Zmotion ECI3808 User manual


Foreword
The motion controller provides rich interface, and it has excellent motion control performance, which
can meet the expansion requirements of various projects.
This manual is copyrighted by Shenzhen Technology Co., Ltd., without the written permission of the
Zmotion Technology, no person shall reproduce, translate and copy any content in this manual. The
above-mentioned actions will constitute an infringement of the copyright of the company's manual, and
Zmotion will investigate legal responsibility according to law.
For details about the ZMC controller software and the introduction and routine of each command,
please refer to the ZBASIC software manual.
Information contained in this manual is only for reference. Due to improvements in design and
functions and other aspects, Zmotion Technology reserves the final interpretation! Subject to change
without notice!
Pay attention to safety when debugging the machine!
Please be sure to design an effective safety protection device in the machine, and add an error
handling program in the software, otherwise Zmotion has no obligation or responsibility for the loss
caused.
In order to ensure the safe, normal and effective use of the product, please be sure to read this
product manual carefully before installing and using the product.

Safety Statement
⚫This chapter describes the safety precautions required for the correct use of this product. Before
using this product, please read the instructions for use and correctly understand the relevant
information on safety precautions.
⚫This product should be used in an environment that meets the design specifications, otherwise
it may cause equipment damage or personal injury, and malfunctions or component damage
caused by failure to comply with relevant regulations are not within the scope of product quality
assurance.
⚫Zmotion will not take any legal responsibility for personal safety accidents and property losses
caused by failure to comply with the contents of this manual or illegal operation of products.
Safety Level Definition
According to the level, it can be divided into " Danger " and " Caution ". Failure to operate as required
may result in moderate injury, minor injury or equipment damage.
Please keep this guide in a safe place for reading when needed, and be sure to hand this manual to
the end user.
Install
Danger
◆When the controller is disassembled, all external power supplies used by the
system should be disconnected before operation, otherwise it may cause
misoperation or damage to the equipment.
◆It is forbidden to use in the following places: places with dust, oil fume, conductive
dust, corrosive gas and flammable gas; places exposed to high temperature,
condensation, wind and rain; places with vibration and shock. Electric shock, fire
and misuse can cause product damage and deterioration.
Notice
◆Avoid metal shavings and wire ends falling into the hardware circuit board during
installation.
◆After installation, ensure that there are no foreign objects on the hardware circuit
board.
◆When installing, make it tightly and firmly with the mounting frame.

◆Improper installation of the controller may result in misoperation, failure and fire.
Wiring
Danger
◆The specifications and installation methods of the external wiring of the
equipment shall comply with the requirements of local power distribution
regulations.
◆When wiring, all external power supplies used by the system should be
disconnected before operation.
◆When powering on and running after the wiring work is completed, the terminals
attached to the product must be installed.
◆Cable terminals should be well insulated to ensure that the insulation distance
between cables will not be reduced after the cables are installed on the terminal
block.
Notice
◆Avoid metal shavings and wire ends falling into the hardware circuit board during
installation.
◆The cable connection should be carried out correctly on the basis of confirming
the type of the connected interface.
◆It should be confirmed that the cables pressed into the terminals are in good
contact.
◆Do not bundle the control wires and communication cables with the main circuit
or power supply wires, etc., and the distance between the wires should be more
than 100 mm, otherwise noise may cause malfunction.
◆If the controller is not installed properly, it may cause electric shock or equipment
failure or malfunction.

