AMCI SMD17E2 User manual

MICRO CONTROLS INC.
ADVANCED
U
s
e
r
M
a
n
u
a
l
SMD17E2
Integrated Stepper
Indexer/Driver/Motor
with Integral 2-Port Ethernet Switch
Device Level Ring functionality for EtherNet/IP
Media Redundancy Protocol for PROFINET
Manual #: 940-0S221
E2 Technology

ADVANCED MICRO CONTROLS INC.
GENERAL INFORMATION
Important User Information
The products and application data described in this manual are useful in a wide variety of different applica-
tions. Therefore, the user and others responsible for applying these products described herein are responsible
for determining the acceptability for each application. While efforts have been made to provide accurate infor-
mation within this manual, AMCI assumes no responsibility for the application or the completeness of the
information contained herein.
UNDER NO CIRCUMSTANCES WILL ADVANCED MICRO CONTROLS, INC. BE RESPONSIBLE OR
LIABLE FOR ANY DAMAGES OR LOSSES, INCLUDING INDIRECT OR CONSEQUENTIAL DAM-
AGES OR LOSSES, ARISING FROM THE USE OF ANY INFORMATION CONTAINED WITHIN THIS
MANUAL, OR THE USE OF ANY PRODUCTS OR SERVICES REFERENCED HEREIN.
No patent liability is assumed by AMCI, with respect to use of information, circuits, equipment, or software
described in this manual.
The information contained within this manual is subject to change without notice.
This manual is copyright 2019 by Advanced Micro Controls Inc. You may reproduce this manual, in whole or
in part, for your personal use, provided that this copyright notice is included. You may distribute copies of this
complete manual in electronic format provided that they are unaltered from the version posted by Advanced
Micro Controls Inc. on our official website: www.amci.com. You may incorporate portions of this documents
in other literature for your own personal use provided that you include the notice “Portions of this document
copyright 2019 by Advanced Micro Controls Inc.” You may not alter the contents of this document or charge a
fee for reproducing or distributing it.
Standard Warranty
ADVANCED MICRO CONTROLS, INC. warrants that all equipment manufactured by it will be free from
defects, under normal use, in materials and workmanship for a period of [18] months. Within this warranty
period, AMCI shall, at its option, repair or replace, free of charge, any equipment covered by this warranty
which is returned, shipping charges prepaid, within eighteen months from date of invoice, and which upon
examination proves to be defective in material or workmanship and not caused by accident, misuse, neglect,
alteration, improper installation or improper testing.
The provisions of the "STANDARD WARRANTY" are the sole obligations of AMCI and excludes all other
warranties expressed or implied. In no event shall AMCI be liable for incidental or consequential damages or
for delay in performance of this warranty.
Returns Policy
All equipment being returned to AMCI for repair or replacement, regardless of warranty status, must have a
Return Merchandise Authorization number issued by AMCI. Call (860) 585-1254 with the model number and
serial number (if applicable) along with a description of the problem during regular business hours, Monday
through Friday, 8AM - 5PM Eastern. An "RMA" number will be issued. Equipment must be shipped to AMCI
with transportation charges prepaid. Title and risk of loss or damage remains with the customer until shipment
is received by AMCI.
24 Hour Technical Support Number
24 Hour technical support is available on this product. If you have internet access, start at www.amci.com.
Product documentation and FAQ’s are available on the site that answer most common questions.
If you require additional technical support, call (860) 583-1254. Your call will be answered by the factory dur-
ing regular business hours, Monday through Friday, 8AM - 5PM Eastern. During non-business hours an auto-
mated system will ask you to enter the telephone number you can be reached at. Please remember to include
your area code. The system will page an engineer on call. Please have your product model number and a
description of the problem ready before you call.
Waste Electrical and Electronic Equipment (WEEE)
At the end of life, this equipment should be collected separately from any unsorted municipal waste.

20 Gear Drive, Plymouth Ind. Park, Terryville, CT 06786
Tel: (860) 585-1254 Fax: (860) 584-1973 http://www.amci.com 3
TABLE OF CONTENTS
GENERAL INFORMATION
Important User Information ..................... 2
Standard Warranty ................................... 2
Returns Policy .......................................... 2
24 Hour Technical Support Number ........ 2
WEEE Statement ..................................... 2
About this Manual
Audience .................................................. 7
Applicable Units ...................................... 7
Trademark Notices ................................... 7
Revision Record ....................................... 7
Navigating this Manual ............................ 8
Manual Conventions ................................ 8
Manual Layout ......................................... 9
Reference: SMD17E2 Specifications
The SMD17E2 Family ............................. 11
Part Numbering System ................. 12
General Functionality .................... 12
Encoder Functionality ................... 13
Network Data Format .................... 13
Specifications ........................................... 14
Indexer Functionality ............................... 15
Stall Detection with
SMD17E2 Units .......................... 16
Driver Functionality ................................. 16
Idle Current Reduction .................. 17
Available Discrete Inputs ......................... 17
Home Input .................................... 17
CW Limit Switch or
CCW Limit Switch ...................... 17
Start Indexer Move Input ............... 17
Emergency Stop Input ................... 17
Stop Jog or Registration
Move Input .................................. 18
Capture Encoder Position Input ..... 18
General Purpose Input ................... 18
Optional Encoder ..................................... 18
Incremental Encoder ...................... 18
Absolute Multi-turn Encoder ......... 18
Status LED’s ............................................ 19
Module Status (MS) LED .............. 19
Network Status (NS) LED ............. 20
Reference: SMD17E2 Specifications
(continued)
SMD17E2 Connectors ............................. 20
Input Connector ............................ 20
Ethernet Connectors ...................... 21
Torque and Power Curves ........................ 21
Power Supply Sizing ................................ 22
Regeneration Effects ..................... 23
Compatible Connectors and Cordsets ...... 23
Connectors .................................... 23
Ethernet Cordset ........................... 24
Power Cordsets ............................. 24
Reference: Motion Control
Definitions ................................................ 25
Units of Measure ........................... 25
Motor Position .............................. 25
Home Position ............................... 25
Count Direction ............................. 25
Starting Speed ............................... 25
Target Position .............................. 26
Definition of Acceleration Types ............. 26
Linear Acceleration ....................... 26
Triangular S-Curve Accel ............. 27
Trapezoidal S-Curve Accel ........... 27
A Simple Move ........................................ 28
Controlled and Immediate Stops .............. 29
Host Control .................................. 29
Hardware Control ......................... 29
Basic Move Types .................................... 30
Relative Move ............................... 30
Absolute Move .............................. 31
CW/CCW Jog Move ..................... 32
CW/CCW Registration Move ....... 33
Assembled Moves .................................... 34
Blend Move ................................... 35
Dwell Move .................................. 36
Assembled Move Programming ............... 38
Control Bits – Output Data ........... 38
Control Bits – Input Data .............. 38
Programming Routine ................... 38
Saving an Assembled Move in Flash 38
Indexed Moves ......................................... 39
Synchrostep (Virtual Axis) Moves ........... 40

TABLE OF CONTENTS
SMD17E2 User Manual
ADVANCED MICRO CONTROLS INC.
4
Reference: Motion Control
(continued)
Controlling Moves In Progress ................ 41
Jog Moves ..................................... 41
Registration Moves ....................... 41
Absolute and Relative Moves ....... 41
Assembled Moves ......................... 41
Reference: Calculating Move
Profiles
Constant Acceleration Equations ............. 43
Variable Definitions ...................... 43
Total Time Equations .................... 45
S-Curve Acceleration Equations .............. 46
Triangular S-Curve Accel ............. 46
Trapezoidal S-Curve Accel ........... 48
Determining Waveforms
by Values .................................... 50
Reference: Homing an SMD17E2
Definition of Home Position .................... 53
Position Preset .......................................... 53
CW/CCW Find Home Commands ........... 53
Homing Inputs .......................................... 54
Physical Inputs .............................. 54
Network Data Input ...................... 54
Homing Configurations ............................ 54
Homing Profiles ....................................... 55
Home Input Only Profile .............. 55
Profile with
Backplane_Proximity_Bit ........... 56
Profile with Overtravel Limit ....... 57
Controlling Find Home
Commands In Progress .......................... 58
Controlled Stop Conditions .......... 58
Immediate Stop Conditions .......... 58
Reference: Configuration Mode
Data Format
Modes of Operation .................................. 59
Configuration Mode ...................... 59
Command Mode ........................... 59
Power Up Behavior .................................. 59
Configuration Mode Data Format ............ 59
Command Mode Data Formats ................ 59
Reference: Configuration Mode
Data Format (continued)
Output Data Format .................................. 61
Configuration Word 0 Format ....... 61
Configuration Word 1 Format ....... 63
Notes on Other Configuration
Words .......................................... 64
Input Data Format ..................................... 64
Configuration Word 0 Format
(Word 0) ...................................... 64
Starting Speed Format ................... 64
Stall Detect Enable ........................ 65
Invalid Configurations .............................. 65
Reference: Command Mode Data
Format
Data Format .............................................. 67
Command Bits Must Transition ............... 68
Output Data Format .................................. 68
Command Word 0 .................................... 69
Command Word 1 .................................... 71
Command Blocks ..................................... 72
Absolute Move .............................. 72
Relative Move ............................... 73
Hold Move .................................... 73
Resume Move ................................ 74
Immediate Stop ............................. 74
Find Home CW ............................. 75
Find Home CCW ........................... 75
Jog CW .......................................... 76
Registration Move CW ................. 76
Jog CCW ....................................... 77
Registration Move CCW ............... 77
Preset Position ............................... 78
Reset Errors ................................... 78
Run Assembled Move ................... 79
Preset Encoder Position ................. 79
Programming Blocks ................................ 80
First Block ..................................... 80
Segment Block .............................. 80
Input Data Format ..................................... 81
Format of Position Data Values .... 81
Status Word 0 Format ................... 81
Status Word 1 Format ................... 83
Notes on Clearing a Driver Fault .............. 84

