ZETRON 1708 User manual

Models 1708 and 1716
Remote Terminal Units
Installation and Operation Manual
025-9209K

Software License
The Zetron software described in this manual is subject to the terms and conditions of Zetron’s Software License
Agreement, a copy of which is contained on the product distribution media or otherwise provided or presented to buyer.
Installation and/or use of the Zetron software constitutes acceptance of Zetron’s Software License Agreement.
Limited Warranty
Buyer assumes responsibility for the selection of the Products to achieve buyer’s or its customer’s intended results obtained
from the Products. If buyer has provided Zetron with any requirements, specifications or drawings, or if Zetron provides
buyer with such materials, such materials are provided solely for buyer’s convenience and shall not be binding on Zetron
unless agreed in writing by the President of Zetron. ZETRON DOES NOT WARRANT THAT THE PRODUCTS OR ITS
CUSTOMER’S REQUIREMENTS OR SPECIFICATIONS OR THAT OPERATION OF THE PRODUCTS WILL BE
UNINTERRUPTED OR ERROR FREE. SUBJECT TO THE LIMITATIONS SET FORTH BELOW, Zetron warrants that
all Zetron Products and Zetron Accessories will be free from material defects in material and workmanship for one year
from date of shipment (except where indicated otherwise in the Zetron Price Book). For buyer’s convenience, Zetron may
purchase and supply additional items manufactured by others. In these cases, although Zetron’s warranty does not apply,
buyer shall be the beneficiary of any applicable third party manufacturer’s warranties, subject to the limitations therein.
Zetron’s warranty covers parts and Zetron factory labor. Buyer must provide written notice to Zetron within the warranty
period of any defect. If the defect is not the result of improper or excessive use, or improper service, maintenance or
installation, and if the Zetron Products or Zetron Accessories have not been otherwise damaged or modified after shipment,
AS ZETRON'S SOLE AND EXCLUSIVE LIABILITY AND BUYER’S SOLE AND EXCLUSIVE REMEDY, Zetron
shall either replace or repair the defective parts, replace the Zetron Products or Zetron Accessories, or refund the purchase
price, at Zetron’s option, after return of such items by buyer to Zetron. Shipment shall be paid for by the buyer. No credit
shall be allowed for work performed by the buyer. Zetron Products or Zetron Accessories which are not defective shall be
returned at buyer’s expense, and testing and handling expense shall be borne by buyer. Out-of-warranty repairs will be
invoiced at the then - current Zetron hourly rate plus the cost of needed components. THE FOREGOING WARRANTY
AND THE THIRD PARTY MANUFACTURER'S WARRANTIES, IF ANY, ARE IN LIEU OF ANY AND ALL OTHER
WARRANTIES EXPRESSED, IMPLIED OR ARISING UNDER LAW, INCLUDING, BUT NOT LIMITED TO, THE
IMPLIED WARRANTIES OF MERCHANTABILITY, NON-INFRINGEMENT AND FITNESS FOR A PARTICULAR
PURPOSE.
Limitation of Liability
Zetron makes no representation with respect to the contents of this document and/or the contents, performance, and function
of any accompanying software. Further, Zetron reserves the right to revise this document or the accompanying software and
to make changes in it from time to time without obligation to notify any person or organization of such revisions or changes.
ZETRON SHALL NOT UNDER ANY CIRCUMSTANCES BE LIABLE TO BUYER OR ANY THIRD PARTY FOR
ANY INCIDENTAL, SPECIAL, CONSEQUENTIAL OR INDIRECT LOSS OR DAMAGE ARISING OUT OF OR
CONNECTED WITH BUYER’S PURCHASE OR USE OF PRODUCTS OR SERVICES, INCLUDING WITHOUT
LIMITATION, LOSS OF USE, LOSS OR ALTERATION OF DATA, DELAYS, LOST PROFITS OR SAVINGS, EVEN
IF ZETRON HAS BEEN ADVISED OF THE POSSIBILITY OF SUCH DAMAGES AND EVEN IF THE LIMITED
REMEDY ABOVE IS FOUND TO FAIL OF ITS ESSENTIAL PURPOSE. IN NO EVENT SHALL ZETRON’S
LIABILITY (WHETHER FOR NEGLIGENCE OR OTHER TORT, IN CONTRACT OR OTHERWISE) EXCEED THE
PRICE PAID TO ZETRON FOR THE PRODUCTS.
IP networks by their nature are subject to a number of limitations, such as security, reliability, and performance. Anyone
using non-dedicated IP networks, such as shared WANs or the Internet, to connect to any Zetron Products or systems should
consider and is responsible for these limitations.
© Zetron, Inc. All rights reserved. This publication is protected by copyright; information in this document is subject to
change without notice. Zetron and the Zetron logo are registered trademarks of Zetron, Inc. Other company names and
product names may be the tradem
arks or registered trademarks of their respective owners. This publication may not be
reproduced, translated, or altered, in whole or in part, without prior written consent from Zetron, Inc.

