3D AEROWORKS Yakovlev Yak-3 Guide

ASSEMBLY MANUAL
AND USER GUIDE
Yakovlev
Yak – 3
By 3D AEROWORKS

OVERVIEW:
This replica of the Yakovlev Yak 3 is designed for quick and easy construction and printed
using light weight PLA (LW-PLA). For best results the canopy should be printed with clear
PLA The motor mount and propeller assembly in regular PLA. A semi-scale propeller is
included in the plans designed to suit the 2804 2300kv outrunner (5x4.75) in 2 or 3 blade
configuration. Utilising full 4 channel controls; aileron, elevator, rudder and throttle, this model
performs extremely well given its small size and lightweight. Links to components used can
be found on the last page of the user guide.
This model has taken many hours of hard work and testing in order to provide a nice flying
aircraft. Please do not share it. Please show your appreciation by directing interested parties
to the link below.
https://cults3d.com/en/3d-model/various/yakovlev-yak-3-600mm-3d_aeroworks
GENERAL SPECIFICATIONS
WINGSPAN: 600mm
PRINT TIME: 46 hrs
PRINT WEIGHT: 150g
PRINT COST: $10 USD (LW-PLA)
FLYING WEIGHT: 300g (without gear) - 320g (with gear)
CENTER OF GRAVITY 52mm aft of L.E at wing root. (Marked with indentation)
ELECTRICS
MOTOR: 2804 2300KV
ESC: 15amp (min) 20amp (recommended)
SERVOS: 3.7g MICRO
BATTERY: 950MAH 2S (or similar)
INCLUDED:
STL FILES OF ALL COMPONENTS (scale to 1000% if not using S3D)
FACTORY FILES FOR (S3D) SIMPLIFY 3D FOR PRINTERS: 200X200X200



REQUIRED TOOLS:
KNIFE
LIGHTER
SANDPAPER (MEDIUM GRIT)
PLIERS
CA GLUE
SCREW DRIVERS
FILE OR RASP
REQUIRED COMPONENTS:
X1 2804 2300KV MOTOR (or similar)
X1 20AMP ESC
X1 950MAH 2S LIPO OR SIMILAR
X4 3.7G MICRO SERVO
BAMBOO SKEWERS 3MM
HEAT SHRINK TUBE 3mm
X2 10mm X 10mm X 2mm MAGNET (ROUND)
X10 MICRO HINGES (OPTIONAL)
VELCRO
X2 x 200mm CARBON STRIP 3mm x 0.6mm (OPTIONAL)
M2 x10mm SCREWS
1mm PIANO WIRE
M2 PUSH ROD (200mm MINIMUM LENGTH)

ASSEMBLY INSTRUCTIONS
1
After all parts have been printed, some may require to be cleaned as LW-PLA is prone to
stringing. Do this by gently sanding back the rough sections with a file, sandpaper or blade
until the surface is smooth.
2
All faces which are to be glued to other parts need to be given a light sanding (scuff the
surface) to assist with glue adhesion.

3
Cut 15mm sections of skewer and place into alignment holes in the fuselage sections.
NOTE - It may be required to open up the holes a small amount if the fit is too tight. Do this
by using a 3mm drill bit. Gently spin it in reverse as you insert it into the hole. This will ensure
the bit does not tear the print.
Test fit the sections of the fuse before gluing to ensure a clean fit.
4
Glue all sections of the fuse together except fuse 1. This will be glued on last in order to
allow for cg balancing.
5
Once glued, with a sharp knife, remove the false floor of the battery hatch. (see pic/
highlighted faces) NOTE: The removed sections of LW-PLA that is the false floor will be
used as hinge pieces later. Do not throw away.

6
From part “fuse 3” remove the inner section of the lead tunnel with a knife or heated metal
rod to allow the servo lead for the aileron to pass through. (refer image)
7
Test fit the hinges in the hinge slots for each control surface and its parent part, this will make
gluing the control surface easier when the time comes. NOTE- Do not force the hinge if it is
too tight. Loosen the slot by gently inserting a stanley knife.
Using the LW-PLA as a hinges:
From the off-cuts from the fuselage false floor, cut small sections of 15mm x 7mm with the
7mm side being against the grain of the layers. Test fit the pieces into the hinge slots of the
control surface and stabiliser or wing.

8
Place a drop of CA in the hinge slot of the control surface and insert the hinge. Be sure that
the hinge is perpendicular to the control surface. Then bend the hinges to 90deg back and
forward a few times to make sure they are appropriately loose. (the outer aileron and
elevator hinge may need to be trimmed). See below
9
Fit the horizontal stabilisers to the fuselage using small sections of 3mm bbq skewers to align
the stabilises and glue with CA.