20 Gear Drive, Plymouth Ind. Park, Terryville, CT 06786
Tel: (860) 585-1254 Fax: (860) 584-1973 http://www.amci.com
SMD17E2 User Manual
TABLE OF CONTENTS
5
Task 1: Installing the SMD17E2
Location ................................................... 85
IP50 Rated Units ............................ 85
IP64 Rated Units ............................ 85
Prevent Electrostatic Damage ........ 85
Prevent Debris From
Entering the Unit ......................... 85
Remove Power Before Servicing .. 85
Operating Temperature Guidelines .......... 86
Mounting .................................................. 86
SMD17E2-M12 Mounting ............ 86
SMD17E2-M12S Mounting .......... 86
SMD17E2-60 Outline Drawing ..... 87
SMD17E2-80 Outline Drawing ..... 88
Connecting the Load ...................... 88
Power and Input Connector ..................... 89
Compatible Connectors
and Cordsets .................................. 89
Power Wiring ........................................... 90
Input Wiring ............................................. 91
Cable Shields ................................. 91
Sinking Sensors Require a
Pull Up Resistor .......................... 91
Network Connectors ................................ 92
Compatible Connectors
and Cordsets ................................ 92
TIA/EIA-568 Color Codes ............ 92
EtherNet/IP Connections ......................... 93
Non-DLR Applications ................. 93
DLR Applications .......................... 93
Modbus TCP Connections ....................... 93
PROFINET Connections ......................... 93
Non-MRP Applications ................. 93
MRP Applications ......................... 93
Task 2: Set the IP Address and
Protocol
Determine the Best Method for
Setting the IP Address ........................... 95
Use Factory Default Settings ................... 95
Use the Embedded Web Server ............... 96
Use the AMCI NET Configurator
Utility ..................................................... 98
Task 3: Implicit Communications
with an EDS
Obtain the EDS file .................................. 103
Install the EDS file ................................... 103
Start the EDS Hardware
Installation Tool .......................... 103
Install the EDS File ....................... 104
Task 3: Implicit Communications
with an EDS (continued)
Host System Configuration ...................... 106
Add the SMD17E2 to Your Project ......... 106
Configure the SMD17E2 Driver .............. 107
General Tab ................................... 107
Connection Tab ............................. 107
Configuration Tab ......................... 107
Buffering the I/O Data ............................. 108
Task 4: Implicit Communications
Without an EDS
Host System Configuration ...................... 109
Add the SMD17E2 ................................... 109
Configure the SMD17E2 .......................... 111
Buffer I/O Data ........................................ 112
Task 5: EtherNet/IP Explicit
Messaging
Required Message Instructions ................ 113
Create Four New Data Files. .................... 113
Add the Message Instructions
to your Ladder Logic .............................. 114
Troubleshooting ....................................... 117
Task 6: Modbus TCP Configuration
Enable Modbus TCP Protocol .................. 119
Modbus Addressing ................................. 119
Modbus Table Mapping ................ 119
Host Addressing ............................ 119
AMCI Modbus TCP Memory Layout ...... 120
Supported Modbus Functions .................. 121
Supported Modbus Exceptions ................ 121
Task 7: PROFINET Network
Configuration
Basic Steps ............................................... 123
Download the GSDML files .................... 123
GSDML File Installation .......................... 123
Configure the PROFINET Network ......... 123
Add the SMD17E2 to the
PROFINET Network .............................. 124
Set the I/O Configuration ......................... 126
Verify and Download the
New Configuration ................................. 127
MRP Installations ..................................... 127
Configure the SMD17E2 as an MRC ....... 127

TABLE OF CONTENTS
SMD17E2 User Manual
ADVANCED MICRO CONTROLS INC.
6
Optional Task A: Configure Your
Network Interfaces
Firewall Settings ....................................... 129
Disable All Unused Network Interfaces ... 129
Configure Your Network Interface .......... 129
Test Your Network Interface .................... 130

20 Gear Drive, Plymouth Ind. Park, Terryville, CT 06786
Tel: (860) 585-1254 Fax: (860) 584-1973 http://www.amci.com 7
ABOUT THIS MANUAL
Audience
This manual explains the installation and operation of the SMD17E2 Integrated Stepper Indexer/Driver/
Motors from AMCI. It is written for the engineer responsible for incorporating these products into a design as
well as the engineer or technician responsible for their actual installation.
These devices support the EtherNet/IP, Modbus TCP, and PROFINET protocols. Each unit contains a two
port Ethernet switch, which simplifies network wiring. When the EtherNet/IP protocol is used, the unit can
act as a node in a Device Level Ring (DLR). When PROFINET is enabled, the unit supports the Media
Redundancy Protocol (MRP) and can be incorporated in PROFINET installations that use a redundant ring
topology.
Applicable Units
This manual applies to all of the units in the SMD17E2 family.
Part Number Description
Trademark Notices
The AMCI logo is a trademark of Advanced Micro Controls Inc.
All other trademarks contained herein are the property of their respective holders.
Revision Record
This manual, 940-0S221, is the second revision of this manual. It fixes typographical errors and adds the
WEEE notification. It was first released January 9th, 2019.
Revision History
940-0S220: June 18st, 2018 - Initial Release
Read this chapter to learn how to navigate through this manual and familiarize
yourself with the conventions used in it. The last section of this chapter highlights
the manual’s remaining chapters and their target audience.
Model Number Description
SMD17E2-60-M12 Size 17 motor, 60 oz-in holding torque with sealed M12 connectors for an
IP50 rating.
SMD17E2-80-M12 Size 17 motor, 80 oz-in holding torque with sealed M12 connectors for an
IP50 rating.
SMD17E2-60A-M12 Same as SMD17E-60-M12 with an integrated absolute multi-turn encoder.
SMD17E2-80A-M12 Same as SMD17E-80-M12 with an integrated absolute multi-turn encoder.
SMD17E2-60E-M12 Same as SMD17E-60-M12 with an integrated incremental encoder.
SMD17E2-80E-M12 Same as SMD17E-80-M12 with an integrated incremental encoder.
SMD17E2-60-M12S Size 17 motor, 60 oz-in holding torque with sealed M12 connectors and shaft
seal for an IP64 rating.
SMD17E2-80-M12S Size 17 motor, 80 oz-in holding torque with sealed M12 connectors and shaft
seal for an IP64 rating.
SMD17E2-60A-M12S Same as SMD17E2-60-M12S with an integrated absolute multi-turn encoder.
SMD17E2-80A-M12S Same as SMD17E2-80-M12S with an integrated absolute multi-turn encoder.
SMD17E2-60E-M12S Same as SMD17E2-60-M12S with an integrated incremental encoder.
SMD17E2-80E-M12S Same as SMD17E2-80-M12S with an integrated incremental encoder.

ABOUT THIS MANUAL
SMD17E2 User Manual
ADVANCED MICRO CONTROLS INC.
8
Navigating this Manual
This manual is designed to be used in both printed and on-line forms. Its on-line form is a PDF document,
which requires Adobe Acrobat Reader version 7.0+ to open it. You are allowed to select and copy sections
for use in other documents and add notes and annotations. If you decide to print out this manual, all sections
contain an even number of pages which allows you to easily print out a single chapter on a duplex (two-sided)
printer.
Manual Conventions
Three icons are used to highlight important information in the manual:
NOTES highlight important concepts, decisions you must make, or the implications of those
decisions.
CAUTIONS tell you when equipment may be damaged if the procedure is not followed
properly.
WARNINGS tell you when people may be hurt or equipment may be damaged if the pro-
cedure is not followed properly.
The following table shows the text formatting conventions:
Format Description
Normal Font Font used throughout this manual.
Emphasis Font Font used the first time a new term is introduced.
Cross Reference When viewing the PDF version of the manual, clicking on
the cross reference text jumps you to referenced section.
HTML Reference When viewing the PDF version of the manual, clicking on
the HTML reference text will open your default web
browser to the referenced web page.

