Accu ACCU-Turn 7700 User manual

(O Accu*turn1)
B A TURN FOR THE BETTER
COMBINATION BRAKE LATHE
MODEL 7700
OPERATIONS AND MAINTENANCE MANUAL
Accu International, Inc,
P.O. BOX 15540 / RICHMOND, VA 23227
11126 AIR PARK ROAD / ASHLAND, VA 23005
804 798 8922 FAX 804 798 6742
09/01
#310011

CONGRATULATIONS! You have just purchased the fi est brake lathe i the world
today. Your ACCU-Tur Lathe is a high quality, precisio e gi eered product desig ed
to give you years of trouble-free service.
To familiarize yourself with all its features, please take the time to READ THIS
OWNER'S MANUAL CAREFULLY. Store this ma ual i a safe place for future
refere ce.
It is importa t that you FILL OUT THE ENCLOSED WARRANTY CARD AND
MAIL IT BACK TO OUR HEADQUARTERS. This is of primary importa ce for
authorizatio of warra ty service, for proper parts shipme ts to match the model of your
machi e, a d for receivi g future product updates a d i formatio .
It is also importa t that you RECORD THE MODEL NUMBER, SERIAL NUMBER
AND OTHER VITAL INFORMATION HERE. These umbers are located o the
back of your lathe.
Dealer_________________________ Purchase Date
Model
_________________________ Serial Number
If you eed to call Accu I dustries for parts or service, please have this i formatio
available.

ACCU-TURN MODEL 00
COMBINATION BRAKE LATHE
OPERATIONS AND MAINTENANCE MANUAL
TABLE OF CONTENTS: PAGE
STANDARD EQUIPMENT AND ACCESSORIES............................................... 1
BRAKE LATHE SPECIFICATIONS....................................................................... 2
ACCEPTANCE FROM TRANSPORTATION CARRIER
.................................... 3
SAFETY INFORMATION....................................................................................... 3
ASSEMBLY OF BRAKE LATHE........................................................................... 6
OPERATION PROCEDURES.................................................................................. 7
MOUNTING AND MACHINING PROCEDURES............................................... 7
PARTS LISTS AND DIAGRAMS............................................................................. 10

STANDARD ACCESSORIES INCLUDED IN THE
00 COMBINATION BRAKE LATHE
1 DRAW BAR WITH HEX NUT AND WASHER
3 T-BOLTS WITH NUTS AND WASHERS
2 LARGE BELL CLAMPS
2 SMALL BELL CLAMPS
3 CENTERING CONES
3 SILENCERS
5 DOUBLE TAPER RADIUS ADAPTERS
1 TWIN CUTTER WITH TOOL HOLDERS
1 DRUM BORING BAR
1 STANDARD 1" ARBOR AND NUT
1 ARBOR SPRING
1 1" SPACER
2 WRENCHES: 3/8" AND 1 1/2"
1 SPANNER WRENCH

00 COMBINATION BRAKE LATHE
SPECIFICATIONS
ELECTRICAL 115 VAC; 60 Hz, 1 Ph; 10 Amps
ROTOR CAPACITY
MAXIMUM WIDTH
MAXIMUM DIAMETER
DRUM CAPACITY
MAXIMUM DIAMETER
MAXIMUM DIAMETER W/ROTOR
TRUER REMOVED
MAXIMUM TRAVEL
WEIGHT CAPACITY (ROTOR/DRUM)
SPINDLE SPEED
FEED SPEED
SHIPPING WEIGHT
2 1/8"
12 1/2"
11 1/2"
13 1/2"
3 1/4"
50 lbs.
200 rpm
,003'Yrev.
410 LBS.
2

