Actisense EMU-1 Series User manual

EMU-1
Engine Monitoring Unit
Analogue to NMEA 2000®
User Manual
For variant:
EMU-1-BAS
Issue 1.06

NMEA 2000 Engine Monitoring Unit - EMU-1
Page 3© 2015 Active Research Limited
Contents
Company information 4
Important Notices 5
Trademarks and Registered Trademarks 5
Fair use Statement 5
Technical Accuracy 5
Product Registration 5
Product Guarantee 5
Product Disposal 5
Product Overview 6
Figure 1 - Example of an EMU-1 Installation 6
Package Contents 6
Installation Warnings 7
Installation Order 8
Selecting a Mounting Location 8
Figure 2 - Example of a Typical Installation 8
Wiring Loom Lengths 9
Installations without Gauges 9
Installations with Gauges 9
Figure 3 - Connecting to Senders 9
Figure 4 - Connecting to Gauges 9
Mounting the EMU-1 10
Bulkhead Mounting 10
DIN Rail Mounting 10
Figure 5 - Mounting Options 10
Connecting to an NMEA 2000 Network 11
NMEA 2000 Networks 11
NMEA 2000 Minimum Network Requirements 11
Figure 6 - NMEA 2000 Minimum Network Requirements Diagram 11
Gauge Input Connections 12
Insulated Terminal Sender with Gauge 12
Insulated Terminal Sender without Gauge 12
Standard Grounded Sender with Gauge 12
Standard Grounded Sender without Gauge 12
Figure 7 - Gauge Input Connection Examples 12
Alarm Input Connections 13
Figure 8 - Alarm Input Connection Examples 13
Tacho Input Connections 14
Ignition Coil 14
Alternator 14
Hall Effect and Electronic Pulse Senders 14
Inductive Senders 14
Figure 9 - Tacho Input Connections 14

NMEA 2000 Engine Monitoring Unit - EMU-1
Page 5© 2015 Active Research LimitedPage 4© 2015 Active Research Limited
Important Notices
Calculating Tacho PPR 15
Auxiliary Input Connections 15
Battery Voltage Sensing 15
Power Requirements 15
Connecting the Power 15
Grounding Requirements 15
Factory Conguration 16
Conguring the EMU-1 16
Conguration Requirements 16
Troubleshooting Guide 17
Technical Support and the Returns Procedure 17
NMEA 2000 PGN List 18
Dimension Diagram 18
Figure 14 - Dimension Diagram 18
Specications 19
EMU-1 Product Order Codes 20
The EMU-1 has been certied to comply with the European directive for Electromagnetic Compatibility
(EN60945) and is appropriately CE marked. Operation of the unit should be in conjunction with appropriate
CE approved shielded connectors and cabling used in accordance with the CE directive EN60945. Any
EMC related issues should be reported to Active Research Limited immediately to allow the company to
rectify or resolve EMC related problems in accordance with its obligations under EN60945.
If the unit is connected such that compliance failure occurs beyond the company’s control, the company shall not be
held responsible for compliance failure until suitable EMC guidelines for connection are seen to have been taken.
Trademarks and Registered Trademarks
Actisense® and the Actisense logo are registered trademarks of Active Research Limited. All other trademarks are the
property of their respective owners.
The NMEA® name and NMEA logo are copyright held by the NMEA. All uses in this manual are by permission and no
claim on the right to the NMEA name or logo are made in this manual.
Fair use Statement
The contents of this manual may not be transferred or copied without the express written permission of Active Research
Limited.
Copyright © 2013 Active Research Ltd. All rights reserved.
Technical Accuracy
To the best of our knowledge the information contained in this document was correct at the time it was produced. Active
Research Ltd cannot accept liability for any inaccuracies or omissions.
The products described in this manual and the specications thereof may be changed without prior notice. Active
Research Ltd cannot accept any liability for differences between the product and this document. To check for updated
information and specications please contact Active Research Limited.
Active Research Limited will not be liable for infringement of copyright, industrial property rights, or other rights of a third
party caused by the use of information or drawings described in this manual.
Product Registration
Please register your product via the online form.
Your product package includes a unit serial number. The serial number is six digits and can be found below the barcode
on the white label on the top of the EMU-1. Alternatively, if your EMU-1 is inaccessible, you will nd the serial number
under the product information on the ‘network list’ page of an NMEA 2000 MFD.
Your registration will assist Actisense Support to link your product to your details, simplifying any future assistance you
may require.
Product Guarantee
This product comes with a three year ‘return to base’ guarantee. If you suspect that the unit is faulty please refer to the
“Troubleshooting Guide” on page 17.
It is a requirement of the guarantee that all installations of electronic equipment follow the NMEA 0400 specication. Any
connection to a battery or power supply must meet the mandatory essential safety requirements that may be
imposed by local regulatory agencies.
Actisense products are intended for use in a marine environment, primarily for below deck use. If a product
is to be used in a more severe environment, such use may be considered misuse under the Active Research
Limited guarantee.
Product Disposal
Please dispose of this product in accordance with the WEEE Directive. The product should be taken to a registered
establishment for the disposal of electronic equipment.
Company information
Active Research Ltd
Unit 5 Wessex Trade Centre
Ringwood Road
Poole, Dorset
UK, BH12 3PF
Telephone: +44 (0)1202 746682
Email: [email protected]
Web: www.actisense.com

NMEA 2000 Engine Monitoring Unit - EMU-1
Page 7© 2015 Active Research LimitedPage 6© 2015 Active Research Limited
All warnings and notices must be followed to ensure the correct operation of the EMU-1. Incorrect
installation may invalidate the guarantee.
It is highly recommended that all of the installation instructions are read before commencing the installation.
There are important warnings and notes throughout the manual that should be considered before the
installation is attempted.
Warning 1: Accuracy
The Actisense EMU-1 is designed to reliably measure voltage levels on senders and sensors; the accuracy is reliant
upon the correct installation and the correct conguration of the EMU-1. Furthermore the information present in the
associated NMEA 2000 PGN’s which are output by the EMU-1 depends on conguration parameters being set correctly.
Therefore, the EMU-1 should only be used as an aid to vessel monitoring, control or navigation and should not be used
as a replacement for traditional aids and techniques.
