting to protect the weakest link in the system.
Never change the pressure setting, only the safety valve manufacturer is qualified
to make a change.
Safety valves are to be place ahead of any potential blockage point which
included but is not limited to, shutoff valves, heat exchangers, pulsation
dampeners, and discharge silencers.
DANGER
Safety valves are to protect system integrity in accordance with ASME Codes &
ANSI B19.3 safety standards. Failure to use safety valves of the proper capacity
and pressure will cause severe personal injury or death.
DANGER
Failure to properly size, set & install pressure relief valves can be fatal.
Pressure Vessels
Air receiver tanks and other pressure containing vessels such as, but
not limited to, pulsation bottles, heat exchangers, moisture separators
and traps, shall be in accordance with ASME Boiler and Pressure Vessel
Code Section VIII and ANSI B19.3 Safety Standards.
guidelines

18
CAUTION
Electric power always exists inside the pressure switch when there is electric
power at the compressor package. Either a qualified electrician should make the
pressure adjustments or the electric power supply should be disconnected and
locked out before making any adjustment.
NEVER exceed the designed pressure for the system or overload the motor
beyond its service factor.
FAILURE TO HEED THESE WARNINGS MAY RESULT IN SERIOUS INJURY
OR DEATH, PROPERTY DAMAGE AND/OR MECHANICAL FAILURE
CAUTION
Relieve compressor and system air pressure by opening the appropriate manual
relief valve prior to servicing. Failure to relieve all system pressure may result in
severe personal injury, death and property damage.
Electrical
Before installation, the electrical supply should be checked for adequate
wire size and transformer capacity. During installation a suitable fused or
circuit breaker disconnect switch should be provided. Where a 3 phase
motor is used to drive a compressor, any unreasonable voltage unbalance
between the legs must be eliminated and any low voltage corrected to
prevent excessive current draw. Compressors must be equipped with a
properly wired magnetic motor starter or a pressure switch rated to carry
the full motor current load. The coil which engages and disengages the
contact points in the motor starter is controlled by the pressure switch.
Never attempt to bypass the pressure switch or adjust it past the factory
set pressure range. Improper installation of the electrical system can
cause the motor to overheat or a short circuit to occur.
Pressure switch
The pressure switch is automatic in operation and is adjusted to start and
stop the unit at the minimum and maximum desired air receiver pressure
by cutting in and out the power to the electric motor. On some models,
the pressure switch incorporates a release valve, which releases air
between the check valve located in the receiver and discharge valve in
the head of the compressor.
DANGER
The installation, wiring, and all electrical controls must be in accordance
with ANSI C1 National Electric Code, ANSE C2 National Electric Safety Code,
state and local codes. All electrical work should be performed by a qualified
electrician. Failure to abide by the national, state and local codes may result in
physical and/or property damage.
guidelines

19
Manual Relief And Shutoff Valves
Install a manual relief valve to vent the compressor to atmosphere. In
those instances where the air receiver tank services a single compressor,
the manual relief valve can be installed on the receiver. When a manual
shut- off valve, and a safety relief valve installed upstream from the
manual relief valve. These valves are to be designed and installed as to
permit maintenance to be performed in a safe manner. Never substitute
a check valve for a manual shut-off valve (block valve) if the purpose is to
isolate the compressor from a system for servicing.
Guards
All mechanical action or motion is hazardous in varying degrees and
needs to be guarded. Guarding shall be in compliance with OSHA Safety
and Health Standards 29 CFR 1910.219 in OSHA manual 2206 and any
state or local code.
Drives
It is important that the compressor and motor pulleys are aligned properly
and the V belt is correctly tensioned. Improper pulley alignment and
belt tension are causes for motor overloading, excessive vibration, and
premature belt and/or bearing failure.
CAUTION
Guards must be fastened in place before starting the compressor and never
removed before cutting off and locking out the main power supply.
CAUTION
Excessive speed of the compressor or driver can be lethal. Never operate
the compressor beyond the manufacturer’s recommendation. Bursting of the
flywheel may be the greatest threat because the normal guard may not contain
all the pieces. Crankshaft and connecting rod breakage is a possibility and
compressor efficiency, valve life and bearing life will be abnormally reduced.
guidelines

20
CAUTION
Removal or painting over safety labels will result in uninformed conditions
This may result in personal injury or property damage. Warnings signs and
labels shall be provided with enough light to read, conspicuously located and
maintained for legibility. Do not remove any warning, caution, or instructional
material attached!
Provisions should be made to have the instruction manual readily available
to the operator and maintenance personnel. If for any reason any part of the
manual becomes illegible or if the manual is lost, have it replaced immediately.
