Zonex System 2000 User manual

Zonex Systems
System 2000
2-20 Zone Auto Changeover
System 1000
2-7 Zone Manual Changeover
Design & Installation for
Part #101ASIM
Rev. September 2003

TABLE OF CONTENTS
System 2000
System Operation.................................................................................................................................................................1
Components.........................................................................................................................................................................1
Component Selection Guide .................................................................................................................................................2
System 2000 System Controllers...........................................................................................................................................3
Gas/Electric (101ASSB).............................................................................................................................................3-5
Heat Pump (101AACBHP) .........................................................................................................................................5-7
Startup.................................................................................................................................................................................8
System 1000
System Operation.................................................................................................................................................................9
Components.........................................................................................................................................................................9
Component Selection Guide ...............................................................................................................................................10
System 1000 Switching Centers
Gas/Electric (SYGE)..............................................................................................................................................11, 12
Heat Pump (SYHPA)..............................................................................................................................................12-14
Startup...............................................................................................................................................................................15
Zone Thermostats ...........................................................................................................................................................16, 17
Remote Sensors .................................................................................................................................................................17
Zone Dampers .......................................................................................................................................................................18
Round Zone Dampers..................................................................................................................................................18, 19
Rectangular Zone Dampers..........................................................................................................................................20, 21
Sizing Zone Dampers .........................................................................................................................................................22
Wiring Zone Dampers........................................................................................................................................................22
Damper Installation Notes..................................................................................................................................................22
Paralleling Zone Dampers..................................................................................................................................................23
Bypass Dampers ....................................................................................................................................................................23
Barometric ..................................................................................................................................................................23, 24
Electronic ....................................................................................................................................................................25, 26
Bypass Position Indicators ..........................................................................................................................................26
Paralleling Bypass Dampers........................................................................................................................................26
Bypass Damper Static Pressure Controller .......................................................................................................................27
Capacity Controllers .............................................................................................................................................................28
101CAPGE....................................................................................................................................................................29, 30
TRLAT ..........................................................................................................................................................................31, 32
TRFPC................................................................................................................................................................................32
SYCAP ..........................................................................................................................................................................33, 34
101ALAS ............................................................................................................................................................................35
CAPL-2.........................................................................................................................................................................36, 37
CAPL-4.........................................................................................................................................................................38, 39
Capacity Controllers Installation.........................................................................................................................................40
Capacity Controllers, Setpoints, Calibration........................................................................................................................41
Important Diagrams
Five Wire Link....................................................................................................................................................................41
Transformer/Fuse Sizing ....................................................................................................................................................42
Application Schematics ................................................................................................................................................42, 43

1
SYSTEM 2000
CONCEPTUAL
DRAWING ONLY
Refer to System 2000
Controller Section for
Wiring Information
System 2000
Zonex Systems Supplied Components
System Controllers ..............................................................Pages 3- 7
Zone Thermostats ...............................................................Pages 16-17
Zone Dampers ....................................................................Pages 18-23
Bypass Dampers .................................................................Pages 23-27
Capacity Controllers............................................................Pages 28-41
System 2000
Field Supplied Components
Thermostat Wire........................................................................Page 41
24V Transformers and Fuse .......................................................Page 42
SYSTEM OPERATION
The System Controller communicates with the Zone Dampers and Zone
Thermostats via a patented Five-Wire Link. The Five-Wire Link is daisy
chained from damper to damper using standard five-conductor
thermostat wire. The System Controller polls every zone every 120 sec-
onds and registers the number of thermostats calling for heating and
cooling. The System Controller then runs the HVAC/Heat Pump unit in the
mode with the most calls. If the majority changes, the System Controller
will automatically change over to the new mode of operation.
The Zone Dampers are open for the zones calling and closed for the
zones not calling for the operating mode. When the HVAC/Heat Pump unit
is not running, all Zone Dampers are open to provide ventilation if the
indoor blower fan is running continuously.
While the unit is running, the Capacity Controller monitors the leaving air
temperature from the unit and will cycle the HVAC/Heat Pump unit off
and on to maintain the air temperature within a preset range to eliminate
coil freeze-up and premature heat exchanger failure.
The System 2000 is a light commercial/residential zone control system.
It enables a single HVAC unit to be controlled by up to twenty zone (room)
thermostats. System 2000 is a vote based, auto changeover system. The
system operates on a first call, first served majority wins on changeover
strategy. To provide economical, effective and simplified remote control
and monitoring capability of one or more System 2000 zone control sys-
tems, the ZonexCommander may be used to manage up to 80 thermostat
schedules. The ZonexCommander is a Window’s based thermal manage-
ment system, which can integrate gas/electric and heat pump zone sys-
tems to include stand alone HVAC systems. For modulating communi-
cating control, use the ZonexCommander (Plus).

2
SYSTEM 2000 COMPONENT SELECTION GUIDE
Auto Changeover for 2 to 20 Zones
5 TONS AND UNDER OVER 5 TONS
BYPASS DAMPERS
ZONE DAMPERS
ZONE THERMOSTATS
❶ Some Heat Pumps utilize Gas/Electric thermostats, typically units over 7.5 tons.
For this application, use the Gas/Electric parts selection and field modify the capacity
control heat cutoff setpoint to 118° F.
❷ Use heavy duty rectangular dampers on systems of 7.5 tons or larger
COMPLETE SYSTEM
Barometric Bypass Damper
Round (101ABBD size)
Rectangular RBB W x H
Electronic Bypass Damper
Round (STMPD size)
Rectangular (STCD W x H)
Static Pressure Controller (101ASPC)
24V, 40VA Independent Transformer
for bypass (Field Supplied)
5 TONS AND UNDER OVER 5 TONS
Low Pressure Dampers Medium Pressure Dampers
Round (101ARZD size) up to .5” SP Round (101AMPD size) up to 1.75” SP
Rectangular (101EC W x H) up to .5” SP Rectangular (101MRTD W x H) up to 1” SP ❷
Heavy Duty Rectangular (101CD W x H) to 1.75” SP
12 X (Number of Dampers) = VA for the 6 X (Number of Dampers) =VA for the
24V System Transformer (Field Supplied) 24V System Transformer (Field Supplied)
Communicating Digital Programmable Auxiliary Heat
(DIGICOM) (101DIGI) (101PROG) for reheat/baseboard
(101DIGITS)
START
Optional
Outdoor T-Stat
(field supplied)
GAS ELECTRIC
System Controller
(101ASSB)
Capacity Controller
Single Stage(TRLAT) or (101CAPGE)
2-Stage (CAPL-2)
3- or 4-Stage (CAPL-4)
HEAT PUMP ❶
System Controller
2 Stage Heat/Cool with Auxiliary Heat
(101AACBHP)
Capacity Controller
101ALAS (Included with Controller)
COMMAND CENTER
(101CEC Communication Package,
one per 20 thermostats)

3
OVERVIEW
The 101ASSB is a Gas/Electric System Controller that will control up to
20 zones for the System 2000 zoning system. The System Controller
selects the mode of operation based on a majority calls basis. It is
used in conjunction with a Capacity Controller. The Capacity Controller
controls the HVAC system staging. Capacity Controllers are available for
one, two, three and four stage systems. Refer to Capacity Controller
section (pg. 28) for further information.
The 101ASSB is a vote based, auto changeover System Controller. It polls
each zone every 120 seconds, registering heat or cool calls. Majority
wins, and the Controller operates the HVAC system in that mode until all
calls are satisfied or it detects a majority of offsetting calls.
The System Controller should be located in an accessible, conditioned
space. The Controller does not sense temperature; it simply receives data
from the zone thermostats. The Controller communicates to the zone
dampers and thermostats through a five-wire link. These five wires are
daisy chained to each zone damper. This simple patented wiring process
eliminates home run wiring.
OPERATION
When heating or cooling calls are sent to the System Controller, the
controller will treat these calls as votes.
COOL CALLS – If the majority of calls are for cooling, the System
Controller will turn on the compressor and fan. The air conditioner will
continue to operate until all cooling calls are satisfied or the majority
changes to heating.
HEAT CALLS – If the majority of calls are for heat, the System Controller
will turn on the heat. If the fan switch is set for auto, the bonnet control
or a delay relay will start the fan. When all heating calls are satisfied or
the majority changes to cooling, the gas valve will turn off.
CHANGEOVER – If the system is running in one mode and the majority
of calls changes to the other mode, a timer will start. The System Con-
troller will give the current operating mode another 4 minutes to try and
satisfy the zone(s). It will then go into a 4-minute purge cycle before
switching modes.
PURGE MODE – When a heat or cool call is satisfied or before chang-
ing modes, the System Controller will go into a 4-minute purge cycle.
The compressor or gas valve will turn off and the indoor blower will con-
tinue to run. The dampers of any zone thermostat not satisfied in the
previous mode will remain open. This allows the supply air to adjust
to room temperature before changeover or ventilation while providing a
time delay to prevent short cycling.
VENTILATION – When no zones are calling, all zone dampers open after
the purge mode. This permits ventilation in all zones if the blower fan is
on continuously.
Dimensions 7” x 7” x 2.5”
SYSTEM 2000 CONTROLLERS
Heat Pump System Controller
with LAS Sensor
(101AACBHP)
Gas Electric System Controller
(101ASSB)
SYSTEM 2000 CONTROLLERS – GAS/ELECTRIC 101ASSB