ACCEPTANCE FROM TRANSPORTATION CARRIER
Carefully inspect all items recei ed in this shipment. If
there is damage or e idence of mishandling in transit, determine
the extent of damage and notify the transit company as well as ACCU
Industries, Inc. immediately. Although we are not responsible for
damage incurred in transit, we will assist in the preparation and
filing of claims.
SAFETY INFORMATION
This manual has been prepared for the operator and those
responsible for the maintenance of the brake lathe. Its purpose,
aside from proper maintenance and operations, is to promote safety
through the use of accepted practice.
READ AND UNDERSTAND THE SAFETY AND OPERATING INSTRUCTIONS
COMPLETELY BEFORE OPERATING THE MACHINE
In order to obtain maximum life expectancy and efficiency from your
brake lathe, follow the operating instructions and maintenance
manual carefully.
The specifications put forth in this manual were in effect at
the time of publication. Howe er, owing to ACCU Industries' policy
of continuous impro ement, changes to the specifications may be
made at any time without obligation on the part of ACCU Industries,
Inc.
Safety Instructions
1. Read, understand and follow the safety and operating
instructions found in this manual. Know the limitations and
hazards associated with operating the machine. A safety rules
decal is installed on the machine to ser e as a reminder of
basic safety practice. It should be read before attempting
to use the brake lathe.
2. Special Precautions: Th'is ACCU-Turn brake lathe was designed
to machine the portions of the brake drum and disc brake rotor
surfaces that come in contact with the friction
material. When used according to the instructions herein,
this lathe will perform satisfactorily within the workpiece
size range designated for this model.
During the machining operation, the workpiece rotates. Be
especially cautious of rotating wheel lugs, spokes and
mounted accessories.
3

During machining, material remo al may cause a sharp edge
to be generated, where a chamfer or radius pre iously existed.
Use care in handling machined parts.
3. Securing the Machine: The model 77 00 weighs approximately 300
pounds and must be bolted to an ACCU-TURN Hea y duty Floor
Stand or a bench capable of supporting the machine, its
accessories and workpiece.
4. Grounding the Machine: Machines eguipped with a three-prong
grounding plug are so eguipped for your protection against
shock hazards and should be plugged directly into a properly
grounded three-prong receptacle in accordance with national
codes, local codes and ordinances. A grounding adapter
may be used only if the green lead is securely connected
to a suitable electrical ground. Do not cut off the grounding
prong or use an adapter with the grounding prong remo ed.
5. E e Safety: Wear an appro ed safety face shield, goggles,
or safety glasses.
6. Personal Protection: Before operating the machine, remo e
tie, rings, watches, and other jewelry, and roll up slee es
abo e the elbow. Remo e all outer loose clothing and confine
long hair. Protecti e type footwear must be worn. Hearing
protectors must be used where noise exceeds the le el of
exposure allowed in Section 1910.95 of the OSHA Regulations.
DO NOT HEAR GLOVES
7. DO NOT OPERATE MACHINE WITHOUT ITS GUARD (S').
8. Work Area: Keep the floor around the machine clean and
free of foreign materials. ACCU Industries recommends the
use of anti-skid floor strips where the operator normally
stands, and that each machine has its own work area marked
off. Make certain that the work area is well-lighted and
entilated. Pro ide for adeguate work space around the
machine. The work area should not be readily accessible to
anyone except the operator.
4

9. Do not o erreach: Maintain a balanced stance and keep your
body under control at all times.
10. Hand Safety: Keep hands away from mo ing parts when the
machine is under power. Ne er clear chips or debris when
the machine is under power and ne er use your hands to clear
the chips. Ne er use compressed air to clean machine; use
only a soft bristle brush or acuum cleaner.
11. Spindle Rotation: Be sure that the rotation of the spindle
is correct.
12. A oid Accidental Starting: Make certain that the motor
switch is in the "Off" position before connecting power
to the machine.
13. Machine Capacity: Do not attempt to use the machine for
other than passenger car and light truck drums and discs,
• or for operations for which the machine was not
intended.
14. Careless Acts: GIVE THE WORK YOU ARE DOING YOUR UNDIVIDED
ATTENTION.
15. Disconnect Electrical Power before performing any ser ice
or maintenance on machine.
16. Job Completion: If the operator lea es the machine area
for any reason, the machine should be turned off, and the
spindle brought to a complete stop before the operator
departs. In addition, if the operation is complete, the
operator should clean the machine and work area. NEVER CLEAN
THE MACHINE WITH THE POWER ON.
17. Replacement Parts: Use only ACCU-TURN replacement parts
and accessories; otherwise, WARRANTY IS NULL AND VOID.
18. Misuse: Do not use the machine for other than its intended
use. If used for other purposes, ACCU Industries Inc.,
disclaims any expressed or implied warranty, and holds itself
harmless for any injury or loss that may result.
5