Warning 2: Installation and Operation
This product must be installed and operated in accordance with the instructions provided. Failure to do so could result
in personal injury, damage to your boat and/or poor product performance.
Warning 3: Installation Code of Practice
When wiring the power supply to the EMU-1 ensure the isolation switch is off. Wiring the EMU-1 while the connection is
live may damage the EMU-1 and is in breach of the guarantee.
All wiring should be in accordance with the regional code of practice for installations.
Warning 4: Firmware Updates
It is highly recommended that the Firmware is kept up to date in the EMU-1. Please check to ensure your EMU-1
shipped with the latest Firmware. You can do this by locating the manufacturers software ID for your EMU-1 on the
network list found in most NMEA 2000 displays or using our freely available NMEA Reader. The latest rmware version
number and details of supporting software such as NMEA Reader can be found on the EMU-1 downloads web page.
Warning 5: NGT-1 Support
It is highly recommended that an NGT-1 (either USB or ISO variants) be available for every EMU-1 installation. The
NGT-1 can be used to update the Firmware, connect to the Conguration Tool and display data on a PC running
compatible software. Details of the NGT-1 can be found here www.actisense.com/NGT-1.
Warning 6: Mounting Requirements
Select a at location to mount the EMU-1. Mounting on a contoured surface may cause damage to the case.
Do not mount the EMU-1 while the device is powered.
Do not mount the EMU-1 while the NMEA 2000 cable is connected.
Do not mount the EMU-1 while the engine cable harness is connected.
Note that the terminals are pluggable for easy disconnection when mounting or removing the EMU-1.
Warning 7: Mounting Locations
Do not mount the EMU-1 in the same plane as transmitting or receiving antennas.
Do not mount the EMU-1 close to an electronic compass.
Warning 8: Wire Noise
Avoid running noisy wires (such as those connected to ignition coils) adjacent to sensitive gauge or alarm wires as
noise may be induced into these wires and this may result in inaccurate measurements and corresponding inaccurate
data being output to the NMEA 2000 bus.
The EMU-1 converts data from analogue engine senders into NMEA 2000 compatible data, allowing modern NMEA
2000 display devices to monitor the engine data and associated gauge levels aboard a vessel.
The unit has been designed to connect in parallel to an existing gauge, so existing instruments can still be used. The
EMU-1 can also be used straight from the sender without a gauge being present. In effect the EMU-1 can be installed
for most engine makes and models.
The EMU-1 provides 6 dedicated Gauge inputs, capable of measuring the output from the required engine senders. The
unit also provides 4 Alarm inputs (e.g. high temp, low pressure), 2 Tacho inputs, and 2 user denable Auxiliary inputs.
See the EMU-1 FAQs section to nd which senders are supported. See “Table 3 - NMEA 2000 PGN List” on page 18 for
a list of NMEA 2000 PGNs that the EMU-1 supports. Refer to the EMU Cong Tool User Manual on the EMU-1
downloads page for instructions on how to congure the EMU-1.
Product Overview
Gauges and Indicators are Optional
Low Oil Pressure
Indicator
High Engine
Temperature
Indicator
Alternator
W Connection
Oil Pressure Sender
10 – 180 Ohms
VDO (0 to 80 PSI /
0 to 5 Bar) Euro
Temperature
Switch
12V Negative
Temperature Sender
700 – 22 Ohms
VDO (40 to 120°C) Euro
Pressure
Switch
12V Negative
RPM Gauge Engine Temperature Gauge Oil Pressure Gauge
NMEA 2000 Backbone
V Supply
Figure 1 - Example of an EMU-1 Installation
Package Contents
1 x EMU-1-BAS with pluggable screw terminals and NMEA 2000 dust cover.
1 x Actisense CD in sleeve (Documents and Software)
1 x EMU-1 user manual
1 x Connector cover
4 x Connector cover screws
4 x Mounting screws
Accessories Supplied Separately
NGT-1 (either USB or ISO variant) for conguring the EMU-1
DIN-KIT-1 mounting kit for use with DIN rails
Installation Warnings
Note: Wire colours are for reference only
!

NMEA 2000 Engine Monitoring Unit - EMU-1
Page 9© 2015 Active Research LimitedPage 8© 2015 Active Research Limited
Selecting a Mounting Location
“Figure 2 - Example of a Typical Installation” shows an example installation. This gives an idea of the connections
that need to be made to install the EMU-1. All these connections need to be considered before selecting an installation
location. Refer to “Warning 7: Mounting Locations” on page 7.
Installations without Gauges
The EMU-1 can be used on senders where the analogue
gauges are not present, connecting directly to the sender
to be measured. In this case it is recommended that the
EMU-1 be mounted close to the engine. The cable length
between the sender and the EMU-1 should typically not
exceed 2 metres.
Installations with Gauges
The EMU-1 can be used in parallel with existing gauges to
compliment the information already displayed. In this case
it is recommended that the EMU-1 be mounted close to
the gauges (instrument panel). The cable length between
the gauges and the EMU-1 should typically not exceed 2
metres.
Engine Monitoring Unit
AUX
+VE
GND
NMEA
DATA
2000®
Tx
Rx
GAUGE ALARM TACH
PWR
G1
G2
G3
G4
G5
G6
A1
A2
A3
A4
X1
X2
12 3 4 5 6 12 3 4 1 2
EMU-1
1 2
T1+
T1
T2+
T2
Gauges and indicators are optional
NMEA 2000 power source does not
need to share a ground with the EMU-1
Fuse Box
Ignition
EMU-1 and supply
have the same ground
Engine has the
same ground
as the EMU-1
Gauges have the
same ground
as the EMU-1
-
s
+
-
s
+
Ignition
Gauge Gauge
Indicator
Battery
Terminated and powered
NMEA 2000 network
Figure 2 - Example of a Typical Installation
Engine Monitoring Unit
AUX
+VE
GND
NMEA
DATA
2000®
Tx
Rx
GAUGE ALARM TACH
PWR
G1
G2
G3
G4
G5
G6
A1
A2
A3
A4
X1
X2
12 3 4 5 6 12 3 4 1 2
EMU-1
1 2
T1+
T1
T2+
T2
Maximum
2 metres
Engine Monitoring Unit
AUX
+VE
GND
NMEA
DATA
2000®
Tx
Rx
GAUGE ALARM TACH
PWR
G1
G2
G3
G4
G5
G6
A1
A2
A3
A4
X1
X2
12 3 4 5 6 12 3 4 1 2
EMU-1
1 2
T1+
T1
T2+
T2
Maximum
2 metres
Gauge Gauge
Indicator
Figure 3 - Connecting to Senders Figure 4 - Connecting to Gauges
Wiring Loom LengthsInstallation Order
1. Select mounting location: Ensure the EMU-1 can be mounted in a suitable location relative to the NMEA 2000 bus
and the senders or gauges. See “Selecting a Mounting Location” on page 8.