Contents
025-9209K 3
Regulatory Compliance
FCC Class A User Information
This equipment has been tested and found to comply with the limits for a Class A digital device, pursuant to Part 15 of the
FCC Rules. These limits are designed to provide reasonable protection against harmful interference when the equipment is
operated in a commercial environment. This equipment generates, uses, and can radiate radio frequency energy and, if not
installed and used in accordance with the instruction manual, may cause harmful interference to radio communications.
Operation of this equipment in a residential area is likely to cause harmful interference in which case the user will be
required to correct the interference at his own expense.
EMC Compliance Standards
This product meets the requirements of the standards listed below.
•FCC Part 15 – Radiated & Conducted Emissions (USA)
Regulatory Compliance Markings
Product Certification Markings:
•FCC Part 15 (USA)
Change List for Rev K, March 2015
•Updated legal front matter and regulatory compliance information, Zetron Logo,
& formatting

Contents
025-9209K 4
INTRODUCTION
GENERAL...........................................................................................................9
SYSTEM DESCRIPTION...................................................................................10
MODBUS SYSTEM............................................................................................10
CONNECTIONS .................................................................................................11
SPECIFICATIONS
PHYSICAL SPECIFICATIONS .........................................................................13
RS-232 INTERFACE ..........................................................................................13
RADIO INTERFACE..........................................................................................13
Radio Modem Specifications...................................................................13
Signal Integrity.........................................................................................14
I/O SPECIFICATIONS .......................................................................................14
External Inputs .........................................................................................14
External Outputs ......................................................................................14
OPERATION
GENERAL OPERATION ...................................................................................15
ADDRESSING THE RTU ..................................................................................16
CONFIGURATION.............................................................................................17
Accessing the RTU Program Mode .........................................................17
MAIN MENU ......................................................................................................18
Prekey Time .............................................................................................18
Channel Busy Detect................................................................................19
Channel Busy Timeout ............................................................................19
Transceiver Type .....................................................................................19
Address Extension ...................................................................................19
Controller Address ...................................................................................19
Group Call Address..................................................................................19
Factory Defaults.......................................................................................20
FAIL SAFE SETUP.............................................................................................20
Communication Failure Enable ...............................................................20

Contents
025-9209K 5
Channel Use Limits..................................................................................21
Enable/Disable Exception Reports ..........................................................21
STORE AND FORWARD ..................................................................................21
Slot No. ....................................................................................................22
Source Address ........................................................................................22
Destination Address .................................................................................22
Replacement Source Address ..................................................................22
Replacement Destination Address ...........................................................22
Next slot...................................................................................................22
Example ...................................................................................................22
DIGITAL INPUT DEFINITION .........................................................................23
Enable Input .............................................................................................23
Disable Input............................................................................................24
N/O Input .................................................................................................24
N/C Input .................................................................................................24
Status Input ..............................................................................................24
Debounce Time ........................................................................................24
Next Input ................................................................................................24
DIGITAL OUTPUT DEFINITION .....................................................................25
Latched Mode ..........................................................................................25
Momentary Mode.....................................................................................25
Output On.................................................................................................25
Force Output Off......................................................................................25
Next Output..............................................................................................25
ANALOG INPUT DEFINITION ........................................................................26
Enable Input .............................................................................................26
Disable Input............................................................................................26
High Threshold ........................................................................................26
Low Threshold .........................................................................................26
High Reset................................................................................................27
Low Reset ................................................................................................27
Accumulator Sampling Rate ....................................................................27
% Change Alert........................................................................................27
% Change Debounce................................................................................27
Next Input ................................................................................................27
SYSTEM OPERATIONAL LIMITS ..................................................................28
Inputs........................................................................................................28
Outputs.....................................................................................................28
Power .......................................................................................................29
Radio Connections and Associated Problems..........................................29
Critical System Failures Summary ..........................................................30
MODBUS SYSTEM SET UP
MODBUS OPTION.............................................................................................31
COMMUNICATIONS ........................................................................................32