20 Gear Drive, Plymouth Ind. Park, Terryville, CT 06786
Tel: (860) 585-1254 Fax: (860) 584-1973 http://www.amci.com
SMD17E2 User Manual
ABOUT THIS MANUAL
9
Manual Layout
You will most likely read this manual for one of two reasons:
If you are curious about the Integrated Stepper Indexer/Driver/Motor products from AMCI, this manual
contains the information you need to determine if these products are the right products for your applica-
tion. The first chapter, SMD17E2 Specifications contains all of the information you will need to fully
specify the right product for your application.
If you need to install and use an Integrated Stepper Indexer/Driver/Motor product from AMCI, then the
rest of the manual is written for you. To simplify installation and configuration, the rest of the manual
is broken down into references and tasks. Using an Integrated Stepper Indexer/Driver/Motor product
requires you to complete multiple tasks, and the manual is broken down into sections that explain how
to complete each one.
Manual Sections
Section Title Section Description
SMD17E2 Specifications Complete specifications for the SMD17E2 products.
Motion Control Reference information on how the SMD17E2 can be used to con-
trol motion in your application.
Calculating Move Profiles Reference information on calculating detailed move profiles.
Homing an SMD17E2 Reference information on how to set the home position of the
SMD17E2.
Configuration Mode Data
Format Reference information on the format of the network data to and
from the SMD17E2 that is used to configure it.
Command Mode Data
Format Reference information on the format of the network data to and
from the SMD17E2 that is used to command it.
Installing the SMD17E2 Task instructions covering how to install an SMD17E2 on a
machine. Includes information on mounting, grounding, and wir-
ing specific to the units.
Set the IP Address and
Protocol Task instructions that covers the options for setting the IP address
on an SMD17E2.
Implicit Communications
with an EDS Task instructions that cover how to add an SMD17E2 to an
EtherNet/IP host that supports the use of EDS files.
Implicit Communications
Without an EDS Task instructions for adding an SMD17E2 to a project as a generic
device. This configuration is for EtherNet/IP hosts that do not sup-
port EDS files while supporting implicit communications.
EtherNet/IP Explicit
Messaging Task instructions for adding message instructions to you host con-
troller program that write data to the SMD17E2 through message
instructions.
Modbus TCP
Configuration Task instructions for communicating with an SMD17E2 using the
Modbus TCP protocol.
PROFINET Network
Configuration Task instructions for communicating with an SMD17E2 using the
PROFINET protocol.
Optional: Configure Your
Network Interfaces Instructions for the optional task of configuring network interfaces
on your computer or laptop.

ABOUT THIS MANUAL
SMD17E2 User Manual
ADVANCED MICRO CONTROLS INC.
10
Notes

20 Gear Drive, Plymouth Ind. Park, Terryville, CT 06786
Tel: (860) 585-1254 Fax: (860) 584-1973 http://www.amci.com 11
REFERENCE 1
SMD17E2 SPECIFICATIONS
The SMD17E2 Family
The SMD17E2 units are part of a growing prod-
uct line from AMCI with a simple concept: a
stepper indexer, driver, and motor that can be
attached to any popular industrial network. Each
SMD17E2 attaches to your Ethernet network and
communicates using the EtherNet/IP, Modbus
TCP, or PROFINET protocols.
The SMD17E2 units are members of the growing
line of products from AMCI that incorporate our
E2 Technology. E2 Technology by AMCI is an
innovative new multi-protocol approach to Ether-
net distributed I/O.
E2 Technology products are simple and intuitive,
allowing easy transition between multiple com-
mon industrial Ethernet protocols without the
need to physically switch parts. An advanced
web server integrated into all AMCI E2 Technol-
ogy devices facilitates simple device configura-
tion and troubleshooting via web-browser.
Furthermore, an impressive array of advanced
features for each supported protocol has been
incorporated into the devices to meet many
unique application requirements.
Each unit has two Ethernet ports which are internally connected through an onboard, two port, 10/100 Mbps
ethernet switch. These ports allow you to wire your network in a “daisy-chain” fashion, which may lower net-
work wiring costs and complexities.
The two ports also allow the SMD17E2 products to function as members of a redundant Device Level Ring
(DLR) network when using the EtherNet/IP protocol or as clients in a Media Redundancy Protocol (MRP)
network when using PROFINET.
In DLR environments, the SMD17E2 units act as Beacon-Based Ring Nodes. All SMD17E2 units can pro-
cess beacon packets at the default rate of every 400 microseconds. Beacon-based nodes can respond faster to
network changes than nodes that only process Announce packets.
Each unit can be ordered with an optional incremental or absolute multi-turn encoder. This encoder gives you
the additional functionality of position verification and stall detection. The absolute multi-turn encoder allows
you to track machine position with power removed, eliminating the need to home the machine after cycling
power.
This manual is designed to get you up and running quickly with an SMD17E2
product from AMCI. As such, it assumes you have some basic knowledge of step-
per systems, such as the resolution you want run your motor at, and the reasons
why you’d want to use Idle Current Reduction and the reasons why you wouldn’t.
If these terms or ideas are new to you, we’re here to help. AMCI has a great deal
of information on our website and we are adding more all the time. If you can’t
find what you’re looking for at http://www.amci.com, send us an e-mail or call us.
We’re here to support you with all of our knowledge and experience.
Figure R1.1 IP50 Rated SMD17E2

SMD17E2 SPECIFICATIONS
SMD17E2 User Manual
ADVANCED MICRO CONTROLS INC.
12
The SMD17E2 Family (continued)
Part Numbering System
Figure R1.2 Part Numbering System
General Functionality
Each member of the SMD17E2 family has three integrated parts:
An indexer that accepts commands over an Ethernet connection using the EtherNet/IP, Modbus TCP, or
PROFINET protocol
A 2.0 Arms micro-stepping driver that accepts 24 to 48 Vdc as its input power source
A high torque size 17 stepper motor (60 or 80 oz-in holding torque).
An incremental or absolute multi-turn encoder is also available for applications that require position feedback
or verification.
The availability of the EtherNet/IP, Modbus TCP, or PROFINET protocols makes the SMD17E2 units easy to
integrate into a wide variety of control systems. This combination of host and driver gives you several advan-
tages:
Sophisticated I/O processing can be performed in the host (PLC or other controller) before sending
commands to the SMD17E2 unit
All motion logic is programmed in the host, eliminating the need to learn a separate motion control lan-
guage
The integral two port Ethernet switch simplifies network cabling
The DLR interface eliminates single point failures in EtherNet/IP environments
The MRP interface eliminates single point failures in PROFINET environments
The elimination of the separate indexer and driver lowers total system cost.
An SMD17E2 is powered by a nominal 24 to 48 Vdc power source, and can accept surge voltages of up to
60 Vdc without damage. The output motor current is fully programmable from 0.1 Arms to 2.0 Arms which
makes the SMD17E2 suitable to a wide range of applications. In addition to the Motor Current setting,
the Motor Steps per Turn, Idle Current Reduction, and Anti-Resonance Circuit features are also fully pro-
grammable. If you have used other stepper indexer products from AMCI, you will find programming an
SMD17E2 to be very similar to these products.
The SMD17E2 contains a true RMS motor current control driver. This means that you will always receive
the motor’s rated torque regardless of the Motor Steps/Turn setting. (Drivers that control the peak current to
the motor experience a 30% decrease in motor torque when microstepping a motor.) The combination of an
ultra-low inductance motor and a high-power, true RMS driver gives unprecedented torque vs. speed perfor-
mance for any DC application.
CONNECTOR TYPE
‘-M12’ =
Network: (2) 4 pin Female D-Type
Power: (1) 5 pin Male A-Type
IP50 Rating
M12 Connectors
‘-M12S’ = M12 Connectors, Shaft Seal
Network: (2) 4 pin Female D-Type
Power: (1) 5 pin Male A-Type
IP64 Rating
SMD17E2 –
ENCODER
‘blank’= No encoder
A=Absolute Multi-turn Encoder
2,048 counts/turn.
E = Incremental Encoder
4,096 counts/turn max.
TORQUE
80 = 80 oz-in
60 = 60 oz-in