ECI3808 Network Motion Control Card User Manual V1.5
Content
Chapter I Production Information........................................................................................3
1.1. Product Information ..........................................................................................3
1.2. Function Features..............................................................................................3
1.3. System Frame ...................................................................................................4
1.4. Hardware Installment........................................................................................4
Chapter II Product Specification .........................................................................................7
2.1. Basic Specification............................................................................................7
2.2. Order Information..............................................................................................8
2.3. Interface Definition............................................................................................9
2.4. Work Environment ...........................................................................................10
Chapter III Wiring, Communication Configuration ............................................................11
3.1. Power Input Interface......................................................................................11
3.1.1. Power Supply Specification .................................................................11
3.2. CAN Interface ..................................................................................................11
3.2.1. CAN Communication Specification & Wiring .......................................12
3.2.2. Basic Usage Method ............................................................................14
3.3. RS232 Serial Port ............................................................................................15
3.3.1. RS232/RS422 Interface Specification & Wiring...................................15
3.3.2. Basic Usage Method ............................................................................16
3.4. IN Digital Input & High-Speed Latch Port .......................................................17
3.4.1. Digital Input Specification & Wiring .....................................................19
3.4.2. Basic Usage Method ............................................................................20
3.5. OUT: Digital Output & PWM Terminal..............................................................20
3.5.1. Digital Output Specification & Wiring...................................................21
3.5.2. Basic Usage Method ............................................................................23
3.6. AD/DA: Analog Input / Output.........................................................................23

ECI3808 Network Motion Control Card User Manual V1.5
3.6.1. Analog Input / Output Specification & Wiring ......................................24
3.6.2. Basic Usage Method ............................................................................25
3.7. ETHERNET .......................................................................................................25
3.8. ENCODER Auxiliary Encoder............................................................................28
3.9. Axis Interface...................................................................................................29
3.9.1. AXIS Interface Signal Specification & Wiring.......................................30
3.9.2. Basic Usage Method ............................................................................33
Chapter IV Expansion Module ...........................................................................................36
4.1. CAN Bus Expansion Wiring .............................................................................36
4.2. CAN Bus Expansion Resource Mapping .........................................................37
Chapter V Expansion Module ............................................................................................42
5.1. ZDevelop Software Usage...............................................................................42
5.2. PC Upper-Computer Program Application .....................................................47
Chapter VI Run and Maintain ............................................................................................50
6.1. Regular Inspection and Maintenance .............................................................50
6.2. Common Problems..........................................................................................51

ECI3808 Network Motion Control Card User Manual V1.5
Chapter I Production Information
1.1. Product Information
ECI is the abbreviation of the network motion control card model launched by
Zmotion Technology.
ECI3808 supports up to 12 axes of linear interpolation, any circular interpolation,
space arc, helical interpolation, electronic cam, electronic gear, synchronization follow,
virtual axes setting, etc.
ECI300 series economical multi-axis motion control card can be used in those pulse
applications within 12 axes, such as, electronic semiconductor equipment (testing
equipment, assembly equipment, locking equipment, soldering machine), dispensing
equipment, assembly line, etc.
1.2. Function Features
◆Up to 12 axes motion control.
◆Pulse output mode: pulse / direction or dual pulses.
◆AXIS interface supports encoder position measurement, which can be configured as
handwheel input mode.
◆Maximum pulse frequency output of each axis: 10MHZ.
◆256 isolated inputs and 256 isolated outputs can be extended at most through CAN
bus.
◆Axis position limit signal / origin signal port can be configured as any input at will.
◆The maximum output current of general digital outputs can reach 300mA, which can
directly drive some kinds of solenoid valves.

ECI3808 Network Motion Control Card User Manual V1.5
◆Support linear interpolation, any circular interpolation, helical interpolation of 12 axes
at most.
◆Support electronic cam, electronic gear, position latch, synchronization follow, virtual
axis setting, etc.
◆A variety of program encryption methods to protect the intellectual property rights of
customers.
◆Support power failure detection and power failure storage.
1.3. System Frame
1.4. Hardware Installment
ECI3808 motion control card adopts the horizontal installation method of screw
fixing, and each controller should be installed with 6 screws for fastening.