Contents
025-9209K 6
Polled-Only System .................................................................................32
Report-By-Exception System ..................................................................32
Which Is Better - Polled-Only or Report-By-Exception?........................33
MODBUS MASTER REQUIREMENTS ...........................................................33
CONFIGURING THE 1700 CONTROLLER.....................................................34
MODBUS Menu ......................................................................................34
Polled-Only Configuration.......................................................................34
Report-By-Exception Configuration........................................................35
RS-232 Watchdog Configuration ............................................................36
CONFIGURING THE RTUs...............................................................................36
Assign Addresses .....................................................................................36
MODBUS Version of the RTU Menu .....................................................37
CONFIGURING THE MASTER PC (OR PLC).................................................37
BASIC MODBUS I/O ADDRESSING ...............................................................38
USING ACCUMULATORS AND COUNTERS ...............................................39
SOFTWARE PRODUCTS FOR THE MODBUS PROTOCOL ........................44
SET UP AND INSTALLATION
INSTALLATION ................................................................................................45
Power Connection....................................................................................45
System Grounding ...................................................................................45
Radio Connection.....................................................................................46
Step 1. Cable Connection.........................................................................46
Step 2. Carrier Detect and Push to Talk Settings.....................................46
Step 3. Transmit and Receive Audio Adjustment....................................47
MODEL 1708 JUMPERS AND I/O....................................................................48
Model 1708 Jumper Settings ...................................................................48
Model 1708 I/O Connections...................................................................48
MODEL 1716 JUMPERS AND I/O....................................................................50
Model 1716 Jumper Settings ...................................................................50
Model 1716 I/O CONNECTIONS...........................................................51
CONNECTION OF LOCAL RTU TO MODEL 1700 CONTROLLER ............52
50-PIN INDUSTRIAL I/O BOARD CONNECTOR..........................................53
THEORY OF OPERATION
BASIC FUNCTIONAL DESCRIPTION ............................................................55
FUNCTIONAL BLOCK DIAGRAM .................................................................55
TROUBLESHOOTING GUIDE
OVERVIEW ........................................................................................................57
REPAIR
MODEL 1708/1716 COVER REMOVAL AND REPLACEMENT ..................59
MODEL 1700 SERIES ENCLOSURE OUTLINE (024-0057B) .......................60

Contents
025-9209K 7
MODEL 1700 SERIES ENCLOSURE INSTRUCTIONS (024-0056D)............61
MODEL 1708 REMOTE TERMINAL UNIT SILKSCREEN (702-9439F) ......63
MODEL 1716 REMOTE TERMINAL UNIT SILKSCREEN (702-9440F) ......64
APPENDIX A
COMMUNICATING OVER TWO-WIRE BALANCED LINE (600Ω) ...........65
APPENDIX B
MODEL 1730/1732 COMMUNICATIONS AND I/O TEST PROGRAM........67
STARTING THE PROGRAM ............................................................................67
SETTING OPTIONS ...........................................................................................68
THE POLL MENU ..............................................................................................69
THE SET MENU.................................................................................................70
THE CLEAR MENU...........................................................................................71
GLOSSARY
INDEX