20 Gear Drive, Plymouth Ind. Park, Terryville, CT 06786
Tel: (860) 585-1254 Fax: (860) 584-1973 http://www.amci.com
SMD17E2 User Manual
SMD17E2 SPECIFICATIONS
13
The SMD17E2 Family (continued)
General Functionality (continued)
The SMD17E2 units have two DC inputs that are used by the indexer. Configuration data from the host sets
the function of these inputs. Each input can be individually configured as a:
CW or CCW Limit Switch
Home Limit Switch
Capture Position Input (Will capture encoder position on units with the internal encoder.)
Stop Jog or Registration Move Input
Start Indexer Move
Emergency Stop Input
General Purpose Input
Encoder Functionality
All SMD17E2 units can be ordered with an internal incremental or absolute multi-turn encoder. Incremental
encoders can be programmed to 1,024, 2,048, or 4,069 counts per turn. Absolute encoders have a fixed reso-
lution of 2,048 counts per turn and encode a total of 221 turns. (32 bits total.) Using an encoder gives you the
ability to:
Verify position during or after a move
Detect motor stall conditions
Maintain machine position when power is removed if using an absolute encoder.
Close the position/velocity loop with the encoder position instead of the motor position when following
a virtual axis.
The motor position can be preset to the encoder position with a single command. SMD17E2 units with abso-
lute encoders allow you to preset the encoder position and save the resulting offset in Flash memory.
Network Data Format
In order to support any host that communicates with the supported protocols, the format of the data read from
and written to the SMD17E2 while in command mode is completely programmable. The format of the network
input and output data can be programmed separately.
The smallest data size used by the SMD17E2 is the sixteen bit word, however some parameters and data values
can exceed this size. For these thirty-two bit values, the default data format is referred to as the
multi-word
for-
mat. The data value is split between the hundreds digit and the thousands digit. For example, a value of 12,345
would have 12 placed in the first (lower addressed) word, and 345 placed in the second (higher addressed)
word. This format greatly simplifies setting parameter values when programming command blocks.
The other data format is a signed thirty-two bit integer format. When using the thirty-two bit format, there is
one additional parameter named Data Endian. Its use is best explained with an example. The value of
123,456 equals 0001:E240 in hexadecimal. When storing and transmitting this data, some host controllers
will store the least significant word (16#E240) in the lower addressed word in their data tables, while others
will store the most significant word (16#0001) stored in the lower addressed word in their data tables. These
controllers expect thirty-two bit values to be returned to them using the same format. Least significant word
first is called little endian, most significant word first is called big endian. Rockwell Automation controllers
use little endian format, the default Modbus format is big endian, and the default PROFINET format is big
endian.
The range of values when using the multi-word format is -32,768,000 to 32,767,999. When
used in continuous rotation applications, it is possible to overflow these values. When a posi-
tion value overflows, the value of the associated data words will become indeterminate. AMCI
strongly suggests using the signed 32-bit integer format for continuous rotation applications.

SMD17E2 SPECIFICATIONS
SMD17E2 User Manual
ADVANCED MICRO CONTROLS INC.
14
Specifications
Network Interface
10/100baseT. Two switched ports.
Supports EtherNet/IP, Modbus TCP, and
PROFINET. EtherNet/IP-DLR and PROFINET-
MRP extensions also supported.
Driver Type
Two bipolar MOSFET H-bridges with 20KHz
PWM current control.
Physical Dimensions
See Outline Drawings, starting on page 87
Weight
SMD17E2-60-M12 ............... 0.90 lbs. (0.41 kg.)
SMD17E2-80-M12 ............... 1.07 lbs. (0.49 kg.)
All weights are without mating connectors
Maximum Shaft Loads
Radial: 6.5 lbs (29 N) at center of flat on shaft
Axial: 5.6 lbs (25 N)
Maximum Operating Temperature
203°F /95°C (Note that this is the operating tem-
perature of the motor, not maximum ambient
temperature. An Over Temperature fault occurs
at this point and current is removed from the
motor.)
Over Temperature Fault
Over temperature faults are reported in the Net-
work Input Data.
Inputs
Electrical Characteristics:
IN1 and IN2: Single ended sinking.
Accept 3.5 to 27Vdc without the need for an
external current limiting resistor. Optoisolated,
1500 Vac/dc isolation.
Specifications
Motor Current
Programmable from 0.1 to 2.0 Arms in 0.1 A steps.
DCPowerAUX Current
70 mA @ 24Vdc, 40mA @48Vdc
Motor Counts per Turn
Programmable to any value from 200 to 32,767
steps per revolution.
Internal Encoder (Optional)
Incremental encoder option supplies 1,024, 2,048,
or 4,096 counts per turn.
Absolute encoder option supplies 2,048 counts per
turn, 32 bit max. counts.
Idle Current Reduction
Programmable from 0% to 100% programmed
motor current in 1% increments. Motor current
is reduced to selected level if there is no motion
for 1.5 seconds. Current is restored to full value
when motion is started.
Environmental Specifications
Input Power ....... 24 to 48 Vdc, surge to 60 Vdc
without damage to unit.
Ambient Operating Temperature
........... -40° to 122°F (-40° to 50°C)
Storage Temperature
........... -40° to 185°F (-40° to 85°C)
Humidity ........... 0 to 95%, non-condensing
IP Rating ........... IP50 or IP64 with shaft seal.
Status LED’s
See Status LED’s section starting on page 19.
Connectors and Cables
All mating connectors are available separately
under the following AMCI part numbers.
Connector AMCI Part # Wire Strip Length Connection Type
Ethernet MS-28 18 AWG max. 0.197 inches Screw Terminals
I/O MS-31 18 AWG max. 0.197 inches Screw Terminals
Cable AMCI Part # Length
Ethernet CNER-5M 5 meter
Power & I/O CNPL-2M 2 meter
Power & I/O CNPL-5M 5 meter

20 Gear Drive, Plymouth Ind. Park, Terryville, CT 06786
Tel: (860) 585-1254 Fax: (860) 584-1973 http://www.amci.com
SMD17E2 User Manual
SMD17E2 SPECIFICATIONS
15
Indexer Functionality
The table below lists the functionality offered by the indexer built into the SMD17E2.
Table R1.1 Indexer Functionality
Feature Description
EtherNet/IP,
PROFINET,
Modbus TCP Allows easy setup and communication with a wide range of host controllers such
as the latest PLC’s from Allen-Bradley.
EtherNet/IP-DLR SMD17E2 units have Device Level Ring functionality, which adds redundancy to
the EtherNet/IP protocol.
PROFINET-MRP SMD17E2 units have Media Redundancy Protocol support, which adds redun-
dancy to the PROFINET protocol.
Programmable
Inputs Each of the inputs can be programmed as a Home Limit, Over Travel Limit, Cap-
ture Input, Manual Jog Stop, Start Indexer Move, E-Stop, or a General Purpose
Input.
Programmable
Parameters Starting Speed, Running Speed, Acceleration, Deceleration, and Accel/Decel
Types are fully programmable.
Homing Allows you to set the machine to a known position. An SMD17E2 homes to a dis-
crete input and can use a bit in the Network Data as a home proximity input.
Jog Move Allows you to drive the motor in either direction as long as the command is active.
Synchrostep Move Allows you to treat the SMD17E2 as a motion axis by constantly updating posi-
tion and velocity data to the unit.
Relative Move Allows you to drive the motor a specific number of steps in either direction from
the current location.
Absolute Move Allows you to drive the motor from one known location to another known loca-
tion.
Registration Move Allows you to jog the motor in either direction based on an input bit from your
host controller. When a controlled stop is issued, the move will output a program-
mable number of steps before coming to a stop.
Blend Move Allows you to perform a sequence of relative moves without stopping between
them.
Dwell Move Allows you to perform a sequence of relative moves with a stop between each
move that has a programmable length of time. Used to create highly accurate
move profiles that avoid network latency issues.
Indexer Move Allows you to program a move that is held in memory. The move is run when one
of the programmable inputs makes a transition. Note that an Indexer Move
requires a connection to a host controller to program the move.
Hold Move Allows you to suspend a move, and optionally restart it, without losing your posi-
tion value.
Resume Move Allows you to restart a previously held move operation.
Immediate Stop Allows you to immediately stop all motion if an error condition is detected by
your host controller.
Stall Detection When an SMD17E2 is purchased with an encoder option, the encoder can be used
to verify motion when a move command is issued.

SMD17E2 SPECIFICATIONS
SMD17E2 User Manual
ADVANCED MICRO CONTROLS INC.
16
Indexer Functionality (continued)
Stall Detection with SMD17E2 Units
Stall Detection is one of the additional features available to you when you order an encoder option on an
SMD17E2. When Stall Detection is enabled, the SMD17E2 monitors the encoder for position changes,
regardless of whether or not a move is in progress. If the error between the encoder position and the motor
position exceeds forty-five degrees, the SMD17E2 responds in the following manner:
The stall is reported in the network input data.
The motor position becomes invalid. (The machine must be homed or the motor position preset before
Absolute moves can be run again.
If a move was in progress, the move is stopped.
Note that a move does not have to be in progress for stall detection to be useful. As described later in this
chapter, there is an auxiliary power pin that powers the electronics of an SMD17E2 but does not power the
motor. The primary use of this feature is to keep the unit on the network while power is removed from the
motor. When using the DCPowerAUX pin, the SMD17E2 cannot sense when power has been removed from
the DCPowerMAIN pin. By enabling stall detection, the SMD17E2 can notify the system if the motor shaft
moves more than forty-five degrees while power is removed from the motor.
Driver Functionality
This table summarizes the features of the stepper motor driver portion of an SMD17E2.
Table R1.2 Driver Functionality
Feature Benefits
RMS Current Control RMS current control give an SMD17E2 the ability to drive the motor at its
fully rated power regardless of the programmed steps per turn. There is no
reduction in power when microstepping that may occur with other drivers.
Programmable
Motor Current
RMS current supplied to the motor can be programmed from 0.1 to 2.0
amps in 0.1 amp increments. Reducing the motor current to the minimum
needed for your application will significantly reduce the motors operating
temperature
Programmable Idle
Current Reduction Extends motor life by reducing the motor current when motion is not
occurring. This extends the life of the motor by reducing its operating
temperature.
Programmable
Motor Steps/Turn Allows you to scale your motor count to a real world value. (counts per
inch, counts per degree, etc.)
Anti-Resonance Circuitry This feedback circuitry and algorithm gives the SMD17E2 the ability to
modify motor current waveforms to compensate for mechanical resonance
in your system. This will give you smooth performance over the entire
speed range of the motor.
Over Temperature
Detection An SMD17E2 sets a warning bit in the network data when the temperature
of the unit approaches its safe operating threshold.
Over Temperature
Protection Protects your SMD17E2 from damage by removing power from the motor
if the internal temperature of the driver exceeds the safe operating thresh-
old of 203°F/95°C.