4
The 101ASSB System Controller consists of the following:
A. TB1 (Terminal Block 1): Wires to daisy chain, transformer
and time clock.
TC1, TC2 – Time clock switch terminals. Used for Select-Temp
system only.
S – Nite call. Used for Select-Temp system only.
Y – Cool call.
W – Heat Call.
Rd – Damper close signal.
B – 24V AC common. Same terminal as TR2.
G – 24V AC hot. Same terminal as TR1 when PWR switch ON.
TR2 – 24V AC common.
TR1 – 24V AC hot.
B. Jumpers J1 and J2:
J1 – Not used.
J2 – Not used for System 2000. Used for Select-Temp system
only.
C. Microcontroller: Responsible for zone communication, activation
and control of outputs based upon zone demand and leaving air
temperature. Occasionally software upgrades may become avail-
able. If so, the 101ASSB software can be field upgraded by chang-
ing this microcontroller.
D. Off board fuse: One amp. Protects Y and W terminals of TB1.
E. Status lights: Refer to status light section for details.
F. TB2 (Terminal Block 2): Wires to Capacity Controller and
HVAC unit.
R – HVAC unit 24V AC power
W1 – Heat enable
Y1 – Cool enable
G – Indoor blower fan enable
G. FAN switch:
AUTO – Turns on indoor blower fan when unit is running in cool
mode.
ON – Indoor blower fan runs continuously.
H. COOL and HEAT mode switches:
AUTO – Accepts calls from thermostats.
OFF – Ignores calls.
I. Power switch. When on, applies 24V AC power to G of TB1.
J. On board fuse. One amp. Protects 101ASSB board only.
DELAY On when HVAC unit energized. Flashing when in purge/delay mode.
HEAT* On in heat mode.
COOL* On in cool mode.
DAMPER When on, dampers of zones not calling for present mode are closed.
UNIT On when HVAC unit energized.
RW1Y1G
TB2
ON
OFF
OFF
OFF
AUTO
ON
AUTO
TB1
TR2 TR1
1
TC2 TC1
1
SYWRdBG
A
J
C
B
D
E
I
H
G
F
101ASSB
DELAY
HEAT
COOL
DAMPER
UNIT
J1
J2
SET BACK
FAN HEAT COOL PWR
Status Lights Mode Function
Delay Heat* Cool* Damper Unit
01000Heat, no calls HVAC unit off. All dampers open.
00100Cool, no calls HVAC unit off. All dampers open.
11011Heat call Heat energized. Heat calling zone dampers open.
10111Cool call AC energized. Cool calling zone dampers open.
FLASH 1010Purge heat Blower fan on, HVAC unit off. Heat calling zone dampers open.
FLASH 0110Purge cool Blower fan on, HVAC unit off. Cool calling zone dampers open.
*MODE LIGHTS TOGGLE BETWEEN HEAT AND COOL EVERY 120 SECONDS. THIS INDICATES THE SYSTEM CONTROLLER IS POLLING FOR HEAT OR COOL CALLS.
SYSTEM 2000 CONTROLLERS – GAS/ELECTRIC 101ASSB
STATUS LIGHTS
COMPONENTS

5
SYSTEM 2000 CONTROLLERS - GAS/ELECTRIC 101ASSB
Fused
24V AC
Damper
Transformer
1
7
6
TR2 TR1
SY WRdB G
TB1
DAISY CHAIN
UP TO 20
ZONES
101ASSB
System Controller
TC2 TC1
3
2
ZONE
DAMPER
WY G RdBW2
WY R C RCW2 MC RO
Open
Close
DAMPER MOTORS
TB2
TB1
WY R C
ZONE
THERMOSTAT
DAMPER RELAY
BOARD (P/N 101ARLY)
W1 Y1RG
TB2
TO CAPACITY CONTROLLER
AND HVAC UNIT (PG 28)
4
5
WIRING
If the heater does not turn on the
blower fan, a blower fan relay must be
installed. See page 43.
24V damper transformer. Requires in-line
fuse. See table on page 42 for sizing trans-
former and fuse.
Refer to page 41 for Five Wire Link wire
sizing.
C terminal for hard wired electronic
thermostats only.
Open motor not utilized on low pressure
(spring open) dampers.
If using more than one damper per
thermostat, refer to Slaving Zone
Dampers section, page 23 and 44.
Do not remove factory installed jumper
between TC1 and TC2. TC1 and TC2 are
used for Select-Temp Zoning System only.
When using the 101ASSB controller in a
heat pump application which utilizes G/E
terminals, a fan relay must be installed,
see page 43.
1
2
3
4
5
6
7
8
Overview
The 101AACBHP Heat Pump Controller greatly simplifies coordination of
single stage or two stage Heat Pumps with dampered zone systems. The
Controller communicates to the zone dampers through a five wire link.
These five wires are daisy chained to each zone damper. This simple
patented wiring process eliminates home run wiring. The 101AACBHP
has a built-in capacity control system which uses an LAS (included with
the Controller) for capacity control. Refer to the section on Capacity
Control LAS for more information.
Operation
The Controller operates the Heat Pump using signals from each zone
thermostat in the system. When heating or cooling calls are sent to the
controller, it treats these calls as votes. If the majority of calls are for
cooling, the Controller will operate in the cool mode. The Heat Pump
will continue to operate in the cool mode until the majority of calls shift
to heating or all cooling calls are satisfied. If the majority of calls are for
heating, the Controller will operate in the heat mode. The Heat Pump
will continue to operate in the heat mode until the majority of calls shift
to cooling or all heating calls are satisfied.
*The reversing valve is energized depending on the O/B
jumper setting.
Second stage operation is based on the leaving air temperature of the unit.
The LAS reports the discharge temperature to the Controller. Three
minutes after initiating cooling, the Controller checks the LAS. If the
discharge temperature is above 52 degrees, the second stage is turned
on. Three minutes after initiating heating, the Controller checks the
LAS. If the discharge temperature is below 114 degrees, the second
stage is turned on.
The Heat Pump Controller is also set up to operate electric strip heat in
the Heat Pump. The Controller monitors the air temperature leaving the
Heat Pump coil. When there is a call for heat and the air leaving the coil
is not above 85 degrees, the electric strip will turn on after an eight minute
delay. This operation can be modified, if desired by an outdoor thermostat.
The Heat Pump Controller simplifies system wiring. The Controller
terminals connect directly to the Heat Pump terminal strip. (Heat Pump
thermostats are not used for this system). Relays, timers and other
miscellaneous controls are not required.
SYSTEM 2000 CONTROLLERS – HEAT PUMP 101AACBHP

6
OPERATION (Continued)
The 101AACBHP Zonex Systems SYSTEM 2000 Heat Pump controller
has a series of lights which indicate different operations. These are
labeled “Heat,” “Cool,” “Damper,” “Pump,” “Rev. Valve,” “Y1 Cool”, “Y2
Cool,” “Y1 Heat” and “Y2 Heat.” The “Heat” and “Cool” lights
indicate, when illuminated, the present mode of operation. These lights
will momentarily toggle to the other mode every 120 seconds when
polling. Polling is when the controller checks to see how many heat and
cool calls are being made. If there are no calls, the “Heat” or “Cool”
light will be on based on the last operating mode. The “Damper” light
indicates that a thermostat is calling and that power is being supplied to
the damper motors. The “Pump” light indicates that the first stage pump
is operating. The “Rev. Valve” light indicates that the reversing valve is
activated, or when it flashes, that a time delay is active. The “Y1” and
“Y2” Cool and Heat lights are part of the Capacity control function
included on the Heat Pump Controller. The Y2 Heat or Cool LED, when
illuminated, indicates the Y2 compressor has cycled OFF, because the
capacity control setpoint has been exceeded. When Y1 and Y2 heat or
Cool LEDs are both illuminated, the controller will initiate a 4-minute
temperature cut out, with both stages cycling off.
When power is first turned on, if there are no calls for cooling or
heating, the “Heat” light will be the only light illuminated, with the
exception of the “Rev. Valve” light. It will also be on if jumper J1 is
removed (“B” operation). When there is a cooling or heating call, the
“Damper” and “Heat” or “Cool” lights will turn on.
When the “Rev. Valve” light is not indicating a time delay by flashing, it
will stay illuminated only when the reversing valve is operated.
HEAT – Reversing valve “O” Mode – When the controller receives
an initial or consecutive call for Heat, the Rev Valve LED will flash; the
Heat, Damper and Pump LEDs will illuminate. The first stage heat will
energize on Y1, and the Rev Valve LED will continue to flash for at least
4 minutes. After 4 minutes from Y1, if the supply temperature is 95° or
less, Y2 will energize and the Rev Valve LED will go OFF (Heat “B” mode
will change the flashing Rev Valve LED to ON when Y2 energizes). The
auxiliary heat will energize 4 minutes after Y2 and when the supply air
temperature is 85° or less.
COOL – Reversing Valve “O” Mode – When the controller receives
an initial or consecutive call for Cool, the Rev Valve LED will flash; the
Cool, Damper and Pump LEDs will illuminate. The first stage cool will
energize on Y1 and O/B with the Rev Valve LED flashing for 8 minutes.
After 8 minutes from Y1, if the supply air temperature is 60° or higher,
Y2 second stage of cooling will energize. The Rev Valve LED will change
from flashing to steady ON. (Cool “B” mode for Rev Valve LED will change
from flashing to OFF after Y2 energizes.)
AUTO CHANGEOVER – If an existing mode is overridden by an opposite
majority, the existing call will remain in operation for 4 minutes, and
then the controller will go into a 2 minute purge with the existing
dampers staying open. After the purge cycle has timed out, the system
blower cycles OFF (when in the auto mode). The controller goes into a
2 to 4 minute delay, switching to the opposite mode, with the dampers
making the opposite call opening. Y1 and Y2 are not energized during
this delay. After this final delay times out, the controller energizes Y1 in
the opposite mode.
If all zones satisfy, the “Pump” and “Damper” lights will go out. The
“Heat” or “Cool” lights will be on based on the last mode of operation.
If your system includes auxiliary heat, it will be activated by the “W”
terminal on the SYSTEM 2000’s Heat Pump Controller. Auxiliary heat
will be activated when the following conditions are met. The “Heat” and
“Damper” lights are on indicating a heat call; the “Pump” light is on
and the “Rev. Valve” light is not flashing, indicating that first and second
stage are activated; four minutes after the “Rev. Valve” light stops
flashing the auxiliary heat will be activated if the leaving air temperature
is below the Electric Heat setpoint (factory set at 85 degrees). The time
delay before bringing on the auxiliary heat gives the second stage time
to raise the leaving air temperature over 85 degrees. Even if the system
is single stage, the controller will still delay the electric heat until after
the second stage time delay is satisfied.
The reversing valve is controlled by the “O/BL” terminal. This terminal
should be connected to the Heat Pumps terminal strip according to the
unit manufacturers recommendations. Jumper J1 on the SYSTEM 2000
Heat Pump board needs to be adjusted to operate with the different
manufacturers designs. The Heat Pump board is shipped from our
factory ready to operate a heat pump unit which requires the “O” wire
to energize the reversing valve in cooling. If the reversing valve needs to
be activated for the “BL” terminal, jumper J1 needs to be removed from
the Controller board. Refer to the Heat Pump Controller drawing on the
previous page for the location of jumper “J1”. Remove the jumper from
the board to activate the reversing valve using the “BL” terminal.
Warning: For heat pumps using standard gas/electric thermostats, do not use the 101AACBHP System Controller. Instead, use the
101ASSB System Controller and the CAPL-2 Capacity Controller.
SYSTEM 2000 CONTROLLERS – HEAT PUMP 101AACBHP