Contents
025-9209K 8

Introduction
025-9209K 9
INTRODUCTION
GENERAL
A Model 1708 or 1716 Remote Terminal Unit (RTU) is one part of a wireless SCADAi
telemetry system. A SCADA system typically consists of a PC with software connected to a
Controller and one or more RTUs at multiple distant locations. The Controller and RTU are
both microprocessor controlled and, along with the user’s radio link, make up the
communications network necessary for monitoring and controlling equipment at remote sites.
The Controller is typically located at a central office and can address up to 65,535 RTUs
located at various remote sites. Using the Controller and the RTUs, the user at the central
office can control equipment or retrieve information from the remote sites.
The size of a system is dependent on airtime available and the total transmissions required.
To determine the maximum number of RTUs your system will support, call Zetron at (425)-
820-6363.
The RTU interfaces directly to a wide variety of two-way radios, either conventional or
trunking. The RTU is designed to connect to remote sensing devices that can provide dry
contact closure to ground, TTL level voltage changes or 0 to 5 volts and 4 to 20 mA for
analog measurement.
Table 1 lists the I/O capability of the Models 1708 and 1716 RTUs and the Model 1700
Controller.
iSCADA = Supervisory Control and Data Acquisition. A general term for an industrial measurement, data
gathering, and control system.

Introduction
025-9209K 10
Table 1. Digital and Analog I/O Capability
I/O
1708
1716
1700
Digital In
8
16
0
Digital Out
8
16
4
Analog In
4
8
0
Analog Out
0
4
0
The RTU is initialized through the RS-232 port, which allows the user to customize the
parameters for each RTU to best fit the application.
SYSTEM DESCRIPTION
Model 1700
Control Unit
PC, CRT,
Printer or Status
Panel
Transceiver
Transceiver
Transceiver
Transceiver
1708/1716
RTU
Unit #1
I/O Lines
1708/1716
RTU
Unit #2
I/O Lines
1708/1716
RTU
Unit #9
I/O Lines
Figure 1. A Typical System with One Controller and Nine RTUs
Figure 1 depicts a model system that might be used to monitor and control pump stations.
This system gives the user PC or status panel control of turning pumps on or off and of
polling the sites to verify status and to receive alarm reports of pump failures or
communications failures.
MODBUS SYSTEM
MODBUS is an industry-standard protocol used to transfer commands and data. An example
of a SCADA program that uses the MODBUS protocol is Lookout (by National Instruments).
Many PLCs also use the MODBUS protocol. A MODBUS option for the Model 1700
controller allows the controller and Zetron RTUs to be used in a MODBUS system.

Introduction
025-9209K 11
A MODBUS SCADA system with a Model 1700 controller is shown in Figure 2.
In a MODBUS system, the PC can communicate with up to 150 Model 1708 or Model 1716
RTUs over radio or wireline through a single Model 1700 controller. A system can be
expanded beyond 150 RTUs by adding additional controllers and using additional serial ports
on the PC. The total number of RTUs in a system is limited only by the number of serial
ports available on the PC, and by the MODBUS slave address limit of 247.
Modbus PLC
- or -
PC with Modbus
SCADA Program
M1708/
M1716
M1708/
M1716
M1708/
M1716
RF
RF
RF
RS232
MODBUS Protocol
M1708/
M1716
RF - Store & Forward
Note: all RF connections could be replaced with leased lines
M1700 with
MODBUS
option
M1708/1716
with MODBUS
option
RS232
MODBUS
Protocol
Figure 2. Generalized MODBUS System
CONNECTIONS
Main Power
Flow Detector
Door Open
High Water
High Temperature
Panic Button
Model 1716
Remote Terminal Unit
Digital #1
Inputs
•
•
•
#16
Analog #1
Inputs
•
•
•
#8
Digital Outputs
#16
•••#1
Radio
Connections
Battery Level
Tank Level
Pump Control On/Off
Alarm On/Off
Panic Acknowledge On/Off
Back Up Power On/Off
Figure 3. Model 1716 RTU Standard Connections for a Pump Site
A standard application of monitoring and controlling a remote pump site could be
accomplished by using output #1 to control the pumps on/off switch and by connecting input
#1 to a flow meter to determine if the pump is pumping. If the control relay on the RTU is
damaged, the pipe is blocked, or a short or open circuit to the pump control has occurred,
then the RTU will report that no liquid is flowing.