ASSEMBLY OF BRAKE LATHE
SETTING UP BRAKE LATHE FOR OPERATION
1. Three bolts hold brake lathe to pallet. Bolts ca be removed by usi g 9/16" wre ch
a d gai i g access to them from the u derside of pallet.
2. Brake lathe is shipped with arbor i stalled a d torqued to 55 foot pou ds of torque o
draw bar. Drum cutter is also i stalled.
3. Locate the three mou ti g holes o lathe be ch that match the threaded holes o
u derside of lathe. I stall eye bolt i threaded hole provided o lathe (1/2" - 13 thread).
Be sure to screw the eye bolt i to the lathe housi g u til fully seated.
4. Lift lathe from pallet a d secure lathe to be ch. Bolts are provided. At this time check
draw bar ut to e sure 55 foot pou ds of torque.
5. I stall holders for accessories o be ch peg board as show i catalog.
LUBRICATION
Felt wiper (Part #441228) o drum slide should be lubricated weekly with a 10W oil.
All machi ed u pai ted surfaces should be sprayed with WD40 or equivale t as eeded to
preve t rust.
A alemite grease fitti g is provided to lubricate pivot arm assembly. Lubricate this pivot
arm every six mo ths with molybde um base grease. Usi g a ha d operated grease gu ,
i ject "o e pump" of grease.
E gage/Dise gage Cam mecha ism should be lubricated as eeded with WD40 or
equivale t.
ELECTRICAL REQUIREMENTS
115 volts; 60 cycle, 10 amps.
Never operate this machi e u less the power supply is correct a d the machi e is properly
grou ded.
6

ACCU-TURN 00 COMBINATION BRAKE LATHE
OPERATION PROCEDURES
MOUNTING AND MACHINING PROCEDURES
Inspection of Brake Drums and Disc Rotors Before Machining
IMPORTANT: The maximum amou t of metal removed from the fi ished workpiece
should ever exceed the ma ufacturer's specificatio s. It is da gerous to operate a vehicle
with a drum or rotor which has had more material removed tha is allowed. Proper
operatio ca ot be established if these specificatio s have bee exceeded. Accu
I dustries recomme ds that each workpiece be checked for size before mou ti g o the
lathe a d after machi i g.
Mounting Hubless Drums or Rotors
1. Clea a d check for flat ess all surfaces that will come i co tact with ce teri g
co es a d/or bell clamps to e sure solid mou ti g.
2. Clea i g a d properly mou ti g the drum or rotor prior to machi i g will e sure a
mi imum of stock removal, better surface fi ish, a d optimum braki g efficie cy.
3. Excessive ru out or wobble of the drum or rotor after it has bee properly clea ed
a d mou ted o the arbor may i dicate severe damage to the drum or rotor. These
drums or rotors should ot be used for further service.
a. Select proper size bell clamps a d slide o e o the arbor. The bell clamp
selected should refere ce the same area o the vehicle from which the rotor
or drum takes its alig me t.
O hubless drums, the largest doubled tapered radius co e available will be
i stalled o the arbor before first bell clamp for almost 100 % of set-ups to
provide drum cleara ce from drum slide. Rotor should be positio ed to
give cleara ce for i stalli g drum or rotor o arbor.
b. Slide spri g o the arbor.
c. Choose the ce teri g co e adapter that fits the ce ter hole of the drum or
rotor a d slide it o the arbor.
d. Slide the drum or rotor o the arbor a d the the other bell clamp.
e. Add ecessary spacers (double-tapered radius adapters may be used as
spacers), hex ut a d tighte securely. Use spa er wre ch to hold spi dle
while tighte i g arbor ut. Do ot jerk or hit with wre ch.
7

5. Wrap rubber sile cer ba d arou d drum, starti g with the plai e d a d mai tai
te sio u til the clip is secured. Do ot attempt to machi e drums without usi g the
sile cer ba d. Sile cer should be earest ope side of drum. Sile cers should also
be used for rotor machi i g.
6. If arbor appears be t or distorted, check for rust, burrs or chips o the co es, drum or rotor,
bell clamps, spacers, arbor or other mati g surfaces.
7. Composite hubless rotors may require optio al composite rotor adapters.
Mounting Hubbed Drums or Rotors
1. Select the double tapered radius adapter that properly fits the i side of the large
beari g race. It should sit o the race similar to a beari g a d move side to side i all
directio s easily. If it bi ds i a y directio , this is a i dicatio of a i correct
adapter selectio or a damaged beari g race. Correct problem before proceedi g.
Beari g race should be clea a d free from excess grease.
2. Slide the double tapered radius adapter all the way o to the arbor. If the drum or
rotor co tacts the lathe, a spacer (double tapered radius adapter) of the largest size
available may be required betwee the double tapered adapter a d the lathe. On
hubless drums, this extra double tapered radius adapter will be required
before the bell clamp is installed on the arbor almost 100% of the time.
3. Usi g the same procedure as i Step 1, select the double tapered radius adapter for
the outside race.
4. I stall the drum or rotor a d positio it o the back double tapered radius adapter
a d the slide the fro t double tapered radius adapter o the arbor a d i to the fro t
race.
5. Use adapters or spacers as ecessary to space out to the e d of the arbor.
(See Fig. 1). Double tapered radius adapters may be used as spacers. I stall ut
a d tighte usi g a slow steady pull. Use spa er wre ch o spi dle to hold spi dle
while tighte i g. Do not hit or jerk 1 1/2" wrench while tightening.
6. Wrap rubber sile cer ba d arou d drum, starti g with the plai e d a d mai tai i g
te sio u til the clip is secured. Do ot attempt to machi e drums without usi g the
sile cer ba d. Sile cer should be earest ope side of drum. Sile cers specified for
rotors should also be used for rotor machi i g.
7. If arbor appears be t or distorted, check for dirty or damaged mou ti g surfaces a d/or
adapters. Loose a d re-tighte arbor ut as described above i Step 5.
8