7
SYSTEM 2000 CONTROLLERS – HEAT PUMP 101AACBHP
POWER UP, NO CALLS: CALL (HEAT/COOL): 1ST STAGE 2ND STAGE AUX. HEAT
DELAY IN MINUTES
STATUS LIGHTS: STATUS LIGHTS: 04* 8
DAMPER OFF DAMPER ON ON ON
REV. VALVE NOTE 1 REV. VALVE FLASH NOTE 1 NOTE 1
HEAT* ON HEAT ON FOR HEAT ON FOR HEAT ON FOR HEAT
COOL* OFF COOL ON FOR COOL ON FOR COOL ON FOR COOL
PUMP OFF PUMP ON ON ON
TB2: TB2:
Y1 OFF Y1 ON ON ON
Y2 OFF Y2 OFF ON ON
GOFF GON ON ON
WOFF WOFF OFF NOTE 2
O/BL NOTE 1 O/BL NOTE 1 NOTE 1 NOTE 1
MODE CHANGE: 1ST STAGE 2ND STAGE AUX. HEAT
STATUS LIGHTS: O 4 8 10 12
DAMPER ON ON ON ON ON
REV. VALVE FLASH FLASH NOTE 1 NOTE 1
HEAT* ON FOR HEAT ON FOR HEAT ON FOR HEAT ON FOR HEAT
COOL* ON FOR COOL ON FOR COOL ON FOR COOL ON FOR COOL
PUMP OFF ON ON ON
TB2:
Y1 OFF ON ON ON
Y2 OFF OFF ON ON
GOFF ON ON ON
WOFF OFF OFF NOTE 2
O/BL NOTE 1 NOTE 1 NOTE 1 NOTE 1
DELAY IN MINUTES
NOTE 1: On if: a) In cool mode and reversing valve set for “O” operation (J1 jumper installed).
b) In heat mode and reversing valve is set for “BL” operation (J1 jumper removed).
NOTE 2: On when in heat mode and supply air temperature below Electric Heat setpoint.Heat, Cool, and Fan switches
in AUTO position. Capacity Controller lights off. Delay times are approximate.
*Momentarily toggles to opposite mode every 120 seconds.
CONTINUE
PREVIOUS
MODE
OPERATION
NOTES:
Refer to page 41 for 5 wire link wire sizing.
24V damper transformer. Requires in-line fuse. See table on page 42 for sizing
transformer and fuse.
C terminal for hardwired electronic thermostats only.
J1 Reversing Valve Selection Jumper. Leave jumper in place to
energize reversing valve in cool mode, “O” mode. Remove
jumper to energize in heat mode, “B” mode. J2 is not used for
System 2000.
If the heat pump does not include an outdoor thermostat, it is
recommended that the “W” wire to the unit is run thru an
optional outdoor thermostat with a manual override switch.
Do not remove the jumper wire from TC1 and
TC2. Used for Select-Temp Zoning System only.
Open motor not utilized on low pressure
(spring open) dampers.
If using more than one damper per thermo-
stat, refer to Slaving Zone Dampers section,
pages 23 and 44.
NOTE:
If the Heat Pump system does not have rev. valve
inputs, use the 101ASSB (Gas/Electric Controller).
UP TO
20
ZONES
WYRC
BWY GRd
W Y R C RC MC RO
TB1
TB2
-
+
NC
W2
W2
FUSED 24 VOLT
TRANSFORMER
ELECTRIC HEAT
PUMP #2
PUMP #1
REV VALVE
FAN
Y1
G
Y2
W
R
OBL
/
TO
HEAT
PUMP
101AACBHP
HEAT PUMP
CONTROLLER
REV.
VALVE
HEAT
COOL
DAMPER
PUMP
Y1
Y2
Y1
Y2
HEAT
COOL J1
ON
PWR
OFF
COOLHEAT
OFF
AUTO
OFF
ON
AUTO
FAN
HEAT ADJ
TP3
COOL ADJ
TP2
ELECTRIC
HEAT ADJ
TP1
GROUND
GND
Y1 G
Y2
TB2 WROBL
/
TC2 YWBG
Rd TR1TR2STB1 TC1TEMP
-
+
J2
5
1
7
2
4
6
Zone
Thermostat
Zone
Damper
Relay Board
(101ARLY)
Motors
Close Open
DUCT
MOUNTED
LEAVING AIR
SENSOR
(101ALAS)
(PG 35)
1
2
3
4
5
6
7
8
OPERATION SUMMARY TABLE (EFFECTIVE HPC V1.04 8/02)
WIRING
*NOTE:
Cool:Y2 delay on
make 8 min.
Heat:Y2 delay on
make 4 min.

8
Make sure the correct size fuse is installed in-line with the transformer
powering the Controller.
For both Gas/Electric and Heat Pump Controllers
1. These system tests are to be done with all wiring to the air condi-
tioning unit disconnected.
A. Be sure that the power switch to the Controller is in the “OFF”
position. For Gas/Electric remove “R,” “W1,” “Y1” and “G” wires
from Terminal Strip 2 labeled (TB2).
B. Be sure that the power switch to the Controller is in the “OFF”
position. For Heat Pumps remove “R,” “W,” “Y2,” “Y1,” “O/BL”
and “G” wires from Terminal Strip 2 labeled (TB2).
2. Check wiring of the 5 wire link to the dampers. All connections
must be made color to color.
3. If you are not using Zonex Systems supplied zone thermostats,
check each one to make sure it is an auto changeover type stat.
Turn all thermostats to the OFF position. Check the Controller
“HEAT” and “COOL” switches to be sure that both are in the “OFF”
position. The “FAN” switch should be in the “AUTO” position. Observe
the fuse on the Controller Board and transformer. Turn the power
switch to “ON.” If the fuse blows, there is a wiring problem. If the
fuse does not blow, turn the “HEAT” switch to “AUTO” and “COOL”
switch to “AUTO.” If the fuse blows at any of these steps, find and
repair the short in the wiring.
4. If the system is operating normally, the Heat light should be on for
the 101ASSB, and 101AACB-HP. Set the “HEAT” switch to “OFF”.
Check the first zone by turning it on and setting it to call for cool-
ing. If the call is received by the Controller, the “Damper” and
“Cool” lights will turn on. If the lights come on, turn off the first
stat and the “Damper” light should turn off. Test each stat this way
to be sure that each one is capable of communicating with the
Controller, and able to start and stop the air conditioner.
NOTE: “Heat” and “Cool” Led indicators will toggle every two min-
utes to check opposite mode callers, regardless of heat and cool
switch positions.
5. After cooling calls are tested, turn the cooling switch to “OFF” and
set the heating switch to “AUTO”. Set the first zone to call for heat.
If the call is received by the Controller, “Damper” and “Heat” lights
will turn on. Test each thermostat to be sure that each properly
communicates with the Controller for the heating sequence.
6. After all zones have been checked, turn the ON/OFF switch at the
System Controller to OFF.
7. Before wiring the System Controller to your A/C unit or furnace,
check the relays with a volt meter (set on 200 Ohms). Be cer-
tain no continuity exists on the A/C unit terminal connections at the
System Controller. Check between each terminal to the “R” termi-
nal. There should be no continuity between the terminals. (If you
do show continuity, your System Control board should be replaced.)
8. If no continuity exists from the test detailed above, connect the
terminal to the A/C unit and the System Controller. Be certain all
thermostats are now in the “OFF” position.
9. Turn the power switch to “ON” and the “HEAT” and “COOL” switch-
es should be set to “AUTO”. Initiate a call for cooling from only one
stat. After a time delay, both compressor and fan should be running.
Turn off the cooling and initiate a heating call, (you may experience
up to a 4 minute time delay). The heat should come on and after a
short time delay the fan will be operated by the internal controls of
the unit. On the Heat Pump controller, eight minutes on the ini-
tial start of CAPL-2 after stage one starts, the LAS or capacity con-
trol will control second stage operation.
10. After completing the system check and startup procedure, set the
system up for normal operation.
SYSTEM 2000 SYSTEM STARTUP