2. Mount the EMU-1 to the bulkhead, cabinet or other suitable location. See “Mounting the EMU-1” on page 10.
3. Connect to the NMEA 2000 network. See “Connecting to an NMEA 2000 Network” on page 11.
4. Connect the Gauge inputs. See ”Gauge Input Connections” on page 12.
5. Connect the Alarm inputs. See “Alarm Input Connections” on page 13.
6. Connect the Tacho inputs. See “Tacho Input Connections” on page 14.
7. Connect the Power to the EMU-1. See “Power Requirements” on page 15.
8. Congure the EMU-1. See “Conguring the EMU-1” on page 16.
Note: Wire colours are for reference only
Note: Wire colours are for reference only

NMEA 2000 Engine Monitoring Unit - EMU-1
Page 11© 2015 Active Research LimitedPage 10© 2015 Active Research Limited
NMEA 2000 Networks
NMEA 2000 devices will only communicate with each
other when connected to a powered and correctly
terminated NMEA 2000 network. It is not enough to simply
connect two NMEA 2000 devices directly together.
All networks need to be powered and terminated correctly
to allow data to be transmitted reliably on the network.
T-Pieces are needed to connect each device to the
network. Additional cable lengths can be used between
any of the connectors to extend the length of the network.
Ensure the NMEA 2000 rules for cable length are adhered
to, see “Table 1 - NMEA 2000 Cable Length Rules”.
Table 1 - NMEA 2000 Cable Length Rules
Cable Type Max
Length
Per drop cable 6m
Sum of all drop cables 72m
Micro Backbone (terminator to terminator) 100m
Mini Backbone (terminator to terminator) 200m
NMEA 2000 Minimum Network
Requirements
All NMEA 2000 networks require a 12V DC supply.
In addition, a correctly functioning network will require the
following components :
• 1 x Power-T
• 2 x Terminating Resistors
• 2 x T-Pieces (one per connected device)
• 2 x NMEA 2000 Devices (such as the EMU-1)
All the required network parts can be supplied by
Actisense www.actisense.com/A2K.
Refer to “Figure 6 - NMEA 2000 Minimum Network
Requirements Diagram” for an example network. Note
that the diagram should not be used as an installation
guide. NMEA 2000 networks should only be installed
following the NMEA 0400 specication and all wiring
should be in accordance with the regional code of practice
for installations.
DIN rail clip (2 in pack)
Counter sunk PT screw (4 in pack)
M3.5 s/s self-tapping
pan-head screw (4 in pack)
Bulkhead Mounting DIN Rail Mounting
See “Connecting to an NMEA 2000 Network” on page 11 before nalising the installation location.
Bulkhead Mounting
• Use the EMU-1 as a template to locate and mark the drill holes for mounting. Do not attempt to drill the holes while
the EMU-1 is in position.
• Refer to “Warning 6: Mounting Requirements” on page 7.
• Four M3.5 stainless steel pan-head screws are provided with the EMU-1 for mounting to the bulkhead. If these
screws are lost, suitable alternatives may be used. Note: Using larger screws can damage the housing and invalidate
the guarantee.
• Secure directly to a bulkhead using the mounting screws provided with the unit.
Refer to the “Dimension Diagram” on page 18.
DIN Rail Mounting
Requirements:
• An Actisense DIN Rail Kit (not included with the EMU-1) Part Code: DIN-KIT-1
• A top hat rail, type EN 50 022 or a G section rail, type EN 50 035.
Mounting using a different rail type or an alternative mounting kit may breach the terms and conditions of the guarantee.
Method:
• Refer to “Warning 6: Mounting Requirements” on page 7.
• Attach the mounting kit to the base of the EMU-1 with the kit supplied screws. There is provision to mount the EMU-1
vertically or horizontally (recommended). Using alternative screws may not be reliable or may result in damage to the
housing and invalidate the guarantee.
Figure 5 - Mounting Options
The EMU-1 has a male Micro connector as specied by the NMEA 2000 standard. This allows the EMU-1 to be
connected directly to an NMEA 2000 bus without complication. If you are using an alternative proprietary CAN bus
network, a suitable adapter cable will be required. It is recommended that the manual for any proprietary CAN bus
network devices be consulted to determine the suitability of connecting an NMEA 2000 device such as the EMU-1.
A certied NMEA 2000 cable is recommended for connection to the EMU-1. Ensure that the drop cable is no longer than
6 meters from the NMEA 2000 backbone, see “Table 1 - NMEA 2000 Cable Length Rules”. The cable connector
should be screwed securely to the EMU-1 connector to ensure reliable operation. It is recommended that the supplied
NMEA 2000 dust cover is left in place until the EMU-1 is connected to the NMEA 2000 network.
There are a number of indicator LEDs that can be used to diagnose the NMEA 2000 connectivity. Please refer to,
“NMEA 2000 Power LED (Red)”, “NMEA 2000 Rx LED (Green)” and “NMEA 2000 Tx LED (Orange)” on page 17
Connecting to an NMEA 2000 NetworkMounting the EMU-1
Power Tap
(A2K-MPT-1)
T-Peice
(A2K-T-MFF)
T-Peice
(A2K-T-MFF)
Terminator
(A2K-TER-F)
Terminator
(A2K-TER-M)
12v
Example Device Example Device
Figure 6 - NMEA 2000 Minimum Network Requirements Diagram

NMEA 2000 Engine Monitoring Unit - EMU-1
Page 13© 2015 Active Research LimitedPage 12© 2015 Active Research Limited
Gauge Input Connections
There are six Gauge inputs which are designed to be connected to existing engine senders (resistive type) either with
or without the gauge connected. In the case where no gauge is connected the EMU-1 automatically provides a feed to
the sender. A dual station sender must always have two gauges connected to it: the EMU-1 cannot replace one or both
of those gauges. If it is required to remove one or both gauges, the dual station sender will need to be replaced with a
single station sender.