ECI3808 Network Motion Control Card User Manual V1.5
→Unit: mm →Installment Hole Diameter: 5.5mm
Installation
attention
⚫Non-professionals are strictly prohibited to operate. Specifically,
professionals who had been trained related electrical equipment,
or who master electrical knowledge.
⚫Please be sure to read the product instruction manual and safety
precautions carefully before installation.
⚫Before installation, please ensure that the product is powered off.
⚫Do not disassemble the module, otherwise the machine may be
damaged.
⚫Avoid direct sunlight installation.
⚫In order to facilitate ventilation and controller replacement, 2-3cm
should be left between the upper and lower parts of the controller
and the installation environment and surrounding components.
⚫Considering the convenient operation and maintenance of the
controller, please do not install the controller in the following
places:
a) places where the surrounding ambient temperature exceeds
the range of -20°C-60°C

ECI3808 Network Motion Control Card User Manual V1.5
b) places where the ambient humidity exceeds the range of 10%-
95% (non-condensing)
c) places with corrosive gases and flammable gases
d) places with many conductive powders such as dust and iron
powder, oil mist, salt, and organic solvents

ECI3808 Network Motion Control Card User Manual V1.5
Chapter II Product Specification
2.1. Basic Specification
Item
Description
Model
ECI3808
Basic Axes
8
Max Extended Axes
12
Basic Axes Type
Pulse/encoder (there is one specialized auxiliary
encoder, the auxiliary encoder axis No. is 8)
Digital IO
40 inputs and 16 outputs.
Max Extended IO
256 inputs and 256 outputs
AD/DA
4 general ADs and 2 general DAs (0-5V)
Max Extended AD/DA
128 ADs and 64 DAs
Pulse Bit
32
Encoder Bit
32
Speed Acceleration Bit
32
Pulse Max Frequency
10MHz
Motion Axis Buffer
128
Array Space
1600
Program Space
4KByte
Flash Space
128KByte
Power Supply Input
24V DC input
Communication Interfaces
RS232, EtherNet, CAN
Dimensions
292mm*188mm

ECI3808 Network Motion Control Card User Manual V1.5
2.2. Order Information
Model
Description
ECI3600
6 axes, point to point, electronic cam, doesn’t support
interpolation.
ECI3602
6 axes, point to point, electronic cam, linear interpolation.
ECI3606
6 axes, point to point, electronic cam, linear interpolation, circular
interpolation.
ECI3606
6 axes, point to point, electronic cam, linear interpolation, circular
interpolation, continuous interpolation, robotic arm.
ECI3800
8 axes, point to point, electronic cam, doesn’t support
interpolation.
ECI3802
8 axes, point to point, electronic cam, linear interpolation.
ECI3806
8 axes, point to point, electronic cam, linear interpolation, circular
interpolation.
ECI3828
8 axes, point to point, electronic cam, linear interpolation, circular
interpolation, continuous interpolation, robotic arm.

ECI3808 Network Motion Control Card User Manual V1.5
2.3. Interface Definition
→Interface Description
Mark
Interface
Number
Description
POW
Status Indication
Led
1
Power indicator: it lights when power is conducted.
RUN
1
Run indicator: it lights when runs normally
ALM
1
Error indicator: it lights when runs abnormally
RS232
RS232 serial port
1
Use MODBUS_RTU protocol
ETHERNET
Net port
1
Use MODBUS_TCP protocol, expand Ethernet

ECI3808 Network Motion Control Card User Manual V1.5
through interchanger, the number of net port
channels can be checked through “?*port”, default IP
address id 192.168.0.11
E+24V
Main power
1
24V DC power supplies for controller
CAN
CAN bus interface
1
Connect CAN expansion module and CAN equipment
of other standards
IN
Digital IO input
40
Leakage type, power supplied by 24V, IN0-1 support
latch function.
OUT
Digital IO output
16
Leakage type, power supplied by 24V, OUT14-15
support PWM function.
AD/DA
Analog
input/output
1
Resolution: 12 bits, 0-5V
ENCODER
Auxiliary encoder
1
Include differential encoder input.
AXIS
Pulse axis
8
It includes differential pulse output and differential
encoder input
2.4. Work Environment
Item
Parameters
Work Temperature
-10℃-55℃
Work relative Humidity
10%-95% non-condensing
Storage Temperature
-40℃~80℃(not frozen)
Storage Humidity
Below 90%RH (no frost)
vibration
Frequency
5-150Hz
Displacement
3.5mm(directly install)(<9Hz)
Acceleration
1g(directly install)(>9Hz)
Direction
3 axial direction
Shock (collide)
15g, 11ms, half sinusoid, 3 axial direction
Degree of Protection
IP20