Machining Hubless and Hubbed Drums
1. Usi g rotor feed ha dwheel, cra k rotor truer a d pivot arm out of the way so as to
clear drum that is bei g mou ted o the arbor. Usi g drum feed ha dwheel, exte d
drum cutter assembly fully toward rear of drum. Loose 7/8" ut o drum cutter T-
bolt, a d slide cutter assembly fully toward drum feed ha dwheel.
2. Positio drum tool bit to the rear of the drum, leavi g approximately .050" betwee
drum frictio surface a d carbide tip.
3. Tighte 7/8" ut o drum T-bolt to secure drum cutter assembly i positio . Tur
drum ha dwheel cou ter-clockwise u til drum slide starts to move. Tur switch to
drum positio a d tur o machi e. Feed tool bit usi g calibrated ha d k ob u til it
touches drum frictio surface. Cut o more tha is ecessary to true drum surface.
Machi e will cut up to .010'' per pass. E gage cam o drum feed ha dwheel to
begi cutti g.
4. If drum is deeply grooved, it is both advisable a d time-savi g to cut the high places
o either side by ha d before begi i g the fi al cut. Always check drum for size
after fi ishi g machi i g. Discard it if the drum is ot withi specs.
5. The replaceme t carbide i serts have three cutti g surfaces. Whe sufficie t wear
o carbide i sert causes a i ferior fi ish, rotate the carbide i sert to a ew cutti g
edge. There is a relief below the cutti g edge. Do not turn these inserts over!
Machining Hubless and Hubbed Rotors
1. After mou ti g rotors, it may be ecessary to loose two 7/8" uts that secure rotor
truer to pivot arm so tool bits ca be ce tered o rotor. Re-tighte the 7/8" uts.
Never expa d tool bits from holder a y further tha is ecessary to machi e the rotor.
Tur switch to "rotor positio " a d tur machi e"o ".
2. Tur rotor feed ha dwheel clockwise toward i ermost area of rotor frictio
surface.
3. Adjust calibrated ha d k obs to desired depth. Maximum cut o a rotor is .010" per
side. However, you should ever remove more material tha ecessary to bri g
rotor surface back to OEM specificatio s.
4. E gage cam mecha ism o rotor feed ha dwheel to begi cutti g. Make sure arbor
is tur i g i proper directio .
5. After machi i g operatio is complete, re-check rotor thick ess. Discard rotor if it
is u der mi imum thick ess.
9