9
SYSTEM OPERATION
The user manually selects the mode (heat/cool) at the Switching Center.
If any zone thermostat calls for the mode selected, the green call light
turns on at the Switching Center, the HVAC/heat pump unit turns on, and
all non-calling zone dampers close.
Once all zones are satisfied, the green call light turns off, the HVAC/heat
pump unit shuts off and all dampers open. If the Switching Center
fan switch is ON, the fan will continue to run to allow ventilation in
all zones.
The Capacity Controller independently monitors the supply air temperature
to prevent coil freeze up or overheating.
The Bypass damper will independently bypass any supply air not needed
back to the return duct.
System 1000
Zonex Systems Supplied Components
Switching Centers................................................................Pages 11-14
Zone Thermostats ...............................................................Pages 16-17
Zone Dampers ....................................................................Pages 18-23
Bypass Dampers .................................................................Pages 23-27
Capacity Controllers............................................................Pages 28-41
System 1000
Field Supplied Components
Thermostat Wire........................................................................Page 41
24V Transformer(s) and Fuse....................................................Page 42
SYSTEM 1000
System 1000
Switching Center
System 1000 Zone Control enables a single HVAC unit to be controlled by
up to seven zone (room) thermostats. System 1000 is a manual
changeover system. This means that the mode of operation (heat/cool)
is manually selected. For auto changeover capability select Zonex
Systems System 2000.
4.25"
1" 2.5"
CONCEPTUAL DRAWING ONLY
Refer to System 1000 Switching
Center Section for Wiring
Information.

10
SYSTEM 1000 – COMPONENT SELECTION GUIDE
Manual Changeover for 2 to 7 Zones
5 TONS AND UNDER OVER 5 TONS
BYPASS DAMPERS
ZONE DAMPERS
START
❶ Some Heat Pumps utilize Gas/Electric thermostats. For this type of Heat Pump,
use the Gas/Electric parts selection and field modify the capacity control heat cutoff
setpoint to 118° F.
❷ Use heavy duty rectangular dampers on systems of 7.5 tons or larger
COMPLETE SYSTEM
Barometric Bypass Damper
Round (101ABBD size)
Rectangular RBB W x H
Digital Programmable
(101DIGI) (101PROG) Digital Programmable
(101DIGI) (101PROG)
Switching Center
(SYGE)
2 Stage
(CAPL-2)
1 Stage
(TRLAT)
or
Digital Version
(101CAPGE)
CAPACITY CONTROLLERS
DIGITAL CAPACITY CONTROLLER
(SYCAP)
Switching Center
(SYHPA)
2 Stage Heat/1 Stage Cool
GAS ELECTRIC
ZONE THERMOSTATS
ZONE THERMOSTATS
HEAT PUMP ❶
5 TONS AND UNDER
Low Pressure Dampers
Round (101ARZD size) up to .5” SP
Rectangular (101EC W x H) up to .5” SP
12 X (Number of Dampers) = VA for the
24V System Transformer (Field Supplied)
OVER 5 TONS
Medium Pressure Dampers
Round (101AMPD size) up to 1.75” SP
Rectangular (101MRTD W x H) up to 1” SP ❷
Heavy Duty Rectangular (101CD W x H) to 1.75” SP
6 X (Number of Dampers) =VA for the
24V System Transformer (Field Supplied)
Electronic Bypass Damper
Round (STMPD size)
Rectangular (STCD W x H)
Static Pressure Controller (101ASPC)
24V, 40VA Independent Transformer
for bypass (Field Supplied)
Optional Outdoor
T-Stat (field supplied)

11
OVERVIEW
The SYGE Switching Center is a manual changeover, Gas/Electric System
Controller. It can control up to 7 zone thermostats. Its function is to look
for calls from the zone thermostats for the mode (heat/cool) selected. If a
call is received, it sends a signal to close the dampers of all zones not
calling and sends a signal to the HVAC unit to energize heating or cooling.
The Mode, Power and Fan control switches are located at the Switching
Center. The Switching Center should be placed in a location that provides
easy access to these switches.
The Switching Center is used in conjunction with a Capacity Controller.
The Capacity Controller protects the evaporator coil from freezing and the
heat exchanger from overheating. The Capacity Controller also controls
staging for multistage HVAC systems. Refer to the Capacity Controller
section (pg. 28) for more information.
OPERATION
The user manually selects the mode (heat/cool) at the Switching Center.
Heat mode – If any zone thermostat calls for heat, electrical current
flows in WD. The Switching Center senses this current, turns on the green
Call light, energizes RD (RD made to GD) which tells the dampers of all
zones not calling to close and energizes W (W made to R) which tells the
HVAC unit to turn on heat.
Cool mode – If any zone thermostat calls for cool, electrical current
flows in YD. The Switching Center senses this current, turns on the green
Call light, energizes RD (RD made to GD) which tells the dampers of all
zones not calling to close, and energizes Y and G (Y and G made to R)
which tells the HVAC unit to turn on cooling and the indoor blower fan.
No calls – When no thermostats are calling, the green Call light is off,
RD is not energized so all dampers are open, and W, Y are not energized
so the HVAC unit is off. If the FAN switch is ON, then G is energized (G
made to R), and the indoor blower fan will run. This allows ventilation
in all zones.
1. 5 Wire Link Terminals – Daisy chain wires to zone dampers.
YD – Cool call input signal. Current flows in this terminal when Mode
switch at COOL, Power switch ON and thermostat calling for cool.
WD – Heat call input signal. Current flows in this terminal when
Mode switch at HEAT and thermostat calling for heat.
BD – 24V return. Same as TR2.
GD – 24V hot. Same as TR1.
RD – Unit on output signal. Energized (RD made to GD) when
Switching Center acknowledges thermostat call. See 7.
2. Transformer Terminals – 24V AC transformer terminals. This
transformer powers the dampers, thermostats and Switching Center.
It does not power the HVAC unit. That power comes from terminal
R; see 3.
3. HVAC Unit Terminals – Connect to HVAC unit via Capac-
ity Controller. See Capacity Controller section for wiring
information.
W – Heat enable. Energized (W made to R) when Switch-
ing Center acknowledges a heat call. See 7.
Y – Cool enable. Energized (Y made to R) when Switch-
ing Center acknowledges a cool call. See 7.
R – HVAC unit 24V power.
G – Fan enable. Energized when FAN switch is at ON posi-
tion or when FAN switch is at AUTO position and Switch-
ing Center acknowledges a cool call. See 7.
4. Mode Switch – Selects mode (heat/cool) to run system.
Switching Center will only respond to thermostats calling
for mode selected.
5. Power Switch – When OFF the Switching Center will not respond to
thermostat calls. Power remains to all dampers and thermostats.
The indoor blower fan will run if fan switch is on.
6. Fan Switch – Controls the indoor blower fan (G).
AUTO – Indoor blower fan turns on when air conditioner is on.
Note: In heat mode, furnace controls indoor blower fan.
ON – Indoor blower fan continuously on as long as Power switch
is ON.
7. Call Light – On when Switching Center responds to a calling
thermostat.
AUTO
ON
FAN
ON
OFF
SYSTEM 1000
GAS/ELECTRIC
SWITCHING CENTER
(SYGE)
HEAT
COOL
GREEN CALL
LIGHT
YD WD BD GD RD TR1 TR2 W Y R G
4
5
67
1 2 3
SYSTEM 1000 SWITCHING CENTERS – GAS/ELECTRIC SYGE
COMPONENTS

12
YD
WD GD
BD RD
LOGIC
BOARD
160
OHMS
COOLHEAT
SWITCHING
CENTER
(SYHPA)
GREEN
CALL LIGHT
OFF
K1
LOGIC
BOARD TR
1
TR2
POWER
K1
F
U
S
E
3P3T
SWITCH
K1
COOL
HEAT
OFF
OFF
E.M.
HEAT
ON
FAN ONAUTO
OB COOLHEAT
OFF
O/B Y G R W2 E L C
E.M. HT LIGHT
(RED)
COMP. FAIL
(YELLOW)
SYSTEM 1000 SWITCHING CENTERS – GAS/ELECTRIC SYGE
SYSTEM 1000 SWITCHING CENTERS – HEAT PUMP SYHPA
WDYD GDBD RD
LOGIC
BOARD
K1
160
OHMS
K1
LOGIC
BOARD
TR1
TR2
POWER
COOL HEAT
K1
COOL HEAT
W
Y
R
G
SWITCHING CENTER
FAN
ON
AUTO
GREEN
CALL LIGHT
SIMPLIFIED SCHEMATIC, SYGE
SIMPLIFIED SCHEMATIC, SYHPA
WIRING
2
3
4
5
NOTES:
24V damper transformer. Requires in line fuse. See table on page
42 for sizing transformers and fuse.
Refer to page 41 for five wire link wire sizing.
C terminal for hard wired electronic thermostats only.
Open motor not utilized on low pressure (spring open) dampers.
If using more than one damper per thermostat, refer to Paralleling
Zone Dampers section, pages 23 and 44.
1
OVERVIEW
The SYHPA Switching Center is a manual changeover, single stage cool,
two stage heat, heat pump System Controller. It can control up to 7 zone
thermostats. Its function is to look for calls from the zone thermostats for
the mode (heat/cool) selected. If a call is received, it sends a signal to close
the dampers of all zones not calling and sends a signal to the heat pump
unit to energize heating or cooling.
The Switching Center is used in conjunction with a SYCAP Capacity
Controller. The SYCAP cycles the heat pump on and off to maintain the
leaving air temperature within a set range. Refer to the SYCAP in the
Capacity Controller section (pg. 33) for more information.