ECI3808 Network Motion Control Card User Manual V1.5
Chapter III Wiring, Communication
Configuration
3.1. Power Input Interface
→Terminal Definition:
Terminal
Name
Type
Function
E+24V
Input
Input for power supply 24V
OGND
Input
Power ground
FG
Grounding
Shield/Protection
3.1.1. Power Supply Specification
→Specification
Item
Description
Voltage
DC24V (-10%~10%)
Current to open
≤0.8A
Current to work
≤0.7A
Anti-reverse connection
Valid
Overcurrent Protection
Valid
3.2. CAN Interface
This interface adopts 5Pin screw-type pluggable terminal with a spacing of 5.08mm.
CAN interface of this controller uses standard CAN communication protocol, and
expansion modules or other standard CAN devices can be connected.

ECI3808 Network Motion Control Card User Manual V1.5
→Terminal Definition
Terminal
Name
Function
NC
Spare
CANH
CAN communication H
EARTH
Case protection
CANL
CAN communication L
GND
Negative of DC input
3.2.1. CAN Communication Specification & Wiring
→Specification
Item
CAN
Max Communication Rate (bps)
1M
Terminal Resistor
120Ω
Topology
Daisy chain connection structure
The number of nodes can be
extended
Up to 16
Communication Distance
Longer communication distance, lower
communication rate, max 100m is recommended.
→Wiring Reference
Connect the CANL and CANH of the standard CAN module to the CANL and CANH of
the other side correspondingly. And public ends of the CAN bus communication both
parties are connected together. In CAN bus left and right sides, connect a 120Ωresistor
respectively (please see below graphic).

ECI3808 Network Motion Control Card User Manual V1.5
→Wiring Notes:
⚫As above, the daisy chain topology is used for wiring (the star topology structure
cannot be used). When the use environment is ideal and there are no many nodes,
the branch structure also can be used.
⚫The communication interface of ECI3808 adopts external 24V power supply, please
pay attention to connect other controllers or HMI.
⚫Please connect a 120Ω terminal resistor in parallel to each end of the CAN bus for
matching the circuit impedance and ensuring communication stability.
⚫Please be sure to connect the public ends of each node on the CAN bus to prevent
the CAN chip from burning out.
⚫Please use STP (Shielded Twisted Pair), especially in bad environments, and make
sure the shielding layer is fully grounded.
⚫When on-site wiring, pay attention to make the distance between strong current and
weak current, it is recommended for the distance to be more than 20cm.
⚫It should be noted that the equipment grounding (chassis) on the entire line must be
good, and the grounding of the chassis should be connected to the standard factory
ground pile.

ECI3808 Network Motion Control Card User Manual V1.5
→Cable Requirements:
Shielded Twisted Pair, and the shielded cable is grounded.
3.2.2. Basic Usage Method
(1) Please follow the above wiring instructions to wiring correctly.
(2) After powered on, please use ETHERNET or RS232 (default parameter, which can be
connected directly) to connect to ZDevelop.
(3) Please use the "CANIO_ADDRESS" command to set the master's "address" and
"speed" according to the needs, and use the "CANIO_ENABLE" command to enable or
disable the internal CAN master function, or through "ZDevelop/Controller/State the
Controller/Communication Info” to view the CAN status intuitively, and refer to the
“ZBasic Programming Manual” for details.
(4) Correctly set the "address" and "speed" of the slave station expansion module
according to the manual of the slave station.