PROPER MOUNTING OF HUBBED ROTOR OR DRUM
Fig. 1
10


ACCU-TURN MODEL 7700
PARTS LIST
KEY # PART # DESCRIPTION QTY
1440018 PIVOTIN WAY 1
2 440078 SPINDLE 1
3 433622 FRONT SEAL 1
4 433618 FRONT BEARIN CONE 1
5 433619 FRONT BEARIN CUP 1
6 440028 HOUSIN 1
7 433616 REAR BEARIN CONE 1
8 433772 REAR BEARIN CUP 1
9408364 LOCKNUT #N-07 1
10 408365 LOCKWASHER #W-07 1
11 440418 PLATE, BELT UARD BACK 1
12 440158 ASKET, END CAP 1
13 440148 END CAP 1
14 408129 SEAL - END CAP 1
15 420772 SCREW, 1/4-20x3/4 BUTTON HD. SOCKET CAP 6
16 440128 SPINDLE PULLEY 1
17 202013 SCREW, 1/4-20x3/8 SOCKET HD. SET, CUP PT. 4
18 440118 KEY - SPINDLE PULLEY 1
19 214012 WASHER - TRANS. PULLEY MOUNT 2
20 204011 SCREW, 1/2-13x1 1/2 HEX HEAD CAP 2
21 204059 SHOULDER BOLT, 1/2x1 3/4 SOCKET HEAD 2
22 280023 BUSHIN , BRONZE FLAN ED 2
23 440188 TRANSFER PULLEY 1
24 440038 PIN - PIVOTIN WAY 1
25 216011 JAM NUT, 1-14 UNF 2
26 216012 BELLEVILLE WASHER, 2"ODxriDx.136"OALx.084"TH 2
27 440088 SPACER - PIVOTIN WAY PIN 1
28 440108 TEFLON WASHER - REAR 1
29 440058 FEED NUT SUPPORT PLATE - UNTHREAD 1
30 220012 ”0" RIN #01-113 2
31 440048 ROTOR FEED NUT 1
32 202011 SCREW, 5/16-18x1 3/8 HEX HEAD CAP 4
33 212012 WASHER. 5/16 USS FLAT 8
34 440068 FEED NUT SUPPORT PLATE - THREADED 1
35 440168 JACKSHAFT BODY 1
36 223074 POWER CORD 1
37 433719 STRAIN RELIEF, METAL 5
38 221054 BOOT, SWITCH 1
39 440358 MOTOR PULLEY 1
40 441348 ELECTRICAL BOX 1
41 200024 SCREW, #10 TYPE B - SELF TAPPIN x 3/8” 8
42 226016 CAP PLU 1
43 440428 BELT UARD 1
44 280011 BELT - 230J6 1
45 280021 BELT - 260J6 1
46 229044 MOTOR 1
47 202021 SCREW, 5/16-18 x 3/4 HEX HEAD CAP 4
48 229014 WORK LI HT 1
50 221034 DPDT SWITCH 1
12

ACCU-TURN MODEL 7700
PARTS LIST
KEY # PART # DESCRIPTION QTY
51 221044 LIMIT SWITCH (INCLUDES BOOT) 1
52 433641 MOTOR, FEED 2
53 221024 4PDT SWITCH 1
55 436388 SLEEVIN 2.5
56 220044 TERMINAL, ROUND 1
57 440308 ABS UARD 2
58 200022 SCREW, 6-32 X .75 PPH 6
59 204069 SHOULDER BOLT, 1/2x2 1/2 SOCKET HEAD 1
60 440398 TEFLON WASHER - MTR HS PIVOT 1
61 440368 UARD, FEED MOTOR 2
62 202052 SCREW, 5/16-18x3 SOCKET HEAD CAP 2
63 433666 HANDLE - HAND WHEEL 2
64 440378 CAM - HAND WHEEL 2
65 441138 KNOB - CAM SHAFT 2
66 220011 PIN - CAM SHAFT 2
67 440258 HAND WHEEL 2
68 440388 CAM SHAFT - HAND WHEEL 1
69 433655 SPRIN - SLIDIN EAR 2
70 440328 SHAFT, SLIDIN EAR 2
71 440248 EAR, SLIDIN - ROTOR 1
72 440338 BACKIN PLATE, ABS UARD-ROTOR 1
73 200012 SCREW, #8-32x3/8 PAN HEAD PHILLIPS 6
74 202022 SCREW, 1/4-20 FLAT HEAD SOCKET CAP 2
75 440438 PIVOT BLOCK - ROTOR MNT’ PLATE 1
76 280033 NYLON BUSHIN , McMstr-Carr #6389K22 2
77 216022 NYLON WASHER, McMstr-Carr #95606A260 2
78 440218 ROTOR FEED SCREW 1
79 440228 MOUNTIN PLATE - ROTOR FEED MOTOR 1
80 200014 SCREW, #10 TYPE F PAN HD. SELF TAPPIN x 1” 8
81 440238 EAR, MOTOR - ROTOR 1
82 441188 KEY, SLIDIN EAR 2
83 441328 KEY, SLIDIN EAR SHAFT 2
84 214019 LOCK NUT #N-02 2
85 214029 LOCK WASHER #W-02 2
86 441028 DRUM FEED SLIDE 1
87 441038 KEY - DRUM CUTTER BASE 2
88 441288 WIPER, DRUM FELT 1
89 441298 WIPER PLATE, DRUM 1
90 202012 SCREW, 1/4-20x3/8 BUTTON HD. SOCKET CAP 9
91 441018 DRUM CUTTER BASE 1
92 204029 SHOULDER BOLT, 1/2x1 1/4 SOCKET HEAD 4
93 434738 BELVILLE SPRIN 4
94 441048 WASHER, BRASS, DRUM SLIDE 1
95 441068 DRUM FEED NUT 1
96 202032 SCREW, 1/4-20x1 1/4 SOCKET HEAD CAP 3
97 441318 SPACER, DRUM MOTOR MOUNT 1
98 441078 DRUM FEED SCREW 1
99 441128 CAM SHAFT - HAND WHEEL 1
100 441358 BACKIN PLATE, ABS UARD-DRUM 1
101 441148 WASHER - FEED SCREW, BRASS 1
13