Introduction
025-9209K 12
There are a variety of other status points that may be monitored: open door or window, high
water alarm, high temperature, main power, panic button for man at site, etc.
The RTU analog input range is 0 to 5 Vdc, and the levels being monitored should be
electrically scaled to fall within this voltage range. Many sensing devices output 0 to 5 Vdc.
However, some sensor outputs are 4 to 20 mA current loops, or an input may be using a 12-
volt power supply. The diagram below shows how to convert these two power sources into 0
to 5 Vdc levels for the RTU (4-20 mA Loop would be converted to 1-5 Vdc). There is a 249 Ω
resistor in the RTU that may be used to convert 4-20 mA to volts.
470 kΩ
Analog
Input
12 Vdc
Power Supply
330 kΩ
Analog
Input
249 Ω
4 - 20 mA
Loop
Figure 4. Common Conversion Circuits for 0-5 Vdc Scaling

025-9209K 13
SPECIFICATIONS
PHYSICAL SPECIFICATIONS
Power
10.5-16 V
dc
Current
75 mA typical, 150 mA maximum
Temperature
0 to +60 degrees C
Size
7.25"W x 10.5"L x 2.25"H
Weight
2 pounds
RS-232 INTERFACE
Baud Rate
4800
Parity
None
Bits
8
Stop Bits
1
RADIO INTERFACE
Audio Output
20 mV to 2 V p-p (mic level audio), 1 kΩ
Audio Input
100 mV to 4 V p-p, 50 kΩ
Channel Busy Input
Low: 0 to 0.7 V
dc
, <100 Ωto ground
High: 3.5 to 12 Vdc, >10 kΩto ground
PTT output
Relay contact closure, 300 mA max
Radio Modem Specifications
Data Rate
1200 baud
Signaling
Minimum Shift Keying (MSK)

2. Specifications
025-9209K 14
Signal Integrity
Required Signal
Strength
95% success at 12 dB SINAD
Probability of False
Data
1 in 109
(0.0000001%)
I/O SPECIFICATIONS
External Inputs
Contact Closure Inputs
Model 1708: 8 inputs
Model 1716: 16 inputs
Contact closure to ground or 0-5 V or 5-0 V voltage
change
Logic low: <500 Ωor <0.8 Vdc
Logic high: >2.5 kΩor >2.0 Vdc
Protected to +50 VDC
Analog Inputs
Model 1708: 4 inputs
Model 1716: 8 inputs
0 to 5 Vdc analog sensor with 8-bit A/D input
External Outputs
Open Collector Outputs
Model 1708: 8 outputs
Model 1716: 16 outputs
12 Vdc, 100 mA max
Analog Outputs
Model 1716: 4 outputs
0 to 5 Vdc 8-bit D/A

025-9209K 15
OPERATION
GENERAL OPERATION
The Model 1708 and Model 1716 Remote Terminal Units (RTUs) perform two basic tasks:
1. RTUs report changes in input/output to the Controller
2. RTUs respond to commands from the Controller.
Analog and digital inputs may be configured to report changes as they occur without being
polled by the Controller (report by exception). When the RTU recognizes an alarm condition,
it will check to see if the radio channel is busy. If the channel is busy, the RTU will wait for
the channel to clear. If the channel is not busy, the RTU will transmit its data and wait for a
reply from the Controller indicating that the alarm was received. If the RTU has not received
a reply within 15 seconds, it will re-send the packet and wait for a reply. In all cases, the
RTU will continue attempting to complete the transmission sequence until it receives the
correct response.
Each RTU can be configured differently so that the user can customize operation to match
the requirements of the application.

Operation
025-9209K 16
ADDRESSING THE RTU
The RTU is DIP switch addressable from 1 to 255. This is done by using the 8-position DIP
switch labeled SW1. Position #1 is the LSB and position #8 is the MSB. All switches off
corresponds to 0, and all switches on is 255. The count is binary:
#1
→
1
#2
→
2
#3
→
4
#4
→
8
#5
→
16
#6
→
32
#7
→
64
#8
→
128
Each unit on a system must have a different ID in order to respond.
Examples:
1 2 3 4 5 6 7 8
ON
OFF
The configuration above would define this unit as #3: 1 + 2 = 3
1 2 3 4 5 6 7 8
ON
OFF
The configuration above would define this unit as #26: 2 + 8 + 16 = 26
Note
The RTU may be given an address greater than 255 by changing the address
extension through the configuration menus. See “Address Extension” on page 19.