ECI3808 Network Motion Control Card User Manual V1.5
(5) After all the settings are completed, restart the power supply of all stations to
establish communication.
(6) Note that the "speed" settings of each node on the CAN bus must be consistent, and
the "address" settings cannot cause conflicts, otherwise the "ALM" alarm light will be
on, and the communication establishment will fail or the communication will be
disordered.
3.3. RS232 Serial Port
RS232 is in one standard DB9 male socket and supports MODBUS_RTU protocol and
custom communication.
→Interface Definition
Terminal
PIN
Name
Type
Function
1,4,6,7,8
NC
Spare
Reserved
2
RXD
Input
RS232 signal receive
3
TXD
Output
RS232 signal send
5
GND
Output
Negative pole of 5V power output
and public end
9
E5V
Output
Positive pole of 5V power, max is
300mA.
3.3.1. RS232/RS422 Interface Specification & Wiring
→Specification:
Item
RS232
Max Communication Rate
115200 (bps)
Terminal Resistor
No
Topology Structure
Connect correspondingly (1 to 1)

ECI3808 Network Motion Control Card User Manual V1.5
The number of nodes can
be extended
1
Communication Distance
The Longer communication distance is, the lower
communication rate is, maximum 10m is recommended.
→Wiring Reference
→Wiring Notes:
⚫The wiring of RS232 is as above, it needs to cross-wiring for sending and receiving
signals, and it is recommended to use a double-female head cross line when
connecting to a computer.
⚫Please be sure to connect the public ends of each communication node to prevent
the communication chip from burning out.
⚫Please use STP, especially in bad environments, and make sure the shielding layer is
fully grounded.
3.3.2. Basic Usage Method
(1) Please follow the above wiring instructions to wiring correctly.
(2) After powered on, please use any ETHERNET or RS232 (there is default parameter,
which can be connected directly) to connect to ZDevelop.
(3) Please use the "ADDRESS" and "SETCOM" commands to set and view the protocol
station number and configured parameters, see "ZBasic Programming Manual" for
details.
Table of contents
Other Zmotion Network Hardware manuals
Popular Network Hardware manuals by other brands
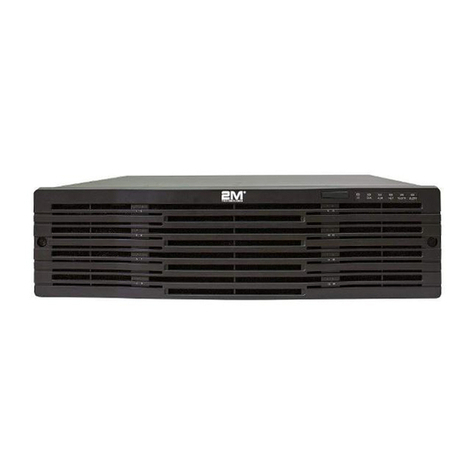
2M Technology
2M Technology 2MN-9004-P user manual
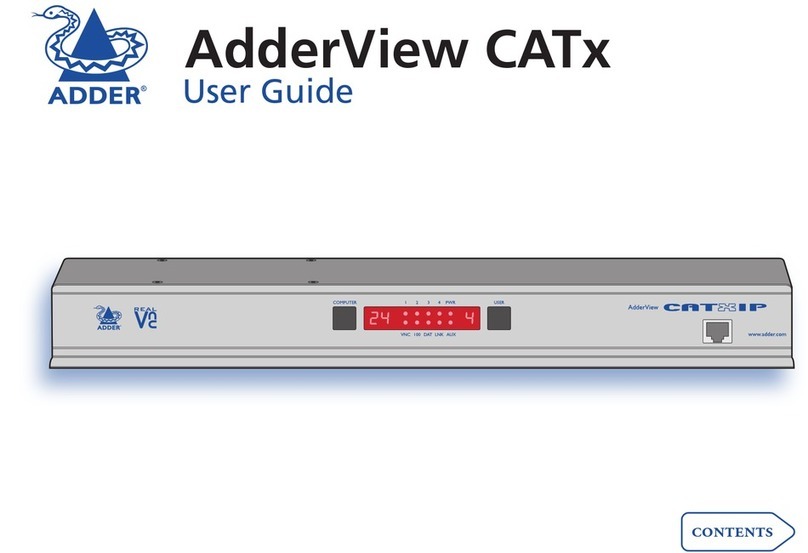
ADDER
ADDER AdderView CATx AVX4016 user guide