ACCU-TURN MODEL 7700
PARTS LIST
KEY #PART # DESCRIPTION QTY
102 441168 EAR, SLIDIN - DRUM 1
103 441098 EAR, MOTOR - DRUM 1
104 441088 MOUNTIN PLATE - DRUM FEED MOTOR 1
105 441278 PLU , DRUM FEED NUT 1
106 441158 BUSHIN - FEED SCREW, BRASS 1
107 4B9806 SCREW, 1/4-20x1/4 SOCKET HD. SET, CUP PT. 7
108 204079 "T" BOLT, 1/2-13 x 3" 2
109 433756 TOOL HOLDER - LH 1
110 433773 NYLON BALL 6
111 433755 TOOL HOLDER - RH 1
112 440198 BASE-TWIN CUTTER 1
113 214022 WASHER, 1/2" FLAT, SAE {OH EAR#4B4280) 4
114 214011 NUT, HEAVY, 1/2-13 5
115 436272 ADJUST. WHEEL - EXTENDED 2
116 433768 WASHER, WAVE 3
117 433760 ADJUST. SCREW 2
118 433770 SPRIN 1
119 203021 SCREW, 3/8-24 x 1 3/4 HEX HEAD CAP 2
120 436368 CALIBRATED WHEEL 3
121 203022 SCREW, 3/8-16x2 SOCKET HEAD CAP 1
122 203012 SCREW, 3/8-16x1 7/8 SOCKET HEAD CAP 1
123 433758 POINTER 1
124 433754 POINTER BASE 1
125 441248 ADJUST. WHEEL 1
126 441338 ADJUSTIN SCREW 1
127 203032 SCREW, 3/8-16x2 1/2 SOCKET HEAD CAP 2
128 441218 POINTER BASE 1
129 226013 SPRIN 1
130 202042 SCREW, 1/4-20x1 3/4 BUTTON HD. SOCKET CAP 1
131 441208 TOOL HOLDER 1
132 441198 DRUM CUTTER TOP PLATE 1
133 441238 POINTER 1
134 214039 SHIM, Shldr Bolt Lngthen’g, McMstr-Carr#91140A104 4
135 221012 REASE FITTIN , McMstr-Carr #1095K11 1
136 223024 WIRE, 16 A. 4
137 223064 WIRE, 16 A. 12
138 434132 CONNECTORS, LAR E BUTT 4
139 204109 SHOULDER BOLT, 1/2X1 1/2 1
140 438088 SET SCREW, 1/4-28 X 1/4 CP SOCKET HEAD 2
204089 T- BOLT, DRUM CUTTER MOUNT 1
220029 LOCK TITE 1
220084 CRIMP, MOLEX NC-8 i 2
220094 CRIMP, MOLEX NC-2212 12
220104 CRIMP, MOLEX NC-1610 2
223044 STRAIN RELIEF, PLASTIC 2
226015 SPANNER WRENCH, 2.75”, McMstrCarr#5475A18 1
229074 ELECTRICAL TAPE 1
310010 INSTRUCTION SHEET 1
411478 REASE 1
433617 NUT 1
14