20 Gear Drive, Plymouth Ind. Park, Terryville, CT 06786
Tel: (860) 585-1254 Fax: (860) 584-1973 http://www.amci.com
SMD17E2 User Manual
SMD17E2 SPECIFICATIONS
17
Driver Functionality (continued)
Idle Current Reduction
Idle Current Reduction allows you to prolong the life of your motor by reducing its idling temperature. Values
for this parameter range from 0% (no holding torque when idle) to 100%.
Idle current reduction should be used whenever possible. By reducing the current, you are reducing the I2R
losses in the motor, which results in an exponential, not linear, drop in motor temperature. This means that
even a small reduction in the idle current can have a significant effect on the temperature of the motor.
Note that the reduction values are “to” values, not “by” values. Setting a motor current to
2 Arms and the current reduction to 25% will result in an idle current of 0.5 Apk. (The
SMD17E always switches from RMS to peak current control when the motor is idle to
prevent motor damage due to excessive heating.)
Available Discrete Inputs
The SMD17E2 has two discrete, sinking, DC inputs that accept 3.5 to 27Vdc signals. (5 to 24Vdc nominal)
How your SMD17E2 uses these inputs is fully programmable. The active state of each input is also program-
mable. Programming their active states allow them to act as Normally Open (NO) or Normally Closed (NC)
contacts.
Home Input
Many applications require that the machine be brought to a known position before normal operation can
begin. This is commonly called “homing” the machine or bringing the machine to its “home” position. An
SMD17E2 allows you to define this starting position in two ways. The first is with a Position Preset com-
mand. The second is with a sensor mounted on the machine. When you define one of the inputs as the Home
Input, you can issue commands to the SMD17E2 that will cause the unit to seek this sensor. How the
SMD17E2 actually finds the Home sensor is described in the Homing an SMD17E2 chapter starting on page
53.
CW Limit Switch or CCW Limit Switch
Each input can be defined as a CW or CCW Limit Switch. When used this way, the inputs are used to define
the limits of mechanical travel. For example, if you are moving in a clockwise direction and the CW Limit
Switch activates, all motion will immediately stop. At this point, you will only be able to jog in the counter-
clockwise direction.
Start Indexer Move Input
Indexer Moves are programmed through the Network Data like every other move. The only difference is that
Indexer Moves are not run until a Start Indexer Move Input makes a inactive-to-active state transition. This
allows an SMD17E2 to run critically timed moves that cannot be reliably started from the network due to data
transfer lags.
If the unit was ordered with the encoder option, and one of the discrete DC inputs is programmed as a Start
Indexer Move Input, then the encoder position data will be captured whenever the DC input makes a transi-
tion. An inactive-to-active state transition on the DC input will also trigger an Indexer Move if one is pend-
ing.
Emergency Stop Input
When an input is defined as an Emergency Stop, or E-Stop Input, motion will immediately stop when this
input becomes active. The driver remains enabled and power is supplied to the motor. Any type of move,
including a Jog or Registration Move, cannot begin while this input is active.

SMD17E2 SPECIFICATIONS
SMD17E2 User Manual
ADVANCED MICRO CONTROLS INC.
18
Available Discrete Inputs (continued)
Stop Jog or Registration Move Input
When an input is configured as a Stop Jog or Registration Move Input, triggering this input during a Jog
Move or Registration Move will bring the move to a controlled stop. The controlled stop is triggered on an
inactive-to-active state change on the input. Only Jog Moves and Registration Moves can be stopped this
way, all other moves ignore this input.
If the unit was order with an integral encoder, the encoder position data will be captured when the DC input
makes an inactive-to-active transition if it is configured as a Stop Jog or Registration Move Input. The
encoder position data is not captured if a Jog or Registration Move is not in progress. If you want to capture
encoder position data on every transition of a DC input, configure it as a Start Indexer Move Input.
Capture Encoder Position Input
As described in the Start Indexer Move Input and Stop Jog or Registration Move Input sections above, an
SMD17E2 can be configured to capture the encoder position value on a transition of a discrete DC input.
General Purpose Input
If your application does not require one or both of the inputs, you can configure the unused inputs as General
Purpose Inputs. The inputs are not used by the SMD17E2, but their on/off state is reported in the network data
and is available to your host controller.
Optional Encoder
The SMD17E2 can be ordered with an integral encoder. An input can be configured to capture the encoder
value when the input makes an inactive to active transition. This captured value is written to the host control-
ler. Two encoder options are available:
Incremental Encoder
The incremental encoder can be programmed to 1,024, 2,048, or 4,096 counts per turn. The SMD23/4E2 has
an internal thirty-two bit counter associated with the encoder. The incremental encoder are primarily used for
position verification and stall detection.
Absolute Multi-turn Encoder
The absolute encoder has a fixed resolution of 2,048 counts per turn. The absolute encoder is a multi-turn
device that encodes a total of 221 turns, yielding a full thirty-two bits of position resolution. The absolute
encoder can be used for position verification and stall detection, but its primary advantage is that it eliminates
the need to home the axis after cycling power to the drive.
Like many intelligent absolute encoders on the market today, the absolute encoder in the SMD17E2 uses
a battery backed circuit to count zero crossings while power is removed from the rest of the device. The
circuit will accurately track position as long as the shaft acceleration is limited to 160,000 degrees/sec2,
(444.4 rev/sec2), or less. Battery life is a minimum of 10 years in the absence of power. The battery cannot
be replaced in the field.

20 Gear Drive, Plymouth Ind. Park, Terryville, CT 06786
Tel: (860) 585-1254 Fax: (860) 584-1973 http://www.amci.com
SMD17E2 User Manual
SMD17E2 SPECIFICATIONS
19
Status LED’s
Each SMD17E2 has two status LED’s that show module and network status. As
shown in figure R1.3, these LED’s are located on the rear cover.
Module Status (MS) LED
The Module Status LED is a bi-color red/green LED. The state of the LED depends
on the state of the network adapter module.
Table R1.3 Module Status LED States
Power Up Behavior
Blinking Green: The unit will blink the Module Status LED green during initialization.
Blinking Red: The unit will blink the Module Status LED red three times if there is an error with the
internal absolute encoder.
LED State EtherNet/IP Definition Modbus TCP Definition PROFINET Definition
Off No Power No Power No power
Alternating
Red/Green
Initializing: Power up Self-Test
Communications failure. There is a communications error between the main processor and
the ethernet co-processor within the unit. You must cycle power to the SMD17E2 to
attempt to clear this fault.
Flashing
Green
Initializing: Waiting for valid physical connection to the
network.
Successful write to flash memory. Power must be cycled to the unit before additional
commands can be written to it.
Steady Green Drive and Network are
operational. Drive and Network are
operational. Device Name or IP Address
are set.
Flashing Red Initializing: Network
Connection Timeout Not Implemented Initializing: Device Name or
IP Address are not set.
Failed write to flash memory. You must cycle power to the unit to clear this fault.
Steady Red Overtemperature fault. Remove power from the unit and allow it to cool to clear the fault.
Figure R1.3 Rear Cover
Status LED’s
PORT 2
POWER & INPUTS
MS
NS
PORT 1
Power: 24 to 48 Vdc

SMD17E2 SPECIFICATIONS
SMD17E2 User Manual
ADVANCED MICRO CONTROLS INC.
20
Status LED’s (continued)
Network Status (NS) LED
The Network Status LED is a bi-color red/green LED. The state of the LED depends on the protocol the
SMD17E2 is configured to for.
Table R1.4 Network Status LED States
SMD17E2 Connectors
Input Connector
As shown in figure R1.4, the Input Connector is located on the back of the
unit near its center. All digital input and power supply connections are
made at this connector. The connector is a standard five pin A-coded M12
connector that is rated to IP67 when the mate is properly attached. Figure
R1.5 shows the pinout of the connector when viewed from the back of the
SMD17E2.
Digital inputs are single ended and referenced to the DC Common pin.
(Sinking inputs.)
There are two power pins. DCPowerMAIN powers both the control electron-
ics and the motor. DCPowerAUX powers only the control electronics. Using
the DCPowerAUX pin is optional. If your application requires you to cut
power to your motor under some conditions, using the DCPowerAUX pin
allows you to cut power to your motor without losing your network con-
nection.
LED State EtherNet/IP Definition Modbus TCP Definition PROFINET Definition
Off No Power No power or no TCP con-
nections
No power, duplicate IP
address on the network, or
no connection to IO Con-
troller.
Alternating
Red/Green Power up Self-Test Power up Self-Test Power up Self-Test
Flashing
Green Ethernet connection,
but no CIP connec-
tions
Indicates number of con-
nections with 2 second
delay between group. The
SMD17E2supportsup to3
concurrent connections.
On-line, Stop state. A con-
nection with the IO Con-
troller is established and it
is in its STOP state.
Steady Green Valid Ethernet net-
work and CIP con-
nections
Should not occur. LED
should always flash when
network is connected.
On-line, Run state. A con-
nection with the IO Con-
troller is established and it
is in its RUN state.
Flashing Red Network Connection
Timeout Not implemented in
Modbus TCP. Not Implimented
Steady Red Duplicate IP address on network. Not Implimented.
Figure R1.4 SMD17E2
Connector Locations
PORT 2
POWER & INPUTS
MS
NS
PORT 1
Power: 24 to 48 Vdc
Figure R1.5 M12 Input Connector
Table of contents
Other AMCI Control Unit manuals