The instruction manual should be periodically read to refresh one’s memory, it
may prevent a serious or fatal accident.
guidelines
This manual suits for next models
5
Table of contents
Other Xstream Air Compressor manuals
Popular Air Compressor manuals by other brands
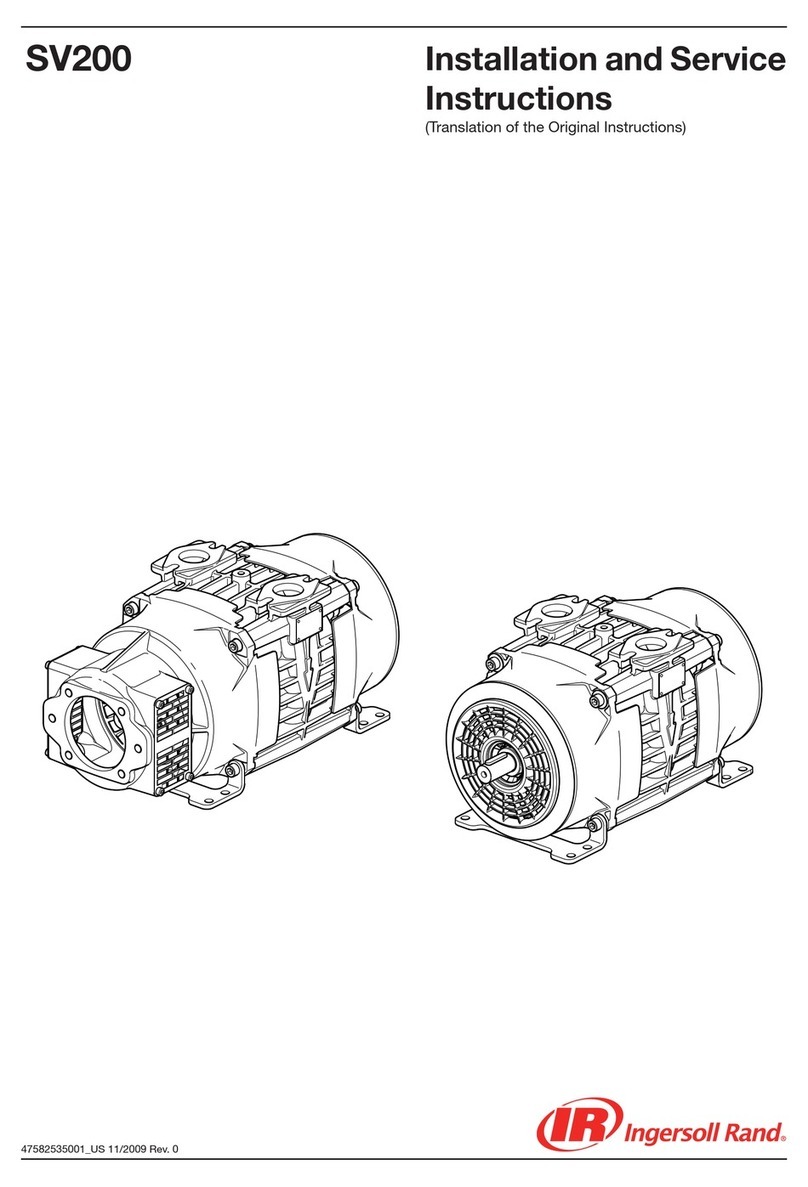
Ingersoll-Rand
Ingersoll-Rand SV200 Installation and service instructions
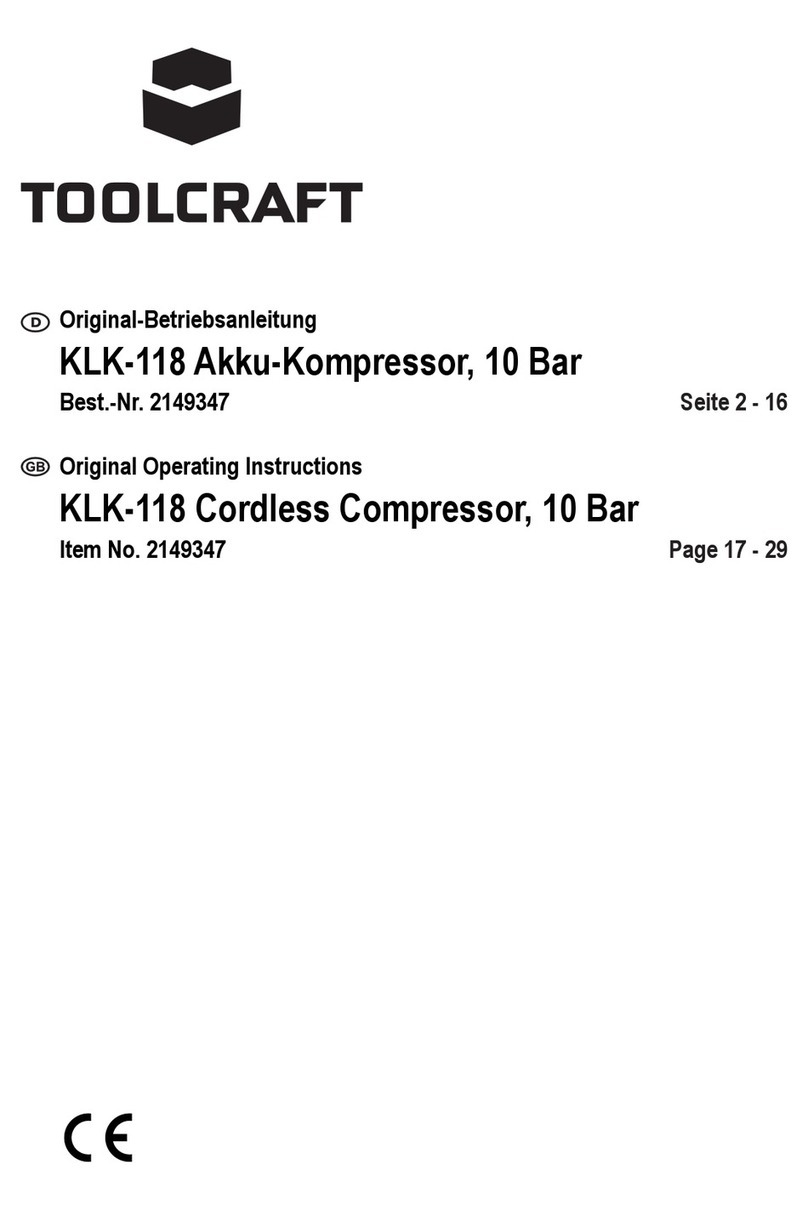
TOOLCRAFT
TOOLCRAFT 2149347 operating instructions

Britpart
Britpart DA2392 user manual