Operation
025-9209K 17
CONFIGURATION
Each RTU will need to be configured prior to its use unless the factory default initialization
values are satisfactory for the application.
To configure an RTU, you will need:
1. A “dumb terminal” or a PC running in the dumb terminal mode. Software programs
such as CrossTalk, Kermit, ZCU, Procomm, and others will provide terminal
emulation on a PC.
2. A cable with a male 9-pin, D-style connector on one end to interface with the RTU
and a connector on the other end to interface with the serial port of your PC or dumb
terminal.
Note
The pins on the RTU are different from those of other serial ports found on printers
and modems. You will need to use the cable provided with the Model 1700
Controller, make up your own cable, or purchase an additional cable from Zetron
for programming the RTUs.
Accessing the RTU Program Mode
1. Connect the serial cable between J2, the 9-pin “D” style connector on the RTU, and the
serial port of the PC or dumb terminal.
2. Connect a 12-volt power supply with power off to the RTU pin 1 of P3 and ground to pin
2 of P3.
3. Make sure your dumb terminal or PC is set at 4800 baud, 8 bit, no parity, 1 stop bit.
4. Turn the 12-volt power supply on. You should see the RTU model number and the
software version displayed on the CRT.
5. Press the space bar three times to enter the Main Menu.

Operation
025-9209K 18
MAIN MENU
Table 2. RTU Main Menu
Menu Selections
Range
Factory Settings
{P}rekey time 0-40 (x0.1 second) 5 (0.5 second)
{C}hannel busy detect Low or High Low (inhibit on logic low)
Channel {B}usy Timeout 0-40 (x0.1 second) 0.5 second
{T}ransceiver type Conventional or Trunking Conventional
Add{r}ess extension 0-65280 0
Co{N}troller Address 0-65535 0
{G}roup Call Address 0-65535 65535
Fai{L} safe setup
{S}tore and Forward
{O}utput Definition
{D}igital Input Definition
{A}nalog Input Definition
{F}actory defaults
E{x}it
To select a menu item, press any key that is within braces {}. Simply pressing ENTER will
redisplay the current menu. If you do not press a key for 30 seconds, the RTU will
automatically exit the menus. You must press the space bar three times to re-access.
Prekey Time
This menu selection allows the user to change the delay between the time PTT is activated
and the time the MSK signaling begins. The default is 500 milliseconds and can range from 0
to 4 seconds in 100 millisecond increments.
For trunked operation, this is the delay from the time a channel-acquired signal is received on
the COR input until the data is sent. If there is no delay required (as should be with trunked
radio), set this to zero.
CAUTION
THE RTU CONTAINS A DATA COLLISION ALGORITHM. TO AVOID
MULTIPLE DATA COLLISIONS, SET THE PREKEY TIME OF EACH RTU
TO THE SAME VALUE!

Operation
025-9209K 19
Channel Busy Detect
To identify when the channel is in use, the carrier must be set to inhibit transmission on
either High (+5 or open) or Low (0 V). The level entered here will PREVENT transmission.
For trunked operation, this is used the same way to inhibit transmission. The proper name for
this parameter should be “channel-acquired indication” when a trunked system is being used.
Channel Busy Timeout
Enter the amount of time (in tenths of seconds) that the channel has to be available before the
RTU can seize the channel. This can prevent the RTU from interrupting a conversation.
For trunked operation, this is used to determine that the TX indicator has stopped flashing
(requesting a channel) and is on long enough to verify that the channel has been acquired.
(This is only if you are using the TX indicator to provide the channel-acquired signal.)
Transceiver Type
This lets the user select whether the RTU is to be used on a conventional or trunking radio
system. The difference being that in trunking, you request a channel by giving PTT and in
conventional, you first look to see if the channel is available before giving PTT.
For trunked operation timing, PTT is pressed for 15 seconds while looking for a channel. If a
channel is acquired prior to the 15 seconds (this is based on the logic indication on the COR
input), the RTU will wait the Prekey delay, send the data, and release PTT. After 15 seconds,
if no channel is available, the RTU will release PTT, wait 30 seconds, and retry.
Address Extension
If you have more than 255 RTUs, enter the number to be added to the dip switch address for
this RTU. It is suggested that you enter a multiple of 256 (256, 512, 768, 1024 etc.) and use
this same number for the rest of the extended address RTUs (up to 255). Record this number
on the sheet provided on the inside top cover of the RTU.
Controller Address
Enter the address of the unit that is to receive alarms from this RTU. The default is the
Controller address 0.
Group Call Address
The Group Call Address allows outputs on several RTUs to be controlled in a single
transmission from the Model 1700 Controller. When the controller sends an output control
command to a group call address, all RTUs in the group will execute the command, but will
not send back a response (in the case of momentary outputs, each RTU makes an exception
report when the output returns to its idle state). Since the RTUs do not send response
messages, the group call address cannot be used to poll inputs or outputs.