AMCI
AMCI 7500 Series User manual
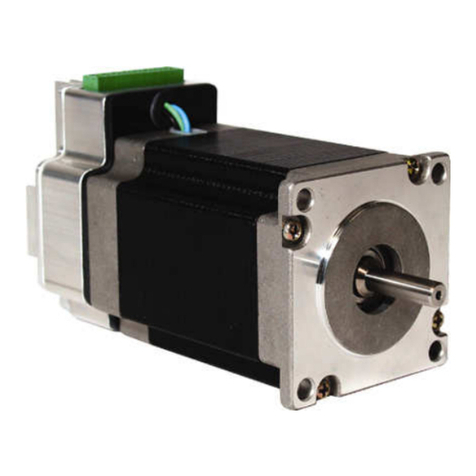
AMCI
AMCI SMD23 Series User manual
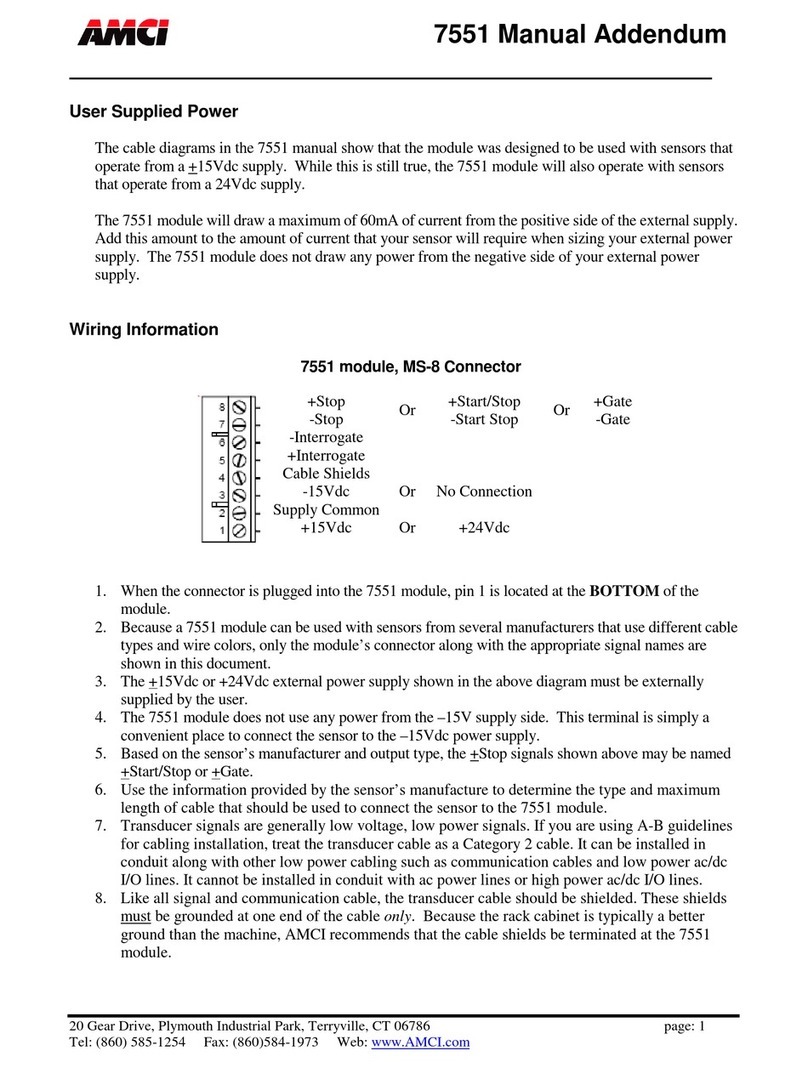
AMCI
AMCI 7551 Installation and operating instructions
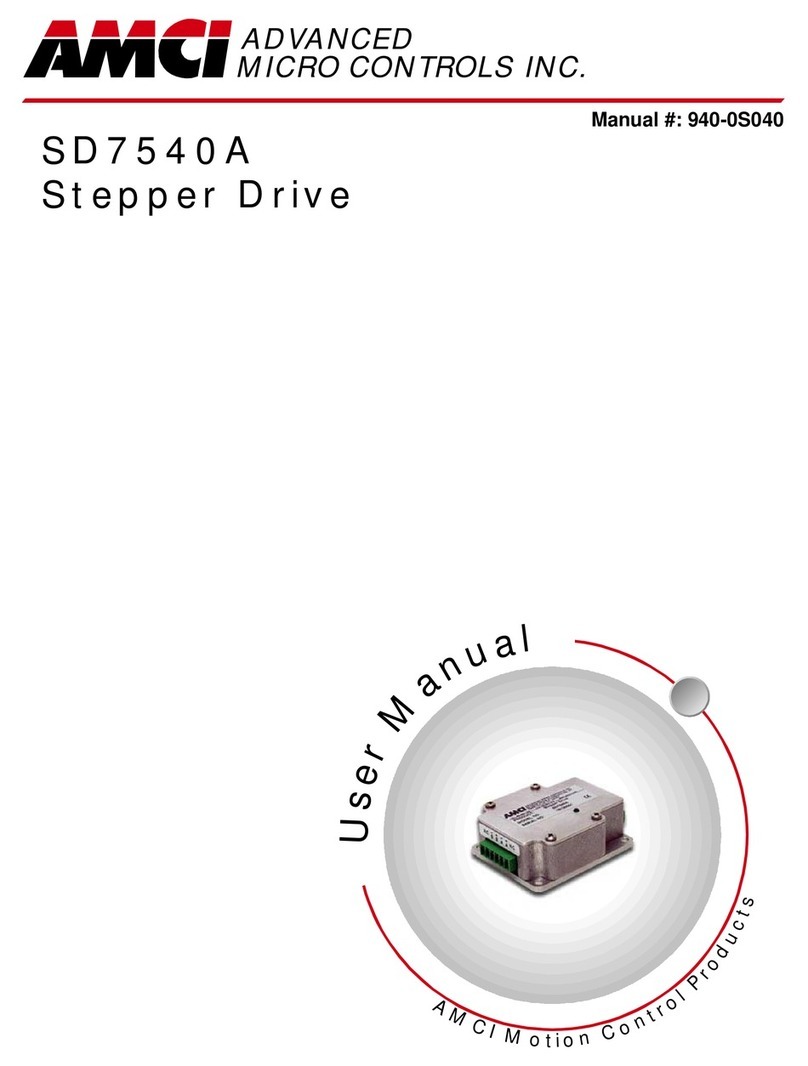
AMCI
AMCI SD7540A User manual
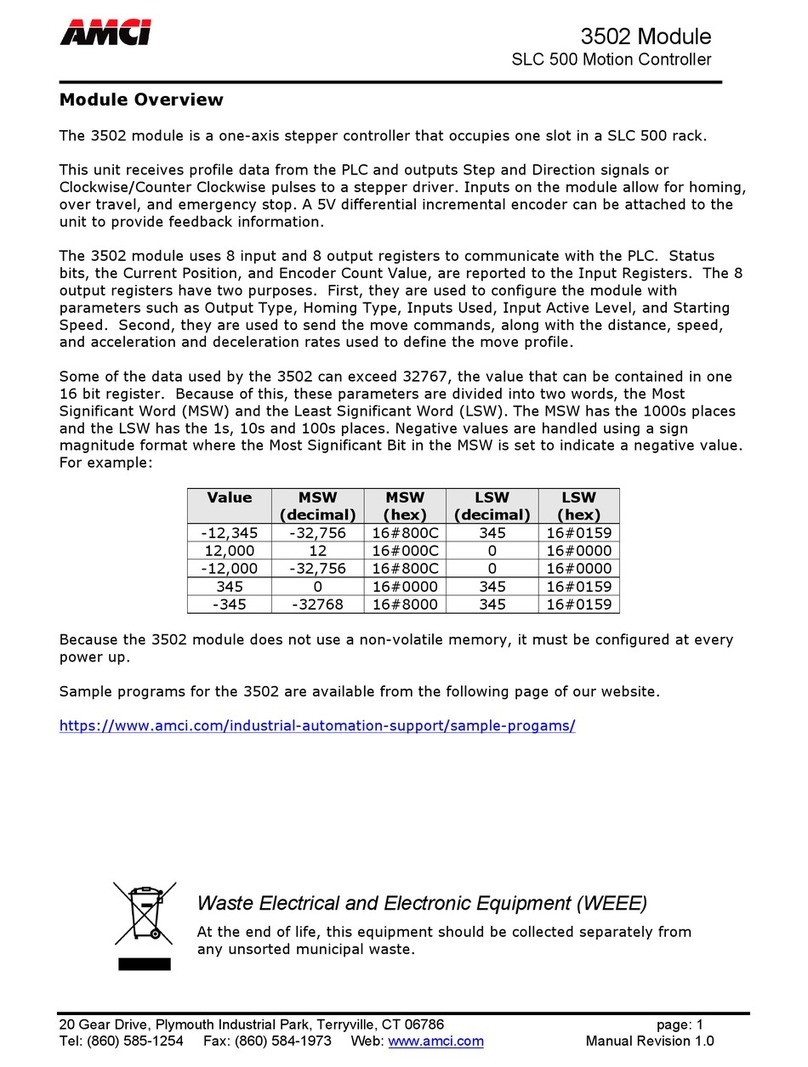
AMCI
AMCI 3502 User manual
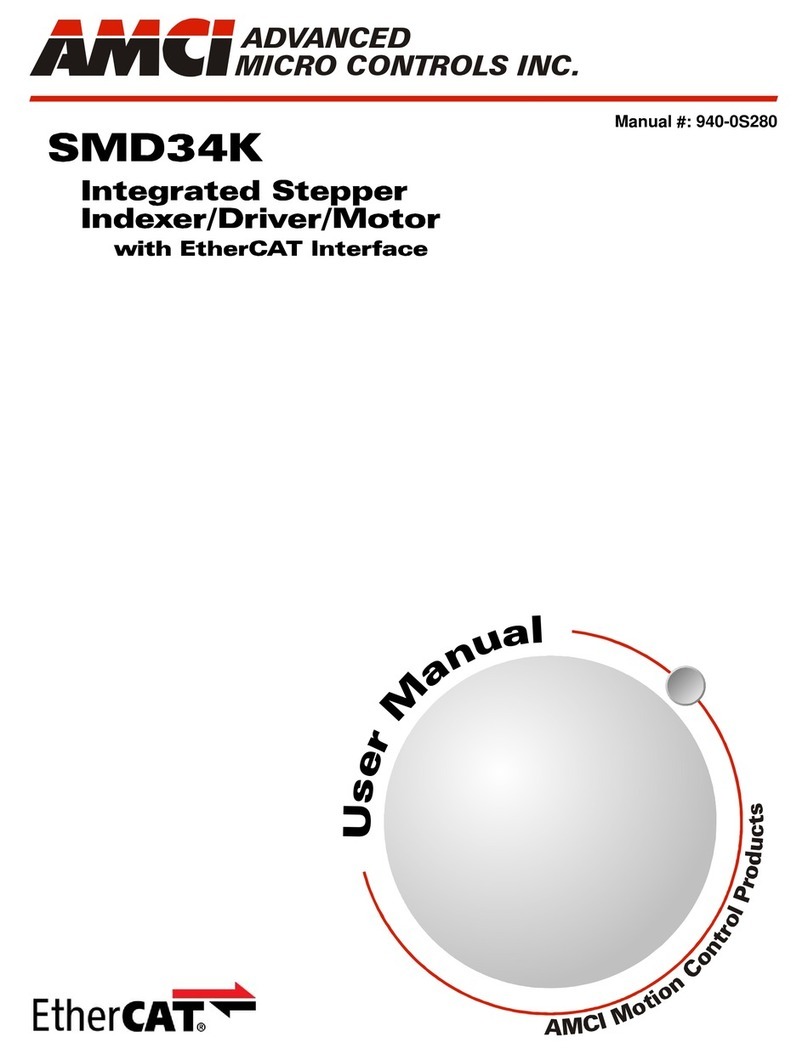
AMCI
AMCI SMD34K User manual
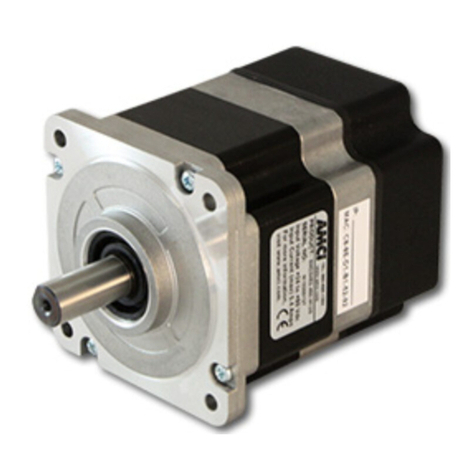