Seyeon Technology
Seyeon Technology FlexWATCH 5440 user guide

Seagate
Seagate Exos AP 4U100 Installation and maintenance guide
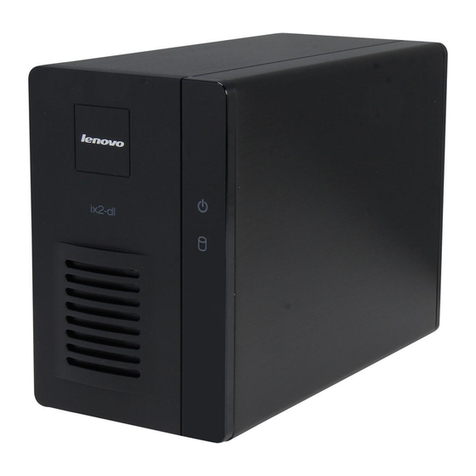
Lenovo
Lenovo Iomega®Iomega ix2-300d Product specifications
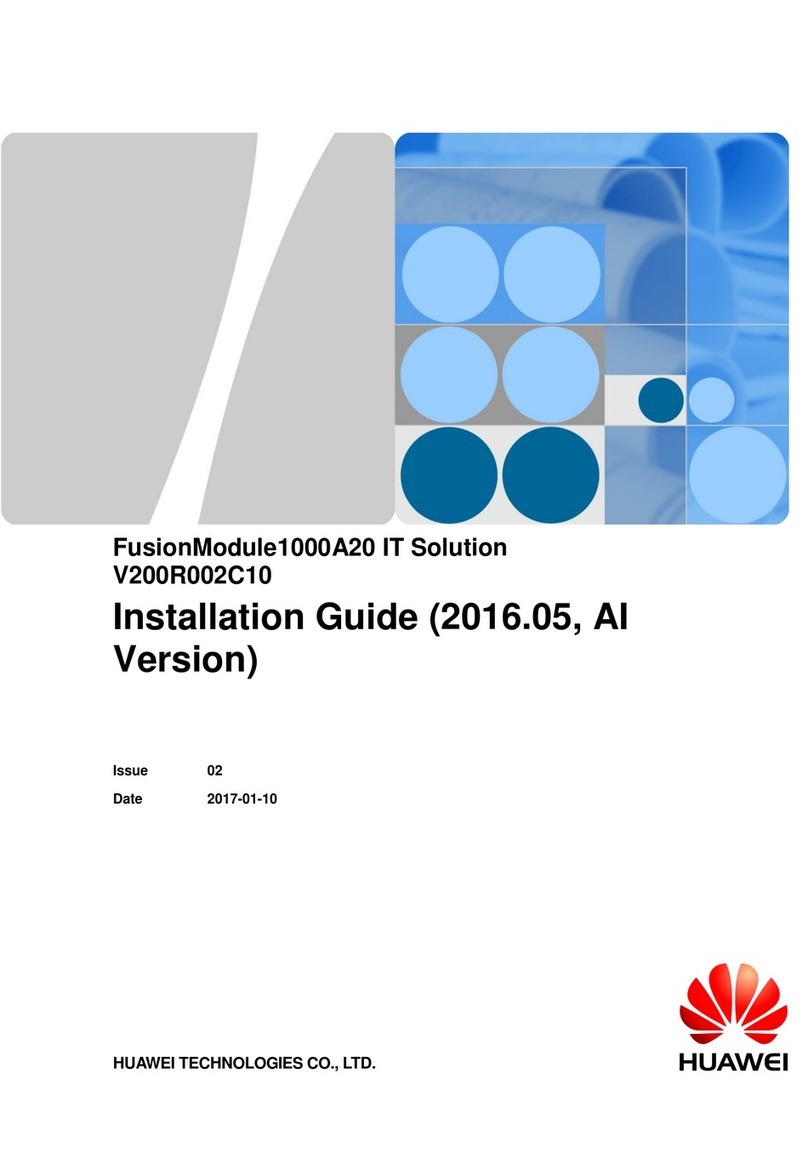
Huawei
Huawei FusionModule1000A20 installation guide