Insulated Terminal Sender with Gauge
“Figure 7 - Gauge Input Connection Examples” G1 Input:
• The gauge power connection is connected to the same positive voltage supply as the EMU-1.
• The gauge ground connection is connected to the same ground as the EMU-1.
• The gauge signal connection is connected to the sender signal line.
• The sender return connection is connected to the same ground as the EMU-1.
• The EMU-1 Gauge input is connected to the gauge signal line, typically with a cable run that does not exceed 2
metres with a minimum 0.5mm wire diameter (24 AWG).
Insulated Terminal Sender without Gauge
“Figure 7 - Gauge Input Connection Examples” G2 Input:
• The senders return connection is connected to the same ground as the EMU-1.
• The EMU-1 Gauge input is connected to the sender signal line, typically with a cable run that does not exceed 2
metres with a minimum 0.5mm wire diameter (24 AWG).
Standard Grounded Sender with Gauge
“Figure 7 - Gauge Input Connection Examples” G4 Input:
• The gauge power connection is connected to the same positive voltage supply as the EMU-1.
• The gauge ground connection is connected to the same ground as the EMU-1.
• The gauge signal connection is connected to the sender signal line.
• The sender chassis is connected to the same ground as the EMU-1.
• The EMU-1 Gauge input is connected to the gauge signal line, typically with a cable run that does not exceed 2
metres with a minimum 0.5mm wire diameter (24 AWG).
Standard Grounded Sender without Gauge
“Figure 7 - Gauge Input Connection Examples” G3 Input:
• The sender chassis is connected to the same ground as the EMU-1.
• The EMU-1 Gauge input is connected to the sender signal line, typically with a cable run that does not exceed 2
metres with a minimum 0.5mm wire diameter (24 AWG).
Note: The examples given are not limited to the input they are shown with. E.g. the G1 Input example can also be
connected to any of the other Gauge inputs. Each input will accept any of the gauge / sender examples described.
Figure 7 - Gauge Input Connection Examples
Alarm Input Connections
There are four Alarm inputs which are designed to be connected to existing alarm type switches. The EMU-1 can be
used with or without the alarm indicator (e.g. lamp or buzzer) connected. If there is no alarm indicator, a suitable resistor
can be used in its place. For 12 V supplies it is recommended to use a 1 kΩ, ¼ W resistor, for 24 V supplies it is
recommended to use a 1 kΩ, 1 W resistor. Some alarm switches are incorporated into their relevant sender and are
also suitable to connect to the EMU-1.
There are several different combinations of switch type and wiring method that the EMU-1 Alarm inputs are compatible
with.
Supported Switch and Installation Types
• Normally Open switches (see Figure 8 Examples A1 and A4).
• Normally Closed switches (see Figure 8 Examples A2 and A3).
• Active High (see Figure 8 Examples A3 and A4).
• Active Low (see Figure 8 Examples A1 and A2).
Critical Circuit Requirements
• The switch circuits positive supply is the same as the supply used to power the EMU-1.
• The switch circuits negative supply (ground) is the same as the EMU-1 power ground.
• The switch circuit has a load (e.g. buzzer, lamp or resistor) in series with the switch between the positive supply and
ground.
• The EMU-1 Alarm input is connected between the switch and the load (e.g. buzzer, lamp or resistor).
Additional Information
• If the EMU-1 is connected at the switch, the cable run should not typically exceed 2 metres.
• If the EMU-1 is connected at the buzzer or lamp, the cable run should not typically exceed 2 metres.
• If replacing the buzzer or lamp with a resistor this should be done as near to the EMU-1 as possible, in this case the
cable run should not typically exceed 2 metres.
Please refer to the examples shown in “Figure 8 - Alarm Input Connection Examples”
Note: The examples given are not limited to the input they are shown with. E.g. the A1 Input example can also be
connected to any of the other Alarm inputs. Each input will accept any of the switch and installation types listed above.
Each input will require the type of installation to be selected using the conguration tool provided.
Engine Monitoring Unit
AUX
+VE
GND
NMEA
DATA
2000®
Tx
Rx
GAUGE ALARM TACH
PWR
G1
G2
G3
G4
G5
G6
A1
A2
A3
A4
X1
X2
12 3 4 5 6 12 3 4 1 2
EMU-1
1 2
T1+
T1
T2+
T2
-
s
+
G1 Input
-
s
+
G4 Input
G2 Input G3 Input
V Supply
V Supply
V Supply
Engine Monitoring Unit
AUX
+VE
GND
NMEA
DATA
2000®
Tx
Rx
GAUGE ALARM TACH
PWR
G1
G2
G3
G4
G5
G6
A1
A2
A3
A4
X1
X2
12 3 4 5 6 12 3 4 1 2
EMU-1
1 2
T1+
T1
T2+
T2
A1 Input A3 Input
A2 Input A4 Input
V Supply
V Supply
V Supply V Supply
V Supply
Figure 8 - Alarm Input Connection Examples
Note: Wire colours are for reference only
Note: Wire colours are for reference only

NMEA 2000 Engine Monitoring Unit - EMU-1
Page 15© 2015 Active Research LimitedPage 14© 2015 Active Research Limited
Power Requirements
Connecting the Power
• Refer to “Warning 3: Installation Code of Practice” on page 7.
• The EMU-1 should be powered from the same supply as the gauges / senders.
• The EMU-1 requires a power source providing between 9 and 35 Volts DC.
• Connect the positive supply wire to the ‘PWR +VE’ screw terminal of the EMU-1.
• Connect the negative / ground supply wire to the ‘PWR GND’ screw terminal of the EMU-1.
• Once connected, turn on the supply. For details on the Power indicator, refer to “EMU-1 Power LED (Blue)” on
page 17.
Grounding Requirements
All measurements are taken relative to the ground power pin of the EMU-1. For both safety and accurate measurements,
it is important to understand the vessels grounding to ensure the EMU-1 is grounded at the appropriate place. The
EMU-1 should always be connected to a good ground connection point which is not susceptible to ground noise. It is
important that the EMU-1 ground is the same as the engine ground.