13
The Mode, Power, Fan and Emergency Heat control switches are located
at the Switching Center. The Switching Center should be placed in
a location that provides easy access to these switches.
NOTE: If your heat pump is controlled by a gas/electric thermostat, use
an SYGE Switching Center. See SYGE Switching Center section, pg. 3.
OPERATION
The user manually selects the mode (heat/cool) at the Switching Center.
Heat mode – With the Mode switch set to HEAT, Fan switch set to AUTO,
EM HT switch set to OFF and Power switch set to ON, if any zone ther-
mostat calls for heat, electrical current flows in WD. The Switching Cen-
ter senses this current, turns on the green Call light, energizes RD (RD
made to GD) which tells the dampers of all zones not calling to close
and energizes Y, W2 and G (Y, W2 and G made to R). G turns on the
indoor blower fan. Y controls the heat pump compressor and W2 controls
auxiliary heat. Y and W2 are further controlled by the SYCAP Capacity Con-
troller which makes and breaks Y and W2 to maintain a minimum and
maximum leaving air temperature. See SYCAP under Capacity Controller
section for further information. The reversing valve is energized (B made
to R) if the reversing valve jumper is set to B.
Cool mode – With the Mode switch set to COOL, Fan switch set to AUTO,
EM HT switch set to OFF and Power switch set to ON, if any zone
thermostat calls for cool, electrical current flows in YD. The Switching
Center senses this current, turns on the green Call light, energizes RD
(RD made to GD) which tells the dampers of all zones not calling to close
and energizes Y, and G (Y and G made to R). G turns on the indoor blow-
er fan. Y controls the heat pump compressor. Y is further controlled by
the SYCAP Capacity Controller which makes and breaks Y to maintain a
minimum leaving air temperature. See SYCAP under Capacity Controller
section for further information. The reversing valve is energized (O made
to R) if the Reversing Valve jumper is set to O.
No calls – When no thermostats are calling, the green Call light is off,
RD is not energized so all dampers are open, and W2, Y are not energized
so the HVAC unit is off. If the FAN switch is ON then G is energized (G made
to R) and the indoor blower fan will run. This allows ventilation in all
zones.
Emergency Heat – With the Mode switch set to HEAT, Fan switch set
to AUTO, EM HT switch set to ON and Power switch set to ON, if any zone
thermostat calls for heat, electrical current flows in WD. The Switching
Center senses this current, turns on the green Call light and red Emer-
gency Heat light, energizes RD (RD made to GD) which tells the dampers
of all zones not calling to close and energizes E (E made to R). What E is
wired to depends on the make of your heat pump. Refer to the SYHPA
wiring diagram for further information.
Note: Do not leave the Emergency Heat switch set to ON when the Mode
switch is set to COOL. Doing so will energize E (turning on emergency
heat) when a thermostat makes a cool call.
SYSTEM 1000 SWITCHING CENTERS – HEAT PUMP SYHPA
1. 5 Wire Link Terminals – Daisy chain wires to zone dampers.
WD – Heat call input signal. Current flows in this terminal when
Mode switch is at HEAT and thermostat is calling for heat.
YD – Cool call input signal. Current flows in this terminal when Mode
switch is at COOL, Power switch is ON and thermostat is calling for
cool.
BD – 24V return. Same as TR2.
GD – 24V hot. Same as TR1.
RD – Unit on output signal. Energized (RD made to GD)
when Switching Center acknowledges thermostat call. See 9.
2. Transformer Terminals – 24V AC transformer terminals. This
transformer powers the dampers, thermostats and Switching Center.
It does not power the HVAC unit. That power comes from terminal
R; see 3.
3. Heat Pump Unit Terminals – Connect to Heat Pump unit via SYCAP
Capacity Controller.
O/B – Reversing Valve terminal. Energized (O/B made to R) in heat
mode when O/B jumper is at B. Energized in cool mode when O/B
jumper is at O.
Y – Compressor enable. Energized (Y made to R) when Switching
Center acknowledges a heat or cool call and Emergency Heat Switch
OFF.
G – Fan enable. Energized when FAN switch is at ON position or
when FAN switch is at AUTO position, Emergency Heat Switch is OFF
and Switching Center acknowledges a heat or cool call.
R – Heat Pump unit 24V power.
E – Emergency Heat enable. Energized (E made to R) when
Switching Center acknowledges a heat call and Emergency Heat
switch is ON. See 6 and 9.
W2 – Auxiliary Heat enable. Energized (W2 made to R) when
Switching Center acknowledges a heat call and Emergency Heat
switch is OFF. Sends signal to SYCAP.
L – Compressor fail flag input terminal. If feature is provided by Heat
Pump, when L is energized (L made to R), red light DL3 is illuminat-
ed to signal compressor is not working.
C – Heat Pump unit 24V power return.
4. Mode Switch – Selects mode (HEAT/OFF/COOL) to run system.
Switching Center will only respond to thermostats calling for mode
selected.
5. Fan Switch – Controls the indoor blower fan (G) when the Emer-
gency Heat switch is OFF.
AUTO – Indoor blower fan turns on when Heat Pump is on.
ON – Indoor blower fan is continuously on as long as Power
switch is ON.
6. Emergency Heat – Disables compressor (Y) and blower fan (G)
and energizes E (E made to R). This tells the Heat Pump to
turn on auxiliary heat. Should only be used when Mode switch is in
HEAT. If used when mode switch is in COOL, auxiliary heat will turn
on when there is a cool call.
COMPONENTS

14
SYSTEM 1000 SWITCHING CENTERS - HEAT PUMP SYHPA
Open motor not utilized on low pressure
(spring open) dampers.
C terminal for hardwired electronic
thermostats only.
24V damper transformer. Requires
in-line fuse. See table on page 42 for
sizing transformer and fuse.
Refer to page 41 for Five Wire Link wire
sizing.
If the heat pump does not include an
outdoor thermostat, it is recommended
that the “W2” wire to the heat pump
unit is run thru an optional outdoor
thermostat with a manual override
switch.
If using more than one damper per
thermostat, refer to paralleling zone
dampers, pages 23 and 44.
If the heat pump does not have an
emergency heat terminal, connect “E”
of Switching Center to auxiliary heat
terminal of heat pump. If the heat
pump does not turn on the indoor
blower fan in emergency heat mode,
add blower fan relay as shown below.
1
2
3
4
5
6
7
Daisy chain up to six additional zones
ZONE
THERMOSTAT
RYW
WYG Rd
W
Y
R
C
RO MC RC
TB2
C
W2
W2
TB1
DAMPER RELAY BOARD
(101ARLY)
FUSED 24V
DAMPER
TRANSFORMER
SYHPA
SWITCHING CENTER
RDBDGDWDYD
TR1 TR2
EGRYO/B W2LC
HEAT PUMP TERMINALS
EGRY
O/B W2LC
SYCAP
CAPACITY
CONTROL
(PG 33)
Y1Y1 W2W2 CR
3
4
5
7
B
2
6
1
CLOSE
MOTOR
OPEN
MOTOR
ZONE DAMPER
If the heat pump does not energize
the indoor blower fan when
emergency heat is energized, add
relay K1 as shown. Relay K1 is a
24VAC SPDT relay.
EMERGENCY HEAT BLOWER FAN RELAY
SYHPA
SWITCHING CENTER
GR E C
GR E C
K1
HEAT PUMP TERMINALS
K1
K1
7. Reversing Valve Selection Jumper – Configures Switching Cen-
ter to energize reversing valve in cool mode or heat mode. Place on
O and center pin to energize reversing valve in cool mode. Place on
B and center pin to energize in heat mode.
8. Fuse – 1/10 amp. Protects WD and YD terminals.
9. Status Lights –
DL1 – Call light, green. On when Switching Center responds to a
calling thermostat.
DL2 – Compressor fail, yellow. On when L terminal is energized
(L made to R). Indicates heat pump compressor is not functioning.
DL3 – Emergency Heat, red. On when E terminal is energized (E
made to R). Indicates emergency heat is on.
10. Power Switch – When OFF the Switching Center will not respond to
thermostat calls. The indoor blower fan will run if Fan switch is ON.
Power remains to all dampers and thermostats.
AUTO
FAN
ON
HEAT
OFF
COOL
OFF
ON
EM. HT.
RDBD GDWD YD
O/B Y G R E W2 L C
OFF ON
DL2 DL3
DL1
O B
4
5
6
7
1
2
3
8
9
10
SYHPA
TR2 TR1
WIRING