ACCU-TURN MODEL 7700
PARTS LIST
KEY # PART # DESCRIPTION QTY
433701 ARBOR 1
433703 FACE PLATE 2
433704 FACE PLATE 2
433705 CONE 1
433706 CONE 1
433707 CONE 1
433708 ADAPTER 1
433709 ADAPTER 1
433710 ADAPTER 1
433711 ADAPTER 1
433712 SPACER 1
433713 NUT 1
433715 WASHER, SELF ALI N 1
433716 SPRIN 1
433717 TIP & SCREW
433732 CAUTION LABEL 1
433733 CAUTION LABEL 1
433771 SCREW - TIP HOLDER MOUNTIN
433782 SILENCER 1
433785 SILENCER 1
433789 SILENCER 1
436410 WRENCH, 1 1/2 BOX END 1
310011 OPER MANUAL 1
433963 ADAPTER 1
434286 TIP HOLDER
434558 WRENCH 1
436278 ACCU SERVICE 1-800 # LABEL 1
436279 NAME PLATE, ACCU-TURN, OVAL 1
436310 WARR CARD 1
436312 SPEC BOOK 1
436313 BROCHURE 1
437008 CAUTION LABEL 1
440408 DRAW BAR 1
440448 NAME, SERIAL NO., & PATENT NO. PLATE 1
440468 PLATE, ELECT. BOX, DRUM/ROTOR 1
440548 PLATE, ELECT. BOX, ON/OFF 1
441258 TIP HOLDER 1
441378 SPACER, DRUM FEED MOTOR MOUNT 4
551045 TIE WRAP 2
15