AMCI
AMCI SMD34E2 Instruction Manual
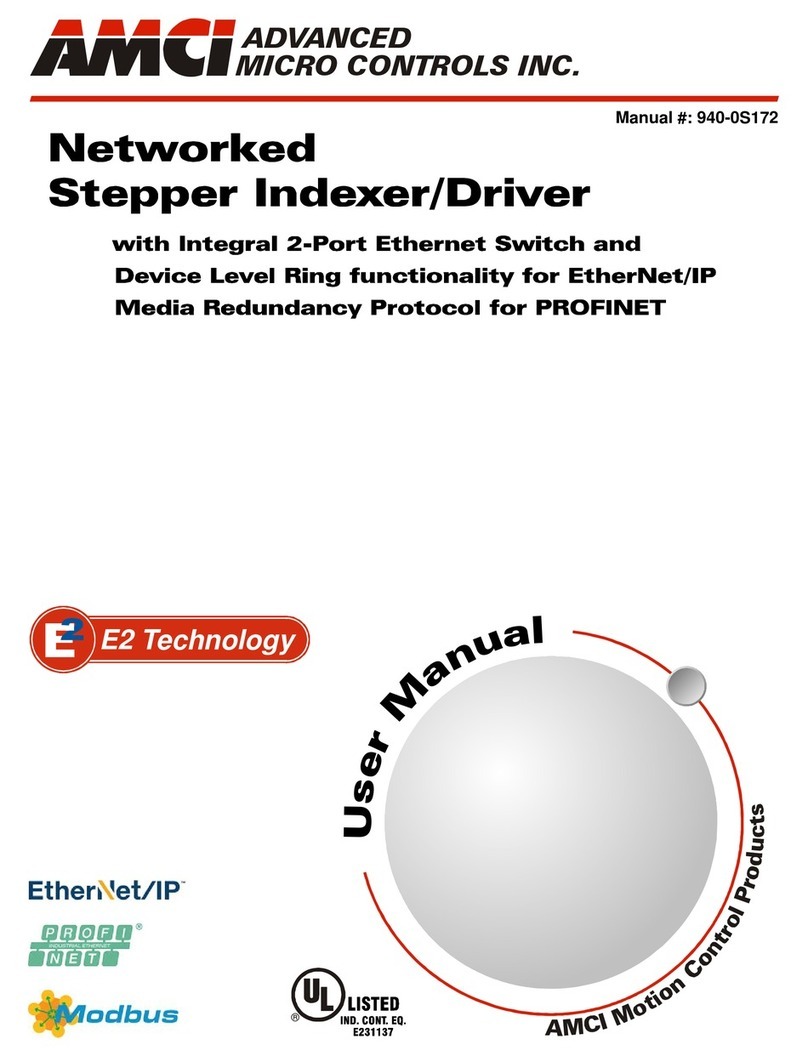
AMCI
AMCI SD17060E2 User manual
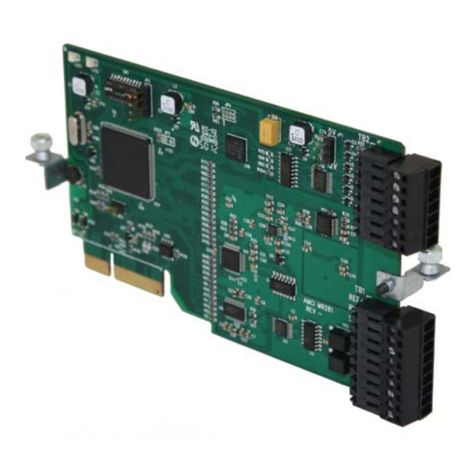
AMCI
AMCI PowerFlex 750 Series User manual
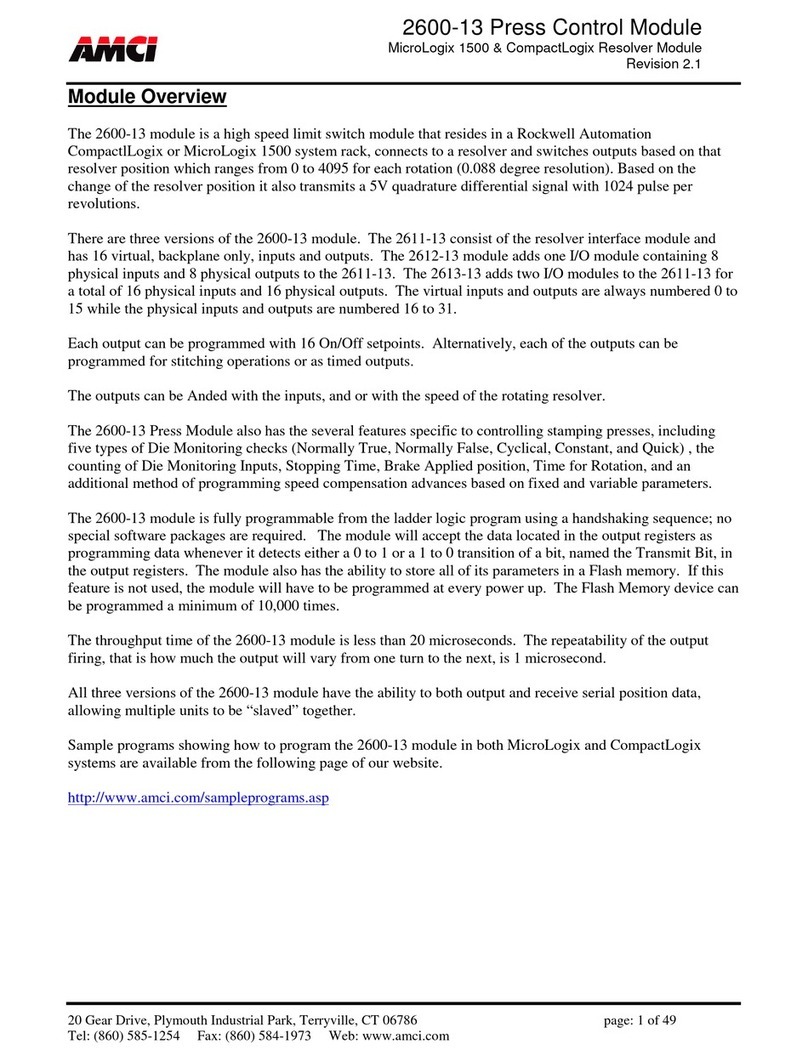
AMCI
AMCI 2600-13 User manual
Popular Control Unit manuals by other brands
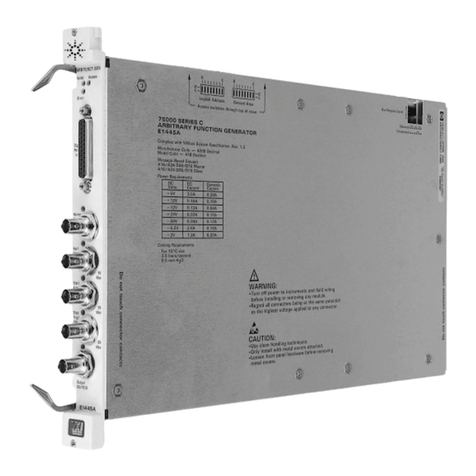
Keysight
Keysight E1445A User's manual and scpi programming guide