15
SYSTEM 1000 STARTUP
When all wiring is completed to the dampers and the gas electric/heat
pump unit, the following tests should be made:
✓Disconnect the Rwire from the Switching Center.
✓Check to be sure that there is 24 volt power between
terminals TR1 & TR2.
✓Set all thermostat switches to the OFF position.
✓Set the Switching Center in the HEAT mode.
✓Set the Switching Center ON/OFF switch to ON.
The green call light should be off at the Switching Center. If it is on, there
is a thermostat calling or the WD wire is shorted.
✓Check all of the thermostats, if they are off, remove the WD wire
from the Switching Center. The green light should go off. If it
does, find the short in the five wire link before re-connecting it. If
the green light does not turn on, test each thermostat, one at a
time. Turn on one thermostat, set it to call for heating, and the
green light on the Switching Center should turn on. When you set
this same thermostat for no heat, the green light at the Switching
Center should turn off. Test each thermostat in this manner to
be sure all thermostats are properly wired.
Now, set the Switching Center in the COOL mode.
If the green light turns on with all thermostats off, there is a short in the
YD wire. Correct the problem before proceeding.
Repeat the test of each thermostat in the cool mode. When a thermostat
is calling, the green call light will turn on. Turning this thermostat off will
turn off the green call light at the Switching Center.
GAS/ELECTRIC SYGE
Turn the ON/OFF switch off and reconnect the Rwire. Be sure that all
thermostats are off. Turn the ON/OFF switch ON. Decide if you want to
test the heating or cooling system and set the HEAT/COOL switch to the
desired position.
If you have set the switch to COOL, set one thermostat to call for cooling.
The green light will turn on and the cooling system compressor and
indoor fan will turn on. If it does not, check wiring between the Switch-
ing Center and the unit.
If you have set the switch to HEAT, set one thermostat to call for heat. The
green light will turn on and the furnace should start. The fan will start
when the time delay or bonnet control turns it on. If the system does not
turn on, check the wiring between the Switching Center and the furnace.
The Switching Center controls the furnace and air conditioner with relay
contacts. The Switching Centers R,Y,W&G terminals operate exactly like
a four wire thermostat. Trouble shooting the heating and air condition-
ing equipment should be handled as though the Switching Center is a
four wire thermostat.
HEAT PUMP (SYHPA) with the SYCAP
Check that the fuse on the SYHPA has not blown. If it has, check for
shorts on the WD and/or YD wires on the five wire link and replace the
1/10 amp fuse.
Turn the POWER switch on the SYHPA and SYCAP OFF: Check all
thermostats to be sure that they are off. Reconnect the Rwire at the SYHPA.
Check to be sure that the O/B jumper on the SYHPA is in the correct
position for the heat pump. Turn the POWER switch on the SYHPA to ON.
To test the COOL mode, set the HEAT/COOL switch on the SYHPA to the
COOL position. Set only one thermostat to call for cooling. The green
call light on the SYHPA should turn on and the compressor will run. The
indoor fan will start with the compressor. If the compressor or fan do
not start, check the wiring between the SYHPA and the Heat Pump.
To test the HEAT mode, turn the POWER switch on the SYHPA to OFF.
Turn all thermostats off. Set the MODE switch on the SYHPA to HEAT and
then turn the POWER switch ON. Set one thermostat to call for heat. The
green call light will turn on at the SYHPA and the compressor will turn on
in the heat mode. The fan will turn on with the compressor. If the
fan or compressor does not turn on, check the wiring.
When yellow DL2 is lit, there is a heat pump compressor failure (if “L”
terminal has been wired).
When the “EM HT” switch is set to ON, the SYHPA will never power the
“Y” or “G” terminal and will power the “E” terminal during a call. While
the “EM HT” switch is set to ON, the red light labeled DL3 will turn on if
there is a call. To test the Auxiliary/Electric heat, see the unit manufac-
turers wiring diagrams and instructions.
SYCAP and Auxiliary/Electric Heat
To test the Auxiliary/Electric heat, turn the SYCAP switch ON. If the dis-
play begins to toggle between “E” and “157”, the factory installed tem-
perature sensor or its wiring to terminals ± is open. If the display toggles
between “E” and “32”, the temperature sensor is shorted. Check con-
nections + and – and the wire holding the sensor in the plenum for shorts.
During normal startup the supply air temperature should be displayed.
Unless modified at this time, the SYCAP will operate at factory cut-out
setpoints of 118 degrees F. for heat and 48 degrees F. for cooling. To
modify these cut-out setpoints see “Determine the existing cut-out set-
points on a CAP” in the Capacity Control section of this manual.
To test the Auxiliary/Electric heat disconnect the Y wire at the SYCAP or
SYHPA. Set one stat to call for heat. If the supply air temperature is below
the electric heat cut-in setpoint, and after a four minute time delay, DL2
and the Auxiliary/Electric heat will turn on.
After testing the SYCAP, replace the Y wire for proper heat pump operation.
Note: At temperatures below 38°F and above 125°F (heat pumps), the
display will toggle between “E” and the supply duct temperature. This is
normal operation and provisions have been made to allow the heating and
cooling to operate.

16
Each zone requires a zone thermostat. This thermostat can be digital,
mechanical, or programmable. All three types are available. Zonex Sys-
tems thermostats have been specifically designed to work with Zonex
Systems Zone Control systems. Attempting to use another manufacturer’s
thermostat may create compatibility problems and cause nuisance calls.
For trouble free installation, use only Zonex Systems supplied thermostats.
Digital Thermostats
Zonex Systems makes two Digital Thermostats for the System 1000/2000:
101DIGI – a single stage thermostat that can be used whenever auxil-
iary zoned heating is not required.
101DIGITS – a single stage cool, two stage heat thermostat. It should
be used when auxiliary zoned heating is needed.
101DIGI: This is a digital, dual setpoint, single stage zone thermostat,
accurate to within one degree. The 101DIGI is auto changeover, is non
power robbing, and is designed with a non-volatile memory to retain all
programmed setpoints. The stat is operated by two push buttons to review
and modify heat and cool setpoints. To avoid unauthorized setpoint mod-
ifications, the 101DIGI has locking setpoint capability. There is also a zone
On/Off switch. Under the cover there is a green and red light. When the
green light is on the stat is calling for cooling. When the red light is on the
stat is calling for heat. Following any call, the stat is designed with a two-
minute minimum run time to prevent short cycling. It can be used with any
of the System 1000/2000 Controllers. This thermostat can be ordered with
a remote sensor (101DIGIRS). The 101DIGI Dimensions are:
2-7/8”W
x 4-1/2”H x 1”D, the color is off white
. Requires four thermostat wires for
installation.
101DIGITS This is an auto
changeover, electronic zone thermo-
stat with auxiliary heat output. This
dual setpoint thermostat has a large
digital readout which displays cur-
rent room temperature. Under the
cover there are two red lights and
one green light. When the green
light is on, the thermostat is calling
for cooling. When the red light labeled “D-1” is on, the the stat is call-
ing for first stage heat. When the the red light labeled “HT2” is on, the
stat is calling for second stage heat. This zone thermostat is designed for
zones that require supplemental heat. This thermostat can be ordered
with a remote sensor by adding RS to its part number. 101DIGITS dimen-
sions are 2 7/8” W x 4 1/2” H x 1” D. Installation requires five
wires.
101DIGI Thermostat Operation
Each digital thermostat has an “ON” / “OFF” switch located at the bottom.
Typically, this thermostat should always be in the “ON” position. When
the room is unoccupied, use this switch to take the zone out of your sys-
tem by sliding it to the left to turn it off. When the room is occupied slide
the switch to the right to turn it on. Assign the Heating and Cooling Set-
points desired by using the following instructions:
1. Determine the existing Set-
points:
A. To determine the existing Heat
Setpoint, press and hold the
top button marked until
the letter “H” appears and
then release. The current heat
setpoint will be displayed
following the letter “H” (If
the button is held down too
long the Heat Setpoint will
begin to increase). Approxi-
mately two seconds after the
button is released the current
room temperature will be
redisplayed.
B. To determine the existing Cool
Setpoint press and hold the low-
er button marked until the
letter “C” appears and then
release. The current Cool
Setpoint will be displayed
following the letter “C” (If the
button is held down too long
the Cool Setpoint will begin to
decrease). Approximately
two seconds after the button is
released the current room
temperature will be redisplayed.
2. Modifying the Setpoints:
A. To change the Heat Setpoint,
press and hold the top button
until the Heat Setpoint is dis-
played. Continue to press this
button (the up button ) to
increase the Heat Setpoint or
press and hold the bottom
button to reduce the Heat
Setpoint to your desired
comfort level in this room.
B. To change the Cool Setpoint,
press and hold the lower button until the Cool Setpoint is
displayed. Continue to hold this button to lower the Cooling
Setpoint or press the top button to raise the Cool Setpoint
to your desired comfort level in this room.
Set up all of the zone thermostats in this way to provide room
by room comfort control.
101DIGI
Requires
4 Wires
101 DIGITS
Requires
5 Wires
ZONE THERMOSTATS
>
>
>
>
>
>