10
Bend a section of 1mm steel wire to connect the elevators together.
Test fit the wire and the elevators connection to the horizontal stabilisers before gluing the
wire to the elevators or the elevators to the tail plane. There should be un-obstructed travel.
11
Glue the rudder, elevators and ailerons in place. Make sure each control surface has full and
free movement.

12
Glue the wingtips and tail cone in place (if required).
13
Cut one 110mm section and four (2 per wing)15mm sections of skewer. Insert the 15mm
sections into the wings and the 110mm section through the fuselage. This is a makeshift spar
to assist supporting the landing gear. (not required if not using the gear)
Glue the wings to the fuselage NOTE – if using 3mm x 0.6mm carbon strip, now is the time
to install it. Simply slide the carbon strip into the slot and cut it so it does not protrude out of
the wing (circled in red, see image). The cross structure of the fuselage spreads the load of
the wings at the root which negates the need of a connecting spar in the fuselage.
.

14
Run a string through the aileron servo wire tube from the mount hole for the aileron servo to
the wing root. Leave enough length so that you will be able to feed the string through the
fuse later.
15
Install all servos using a small amount of hot glue to secure it in place. The aileron servos
mounting tabs will need to be trimmed. Connect the ailerons to the servos using 1mm wire
and the printed linkage locks.
16
Using an appropriate length of skewer with 1mm steel wire on each end covered in heat
shrink tubing, connect the elevator and rudder to their relative servo.
Elevator = left side
Rudder = right side

17
Install the magnets to both the fuselage and the canopy using CA.
18
Install the desired motor mount to the fuselage using m2 screws. The mount holes may need
to be pre-drilled with a 2mm drill bit.
19
Wire up the ESC to the motor. The esc is intended to sit below the battery floor with the wires
connecting to the battery through the hole in the mid section of the fuselage floor.

20
Install the motor to the motor mount. The motor mount holes may need to be pre-drilled with
a 2mm drill bit.
21
Fit the propeller hub to the motor and screw in the blades using m2 x 10mm screws. Then
secure the spinner to the hub. The propeller blades will need to be pre-drilled with a 2mm
drill bit for ease of fitment.
Installing the propeller:
- Install the blade to the hub and secure it with an m2 x 10mm screw. (screw direction
towards the back of the hub)
- Install the hub to the motor.
- Secure with either metal nut provided or printed nut.
- Install the spinner. The spinner is designed with an m5 thread to suit most small
motors with a regular cw thread.

22 ** IF NOT USING LANDING GEAR SKIP AHEAD TO STEP 27 **
Bend up the 2mm section of piano wire according to the diagram below.
TOP VIEW
FRONT VIEW
(X)mm refers to the distance required to fit the wheel and wheel lock of your choice to the
axel. Test wheel was a 45mm diameter x 17mm wide foam wheel.

Add a slight rake forward to the main gear leg. This will assist in preventing the model from
nosing over on grass fields. See below.

23
Insert the gear leg into the wing as pictured below.
Apply a small amount of hot glue to the outer bend of the leg (red circle on image above.
This will hold it in place but also allow it to be removed if desired. Fit the wheel and secure it
with a shaft collar.

24
Bend up the tailwheel link from 1mm piano wire as pictured below.
SIDE VIEW
ISO VIEW
(X)mm refers to the distance required to fit the wheel and wheel lock of your choice to the
axel. Test wheel was a 20mm diameter x 5mm wide printed. 2mm should protrude from the
wheel collar once fitted to allow crimping of the wire.

25
Insert the tail wheel assembly into the rudder as pictured.
The slot should not be drilled out so as to maintain friction and stop the wheel from rotating in
the slot. A drop of CA can be applied to the link once in place if desired however this will
make removal later on much more difficult. Ensure the link is aligned with the rudder so that
the wheel will track straight when taxiing.
26
Install the wheel and secure it with the printed collar. Crimp the end of the wire with a pair of
vice grips so that the collar will not slip off. A drop of CA can also be added to ensure the
collar does not spin with the wheel.