The EMU-1 should only be used with standard negative ground DC systems.
When the EMU-1 is connected to senders only (no gauges are connected), it is important that the EMU-1 ground is the
same as the engine ground.
Dual Engine Power Supply
When monitoring two engines using a single EMU-1, both engines and the EMU-1 must share the same power supply
if the gauges are to remain in circuit. If a seperate power supply must be used for each engine, either a seperate EMU-
1 is required for each engine or the gauges will need to be removed for the EMU-1 to correctly monitor the sensors of
both engines.
Tacho Input Connections
Auxiliary Input Connections
There are two Auxiliary inputs which are included for future expansion. Currently these inputs are disabled.
Ignition Coil
• Connect the negative connection of the ignition coil to the positive Tacho input of the EMU-1.
• The negative Tacho input of the EMU-1 should be left unconnected.
• Refer to the connection in “Figure 9 - Tacho Input Connections” and “Figure 10”.
• For calibration the PPR or the number of cylinders will need to be entered in the conguration
tool.
Alternator
• Connect the Tacho (AC Tap) or ‘W’ connection of the alternator to the positive Tacho input of
the EMU-1.
• The negative Tacho input of the EMU-1 should be left unconnected.
• Refer to the connection in “Figure 9 - Tacho Input Connections” and “Figure 11”.
• For calibration the PPR or the number of poles and the pulley ratio will need to be entered in
the conguration tool.
Hall Effect and Electronic Pulse Senders
• Connect the signal line of the sender to the positive Tacho input on the EMU-1.
• The negative Tacho input of the EMU-1 should be left unconnected.
• Refer to the connection in “Figure 9 - Tacho Input Connections” and “Figure 12”.
• For calibration the PPR or the number of teeth on the y wheel will need to be entered in the
conguration tool.
Inductive Senders
• Connect the positive signal line from the sender to the positive Tacho input of the EMU-1.
• Connect the negative signal line from the sender to the negative Tacho input of the EMU-1.
• Refer to the connections in “Figure 9 - Tacho Input Connections” and “Figure 13”.
• If the negative signal line is not available, the negative Tacho input of the EMU-1 should be left
unconnected, and the sender should be connected to the same ground as the EMU-1.
• Refer to the connection in “Figure 9 - Tacho Input Connections” and “Figure 12”.
• For calibration the PPR or the number of teeth on the y wheel will need to be entered in the
conguration tool.
-
s
+
V Supply
V Supply
-
+
Not
Connected
-
s
+
V Supply
W
V Supply
Not
Connected
-
s
+
V Supply
Not
Connected
-
s+
+
V Supply
s-
Engine Monitoring Unit
AUX
+VE
GND
NMEA
DATA
2000®
Tx
Rx
GAUGE ALARM TACH
PWR
G1
G2
G3
G4
G5
G6
A1
A2
A3
A4
X1
X2
12 3 4 5 6 12 3 4 1 2
EMU-1
1 2
T1+
T1
T2+
T2
V Supply
Figure 9 - Tacho Input Connections
Figure 10
Figure 11
Figure 12
Figure 13
Battery Voltage Sensing
The EMU-1 automatically measures the voltage across it’s supply inputs (marked ‘PWR +VE’ and ‘PWR GND’). This
value is provided in the battery status PGN.
Calculating Tacho PPR
The EMU-1 conguration tool allows the “ratio” to be congured. This ratio is usually referred to as the PPR (Pulses Per
Revolution). The engine manufacturer will usually be able to supply this ratio so it should not need to be calculated.
For an Alternator (“W”. “R” or “AC”) terminal connection it can be calculated from:
PPR = (Crank pulley diameter / Alternator pulley diameter) × (No.of poles in Alternator / 2)
For an inductive sender it is derived from the number of teeth on the ywheel:
PPR = No.of teeth on ywheel
For an ignition coil it can normally be calculated from
PPR = (No.of cylinders × 2) / (No.of strokes × No.of ignition coils)
Note: Wire colours are for reference only
There are two Tacho inputs which are designed to be connected
to existing engine senders either with or without the gauge
connected.
The Tacho inputs must be calibrated in the conguration tool.
The Pulses per Revolution (PPR) must be entered to allow the
correct RPM to be calculated by the EMU-1.
There are several different sender options that can be used to
generate NMEA 2000 RPM data. Each supported type is listed
below along with the information required to congure the input
using the conguration tool.

NMEA 2000 Engine Monitoring Unit - EMU-1
Page 17© 2015 Active Research LimitedPage 16© 2015 Active Research Limited
The conguration loaded into the EMU-1 is detailed in “Table 2 - Default EMU-1 Input Conguration”.
Connecting to any other type of sender without conguring the unit is likely to cause incorrect data to be output to the
NMEA 2000 bus. See “Conguring the EMU-1” for how to congure the unit.
Table 2 - Default EMU-1 Input Conguration
EMU-1 Input Gauge
G1 - Gauge 1 Temperature Sender 287 - 22Ω VDO (40 to 120°C) Euro
G2 - Gauge 2 Oil Pressure Sender, 10 - 180Ω, VDO (0 to 80 PSI / 0 to 5 Bar) Euro
G3 - Gauge 3 Disabled without conguration
G4 - Gauge 4 Disabled without conguration
G5 - Gauge 5 Disabled without conguration
G6 - Gauge 6 Disabled without conguration
A1 - Alarm 1 Temperature Switch (High Temp Alarm), Normally Open (V Negative)
A2 - Alarm 2 Pressure Switch (Low Oil Pressure Alarm), Normally Open (V Negative)
A3 - Alarm 3 Disabled without conguration
A4 - Alarm 4 Disabled without conguration
T1 - Tacho 1 Alternator, “W” Connection - 11.78 Pulses Per Revolution
T2 - Tacho 2 Disabled without conguration
X1 - Aux 1 Disabled without conguration
X2 - Aux 2 Disabled without conguration
Factory Conguration
Conguring the EMU-1
Conguration Requirements
To congure the EMU-1 the following is required:
• A working NMEA 2000 network.
• An NGT-1 (either the ISO or USB variant).