Operation
025-9209K 20
All RTUs in a system can have the same group call address, or you can achieve a zoning
effect by assigning one address to one group of RTUs and another address to a different
group. The group call address should not be the same as the RTUs DIP switch address.
Factory Defaults
This menu selection will allow the user to reset all configurable parameters to the defaults set
at the factory including input/output definitions. The user is prompted again to make sure all
definitions really should be cleared.
Exit
This menu selection will take the user out of the configuration mode and reset the RTU to its
“online” mode.
FAIL SAFE SETUP
The fail-safe menu contains several items that determine how the RTUs behave under
abnormal conditions. In many installations, these features will not be needed, so they are
disabled by default.
Table 3. RTU Fail Safe Setup Menu
Menu Selections
Range
Factory Settings
{C}ommunication failure enable 0-10 0 (disabled)
Channel {U}se limits
Time period 0 to 30 minutes 0 (disabled)
# of reports 1 to 999 100
Time out interval 1 to 10 minutes 5 minutes
{E}nable exception reports enabled
{D}isable exception reports
E{X}it
Communication Failure Enable
Selecting this menu item allows you to set the number of times an exception report (power up
alarm, input change alarm, or output change alarm) is sent without acknowledgement from
its controller before the RTU enters the communications fail state.
The range is 1 to 10 times. Entering a “0” (the default value) disables communications failure
detection.
In the failed state, all outputs on the RTU will be turned off - digital outputs go in to the high
impedance state and analog outputs go to 0 volts. The outputs remain off even after commu-
nications are restored; they remain off until turned on again by a command from the
controller.
This manual suits for next models
1
Table of contents
Other ZETRON Touch Terminal manuals
Popular Touch Terminal manuals by other brands