Siemens
Siemens Simatic S7-1500 manual
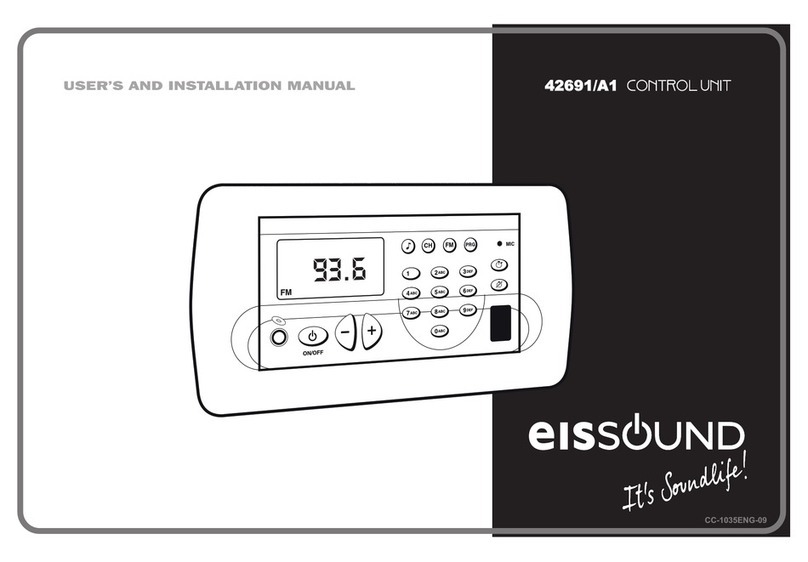
EisSound
EisSound 42691/A1 User and installation manual
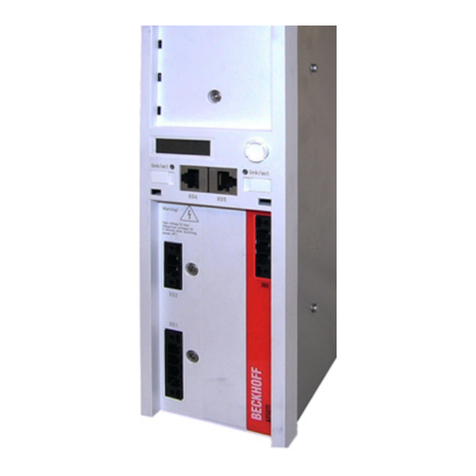
Beckhoff
Beckhoff AX5021 Documentation
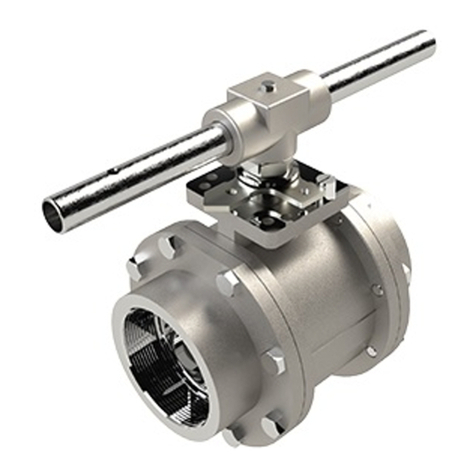
SVF
SVF FS7 Series Installation, Operation and Maintenace Manual
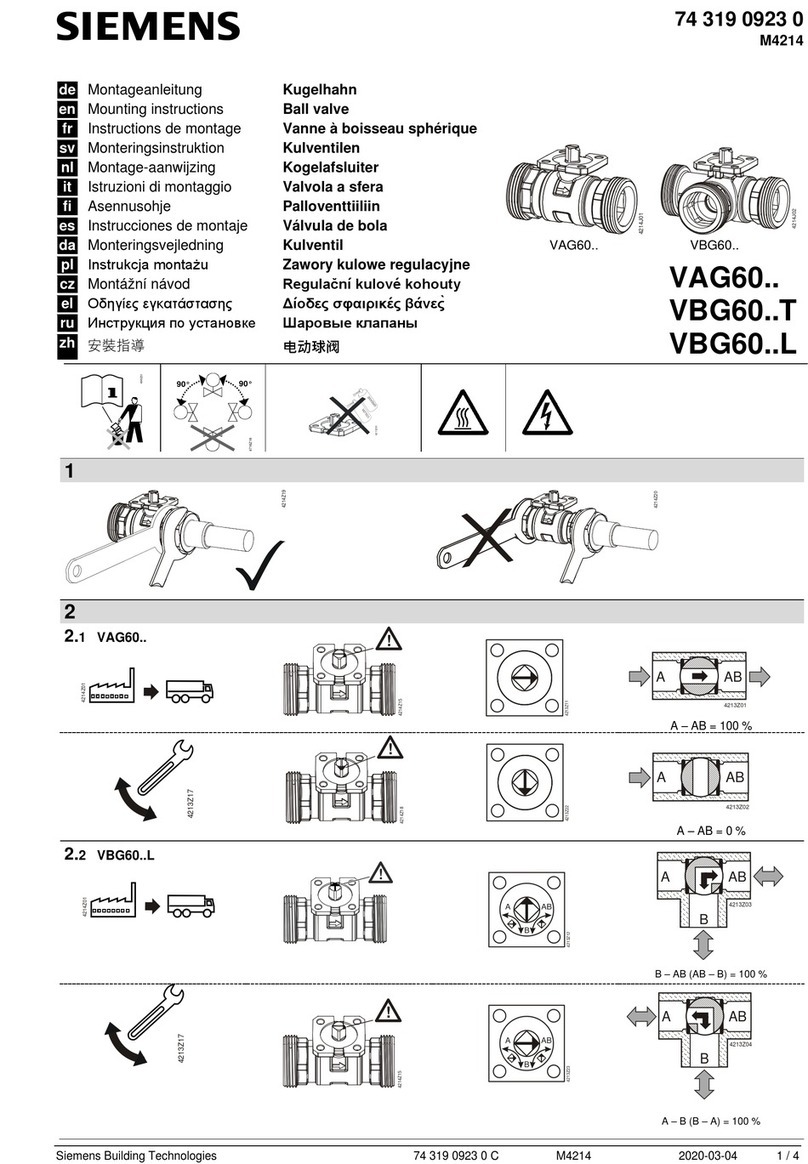
Siemens
Siemens VAG60 Series Mounting instructions