27 BALANCING AND CG
The ballast lead required should be placed in the hollow section of fuse 1. NOTE! Balancing
needs to be done with the propeller attached. See below
Installing the propeller:
- Install the blade to the hub and secure it with an m2 x 10mm screw. (screw direction
towards the back of the hub)
- Install the hub to the motor.
- Secure with either metal nut provided or printed nut.
- Install the spinner. The spinner is designed with an m5 thread to suit most small
motors with a regular cw thread.
Once balanced appropriately, glue Fuse 1in place with ca.
Fit the battery using Velcro as required and balance the aircraft inverted on the CG marking
points located 52mm aft of the leading edge at the wing root. Using components
mentioned in the parts list, 20g of lead was needed in the nose section to balance without the
wheels.
Table of contents
Other 3D AEROWORKS Toy manuals
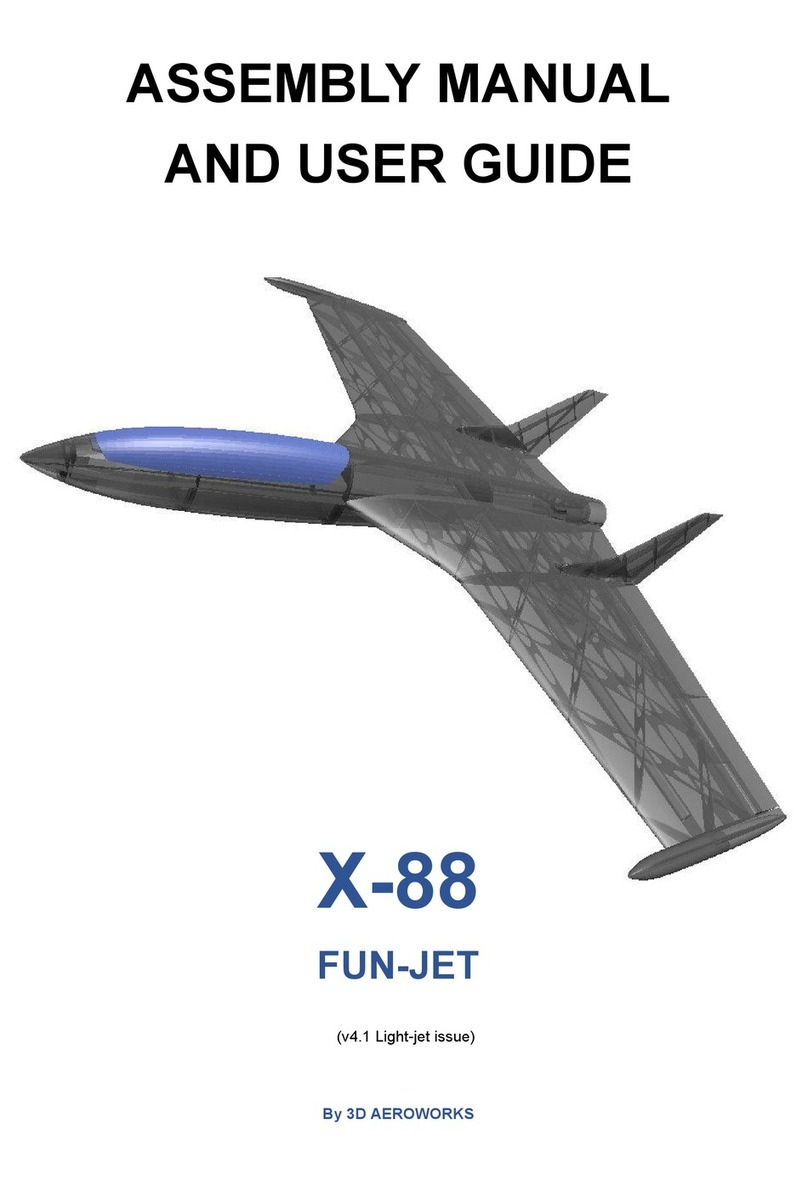
3D AEROWORKS
3D AEROWORKS X-88 Fun-Jet Guide
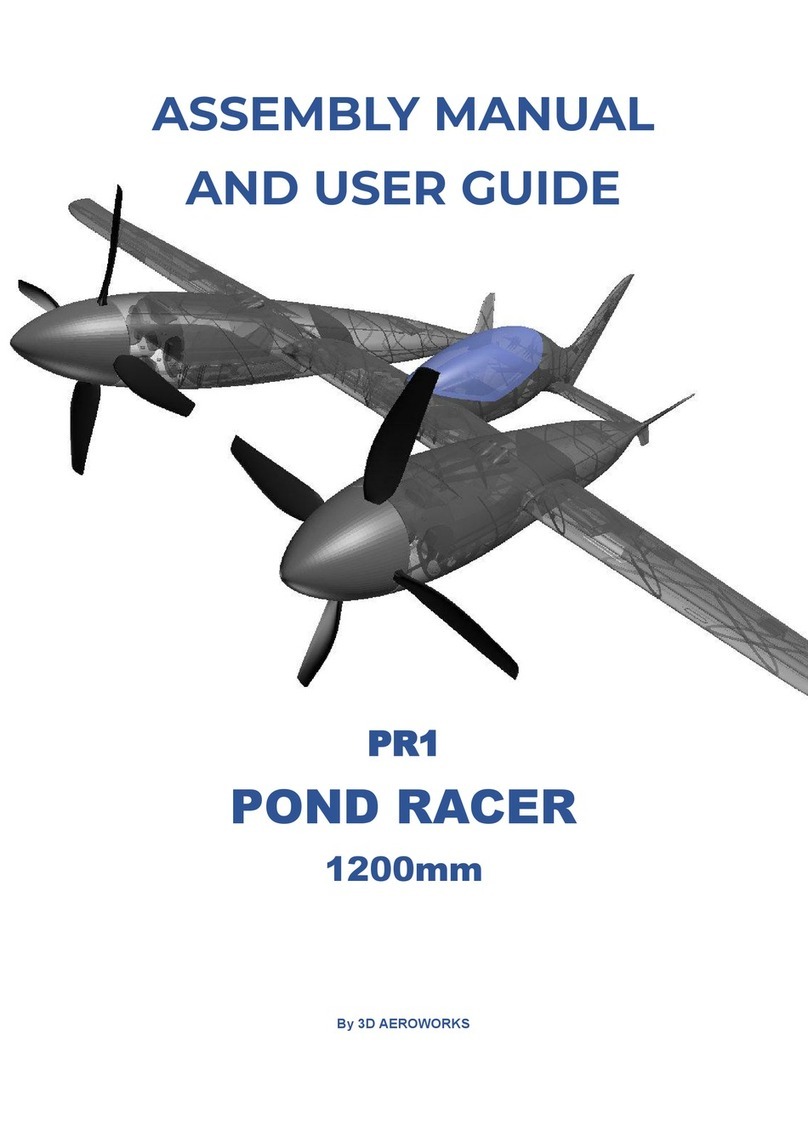
3D AEROWORKS
3D AEROWORKS PR1 Guide
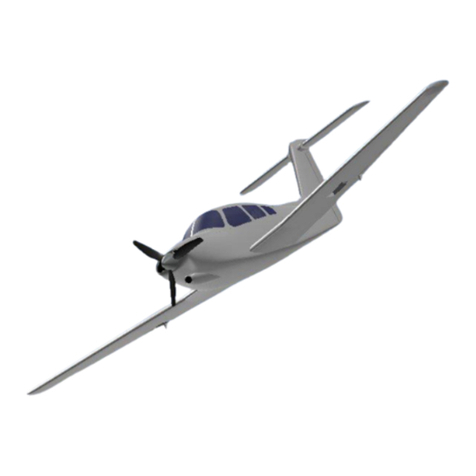
3D AEROWORKS
3D AEROWORKS Piper Turbo Arrow IV Guide
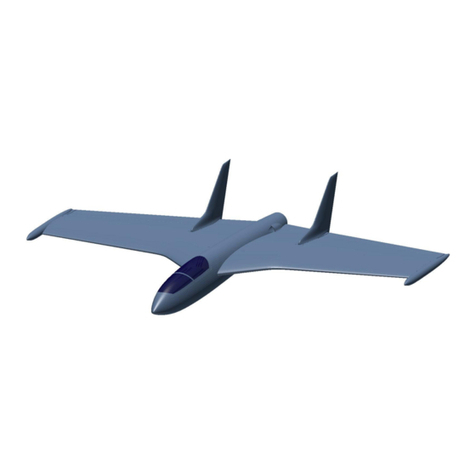
3D AEROWORKS
3D AEROWORKS FUN JET X-88 Guide
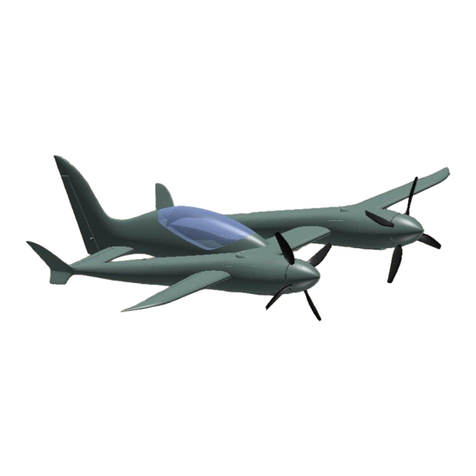
3D AEROWORKS
3D AEROWORKS PR1 Guide

3D AEROWORKS
3D AEROWORKS Focke Wulf FW190-D9 Guide

3D AEROWORKS
3D AEROWORKS Extra 500 Guide

3D AEROWORKS
3D AEROWORKS Pilatus PC-21 Guide