Mitsubishi Electric
Mitsubishi Electric F930GOT-BWD-E user manual
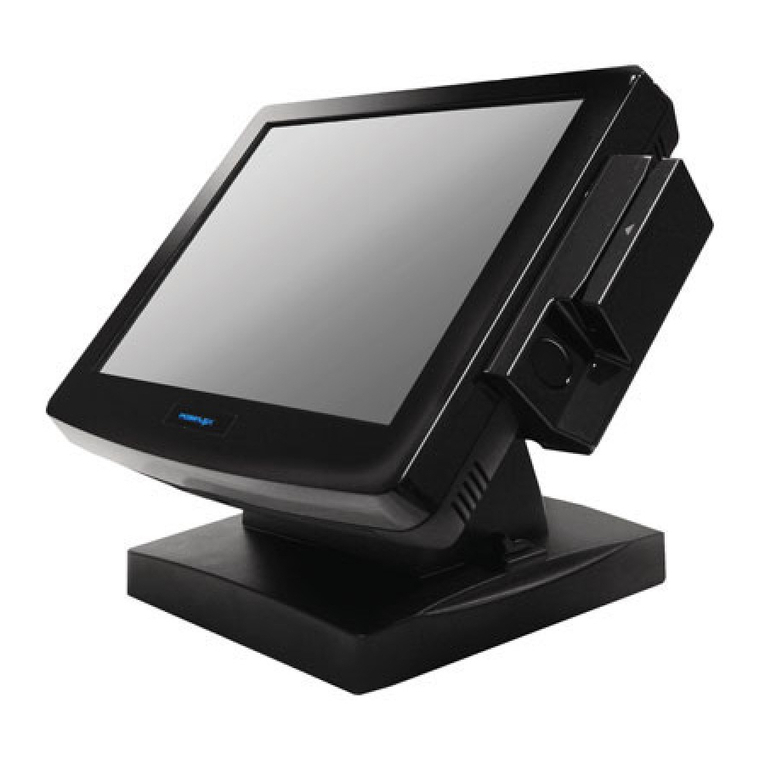
POSIFLEX
POSIFLEX KS-6315 user manual
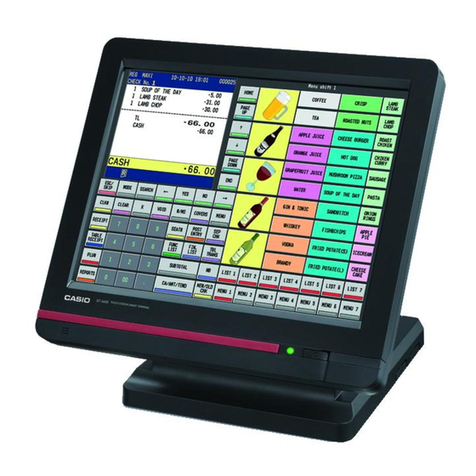
Casio
Casio QT-6600 user manual
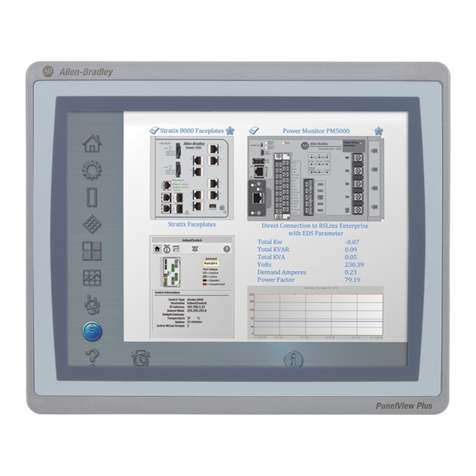
Allen-Bradley
Allen-Bradley PanelView Plus 7 installation instructions
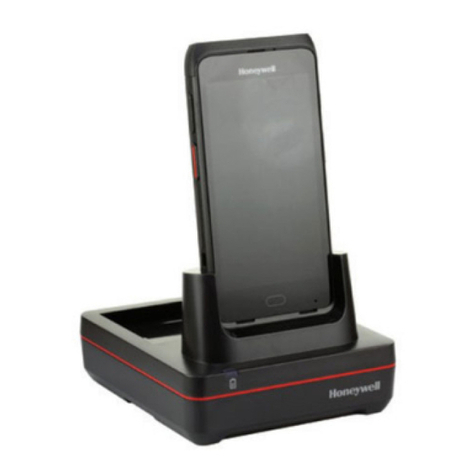
Honeywell
Honeywell CT40 HomeBase quick start guide
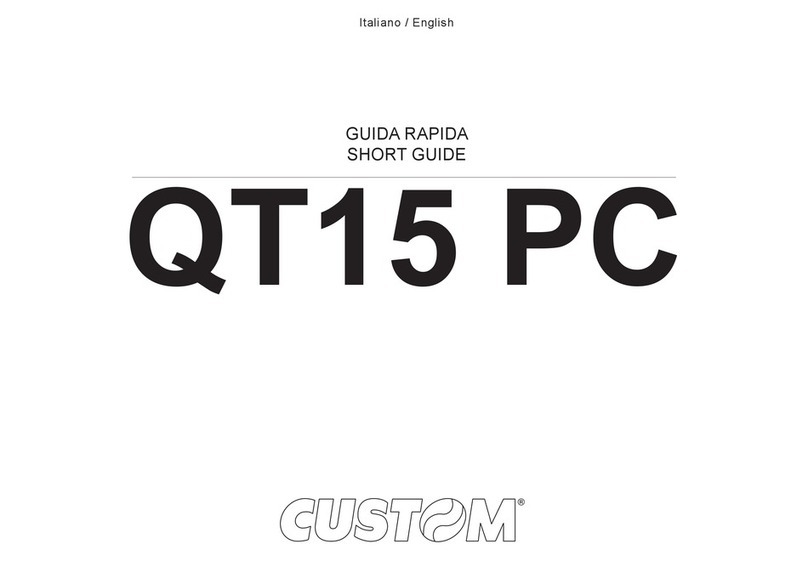
Custom Audio Electronics
Custom Audio Electronics QT15 Short guide