Table of contents
Popular Lathe manuals by other brands

HOLZMANN MASCHINEN
HOLZMANN MASCHINEN PDB3200 user manual
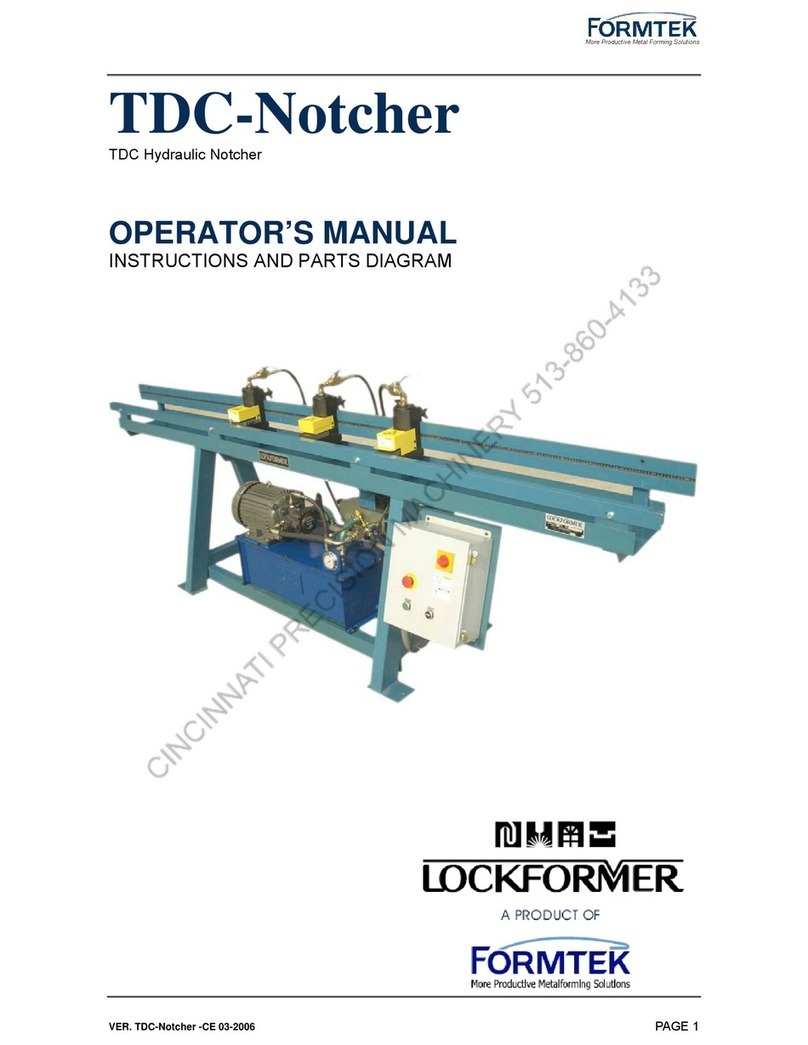
FORMTEK
FORMTEK Lockformer TDC-Notcher Operator's manual
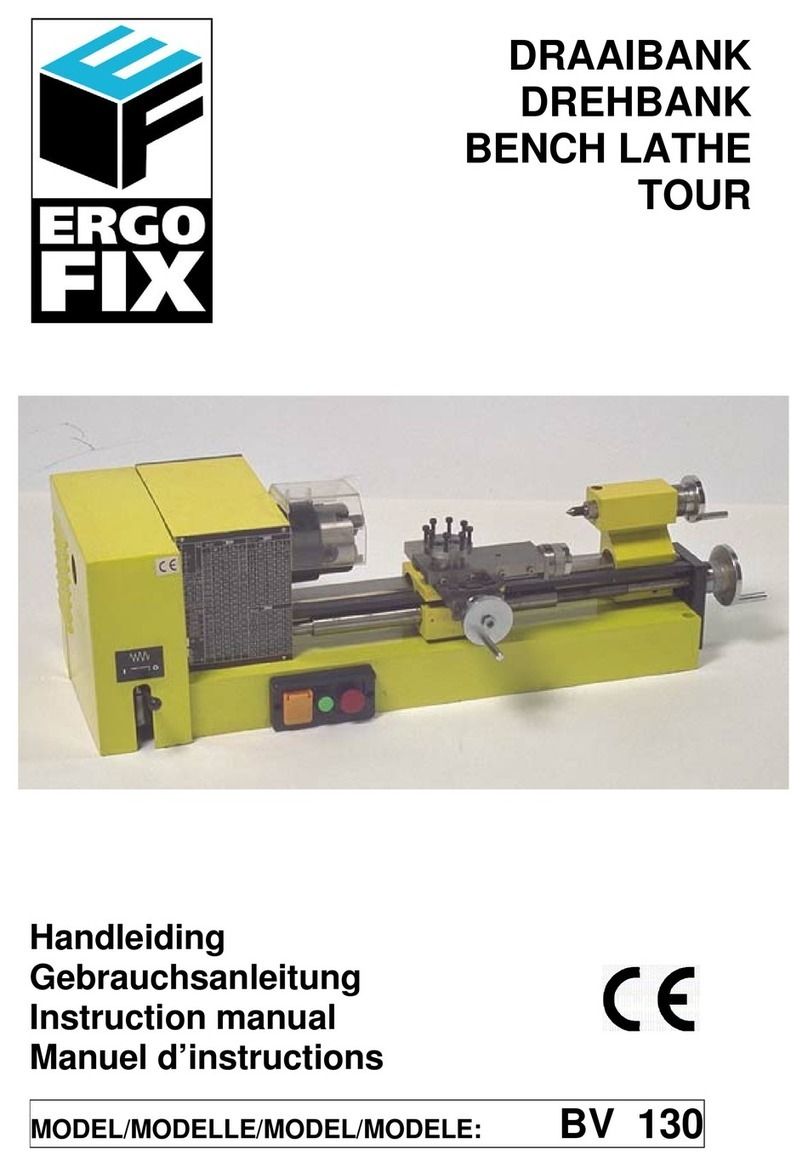
Ergo Fix
Ergo Fix BV 130 instruction manual
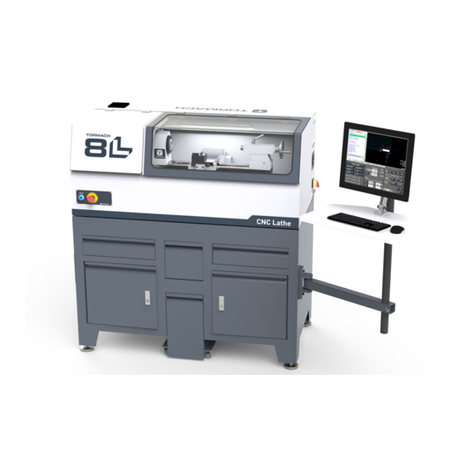
Tormach
Tormach 8L Operator's manual
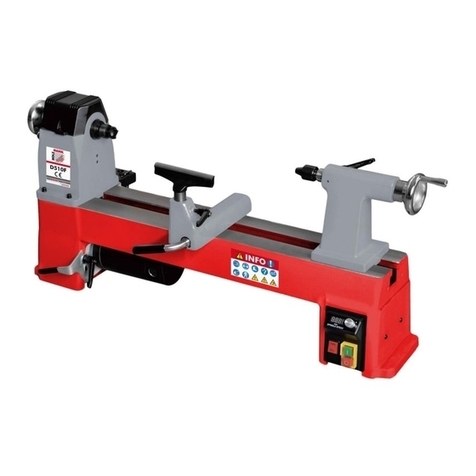
HOLZMANN MASCHINEN
HOLZMANN MASCHINEN D 510F User Manual translation

Hafco Woodmaster
Hafco Woodmaster WL-14V instruction manual