• A PC running the Actisense EMU-1 Conguration Tool. The tool is provided on the CD but it is recommended that the
latest version is downloaded from www.actisense.com/EMU-1/Downloads.
• Information about the senders/gauges being connected. Note: For the Tacho inputs additional information will be
needed, see “Tacho Input Connections” on page 14.
All instructions for conguring the EMU-1 can be found in the help menu of the conguration tool software.
Troubleshooting Guide
The majority of issues can be resolved by conrming the EMU-1 is connected correctly, refer to the LED
descriptions below to conrm the power and NMEA 2000 connections are operational. Once these connections
are conrmed, the analogue connections and conguration need to be checked. Refer to “Conguring the
EMU-1” on page 16.
LED Indicators
EMU-1 Power LED (Blue)
There is a power LED located above the power supply terminal connectors which is visible through the connector cover.
The LED ashes blue to indicate power and denotes the active mode of the unit.
The LED ashes 5 times a second when in Bootloader mode. This should be seen for the rst 2 seconds following
power on and when ‘connected’ to ActiPatch for updating. If the LED continues to ash 5 times a second after initial
power on, the unit no longer has its Firmware. In this case, connect the EMU-1 to Actipatch and reinstall the Firmware.
The LED ashes once a second when in Normal mode, this indicates the Firmware is running and the EMU-1 can be
congured and will connect to an NMEA 2000 network when available.
NMEA 2000 Power LED (Red)
There is a red LED located near to the NMEA 2000 connector which is visible through the main body of the EMU-1.
When the EMU-1 is connected to an NMEA 2000 network with a suitable power supply the LED will light. This does not
indicate that the bus is correctly terminated or that there is any data on the network. The LED will light regardless of
whether the EMU-1 has power to the terminal connections. The EMU-1 requires power on both the terminals and the
NMEA 2000 bus to function correctly. These two power supplies do not need to be the same or have the same ground.
The NMEA 2000 bus and EMU-1 power are isolated from each other within the EMU-1 as required in the NMEA 2000
specication.
NMEA 2000 Rx LED (Green)
There is an NMEA 2000 data receive LED located to the left of the terminal connectors which is visible through the
connector cover. The LED ashes green on reception of an NMEA 2000 PGN message that is in the PGN list, see
“Table 3 - NMEA 2000 PGN List” on page 18.
As this is a small list, a blank LED should not be interpreted as a failure to connect to the NMEA 2000 bus without
conrming that compatible PGNs are present on the bus.
NMEA 2000 Tx LED (Orange)
There is an NMEA 2000 data transmit LED located to the left of the terminal connectors which is visible through the
connector cover. The LED ashes orange on transmission of an NMEA 2000 PGN message.
Technical Support and the Returns Procedure
All installation instructions and any warnings contained in this manual must be applied before contacting Actisense
technical support. If the troubleshooting guide did not help resolve the problem and an error persists, please contact
Actisense technical support to help trace the issue before considering the return of the product. If Actisense support
concludes that the EMU-1 unit should be returned to Actisense a Returns Number will be issued by the support engineer.
The Returns Number must be clearly visible on both the external packaging and any documentation returned with the
product. Any returns sent without a Returns Number will incur a delay in being processed and a possible charge.

NMEA 2000 Engine Monitoring Unit - EMU-1
Page 19© 2015 Active Research LimitedPage 18© 2015 Active Research Limited
Specications
Table 4 - Specication Table
Table 3 - NMEA 2000 PGN List
PGN PGN Name Rx Tx Data Tx Rate
59392 ISO Acknowledge YES YES
59904 ISO Request YES NO
60160 ISO Transport Protocol, Data Transfer YES YES
60416 ISO Transport Protocol, Connection Management YES YES
60928 ISO Address Claim YES YES
65240 ISO Commanded Address YES NO
126208 NMEA Request/Command/Acknowledgement YES YES
126464 Rx & Tx PGN Lists NO YES
126720 Proprietary Fast-Packet YES YES
126996 Product Information NO YES
126998 Conguration Information NO YES
127488 Engine Parameters, Rapid Update NO YES 0.1 seconds
127489 Engine Parameters, Dynamic NO YES 0.5 seconds
127493 Transmission Parameters, Dynamic * NO YES 0.5 seconds
127505 Fluid Level * NO YES 2.5 seconds
127508 Battery Status NO YES 1.5 seconds
* Not enabled by default / Enabled by EMU Cong Tool
Supported NMEA 2000 PGNs
118.0
127.0
105.5
96.5
3.5
47.5
All measurements in mm
112.0
Dimension Diagram
Power Supply
Supply Voltage 9 to 35V DC
Supply Current Typically < 25mA @ 12V DC
Supply Protection
Continuous reverse polarity
protection and load dump
protection (meets SAE J1113)
Supply Connector Pluggable 2-way screw terminal,
3.5mm pitch
Supply Voltage
(NMEA 2000 port) 9 to 29V DC
Supply Current
(NMEA 2000 Port)
< 20mA @ 12V DC from NMEA
2000 bus
Load Equivalence Number
(NMEA 2000 Port) 1 LEN
Supply Protection
(NMEA 2000 Port)
Continuous reverse polarity
protection and overvoltage
protection to 40V
NMEA 2000 Port - In/Out
Compatibility NMEA 2000 compatible
Galvanic Isolation 2500V input to ground
Speed / Baud Rate 250kbps
NMEA 2000 connector M12 male (A coded) connector
Gauge Inputs
Voltage Range 0 to 35V DC
Input Impedance > 50kΩ
Sender Feed 0, 4 or 18mA
Accuracy <= 2%
Input Connector Pluggable 6-way screw terminal,
3.5mm pitch
Input Protection Overvoltage protection to ±40V
Alarm Inputs
Voltage Range 0 to 37V DC
Input Impedance > 50kΩ
Threshold Voltage Congurable, default is 5V
Alarm Polarity Congurable, default is alarm on
low input
Accuracy <= 2%
Input Connector Pluggable 4-way screw terminal,
3.5mm pitch
Input Protection Overvoltage protection to ±40V
Tacho Inputs
Voltage Range ±3 to ±60V
Input Impedance > 100kΩ to ground
Input Pulse Range 4 to 50,000Hz
Accuracy <= 1%
Sender Compatibility
Ignition coil, alternator (“W”, “R” or
“AC”) terminal, hall effect, VR or
inductive sender
Threshold Automatically adjusts to signal
level
Input Connector Pluggable 4-way screw terminal,
3.5mm pitch
Input Protection Can withstand an ignition pulse to
±500V
Engine Log
Engine Hours
2 separate engine hour logs
internally connected to the tacho
Inputs. Hours are logged when
RPM is present, stored in non-
volatile memory
Mechanical
Housing Material Polycarbonate
Protective Lid Material Polycarbonate
Sealing Materials
Expanded silicone foam gasket,
closed cell polyurethane splash
guard and ePTFE waterproof vent
Dimensions 127mm (L) x 112mm (W)
x 48mm (H)
Weight 250g
Mounting
4 x 3.5mm lugs to allow panel
mount with self tapping s/s screws
(included), optional DIN Rail
mount available on request
Approvals and Certications
Fully NMEA 2000 Certied
EMC EN 60945 (sections 9 & 10)
Environmental Protection IP66 (PCB housing)
Operating Temperature -20°C to +55°C
Storage Temperature -30°C to +70°C
Relative Humidity 0 to 93% RH
Guarantee 3 years
Figure 14 - Dimension Diagram
All specications are taken with reference to an ambient temperature (TA) of +25°C.