17
3. Locking the Set points:
To avoid unauthorized setpoint
modifications, the 101DIGI has
locking setpoint capability. After
the heat and cool setpoints have
been selected, use the jumper
located under the cover near
the middle of the board labeled
LCK to lock the setpoints. Slide
the jumper over both terminals
as shown in the diagram above.
This will lock the setpoints in
place. To modify the setpoints,
the jumper must be to moved to
the adjustable position.
DIGICOM: The DIGICOM auto
changeover, communicating
thermostat is used exclusively in ZonexCommander thermal management
systems. Using a computer and the ZonexCommander software, all ther-
mostats in the system can be programmed and viewed. The DIGICOM
may be applied in stand alone unit control, from 1 to 80 split or pack-
aged systems. When used with a modem, all ZonexCommander software
functions can be controlled remotely. The DIGICOM requires 24V AC
power from either the zone system or HVAC unit transformer, with the
addition of a two conductor, twisted pair cable for communications.
Dimensions: 2-7/8” W x 4-1/2” H x 1” D.
101PROG: Features a battery powered,
7-day programmable, auto changeover
control for single stage heating and cooling
applications. Thermostat can be programmed
for up to four periods per day, and offers
three operating modes: Manual, Automatic
and Vacation. Blower operation is manual
selectable for auto, on, or programmed for
fossil fuel or electric heat, fan cycling. The
oversized LCD display clearly shows the
time, day of the week, space temperature,
and selected operating mode. The 101PROG
also provides for mode control through an optional telephone controller.
Dimensions are 3.75”W x 5”H x 1”D. Color: White.
ZONE THERMOSTATS – COMPATIBILITY
The 101ASSB gas/electric and 101AACBHP heat pump controllers are
compatible with most thermostats, offering a wide thermostat selection
to the installing contractor. NOTE: the 101AACBHP pump controller
utilizes gas/electric thermostats. When using other than Zonex
Systems thermostats, please refer to the following guidelines:
Electronic Thermostats: Digital thermostats requiring 24V AC power
must be “Hard wired” with a separate R and C or common terminal.
Power robbing type thermostats are not compatible. All types of battery
operated thermostats may be used with any System 2000 control system.
Mechanical Thermostats: When using a mechanical thermostat,
ensure the cooling compensator (anticipator) is removed, and the
heating anticipator is shorted or set to its lowest setting.
Please contact Factory Technical Support for additional thermostat
compatibility information.
ZONE THERMOSTATS
The Zonex Systems digital thermostats can be ordered with a remote sen-
sor. Remote sensors are useful if you would like to place the thermostat
and sensor in different locations. Simply add “RS” at the end of the part
number to order with a remote sensor; i.e.: “101DIGIRS”.
Wiring: The remote sensor must be wired with a minimum 18 ga., two
conductor shielded cable, with a maximum length of 200 feet. The wires
have no polarity. Use field supplied wire nuts to connect the sensor. Flare
back and tape off the cable shield closest to the sensor. Connect the
shield at the thermostat to the “R” terminal.
ZONE THERMOSTATS – REMOTE SENSORS
REMOTE SENSOR BOARD
Temperature
Sensing
Thermistor
REMOTE SENSOR
COVER
TYPICAL
ZONE
THERMOSTAT
Wire Nut
Wire Nut
R
Shield to the "R" terminal
4.5" x 2.75"
DIGICOM
101PROG