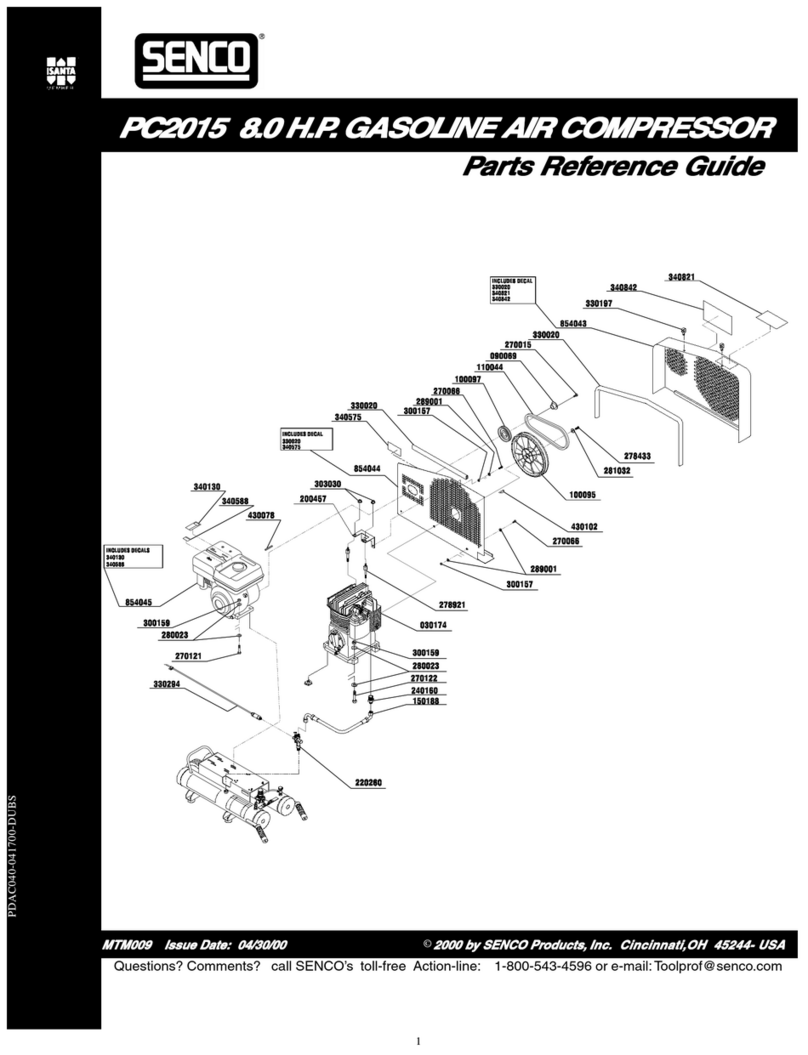
Senco
Senco PC2015 Parts reference guide
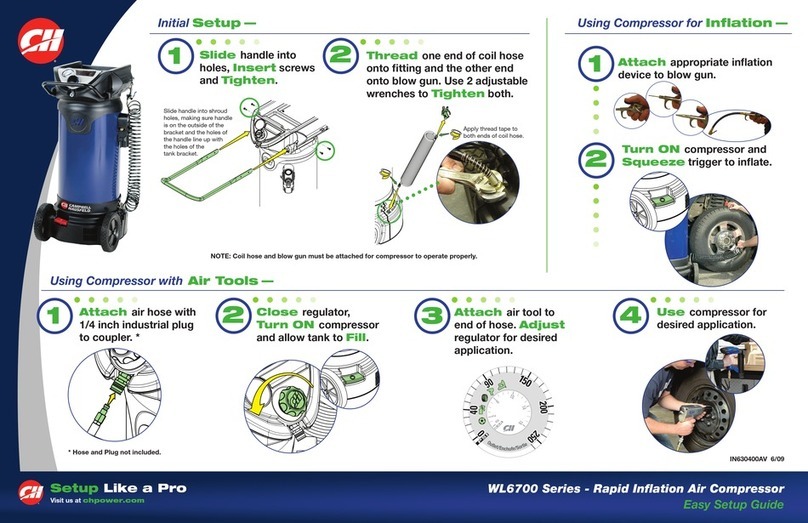
Campbell Hausfeld
Campbell Hausfeld WL6700 Series Easy setup guide
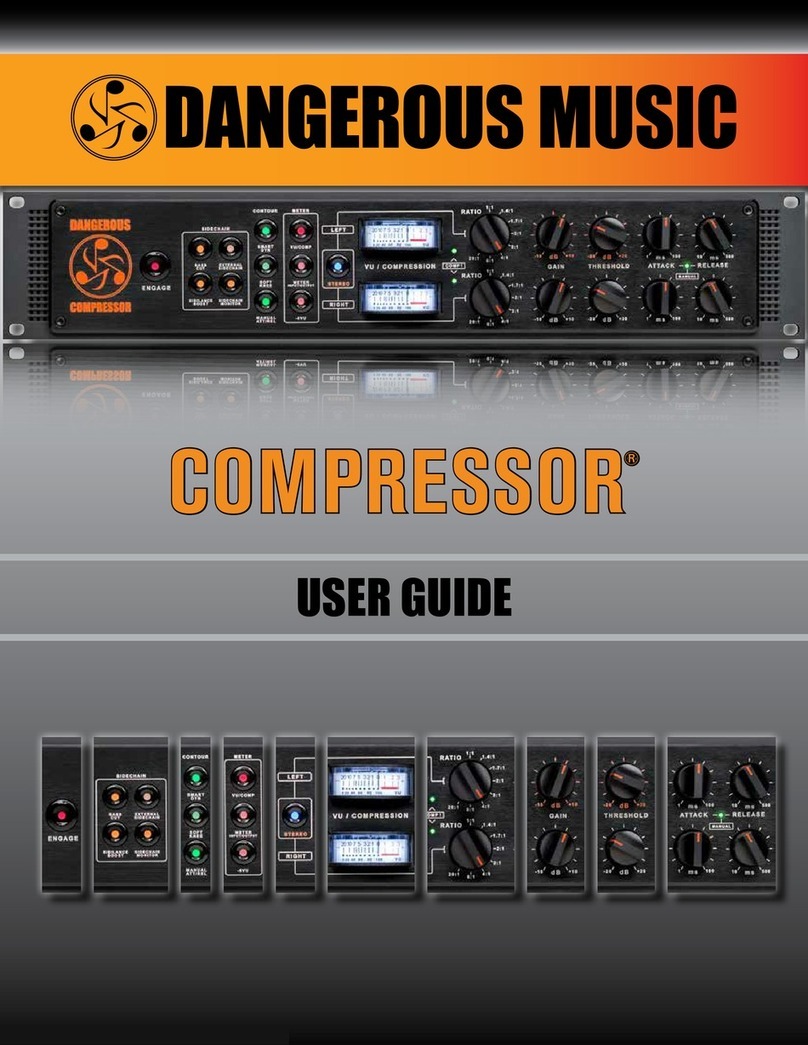
Dangerous Music
Dangerous Music COMPRESSOR user guide