Page 20© 2015 Active Research Limited
Product Code Product Description
EMU-1-BAS Engine Monitoring Unit, Analogue to NMEA 2000, standard conguration
Product Code Accessory Description
NGT-1-USB NMEA 2000 PC interface, standard version with USB
NGT-1-ISO NMEA 2000 PC interface, specialist version with RS422 serial
DIN-KIT-1 Kit of 2 clips & 4 screws. Use with EMU-1-BAS & NBF-3-BAS on top hat (EN 50 022) or G
section (EN 50 035) rails
STNG-A06045 SeaTalkNG to NMEA 2000 adaptor cable (drop).
EMU-1 Product Order Codes
®
Active Research Ltd
Unit 5, Wessex Trade Centre
Ringwood Road
Poole, Dorset
UK, BH12 3PF
Telephone: +44 (0)1202 746682
Email: [email protected]
Web: www.actisense.com
This manual suits for next models
1
Table of contents
Other Actisense Measuring Instrument manuals
Popular Measuring Instrument manuals by other brands

Bruker
Bruker D8 Discover Standard operating procedure
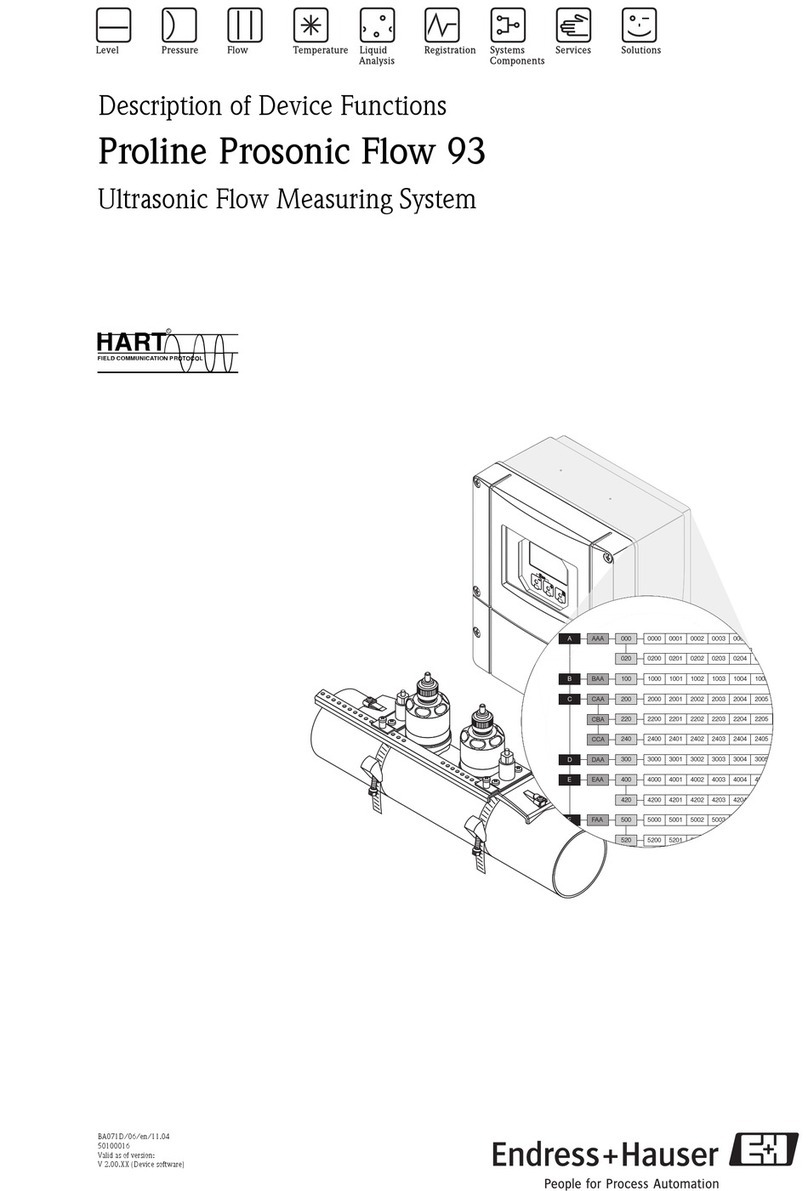
Endress+Hauser
Endress+Hauser Proline Prosonic Flow 93 Function manual
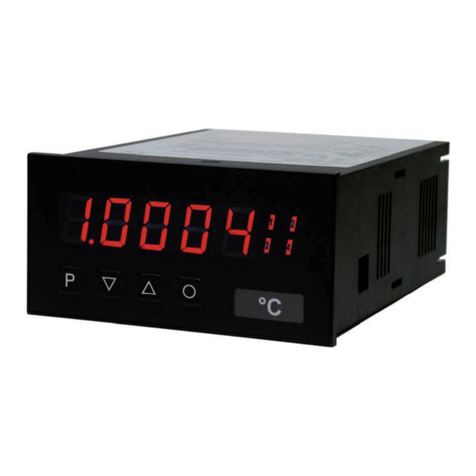
ACS contsys
ACS contsys DAL-311 5 0S Series operating instructions

Baumer
Baumer Hubner HENQ 1100 operating instructions
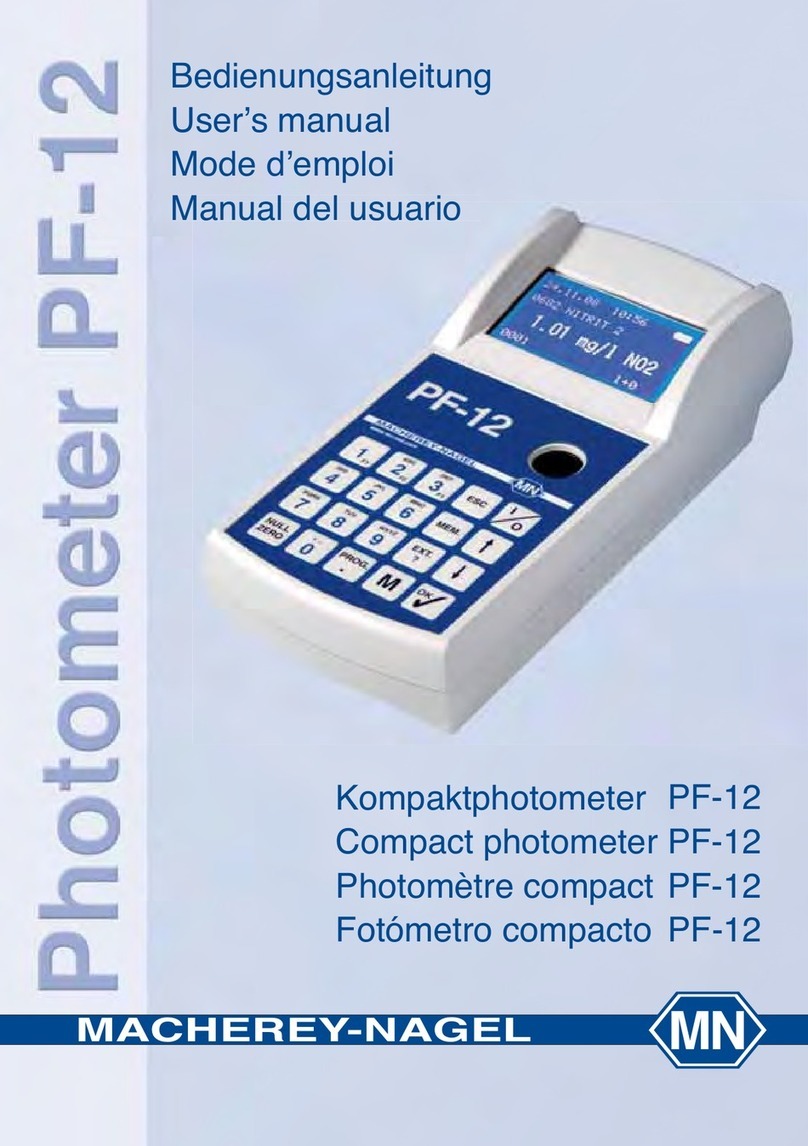
Macherey-Nagel
Macherey-Nagel PF-12 user manual
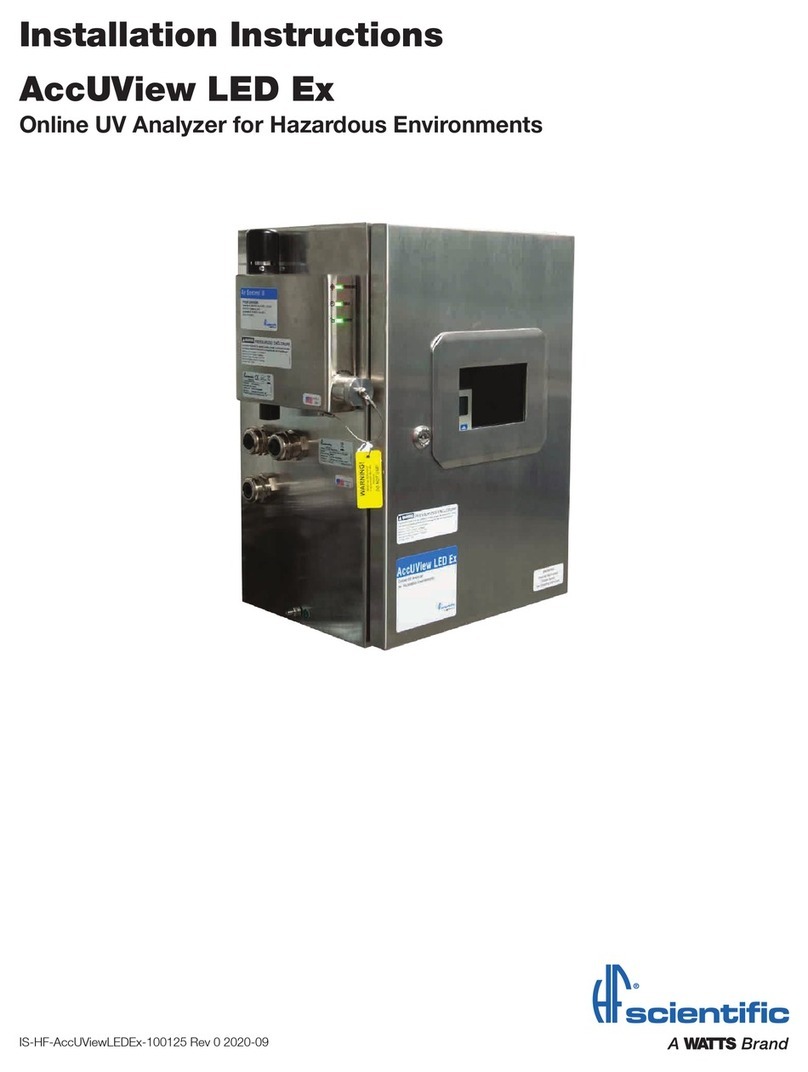
Watts
Watts HF Scientific AccUView LED Ex installation instructions