18
Zonex Systems zone dampers are used in cooling/heating systems to
provide room by room zone control. The damper is provided with a
factory mounted relay board and zone actuator. Each zone damper is
controlled by a zone thermostat. More than one damper can be
controlled by one zone thermostat; see Slaving Dampers. Use the table
below to determine which zone dampers to use.
Maximum Differential Pressure refers to the maximum static pressure drop in inches of water column between the
input (upstream) of the zone damper and the output (downstream) when the damper is closed.
There are two styles of round zone dampers, low pressure or medium
pressure. For systems 5 tons or under with a maximum differential static
pressure of 0.5”, use low pressure dampers. Otherwise use medium
pressure for up to 1.75” differential pressure on any system over 5 tons.
ROUND LOW PRESSURE ZONE DAMPERS
Zonex Systems round low pressure zone dampers can be used for systems
up to 5 tons with a maximum differential static pressure of 0.5”. These are
two position, spring open, power close dampers for very simple operation.
Round damper sizes 9 inches and under are manufactured from 24
gauge galvanized steel. Sizes 10”, 12”, 14” and 16” are made from 20 - 22
gauge steel. All sizes are designed with rolled-in stiffening beads for superi-
or rigidity. The damper pipe is furnished with one crimped end and one
straight end for easy installation. A hat section supports a synchronous 24V
AC 60Hz 12VA motor and terminal board. The motor is designed for contin-
uous full stall operation. Special winding and heavy duty gearing provide for
long motor life and easy spring open operation. A cross pin on the motor
shaft provides positive direct drive to the damper blade shaft without a cou-
pling or set screws, allowing for a quick and easy motor change if required.
Motor drive time from full open to full close is 30 seconds. Since this is a
spring open damper, in the event of power failure, the damper fails to the full
open position.
ROUND MEDIUM PRESSURE ZONE DAMPERS
Zonex Systems round medium pressure zone dampers are recommend-
ed for systems over 5 tons or with a maximum differential static pressure
up to 1.75”. This power open / power close damper is manufactured from
20-22 gauge galvanized steel with rolled-in stiffening beads for superior rigid-
ity. Mechanical minimum and maximum set stops are provided and easily
adjustable. The damper pipe is furnished with one crimped end and one
straight end for easy installation. A hat section supports a 35 lb./in. 24V, 6 VA
power open, power closed actuator with a damper relay board interface. The
actuator is designed for full stall operation, with a magnetic clutch to protect the
internal gearing. The actuator is direct coupled to the damper shaft, which pro-
vides positive operation and offers replacement ease if required. Drive time from
full open to full closed is 60 seconds. MEDIUM PRESSURE (101AMPD)
LOW PRESSURE (101ARZD)
SYSTEM SIZE
5 TONS OR UNDER
UNDER 7.5 TONS
7.5 TONS OF LARGER
MAXIMUM
DIFFERENTIAL
PRESSURE
0.5"
1"
1.75"
ROUND
DAMPER
LOW PRESSURE
MEDIUM PRESSURE
MEDIUM PRESSURE
RECTANGULAR
DAMPER
LOW PRESSURE
MEDIUM PRESSURE
HEAVY DUTY
ZONE DAMPERS
ROUND ZONE DAMPERS
This manual suits for next models
1
Table of contents
Other Zonex Control System manuals
Popular Control System manuals by other brands
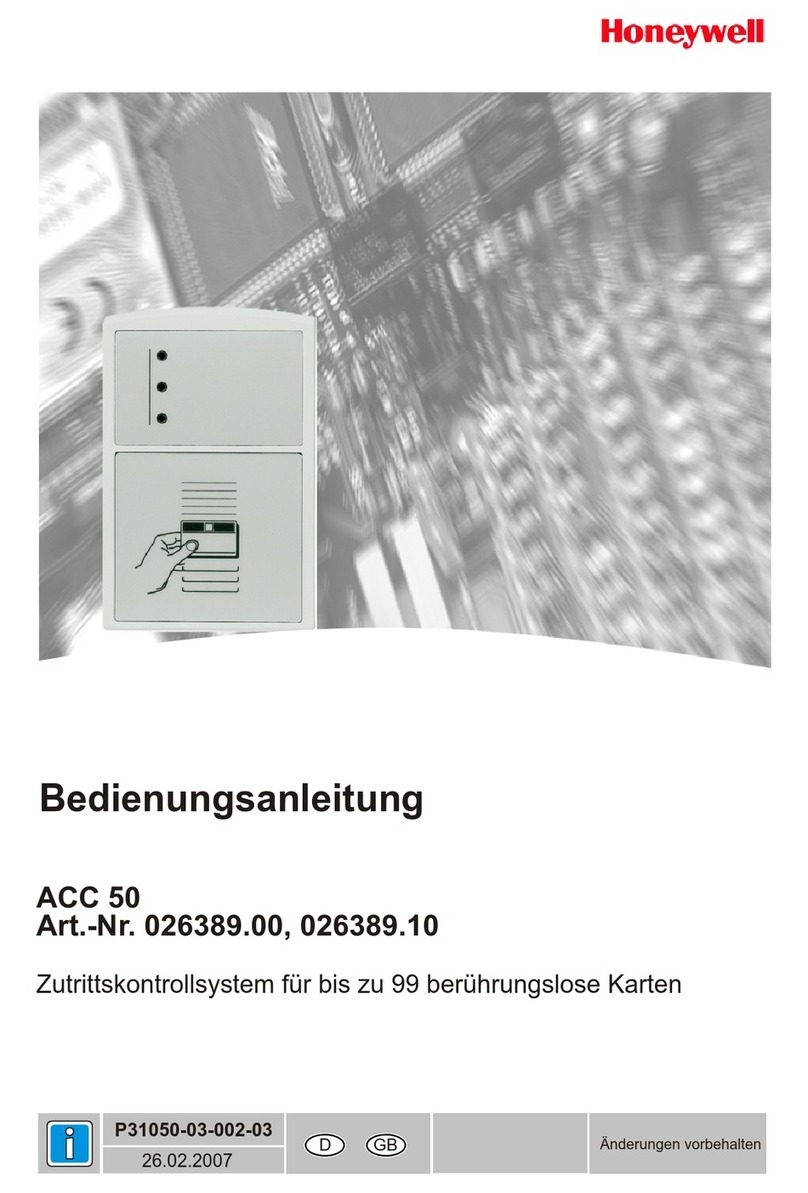
Honeywell
Honeywell ACC 50 operating instructions
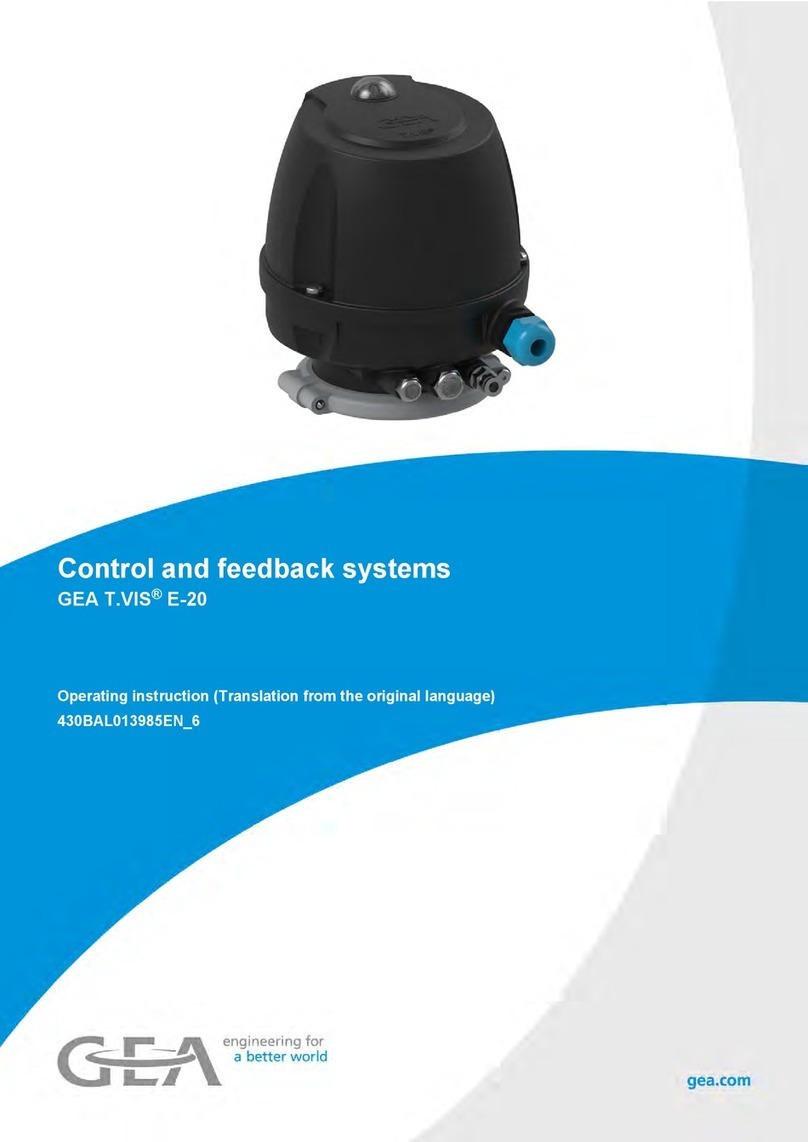
GEA
GEA T.VIS E-20 Operating instruction
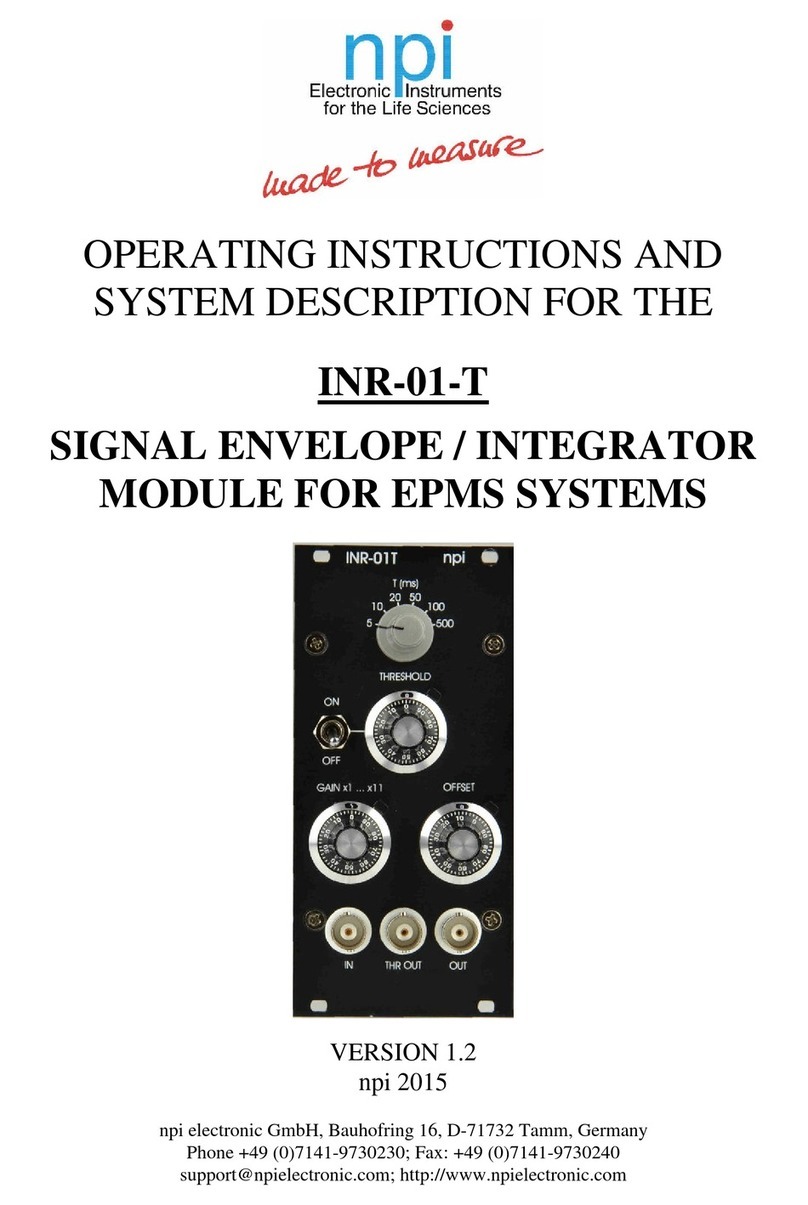
NPI
NPI INR-01-T Operating instructions and system description
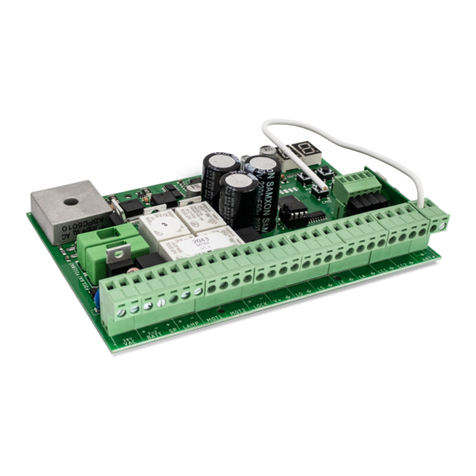
Motorline professional
Motorline professional MC62 User's and installer's manual
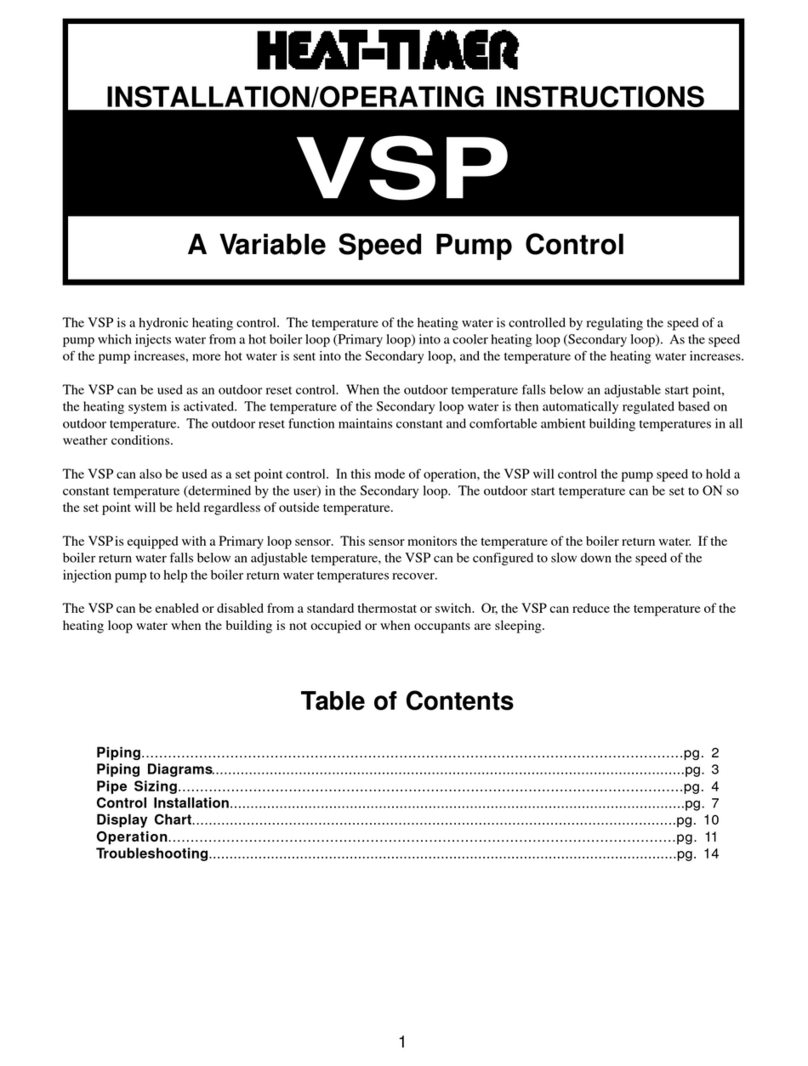
heat-timer
heat-timer VSP Installation & operating instructions
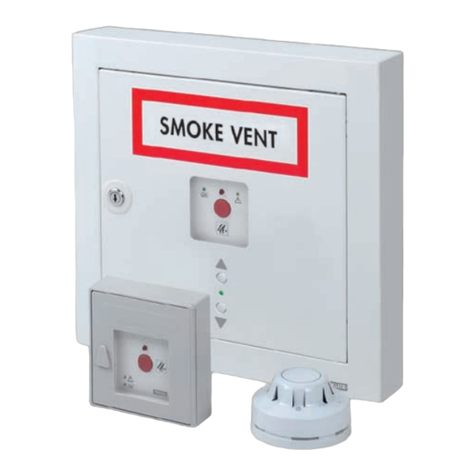
Velux
Velux KFX 100 instructions